精益改善项目实例 ppt课件
合集下载
精益改善案例ppt课件

刀片夹板
绝缘胶带缠绕完成用刀片切断,刀片裸露,存在重大安全 隐患。
刀片内陷,减少安全隐患。
5
隔板循环使用
主体车的隔层垫板需循环利用,放置在架子上,占用场地。
在主体车上安装垫板托架,垫板放置方便,随车流动,方 便循环周转。
6
防止磁块漏装
客户反馈磁块多次漏安装。
从源头改善,制作工装,磁块单个弹出,方可用角铁拉杆铺设通道,货架 背靠背放置,减少铺设通道数量。
14
线路测试改善
手挡
欠 品
放置架
放置架 车附件
组装好线束需进行测试: 1、连接导线与线束都在桌面,凌乱。 2、寻找对应连接插座 3、车灯、手档未固定,操作不便。
插头
将连接线插座固定在桌面,并标明标识。 1、可以双手同时插插头。 2、减少寻找动作。 3、桌面整齐。
10
弯头安装
冷凝器需安装较多弯头,工作量大,在安装时参照图纸, 生产效率低,且有插错的品质不 良发生。
安装正确
安装错误 模板取不出
根据各品种制作简易对照模板,安装弯头前套入,免去安 装时对照图纸,提升作业效率。
在安装错误时,安装模板取不出,防止安装错误,保证产 品品质.
11
小物料拿取
垫片类物料拿取困难,效率低。
1
相互伤害
停车位区域划线
单线间隔,停车间距不好把握,开门易磕碰车身。
双线间隔,预留安全空隙,防止车门碰伤,促进和谐。 2
线体布局
横向走动作业,物流线路长。
流水线传送,由走动作业递减为转身作业。 3
夹具快速装卸
夹具装卸使用手拧螺丝。
螺丝上焊接把手,方便快捷。 或小气缸、快速夹。
4
刀片安全隐患
精益生产-改善项目案例讲解共45页PPT
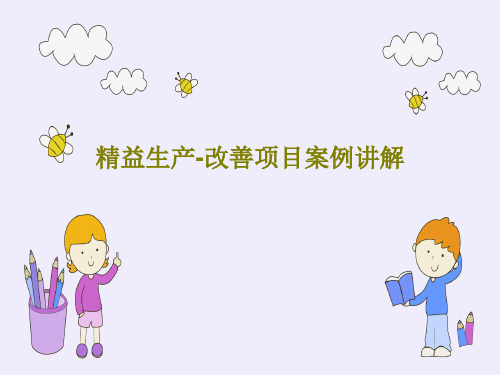
40、人类法律,事物有规律,这是不 容忽视 的。— 何源泉吸 收都不可耻。——阿卜·日·法拉兹
42、只有在人群中间,才能认识自 己。——德国
43、重复别人所说的话,只需要教育; 而要挑战别人所说的话,则需要头脑。—— 玛丽·佩蒂博恩·普尔
44、卓越的人一大优点是:在不利与艰 难的遭遇里百折不饶。——贝多芬
45、自己的饭量自己知道。——苏联
精益生产-改善项目案例讲解
36、如果我们国家的法律中只有某种 神灵, 而不是 殚精竭 虑将神 灵揉进 宪法, 总体上 来说, 法律就 会更好 。—— 马克·吐 温 37、纲纪废弃之日,便是暴政兴起之 时。— —威·皮 物特
38、若是没有公众舆论的支持,法律 是丝毫 没有力 量的。 ——菲 力普斯 39、一个判例造出另一个判例,它们 迅速累 聚,进 而变成 法律。 ——朱 尼厄斯
42、只有在人群中间,才能认识自 己。——德国
43、重复别人所说的话,只需要教育; 而要挑战别人所说的话,则需要头脑。—— 玛丽·佩蒂博恩·普尔
44、卓越的人一大优点是:在不利与艰 难的遭遇里百折不饶。——贝多芬
45、自己的饭量自己知道。——苏联
精益生产-改善项目案例讲解
36、如果我们国家的法律中只有某种 神灵, 而不是 殚精竭 虑将神 灵揉进 宪法, 总体上 来说, 法律就 会更好 。—— 马克·吐 温 37、纲纪废弃之日,便是暴政兴起之 时。— —威·皮 物特
38、若是没有公众舆论的支持,法律 是丝毫 没有力 量的。 ——菲 力普斯 39、一个判例造出另一个判例,它们 迅速累 聚,进 而变成 法律。 ——朱 尼厄斯
工厂精益生产改善案PPT(共 33张)
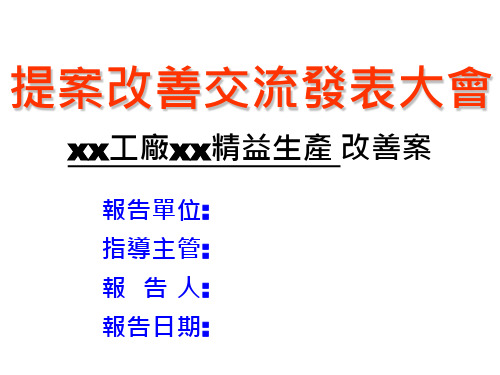
10 5 0
品質不穩定
00:00~ 02:00~ 04:00~ 06:00~ 08:00~ 10:00~ 12:00~ 14:00~ 16:00~ 18:00~ 20:00~ 22:00~
01:00 03:00 05:00 07:00 09:00 11:00 13:00 15:00 17:00 19:00 21:00 23:00
案
傳送帶
安裝節
實施單
層
上標示
拍控制
元生產
節拍線
器
(C1)
(C2)
(C3)
三. 改善歷程(2) --節奏式生產-矩陣分析
構造四個兩兩比較矩陣
A
A/B C1 C2
C3
C1 1 C1/C2 C1/C3 B1 B2
B3
C2 C2/C1 1 C2/C3
…… C3 C3/C1 C3/C2 1
C1 C2 C3
檢嚴重 段
生
工站排 配不合
理
物料搬 運頻繁
前後工站存 在重複動作
產
不
物料設計不 精
合理
益
Machine
Material
三. 改善歷程--改善思路
主要 問題
平衡性浪費
工時浪費
改善 1.消除動作浪費 3.縮短瓶頸時間
內容
2.推行節奏式生產 4.優化排班管理
改善
目的
消除工廠浪費,實現精益生產
三. 改善歷程(1) --改善HI-POT工站-動作分析
三. 改善歷程(1) --改善HI-POT工站-改善實施
合併Hi-Pot & Ast工站
Hi-pot工站 Combine
Ast工站
V=
F C
品質不穩定
00:00~ 02:00~ 04:00~ 06:00~ 08:00~ 10:00~ 12:00~ 14:00~ 16:00~ 18:00~ 20:00~ 22:00~
01:00 03:00 05:00 07:00 09:00 11:00 13:00 15:00 17:00 19:00 21:00 23:00
案
傳送帶
安裝節
實施單
層
上標示
拍控制
元生產
節拍線
器
(C1)
(C2)
(C3)
三. 改善歷程(2) --節奏式生產-矩陣分析
構造四個兩兩比較矩陣
A
A/B C1 C2
C3
C1 1 C1/C2 C1/C3 B1 B2
B3
C2 C2/C1 1 C2/C3
…… C3 C3/C1 C3/C2 1
C1 C2 C3
檢嚴重 段
生
工站排 配不合
理
物料搬 運頻繁
前後工站存 在重複動作
產
不
物料設計不 精
合理
益
Machine
Material
三. 改善歷程--改善思路
主要 問題
平衡性浪費
工時浪費
改善 1.消除動作浪費 3.縮短瓶頸時間
內容
2.推行節奏式生產 4.優化排班管理
改善
目的
消除工廠浪費,實現精益生產
三. 改善歷程(1) --改善HI-POT工站-動作分析
三. 改善歷程(1) --改善HI-POT工站-改善實施
合併Hi-Pot & Ast工站
Hi-pot工站 Combine
Ast工站
V=
F C
精益持续改善PPT课件
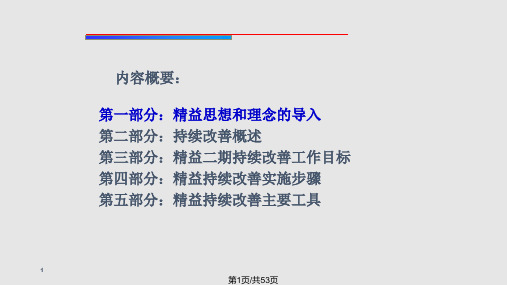
27
第27页/共53页
第四部分:持续改善活动实施步骤
1、实施步骤 步骤三:应对收集到的数据进行深入分析,以 便能弄清事情的真正背景及原因。 步骤四:在分析的基础上研究对策。 步骤五:导入、执行对策。
28
第28页/共53页
第四部分:持续改善活动实施步骤
1、实施步骤 步骤六:观察并记录采用对策后的影响。 步骤七:修改或重新制订标准,以避免类似问 题的再次发生。 步骤八:检查从步骤1到7的整个过程,据以引 入下一步的行动。
■工作场所人员改善意识的提高 ■改善氛围的营造 ■员工发现问题、解决问题能力的提高
各部门
持续
■标准作业表的优化及完善 ■现场各种浪费的杜绝 ■员工作业目标设定及执行 ■现场作业工具的改善,劳动生产率的提高 ■作业流程改善 ■现场安全作业标准制定
■“5S”及目视化推行
■物料出入库管理办法完善
■仓库呆废料的处置方法的制定
(2)能力开发和活用 养成经常考虑问题的习惯 加强发现问题的意识 提高工作的主人翁责任感 提高成本意识
第15页/共53页
16
第二部分:持续改善概述
7、“改善提案” 作用和意义
(3)提高人与人之间关系 加强部下与上司交流 加强横向交流 提高工作场所内的协作关系 (4)提高参与经营的意识 加强公司与个人的一体感 提高工作热情
26
第26页/共53页
第四部分:持续改善活动实施步骤
1、实施步骤
步骤一:选择工作任务
首先要阐明选择这个项目或工作任务的理由。这些 任务通常是根据企业的发展目标确定的,但有时企业的 现状也会影响这种选择—依据其重要性、紧迫性或经济 性。
步骤二:弄清当前的情况
在项目开始前必须要弄清项目当前情况的本质,并 予以分析。这需要人们去现场了解情况,运用KAIZEN 的“三现”原则,收集数据。
第27页/共53页
第四部分:持续改善活动实施步骤
1、实施步骤 步骤三:应对收集到的数据进行深入分析,以 便能弄清事情的真正背景及原因。 步骤四:在分析的基础上研究对策。 步骤五:导入、执行对策。
28
第28页/共53页
第四部分:持续改善活动实施步骤
1、实施步骤 步骤六:观察并记录采用对策后的影响。 步骤七:修改或重新制订标准,以避免类似问 题的再次发生。 步骤八:检查从步骤1到7的整个过程,据以引 入下一步的行动。
■工作场所人员改善意识的提高 ■改善氛围的营造 ■员工发现问题、解决问题能力的提高
各部门
持续
■标准作业表的优化及完善 ■现场各种浪费的杜绝 ■员工作业目标设定及执行 ■现场作业工具的改善,劳动生产率的提高 ■作业流程改善 ■现场安全作业标准制定
■“5S”及目视化推行
■物料出入库管理办法完善
■仓库呆废料的处置方法的制定
(2)能力开发和活用 养成经常考虑问题的习惯 加强发现问题的意识 提高工作的主人翁责任感 提高成本意识
第15页/共53页
16
第二部分:持续改善概述
7、“改善提案” 作用和意义
(3)提高人与人之间关系 加强部下与上司交流 加强横向交流 提高工作场所内的协作关系 (4)提高参与经营的意识 加强公司与个人的一体感 提高工作热情
26
第26页/共53页
第四部分:持续改善活动实施步骤
1、实施步骤
步骤一:选择工作任务
首先要阐明选择这个项目或工作任务的理由。这些 任务通常是根据企业的发展目标确定的,但有时企业的 现状也会影响这种选择—依据其重要性、紧迫性或经济 性。
步骤二:弄清当前的情况
在项目开始前必须要弄清项目当前情况的本质,并 予以分析。这需要人们去现场了解情况,运用KAIZEN 的“三现”原则,收集数据。
精益改善项目案例生产效率提升PPT课件(42页)(2024版)

项目范围: 项目通过推进精益生产,减少生产制造全流程内的浪费,有效减少作业人员、提升产量,缩短交付周期,在降低制造成本的同时,快速满足客户的需求。以工厂为试点,三地工厂同步实施,在制冷集团各事业部推广。
变量
名称
CTQ
单位
Y
生产效率提升
月人均产出
套/人
Y1
生产组织模式变革
订单交付周期
天
Y2
制造技术提升
大线组长 柔性线组长 柔性线巡检
减少1人 两两合并 两两合并
15
Y2改善(节选)—管理优化减员
改善效果:计划减员101人,实际减员101人,计划达成率100%。
部门(分厂)
总一
总二
总三
部装
注塑
财务
品质
职能部
目标(人)
7
2
6
3
31
14
18
20
推进 方向
Y1的改善 摘录1
改善项目名称:订单下达规范性
改善类别
技术
管理
设备
材料
费用
其它
√
改善前
改善后
问题点
改善方案
1、针对计划下达准确率、计划完成及时性的责任划分不明晰,产销责权关系不清,存在管理真空; 2、相关流程时间节点不规范、不合理,且操作随意性较强; 3、产销信息传递不畅。经常出现生产计划与销售计划间的信息不对称;
1、以文件形式彻底固化尾数清理流程、明确激励考核要求; 2、计划管理建立专人监控机制,按周、月通报 3、物资管理监督车间生产过程物料损耗,并每日统计滚动输出; 4、供应商建立安全库存,保证欠产物料补缺的及时性,减少超期作业任务产生; 5、车间物料管护规范每周稽查不少于2次。
精益改善项目实例PPT课件
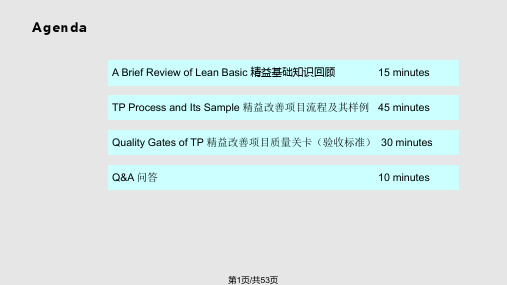
第21页/共53页
TP Process and Its Sample 改善项目流程及其样例
Design Phase Introduction 设计阶段介绍
第22页/共53页
TP Process and Its Sample 改善项目流程及其样例
Planning Phase Introduction 计划阶段介绍
第13页/共53页
A Brief Review of Lean Basic
CIP 持续改善
第14页/共53页
Agenda
A Brief Review of Lean Basic 精益基础知识回顾
15 minutes
TP Process and Its Sample 精益改善项目流程
45 minutes
Planning phase 计划阶段 1. 计划阶段的主要工作:
* 确定需要采取的改善行动区域的优先顺序; * 识别项目中工作任务分解后的工作包(WBS); * 识别资源需求及资源的可获得性; * 工作任务的职责确立; * 制定项目监督机制、制定行动计划等, * 通过计划这些活动从而可以制定出一套推行计划和对应的职责。 2. 该推行计划获得管理层的承诺以及推行小组签署该推行计划,来增加这些人 员的紧迫感和责任意识,使得接下来的推行阶段更加顺畅。 3. 值得借鉴的一条经验是要快速推行,以便打破旧有的模式如工作习惯、流程 等。
Mindset& Capability
第5页/共53页
A Brief Review of Lean Basic LHT three elements of success factors 汉莎精 益 管 理 三 要 M素anagement Infrastructure 管理基础
TP Process and Its Sample 改善项目流程及其样例
Design Phase Introduction 设计阶段介绍
第22页/共53页
TP Process and Its Sample 改善项目流程及其样例
Planning Phase Introduction 计划阶段介绍
第13页/共53页
A Brief Review of Lean Basic
CIP 持续改善
第14页/共53页
Agenda
A Brief Review of Lean Basic 精益基础知识回顾
15 minutes
TP Process and Its Sample 精益改善项目流程
45 minutes
Planning phase 计划阶段 1. 计划阶段的主要工作:
* 确定需要采取的改善行动区域的优先顺序; * 识别项目中工作任务分解后的工作包(WBS); * 识别资源需求及资源的可获得性; * 工作任务的职责确立; * 制定项目监督机制、制定行动计划等, * 通过计划这些活动从而可以制定出一套推行计划和对应的职责。 2. 该推行计划获得管理层的承诺以及推行小组签署该推行计划,来增加这些人 员的紧迫感和责任意识,使得接下来的推行阶段更加顺畅。 3. 值得借鉴的一条经验是要快速推行,以便打破旧有的模式如工作习惯、流程 等。
Mindset& Capability
第5页/共53页
A Brief Review of Lean Basic LHT three elements of success factors 汉莎精 益 管 理 三 要 M素anagement Infrastructure 管理基础
精益改善报告ppt课件

5.工具板的制作及刀具清单的建立
6.工位5S检点表及作业指导书的制作
.
14
改善前后对比(观测)(以46302011ACG为例)
改善前各工序标准工时
改善后各工序标准工时
序号 工序
机器
人标准工时 机器标准工时 序号 工序
机器
人标准工时 机器标准工时
1 下料
卧铣
15
5
1 下料
卧铣
10
3
2 飞底面
立铣
无 无
618m 12PCS/h/2人
改善后
U型布局 定岗定人
已建立 已建立
407m 24/h2人
提高了51.8% 提高了100%
.
22
活动目标:
一、生产效率提升50% 二、建立小批量生产线,岗位及人员的确定。
活动时间:6月3日-6月10日
.
23
改善范围:
观测小批量产品族的生产过程.
所做的工作:
.
25
改善前
改善后
550316员工负荷表
250
200 108
150
100
120 50
108
0 CNC2
工人总时间
.
26
改善前
改善后
543784员工负荷表
400
350 54
300
250
200
150
299
100
50
0 CNC1
67
310
318
CNC2
人工总时间
.
27
改善前
改善后
250 200 150 100
使用方便、快倢,便于锁咀的统计
与补充
精益生产成本改善实例PPT精品文档

.
*
只把人或设备的等待,看做等待浪费 的情况较多. 资材等待投入或产品在工艺流程中处于 停止状态、 资材或产品停滞在仓库的情况也是等待 浪费
等待浪费 因材料或作业的等待 或者闲暇时间而发生
等待浪费
对不起,请少等会儿...
还没 好吗?.
制造现场的七大浪费
.
*
加工本身的浪费 现在正做的作业是否真的 必要?为什么要这么做? 对作业进行反问。
”精益“
成本
什么是精益生产
.
*
精益生产-五个原则
Lean Manufacturing 精益生产
Value 价值
站在客户 的立场上
Value Stream 价值流
从接单到发货 过程的一切活动
Flow 流动
象开发的河流 一样通畅流动
Demand Pull 需求拉动
按需求生产
Perfect 追求完美
搬运浪费
制造现场的七大浪费
.
*
■ 3现原则
“ 浪费发现基于意识的改变 ..... " 没有思考的转变,就不可能发现浪费。 摈弃现有的想法、方式、基准。
▶ 3现的原则 到现场,看现物,掌握现象。
浪费的发现
去现场
看现物
掌握现象
[三现原则]
.
*
一切都从这里开始的 “三现主义” 到现场去 观察现物 了解现实
没有任何事物 是完美的 不断改进
降低成本, 改善质量, 缩短生产周期
.
*
什么是价值
按照顾客需求,在正确的时间,以合适的价格提供产品或者服务 根据顾客的需求定义价值
PCB
插装
搬运
波峰焊
检验
灌胶
*
只把人或设备的等待,看做等待浪费 的情况较多. 资材等待投入或产品在工艺流程中处于 停止状态、 资材或产品停滞在仓库的情况也是等待 浪费
等待浪费 因材料或作业的等待 或者闲暇时间而发生
等待浪费
对不起,请少等会儿...
还没 好吗?.
制造现场的七大浪费
.
*
加工本身的浪费 现在正做的作业是否真的 必要?为什么要这么做? 对作业进行反问。
”精益“
成本
什么是精益生产
.
*
精益生产-五个原则
Lean Manufacturing 精益生产
Value 价值
站在客户 的立场上
Value Stream 价值流
从接单到发货 过程的一切活动
Flow 流动
象开发的河流 一样通畅流动
Demand Pull 需求拉动
按需求生产
Perfect 追求完美
搬运浪费
制造现场的七大浪费
.
*
■ 3现原则
“ 浪费发现基于意识的改变 ..... " 没有思考的转变,就不可能发现浪费。 摈弃现有的想法、方式、基准。
▶ 3现的原则 到现场,看现物,掌握现象。
浪费的发现
去现场
看现物
掌握现象
[三现原则]
.
*
一切都从这里开始的 “三现主义” 到现场去 观察现物 了解现实
没有任何事物 是完美的 不断改进
降低成本, 改善质量, 缩短生产周期
.
*
什么是价值
按照顾客需求,在正确的时间,以合适的价格提供产品或者服务 根据顾客的需求定义价值
PCB
插装
搬运
波峰焊
检验
灌胶
精益生产改善专题项目模板(ppt)
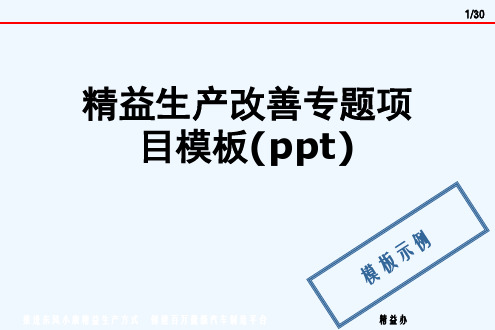
间
放吸塑盘
打包
QC抽检
半
成
品 仓
存放
周转过程
物
除尘
料 房
打包
周转过程
来料检验+试喷
静电除尘
素材组装
PVD
素材人工清洗
放入流水拉
车 间
自动喷底漆
转挂
镀膜
转挂
自动喷中漆
自动喷面漆
下件到吸塑盘
全检
半
成
存放
品
仓
3.3b 因果分析
编号
大Y或小Y
无△不良
无M1M2下 无M1M2上 限不良 限不良
合计
工序
输入
10
相 位 影 响 件 制 造
出 油 阀 制 造 与 改
与 改
与进 改
进
进
油柱 门塞 手付 柄制 问造 题与 改改 进进
第一次 气密检查
调试
第二次 气密检查
NO
NO
NO
不合格的M泵总成 返修
后期处理 入库
2.3 现状调查
直行率
75.00% 70.00%
焊装直行率的时间序列图
72.77%
73.49%
65.00% 60.00%
员工未按SOP 严格操作
装配后溢胶
点胶治具残胶
压合前时 间控制 装配顺序不当
胶路偏位
针头有残胶
两头溢胶
点胶路线不合理
点胶路径 装配手法不明确
未明确
环 针头外露长 度太短
法 员工培训 不到位
料
胶水长时间加热
PVD件变形导致 点胶量过多
溢胶\漏胶\ 断胶不良
3.2b 5Why分析
项目管理:质量改善案例DMAICPPT幻灯片
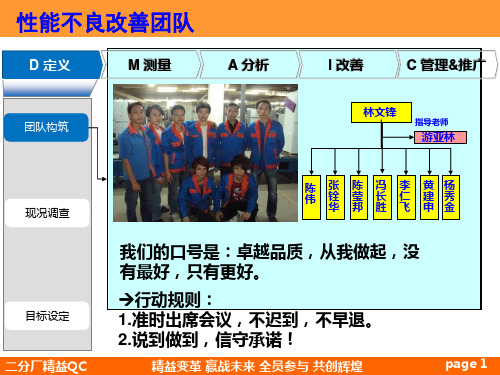
更换长弹簧,接触良好
C 管理&推广
效果确认
改善效果
1)减少由于电源接触不良导致箱体在抽空过程中出现断电现 象,加强抽空效果,减少抽空不良
二分厂精益QC
精益变革 赢战未来 全员参与 共创辉煌
page 14
改善事例 四
D定义
M测量
A 分析
I 改善
C 管理&推广
方案导出 方案实施
工位
管道 吹污
改善者
贺洪明 林文锋
200
不良数
70.0%
累积不良率
60.0%
150
50.0%
40.0% 100
30.0%
50
20.0%
10.0%
0
0.0%
结霜不均
不制冷
管折
制冷不合格 无停机点(cn) 回气管结霜
本月后续事项:对策标准化、水平展开
下期改善点现状调查
下期重点改善:结霜不均、安检不良
改善目标:结霜不均下降30%;安检不良下降
-20.45%
现状调查 目标设定
二分厂精益QC
11月性能不良改善目标
改善周期:
4.4%
10-11~11-30日;
3.5%
2.0%
本期目标:3%以下 质量改善以一个月
为PDCA循环改善,每
10月
11月 最终
月设定改善目标。
不良
目标 目标
精益变革 赢战未来 全员参与 共创辉煌
page 3
二分厂精益QC
二分厂精益QC
精益变革 赢战未来 全员参与 共创辉煌
page 8
工程流程图分析
D定义
M 测量
A 分析
精益生产系列现场管理和改善PPT
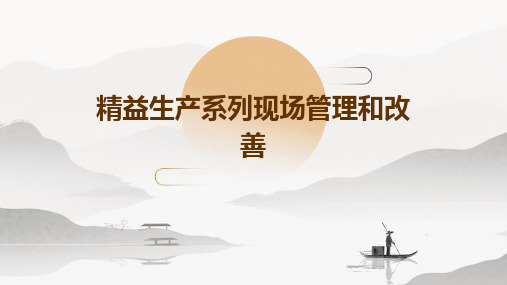
制定物品定置管理的标准操作流程,确保员 工能够按照标准执行。
目视化管理
01
视觉识别
利用颜色、图形、文字等视觉元素, 使信息传递更加直观。
异常预警
通过红、黄、绿等颜色标识,及时 发现异常情况并进行处理。
03
02
标准化操作流程
通过可视化的方式展示操作步骤和 要点,提高工作效率。
目视化沟通
促进员工之间的信息交流和协作, 提高整体工作效率。
生产布局优化
• 总结词:通过合理规划生产布局,降低物料搬运成本和时间。
• 详细描述:生产布局是指生产设备和人员在工作场所的布局方式。合理的生产布局可以降低物料搬运成本和时间,提高 生产效率。在传统生产模式下,设备和人员布局可能存在不合理之处,导致物料搬运距离过长、时间浪费等问题。通过 优化生产布局,企业可以将设备和人员集中在一起,减少物料搬运距离和时间。这不仅可以降低生产成本,还可以提高 产品质量和客户满意度。为了实现生产布局优化,企业需要对工作场所进行重新规划和设计,并加强员工培训和标准化 操作。
跨部门协作与沟通
加强部门间的沟通和协作, 共同推进持续改进工作。
培训与知识分享
开展相关培训和知识分享 活动,提高员工的质量意 识和持续改进能力。
05
员工参与与多技能培养
员工建议系统
鼓励员工提出改进意见
建立一个平台或渠道,让员工可以随时提出对生产流程、设备、 工作环境等方面的改进意见。
定期评审与实施
持续学习与发展
鼓励员工持续学习和提升,提供进一步培训和认证的机会,促进 个人职业发展。
员工激励措施
薪酬激励
提供具有竞争力的薪酬待遇,激励员工努力工作。
晋升机会
为员工提供明确的晋升通道和机会,激发员工的 积极性和工作动力。
目视化管理
01
视觉识别
利用颜色、图形、文字等视觉元素, 使信息传递更加直观。
异常预警
通过红、黄、绿等颜色标识,及时 发现异常情况并进行处理。
03
02
标准化操作流程
通过可视化的方式展示操作步骤和 要点,提高工作效率。
目视化沟通
促进员工之间的信息交流和协作, 提高整体工作效率。
生产布局优化
• 总结词:通过合理规划生产布局,降低物料搬运成本和时间。
• 详细描述:生产布局是指生产设备和人员在工作场所的布局方式。合理的生产布局可以降低物料搬运成本和时间,提高 生产效率。在传统生产模式下,设备和人员布局可能存在不合理之处,导致物料搬运距离过长、时间浪费等问题。通过 优化生产布局,企业可以将设备和人员集中在一起,减少物料搬运距离和时间。这不仅可以降低生产成本,还可以提高 产品质量和客户满意度。为了实现生产布局优化,企业需要对工作场所进行重新规划和设计,并加强员工培训和标准化 操作。
跨部门协作与沟通
加强部门间的沟通和协作, 共同推进持续改进工作。
培训与知识分享
开展相关培训和知识分享 活动,提高员工的质量意 识和持续改进能力。
05
员工参与与多技能培养
员工建议系统
鼓励员工提出改进意见
建立一个平台或渠道,让员工可以随时提出对生产流程、设备、 工作环境等方面的改进意见。
定期评审与实施
持续学习与发展
鼓励员工持续学习和提升,提供进一步培训和认证的机会,促进 个人职业发展。
员工激励措施
薪酬激励
提供具有竞争力的薪酬待遇,激励员工努力工作。
晋升机会
为员工提供明确的晋升通道和机会,激发员工的 积极性和工作动力。
精益项目报告(改善模板)ppt26

对课题进行统计分析并定义关注范围
Pareto Chart of Key Opportunities(关
键改善机会柏拉图)
4. Check(检查)Biblioteka 3. Do(实施)
Independent Study on Kaizen Needs(自主研讨改进需求)
Present Situation and Problems(现状及问题) Needed Output(需要产出):
Operations/ Station
Customer
Problem (问题)
Action Taken (采取行动)
Matrix (Unit) (单位)
Before(改 善前)
Result(结果)
After(改善 后)
% Improved (改善百分 比)
Savings(节约)
Method for Sustaining (持续改进 方法)
Hard ($/mth) Soft ($/mth)
硬收益
软收益
Photo - Before Kaizen(改善前图片)
Photo - After Kaizen(改善后图片)
Kaizen News Paper(改善新闻)
Action Item(改善项)
Who(改善 人)
Due Date (截止日期)
Hard ($/mth) Soft ($/mth)
硬收益
软收益
Photo - Before Kaizen(改善前图片)
Photo - After Kaizen(改善后图片)
Title: XXX
Sub-Title 2(子项目2) :XXXX (Individual Kaizen under the Project自主改善)
Pareto Chart of Key Opportunities(关
键改善机会柏拉图)
4. Check(检查)Biblioteka 3. Do(实施)
Independent Study on Kaizen Needs(自主研讨改进需求)
Present Situation and Problems(现状及问题) Needed Output(需要产出):
Operations/ Station
Customer
Problem (问题)
Action Taken (采取行动)
Matrix (Unit) (单位)
Before(改 善前)
Result(结果)
After(改善 后)
% Improved (改善百分 比)
Savings(节约)
Method for Sustaining (持续改进 方法)
Hard ($/mth) Soft ($/mth)
硬收益
软收益
Photo - Before Kaizen(改善前图片)
Photo - After Kaizen(改善后图片)
Kaizen News Paper(改善新闻)
Action Item(改善项)
Who(改善 人)
Due Date (截止日期)
Hard ($/mth) Soft ($/mth)
硬收益
软收益
Photo - Before Kaizen(改善前图片)
Photo - After Kaizen(改善后图片)
Title: XXX
Sub-Title 2(子项目2) :XXXX (Individual Kaizen under the Project自主改善)
超实用精益改善案例PPT幻灯片课件

• 所做的工作:
– 1.现场时间的观测 – 2.确定了存在的浪费 – 3.分析内部时间,外部时间 – 4.工位工刀具盒的制做 – 5.文件架的制做 – 6.建立快速换模工作站
41
珠海市俊凯机械有限公司
改善前
改善后
刀具无标志,使用时需寻找,测量, 这样会增加工人劳动强度,影响工 作效率,也不便刀具寿命的统计
序号 工序
机器
人标准工时 机器标准工时 序号 工序
机器
人标准工时 机器标准工时
1 下料
卧铣
15
5
1 下料
卧铣
10
3
2 飞底面
立铣
35
15
2 飞底面
立铣
30
15
3 铣长度
哈斯机
15
60
3 铣长度
哈斯机
10
64
4 铣内腔
起亚机
15
270
4 铣内腔
起亚机
10
110
5 铣外宽
哈斯机
15
80
5 铣外宽及沉孔 哈斯机
U型布局 定岗定人
已建立 已建立
407m 24/h2人
提高了51.8% 提高了100%
22
珠海市俊凯机械有限公司 活动目标:
一、生产效率提升50% 二、建立小批量生产线,岗位及人员的确定。
活动时间:6月3日-6月10日
23
珠海市俊凯机械有限公司
• 改善范围:
– 观测小批量产品族的生产过程.
• 所做的工作:
工具摆放混乱,没有标示,经常用工 具时需要到处寻找工具浪费时间
工具摆放整齐、标示清楚明了, 员工不需要再寻找工具。
33
珠海市俊凯机械有限公司
– 1.现场时间的观测 – 2.确定了存在的浪费 – 3.分析内部时间,外部时间 – 4.工位工刀具盒的制做 – 5.文件架的制做 – 6.建立快速换模工作站
41
珠海市俊凯机械有限公司
改善前
改善后
刀具无标志,使用时需寻找,测量, 这样会增加工人劳动强度,影响工 作效率,也不便刀具寿命的统计
序号 工序
机器
人标准工时 机器标准工时 序号 工序
机器
人标准工时 机器标准工时
1 下料
卧铣
15
5
1 下料
卧铣
10
3
2 飞底面
立铣
35
15
2 飞底面
立铣
30
15
3 铣长度
哈斯机
15
60
3 铣长度
哈斯机
10
64
4 铣内腔
起亚机
15
270
4 铣内腔
起亚机
10
110
5 铣外宽
哈斯机
15
80
5 铣外宽及沉孔 哈斯机
U型布局 定岗定人
已建立 已建立
407m 24/h2人
提高了51.8% 提高了100%
22
珠海市俊凯机械有限公司 活动目标:
一、生产效率提升50% 二、建立小批量生产线,岗位及人员的确定。
活动时间:6月3日-6月10日
23
珠海市俊凯机械有限公司
• 改善范围:
– 观测小批量产品族的生产过程.
• 所做的工作:
工具摆放混乱,没有标示,经常用工 具时需要到处寻找工具浪费时间
工具摆放整齐、标示清楚明了, 员工不需要再寻找工具。
33
珠海市俊凯机械有限公司
精益持续改善课件

流动与拉动的实现方式
企业可以通过单件流、单元化生产等方式实现流 动与拉动,提高生产效率和灵活性。
持续改进
持续改进的概念
持续改进是指不断发现问题、分析问题并采取措施解决问题,以提 高效率和效益的过程。
持续改进的方法
持续改进需要运用PDCA循环(Plan-Do-Check-Act循环)等工具 进行计划、执行、检查和行动,不断优化和改进生产和管理过程。
CHAPTER 02
精益持续改善的核心概念
价值流分析
价值流定义
价值流是指从原材料到最终产品 的一系列增值活动和过程,包括 产品设计、生产、运输、销售等
环节。
价值流分析的意义
通过价值流分析,企业可以识别 出哪些环节对创造价值有贡献, 哪些环节是浪费,从而优化整个
价值流,提高效率和效益。
价值流分析的方法
持续改进的文化建设
企业应该建立持续改进的文化,鼓励员工发现问题并提出改进意见, 通过团队协作和知识共享实现持续改进。
单元化生产
单元化生产的定义
单元化生产是指将生产线划分为独立的单元,每个单元负责特定的产品或零部件的生产, 以提高生产效率和灵活性。
单元化生产的优势
单元化生产可以减少产品在生产线上的停滞和等待时间,提高生产效率和质量稳定性。同 时,单元化生产还可以降低库存成本和运输成本,提高企业的整体效益。
单元化生产的实施方法
实施单元化生产需要对企业生产线进行重新规划和设计,根据产品特性和工艺要求划分单 元,并采用相应的设备和管理工具进行生产管理。同时,还需要对员工进行培训和技能提 升,以确保单元化生产的顺利实施和效益提升。
CHAPTER 03
精益持续改善工具与技术
5S管理
5S管理是精益生产中的一项基础管理技术,包括整理、整顿、清扫、清洁和素养五 个方面。
企业可以通过单件流、单元化生产等方式实现流 动与拉动,提高生产效率和灵活性。
持续改进
持续改进的概念
持续改进是指不断发现问题、分析问题并采取措施解决问题,以提 高效率和效益的过程。
持续改进的方法
持续改进需要运用PDCA循环(Plan-Do-Check-Act循环)等工具 进行计划、执行、检查和行动,不断优化和改进生产和管理过程。
CHAPTER 02
精益持续改善的核心概念
价值流分析
价值流定义
价值流是指从原材料到最终产品 的一系列增值活动和过程,包括 产品设计、生产、运输、销售等
环节。
价值流分析的意义
通过价值流分析,企业可以识别 出哪些环节对创造价值有贡献, 哪些环节是浪费,从而优化整个
价值流,提高效率和效益。
价值流分析的方法
持续改进的文化建设
企业应该建立持续改进的文化,鼓励员工发现问题并提出改进意见, 通过团队协作和知识共享实现持续改进。
单元化生产
单元化生产的定义
单元化生产是指将生产线划分为独立的单元,每个单元负责特定的产品或零部件的生产, 以提高生产效率和灵活性。
单元化生产的优势
单元化生产可以减少产品在生产线上的停滞和等待时间,提高生产效率和质量稳定性。同 时,单元化生产还可以降低库存成本和运输成本,提高企业的整体效益。
单元化生产的实施方法
实施单元化生产需要对企业生产线进行重新规划和设计,根据产品特性和工艺要求划分单 元,并采用相应的设备和管理工具进行生产管理。同时,还需要对员工进行培训和技能提 升,以确保单元化生产的顺利实施和效益提升。
CHAPTER 03
精益持续改善工具与技术
5S管理
5S管理是精益生产中的一项基础管理技术,包括整理、整顿、清扫、清洁和素养五 个方面。
- 1、下载文档前请自行甄别文档内容的完整性,平台不提供额外的编辑、内容补充、找答案等附加服务。
- 2、"仅部分预览"的文档,不可在线预览部分如存在完整性等问题,可反馈申请退款(可完整预览的文档不适用该条件!)。
- 3、如文档侵犯您的权益,请联系客服反馈,我们会尽快为您处理(人工客服工作时间:9:00-18:30)。
设计阶段
Project Management Feb 2011, Page 12
技术体系
管理基础
Mindset& Capability
意识及能力
A Brief Review of Lean Basic Six phases of transformation project 改善项目六个阶段
计划阶段
Project Management Feb 2011, Page 13
计划阶段: • 识别需要的资源及其可获得性; • 确定职责; • 确定项目进度控制; • 排序设计出来的措施的执行计划; • ……
A Brief Review of Lean Basic Six phases of transformation project 改善项目六个阶段
A Brief Review of Lean Basic Six phases of transformation project 改善项目六个阶段
诊断阶段
Project Management Feb 2011, Page 11
技术体系
管理基础
Mindset& Capability
意识及能力
A Brief Review of Lean Basic Six phases of transformation project 改善项目六个阶段
举例说明三要素的相互作用关系
Project Management Feb 2011, Page 8
M&C 意识和能力 的改善
MI 管理基础的改善 如5S审核
A Brief Review of Lean Basic
Influence Model 影响模型
榜样及领导力
理解和信奉
能力提升
Project Management Feb 2011, Page 9
体系及结构
A Brief Review of Lean Basic
Six phases of transformation project 改善项目六个阶段
准备阶段
ProjeБайду номын сангаасt Management Feb 2011, Page 10
准备阶段: • 确定项目范围、项目目标; • 项目计划; • 团队组建、项目组成员培训; • 现场采访、数据收集; • 跟各个部门商谈项目成员、部门期望及前提; • 项目动员会/启动会…..
实施阶段
Project Management Feb 2011, Page 14
实施阶段 • 按照制定的实施计划去落实执行相应的措施; • 监控实施的效果:如质量、准时、效率等; • 必要的调整; • 更新IQ MOVE的程序; • ……
A Brief Review of Lean Basic
CIP 持续改善
Q&A 问答
10 minutes
Project Management Feb 2011, Page 16
TP Process and Its Sample 改善项目流程及其样例
Overview of TP Process 改善项目总览
改善项目总览 1. 汉莎提出了包含六个步骤“准备、诊断、设计、计划、执行、巩固”的实施流程(如 下图所示),每个步骤都定义了其要实现的目标,在各个阶段的工作重点涵盖前面所说 的成功实施精益管理的三个要素:技术体系(Technical System)、管理基础(Management Infrastructure)、意识和能力 (Mindset & Capability)。后面将逐一介绍各个阶段的 目标、工作内容、需要进行的沟通等,其中汉莎的经验被列在借鉴经验一栏中。
Q&A 问答
10 minutes
Project Management Feb 2011, Page 2
A Brief Review of Lean Basic
Value Added Activities 增值活动
Project Management Feb 2011, Page 3
A Brief Review of Lean Basic
Lean TP Process Introduction 精益改善项目流程介绍
Agenda
A Brief Review of Lean Basic 精益基础知识回顾
15 minutes
TP Process and Its Sample 精益改善项目流程及其样例 45 minutes
Quality Gates of TP 精益改善项目质量关卡(验收标准) 30 minutes
Project Management Feb 2011, Page 15
Agenda
A Brief Review of Lean Basic 精益基础知识回顾
15 minutes
TP Process and Its Sample 精益改善项目流程
45 minutes
Quality Gates of TP 精益改善项目质量关卡(验收标准) 30 minutes
Management Infrastructure 管理基础: 管理与技术体系相关资源的组织结构、流 程、 体系等
Mindset & Capability 意识和能力: 个体和团队的观念意识, 正确对待改善活 动及挑战,以及有能力去面对需要的改进 和应对挑战
Mindset& Capability
Project Management Feb 2011, Page 6
Increased value creation first required waste reduction
Project Management Feb 2011, Page 4
增值活动所占比例的增加是通 过减少浪费,而非提高产能
A Brief Review of Lean Basic
Overview of 7 types of waste 7大浪费总览
Project Management Feb 2011, Page 5
A Brief Review of Lean Basic
LHT three elements of success factors 汉莎精益管理三要素
Technical System 技术体系: 创造价值的工艺过程、方法、工具、设备等
A Brief Review of Lean Basic LHT three elements of success factors 汉莎精益管理三要素
Management Infrastructure 管理基础
Project Management Feb 2011, Page 7
A Brief Review of Lean Basic LHT three elements of success factors 汉莎精益管理三要素
Project Management Feb 2011, Page 12
技术体系
管理基础
Mindset& Capability
意识及能力
A Brief Review of Lean Basic Six phases of transformation project 改善项目六个阶段
计划阶段
Project Management Feb 2011, Page 13
计划阶段: • 识别需要的资源及其可获得性; • 确定职责; • 确定项目进度控制; • 排序设计出来的措施的执行计划; • ……
A Brief Review of Lean Basic Six phases of transformation project 改善项目六个阶段
A Brief Review of Lean Basic Six phases of transformation project 改善项目六个阶段
诊断阶段
Project Management Feb 2011, Page 11
技术体系
管理基础
Mindset& Capability
意识及能力
A Brief Review of Lean Basic Six phases of transformation project 改善项目六个阶段
举例说明三要素的相互作用关系
Project Management Feb 2011, Page 8
M&C 意识和能力 的改善
MI 管理基础的改善 如5S审核
A Brief Review of Lean Basic
Influence Model 影响模型
榜样及领导力
理解和信奉
能力提升
Project Management Feb 2011, Page 9
体系及结构
A Brief Review of Lean Basic
Six phases of transformation project 改善项目六个阶段
准备阶段
ProjeБайду номын сангаасt Management Feb 2011, Page 10
准备阶段: • 确定项目范围、项目目标; • 项目计划; • 团队组建、项目组成员培训; • 现场采访、数据收集; • 跟各个部门商谈项目成员、部门期望及前提; • 项目动员会/启动会…..
实施阶段
Project Management Feb 2011, Page 14
实施阶段 • 按照制定的实施计划去落实执行相应的措施; • 监控实施的效果:如质量、准时、效率等; • 必要的调整; • 更新IQ MOVE的程序; • ……
A Brief Review of Lean Basic
CIP 持续改善
Q&A 问答
10 minutes
Project Management Feb 2011, Page 16
TP Process and Its Sample 改善项目流程及其样例
Overview of TP Process 改善项目总览
改善项目总览 1. 汉莎提出了包含六个步骤“准备、诊断、设计、计划、执行、巩固”的实施流程(如 下图所示),每个步骤都定义了其要实现的目标,在各个阶段的工作重点涵盖前面所说 的成功实施精益管理的三个要素:技术体系(Technical System)、管理基础(Management Infrastructure)、意识和能力 (Mindset & Capability)。后面将逐一介绍各个阶段的 目标、工作内容、需要进行的沟通等,其中汉莎的经验被列在借鉴经验一栏中。
Q&A 问答
10 minutes
Project Management Feb 2011, Page 2
A Brief Review of Lean Basic
Value Added Activities 增值活动
Project Management Feb 2011, Page 3
A Brief Review of Lean Basic
Lean TP Process Introduction 精益改善项目流程介绍
Agenda
A Brief Review of Lean Basic 精益基础知识回顾
15 minutes
TP Process and Its Sample 精益改善项目流程及其样例 45 minutes
Quality Gates of TP 精益改善项目质量关卡(验收标准) 30 minutes
Project Management Feb 2011, Page 15
Agenda
A Brief Review of Lean Basic 精益基础知识回顾
15 minutes
TP Process and Its Sample 精益改善项目流程
45 minutes
Quality Gates of TP 精益改善项目质量关卡(验收标准) 30 minutes
Management Infrastructure 管理基础: 管理与技术体系相关资源的组织结构、流 程、 体系等
Mindset & Capability 意识和能力: 个体和团队的观念意识, 正确对待改善活 动及挑战,以及有能力去面对需要的改进 和应对挑战
Mindset& Capability
Project Management Feb 2011, Page 6
Increased value creation first required waste reduction
Project Management Feb 2011, Page 4
增值活动所占比例的增加是通 过减少浪费,而非提高产能
A Brief Review of Lean Basic
Overview of 7 types of waste 7大浪费总览
Project Management Feb 2011, Page 5
A Brief Review of Lean Basic
LHT three elements of success factors 汉莎精益管理三要素
Technical System 技术体系: 创造价值的工艺过程、方法、工具、设备等
A Brief Review of Lean Basic LHT three elements of success factors 汉莎精益管理三要素
Management Infrastructure 管理基础
Project Management Feb 2011, Page 7
A Brief Review of Lean Basic LHT three elements of success factors 汉莎精益管理三要素