轧钢用水平连铸圆坯标准
连铸圆坯标准

连铸圆坯标准
连铸圆坯是指通过钢铁连铸技术,在连铸机上连续铸造出的圆形钢坯。
目前,国家标准中对连铸圆坯的技术要求主要包括以下两个标准:
GB/T 17426-2019《连铸钢坯尺寸、形状、重量和允许偏差》:该标准规定了连铸钢坯尺寸、形状、重量和允许偏差的技术要求,包括圆径、圆周、偏差、重量等方面的要求。
GB/T 6394-2017《钢铁产品取样方法》:该标准规定了钢铁产品取样的方法和规范,包括取样位置、数量、样品标识和保存等要求。
除了以上两个标准,还有许多与连铸圆坯生产相关的标准和规范,如废钢管理、铸坯表面质量要求等。
这些标准和规范对于保障连铸圆坯的生产质量和安全性具有重要意义。
1。
连铸圆坯质量控制

连铸圆坯质量控制连铸坯质量检验及控制一、连铸坯的内部结构(凝固组织)的一般特征及检验。
连铸坯的检验方法连铸坯的内部结构:经过酸浸(酸洗)或硫印的方法在连铸坯横断面或纵断面上用肉眼或低倍放大镜看到内部组织结果。
硫印硫印是用感光相纸显示试样上硫偏析(合金中各组成元素在结晶时分布不均匀的现象称为偏析)的方法,主要用于钢铁行业铸坯质量的检验。
从铸坯上取纵向或横向试样,试验面加工的光洁度不应低于6。
使用反差大的溴化银表面相纸,把与试样大小相同的相纸放入稀硫酸中浸泡1-2分钟后取出,将相纸对准检查面轻轻覆盖好,将试样与相纸间气泡赶净,待接触2-5分钟后取下,将相纸在流水中冲洗,然后定影烘干,即完成一张硫印。
印基本原理:硫酸与试样上的硫化物(FeS、MnS)发生反应,生成硫化氢气体,硫化氢气体再与感光相纸上的溴化银作用,生成硫化银沉淀在相纸相应的位置上,形成黑色或褐色斑点。
用硫印试验,可显示钢锭、连铸坯中心裂纹、偏析线、低倍结构和夹杂分布等。
酸洗用酸液洗去基体表面锈蚀物和轧皮的过程。
用酸浸或硫印法所显示的组织结构属于宏观结构,是连铸坯和金属材料检验中最为常见的检验技术。
连铸坯的内部结构连铸坯自表面至中心都是由边缘等轴晶区(激冷区)、柱状晶区和中心等轴晶,区三部分组成。
温度梯度较大时,固液两相区(图1)小,有利于柱状晶的生长,而凝固速度较快,则易于生成枝晶间距小的铸造组织,所以连铸坯具有较发达的柱状晶组织,并具有较小的枝晶间距。
(图1)枝晶间距是指相邻同次枝晶间的垂直距离,它是树枝晶组织细化程度的表征。
枝晶间距越小,组织就越细密,分布于其间的元素偏析范围也就越小,故越容易通过热处理而均匀化。
通常采用的有一次枝晶(柱状晶主干)间距d1,和二次分枝间距d2两种。
连铸坯宏观组织的好坏可以用等轴晶所占的比例多少来衡量,轴晶结构致密,加工性能能好。
柱状晶具有明显的方向性,加工性能差,容易导致中心偏析,中心疏松和中心裂纹等缺陷。
连铸坯、钢板检验规定
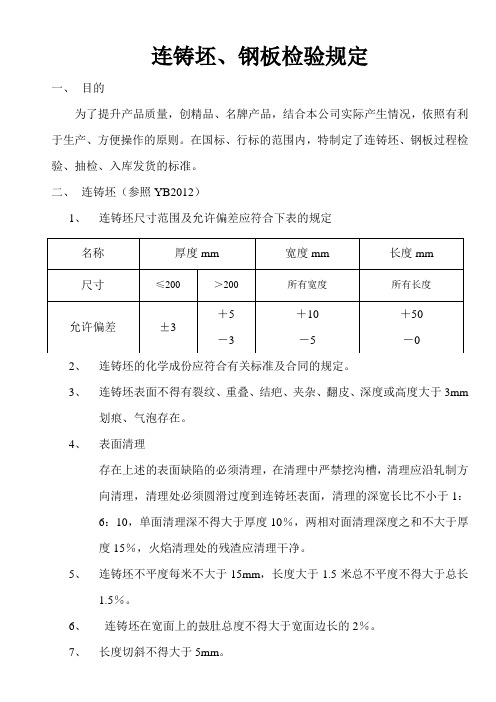
连铸坯、钢板检验规定一、目的为了提升产品质量,创精品、名牌产品,结合本公司实际产生情况,依照有利于生产、方便操作的原则。
在国标、行标的范围内,特制定了连铸坯、钢板过程检验、抽检、入库发货的标准。
二、连铸坯(参照YB2012)1、连铸坯尺寸范围及允许偏差应符合下表的规定2、连铸坯的化学成份应符合有关标准及合同的规定。
3、连铸坯表面不得有裂纹、重叠、结疤、夹杂、翻皮、深度或高度大于3mm划痕、气泡存在。
4、表面清理存在上述的表面缺陷的必须清理,在清理中严禁挖沟槽,清理应沿轧制方向清理,清理处必须圆滑过度到连铸坯表面,清理的深宽长比不小于1:6:10,单面清理深不得大于厚度10%,两相对面清理深度之和不大于厚度15%,火焰清理处的残渣应清理干净。
5、连铸坯不平度每米不大于15mm,长度大于1.5米总不平度不得大于总长1.5%。
6、连铸坯在宽面上的鼓肚总度不得大于宽面边长的2%。
7、长度切斜不得大于5mm。
8、测量位置厚度---以距侧边及端面部位约100-200mm处卡量。
宽度---在长度方向中部测量为准长度---连铸坯长度的最短距离处测量为准三、钢板(参照GB709)1、钢板尺寸范围及允许偏差应符合下表的规定宽度公差钢板的长度允许偏差注:厚度公差见附后表A四切边钢板:对角线按5-15mm验收,单边长度按0-8mm验收。
四毛边钢板:在宽度方向上单边距板边40mm不保性能,小缺陷不于修磨,长度距板头150mm内不保性能及不于修磨表面缺陷。
两头切钢板:单边长度按0-8mm验收,两端头凸凹小于150mm不于切头,大于150mm需切头。
2、表面不得有裂纹、重叠、结疤、夹杂、气泡、拉裂、氧化铁皮压入等缺陷存在。
3、钢板的化学成份应符合有关标准及合同的规定。
4、表面清理存在上述的表面缺陷应进行修磨,在清理中严禁挖沟槽,修磨应光滑过渡到钢板表面,清理深宽长比不小于1:6:10。
5、对于锅炉、压力容器、船体结构用的钢板和合同中规定的特殊用途的钢板,缺陷下面钢板的厚度应不小于相应钢板产品标准中规定的最小允许厚度。
圆管坯检验质量标准
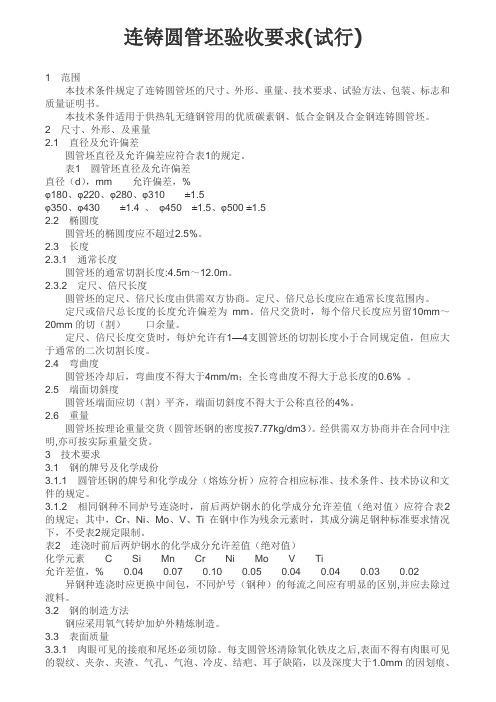
连铸圆管坯验收要求(试行)1 范围本技术条件规定了连铸圆管坯的尺寸、外形、重量、技术要求、试验方法、包装、标志和质量证明书。
本技术条件适用于供热轧无缝钢管用的优质碳素钢、低合金钢及合金钢连铸圆管坯。
2 尺寸、外形、及重量2.1 直径及允许偏差圆管坯直径及允许偏差应符合表1的规定。
表1 圆管坯直径及允许偏差直径(d),mm 允许偏差,%φ180、φ220、φ280、φ310 ±1.5φ350、φ430 ±1.4 、φ450 ±1.5、φ500 ±1.52.2 椭圆度圆管坯的椭圆度应不超过2.5%。
2.3 长度2.3.1 通常长度圆管坯的通常切割长度:4.5m~12.0m。
2.3.2 定尺、倍尺长度圆管坯的定尺、倍尺长度由供需双方协商。
定尺、倍尺总长度应在通常长度范围内。
定尺或倍尺总长度的长度允许偏差为mm。
倍尺交货时,每个倍尺长度应另留10mm~20mm的切(割)口余量。
定尺、倍尺长度交货时,每炉允许有1—4支圆管坯的切割长度小于合同规定值,但应大于通常的二次切割长度。
2.4 弯曲度圆管坯冷却后,弯曲度不得大于4mm/m;全长弯曲度不得大于总长度的0.6% 。
2.5 端面切斜度圆管坯端面应切(割)平齐,端面切斜度不得大于公称直径的4%。
2.6 重量圆管坯按理论重量交货(圆管坯钢的密度按7.77kg/dm3)。
经供需双方协商并在合同中注明,亦可按实际重量交货。
3 技术要求3.1 钢的牌号及化学成份3.1.1 圆管坯钢的牌号和化学成分(熔炼分析)应符合相应标准、技术条件、技术协议和文件的规定。
3.1.2 相同钢种不同炉号连浇时,前后两炉钢水的化学成分允许差值(绝对值)应符合表2的规定;其中,Cr、Ni、Mo、V、Ti在钢中作为残余元素时,其成分满足钢种标准要求情况下,不受表2规定限制。
表2 连浇时前后两炉钢水的化学成分允许差值(绝对值)化学元素 C Si Mn Cr Ni Mo V Ti允许差值,% 0.04 0.07 0.10 0.05 0.04 0.04 0.03 0.02 异钢种连浇时应更换中间包,不同炉号(钢种)的每流之间应有明显的区别,并应去除过渡料。
连铸圆坯工艺规程

大方圆坯连铸技术工艺规程1 连铸钢水要求连铸钢水必须经炉外精炼,保证脱氧充分,成分、温度均匀,符合连铸要求。
1.1 液相线温度的确定钢水液相线温度按照下式计算:TL=1536℃-[78×C%+7.6×Si%+4.9×Mn%+34×(P+S)%+5×Al%+1.5%×Cr%+2.0×Mo%+2.0×V%+18.0×Ti%+4.0×Ca%+5.0×Cu%]其中:C%——为钢种中碳的百分含量Si%——为钢种中硅的百分含量Mn%——为钢种中锰的百分含量(P+S)%——为钢种中的硫和磷的百分含量Al%——为钢种中铝的百分含量1536℃——为纯铁的液相线温度,TL——为钢种液相线温度1.2 连铸钢水温度要求钢包钢水温度必须控制在连铸要求的范围内,即:a.低碳钢:TL+(70~80)℃(第一炉)b.中碳钢:TL+(65~75)℃(第一炉)c.高碳钢:TL+(55~65)℃(第一炉)d.三流浇注、零次罐+5:℃e.浇注小断面:+5℃第二炉及以后各炉均比第一炉低10~20℃2 中间包准备2.1 中间包修砌2.1.1 绝热层砌砖A.砖与座砖模子应留出120mm的间距。
B.不得使用有裂纹、受潮变质及严重残缺的砖。
C.砖缝≯2mm,并保证砌缝灰浆饱满。
D.砌筑用高温火泥搅拌均匀、稠度合适。
2.1.2 中间包永久层浇注A.投入搅拌机的搅拌量不应超过搅拌机定量的50%。
B.干料加入搅拌机内,应干混1-2分钟,按重量比加入8-10%的水,继续搅拌2-3分钟,混匀即可出料。
C.搅拌好的料应尽快使用,以在15分钟内用完为宜。
D.浇注时应用边加料边振动的连续施工法,一次加料不宜超过300mm高。
E.包底浇注高度距包底钢板180mm。
F.振动以泥料充分泛浆无大的气泡冒出为宜,从料中取出振动棒时,不宜过快,防止造成空洞。
G.浇注完中间包底养生2小时后方可支模板,模板与绝热层间距为123mm。
钢锭连铸坯验收标准

钢锭连铸坯验收标准
1、连铸坯的化学成份应符合有关标准的规定;
2、尺寸允许偏差;
尺寸130×130、200×200、φ130、φ200边长允许偏差(mm)±4.0±6.0 对角线长度之差(mm)≤6.0≤9.0 允许偏差(mm)±3.0±4.0椭圆度(mm)不大于直径公差的0.75倍;
3、外形:
3.1、方坯弯曲度每米不大于20 mm,总弯曲度不大于总长度的1.5%;
3.2、圆坯弯曲度每米不大于15 mm,总弯曲度不大于总长度的1.0%;
3.3不得有明显的扭转,端部切斜不得大于10 mm;
4、表面质量□不得有肉眼可见的裂纹、重叠、结疤、夹渣、夹杂、气孔、深度(高度)大于3mm的滑痕、划伤、皱纹、凸块。
如有上述缺陷存在则必须清除,清除深、宽、长比不得小于1:6:8;
5、保证连铸坯的质量,头坯、尾坯的切除量规定如下:
头坯:不得少于700mm;
尾坯:不得少于1000 mm 如头坯切除量达不到上述要求,则判第一条坯为利用品;
尾坯切除量达不到上述要求,则判最后一条坯为利用品;
6、班组质量员对连铸坯进行逐支检查,写上炉号和钢号,注明利用品,按炉做好原始记录;
7、质检部质检员每天对表面质量进行检查,合格品盖上“检”字章,做好抽查记录。
铸坯质量相关问题

铸坯质量相关问题铸坯质量标准如下:1、边长允许偏差±5.0 mm。
2、对角线之差±14.0 mm。
3、连铸坯的弯曲度每米不得大于20 mm,总弯曲度不得大于总长度的2%。
4、连铸坯允许鼓肚,但高度不得超过连铸坯边长的允许正偏差(5 mm)。
5、连铸坯端部切斜不得大于20 mm。
6、连铸坯不得有明显的扭转。
7、连铸坯表面不得有肉眼可见的裂纹、重接、翻皮、结疤、夹杂、深度或高度大于3 mm的划痕、压痕、擦伤、气孔,皱纹、冷溅、耳子、凹坑和深度大于2 mm的发纹。
连铸坯横截面不得有缩孔、皮下气泡。
铸坯质量分析:(一)、脱方1、缺陷特征:横截面上两个对角线超标,常伴随有角部横裂和内部裂纹的产生。
2、影响:在加热炉内造成堆钢,在轧制时产生折叠或扭转;铸坯因脱方而伴随角部内裂,易在轧制时产生裂边缺陷。
3、产生原因:(1)一冷、二冷冷却不均匀;(2)结晶器铜管尺寸不合适,铜管变形,磨损严重;(3)连铸机对弧不准;(4)结晶器振动不平稳。
4、预防及消除办法(1)保证结晶器水缝均匀;(2)保证一冷水水质,防止结垢;(3)保证结晶器铜管尺寸,及时更换结晶器铜管;(4)保证二冷段喷嘴对中,切喷嘴无堵塞;(5)对弧精度符合工艺要求;(6)调整好振动参数,使结晶器振动平稳,无偏振现象。
(二)、中心线裂纹1、缺陷特征:铸坯中心线有裂纹,类似方坯的中心疏松,中心线周围有严重的疏松、偏析和夹杂物。
2、影响及危害:在轧制无法焊合,在钢材上成为缩孔残余或分层。
3、产生原因:钢液在冷却和结晶过程中体积收缩时填充不足所致。
具体原因如下:(1)铸坯在冷却的过程中冷却强度不够;(2)拉速过快;(3)浇注温度过高;(4)扇形段辊间距不合适。
4、预防和消除办法:(1)增大比水量,延长冷却段;(2)控制拉速;(3)降低钢水过热度;(4)合理的配水制度;(5)调整合适的辊间距,避免鼓肚。
(三)、切割断面不齐1、缺陷特征:切割断面粗糙,凹凸不平。
连铸板坯BQB131-2003

-
SS540
G
≤6
0.12~0.21 ≤0.25 0.90~1.40 ≤0.035 ≤0.035
-
一 St33 般 St37-2 结 St37-2 构 St37-2 钢 St37-2
St37-3 St37-3 St37-3 St37-3 St37-3 St44-2 St44-2 St50-2
A
≤13 0.03~0.12 ≤0.08 0.15~0.65 ≤0.035 ≤0.035 Alt≥0.01
-
St52-3 St52-3 St52-3
G
<7
0.13~0.22 0.20~0.55 1.20~1.70 ≤0.035 ≤0.035 Alt≥0.01
G
7~<18 0.13~0.22 0.20~0.55 1.10~1.60 ≤0.035 ≤0.035 Alt≥0.01
G 18~25.4 0.13~0.22 0.20~0.55 1.10~1.60 ≤0.030 ≤0.030 Nb≤0.04
SM520B
G
1.4~9 0.12~0.21 ≤0.25 0.90~1.40 ≤0.035 ≤0.035 Nb≤0.04
SM520B
G
>9~12 0.06~0.15 0.20~0.60 1.10~1.60 ≤0.035 ≤0.035 Nb≤0.04
SM520C
G
1.6~6 0.12~0.21 ≤0.25 0.85~1.35 ≤0.035 ≤0.035 Nb≤0.04
A >6~12.7 0.06~0.15 ≤0.05 0.45~0.95 ≤0.035 ≤0.035 Alt≥0.008
G
≤6
0.12~0.21 0.04~0.30 0.20~0.70 ≤0.035 ≤0.035
连续铸钢板坯
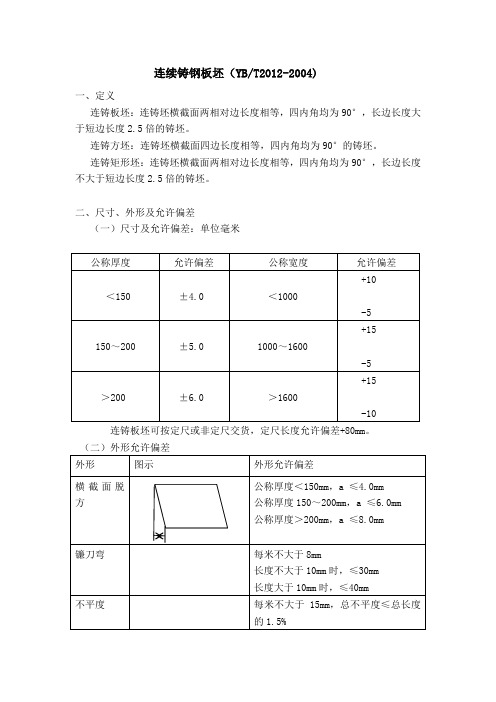
连续铸钢板坯(YB/T2012-2004)一、定义连铸板坯:连铸坯横截面两相对边长度相等,四内角均为90°,长边长度大于短边长度2.5倍的铸坯。
连铸方坯:连铸坯横截面四边长度相等,四内角均为90°的铸坯。
连铸矩形坯:连铸坯横截面两相对边长度相等,四内角均为90°,长边长度不大于短边长度2.5倍的铸坯。
二、尺寸、外形及允许偏差(一)尺寸及允许偏差:单位毫米公称厚度允许偏差公称宽度允许偏差<150 ±4.0 <1000+10-5150~200 ±5.0 1000~1600+15-5>200 ±6.0 >1600+15-10 连铸板坯可按定尺或非定尺交货,定尺长度允许偏差+80mm。
(二)外形允许偏差外形图示外形允许偏差横截面脱方公称厚度<150mm,a ≤4.0mm公称厚度150~200mm,a ≤6.0mm 公称厚度>200mm,a ≤8.0mm镰刀弯每米不大于8mm长度不大于10mm时,≤30mm长度大于10mm时,≤40mm不平度每米不大于15mm,总不平度≤总长度的1.5%鼓肚宽面鼓肚:铸坯厚度最大尺寸与铸坯厚度最小尺寸之差≤1%铸坯宽度侧面鼓肚:≤5%铸坯厚度切斜宽度方向≤25mm厚度方向≤10mm凹陷侧面凹陷≤5mm宽面凹陷≤5mm楔形厚度高低不一的楔形≤3mm宽度宽窄不一的楔形≤20mm(测量时均应距铸坯端面150mm)剪切变形展宽≤10%铸坯厚度三、化学成分(熔炼成分)符合相应标准的规定。
四、浇注应由同一牌号钢水浇注,如不同牌号混浇时,对中间坯应根据实际成分进行判定。
五、头、尾坯切除后应保证板坯无缩孔。
六、低倍:优质非合金钢、特殊质量非合金钢和合金钢每一浇次可取样进行低倍分析。
优质非合金钢、电工用磁性钢按YB/T4003的规定进行评级;不锈钢、耐热钢及合金钢的检验,要求注明缺陷的种类、尺寸、外形及数量。
此条未在公司实行。
七、表面质量1、表面不得有目视可见的重接、重叠、翻皮、结疤、夹杂、深度或高度大于3mm 的划痕、压痕、擦伤、气孔、冷溅、皱纹、凸块、凹坑和深度大于2mm的裂纹。
热轧带钢及板坯标准要求及不同厚度精度范围

1、板坯尺寸要求板坯采用100%的连铸坯板坯厚度:210、230mm板坯宽度:950~1650mm板坯长度:长尺:9000~11000mm短尺:4500~5300mm最大坯重:厚度公差:±5mm宽度公差:±10mm长度公差:±30mm镰刀弯:长尺:≤50mm 短尺:≤25mm上下弯:长尺:≤50mm 短尺:≤25mm板坯表面不允许有裂纹、角裂、拉裂和结疤板坯端面不允许有肉眼可见的内裂板坯表面允许有深度不大于3mm的气孔、划痕、凹坑,以及深度不大于2mm的水纹2、产品的质量要求产品的尺寸、外形质量应符合GB709-88的规定①厚度偏差如表1-6所示②宽度偏差带宽≤1000mm+20mm带宽>1000mm +30mm③带钢的镰刀弯每米不大于3mm④塔形高度产品厚度<2.5mm 产品厚度≥2.5mm带宽≤1000mm60 5060带宽>1000mm 80 7080塔形的高宽比≤时适用表面质量要求产品表面质量的保证条件一般参照碳素钢和低合金钢的GB912—89适用于厚度≤4.0mm的产品与GB3274—88适用于厚度>4.0mm的产品的现行国标;1GB/912—89①钢板表面不允许有裂纹、结疤、折迭、气泡和夹杂,钢板不得有分层;②钢板和钢带的表面允许有深度和高度不大于厚度公差之半的折印、麻点、划伤、小拉痕、压痕以及氧化铁皮脱落所造成的表面粗糙等局部缺陷;对表面的薄层氧化铁皮,轻微铁锈和残余涂料、污迹等不影响表面检查的局部缺陷允许存在;③钢板和钢带表面的局部缺陷,允许用修磨方法清除,但清除深度不得大于钢板和钢带厚度公差之半;④钢带允许带缺陷交货,但缺陷部分,不得超过每卷总长度的8%;表1-6产品厚度精度注:带钢两端不考核的总长度<90/公称厚度,且最大不超过20m2GB/3274—88①钢板表面不得有气泡、结疤、拉裂、裂纹、折迭、夹杂和压入氧化铁皮,钢板不得有分层;②钢板表面允许有不妨碍检查表面缺陷的薄层氧化铁皮,铁锈,由于压入氧化铁皮脱落所引起的不显着的粗糙、划痕,轧辊造成的网纹及其它局部缺陷,但凸凹度不得超过钢板厚度公差之半,对低合金钢板和钢带并应保证不超过钢板允许的最小厚度;③钢板表面的缺陷,不允许焊补和堵塞,应用凿子或砂轮清理,清理处应平缓无棱角,清理深度不得超过钢板厚度负偏差范围,对低合金钢板并应保证不超过钢板的允许最小厚度;④成卷钢带允许带缺陷交货,但表面缺陷质量不正常部分,不得超过每卷钢带总长度的10%;⑤切边钢板和钢带的边缘,不得有锯齿形凸凹,但允许有深度不大于2mm,长度不大于25mm 的个别裂纹;不切边钢板和钢带,因轧制而产生的边裂及其它缺陷,其横向深度不得超过钢板和钢带宽度偏差之半,并且不得使钢板小于公称宽度;产品质量中的理化指标应根据不同的钢号、用途分别符合其相应交货标准的规定;①按现行国标生产的钢号与其对应的产品标准表1-7现行国标生产的钢号与其对应的产品标准②按日本标准生产的钢号与其对应的产品标准表1-8日本标准生产的钢号与其对应的产品标准③按德国标准生产的钢号与其对应的产品标准表1-9德国标准生产的钢号与其对应的产品标准④按美国材料实验室标准生产的钢号与其对应的产品标准表1-10美国材料实验室标准生产的钢号与其对应的产品标⑤按英国欧洲标准生产的钢号与其对应的产品标准表1-11英国欧洲标准生产的钢号与其对应的产品标准。
连铸圆坯BQB151-2003

≤0.17
0.10~0.35
0.40~0.80
≤0.035
≤0.035
St45.8
≤0.21
0.10~0.35
0.40~1.20
≤0.035
≤0.035
27MnSi
0.24~0.32
1.10~1.40
1.10~1.40
≤0.030
≤0.030
4.2 冶炼方法
钢由电炉冶炼,并根据不同钢种的技术要求采取相应的炉外精炼工艺。
4.3 交货状态
以连续浇铸的圆坯交货。
4.4 低倍
经供需双方协商,并在合同中注明,可进行低倍组织检验,指标由双方协议规定。
4.5 表面质量
4.5.1 圆坯表面不得存在肉眼可见的裂纹、结疤、砂眼、气孔、针眼等缺陷,但允许存在深度
小于 1.5mm 的机械划痕、印痕等缺陷。
4.5.2 圆坯表面缺陷允许清理。清理处应圆滑无棱角。清理深度不得超过 7mm,其长深比≥8,
圆坯原则上应是平直的,局部弯曲≤4mm/m,总的弯曲不得大于全长 0.4%。 3.3.2 不圆度
圆管坯的不圆度不得大于直径公差的 85%。 3.3.3 端面切斜
圆坯端面应与轴线垂直,切斜不得大于 6mm。 3.4 重量
圆坯按实际重量交货,经供需双方协商并在合同中注明,也可按理论重量交货。
4 技术要求 4.1 牌号及化学成分
0.17~0.37
0.50~0.80
≤0.035
≤0.035
St52.0
≤0.22
≤0.55
≤1.60
≤0.035
≤0.035
St55
0.33~0.41
0.17~0.37
0.50~0.80
水平连铸
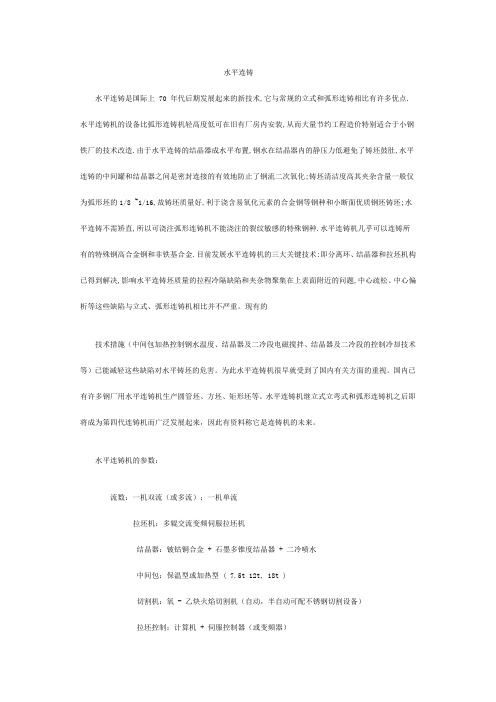
水平连铸水平连铸是国际上 70 年代后期发展起来的新技术,它与常规的立式和弧形连铸相比有许多优点.水平连铸机的设备比弧形连铸机轻高度低可在旧有厂房内安装,从而大量节约工程造价特别适合于小钢铁厂的技术改造.由于水平连铸的结晶器成水平布置,钢水在结晶器内的静压力低避免了铸坯鼓肚,水平连铸的中间罐和结晶器之间是密封连接的有效地防止了钢流二次氧化;铸坯清洁度高其夹杂含量一般仅为弧形坯的1/8 ~1/16,故铸坯质量好,利于浇含易氧化元素的合金钢等钢种和小断面优质钢坯铸坯;水平连铸不需矫直,所以可浇注弧形连铸机不能浇注的裂纹敏感的特殊钢种.水平连铸机几乎可以连铸所有的特殊钢高合金钢和非铁基合金.目前发展水平连铸机的三大关键技术:即分离环、结晶器和拉坯机构已得到解决,影响水平连铸坯质量的拉程冷隔缺陷和夹杂物聚集在上表面附近的问题,中心疏松、中心偏析等这些缺陷与立式、弧形连铸机相比并不严重。
现有的技术措施(中间包加热控制钢水温度、结晶器及二冷段电磁搅拌、结晶器及二冷段的控制冷却技术等)已能减轻这些缺陷对水平铸坯的危害。
为此水平连铸机很早就受到了国内有关方面的重视。
国内已有许多钢厂用水平连铸机生产圆管坯、方坯、矩形坯等。
水平连铸机继立式立弯式和弧形连铸机之后即将成为第四代连铸机而广泛发展起来,因此有资料称它是连铸机的未来。
水平连铸机的参数:流数:一机双流(或多流);一机单流拉坯机:多辊交流变频伺服拉坯机结晶器:铍钴铜合金 + 石墨多锥度结晶器 + 二冷喷水中间包:保温型或加热型 ( 7.5t 12t, 18t )切割机:氧 - 乙炔火焰切割机(自动,半自动可配不锈钢切割设备)拉坯控制:计算机 + 伺服控制器(或变频器)铸坯规格:φ50—φ230 ;□60-□180 ;( 50-160 ) X ( 80—220 )设备长度: 36----50 M设备高度: 2.5 M( 中包 );4.5M ( 切割机 )拉坯速度 : 0.8----4.2 m / min拉坯频率: 80--150生产能力: 6—13 t / h适用钢种:不锈钢、合金钢、有色合金、碳钢等--弧形方(圆)连铸机--弧型连铸机是一种直接将钢水浇注成铸坯的连续铸钢设备,可用于生产方、圆、矩形、板坯铸坯,由于具有铸坯质量好,成材率高、技术成熟等优点,已被广泛采用。
轧钢用水平连铸圆坯标准

轧钢用水平连铸圆坯标准QJ/HYXC03.01—20021 范围本标准规定了轧钢用水平连铸圆坯(以下简称圆棒)的尺寸、外形、重量及允许偏差、技术要求、试验方法、检验规则、包装、标志及质量证明书。
本标准是我公司购水平连铸圆坯签订合同和对圆坯检查、验收、使用的依据。
2 引用标准下列标准所包含的条文,通过在本标准中引用而构成本标准的条文。
GB700 普通碳素钢;GB1591 低合金结构钢;GB1222 弹簧钢;GB222 钢的化学分析用试验取样法及成品化学成分允许偏差;GB223 钢铁及合金化学分析法;GB2101 型钢验收、包装标专及质量证明书的一般规定。
3 术语热点裂纹:由于铸坯热收缩,集中发生在凝固壳最薄弱的热点处而引起的与冷隔平行的一种横裂纹。
4 尺寸、外形、重量及允许偏差4.1 直径及允许偏差和外形圆棒的直径及允许偏差和外形应符合附表1规定4.2 长度及允许偏差圆棒通常定尺长度为6m±mm,非定尺长度应是1.5m的倍数,即3.0m、4.5m,但总量不超过10%。
4.3 重量圆棒按实际重量交货。
5 技术要求5.1 牌号及化学成分5.1.1 牌号及化学成分应符合附表2规定。
5.1.2 圆棒的化学成分允许偏差应符合GB222的标准。
5.2 冶炼方法电弧炉冶炼。
5.3 交货状态圆棒以铸态交货。
5.4 表面质量5.4.1 圆棒表面不应有肉眼可见的结疤、纵裂纹、夹渣及深度超过3mm的气孔等缺陷。
圆棒端面不应有肉眼可见的缩孔。
允许有从实际尺寸算起不超过2mm的划痕、压痕及折皱存在,允许有深度不大于1mm的热点裂纹及冷隔存在。
5.4.2 圆棒表面缺陷应清除,清除深度从实际尺寸算起不应大于直径的5%,清理处应圆滑无棱角,清理宽度不应小于深度的6倍,在同一截面最大清理深度只准有一处。
6 试验方法圆棒的试验方法、取样部位及数量应符合附表3的规定。
7 检验规则7.1 检查和验收圆棒的化学成分由供方提供。
圆棒的尺寸和表面质量由技术质量部负责检查验收。
连续铸钢板坯 标准

连续铸钢板坯标准
连续铸钢板坯的尺寸和外形允许偏差以及外形允许偏差都有相应的标准。
连续铸钢板坯的尺寸允许偏差为:公称厚度+4.0mm。
公称宽度+10mm,连铸板坯可按定尺或非定尺交货,定尺长度允许偏差+ 80mm。
连续铸钢板坯的外形允许偏差包括横截面脱方、镰刀穹、不平度、鼓肚、切斜、凹陷等,具体标准如下:
1.横截面脱方:公称厚度< 150mm,as4.0mm; 公称厚度150 ~ 200mm, a<6.0mm; 公称厚度> 200mm,as8.0mm。
2.镰刀穹:每米不大于8mm.
3.不平度:每米不大于15mm,总不平度总长度的1.5%。
4.鼓肚:宽面鼓肚:铸坯厚度最大尺寸与铸坯厚度最小尺寸之差<1%铸坯宽度;侧面鼓肚:≤5%铸坯厚度。
5.切斜:宽度方向s25mm,厚度方向≤10mm。
6.凹陷:侧面凹陷≤5mm,宽面凹陷≤5mm。
此外。
连续铸钢板坯还规定了连铸板坯牌号和连铸板坯标准。
制表:审核:批准:。
冶金行业标准连铸圆坯低倍评级比较研究(YBT153-2015及YBT4149-2006)

YB/T 153-2015 YB/T 4149-2006中心裂纹1级裂纹占比YB/T 153-2015:0.24/6.65=3.6%YB/T 4149-2006:0.42/6.7=6.2%YB/T 153-2015 YB/T 4149-2006中心裂纹2级裂纹占比YB/T 153-2015:0.69/6.4=10.7%YB/T 4149-2006:0.8/6.5=12.3%YB/T 153-2015 YB/T 4149-2006中心疏松1级疏松占比YB/T 153-2015:1.1/6.65=16.5%YB/T 4149-2006:1.19/6.55=18.2%YB/T 153-2015 YB/T 4149-2006中心疏松2级疏松占比YB/T 153-2015:1.63/6.75=24.1%YB/T 4149-2006:1.97/6.8=29.0%YB/T 153-2015 YB/T 4149-2006缩孔1级缩孔占比YB/T 153-2015:0.13/6.7=1.9%YB/T 4149-2006:0.2/6.55=3.1%YB/T 153-2015 YB/T 4149-2006缩孔2级缩孔占比YB/T 153-2015:0.22/6.7=3.3%YB/T 4149-2006:0.34/6.7=5.1%YB/T 153-2015 YB/T 4149-2006中间裂纹1级中间裂纹占比YB/T 153-2015:0.35/6.6=5.3%,;两条裂纹;YB/T 4149-2006:0.59/6.6=8.9%,两条裂纹。
YB/T 153-2015 YB/T 4149-2006中间裂纹1级中间裂纹占比YB/T 153-2015:0.63/6.65=9.5%,;三条裂纹;YB/T 4149-2006:0.87/6.62=13.1%,六条裂纹。
YB/T 153-2015 YB/T 4149-2006皮下裂纹1级皮下裂纹占比YB/T 153-2015:三条细裂纹;YB/T 4149-2006:两条细裂纹。
连铸坯质量外观检验标准

连铸坯质量外观检验标准
作者:周毅发表日期:2007-9-19 阅读次数:157
1、尺寸及允许偏差单位:毫米
2、连铸坯长度根据客户要求交货,具体如下:单位:米
3、连铸坯头尾切除量
新开浇的连铸坯,接头部切除应不小于200mm,尾部切除应符合表2的规定。
表2
表面质量
连铸坯表面不得有肉眼可见的裂纹、重接、翻皮、结疤、缩孔,深度或高度大于3 mm的划痕、压痕、擦伤、冷溅、耳子、凸坑凹坑,深度大于2mm,的气孔、皱纹、横向振痕和深度大于1mm,发纹。
低碳低硅和焊条钢坯表面及横截面距表面2 mm 之内不得有气泡或针孔,其它部位允许存在气泡和针孔,其它钢坯横截面不得有皮下气泡。
连铸坯表面如存在上述不允许或超出允许规定的缺陷,应进行清除,应沿纵向清除,清除处应圆滑无棱角,清除宽度应不小于深度的6倍,长度应不小于深度的8倍。
表面清除深度,单面应不大于连铸坯边长10%,两相对面清除深度之和不大于深度的12%。
弯曲度
(1)连铸坯弯曲度每米不大于20mm, 弯曲度不大于总长的2%
(2)长度不小于6米、边长为150*150及200*200的连铸坯总弯曲度不大于80mm
(3)连铸坯不得有明显的扭转
边长测量
在连铸坯长度的垂直方向测量,测量部位应在有缺陷区以外。
鼓肚总高度
测量连铸坯有鼓肚处的最大厚度减去边长。
圆坯标准

东方钢铁有限公司编号:DG—JS—LG514部门:炼钢厂页数:共2页第1页批准日期:生效日期:连铸圆坯标准分发号:本标准适用于直径为110mm的优质碳素结构钢和合金结构钢圆形连铸坯(以下简称圆坯)。
1 坯料长度、尺寸偏差和坯料外形1.1 坯料长度:供本公司无缝钢管厂用坯长为5950+50mm或坯长符合合同要求。
1.2 直径偏差:+1.0mm1.3 外形1.3.1 坯料不圆度应不大于公称直径公差的75%。
1.3.2 弯曲度。
每米不答于4mm,总弯曲度不大于0.4%。
1.3.3 坯料端部切斜应不大于30mm。
1.3.4 用户无法使用的坯料应报废。
2 低倍圆坯酸浸低倍试片上不得有夹杂、翻皮等缺陷,低倍组织评级按YB 4002—91进行评定。
合格管坯低倍:中心疏松、一般疏松、方框偏析、点状偏析的合格级别应不大于3级。
优质管坯低倍:中心疏松、一般疏松、方框偏析、点状偏析的合格级别应不大于2级。
3 表面质量3.1 圆坯表面不得有肉眼可见的裂纹、重接、翻皮、结疤、夹杂、深度或高度大于2mm的划痕、压痕、擦伤、气孔、皱纹、冷溅、耳子、凸块、凹坑和深度大于等于2mm的发纹,圆坯横截面不得有缩孔、皮下气泡。
3.2 如有上述缺陷存在,必须清除,应沿纵向清除,清除处应圆滑无棱角。
表面清除的深度(按实际尺寸计算)单向不大于公称直径的5%,两相对向深度之和不大于公称直径的8%,深度小于2mm 的压痕、麻点、波纹等缺陷可不清理。
4 其他4.1 未提及的事项,参照连铸方坯矩形坯标准办理。
4.2 本标准自公布之日起生效,本标准解释权属炼钢厂。
编制:审核:批准:。
连铸板坯标准

一期主要产品
名称
规格
数量
生产日期
一、连铸板坯
厚:210、230mm
宽:950~1650mm
长:9000~11000mm
短尺:4500~5300mm
240万t/a
2004.6
二、水渣
30~60万t/a
2004.6
三、冶金焦
10~25mm>25mm
30万t/a
2004.4
注:冶金焦执行标准:GB/T1996-94
GB/T 14164-93
等同于A,待开发
21
S240
GB/T 14164-93
YB 2012-83或
YB/T 168-2000
等同于B,待开发
22
S290
等同于X42,待开发
23
S315
等同于X46,待开发
24
S360
等同于X52,待开发
25
自行车用钢
ZQ195
YB/T 5066-93
YB 2012-品名
牌号
连铸板坯标准
备注
1
碳素结构钢、
焊接钢管用钢
Q195
GB700-88
YB 2012-83
2004.10生产
2
Q215A
2004.6生产
3
Q215B
2004.6生产
4
Q235A
2004.6生产
5
Q235B
2004.6生产
6
Q235C
待开发
7
优质碳素结构钢、
焊接钢管用钢
08
GB/T699-1999
YB 2012-83或
YB/T 168-2000
热轧带钢及板坯标准要求及不同厚度精度范围
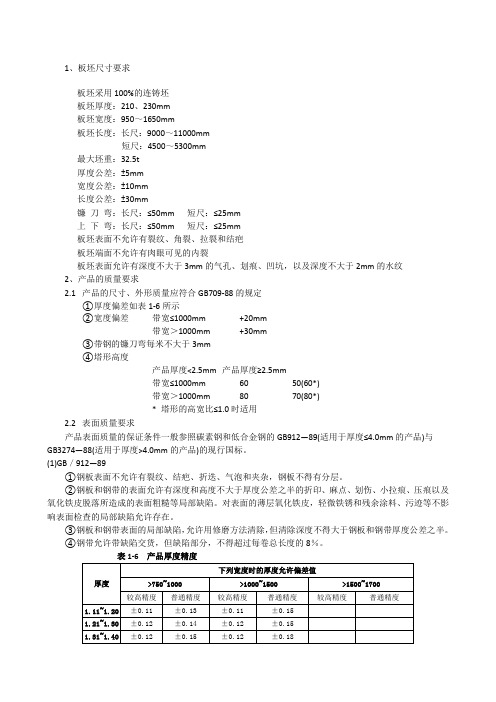
1、板坯尺寸要求板坯采用100%的连铸坯板坯厚度:210、230mm板坯宽度:950~1650mm板坯长度:长尺:9000~11000mm短尺:4500~5300mm最大坯重:32.5t厚度公差:±5mm宽度公差:±10mm长度公差:±30mm镰刀弯:长尺:≤50mm 短尺:≤25mm上下弯:长尺:≤50mm 短尺:≤25mm板坯表面不允许有裂纹、角裂、拉裂和结疤板坯端面不允许有肉眼可见的内裂板坯表面允许有深度不大于3mm的气孔、划痕、凹坑,以及深度不大于2mm的水纹2、产品的质量要求2.1 产品的尺寸、外形质量应符合GB709-88的规定①厚度偏差如表1-6所示②宽度偏差带宽≤1000mm+20mm带宽>1000mm +30mm③带钢的镰刀弯每米不大于3mm④塔形高度产品厚度<2.5mm 产品厚度≥2.5mm带宽≤1000mm60 50(60*)带宽>1000mm 80 70(80*)* 塔形的高宽比≤1.0时适用2.2 表面质量要求产品表面质量的保证条件一般参照碳素钢和低合金钢的GB912—89(适用于厚度≤4.0mm的产品)与GB3274—88(适用于厚度>4.0mm的产品)的现行国标。
(1)GB/912—89①钢板表面不允许有裂纹、结疤、折迭、气泡和夹杂,钢板不得有分层。
②钢板和钢带的表面允许有深度和高度不大于厚度公差之半的折印、麻点、划伤、小拉痕、压痕以及氧化铁皮脱落所造成的表面粗糙等局部缺陷。
对表面的薄层氧化铁皮,轻微铁锈和残余涂料、污迹等不影响表面检查的局部缺陷允许存在。
③钢板和钢带表面的局部缺陷,允许用修磨方法清除,但清除深度不得大于钢板和钢带厚度公差之半。
④钢带允许带缺陷交货,但缺陷部分,不得超过每卷总长度的8%。
表1-6 产品厚度精度注:带钢两端不考核的总长度<90/公称厚度,且最大不超过20m(2)GB/3274—88①钢板表面不得有气泡、结疤、拉裂、裂纹、折迭、夹杂和压入氧化铁皮,钢板不得有分层。
- 1、下载文档前请自行甄别文档内容的完整性,平台不提供额外的编辑、内容补充、找答案等附加服务。
- 2、"仅部分预览"的文档,不可在线预览部分如存在完整性等问题,可反馈申请退款(可完整预览的文档不适用该条件!)。
- 3、如文档侵犯您的权益,请联系客服反馈,我们会尽快为您处理(人工客服工作时间:9:00-18:30)。
轧钢用水平连铸圆坯标准
QJ/HYXC03.01—2002
1 范围
本标准规定了轧钢用水平连铸圆坯(以下简称圆棒)的尺寸、外形、重量及允许偏差、技术要求、试验方法、检验规则、包装、标志及质量证明书。
本标准是我公司购水平连铸圆坯签订合同和对圆坯检查、验收、使用的依据。
2 引用标准
下列标准所包含的条文,通过在本标准中引用而构成本标准的条文。
GB700 普通碳素钢;
GB1591 低合金结构钢;
GB1222 弹簧钢;
GB222 钢的化学分析用试验取样法及成品化学成分允许偏差;
GB223 钢铁及合金化学分析法;
GB2101 型钢验收、包装标专及质量证明书的一般规定。
3 术语
热点裂纹:由于铸坯热收缩,集中发生在凝固壳最薄弱的热点处而引起的与冷隔平行的一种横裂纹。
4 尺寸、外形、重量及允许偏差
4.1 直径及允许偏差和外形
圆棒的直径及允许偏差和外形应符合附表1规定
4.2 长度及允许偏差
圆棒通常定尺长度为6m±mm,非定尺长度应是1.5m的倍数,即3.0m、4.5m,但总量不超过10%。
4.3 重量
圆棒按实际重量交货。
5 技术要求
5.1 牌号及化学成分
5.1.1 牌号及化学成分应符合附表2规定。
5.1.2 圆棒的化学成分允许偏差应符合GB222的标准。
5.2 冶炼方法
电弧炉冶炼。
5.3 交货状态
圆棒以铸态交货。
5.4 表面质量
5.4.1 圆棒表面不应有肉眼可见的结疤、纵裂纹、夹渣及深度超过3mm的气孔等缺陷。
圆棒端面不应有肉眼可见的缩孔。
允许有从实际尺寸算起不超过2mm的划痕、压痕及折皱存在,允许有深度不大于1mm的热点裂纹及冷隔存在。
5.4.2 圆棒表面缺陷应清除,清除深度从实际尺寸算起不应大于直径的5%,清理处应圆滑无棱角,清理宽度不应小于深度的6倍,在同一截面最大清理深度只准有一处。
6 试验方法
圆棒的试验方法、取样部位及数量应符合附表3的规定。
7 检验规则
7.1 检查和验收
圆棒的化学成分由供方提供。
圆棒的尺寸和表面质量由技术质量部负责检查验收。
7.2 炉号划分
圆棒的上下相邻炉号划分方法:以盛钢桶钢水注入中间包时起,即做为下一炉的开始。
7.3 组坯规则
圆棒应按批进行检查和验收,每批由同一牌号、同一炉号的圆棒组成。
8 包装、标志及质量证明书
8.1 包装
每批圆棒可分为若干捆包装,通常每捆10—15支(重量不应超过10吨),用盘条或铁丝均匀捆扎结实。
8.2 标志
每捆圆棒应附有标志,写明牌号、炉号、规格、数量及重量。
8.3 质量证明书
圆棒的质量证明书应符合GB2101的规定。
9 本标准由魏克冲起草,。
10 本标准自2002年10月1日起生效。