表面组装技术简介
表面组装技术SMT基本常识简介

基础知识SMT基础知识SMT(Surface Mounted Technology)是目前电子组装行业最流行的技术和工艺。
SMT有什么特点:电子产品组装密度高,体积小,重量轻。
贴片元器件的体积和重量只有传统插件的1/10左右。
一般采用SMT 后,电子产品体积会缩小40%~60%,重量会减轻60%~80%。
可靠性高,抗振能力强。
焊点不良率低。
良好的高频特性。
减少了电磁和射频干扰。
易于实现自动化,提高生产效率。
成本降低30%-50%。
节省材料、能源、设备、人力、时间等。
为什么要用SMT:电子产品追求小型化。
过去用的打孔插件,并不能减少电子产品的功能,让电子产品更齐全。
所用的集成电路(IC)没有冲压元件,特别是大规模、高集成度的IC,不得不采用表面贴装元件,进行批量生产和自动化。
制造商应以低成本和高产量生产高质量的产品,以满足客户需求,并加强开发具有市场竞争力的电子元件。
随着集成电路(IC)的发展和半导体材料的多种应用,电子技术革命势在必行,追逐SMT工艺流程的国际潮流——双面组装工艺A:来料检验、PCB的A面丝印焊膏(点胶)、烘干(固化)、A面回流焊、清洗、翻板、PCB的B面丝印焊膏(点胶)、烘干和回流焊(B:来料检验、PCB的A面丝印焊膏(点胶)、烘烤(固化适用于PCB板A面回流焊和B面波峰焊。
在组装在PCB B侧的SMD 中,当只有SOT或SOIC(28)引脚在下方时,应采用这种工艺。
助焊剂产品的基本知识。
表面贴装用助焊剂的要求:残留在基板上的助焊剂残渣具有一定的化学活性,热稳定性好,润湿性好,能促进焊料的膨胀,对基板无腐蚀性,可清洗性好的氯含量在0.2%(W/W)以下。
二。
通量的作用。
焊接过程:预热/开始熔化焊料/形成焊料合金/形成焊点/固化焊料。
作用:辅助传热/去除氧化物/减少表面力/防止再氧化。
描述:溶剂蒸发/被加热,助焊剂覆盖基板和焊料。
表面,使传热均匀/释放活化剂与基板表面的离子氧化物反应,去除氧化膜/使熔融焊料的表面力变小,润湿良好/覆盖高温焊料表面,控制氧化提高焊点质量。
表面组装技术SMT

表面组装技术概述及组装设备学习目标✧ 能了解表面组装技术;✧ 能了解表面组装设备;工作任务✧ 去相关企业(公司)参观或实习。
案例说明✧ 通过观看贴片机工作过程、SMT 工艺流程、MMIC 单片混合集成电路工艺视频,以及识读HT203-SMT 作业指导书,让学生能了解贴片机工作过程、能熟悉SMT 工艺流程、能了解最新微组装工艺流程和设备,从而进一步能了解表面组装技术及表面组装设备。
表面组装技术(Surface Mount Technology,简称SMT )是突破了传统的印制电路板(PCB )通孔基板插装元器件工艺(Through-hole Mounting Technology, THT )发展起来的第四代电子装联技术。
它是将表面贴装元器件(无引脚或短引脚的元器件)贴、焊到印制电路板表面规定位置上的电子装联技术,所用的印制电路板无需插孔。
概括地说,就是首先在印制电路板焊盘上涂覆焊锡膏,再将表面贴装元器件准确地放到涂有焊锡膏的焊盘上,再通过加热印制电路板直至焊膏熔化,冷却后便实现了元器件与印制电路板之间的互联。
图4-1为表面组装技术示意图。
4.1.1 表面组装技术的发展过程SMT 发展至今,已经经历了四个阶段:1)第一阶段(1970-1975年):以小型化为主要目标,此时的表面组装元器件主要用于混合集成电路,如石英表和计算器等。
图4-1 SMT 示意图2)第二阶段(1976-1980年):这一阶段的主要目标是减小电子产品的单位体积,提高电路功能,产品主要用于摄像机、录像机、电子照相机等。
3)第三阶段(1980-1995年):这一阶段的主要目标是降低成本,大力发展组装设备,表面组装元器件进一步微型化,提高电子产品的性价比。
4)第四阶段(1996-至今):SMT已经进入了微组装技术(Microelectronics Packaging Technology,简称MPT)、高密度组装和立体组装的新阶段,以及多芯片组件等新型表面组装元器件快速发展和大量应用阶段。
第二章、表面组装元器件
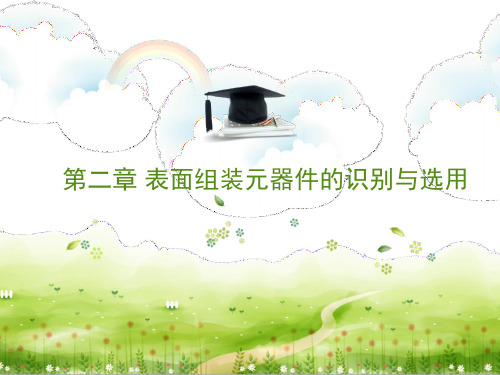
• 二极管:2端或3端封装;小功率晶体管: 3端或4端封装; 4~6端SMD内大多封装两支晶体管或场效应管。
• 2、表面组装元件(SMD)引脚形状
• • • • 翼形 钩形 球形 I形
•
•
针形
• 2、表面组装二极管
• 无引线柱形玻璃封装二极管:稳压开关、通用二极管 • 片状塑料封装二极管:矩形片状 • 3、小外形塑封晶体管(SOT) • 采用带翼形短脚引线的塑料封装
• SMC:指表面组装无源元件,如片式电阻、电容、电感称 为。 • SMD:指有源器件,如小外形晶体管(SOT)及四方扁平组 件(QFP) 。
• 2、特点:
• (1)在表面组装器件的电极上,完全没有引线,或只有非 常短小的引线,引线间距小。
• (2)表面组装元器件直接贴装在PCB的表面,将电极焊接 在与元器件同一面的焊盘上。
第三章、表面组装印制板的设计与制 造
• 印制电路:是一种附着于绝缘基材表面,用于连接电子 元器件的导电图形。
• 印制电路板:简称印制板或PCB(Printed Circuit Board), 是指印制电路的成品板。 • 为了区别THT与SMT所用基板不同: • 通孔插装元器件所用的PCB称为插装印制板 • 表面贴装元器件所用的印制板称为SMB
• (2)圆柱型电阻器 • 三色环 • 四色环 • 五色环
普通电阻器标注
• 精度为± 1%的精密电阻器还可以用两位数字代码加一位 字母代码表示。
•
精密电阻器标注
2.3.2 表面组装电阻器
• 1、普通表面组装电阻器(图)
• 按制造工艺分为:厚膜 • 薄膜 • 按封装外形分为:片状采用厚膜工艺制造 圆柱形(MELF)采用薄膜工艺 • 2、表面组装电阻排(图)
表面组装技术简介

表面组装技术概述一、表面组装技术的概念及其类型表面组装技术,又称表面安装技术或表面贴装技术,用SMT(Surface Mounting Technology)表示。
它是将片式元器件安装在印刷电路板或其它基板表面上,通过波峰焊、再流焊等方法焊接的一种新型的组装技术。
采用表面组装技术,可使电子产品小型化、薄型化、提高装配密度和装配速度,提高产品的质量,降低产品的成本。
表面组装技术包括片式元器件的设计、制造和选用,基板的选择,表面组装方案的制定和设计,印制线路板的设计与制造,粘结剂的点涂,焊膏印刷,片式元器件贴放,贴装部件的焊接,贴装部件的清洗,部件质量的检验和性能测试,部件的返修等。
表面组装技术的内容详见图1-1所示。
性能要求:电气性能、机械性能、稳定性、可靠性、一致性等片式元器件设计技术与制造:选用什么材料、结构形状、焊接端形式、尺寸精度、可焊性、制造技术包装形式:散装(塑料袋)、盒装(料盒)、带装(编带)、盘式。
基板材料、单(多)层印刷电路板、陶瓷、被釉金属、金属聚合物等基板电路图形制作:图形设计、元器件位置、焊盘、焊区间隙、尺寸大小、通孔金属化、测试点等片片式元器件在基板上单面组装式片式元器件和有引线元器件在基板两面混装元组装片式元器件在基板两面组装器多芯片组装件组装粘合剂:环氧树脂系、丙烯系等、用印刷或涂敷方法形成的组装技术材料工艺材料:助焊、清洗剂、阻焊剂、助溶剂表焊料:锡、锡-铅面流动材粘结剂涂敷:丝网印刷、涂布头组料涂敷粘结剂固化:紫外线照射加热、红外线照射加热、超声波加热装焊料涂敷:丝网印刷、涂布头技浸焊术流动焊波峰焊(水平喷流、倾斜喷流)焊接电热、红外线、喷热气、气相饱和蒸汽再流焊用焊料膏法、预焊料膏法顺序式:将印制电路板放在X-Y工作台上,元器件按程序逐个依次贴装上去组装机一次式:可通过模板一次同时将多个元器件贴装到印制电路板上序列式:有多个贴装头,印制电路板从一个工位移动至另一个工位,每个工位贴装一个元器件图1-1 表面组装技术的内容表面组装的类型根据有源器件和无源元件在基板上贴装的情况一般分为三种类型,如图1-2所示。
表面组装技术(SMT工艺)
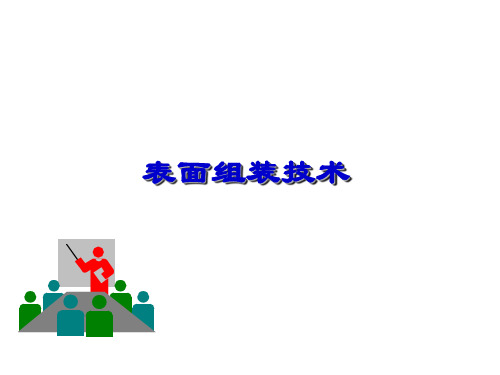
5、与PCB表面非常接近,间隙小,清洗困难。
二、分类: 1、按功能分为三大类(两类:SMC、SMD) 无源元件(SMC):片式电阻、电容、电感等 有源元件(SMD):SOT、SOP、PLCC、QFP、LCCC等
机电元件:异型元件,如继电器、开关、变压器等
2、按结构形状分:薄片矩形、圆柱形、扁平异型
A B
A面回流焊 清洗
B面胶水固化
翻板
B面波峰焊
检测
3.单面混合组装工艺流程
⑴ 先贴法 来料检测 B面点胶
A B
B面贴装元器件
A面插装元器件
B面波峰焊
翻板
检测
B面胶水固化
清洗
3.单面混合组装工艺流程
A B
⑵ 后贴法
来料检测 B面胶水固化 翻板 A面插装元器件 B面贴装元器件 B面波峰焊 检测 翻板 B面点胶 清洗
★ 环境温度
最佳: 23±3 ℃
一般:17~28℃
极限:15~35℃
★ 环境湿度 45%~70%RH
SMT发展趋势
一、绿色化生产 1、无铅焊料,无铅焊接 2、PCB制造过程中不再使用阻燃剂 3、使用无VOC助焊剂
二、元器件的发展 1、无源元件(小型化) 1812 1210 1206 0805 0603 0402 0201 01005 2、有源器件 SOT SOP PLCC QFP BGA CSP FC COB MCM
A
A B A B
4、双面混合组装
① ②
A B A B
二、基本工艺流程(两条
) ※ 先在印制电路板焊盘上印刷适量的焊膏,再将 片式元器件贴放到印制板规定位置上,最后将贴装 好元器件的印制板通过回流炉完成焊接过程。
※ 焊膏-回流焊工艺(表贴元器件)
SMT表面组装技术SMT工艺

SMT表面组装技术SMT工艺一.概述.1.S MT:表面装贴工艺.指将无引脚的片式元件(SMD)装贴于线路板上的组装技术SMT技术在电子产品制造业中,已被越来越多的工厂采用.是电子制造业的发展趋势.SMT:Surfacemountingtechnology表面装贴工艺SMD:Surfacemountingdevice表面装贴元件2.特点A.由于采用SMT机器,自动化程度高,减少了人力。
B.元件尺寸小,且无引脚,可使电子产品轻,薄,小型化。
C.装配密度高,速度快。
二.OKMCOSMT生产工艺流程,如下::使用机器将锡浆印刷在线路板上。
(DEK-265 印刷锡浆机):使用机器将规则元件贴在线路板上。
(NITTO 多元件高速贴片机):使用机器将不规则元件贴在线路板上。
(TENRYU中速贴片机)热风回流,将锡浆熔解,形成焊点.(HELLER回流炉),如短路,少锡,元件移位等。
(使用检查模板检查)三.工艺简介。
1. 锡浆印刷。
采用的机器:DEK-265锡浆印刷机(英国DEK 公司)。
1.1基本原理。
以一定的压力及速度,用金属或橡胶刮刀将装在钢网上的锡浆通过钢网漏印在线路板上。
锡浆成份为:锡63%,铅37%,松香含量:9-10%,熔点为183O C. 步骤为:图示:刮刀锡浆钢网(厚0.15MM)顶针 线路板(PCB)1.2DEK265印刷锡浆机印刷锡浆的品质直接影响点焊回流炉的品质,所以需要检查锡浆的印刷品质.一般地,主要检查以下的项目:少锡 短路 无锡浆 偏位印刷轮廓不良:拉尖,锡浆下垂。
如果钢网无损坏,印刷参数设置合适,通常印刷后,无以上不良。
主要的控制方法为过程技术员监控锡浆的厚度,如太厚,易产生QFPIC短路或锡珠。
如太薄,易产生假焊或少锡。
1.3要达到好的印刷品质,必须具备以下几点:(OKMCO选用原则)A.好的印刷钢网: 钢网厚度,钢网的开口尺寸等参数合适,孔壁垂直,无损坏。
如果钢网太厚,或开口尺寸太大,印刷在线路板上的锡浆份量就会太多,容易引起锡珠问题.同时,在元件较密集或IC脚距较小的地方,容易引起短路。
电子产品制造工艺表面组装焊接技术课件

CSP焊接工艺
CSP焊接工艺是一种将芯片尺寸 封装(CSP)元件焊接到PCB板
上的制造工艺。
CSP焊接工艺需要使用特殊的焊 料和焊接设备,通过精确控制温 度和时间,将元件与板子紧密连
接在一起。
CSP焊接工艺具有小型化、轻量 化、高可靠性等优点,广泛应用
焊接是通过加热或加压,或两 者并用,使两个分离的物体产 生原子间相互扩散和联结,形 成一个整体的工艺过程。
焊接是通过加热或加压,或两 者并用,使两个分离的物体产 生原子间相互扩散和联结,形 成一个整体的工艺过程。
焊接是通过加热或加压,或两 者并用,使两个分离的物体产 生原子间相互扩散和联结,形 成一个整体的工艺过程。
焊剂特性
焊剂的作用是去除焊接表面的 氧化物,提高焊接润湿性,需 根据焊料选择合适的焊剂。
焊料与焊剂的匹配性
选择合适的焊料与焊剂组合, 以达到最佳的焊接效果。
辅助材料的选用
辅助材料种类
包括导电胶、绝缘胶、散热材料等,每种材料有其特 定的用途。
材料性能要求
辅助材料需满足一定的物理和化学性能要求,以确保 其稳定性和可靠性。
材料选择原则
根据产品特点和工艺要求选择合适的辅助材料,以达 到最佳的工艺效果。
05
表面组装焊接技术实例
SMT贴片元件焊接
SMT贴片元件焊接技术是一种将电子元件直接贴装 在PCB板表面,并通过焊接工艺实现元件与板子的连 接的制造工艺。
焊接过程中,需要使用焊料、焊膏等材料,通过加 热、加压等方式,使元件与板子紧密连接在一起, 实现电气连接。
详细描述
焊膏印刷应保证焊膏量适中、分布均匀,无堵塞、拉丝等问题,同时要控制印 刷厚度和精度,以确保焊接质量。
电子产品制造工艺表面组装技术概述

(3)组装设计——电设计、热设计、元器件布局、基板图形 布线设计等。
组装材料——粘接剂、焊料、焊剂、清洗剂等 (4)组装工艺 组装技术——涂敷技术、贴装技术、焊接技术 、清洗技术、检测技术等。 组装设备——涂敷设备、贴装机、焊接机、 清洗机、测试设备等。
SMT生产系统的基本组成
由表面涂敷设备、贴装机、焊接机、清洗机、测试设备等 表面组装设备形成的SMT生产系统习惯上称为SMT生产线。 SMT生产线基本组成示例1
SMT的内容
SMT 元器件 /印制板 SMC/SMD SMB 工艺 点胶 印刷 波峰焊/再流焊 设备 印刷/贴片/焊接/检测
SMT组成
SMT的主要组成部分
(1)表面组装元器件 设计——结构尺寸、端子形式等。 制造——各种元器件的制造技术。 包装——编带式、棒式、散装等。
(2)电路基板——单(多)层PCB、陶瓷等。
SMT?
表面组装技术示意图
SMT的回顾
起源 发展 成熟 美国军界 小型化/ 微型化的需求 民品 IT 数字化 移动产品 办公 通讯 学习 娱乐 … 例:手机 1994-2003 重量700g 120g 68g 手表式
20世纪70年代,以发展消费类产品著称的日本电 子行业首先将SMT在电子制造业推广开来,并很 快推出SMT专用焊料和专用设备,为SMT的发展 奠定了坚实的基础。
SMT在持续发展 先进国家 >80% 我国 ~50% SMT——别无选择的趋势 SMT总的发展趋势 元器件越来越小 安装密度越来越高 安装难度越业越大
火柴/蚂蚁 /SMC
SMT在投资类电子产品、军事装备领域、计算机、 通信设备、彩电调谐器、录像机、数码相机、数 码摄像机、袖珍式高档多波段收音机、MP3、传 呼机和手机等几乎所有的电子产品生产中都得到 广泛应用。
什么是SMT和SMT工艺流程介绍
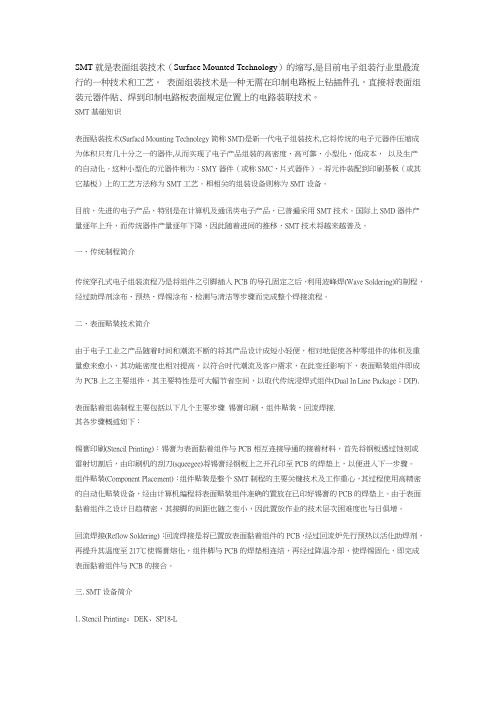
SMT就是表面组装技术(Surface Mounted Technology)的缩写,是目前电子组装行业里最流行的一种技术和工艺。
表面组装技术是一种无需在印制电路板上钻插件孔,直接将表面组装元器件贴﹑焊到印制电路板表面规定位置上的电路装联技术。
SMT基础知识表面贴装技术(Surfacd Mounting Technolegy简称SMT)是新一代电子组装技术,它将传统的电子元器件压缩成为体积只有几十分之一的器件,从而实现了电子产品组装的高密度、高可靠、小型化、低成本,以及生产的自动化。
这种小型化的元器件称为:SMY器件(或称SMC、片式器件)。
将元件装配到印刷基板(或其它基板)上的工艺方法称为SMT工艺。
相相关的组装设备则称为SMT设备。
目前,先进的电子产品,特别是在计算机及通讯类电子产品,已普遍采用SMT技术。
国际上SMD器件产量逐年上升,而传统器件产量逐年下降,因此随着进间的推移,SMT技术将越来越普及。
一、传统制程简介传统穿孔式电子组装流程乃是将组件之引脚插入PCB的导孔固定之后,利用波峰焊(Wave Soldering)的制程,经过助焊剂涂布、预热、焊锡涂布、检测与清洁等步骤而完成整个焊接流程。
二、表面贴装技术简介由于电子工业之产品随着时间和潮流不断的将其产品设计成短小轻便,相对地促使各种零组件的体积及重量愈来愈小,其功能密度也相对提高,以符合时代潮流及客户需求,在此变迁影响下,表面贴装组件即成为PCB上之主要组件,其主要特性是可大幅节省空间,以取代传统浸焊式组件(Dual In Line Package;DIP).表面黏着组装制程主要包括以下几个主要步骤锡膏印刷、组件贴装、回流焊接.其各步骤概述如下:锡膏印刷(Stencil Printing):锡膏为表面黏着组件与PCB相互连接导通的接着材料,首先将钢板透过蚀刻或雷射切割后,由印刷机的刮刀(squeegee)将锡膏经钢板上之开孔印至PCB的焊垫上,以便进入下一步骤。
第四章表面组装技术优选全文
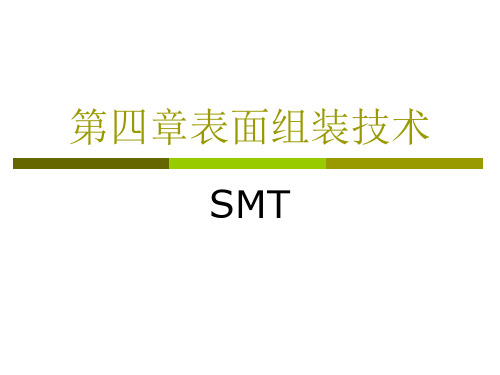
接方法有下列几种。 板载芯片(简称:COB)
COB是将裸芯片直接粘在电路基板上,用引线键合达到芯 片与SMB的连接,然后用灌封材料包封,这种形式主要用在 消费类电子产品中。
载带自动键合(简称:TAB) 载带:基材为聚酰亚胺薄膜,表面覆盖上铜箔后,用化学
它的特点是: 无引线 引出端是陶瓷外壳
四侧的镀金凹槽 (常被称作:城堡式), 凹槽的中心距有1.0mm、 1.27mm两种。
集成电路 Integration circuit
大规模集成电路:Large Scale IC(简称:LSI) 超大规模集成电路:Ultra LSIC (简称:USI) 1.小外型塑料封装 (Small Outline Package)(简称:SOP或SOIC) 引线形状: 翼型、J型、I型; 引线间距(引线数): 1.27mm(8-28条) 1.0mm (32条) 、 0.76mm(40-56条)
1. 电子产品追求小型化,以前使用的穿孔插件元件已 无法缩小
2. 电子产品功能更完整,所采用的集成电路(IC)已无 穿孔元件,特别是大规模、高集成IC,不得不采用 表面贴片元件,
3. 产品批量化,生产自动化,厂方要以低成本高产量, 出产优质产品以迎合顾客需求及加强市场竞争力
4. 电子元件的发展,集成电路(IC)的开发,半导体材 料的多元应用
适用于中功率的晶体管(300mw—2w),它的三条短引线是从 管子的同一侧引出。
4. TO—252型 适用于大功率晶体管,在管子的一侧有三条较粗的引线,芯
片贴在散热铜片上。
SMD集成电路
(1)SO封装 引线比较少的小规模集成电路的封装方式 SOP封装:芯片宽度小于0.15in 引脚数目在8-40 SOL封装:芯片宽度在0.25以上,引脚数目在44
SMT表面组装技术工艺介绍

SMT表面组装技术工艺介绍SMT就是表面组装技术(Surface Mounted Technology)的缩写,是目前电子组装行业里最流行的一种技术和工艺。
表面组装技术是一种无需在印制板上钻插装孔,直接将表面组装元器件贴﹑焊到印制电路板表面规定位置上的电路装联技术。
具体的说,表面组装技术就是一定的工具将表面组装元器件引脚对准预先涂覆了了粘接剂和焊膏的焊盘图形上,把表面组装组件贴装元器件贴装到未钻安装孔的PCB表面上,然后经过波峰焊或回流焊使表面组装元器件和电路之间建立可靠的机械和电气连接。
SMT(Surface Mounting Technology)表面安装技术的由来在几十年代的温长岁月中,电路组装技术得到经历三次大的变革。
六十年代和七十年代导体集成电路的推广应用爆发了电路组装技术的第一次变革─通孔插装技术的兴起和发展,出现了半自动和全自动插装以及浸焊和波峰焊接技术。
六十年代开发,七十年代开始应用的表面组装元器件动遥了通孔插装技术的“统治地位”,以自身的特点显示出强大的生命力,激起了电路组装技术的第二次变革─表面组装技术的蓬勃发展。
八十年代中期出现高速发展局面,九十年代初进入完全成熟阶段,现已成为电路组装技术主流,九十年代初兴起的第三次变革,使电路组装技术进入微组装技术的新时代。
一、SMT的特点:1.组装密度高、电子产品体积小、重量轻,贴片元件的体积和重量只有传统插装元件的1/10左右,一般采用SMT之后,电子产品体积缩小40%~60%,重量减轻60%~80%。
2.可靠性高、抗振能力强。
焊点缺陷率低。
3.高频特性好。
减少了电磁和射频干扰。
4.易于实现自动化,提高生产效率。
5.降低成本达30%~50%。
节省材料、能源、设备、人力、时间等。
二、为什么要用表面贴装技术(SMT)?1.电子产品追求小型化,以前使用的穿孔插件元件已无法缩小。
2.电子产品功能更完整,所采用的集成电路(IC)已无穿孔元件,特别是大规模、高集成IC,不得不采用表面贴片元件。
表面组装技术及工艺管理

表面组装技术及工艺管理近年来,随着科技的不断发展和应用的广泛推广,表面组装技术在电子产品制造中扮演着至关重要的角色。
本文将重点探讨表面组装技术的概念、工艺以及管理方法,以期为相关行业提供一定的参考和指导。
一、表面组装技术的概念与发展表面组装技术,简称SMT(Surface Mount Technology),是电子元器件组装的一种重要方式。
与传统的插件式组装技术相比,SMT技术具有体积小、重量轻、可靠性高等优点,因此在现代电子产品的制造中得到广泛应用。
SMT技术起源于20世纪60年代,当时被视为一项革命性的技术创新。
在70年代至80年代,随着电子产品小型化与功能的不断增强,SMT技术迅速发展,并逐渐成为了电子制造业的主流技术。
目前,SMT技术已广泛应用于手机、电脑、智能家居等领域,推动了电子产业的发展。
二、表面组装技术的工艺流程1. 元器件贴装表面组装的第一步是将元器件粘贴在PCB(Printed Circuit Board)上。
这一过程中需要借助贴片机完成自动化贴装,也可采用手工贴装的方式。
贴装的关键是保证元器件的位置和姿态的准确性,以确保后续的焊接工艺能够进行。
2. 焊接工艺元器件贴装完成之后,需要进行焊接工艺。
常见的焊接方式有波峰焊、回流焊和手工焊接。
波峰焊和回流焊是主流方式,能够提高焊接效率和可靠性。
手工焊接适用于少量生产和修复工作。
3. 焊接检测焊接完成后,需要对焊接质量进行检测。
这是保证电子产品质量的关键环节。
常用的焊接缺陷检测方法有AOI(Automated Optical Inspection)和X射线检测。
AOI通过光学镜头识别焊点异常,X射线检测可以检测隐蔽焊点问题。
三、表面组装技术的管理方法为了确保表面组装工艺的可靠性和稳定性,有效的工艺管理是必不可少的。
以下是几种常用的管理方法:1. 设计优化在产品设计阶段,应考虑元器件的可焊性和可贴装性,合理布局元器件的尺寸和间距。
通过优化设计,可降低组装难度和提高贴装效率。
表面组装技术
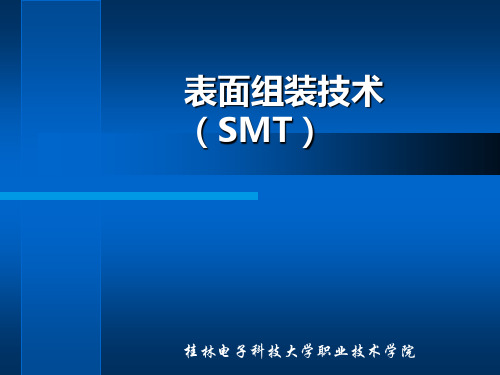
SMT技术优越性
1)微型化—组装密度高、电子产品体积小、重量轻
贴片元件体积和重量只有传统插装件的1/10左右,采用 SMT后电子产品体积缩小40%-60%,重量减轻60%-80% 。
SMT技术优越性
2) 可靠性高、抗振能力强。焊点缺陷率低。 3) 电性能优异。信号传输加快:连线短、延迟小, 减少了电磁和射频干扰。 4) 易于实现自动化,提高生产效率。 5) 降低成本达30%-50%。节省材料、能源等。 6)简化了电子整机生产工序。
表面组装技术 (SMT)
桂林电子科技大学职业技术学院
主要内容
➢表面组装技术概述 ➢SMT发展现状与趋势 ➢SMT技术特点与SMT生产系统组成
表面组装技术的概念
➢表面组装技术通常指采用自动化组装设备将片式化微型 无引线或短引线表面组装元器件(SMC/SMD,统称片状 元器件)直接贴装、焊接到印制电路板(PCB)表面或其 他基板表面规定位置的一种电子装联技术。 ➢电子行业中标准将SMT(Surface Mounting Technology)称为表面组装技术,也常称为表面贴装技 术或表面安装技术,是现代电子产品先进制造技术的重要 组成部分。
SMT包涵的基本内容
材料
测试
管理 工程
元器件
SMT
设备
基板
设计
工艺 方法
SMT包涵的基本内容
元器件:设计、制造与包装(托盘、编带等) 基板:单(多)层PCB、陶瓷基板等 设计:电、热设计、元件布局设计、PCB设计等 工艺方法:组装材料、组装工艺设计和组装设备应用 管理工程:生产线组装、控制和管理
加 强 交 通 建 设管理 ,确保 工程建 设质量 。16:08:1916:08:1916:08Tuesday, October 20, 2020
- 1、下载文档前请自行甄别文档内容的完整性,平台不提供额外的编辑、内容补充、找答案等附加服务。
- 2、"仅部分预览"的文档,不可在线预览部分如存在完整性等问题,可反馈申请退款(可完整预览的文档不适用该条件!)。
- 3、如文档侵犯您的权益,请联系客服反馈,我们会尽快为您处理(人工客服工作时间:9:00-18:30)。
表面组装技术概述一、表面组装技术的概念及其类型表面组装技术,又称表面安装技术或表面贴装技术,用SMT(Surface Mounting Technology)表示。
它是将片式元器件安装在印刷电路板或其它基板表面上,通过波峰焊、再流焊等方法焊接的一种新型的组装技术。
采用表面组装技术,可使电子产品小型化、薄型化、提高装配密度和装配速度,提高产品的质量,降低产品的成本。
表面组装技术包括片式元器件的设计、制造和选用,基板的选择,表面组装方案的制定和设计,印制线路板的设计与制造,粘结剂的点涂,焊膏印刷,片式元器件贴放,贴装部件的焊接,贴装部件的清洗,部件质量的检验和性能测试,部件的返修等。
表面组装技术的内容详见图1-1所示。
性能要求:电气性能、机械性能、稳定性、可靠性、一致性等片式元器件设计技术与制造:选用什么材料、结构形状、焊接端形式、尺寸精度、可焊性、制造技术包装形式:散装(塑料袋)、盒装(料盒)、带装(编带)、盘式。
基板材料、单(多)层印刷电路板、陶瓷、被釉金属、金属聚合物等基板电路图形制作:图形设计、元器件位置、焊盘、焊区间隙、尺寸大小、通孔金属化、测试点等片片式元器件在基板上单面组装式片式元器件和有引线元器件在基板两面混装元组装片式元器件在基板两面组装器多芯片组装件组装粘合剂:环氧树脂系、丙烯系等、用印刷或涂敷方法形成的组装技术材料工艺材料:助焊、清洗剂、阻焊剂、助溶剂表焊料:锡、锡-铅面流动材粘结剂涂敷:丝网印刷、涂布头组料涂敷粘结剂固化:紫外线照射加热、红外线照射加热、超声波加热装焊料涂敷:丝网印刷、涂布头技浸焊术流动焊波峰焊(水平喷流、倾斜喷流)焊接电热、红外线、喷热气、气相饱和蒸汽再流焊用焊料膏法、预焊料膏法顺序式:将印制电路板放在X-Y工作台上,元器件按程序逐个依次贴装上去组装机一次式:可通过模板一次同时将多个元器件贴装到印制电路板上序列式:有多个贴装头,印制电路板从一个工位移动至另一个工位,每个工位贴装一个元器件图1-1 表面组装技术的内容表面组装的类型根据有源器件和无源元件在基板上贴装的情况一般分为三种类型,如图1-2所示。
Ⅰ型表面组装,又称全SMT组装,即有印制板上只含有表面组装元器件,可以是单面组装,也可以是双面组装。
Ⅱ型表面组装件,又称为全混合组装件,既采用了SMT,又采用插装技术,可以是单面组装,或双面组装,一般是基板上表面为片式元器件和插装件,而基板底面为片式元件。
Ⅲ型表面组装件,又称为分面混合组装,也是同时采用SMT和插装技术的一种混合表面组装件,但印制板的上表面为插装元器件,印制板底面为片式元器件,如电阻器、电容器及晶体管等。
换句话说,即印制板的上表面为插装,底面为片式元器件的组装。
图1-2 三种表面组装技术的组装件图1-3示了Ⅰ型表面组装技术的工艺流程。
Ⅰ型不使用通孔插装元件。
先用丝网印刷焊膏、安放元器件,然后在再流焊炉或红外焊炉中,先预热除去焊膏中的挥发物,然后将组件再流焊焊接,用清洗剂消除残留的焊剂。
对于双面组装的组件,还需将电路板翻转,重复上述工艺流程。
电路板上表面的焊接点再一次被再流焊焊一次。
第二次再流焊时,元件由第一次再流焊焊过的焊膏表面张力定位。
通常第一次再流焊的焊膏的熔点比第二次再流焊的焊膏熔点约高一些,因此在组件翻转后,进行第二次再流焊焊接时元件不会脱落。
图1-3 Ⅰ型SMT的典型工艺流程Ⅲ型SMT的工艺流程如图1-4所示。
首先利用已有的通孔插装设备将通孔插装元器件自动插入并打弯。
然后,把组件翻转,涂上胶粘剂,这时已打弯的元器件不会脱落。
用贴装机放置表面组装元器件,在再流焊炉或红外炉中将粘胶剂固化,然后再将组件翻转过来,用波峰焊将带引线元器件和表面组装元器件同时加以焊接。
在波峰焊的过程中,印制线路板底面上的分立元器件用胶粘剂定位,如果不使用自动插装机,引线也未打弯,则工艺流程和上述相反。
首先涂布胶粘剂,放置片式表面组装元器件,胶粘剂固化,然后将组件翻转,用手工方式把全部通孔插装元器件插入,最后将两面的元器件用波峰焊焊接、清洗、测试和封装。
图1-4 Ⅲ型表面组装典型工艺流程Ⅱ型SMT的工艺流程如图1-5所示,它包括Ⅰ型和Ⅲ型的制作工艺。
它的工艺步骤最多,是最难制作的组件。
它的工艺流程为Ⅰ型工艺流程后,紧接着经过Ⅲ型的工艺流程。
图1-5 Ⅱ型表面组装典型工艺流程不同类型的表面组装件有不同的表面组装工艺,在整个工艺过程中,贴装和焊接是关键的工艺。
贴装工艺主要靠自动化的贴片机来完成,要求印制电路板的焊盘设计和制造精度高、片式元器件尺寸精度高、贴片时能准确无误地把片式元器件贴到规定的焊盘位置上,要完成这一点一般是由机械手按预先编好的程序来进行。
表面组装技术所组装的元器件主要靠波峰焊和再流焊来焊接,不同的组装方式采用不同的焊接工艺流程。
反过来,采用什么焊接工艺决定什么样的表面组装设计和元器件的排布。
有关波峰焊和再流焊的工艺流程见图1-6和图1-7。
从图1-6中看出,波峰焊工艺首先在PCB上网印粘结剂,贴装片式元器件,紫外线固化粘牢,翻转1800,在另一面上插装引线元器件,再焊接。
从图1-7看出,再流焊工艺先在PCB上网印焊膏,在同一面上贴装片式元器件,不需要翻转1800,插装元器件,再流焊接。
前者PCB两面都装了元器件,后者PCB的一面上装了元器件。
如果PCB正反两面皆有片式元器件,而有一面上又有引线元器件,其SMT的工艺过程就复杂多了。
图1-8示出了PCB正反两面上有片式元器件,而反面上又有引线元器件的情况。
在组装过程中,先网印粘结剂、贴装片式元器件、固化粘牢,PCB翻转1800,再网印焊料膏,贴装片式元器件,再流焊。
然后再插装引线元器件,预热,用波峰焊将正面的片式元器件和反面的引线元器件一起焊接。
这种PCB两面混组装,兼有两种焊接工艺。
对波峰焊来讲,有水平喷流(两波)和倾斜喷流(片波)。
采用波峰焊能够把片式元器件焊牢,不会产生气泡,能焊接极小的元器件,适合高密度PCB,在0.2mm间距时也不会产生桥接,焊接时使PCB与焊料接触面积减少,PCB吸热量小,这样可减少元器件因高热而损坏。
波峰焊效率高,适宜于焊接带引线的大批量的元器件。
它的不足之处是对片式元器件会产生热应力,焊接精度较差。
再流焊主要有红外再流焊、汽相再流焊。
这种焊接的主要优点:焊接温度均匀且精度高,不氧化,可以焊接任意形状的元器件,特别适宜于片式表面组装芯片和元器件的焊接。
图1-6 SMT的波峰焊工艺流程二、表面组装技术与片式元器件的发展情况片式元器件作为混合集成电路外贴件在60年代就开始用了,如用于制作IBM电子计算机、宇航和工业电子设备,至今已有30多年的历史。
70年代后期消费类电子产品向小型、薄型、多功能方面发展,表面组装技术得到了迅速的发展。
国际上SMT和片式元器件的发展经历了三个阶段;70年代中期,主要以小型化为目标,片式元器件主要用于混合集成电路、石英表和计算器。
70年代后期主要发展目标是提高电子产品的性能,片式元器件主要用于摄像机、随声听立体声收录机、电子照相机等。
在此期间,表面组装设备、组装工艺以及所需的材料逐渐成熟,从而形成了表面组装技术这一新型的技术。
80年代以后,主要目标是降低成本,提高产品的性能与价格比,大力发展自动高效的生产工艺,使表面组装技术在国际上成为电子产品组装技术的主流。
在此同时,世界各国都有不同程度的发展,我国对片式元器件的研制、生产和使用已有近廿年的历史。
片式电阻器、电容器、电感器及电子器件的自动化生产线已初具规模,用表面组装技术制造的电视机高频头、移动通讯机及一些测量仪器已投放市场。
表面组装技术不断迅速发展,已进入了电子产品组装自动化的第三次高潮,现在的表面组装技术的概念和过去相比发生了很大的变化,表现在用于贴装的片式元器件种类越来越多,从大类来讲就有30~40种。
原来认为不能片式化的有机薄膜电容器、铝电解电容图1-7SMT的再流焊工艺流程器等卷绕型的电容器,现在也能片式化了。
从产量方面来看,世界各国的产量都以很快的速度增大,1986年日本片式元器件产量已占元器件总量的47%,美国只有6%,90年代美国已超过50%。
因此片式元器件在元器件中扮演主角的时代即将来到。
以用得最多的阻容元器件为例,日本1986年固定电阻器和固定电容器片式化使用率占33%和46%,1990年占65%和70%,1992年电阻器为76%,多层陶瓷电容器占75%,钽电容器占67.9%,小型大容量多层陶瓷电容器占80%。
片式元器件逐渐朝着小型化和规范化方向发展,1983年前后,阻容片式元器件以3216型(3.2mm×1.6mm)扁平型为主,随着贴片机和片式元器件的进步,其尺寸逐渐减小,出现了如2125(2.0mm×1.25mm)型、2010(2.0mm×1.0mm)型、1608(1.6mm×0.8mm)型、1508(1.5mm×0.8mm)型和1005(1.0mm ×0.5mm)型。
目前正在研制0.8mm×0.4mm、0.5mm×0.25mm、0.4mm×0.2mm的小型化片式元器件。
其形状方面有矩形、圆筒形和异形。
矩形(又称方形)元件大部分都是长方形和扁平形,两端是由一层导电的材料形成电极。
典型的元器件有片式电阻器、叠片式陶瓷电容器、片式叠层电感器。
还有带金属电极的塑模器件,如片式钽电解电容器和片式薄膜电容器。
圆筒形片式元器件,看上去与一般元器件差不多,只是没有引线,其电极,一种是厚膜电极,另一种是金属帽电极,称为金属电极无引线端面键合元器件,用MELF表示。
异形片元器件,如线绕片式元器件、片式铝电解电容器、半可变电阻器、微调电容器及其它一些形状的元器件。
图1-8 PCB两面混合组装元器件的焊接工艺半导体器件的形状与异形元器件类似,小型模压塑封结构是小尺寸封装的主要封装形式,如塑料有引线芯片载体(PLCC)和平面封装。
平面封装有SOP的小型电路封装,它的引线在左右两侧。
另一种为QFP扁平封装,其引线间距在四个边上。
这两类型的封装可以部分取代DIP双列直插式标准形的封装,其引线间距可以小一半,而且还在不断缩小,如VQFP微小型扁平封装的引线间距已经缩小到0.5mm。
片式元器件尺寸的缩小无疑是提高贴装密度的一种手段。
但是这种方法迟早会达到极限。
另一方面,能被自动化贴装机贴装的元器件尺寸也有一定限度,而且随着元器件尺寸进一步减小,焊接缺陷也会不断增加。
如果采用组合片式元器件,即由一组元器件组成,将打破这一极限。
组合片式元器件即是把原来元器件和器件组成的电路模块集成在一个单个的复合元器件上。
组合式片式元器件的实际应用将从本质上改进元器件的贴装密度,并简化装配及检测过程,同时降低设备和机械的生产价格。