精馏塔的计算
精馏塔的计算

3.解吸:从吸收剂中分离出已被吸收气体的操作。
4.吸收操作传质过程:单向传质过程,吸收质从气相转移到液相的传质过程。
其中包括吸收质由气相主体向气液相界面的传递,及由相界面向液相主体的传递。
5.吸收过程:通常在吸收塔中进行。为了使气液两相充分接触,可采用板式塔或填料塔,少数情况下也选用喷洒塔。
对于易溶气体,H很大,此时,传质阻力集中于气膜中,液膜阻力可以忽略,1/ KG≈1/kG气膜阻力控制着整个吸收过程的速率,吸收总推动力的绝大部分用于克服气膜阻力,这种情况称为“气膜控制”。
对于气膜控制的吸收过程,如要提高其速率,在选择设备型式及确定操作条件时,应特别注意减小气膜阻力。
(2)以C*-C表示总推动力的吸收速率方程式(液相总吸收速率方程式)
解:将液组成换算成摩尔分率。
xF=(40/78)/(40/78+60/92)= 0.44
xD=(97/78)/(97/78+3/92)=0.974
xW=(2/78)/(2/78+98/92)=0.0235
原料平均摩尔质量MF=78×0.44+92×0.56=85.8kg/kmol
由物料衡算:F= D+W =15000/85.8= 175kmol/h
则F = D + W
FxF= DxD+ WxW
175 = D + WD=76.6kmol/h
175×0.44=0.974D+0.0235WW=98.4kmol/ h
例:将含24%(摩尔分率,以下同)易挥发组分的某混合液送入连续操作的精馏塔。要求馏出液中含95%的易挥发组分,残液中含3%易挥发组分。塔顶每小时送入全凝器850kmol蒸汽,而每小时从冷凝器流入精馏塔的回流量为670kmol。试求每小时能抽出多少kmol残液量。回流比为多少?
化工单元操作:精馏塔计算

(四)单股进料,无侧线出料 塔体上只有一个进料口,除塔顶馏出液和塔底残液,没有其他出料口。
二、全塔物料衡算(质量守恒)
1、物料衡算公式:
F = D + W FzF = DxD + WxW 2、采出率、易挥发组分回收率、难挥发组分回收率的概念和计算
2、提馏段操作线方程
L′ =V ′ + W
L′xm = V ′ym+1 + WxW
y m +1
=
L′ L′ −W
xm
−
WxW L′ −W
或者
y m +1
=
L′ V′
xm
− Wxw V′
它表达了在一定的操作条件下,提馏段内相邻两层塔板的下一层塔板上升蒸汽浓度 ym+1 与上 一层塔板下降液体浓度 xm 的关系。
3)进料线方程 y = q x − xF 进料线的意义:精馏段与提馏段两段操作线的交点轨迹。 q −1 q −1
二、操作线的绘制 步骤:
1、精馏段操作线 2、进料线,并与精馏段操作线有一交点 3、提馏段操作线
精馏塔计算
一、精馏塔塔板层数的确定
1、理论塔板的概念 汽液两相在塔板上充分接触,使离开塔板的两相温度相同,且两相组成互为平衡,则称
D = z F − xW F xD − xW
W = xD − zF =1− D
F xD − xW
F
ηD
=
Dx D Fz F
× 100%
ηW
= W (1 − xW ) ×100% F (1 − z F )
三、精馏操作线方程
1、精馏段操作线方程
精馏塔主要尺寸的计算
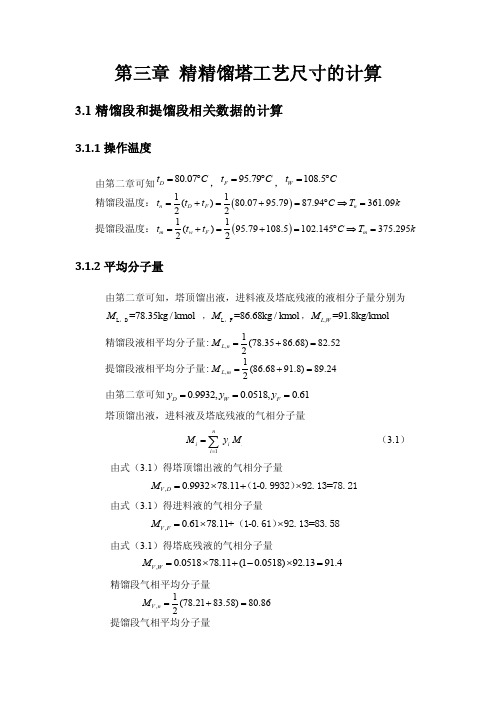
第三章 精精馏塔工艺尺寸的计算3.1精馏段和提馏段相关数据的计算3.1.1操作温度由第二章可知80.07D t C =︒,95.79F t C =︒,108.5W t C =︒精馏段温度:()11()80.0795.7987.94361.0922n D F n t t t C T k =+=+=︒⇒=提馏段温度:()11()95.79108.5102.145375.29522m w F m t t t C T k =+=+=︒⇒=3.1.2平均分子量由第二章可知,塔顶馏出液,进料液及塔底残液的液相分子量分别为=78.35kg /kmol M L ,D ,=86.68kg /kmol M L ,F ,,=91.8kg/kmol L W M精馏段液相平均分子量:,1(78.3586.68)82.522L n M =+=提馏段液相平均分子量:,1(86.6891.8)89.242L m M =+=由第二章可知0.9932,0.0518,0.61D W F y y y === 塔顶馏出液,进料液及塔底残液的气相分子量1ni iii M y M ==∑ (3.1)由式(3.1)得塔顶馏出液的气相分子量,0.993278.11-=V D M =⨯+⨯(10.9932)92.1378.21由式(3.1)得进料液的气相分子量,0.6178.11+-=V F M =⨯⨯(10.61)92.1383.58由式(3.1)得塔底残液的气相分子量,0.051878.11(10.0518)92.1391.4V W M =⨯+-⨯=精馏段气相平均分子量,1(78.2183.58)80.862V n M =+=提馏段气相平均分子量,1(83.5891.4)84.82V m M =+= 3.1.3平均气相密度根据任务书的要求,塔顶表压为4 kPa ,压降为0.7 kPa 则塔顶压力:104,D p kPa =进料压力:1040.716115.2F p kPa =+⨯=塔底压力:1040.725121.5,W p kPa =+⨯=精馏段压力:1(104115.2)109.6,2n p kPa =+=提馏段压力:1(121.5115.2)118.35,2m p kPa =+=pM RT ρ= (3.2)精馏段密度:,,109.680.642.948.314361.09V nn 3V n n p M kg /m RT ρ⨯===⨯提馏段段:, 3.383V m kg /m ρ=3.1.3.1平均液相密度由任务得:98%,35%,2%D F W a a a ===利用表1.3的数据用插值法求得苯和甲苯在塔顶、塔底及进料温度时的密度其中,a D ρ表示苯在塔顶温度下的密度,,b D ρ表示甲苯在塔顶温度下的密度。
精馏塔的工艺计算

2 精馏塔的工艺计算2.1精馏塔的物料衡算2.1.1根底数据 〔一〕生产能力:10万吨/年,工作日330天,每天按24小时计时。
〔二〕进料组成:乙苯212.6868Kmol/h ;苯3.5448 Kmol/h ;甲苯10.6343Kmol/h 。
〔三〕别离要求:馏出液中乙苯量不大于0.01,釜液中甲苯量不大于0.005。
2.1.2物料衡算〔清晰分割〕以甲苯为轻关键组分,乙苯为重关键组分,苯为非轻关键组分。
01.0=D H K x ,005.0=W LK x ,表2.1 进料和各组分条件由?别离工程?P65式3-23得:,1,,1LKi LK Wi HK D LK Wz xD Fx x =-=--∑ 〔式2. 1〕编号 组分 i f /kmol/h i f /%1 苯 3.5448 1.56252 甲苯 10.6343 4.6875 3 乙苯 212.6868 93.7500总计226.86591002434.13005.001.01005.0046875.0015625.08659.226=---+⨯=D Kmol/hW=F-D=226.8659-13.2434=213.6225Kmol/h 0681.1005.06225.21322=⨯==W X W ,ωKmol/h5662.90681.16343.10222=-=-=ωf d Kmol/h 132434.001.02434.1333=⨯==D X D d ,Kmol/h 5544.212132434.06868.212333=-=-=d f ωKmol/h表2-2 物料衡算表2.2精馏塔工艺计算2.2.1操作条件确实定 一、塔顶温度纯物质饱和蒸气压关联式〔化工热力学 P199〕:CC S T T x Dx Cx Bx Ax x P P /1)()1()/ln(635.11-=+++-=-表2-3 物性参数编号 组分 i f /kmol/h 馏出液i d 釜液i ω 1 苯 3.5448 3.5448 0 2 甲苯 10.6343 9.5662 1.0681 3 乙苯 212.6868 0.1324 212.5544总计226.865913.2434213.6225组份 相对分子质量临界温度C T 临界压力C P苯 78 562.2 48.9 甲苯 92 591.841.0 乙苯106617.236.0注:压力单位0.1Mpa ,温度单位K表2-3饱和蒸汽压关联式数据以苯为例,2.562/15.3181/1-=-=C T T x1.5)434.033399.3434.062863.2434.033213.1434.098273.6()434.01()(635.11-=⨯-⨯-⨯+⨯-⨯-=-CSP PIn01.02974.09.48)1.5exp(a S P MPa P =⨯=⨯-=同理,可得MPa P b 1.00985.00⨯=露点方程:∑==ni ii p p y 11,试差法求塔顶温度表2-4 试差法结果统计名称 A B C D 苯 -6.98273 1.33213 -2.62863 -3.33399 甲苯-7.28607 1.38091-2.83433 -2.79168 乙苯 -7.48645 1.45488-3.37538-2.23048故塔顶温度=105.5℃二、塔顶压力塔顶压力Mpa p 1.0013.1⨯=顶 三、塔底温度 泡点方程:p x pni i i=∑=10试差法求塔底温度故塔底温度=136℃四、塔底压力塔底压力Mpa p 1.0013.1⨯=底 五、进料温度进料压力为Mpa p 1.0013.1⨯=进,泡点方程:p x pni i i=∑=1试差法求进料温度故进料温度=133℃六、相对挥发度的计算据化学化工物性数据手册,用内插法求得各个数据5.105=顶t ℃,961.5=苯α514.2=甲苯α1=乙苯α; 136=底t ℃, 96.1=甲苯α1=乙苯α; 133=进t ℃, 38.4=苯α97.1=甲苯α1=乙苯α 综上,各个组份挥发度见下表据清晰分割结果,计算最少平衡级数。
精馏塔的计算
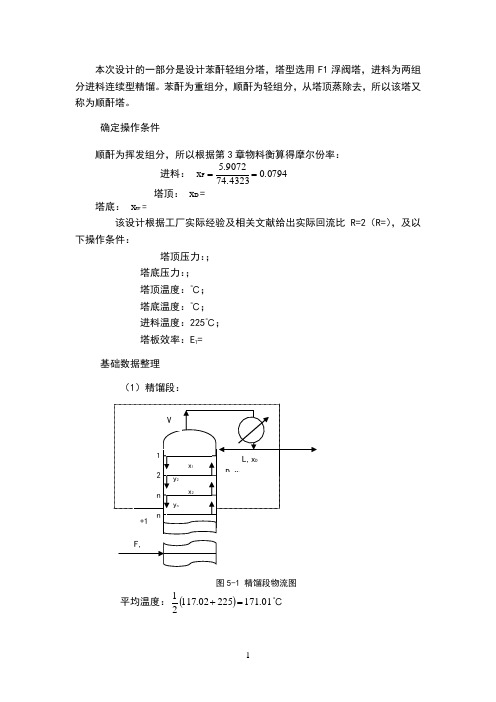
本次设计的一部分是设计苯酐轻组分塔,塔型选用F1浮阀塔,进料为两组分进料连续型精馏。
苯酐为重组分,顺酐为轻组分,从塔顶蒸除去,所以该塔又称为顺酐塔。
确定操作条件顺酐为挥发组分,所以根据第3章物料衡算得摩尔份率:进料: 794.0074.43239072.5x F ==塔顶: D x = 塔底: w x =该设计根据工厂实际经验及相关文献给出实际回流比R=2(R=),及以下操作条件:塔顶压力:; 塔底压力:; 塔顶温度:℃; 塔底温度:℃; 进料温度:225℃; 塔板效率:E T = 基础数据整理 (1)精馏段:图5-1 精馏段物流图平均温度:()01.17122502.11721=+℃平均压力:()=⎥⎦⎤⎢⎣⎡⨯+⨯⨯-⨯333100.107519.75100.10100.30213103.015⨯pa 根据第3章物料衡算,列出精馏段物料流率表如下:标准状况下的体积: V 0=2512.779.42234.7880=⨯Nm 3/h操作状况下的体积:V 1=63610101.01003.1510101.027301.1712732512.779⨯+⨯⨯⨯+⨯= Nm 3/h气体负荷: V n =3064.036001103.2112= m 3/s气体密度: =n ρ0903.32112.11033409.2240= kg/m 3液体负荷: L n =9470.036003409.2240= m 3/s℃时 苯酐的密度为1455kg/m 3(2)提馏段:图5-2 提馏段物料图平均温度:()01.23122502.23721=+℃入料压力:()Pa k 9.147519751030=-⨯- 平均压力:()=+0.309.1421根据第3章物料衡算列出提馏段内回流如下图:表5-2 提馏段内回流标准状况下的体积:='0V 4054.4974.222056.22=⨯Nm 3/h 操作状态下的体积:='1V 63610101.0105.2210101.027301.2312734054.497⨯+⨯⨯⨯+⨯= Nm 3/h气体负荷:V m =2086.03600751.0162=m 3/s气体密度 m ρ=7022.110162.7518788.5420=kg/m 3查得进料状态顺酐与苯酐混合物在温度225℃下,含顺酐(wt)%,密度1546kg/m 3。
精馏塔和塔板的主要工艺尺寸的计算
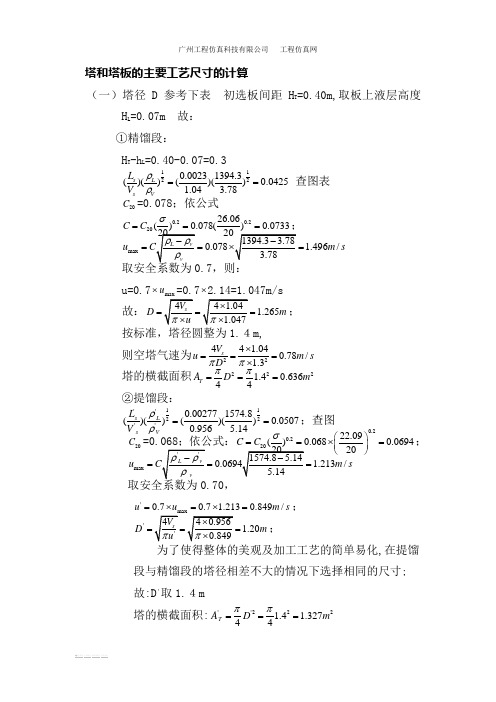
塔和塔板的主要工艺尺寸的计算(一)塔径 D 参考下表 初选板间距H T =0.40m,取板上液层高度H L =0.07m 故: ①精馏段:H T -h L =0.40-0.07=0.311220.00231394.3()()()()0.04251.04 3.78s L s V L V ρρ== 查图表 20C =0.078;依公式0.20.22026.06()0.078()0.0733C C σ===;max0.078 1.496/u m s ===,则:u=0.7⨯u =0.7⨯2.14=1.047m/s 故: 1.265D m ===; 按标准,塔径圆整为1.4m,则空塔气速为2244 1.040.78/1.3s V u m s D ππ⨯===⨯ 塔的横截面积2221.40.63644T A D m ππ===②提馏段:11''22''0.002771574.8()()()()0.05070.956 5.14s L s V L V ρρ==;查图20C0.20.222.09()0.0680.069420C C σ⎛⎫==⨯= ⎪⎝⎭; max 1.213/u m s===,'0.70.7 1.2130.849/u u m s =⨯=⨯=;' 1.20D m ===; 为了使得整体的美观及加工工艺的简单易化,在提馏段与精馏段的塔径相差不大的情况下选择相同的尺寸; 故:D '取1.4m塔的横截面积:''2221.4 1.32744T A D m ππ===空塔气速为22440.956'0.720/1.3s V u m s D ππ⨯===⨯ 板间距取0.4m 合适(二)溢流装置采用单溢流、弓形降液管、平形受液盘及平形溢流堰,不设进流堰。
各计算如下: ①精馏段:1、溢流堰长 w l 为0.7D ,即:0.7 1.40.91w l m =⨯=;2、出口堰高 h w h w =h L -h ow 由l w /D=0.91/1.4=0.7, 2.5 2.58.2810.480.91h w L l m ==查手册知:E 为1.03 依下式得堰上液高度:22332.84 2.848.281.030.013100010000.91h ow w L h E m l ⎛⎫⎛⎫==⨯= ⎪ ⎪⎝⎭⎝⎭ 故:L ow h -h 0.070.0130.057w h m ==-=3、 降液管宽度d W 与降液管面积f A有/w l D =0.7查手册得/0.14,/0.08d fT W D A A ==故:d W =0.14D=0.14 ⨯1.3=0.182m2220.080.08 1.30.106244f A D m ππ==⨯⨯=()0.10620.418.55,0.0023f T s A H s s L τ⨯===>符合要求4、降液管底隙高度0h取液体通过降液管底隙的流速0u =0.1m/s 依式计算降液管底隙高度0h , 即:000.00230.0250.910.1s w L h m l u ===⨯ ②提馏段:1、 溢流堰长'w l 为0.7'D ,即:'0.7 1.40.91w l m =⨯=;2、出口堰高'w h ''w L ow h =h -h ;由 '/D=0.91/1.4=0.7w l ,'2.5 2.59.9812.630.91h w L l m ==查手册知 E 为1.04依下式得堰上液高度:2233''2.84 2.849.981.040.0146100010000.91h oww L h E ml ⎛⎫⎛⎫==⨯= ⎪ ⎪⎝⎭⎝⎭0.070.01460.0554w h m =-=。
精馏塔计算

逐板计算非泡点进料时精馏塔的加料板位置扬州化工学校徐忠娟申丽1.前言精馏塔的理论板层数的求取,通常采用两种方法:逐板计算法和图解法。
比较两种方法各有利弊:图解法简捷、方便但是准确性差;用逐板计算法得到的理论塔板数准确,不足的是计算过程复杂繁琐。
随着计算机知识的普及,学生掌握编程语言后,利用计算机瞬间即可完成繁琐的迭代运算,因而逐板计算法的应用也就越来越多。
无论是逐板计算法还是图解法,求取理论板层数,都需要确定加料板的位置。
2.加料板位置确定的原则图1 适宜的加料位置在图解法中适宜的加料板位置是以跨过两操作线交点的梯级来确定的。
如图(1)所示,当工艺条件和分离要求相同时,对于同一个塔,确定的加料位置不同,所需的理论塔板数不相同。
在图(1)的(a)中梯级已跨过精馏段操作线和提馏段操作线的交点d而仍在精馏段操作线和平衡线间作梯级,由于交点d以后精馏段操作线和平衡线间垂直距离较提馏段操作线和平衡线间的垂直距离小,作出的理论塔板数会增加。
反之若如图(1)中的(b)所示,在梯级尚未跨过两操作线的交点时就过早地更换操作线也同样会使理论塔板数增加。
只有当梯级刚跨过操作线交点就更换操作线作梯级如图(1)中(c)的所示,所得的理论板层数最少。
可见过迟或过早的更换操作线,都将导致理论板层数的增加。
同理逐板计算法中也存在该问题,在一般的化工原理教材中,介绍逐板计算法求理论板层数时,均以泡点进料为例,指出当计算到x N,≤x F 时(x F 为原料液的易挥发组分的摩尔分率),说明第N 层是加料板,那么对于非泡点进料状况又该如何确定,几乎不提。
许多学生碰到非泡点进料时,也用x N,≤x F 来确定加料板位置,结果是加料位置不适宜,导致理论板层数增多。
根据图解法中跨过两段操作线交点的梯级为适宜加料板位置的原则,结合多年的教学实践,我们总结出了最适宜的加料位置是该板的液相组成等于或略低于x q 。
其中x q 为精馏段操作线方程式和提馏段操作线方程式所联立的方程组解的x 值(相当于图解法中两操线交点的横坐标),当然,对于饱和液体进料,就有x q =x F 。
精馏塔的工艺计算
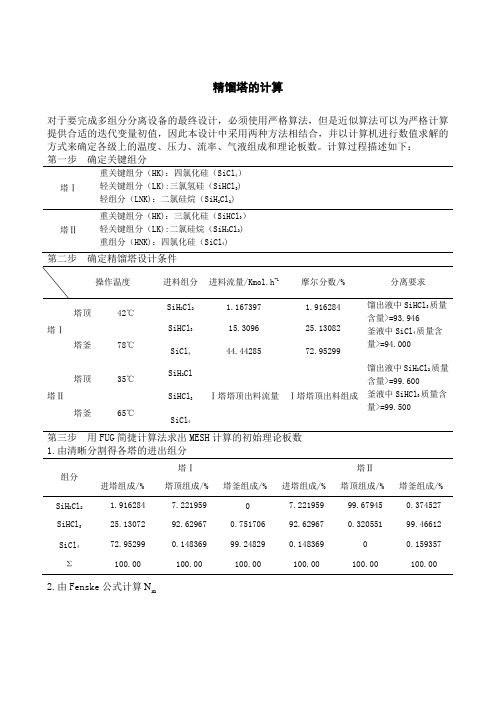
精馏塔的计算对于要完成多组分分离设备的最终设计,必须使用严格算法,但是近似算法可以为严格计算提供合适的迭代变量初值,因此本设计中采用两种方法相结合,并以计算机进行数值求解的方式来确定各级上的温度、压力、流率、气液组成和理论板数。
计算过程描述如下:第一步确定关键组分塔Ⅰ重关键组分(HK):四氯化硅(SiCl4)轻关键组分(LK):三氯氢硅(SiHCl3) 轻组分(LNK):二氯硅烷(SiH2Cl2)塔Ⅱ重关键组分(HK):三氯化硅(SiHCl3)轻关键组分(LK):二氯硅烷(SiH2Cl2) 重组分(HNK):四氯化硅(SiCl4)塔Ⅰ塔顶42℃SiH2Cl2 1.167397 1.916284 馏出液中SiHCl3质量含量>=93.946釜液中SiCl4质量含量>=94.000SiHCl315.3096 25.13082塔釜78℃SiCl444.44285 72.95299塔Ⅱ塔顶35℃SiH2ClⅠ塔塔顶出料流量Ⅰ塔塔顶出料组成馏出液中SiH2Cl2质量含量>=99.600釜液中SiHCl3质量含量>=99.500SiHCl3塔釜65℃SiCl4第三步用FUG简捷计算法求出MESH计算的初始理论板数组分塔Ⅰ塔Ⅱ进塔组成/% 塔顶组成/% 塔釜组成/% 进塔组成/% 塔顶组成/% 塔釜组成/% SiH2Cl2 1.916284 7.221959 0 7.221959 99.67945 0.374527 SiHCl325.13072 92.62967 0.751706 92.62967 0.320551 99.46612 SiCl472.95299 0.148369 99.24829 0.148369 0 0.159357 Σ100.00 100.00 100.00 100.00 100.00 100.002.由Fenske公式计算mNlg lg LK HKLK HKd d w w Nm a-轾骣骣犏琪琪琪琪犏桫桫臌=3.由恩特伍德公式计算最小回流比,,1()i i Fim i i D m m i x q R x R a a q a a q üï=-ï-ï?ýï=ï-ïþåå4.由芬斯克公式计算非清晰分割的物料组成()1i i Nm HK i HK HK f w d w a -=骣琪+琪桫 ,()()1NmHK i i HK HK i NmHK i HKHK d f w d d w a a--骣琪琪桫=骣琪+琪桫5.由Kirkbride 经验式确定进料位置0.2062,,,,HK F LK WR S LK F HK D z x N W N z x D 轾骣骣骣犏琪琪琪=琪犏琪琪桫犏桫桫臌6.由吉利兰关系式计算理论板数即0.56680.750.75Y X=-式中1m R R X R -=+ ,1mN N Y N -=+ 第四步 由MESH 方程计算理论板数 1. 用FUG 简捷计算法得到的理论板数N 和进料位置M 作为初始值,初始化汽液流量j V 和j L 。
精馏塔全塔效率计算公式
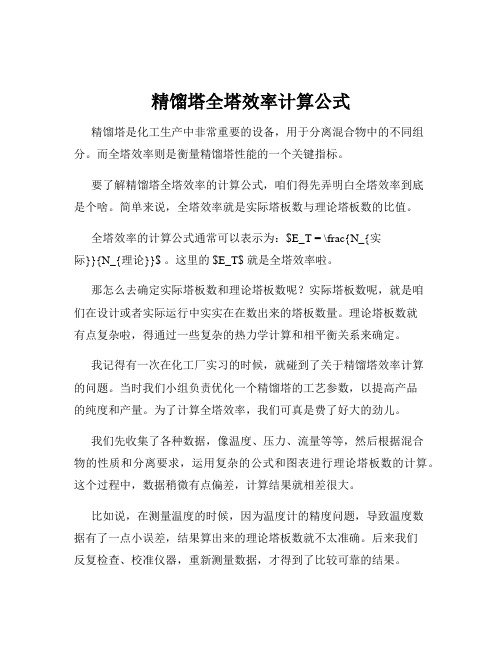
精馏塔全塔效率计算公式精馏塔是化工生产中非常重要的设备,用于分离混合物中的不同组分。
而全塔效率则是衡量精馏塔性能的一个关键指标。
要了解精馏塔全塔效率的计算公式,咱们得先弄明白全塔效率到底是个啥。
简单来说,全塔效率就是实际塔板数与理论塔板数的比值。
全塔效率的计算公式通常可以表示为:$E_T = \frac{N_{实际}}{N_{理论}}$ 。
这里的 $E_T$ 就是全塔效率啦。
那怎么去确定实际塔板数和理论塔板数呢?实际塔板数呢,就是咱们在设计或者实际运行中实实在在数出来的塔板数量。
理论塔板数就有点复杂啦,得通过一些复杂的热力学计算和相平衡关系来确定。
我记得有一次在化工厂实习的时候,就碰到了关于精馏塔效率计算的问题。
当时我们小组负责优化一个精馏塔的工艺参数,以提高产品的纯度和产量。
为了计算全塔效率,我们可真是费了好大的劲儿。
我们先收集了各种数据,像温度、压力、流量等等,然后根据混合物的性质和分离要求,运用复杂的公式和图表进行理论塔板数的计算。
这个过程中,数据稍微有点偏差,计算结果就相差很大。
比如说,在测量温度的时候,因为温度计的精度问题,导致温度数据有了一点小误差,结果算出来的理论塔板数就不太准确。
后来我们反复检查、校准仪器,重新测量数据,才得到了比较可靠的结果。
在确定了实际塔板数和理论塔板数之后,代入全塔效率的计算公式,就能得出全塔效率啦。
通过计算全塔效率,我们可以评估精馏塔的性能,找出可能存在的问题,比如塔板结构不合理、操作条件不合适等等。
总之,精馏塔全塔效率的计算公式虽然看起来简单,但是要准确计算和应用,还需要我们对精馏过程有深入的理解,对数据的收集和处理要非常严谨。
只有这样,才能真正发挥全塔效率这个指标的作用,让精馏塔更好地为化工生产服务。
希望通过我的讲解,能让您对精馏塔全塔效率的计算公式有更清楚的认识。
要是在实际应用中遇到问题,别着急,多思考、多尝试,总会找到解决办法的!。
精馏塔指标计算

2.精馏塔工艺计算2.1塔的物料衡算2.1.1料液及塔顶,塔底产品含乙醇的摩尔分率F:原料液流量(kmol/s) xF:原料组成(摩尔分率,下同)D:塔顶产品流量(kmol/s) xD:塔顶组成W:塔底残液流量(kmol/s) xW:塔底组成2.1.2进料2.1.3物料衡算2.2有关的工艺计算2.2.1原料液的平均摩尔质量:Mf =xfMOHCHCH23+(1-xf)MOH2=0.1934⨯46+(1-0.1934)⨯18=23.4kg/kmol 同理可求得:MD =42.6972kg/kmol MW=18.5544kg/kmol45 C下,原料液中ρOH2=971.1kg/m3,ρOHCHCH23=735kg/m3由此可查得原料液,塔顶和塔底混合物的沸点,以上计算结果见表6。
表6 原料液`馏出液与釜残夜的流量与温度2.3 最小回流比及操作回流比的确定如图所示的乙醇-水物系的平衡曲线,具有下凹的部分,当操作线与q线的交点尚未落到平衡线上之前,操作线已与平衡线相切,如图中点g所示。
点g附近已出现恒浓区,相应的回流比便是最小回流比。
对于这种情况下的Rmin的求法只能是通过作图定出平衡线的切线之后,再由切线的截距或斜率求之。
如图1-63所示,可用下式算出:1min min +R R =1934.08814.037.08814.0-- ⇒ R min =2.889可取操作回流比R=1.5⨯2.889=4.3342.4 全凝器冷凝介质的消耗量塔顶全凝器的热负荷:Q C =(R+1)D(I VD -I LD ) 可以查得I VD =1266kJ/kg I LD =253.9kJ/kg,所以 Q C =(1.612+1)⨯2.0330⨯(1266-253.9)=5317.45kJ/h取水为冷凝介质,其进出冷凝器的温度分别为25 C 和35 C 则 平均温度下的比热c pc =4.174kJ/kg C,于是冷凝水用量可求 W C =)(c Q 12pc C t t -=)2535(174.445.5317-⨯=127.4kg/h4.精馏塔主体尺寸计算4.3提留段塔径的计算1t 2DF t t +=705.91258.9983.83=+=℃查t-x-y 图在91.705℃下:0552.0=x A, A y 3273.0= 9448.0=xB, B y 6727.0=KmolKg xM xM MBAL/5456.199448.0180552.04621=⨯+⨯=+=M g =M 1y A +M 2y B =46⨯0.3273+18⨯0.6727=27.1644 kg/kmol 汽塔气相平均密度 v ρ=RTPM g=)705.91273(314.81644.27325.101+⨯⨯=0.9077 kg/m 3x AW =LA Mx M 1=5456.190552.046⨯=0.1299x BW =1-x AW =0.8701 汽塔的液相平均密度 在91.705℃下查表得:A ρ=729.5 kg/m 3B ρ=964.3 kg/m 3Lρ1=AAWx ρ+BBWx ρ=7295.01299.0+9643.08701.0=1.0804 L ρ=925.6 kg/m 3V=(R+1)D=(4.334+1)⨯8.057=42.976 kmol/h v B =vg 3600 vM ρ⨯ =9077.036001644.27976.42⨯⨯=0.3573 m/sL '=L+qF=8.811+1⨯10.09=18.901 kmol/h L 3=LLML ρ⨯3600'=6.92536005456.19901.18⨯⨯=0.1109⨯103-m 3/s查化工数据手册求取:A σ=16.1 mN/mB σ=60.05 mN/m5.塔高的确定:Z=(TT E N -1)H T =(7968.015-1)⨯0.45=8.02 m塔板结构尺寸的确定: ● 溢流装置● 由于塔径小于800mm,所以采用单溢流弓形降液管,平行受液盘及平行溢流堰, 取堰长L w =0.66D,即L w =0.66⨯0.3=0.198m 出口堰高HW=H1-HOW,66.0=DLw,则H ow =m 003.0)0198.02412.0(1100084.232=⨯⨯H w =H l - H OW =0.06-0.003=0.057m 降液管的宽度W d 与降液管的面积A f 由66.0=Dlw,125.0Dw d ,=tf A A 0.0700W d =0.125⨯0.3=0.0375mA f =0.07⨯3202.04m D=π停留时间(03.25100899.045.0005.03s LsHtAf =⨯⨯=⋅=- 〉5S 符合要求)降液管底隙高度Ho h o =h w -0.006=0.051m 取边缘宽度取边缘宽度为W C =0.03m 安定区宽度安定区宽度为W S =0.050m 开孔区面积A a X=(2-D W d +W S )=)050.00375.0(23.0+-=0.0625mR=-2D W C =0.15-0.03=0.12mA a =2[x 222180R xR π+-sin 1-Rx =0.068m 2。
精馏塔主要工艺尺寸计算

精馏塔主要工艺尺寸计算一、塔径D1、精馏段塔径初选板间距m H T 40.0=,取板上液层高度m h L 06.0=,故m h H L T 34.006.040.0=-=-; 0319.030.28.87792.00015.02121=⎪⎭⎫ ⎝⎛⨯=⎪⎪⎭⎫ ⎝⎛⎪⎪⎭⎫ ⎝⎛vL SS V L ρρ 查Smith 关联图得C 20;依2.02020⎪⎭⎫⎝⎛=σC C 校正物系表面张力为m mN /45.21时的C0720.02045.21071.0202.02.020=⎪⎭⎫⎝⎛⨯=⎪⎭⎫⎝⎛=σC Cs m Cu V V L /405.130.230.28.8770720.0max =-⨯=-=ρρρ可取安全系数为,则s m u u /843.0405.160.060.0max =⨯==故m u V D S 179.1843.092.044=⨯⨯==ππ 按标准,塔径圆整为1.2m,则空塔气速。
2、提馏段塔径初选板间距m H T 40.0=,取板上液层高度m h L 06.0=,故m h H L T 34.006.040.0=-=-; 0782.070.20.96041.00017.02121=⎪⎭⎫ ⎝⎛⨯=⎪⎪⎭⎫ ⎝⎛⎪⎪⎭⎫ ⎝⎛vL SSV L ρρ 查Smith 关联图得C 20;依2.02020⎪⎭⎫⎝⎛=σC C 校正物系表面张力为m mN /92.19时的C ,即0679.02092.19068.0202.02.020=⎪⎭⎫⎝⎛⨯=⎪⎭⎫⎝⎛=σC Cs m Cu V V L /279.170.270.20.9600679.0max =-⨯=-=ρρρ 可取安全系数为,则s m u u /767.0279.160.060.0max =⨯== 故m u V D S 825.0767.041.044=⨯⨯==ππ 按标准,塔径圆整为1.0m,则空塔气速。
为统一精馏段和提馏段塔径,取为。
精馏塔计算书

精馏塔计算书1. 精馏塔简介精馏塔是工业生产中常见的分离设备,用于分离液体混合物中的各个组分。
其基本原理是利用不同组分之间的沸点差异,将混合物加热至某一温度,使其中沸点较低的组分蒸发成气体,之后再将气体经过冷却、凝结等步骤,得到纯净的分离物质。
2. 精馏塔分类根据不同的液相分配方式和气液分布情况,可以将精馏塔分为以下几种类型:1.板式精馏塔:使用平行垂直放置的薄板或网格作为液相分配器,其优点是能够在塔内产生较好的液相分布和良好的接触效果。
2.填料式精馏塔:通过填充一定形状、大小和材质的填料物质以帮助气液接触传递质量,减少气液间的不均匀性,填料的选择主要依据溶液的性质、处理量和筛选效果等因素。
3.旋转精馏塔:利用塔底的旋转器生成涡流效应,使气液分布均匀,提高精馏效果。
3. 精馏塔操作参数和计算方法精馏塔的分离效果主要取决于操作参数的选择和控制。
以下是常见的操作参数及其计算方法:1.通量:通量又称液循环速度,表示液相在塔内的运动速度。
通量的大小直接影响精馏效果,通常采用下列公式计算:Q=K*F*(ρL-ρG)^0.5式中,Q为液相通量,m3/(h.m2),K为液相流动系数,一般取值范围为0.03~0.4,F为液相流量,m3/h,ρL、ρG分别为液相和气相密度,kg/m3。
2.板间液流速度:指单位时间内液相通过精馏塔中单个板面积的速度,这个参数可以通过下列公式计算:V=Q/S式中V为液相速度,m/s,Q和S分别为板面积和液相通量。
3.泡点:泡点是指在一定气体流量和压力下,液体中开始产生气泡的温度。
泡点的大小主要取决于液相成分及液相通量,计算泡点通常采用下列公式:Tb=K1+(K2/K3)*ln(P)式中,Tb为泡点温度,K1、K2、K3均为常数,P为气体部分压力。
4. 精馏塔设计精馏塔设计通常需要考虑以下因素:1.分离要求:包括物料的沸点范围、分离塔的纯度要求等。
2.处理量:即单位时间内处理的混合物体积。
精馏塔计算方法

目录1 设计任务书 (1)1.1 设计题目………………………………………………………………………………………………………………………………………………………………………1.2 已知条件………………………………………………………………………………………………………………………………………………………………………1.3设计要求…………………………………………………………………………………………………………………………………………………………………………2 精馏设计方案选定 (1)2.1 精馏方式选择…………………………………………………………………………………………………………………………………………………………………2.2 操作压力的选择…………………………………………………………………………………………………………………………………………………………………2.4 加料方式和加热状态的选择……………………………………………………………………………………………………………………………………………………2.3 塔板形式的选择…………………………………………………………………………………………………………………………………………………………………2.5 再沸器、冷凝器等附属设备的安排……………………………………………………………………………………………………………………………………………2.6 精馏流程示意图…………………………………………………………………………………………………………………………………………………………………3 精馏塔工艺计算 (2)3.1 物料衡算…………………………………………………………………………………………………………………………………………………………………………3.2 精馏工艺条件计算………………………………………………………………………………………………………………………………………………………………3.3热量衡算…………………………………………………………………………………………………………………………………………………………………………4 塔板工艺尺寸设计 (4)4.1 设计板参数………………………………………………………………………………………………………………………………………………………………………4.2 塔径………………………………………………………………………………………………………………………………………………………………………………4.3溢流装置…………………………………………………………………………………………………………………………………………………………………………4.4 塔板布置及浮阀数目与排列……………………………………………………………………………………………………………………………………………………5 流体力学验算 (6)5.1 气相通过塔板的压降……………………………………………………………………………………………………………………………………………………………5.2 淹塔………………………………………………………………………………………………………………………………………………………………………………5.3 雾沫夹带…………………………………………………………………………………………………………………………………………………………………………6 塔板负荷性能图 (7)6.1 雾沫夹带线………………………………………………………………………………………………………………………………………………………………………6.2 液泛线…………………………………………………………………………………………………………………………………………………………………………6.3 液相负荷上限线…………………………………………………………………………………………………………………………………………………………………6.4 漏液线…………………………………………………………………………………………………………………………………………………………………………6.5 液相负荷下限线…………………………………………………………………………………………………………………………………………………………………6.6 负荷性能图………………………………………………………………………………………………………………………………………………………………………7 塔的工艺尺寸设计 (8)8釜温校核 (9)9热量衡算 (9)10接管尺寸设计 (10)符号说明 (10)参考文献 (13)结束语 (13)1.设计任务1.1设计题目:年产8000吨乙醇板式精馏塔工艺设计1.2已知条件:1原料组成:含35%(w/w)乙醇的30度液体,其余为水。
精馏塔的规格如何计算公式
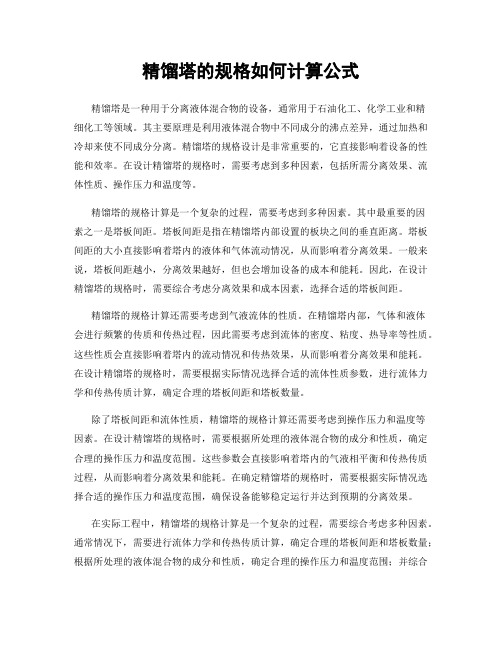
精馏塔的规格如何计算公式精馏塔是一种用于分离液体混合物的设备,通常用于石油化工、化学工业和精细化工等领域。
其主要原理是利用液体混合物中不同成分的沸点差异,通过加热和冷却来使不同成分分离。
精馏塔的规格设计是非常重要的,它直接影响着设备的性能和效率。
在设计精馏塔的规格时,需要考虑到多种因素,包括所需分离效果、流体性质、操作压力和温度等。
精馏塔的规格计算是一个复杂的过程,需要考虑到多种因素。
其中最重要的因素之一是塔板间距。
塔板间距是指在精馏塔内部设置的板块之间的垂直距离。
塔板间距的大小直接影响着塔内的液体和气体流动情况,从而影响着分离效果。
一般来说,塔板间距越小,分离效果越好,但也会增加设备的成本和能耗。
因此,在设计精馏塔的规格时,需要综合考虑分离效果和成本因素,选择合适的塔板间距。
精馏塔的规格计算还需要考虑到气液流体的性质。
在精馏塔内部,气体和液体会进行频繁的传质和传热过程,因此需要考虑到流体的密度、粘度、热导率等性质。
这些性质会直接影响着塔内的流动情况和传热效果,从而影响着分离效果和能耗。
在设计精馏塔的规格时,需要根据实际情况选择合适的流体性质参数,进行流体力学和传热传质计算,确定合理的塔板间距和塔板数量。
除了塔板间距和流体性质,精馏塔的规格计算还需要考虑到操作压力和温度等因素。
在设计精馏塔的规格时,需要根据所处理的液体混合物的成分和性质,确定合理的操作压力和温度范围。
这些参数会直接影响着塔内的气液相平衡和传热传质过程,从而影响着分离效果和能耗。
在确定精馏塔的规格时,需要根据实际情况选择合适的操作压力和温度范围,确保设备能够稳定运行并达到预期的分离效果。
在实际工程中,精馏塔的规格计算是一个复杂的过程,需要综合考虑多种因素。
通常情况下,需要进行流体力学和传热传质计算,确定合理的塔板间距和塔板数量;根据所处理的液体混合物的成分和性质,确定合理的操作压力和温度范围;并综合考虑成本和能耗等因素,选择合适的设备规格。
精馏塔的计算

X1、X2—分别为出塔和进塔液体的组成,
(1)分子扩散的阻力和速率主要决定于扩散物质和流体的温度以及某些物理性质。
(2)分子扩散速率与其在扩散方向上的浓度梯度成正比。
分子扩散系数是物质的物理性质之一。扩散系数大,表示分子扩散快。
(3)分子在液体中扩散速率比在气体中要慢的多。因为液体的密度比气体的密度大得多,其分子间距小。
2.涡流扩散:通过流体质点的湍动和旋涡而传递物质的现象。主要发生在湍流流体中。
所以气体的摩尔分率为yA=pA/P=vA/V;xD
yB=PB/P= vB/V或yB=1-yAF,xF
三.物料衡算(双组分)
对总物料衡算F =D+W
对易挥发组分衡算FxF=DxD+ WxW
式中:W
F——原料液、塔顶产品(馏出液)、塔底产品(釜残液)流量,kmol/hxW
xF、xD、xW——分别为原料液、馏出液、釜残液中易挥发组分的摩尔分率
二.吸收分类
组分数目:单组分吸收,多组分吸收。
化学反应:物理吸收,化学吸收。
热效应:等温吸收,非等温吸收。
三.相组成表示
1.比质量分率XW(YW):混合物中两组分的质量之比。
XW(YW)= GA/GB=αA/αBkgA / kgB
2.比摩尔分率X(Y):混合物中两组分的摩尔数之比。
X =nA/nB=xA/xB=xA/(1-xA)kmolA / kmolB
3.对流扩散:湍流主体与相界面间的涡流扩散与分子扩散两种传质作用的总称。
它与传热过程的对流传热类似。
六.吸收机理
(一)吸收机理(双膜理论要点)
1.相互接触的汽液两流体间存在着稳定的相界面,界面两侧各存在着一个很薄的有效层流膜层。吸收质以分子扩散方式通过两膜层。
精馏塔计算

塔板总面积为 弓形溢流管宽度 弓形降液管面积 检验: 液体在精馏段降液管内的停留时间 τ 液体在提留段降液管内的停留时间 τ 堰上液流高度 塔的平均液相流量 查表得液流收缩系数 堰高度 溢流塔底与塔盘间距离
how 6mm<how<60mm Lh kmol/h Lh/(lw)^2.5 E hw ho
处理量: 4万吨/年 原料组成:甲醇的质量分率wf=0.35(质量分数) 产品要求:塔顶甲醇的质量分率wd=0.94(质量分数) 塔底甲醇的质量分率 =0.02(质量分数) 生产时间: 300天/年 冷却水进口温度:25℃ 加热剂: 0.9MP饱和水蒸汽 单板压降: 小于或等于0.7kpa 生产方式: 连续操作,泡点回流 全塔效率: Et=50%
塔板结构尺寸确定 因塔径大于800mm,所以采取单溢流型分块式塔板 堰长 假设 则 据图可得, lw lw=(0.6-0.8)*D lw m lw/D Wd/D Af/AT AT ㎡ Wd m Af ㎡ τ >5s τ >5s (1.08-1.44) 1.4 0.777777778 0.19 0.13 2.5434 0.342 0.330642 47.5494361 47.03750803 11.10990396 10.06774099 4.341221497 1.05 48.89009604
64.86036036 196.9396396
Байду номын сангаас
原料液 0.35 0.23 261.8
釜残液 0.02 0.01 196.9396396
0.898 101.325 PA0 PB0
110.6967938 43.01562333 0.861530264 0.941215277 107.3913823 41.57949972 0.907822386 0.962174201 85.06190349 117.7631723 46.10280151 2.55436044
精馏塔的简洁计算公式

精馏塔的简洁计算公式精馏塔是一种用于分离液体混合物的设备,通过不同组分的沸点差异来实现分离。
在工程设计和操作中,需要对精馏塔进行计算和分析,以确保其正常运行和达到预期的分离效果。
在本文中,我们将介绍精馏塔的简洁计算公式,帮助读者更好地理解和应用这些公式。
1. 精馏塔的传质效率公式。
精馏塔的传质效率是评价其性能的重要指标之一。
传质效率通常用塔板数或高度来表示,其计算公式如下:N = HETP × (n-1)。
其中,N表示塔板数或塔高度,HETP表示每塔板传质高度,n表示理论板数。
2. 精馏塔的塔板压降公式。
塔板压降是精馏塔运行中需要考虑的重要参数之一。
塔板压降的计算公式如下:ΔP = ρ× g × H × (1-ε) + ΔPv。
其中,ΔP表示塔板压降,ρ表示液体密度,g表示重力加速度,H表示塔板高度,ε表示塔板孔隙率,ΔPv表示气体速度压降。
3. 精馏塔的塔顶温度计算公式。
精馏塔的塔顶温度是其操作中需要重点关注的参数之一。
塔顶温度的计算公式如下:T = T0 + ΔT。
其中,T表示塔顶温度,T0表示进料温度,ΔT表示塔顶降温。
4. 精馏塔的塔板液体高度计算公式。
塔板液体高度是精馏塔操作中需要实时监测和控制的参数之一。
塔板液体高度的计算公式如下:H = H0 + ΔH。
其中,H表示塔板液体高度,H0表示初始液位高度,ΔH表示液位变化量。
5. 精馏塔的塔板塔顶气体速度计算公式。
塔板塔顶气体速度是精馏塔操作中需要关注的参数之一。
塔板塔顶气体速度的计算公式如下:V = Q / A。
其中,V表示塔板塔顶气体速度,Q表示气体流量,A表示塔板横截面积。
总结。
精馏塔是一种重要的分离设备,其性能和操作参数需要通过计算和分析来进行评估和控制。
本文介绍了精馏塔的传质效率、塔板压降、塔顶温度、塔板液体高度和塔板塔顶气体速度的计算公式,希望能对读者有所帮助。
当然,精馏塔的计算和分析涉及到更多的参数和复杂的情况,需要结合具体的工程实际情况进行综合分析和计算。
精馏塔塔径与塔高计算

Z
NT HT ET
其中:Z —板式塔有效高度(传质段),m NT —理论塔板数(不包括塔釜) HT —塔板间距(经验值:见P344表8—2) ET —全塔效率(<1,实测)
应掌握:1. 全塔操作线绘制 2. 图解法求NT 3. Rmin(图解法、解析法) 4. Z的计算
附二:理论板 数的求解思路
5)最小回流比的计算 — 操作参数
根据: y R x 1 x n 1 n P R 1 R 1 其中:R= L / P 当系统处于全回流状态时 R=∞。 精馏段操作线为y=x(斜率最大、截距为零) 理论塔板数NT=NTmin。 当系统处于R=Rmin状态(斜率最小、截距 最大)时,精馏段操作线、加料线(q 线)、 相平衡方程线交汇于同一点(x=xq、y=yq ) 理论塔板数NT→∞。即方程满足:
对精馏段第一块板有 y1=xP ①点: 精馏段第一块板上发生的气液 相平衡关系: 气相组成y1 液相组成x1 ②点: 精馏段第一块板下降液与第二 块板上升气的操作组成关系: 气相组成y2 液相组成x1 ③点: 加料板(提馏段第1块板)上发 生的气液相平衡关系: 气相组成y4=y’1 液相组成x4 =x’1 <xq 饱和液进料时:xq=xF ④点: 提馏段第1块板下降液与第2块 板上升气的操作组成关系: 气相组成y’2 液相组成x’1 ⑤点: 提馏段第2块板发生的气液相平 衡关系: 气相组成y’2 液相组成x’2 ⑥ 点: 塔釜(提馏段最后1块板)里发 生的气液相平衡关系: 气相组成y’4=y’釜 液相组成x’4 <x釜
而 实际操作中的回流比: R=(1.1~2) Rmin. R↑:斜率↑、板数↓(分离效率↑) 、设 备造价↓、产品↓。 R↓:则与上述相反
yF
xF 1 ( 1) xF
精馏塔理论塔板数计算
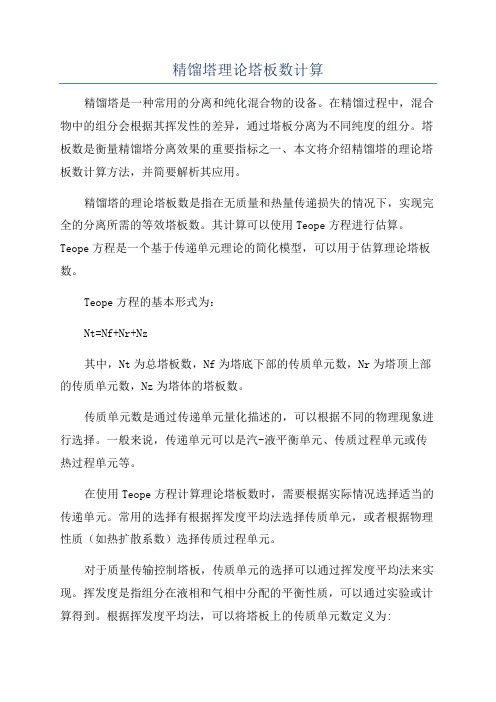
精馏塔理论塔板数计算精馏塔是一种常用的分离和纯化混合物的设备。
在精馏过程中,混合物中的组分会根据其挥发性的差异,通过塔板分离为不同纯度的组分。
塔板数是衡量精馏塔分离效果的重要指标之一、本文将介绍精馏塔的理论塔板数计算方法,并简要解析其应用。
精馏塔的理论塔板数是指在无质量和热量传递损失的情况下,实现完全的分离所需的等效塔板数。
其计算可以使用Teope方程进行估算。
Teope方程是一个基于传递单元理论的简化模型,可以用于估算理论塔板数。
Teope方程的基本形式为:Nt=Nf+Nr+Nz其中,Nt为总塔板数,Nf为塔底下部的传质单元数,Nr为塔顶上部的传质单元数,Nz为塔体的塔板数。
传质单元数是通过传递单元量化描述的,可以根据不同的物理现象进行选择。
一般来说,传递单元可以是汽-液平衡单元、传质过程单元或传热过程单元等。
在使用Teope方程计算理论塔板数时,需要根据实际情况选择适当的传递单元。
常用的选择有根据挥发度平均法选择传质单元,或者根据物理性质(如热扩散系数)选择传质过程单元。
对于质量传输控制塔板,传质单元的选择可以通过挥发度平均法来实现。
挥发度是指组分在液相和气相中分配的平衡性质,可以通过实验或计算得到。
根据挥发度平均法,可以将塔板上的传质单元数定义为:Nf = ΔHF / ln(αi)其中,ΔHF为进料组分的化学势差,αi为塔底和塔顶组分浓度的挥发度比。
对于能量传输控制塔板,传热过程单元的选择可以使用传热系数的平均法。
传热系数是描述传热过程的性质,可以根据传热模型或实验来确定。
传热过程单元的计算可以使用下式:Nr=ΔHR/(KlA)其中,ΔHR为进料组分的焓差,Kl为液相传热系数,A为塔板有效面积。
总的塔板数Nt的计算可以通过对Nf、Nr和Nz进行求和得到。
需要注意的是,由于Teope方程是一个估算模型,其计算结果只能作为初步参考,并不能完全准确地预测塔板数。
精馏塔的理论塔板数计算是精馏塔设计的重要一步。
- 1、下载文档前请自行甄别文档内容的完整性,平台不提供额外的编辑、内容补充、找答案等附加服务。
- 2、"仅部分预览"的文档,不可在线预览部分如存在完整性等问题,可反馈申请退款(可完整预览的文档不适用该条件!)。
- 3、如文档侵犯您的权益,请联系客服反馈,我们会尽快为您处理(人工客服工作时间:9:00-18:30)。
4.3 塔设备设计4.3.1 概述在化工、石油化工及炼油中,由于炼油工艺和化工生产工艺过程的不同,以及操作条件的不同,塔设备内部结构形式和材料也不同。
塔设备的工艺性能,对整个装置的产品产量、质量、生产能力和消耗定额,以及“三废”处理和环境保护等各个方面,都用重大的影响。
在石油炼厂和化工生产装置中,塔设备的投资费用占整个工艺设备费用的25.93%。
塔设备所耗用的钢材料重量在各类工艺设备中所占的比例也较多,例如在年产250万吨常压减压炼油装置中耗用的钢材重量占62.4%,在年产60-120万吨催化裂化装置中占48.9%。
因此,塔设备的设计和研究,对石油、化工等工业的发展起着重要的作用。
本项目以正丁醇精馏塔的为例进行设计。
4.3.2 塔型的选择塔主要有板式塔和填料塔两种,它们都可以用作蒸馏和吸收等气液传质过程,但两者各有优缺点,要根据具体情况选择。
a.板式塔。
塔内装有一定数量的塔盘,是气液接触和传质的基本构件;属逐级(板)接触的气液传质设备;气体自塔底向上以鼓泡或喷射的形式穿过塔板上的液层,使气液相密切接触而进行传质与传热;两相的组分浓度呈阶梯式变化。
b.填料塔。
塔内装有一定高度的填料,是气液接触和传质的基本构件;属微分接触型气液传质设备;液体在填料表面呈膜状自上而下流动;气体呈连续相自下而上与液体作逆流流动,并进行气液两相的传质和传热;两相的组分浓度或温度沿塔高连续变化。
4.3.2.1 填料塔与板式塔的比较:表4-2 填料塔与板式塔的比较4.3.2.2 塔型选择一般原则:选择时应考虑的因素有:物料性质、操作条件、塔设备性能及塔的制造、安装、运转、维修等。
(1)下列情况优先选用填料塔:a.在分离程度要求高的情况下,因某些新型填料具有很高的传质效率,故可采用新型填料以降低塔的高度;b.对于热敏性物料的蒸馏分离,因新型填料的持液量较小,压降小,故可优先选择真空操作下的填料塔;c.具有腐蚀性的物料,可选用填料塔。
因为填料塔可采用非金属材料,如陶瓷、塑料等;d.容易发泡的物料,宜选用填料塔。
(2)下列情况优先选用板式塔:a.塔内液体滞液量较大,操作负荷变化范围较宽,对进料浓度变化要求不敏感,操作易于稳定;b.液相负荷较小;c.含固体颗粒,容易结垢,有结晶的物料,因为板式塔可选用液流通道较大的塔板,堵塞的危险较小;d.在操作过程中伴随有放热或需要加热的物料,需要在塔内设置内部换热组件,如加热盘管,需要多个进料口或多个侧线出料口。
这是因为一方面板式塔的结构上容易实现,此外,塔板上有较多的滞液以便与加热或冷却管进行有效地传热;e.在较高压力下操作的蒸馏塔仍多采用板式塔。
综合考虑,本项目采用板式塔。
4.3.3 塔盘的类型与选择4.3.3.1 板式塔塔板种类:根据塔板上气、液两相的相对流动状态,板式塔分为穿流式和溢流式。
目前板式塔大多采用溢流式塔板。
穿流式塔板操作不稳定,很少使用。
4.3.3.2 各种塔盘性能比较:工业上需分离的物料及其操作条件多种多样,为了适应各种不同的操作要求,迄今已开发和使用的塔板类型繁多。
这些塔板各有各的特点和使用体系,现将几种主要塔板的性能比较列表如下:表4-3 几种主要塔板的性能比较下表给出了几种主要塔板性能的量化比较表4-4 几种主要塔板性能的量化比较从以上各图可以看出:浮阀塔在蒸汽负荷、操作弹性、效率和价格等方面都比泡罩塔优越,结合本项目实际情况,初步选择浮阀塔。
浮阀塔的工艺尺寸计算提取Aspen plus各塔板上的物性参数,选取塔板上气液相负荷最大的第3块塔板进行手工计算和校核,然后再用KG-TOWER进行软件计算,通过比较来检查计算的正确性。
第3块物性参数如下表:表4-5 浮阀塔塔板参数气相流液相流气相密度液相密度混合液表面7.85 0.0333.045726.0330.0071.塔径计算 初选塔板间距mm H 800=板上液层高度mm h L 100=m h H L T 7.0=-气液两相流动参数:0.0653.045726.03384986.703306.05.05.0V L =⎪⎭⎫ ⎝⎛=⎪⎪⎪⎭⎫ ⎝⎛ρρs s V L查史密斯关联图图4.1 史密斯关联图可查得:14.020=C矫正到表面张力为0.00699157N/m 时134.020919.1514.020σ2.02.020=⎪⎭⎫⎝⎛⨯=⎪⎭⎫⎝⎛=C C泛点气速s m cu f /065.23.045045.3003.267134.0-V V L =-⨯==ρρρ 为避免雾沫夹带及液泛的发生,一般情况,f u u )8.0~6.0('=在此取安全系数0.7,s m u u f /45.1065.257.07.0'=⨯=⨯= 流通截面积243.545.184986.7''m u V A s ===由《化工原理》(朱家骅编制)表11.3选取塔板上的液体流动方式 本次设计选择双溢流弓形降液管,一般双溢流型7.0~5.0=D l w此处取0.7wl D= 由《化工原理》(朱家骅编制)图11.19查弓形降液管的参数,如下图088.0=TfA A 所以96.5912.043.5088.01'==-=A A Tm A D T75.296.544=⨯==ππ图4.2 弓形降液管参数图精馏段的塔径圆整为2.8m ,由《化工原理》(朱家骅编制)表11-2校核。
对应板间距范围为≥800mm ,故满足条件,假设成立。
实际塔载面积22955.54/m D A T ==π 实际空塔气速s m D V u s /275.175.214.385.744'22=⨯⨯==π 2.溢流装置 弓形降液管:0.7wl D =故堰长96.18.27.0=⨯=w l降液管面积2524.0955.609.099.0m A A T f =⨯==由《化工原理》(朱家骅编制)图11.19弓形降液管的参数图 查得148.0=DW d故降液管宽度m W d 481.08.2148.0=⨯=为降低气泡夹带,液体在降液管内应有足够的停留时间以使气体从液相中分离出,一般要求τ不应小于3~5s ,而对于高压下操作的塔以及易起泡的物系,停留时间应更长些,为此,必须进行校核。
液体在降液管中停留时间:s s L H A s T f 56.21033147.08.0245.0>=⨯=⋅=τ 故降液管尺寸适宜。
溢流堰 取0.1L h m =则19.2296.133.119)(5.25.2==w h l L图4.3 液体收缩系数计算图由《化工原理》(朱家骅编制)图11.20液体收缩系数计算图查得:30.1=E由弗朗西斯公式,堰上液层高度m l L E h w s ow 232231053.41.9633.11930.100284.0100084.2-⨯=⎪⎭⎫ ⎝⎛⨯⨯=⎪⎭⎫ ⎝⎛⋅=堰高0547.00453.01.0=-=-=ow L w h h h 受液盘和底隙:塔板上接受降液管流下液体的那部分区域称为受液盘,常用平形型式。
为减小液体流动阻力和考虑到固体杂质可能在底隙处沉积,所以h 不可过小。
但若h 过大,气体又可能通过底隙窜入降液管,故底隙宜小些以保证液封。
取0.15/OL m s u = 则m u lw Ls h OL 113.015.096.1033147.00=⨯=⋅=塔板布置a.受液区和降液区:一般这两个区域的面积相等,均可按降液管截面积f A 计。
b.边缘区:在塔壁边缘留出一定宽度的环形区域供固定塔板用。
c.入口安定区和出口安定区,通常宽度相等。
d.有效传质区:余下的塔板上有浮阀孔的区域。
于此处考虑:塔径900D mm >,采用分块组装式; 边缘宽度取500.05c W mm m ==; 安定区宽度均取0.08s W m =; 降液管宽0.3d W m =4.3.4 浮阀数目N 及孔间距F1重型浮阀阀孔直径00.039d m =。
取120=F 。
阀孔气速s m F u v/88.6045.3120===ρ 每层塔板浮阀数6.95588.6039.043600/5086.2825942020=⨯⨯=⨯=ππu d VsN圆整为956=N浮阀排列:采用等腰三角形叉排。
由上一小节所假设,鼓泡区面积为⎥⎦⎤⎢⎣⎡⎪⎭⎫ ⎝⎛+-+⎥⎦⎤⎢⎣⎡⎪⎭⎫ ⎝⎛+-=--r x r x r x r x r x r x A a 12221222sin 180'sin 180''ππ 其中m W W D x x s d 9056.008.0.4144022.82'=--=--== m W D r c 35.105.022.82=-=-=故49.4)35.19056.0(sin 35.11809056.025.19056.021222=⎥⎦⎤⎢⎣⎡⨯⨯+⨯⨯⨯=-πa A0.075t m =取 则0626.0075.095649.4'=⨯=⋅=t N A t a 由于塔直径D=2.8m ,采用分块式塔板四块(其中两块弓形板、通道板和矩形板各一块)。
0626m .0t 、075.0='=m t以等腰三角形交叉方式绘图排列如图所示:图4.4 塔板内部结构图由排布图可得实际的开孔数950个sm N d V u s /6.92950039.04849.74220=⨯⨯==ππ07.12045.392.600=⨯==V u F ρ 在适宜范围8-12内 塔板开孔率%4.88.2039.0950%100220=⎪⎪⎭⎫ ⎝⎛⨯=⨯⎪⎪⎭⎫ ⎝⎛=D d N φ1.塔板的流体力学校核 塔板压降校核:1f d h h h =+ a 、干板阻力 阀全开前0()oc u u <:L d u h ρ175.009.19=阀全开后0()oc u u >:g u h L V d ρρ234.520⋅=临界速度s m u Voc /71.5045.35.105.10825.11825.11===ρ有oc u u >0故054.081.9033.726288.6045.334.5234.522=⨯⨯⨯⨯=⋅⋅=g u h L o v d ρρb 、板上充气液层阻力0.6β=取m h h h ow w 60.01.06.0)(1=⨯=+=βm h h h d f 114.0540.060.01=+=+=故塔板压降为Pa gh P f L 9.118114.081.9033.726=⨯⨯==∆ρ满足要求。
液沫夹带的校核:因塔径D>900mm,应控制泛点率不超过80%。
由3/045.3m Kg v =ρ及m H T 6.0=查《化工原理》(朱家骅编制)图11.22泛点负荷因子图:图4.5 泛点负荷因子图得C F =0.15,并查物性系数表得K=1%80%1.73%10096.50.1578.03600045.303.7263.0455086.28259%10078.01<=⨯⨯⨯⨯-⨯=⨯-=FT VL V sKC A V F ρρρ满足上述条件,不会发生过量雾沫夹带。