模具圆筒件翻边、冲孔模设计
圆筒形件翻孔冲压模设计

的形 件 翻孔 冲 J 馍 设{‘ 』 i f
圆筒 形 件 翻 孑 冲 压 模 设 计 L
姚 建 平 王 翠 芳
( . 西 省 化 3学 校 南 昌 3 0 1 ; 西 旅 游 商 贸学 院 南 昌 30 0 ) 1江 2 30 2 江 3 10
I :
;
图 3 工 件 示 意 图 4 模 具 主 要零 件设 计要 点
图 4 工 件 示 意 图
压 平凸模与压弯 凸模 采取 H / 6的间 隙配合 , 7h 为 保 正导 向 , 导套与导柱 的间隙要小 , 在开模过程 中尽量
不分离。其 中压 弯凸模结构如 图 5所示。
5~支承板 1 一导套 1
6一凸模 固定板
1 2一下模 座
9一压弯 凸模
16一滑动凹模
1 7~凹模 滑套
3 模 具 工 作 过 程
模具 工作时 , 上模座带 动压平 凸模 7与压弯 凸模 9 ( 即可滑动凸模 ) 一起 下行 , 压弯 凸模接触 工作后 , 弹 在
上模座继续 下 行 时 , 弯 凸模 9在压 平 凸模 7中 压 滑动 , 直到被限位 圆柱销 1 0挡住 。压 平 凸模 则继续 下
行 , 翻孔 压 平 。如 图 4所 示 。 将
簧力作用 下 , 将工件 预压 为喇叭 口形状 , 图 3所示 。 如
维普资讯
28 2
2 0 第 4期 0 7年
: f / // /
1.J / , / ,
l J ’ 一
I
图 5 压 弯 凸模 5 结 束 语
参考文献
经生产 , 此模具 冲压 出的零 件符合 图纸要 求 , 结构 简单 、 合理 , 易于维修。这种 模具结构 不仅适 用于外 翻
冲压模具毕业设计 翻边模的设计

基本内容及拟解决的主要问题:
1)设计落料模具
2)设计液压拉深模具
3)设计翻边模具
4)设计卷边模具
落料模具的设计主要是为了得到圆形板料的设计,根据逆向设计和理论要求,确定圆形板料的尺寸,根据圆形板料的尺寸来设计落料模具。在落料模设计的过程中,对板料的利用率进行计算,使其符合经济实用的要求[4]。在对落料模的设计中,根据其它相关类似模具的设计,落料模设计成通用的落料模结构。同时对落料冲压力进行计算来选择相对应的压力机。根据设计的数据,利用Solidworks软件画出三维模型。
Analysis of the complexity of the shade of such a shape, thin-walled parts of the structural characteristics.Easy for die-casting in the formation of cracks, lack of defects in the tensile properties of the process, and in accordance with the requirements of theoretical analysis and data based on the use of Solidworks 3D solid modeling software, and the provisions of unknown size. Then calculated using the three-dimensional entities, the quality of parts, in accordance with Solidworks software to design parts of the quality of the target plate thickness the diameter of the circular blank. According to the original blank diameter to determine the number of dimensions for the design and follow-up to provide a basis for research. At the same time, the use of Solidworks software or other three-dimensional software model of the stamping feasibility analysis and design, use of software related to shade Mold mold design.
拉深、翻边、切边和冲底孔复合模具设计

Co mp o s i t e Di e De s i g n o f De e p Dr a wi ng Fl a n g i ng Tr i mmi ng a n d Pu n c h i ng Bo t t o m Ho l e
某 产 品的 1个 盒形 零 件 结 构 简 图如 图 1所 示 , 材料 为 0 8 F钢 板 , 厚度为 1 . 2 mm。图 1中未 标 注 的尺 寸公 差 等级 为 I T1 2 级, 生 产批 量 为 5 万件 。
LI S u l i , J I A Ba o q i n
( Sha a nx i i ns t i t ut e of t e c hn ol o gy, Xi ’ a n 71 0 30 2,Chi na ) Ab s t r a c t:A c c or di ng t o t he s t r uc t u r e f e a t ur e s a n d t e c hni c a l r e q ui r e me n t s of pa r t s, f o c us i n g on how t o r e d uc e t h e pr o d uc t i on c os t ,i m pr ov e wor k e f f i c i e nc y a n d s i mp l i f y t he mo ul d s t r u c t ur e ,t hr o ug h a va r i e t y o f p r o c e s s s c h e me c om p a r i s o n,f i — n al l y, l i ne a r c u t t i n g s h e a r ma t e r i a l t o l o c a t e p l a t e l o c a t i on d e e p dr a wi ng,f l a ng i n g, t r i mmi ng, pun c hi ng b ot t o m ho l e we r e s y nt he t i c a l l y us e d a s pu nc h i n g pr oc e s s s c h e m e,a l l pr oc e s s e s we r e c a l c u l a t e d,a n d d e t a i l e d de s i g n o f a p a i r of d e e p dr a wi ng, f l a n gi ng,t r i mmi ng,pu nc hi ng bot t o m ho l e c om po s i t e di e s t r u c t u r e we r e d i d, a nd t h e p r o c e s s s c he me a nd t he d i e s t r uc t ur e we r e i l l u s t r a t e d, whi c h o bv i o us l y i m pr ov e d t he box pa r t s pr od uc t i on e f f i c i e nc y a nd p r odu c t s q ua l i t y . Ke y wo r d s:dr a wi ng,f l a n gi ng,t r i mmi ng,i mp a c t bo t t om h ol e s, moul d d e s i gn
冲孔加翻边一体具设计

冲孔加翻边钣金模具设计
设计的零件冲压成型模样图如下:
技术要求:
1:为标公差尺寸按QB/JU01.001-2006
2: 未注折弯内径R0.3,为注圆角R0.5。
3:零件外表要求平整,五凹坑,无擦伤,无划伤
4:落料,冲孔毛刺高度小于0.1MM,方向朝内部,边缘毛刺不允许有挂,划手现象。
5:直径2.5的翻边孔允许有不影响使用的梅花裂纹。
6:该零件的成型模借用后面板《JUW8.041.00005762》,冲孔改变。
注:是已做的钣金模具
模具的总装主视图如上。
模具的总装俯视图如上。
下面就是我所设计模具的选材和加工,主要是针对模版以至于冲孔的小件就不多讲。
根据模具总的组装主
视图一次往下设计。
下面所有的图都是CAD-2007版本上截图下来的
上模座加工要求如下。
这个是上托板我们也俗称它叫上模座作用:模具的基座,所有的钣都紧紧固定在模座上,模具装夹到冲压机上。
通常都是装夹模座。
我们选择的材料是45钢(注:上下模座都用45号钢,下模座就不说选材问题)。
选择45钢的原因有两点:1:在价格方面比较便宜而且上模座厚度一般比较厚。
(注:我现在设计的模具上模座厚度达到35MM,我在钣金模具厂见过最厚的上模座达到55MM)
2:45号钢为优质碳素结构用钢,硬度不宜用来且削加工,模具中常用来做模版。
圆形零件侧壁冲孔模具结构设计
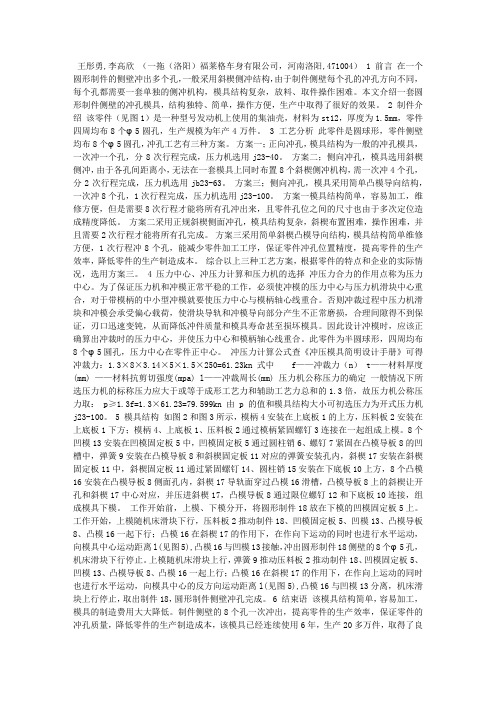
王彤勇,李高欣(一拖(洛阳)福莱格车身有限公司,河南洛阳,471004) 1 前言在一个圆形制件的侧壁冲出多个孔,一般采用斜楔侧冲结构,由于制件侧壁每个孔的冲孔方向不同,每个孔都需要一套单独的侧冲机构,模具结构复杂,放料、取件操作困难。
本文介绍一套圆形制件侧壁的冲孔模具,结构独特、简单,操作方便,生产中取得了很好的效果。
2 制件介绍该零件(见图1)是一种型号发动机上使用的集油壳,材料为st12,厚度为1.5mm,零件四周均布8个φ5圆孔,生产规模为年产4万件。
3 工艺分析此零件是圆球形,零件侧壁均布8个φ5圆孔,冲孔工艺有三种方案。
方案一;正向冲孔,模具结构为一般的冲孔模具,一次冲一个孔,分8次行程完成,压力机选用j23-40。
方案二;侧向冲孔,模具选用斜楔侧冲,由于各孔间距离小,无法在一套模具上同时布置8个斜楔侧冲机构,需一次冲4个孔,分2次行程完成,压力机选用jb23-63。
方案三;侧向冲孔,模具采用简单凸模导向结构,一次冲8个孔,1次行程完成,压力机选用j23-100。
方案一模具结构简单,容易加工,维修方便,但是需要8次行程才能将所有孔冲出来,且零件孔位之间的尺寸也由于多次定位造成精度降低。
方案二采用正规斜楔侧面冲孔,模具结构复杂,斜楔布置困难,操作困难,并且需要2次行程才能将所有孔完成。
方案三采用简单斜楔凸模导向结构,模具结构简单维修方便,1次行程冲8个孔,能减少零件加工工序,保证零件冲孔位置精度,提高零件的生产效率,降低零件的生产制造成本。
综合以上三种工艺方案,根据零件的特点和企业的实际情况,选用方案三。
4 压力中心、冲压力计算和压力机的选择冲压力合力的作用点称为压力中心。
为了保证压力机和冲模正常平稳的工作,必须使冲模的压力中心与压力机滑块中心重合,对于带模柄的中小型冲模就要使压力中心与模柄轴心线重合。
否则冲裁过程中压力机滑块和冲模会承受偏心载荷,使滑块导轨和冲模导向部分产生不正常磨损,合理间隙得不到保证,刃口迅速变钝,从而降低冲件质量和模具寿命甚至损坏模具。
圆形板件冲孔模设计说明书
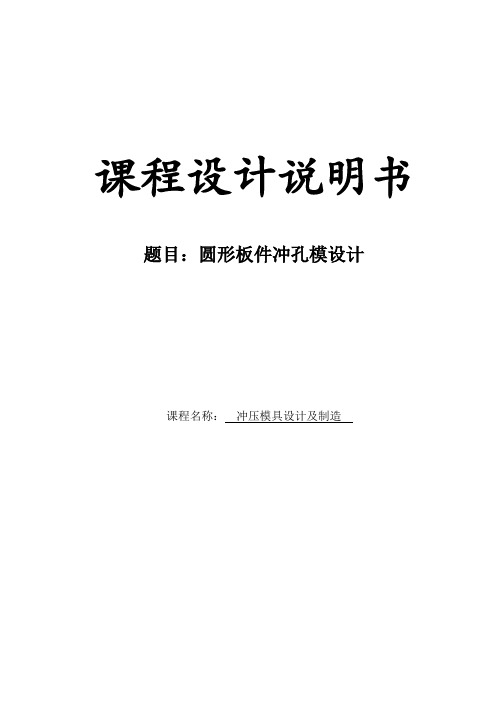
课程设计说明书题目:圆形板件冲孔模设计课程名称:冲压模具设计及制造目录一、课程设计目的 (1)二、工件简图 (2)三、工艺分析 (2)3.1工件材料 (2)2.2工件结构形状 (2)2.3工件尺寸精度 (3)2.4工艺方案选择 (3)四、工艺计算 (5)4.1冲裁力的计算 (5)4.2工作零件刃口尺寸计算 (5)4.3凹模结构厚度H计算 (6)4.4选定标准模架 (7)4.5凸模长度计算 (7)4.6橡胶计算 (7)五、设备选择 (8)六、装配图及零件图绘制 (8)七、参考文献 (9)一、课程设计目的冲压工艺设计主要包括冲压件的工艺性分析和冲压工艺方案的确定两个方面的内容。
良好的工艺性和合理的工艺方案,可以用最小的材料消耗,最少的工序数量和工时,稳定地获得符合要求的优质产品,并使模具结构简单,模具寿命高,因而可以减少劳动量和冲裁成本。
冲裁件的工艺性是指冲裁件对冲裁工艺的适应性,一般情况下,对冲裁件工艺性影响较大的是制件的结构形状、精度要求、形位公差及技术要求等。
冲压件的工艺性合理与否,影响到冲压件的质量、模具寿命、材料消耗、生产效率等,设计中应尽可能提高其工艺性。
课程设计是将大学课本上所学的课程知识、理论联系实际,提高分析、解决问题的能力的一种形式。
通过对具体产品的分析、计算,设计出一套合理的模具,使我们对于模具设计的理念更加深刻,也巩固了课上所学的专业知识,对以后工作奠定了基础,工艺与模具设计能力是材料成型及控制工程专业学生所必备的工程技术能力。
课程设计是教学大纲的必修课,也是锻炼学生加强工艺与模具设计能力的的重要教学环节。
二、工件简图材料为Q235钢,板厚为t=1.5mm,生产批量:大批量。
三、工艺分析3.1工件材料由图分析知:Q235为钢优质金属材料,具有良好的塑性,及压力加工性能。
适合冲裁加工。
3.2工件结构形状工件结构形状相对简单,只有一个圆孔。
料厚为1.5mm满足许用壁厚要求(孔与孔之间、孔与边缘之间的壁厚),可以冲裁加工。
毕业设计(论文)-圆筒件冲压模具设计

南充职业技术学院毕业设计说明书题目: 圆筒件冲压模具设计系部: 机电工程系专业: 模具设计与制造年级: 2004级三普模具班指导老师:学生姓名:学号:2006年12月6日目录1. 前言 (2)2. 分析冲压件的工艺性 (2)2.1零件冲裁件工艺性分析 (2)2.2零件拉深工艺性分析 (4)2.3材料分析及其机械性能 (5)3. 计算毛坯展开尺寸 (6)4. 排样及裁板方式的经济,并计算材料利用率性分析 (6)4.1. 材料的利用率 (6)4.2. 排料方式和材料的经济利用率 (7)4.3. 根据材料利用率选择裁板方式 (8)5. 工序次数的确定 (9)6. 确定工艺方案并对工艺方案的技术、经济综合分析比较 (10)7. 确定各工序模具结构型式 (11)7.1设计落料、拉深件复合模 (11)7.2导向装置 (15)7.3固定与连接零件 (16)8.选定模具结构型式的合理性分析 (17)9. 凸、凹模工作部分尺寸、公差的计算 (17)10.冲压工艺卡 (18)总结与体会 (19)致谢词 (19)参考文献 (20)1.前言本次冲压模具的设计,主要是设计圆角冲压模具,其中包括了模具的设计步骤、计算方法,零件图及装配图等内容,充分体现了清晰的设计思路,合理的安排布局,严格按照相关标准选取设计所需资料,保证了设计的准确性,但其中仍有不足及错误,有待改进。
本次设计的主要目的是熟悉设计模具的基本步骤和将理论知识与实际联系在一起,使我们在以后工作中能更好地设计模具。
2.分析冲压件的工艺性根据产品图样,分析冲压件的形状特点、尺寸大小、精度要求及所用材料的性能等是否符合冲压工艺的要求。
良好的冲压工艺性应保证材料消耗少、工序数目少、占用设备数量小、模具结构简单而寿命高、产品质量稳定以及操作简单方便等。
在分析审查中若发现冲压件的工艺性差,则应会同设计人员,在保证产品使用要求的前提下,对冲压件的形状、尺寸、精度要求乃至选材进行必要的修改。
如何设计一套圆管双头冲孔与翻孔模具
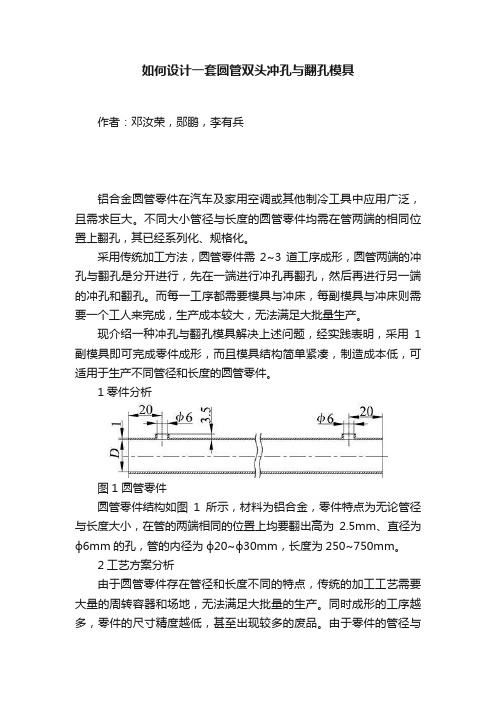
如何设计一套圆管双头冲孔与翻孔模具作者:邓汝荣,郧鹏,李有兵铝合金圆管零件在汽车及家用空调或其他制冷工具中应用广泛,且需求巨大。
不同大小管径与长度的圆管零件均需在管两端的相同位置上翻孔,其已经系列化、规格化。
采用传统加工方法,圆管零件需2~3道工序成形,圆管两端的冲孔与翻孔是分开进行,先在一端进行冲孔再翻孔,然后再进行另一端的冲孔和翻孔。
而每一工序都需要模具与冲床,每副模具与冲床则需要一个工人来完成,生产成本较大,无法满足大批量生产。
现介绍一种冲孔与翻孔模具解决上述问题,经实践表明,采用1副模具即可完成零件成形,而且模具结构简单紧凑,制造成本低,可适用于生产不同管径和长度的圆管零件。
1零件分析图1 圆管零件圆管零件结构如图1所示,材料为铝合金,零件特点为无论管径与长度大小,在管的两端相同的位置上均要翻出高为2.5mm、直径为ϕ6mm的孔,管的内径为ϕ20~ϕ30mm,长度为250~750mm。
2工艺方案分析由于圆管零件存在管径和长度不同的特点,传统的加工工艺需要大量的周转容器和场地,无法满足大批量的生产。
同时成形的工序越多,零件的尺寸精度越低,甚至出现较多的废品。
由于零件的管径与长度不同,需要不同的模具与之相适应,模具通用性低、互换性差,需要的模具数量多,生产成本大,不便于管理。
面对零件批量大、劳动力成本不断上涨的市场环境,传统的加工方法已不适应当前生产。
通过对不同的管径和长度系列的模具进行优化后,采用1副模具则可生产任何规格的圆管零件,大幅度减少了模具制造成本,提高了生产效率,并提高了零件的成形尺寸精度。
3成形过程与工作原理图2 模具结构1.连接螺母2.推板3.限位安全块4.压板5.上模板6.模柄7.凸模固定板8.冲孔凸模9.上卸料板 10.导柱导套 11.导向杆 12.右导向杆支承块 13.螺钉 14.限位块 15.底座 16.锁紧块 17.凸凹模固定板 18.下卸料板 19.弹簧 20.螺钉 21.螺钉 22.弹簧 23.托料板 24.螺钉 25.下模板 26.凸凹模 27.气缸 28.左导向杆支承块 29.螺钉 30.调节块 31.弹簧1模具结构如图2所示。
冲压模具毕业设计翻边模设计

刃口尺寸的调整方法:根据冲压件的尺寸和形状,以及冲压机的压力和速度,进行适当的调整
刃口尺寸的确定注意事项:刃口尺寸的确定要符合冲压件的尺寸和形状,以及冲压机的压力和速度,以保证冲压件的质量和生产效率。
刃口尺寸的确定原则:根据冲压件的尺寸和形状,以及冲压机的压力和速度来确定
刃口尺寸的计算方法:根据冲压件的尺寸和形状,以及冲压机的压力和速度,利用公式进行计算
材料处理:对材料进行热处理、表面处理等,提高材料的耐磨性、耐腐蚀性和抗疲劳性
翻边模的工艺参数设计
PART FIVE
冲压工艺方案的确定
确定冲压工艺方案的目的:提高生产效率,降低成本,保证产品质量
冲压工艺方案的选择:根据产品形状、尺寸、材料等因素选择合适的冲压工艺方案
冲压工艺方案的设计:包括模具设计、冲压设备选择、冲压工艺参数设定等
退火:将模具材料加热到一定温度后保温一定时间,消除应力,提高塑性和韧性
调质:将模具材料加热到一定温度后保温一定时间,然后冷却,提高硬度和韧性
渗碳:将模具材料加热到一定温度后渗入碳元素,提高表面硬度和耐磨性
模具材料的选用原则
材料强度:应满足模具的使用寿命要求
材料硬度:应与冲压件的硬度相匹配
材料耐磨性:应具有良好的耐磨性,减少磨损
冲压工艺方案的优化:根据生产实际情况,对冲压工艺方案进行优化和改进,以提高生产效率和产品质量。
冲裁间隙的确定
冲裁间隙的定义:冲裁过程中,冲头和被冲材料之间的最小距离
冲裁间隙的确定方法:经验公式法、试验法、计算机模拟法等
冲裁间隙的确定原则:保证冲裁质量、提高生产效率、降低成本等
冲裁间隙的影响因素:材料性质、冲头形状、冲压速度等
寿命预测的重要性:合理预测模具寿命,有助于优化生产工艺,降低生产成本,提高产品质量。
圆筒件翻边模具设计

时 m=0 8 . ,查 工 具 书 得 知 低 碳 钢 极 限 翻 边 因数 为 0 6 ,小 于 .5
m,所 以零件可 以成形 ,方案可行。
巾2 O
可 :
2 0
12 毛 坯 尺 寸 计算 .
图 l) c所示零 件实际上是一种 平 口形扩 口件 。在参考文献
[】 ,依据 体积不变 条件和有关 几何关 系 ,推导 出了翻边件 3中
c m b n ton be we n a o i a i t e a f dng pu h a n a pl na i n pu h The di tuc u e s e s nd ha i s .t wilbe a oo x m pl o l nc nd a p a to nc . e s r t r i a y a nd ne s I l g d e a efra sm ia o d de i n. i l rm l sg Ke y wor :Fl n ng M o d f rt yl r pa t fa i un h;a l na i unc ds a【 gi l he c i r ; rng p c o de l pp a ton p h1 3 翻 边 Nhomakorabea计 算 .
翻 边 力 是 模 具 的 主 要 设 计 参 数 之 一 , 以 此 来 设 计 、 校 核 工 作 部 件 强 度 和 选 择 冲 压 设 备 。 圆 筒 零 件 最 大 翻 边 力 的 计 算
公式为 :
限位 圆柱l一方面用来限制扩 1凸模9 5 : 1 的行程下限,另一方
圆 筒 件 翻 边 模 具 设 计
张骞 田福祥 ( 青岛 理工 大 学 , 东青 岛 , 6 0 3 山 263)
摘
翻孔翻边模设计
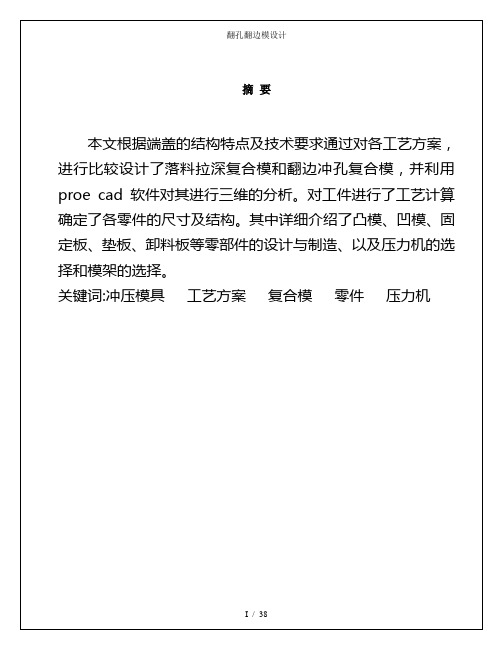
第2章产品工艺分析以及工艺方案的确定产品介绍材料:08 板厚:1mm 生产纲领:10万件/年尺寸如图所示课题介绍本次课题主要是分析该产品的工艺性,绘制产品的三维图,在多种工艺方案中选择其最优冲压工艺方案,然后进行工艺计算、确定其模具结构并设计其模具。
2.1 产品冲压工艺性分析冲压工艺设计主要包括冲压件的工艺性分析和冲压工艺方案的确定两个方面的内容。
良好的工艺性和合理的工艺方案可以用最小的材料消耗最少的工序数量和工时稳定地获得符合要求的优质产品并使模具结构简单模具寿命高因而可以减少劳动量和冲裁成本。
2.2工艺方案确定1)方案只有一种该工件包括折弯、压平1.折弯——压平1定位套2.凸轮把手3盖板.3.3.3压力机的选择压力机型号的确定主要取决于冲压工艺的要求和冲模结构情况,结合已求得的两幅模具的总压力F1=418KN,F2=311KN,查文献[1]表22.6-19选择公称压力F=630KN的开式压力机JB23—63和公称压力F=250KN 的开式压力机JB23—25。
装式特点。
冲孔废料由冲孔凸模冲入凹模洞口中,积聚到一定数量,由下模漏料孔排出,不必清除废料。
工件表面平直度较差,凸凹模承受张力较大。
但模具结构简单,操作方便。
经分析,此工件按IT14级加工制造,平直度要求较高,工件精度要求也较高。
所以从工件的加工精度考虑,采用正装复合模。
4.1.1翻孔翻边模工作零件的设计1.凹模(1)凹摸结构尺寸的确定。
凹模的刃口形式考虑到零件形状所以采用圆形刃口凹模。
凹模外形尺寸主要包括凹模厚度H凹模壁厚c凹模周径D0。
(2)凹模厚度的确定。
由模具结构得凹模厚度尺寸H=16mm。
(3)凹模壁厚的确定。
可取c=( 1.5~2)H=2mm。
(4)凹模周径的确定。
孔口尺寸b=40mm D=46mm查文献[1]表22.5-18材料选用T10A热处理淬火58~62HRC。
其结构与尺寸如图所示2.凸模凸模长度尺寸与凹模和凸模固定板的厚度有关。
深筒件的冲压工艺及模具设计
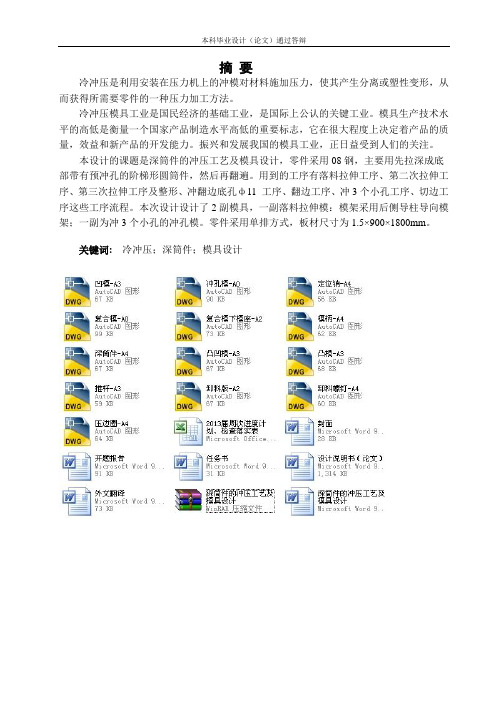
本科毕业设计(论文)通过答辩摘要冷冲压是利用安装在压力机上的冲模对材料施加压力,使其产生分离或塑性变形,从而获得所需要零件的一种压力加工方法。
冷冲压模具工业是国民经济的基础工业,是国际上公认的关键工业。
模具生产技术水平的高低是衡量一个国家产品制造水平高低的重要标志,它在很大程度上决定着产品的质量,效益和新产品的开发能力。
振兴和发展我国的模具工业,正日益受到人们的关注。
本设计的课题是深筒件的冲压工艺及模具设计,零件采用08钢,主要用先拉深成底部带有预冲孔的阶梯形圆筒件,然后再翻遍。
用到的工序有落料拉伸工序、第二次拉伸工序、第三次拉伸工序及整形、冲翻边底孔ф11 工序、翻边工序、冲3个小孔工序、切边工序这些工序流程。
本次设计设计了2副模具,一副落料拉伸模:模架采用后侧导柱导向模架;一副为冲3个小孔的冲孔模。
零件采用单排方式,板材尺寸为1.5×900×1800mm。
关键词: 冷冲压;深筒件;模具设计AbstractCold stamping is using presses installed in the die pressure on the material, make its produce a separation or plastic deformation, obtained from the required parts of a pressure processing method.Cold stamping die industry is the foundation of the national economy industry, is internationally recognized as one of the key industries. Mold production technology level of high and low is a measure of a national product manufacture level of important symbol, it largely determines the quality of products, and new product development capability. Revitalization and development of mould industry in China, are increasingly being people's attention.This design topic is Cold stamping technology and die design of tube parts, parts using 08 steel, mainly used to pull with pre punching deep into the bottom of the step cylinder, and then went through. Use process with blanking stretching process, the second stretching process, the t hird stretching process and plastic and flanging bottom hole ф 11 work procedure and three holes, flanging process, trimming process these processes. The two vice mould design design, a blanking tensile mold: mold frame with side guide column guide die set; A pair of blunt three holes of punching die. Parts adopt single method, board size is 1.5 * 900 * 1800 mm,Key words: cold stamping;tube pieces;the mold designII目录摘要 (I)ABSTRACT (II)目录........................................................................................................................................... I II 1 绪论. (1)1.1 本课题的研究内容和意义 (1)1.2国内外的发展概况 (1)1.3本课题应达到的要求 (2)2 深筒件的分析 (3)2.1深筒件的设计要求 (3)2.2深筒件的尺寸分析 (3)2.3深筒件材料的选用 (3)2.4深筒件圆孔加工计算 (3)2.5深筒件加工工艺的分析 (4)3 工艺方案的选择 (5)3.1毛坯直径计算 (5)3.1.1 翻边变形程度的计算 (5)3.1.2 深筒件翻边前半成品的尺寸计算 (5)3.1.3 深筒件毛坯直径的计算 (6)3.2拉伸次数计算 (6)3.3工序的组合和顺序的选定 (7)3.3.1 深筒件基本工序 (7)3.3.2 冲压方案选择 (7)3.3.3 方案比较 (11)4 深筒件数据计算 (12)4.1零件排样方式选择 (12)4.2板料尺寸的选择 (12)4.2.1 板料的利用率计算 (12)4.3材料消耗数据计算 (12)4.4各次拉伸是工件尺寸计算 (13)4.4.1 首次拉伸半成品尺寸 (13)4.4.2 二次拉深半成品尺寸 (14)4.4.3 第三次拉深半成品尺寸 (14)4.5工序的压力计算和压力机的选取 (15)4.5.1 落料拉深工序 (15)4.5.2 第二次拉深工序 (16)4.5.3 第三次拉深工序 (16)4.5.4 冲孔翻边工序 (17)4.5.5 翻边工序 (18)4.5.6 冲三个小孔工序 (18)4.5.7 切边工序 (19)5 深筒件的模具设计 (20)5.1落料拉深复合模 (20)5.1.1 模具结构形式 (20)5.1.2 卸料弹簧选取 (21)5.1.3 拉伸落料复合模模具相关尺寸设计 (21)5.2冲3个小孔模具设计 (24)6 结论与展望 (26)6.1结论 (26)6.2不足之处及未来展望 (26)致谢 (26)参考文献 (27)IV1 绪论1.1 本课题的研究内容和意义冷冲压是利用安装在印刷机上的材料上的压力的模具,以产生分离或塑性变形,从而获得所需的部分的压力加工方法。
模具翻边设计
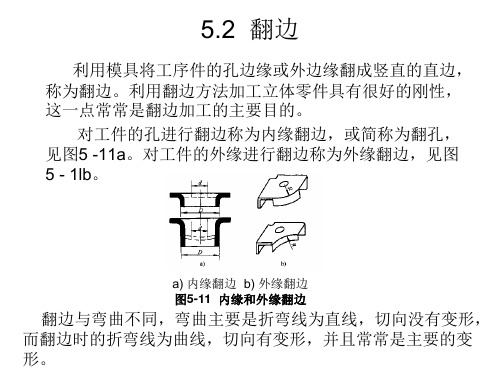
翻边与弯曲不同,弯曲主要是折弯线为直线,切向没有变形, 而翻边时的折弯线为曲线,切向有变形,并且常常是主要的变 形。
5.2 翻边
5.2.1内缘翻边 一、圆孔翻边 (一) 圆孔翻边的变形特点
图5-12 圆孔翻边应力状态
图5-13 圆孔翻边应力—应变分布
5.2 翻边
如图5-12所示, 翻边变形区切向受拉应力σ θ ,径向 受拉应力σ P,而板厚方向应力可忽略不计,因此应力状 态可视为双向受拉的平面应力状态。 圆孔翻边时,应力和切向应变的分布情况如图5-13所 示。切向应力σ θ 为最大主应力,径向应力σ P是由凸模对 板料的摩擦作用引起的,其值较小。应力沿径向的分布是 不均匀的,在底孔边缘处,切向应力σ θ 达到其最大值, 而径向应力σ P为零,因此该处可视为单向拉伸应力状态。 切向应变为拉应变,沿径向的分布也是不均匀的,在底孔 边缘处其值最大,越远离中心,其值越小。 可见,翻孔时底孔边缘受到强烈的拉伸作用。变形程 度过大时,在底孔边缘很容易出现裂口。因此翻孔的破坏 形式就是底孔边缘拉裂。为了防止出现裂纹,需限制翻孔 的变形程度。
0.5D(1 K f ) 0.57rp
(5-14) (5-15)
5.2 翻边
这时,底孔直径可由式(5-14)求得:
d 0 D 1.14rp 2h
(5-16)
注意:rp为拉深凸模半径,一般取rp≥2t 底孔直径也可按下式计算: d0=DKfmin (5-17) 最大翻边高度确定之后,便可按下式计算拉深工序 件的高度h1:h1=H-hmax+rp+t (5-18) 余下的问题便是进行拉深工艺计算。
5.2 翻边
4.翻边凸模的形状: 图5-12所示为用平头凸模翻边,当凸模圆角 半径rp较小时,变形过分集中于底孔边缘,容易 引起开裂。随着值的增大,直至采用球形、抛 物面形或锥形凸模,变形将得到分散,可减小 底孔边缘开裂的可能性,因而允许采用较小的 翻边系数。 表5-4给出了低碳钢的极限翻边系数Kfmin , 从中可以看出上述因素对其值的影响程度。
圆筒零件落料冲孔复合模设计

目录一、冲压件工艺过程设计 (2)1. 冲压件的工艺分析 (2)2、确定工艺方案及模具结构形式 .................... 错误!未定义书签。
3、零件的工艺过程 ............................................ 错误!未定义书签。
二、冲裁模具设计 (9)1、模具的设计计算 (9)(1)排样和计算条料宽度 .......................... 错误!未定义书签。
(2)计算总冲压力 ...................................... 错误!未定义书签。
(3)压力中心的计算 (8)(4)冲压设备的选择 (8)(5)主要工作部分尺寸计算 (9)( 6 ) 模具主要零件及结构设计 (10)三、参考资料 (12)Ⅰ、冲压件工艺过程设计工件名称:圆形深筒生产批量:中批量材料:08F厚度:2mm描述:圆筒类零件,底部中央有一个直径为10mm的圆孔。
一、零件的工艺分析1.1、材料08F,是优质碳素结构钢,塑性好、组织均匀、晶粒大小适当具有良好的拉深性能。
1.2、工件结构零件为圆筒类带孔拉深件,孔在底部并且不在拉深变形区,冲孔尺寸符合要求,零件的孔与孔和孔的边缘的距离同样符号要求。
1.3、尺寸精度零件图上尺寸属于IT14级。
一般冲压能满足精度要求。
结论:可以进行冲裁拉深加工。
二、确定工艺方案及模具结构形式从工件结构形状可知,工件成型所需的基本工序为冲孔、落料、拉深、切边四种。
其中冲孔、落料的方法可采用单工序模、复合模和级进模。
2.1、方案的提出方案一:采用复合模。
首先在复合模上同时完成冲孔落料复合工序,然后在拉深模上完成拉深。
方案二:采用单工序模。
首先在冲孔模上冲孔,然后落料,最后在拉深模上完成拉深。
方案三;采用连续模具。
首先在连续模具上完成冲孔和落料工序,然后在拉深模上完成拉深。
2.2、方案的比较方案一的优点是工序相对集中,需要用模具较少,压力机和操作人员的效力较高。
薄壁圆管冲孔模具设计

薄壁圆管冲孔模具设计1薄壁圆管冲孔模具设计初步构思按工艺流程先冲压翻边孔,并以翻边孔内插入定位销定位保证翻边孔和圆孔两孔间的中心距及角度尺寸公差。
在薄壁圆管圆弧外壁上冲孔,凸、凹模接触的零件工作面是圆弧面,因此凹模只能设计在圆管内腔,所以将凹模设计成镶嵌在仿形圆管内腔的芯棒上,刃口部位圆弧与芯棒外径圆弧重合,芯棒外径与圆管内径间隙单边0.2mm,方便装、卸工件;由于管壳将凹模包在圆管内,所以冲孔的落料只能在取下工件后排出;在取下工件前落料需在芯棒落料孔内暂时存放;上述是冲孔模具结构的初步构思,具体的模具零件结构、尺寸公差、零件的加工工艺性及装配工艺性还需从模具整体细致的设计。
构思冲压步骤:上料装卡管壳,将冲压完翻边孔的半成品管壳,插入芯棒,翻边孔端向外,将定位销插入翻边孔及芯棒定位孔,工件固定;凸模下行至冲压行程下限,冲孔完成;落料停留在芯棒落料孔内;凸模回程至行程上限,拔出定位销,取下工件,落料从落料孔排出。
2薄壁圆管冲孔模具设计分析按上述模具构思详细分析后进行冲孔模具零件的细节设计2.1凹模设计凹模设计成镶嵌在仿形圆管内腔的芯棒上;因此凹模外径Ф26±0.01mm与芯棒Ф26孔按过度配合设计;Ф14.1(0,-0.02)mm尺寸为凹模刃口,Ф15mm沉孔为冲压落料孔;R25.8mm 圆弧与芯棒外径圆弧一致,可采用将凹模镶嵌入芯棒后磨削芯棒外圆至凹模与芯棒圆弧完全重合;凹模刃口磨损后可通过底部多次增加垫片重新磨削开刃来增加凹模使用寿命。
2.2芯棒设计工件装卡胎具:芯棒外径Ф51.6mm按管壳内径尺寸间隙单边0.2mm设计,方便装、卸工件;芯棒根部50mm长度设计外径Ф52±0.01mm与底座Ф52mm圆孔过渡配合,防止冲压过程中芯棒前后窜动导致凸模及凹模报废;镶嵌固定凹模:Ф26±0.01mm沉孔为凹模镶嵌孔,与凹模外径按过渡配合装配;Ф16mm孔为冲压落料孔,暂时存放冲压圆孔的落料;60±0.01mm 尺寸扁与底座沉台外形过渡配合,避免芯棒在冲压过程中发生转动导致凸模及凹模报废;定位销孔定位管壳工件,Ф12mm销孔为定位管壳翻边孔的定位销孔,管壳插入芯棒后翻边孔与销孔对正,插入定位销,工件固定。
50的圆孔翻边模具预冲孔尺寸表
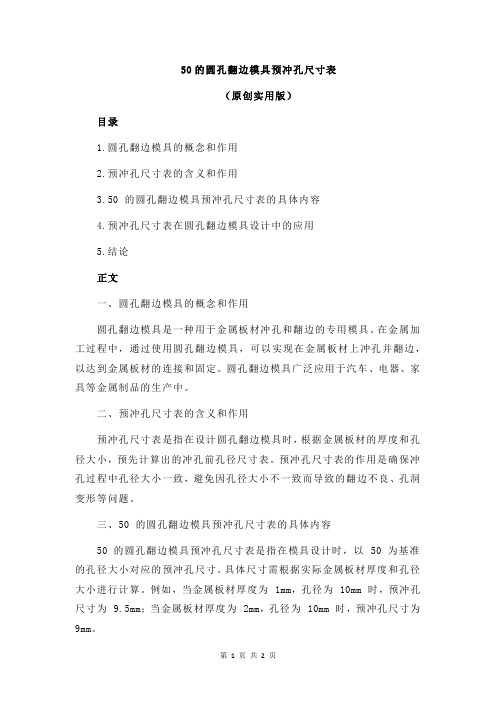
50的圆孔翻边模具预冲孔尺寸表(原创实用版)目录1.圆孔翻边模具的概念和作用2.预冲孔尺寸表的含义和作用3.50 的圆孔翻边模具预冲孔尺寸表的具体内容4.预冲孔尺寸表在圆孔翻边模具设计中的应用5.结论正文一、圆孔翻边模具的概念和作用圆孔翻边模具是一种用于金属板材冲孔和翻边的专用模具。
在金属加工过程中,通过使用圆孔翻边模具,可以实现在金属板材上冲孔并翻边,以达到金属板材的连接和固定。
圆孔翻边模具广泛应用于汽车、电器、家具等金属制品的生产中。
二、预冲孔尺寸表的含义和作用预冲孔尺寸表是指在设计圆孔翻边模具时,根据金属板材的厚度和孔径大小,预先计算出的冲孔前孔径尺寸表。
预冲孔尺寸表的作用是确保冲孔过程中孔径大小一致,避免因孔径大小不一致而导致的翻边不良、孔洞变形等问题。
三、50 的圆孔翻边模具预冲孔尺寸表的具体内容50 的圆孔翻边模具预冲孔尺寸表是指在模具设计时,以 50 为基准的孔径大小对应的预冲孔尺寸。
具体尺寸需根据实际金属板材厚度和孔径大小进行计算。
例如,当金属板材厚度为 1mm,孔径为 10mm 时,预冲孔尺寸为 9.5mm;当金属板材厚度为 2mm,孔径为 10mm 时,预冲孔尺寸为9mm。
四、预冲孔尺寸表在圆孔翻边模具设计中的应用在圆孔翻边模具设计中,预冲孔尺寸表起到了重要的指导作用。
设计人员可以根据预冲孔尺寸表,选择合适的模具材料和设计方案,以确保模具的精度和耐用性。
同时,在模具制造过程中,预冲孔尺寸表也可以作为检验模具质量的重要依据。
五、结论50 的圆孔翻边模具预冲孔尺寸表是模具设计中不可或缺的一部分,它对确保模具的精度和耐用性起到了关键作用。
筒形件落料、拉深、冲孔、复合模模具课程设计剖析

目录序言 (2)第一部分冲压成形工艺设计 (5)Ⅰ明确设计任务,收集相关资料 (5)Ⅱ冲压工艺性分析 (6)Ⅲ制定冲压工艺方案 (6)Ⅳ确定毛坯形状,尺寸和主要参数计算 (10)第二部分冲压模具设计 (15)rⅡ计算工序压力,选择压力机 (16)Ⅲ计算模具压力中心 (19)Ⅴ、弹性元件的设计 (25)Ⅵ模具零件的选用 (27)Ⅶ冲压设备的校核 (29)Ⅷ其他需要说明的问题 (30)Ⅸ模具装配 (32)设计总结 (35)参考文献 (36)序言目前我国模具工业与发达国家相比还相当落后。
主要原因是我国在模具标准化,模具制造工艺及设备等方面与工业发达国家相比差距很大。
随着工业产品质量的不断提高,模具产品生成呈现的品种、少批量、复杂、大型精密更新换代速度快。
模具设计与技术由于手工设备,依靠人工经验和常规机加工,技术向以计算机辅助设计,数控编程切屑加工,数控电加工核心的计算机辅助设计(CAD/CAM)技术转变。
模具生产制件所表现出来的高精度,高复杂程度,高生产率,高一致性和抵消耗是其它制造加工方面所不能充分展示出来,从而有好的经济效益,因此在批量生产中得到广泛应用,在现代工业生产中有十分重要的地位,是我国国防工业及民用生产中必不可少的加工方法。
随着科学技术的不断进步和工业生产的迅速发展,冲压零件日趋复杂化,冲压模具正向高效、精密、长寿命、大型化方向发展,冲模制造难度日益增大。
模具制造正由过去的劳动密集、依靠人工的手工技巧及采用传统机械加工设备的行业转变为技术密集型行业,更多的依靠各种高效、高精度的NC机床、CNC机床、电加工机床,从过去的单一的机械加工时代转变成机械加工、电加工以及其他特种加工相结合的时代。
模具制造技术,已经发展成为技术密集型的综合加工技术。
本专业以培养学生从事模具设计与制造工作能力的核心,将模具成型加工原理、设备、工艺、模具设计与制造有机结合在一起,实现理论与实际相结合,突出实用性,综合性,先进性。
- 1、下载文档前请自行甄别文档内容的完整性,平台不提供额外的编辑、内容补充、找答案等附加服务。
- 2、"仅部分预览"的文档,不可在线预览部分如存在完整性等问题,可反馈申请退款(可完整预览的文档不适用该条件!)。
- 3、如文档侵犯您的权益,请联系客服反馈,我们会尽快为您处理(人工客服工作时间:9:00-18:30)。
毕业设计(论文)题目:圆筒件翻边、冲孔模设计年级专业:模具设计与制造学生姓名:指导教师:2010 年8 月26 日目录摘要 (3)绪论 (5)一、冲压工艺性分析 (7)二、冲压工艺方案的确定 (8)1.方案种类 (8)2.方案的比较 (8)3.方案的确定 (8)三、模具结构形式的确定 (9)四、设计工艺计算 (10)1.基本尺寸与计算 (10)2.冲裁压力的计算 (12)3.压力机公称压力的确定 (12)4.冲裁压力中心的确定 (13)5.工作零件刃口尺寸的计算 (15)五、模具总体结构设计 (19)六、主要零部件的设计 (20)1.工作零件的结构设计 (20)2.定位零件的设计 (22)3.卸料部件的设计 (23)4.导柱、导套位置的确定 (23)5.模架及其他零部件的设计 (24)七、模具总装图 (24)八、填写冲压工艺卡片 (27)九、填写模具零件加工工艺卡 (29)十一、结束语 (34)致谢 (35)主要参考文献 (36)摘要论文是由翻边设计、冲孔模设计组成,冲压模具主要是将板料分离或成形而得到制件的加工方法。
因为模具的生产主要是大批量的生产,而且模具可以保证冲压产品的尺寸精度和产品质量,模具的设计与制造主要考虑到模具的设计能否满足工件的工艺性设计,能否加工出合格的零件,以及后来的维修和存放是否合理等。
在本次设计中的取暖器主机连接座中,不仅要考虑要使做出的零件能满足工作要求,还要保证它的使用寿命。
其次设计中还要考虑到它的实际工作环境和必须完成的设计任务,两套模具的模架分别采用后置和中间形式,凹模采用整体凹模,这样可以采用线切割等数控设备来一次完成全部的工序加工,在设计中我要考虑到很多关于我所设计模具的知识,包括它的使用场合、外观要求等,从这里可以知道模具设计是一项很复杂的工作,所以在设计要不断的改进直到符合要求。
关键词:翻边冲孔工艺性AbstractPaper is designed by the flanging, punching mould design, sheet metal stamping is mainly will get separated or forming parts processing methods. Because the mold production mainly mass production, and mould can ensure the precision stamping products and product quality, the mold design and manufacture of the main consideration of mould design can meet the design, can processing manufaturability qualified parts, and then repair and storage whether reasonable, etc. In the design of the main building, connect heater to make the parts can satisfy the requirements, it also ensures that its service life.Second design to consider its actual working environment and must complete the task, two sets of mould design of formwork used respectively, and the form of dies.the using integral dies.the, so can using such equipment to a linear control all the process in the design, I will consider a lot about my knowledge of mould design, including the use of its appearance, etc,from here can know mold design is a very complicated work, so in the design to continuous improvement until meets the requirement.Keywords: flanging punching process绪论(1)课题来源及要求本次模具毕业设计的课题属于零件设计类,来源于生产实际问题,是一个圆孔类取暖器主机连接座,该零件需通过①落料--②拉伸--③落料冲孔--④平面翻边--⑤内孔翻边-- ⑥冲侧面孔六道工序完成。
我的课题任务是设计两套模具来完成该零件的最后两道工序。
(2)设计内容a分析零件的成形工艺性,进行制品的基本参数的计算、冲压模的设计计算,选用压力机,确定模具类型及结构;b 模具和成型机械关系的校核;c模具零件的必要计算;d使用AutoCAD绘制模具装配图一张,绘制凸模、凹模、及重要零部件零件图共五张;e编写设计说明书;f严格执行相关国家标准;g上交电子文档和打印文档并存档;(3)介绍的内容与意义此次毕业设计说明书涉及的知识面广、衔接紧密、结构整合或综合性强、实用性强。
本说明书介绍了冲裁件的工艺性分析、冲压工艺方案的确定、模具结构形式的确定、设计工艺计算、模具总体结构设计、主要零部件设计、冲压设备的选取、填写冲压工艺卡及模具零件加工工艺卡等。
本说明书对冲压模具设计的基本流程介绍相对比较全面,理论联系实际,同时也培养了个人的较强实践动手能力和对模具设计专业知识的系统化、完整化,以及对于工程技术的严谨性。
(4)设计过程为缩短本次设计的时间,让模具设计充分理解其设计意图,在模具各部分设计中采用了计算机辅助设计(AutoCAD)系统,以及利用Pro/E对其尺寸进行分析,让模具各部分的结构明确的展现在我们面前,提高效率。
1,材料为Q235,厚度为1.2mm:工件简图:零件1-1一、冲压件工艺性分析1.1 零件材料分析该零件材料为Q195冷板材料,厚度t=1.5mm。
Q195属于普通碳素钢,力学性能抗剪强度255-314τ/MPa 抗拉强度314-392τ/Mpa 具有良好的冲压成形性能,为一般冲压用钢,适合冲裁。
1.2 零件形状从零件的形状分析,该零件属于圆孔类零件,壁厚为1.5 mm,需把内孔翻边成一个Ф56.5 0 -0.2通孔,和在圆筒侧面上冲四个Ф5.1的小孔。
1.3尺寸分析该工件尺寸有标注公差,查公差表,可按GB1800-79 IT112级精度确定,尺寸精度较低,普通冲裁(经济精度为IT11)完全能满足要求。
以凹模为基准件凸模根据凹模尺寸进行配制加工。
1.4要求零件表面不允许有划痕1.5结论综上所述,该零件的冲裁工艺性较好,冲裁加工能够达到设计要求。
二、冲压工艺方案的确定2.1方案种类从零件的结构特征可以看出,冲压所需的基本工序包括翻边、冲孔。
由于零件的完成的工序不在体同一个平面上,而且定位方式也不相同,只能分两次完成。
根据零件底部成型方式,可能有如下3种冲成型方案:方案一:通过机械且学的方式,如车削除去底部,再冲侧孔。
方案二:采用冲切的方式除去底部,再冲侧孔。
方案三:采用翻边成型,再冲侧孔。
图1-2 方案成型流程2.2方案的比较方案一:采用车削底部的方法,再冲侧孔。
无疑零件的断面质量高,但生产效率低,不适用批量生产,在零件底部要求不高的情况下不宜采用。
方案二:采用冲切的方式,再冲侧孔。
则要求零件底部的远角半径在冲切前必须冲压成接近清角(即R≈0),因此在冲切前先要增加一道整形工序,并且清角的技术质量要求不易保证。
较难加工。
方案三:采用翻边形式,再冲侧孔。
生产效率高并且节省材料,翻边的孔口虽然没有以上两种的好,但零件的高度尺寸29.5mm可以看做IT12级的未注公差,翻边方式可以满足零件技术要求。
因此从零件的底部成形方式来考虑采用第三种方式,即翻边---冲侧孔。
2.3方案的确定综合上述分析:对于一个工件可以得出多种工艺方案,经比较,综合冲裁件的质量、经济性、安全性所以决定采用方案三。
三、模具结构形式的确定( a ) ( b )图1-3 单工序模具方案—各工序模具工作部分原理图( c ) ( d )图1-4 单工序模具方案二各工序模具工作部分原理图方案一和方案二的后一个工序模具是一致的,两个的主要不同在前道工序模具结构上。
方案一种模具结构为正装单工序模具,方案二为倒装单工序模具正装式单工序模具和倒装式单工序模具结构比较:正装式单工序模具适用于冲制材质较软或板料较薄的平直度要求较高的冲裁件,还可以冲制孔边距较小的冲裁件。
倒装式单工序模具不宜冲制孔边距较小的冲裁件,但倒装式复合模结构简单,又可以直接利用压力机的打杆装置进行推件卸件可靠,便于操作,并为机械化出件提供了有利条件,所以应用十分广泛。
而且从本次零件的卸料回弹上考虑的话,比方案一容易控制。
因此形状和尺寸精度比方案一更加的高。
根据零件分析,制件的精度不高,为了提高经济效益和简化模具结构,宜采用方案二,即倒装式单工序模具结构。
四、设计工艺计算4.1基本尺寸计算4.1.1、因为加工工件需分为几个不同的工序,所以从上一道工序得到的尺寸是,预冲孔直径是Ф43 高度为22mm 冲孔的直径是Ф5.1mm4.2各工序冲压力的计算即压力机的选取1、翻边工序翻边力计算计算翻边力的目的是为了合理地选用冲压设备、设计模具和检验模具的强度。
压力机的吨位必须大于所计算的翻边力,以适应冲裁的需求。
查“模具设计与制造简明手册(第二版).pdf”P92、表1-119其中翻边力F可按下式进行计算:F=1.1π(D-d) tσs有上次工序设计可以知道D =55mm d=43 mm查附表1,Q195的屈服强度为195 /MPa。
P=1.1³3.14³(55-43)³1.5³195≈12162N式中:σs—材料抗剪强度(MPa);D、d—翻空前孔径、翻孔后孔径(mm);t—零件厚度。
顶件力取翻边力的10%F顶=0.1³12162=1216N整形力F整=A P= 1/4π(53.5-43)³80=659N式中:A—整形零件的面积(mm2);P—整形单位面积压力,可查表课本冷冲压模具设计P223、表5-6(P /MPa)。
推料力F推=K推F翻=0.04³12162=486N卸料力F卸=nK卸F翻=1³0.055³12162=669N式中:K推—推料力系数,其值为0.03~ 0.07(薄料取大值,厚料取小值);K卸—卸料力系数,其值为0.02 ~0.06(薄料取大值,厚料取小值);n—梗塞在凹模内制件或废料数量(n=h/t),其中h为刃口部分的高(mm),t为材料厚度(mm)。