注塑成型不良原因及解决方法
塑料注塑成型不良现象的原因及处理办法

塑料注塑成型不良现象的原因及处理办法1、充填不足(缺胶)[1] 成形品的体积过大1-1)要使用成形能力大的成形机。
1-2)使用成形多数个成品的模具时,要关闭内腔。
[2] 流道、浇口过小2-1)扩展流道或浇口。
2-2)放快射出速度。
2-3)增强射出压力。
[3] 喷头温度低3-1)喷射空气,以排出冷却的材料。
3-2)升高材料的温度。
3-3)改用大型喷头。
[4] 材料的温度或者射出压力低4-1)升高材料的温度。
4-2)增强射出压力。
4-3)添加外部润滑。
[5] 内腔里的流体流动距离过长5-1)设置冷余料洼坑。
5-2)升高材料的温度。
[6] 模具温度低了6-1)升高模具温度。
6-2)放快射出速度。
6-3)增强射出压力。
6-4)升高材料的温度[7] 射出速度慢了7-1)加快射出速度。
7-2)升高材料的温度[8] 材料的供给量过少8-1)如属螺桨式装置,增加增塑量;而采用柱塞方式时,则增加从料斗落下的数量。
8-2)减少外部润滑,改进螺桨的加工条件[9] 排气不良9-1)放慢射出速度。
9-2)将填充不良的位置改为镶件结构或在模具上加设排气槽。
9-3)改变胶口的位置9-4)改变成形品的厚度2、溢料(飞边)[1]锁模力不足1-1)加强锁模力。
1-2)降低射出压力。
1-3)改用大型成形机。
1-4)确实调整好连杆。
[2]模具不好2-1)补修导推杆或导钉梢的部位2-2)修正模具安装板。
增加支撑柱。
2-3)使用轨距联杆的强度足够的成机2-4)确实做好模具面的贴合。
[3]模具面的杂质3-1)除去杂物[4]成形品的投影面积过大4-1)使用大型成形机。
[5]材料的温度过高5-1)降低材料的温度。
5-2)放慢射出速度。
[6]材料供给量过剩6-1)调整好供给量。
[7]射出压力高7-1)降低射出压力。
7-2)降低材料的温度。
3气孔在材料为充分干燥时,是挥发物或空气所致;大多时候发生在产品胶厚的位置,实际是材料的收缩引起的真空气泡[1] 流道或浇口过小1-1)将流道或浇口扩展。
注塑成型缺陷及解决方法

注塑成型缺陷及解决方法注塑成型是一种常见的塑料加工方法,广泛应用于各行各业。
然而,在注塑成型过程中,可能会出现一些缺陷。
本文将介绍一些常见的注塑成型缺陷,并提供一些常用的解决方法。
1.短-shot(短充)短-shot指的是注塑件的一部分或全部体积没有完全填满模具腔体的现象。
短-shot的原因可能有:-温度不足:熔融塑料的温度不够高,使得塑料的流动性不佳。
-压力不足:注塑机的射出压力不足,无法将足够的塑料材料推入模具中。
解决方法:-提高温度:提高熔融塑料的温度,以增加其流动性。
-增加压力:增加注塑机的射出压力,以确保足够的塑料材料填充模具腔体。
2. Flash(闪边)Flash是指在注塑成型过程中,塑料溢出模具腔体形成的薄膜或边缘。
Flash的原因主要包括:-模具不平整:模具表面存在间隙或损坏,导致塑料从模具表面溢出。
-压力过高:注塑机的射出压力过高,使得塑料在模具闭合时被挤出。
解决方法:-检查模具:检查模具表面是否平整,并修复损坏的部分。
-调整压力:调整注塑机的射出压力,使其在模具闭合时不会挤出塑料。
3. Sink mark(沉痕)Sink mark是指注塑件表面出现的凹陷或不平整的现象。
Sink mark的原因可能有:-塑料收缩:在注塑件冷却过程中,熔融塑料由于收缩而导致表面出现凹陷。
-总量不足:注塑机注入的塑料总量不足,无法填满模具腔体。
解决方法:-调整冷却时间:延长注塑件的冷却时间,使塑料充分收缩并填满模具腔体。
-增加注塑量:增加注塑机的注塑量,确保塑料充分填充模具腔体。
4. Weld line(焊痕)Weld line是指注塑件表面出现的一条或多条由于不同流动方向的熔融塑料相遇而形成的线缝。
Weld line的原因主要包括:-塑料温度不一致:在注塑过程中,熔融塑料的温度不一致,导致相遇处出现冷凝。
-流动路径过长:塑料在流动过程中,由于流动路径过长而冷却,形成焊痕。
解决方法:-调整温度:调整注塑机的温度控制系统,使塑料熔融温度均匀一致。
注塑成型常见不良现象及处理措施

注塑成型常见不良现象及处理措施在注塑成型过程中,常常会出现一些不良现象,这些现象可能会导致产品的质量下降,甚至无法使用。
因此,及时发现并解决这些问题是非常重要的。
下面将介绍一些常见的注塑成型不良现象及处理措施。
1. 短射短射是指注塑制品在填充过程中未能充满模具腔体,导致制品出现不完整的现象。
短射的原因可能有:- 注塑机温度设置过低,导致熔融物质无法充分流动;- 模具温度过低,使得熔融物质凝固速度过快;- 注射压力过低,无法将熔融物质充分填充到模具腔体中。
处理措施:- 调整注塑机温度,确保熔融物质能够充分流动;- 提高模具温度,延缓熔融物质的凝固速度;- 增加注射压力,确保熔融物质能够充分填充到模具腔体中。
2. 气泡气泡是指制品内部或表面出现的气体聚集现象,给产品的外观和性能带来负面影响。
气泡的原因可能有:- 熔融物质中含有过多的挥发性物质;- 注射速度过快,导致气体无法及时排出;- 模具中存在气体积聚的死角。
处理措施:- 选择低挥发性的熔融物质;- 控制注射速度,避免气体无法及时排出;- 优化模具结构,减少气体积聚的死角。
3. 热胀冷缩热胀冷缩是指注塑制品在冷却过程中由于热胀冷缩系数不一致而导致尺寸变化的现象。
热胀冷缩的原因可能有:- 注塑机温度和模具温度不匹配;- 熔融物质的热胀冷缩系数不一致。
处理措施:- 调整注塑机温度和模具温度的匹配度;- 选择热胀冷缩系数相近的熔融物质。
4. 毛刺毛刺是指制品表面出现的细小突起,给产品的外观和触感带来不良影响。
毛刺的原因可能有:- 模具中存在不平整的表面;- 注塑机压力过高,使得熔融物质溢出模具腔体。
处理措施:- 修复模具表面,保持其光滑平整;- 调整注塑机压力,避免熔融物质溢出模具腔体。
5. 缩水缩水是指注塑制品在冷却过程中由于体积收缩而导致尺寸变小的现象。
缩水的原因可能有:- 熔融物质中含有过多的收缩剂;- 注塑机温度和模具温度不匹配。
处理措施:- 选择低含量的收缩剂;- 调整注塑机温度和模具温度的匹配度。
注塑缺陷原因分析与解决方案
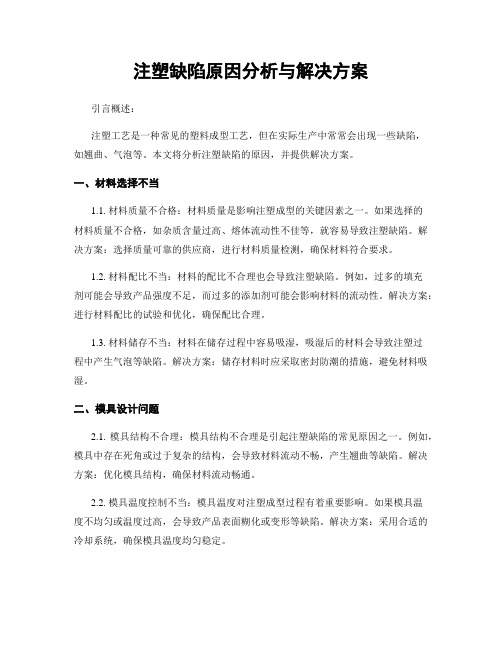
注塑缺陷原因分析与解决方案引言概述:注塑工艺是一种常见的塑料成型工艺,但在实际生产中常常会出现一些缺陷,如翘曲、气泡等。
本文将分析注塑缺陷的原因,并提供解决方案。
一、材料选择不当1.1. 材料质量不合格:材料质量是影响注塑成型的关键因素之一。
如果选择的材料质量不合格,如杂质含量过高、熔体流动性不佳等,就容易导致注塑缺陷。
解决方案:选择质量可靠的供应商,进行材料质量检测,确保材料符合要求。
1.2. 材料配比不当:材料的配比不合理也会导致注塑缺陷。
例如,过多的填充剂可能会导致产品强度不足,而过多的添加剂可能会影响材料的流动性。
解决方案:进行材料配比的试验和优化,确保配比合理。
1.3. 材料储存不当:材料在储存过程中容易吸湿,吸湿后的材料会导致注塑过程中产生气泡等缺陷。
解决方案:储存材料时应采取密封防潮的措施,避免材料吸湿。
二、模具设计问题2.1. 模具结构不合理:模具结构不合理是引起注塑缺陷的常见原因之一。
例如,模具中存在死角或过于复杂的结构,会导致材料流动不畅,产生翘曲等缺陷。
解决方案:优化模具结构,确保材料流动畅通。
2.2. 模具温度控制不当:模具温度对注塑成型过程有着重要影响。
如果模具温度不均匀或温度过高,会导致产品表面糊化或变形等缺陷。
解决方案:采用合适的冷却系统,确保模具温度均匀稳定。
2.3. 模具磨损严重:模具长时间使用后会出现磨损,磨损严重的模具会导致产品尺寸不准确或表面粗糙等缺陷。
解决方案:定期检查和维护模具,及时更换磨损严重的模具部件。
三、注塑工艺参数设置不当3.1. 注射压力过高或过低:注射压力是影响注塑成型的关键参数之一。
如果注射压力过高,会导致产品变形或开裂,而注射压力过低则会导致产品表面光洁度不高。
解决方案:根据产品要求和材料特性,合理设置注射压力。
3.2. 注射速度不合理:注射速度对产品的充填和冷却过程有着重要影响。
如果注射速度过快,会导致产品内部产生气泡或短射,而注射速度过慢则会导致产品表面瑕疵。
注塑成型缺陷及解决方法

注塑成型缺陷及解决方法注塑成型是一种常用的塑料制品生产工艺,但在实际操作过程中,难免会出现一些缺陷。
下面将介绍几种常见的注塑成型缺陷及其解决方法。
1.短射:短射指的是塑料在模腔中注入不完全,导致制品形状不完整或缺少一部分。
短射可能由于注射速度过快或进气不畅引起。
解决方法是调整注塑机的注射速度和压力,确保塑料充分进入模腔,并检查进气口是否畅通。
2.气泡:气泡是指制品表面或内部出现空洞。
气泡的形成可能由于塑料中含有水分、模具开放不当等原因。
解决方法是在注塑前将塑料干燥处理,确保塑料中不含水分,并检查模具密封性以防止气体进入模腔。
3.缩短:缩短是指制品尺寸比设计要小,可能由于塑料收缩不均匀或模具温度不稳定引起。
解决方法是通过调整模具温度和冷却系统,使塑料在注塑过程中均匀收缩,并确保模具温度稳定。
4.色差:色差是指制品表面颜色不均匀,可能由于塑料熔融不充分、颜料添加不均匀等原因。
解决方法是加长塑料的熔化时间,确保塑料充分熔融,并确保颜料充分混合均匀。
5.枝晶:枝晶是指制品表面出现树枝状的纹理,可能由于注塑温度过高或冷却时间不足引起。
解决方法是降低注塑温度,延长冷却时间,确保塑料在注塑过程中充分凝固。
6.毛刺:毛刺是指制品表面出现刺状的尖突物,可能由于模具间隙过大或模具磨损引起。
解决方法是调整模具间隙,确保模具紧密结合,并定期检查模具磨损情况。
7.烧焦:烧焦是指塑料在注塑过程中受热过度,产生发黑或炭化的现象。
烧焦可能由于注塑温度过高或注射速度过快引起。
解决方法是降低注塑温度,调整注射速度,确保塑料受热均匀。
总结起来,解决注塑成型缺陷的关键是调整注塑机参数、保证模具质量和稳定性,以及进行适当的后处理工艺。
此外,及时发现和修复模具的损坏也是避免缺陷的重要措施。
注塑成型过程中不良及原因分析对策
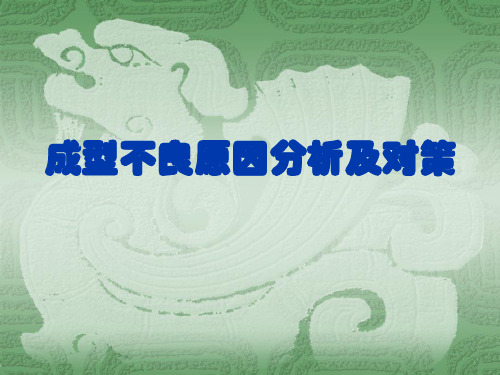
◆ 与成型品外观有关的成型不良
飞边 树脂进入模具分型线(PL)从而使薄膜附着在成型品四周 的现象。树脂粘度较低或保压过高时会出现这种现象。 凹痕 成型品表面出现凹陷的现象。厚壁产品容易出现这种现象。 须状斑纹 浇口周边形成独特的胡须状旋涡斑纹的现象。POM树脂容 易产生这一问题。 表面剥离 成型品的表面层与内部层产生分离的现象。 气泡 成型品表面拱状鼓起的现象。 变色 成型品颜色发生变化的现象。原因估计是滞留或树脂分解 等。
(2)产生熔合纹的原因
(2-1) 树脂温度偏低 两股树脂流相遇时便会出现熔合。此时,两者的温度越低,熔合就越明显。由于熔合处的 两股树脂流并不会相互混合(因为在喷流中一边半固化一边前进),因此如果温度偏低, 表层就会变厚,纹路很明显,而且强度也会降低。这是因为两者的粘合力变弱所致。相 反,如果两股树脂流的温度较高,粘合力便会增强,外观也就变得不很明显。
(2-3) 流动性和射出速度 材料的流动性较差时,充填时间 将延长,成型品表面层在保压工 序之前就已凝固,因此有时无法 向树脂施加保压。结果容易产生 麻点等不良外观。注射速度较慢 时也会由于同样的理由而易于产 生麻点。
(3)“麻点”的对策
(3-1) 尝试提高保压
首先尝试着逐渐提高保压设定值。这样基本上会解决问题。下面有指向本公司推 荐的材料成型条件的链接,请参阅。
◆ 与成型品外观有关的成型不良
空洞 成型品内部产生空洞的现象。厚壁 产品容易产生这种现象。 波纹 浇口附近出现波纹状皱纹的现象。 射速过慢时会产生这种现象。
BS(黑点)
(1)何谓“黑点”(外观)? 黑点是指成型品中出现黑色的点或条纹的现象。 成型品表面上出现的黑色的点便是BS(黑点)。由于某些原因,其成 分估计是焦化树脂或碳化树脂。
注塑成型不良现象及解决方法
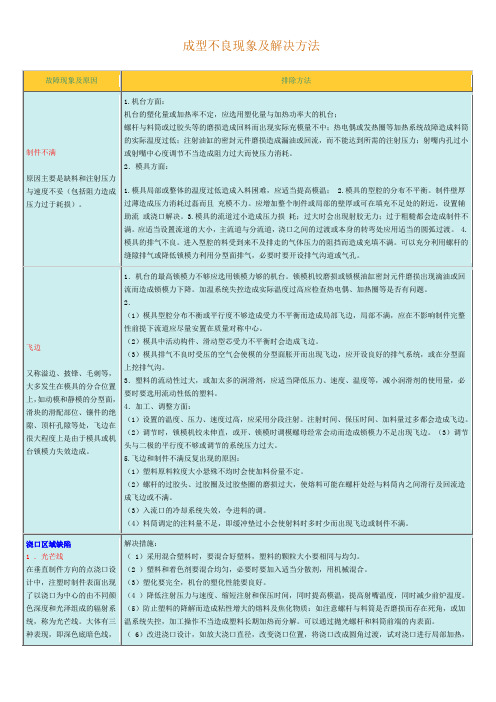
(4)对薄件应提高温度,保证料流畅顺,对厚壁制件应降低模温。
(5)浇口要对称开设,尽量开设在制件厚壁部位,应增加冷料井容积。
3.塑料方面:
结晶性的塑料比非结晶性塑料收缩历害,加工时要适当增加料量,或在塑料中加成换剂,以加快结晶,减少收缩凹陷。
4.加工、调整方面:
(1)设置的温度、压力、速度过高,应采用分段注射。注射时间、保压时间、加料量过多都会造成飞边。(2)调节时,锁模机铰未伸直,或开、锁模时调模螺母经常会动而造成锁模力不足出现飞边。(3)调节头与二极的平行度不够或调节的系统压力过大。
5.飞边和制件不满反复出现的原因:
(1)塑料原料粒度大小悬殊不均时会使加料份量不定。
分析如下:
1.加工方面:
(1)加工压力过大、速度过快、充料愈多、注射、保压时间过长,都会造成内应力过大而开裂。
(2)调节开模速度与压力防止快速强拉制件造成脱模开裂。
(3)适当调高模具温度,使制件易于脱模,适当调低料温防止分解。
2.
(1)模具型腔分布不衡或平行度不够造成受力不平衡而造成局部飞边,局部不满,应在不影响制件完整性前提下流道应尽量安置在质量对称中心。
(2)模具中活动构件、滑动型芯受力不平衡时会造成飞边。
(3)模具排气不良时受压的空气会使模的分型面胀开而出现飞边,应开设良好的排气系统,或在分型面上挖排气沟。
3.塑料的流动性过大,或加太多的润滑剂,应适当降低压力、速度、温度等,减小润滑剂的使用量,必要时要选用流动性低的塑料。
成型不良现象及解决方法
故障现象及原因
注塑成型常见不良现象及处理措施

注塑成型常见不良现象及处理措施注塑成型常见的不良现象有以下几种:
1. 短射:指注塑料进模型中未充满模腔,导致产品缺陷。
处理措施:增加注射
压力、延长注射时间、增加料缸温度、增加模具温度、增加模具出料口直径等。
2. 气泡:指产品表面或者内部浮现气泡,影响产品质量。
处理措施:增加注射
压力、延长注射时间、增加模具温度、增加料缸温度、增加模具出料口直径、增加模具排气孔等。
3. 热熔线:指产品表面浮现细小的线状缺陷,通常是由于注射速度过快导致的。
处理措施:减小注射速度、增加模具温度、增加模具出料口直径等。
4. 毛刺:指产品表面浮现细小的凸起,通常是由于模具设计不合理或者模具磨
损导致的。
处理措施:修复模具、修改模具设计、增加模具温度、增加模具出料口直径等。
5. 缩水:指产品尺寸缩小,通常是由于注射压力不足或者冷却时间不足导致的。
处理措施:增加注射压力、延长冷却时间、增加模具温度等。
6. 毛洞:指产品表面或者内部浮现凹陷,通常是由于注射速度过快或者模具设
计不合理导致的。
处理措施:减小注射速度、修改模具设计、增加模具温度等。
处理不良现象的关键是找到问题的根源,然后针对性地采取相应的处理措施。
同时,注塑成型过程中的参数控制和模具维护也是关键的因素,需要进行定期检查和调整。
- 1、下载文档前请自行甄别文档内容的完整性,平台不提供额外的编辑、内容补充、找答案等附加服务。
- 2、"仅部分预览"的文档,不可在线预览部分如存在完整性等问题,可反馈申请退款(可完整预览的文档不适用该条件!)。
- 3、如文档侵犯您的权益,请联系客服反馈,我们会尽快为您处理(人工客服工作时间:9:00-18:30)。
2.4喷嘴孔径太小,塑料在浇道衬套内凝固,减低背压效果: 调整模具或更换射嘴
2.5模温不当: 调整适当温度
2.6浇口太小,塑料凝固失去背作用: 加大浇口尺寸
2.7背压压力不够: 提高背压压力
2.8冷却效果不好,制品顶出后继续收缩: 延长冷却时间
2.9注射时间太短: 增加注射时间
1.4喷嘴温度太低: 提高喷嘴温度
1.5注射速度太慢:加快注射速度
1.6进胶不平均: 重开模具溢口位置
1.7注射压力过低:提高注射压力
1.8浇道或溢口太小: 加大浇道或溢口
1.9注射时间太短: 增加注射时间
1.10塑料内润滑剂不够: 增加润滑剂
1.11浇口衬套与喷嘴配合不正,塑料溢漏: 调整喷嘴配合
8.5注射速度太快: 减慢注射速度
8.6注射压力太高: 降低注射压力
8.7熔胶速度太低: 提高熔胶速度
8.8模具温度太低: 提高模具速度
8.9塑料粒粗细不匀: 使用粒状均匀原料
8.10料筒内夹有空气: 降低料筒后段温度、提高背压、减小压缩段长度
8.11塑料在模内流程不当: 调整溢口大小及位置、模具温度保持平均、成品厚度平均
2.10蓄压段过多: 注射终止应在最前端
注塑成型不良原因
及解决方法
共8页,第3页
文件编号
ZM-QW-E02
版本/状态
A /1
2.11注射速度太慢: 加快注射速度
2.12成品本身或其肋骨及柱位过厚,结构不合理: 合理的成品设计
3.粘模
可能出现的不良原因及解决办法:
3.1注射压力太高: 降低注射压力
3.2脱模剂不足: 略为增加脱模剂用量
1.12背压不足: 稍增背压
1.13保压调整不当: 重新调节
1.14止退环、密封环、螺杆磨损、倒流现象: 拆除检查修理
1.15模具温度太低: 提高模具温度
1.16制品太薄: 使用氮气射胶
1.17模具温度不匀: 重调模具水管
2.缩水
可能出现的不良原因及解决办法:
2.1模内进胶不足: 增加注塑量
2.2溢口不平衡: 调模模具溢口大小或位置
签署姓名 日期
■受控文件 □ 非受控文件
制定:
核准:
注塑成型不良原因
及解决方法
共8页,第2页
文件编号
ZM-QW-E02
版本/状态
A.1射胶量不够:增加射胶量或更换较大规格注塑机
1.2模具排气不良: 恰当位置加适度排气孔
1.3融料温度太低:提高料筒温度
8.银纹、汽泡
可能出现的不良原因及解决办法:
8.1塑料含有水份: 塑料彻底烘干、提高背压
8.2塑料温度过高或塑料在机筒内停留过久: 降低塑料温度,更换较小注射量的注塑机,降低喷嘴及前段温度
8.3塑料中其它添加物如润滑剂、染料等分: 减小其使用量或更换耐温较高的代替品
8.4塑料中其它添加物混合不匀: 彻底混合均匀
、
注塑成型不良原因
及解决方法
共8页,第5页
文件编号
ZM-QW-E02
版本/状态
A /1
7.7注射速度太快或太慢: 调整适当注射速度
7.8模内有过多脱模油: 擦拭干净
7.9注射压太高或太低: 调整适当注射压力
7.10模内表面有水: 擦拭并检查是否有漏水
7.11塑料不洁或渗有其它料: 检查塑料
7.12模内表面不光滑: 打磨模具
3.11模具表面不光滑: 打磨模具
3.12浇道外孔有损坏: 检修模具
3.13脱模造成真空: 开模或顶出减慢,或模具加进气设备
3.14无浇道抓销: 增设抓销
3.15注塑周期太短: 加强冷却
3.16浇道过大: 修改模具
4.披峰
可能出现的不良原因及解决办法:
4.1塑料温度太高: 降低塑料温度、降低模具温度
注塑成型不良原因
及解决方法
共8页,第4页
文件编号
ZM-QW-E02
版本/状态
A /1
5.2顶杆不够或位置不当: 检修模具
5.3模温太低: 升高模温
5.4脱模时局部产生真空现象: 开模及顶出慢速,加进气设备
5.5部份脱模角不够: 检修模具
5.6脱模剂不足: 略为增加脱模剂用量
5.7有脱模倒角: 检修模具
6.12太多脱模剂: 有用或减少脱模剂
7.流纹、成品表面不光泽
可能出现的不良原因及解决办法:
7.1塑料熔融不佳: 提高塑料温度、提高背压、加快螺杆转速
7.2塑料干燥处理不当: 改良干燥处理
7.3模具温度太低: 提高模具温度
7.4溢口过小产生射纹: 加大溢口
7.5模具冷却不当: 重调模具水管
7.6成品断面厚薄相差太多: 变更成品设计或溢口位置
6.4浇道及溢口过大或过小: 调整模具
6.5喷嘴温度过低: 提高喷嘴温度
6.6熔胶拼命的地方离浇道口太远: 调整模具
6.7注射速度太慢: 增快注射速度
6.8模内空气排除不及时: 增开排气孔或检查原有排气孔是否堵塞
6.9注射压力太低: 提高注射压力
6.10熔胶量不足: 使用较大的注塑机
6.11塑料不洁或渗有其它料: 检查塑料
5.8模具设计不良,成品内有过多余应力: 改良成品设计
5.9成品脱模时不能平衡脱离: 检修模具
5.10侧滑块动作之时间或位置不当: 检修模具
6.结合线
可能出现的不良原因及解决办法:
6.1塑料熔融不佳: 提高塑料温度、提高背压、加快螺杆转速
6.2脱模油太多: 少用脱模油或尽量不用
6.3模具温度过低: 提高模具温度
3.3填料过饱: 降低注射量、时间及速度
3.4浇道冷却不够: 延长冷却时间
3.5塑料温度过高: 降低塑料温度
3.6浇道脱模角不够: 修改模具增加角度
3.7进料不均使部分过饱: 变更溢口大小或位置
3.8浇道衬套与喷嘴配合不正: 重新调整其配合
3.9模具温度过高或过低: 调整模温及两侧相对温度
3.10浇道内表面不光或有脱模倒角: 检修模具
4.2填料太饱: 降低注射时间、速度及剂量
4.3注射速度太快: 降低注射速度
4.4合模面或吻合面不良: 检修模具
4.5注射压力太高: 降低注射压力
4.6锁模压力不够: 增加锁模压力或更换锁模压力较大的注塑机
5.开模时或顶出时成品破裂
可能出现的不良原因及解决办法:
5.1填料过饱: 降低注射压力、时间、速度及注胶量
注塑成型不良原因
及解决方法
共8页,第 1 页
文件编号
ZM-QW-E02
版本/状态
A/1
COVER PAGE(封面)
DOCUMENT CATEGORY 文件种类:
□ QML质量手册 □ OPP程序文件 ■ WGI工作指引
REVISION RECORD 修订记录
项次
修订日期
版本/状态
修订内容
备注
受控类型