下车身平台化设计方法研究
汽车基础知识(车身方向)试题及答案

汽车基础知识(车身方向)试题及答案一、判断题1、乘用车下车身包括地板总成、前舱总成和车身辅料。
( )2、乘用车多为非承载式车身( )3、使车身能满足刚度和强度的要求,结构设计中采用各种结构加强措施。
是有必要的。
( )4、从车身结构来看,承载式车身的强度和刚度要比非承载式车身的大( )5、钢板是目前乘用车车身占比最大的材料种类。
( )6、上车身和下车身一起组成了白车身&彩车身,彩车身过了涂装完成电泳喷漆后,成了白车身。
( )7、一辆白车身需要涂10公斤左右的密封胶。
( )8、涂胶工艺需确保如下要求:防水、尘、气流、污染气体侵入车体;防振动、噪音、热量侵入室内;防腐蚀介质侵蚀车身板件。
( )9、侧门开闭系统主要包括:侧门锁体总成、侧门锁环、车门外把手、侧门限位器总成、侧门密封条。
( ) 10、门框密封条中的海绵胶泡管内含金属骨架,起到加强胶条的定型及固定作用。
( ) 11门框密封条中的密实胶柔软并富有弹性,起着受压变形,卸压反弹的功能。
( )12、升降系统主要包括:前后门活动导轨总成、前后门玻璃总成/角商玻璃总成(车门安装)、玻璃升降器、外水切、内水切、玻璃呢槽、前后门亮饰条。
( )13、佩戴过程带扣插入力,是体验评价安全带的力学性能之一( )14、车身附件产品开发的关键,是要建立早期验证,模拟客户使用工况进行分析验证提升体验舒话性( )15、前期对安全布置设计不合理,会造成安全带佩戴过程拿取不方便,佩戴后有磕脖或滑肩的问题。
( )16、除了因为布置上造成的问题,安全带佩戴后感觉有压迫感等舒适性问题,会造成乘客不愿意去系安全帯。
( )17、车身平台科负责下车身平台化规划工作,负责车身新技术研究、开发及推广工作。
( )18、车身部尺寸工程科的职责为负责牵头尺寸性能小组工作,落实项目产品尺寸工程实施,根据项目需求提供各阶段、各级系统性尺寸工程问题解决方案,各阶段各系统性尺寸性能类问题解决和精度提升工作,研究尺寸工程行业发展趋势,掌握尺寸工程应用相关理论,探索尺寸工程实际应用方法,建立并推行尺寸性能开发工作体系。
汽车底盘的模块化设计技术研究与应用

汽车底盘的模块化设计技术研究与应用发布时间:2022-01-20T08:07:41.321Z 来源:《中国科技人才》2021年第30期作者:刘新新[导读] 目前,常见的汽车底盘设计方法有模块化设计方法,对此本文为了了解该方法的有效性,将进行相关的研究工作,研究当中,将介绍底盘功能模块、底盘模块编码与数据管理等,最终结合实例分析其具体应用。
另外,在汽车底盘模块化设计当中,还提倡五化概念,即系统平台化、零部件通用化、标准化、架构化、模块化,此概念可以保障设计有计划、有方向的开展。
刘新新山东交通技师学院山东省临沂市 276000摘要:目前,常见的汽车底盘设计方法有模块化设计方法,对此本文为了了解该方法的有效性,将进行相关的研究工作,研究当中,将介绍底盘功能模块、底盘模块编码与数据管理等,最终结合实例分析其具体应用。
另外,在汽车底盘模块化设计当中,还提倡五化概念,即系统平台化、零部件通用化、标准化、架构化、模块化,此概念可以保障设计有计划、有方向的开展。
关键词:汽车底盘;模块化设计;研究与应用模块化设计技术的出现和应用对制造行业有着重要的意义,既能帮助产品进行重新的设计和发展,还能通过对产品架构和系统的升级促进产品的更新发展。
近年来,在信息技术的存进和带动下,模块化设计技术和理念在汽车行业的应用愈加广泛,对汽车行业的发展起着至关重要的作用。
1. 汽车底盘模块化设计技术研究与应用的重要性在科技生产力不断提升的今天,汽车设计生产行业需要不断地加大对设计生产技术的研发,才能够使生产技术适应不断提升的客户需求和市场环境,实现长效的发展,对汽车底盘模块化设计技术进行研究和有效的应用对整个汽车行业都有着积极的意义。
1.1降低底盘部件开发的难度底盘设计与开发是规模巨大的工程,由于底盘产品的在结构上上复杂性、在部件上的繁多性以及在技术上的密集性特点,使得底盘设计开发工作的难度很大。
利用模块化设计技术进行底盘开发能够讲底盘设计划分为细小的不同模块,对设计研究的难度进行分解,进而对设计难度进行有效的降低,促进底盘产品的开发设计。
车身平台化开发策略研究

Ke r s Bo y P a f r , sg , v l p e t y wo d : d , l to m De i n De e o m n
汽车 平 台化 、模 块化 开发 在 国外 已经 发展成 熟 ( 车模块 化是 对汽 车平 台化 的进一 步发 展和细 化 , 汽
本 文 以汽车平 台化 泛指Ⅲ 。 ) 国外汽 车企业 的多 品种 、 全 系列 车型 开发 大都 依 托 汽 车平 台化 技 术 的运 用 . 由图 1 0可 以看 出 . 着 速 度 增 大 . 向力 和 随 纵 侧 向力 都 逐渐 减 小 . 献[5 的试 验 结 果是 侧 向力 文 51 在 侧 偏 角 较 小 时 随 速 度 的增 大 而增 大 .在 侧 偏 角 逐 渐 增 大 后 ,侧 向力 随 速度 的增 大 而减 小 ;文 献 『6与 文献 『7给 出 的试 验 结果 是 纵 向力 和 摩擦 系 5] 51 数 随速 度 的增 大 而 减 小 由 于纵 向力 和侧 向力 的
定基 于 目标 市场 、 品牌 定义 、 品配置需 求等 限制条 产 件 的整 车架 构 ( 包含 电器架 构方 案 、 规 需求 、 法 初始
整 车技术 规 范 、 主要 系 统概 念 、 案 和技 术要 求 、 方 初
但是 费用 昂贵 . 实现最 优设 计 未
由于前 舱对 碰撞安 全性 能影 响 巨大 .需在 车身 平 台化 的前 舱布 置基础 上 .考虑 吸能空 间和 碰撞传 力路径 的设计 .而传力 路径 的布置 将决定 前舱 的设 计风格 前 纵梁 末端 可以设 计成 与前 围板相 连 ( 图
和后 地板 总成 。车身 平 台化 开发 目标 是要在 满 足平
身平 台上 的零件 最大化 共用 .而 车身 与整车 其他 系
基于平台化的车身零件设计与制造成本分析
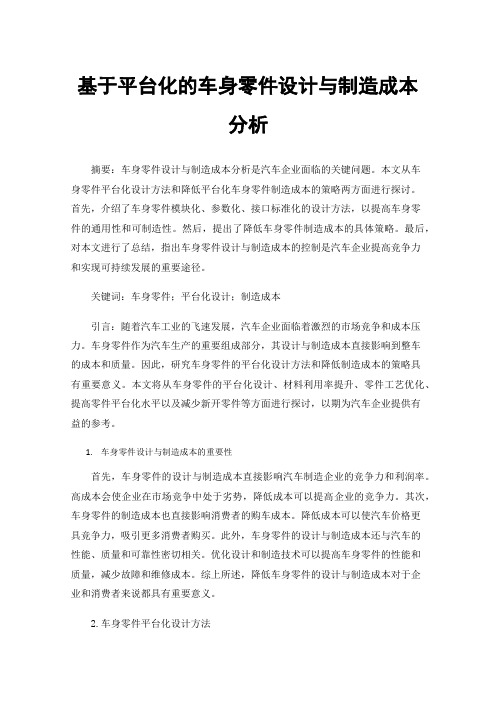
基于平台化的车身零件设计与制造成本分析摘要:车身零件设计与制造成本分析是汽车企业面临的关键问题。
本文从车身零件平台化设计方法和降低平台化车身零件制造成本的策略两方面进行探讨。
首先,介绍了车身零件模块化、参数化、接口标准化的设计方法,以提高车身零件的通用性和可制造性。
然后,提出了降低车身零件制造成本的具体策略。
最后,对本文进行了总结,指出车身零件设计与制造成本的控制是汽车企业提高竞争力和实现可持续发展的重要途径。
关键词:车身零件;平台化设计;制造成本引言:随着汽车工业的飞速发展,汽车企业面临着激烈的市场竞争和成本压力。
车身零件作为汽车生产的重要组成部分,其设计与制造成本直接影响到整车的成本和质量。
因此,研究车身零件的平台化设计方法和降低制造成本的策略具有重要意义。
本文将从车身零件的平台化设计、材料利用率提升、零件工艺优化、提高零件平台化水平以及减少新开零件等方面进行探讨,以期为汽车企业提供有益的参考。
1.车身零件设计与制造成本的重要性首先,车身零件的设计与制造成本直接影响汽车制造企业的竞争力和利润率。
高成本会使企业在市场竞争中处于劣势,降低成本可以提高企业的竞争力。
其次,车身零件的制造成本也直接影响消费者的购车成本。
降低成本可以使汽车价格更具竞争力,吸引更多消费者购买。
此外,车身零件的设计与制造成本还与汽车的性能、质量和可靠性密切相关。
优化设计和制造技术可以提高车身零件的性能和质量,减少故障和维修成本。
综上所述,降低车身零件的设计与制造成本对于企业和消费者来说都具有重要意义。
2.车身零件平台化设计方法2.1 车身零件模块化设计车身零件模块化设计是一种创新的设计方法,它将车身零件划分为多个具有独立功能与接口的模块,以便在设计、生产和维护过程中实现灵活的组合和替换。
这种模块化设计策略有助于降低设计的复杂性,提高生产效率和质量,同时也方便维修和升级。
为了实现模块化设计,需要对车身零件进行标准化和系列化,以便在不同车型之间实现零部件的共享和互换。
车身平台化开发策略研究

车身平台化开发策略研究鞠晓锋【摘要】Base on SAIC MOTOR'S project experience, this paper studied the key points and introduced basic guidelines of platform develop strategy of BIW. Based on the study of front cabin assembly, front and rear floor assembly of a foreign company's platform, it concluded that, the principle for platform design was to design the BIW with highest standards and limits, on the premise of comprehensive consideration of vehicle system requirements, legal and process requirements etc., which would enable the design to configure its components freely to meet low standard requirements.%依托于上海汽车自主品牌的开发经验,系统分析了车身平台化开发的主要问题和关键点,阐述了车身平台化开发的基本思路.通过对国外某汽车公司车型平台前舱总成、前地板总成、后地板总成设计的研究,得出平台化设计原则,即在综合考量整车各系统要求、法规、制造工艺等前提下,以最高标准要求和限制条件来开发设计车身架构,使之在低标准要求情况下可以灵活对零部件组合配置进行更改.【期刊名称】《汽车技术》【年(卷),期】2012(000)002【总页数】4页(P7-10)【关键词】车身;平台化;开发策略【作者】鞠晓锋【作者单位】上海汽车集团股份有限公司乘用车公司技术中心【正文语种】中文【中图分类】U462.2汽车平台化、模块化开发在国外已经发展成熟(汽车模块化是对汽车平台化的进一步发展和细化,本文以汽车平台化泛指[1])。
汽车产品平台化设计

陈福全
(安徽奇瑞汽车股份有限公司 241009)
摘要:本文对平台化设计相关概念、平台化设计方法及产品设计理念进行了阐述,帮助设计者正确认识平台化设计,并引导其践行平台化设计,树立良好的设计理 念,科学创新,促进汽车产品平台化水平的提高。 关键词:平台化;平台化设计;平台化产品;标准化;通用化 中图分类号: F407.471 文献标示码: A
平台化产品与其所应用产品及扩展、衍生产品间相互联系、 互补,形成稳固的产品链。任何标准化、通用化产品都是平台化产 品,但反之不一定成立。平台化产品与标准化、通用化产品的图示 集合关系如图1所示。
平台化产品具有平台性,是比一 般沿用件通用性更强的零件。平台化 产品可被沿用,但沿用件不一定能够 作为平台化产品。很多现产品都可被 沿用。
4 结束语
好的平台化设计产品,有益于企业赢得市场先机,奠定品牌调 性、品牌信赖与忠诚。世界优秀汽车厂商车型相互间都延续着某些 相同的被称之为基因的经典元素,这些元素的传承即是平台化设计 的成果,其存在使车型透露出浓厚的产品设计气息,丰富了汽车的 灵魂与魅力。希望设计者能够借鉴,树立更为正确完善的产品设计 理念,充分理解平台化设计,应用以上平台化设计方法,更快设计 出价格低、IQS与APEAL表现好、化设计要基于质量、成本与
图1 平台化产品与标准化/ 通用化产品关系
平台化设计时,先列出平台化相关的技术要素,比如组合开关的要 素,与转向管柱的连接结构、角度传感器有无、功能结构等,再对 技术要素组合并予以标准、规范,确定出几种有限状态的满足各种 车型的产品,至此即完成该产品平台化。现产品能满足的则以其作 为平台化产品,不能满足的则在在研或将来研发的车型上设计。
【参考文献】 [1]姚文轩.汽车零部件产品平台化研究及案例分析[D].上海:上海交通大学,2012. [2]杨茂华.浅谈整车平台与平台化开发[J].企业技术开发,2015,34(30):9-11+14.
汽车机械制造的零部件标准化与模块化
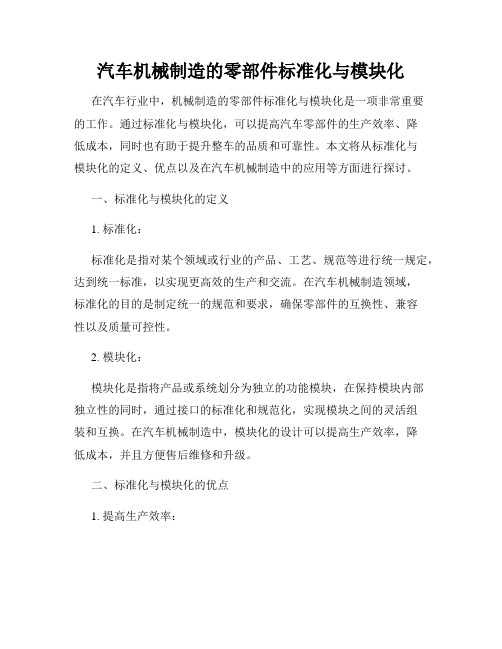
汽车机械制造的零部件标准化与模块化在汽车行业中,机械制造的零部件标准化与模块化是一项非常重要的工作。
通过标准化与模块化,可以提高汽车零部件的生产效率、降低成本,同时也有助于提升整车的品质和可靠性。
本文将从标准化与模块化的定义、优点以及在汽车机械制造中的应用等方面进行探讨。
一、标准化与模块化的定义1. 标准化:标准化是指对某个领域或行业的产品、工艺、规范等进行统一规定,达到统一标准,以实现更高效的生产和交流。
在汽车机械制造领域,标准化的目的是制定统一的规范和要求,确保零部件的互换性、兼容性以及质量可控性。
2. 模块化:模块化是指将产品或系统划分为独立的功能模块,在保持模块内部独立性的同时,通过接口的标准化和规范化,实现模块之间的灵活组装和互换。
在汽车机械制造中,模块化的设计可以提高生产效率,降低成本,并且方便售后维修和升级。
二、标准化与模块化的优点1. 提高生产效率:通过标准化与模块化的应用,可以减少生产过程中的重复工作,提高生产效率。
采用标准化零部件和模块化设计,可以缩短产品的研发周期和制造周期,提高汽车制造商的生产能力和产品的交付速度。
2. 降低成本:标准化与模块化设计可以实现零部件的批量生产和共享使用,减少重复开发和生产的成本。
此外,通过标准化设计,还可以降低供应链管理成本和库存成本,提高整体供应链的效率。
3. 提升品质和可靠性:标准化与模块化可以确保零部件的一致性和互换性,减少因不合格零部件使用而导致的质量问题。
同时,模块化设计也有助于提高产品的可靠性和可维护性,方便售后服务和维修。
三、标准化与模块化在汽车机械制造中的应用1. 零部件标准化:汽车机械制造中的零部件可以通过标准化来规范其设计、制造和交付过程。
通过建立统一的标准和规范,可以实现不同供应商生产的零部件的互换性,减少整体供应链的管理成本,并提高产品的质量和可靠性。
2. 模块化设计:在汽车机械制造中,模块化设计可以将整车划分为多个独立的功能模块,每个模块都有明确的接口和规范。
汽车下车身平台化设计方法研究

汽车下车身平台化设计方法研究汤湧,王丛,麻桂艳(华晨汽车工程研究院白车身工程室,辽宁沈阳110141)摘要:文章以我公司某平台车型为例,,主要介绍了一种平台化的下车身结构设计方法。
即通过合理的零件拆分和 零件设计分别满足平台车型造型变化、轴距变化、后悬变化及配置变化的需求,文章针对以上变化分别详细阐述平 台化设计方法。
平台化的设i t方法提高了车身零件的通用化率、缩短了牢型的开发周期,降低了单车的开发成本。
关键词:汽车;车身;平台化中图分类号:U462.1文献标识码:A文章编号:1671-7988(2018)06-110-03The Study on Platform Method of Car BodyTang Yong,Wang Cong,Ma Guiyan(Brilliance Automotive Engineering Research Institute BIW Section,Liaoning Shenyang 110141)Abstract: In this paper,a model of a platform in our company is taken as an example,Introduces a platform design method of underbody structure.Through the rational design of t he parts and components split respectively meet the platform models,styling change,wheelbase change,rear overhang changes and configuration changes,The platform design method is described for the above changes in this paper.The design method of the platform improves the universal rate of body parts, Shorten the development cycle of cars,Reduced the development cost of the car.Keywords: Automobile; Car Body; Car Body; PlatformCLC NO.: U462.1 Document Code: A Article ID: 1671-7988(2018)06-110-03刖g平台化的结构概念不仅可以满足频繁的车型变换需求,而且可以降低开发及生产成本,保证车型的竞争力[1]。
铝合金乘用车车身平台设计与开发

车身结构设计的目的。铝合金乘用车车身平台设计与开
发是庞大的系统工程,限于篇幅,本文仅从三方面内容进
加 强 横 梁 ,传
力路径缩减,
碰撞力由纵梁
经铸件直接传
递给门槛梁,
加之车身平台
图9 某铝合金车身SUV碰撞仿真连接 铸件失稳
设计存在纵梁 与门槛梁高差 过大的缺点。
两方面因素共
同导致连接铸
件失稳折弯问
题的发生。克
图10 燃油钢制车身碰撞传力路径 服 上 述 问 题 ,
需对连接铸件
进行结构加
强,甚至新建
接部位(如前纵梁和门槛梁部位的连接),铝合金铸件的
使用就尤为必要[3]。在连接铸件设计过程中可以采用结构
拓扑方法进行弯曲、扭转、前碰、侧碰等单一工况和由单
一工况叠加的多种复合工况加载分析。首先根据铸件周
边布置条件和搭接需求确定初始设计边界;然后按照应
变最小原则,得出各种工况下连接铸件加强筋的分布情
况;最后综合考虑成型要求,确定加强筋分布和厚度[4]。在
收、平台空间布局,关键点位精度起到至关重要的影响。
铝合金车身平台下车体共计分布六大铸件,分别是左右
减震器塔座铸件、左右前纵梁连接铸件、左右后纵梁连接
铸件。传统钢制车身钣金随形避让能力强。型材的加工是
挤出工艺,折弯和回弹控制是生产工艺的难点。车体作为
装配基体,焊装精度要求较高,应避免型材3D弯曲。在连
行设计要点 论述,分别是 平台技术方 向的平台布 置 设 计 、车 身技术方向
车身平台化开发策略研究

车身平台化开发策略研究随着汽车工业的不断发展,车身平台化开发策略越来越受到汽车制造商的关注。
车身平台化开发是指在保持车型独特性的前提下,将不同车型的设计、工艺、技术等核心元素集成到一个公共平台上,以提高汽车设计和制造的效率、降低成本,同时增强市场竞争力。
本文将探讨车身平台化开发策略的研究。
一、车身平台化开发策略的优势1. 降低成本车身平台化开发可以实现生产线的标准化和自动化,降低人力和物力成本,提高生产效率和质量,进而降低成本。
2. 增强市场竞争力通过将多款车型的设计、工艺、技术等核心元素集成到一个公共平台上,可以更加灵活地满足市场需求,提高产品的竞争力。
3. 提高研发效率由于不同车型共用同一个平台,可以节约研发时间和研发成本,提高研发效率。
二、车身平台化开发策略的实践经验1. 法国雷诺公司法国雷诺公司通过实行车身平台化开发,利用同一基础平台,生产不同品牌和车型的汽车,从而降低了生产成本,提高了生产效率和质量。
2. 德国大众公司德国大众公司推出了“模块化跨平台设计(MQB)”技术,通过同一汽车平台的多品牌生产,降低了生产成本,提高了效率和质量,同时实现了产品的多样化和市场的快速响应。
三、车身平台化开发策略的创新思路1. 引入新材料引入新材料,提高车身轻量化水平,增强排放性能,降低运营成本。
2. 加强数据分析加强对客户需求的数据分析,通过大数据技术,实现车型定制化,提高市场竞争力。
3. 无人驾驶技术应用随着无人驾驶技术的发展,通过将无人驾驶技术应用到车身平台化开发中,可以增强车辆的安全性和可靠性,提高生产效率,降低运营成本。
四、总结车身平台化开发具有降低成本、增强市场竞争力和提高研发效率等优势,其在实践中已经得到广泛应用。
未来,通过引入新材料、加强数据分析和应用无人驾驶技术,车身平台化开发策略将继续发挥其作用,为汽车工业的发展提供更多的支持。
车身平台化的优势在于降低成本、增强市场竞争力和提高研发效率。
汽车产品平台化模块化设计要则及案例分析_2010[1].1.13
![汽车产品平台化模块化设计要则及案例分析_2010[1].1.13](https://img.taocdn.com/s3/m/f9ffe839af45b307e87197b5.png)
1.5
•
实施平台战略应避免的问题
风险强度控制难度大:当汽车制造商们体验着在一个专用平台外以较低风 险制造出各种车型拓展产品的同时,如果他们已经发展和改进的基础平台 经证实是错误的,那么他们也许正在经受着更大的风险。 – 标准化工艺技术的一个缺点就是会在遍布众多的车型中使风险加倍, 使召回和重新设计潜在的费用非常昂贵。正如通用汽车公司近期因为 一个普通的刹车安全装置召回110万辆汽车,并为提供免费维修而使花 费超过了240万美元。 – 消费者的品位改变得很快(如从普通汽车到SUV),这便使得平台将做物 理上的修改或者其功能特性很有可能会同市场错位匹配。 – 工艺技术也会改变,尤其是汽车电子,因此平台不一定能够兼容这种 升级。 – 潜在地情况包括法律法规,公众焦点或者一次石油事件,这些都能够 使一个平台为了迎合不断增长的功能上的需求而在技术上错位。
1.4
•
实施平台化及模块化的好处
采取平台而生产的不同的车型在市场中更具有价值。 – 各具特色的汽车能更好地同目标消费者的需求相一致。 • 如有实用主义思想的美国消费者愿意花更高的价钱购买以运动性 能为主的变异汽车产品(如售价为五千美元的Subaru Outback和 本田CR-V远远胜过了其公司的主流产品Subaru Legacy和本田 Civic); – 脱离同一平台制造出的拓展产品通常通过品牌的强化能够给人以独特 感和优越感。 • 有1%的人“能从一辆卡车上得到更多”,GMC Sierras就同那些人 进行交易,并在事实上等同雪弗莱Silverado的装备上售出更高的 价钱。
零件
1.2
建立平台的四要素
尽管帕萨特和高尔夫的界面和零件不同,但发动机组装的程序是相似的:
敞开的发动机机厢
相同工艺流程:
汽车车身设计与制造工艺新技术
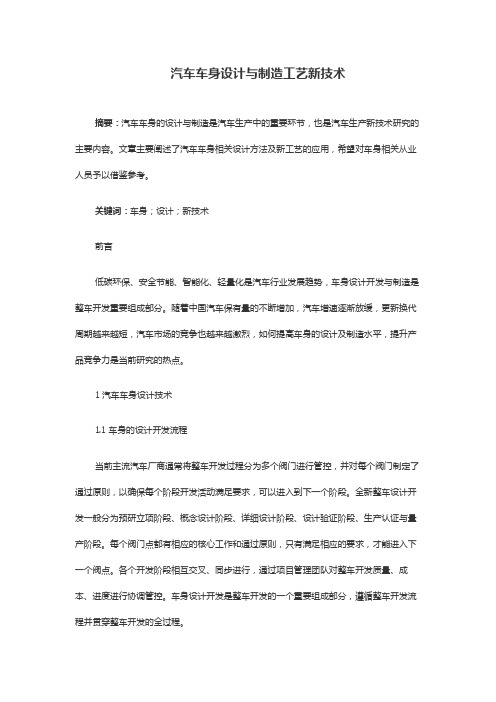
汽车车身设计与制造工艺新技术摘要:汽车车身的设计与制造是汽车生产中的重要环节,也是汽车生产新技术研究的主要内容。
文章主要阐述了汽车车身相关设计方法及新工艺的应用,希望对车身相关从业人员予以借鉴参考。
关键词:车身;设计;新技术前言低碳环保、安全节能、智能化、轻量化是汽车行业发展趋势,车身设计开发与制造是整车开发重要组成部分。
随着中国汽车保有量的不断增加,汽车增速逐渐放缓,更新换代周期越来越短,汽车市场的竞争也越来越激烈,如何提高车身的设计及制造水平,提升产品竞争力是当前研究的热点。
1汽车车身设计技术1.1车身的设计开发流程当前主流汽车厂商通常将整车开发过程分为多个阀门进行管控,并对每个阀门制定了通过原则,以确保每个阶段开发活动满足要求,可以进入到下一个阶段。
全新整车设计开发一般分为预研立项阶段、概念设计阶段、详细设计阶段、设计验证阶段、生产认证与量产阶段。
每个阀门点都有相应的核心工作和通过原则,只有满足相应的要求,才能进入下一个阀点。
各个开发阶段相互交叉、同步进行,通过项目管理团队对整车开发质量、成本、进度进行协调管控。
车身设计开发是整车开发的一个重要组成部分,遵循整车开发流程并贯穿整车开发的全过程。
1.2车身平台化模块化随着汽车行业竞争加剧以及消费者对汽车品质要求的不断提高,各大汽车厂商推出新车型的速度不断加快。
车身平台化、模块化开发的运用,不但可以大幅缩短研发的周期、降低开发成本,提升规模效益,而且可以有效降低技术风险、提高产品可靠性。
基于新的平台发展规划策略,丰田、大众、通用、日产等主流汽车企业越来越多的新车型逐步上市,增强了市场竞争力并取得了良好的经济效益。
国内自主品牌也从早期的完全逆向开发逐渐进入到正向开发阶段,并开始重视并加大平台化研究。
1.3车身新结构新材料的运用(1)车身新结构车身概念设计阶段通常会根据总布置和造型进行主体架构的设计构想,再进行详细结构设计。
概念设计阶段运用先进的仿真分析方法,不需要详细的3D几何模型就可构建前期概念有限元模型,进行大量有较大差异的方案分析并逐渐优化,按照先整体后局部的设计思路,在概念设计阶段确定车身整体框架结构。
汽车平台化应用与设计

◇科技 论坛◇
科技 强向导
21年第0 期 02 5
汽车平台化应用与设计
(. 1长城汽车股份有限公司技术中心 河北
田越强 , 李 景 , 张凤超 2 , 2 , 2 , 保定 0 1 0 ; . l省汽车工程技术研究 中心 7 0 0 2 ̄z l :
河北
保定பைடு நூலகம்
0 10 ) 7 0 0
【 要】 摘 汽车行业是一个资金 、 技术及 劳动 密集型的大产业 , 大投入 、 其“ 大产 出” 的传 统生产及 研发模式 , 需要相应车型达到一定的销售 规模 才能确保有盈利 的投资 回报。为保证投资回报率 , 汽车平台化 应运 而生, 文中分析 了汽车平 台化在i - ̄域的应用与设计 , %- t - 为汽车平 台化 设计应 用提供 了借鉴 , 缩短整车开发周期 , 降低 整车开发 成本 。 【 关键词 】 台化 ; 平 标准化 ; 系列化 ; 块化 ; 用化 模 通 O前 言 . 众所周 知 . 汽车行业 是一个 资金 、 技术及劳 动密集 型的大产业 , 其 “ 大投入 、 大产 出” 的传统生产及研 发模式 . 要相应车型达 到一定 的 需 销售规模才 能确保有盈利 的投资 回报 。作为后起之秀 的汽车大国 . 中 国汽 车行业 一直借鉴 欧美 日 汽车工业发达 国家“ 大投入 、 大产 出” 的产 研模式 。 如今汽车市场竞 争异 常激烈 , 不可能有所谓的“ 暴利” 如果还 , 按照传 统方式投入 巨资开发新车 型、 添置模具及先 进生产设备 . 于 对 那些 年销量不足 5 辆的车型 . 万 每辆 车分摊 的研发 、 人力及设备 折旧 等费用势必居高不下 . 这些车型很难有赢利能力。
整车开发的平台和架构方法
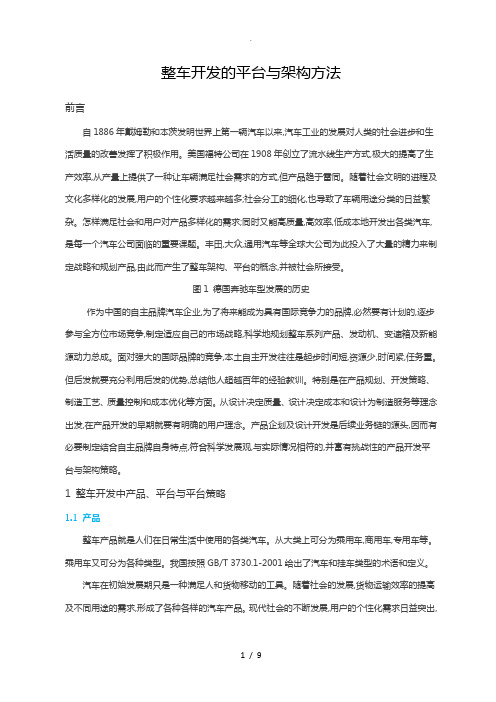
整车开发的平台与架构方法前言自1886年戴姆勒和本茨发明世界上第一辆汽车以来,汽车工业的发展对人类的社会进步和生活质量的改善发挥了积极作用。
美国福特公司在1908年创立了流水线生产方式,极大的提高了生产效率,从产量上提供了一种让车辆满足社会需求的方式,但产品趋于雷同。
随着社会文明的进程及文化多样化的发展,用户的个性化要求越来越多;社会分工的细化,也导致了车辆用途分类的日益繁杂。
怎样满足社会和用户对产品多样化的需求;同时又能高质量,高效率,低成本地开发出各类汽车,是每一个汽车公司面临的重要课题。
丰田,大众,通用汽车等全球大公司为此投入了大量的精力来制定战略和规划产品,由此而产生了整车架构、平台的概念,并被社会所接受。
图1 德国奔驰车型发展的历史作为中国的自主品牌汽车企业,为了将来能成为具有国际竞争力的品牌,必然要有计划的,逐步参与全方位市场竞争,制定适应自己的市场战略,科学地规划整车系列产品、发动机、变速箱及新能源动力总成。
面对强大的国际品牌的竞争,本土自主开发往往是起步时间短,资源少,时间紧,任务重。
但后发就要充分利用后发的优势,总结他人超越百年的经验教训。
特别是在产品规划、开发策略、制造工艺、质量控制和成本优化等方面。
从设计决定质量、设计决定成本和设计为制造服务等理念出发,在产品开发的早期就要有明确的用户理念。
产品企划及设计开发是后续业务链的源头,因而有必要制定结合自主品牌自身特点,符合科学发展观,与实际情况相符的,并富有挑战性的产品开发平台与架构策略。
1 整车开发中产品、平台与平台策略1.1 产品整车产品就是人们在日常生活中使用的各类汽车。
从大类上可分为乘用车,商用车,专用车等。
乘用车又可分为各种类型。
我国按照GB/T 3730.1-2001给出了汽车和挂车类型的术语和定义。
汽车在初始发展期只是一种满足人和货物移动的工具。
随着社会的发展,货物运输效率的提高及不同用途的需求,形成了各种各样的汽车产品。
汽车车身制造工艺同步工程浅析

汽车车身制造工艺同步工程浅析到目前为止,我国人民在交通出行方面选择私人汽车的比例已经越来越高。
在目前市场中,消费者群体规模也越来越趋向于饱和,在这样的情况下,汽车设计和制造行业未来发展的重点应当在于性能、环保等方面的改革和进步。
与时俱进,吸收先进设计理念,并且将优势明显的现代科技应用到汽车制造中来,已经成为了当下势在必行的首要任务。
为了进一步促进我国社会主义建设进程健康发展,缓解人文社会进步与自然环境之间的矛盾,如何能够降低成本,减少污染,成了接下来研究工作的重要侧重点。
标签:汽车车身设计;制造工艺新技术;未来发展1 汽车车身设计技术分析1.1 汽车车身设计流程分析现阶段,汽车主流厂商在进行汽车开发过程中,主要是利用多个阀门进行控制,并根据实际情况制定完善的通过原则,以保证各个环节的有效进行,为后续的开发鉴定良好的基础。
整个阶段可以分为预研立项阶段、概念设计阶段、详细设計阶段、试验阶段以及生产阶段,保证每一个阀门点充分发挥出自身的作用优势,进而有效的开展下一道工序,并实现各个阶段的研究开发,提升整车的质量提升,遵循现有的流程要求。
1.2 车身设计的平台化与模块化人们生活水平的提升促使人们对汽车的需求逐渐增大,大量的汽车企业应时代而生,导致市场压力增大,各大汽车厂商为提升自身的竞争力,加快新型车的研究,以满足人们的需求。
车身设计的平台化与模块化发展是当前的重点内容,可以有效的缩短研发周期,帮助企业降低在研发环节的成本投入,充分发挥出技术优势,保证产品的性能质量。
灵活应用新平台规划策略优势,扩大新型车型种类,促使企业提升自身的竞争力与经济效益,逐渐实现大平台化发展。
1.3 车身新结构材料的创新应用在进行车身结构设计过程中,是以总布置和造型框架为基础进行构想,结合实际情况进行设计构想,如灵活运用当前的仿真分析,进行有限元模型构建,建立整体的设计思路,形成框架优化设计,以满足当前的需求,并提升车身的弯扭刚度与耐久性,提升整体质量。
车身平台轻量化设计方法研究

车身平台轻量化设计方法研究叶宝文;吴纯福;陈东;耿富荣【摘要】文章以某国产车型平台化开发时所用的轻量化设计方法为研究对象,介绍从平台原型车到同平台的系列车型开发过程引入基于特征参数化概念开发技术、结构拓扑优化、几何形状优化、料厚优化、复合材料使用等设计方法,对比、分析平台车型进行轻量化设计前后的弯曲刚度、扭转刚度、模态等性能变化,在满足车身性能前提下减重,为车身平台轻量化提供了有效设计方法.【期刊名称】《汽车实用技术》【年(卷),期】2017(000)020【总页数】4页(P42-45)【关键词】平台轻量化;车身平台;设计方法【作者】叶宝文;吴纯福;陈东;耿富荣【作者单位】广汽研究院,广东广州 510000;广汽研究院,广东广州 510000;广汽研究院,广东广州 510000;广汽研究院,广东广州 510000【正文语种】中文【中图分类】U467.1CLC NO.: U467.1 Document Code: A Article ID: 1671-7988 (2017)20-42-04 目前国内平台化技术处于发展时期,每个主机厂的平台化方案策略不尽相同,一般而言,主流平台设计思路是采用相同关键尺寸锁定的底盘设计、相同发动机布置等配合框架一致的车身结构及布置空间,由原型车衍生出更多类型的平台车型或通过不同的车身子模块组合得到满足高性能要求的车身结构,由于平台开发是产品群开发模式,面对日趋严重的能源问题、节能减排及开发成本控制,车身平台轻量化则成为开发过程中必不可少的关键环节之一。
为开发满足高性能、高刚度的产品群车身结构,在平台初期的概念设计阶段就需根据平台整车开发输入,确定车身平台的开发思路、车身平台拓展性、平台车身的性能目标定义,通过CAE等先进分析方法对计划内开发车型进行整体性能优化,找到影响平台车身性能的关键结构,通过有方向性、针对性进行结构优化设计,在平台开发过程中从材料轻量化、结构轻量化、架构轻量化、料厚等方面进行轻量化设计,从而使每个平台车型的性能达到最佳水平和可持续升级且富有竞争力。
- 1、下载文档前请自行甄别文档内容的完整性,平台不提供额外的编辑、内容补充、找答案等附加服务。
- 2、"仅部分预览"的文档,不可在线预览部分如存在完整性等问题,可反馈申请退款(可完整预览的文档不适用该条件!)。
- 3、如文档侵犯您的权益,请联系客服反馈,我们会尽快为您处理(人工客服工作时间:9:00-18:30)。
下车身平台化设计方法研究
摘要:近年来,我国的汽车行业发展迅速,汽车制造行业也有了很大进展。
文章主要介绍了一种平台化的下车身结构设计方法。
即通过合理的零件拆分和零件设计分别满足平台车型造型变化、轴距变化、后悬变化及配置变化的需求,文章针对以上变化分别详细阐述平台化设计方法。
平台化的设计方法提高了车身零件的通用化率、缩短了车型的开发周期,降低了单车的开发成本。
关键词:汽车;车身;平台化
引言
在汽车研发过程中,为了快速适应市场的需求、避免大量的技术集成、零部件设计、仿真及实验验证等资源的重复和浪费,平台化架构思想逐渐被各大主机厂重视。
通过平台化架构的建立,实现技术、零件、设计等的共用,既降低了研发费用,也缩短了产品开发周期。
车身平台化架构则是在整车平台化的框架内指导同平台车型的设计和开发,做到相同或相似车身结构的共用,同时又能满足车身结构主要力学性能、质量需求和成本限制等。
1车身平台化概念
车身平台化这一概念是指汽车从开发阶段到生产制造过程中的设计方法、设备基础、生产工艺、制造流程乃至车身核心零部件及质量控制的一整套系统。
汽车平台技术发展到一定阶段,零部件的通用率不断提高,车身各部分(主要指下车体)总成,例如前机舱总成、前地板总成、后地板总成等都能像乐高积木一样以模块的形式自由组合,从而厂商可以在一个平台上开发出不同级别、不同类型的车型来。
2平台化车身架构开发流程
车身平台化开发策略可实现同一平台下车身的主要结构共用,在开发不同车型时只需要根据不同车型的具体要求和限制更改部分结构即可。
进而,采用车身结构多目标优化方法,把共用结构看作预留非设计空间,需要更改的结构看作设计空间。
通过拓扑优化方法计算和解读车身结构的最佳载荷路径,根据具体车型相关性能要求确定主要受力构件的截面尺寸,初步规划平台化车身结构的尺寸、性能及质量。
具体如下:1)基本车型选择。
以平台化架构的主导车型为基本型(一般为三厢车),可以拓展为SUV和MPV。
2)定义几何空间。
根据车身外部造型、底盘布置和人机工程要求,除掉开闭件、机舱和后行李舱,初步定义车身的几何空间。
采用有限元前处理软件,对几何空间进行建模及网格生成,所采用的有限单元为四面体或者六面体等参单元,材料为钢。
3)定义设计空间。
将需要优化的结构定义为设计空间,根据载荷的分布,设计空间有限元网格的分布及其数量会发生变化。
4)定义非设计空间。
开闭件洞口线、地板上一些固定点位置及平台化架构内的通用结构件在拓扑优化中不需要变更,可将其定义为非设计空间。
5)基本约束条件。
将设计空间体积变化百分数定义为基本约束条件,定义SIMP法的惩罚因子为r=3。
6)载荷工况。
载荷工况可根据相关技术标准、法规及要求设定,包括弯、扭载荷,碰撞载荷等;另外,根据拓扑优化的特点,碰撞载荷需要转化为线性静态载荷。
7)工程约束。
工程约束重要考虑待开发车型底盘、动力总成布置、人机工程、制造工艺和不同车型结构特征的要求。
8)拓扑优化。
采用商业软件Optistruct,将结构的柔度(应变的)最小化定义为优化目标。
9)根据不同工程约束下车身结构的拓扑优化结果,确定结构布局及材料密度,得到最佳的载荷传递路径。
3汽车下车身平台化设计方法
下车体总成由前机舱总成、前地板总成、后地板总成组成,下车体的框架结
构作为平台车身刚强度以及抗撞性等性能的保障至关重要,现将下车体平台框架
进行如下定义。
前机舱采取封闭多环形设计,传力稳定,能有效地吸收正面和偏
置碰撞的能量并抵抗碰撞冲击力,前围板横梁结构尤其为抵抗发动机入侵乘员舱
有着重要的作用。
下车体主框架纵梁布置采用前段2通道-中段6通道-后段2通
道的传力模式,有效分散正面碰撞的冲击力,最大程度的保护中部乘员舱的完整性;主框架的纵梁分布模式也保证车身弯曲刚强度,直接提高了乘员的主观颠簸感受。
下车体主框架横梁梁均采用贯通式横梁,形成5条传力通道,可以有效抵抗
侧面碰撞冲击力,并提高车身的扭转刚强度。
下车体主体结构形成井字型框架,
该框架的横梁和纵梁互通传力,为基础平台乘员舱提供稳定的刚强度以及抗撞性能。
下车身结构示意图如图1所示,阐述平台化设计方法。
3.1造型变化
1)流水槽总成。
将流水槽总成拆分为流水槽、风挡横梁上板和风挡横梁下板。
流水槽全系通用,风挡横梁上、下板随玻璃造型全系开发。
2)A柱内板总成将A
柱内板总成拆分为A柱上内板和A柱下内板两个零件,A柱上内板与造型相关,
通过新开发A柱上内板匹配不同的造型。
A柱下内板平台通用。
上、下内板分缝
设计时尽量靠近Z向下方,这样对前门止口不会有过多约束;又要将线束过孔设
计在一个零件上,这样能保证胶堵的密封性能。
图1下车身结构示意图
3.2轴距变化
1)前地板总成。
将前地板总成后端设计为长度可变结构,通过此处结构实现轴距的变化。
我公司某平台车型存在三种轴距,差值分别为100mm和170mm。
在前地板总成后端分缝处前移100mm和170mm设计分缝,保证每次分缝的断面
相同,即可采用开口拉延的形式使用最大零件的模具,不同的料片尺寸实现同模
具生产三款轴距车型的零件。
使用这种设计方法可以保证前地板总成上五个零件:左右前地板、中通道、左右前地板下纵梁同模具生产不同车型零件。
2)门槛内
板总成。
将门槛内板总成在后门止口右下角圆角前端145mm处分缝,设计为门
槛前段与门槛后段。
门槛前段设计为平台通用,门槛后段为适应不同造型的后门
止口走势全新开发。
平台通用的门槛前段X长度为1374mm。
3.3后悬变化
1)后地板总成。
将后地板总成拆分为后地板及后地板左右补板。
通过后地板前端的伸长和缩短实现后悬的变化,因保证轮罩的位置不变,通过后地板补板后
端长度的变化实现后悬的变化。
后地板总成上的零件同样采用相同的模具生产不
同的零件。
2)后纵梁总成。
将后纵梁总成拆分为后纵梁前段及后纵梁后段,后
纵梁前段为平台通用件,通过全新开发后纵梁后段实现后悬长度的变化。
后纵梁
前段考虑布置下三个定位孔的空间,后纵梁后段的长度设计时考虑最短车型可以
布置下后拖车钩的结构。
4平台化车身架构载荷传递路径优化分析
基于平台化的车身开发策略,在车身结构概念设计阶段,根据法规和市场对
汽车各项性能的要求,对平台化基础车身结构施加不同的工程约束,为目标车型
的结构设计提供方向性的思路。
事实上,对车身结构传力路径的研究旨在保证汽
车在发生碰撞时,驾乘舱内乘客的生命不受威胁,通过传力路径的研究可合理有
效地规划车身承载构件的分布,避免或减少撞击力对驾乘舱的作用。
同时,结合
材料及结构的性能需求,以达到汽车轻量化的目标。
在车身前期开发阶段,为探索合理的车身结构规划。
结语
综上所述,通过平台化结构的设计方法可以实现同平台车型不同造型、不同轴距、不同后悬及不同配置车型的生产。
该种设计方法使下车身的通用化率最高可达99%以上。
同时,平台化的设计方法可缩短开发周期,降低开发成本,增加车型上市的速度,提高车型市场竞争水平。
参考文献
[1]鞠晓峰.车身平台化开发策略研究[J].汽车技术,2012(2):7-10.[2]张亚萍.浅析汽车平台演进和模块化战略[J].汽车工业研究,2015(1):27-31.
[3]黄向东.高拓展性模块化车身架构的研究和应用[J].汽车工程,2016(9):1101-1106.
[4]吴纯福.车身平台兼容性设计与运用[J].汽车实用技术,
2017(15):58-60.。