结晶器在连铸过程中的应用
分析结晶器电磁搅拌对连铸坯质量的影响

分析结晶器电磁搅拌对连铸坯质量的影响摘要:连铸坯是炼钢炉炼成的钢水经过连铸机铸造后所得的产品。
其应用领域十分广泛,国内外在机械工程设备方面都在使用连铸坯制件。
其中,一些钢用的连铸坯可以直接轧钢,制成管、板、型钢等。
连铸坯在经过结晶器电磁搅拌后能够有效改善一些存在缺陷的地方。
基于此,本文对结晶器电磁搅拌、连铸坯概念以及相关实验进行简要分析。
关键词:结晶器;电磁搅拌;连铸坯引言:连铸坯中最关键的问题就是其中心偏析、夹杂物以及中心缩孔等严重影响铸坯的内部质量。
电磁搅拌是最常使用的连铸生产技术,它通过电磁力来优化消除结晶器内钢水过热度。
铸坯在经过电磁搅拌后其等轴晶率会有明显提高,从而得到良好凝固组织的铸坯,使得成品性能得到改善。
可以有效地解决连铸坯中心缩孔、纯净度等问题。
一、结晶器电磁搅拌及连铸坯概述连铸坯是钢水通过连续铸钢机铸成的钢坯。
连续铸钢技术可以把生产钢水到钢坯的整个过程进行简化,不需要经过初轧过程。
因此,连铸坯具备生产成本低、金属获得率高以及劳动条件好等一系列优点。
目前,连铸坯已是轧钢生产的重要原料。
然而,连铸坯也有一定的缺陷。
例如,一般疏松、中心疏松、锭型偏析、一般点状偏析、边缘偏析、皮下气泡、内部气泡、缩孔残余、翻皮、白点、轴心晶体裂缝、非金属夹杂物和心部裂纹等。
在低倍检验中会出现中心疏松、缩孔、中心偏析、表面角部裂纹、表面边部裂纹等缺陷。
电磁搅拌就是借助在铸坯的液相穴内感生的电磁力强化液相穴内钢水的运动,由此强化钢水的对流、传热和传质过程,从而控制铸坯的凝固过程,对提高铸坯质量具有积极的作用。
其中,结晶器电磁搅拌是目前最常见的、适用于各类连铸机的装置,它对改善铸坯表面质量、细化晶粒和减少铸坯内部夹杂及中心疏松等都有明显的作用。
一般情况下,为避免影响液面自动控制装置的使用,通常将其安装在结晶器的下部。
结晶器电磁搅拌的作用有以下几点:第一,改善铸坯表面质量。
铸坯在结晶器下面其表面呈现凝固的状态,此时可以将搅拌器置于结晶器的弯月面处,以起到对铸坯表面凝固开始前对其“清洗”的作用。
344-其他资源-连铸机的结晶器

2.6 结晶器☐结晶器是连铸机非常重要的部件,称之为连铸设备的“心脏”。
钢液在结晶器内冷却初步凝固成一定坯壳厚度的铸坯外形,并被连续地从结晶器下口拉出,进入二冷区。
结晶器应具有良好的导热性和刚性,不易变形和内表面耐磨等优点,而且结构要简单,便于制造和维护。
☐按结晶器外形可分为直结晶器和弧形结晶器。
直结晶器用于立式、立弯式及直弧形连铸机,而弧形结晶器用在全弧形和椭圆形连铸机上。
☐从结构来看,有管式结晶器和组合式结晶器。
小方坯及矩形多采用管式结晶器,而大型方坯、矩型坯和板坯多采用组合式结晶器。
管式结晶器的结构如图所示。
其内管为冷拔异形无缝铜管,外面套有钢质外壳,钢管与铜套之间留有约7mm的缝隙通以冷却水,即冷却水缝。
铜管与钢套可以制成弧形或直形。
铜管的上口通过法兰用螺钉固定在钢质的外壳上,铜管的下口一般为自由端,允许热胀冷缩,但上下口都必须密封。
结晶器外套是圆形的。
外套中部有底脚板,将结晶器固定在振动框架上。
结晶器铜制壁厚10-15mm,磨损后可加工修复,但最薄不能小于3-6mm。
1-O形密封圈;2-润滑法兰;3-O形密封圈;4-铜管;5-压紧法兰;6-压紧弹簧;7-排水管;8-足辊组合式结晶器是由4块复合壁板组合而成。
每块复合壁板都是由铜质内壁和钢质外壳组成。
在与钢壳接触的铜板面上铣出许多沟槽形成中间水缝。
复合壁板用双螺栓连接固定,冷却水从下部进入,流经水缝后从上部排出。
4块壁板有各自独立的冷却水系统。
在4块复合壁板内壁相结合的角部,垫上厚3-5mm并带来45°倒角的铜片,以防止铸坯角裂。
现已广泛采用宽度可调的板坯结晶器。
可用手动、电动或液压驱动调节结晶器的宽度。
内壁铜板厚度在20-50mm,磨损后可加工修复,但最薄不能小于10mm。
随着连铸机拉坯速度的提高,出结晶器下口的铸坯坯壳厚度越来越薄;为了防止铸坯变形或出现漏钢事故,采用多级结晶器技术。
多级结晶器即在结晶器下口安装足辊、铜板或冷却格栅。
7月-结晶器热流监测系统(MTM)在梅钢2号连铸机上的应用
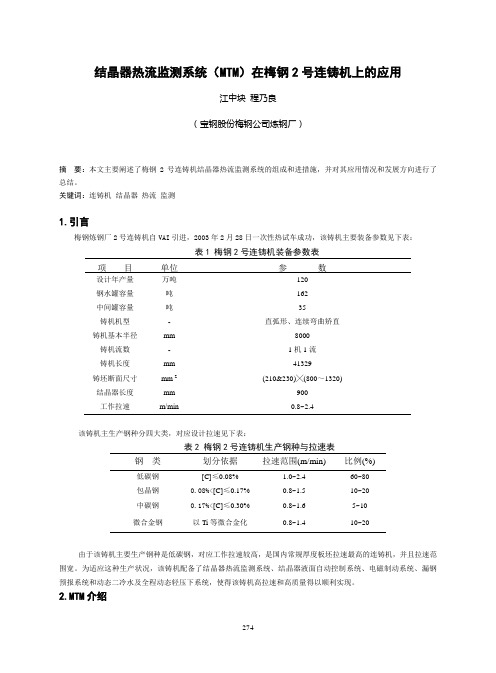
结晶器热流监测系统(MTM)在梅钢2号连铸机上的应用江中块程乃良(宝钢股份梅钢公司炼钢厂)摘要:本文主要阐述了梅钢2号连铸机结晶器热流监测系统的组成和进措施,并对其应用情况和发展方向进行了总结。
关键词:连铸机结晶器热流监测1.引言梅钢炼钢厂2号连铸机自VAI引进,2003年2月28日一次性热试车成功,该铸机主要装备参数见下表:表1 梅钢2号连铸机装备参数表项目单位参数设计年产量万吨120钢水罐容量吨162中间罐容量吨35铸机机型- 直弧形、连续弯曲矫直铸机基本半径mm 8000铸机流数- 1机1流铸机长度mm 41329铸坯断面尺寸mm 2(210&230)╳(800~1320)结晶器长度mm 900工作拉速m/min 0.8~2.4该铸机主生产钢种分四大类,对应设计拉速见下表:表2 梅钢2号连铸机生产钢种与拉速表钢类划分依据拉速范围(m/min) 比例(%)低碳钢[C]≤0.08% 1.0~2.4 60~80包晶钢0.08%<[C]≤0.17% 0.8~1.5 10~20中碳钢0.17%<[C]≤0.30% 0.8~1.6 5~10微合金钢以Ti等微合金化0.8~1.4 10~20由于该铸机主要生产钢种是低碳钢,对应工作拉速较高,是国内常规厚度板坯拉速最高的连铸机,并且拉速范围宽。
为适应这种生产状况,该铸机配备了结晶器热流监测系统、结晶器液面自动控制系统、电磁制动系统、漏钢预报系统和动态二冷水及全程动态轻压下系统,使得该铸机高拉速和高质量得以顺利实现。
2.MTM介绍结晶器热流监测系统由西门子公司开发,该系统置于L1控制系统,实时跟踪结晶器四个面的铜板热流强度变化趋势,供操作和工艺技术人员参考使用。
该系统计算原理主要是通过冷却水温差与水流量来计算各个面的平均热流密度,再给合现场经验值判断热流的正常与否。
下图1为现场使用的L1监控画面。
图1 2号连铸机结晶器热流监测系统画面下文将主要阐述梅钢2号连铸机结晶器热流监测系统的计算原理与控制过程。
连铸板坯倒角结晶器优化设计及应用

连铸板坯倒角结晶器优化设计及应用连铸板坯倒角结晶器是铸造行业中的一项关键设备,它可以产生优质的板坯,同时提高生产效率和降低成本。
然而,现有的连铸板坯倒角结晶器存在一些不足之处,例如流量不均匀、结晶器内部存在死角等。
因此,优化设计和应用连铸板坯倒角结晶器显得尤为重要。
一、连铸板坯倒角结晶器的定义连铸板坯倒角结晶器是连铸线中一种重要的设备。
它是铸造设备中用于制造高质量板坯的主要机器之一,其主要作用是在连铸过程中将液态金属均匀地输送到结晶器中,并通过坯内气泡和悬浮物的消除,使得板坯表面质量得到提高。
二、连铸板坯倒角结晶器的不足之处连铸板坯倒角结晶器在使用过程中存在一些不足之处。
首先,结晶器流量分配不均匀,导致板坯表面质量得不到保证。
其次,结晶器内部存在死角和难以清洗的区域,严重影响连铸板坯的品质。
此外,目前的结晶器设计以经验为主,缺乏系统性和标准化的研究,造成了结晶器设计水平低下、使用成本高和设备寿命短等问题。
三、连铸板坯倒角结晶器的优化设计为了解决上述问题,我们可以对连铸板坯倒角结晶器进行优化设计。
优化设计主要包括流量优化、结构优化和材料优化等。
1、流量优化:在结晶器内加入分流器,使进入结晶器的金属流量分布均匀,同时加强进口处的金属混合。
通过调整导流板、冷却水管和送料系统等组件来优化结晶器内的金属流量,从而保证板坯表面的均匀性。
除此之外,可以采用流场数值模拟的方法,对结晶器的气体、液态金属和固态晶体流场进行计算和模拟。
2、结构优化:由于连铸板坯倒角结晶器中存在很多死角和难以清洗的区域,因此我们可以通过调整结晶器的结构和灵活的取料系统来改进结晶器内部的流动性。
在结晶器的角落和内壁设计凸缘,让结晶器内的气泡和悬浮物聚集在防凸缘处,避免了气泡和悬浮物的固化成本体,减少了结晶器内结晶的阻塞作用。
此外,通过采用高强度、耐磨材料和高温耐受性材料,可以增强结晶器的使用寿命。
3、材料优化:不同材质的全部性能和特殊要求也是设计过程中需要考虑的重要因素,如耐磨性、耐热性、承压性和可加工性等。
常规板坯连铸机结晶器技术

常规板坯连铸机结晶器技术【保护视力色】【打印】【进入论坛】【评论】【字号大中小】2006-12-0711-07杨拉道刘洪王永洪刘赵卫邢彩萍田松林 (西安重型机械研究所)结晶器是连铸机中的铸坯成型设备, 是连铸机的核心设备之一。
其作用是将连续不断地注入其内腔的钢液通过水冷铜壁强制冷却,导出钢液的热量,使之逐渐凝固成为具有所要求的断面形状和一定坯壳厚度的铸坯,并使这种芯部仍为液相的铸坯连续不断地从结晶器下口拉出.为其在以后的二冷区域内完全凝固创造条件。
在钢水注入结晶器逐渐形成一定厚度坯壳的凝固过程中.结晶器一直承受着钢水静压力、摩檫力、钢水热量的传递等诸多因素引起的的影响.使结晶器同时处于机械应力和热应力的综合作用之下.工作条件极为恶劣.在此恶劣条件下结晶器长时间地工作.其使用状况直接关系到连铸机的性能.并与铸坯的质量与产量密切相关。
因此.除了规范生产操作、选择合适的保护渣和避免机械损伤外.合理的设计是保证铸坯质量、减小溢漏率、提高其使用寿命的基础和关键。
板坯连铸机一般采用四壁组合式(亦称板式)结晶器.也有一个结晶器浇多流铸坯的插装式结构。
结晶器主要参数的确定1 结晶器长度H结晶器长度主要根据结晶器出口的坯壳最小厚度确定。
若坯壳过薄.铸坯就会出现鼓肚变形.对于板坯连铸机.要求坯壳厚度大于10~15mm。
结晶器长度也可按下式进行核算:H=(δ/K)2Vc+S1+S2 (mm)式中δ——结晶器出口处坯壳的最小厚度.mmK——凝固系数.一般取K=18~22 mm/min0.5Vc——拉速.mm/minS1——结晶器铜板顶面至液面的距离.多取S1=100 mmS2——安全余量.S=50~100 mm对常规板坯连铸机可参考下述经验:当浇铸速度≤2.0m/min时.结晶器长度可采用900~950mm。
当浇铸速度2.0~3.0m/min时.结晶器长度可采用950~1100mm。
当浇铸速度≥3.0m/min时.结晶器长度可采用1100~1200mm。
炼钢厂结晶器使用管理制度
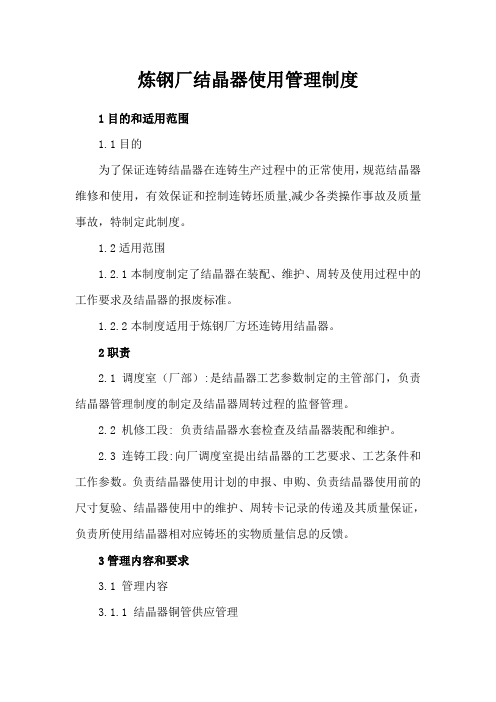
炼钢厂结晶器使用管理制度1目的和适用范围1.1目的为了保证连铸结晶器在连铸生产过程中的正常使用,规范结晶器维修和使用,有效保证和控制连铸坯质量,减少各类操作事故及质量事故,特制定此制度。
1.2适用范围1.2.1本制度制定了结晶器在装配、维护、周转及使用过程中的工作要求及结晶器的报废标准。
1.2.2本制度适用于炼钢厂方坯连铸用结晶器。
2职责2.1调度室(厂部):是结晶器工艺参数制定的主管部门,负责结晶器管理制度的制定及结晶器周转过程的监督管理。
2.2 机修工段: 负责结晶器水套检查及结晶器装配和维护。
2.3 连铸工段:向厂调度室提出结晶器的工艺要求、工艺条件和工作参数。
负责结晶器使用计划的申报、申购、负责结晶器使用前的尺寸复验、结晶器使用中的维护、周转卡记录的传递及其质量保证,负责所使用结晶器相对应铸坯的实物质量信息的反馈。
3管理内容和要求3.1 管理内容3.1.1 结晶器铜管供应管理3.1.1.1 厂备件库根据调度室提供的工艺参数和连铸工段申报报的结晶器铜管用量计划,向公司采购部门申报结晶器铜管货源。
入厂后由厂备件库组织,同连铸工段主管结晶器人员共同验收;连铸工段对准备更换的每一只新铜管进行测量、填写结晶器周转卡。
厂备件库负责每支新铜管的编号工作。
3.1.1.2未验收或验收不合格的结晶器铜管不得使用。
连铸工段应以书面形式通知调度室及备件库确认,由调度室汇报主管厂长后,拿出处理意见。
3.1.2 结晶器铜管使用管理3.1.2.1新铜管由连铸工段领用、测量并记录在周转卡上,结晶器装配时由结晶器装配人员进行相关计录,内容包括:结晶器号、铜管号、水缝、零段水管对弧等情况。
3.1.2.2连铸工段结晶器管理专职人员应在现场了解结晶器组装情况。
3.1.2.3连铸工段应指定专人负责连铸三班在线结晶器每个浇次后的检测,发现问题及时更换,新换结晶器安装到位后及时安装水嘴。
3.1.2.4由连铸机长负责组织在线结晶器的检查,每个浇次后检测内容:铜管内腔(弯月面)的镀层磨损情况,铜管内壁有无明显的划痕,零段水管喷嘴状态。
连铸板坯倒角结晶器及应用

牟桂梅 孙金福
( 秦 皇岛首钢 长白机械有限责任公司 河北秦皇 岛)
摘要 关键词 分析连铸板坯角部横 裂纹形成 , 采用倒 角结晶器解决连铸板坯角部横 裂纹缺 陷问题 。 连铸板坯 倒 角结 晶器 角部横裂纹
B
应用
中 图分 类 号
概 述
连铸板坯倒角结 晶器角部的最佳倒角尺寸取 3 5 m m ̄ 3 5 m m 比较合理 ,能使矫直时连铸 板坯 的角部温度高于钢 的高温脆 性
5 ~ 2 0 I T l m, 由铸坯表面 内部沿钢的晶界展开 。低碳钢 、 低合金 钢 和含铌 、 钒、 钛微合金钢铸坯的角部横 裂纹发生率高于其他成分 钢, 连铸板坯角部横 裂纹形成分析如下 。 1 . 连铸板坯在钢的高温脆性 区矫直产生角部横裂纹 连铸板坯角部横裂纹 的产 生与钢的高温脆性 温度 区( 7 0 0 ~ 9 0 0℃) 有关 , 实际连铸生产 中 , 多数 钢种的高温脆性 区在 7 0 0 — 9 0 0℃之间 。在连铸矫直 区域 , 如铸坯边角部温度位于钢的高温
角部横裂纹缺陷的铸坯 , 造成降低金属收得率 , 增加生产成本 。 通过对连铸板坯结 晶器角部结构优化设计 ,将直角结晶器
3 . 首秦直角连铸板坯角部横 裂纹成 因分析 首秦直角连铸板坯角部横裂纹发生在铸坯 宽面与窄 面交汇 的角部 以及宽面侧偏离角部的部位 , 垂直铸坯拉坯方向 , 角部横 裂纹长度 5 ~ 1 5 m m, 深度 4 ~ 1 2 m m, 中碳含铌钢直角连铸坯角部 横裂纹形貌是从铸坯表面一直延伸至基体 内部 , 呈穿晶断裂。 连铸板坯角部横裂纹起源于角部粗 大原奥 氏体 晶界 ,在角
动、 优 化连铸二冷配水及提高连铸设备安装精度等 , 使角部横裂
连铸的生产工艺流程

连铸的生产工艺流程:将装有精炼好钢水的钢包运至回转台,回转台转动到浇注位置后,将钢水注入中间包,中间包再由水口将钢水分配到各个结晶器中去。
结晶器是连铸机的核心设备之一,它使铸件成形并迅速凝固结晶。
拉矫机与结晶振动装置共同作用,将结晶器内的铸件拉出,经冷却、电磁搅拌后,切割成一定长度的板坯。
连铸钢水的准备一、连铸钢水的温度要求:钢水温度过高的危害:①出结晶器坯壳薄,容易漏钢;②耐火材料侵蚀加快,易导致铸流失控,降低浇铸安全性;③增加非金属夹杂,影响板坯内在质量;④铸坯柱状晶发达;⑤中心偏析加重,易产生中心线裂纹。
钢水温度过低的危害:①容易发生水口堵塞,浇铸中断;②连铸表面容易产生结疱、夹渣、裂纹等缺陷;③非金属夹杂不易上浮,影响铸坯内在质量。
二、钢水在钢包中的温度控制:根据冶炼钢种严格控制出钢温度,使其在较窄的范围内变化;其次,要最大限度地减少从出钢、钢包中、钢包运送途中及进入中间包的整个过程中的温降。
实际生产中需采取在钢包内调整钢水温度的措施:1)钢包吹氩调温2)加废钢调温3)在钢包中加热钢水技术4)钢水包的保温中间包钢水温度的控制一、浇铸温度的确定浇铸温度是指中间包内的钢水温度,通常一炉钢水需在中间包内测温3次,即开浇后5min、浇铸中期和浇铸结束前5min,而这3次温度的平均值被视为平均浇铸温度。
浇铸温度的确定可由下式表示(也称目标浇铸温度):T=TL+△T 。
二、液相线温度:即开始凝固的温度,就是确定浇铸温度的基础。
推荐一个计算公式:T=1536-{78[%C]+7.6[%Si]+4.9[%Mn]+34[%P]+30[%S]+5.0[%Cu]+3.1[% Ni]+1.3[%Cr]+3.6[%Al]+2.0[%Mo]+2.0[%V]+18[%Ti]}三、钢水过热度的确定钢水过热度主要是根据铸坯的质量要求和浇铸性能来确定。
钢种类别过热度非合金结构钢10-20℃铝镇静深冲钢15-25℃高碳、低合金钢5-15℃四、出钢温度的确定钢水从出钢到进入中间包经历5个温降过程:△T总=△T1+△T2+△T3+△T4+△T5△T1出钢过程的温降;△T2出完钢钢水在运输和静置期间的温降(1.0~1.5℃/min);△T3钢包精炼过程的温降(6~10℃/min);△T4精炼后钢水在静置和运往连铸平台的温降(5~1.2℃/min);△T5钢水从钢包注入中间包的温降。
连铸连轧生产:连铸过程冷却控制

4.5.1结晶器一次冷却控制
2 冷却水压力 冷却水压力是保证冷却水在结晶器水缝中流动的主要动力,冷却水压力 一般控制在0.6~1.0MPa。例如某钢厂正常供水压力为0.8MPa,报警压力为 0.6MPa。在实际生产过程中,结晶器供水压力是需要重点监控的工艺参数, 出现压力波动,必须及时查清原因,采取措施。 3 冷却水温度 冷却水温度在20℃~40℃范围内波动时,结晶器总热流变化不大。结晶 器进出温度差一般控制在5~8℃,出水温度约在45~50℃。出水温度过高, 结晶器容易形成水垢,影响传热效果。冬季,如果开机前水温比较低,需要 提前利用加热器进行加热,确保冷却水温达到工艺要求;夏季,水温超过 40℃后,需要开启冷却塔进行冷却降温。
4.5.2二冷区二次冷却控制
二冷区二次冷却控制的主要内容包括确定二次冷却强度、二次冷却方式 、冷却水量的分配以及二次冷却控制方式。
1确定冷却强度的原则 (1)冷却强度由强到弱的原则。由结晶器一次冷却的连铸坯拉出结晶器 后进入二冷区,此时铸坯坯壳比较薄,坯壳内部大部分还是未凝固的钢液, 坯壳的热阻小,此时加大冷却强度可以快速冷却连铸坯,使得坯壳厚度快速 变厚以抵抗钢水静压力对凝固坯壳产生的不利影响。随着坯壳厚度不断变厚 ,坯壳的导热热阻逐渐增加,此时需要不断降低冷却强度,防止铸坯表面热 应力过大产生裂纹。
4.5.2二冷区二次冷却控制
C 目标表面温度动态控制 控制模型每隔一段时间计算一次铸坯表面温度,并与考虑了二冷配水原 则所预先设定的目标表面温度进行比较,根据比较的差值结果给出各冷却区 冷却水量,以使铸坯表面温度与目标表面温度相吻合。该控制方式的难点是 目标表面温度计算模型的准确性。
Hale Waihona Puke 谢谢同学们!4.5.2二冷区二次冷却控制
简述结晶器在连铸生产中的作用

简述结晶器在连铸生产中的作用连铸是指将熔化的金属直接浇铸成连续的坯料,是铸造技术中一种重要的工艺。
在连铸过程中,结晶器是起着至关重要作用的设备之一。
它位于连铸机的浇注部位,主要用于控制坯料的结晶过程和形成坯料的结晶组织,以保证连铸坯料的质量和性能。
结晶器在连铸生产中的作用主要体现在以下几个方面:1. 控制结晶过程:结晶器可以通过控制结晶过程来影响坯料的结晶组织。
结晶器内部设有一定形状和尺寸的结晶孔道,通过调整结晶器的温度、冷却水流量等参数,可以控制坯料的结晶速度和结晶核的形成,从而影响坯料的晶粒尺寸和分布。
合理的结晶过程控制可以获得细小、均匀的晶粒,提高坯料的塑性和韧性。
2. 保证连铸坯料质量:结晶器可以有效地阻止浇注过程中的气体和杂质进入坯料中,减少坯料的气孔、夹杂和缺陷。
结晶器的结构设计和材料选择都需要考虑到其抗氧化、抗腐蚀、耐磨损等性能,以保证结晶器能够长时间稳定地工作,并确保坯料的质量。
3. 调整结晶组织:通过改变结晶器的结构和工艺参数,可以调整坯料的结晶组织,以满足不同材料和产品的要求。
例如,对于高强度钢材,可以采用细小晶粒的结晶器,以提高材料的强度和韧性;对于特殊用途的合金材料,可以采用特殊结构的结晶器,以获得特定的晶粒形态和组织结构。
4. 提高连铸效率:结晶器的优化设计可以提高连铸的效率和生产能力。
通过合理布置结晶器的数量和位置,可以实现多流道连铸,同时浇注多块坯料,提高连铸机的产能。
此外,结晶器还可以通过调节结晶器的冷却水流量和温度分布,优化坯料的冷却过程,提高连铸的速度和效率。
结晶器在连铸生产中起着至关重要的作用。
通过控制结晶过程、保证坯料质量、调整结晶组织和提高连铸效率,结晶器可以有效地提高连铸坯料的质量和性能,满足不同材料和产品的要求。
因此,在连铸生产中,合理选择和使用结晶器,不仅能够提高产品质量,还能够提高生产效率,降低生产成本,具有重要的经济和社会意义。
结晶器总结
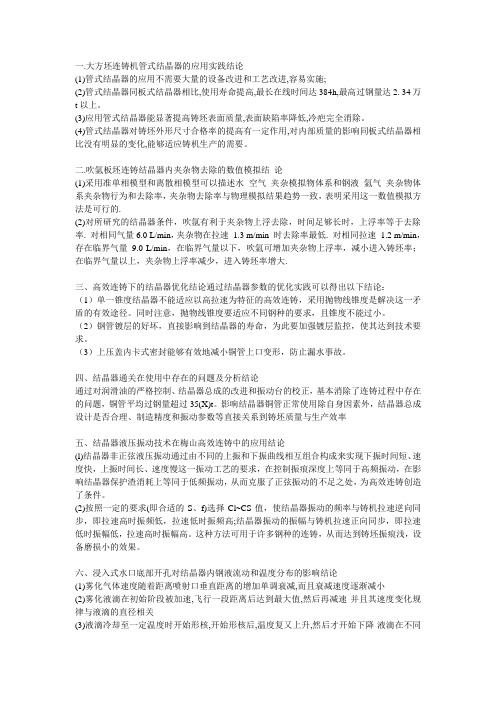
一.大方坯连铸机管式结晶器的应用实践结论(1)管式结晶器的应用不需要大量的设备改进和工艺改进,容易实施;(2)管式结晶器同板式结晶器相比,使用寿命提高,最长在线时间达384h,最高过钢量达2. 34万t以上。
(3)应用管式结晶器能显著提高铸坯表面质量,表面缺陷率降低,冷疤完全消除。
(4)管式结晶器对铸坯外形尺寸合格率的提高有一定作用,对内部质量的影响同板式结晶器相比没有明显的变化,能够适应铸机生产的需要。
二.吹氩板坯连铸结晶器内夹杂物去除的数值模拟结论(1)采用准单相模型和离散相模型可以描述水空气夹杂模拟物体系和钢液氩气夹杂物体系夹杂物行为和去除率,夹杂物去除率与物理模拟结果趋势一致,表明采用这一数值模拟方法是可行的.(2)对所研究的结晶器条件,吹氩有利于夹杂物上浮去除,时间足够长时,上浮率等于去除率. 对相同气量6.0 L/min,夹杂物在拉速 1.3 m/min 时去除率最低. 对相同拉速1.2 m/min,存在临界气量9.0 L/min,在临界气量以下,吹氩可增加夹杂物上浮率,减小进入铸坯率;在临界气量以上,夹杂物上浮率减少,进入铸坯率增大.三、高效连铸下的结晶器优化结论通过结晶器参数的优化实践可以得出以下结论:(1)单一锥度结晶器不能适应以高拉速为特征的高效连铸,采用抛物线锥度是解决这一矛盾的有效途径。
同时注意,抛物线锥度要适应不同钢种的要求,且锥度不能过小。
(2)钢管镀层的好坏,直接影响到结晶器的寿命,为此要加强镀层监控,使其达到技术要求。
(3)上压盖内卡式密封能够有效地减小铜管上口变形,防止漏水事故。
四、结晶器通关在使用中存在的问题及分析结论通过对润滑油的严格控制、结晶器总成的改进和振动台的校正,基本消除了连铸过程中存在的问题,铜管平均过钢量超过35(X)t。
影响结晶器铜管正常使用除自身因素外,结晶器总成设计是否合理、制造精度和振动参数等直接关系到铸坯质量与生产效率五、结晶器液压振动技术在梅山高效连铸中的应用结论(l)结晶器非正弦液压振动通过由不同的上振和下振曲线相互组合构成来实现下振时间短、速度快,上振时间长、速度慢这一振动工艺的要求,在控制振痕深度上等同于高频振动,在影响结晶器保护渣消耗上等同于低频振动,从而克服了正弦振动的不足之处,为高效连铸创造了条件。
常规板坯连铸机结晶器技术

常规板坯连铸机结晶器技术结晶器是连铸机中的铸坯成型设备, 是连铸机的核心设备之一。
其作用是将连续不断地注入其内腔的钢液通过水冷铜壁强制冷却,导出钢液的热量,使之逐渐凝固成为具有所要求的断面形状和一定坯壳厚度的铸坯,并使这种芯部仍为液相的铸坯连续不断地从结晶器下口拉出,为其在以后的二冷区域内完全凝固创造条件。
在钢水注入结晶器逐渐形成一定厚度坯壳的凝固过程中,结晶器一直承受着钢水静压力、摩檫力、钢水热量的传递等诸多因素引起的的影响,使结晶器同时处于机械应力和热应力的综合作用之下,工作条件极为恶劣,在此恶劣条件下结晶器长时间地工作,其使用状况直接关系到连铸机的性能,并与铸坯的质量与产量密切相关。
因此,除了规范生产操作、选择合适的保护渣和避免机械损伤外,合理的设计是保证铸坯质量、减小溢漏率、提高其使用寿命的基础和关键。
板坯连铸机一般采用四壁组合式(亦称板式)结晶器,也有一个结晶器浇多流铸坯的插装式结构。
ﻫ结晶器主要参数的确定ﻫ1 结晶器长度Hﻫ结晶器长度主要根据结晶器出口的坯壳最小厚度确定。
若坯壳过薄,铸坯就会出现鼓肚变形,对于板坯连铸机,要求坯壳厚度大于10~15mm。
结晶器长度也可按下式进行核算:ﻫﻫH=(δ/K)2Vc+S1+S2 (mm)ﻫﻫ式中δ——结晶器出口处坯壳的最小厚度,mmﻫK——凝固系数,一般取K=18~22 mm/min0.5ﻫ Vc——拉速,mm/minS1——结晶器铜板顶面至液面的距离,多取S1=100 mmﻫﻫS2——安全余量,S=50~100 mmﻫﻫ对常规板坯连铸机可参考下述经验:ﻫﻫ当浇铸速度≤2.0m/min时,结晶器长度可采用900~950mm。
ﻫﻫ当浇铸速度2.0~3.0m/min 时,结晶器长度可采用950~1100mm。
当浇铸速度≥3.0m/min时,结晶器长度可采用1100~1200mm。
ﻫﻫ 2 结晶器铜板厚度hﻫﻫ铜板厚度的确定是依据热量传热原理和高温下的使用性能,具体说,与铜板材质、镀层、机械性能、拉速、冷却水量的大小和分布等有关。
基于PID控制的连铸机结晶器液压震动系统的应用

的位 置 , 系 统 由两 个 独 立 的液 压 缸 组 成 , 每 个 液 压 缸 有 一 个 伺 服 阀来 控 制 结 晶器 液 压 缸 位 置 , 结 晶器 将 以 一 定 的 频 率 、 行 程 和 波 形来振动 。
内部 质 量 的 要求 。 结 晶器 液 压 震 动 的作 用 主 要 表 现 在 两 个 方 面 : 1 ) 防止 铸 坯 在 凝 固过 程 中 与结 晶 器 铜 壁 发 生 粘 结 而 出现 坯 壳拉裂或漏钢事故。 在结 晶器 上 下 振 动 时 按 振 动 曲线 周 期 性 地 改 变 钢 液 面 与 结 晶 器铜 壁 的 相 对 位 置 ,对 坯 壳 有 一 个 强 制 脱 模 的作 用 , 并 使 得 拉 漏 的坯 壳 在 结 晶 器 内部 得 以 焊 合 。
结 晶器 是 连 铸 设 备 中 的铸 坯 成 型设 备 ,人们 称 它 是 连 铸 机
的 心脏 。它 的功 能 是 将 连 续 不 断地 注入 其 腔 内 的 高 温 钢 液 通 过
结 晶 器 必 须 在 浇 注 期 间 保 持 振 动 。如 果 振 动 是 以不 正 确 的 频率 、 振幅或波 形进行 , 则会引起较差 的表面质量 , 增 加 结 晶 器 润滑粉的消耗 , 或者可能引起漏钢 。
级 计 算 机 系 统 的 模 型 设 定 数 据 、连 铸 机 一 级 控 制 系统 操 作 员设 定 数 据 及 来 自控 制 器 本 身 自带 的控 制 面 板 的人 工 设 定 ,然 受 下 载 到控 制 器 实 现 震 动 控 制 。此 控 制 方 式 较 好 的满 足 了 冶 金 工 艺 的要 求 , 对 板 坯 的 内 部 和表 面质 量 起 到 很 好 的效 果 。 系 统 在 宝 钢
连铸机结晶器铜板简介及影响寿命因素

连铸机结晶器铜板简介及影响寿命因素作者:王腾飞戴昭颖张博来源:《科学与财富》2015年第23期摘要:本文简要介绍了京唐公司连铸机结晶器铜板的作用及镀层材质情况,并结合实际生产总结影响结晶器铜板寿命的因素及改进措施。
关键词:连铸机结晶器铜板;镀层材质;寿命前言:结晶器是连铸机的关键部件,铜板是结晶器的核心部件,钢水通过结晶器铜板向外导出热量而使钢水凝固结晶成一定厚度的坯壳,铜板在此过程中承受着高低温度产生的热应力、高温热膨胀带来的塑性变形、冷却收缩时带来的巨大拉应力、钢坯与铜板相对运动产生的摩擦力,这就要求结晶器铜板必须具有较高的热传导性,较高的抗拉强度,较高的再结晶温度,软化温度,热强性以抵抗变性,热疲劳能力,同时要有抵抗磨损的能力,提高过钢量,因此结晶器铜板在连铸过称中起到不可或缺的作用,提高结晶器铜板寿命更是降低炼钢成本的重要工作之一。
1 结晶器作用及其要求结晶器是连铸机的核心,其作用是将连续不断地注入其内腔的钢液通过水冷铜板强制冷却,导出钢液的热量,使之逐渐凝固成为具有所需要求的断面形状和一定均匀厚度的坯壳,并使这种芯部为液相的铸坯连续不断地从结晶器下口拉出,为其在二冷区域内完全凝固创造条件。
钢水在结晶器中的凝固对铸坯表面质量和铸机的正常生产有着重大影响,在高温钢水注入结晶器,逐渐形成一定厚度坯壳的凝固过程中,结晶器铜板一直处于钢水与冷却水的静压力、高温氧化、冷热疲劳产生的热裂纹、温度梯度大产生变形、冷却水和保护渣成份的化学腐蚀、高温蒸汽的侵蚀,引锭、拉坯、振动产生的摩擦、磨损和调锥宽导致的擦痕等诸多损伤。
(1)良好的导热性,能使钢液快速凝固。
每1Kg钢水浇注成坯并冷却到室温,放出的热量约为1340KJ/Kg,若板坯尺寸为250×1700mm,拉速为1m/min,结晶器每分钟带走的热量多达20万KJ。
而结晶器长度又较短,一般不超过1m,在这样短的距离内要能带走大量的热量,要求它必须具有良好的导热性能。
常规板坯连铸机结晶器技术(知识学习)
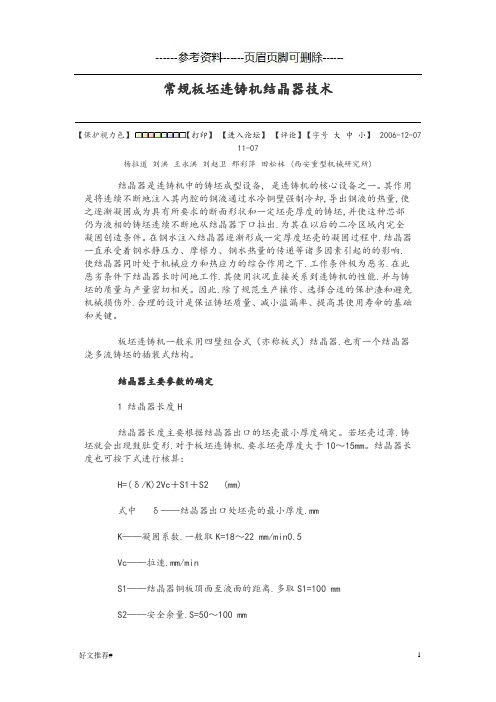
常规板坯连铸机结晶器技术【保护视力色】【打印】【进入论坛】【评论】【字号大中小】2006-12-0711-07杨拉道刘洪王永洪刘赵卫邢彩萍田松林 (西安重型机械研究所)结晶器是连铸机中的铸坯成型设备, 是连铸机的核心设备之一。
其作用是将连续不断地注入其内腔的钢液通过水冷铜壁强制冷却,导出钢液的热量,使之逐渐凝固成为具有所要求的断面形状和一定坯壳厚度的铸坯,并使这种芯部仍为液相的铸坯连续不断地从结晶器下口拉出.为其在以后的二冷区域内完全凝固创造条件。
在钢水注入结晶器逐渐形成一定厚度坯壳的凝固过程中.结晶器一直承受着钢水静压力、摩檫力、钢水热量的传递等诸多因素引起的的影响.使结晶器同时处于机械应力和热应力的综合作用之下.工作条件极为恶劣.在此恶劣条件下结晶器长时间地工作.其使用状况直接关系到连铸机的性能.并与铸坯的质量与产量密切相关。
因此.除了规范生产操作、选择合适的保护渣和避免机械损伤外.合理的设计是保证铸坯质量、减小溢漏率、提高其使用寿命的基础和关键。
板坯连铸机一般采用四壁组合式(亦称板式)结晶器.也有一个结晶器浇多流铸坯的插装式结构。
结晶器主要参数的确定1 结晶器长度H结晶器长度主要根据结晶器出口的坯壳最小厚度确定。
若坯壳过薄.铸坯就会出现鼓肚变形.对于板坯连铸机.要求坯壳厚度大于10~15mm。
结晶器长度也可按下式进行核算:H=(δ/K)2Vc+S1+S2 (mm)式中δ——结晶器出口处坯壳的最小厚度.mmK——凝固系数.一般取K=18~22 mm/min0.5Vc——拉速.mm/minS1——结晶器铜板顶面至液面的距离.多取S1=100 mmS2——安全余量.S=50~100 mm对常规板坯连铸机可参考下述经验:当浇铸速度≤2.0m/min时.结晶器长度可采用900~950mm。
当浇铸速度2.0~3.0m/min时.结晶器长度可采用950~1100mm。
当浇铸速度≥3.0m/min时.结晶器长度可采用1100~1200mm。
4.连铸工艺与设备-结晶器-2011.4.12

4.2 结晶器的新形式新技术
热顶结晶器 在结晶器弯月面区域镶嵌导热材料,以减少热流密度, 延缓坯壳收缩,即热顶结晶器。 喷淋式结晶器 喷淋式结晶器是将管式结晶器隔离水缝改为喷淋水冷 却,即由喷嘴喷出的喷淋水直接喷到结晶器铜管上实现 冷却。冷却效率高,有较显著的节水效果。
22/86
压力水膜结晶器 压力水膜结晶器是比利时冶金研究中心(CRM)和阿贝 德厂(Arbed)联合开发的一种高效结晶器技术。 曲面结晶器 曲面结晶器是中冶连铸开发的一种高效方坯结晶器技 术。该技术是从传热角度,根据气隙产生的主要原因, 通过对结晶器热变形和小方坯收缩的分析开发出来的。 人工附加气隙结晶器 人工附加气隙结晶器是新日本制铁株式会社开发的一 种高效方坯结晶嚣技术,又称X-MOLD。
8/86
4.1 连铸结晶器的性能要求
(5)振动时惯性力要小。为提高铸坯表面质量,结晶 器的振动广泛采用高频率小振幅,最高已达400次 /min,在高频振动时惯性力不可忽视,过大的惯性 力不仅影响到结晶器的强度和刚度,进而也影响到 结晶器运动轨迹的精度。重量要小,以减少振动时 的惯性力; (6)结晶器结构要简单,以便于制造和维护; (7)有良好的刚性和加工性,易于制造; (8)成本要低。
10/86
4.1 结晶器形式和结构-构造
按结晶器的外形(型式)可分为直形结晶器和弧形结 晶器。 直形结晶器四面壁板都是平面状的,直形结晶器的 内壁沿坯壳移动方向呈垂直形,因此导热性能良好, 坯壳冷却均匀。该类型结晶器还有利于提高坯壳的质 量和拉坯速度、结构较简单、易于制造、安装和调试 方便;夹杂物分布均匀;但铸坯易产生弯曲裂纹,连 铸机的高度和投资增加。直形结晶器用于立式和立弯 式及直弧连铸机。
通俗的讲连铸结晶器就是一个钢水制冷成型设备。 基本由框架、水箱和铜板、调整系统(调整装置、减 速机等);润滑系统(油管油路),冷却系统和喷淋等设 备组成。连铸结晶器需要和连铸结晶器保护材料(渣) 一同使用。 2/86
板坯连铸机结晶器研究课件

摘要结晶器是钢坯连续铸造的关键设备,其设计和制造的优劣直接影响到连铸生产的正常与稳定。
本文就目前连铸结晶器采用的铜板材料及铜板材料表面处理技术的发展现状进行了总结和分析。
指出针对板坯结晶器窄面铜板易高温变形、磨损的情况,采用高强度、高导热率的弥散强化铜材料,进而延长结晶器的维修周期,提高生产效率。
同时针对现有结晶器铜板表面改性技术的优缺点,发展新型合金涂、镀层技术,进一步提高涂、镀层的硬度,耐磨和耐腐蚀性能。
目前结晶器铜板表面处理的几种方法:电镀法、热喷涂法、化学热处理法以及具有潜在发展前景的激光熔覆法。
激光熔覆法由于具有清洁无污染,成品率高以及性价比高等特点,具有广阔的发展和应用空间。
而且,通过优化熔覆工艺参数,设计合理的熔覆材料体系,能够形成与铜板呈冶金结合的优良抗热耐磨复合涂层,从而显著提高结晶器的使用寿命。
关键词:结晶器;化学热处理;激光熔覆;铜板AbstractThe progress of mould plates was reviewed in continuous casting. The techniques such a solution or aging or forming or fine crystal and their combination were an effect tiveme thod which benefit for high conductivity and high strengthen of copper base alloy. Copper base composite maerial through dispersion technique and composite hardening and surface strengthening have more promising for mouldes in the future.Based on the current study stat of surface strength ening on copper crystallizer, several surface treatment means,such as electro plating thermal spraying,penetration and laserclad dingte chnique with potential development are described. Because of cleanliness without any pollution, high finished product ratio and high performance costratio, laser cladding has wide development and application range. Moreover, by optimizing process parameters and designing suitable material system, fine hea-t resistant and wear-resistant coating having metallurgy bonding with copper substrate can be fabricated, therefore, it may notably improve the service life of copper crystallizer.Key words:Copper crystallizer; Electroplating; Thermal Chemical heat treatme;Copper plate目录摘要 (I)Abstract (II)第1章绪论 (1)1.1连扎连铸简介 (1)1.2工艺流程 (3)1.3板坯连铸机质量优势 (4)1.4研究背景 (5)1.5国内外状况 (6)1.6结晶器概述 (7)1.7结晶器存在的问题 (9)1.8结晶器使用前的安全检查 (9)1.9本章小结 (10)第2章结晶器夹紧装置的选择计算 (11)2.1结晶器夹紧装置简介 (11)2.2结晶器夹紧受力分析及计算选择 (12)2.3结晶器宽边调整机构的安装 (14)2.4本章小结 (14)第3章结晶器调宽装置的选择计算 (15)3.1调宽装置简介 (15)3.2调宽装置的确定和基本参数的选择 (16)3.3调宽装置驱动选择 (18)3.4窄边调整机构的安装 (18)3.5本章小结 (19)第4章结晶器铜板及水箱的选择计算 (20)4.1结晶器铜板的设计 (20)4.1.1结晶器长度的选择 (20)4.1.2结晶器断面尺寸和倒锥度 (22)4.1.3结晶器铜板材质及表面镀层的选择 (23)4.1.4铜板厚度计算 (24)4.2水箱设计 (25)4.3本章小结 (26)第五章结晶器振动装置的应用和发展 (27)5.1振动装置的概述 (27)5.2结晶器的振动方式 (27)5.3总结 (30)5.4本章小结 (31)结论 (32)参考文献 (33)致谢 (35)第1章绪论1.1连扎连铸简介连铸连轧全称连续铸造连续轧制(Continue Casting Direct Rolling,简称CCDR),是把液态钢倒入连铸机中轧制出钢坯(称为连铸坯),然后不经冷却,在均热炉中保温一定时间后直接进入热连轧机组中轧制成型的钢铁轧制工艺。
连铸结晶器钢水流动控制技术(四篇)

连铸结晶器钢水流动控制技术连铸板坯的表面和内部缺陷与结晶器内钢液的流动状态密切相关。
伴随着连铸机拉速的提高,结晶器内液面波动加剧,容易产生卷渣,造成铸坯质量恶化。
采用结晶器钢水流动控制技术可以改善结晶器内流场形态,抑制水口出流速度以平稳液面,促进夹杂物上浮。
连铸板坯的表面和内部缺陷与结晶器内钢液的流动状态密切相关。
伴随着连铸机拉速的提高,结晶器内液面波动加剧,容易产生卷渣,造成铸坯质量恶化。
采用结晶器钢水流动控制技术可以改善结晶器内流场形态,抑制水口出流速度以平稳液面,促进夹杂物上浮。
用于板坯结晶器的电磁制动(EMBr)、电磁流动控制(FC结晶器)和多模式电磁搅拌(M-MEMS)是结晶器钢水流动控制技术的典型代表。
电磁制动器通过对结晶器施加一个与铸流方向垂直的静态磁场而对流动的钢液进行制动。
钢流由于电磁感应而产生感应电压,因此在钢液中产生感应电流,这些电流由于受到静态磁场的作用而产生一个与钢水运动方向相反的制动力。
钢液的流速越快,制动力也越大。
电磁制动器具有一个单一的、覆盖整个板坯宽度的静态磁场。
电磁制动技术可抑制水口射流速度,减缓沿凝固壳向下流动,促进夹杂物和气泡上浮。
FC结晶器含有两个方向相反的制动磁场,第一个位于弯月面区域,另一个位于结晶器的下部,每一个磁场都覆盖了板坯的整个宽度。
FC结晶器的磁场的上电磁场减少了结晶器弯月面紊流,可防止保护渣卷入凝固壳和角部横裂;下电磁场可减少钢液向下流速,有利于夹杂物和气泡上浮。
利用M-MEMS多模式电磁搅拌器可根据需要以不同的方式搅动结晶器内的钢水,显著减少板坯铸造缺陷。
该技术采用4个线性电磁搅拌器,位于结晶器高度方向的中部、浸入式水口两侧,每侧2个线圈并排设置,可用于使浸入式水口流出的钢水制动(EMIS)或加速(EMLA)。
第三种工作模式则用于使位于弯月面的钢水转动(EMRS),此项技术可有效控制热传导梯度和坯壳凝固前沿的均匀性,消除某些钢种存在的气孔、针孔和表面夹渣等铸造缺陷。
炼钢厂连铸结晶器液位控制系统的应用

电动 缸控 制 器 接 收 液 位 PD控 制 器 的设 定 I
值、 电动缸 的实 际位 置 反馈 值 以及 现 场 手操 器上 的信 号 (自动/ 动/ 棒/ 急 停 止 模 式 选 择 ) 手 扛 紧 后 , 处 理 将 控 制 信 号 发送 给 执 行 机 构 ( 经过 电动
缸 ) 自动 方式 下 , 控 制器 主要 有 两 个 重 要 的 。 该
图2 V H U Z液 位传 感 器机 构 组成
・
l 6・
梅 山科 技
4 2 电动缸控 制器 .
21 00年第 3 期
由于传 感器 装在 结 晶器铜 板 上 , 故才 用 水对 传感 器进行 冷却 , 传感 器 将 信号 传 到前 置 放 大器
并最 终送到 信号处理 单元 。信号处理 单元接 收前
有影响 , 以操作上在 开浇前发送 “ 所 回零”命 令 给信号处 理单元 ,让信号 处理单 元根据 此时 的
磁场 确 定 传 感 器 的 零 位 ,从 而 保 证 测 量 的 准
确 度。
臣臣正口
图 3 设 定值 堆 栈 P1 e = o+A×s H i n
械
() 1
3 设定值
传 送 电 动缸 的设 定 值 到 电 动 缸 控 制 器 。执 行 机
制 系统 到执行 机构 都进 行 了更 换 。本 文对 新 的控
制 系统 和执行 机构进 行 了详 细 的阐述 。
1 系统控 制流 程
整个 系统 的控 制 流 程 见 图 1 其 具 体 工 作 。 过程 是 : 开浇 时 , 作 工选 择 扛 棒 模 式 控 制 结 晶 操 器 液位 , 时 控 制 系 统 仅 测 量 结 晶 器 液 位 而 不 此
- 1、下载文档前请自行甄别文档内容的完整性,平台不提供额外的编辑、内容补充、找答案等附加服务。
- 2、"仅部分预览"的文档,不可在线预览部分如存在完整性等问题,可反馈申请退款(可完整预览的文档不适用该条件!)。
- 3、如文档侵犯您的权益,请联系客服反馈,我们会尽快为您处理(人工客服工作时间:9:00-18:30)。
关于
《连铸设备与工艺》
课程的结课论文
结晶器在连铸过程中的应用
摘要:本文主要简单介绍结晶器在连铸过程中的应用。
重点介绍介绍结晶器专家系统,简单介绍结晶器液面检测及控制系统、结晶器在线调宽等等。
关键词:连铸;结晶器;结晶器专家系统
金属连铸结晶器就是有冷却系统和成型器组成。
冷却系统的作用是使铁水进入结晶器后逐渐凝固,成型器根据客户需求<圆的、方的、
半圆的等形状)选用。
为了适应生产多种规格铸坯的需要,缩短更换结晶器的时间,结晶器调宽可以在线调节。
板坯在线调宽结晶器既是结晶器的两个窄边可以多次分小步向内或向外移动,直至调到预定的宽度,在生产过程中可在不停机的条件下完成对结晶器宽度的调整。
一.结晶器专家系统
1.结晶器热力学软件包
结晶器热力学软件包的监控主要基于安装在铜板内热电偶所测得的温度。
1.1 温度监控
钢水在结晶器内凝固早期的温度变化行为能够得到,所以我们能监控结晶器内部的温度变化,从温度监控中可得知:
1窄边和宽边铜板表面的热流分布2保护渣对温度分布的影响
3热流瞬时行为(斜坡,速度改变)4收缩行为(坯壳离开时)5观察危险区域6提高铸坯质量和操作的安全性7提高浇注实践能力
温度监控描绘出了安装在结晶器内的热电偶测得的温度值,镶嵌在结晶器铜板内的热电偶,将检测到的铜板温度传送到系统中,根据检测到的信号和各热电偶所安装的位置,可以不同颜色描绘出结晶器内铸坯各部分的温度。
1.2 漏钢预报
热电偶镶嵌在结晶器铜板中,给出重要的钢水凝固前温度信息,这些数据用于漏钢预报也用作阐明结晶器内部热传输的依据。
漏钢预报系统作为一个工具去分配、收集、储存、比较和将结晶器所有数据参数可视化。
这些数据可以帮助分析浇铸过程中的问题或产生报警信息或改变浇铸作业进程,漏钢预报系统的运行对于操作人员监控浇铸进程是非常有利的,由于在线的可视性,员工可找到最佳最稳定的浇铸进程。
1.3 计算结晶器热流交换
利用计算结晶器热交换防止拉漏是监控通过结晶器的总吸热量,根据统计数据,确定最低吸热量,在拉坯前确定一个合适的铸坯壳厚度。
为了预报拉漏,只需检测总的吸热量,可定义为“单位吸热量”,也可用流经结晶器壁的热流量(Kw/m²)来度量,这个热流量QA 可表示如下:QA=(CpρwWΔT)/A 式中
QA——单位面积的吸热量Cp——水的比热ρw——水的密度W——冷却水流量ΔT——冷却水进出口温度A——结晶器暴露的表面积
为了准确的了解结晶器的吸热情况,要分别测定和监控结晶器每一面的热流,因为可能结晶器某一面的热流值低到危险值而传热仍大于可接受的最小值,如果只测总传热并认为正常,就会漏钢。
热流量QA越限降告诉操作人员注意,并采取措施,以避免漏钢。
2 结晶器振软件包
根据结晶器振动系统的液压缸冲程和压力反馈,计算出铸坯和结晶器铜板之间的摩擦力,根据在粘结漏钢前粘结处铜板温度升高,摩擦力增大的特性,通过检测装置,按照一定的判断模型,对漏钢进行
预报。
2.1 结晶器摩擦力
根据液压振动液压缸振幅和压力反馈计算出结晶器的摩擦力,有两种不同的操作状况必须区分:浇铸过程中的振动操作为“热”,离线的振动为“冷”。
两种状况下的摩擦力的不同,可得出结晶器摩擦力。
此计算方法是基于物理工作的离线冷力和在线热力,对得出摩擦力的值它是非常重要的。
在线热力由结晶器专家系统测得的振幅和压力计算出,它包括离线冷力和铜板及铸坯之间的摩擦力,所以,离线冷力必须被测量。
离线冷力主要根据振幅,其计算方程为:离线冷力=a+b*A+c*A²
a、b、c为系数常数A为振幅
2.2 摩擦力监控
结晶器摩擦力监控画面(如图)被分为3部分,以便最重要的摩擦力的测量和计算赋值能在一个窗口监控。
左上是在线摩擦力和振幅的显示;右上是被称作摩擦力循环圈;在线工作曲线,浇铸速度,结晶器液位等显示在下部区域。
3 利用多种技术显示结晶器铸坯结壳情况预报拉漏
由于计算技术、图像处理技术的进步和数学模型的深化,出现了连铸结晶器可视化技术,它把结晶器钢水液位、热电偶温度、冷却水温度和流量、结晶器宽度、摩擦力、振幅等数据送入专用可视化PC 机中,进行数据处理和数模运算,作成可视化画面(包括结晶器内钢水温度场分布、凝固、结壳情况),早期的热现象模型只涉及热传导问题,与热传导方程有关的热物性值多做简化处理,随着数值计算技术的发展和计算机运行速度的提高,开始以热传输耦合流体流动来获得速度场和温度场,使其更实用化。
二.结晶器液面检测及控制系统
1.弯月面波动不仅造成诸如漏钢等生产上的问题,还严重影响铸坯质量。
当弯月面波动加剧时,板坯表面非金属夹杂物增加,导致钢材板坯表面缺陷加重。
2.采用涡流式传感器检测结晶器内钢水液面位置,并与塞棒装置
构成闭环的结晶器液面控制系统,将液面波动控制在 2mm以内
三、结晶器液压伺服振动装置
1.现在所开发的结晶器液压振动系统可实现振动频率和振幅的最佳组合,再加上最合适振动波型和偏斜率,可用于所有的浇铸条件和生产钢种。
2.液压非正弦振动可在线调节振动参数,如振动频率、振幅、偏斜率。
选择适当的参数可减小负滑动时间,使振痕变浅,并可增加正滑动时间,增加保护渣消耗量,改善润滑。
3.液压非正弦振动可在最佳负滑动时间和正滑动时间的情况下降低振动频率,提高设备的使用寿命和稳定性。
4.液压非正弦振动可对于不同钢种,通过选择优化的控制模型及参数获得良好的铸坯质量。
液压非正弦振动数学模型
液压非正弦振动控制模型
Vc-f控制模型
Vc-h控制模型
Vc -f、h控制模型
Vc-θ控制模型
下图为Vc-f控制模型速度波形图和位移、速度波形图
四、结晶器在线调宽
•为满足用户产品宽度变化以适应市场的要求,铸机设计的结晶器宽度调整系统可实现:
•离线宽度调节。
•浇铸过程中在线宽度调节。
•拉坯速度和冷却系统连续监视。
•在线宽度和锥度调节以补偿拉坯速度变化对冷态铸坯宽度的应响。
•该系统主要包括:
•结晶器夹紧和调宽装置
•在线宽度和锥度调节数学模型(与铸坯规格、钢种、过热度、拉速、冷却等有关)
•拉坯速度和冷却系统连续监视系统
•在线宽度和锥度调节控制模型
五.结语
在钢水连续浇铸过程中,结晶器是铸机设备中非常重要的设备,结晶器工作状况将直接影响铸坯质量。
为了保证生产的稳定和提高铸坯质量,尽最大可能得到尽可能的有关结晶器工作的数据参数,尤其是直接影响设备和铸坯质量的数据,将其完善和优化使铸机设备运行更加稳定、协调。
漏钢预报技术已从早期只是检测出漏钢,经过研究漏钢成因与机理、检测出拉漏的征兆并报警和控制、建立预报数学模型、使用人工智能技术和可视化技术使漏钢率大大降低。
参考文献
[1]蔡开科、士富主编,连续铸钢原理与工艺,冶金工业出版社,1994,12;
[2]刘明延等铸机设计与计算,机械工业出版社,1990,2;
[3]王宝峰、董方等,电磁场相位对小方块坯结晶器电磁搅拌效果的影响(J).连铸,2007。
[4]陈明,周代文. 电磁搅拌技术在连铸上的应用[J]. 宽厚板 ,2009,(05).
[5]电磁搅拌装置[J]. 现代制造,1996,(10).
[6]潘秀兰,王艳红,梁慧智. 国内外电磁搅拌技术的发展与展望[J]. 鞍钢技术 ,2005,(04).
[7]金萍,孔繁华,张元健. 连铸机电磁搅拌技术[J]. 一重技术,1999,(03).
学习体会和心得
做为学生,学习是自己重要的事情是理所当然的,在明确它的重要性之后,就要以严谨的态度对待学习,认真的态度是学习上取得成绩的首要条件。
这门课程让我收获颇为丰富,让我更深层次的认识了关于连铸工艺和设备相关的知识。
为我们即将毕业的学子在以后的工作中打下了良好的基础知识。
再此我感谢老师这一个学期对我们的培育。