波峰焊短路的原因及解决方案
波峰焊常见问题解决方法
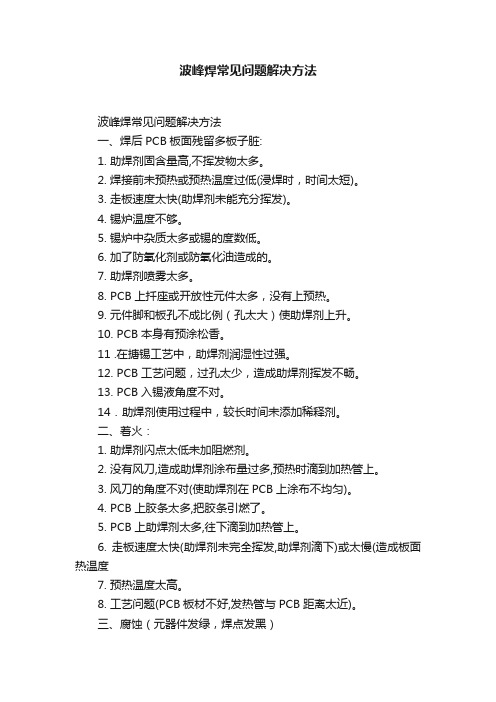
波峰焊常见问题解决方法波峰焊常见问题解决方法一、焊后PCB板面残留多板子脏:1. 助焊剂固含量高,不挥发物太多。
2. 焊接前未预热或预热温度过低(浸焊时,时间太短)。
3. 走板速度太快(助焊剂未能充分挥发)。
4. 锡炉温度不够。
5. 锡炉中杂质太多或锡的度数低。
6. 加了防氧化剂或防氧化油造成的。
7. 助焊剂喷雾太多。
8. PCB上扦座或开放性元件太多,没有上预热。
9. 元件脚和板孔不成比例(孔太大)使助焊剂上升。
10. PCB本身有预涂松香。
11 .在搪锡工艺中,助焊剂润湿性过强。
12. PCB工艺问题,过孔太少,造成助焊剂挥发不畅。
13. PCB入锡液角度不对。
14.助焊剂使用过程中,较长时间未添加稀释剂。
二、着火:1. 助焊剂闪点太低未加阻燃剂。
2. 没有风刀,造成助焊剂涂布量过多,预热时滴到加热管上。
3. 风刀的角度不对(使助焊剂在PCB上涂布不均匀)。
4. PCB上胶条太多,把胶条引燃了。
5. PCB上助焊剂太多,往下滴到加热管上。
6. 走板速度太快(助焊剂未完全挥发,助焊剂滴下)或太慢(造成板面热温度7. 预热温度太高。
8. 工艺问题(PCB板材不好,发热管与PCB距离太近)。
三、腐蚀(元器件发绿,焊点发黑)1. 铜与助焊剂起化学反应,形成绿色的铜的化合物。
2. 铅锡与助焊剂起化学反应,形成黑色的铅锡的化合物。
3. 预热不充分(预热温度低,走板速度快)造成助焊剂残留多,4.残留物发生吸水现象,(水溶物电导率未达标)5.用了需要清洗的助焊剂,焊完后未清洗或未及时清洗。
6.助焊剂活性太强。
7.电子元器件与助焊剂中活性物质反应。
四、连电,漏电(绝缘性不好)1. 助焊剂在板上成离子残留;或助焊剂残留吸水,吸水导电。
2. PCB设计不合理,布线太近等。
3. PCB阻焊膜质量不好,容易导电。
五、漏焊,虚焊,连焊1. 助焊剂活性不够。
2. 助焊剂的润湿性不够。
3. 助焊剂涂布的量太少。
4. 助焊剂涂布的不均匀。
波峰焊接不良原因及解决对策讲义
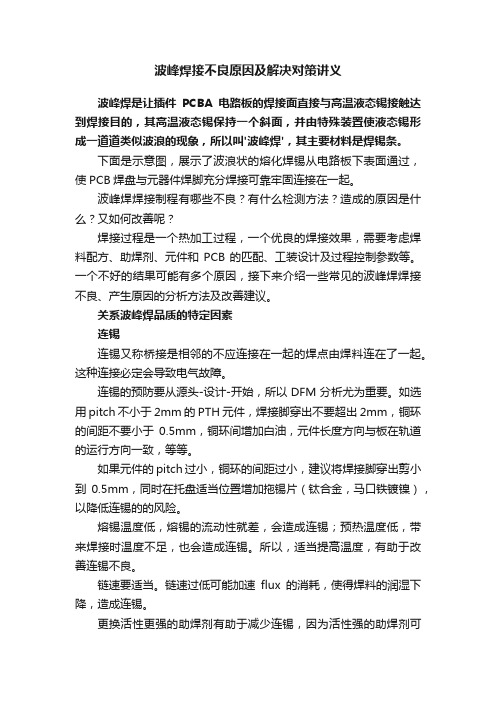
波峰焊接不良原因及解决对策讲义波峰焊是让插件PCBA电路板的焊接面直接与高温液态锡接触达到焊接目的,其高温液态锡保持一个斜面,并由特殊装置使液态锡形成一道道类似波浪的现象,所以叫'波峰焊',其主要材料是焊锡条。
下面是示意图,展示了波浪状的熔化焊锡从电路板下表面通过,使PCB焊盘与元器件焊脚充分焊接可靠牢固连接在一起。
波峰焊焊接制程有哪些不良?有什么检测方法?造成的原因是什么?又如何改善呢?焊接过程是一个热加工过程,一个优良的焊接效果,需要考虑焊料配方、助焊剂、元件和PCB的匹配、工装设计及过程控制参数等。
一个不好的结果可能有多个原因,接下来介绍一些常见的波峰焊焊接不良、产生原因的分析方法及改善建议。
关系波峰焊品质的特定因素连锡连锡又称桥接是相邻的不应连接在一起的焊点由焊料连在了一起。
这种连接必定会导致电气故障。
连锡的预防要从源头-设计-开始,所以DFM分析尤为重要。
如选用pitch不小于2mm的PTH元件,焊接脚穿出不要超出2mm,铜环的间距不要小于0.5mm,铜环间增加白油,元件长度方向与板在轨道的运行方向一致,等等。
如果元件的pitch过小,铜环的间距过小,建议将焊接脚穿出剪小到0.5mm,同时在托盘适当位置增加拖锡片(钛合金,马口铁镀镍),以降低连锡的的风险。
熔锡温度低,熔锡的流动性就差,会造成连锡;预热温度低,带来焊接时温度不足,也会造成连锡。
所以,适当提高温度,有助于改善连锡不良。
链速要适当。
链速过低可能加速flux的消耗,使得焊料的润湿下降,造成连锡。
更换活性更强的助焊剂有助于减少连锡,因为活性强的助焊剂可以增加润湿性。
冷焊冷焊是由于热量不足等原因造成焊点出现润湿不佳,呈灰色和有褶皱。
此类不良通常是因为热量不足使得焊接时间短,造成焊点灰暗。
适当增加焊接时间、调高预热温度和熔锡温度有助于不良的改善。
如果焊点看似碎裂、不平,大部分原因是元件在焊锡正要冷却形成焊点时振动而造成,这种情况下要注意链爪是否有异常振动。
波峰焊常见问题及解决方案范文

波峰焊常见问题及解决方案范文1、白色残留物在焊接或溶剂清洗过后发现有白色残留物在基板上,通常是松香的残留物,这类物质不会影响表面电阻质,但客户不接受。
(1)助焊剂通常是此问题主要原因,有时改用另一种助焊剂即可改善,松香类助焊剂常在清洗时产生白班,此时最好的方式是寻求助焊剂供货商的协助,产品是他们供应他们较专业。
(2)基板制作过程中残留杂质,在长期储存下亦会产生白斑,可用助焊剂或溶剂清洗即可。
(3)不正确的CURING亦会造成白班,通常是某一批量单独产生,应及时回馈基板供货商并使用助焊剂或溶剂清洗即可。
(4)厂内使用之助焊剂与基板氧化保护层不兼容,均发生在新的基板供货商,或更改助焊剂厂牌时发生,应请供货商协助。
(5)因基板制程中所使用之溶剂使基板材质变化,尤其是在镀镍过程中的溶液常会造成此问题,建议储存时间越短越好。
(6)助焊剂使用过久老化,暴露在空气中吸收水气劣化,建议更新助焊剂(通常发泡式助焊剂应每周更新,浸泡式助焊剂每两周更新,喷雾式每月更新即可)。
(7)使用松香型助焊剂,过完焊锡炉候停放时间太九才清洗,导致引起白班,尽量缩短焊锡与清洗的时间即可改善。
详情登陆粤成官网:(8)清洗基板的溶剂水分含量过高,降低清洗能力并产生白班。
应更新溶剂。
2、深色残余物及浸蚀痕迹通常黑色残余物均发生在焊点的底部或顶端,此问题通常是不正确的使用助焊剂或清洗造成。
(1)松香型助焊剂焊接后未立即清洗,留下黑褐色残留物,尽量提前清洗即可。
(2)酸性助焊剂留在焊点上造成黑色腐蚀颜色,且无法清洗,此现象在手焊中常发现,改用较弱之助焊剂并尽快清洗。
(3)有机类助焊剂在较高温度下烧焦而产生黑班,确认锡槽温度,改用较可耐高温的助焊剂即可。
3、绿色残留物绿色通常是腐蚀造成,特别是电子产品但是并非完全如此,因为很难分辨到底是绿锈或是其它化学产品,但通常来说发现绿色物质应为警讯,必须立刻查明原因,尤其是此种绿色物质会越来越大,应非常注意,通常可用清洗来改善。
波峰焊接常见不良情况及改进措施

波峰焊接常见不良情况及改进措施波峰焊接是一种常见的电子元器件焊接方法。
在进行波峰焊接过程中,常常会出现一些不良情况。
下面是一些常见的波峰焊接不良情况及相应的改进措施:1.焊接不良焊接不良是最常见的问题之一、主要表现为焊接点明显不良、焊接点形状不规则、焊接点飞溅等。
这种情况可能是由于焊接温度不到位、焊接时间过长、焊接速度过快等原因造成的。
改进措施可以是优化焊接参数,确保温度和时间的准确控制,并进行焊接前的材料准备。
2.焊接过热焊接过热是指焊接温度过高,导致焊接点产生熔化或烧毁。
这种情况可能是由于焊接温度设置过高、焊接时间过长、焊接速度过慢等原因造成的。
改进措施可以是降低焊接温度,缩短焊接时间,并确保焊接速度适中。
3.焊接不牢固焊接不牢固是指焊接点容易脱落或松动。
这种情况可能是由于焊接材料选择不当、焊接技术不熟练等原因造成的。
改进措施可以是选择适当的焊接材料,提高焊接技术,并进行焊接前的材料表面处理。
4.焊接变形焊接变形是指焊接后的零件出现形状偏差或形变。
这种情况可能是由于焊接过程中的热应力导致的。
改进措施可以是优化焊接工艺,采用合适的预热和冷却措施,以减少焊接过程中的热应力。
5.焊接气泡焊接气泡是指焊接点表面出现气泡或孔洞。
这种情况可能是由于焊接前的材料处理不当、焊接速度过快、焊接温度不到位等原因造成的。
改进措施可以是优化焊接前的材料处理工艺,控制焊接速度和温度,并确保焊接材料的质量。
总之,为了避免以上不良情况的发生,可以通过优化焊接参数、提高焊接技术、优化焊接材料等方式来改进焊接质量。
此外,还可以进行焊接前的材料准备、焊接中的温度和时间控制、焊接后的质量检验等措施,以确保焊接质量的稳定性和可靠性。
波峰焊过程中十五种常见不良分析

波峰焊过程中十五种常见不良分析波峰焊是一种常见的电子组装焊接方法,常用于表面贴装技术。
在波峰焊过程中,由于各种原因,可能会出现一些不良情况。
下面是十五种常见的波峰焊不良现象及其分析。
1.电极气泡:在焊接过程中,电极附近出现气泡。
可能原因包括焊盘上有焊通孔、元件附近的胶层不稳定或饱和,或是波峰炉中的气体未完全排除。
解决方法包括检查焊盘、调整胶层的饱和度或增加排气时间。
2.焊接引脚偏向:焊接引脚位置相对于焊盘中心有轻微偏离。
可能原因包括焊盘孔偏移、引脚与焊盘孔配合松动或使用不合适的焊接参数。
解决方法包括检查焊盘孔位置、更换焊盘或调整焊接参数。
3.引脚贴焊:引脚之间或引脚与焊盘之间出现短路现象。
可能原因包括焊盘上有过多的锡、焊接温度过高或焊接时间过长。
解决方法包括调整波峰炉的锡温度、控制锡量或降低波峰焊时间。
4.焊接亮点:焊接位置出现镜面反射的亮点。
可能原因包括过多的锡在焊接位置、焊接温度过高或焊接时间过长。
解决方法包括控制锡量、调整波峰炉的温度或缩短焊接时间。
5.锡球:焊盘上出现小球状物体。
可能原因包括过多的锡或焊接时引脚有轻微的震动。
解决方法包括控制锡量或检查焊接设备的震动情况。
6.渣球:焊盘上出现焊接渣滓。
可能原因包括焊盘或引脚上有杂物,或是焊接时引脚有震动。
解决方法包括清理焊盘和引脚,或修复焊接设备的震动问题。
7.引脚焊斑:焊盘上的焊接位置出现不均匀的焊锡。
可能原因包括焊盘不平、使用不合适的焊接参数或焊接位置不正确。
解决方法包括矫正焊盘、调整焊接参数或重新定位焊接位置。
8.焊盘脱落:焊盘完全或部分脱离基板。
可能原因包括焊盘与基板之间的附着力不够、焊盘尺寸不合适或基板材料不适合波峰焊。
解决方法包括增加焊盘与基板的附着力、更换合适尺寸的焊盘或考虑其他焊接方法。
9.焊盘凹陷:焊盘上出现凹陷或剥落。
可能原因包括焊盘材料不合适、焊接温度过高或焊接时间过长。
解决方法包括使用合适材料的焊盘、降低焊接温度或缩短焊接时间。
波峰焊问题改善方案

波峰焊问题改善方案波峰焊锡炉的制程分析及改善处理方案综合1 锡尖(1) 锡液中杂质或锡渣太多(2) 输送带传输角度太小(3) 输送带有振动现象(4) 锡波高度太高或太低(5) 锡波有扰流现象(6) 零件脚污染氧化(7) 零件脚太长(8) PCB未放置好(9) PCB可焊性不良,污染氧化(10) 输送带速度太快(11) 锡温过低或吃锡时间太短(12) 预热温度过低(13) 助焊剂喷量偏小(14) 助焊剂未润湿板面(15) 助焊剂污染或失去效能(16) 助焊剂比重过低2针孔及氧化(1) 输送带速度太快(2) Conveyor角度太大(3) 零件脚污染氧化(4) 锡波太低(5) 锡波有扰流现象(6) PCB过量印上油墨(7) PCB孔内粗糙(8) PCB孔径过小,零件阻塞,空气不易逸出(9) PCB孔径过大(10) PCB变形,未置于定位(11) PCB可焊性差,污染氧化,含水气(12) PCB贯穿孔印上油墨(13) PCB油墨未印到位(14) 焊锡温度过低或过高(15) 焊锡时间太长或太短(16) 预热温度过低(17) 助焊剂喷雾量偏大(18) 助焊剂污染成效能失去(19) 助焊剂比重过低或过高3短路(1) 输送带速度太快(2) Conveyor角度太小(3) 吃锡时间太短(4) 锡波有扰流现象(5) 锡波中杂质或锡渣过多(6) PCB两焊点间印有标记油墨,造成短路(7) 抗焊印刷不良(8) 线路设计过近或方向不良(9) 零件脚污染(10) PCB可焊性差,污染氧化(11) 零件太长或插件歪斜(12) 锡温过低(13) 预热温度过低(14) 助焊剂喷雾量太小(15) 助焊剂污染或失去效能(16) 助焊剂比重过低4 SMD漏焊(1) 改用双喷流焊喷嘴可减少漏焊(走双波)(2) 在PCB接近浮贴零件端点的铜膜加排气孔,可减少漏焊(3) 零件排列整齐及空出适当空间,可减少漏焊(4) 电路分布线设计时,零件长向和输送带方向或直角关系,可减少漏焊(5) 输送带速度太快(6) 零件死角或焊锡的阴影效应(7) 锡液中杂质或锡渣过多(8) PCB表面处理不当(9) PCB印刷油墨渗入铜箔(10) 零件受污染氧化(11) 锡波太低(12) 锡温过低(13) 预热温度过低(14) 助焊剂喷量太大或太小(15) 助焊剂污染或含水气(16) 助焊剂比重过低5 锡洞(1) 铜箔较多处应将铜箔较少处的锡拉走(靠边的锡易成锡洞)(2) PCB临时钻孔,造成铜箔有毛边,容易造成锡洞(3) 零件脚插件歪斜(4) 零件脚太长(5) 铜箔破孔(6) PCB孔径过大(7) 零件受污染氧化(8) PCB可焊性差,污染氧化含水气(9) PCB贯穿孔印有油墨(10) PCB油墨未印到位(11) 预热温度过低(12) 助焊剂喷量过大或过小(13) 助焊剂污染或含水气(14) 助焊剂比重过低6 多锡(1) 链条速度太快(2) 轨道角度太小(3) 锡波不正常,有扰流现象(4) 锡液中杂质或锡渣过多(5) 焊锡面设计不良(6) PCB未放置好(7) 预热温度过低(8) 锡温过低或吃锡时间太短(9) 助焊剂比重低或过高(比重过高,残留物越多)7 焊点不光滑(空焊,吃锡不良)(1) 预热温度过低或太高(2) 锡温过低或过高(3) 锡液中杂质或锡渣过多(4) PCB可悍性不良,污染氧化(5) 零件脚污染氧化(6) 链条有微振现象(7) 链条速度太快或太慢8 锡珠(1) 锡液中含水分(2) 框架底部含水滴太多(清洗机内未烘干)(3) PCB未插零件大孔,因PCB的弯曲,造成锡珠溢上来(4) PCB保护层处理不当(5) 抗焊印刷不良,防焊线路漏铜,造成焊锡面粘上锡珠(较难排除)防焊胶未干(6) 超音波过大(7) 锡波太高或不平(8) 锡波有扰流现象(9) 锡液中杂质或锡渣过多(10) 零件脚污染(11) PCB可焊性差,污染氧化,含水气(12) 链条的速度太快(13) 锡温过高(14) 预热温度过低(15) 助焊剂喷量过大(16) 助焊剂污染或含水气(17) 助焊剂比重过低9 锡少(1) 零件脚细而铜箔面积较大,相对吃锡高度较低,易造成锡少的误断(2) 轨道角度太大(3) 锡波有扰流现象(4) 锡波太低或太高(5) 助焊剂种类选择错误(6) 零件脚污染,氧化(7) 零件脚太长(8) PCB贯穿孔印上油墨(9) PCB油墨未印到位(10) PCB孔径太大(11) PCB铜箔过大或过小(12) PCB变形,未置于定位(13) PCB可焊性差,污染氧化,含水气(14) 输送带速度太快或太慢(15) 焊锡时间太长或太短(16) 锡温过高(17) 预热温度过低或过高(18) 助焊剂喷量太小(19) 助焊剂污染或失去功效(20) 助焊剂比重过低或过高10 不沾锡(1) 框架过高,不平均(2) 锡波太低(3) 锡液中杂质或锡渣过多(4) 零件脚污染,氧化(5) PCB或零件过期及储存不当(6) PCB表面处理不当(7) PCB贯穿孔印上油墨(8) PCB可焊性差,污染氧化,含水气,油脂(9) 焊锡时间太短(10) 锡温过低(11) 预热温度过低或过高(12) 助焊剂喷量太小(13) 助焊剂污染或失去效能(14) 助焊剂比重过低或过高11 退锡:(1) 助焊剂比重过低或过高(2) 助焊剂污染或失去效能(3) 预热温度过高或过低(4) 锡温过高或过低(5) PCB可焊性差,污染氧化,含水气,油脂(6) PCB无表面处理污染,药水未洗干净(7) 锡波太高(8) 助焊剂种类选择错误(9) 焊锡时间太长12 锡渣(1) 后挡板太高,再降低一点后,使锡渣暂时经后挡板流溢.(2) 零件脚太长(3) 抗焊印刷不够(4) 印刷油墨不良(5) 锡液中杂质或锡渣过多(6) 锡波过低(7) 输送带速度太快(8) 焊锡时间太短(9) 锡温过低(10) 预热温度过低(11) 助焊剂喷量太小(12) 助焊剂比重过低(13) 输出线熔损13 输出线熔损(1) 预热温度过高(2) 线材耐热差,材料不良(3) 锡温过高(4) 输送带速度太慢(5) PCB卡列停留过久在锡炉中(6) 输出线未摆好,以至于碰到预热板或锡槽内14 PCB彎曲(1) PCB四周多用夾具扶助支撐,可克服板子彎曲(2) PCB卡列停留過久在錫爐中(3) 第一次過爐(4) 零件過重,集中于某一區域(5) PCB尺寸設計不良(6) PCB載重過多(7) PCB材料本身就彎曲變形(8) 板夾得太緊(9) 焊錫時間太長(10) 輸送帶速度太慢(11) 錫溫過高(12) 預熱溫度過低或過高15 白色殘留物(1) 助焊劑中含水分(2) 預熱溫度過高(3) 錫溫過高(4) 焊錫時間太長或錫波太高(5) PCB處理不當(保護層)(6) 抗焊印刷不良(7) 助焊劑種類選擇錯誤(8) PCB本身含有水氣(9) 清潔機的水質不干淨(10) PCB銅面氧化防止劑之配方不相容(11) 焊錫后停留過久時間才清洗16 溢錫(1) 錫波不平或太高(2) PCB本身不平或彎曲(3) PCB孔徑太大(4) 預熱溫度過高或過低(5) 速度過慢易使PCB彎曲而溢錫(6) 焊錫溫度過高(7) PCB未放好(8) 設計不良,零件過重(9) 框架過緊, PCB中間易變形溢錫(10) 超音波過大。
波峰焊工艺常见问题及改良方案

波峰焊工艺常见问题及改良方案一、沾锡不良:这种情况是不可接受的缺点,在焊点上只有部分沾此类污染物锡. 原因及改善方式如下:1.外界的污染物如油,脂,腊,灰尘等,此类污染物通常可用溶剂清洗, 此类污染物有时是在印刷防焊剂时沾上.2.SILICON OIL通常用於脱模及润滑之用,通常会在基板及零件脚上发现, 并SILICONOIL不易清理,因此使用它要非常小心尤其当它做抗氧化油常会发生问题,因它会蒸发沾在基板上造成沾锡不良.3.因储存不良或基板制程上的问题发生氧化,助焊剂无法除去时沾锡不良,过两次锡焊或可解决此问题.4.喷助焊剂不良,造成原因为气压不稳定或不足,喷头坏或喷雾控制系统不良,致使喷助焊剂不稳或不均及时喷时不喷,使基板部分没有沾到助焊剂.5.PCB板吃锡时间不足或锡温不够会造成锡焊不良,因为熔锡需要足够的温度及时间WETTING,通常焊锡温度应高於熔点温度50 ℃--80 ℃之间,沾锡总时间为3秒.二、局部沾锡不良:此一情形与沾锡不良相似,不同的是局部锡不良不会露出铜箔面.只有薄薄的一层锡无法形成饱满的焊点,波峰不平.三、冷焊或焊点不亮焊点看似碎裂,不平,大部分原因是零件在焊锡正要冷却形成焊点时振动造成,注意锡炉运输是否有异常振动.四、焊点破裂此一情形通常是焊锡, 基板,导通孔及元件脚之间膨胀系数未配合造成,应在基板材质, 元件材料及设计上去改善.五、焊点锡量太大通常在评定一个焊点,希望能又大又圆又胖的焊点,但事实上过大的焊点对导电性及抗拉强度未必有所帮助.1.锡炉输送角度不正确会造成焊点过大,倾斜角度由1—7度依PCB板的设计方式调整,角度越大沾锡越薄, 角度越小沾锡越厚.2.提高锡槽温度,加长焊锡时间,使多馀的锡再回流到锡槽.来改善3.提高预热温度,可减少PCB板沾锡所需热量,曾加助焊效果.4.改变助焊剂比重,降低助焊剂比重,通常比重越高吃锡越厚越易短路, 比重越低吃锡越薄越易造成锡桥,锡尖.六、锡尖(冰柱)此一问题通常发生在DIP或WIVE的焊接制程上,在电子元件脚顶端或焊点上发现有冰尖般的锡.1.PCB板的可焊性差, 此一问题通常伴随著沾锡不良,应从PCB板的可焊性去探讨,可试由提升助焊剂比重来改善2.PCB板上金道(PAD)面积过大,可用绝缘(防焊)漆线将金道分隔来改善, 绝缘(防焊)漆线在大金道面分隔成5mm乘10mm区块.3.锡槽温度不足吃锡时间太短,可用提高锡槽温度,加长焊锡时间,使多馀的锡再回流到锡槽来改善.4.PCB板出波峰后之冷却风流角度不对,不可朝锡槽方向吹,会造成锡点急速冷却,多馀焊锡无法受重力於内聚力拉回锡槽.5.手焊时产生锡尖,通常为烙铁温度太低,致锡温度不足无法立即因内聚力回缩形成焊点. 可用提高烙铁温度,加长焊锡时间.七、防焊绝缘漆留有残锡1.PCB板制作时残留物与助焊剂不相容的物质,在预热之后熔化产生粘性粘著焊锡形成,可用丙酮(已被蒙特娄公约禁用之化学溶剂)氯化烯类等溶剂来清洗,若清洗后还是无法改善,则PCB板的层材CURING不正确的可能,本项事故应即使回馈PCB板供应商.2.不正确的PCB板CURING会造成此一现象,可在插件前先进行烘烤120℃两小时, 本项事故应即使回馈PCB板供应商.3.锡渣被PUMP打入锡槽内再喷流出来, 造成PCB板面沾上锡渣,此一问题较为单纯良好的锡炉维护,锡槽正确的锡面高度.。
波锋焊-去除短路
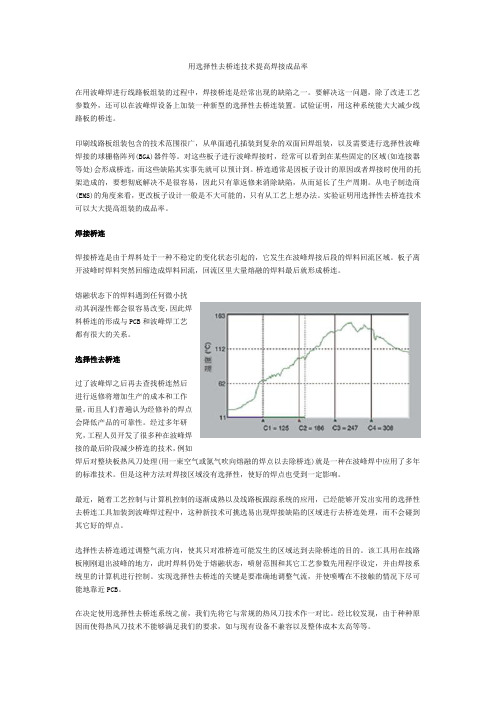
用选择性去桥连技术提高焊接成品率在用波峰焊进行线路板组装的过程中,焊接桥连是经常出现的缺陷之一。
要解决这一问题,除了改进工艺参数外,还可以在波峰焊设备上加装一种新型的选择性去桥连装置。
试验证明,用这种系统能大大减少线路板的桥连。
印刷线路板组装包含的技术范围很广,从单面通孔插装到复杂的双面回焊组装,以及需要进行选择性波峰焊接的球栅格阵列(BGA)器件等。
对这些板子进行波峰焊接时,经常可以看到在某些固定的区域(如连接器等处)会形成桥连,而这些缺陷其实事先就可以预计到。
桥连通常是因板子设计的原因或者焊接时使用的托架造成的,要想彻底解决不是很容易,因此只有靠返修来消除缺陷,从而延长了生产周期。
从电子制造商(EMS)的角度来看,更改板子设计一般是不大可能的,只有从工艺上想办法。
实验证明用选择性去桥连技术可以大大提高组装的成品率。
焊接桥连焊接桥连是由于焊料处于一种不稳定的变化状态引起的,它发生在波峰焊接后段的焊料回流区域。
板子离开波峰时焊料突然回缩造成焊料回流,回流区里大量熔融的焊料最后就形成桥连。
熔融状态下的焊料遇到任何微小扰动其润湿性都会很容易改变,因此焊料桥连的形成与PCB和波峰焊工艺都有很大的关系。
选择性去桥连过了波峰焊之后再去查找桥连然后进行返修将增加生产的成本和工作量,而且人们普遍认为经修补的焊点会降低产品的可靠性。
经过多年研究,工程人员开发了很多种在波峰焊接的最后阶段减少桥连的技术,例如焊后对整块板热风刀处理(用一束空气或氮气吹向熔融的焊点以去除桥连)就是一种在波峰焊中应用了多年的标准技术。
但是这种方法对焊接区域没有选择性,使好的焊点也受到一定影响。
最近,随着工艺控制与计算机控制的逐渐成熟以及线路板跟踪系统的应用,已经能够开发出实用的选择性去桥连工具加装到波峰焊过程中,这种新技术可挑选易出现焊接缺陷的区域进行去桥连处理,而不会碰到其它好的焊点。
选择性去桥连通过调整气流方向,使其只对准桥连可能发生的区域达到去除桥连的目的。
波蜂焊接的不良原因及对策

波蜂焊接的不良原因及对策吃锡不良其现象为线路的表面有部份未沾到锡,原因为:1.表面附有油脂、杂质等,可以溶剂洗净。
2.基板制造过程时打磨粒子遗留在线路表面,此为印刷电路板制造厂家的问题。
3.硅油,一般脱模剂及润滑油中含有此种油类,很不容易被完全清洗干净。
所以在电子零件的制造过程中,应尽量避免化学品含有硅油者。
焊锡炉中所用的氧化防止油也须留意不是此类的油。
4.由于贮存时间、环境或制程不当,基板或零件的锡面氧化及铜面晦暗情形严重。
换用助焊剂通常无法解决此问题,重焊一次将有助于吃锡效果。
5.助焊剂使用条件调整不当,如发泡所需的空气压力及高度等。
比重亦是很重要的因素之一,因为线路表面助焊剂分布数量的多寡受比重所影响。
检查比重亦可排除因卷标贴错,贮存条件不良等原因而致误用不当助焊剂的可能性。
6.焊锡时间或温度不够。
一般焊锡的操作温度较其熔点温度高55~80℃7.不适合之零件端子材料。
检查零件,使得端子清洁,浸沾良好。
8.预热温度不够。
可调整预热温度,使基板零件侧表面温度达到要求之温度约90℃~110℃。
9.焊锡中杂质成份太多,不符合要求。
可按时测量焊锡中之杂质,若不合规定超过标准,则更换合于标准之焊锡。
退锡多发生于镀锡铅基板,与吃锡不良的情形相似;但在欲焊接的锡路表面与锡波脱离时,大部份已沾在其上的焊锡又被拉回到锡炉中,所以情况较吃锡不良严重,重焊一次不一定能改善。
原因是基板制造工厂在渡锡铅前未将表面清洗干净。
此时可将不良之基板送回工厂重新处理。
冷焊或焊点不光滑此情况可被列为焊点不均匀的一种,发生于基板脱离锡波正在凝固时,零件受外力影响移动而形成的焊点。
保持基板在焊锡过后的传送动作平稳,例如加强零件的固定,注意零件线脚方向等;总之,待焊过的基板得到足够的冷却再移动,可避免此一问题的发生。
解决的办法为再过一次锡波。
至于冷焊,锡温太高或太低都有可能造成此情形。
焊点裂痕造成的原因为基板、贯穿孔及焊点中零件脚等热膨胀收缩系数方面配合不当,可以说实际上不算是焊锡的问题,而是牵涉到线路及零件设计时,材料及尺寸在热方面的配合。
波峰焊常见焊接缺陷原因分析及预防对策
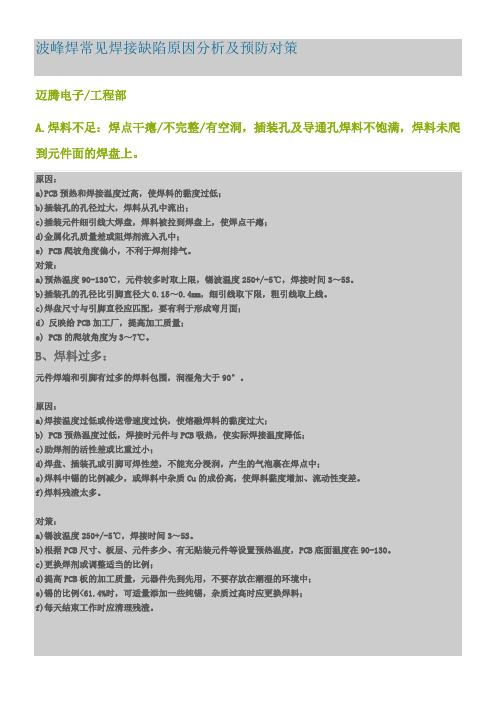
波峰焊常见焊接缺陷原因分析及预防对策迈腾电子/工程部A.焊料不足:焊点干瘪/不完整/有空洞,插装孔及导通孔焊料不饱满,焊料未爬到元件面的焊盘上。
原因:a)PCB预热和焊接温度过高,使焊料的黏度过低;b)插装孔的孔径过大,焊料从孔中流出;c)插装元件细引线大焊盘,焊料被拉到焊盘上,使焊点干瘪;d)金属化孔质量差或阻焊剂流入孔中;e) PCB爬坡角度偏小,不利于焊剂排气。
对策:a)预热温度90-130℃,元件较多时取上限,锡波温度250+/-5℃,焊接时间3~5S。
b)插装孔的孔径比引脚直径大0.15~0.4mm,细引线取下限,粗引线取上线。
c)焊盘尺寸与引脚直径应匹配,要有利于形成弯月面;d)反映给PCB加工厂,提高加工质量;e) PCB的爬坡角度为3~7℃。
B、焊料过多:元件焊端和引脚有过多的焊料包围,润湿角大于90°。
原因:a)焊接温度过低或传送带速度过快,使熔融焊料的黏度过大;b) PCB预热温度过低,焊接时元件与PCB吸热,使实际焊接温度降低;c)助焊剂的活性差或比重过小;d)焊盘、插装孔或引脚可焊性差,不能充分浸润,产生的气泡裹在焊点中;e)焊料中锡的比例减少,或焊料中杂质Cu的成份高,使焊料黏度增加、流动性变差。
f)焊料残渣太多。
对策:a)锡波温度250+/-5℃,焊接时间3~5S。
b)根据PCB尺寸、板层、元件多少、有无贴装元件等设置预热温度,PCB底面温度在90-130。
c)更换焊剂或调整适当的比例;d)提高PCB板的加工质量,元器件先到先用,不要存放在潮湿的环境中;e)锡的比例<61.4%时,可适量添加一些纯锡,杂质过高时应更换焊料;f)每天结束工作时应清理残渣。
C、焊点桥接或短路原因:a) PCB设计不合理,焊盘间距过窄;b)插装元件引脚不规则或插装歪斜,焊接前引脚之间已经接近或已经碰上;c) PCB预热温度过低,焊接时元件与PCB吸热,使实际焊接温度降低;d)焊接温度过低或传送带速度过快,使熔融焊料的黏度降低;e)阻焊剂活性差。
影响波峰焊焊接质量不良分析及解决对策

夹具损坏 第二次再过锡 抗焊印刷不夠 锡液杂质过多(芜湖、武汉 锡炉焊锡铜、磷杂质较多,日 本主板引锡焊盘) 焊接角度过小
过多焊锡导致无法 看见元件脚,甚至 连元件脚的棱角都 看不到
6、冷焊
原因分析:
传送帶微振现象、速度太快
波峰焊接高度不够
焊锡波面不正常
夹具过热 •
因温度不够造成的 表面焊接现象,无
金属光泽
7、 空焊
原因分析:
印刷电路板氧化,受污染
助焊剂喷雾不正常
焊锡波不正常,有扰流现象
预热温度太高
焊锡时间太短
基材元器件插入孔全 部露出,元器件引脚 及焊盘未被焊料润湿
9、 焊球现象:(锡珠)
原因分析:
助焊剂喷雾不正常 锡液杂质过多、波峰锡面不平稳 印刷电路板及零件受污染 预热温度太高,太低 焊锡时间太短 焊接过程中轨道有抖动现象
影响波峰焊焊接质量不良分析及解决对策
1、拉尖
原因分析:
元器件引脚有毛刺 锡炉焊接温度过底 预热溫度过高或时间过长 焊锡时间太长 助焊剂比重太低,喷雾不正常
元器件引脚头部 有焊锡拉出呈尖
形
2、焊点上有气孔
原因分析: 元器件引脚受污染 PCB板氧化 PCB板受污染或受潮
焊点内部有 针眼或大小 不等的孔洞
成圆形锡珠黏在 底板或板面的表
面上
3、 短路
原因分析:
插件位置不当 夾具损坏 元器件引脚过长 焊锡时间过长、锡温过底 助焊剂选择错误、助焊喷雾不正常 焊锡波管不正常,有扰流现象 焊接角度过小
相邻焊点之间 的焊料连接在 一起,形成桥
连
4、 抗焊現象
原因分析:
零件污染 印刷電路板锡(包焊)
波峰焊过程产生故障的主要原因及预防对策
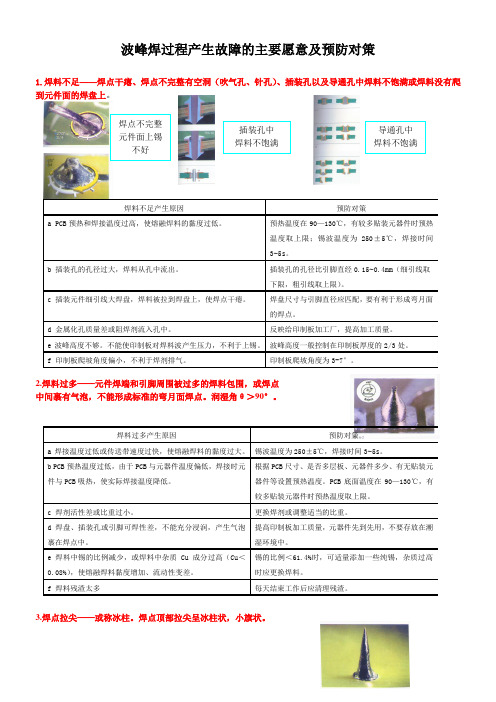
波峰焊过程产生故障的主要愿意及预防对策1.焊料不足——焊点干瘪、焊点不完整有空洞(吹气孔、针孔)、插装孔以及导通孔中焊料不饱满或焊料没有爬到元件面的焊盘上。
2.焊料过多——元件焊端和引脚周围被过多的焊料包围,或焊点 中间裹有气泡,不能形成标准的弯月面焊点。
润湿角θ>90°。
3.焊点拉尖——或称冰柱。
焊点顶部拉尖呈冰柱状,小旗状。
焊点不完整 元件面上锡不好插装孔中 焊料不饱满导通孔中 焊料不饱满焊料不足产生原因预防对策a PCB 预热和焊接温度过高,使熔融焊料的黏度过低。
预热温度在90—130℃,有较多贴装元器件时预热温度取上限;锡波温度为250±5℃,焊接时间3~5s 。
b 插装孔的孔径过大,焊料从孔中流出。
插装孔的孔径比引脚直经0.15~0.4mm (细引线取下限,粗引线取上限)。
c 插装元件细引线大焊盘,焊料被拉到焊盘上,使焊点干瘪。
焊盘尺寸与引脚直径应匹配,要有利于形成弯月面的焊点。
d 金属化孔质量差或阻焊剂流入孔中。
反映给印制板加工厂,提高加工质量。
e 波峰高度不够。
不能使印制板对焊料波产生压力,不利于上锡。
波峰高度一般控制在印制板厚度的2/3处。
f 印制板爬坡角度偏小,不利于焊剂排气。
印制板爬坡角度为3-7°。
焊料过多产生原因 预防对策a 焊接温度过低或传送带速度过快,使熔融焊料的黏度过大。
锡波温度为250±5℃,焊接时间3~5s 。
b PCB 预热温度过低,由于PCB 与元器件温度偏低,焊接时元件与PCB 吸热,使实际焊接温度降低。
根据PCB 尺寸、是否多层板、元器件多少、有无贴装元器件等设置预热温度。
PCB 底面温度在90—130℃,有较多贴装元器件时预热温度取上限。
c 焊剂活性差或比重过小。
更换焊剂或调整适当的比重。
d 焊盘、插装孔或引脚可焊性差,不能充分浸润,产生气泡裹在焊点中。
提高印制板加工质量,元器件先到先用,不要存放在潮湿环境中。
波峰焊常见故障解答

波峰焊常见故障原因及处理方法1.开机时电脑没有任何反应?答:首先确认主机电源是否供电,方法就是将电脑主机的输入电源线拔下测试电压;再确认主机上的电脑硬盘指示灯是不是亮的,如果主机给电但硬盘灯不亮,则说明可能是电脑主机的电源出了问题,此时需要将主机拆出,检查主板有否供电,更换匹配的电源;如果是硬盘指示灯亮,显示器也有电,但就是无显示,则看电脑启动后主机有没有发生嘟嘟的报警声,如果有,可以确定是电脑内存坏了,更换相应型号的内存;如果电脑可以进入启动界面,但有其他的错误提示,如”boot failure”,则可能是硬盘坏了,更换备用硬盘。
2.开机后启动波峰焊软件时提示工作文件丢失?答:首先检查C盘LN文件夹中是不是有机器的工作文件(一般为Work File名),如果没有的话,要从D盘的备份文件中将备份的工作文件拷贝到LN文件夹下,重新启动,如果还不行,可能是程序文件丢失,从“控制面板”的“添加删除程序”里将“日东发展有限公司”卸载,然后重新安装软件即可。
3.机器提示“测温模块错误”?答:第一,有可能是机器电箱里面的控制板上的几个大的端子脱落或者松掉了;第二,有可能是哪几个端子位置不对或者顺序颠倒了,按编号插好端子;第三,可能是工控机上的板卡上的端子松掉了或者板接触不良;第四,温控板卡坏,要报告处理。
4.波峰焊预热温度下降很快?答:第一、如果是单个预热区温度下降,则可能是发热丝断了;第二,如果所有的预热区温度都下降,并且锡炉温度也下降,则要检查电箱中的过流保护开关,是否有跳闸的,如果有跳闸的,需要将电源关闭后再将此开关合上,然后再启动;第三,检查机器的动力电源接触器的输出,看是否有掉相的现象,如果输入未掉相,输出掉相,则可能是输出处的线没有拧紧,或者是接触器坏了。
5.预热持续上升?答:关闭预热后预热还是一直加热,则肯定是温控固态出了问题,在断电的情况下用万用表量测A1和A2之间,如果短路的话则可以肯定是温控固态被击穿了,正常的情况下温控固态是给信号的时候接通,而不给信号的时候断开的。
4-3-波峰焊接中产生锡珠(球)、短路问题分析和正确的工艺方法解析

• 锡波高度过低
• 焊接时间过长
• 助焊剂活性不足
进板方向
五. 工艺优化改进措施(实验)
• 1、优化波峰焊温度曲线
• 2、改用亚光(粗糙类型)solder mask
• 3、扰流波与平滑波实验
• 4、减少两个波之间的降落(波谷)深度
• 5、控制液面高度,减少锡波的降落高度等
1、优化波峰焊温度曲线
② 与物料管理和存储条件有关。PCB和元 件受潮或元件引脚严重氧化,波峰焊时水 严格物料管理,对受潮的 气挥发炸锡造成锡珠,或化学反应剧烈产 PCB和元件进行去潮处理。 生飞溅。在PCB板的元件面形成锡珠。 ③ 预热温度过低,助焊剂中的溶剂、水气 提高预热温度,使PCB板 及其他气体没有挥发干净。 顶面温度达到至少100℃ ④与设计有关。金属化孔过大,进入孔内 的焊料过多 适当降低波峰高度 修改设计
优化后的效果 1、使183以下的温度提高了5~10℃ 2、对减少锡珠有一定的改善
2、改用亚光(粗糙类型)solder mask
⑴ 亚光(粗糙类型)的solder mask 对背面锡珠 减少有很大帮助
⑵ 亚光(粗糙类型)的solder mask 对连接器锡
连减少也有帮助
3、扰流波与平滑波实验
扰流波与平滑波各有优缺点: • 扰流波能够减少锡连
产生原因
预防对策
④ 与阻焊层的质量有关。比较粗燥的阻 焊层和锡球有更小的接触面,锡球不易 粘在PCB表面。在无铅焊接过程中,高 选择亚光型和耐高温的阻焊层材料; 温会使阻焊层更柔滑,更易造成锡球粘 尽量设置较低的波峰温度。 在PCB板上。另外如果阻焊层不耐高温, 高温下会发粘,也会造成锡球粘在PCB 板上。 严格来料检验,元器件先到先用,不要 ⑤ 元器件焊端和引脚、印制电路基板的 存放在潮湿环境中,不要超过规定的使 焊盘氧化或污染,或印制板受潮 用日期;对印制板进行清洗和去潮处理 锡铅焊料中锡的比例<61.4%时,可适 ⑥ 焊料中锡的比例减少,焊锡的氧化和 量添加一些纯锡,还可采用重力法清除 杂质含量的影响 一些Cu的化合物。每天结束工作后应清 理残渣,杂质过高时应更换焊料。 ⑦ 波峰焊接面SMC/SMD没有过孔, 焊 接时排气不畅, 从而引起飞溅及锡球 可设计一些排气孔
波峰焊技术及常见问题解决方法
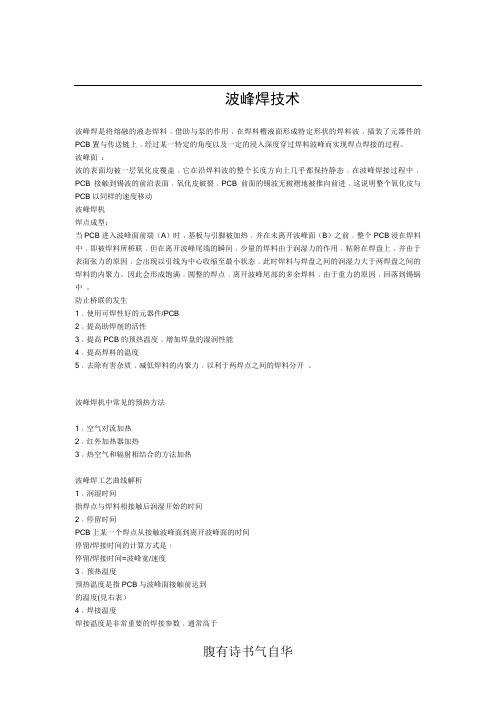
波峰焊技术波峰焊是将熔融的液态焊料﹐借助与泵的作用﹐在焊料槽液面形成特定形状的焊料波﹐插装了元器件的PCB置与传送链上﹐经过某一特定的角度以及一定的浸入深度穿过焊料波峰而实现焊点焊接的过程。
波峰面:波的表面均被一层氧化皮覆盖﹐它在沿焊料波的整个长度方向上几乎都保持静态﹐在波峰焊接过程中﹐PCB接触到锡波的前沿表面﹐氧化皮破裂﹐PCB前面的锡波无皲褶地被推向前进﹐这说明整个氧化皮与PCB以同样的速度移动波峰焊机焊点成型:当PCB进入波峰面前端(A)时﹐基板与引脚被加热﹐并在未离开波峰面(B)之前﹐整个PCB浸在焊料中﹐即被焊料所桥联﹐但在离开波峰尾端的瞬间﹐少量的焊料由于润湿力的作用﹐粘附在焊盘上﹐并由于表面张力的原因﹐会出现以引线为中心收缩至最小状态﹐此时焊料与焊盘之间的润湿力大于两焊盘之间的焊料的内聚力。
因此会形成饱满﹐圆整的焊点﹐离开波峰尾部的多余焊料﹐由于重力的原因﹐回落到锡锅中。
防止桥联的发生1﹐使用可焊性好的元器件/PCB2﹐提高助焊剞的活性3﹐提高PCB的预热温度﹐增加焊盘的湿润性能4﹐提高焊料的温度5﹐去除有害杂质﹐减低焊料的内聚力﹐以利于两焊点之间的焊料分开。
波峰焊机中常见的预热方法1﹐空气对流加热2﹐红外加热器加热3﹐热空气和辐射相结合的方法加热波峰焊工艺曲线解析1﹐润湿时间指焊点与焊料相接触后润湿开始的时间2﹐停留时间PCB上某一个焊点从接触波峰面到离开波峰面的时间停留/焊接时间的计算方式是﹕停留/焊接时间=波峰宽/速度3﹐预热温度预热温度是指PCB与波峰面接触前达到的温度(見右表)4﹐焊接温度焊接温度是非常重要的焊接参数﹐通常高于焊料熔点(183°C )50°C ~60°C大多数情况是指焊锡炉的温度实际运行时﹐所焊接的PCB焊点温度要低于炉温﹐这是因为PCB吸热的结果SMA類型元器件預熱溫度單面板組件通孔器件與混裝90~100雙面板組件通孔器件100~110雙面板組件混裝100~110多層板通孔器件115~125多層板混裝115~125波峰焊工艺参数调节1﹐波峰高度波峰高度是指波峰焊接中的PCB吃錫高度。
波峰焊问题分析与解决方案
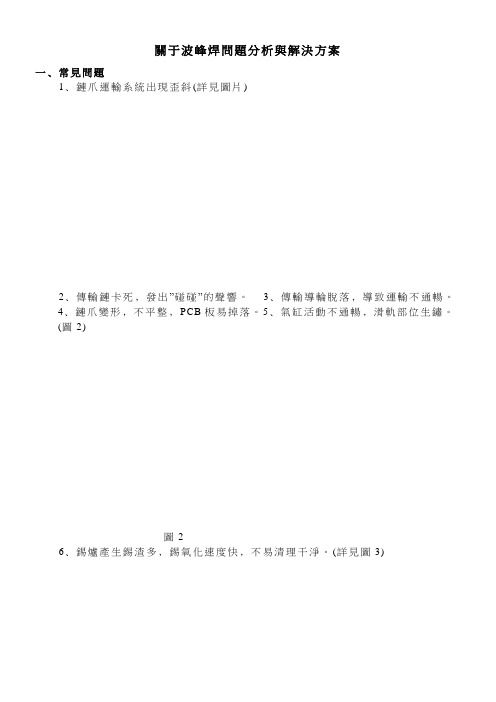
關于波峰焊問題分析與解決方案一﹑常見問題1﹑鏈爪運輸系統出現歪斜(詳見圖片)2﹑傳輸鏈卡死﹐發出”碰碰”的聲響。
3﹑傳輸導輪脫落﹐導致運輸不通暢。
4﹑鏈爪變形﹐不平整﹐PCB板易掉落。
5﹑氣缸活動不通暢﹐滑軌部位生鏽。
(圖2)圖26﹑錫爐產生錫渣多﹐錫氧化速度快﹐不易清理干淨。
(詳見圖3)圖37﹑傳輸系統變形﹐產生中間寬﹑兩邊窄的現象。
8﹑波峰達不到所需的高度。
9﹑波峰焊加錫時將不同廠牌的錫加入錫爐。
10﹑波峰焊PCB板過波峰焊時﹐有虛焊﹐短路﹐表面附有錫渣現象。
11﹑接駁口與傳輸帶的距離稍大﹐元件常被卡出。
12﹑錫渣不能從波峰邊緣流出﹐導致沾附在PCB板上面。
13﹑波峰錫槽因螺絲斷掉有裂縫﹐錫爐里的錫被濺出。
14﹑波峰2的爐道堵塞﹐錫不能從波峰口噴出二﹑問題分析1﹑鏈爪台的同步手柄內擋銷移位﹐旋轉手柄時﹐鏈爪台兩邊的升降螺杆不能同步轉向﹐產生一邊低一邊高的歪斜現象。
2﹑工程在保養過程中﹐對各傳輸鏈加防鏽劑及潤滑油后﹐產線員在打掃清洗時﹐將防鏽劑及潤滑油擦掉使傳輸鏈軸生鏽﹐導輪不能與傳輸鏈同時轉動﹐至使發生”碰碰”的響聲。
3﹑傳輸鏈的松緊螺絲向中間偏移﹐使傳輸鏈松動﹐在接駁PCB時﹐易掉板。
4﹑由于氣缸的動向原按上級指示﹐不讓噴霧系統滑動而改為固定式﹐由于氣壓對著PCB中間噴射﹐常將PCB板上的元件噴掉﹐而氣缸滑軌在助焊劑的浸蝕下生鏽。
5﹑生產及儀保在使用時﹐剪落的元件端子由于未被清理干淨﹐在浸錫時﹐掉落于錫爐里﹐甚至有時生產在插件時元件腳未剪﹐元件被刮落于錫爐﹐而在使用后不及時對錫爐進行清理﹐元件被馬達卷進錫槽﹐使錫槽堵塞。
6﹑由于錫槽里的污垢太多﹐使錫槽堵塞﹐錫不能從波峰口噴出。
7﹑鏈爪運輸系統不平﹐過產品時一邊高﹐一邊低。
所以產生短路﹐一邊虛焊8每次對波峰焊加錫時都不是固定的人員﹐因產線干部在沒有確定不同廠牌的錫時﹐就對波峰焊進行加錫。
造成不同廠牌的錫混合在一起。
三﹑解決方案1﹑將同步手柄拆下﹐重新裝配﹐使鏈爪台兩邊的螺絲杆能同時轉向。
- 1、下载文档前请自行甄别文档内容的完整性,平台不提供额外的编辑、内容补充、找答案等附加服务。
- 2、"仅部分预览"的文档,不可在线预览部分如存在完整性等问题,可反馈申请退款(可完整预览的文档不适用该条件!)。
- 3、如文档侵犯您的权益,请联系客服反馈,我们会尽快为您处理(人工客服工作时间:9:00-18:30)。
波峰焊短路的原因及解决方案
波峰焊是一种常见的电弧焊接方法,广泛应用于金属制品的生产加工中。
然而,在实际操作中,我们有时会遇到波峰焊短路的问题,导致焊接质量下降甚至造成设备损坏。
本文将针对波峰焊短路的原因及解决方案展开讨论。
我们来了解一下波峰焊的原理。
波峰焊是利用电弧产生高温,将焊接材料熔化并连接在一起的过程。
在焊接过程中,电流通过焊接电极和工件之间的接触区域,形成一个电弧。
电弧在焊接区域产生高温,使工件表面熔化,从而实现焊接。
然而,在波峰焊过程中,可能会出现短路现象。
波峰焊短路是指焊接过程中,电弧突然熄灭或电流突然增大,导致电弧不稳定或无法维持。
造成波峰焊短路的原因有多种,下面将分别进行讨论。
焊接电极的损坏是导致波峰焊短路的常见原因之一。
焊接电极在使用过程中会受到磨损和烧蚀,当电极表面磨损严重或烧蚀过深时,电弧就容易熄灭或不稳定,从而导致短路。
解决这个问题的方法是定期更换焊接电极,保持电极表面的光滑和整洁,以确保电弧的稳定性。
焊接工件表面的污染也是导致波峰焊短路的原因之一。
焊接工件表面的油污、氧化物或其他杂质会导致电弧不稳定,从而引发短路。
解决这个问题的方法是在焊接前彻底清洁工件表面,去除油污和杂
质,可以使用溶剂或机械方法清洁工件表面。
焊接电流过大也可能导致波峰焊短路。
当焊接电流超过焊接材料的承载能力时,电弧会变得不稳定,从而引发短路。
解决这个问题的方法是调整焊接电流,使其适应焊接材料的特性和要求。
要根据焊接材料的种类和厚度确定合适的焊接电流,以保证焊接质量。
焊接速度过快也可能导致波峰焊短路。
当焊接速度过快时,焊接区域的热量不足以使工件表面熔化,从而导致电弧不稳定或熄灭。
解决这个问题的方法是降低焊接速度,确保焊接区域的温度达到熔化温度,并保持稳定。
波峰焊短路是影响焊接质量的一个重要问题。
我们可以通过定期更换焊接电极、清洁工件表面、调整焊接电流和降低焊接速度等方法来解决波峰焊短路问题。
通过合理的操作和维护,我们可以提高波峰焊的质量和效率,确保焊接工艺的稳定性和可靠性。