轮对压装过程中几个关键工艺参数的分析
轮轴几何参数在轮对压装中的应用分析
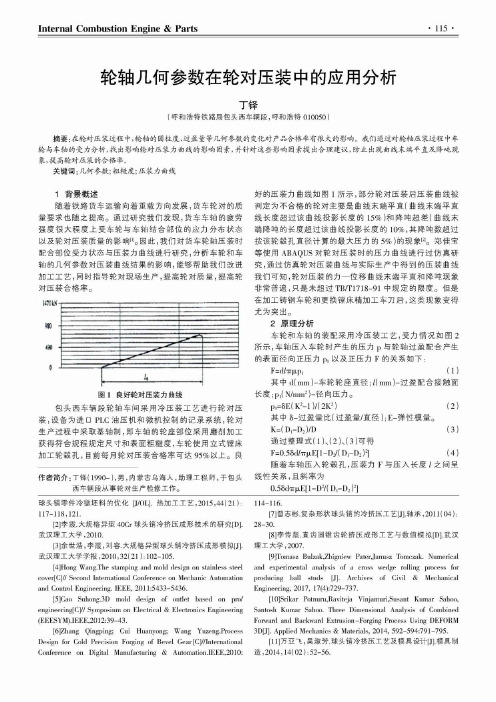
Internal Combustion Engine & Parts• 115 •轮轴几何参数在轮对压装中的应用分析丁铎(呼和浩特铁路局包头西车辆段,呼和浩特010050 )摘要:在轮对压装过程中,轮轴的圆柱度、过盈量等几何参数的变化对产品合格率有很大的影响。
我们通过对轮轴压装过程中车轮与车轴的受力分析,找出影响轮对压装力曲线的影响因素,并针对这些影响因素提出合理建议,防止出现曲线末端平直及降吨现 象,提高轮对压装的合格率。
关键词:几何参数;粗糙度;压装力曲线1背景概述随着铁路货车运输向着重载方向发展,货车轮对的质 量要求也随之提高。
通过研究我们发现,货车车轴的疲劳 强度很大程度上受车轮与车轴结合部位的应力分布状态 以及轮对压装质量的影响[|」。
因此,我们对货车轮轴压装时 配合部位受力状态与压装力曲线进行研究,分析车轮和车 轴的几何参数对压装曲线结果的影响,能够帮助我们改进 加工工艺,同时指导轮对现场生产,提高轮对质量,提高轮 对压装合格率。
包头西车辆段轮轴车间采用冷压装工艺进行轮对压 装,设备为进□ PLC 油压机和微机控制的记录系统,轮对生产过程中采取基轴制,即车轴的轮座部位采用磨削加工 获得符合规程规定尺寸和表面粗糙度,车轮使用立式镗床 加工轮毂孔,目前每月轮对压装合格率可达95%以上。
良作者简介:丁铎(1990-),男,内蒙古乌海人,助理工程师,于包头西车辆段从事轮对生产检修工作。
球头销零件冷镦坯料的优化[J /O L ].热加工工艺,2015,44(21): 117-118,121.[2」李霞.大规格异型40Cr 球头销冷挤压成形技术的研究[D 」. 武汉理工大学,2010.[3]余世浩,李霞,刘容.大规格异型球头销冷挤压成形模拟[J ]. 武汉理工大学学报,2010,32(21 ): 102-105.[4」H ong W ang.The stam ping and m old design o n stainless steel cover [C 」// Second International Conference o n M echanic A utom ation and C ontrol Engineering . IEEE , 2011:5433-5436.[5] C ao Suhong .3D m old design of outlet based on pro / engineering [C ]// Sym posium o n Electrical & Electronics Engineering (EEESYM ).IEEE ,2012:39-43.[6] Zhang Q ingping ; Cui H uanyong ; W ang Yuzeng.Process Design for Cold Precision Forging of Bevel Gear [C ]//InternationalConference o n D igital M anufacturing & A utom ation .IEEE ,2010:好的压装力曲线如图1所示,部分轮对压装后压装曲线被 判定为不合格的轮对主要是曲线末端平直(曲线末端平直线长度超过该曲线投影长度的15%)和降吨超差(曲线末 端降吨的长度超过该曲线投影长度的10%,其降吨数超过 按该轮毂孔直径计算的最大压力的5%)的现象[2]。
轮对一次压装的浅析与对策

轮对一次压装的浅析与对策发布时间:2022-09-02T01:38:38.300Z 来源:《科学与技术》2022年4月8期(下)作者:思晓花[导读] 统计近年来的一次压装合格率,经过分析轮对压装曲线,找到影响一次压装合格的关键因素,思晓花中国铁路青藏集团有限公司青海省西宁市 810006摘要:统计近年来的一次压装合格率,经过分析轮对压装曲线,找到影响一次压装合格的关键因素,制订相应措施,使得各型轮对压装合格率明显提高。
关键词:轮对;加工;压装;粗糙度;圆柱度;过盈量。
轮对一次压装是按厂修技术标准将加工选配好的车轮、车轴经同温后利用轮对压装机过盈冷压,通过压装压力曲线来判断轮对是否压装合格。
一、轮对一次压装合格率的数据统计西宁东车辆段承担着青藏集团公司客货车轮对的组装工作,具有10种轮对的厂修资质,而现场仅有一条轮对组装流水线,承担8种客车轮对、2种货车轮对组装工作,无法同时组装客、货车轮对。
经统计2017年至2020年共计压装轮对10625条,其中客车轮对压装1508条,共计压装1637次,其一次压装合格率平均为92%;货车轮对压装共计9117条,共计压装9422次,其一次压装合格率平均为为96%。
其中RDAM96轮对的一次压装合格率,最低仅为65%。
二、轮对一次压装的过程分析由以上数据可以看出,西宁东车辆段厂轮轮对一次压装合格率偏低。
进而分析2020年度压装不合格曲线,主要有降吨、超吨、平直、轮位差(盘位差)超限及中间凹下等原因。
对轮对一次压装过程进行分析如下:1.人员素质。
由于从2016年才开始从事轮对压装工作,业务技能及经验掌握有一定差距,加之10种轮对组装之间换型频繁,导致作业人员对标准易混淆。
比如2017至2020年厂轮共计压装RDAM96轮对188条,分11次完成,平均每次17条,实际生产中最多一次压32条,最少一月仅有2条,无法对轮座、轮毂孔、盘座、盘毂孔的粗糙度、圆柱度及过盈量等因素调整到最佳配合,缺乏经验值。
轮对压装的影响因素.
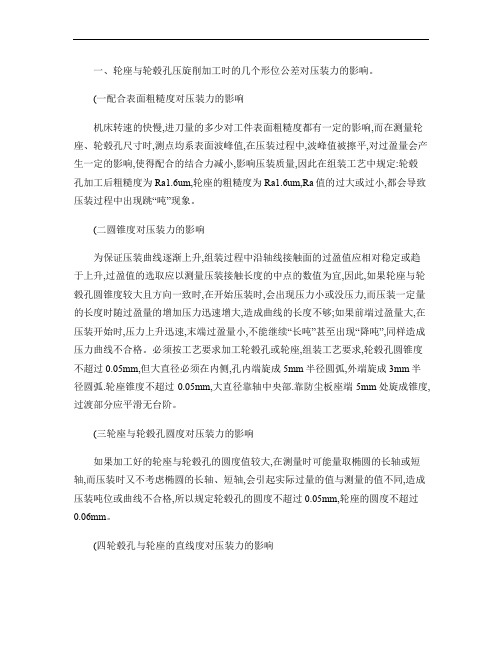
一、轮座与轮毂孔压旋削加工时的几个形位公差对压装力的影响。
(一配合表面粗糙度对压装力的影响机床转速的快慢,进刀量的多少对工件表面粗糙度都有一定的影响,而在测量轮座、轮毂孔尺寸时,测点均系表面波峰值,在压装过程中,波峰值被擦平,对过盈量会产生一定的影响,使得配合的结合力减小,影响压装质量,因此在组装工艺中规定:轮毂孔加工后粗糙度为Ra1.6um,轮座的粗糙度为Ra1.6um,Ra值的过大或过小,都会导致压装过程中出现跳“吨”现象。
(二圆锥度对压装力的影响为保证压装曲线逐渐上升,组装过程中沿轴线接触面的过盈值应相对稳定或趋于上升,过盈值的选取应以测量压装接触长度的中点的数值为宜,因此,如果轮座与轮毂孔圆锥度较大且方向一致时,在开始压装时,会出现压力小或没压力,而压装一定量的长度时随过盈量的增加压力迅速增大,造成曲线的长度不够;如果前端过盈量大,在压装开始时,压力上升迅速,末端过盈量小,不能继续“长吨”甚至出现“降吨”,同样造成压力曲线不合格。
必须按工艺要求加工轮毂孔或轮座,组装工艺要求,轮毂孔圆锥度不超过0.05mm,但大直径必须在内侧,孔内端旋成5mm半径圆弧,外端旋成3mm半径圆弧.轮座锥度不超过0.05mm,大直径靠轴中央部.靠防尘板座端5mm处旋成锥度,过渡部分应平滑无台阶。
(三轮座与轮毂孔圆度对压装力的影响如果加工好的轮座与轮毂孔的圆度值较大,在测量时可能量取椭圆的长轴或短轴,而压装时又不考虑椭圆的长轴、短轴,会引起实际过量的值与测量的值不同,造成压装吨位或曲线不合格,所以规定轮毂孔的圆度不超过0.05mm,轮座的圆度不超过0.06mm。
(四轮毂孔与轮座的直线度对压装力的影响当直线度较大时,轮座与轮毂孔的部分接触面会趋于过大或者过滤,甚至形成间隙,从而造成压力曲线的起伏较大,影响压装的质量。
HXsubDsub1C机车轮对压装工艺难点和工艺参数的确定

HX D1C机车轮对压装工艺难点和工艺参数的确定作者:曹新荣来源:《科技资讯》2012年第30期摘要:本文介绍了HXD1C大功率电力机车轮对驱动系统整体压装的工艺难点,并对压装的工艺设备、压装原理和压装参数进行详细的介绍,为实际压装提供了很好的借鉴。
关键词:HXD1C大功率电力机车压装工艺难点工装设备压装参数中图分类号:U26 文献标识码:A 文章编号:1672-3791(2012)10(c)-0085-01HXD1C大功率电力机车是南车株洲电力机车有限公司设计制造的新一代交流传动重载货运电力机车,是今后中国铁路货运运输的主力车型。
HXD1C机车车轮和车轴采用注油压装,执行中华人民共和国铁道行业标准TB/T1463-2006《电力机车轮对组装技术条件》。
1 HXD1C大功率电力机车轮对驱动系统的结构形式(如图1)2 HXD1C轮对压装工艺难点(1)HXD1C车轮在压装前已经精加工到位,不通过镟轮来保证轮对内侧距和滚动圆直径差,因此压装时需保证车轮一次到位。
(2)HXD1C机车轮对压装再抱轴箱组装、电机组装、齿轮箱组装、驱动装置空转试验后完成,总重量达五吨,原压装设备和压装工艺是轮对驱动装置悬空,这时很难保证车轴水平,再加上车轮的自重,容易造成车轴和车轮拉伤。
(3)HXD1C机车轮对压装需保证车轴两端防尘座端面到车轮内侧轮辋面尺寸C1、C2两值之差的绝对值,即轮位差不大于1 mm。
原压装设备以车轴轴端定位,压装虎口深度保证车轴轴端到车轮外侧轮毂的距离,这种工艺很难保证C1、C2的尺寸要求。
3 HXD1C轮对压装设备3.1 轮对压装设备为满足HXD1C机车轮对压装工艺要求,特采用了泰格自动化有限公司生产的TG01 01J/500型微机控制轮对压装机。
该轮对压装机由主机、测量系统、轮对支撑输送系统、液压系统、曲线记录输出系统、控制系统等构成。
主机采用立式框架结构,由主立副立柱、下横梁、主压头及副压头通过销钉连接构成稳定的平行四边形框架结构。
锥度车轴轮对压装分析

锥度车轴轮对压装分析摘要我国轨道车辆转向架造、修普遍采用轮轴冷压装工艺, 基于基轴制(或基孔制)采用过盈配合,选配车轮轮毂孔、车轴轮座直径后, 均匀涂抹润滑介质后压装,通过压装过程产生的位移--压力曲线判定配合标准。
但冷压装轮对在退卸时往往产生车轴、车轮拉伤现象,致使车轴、车轮报废。
锥度车轴车轮压装的轮对,可以很好避免该项问题的发生。
锥度车轴轮对的压装需解决的是如何在制造过程中保证压装曲线符合标准要求。
通过以往车轴加工经验,分析、实践锥度车轴的加工过程和参数指标控制方法。
建立力学模型,分析锥度车轴压装过程中车轴车轮配合直径变化对压力变化产生的影响,制定压装过程中达到符合要求的压装曲线的控制方法。
关键词转向架锥度车轴轮对压装曲线1问题的提出目前,部分轨道交通车辆在运营维护过程中为便于更换车轮及降低车轴损伤率,提出车轴轮座、车轮轮毂孔须采用锥度配合的冷压装组装。
锥度车轴轮对压装技术标准依托于《EN 13260 铁路应用-轮对与转向架-轮对-产品要求》及《UIC 813 为动车和拖车提供轮对的技术说明--公差和组装》。
基于国内普速客车以及高速动车组转向架等干线铁路客车轮对成熟、完备的轮对冷压装制造工艺技术,以及理论计算压装力及压装速度等参数,进行理论探讨。
2工艺性分析2.1锥度车轴加工与检测锥度车轴压装以轮对冷压工艺为基础,采取基轴制,先计算得出满足要求过盈量,选配确认车轮内孔直径与车轴轮座直径后,均匀涂抹润滑介质,用压力机一一对应进行压装。
检测、选配、压装时应使轮轴处于同一温度下进行,压装后压装曲线是唯一的检验依据。
锥度车轴压装的关键因素是过盈量的选取,其决定压装曲线走势。
过盈量的选取要保证提供足够的配合力,使轮对在运用中不发生相对运动,保证运行的安全。
故尺寸范围内,选取合适的过盈量进行车轴单件加工、检测,是首先需要解决的问题。
加工1:300锥度轮座无技术难点,加工前进行砂轮修型后,参照既有工艺可完成轮座精磨削加工。
轮对压装

摘要:本文主要介绍的是轮对的组装过程和轮轴联结质量及其分析等问题。
引言:车辆轮对是由两个同类型和同材质的车轮与一根车轴按规定压力和规定尺寸紧压配合组装成的一个整体。
他承受着车辆的全部载荷,并在负重的条件下沿轨道作高速运转。
因此,要求能圆滑的滚动并坚固耐用,以确保行车的安全、平稳。
对于快速客车来讲,车辆轮对还需包括两个同类型筒材质的制动盘组成,按规定的压力和尺寸紧压配合在车轴上,以提高整个车辆的制动力。
轮对的制造是指将车轴及车轮、制动盘的毛胚经机械加工后组装成轮对,并最后对整个轮对进行加工、检查等全部工作而言,轮对制造的工艺过程如下:车轴、车轮、制动盘是靠过盈时显得紧配合联接,并采用压装法。
紧配合联接不需用键和螺钉,便能传递较大的扭矩和承受轴向载荷,因而在相同的载荷下,能减小零件的尺寸,节省金属材料。
零件的紧配合联接,也可用热装或冷装法来实现。
热装和冷装系利用加热或冷却相互配合中的某一零件,使过盈量暂时消除,以便自由的完成两者的组装,待恢复至室温后,即形成过盈而达到紧配合联接。
由于热装法及冷装法难以检查轮对组装后的质量,所以目前尚未应用于轮对组装,而压装法能根据压力及自动记录器及压力表所示出的压力曲线及压入力大小来鉴定联接的可靠程度。
因此在车辆制造中轮对的紧配合联接目前均采用压装法。
轮对的组装轮对组装的技术要求:轮对的组装质量,直接关系到行车安全,因此在组装前后应严格按下列要求进行检查。
(1)车轴、车轮、制动盘组成应符合按规定程序审批的图纸及技术条件的要求车轴座及制动盘座部的表面粗糙度应达到Ra≤1.6um,而相应的轮毂孔的表面粗糙度应达到Ra≤6.3um。
为使车轮、制动盘易于压入车轴,在车轴的轮座及制动盘座靠近外侧均应旋成锥形,作为导入部分,长度分别为(12+40)mm、(10+20)mm 。
其小端直径较大端直径小1mm,轮座与制动盘座其余部分均应旋成圆柱形,在这一部分全长内的圆柱度不得超过0.05mm,大端必须靠近轴中央一端,圆度不得超过0.02mm,直线度不得超过0.015mm;轮座、盘座加工时,应向轴中央方向加旋,轮座长为186mm,盘座长为180mm。
轮对压装关键因素浅析

轮对压装关键因素浅析作者:曹振山宋宇晗李钊来源:《山东工业技术》2018年第07期摘要:轮对是转向架的重要组成部分。
通过了解轮对压装的基本工艺的基础上,并进一步分析圆柱度,过盈量,压入速度和润滑剂等关键因素对轮对压装质量的影响。
通过分析关键因素的影响,有助于提高轮对压装质量,从而为转向架安全工作提供重要保障。
关键词:转向架;轮对压装;关键因素DOI:10.16640/ki.37-1222/t.2018.07.023轮对本身的结构并不复杂,但是由于它承担的任务多且重要,因此它的加工制造以及组装要求都非常高。
尤其是轮对的组装对于转向架的运行表现起到关键性的作用,组装稍有差错容易引发列车停车,甚至脱轨等重大事故。
通过对轮对组装过程的分析,可以更好地保证轮对正常使用,保障列车行驶安全。
1 轮对压装工艺简介轮对本身结构较为简单,但是其对压装的要求却十分严格。
目前常见压装根据压装方式不同可以分为普通压装和注油压装两种方式。
其中普通压装根据压装温度不同可以分为热压装和冷压装。
热压装是将车轮内孔进行加热使其膨胀后再进行压装,其主要是针对过盈量较大的情况下使用。
热压装工艺设备一般较为复杂,一次投入成本较高,压装合格率较高,可提高车轴的使用寿命,止推试验效率低。
冷压装是直接通过压装机将车轮压到车轴上的方式,其主要是针对过盈量较小的情况下使用。
冷压装设备较为简单,一次性投入成本较低,但压装合格率一般,对操作要求较高,操作不当容易“戗轴”,对车轴寿命有一定影响,止推试验效率高。
而注油压装是在车轮上开注油孔,在压装过程中通过注入高压油,在车轮和车轴接触面之间形成一层油膜进行压装,其主要是针对车轴表面要求较高时使用。
注油压装设备较为复杂,操作难度较大,加工难度大,但压装过程允许停顿且不限时间,可以在一定范围内自由调整车轮位置。
这三种压装工艺目前都在使用,都有各个的优缺点。
这三种压装工艺的选择主要根据车轮和轮轴的结构以及压装的具体要求来决定的。
轮对压装工艺过程浅析

轮对压装工艺过程浅析作者:林路路宋宇晗来源:《中国科技博览》2019年第11期[摘要]随着城市轨道交通的蓬勃发展,城轨车辆运行的平稳性及安全性受到越来越多的人的关注。
轮对组成作为转向架的核心组成部分,其组装质量直接关系到了列车的运行安全。
轮对组成采用压装的工艺方法,利用过盈配合使车轴与车轮之间紧密连接,本文针对目前城轨转向架的轮对压装过程,总结压装过程中的关键工艺要点,为转向架轮对压装质量提升提供参考。
[关键词]城轨转向架,轮对压装,工艺要点,质量提升中图分类号:U270.331.1 文献标识码:A 文章编号:1009-914X(2019)11-0298-011、引言随着我国经济的快速稳定发展,越来越多的城市为缓解城市拥堵开始修建城市轨道交通网络。
转向架作为城轨车辆的走行部,组装质量要求更是严格。
转向架上的轮对组成直接与轨道接触,最先受到轮轨间的作用力,尤其是运行过程中的硬性冲击。
轮对压装的难度系数大,质量管控要求高,本文通过浅析目前城轨转向架轮对压装的一般过程,找出压装过程中着重注意的关键工艺要点,提高轮对压装效率。
2、轮对组成结构由于城轨车辆运行速度一般限制于80km/h~120 km/h之间,速度等级不高,车轮材质往往选择CL60钢材,车轴材质选择LZ50钢材。
车轮上与钢轨相接触的部分称为轮辋。
轮辋上与钢轨相接触的表面称为踏面,目前采用的一般为LMA型磨耗踏面。
踏面一侧凸起的部分称为轮缘,轮缘位于钢轨的内侧,可防止轮对滚动脱轨,并起导向作用。
车轮上与车轴相结合的部分称为轮毂。
轮毂与轮辋用轮辐连接。
轮辐可以是连续的圆盘,称为辐板。
为了进一步缓和轮轨间的硬性冲击,缓冲作用力,部分城轨车辆采用空心车轴进行轮对组成,以达到减少簧下质量减少冲击作用的效果,轮对组成如图1所示。
3、压装方法车轴与车轮间采用压装方法来实现彼此间的过盈配合。
过盈配合产生的过盈量可以实现半径方向产生接触面的强压力,并依靠接触面的强压力产生静摩擦力实现扭矩及轴向力的传递。
轮对压装标准关键技术研究

参考文献
[1]徐国明影响轮对压装质量的因数[J].《机车车辆工艺》.1984.02
[2]冯绍艳机车轮对组装标准对比研究[J].《机车车辆工艺》.201》.2002.02
压装前需测量车轮轮毂孔及车轴轮座的大端直径符合,并确认过盈量满足要求。在批量生产过程中,根据技术要求及实际操作经验,可将过盈量确定在要求范围的中值偏上,并将车轴及车轮加工的尺寸范围减小以达到轮轴任意配和便可满足要求。由于测量工具的精度及磨损、测量方式及准确度等原因,轮轴测量直径易出现测量误差,导致过盈量不满足实际压装需求。在实际生产中需要对测量的工具,如千分尺、千分表等测量器具进行校准并定期检定,尽量避免工具误差;人工测量车轮及车轴尺寸时可选取多截面,且每个界面在不同角度测量多组数据进行比对,减少人为测量误差。
车轮加工后压人端定大小的圆角且圆角与轮毂孔的相切点须处理圆滑过渡使车轮易于压人轮毂由于机械切削加工特性过渡位置处易产生挤压变形棱边划痕等情况压装前需将车轴轮座包含引入部分车轮轮毂孔包含引人部分进行充分处理清除上面的毛刺高点粒状或线状杂质等
轮对压装标准关键技术研究
轮对承受着轨道车辆全部载荷,需要在高负载工况下进行高速转动。车轮与车轴压装作为关键工序,保证各项压装参数,控制轮轴压装质量是轮对生产控制的重点。
HXD1C机车轮对压装工艺难点和工艺参数的确定

HXD1C机车轮对压装工艺难点和工艺参数的确定摘要:本文介绍了hxd1c大功率电力机车轮对驱动系统整体压装的工艺难点,并对压装的工艺设备、压装原理和压装参数进行详细的介绍,为实际压装提供了很好的借鉴。
关键词:hxd1c大功率电力机车压装工艺难点工装设备压装参数中图分类号:u26 文献标识码:a 文章编号:1672-3791(2012)10(c)-0085-01hxd1c大功率电力机车是南车株洲电力机车有限公司设计制造的新一代交流传动重载货运电力机车,是今后中国铁路货运运输的主力车型。
hxd1c机车车轮和车轴采用注油压装,执行中华人民共和国铁道行业标准tb/t1463-2006《电力机车轮对组装技术条件》。
1 hxd1c大功率电力机车轮对驱动系统的结构形式(如图1)2 hxd1c轮对压装工艺难点(1)hxd1c车轮在压装前已经精加工到位,不通过镟轮来保证轮对内侧距和滚动圆直径差,因此压装时需保证车轮一次到位。
(2)hxd1c机车轮对压装再抱轴箱组装、电机组装、齿轮箱组装、驱动装置空转试验后完成,总重量达五吨,原压装设备和压装工艺是轮对驱动装置悬空,这时很难保证车轴水平,再加上车轮的自重,容易造成车轴和车轮拉伤。
(3)hxd1c机车轮对压装需保证车轴两端防尘座端面到车轮内侧轮辋面尺寸c1、c2两值之差的绝对值,即轮位差不大于1 mm。
原压装设备以车轴轴端定位,压装虎口深度保证车轴轴端到车轮外侧轮毂的距离,这种工艺很难保证c1、c2的尺寸要求。
3 hxd1c轮对压装设备3.1 轮对压装设备为满足hxd1c机车轮对压装工艺要求,特采用了泰格自动化有限公司生产的tg01 01j/500型微机控制轮对压装机。
该轮对压装机由主机、测量系统、轮对支撑输送系统、液压系统、曲线记录输出系统、控制系统等构成。
主机采用立式框架结构,由主立副立柱、下横梁、主压头及副压头通过销钉连接构成稳定的平行四边形框架结构。
测量系统由侧尺及侧尺位移传感器组成,压装过程中实时检测待压装车轮位置,为压装控制提供准确数据。
轮对冷压工艺分析与研究

轮对冷压工艺分析与研究作者:金显贺,郭文孝,申博来源:《科技创新与生产力》 2015年第10期金显贺,郭文孝,申博(1. 太原重工轨道交通设备有限公司,山西太原 030006;2. 中国煤炭科工集团太原研究院有限公司,山西太原 030006;3. 山西水利职业技术学院,山西太原 030006)摘要:文中主要从轮对压装原理、压装工艺流程、轮对压装工艺参数以及轮对压装的验收指标等方面进行探讨与分析,为轮对压装质量提供参考依据,为列车的安全提供保障。
关键词:车辆轮对;轨道交通车辆;载荷;列车轨道中图分类号:U260.6 文献标志码:A DOI:10.3969/j.issn.1674-9146.2015.10.074车辆轮对的主要作用是承受着车辆的全部动、静载荷,将它传递给导轨并在重载下沿着轨道作高速旋转。
不仅如此,轨道交通车辆的驱动制动也主要是通过作用在轮对上得以实现的。
因此,轮对在机车中具有极其关键的作用,装配质量的好坏直接影响着铁路运输的安全性和舒适性。
轨道交通车辆的轮对不仅承受着列车总体的全部载荷,而且其需要在负重的条件下高速转动在列车轨道上,这就对车轴和车轮的制造工艺以及轮对的压装工序上具有很高的要求。
在高铁制造工艺中,轮对压装技术是非常重要的一环,好的压装质量和精度对列车的安全运行具有至关重要的影响。
目前,针对车轴与车轮的压装的主流压装方法为冷压装,冷压装工艺由于其操作便捷,质量可靠,成为了应用较为普遍的压装工艺[1]。
1 轮对冷压压装的原理首先将车轴水平放置,将车轮套在车轴上,在压装力的作用下,使车轮沿轴向向内运动,在车轮与车轴接触面产生弹塑性变形。
当压装力大于接触面间的摩擦力时,车轴与轮毂孔表面会发生相对运动,从而达到压装的目的。
冷压的技术参数有以下几点:表面粗糙度、轮座圆柱度、轮毂孔圆柱度、配合过盈量、压装速度、润滑介质等。
2 压装工艺流程高速动车组的轮对一方面连接在转向架上,对动车整体起到支撑作用,另一方面接触导轨,并沿着导轨做高速旋转运动,是列车中最基本并且最重要的结构,对列车的安全性具有重要影响。
出口车轮对工艺研究,实现多品种小批量轮对自动压装

出口车轮对工艺研究,实现多品种小批量轮对自动压装摘要:本文对轮对压装工序新产品试制工艺研究过程进行了阐述,着重针对出口车轮对压装生产过程遇到的问题开展工艺分析、工艺攻关,最终实现多品种小批量轮对的自动压装,保质保量完成生产任务。
关键词:工艺尺寸参数轮对压装一、出口车轮对工艺分析根据图纸及工艺标准,将典型出口车标轨轮对、米轨轮对与国铁RD2型轮对进行主要压装参数的对比(见表1),可以发现出口车标轨轮对与RD2型轮对尺寸差异不大,米轨轮对差异较大。
表1出口轮对轮对压装最终压力、曲线判断标准等与RD2型轮对差异较大,需进行轮对轴型参数调整设置(见图1),同时开展工艺试验,明确压装过盈量内控标准,保证压装压力曲线图表符合AAR RP-631中曲线要求。
另一方面米轨轮对在压装过程中,需对设备进行多方面的调整,其中最主要的就是需选用内测尺(见图2)进行压装过程中的尺寸控制。
图1 图2二、出口车轮对压装工艺重点1、优化设备工装配置轮对压装工序使用设备为TG0101轮对压装机,通过对该设备摆锤压装行程及车轮压块开档尺寸(见图3)进行测量后,明确现有工装满足车轴总长为2000mm~2200mm,轮座直径为φ175mm~φ225mm轮对的压装。
综上,根据出口车轮对车轴总长、轮座直径、轮毂厚度等各部位尺寸,明确需重新制作各型轮对专用摆锤顶块,以满足出口车轮对的压装生产。
2、完善轮对压装机参数对出口车轮对图纸各部位尺寸及轮对压装标准进行明确,而后在设备轮对轴型参数修改界面内增加轴型参数,根据项点将相应的尺寸参数进行输入,完善各型出口车轮对压装参数。
图4为米轨轮对的参数设置界面,其中需注意产品压装曲线判断标准需按要求选用AAR标准,同时米轨轮对压装使用测尺应选用内测尺。
图3 图43、规范设备性能校验轮对压装工序每班开班前需使用RD2型标准轮对进行轮对压装机的日常性能校验。
因米轨轮对与RD2型轮对使用测尺不一致,同时出口车轮对尺寸与RD2型轮对尺寸间存在一定的差异,校验后不能保证出口车轮对压装尺寸合格。
轮对压装工艺分析

轮对压装工艺分析作者:杨廷琦曹振山纪炜来源:《科学与信息化》2019年第04期摘要轮对组成承载着整个车辆的载荷,是车辆走行部的重要组成部分,直接影响到车辆运行的安全性与稳定性。
本文从轮对的压装工艺着手,分析轮对压装质量保证及质量提升。
关键词轮对组成;压装工艺;质量提升1 研究背景随着高速动车组的不断发展,列车运行速度在不断刷新。
高速度运行的动车组列车受到的振动成倍增加,导致走行部轮对受到的硬性冲击不断增强。
轮对组成作为走行部的重要零件,主要负责承载列车重量,承受轨道对轮对的冲击,利用与轨道的黏着力产生驱动力及制动力等。
轮对组成的质量决定了列车运行的安全与稳定,本文从轮对压装工艺着手,分析讨论提升轮对压装质量的关键点[1]。
2 轮对组成结构轮对组成分为动车车轮以及拖车车轮,主要区别在于是否均有驱动装置。
本文主要对轮对压装工艺进行探究,动车轮对组成与拖车轮对组成在轮对压装方面不存在差异性,本文以拖车轮对组成作为研究对象进行分析。
拖车轮对组成主要由车轴、车轮、制动盘、轴箱组成等部分构成[2]。
3 压装工艺分析3.1 压装工艺简介轮对压装工艺有三种不同的类型,分别为注油压装,冷压装,热压装。
注油压装工艺即利用车轮上预先加工的注油孔,使用高压油在车轴与车轮接触面之间形成一层油膜,使整个压装过程被油膜隔开;热压装工艺即车轮进行均匀加热处理,以热涨效应抵消车轮孔与轴径之间的过盈量;冷压装即是在同一温度下,使用压力设备将接触表面涂油润滑油的车轮与车轴进行压装作业。
3.2 轮对注油压装工艺根据轮对材质及结构的差异性,采用不同的压装工艺。
本文介绍的动车组轮对压装采用注油压装工艺操作方法,由于油膜的作用提高了压装成功率与压装质量,且注油压装会使轮对与车轴之间具有较高的紧固力,在一定程度上提高了轮对的使用寿命[3]。
轮对注油压装在轮对组装压力机上完成,组装前首先对轮对及车轴配合处清洁处理,保证接触面无灰尘、无损伤。
将轮对及车轴放置于压力机的位置,向注油口中注入高压油,注油油压约为(120~150)MPa,压装力小于900kN。
轮对压装工艺要点分析

轮对压装工艺要点分析作者:安迪徐华祥宋宇晗来源:《青年生活》2019年第18期摘要:轮对是轨道列车的重要组成部分,也是影响车辆运行安全的关键零部件,主要由一根车轴及两个车轮组成。
轮轴采用过盈配合连接,依靠过盈量传递扭矩和轴向力。
轮对采用压装工艺压装到车轴处,实现两者的过盈配合。
本文对轮对压装工艺进行论述,从压装过程中压装曲线、压装力、过盈量等多方向分析,提出压装过程中的关键工艺要点及注意要点。
关键词:轮对组成,压装工艺,关键项点1.研究背景铁路运输是我国重要的客运及货运方式,随着近些年经济的快速发展,轨道行业更是飞速发展。
轨道车辆主体由车体,转向架,制动系统,驱动系统,车辆设备等部分组成,其中转向架作为车辆的走行部结构,承担着支持车体载荷,提供驱动、制动功能以及自导向能力。
轮对作为转向架的关键部件,直接与轨道接触,为车辆安全运行提供了不可或缺的作用。
轮对与车轴压装组成,结合处过盈配合,依靠连接面产生的弹性、塑性变形,使轮对与车轴实现紧密连接。
2.轮对结构轮对组成由一条车轴与两个车轮配合组装而成。
车轴主要包括轴颈、轮座、防尘板座等组成。
轴颈承载车辆并传递载荷;轮座与车轮配合,作为结合面,通常采用锥体结构;防尘板座是轴颈与轮座的过渡部分,避免应力集中。
车轴采用碳素钢材质,热处理及机械加工处理。
为了减轻簧下质量,部分车轴采用空心车轴。
车轮由踏面、轮缘、轮辋、轮毂和辐板组成。
踏面是车轮与轨道接触的部分,现多采用LMA磨耗型踏面;轮缘是保证车辆在轨道上运行不脱离的部分;轮毂是车轮与车轴配合的部分。
车轮车轴组成如图1所示。
3.压装过程选择合适的车轴车轮进行压装,车轴与车轮结合处打磨去除毛刷,表面涂抹植物油润滑。
将车轮车轴放置恒温间8小时,实现温度的恒定。
车轮的压装采用冷压法进行,首先将车轴吊运至车轴支架处,调节车轴高度尺寸,使车轴纵向中心线水平。
然后吊运车轴套在车轴上,调节车轮状态,使车轴与车轮纵向中心线重合,进行预压装。
轮对组装加工工艺分析及论证

轮对组装加工工艺分析及论证摘要:基于对某机车轮对的加工工艺,从轮心、轮箍、整体轮对加工技术要求、工艺过程设计、装夹及定位基准的选择、加工过程的跟踪与确认、工艺参数的确定对轮对组装的加工工艺进行分析与验证。
关键字:轮心加工工艺过程设计定位基准工艺参数1绪论轮对是火车车辆行走的重要行走部件,它的安全性、可靠性非常重要,加工质量直接影响机车行车安全。
因此,对轮对的质量要求越来越高,既要保证其内在质量,又要保证形状尺寸及外观精度,本文将主要研究轮对的加工工艺,分析及论证轮对加工。
2 工艺方案确定根据轮对结构,制定工艺流程为:长短轮心加工、从动齿轮热套、轮辋加工、轮箍组装、踏面加工。
2.1 主要设备、工装工具2.1.1设备1小面及高差精车:数控加工中心2钻孔、攻丝:Z35钻床3半精车内孔:C5116H10/8F-1加工中心4精车内孔:数控立式车床5半精车外圆:数字控制车床2.1.2 工具工装1轮心加工:100~250/0.01内径百分表、225~250/0.01外径千分尺、TR200粗糙度仪2轮对组装:轮辋外径测量仪、225~250/0.01外径千分尺、160~250/0.01内径百分表、300~400/0.01外径千分尺3 踏面加工:机车车辆轮辋内距尺、机车轮箍外径测量仪3长短轮心的加工3.1加工技术要求幅板厚度公差小于4,幅板与轮辋连接处厚度公差为4,幅板与轮毂连接处厚度公差为4,幅板对内孔圆跳动小于2,轮心的圆弧表面和圆弧相切直面对基准比的斜向圆跳动公差为2.3.2工艺过程设计对工艺流程确定,对轮心来料检查-钻孔攻丝-精车内孔。
加工前对轮心各主要尺寸和幅板厚度,圆跳动进行检查。
3.3装夹及定位基准的选择将轮心油孔钻胎调至长轮心工位,用天车将轮心吊至轮心油孔钻胎上,再以轮辋外圆面及轮辋内侧端面相对轮心钻胎定位支撑面定位。
精车采用三爪吊具将轮心吊至立式车床四爪卡盘上,注意,吊装平稳,防止磕碰及轮心平面需全部放平至四爪上,以轮心外侧面辋端面及外圆为基准找圆并采用百分表测量圆跳动找正工件完成装夹。
高铁轮对压装过程中几个关键问题的分析

高铁轮对压装过程中几个关键问题的分析动车轮对除了承受一定的装配力,还要承受复杂的静载荷、动载荷以及在制动时由闸瓦的摩擦产生的热应力,随着车速的提高,这种动载荷的影响会越来越大。
为提高行车安全,对轮对的制造工艺提出了很高的要求。
本文从影响轮对压装过程的几个关键问题进行研究分析,提出了轮对压装解决方案。
标签:轮对;轮;轴;压装曲线;压装动车轮对是动车组关键重要的零部件之一,而轮对的压装质量是保证车辆在安全运行过程中重要的环节。
其中车轴和车轮是轮对压装的主要零部件。
通过对车轴、车轮加工和压装前轮轴处理过程的跟踪分析,我们找到几个影响轮对压装的关键问题,并重点分析加强控制,提出了合理的压装方案。
1 影响压装的几个关键原因轮对压装质量是通过压装曲线来判定是否合格,压装曲线的判定合格要求具体为:①在轮座压入轮毂孔长度30mm范围内,必须起吨,但起始吨位不得超过车轴轮座直径公称尺寸的1.3倍;②在车轮的注油槽部位,压装力允许下降,但在下降后的25mm内压装力恢复上升,且25mm处的压力值不小于压装曲线下降前的最大压力值;③最后25mm的位移中,压装力允许下降,但压力下降值不得超过50kN。
④最终压装力及最大压装力须介于最大最小压装力之间。
影响压装曲线的的因素:主要是过盈量、轮轴压装表面的粗糙度、润滑剂的涂抹、表面形状误差、压装速度、温湿度、材料的机械性能等因素。
我们取其中关键的几点因素进行具体分析。
1.1 过盈量压装过程中车轮和车轴配合面处的應力应变状态会发生改变,在轮对的微小结构特征处如圆角、倒角和过渡圆弧等会有应力集中的现象,它是轮对微动损伤和疲劳裂纹形成的主要源头,为了保证所需要的连接强度及防止轮对联接部分应力过高,必须正确选择过盈量。
例如复兴号标准动车组的过盈量配合最小0.238mm最大0.313mm。
1.2 轮轴压装表面的粗糙度压装面的粗糙度对压装力的影响较大。
工件表面的粗糙度与加工时的刀具速度,进给量的大小有直接关系。
试论动车组轮对压装工艺项点
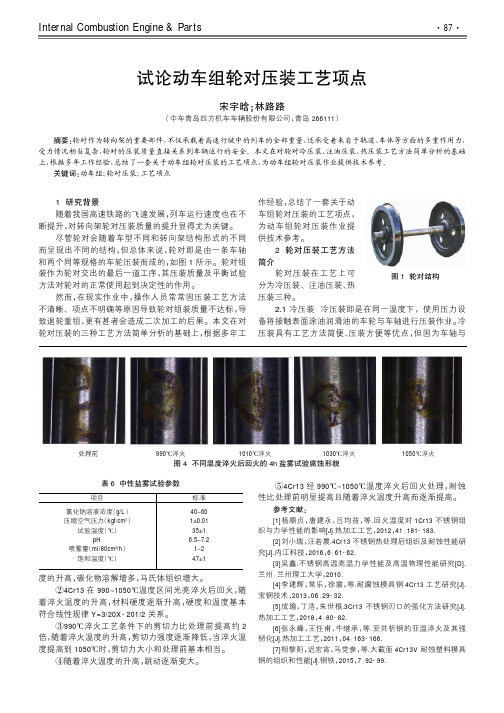
Internal Combustion Engine &Parts1研究背景随着我国高速铁路的飞速发展,列车运行速度也在不断提升,对转向架轮对压装质量的提升显得尤为关键。
尽管轮对会随着车型不同和转向架结构形式的不同而呈现出不同的结构,但总体来说,轮对即是由一条车轴和两个同等规格的车轮压装而成的,如图1所示。
轮对组装作为轮对交出的最后一道工序,其压装质量及平衡试验方法对轮对的正常使用起到决定性的作用。
然而,在现实作业中,操作人员常常因压装工艺方法不清晰、项点不明确等原因导致轮对组装质量不达标,导致退轮重组,更有甚者会造成二次加工的后果。
本文在对轮对压装的三种工艺方法简单分析的基础上,根据多年工作经验,总结了一套关于动车组轮对压装的工艺项点,为动车组轮对压装作业提供技术参考。
2轮对压装工艺方法简介轮对压装在工艺上可分为冷压装、注油压装、热压装三种。
2.1冷压装冷压装即是在同一温度下,使用压力设备将接触表面涂油润滑油的车轮与车轴进行压装作业。
冷压装具有工艺方法简便、压装方便等优点,但因为车轴与试论动车组轮对压装工艺项点宋宇晗;林路路(中车青岛四方机车车辆股份有限公司,青岛266111)摘要:轮对作为转向架的重要部件,不仅承载着高速行驶中的列车的全部重量,还承受着来自于轨道、车体等方面的多重作用力,受力情况相当复杂,轮对的压装质量直接关系到车辆运行的安全。
本文在对轮对冷压装、注油压装、热压装工艺方法简单分析的基础上,根据多年工作经验,总结了一套关于动车组轮对压装的工艺项点,为动车组轮对压装作业提供技术参考。
关键词:动车组;轮对压装;工艺项点图1轮对结构度的升高,碳化物溶解增多,马氏体组织增大。
②4Cr13在990~1050℃温度区间光亮淬火后回火,随着淬火温度的升高,材料硬度逐渐升高,硬度和温度基本符合线性规律Y=3/20X-201/2关系。
③990℃淬火工艺条件下的剪切力比处理前提高约2倍,随着淬火温度的升高,剪切力强度逐渐降低,当淬火温度提高到1050℃时,剪切力大小和处理前基本相当。
轮对关键工艺参数对非标轮对压装质量的影响分析
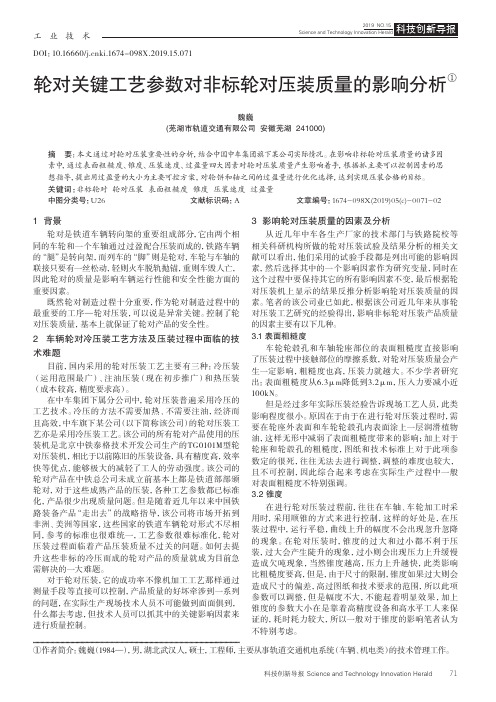
工业技术科技创新导报 Science and Technology Innovation Herald71DOI:10.16660/ki.1674-098X.2019.15.071轮对关键工艺参数对非标轮对压装质量的影响分析①魏巍(芜湖市轨道交通有限公司 安徽芜湖 241000)摘 要:本文通过对轮对压装重要性的分析,结合中国中车集团旗下某公司实际情况。
在影响非标轮对压装质量的诸多因素中,通过表面粗糙度、锥度、压装速度、过盈量四大因素对轮对压装质量产生影响着手,根据抓主要可以控制因素的思想指导,提出用过盈量的大小为主要可控方案,对轮饼和轴之间的过盈量进行优化选择,达到实现压装合格的目标。
关键词:非标轮对 轮对压装 表面粗糙度 锥度 压装速度 过盈量中图分类号:U26 文献标识码:A 文章编号:1674-098X(2019)05(c)-0071-02①作者简介:魏巍(1984—),男,湖北武汉人,硕士,工程师,主要从事轨道交通机电系统(车辆、机电类)的技术管理工作。
1 背景轮对是铁道车辆转向架的重要组成部分,它由两个相同的车轮和一个车轴通过过盈配合压装而成的,铁路车辆的“腿”是转向架,而列车的“脚”则是轮对,车轮与车轴的联接只要有一丝松动,轻则火车脱轨抛锚,重则车毁人亡,因此轮对的质量是影响车辆运行性能和安全性能方面的重要因素。
既然轮对制造过程十分重要,作为轮对制造过程中的最重要的工序—轮对压装,可以说是异常关键。
控制了轮对压装质量,基本上就保证了轮对产品的安全性。
2 车辆轮对冷压装工艺方法及压装过程中面临的技术难题目前,国内采用的轮对压装工艺主要有三种:冷压装(运用范围最广)、注油压装(现在初步推广)和热压装(成本较高,精度要求高)。
在中车集团下属分公司中,轮对压装普遍采用冷压的工艺技术。
冷压的方法不需要加热、不需要注油,经济而且高效,中车旗下某公司(以下简称该公司)的轮对压装工艺亦是采用冷压装工艺。
- 1、下载文档前请自行甄别文档内容的完整性,平台不提供额外的编辑、内容补充、找答案等附加服务。
- 2、"仅部分预览"的文档,不可在线预览部分如存在完整性等问题,可反馈申请退款(可完整预览的文档不适用该条件!)。
- 3、如文档侵犯您的权益,请联系客服反馈,我们会尽快为您处理(人工客服工作时间:9:00-18:30)。
轮对压装过程中几个关键工艺参数的分析摘要:铁路客车轮对承受着车辆的全部载荷,并在负重的条件下沿轨道作高速运转,轮对压装作为重要工序之一,其参数直接影响着行车安全。
本文分析了轮对压装的工艺过程中的几个关键参数,阐述了压装过程中易产生的问题,分析了产生这些问题的原因。
关键词:轮对;工艺;参数轮对是铁路客车最主要的零部件之一,而轮对组装的质量是保证车辆在高速运行中安全的至关重要的环节,车轴、车轮经过几道工序的加工,最后冷压组装,轮轴的加工质量好坏直接影响到轮轴压装环节的合格与否。
通过对压装环节主要质量问题的分析,我们找到了引起这些问题的原因,并在相应生产工序中采取措施,加强了工艺管理。
1. 影响轮对一次压装合格率的因素轮轴压装合格与否是用压装曲线来判别的,所以压装曲线记录仪的灵敏度也直接影响着轮对一次压装合格率。
同时,为了保证所需的联接强度及防止轮对联接部分的应力过高,必须正确选择过盈量。
但在实践中只满足过盈量的选取值,并不能取得理想的压力曲线和终止压装力,它还受到配合表面几何形状误差等因素的制约。
1.1 轮座、轮毂孔锥度对压装合格率的影响通常,在车轮轮毂孔上加工0.04的正向锥度,车轴轮座上加工0.10的正向锥度,以保证曲线形状及终止压装力合格。
在轮对压装过程中,由于轮座、轮毂孔锥度不一致,轮轴配合表面各部位的尺寸(沿径向方向)都不相等,因而沿轴向方向每一横截面的过盈量也不相等。
如果轮座与轮毂孔圆锥度较大且方向一致时,在开始压装时,会出现压力小或没压力,而压装一定量的长度时随过盈量的增加压力迅速增大,造成曲线的长度不够。
1.2 测量误差对轮对压装合格率的影响由于外径干分尺和百分表本身的不确定度(外径千分±0.006 mm,百分表±0.O25mm),再加上选配时测量部位和测量温度及湿度的影响,对过盈量的选取值形成累积误差,不能反映轮轴尺寸的真实值,直接影响过盈量选取的准确性,导致轮对一次压装合格率下降。
1.3 直线度、椭面度及表面粗糙度对压力曲线的影响由于椭圆度的存在,对同一孔和轴在同一横截面上测量直径时,由于选取的方向不同,所得的过盈量也不同。
当椭圆度偏大时,往往得到比实际上过大或过小的过盈量。
此外,加工设备、刀具等影响使得加工粗糙度有一定的偏差,压装时有效过盈量相对减少,压装力也随之下降,使终止压力低于极限值,影响轮对一次压装合格率。
2. 对策2.1 严格执行加工工艺严格执行轮轴加工工艺文件,严格控制几何形状偏差。
统一测量部位,使轮座、轮孔相对应的尺寸准确。
具体操作上时,按照规定的位置即距轮座(孔)外侧面12~20mm、95~105mm 及距轮座(孔)内侧面12~20mm 3个截面,每个截面在相互垂直方向测量两个值,取6个测量值的平均值作为轮座、轮孔直径,来计算过盈量,挑选最佳组合进行压装。
2.2 保证轮座、轮毂孔锥度,提高轮座、轮毂孔加工精度(1)轮座锥度是靠磨削来保证的,每次开工前首先实行首件试磨,检查其锥度是否符合要求。
粗磨时,砂轮作周期性横向进给,其进给量不超过0.025 mm,走刀次数6~10次(根据加工余量确定),精磨时横向进给量为0.005~0.015mm,最后做几次无横向进绐的光磨行程,直至火花消失为止。
在磨削过程中砂轮的磨粒在摩擦、挤压作用下,棱角逐渐磨圆变钝,影响工件表面的锥度及粗糙度,所以要求最多磨削2个工件后必须修整砂轮。
(2) 修整车轴中心孔。
车轴两端中心是磨削工序中重要的定位点,中心孔稍有磨损将直接影响车轴的定位精度。
所以,工件吊装前须先将车轴的两端清理干净;防止车轴中心孔与机床顶尖相碰撞,避免人为碰伤车轴而影响定位精度,同时必须保证中心孔、顶尖润滑油的清洁,严防砂粒等杂物混入中心孔。
3 轮对压装最小有效过盈量δmin的分析在轮对组装时,过盈量对于压入力的影响极大,在一般情况下,压入力与过盈量成正比关系。
所以过盈量的正确选择是取得良好的轮轴连接质量的关键。
通常,计算过盈量有以下几种方法:①现场经验计算公式;②lame公式;③扭矩 Mk 已知法计算过盈量;④弹性极限法计算过盈量法;⑤等效应力Y法;⑥应变常数Ox法我们用Lame公式对轮轴压装过盈量进行如下计算:根据材料力学有关厚壁圆筒的计算理论,在压力P 作用下的2个配合零件保证正常工作的最小有效过盈量为:δmin=pd式中:P—径向压力,MPa ;d—配合的公称直径,mm ;E1—被包容件材料的弹性模量,MPa ;E2—包容件材料的弹性模量,Mpa;,;—被包容件的刚性系数,—包容件的刚性系数,—被包容件的内径,mm;—包容件的外径,mm ;—被包容件材料的泊松比,—包容件材料的泊松比,对于钢,= 0.3;对于铸铁,= O.25.例如,对于KKD车轮和50钢车轴,查表取E=2.06×Mpa。
取d=188mm,按 TB/T1718-2003 标准,终止压装力最小值F=1.88×343KN=644.84KN,由于车轴是实体,故=0,由图纸,=274mm,则 =0.7, =2.71。
代入得δ= 0.20mm。
这与实际中的选配值相符。
虽然过盈量可以用理论计算方法获得,但由于影响轮轴压装质量的各项因素错综复杂,在计算中不容易做得准确,所以只能根据长期实践经验,确定采用的过盈量。
如对于KKD车轮组装选配时,按照 TB/T1718—2003 的规定,过盈量的选取范围为轮孔直径的0.8‰~1.5‰,即0.16~0.29 mm,根据实际生产经验,总结出过盈量以0.18~0.22 mm为宜。
4 轮对压装过程中受力与压力曲线的分析车轴在压装过程中受力情况如图l 所示。
若轮轴压装曲线的横坐标表示压装过程中车轮、车轴的相对位移,纵坐标表示压装力(又称压装吨位),则理想状态下,压装曲线应符合公式:F=πDLμP式中:F—压装力;D—轮座直径;L—接触面的长度;μ—摩擦因数;P—单位接触面积上的压力。
因此,正常情况下压装曲线应如图1所示。
在实际生产过程中,常出现不正常的压装曲线。
我们选择三类典型曲线进行分析如下:图1 正常的压装曲线位移图2 压装时压力曲线末端陡升4.1压力曲线末端陡升图2所示的压装曲线,起吨正常,中间部位受油槽影响稍有平凹走势,第15格内曲线开始陡升。
一般引起压装力突变的因素主要有:(1)轮轴加工质量。
轮轴加工质量即轮轴表面光洁度和形状公差,其变化直接影响到压装过程中的实际过盈量,使局部接触应力突变;(2)轮轴局部硬度不均匀。
由于轮轴在碾制和锻造过程中,材质不均匀,正火后形成局部硬度不均;(3)轮轴加工的表面缺陷。
车轮内孔加工由于刀具磨损, 使车轮内孔表面形成局部硬度不均、成型不好等加工缺陷;车轴在磨削过程中,由于采用分段磨削,经常出现磨削螺旋纹,所以有加工缺陷的轮、轴组装时,必然会引起压装力变化。
4.2压力曲线起点陡吨。
TB/T1718—2003规定,起点压力陡升不得超过98KN。
产生陡吨的原因有以下几种:(1)车轮轮毂孔镟削时依轮辋外侧定位,依内侧找正一加工,而轮对压装时依轮毂孔外侧面定位,2个基准面不一致。
(2) 轮座与轮毂孔中心不一致,压力机的压头前进时轮子先被压正,车轴不前进,因而产生陡吨;(3)加工方面:车轴的引导部与轮座的圆柱部分不是圆滑过渡,有棱台,这一棱台是在磨削轮座时留下的,轮对在压装时首先要压平这个棱台,因此产生陡吨。
4.3压力曲线末端降吨车轮的轮毂厚度在距轮毂内侧面约2/3的范围内由于车轮辐板的原因逐渐增加,约从距轮毂内侧面2/3处开始逐渐远离车轮辐板,轮毂的厚度在逐渐减少,压装力不再保持原有的增加趋势,曲线末端出现了平直降吨的现象。
这是由轮毂壁变薄导致过盈量比变小造成的。
有效解决该问题的方法是: 在加工轮座时使其正向锥度在国家标准允许的情况下应尽可能地大一些。
5.轮轴压装损伤分析轮对是铁路机车车辆走行部的关键部件,若轮对组装时形成严重压装损伤, 工厂很难发现, 在运用过程中又无法直接观测和不易探伤,对铁路运输安全构成巨大的潜在危险。
从实际应用情况看,冷压装的工艺存在一些弊病。
在组装时,为了满足车轮与车轴的紧固力,把紧固力调得很高,容易在组装时破坏车轴与轮座配合面的应力均匀分布,使车轴出现应力集中区和产生裂纹的胚芽等,降低了车轴的使用寿命和安全性;此外,压装时,摩擦力较大,压入时轮座表面的金属会发生纵向的滑移堆积,产生鱼鲮片和挤压包。
滑移堆积是压装的致命伤,纵向拉伤是数量最多的故障。
调查表明,轮轴压装损伤经常出现的可能原因有: 1.金属异物进入轮座和轮毂孔的压装间隙;2.轮毂孔内边缘R3不是圆弧过度,而是带棱的倒角;3.轮毂孔与车轮外形基准面不垂直(轮孔偏斜);4.轮座与轮毂孔的轴线之间有一夹角,形成偏斜压装;5.尺寸选配过盈量过大; 6.锥度不匹配;7.轮毂孔加工过程有停刀和接刀(即孔内壁可能有台阶);8.轮座和轮毂孔的椭圆长轴(或短轴)方向相互垂直;9.轮座或(和)轮孔的粗糙度过大;10.轮座或(和)轮孔涂油的油质质量不好,局部或全部的涂油油层过薄,局部或全部未涂油。
其中,5、6、7、9、10为最有可能引起压装损伤的因素。
通过对轮对压装过程中几个关键问题的分析,我们找出了影响轮对组装质量的关键因素,并提出了解决措施;为了进一步获得理想的轮轴压装曲线, 提高一次性压装合格率, 还需要进一步深入、系统、全面的研究分析——通过对轮、轴的力学性能分析、有限元应力分析、压装轮轴的宏、微观特征分析, 更深层次探讨压装过程中各种现象的机理等内容,建立轴、轮加工和轮轴压装的最优化参数,进一步提高和开发先进的轮对制造工艺,把轮轴压装质量提高到一个新的水平。
参考文献[1] 广重严.铁路机车车辆轮对[M].北京:中国铁道出版社,1981.[2] TB/T1718-2003,车辆轮对组装技术条件[S].[3] 魏延刚,宋亚听.机车轮对压装过程弹塑性模拟[J].机械设计.2004(9):46-48.[4] 刘红生.提高轮对压装质量的途径[J].机车车辆工艺,2001(2):16-18.[5] 王涛.对轮对压装曲线中几个限度的探讨[J].机车车辆工艺,2007(6):43—44.[6] BSEN13260—2003标准.。