产品检验知识
产品质量检验知识概述--

产品质量检验知识概述一、产品质量检验的意义经济全球化已经成为世界经济发展的必然趋势,这一趋势的发展,使国际竞争愈加激烈。
因此,如何对待产品质量检验并应对竞争,以及经济全球化推动质量创新是现代企业发展的焦点。
由于欧盟将茶叶产品中农药残留的检验种类由6种扩大到62种,降低茶叶中农药最大残留限量标准10-100倍,个别达到200倍,致使2001年中国对欧盟的茶叶出口减幅超过37%,2002年一季度又减31%; 日本将进口大米的检测指标由1993年的47项,增加到现在的116项,致使某地大米由20世纪80年代每年10多万吨的出口量下降为零。
江苏某集团出口德国的一批针织服装,经检验因没有达到产品合同约定的生态纺织品标准,被处以16万美元的罚款;无锡某钢绳有限公司生产的3mm以上钢丝绳,因检测达不到欧盟质量技术标准,损失300多万元。
有关资料显示,技术性贸易壁垒中由于检验检测给国际贸易造成的障碍占关税等各种壁垒总和的比重,已经由原来的20%上升到目前的80%左右。
发达国家贸易技术壁垒名目繁多,受制范围广。
发达国家不断制定各种技术法规、标准,增加交验产品的检验项目,阻挡国外产品进入其市场,范围涉及轻纺类、机电产品类、食品化工类、认证注册、标签标识、产品包装等等。
具体到食品中的农药残留量、陶瓷产品的含铅量、皮革中的PCP残留量、烟草中的有机氯含量、机电产品、玩具的安全指标、汽油中的铅含量、汽车的尾气排放标准、包装的可回收性指标、纺织品纤维及染料指标、保护臭氧层的受控物质和含有POPs杂质的化工、医药等产品。
所有这些法规和标准都对我们的出口贸易产生重大影响。
而我们企业存在的问题,一是从产品的设计、生产及其销售过程片面追求某种利益,而对产品的检验以及生产条件不合格引发的质量问题,一直未能引起足够重视。
二是缺乏与国际接轨的产品标准,生产技术和质量管理水平限制,难以达到发达国家的相应要求。
三是缺乏先进的检测技术和设备,缺乏完整的产品质量检测体系。
产品检验基础知识(检验员培训资料含试题及标准答案)
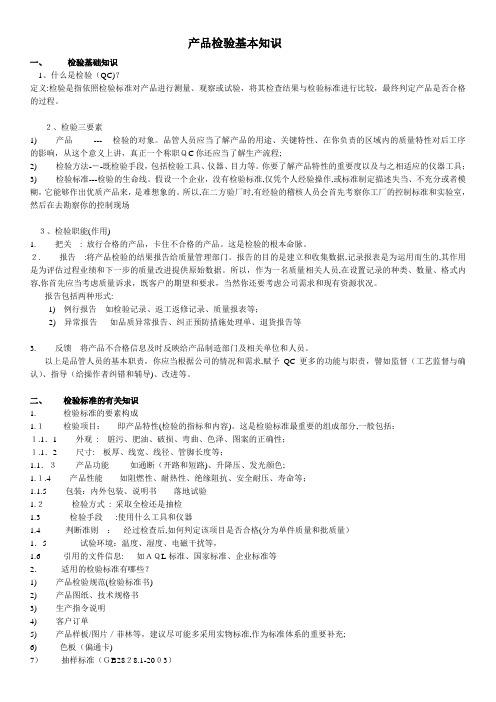
产品检验基本知识一、检验基础知识1、什么是检验(QC)?定义:检验是指依照检验标准对产品进行测量、观察或试验,将其检查结果与检验标准进行比较,最终判定产品是否合格的过程。
2、检验三要素1) 产品--- 检验的对象。
品管人员应当了解产品的用途、关键特性、在你负责的区域内的质量特性对后工序的影响,从这个意义上讲,真正一个称职QC你还应当了解生产流程;2) 检验方法---既检验手段,包括检验工具、仪器、目力等。
你要了解产品特性的重要度以及与之相适应的仪器工具;3) 检验标准---检验的生命线。
假设一个企业,没有检验标准,仅凭个人经验操作,或标准制定描述失当、不充分或者模糊,它能够作出优质产品来,是难想象的。
所以,在二方验厂时,有经验的稽核人员会首先考察你工厂的控制标准和实验室,然后在去勘察你的控制现场3、检验职能(作用)1. 把关: 放行合格的产品,卡住不合格的产品。
这是检验的根本命脉。
2. 报告:将产品检验的结果报告给质量管理部门。
报告的目的是建立和收集数据,记录报表是为运用而生的,其作用是为评估过程业绩和下一步的质量改进提供原始数据。
所以,作为一名质量相关人员,在设置记录的种类、数量、格式内容,你首先应当考虑质量诉求,既客户的期望和要求,当然你还要考虑公司需求和现有资源状况。
报告包括两种形式:1)例行报告如检验记录、返工返修记录、质量报表等;2)异常报告如品质异常报告、纠正预防措施处理单、退货报告等3. 反馈将产品不合格信息及时反映给产品制造部门及相关单位和人员。
以上是品管人员的基本职责,你应当根据公司的情况和需求,赋予QC更多的功能与职责,譬如监督(工艺监督与确认)、指导(给操作者纠错和辅导)、改进等。
二、检验标准的有关知识1. 检验标准的要素构成1.1检验项目:即产品特性(检验的指标和内容)。
这是检验标准最重要的组成部分,一般包括:1.1.1 外观:脏污、肥油、破损、弯曲、色泽、图案的正确性;1.1.2 尺寸: 板厚、线宽、线径、管脚长度等;1.1.3产品功能如通断(开路和短路)、升降压、发光颜色;1.1.4 产品性能如阻燃性、耐热性、绝缘阻抗、安全耐压、寿命等;1.1.5 包装:内外包装、说明书落地试验1.2检验方式: 采取全检还是抽检1.3 检验手段:使用什么工具和仪器1.4 判断准则:经过检查后,如何判定该项目是否合格(分为单件质量和批质量)1.5试验环境:温度、湿度、电磁干扰等,1.6 引用的文件信息:如AQL标准、国家标准、企业标准等2.适用的检验标准有哪些?1) 产品检验规范(检验标准书)2) 产品图纸、技术规格书3) 生产指令说明4) 客户订单5) 产品样板/图片/菲林等,建议尽可能多采用实物标准,作为标准体系的重要补充;6) 色板(偏通卡)7)抽样标准(GB2828.1-2003)三、产品检验的分类1.按产品形成的阶段分类:来料检验包括采购物料和委外加工产品的检验。
有关产品质量检验报告的知识4400字
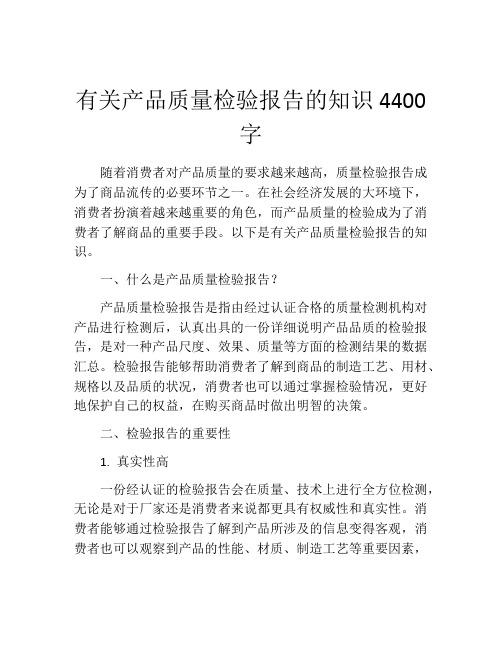
有关产品质量检验报告的知识4400字随着消费者对产品质量的要求越来越高,质量检验报告成为了商品流传的必要环节之一。
在社会经济发展的大环境下,消费者扮演着越来越重要的角色,而产品质量的检验成为了消费者了解商品的重要手段。
以下是有关产品质量检验报告的知识。
一、什么是产品质量检验报告?产品质量检验报告是指由经过认证合格的质量检测机构对产品进行检测后,认真出具的一份详细说明产品品质的检验报告,是对一种产品尺度、效果、质量等方面的检测结果的数据汇总。
检验报告能够帮助消费者了解到商品的制造工艺、用材、规格以及品质的状况,消费者也可以通过掌握检验情况,更好地保护自己的权益,在购买商品时做出明智的决策。
二、检验报告的重要性1. 真实性高一份经认证的检验报告会在质量、技术上进行全方位检测,无论是对于厂家还是消费者来说都更具有权威性和真实性。
消费者能够通过检验报告了解到产品所涉及的信息变得客观,消费者也可以观察到产品的性能、材质、制造工艺等重要因素,从而使得消费者的势力更加的有效,有利于消费者做出正确的购买决策。
2. 维护消费者权益在消费者购买商品时,产品的质量是消费者最为关心的问题之一,而一份能够证明产品质量的检验报告,可以为消费者购买时的权益保驾护航,减少消费者因产品质量问题所产生的经济损失,这样的检验报告更能够维护消费者的合法权益。
3. 促进产品质量提升对于厂家来说,检验报告也是对产品质量的一种监管,通过检验报告能够了解所生产的产品在哪些方面出现不足,并通过改进工艺和材料的方式提高产品的质量,以达到更好的销售效果。
随着消费者对产品质量的潜意识要求越来越高,用检验报告促进产品质量提升已成为厂家必备的手段。
三、常见的产品质量检验报告1. CCC认证CCC认证就是中国强制性产品认证制度,是我国的法定认证制度,适用于电器、电线、电缆等高风险的消费品的认证,遵循的是我国的国际质量标准,这份检验报告能够证明产品的合格性,并可以进入中国市场销售。
抽样方案产品检验知识
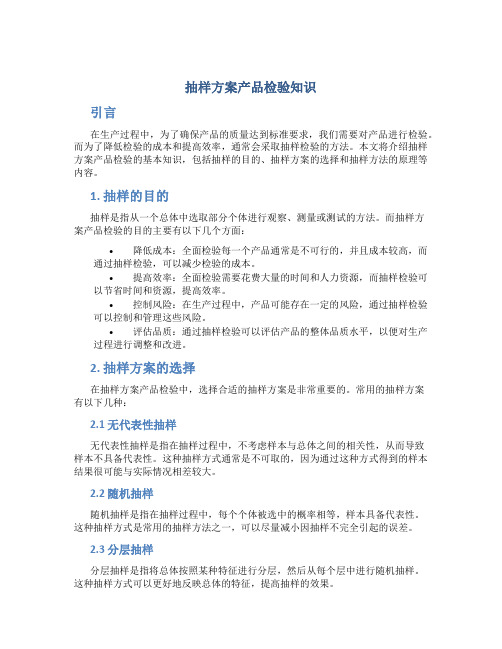
抽样方案产品检验知识引言在生产过程中,为了确保产品的质量达到标准要求,我们需要对产品进行检验。
而为了降低检验的成本和提高效率,通常会采取抽样检验的方法。
本文将介绍抽样方案产品检验的基本知识,包括抽样的目的、抽样方案的选择和抽样方法的原理等内容。
1. 抽样的目的抽样是指从一个总体中选取部分个体进行观察、测量或测试的方法。
而抽样方案产品检验的目的主要有以下几个方面:•降低成本:全面检验每一个产品通常是不可行的,并且成本较高,而通过抽样检验,可以减少检验的成本。
•提高效率:全面检验需要花费大量的时间和人力资源,而抽样检验可以节省时间和资源,提高效率。
•控制风险:在生产过程中,产品可能存在一定的风险,通过抽样检验可以控制和管理这些风险。
•评估品质:通过抽样检验可以评估产品的整体品质水平,以便对生产过程进行调整和改进。
2. 抽样方案的选择在抽样方案产品检验中,选择合适的抽样方案是非常重要的。
常用的抽样方案有以下几种:2.1 无代表性抽样无代表性抽样是指在抽样过程中,不考虑样本与总体之间的相关性,从而导致样本不具备代表性。
这种抽样方式通常是不可取的,因为通过这种方式得到的样本结果很可能与实际情况相差较大。
2.2 随机抽样随机抽样是指在抽样过程中,每个个体被选中的概率相等,样本具备代表性。
这种抽样方式是常用的抽样方法之一,可以尽量减小因抽样不完全引起的误差。
2.3 分层抽样分层抽样是指将总体按照某种特征进行分层,然后从每个层中进行随机抽样。
这种抽样方式可以更好地反映总体的特征,提高抽样的效果。
2.4 系统抽样系统抽样是指按照某种规则从总体中选择样本,通常是按照等间隔的方式进行抽样。
这种抽样方式在保证样本具备代表性的同时,还可以减少抽样过程中的随机误差。
3. 抽样方法的原理在抽样方案产品检验中,不同的抽样方法有不同的原理。
下面介绍几种常用的抽样方法及其原理:3.1 单次抽样单次抽样是指从总体中抽取一次样本进行检验,然后根据样本的结果判断总体的质量状况。
产品检验抽样方案基础知识

产品检验抽样方案基础知识引言在产品制造和供应过程中,产品检验是保证产品质量的重要环节。
而产品检验抽样方案是指在大批产品中抽取一部分样品进行检验,以代表整个批次产品质量的一种方法。
本文将介绍产品检验抽样方案的基础知识。
什么是产品检验抽样方案产品检验抽样方案是通过对大批产品进行抽样检验,以推断整个批次产品质量的一种方法。
它在产品制造和供应过程中起到了重要的作用,能够减少检验成本和提高检验效率。
产品检验抽样方案的目的和优势产品检验抽样方案的主要目的是通过对抽样样本的检验,来推断整个产品批次的质量状况,从而减少对整个批次产品的检验。
这种抽样方式具有以下几个优势:1.节省时间和成本:相比于对整个批次产品进行检验,抽样检验可以大大缩短检验时间,减少人力和资源投入,从而降低检验成本。
2.减少破坏性检验:某些产品的检验需要破坏性测试,这将导致一部分产品被破坏。
而采用抽样检验可以通过对样本进行测试,使得产品的破坏性检验数量大大减少。
3.提高检验效率:通过合理设计抽样方案,可以有效地降低检验的误判率和满意度,并提高检验效率。
产品检验抽样方案的常见方法在产品质量管理中,有多种常见的产品检验抽样方案。
下面介绍几种常见的方法:1. 简单随机抽样简单随机抽样是最简单也是最常见的抽样方法之一。
这种方法的特点是每个样本被选择的概率相等且相互独立,能够有效地反映整个样本总体的特征。
2. 系统抽样系统抽样是按照一定的规则选择样本的抽样方法。
例如,每隔一定的间隔选择一个样本进行检验。
这种抽样方法适用于样本的分布存在某种规律的情况。
3. 分层抽样分层抽样是将总体分为多个层次,在每个层次中进行抽样。
这种方法可以更好地保证各个层次的样本在抽样中被充分考虑到,提高了总体抽样的效果。
4. 整群抽样整群抽样是将总体分为若干个群体,每个群体中的样本都要进行检验。
这种方法适用于总体中群体差异较大的情况,可以更加全面地了解群体的特征。
产品检验抽样方案的设计原则在设计产品检验抽样方案时,应遵循以下几个原则:1.抽样方法的选择要合理:根据产品特性、检验目的和样本总体分布等因素,选择合适的抽样方法。
产品检验知识

产品检验知识一.产品的概念1.1.产品——活动或过程的结果;产品包括服务,也可以是有形的,也可以是无形的,或它们的组合;ISO9001标准中产品仅指期望提供给顾客所要求的产品,而不是影响环境的非期望的副产品; 2.产品有四类:硬件,软件,流程性材料,服务;3.硬件是有形产品并具有计数的特性4.软件由信息组成,通常是无形产品并可用方法、记录、或程序的形式存在如设计软件、程序、字典、手册、文件5.流程性材料是在形产品并具有连续的特性;流程性材料和硬件称为货物;6.服务:是在供方和顾客接触面上需要完成的至少一项活动的结果,并且通常是无形的;7.非预期性产品:指生产过程中的附产物;在生产过程中伴随的废料、废气、废液等物,有可能造成环境污染,不属于质量管理的范畴,属于环境管理的范畴;8.产品的标识:名称标识和标识状态9.产品并非一定是成品装配并包装完成的产品,它也可指半成品、完成品中间过程的产物,一般指装配完成产品;二.品质的概念1.品质:反映产品或服务满足明确或隐含需要能力的特征和特征的总和;ISO9001:942.品质:一组固有特性满足要求的程度; ISO9001:20003.“固有的”其相反是“外来的”就是指在某事或某物中本来就有的,尤其是那种永久的特性4.品质=特性+交期+成本+服务5.质量特性:产品满足人们某种所具备的属性和特性;综合归纳为:性能、寿命、可靠性、安全性、经济性和外观质量六大质量特性;6.质量特性分为真正质量特性和代用质量特性;真正质量特性:用户所要求的使用特性;代用质量特性:真正质量特性在转化为在生产中衡量产品质量的标准或规格;7.性能:根本产品使用目的所提出的各项功能要求,包括正常性能、特性性能、效率等;8.寿命:产品能够正常使用的期限,包括使用寿命和储存寿命两种;使用寿命:在规定条件满足规定功能的工作总时间;储存寿命:在规定条件、功能不失效的储存总时间;9.可靠性:产品在规定时间、条件下完成规定功能的能力;10.安全性:产品在流通和使用过程中保证安全的程度;11.影响质量问题的制造和检测条件——6个因素:“5M1E”人员Man、机器Machine、材料Material、方法Method、测试Measurement环境Environment12.相同的制造检测条件下,仍有许多变异;这些变异形成之原因分为两类:机遇原因、非机遇原因:A.机遇原因;又叫不可避免原因、非人为原因、共同原因、偶然原因、一般原因:同一量测器在十分钟内测同一个人的身高,不一定每次相同;同人同机按生产标准作业,但产品在容差内变化;气候及环境变化造成的品质变异;大量微小原因,不易除去;特点是:影响微小、始终存在、方向不定、难以控制;呈典型分布B.非机遇原因;又叫可避免原因、人为原因、特殊原因、异常原因、局部原因:4M不同造成的品质异常,本可避免;未按作业标准操作;作业标准还完善而造成;量具不同而造成;可避免且必须除去特点是:影响很大、时有时无、方向一定、可以控制;呈非典型分布,表现为分布中心和标准偏差的变化;三.检验的基本概念1.定义:对实体的一个或多个特性进行的诸如测量、检查、试验或度量,并将结果与规定要求进行比较以确定每项特性合格情况所进行的活动;GB84022.定义:通过观察或判断,适当地结合测量、试验所进行的符合性评价;GB19000:20003.说明:检验判定“合格”、“不合格”是符合性判定;而不合格处理是适用性判定,不是检验的职能;4.判定合格只是对品质标准而言,并不意味着质量水平的高低;四.检验的过程1.图示测量检查合格试验不合格2.根据图示可归纳为检验的三大要素:A.检验合格判定标准品质标准 B.检验方法和规范 C.检验记录3.检验合格判定标准是单个产品之检验判定的依据,是产品质量内涵的体现,内容包括:检验的质量特性项目的描述;各种质量特性的标准值和允差范围;各种质量特性缺陷的重要性严重性规定;4.检验方法和规范:规定如何进行检验检验方法目测、量测、试验等;抽样方案计数或计量,样组大小,AQL,取样方法检查手段的精度、功能要求如工具、仪器、量具等;检验环境、设施要求如温湿度、噪音、照明光线等;检验人员的技能、资格要求;检验的步骤和具体操作方法;5.检验记录,内容包括检验对象的记录,其产品名称、规格、批量、编号等;检验环境、设备的记录;检验员、审核员记录:日期、时间记录;检验结果数据,如长度、温度、电阻、缺陷数等;判定结论的记录;五.检验的分类1.按检验数分:全检、抽检、免检;2.按工序流程分:IQC、IPQC可再分:首检、巡检、转序检验、FQC、OQC、驻厂QC;3.按检验人责任分:专检、自检、互检;4.按检验场所分:工序专检和线上巡检,外发检验、库存检验、客处检验;5.按检验性质分:破坏检验、非破坏检验6.按检验内容分:试制品检验、性能检验、可靠性检验、苛刻检验、分解检验7.按检验数据类别分:计数检验、计量检验六.全检适用范围1.批量太小,失去抽检意义时;2.检验手续简单,不致于浪费大量人力、经费时;3.不允许不良品存在,该不良品对制品有致命影响时;4.工程能力不足,其不良率超过规定、无法保证品质时;5.为了解该批制品实际品质状况时;七.抽检的适用范围1.产量大、批量大,且是连续生产无法作全检时;2.破坏性测试;3.允许有某种程序的不良品存在时;4.欲减少时间和经费时;5.刺激生产者要注意品质时;6.满足消费者要求时;八.免检适用范围1.生产过程相对稳定,对后续生产无影响;2.国家批准的免检产品及产品质量认证产品的无试验买入时;3.长期检验证明质量优良,使用信誉高的产品的交收中,双方认可生产方的检验结果,不再进行进料检验;☆免检并非放弃检验,应加强生产方过程质量的监督,一有异常,拿出有效措施;九.紧急放行当原材料、半成品来不及检验时,可以紧急放行,但要作明确标识;一般情况下,须要留一少部分作即时检验;若发现不良时,立即召回;成品不能紧急放行;召回后质量特性不可复原时,不能紧急放行;十.质量成本1.定义:为确保和保证满意的质量而发生的费用以及没有达到满意的质量所造成的损失;◎质量成本分为和间接两种;某些损失可级难以定量,但很重要,如丧失信誉;2.产品价值=利润+质量成本+生产成本+设计成本3.直接质量成本项目:分为4个二级子目和20个三级细目A;预防成本:质量工作费、质量培训费、质量奖励费、产品评审费、质量改进费、工资及福利基金B.固定成本检验成本:检测费、办公室费、检测设备折旧费、工资及福利基金C.内部损失故障成本:废品损失、返修损失、停工损失、产品降级损失、事故分析处理费D.外部故障成本:保修费用、退货损失、诉讼费、索赔费用、产品降价损失4.间接质量成本:顾客遭遇故障之品质成本、顾客不满意之品质成本、信誉损失之品质成本十一..产品检验的基本事项1 单个产品的划分A.自然划分:一个钉,一台机器B.非自然划分:布匹、油漆、钢材2 三类不合格Nonconformity,ISO9001:2000以“不合格”取代94版的“缺陷”DefectA类不合格严重不合格,Cr, CriticalB类不合格主要不合格,Major, MA, MajC类不合格次要不合格,Minor, MI, Min3.四类不合格分级贝尔系统A级——非常严重缺陷值1001.必然会造成部件在使用中运转失灵,并在现场难以纠正,如继电器的断开;2.必然会造成间歇的运转故障,在现场难以确定其位置,如连接不紧;3.会使部件完全不合用,如拔号指盘在运转后不回复到正常状态;4.在正常使用情况下,易于造成人员伤害或财产损失,如露出部分有锐利边缘;B 级–严重缺陷值501.可能会造成部件在使用中运转失灵,并在现场难以纠正,如同轴插塞的保护系统涂层缺损;2.必然会造成部件在使用中运转失灵,但在现场易于纠正,如继电器接触不良;3.必然会造成那种尚未严重到运转失灵程度的麻烦,象次于标准运转之类麻烦,如保安器件不能在特定电压之下运转;4.必然会导致增加保养次数或减短寿命,如单接点圆盘缺漏;5.造成大大增加顾客安装上的困难,如安装孔错位’;6.极严重的外形或涂层上缺陷,如涂层颜色与其它部件不能匹配;需要重涂;C级–中等严重缺陷值101.可能会造成部件在使有中运转失灵,如接触低于最低限度;2.可能造成那种尚未严重到运转失灵程度的故障,象次于标准运行之类故障,如振铃不在特定范围内运转;3.可能导致增加保养次数或减短寿命,如接触肮脏;4.造成顾问安装上的小困难,如安装托座歪曲;5.较大的外形、涂层或工艺缺陷,如涂层有明显的划痕,标志漏缺或模糊;D级–不严重缺陷值11.不影响部件在使用时的运转、保养或寿命包括对工艺要求上的小偏差,如套管太短;2.外形、涂层或工艺上小毛病,如涂层轻微划痕;这是由贝尔实验室首先提出;对质量特性进行分级控制具有的作用:1.能够重点保障重要特性的满足,能节省检验成本;当年贝尔公司把一道重要工序检验项目分四级后,检验时间从120分钟减为50分钟;2.可将多个质量特性综合量化进行评价;以上列出的缺陷值是一个加权值;通过这个加权值可以把不同缺陷累加综合在一起,量化地反映出产品质量水平;4.单位产品的度量方法:A.计数法,又分为计件法:以产品的个数计算的方法;如不合格品数,或一等品、二等品数;计点法:衡量缺陷数的方法B.计量法:物理量表示5 质量管理活动的基础:一切以数据说话;6 数据分为数字数据和非数字数据又叫情理型数据a)数字数据分为计数值数据和计量值数据b)计数值数据:只能是一个非连续性的特定数值,不能取这些数值之间的值,只可点出整数,如人数、件数,缺点数等;计数值数据分为计件数据和计点数据;计量值数据:能取给定范围内的任何一个可能的值,可连续收集;如长度、重量、时间、温度等;C.非数字数据:语言、文字、图形所表示的数据;如信息、意见、反应、议题、图形等;十二.抽样检验的相关定义1 批在一定条件下生产出来的一定数量的单位产品所构成的团体,批的单位:卷、箱、包、个、张、板、公斤2 检验批为实施检验而汇集起来的单位,便于抽样进行,便于抽样结果更具代表性3 批量N4 样本及样本大小n5 样品6 对于规格精度不高如±1~2mm、破坏性检验等的项目,一般采用抽检1~5个的特殊方法,可对应MIL—STD—105E的S-I抽样;7 合格判定数AC,不合格判定数RE8 抽样检验:从检验批中,依批量大小抽出一定数量样本进行检验的方法;9 抽样标准:抽样方案所依附的具有一定规则的表单,如MIL-STD-105E,GB2828-87;10 抽样方法抽样技术:从检验批中抽取样品的方法;11 抽样方案计划:样本大小或样本大小系列和判定数组的组合n /AC,RE;12 判定数组:合格判定数与不合格判定数结合在一起;13 检查水平IL:检验批与样本大小之间的等级对应关系;14 合格品质水平AQL :消费者满意的送检批的最高大不良率;15消费者冒险率β第Ⅱ型误差,品质差,但样品品质合格却判整批合格的机率较 小,一般β=10%;16 生产者冒险率α第Ⅰ型误差,品质好,但样品品质不合格却判整批不合格的机率较少,一般α=5%;17 拒收品质水准LTPDRQL :消费者认为品质恶劣的送检批所含有的最低不良率;18 严重不良品:含有一个或一个以上严重不合格的产品;主要不良品:含有一个或一个以上主要不合格,但严重其它不合格的产品; 次要不良品:含有一个或一个以上次要不合格,但没有其它不合格的产品;19 不良率p 百件不合格品数22. 抽检特性曲线-OC 曲线一个抽检方案对产品质量高低的辨别能力转为该方案的抽检特性;110020304050607080901002345678910P a=1-aaB允收機率P aAQ L L T PD送驗批百分不良率(100)p一个抽样方案已对应着一条OC 曲线,严格说来是一个N 、n 、c 它定量表示了产品质量状况P 和被接收可能性大小之内的关系,表示接收概率LP 当批不合格率P 的函数关系; 1. 当n,c 一定时批量大小对OC 曲线影响不大; 2. 当c 一定时,n 越大,oc 曲线越陡;3. 当一批中P,不合格固定时,n 越大,抽样方案越严;十三.抽样检验类型1按品质数据类分:计量值抽检,计数值抽检一计数值抽样检验规则型单次 , 选别型单次 ,调整型单次 , 连续抽样型 ,逐次抽样型双次双次双次二计量值抽样检验规则型单次 GB8053-87调整型单次 GB6387-86 ISO3951-812按检验方式和水平分:调整型抽检,非调整型抽检调整型抽检:加严抽检,正常抽检,放宽抽检特宽抽样非调整型抽检:标准型抽检,挑选型抽检,连续型抽检,逐批抽检标准型抽检:此抽样计划的精神在兼顾买卖双方之利益各损失,即规定双方的冒险率α及β为一定之数字一般α取=, β=要查表挑选型抽检:被判为不合格批,须进行全数剔选,将不良品剔除,并以良品补足之而予以允收;这种抽验方式在长期连续几批抽验后,允收批的品质将比原作业平均为佳,可保证验收批的平均品质;仅适用于非破坏性检验;连续型抽检:适用于连续生产之产品,在制程上抽验,起始时连续抽验一定数目之样品,均为良品时则改为每一定个数间抽一样品检验,若为不良品,即回到起始时方式重新检验;逐批抽检:本计划是在每一送验批中每次抽出一个样品检验,累计其良品和不良品数,然后依公式计算或查表决定允收或拒收;此抽样计划是唯一不能事先预知抽样数的,须待抽验后判定合格或不合格后才知其样本数为若干,一般讲,此种抽样法其样本数较少;3按抽样次数分:一次抽检,两次抽检,多次抽检;4按控制重点分:AQL型,RQLLTPD型,AOQL型AOQL:平均出厂品质界限5正常检验二次抽样32,32/2,66加严检验单次抽样一般在判定数组上加严,AQL不变7减量检验单次抽样在抽样的样本大小上减量,AQL不变. 如正常检验单次抽样样本N=5000,IL=GⅡ,n=L=200,AQL=时之判定数组为5,6,而减量检验单次抽样的n=L=80, 判定数组为2,5.不合格数为2时AC;3、4时AC,但下批转正常抽检;5时RE;十四.抽样技术取样方法1.单纯随机抽样:完全随机,无限制;一般多利用乱数表或抽样球2.系统抽样:按一定的时间/数量间隔抽样3.分层抽样:先层别后再抽样4.曲折抽样:是希望减少系统抽样因周期性而发生偏差等缺点所采用的方法;可视为随机抽样,但较复杂,具有规则性;5.区域抽样:群体如一大箱物品,箱中有数十个小盒,每一小盒装有若干物品;为抽样之方便,可自数十个小盒中随机抽取若干样本盒,然后就各样本盒进行全数检验;这方法如社会调查时分为城镇或乡村取样,故称为区域抽样;适用前提:区域内变异大,区域间变异小;与分层抽样刚相反;6.分段抽样:先采用区域抽样,在从样本单位中从随机抽样;可有两段、多段之分;7.反复抽样:在同一检验批内作一次以上的抽样来推定群体品质的抽样方法;一般用在抽样检验中之双次、多次或逐次抽样十五.不合格品之短期对策:1.标识、摆放要区别要考虑正采购、在制、库存、成品、呆滞品、已出货、待生产品2.抽样发现的不良品,在厂发现要取出,或以良品补足数量;在客处检验发现一般要取出,或以良品补足数量3.不合格批之审核一般以MRB形式:物料重审会议后:返工返修、全拣挑选、特采、允收放行、降级、拒收十六.抽样标准1.抽样标准经中国批准的有20多种,在工业企业中只有GB2828和GB2829为常用标准;当然,这两个标准以外,国际上许多类似标准几乎是通用等效的;:计数值调整型抽样类型,共细分为十二种;GB2829-87:计数值逐次型抽样类型用得少计数值调整型抽样类型:1989 MIL-STD-105E,1963MIL-STD-105D,1974ISO28591993ANSI/,1963BS9001=0抽样计划1965年,C=0抽样计划首次发表1981年,C=0抽样计划第二版1983年第三版,欧美许多企业都采用C=0抽检计划MIL-STD-105E说明,规定AQL数值,并不意味供货方有权提供任何已知的不合格产品单元;当C=0时,才为合格;当C>0时,判为暂扣批Withhold the lot,需工程/管理部门作MRB决定;4.流水线抽样计划:GB8052MIL-STD-1235BA. 名义上是计数连续抽检,实际上计件检验,对应的是连续抽样方案CSP.检验时不良品数B.过程平均不良率= __________________ ,定义为:生产方对规定期间内检查时产品总数的产品进初次检查时的平均不良率中的逐批抽检中之“过程平均不良率”定义为:一系列初次提高检验批中的不合格率,既可指不良品率,也可指百件缺点数;D. 初次检验:产品加工后的第一次初次提交检验,是相对返工返修或挑选后再检验而言;与 GB2828中的AQL含义有一定差别不概述F.过程不合格品率,指产品整个生产过程中不合格品数与生产数之比;平均检出质量平均检出不合格品率AQL:检验抽检或全检出的不合格品以合格品替代,经过这样处理的产品的平均质量,不合格品百分数P.5.跳批抽检方案:GB/T3263-91当检验满足一定条件后,后执行跳批检验,若f=1/3则3批跳检1批,即有两批不检,当检查有问题,则恢复逐批检查同MIL-STD-105E CNS是中华民国标准的代号,JISZ9003,JISZ9004,JISZ9009,JISZ9010 日本标准型抽检计划JISZ9006 日本选别型抽检计划JISZ9008 日本连续生产型抽检计划MIL-STD-414 Array十七.抽样方案1.样本大小代字表2.AQL表3.抽样方案N / AC,RE4.样本大小的可变性及复合抽检方案4.1样本大小的可变性4.2成品检验, 当L=200时,AQL/MA=,5,6;AQL/MI=,10,11错误!个别判别定:MA<=5,且MI<=10时,AC最常用如MA=6,MI=0, REMA=5,MI=10,ACMA=0,MI=11, RE请问:5个MA还不如1个MI有判别力吗错误!MA+MI<=10,且MA<=5时,AC错误!综合判定:AQL/MA+ AQL/MI=,同AQL序列,,,,,中最接近的是,查得判定数组为14,15,所以MA+MI<=14时,AC也有3MI=1MA的转换方法错误!双重判定: MA<=5, MI<=10,且MA+MI<=14时,AC5.AQL的特点:5.1代表消费者满意的送检批的最高大不良率5.2当批量水平等于或优于AQL时,高概率合格质量好更安全当批量水平较大形势劣于AQL时,高概率不合格质量差更危险5.3 AQL值的单位是%百分比5.4 AQL可用百件缺点数或百件不良率表示,但AQL>10时,一般用百件缺数表示;当AQL<=10,且n<=80时,一般用不良率表示;5.5每相邻AQL值以5√10 倍数取值5.6 AQL定值原则A.军用产品 < 工业产品 < 民用品B.A缺点 < B缺点 < C缺点C.原材料 < 成品D.由设计需要的元器件的失效率而确定AQL值E.买才要考虑供方能力的设定F.检验项目多少定AQL值G.损益平衡点% AQL%—11——3 13—44—6 46——17 10H.归纳分类法:非常实用可行,较复杂这是一个非常实用与可行的AQL设定法;这种方法不但考虑成本,也考虑到不良缺点之等级与其它要素,又容易设定;(A)如下图,把AQL有关之要素列于上列,通常这些要素包括:a.检验成本与修理成本之比b.可能发现不良地区c.不良品处理方式d.制程方式e.鉴定不良之难易等等;B将AQL从最严到最宽例如由%到15%,由上而下列于下图右方;C将各要素所产生之状况分为三类即a.把全公司的检验成本与修理成本之比例,分为以下,至1,与超过1以上三种;b.不良品可能被发现处,也分为:顾客使用时,制程最终检查与制程中间检查三种;c.不良品处理方式:分为报废处理、可整修或可特别降低规格使用三种;d.本身工厂之制程是属于全自动、半自动或人工三种;e.不良是否容易鉴定,不易鉴定与很难鉴定;D由最左边起点开始,依照各不同要素之状况而向右边行进,而达到最右边即可得所要之AQL.E若使用上方便;可以考虑把AQL再缩减为几种,如所建议之AQL.假如工厂所要考虑的要素超过五种时,可以把下图增加AQL之范围,用同样方法求得AQL,上页图中之建议AQL可依各工厂实际需要斟酌分组得之;十八.检验记录的填写要求1.一般不准用铅笔,红笔,萤光笔填写;2.窗体涉及字段的签名者,均要签名且签全名,且均要带日期签名,且要符合签名样式;正式的公文签名时一定要黑色的水笔签;3.未填的多余字段要划掉备注栏可不用划掉,若有某些字段长期多余,可申请修改格式;4.填写不准涂改,若不得已涂改,必须在涂改处签名,一般涂改三处要重写一张;涂改时在涂改处划上一、二条删除线即可,要留意美观,不可涂成黑团,甚至涂破纸;5.若窗体为无碳纸过底纸时,注意用厚纸隔开,以免影响下面的空白页;6.一些小项目:序号、编号、日期、单位等不要遗漏;。
品检知识

品检知识(2)传统的检验方式主要是全检和抽检。
在保证质量和节约检验费用的前提下,许多发达国家在生产过程中的无检验方式得到推广。
一、检验误差的指标及考核方法1.检验误差的两个主要指标不论哪类原因造成的误差,均可概括为以下两类:1.1漏检,漏检就是有的不合格品没有被检查出来,当成了合格品,这当然使用户遭受损失。
这里所指的用户是广义的,下道工序也可以认为是上道工序的用户。
1.2错检,错检就是把合格品当成了不合格品,在检验员检查出来不合格品中还有的是合格品,这当然使生产者遭受损失。
2.测定和评价检验误差的方法2.1重复检查,由检验人员对自己检查过的产品再检查一到二次。
查明合格品中有多少不合格品,及不合格品中有多少合格品。
2.2复核检查,由技术水平较高的检验人员或技术人员,复核检验已检查过的一批合格品和不合格品。
2.3改变检验条件,为了解检验是否正确,当检验员检查一批产品后,可以用精度更高的检测手段进行重检,以发现检测工具造成检验误差的大小。
2.4建立标准品,用标准品进行比较,以便发现被检查过的产品所存在的缺陷或误差。
3.考核注意事项目前各企业对检验人员工作质量的考核办法,各不相同,还没有统一的计算公式。
由于考核是同奖金挂钩,而各个工厂的情况又互不相同,所以要采用统一的考核制度,比较困难。
但在考核中有些问题是共同性的,必须加以明确。
3.1质量检验部门和人员不能承包企业或车间的产品质量指标。
尽管检验工作对提高质量有促进作用。
但产品质量好坏主要决定于产部门的工作质量和控制能力。
检验人员的主要职能是把关,是把已经发生的不合格品从合格品中挑出来,并予以剔除。
剔除越干净越好,漏检越少,检查人员的工作质量就越高。
如果把产品质量由检验人员承包下来,就无益于检验人员自己考核自己,这是对质量检验职能的误解和歪曲,必将导致产品质量管理走入歧途,其后患将是无穷的,这种承包显然是不可取的。
3.2关于检验人员和操作人员的责任界限问题。
产品检测基础知识

管件的防腐检验
防腐的分类 1、单、双环氧粉末防腐。 2、聚乙烯胶粘带(冷缠带)防腐。 3、聚乙烯热缠带防腐。
环氧粉末防腐的检验
1、防腐前弯管表面必须达到下面要求: a、必须将附着在弯管表面的油及任何其他杂质清除 干净。 b、喷砂除锈后,应将弯管表面残留的钢丸、砂粒和 外表面锈粉微尘清除干净。 c、对可能影响涂层质量的表面缺陷应进行修理,使 表面完全满足涂敷的要求。 d、钢管外表面喷(抛)射除锈应达到GB/T8923中规定 的Sa2.5级。钢管表面的锚纹深度应在40μm~ l00μm范围内,并符合环氧粉末生产厂的推荐要求。
聚乙烯热缠带 热缠带可以单独进行防腐,也可在环氧后进 行防腐,性能比冷缠带要好。
品牌是企业最宝贵的资产,我们必须坚定 不移地进行品牌建设,弯管和管件的检验 不仅靠质检,也要靠大家的支持和帮助, 希望大家要认真学习公司质量文化,牢记 公司质量三耻观,不断的学习和创新,树 立大质量观意识,真正把质量提上去,树 立公司形象。
三检制度: 三检制——就是实行操作者自检、工序之 间的互检和专职检验人员的专检相结合的 一种检验制度。
UT(超声波检测)
无损检测
RT(射线检测) PT(渗透检测) MT(磁粉检测)
质量管理
外观检验
形位尺寸
尺寸检验
力学实验 化学实验
防腐检验
一、管件的外观尺寸检验。
二、管件、弯管防腐检验。
4、涂敷后至冷却之前的钢管温度应予以控制,从开 始涂敷起至少每小时测量并记录一次。 5、对每次开始生产的第一根管,要随机测量12个点 的总厚度和各层厚度值并做记录。如果涂层厚度 没有达到业主或本标准要求,则需要调整工艺参 数重新涂敷,直到达到要求为止,记录工艺参数。 正常生产后每2h用多功能涂层测厚仪按照ASTM D4138的要求在管端涂层边缘随机测量两层的厚度 一次。应对每一根钢管进行总厚度的测量,所有 的测量数据都应记录。
检验方面的科普小知识

检验方面的科普小知识一、检验的概念和分类检验是指通过对物质、产品或人体等进行实验、测定、观察等手段,以判断其是否符合规定要求的过程。
根据检验对象的不同,可以将检验分为物质检验、产品检验和人体检验三类。
二、物质检验1. 物质的组成分析:通过对物质进行化学分析,了解其组成和性质。
2. 物质的结构分析:通过对物质进行物理分析,了解其结构和性能。
3. 物质的纯度测定:通过对物质进行纯度测定,判断其是否符合规定要求。
4. 物质的微生物检测:通过对物质进行微生物检测,了解其是否受到污染。
三、产品检验1. 外观缺陷:通过对产品外观进行检查,发现并记录缺陷情况。
2. 尺寸偏差:通过对产品尺寸进行测量,发现并记录偏差情况。
3. 功能性能:通过对产品功能性能进行测试,判断其是否符合规定要求。
4. 耐久性测试:通过对产品耐久性进行测试,了解其使用寿命和可靠性。
四、人体检验1. 体格检查:通过对人体进行外观、生理和病理等方面的检查,了解其身体状况。
2. 生化检验:通过对人体血液、尿液等进行化学分析,了解其生化指标。
3. 免疫学检验:通过对人体免疫系统进行检测,了解其免疫功能是否正常。
4. 病原学检验:通过对人体样本进行细菌、病毒等的检测,判断其是否感染。
五、常见的检验方法1. 化学分析法:利用化学反应原理,通过对物质的成分和性质进行分析。
2. 物理分析法:利用物理原理,通过对物质的结构和性能进行分析。
3. 光谱分析法:利用光谱技术,通过对物质吸收、发射或散射光线的特性进行分析。
4. 检测仪器法:利用各种专业仪器设备,通过对物质或产品进行测试和测量。
六、常见的检验标准1. 国家标准(GB):由国家标准化委员会制定并公布实施的强制性标准。
2. 行业标准(JB):由各个行业协会或组织制定的标准,具有行业性质。
3. 企业标准(QB):由企业自行制定的标准,主要用于内部管理和产品质量控制。
七、检验的重要性1. 确保产品或物质的质量安全。
产品质量检验基础知识.
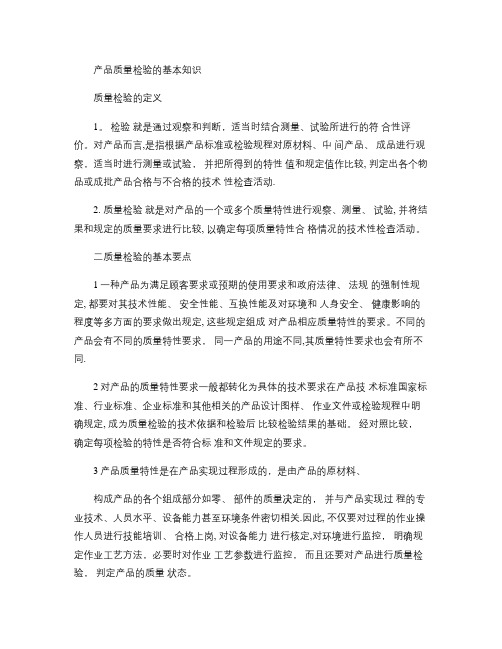
产品质量检验的基本知识质量检验的定义1。
检验就是通过观察和判断,适当时结合测量、试验所进行的符合性评价。
对产品而言,是指根据产品标准或检验规程对原材料、中间产品、成品进行观察,适当时进行测量或试验,并把所得到的特性值和规定值作比较, 判定出各个物品或成批产品合格与不合格的技术性检查活动.2. 质量检验就是对产品的一个或多个质量特性进行观察、测量、试验, 并将结果和规定的质量要求进行比较, 以确定每项质量特性合格情况的技术性检查活动。
二质量检验的基本要点1一种产品为满足顾客要求或预期的使用要求和政府法律、法规的强制性规定, 都要对其技术性能、安全性能、互换性能及对环境和人身安全、健康影响的程度等多方面的要求做出规定, 这些规定组成对产品相应质量特性的要求。
不同的产品会有不同的质量特性要求,同一产品的用途不同,其质量特性要求也会有所不同.2对产品的质量特性要求一般都转化为具体的技术要求在产品技术标准国家标准、行业标准、企业标准和其他相关的产品设计图样、作业文件或检验规程中明确规定, 成为质量检验的技术依据和检验后比较检验结果的基础。
经对照比较,确定每项检验的特性是否符合标准和文件规定的要求。
3产品质量特性是在产品实现过程形成的,是由产品的原材料、构成产品的各个组成部分如零、部件的质量决定的,并与产品实现过程的专业技术、人员水平、设备能力甚至环境条件密切相关.因此, 不仅要对过程的作业操作人员进行技能培训、合格上岗, 对设备能力进行核定,对环境进行监控,明确规定作业工艺方法,必要时对作业工艺参数进行监控,而且还要对产品进行质量检验,判定产品的质量状态。
4质量检验是要对产品的一个或多个质量特性,通过物理的、化学的和其他科学技术手段和方法进行观察、试验、测量,取得证实产品质量的客观证据。
因此,需要有适用的检测手段,包括各种计量检测器具、仪器仪表、试验设备等等,并且对其实施有效控制,保持所需的准确度和精密度。
检验知识点总结

检验知识点总结本文将对常见的检验知识点做一个总结,包括检验的基本原理、常见的检验方法以及其应用。
希望本文能够帮助读者对检验有一个更深入的了解。
一、检验的基本原理1. 检验的概念检验是指通过对物质的性质、成分、结构、形态等进行观察、测定、实验,以了解其质量、特性、使用价值等的一种科学技术活动。
检验是确保产品质量的一种手段。
2. 检验的目的检验的目的是为了保证产品的质量,防止不合格产品的流入市场,保护消费者的权益,维护生产者的合法权益,促进经济的健康发展。
3. 检验的原则(1)客观性原则:检验结果应该客观、公正,不受主观因素的影响。
(2)可靠性原则:检验方法和仪器设备应该是经过验证和认可的,能够保证结果的可靠性。
(3)全面性原则:检验应该对全部指标进行检测,不能遗漏任何一个指标。
(4)安全性原则:检验设备和环境应该是安全的,不会对操作者和被检测物质造成危害。
二、常见的检验方法1. 化学分析方法化学分析方法是通过化学反应来测定物质的成分和性质。
常见的化学分析方法包括滴定法、比色法、光度法、荧光法等。
2. 物理分析方法物理分析方法是通过物质的物理性质来测定其成分和性质。
常见的物理分析方法包括光谱法、色谱法、质谱法、磁谱法等。
3. 生物检验方法生物检验方法是通过生物学的特性来检验物质的成分和性质。
常见的生物检验方法包括生物酶法、生物耗氧法、生物毒性测试等。
4. 表面检验方法表面检验方法是通过表面的形态和结构来检验物质的性质。
常见的表面检验方法包括电镜法、扫描电镜法、显微镜法等。
5. 扩散检验方法扩散检验方法是通过物质的扩散性质来检验其成分和性质。
常见的扩散检验方法包括扩散法、渗透法、渗透磁阻法等。
三、检验的应用1. 工业生产工业生产中需要对原材料、中间产品和成品进行检验,以确保产品质量,减少不良品率,提高产品合格率。
2. 食品安全食品安全是关乎人民身体健康的重要问题,食品的质量安全需要经过严格的检验,确保食品的安全性和卫生。
产品检验入门基础知识题库100道及答案解析

产品检验入门基础知识题库100道及答案解析1. 产品检验的目的是()A. 发现不合格产品B. 确保产品质量C. 提高生产效率D. 降低成本答案:B解析:产品检验的首要目的是确保产品质量符合规定的要求。
2. 在产品检验中,抽样检验适用于()A. 少量产品B. 大量产品C. 贵重产品D. 定制产品答案:B解析:抽样检验通常用于大量产品的检验,以提高检验效率。
3. 产品检验的依据不包括()A. 国家标准B. 客户要求C. 企业内部标准D. 员工个人经验答案:D解析:产品检验应依据客观的标准,而不是员工个人经验。
4. 以下哪种检验属于破坏性检验()A. 外观检验B. 尺寸检验C. 硬度检验D. 拉伸试验答案:D解析:拉伸试验会对产品造成破坏,属于破坏性检验。
5. 抽样方案中,接收概率与()有关A. 样本容量B. 合格判定数C. 批质量水平D. 以上都是答案:D解析:接收概率与样本容量、合格判定数以及批质量水平都有关系。
6. 产品检验记录应包括()A. 检验项目B. 检验结果C. 检验日期D. 以上都是答案:D解析:产品检验记录需要包含检验项目、结果和日期等信息。
7. 检验误差可分为()A. 随机误差和系统误差B. 人为误差和设备误差C. 环境误差和方法误差D. 以上都是答案:A解析:检验误差主要分为随机误差和系统误差。
8. 提高检验准确性的方法不包括()A. 选用高精度仪器B. 增加检验人员C. 规范检验流程D. 对检验人员进行培训答案:B解析:增加检验人员不一定能提高检验准确性,关键在于检验流程的规范和人员的培训等。
9. 产品检验的“三检制”不包括()A. 自检B. 互检C. 专检D. 巡检答案:D解析:“三检制”包括自检、互检和专检。
10. 对于不合格产品,通常采取的措施是()A. 报废B. 返工C. 降级使用D. 以上都是答案:D解析:根据不合格产品的具体情况,可以采取报废、返工或降级使用等措施。
产品检验基础知识

3、最终检验 最终检验概述:是涉及实物质量的最后一个关
口,因此必须根据合同规定及有关技术标准或 技术要求对产品实施最终检验。 目的:防止不合格品出厂和流入到用户手中, 损害用户利益和企业的信誉。 主要形式 (1) 成品入库检验
① 定义:在将仓库中的产品送交客户前进行的检验 ② 如入库前已进行了严格检验,则一无需进行出厂检验;
d为抽样检验不合格(品)数,d1,d2…d5为1~5次检验不合格(品)数
8、检索抽样方案 1)样本大小字码表; 2)抽样方案表 9、样本的抽取 10、样本的检查 11、批合格或不合格的判断 12、检查后的处置
缺陷
的危害和重大财产损失
出现重大故障
B级 严重不合格 严重故障,不能满足预期的使用 目的
不可靠
C级 一般不合格 产品不符合要求,但能满足预期 产品使用期内
使用目的
可靠性有轻微
影响
D级 轻微不合格
无影响
无影响
二. GB2828的若干要素 (一) 设计目的 1. 通过调整检验的宽严程度,促使生产提高产品质量 . 2. 使用方可按质量的好坏选择供方 (二) 设计原则 1.AQL-可接收的质量水平是基础 2.保护供方利益的接受利益准则(优于AQL时全接受 ) 3.保护使用方利益的接受利益准则(劣于AQL时,加 严) 4.不合格分类是整个抽样系统的重要特点
开始检查
连续5批或少于 5批中有2批未接收
放宽检查
正常检查
有一批未接收 或接收但不合格数介于 Ac和Re之间 生产不稳定 或其他必要的情况
连续5批接收
加严检查 连续5批加严检查
停止检查
7、抽样方案类型
一次、二次、五次抽样方案只要设定的AQL值和检验水 平相同,对产品的质量保证能力是相同的;
- 1、下载文档前请自行甄别文档内容的完整性,平台不提供额外的编辑、内容补充、找答案等附加服务。
- 2、"仅部分预览"的文档,不可在线预览部分如存在完整性等问题,可反馈申请退款(可完整预览的文档不适用该条件!)。
- 3、如文档侵犯您的权益,请联系客服反馈,我们会尽快为您处理(人工客服工作时间:9:00-18:30)。
产品检验知识一.产品的概念1.产品——活动或过程的结果。
产品包括服务,也可以是有形的,也可以是无形的,或它们的组合。
ISO9001标准中产品仅指期望提供给顾客所要求的产品,而不是影响环境的非期望的副产品。
2.产品有四类:硬件,软件,流程性材料,服务。
3.硬件是有形产品并具有计数的特性4.软件由信息组成,通常是无形产品并可用方法、记录、或程序的形式存在(如设计软件、程序、字典、手册、文件)5.流程性材料是在形产品并具有连续的特性;流程性材料和硬件称为货物;6.服务:是在供方和顾客接触面上需要完成的至少一项活动的结果,并且通常是无形的。
7.非预期性产品:指生产过程中的附产物;在生产过程中伴随的废料、废气、废液等物,有可能造成环境污染,不属于质量管理的范畴,属于环境管理的范畴;8.产品的标识:名称标识和标识状态9.产品并非一定是成品(装配并包装完成的产品),它也可指半成品、完成品(中间过程的产物,一般指装配完成产品)。
二.品质的概念1.品质:反映产品或服务满足明确或隐含需要能力的特征和特征的总和。
(ISO9001:94)2.品质:一组固有特性(3.5.1)满足要求(3.1.2)的程度。
(ISO9001:2000)3.“固有的”(其相反是“外来的”)就是指在某事或某物中本来就有的,尤其是那种永久的特性4.品质=特性+交期+成本+服务5.质量特性:产品满足人们某种所具备的属性和特性。
综合归纳为:性能、寿命、可靠性、安全性、经济性和外观质量六大质量特性。
6.质量特性分为真正质量特性和代用质量特性。
真正质量特性:用户所要求的使用特性;代用质量特性:真正质量特性在转化为在生产中衡量产品质量的标准或规格。
7.性能:根本产品使用目的所提出的各项功能要求,包括正常性能、特性性能、效率等。
8.寿命:产品能够正常使用的期限,包括使用寿命和储存寿命两种。
使用寿命:在规定条件满足规定功能的工作总时间。
储存寿命:在规定条件、功能不失效的储存总时间。
9.可靠性:产品在规定时间、条件下完成规定功能的能力。
10.安全性:产品在流通和使用过程中保证安全的程度;11.影响质量问题的制造和检测条件——6个因素:“5M1E”人员(Man)、机器(Machine)、材料(Material)、方法(Method)、测试(Measurement)环境(Environment)12.相同的制造检测条件下,仍有许多变异。
这些变异形成之原因分为两类:机遇原因、非机遇原因:A.机遇原因。
又叫不可避免原因、非人为原因、共同原因、偶然原因、一般原因:同一量测器在十分钟内测同一个人的身高,不一定每次相同;同人同机按生产标准作业,但产品在容差内变化;气候及环境变化造成的品质变异;大量微小原因,不易除去;特点是:影响微小、始终存在、方向不定、难以控制。
呈典型分布B.非机遇原因。
又叫可避免原因、人为原因、特殊原因、异常原因、局部原因:4M不同造成的品质异常,本可避免;未按作业标准操作;作业标准还完善而造成;量具不同而造成;可避免且必须除去特点是:影响很大、时有时无、方向一定、可以控制。
呈非典型分布,表现为分布中心和标准偏差的变化。
三.检验的基本概念1.定义:对实体的一个或多个特性进行的诸如测量、检查、试验或度量,并将结果与规定要求进行比较以确定每项特性合格情况所进行的活动。
(GB8402)2.定义:通过观察或判断,适当地结合测量、试验所进行的符合性评价。
(GB19000:2000)3.说明:检验判定“合格”、“不合格”是符合性判定;而不合格处理是适用性判定,不是检验的职能。
4.判定合格只是对品质标准而言,并不意味着质量水平的高低。
四.检验的过程测量检查试验2.根据图示可归纳为检验的三大要素:A.检验合格判定标准(品质标准)B.检验方法和规范C.检验记录3.检验合格判定标准是单个产品之检验判定的依据,是产品质量内涵的体现,内容包括:3.1检验的质量特性(项目)的描述。
3.2各种质量特性的标准值和允差范围。
3.3各种质量特性(缺陷)的重要性(严重性)规定。
4.检验方法和规范:规定如何进行检验4.1检验方法(目测、量测、试验等)。
4.2抽样方案(计数或计量,样组大小,AQL,取样方法)4.3检查手段的精度、功能要求(如工具、仪器、量具等)。
4.4检验环境、设施要求(如温湿度、噪音、照明光线等)。
4.5检验人员的技能、资格要求。
4.6检验的步骤和具体操作方法。
5.检验记录,内容包括检验对象的记录,其产品名称、规格、批量、编号等。
检验环境、设备的记录;检验员、审核员记录:日期、时间记录。
检验结果数据,如长度、温度、电阻、缺陷数等。
判定结论的记录。
五.检验的分类1.按检验数分:全检、抽检、免检。
2.按工序流程分:IQC、IPQC(可再分:首检、巡检、转序检验)、FQC、OQC、驻厂QC。
3.按检验人责任分:专检、自检、互检。
4.按检验场所分:工序专检和线上巡检,外发检验、库存检验、客处检验。
5.按检验性质分:破坏检验、非破坏检验6.按检验内容分:试制品检验、性能检验、可靠性检验、苛刻检验、分解检验7.按检验数据类别分:计数检验、计量检验六.全检适用范围1.批量太小,失去抽检意义时。
2.检验手续简单,不致于浪费大量人力、经费时。
3.不允许不良品存在,该不良品对制品有致命影响时。
4.工程能力不足,其不良率超过规定、无法保证品质时。
5.为了解该批制品实际品质状况时。
七.抽检的适用范围1.产量大、批量大,且是连续生产无法作全检时。
2.破坏性测试。
3.允许有某种程序的不良品存在时。
4.欲减少时间和经费时。
5.刺激生产者要注意品质时。
6.满足消费者要求时。
八.免检适用范围1.生产过程相对稳定,对后续生产无影响。
2.国家批准的免检产品及产品质量认证产品的无试验买入时。
3.长期检验证明质量优良,使用信誉高的产品的交收中,双方认可生产方的检验结果,不再进行进料检验。
☆免检并非放弃检验,应加强生产方过程质量的监督,一有异常,拿出有效措施。
九.紧急放行当原材料、半成品来不及检验时,可以紧急放行,但要作明确标识;一般情况下,须要留一少部分作即时检验。
若发现不良时,立即召回。
成品不能紧急放行。
召回后质量特性不可复原时,不能紧急放行。
十.质量成本1.定义:为确保和保证满意的质量而发生的费用以及没有达到满意的质量所造成的损失。
◎质量成本分为和间接两种。
某些损失可级难以定量,但很重要,如丧失信誉。
2.产品价值=利润+质量成本+生产成本+设计成本3.直接质量成本项目:(分为4个二级子目和20个三级细目)A。
预防成本:质量工作费、质量培训费、质量奖励费、产品评审费、质量改进费、工资及福利基金B.固定成本(检验成本):检测费、办公室费、检测设备折旧费、工资及福利基金C.内部损失故障成本:废品损失、返修损失、停工损失、产品降级损失、事故分析处理费D.外部故障成本:保修费用、退货损失、诉讼费、索赔费用、产品降价损失4.间接质量成本:顾客遭遇故障之品质成本、顾客不满意之品质成本、信誉损失之品质成本十一..产品检验的基本事项1 单个产品的划分A.自然划分:一个钉,一台机器B.非自然划分:布匹、油漆、钢材2 三类不合格(Nonconformity,ISO9001:2000以“不合格”取代94版的“缺陷”Defect)A类不合格(严重不合格,Cr, Critical)B类不合格(主要不合格,Major, MA, Maj)C类不合格(次要不合格,Minor, MI, Min)3.四类不合格分级(贝尔系统)A级——非常严重(缺陷值100)1.必然会造成部件在使用中运转失灵,并在现场难以纠正,如继电器的断开;2.必然会造成间歇的运转故障,在现场难以确定其位置,如连接不紧;3.会使部件完全不合用,如拔号指盘在运转后不回复到正常状态;4.在正常使用情况下,易于造成人员伤害或财产损失,如露出部分有锐利边缘。
B 级– 严重(缺陷值50)1.可能会造成部件在使用中运转失灵,并在现场难以纠正,如同轴插塞的保护系统涂层缺损;2.必然会造成部件在使用中运转失灵,但在现场易于纠正,如继电器接触不良;3.必然会造成那种尚未严重到运转失灵程度的麻烦,象次于标准运转之类麻烦,如保安器件不能在特定电压之下运转;4.必然会导致增加保养次数或减短寿命,如单接点圆盘缺漏;5.造成大大增加顾客安装上的困难,如安装孔错位’;6.极严重的外形或涂层上缺陷,如涂层颜色与其它部件不能匹配;需要重涂。
C级– 中等严重(缺陷值10)1.可能会造成部件在使有中运转失灵,如接触低于最低限度;2.可能造成那种尚未严重到运转失灵程度的故障,象次于标准运行之类故障,如振铃不在特定范围内运转;3.可能导致增加保养次数或减短寿命,如接触骯脏;4.造成顾问安装上的小困难,如安装托座歪曲;5.较大的外形、涂层或工艺缺陷,如涂层有明显的划痕,标志漏缺或模糊。
D级– 不严重(缺陷值1)1.不影响部件在使用时的运转、保养或寿命(包括对工艺要求上的小偏差),如套管太短;2.外形、涂层或工艺上小毛病,如涂层轻微划痕;这是由贝尔实验室首先提出。
对质量特性进行分级控制具有的作用:1.能够重点保障重要特性的满足,能节省检验成本。
当年贝尔公司把一道重要工序检验项目分四级后,检验时间从120分钟减为50分钟。
2.可将多个质量特性综合量化进行评价。
以上列出的缺陷值是一个加权值。
通过这个加权值可以把不同缺陷累加综合在一起,量化地反映出产品质量水平。
4.单位产品的度量方法:A.计数法,又分为计件法:以产品的个数计算的方法;如不合格品数,或一等品、二等品数;计点法:衡量缺陷数的方法B.计量法:(物理量表示)5 质量管理活动的基础:一切以数据说话。
6 数据分为数字数据和非数字数据(又叫情理型数据)a)数字数据分为计数值数据和计量值数据b)计数值数据:只能是一个非连续性的特定数值,不能取这些数值之间的值,只可点出整数,如人数、件数,缺点数等;计数值数据分为计件数据和计点数据。
计量值数据:能取给定范围内的任何一个可能的值,可连续收集。
如长度、重量、时间、温度等;C.非数字数据:语言、文字、图形所表示的数据;如信息、意见、反应、议题、图形等。
十二.抽样检验的相关定义1 批(在一定条件下生产出来的一定数量的单位产品所构成的团体),批的单位:卷、箱、包、个、张、板、公斤)2 检验批(为实施检验而汇集起来的单位,便于抽样进行,便于抽样结果更具代表性)3 批量N4 样本及样本大小n5 样品6 对于规格精度不高(如±1~2mm)、破坏性检验等的项目,一般采用抽检1~5个的特殊方法,可对应MIL—STD—105E的S-I抽样。
7 合格判定数(AC),不合格判定数(RE)8 抽样检验:从检验批中,依批量大小抽出一定数量样本进行检验的方法。