聚氨酯湿法合成革
水性聚氨酯树脂(水性合成革表处剂肤感树脂)

水性聚氨酯树脂(水性合成革表处剂肤感树脂)
产品描述
GSB-3660是聚氨酯水分散体,专用于水性合成革表面消光处理剂的制作,加入消光粉后具有较强的消光作用,光泽柔和自然不泛白、手感舒适丰满并有丝绒般效果;同时涂层还具有优异的耐曲挠性、耐磨性、耐水性、耐候性,是生产皮革顶涂的理想材料。
物化指标
●外观:淡黄色半透明液体
●固含量:29±1%
●PH值:7-8
●稀释剂:水
●离子性:阴离子
性能特点
●对消光粉有较好的相溶性、润湿性
●成膜后能赋予皮革细柔的弹性及皮纹精细均匀的性能
●带给皮革表面棉滑、丝绸、滋润之手感,不会影响皮革表面物性
●用水作稀释剂,不含甲醛、重金属
●优良的成膜性、均匀性、填充性、透色性
应用范围
●适用于PU革、PVC合成人造革及皮革制品的表层手感处理用树脂
包装贮运
●本产品用塑料包装桶包装,125Kg。
●本品属水性乳液,不易燃、不易爆,按非危险品运输。
●本品应在5-35℃运输和储存,有效储存期为12个月。
备注
本说明均为实践认证的资料,因用户使用条件及产品要求各异,请务必进行实验或与我厂技术部联系,再确定适合贵厂的使用工艺。
我们承载不止是树脂,更多的是配方支持。
合成革用自消光水性聚氨酯树脂的制备和表征
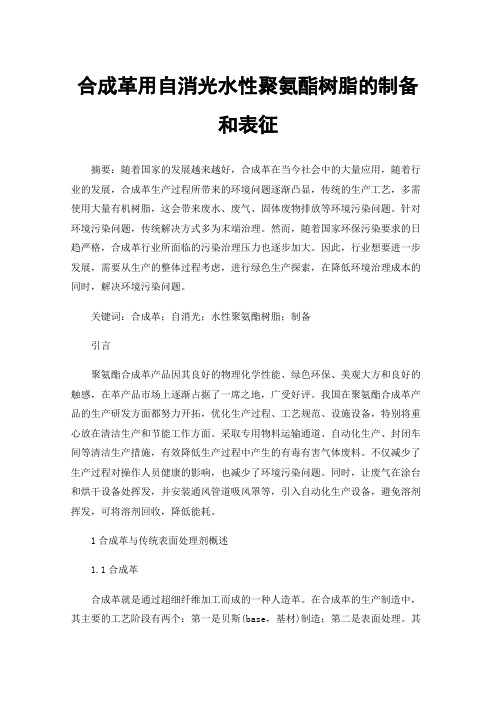
合成革用自消光水性聚氨酯树脂的制备和表征摘要:随着国家的发展越来越好,合成革在当今社会中的大量应用,随着行业的发展,合成革生产过程所带来的环境问题逐渐凸显,传统的生产工艺,多需使用大量有机树脂,这会带来废水、废气、固体废物排放等环境污染问题。
针对环境污染问题,传统解决方式多为末端治理。
然而,随着国家环保污染要求的日趋严格,合成革行业所面临的污染治理压力也逐步加大。
因此,行业想要进一步发展,需要从生产的整体过程考虑,进行绿色生产探索,在降低环境治理成本的同时,解决环境污染问题。
关键词:合成革;自消光;水性聚氨酯树脂;制备引言聚氨酯合成革产品因其良好的物理化学性能、绿色环保、美观大方和良好的触感,在革产品市场上逐渐占据了一席之地,广受好评。
我国在聚氨酯合成革产品的生产研发方面都努力开拓,优化生产过程、工艺规范、设施设备,特别将重心放在清洁生产和节能工作方面。
采取专用物料运输通道、自动化生产、封闭车间等清洁生产措施,有效降低生产过程中产生的有毒有害气体废料。
不仅减少了生产过程对操作人员健康的影响,也减少了环境污染问题。
同时,让废气在涂台和烘干设备处挥发,并安装通风管道吸风罩等,引入自动化生产设备,避免溶剂挥发,可将溶剂回收,降低能耗。
1合成革与传统表面处理剂概述1.1合成革合成革就是通过超细纤维加工而成的一种人造革。
在合成革的生产制造中,其主要的工艺阶段有两个:第一是贝斯(base,基材)制造;第二是表面处理。
其中,表面处理就是对贝斯半成本表面进行涂饰处理,使成为终端成品。
在合成革中,主要的构成部分有三层:第一层是粘接层;第二层是中间发泡层;第三层是表面效应层,也就是表面处理剂层。
这种材料的主要优势是透气性好、耐磨、不易破坏,且具备一定的抗腐蚀性能。
凭借着这些优势,合成革在当今的服饰领域中已经得到了广泛的应用。
1.2传统合成革表面处理剂在以往的合成革表面处理中,其处理剂主要包括溶剂形式的丙烯酸树脂处理剂以及聚氨酯处理剂。
合成革湿法
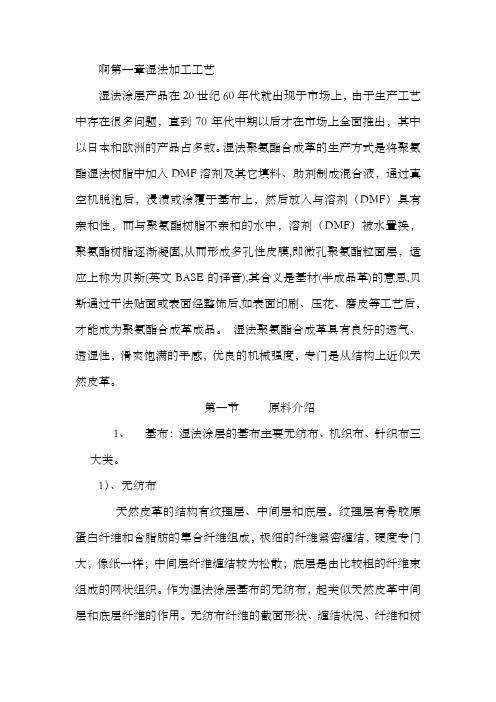
啊第一章湿法加工工艺湿法涂层产品在20世纪60年代就出现于市场上,由于生产工艺中存在很多问题,直到70年代中期以后才在市场上全面推出,其中以日本和欧洲的产品占多数。
湿法聚氨酯合成革的生产方式是将聚氨酯湿法树脂中加入DMF溶剂及其它填料、助剂制成混合液,通过真空机脱泡后,浸渍或涂覆于基布上,然后放入与溶剂(DMF)具有亲和性,而与聚氨酯树脂不亲和的水中,溶剂(DMF)被水置换,聚氨酯树脂逐渐凝固,从而形成多孔性皮膜,即微孔聚氨酯粒面层,适应上称为贝斯(英文BASE的译音),其含义是基材(半成品革)的意思,贝斯通过干法贴面或表面经整饰后,如表面印刷、压花、磨皮等工艺后,才能成为聚氨酯合成革成品。
湿法聚氨酯合成革具有良好的透气、透湿性,滑爽饱满的手感,优良的机械强度,专门是从结构上近似天然皮革。
第一节原料介绍1、基布:湿法涂层的基布主要无纺布、机织布、针织布三大类。
1)、无纺布天然皮革的结构有纹理层、中间层和底层。
纹理层有骨胶原蛋白纤维和含脂肪的集合纤维组成,极细的纤维紧密缠结,硬度专门大,像纸一样;中间层纤维缠结较为松散;底层是由比较粗的纤维束组成的网状组织。
作为湿法涂层基布的无纺布,起类似天然皮革中间层和底层纤维的作用。
无纺布纤维的截面形状、缠结状况、纤维和树脂之间的彼此关系,决定了湿法涂层织物类似于天然皮革的程度。
作为革基布的无纺布,它的原料主如果利用的聚酯纤维和聚酰胺纤维。
制造方式有针刺法、水刺法。
针刺法工艺:纤维开包混棉梳理铺网多台针刺机成卷后处置通过带有倒钩的钢针垂直方向高频率针刺把纤维与纤维进行缠结。
水刺法工艺:纤维开包混棉梳理铺网多台水刺机成卷后处置通太高压水流从小孔中喷射形成水针使纤维发生缠结。
2)、机织布坯布织成后,通过练漂、染色、定性、起毛等工序才能涂层。
在这些工序中起毛是最重要的,应尽可能做到绒毛密度大,散布匀,长度齐。
由于起毛的绒毛主要来自纬纱,纬纱要比经纱粗,纱的线密度比越为2:1,而且加大纬纱密度来增加绒毛密度,能够更好地遮盖织物的组织点。
合成革用聚氨酯的研制及染色研究
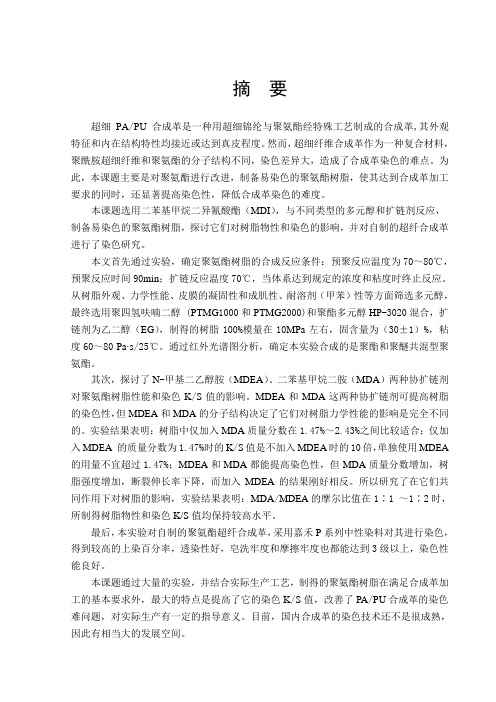
摘要超细PA/PU合成革是一种用超细锦纶与聚氨酯经特殊工艺制成的合成革,其外观特征和内在结构特性均接近或达到真皮程度。
然而,超细纤维合成革作为一种复合材料,聚酰胺超细纤维和聚氨酯的分子结构不同,染色差异大,造成了合成革染色的难点。
为此,本课题主要是对聚氨酯进行改进,制备易染色的聚氨酯树脂,使其达到合成革加工要求的同时,还显著提高染色性,降低合成革染色的难度。
本课题选用二苯基甲烷二异氰酸酯(MDI),与不同类型的多元醇和扩链剂反应,制备易染色的聚氨酯树脂,探讨它们对树脂物性和染色的影响,并对自制的超纤合成革进行了染色研究。
本文首先通过实验,确定聚氨酯树脂的合成反应条件:预聚反应温度为70~80℃,预聚反应时间90min;扩链反应温度70℃,当体系达到规定的浓度和粘度时终止反应。
从树脂外观、力学性能、皮膜的凝固性和成肌性、耐溶剂(甲苯)性等方面筛选多元醇,最终选用聚四氢呋喃二醇 (PTMG1000和PTMG2000)和聚酯多元醇HP-3020混合,扩链剂为乙二醇(EG),制得的树脂100%模量在10MPa左右,固含量为(30±1)%,粘度60~80 Pa·s/25℃。
通过红外光谱图分析,确定本实验合成的是聚酯和聚醚共混型聚氨酯。
其次,探讨了N-甲基二乙醇胺(MDEA)、二苯基甲烷二胺(MDA)两种协扩链剂对聚氨酯树脂性能和染色K/S值的影响。
MDEA和MDA这两种协扩链剂可提高树脂的染色性,但MDEA和MDA的分子结构决定了它们对树脂力学性能的影响是完全不同的。
实验结果表明:树脂中仅加入MDA质量分数在1.47%~2.43%之间比较适合;仅加入MDEA的质量分数为1.47%时的K/S值是不加入MDEA时的10倍,单独使用MDEA 的用量不宜超过1.47%;MDEA和MDA都能提高染色性,但MDA质量分数增加,树脂强度增加,断裂伸长率下降,而加入MDEA的结果刚好相反。
所以研究了在它们共同作用下对树脂的影响,实验结果表明:MDA/MDEA的摩尔比值在1∶1 ~1∶2时,所制得树脂物性和染色K/S值均保持较高水平。
湿法pu合成革生产工艺

湿法聚氨酯合成革生产工艺湿法聚氨酯合成革的生产方法是将聚氨酯湿法树脂中加入DMF 溶剂及其它填料、助剂制成混合液,经过真空机脱泡后,浸渍或涂覆于基布上,然后放入与溶剂(DMF)具有亲和性,而与聚氨酯树脂不亲和的水中,溶剂(DMF)被水置换,聚氨酯树脂逐渐凝固,从而形成多孔性皮膜,即微孔聚氨酯粒面层,习惯上称为贝斯(英文BASS的译音),其含意是基材(半成品革)的意思,贝斯经过干法贴面或表面经整饰后,如表面印刷、压花、磨皮等工艺后,才能成为聚氨酯合成革成品。
湿法聚氨酯合成革具有良好的透气、透湿性,滑爽丰满的手感,优良的机械强度,特别是从结构上近似天然皮革,湿法合成革贝斯的生产工艺可分为单涂覆法、浸渍法和含浸涂覆法三种,所用基布有纺织布和无纺布两类。
(一)、单涂覆法聚氨酯贝斯1、生产工艺流程基布开卷经储布架进入浸槽浸湿,再通过挤压辊将水挤出大部分,通过烫平轮除去部分水分,同时将基布烫平,然后在涂布机上涂覆配合浆料,再进入凝固槽成皮膜,再充分水洗、烘干定型、冷却成大卷贝斯。
2、主要原料A、聚氨酯树脂:通常为普通湿法树脂,磨皮专用,含浸专用及耐寒树脂等,树脂的模量(100%)从2。
0MPa至30.0MPa不等.根据贝斯软硬度,选用高低模量牌号树脂,单涂覆贝斯由于泡孔小、密度大,往往加入大量木质粉及其他填料,故当产品用于寒冷地区时,要充分考虑产品的耐寒性能,采用耐寒性能好的树脂。
B、木质粉:在单涂覆贝斯中使用一定量的木质粉,既能降低产品成本,又能在凝固过程中起到骨架的作用,不同型号厂家的木质粉,其膨胀系数不同,这样便在同等其他材料相同的情况下,其粘度值均不相同,也直接影响到产品的质量及相应的成本,木质粉的细度要求一般要达到400目以上。
C、阴离子表面活性剂(C-70,C—90):又称为快速渗透剂,具有亲水性.主要起到加快DMF与水的交换速度,提高生产速度,同时使泡孔细密化.阴离子表面活性剂可生成球形泡孔结构,增加回弹性、透气性、透湿性。
聚氨酯合成革工艺过程及环境影响分析
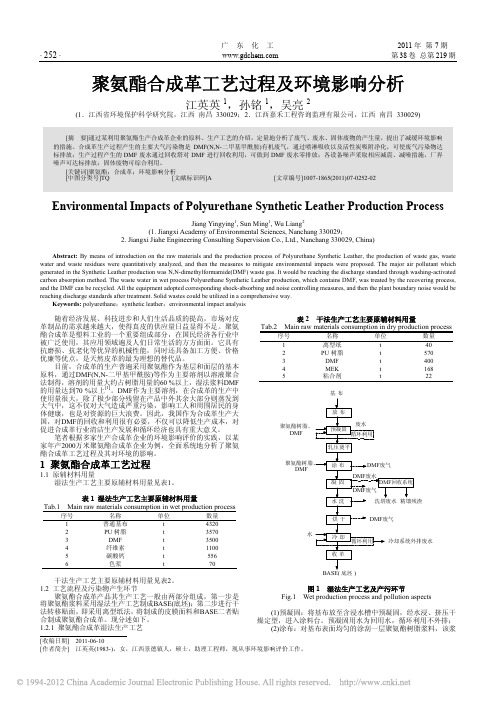
414.723 4.577
4.977 0.055
12000
2.074 0.023
0.025 0.0003
烫平
0.01
0.0001
0.0001
0
表 4 干法工艺中 DMF 产生与排放情况
Tab.4 DMF generation and emissions in dry process
污染工艺
产生浓度 产生速率 风量 排放浓度 排放速率 /(mg·m-3) /(kg·h-1) /(m3·h-1) /(mg·m-3) /(kg·h-1)
Keywords: polyurethane;synthetic leather;environmental impact analysis
随着经济发展、科技进步和人们生活品质的提高,市场对皮 革制品的需求越来越大,使得真皮的供应量日益显得不足。聚氨 酯合成革是塑料工业的一个重要组成部分,在国民经济各行业中 被广泛使用,其应用领域遍及人们日常生活的方方面面。它具有 抗磨损、抗老化等优异的机械性能,同时还具备加工方便、价格 优廉等优点,是天然皮革的最为理想的替代品。
(4)剥离:冷却后,将聚氨酯合成革与离型纸分离,聚氨酯合 成革收缩成卷得成品革。分离产生的废离型纸可重新使用10次后 废弃,产生废弃离型纸。此过程产生冷却系统定期外排水。
因此干法过程主要污染物包括洗桶废水、喷淋系统产生的含 DMF废水,冷却系统外排水;干法配料、涂布和烘干过程中产生
的DMF废气和VOCs废气;以及配料过程中产生的废弃原料桶和 原材料包装材料,剥离过程产生的废弃离型纸。
放布
废水 预凝固
循环利用
轧压烫平
聚氨酯树脂、 DMF
涂布 凝固 水洗
DMF废气
pu合成革的干法与湿法工艺

pu合成革的干法与湿法工艺PU合成革的干法与湿法工艺1. 引言•PU合成革是一种人造材料,具有与天然皮革相似的外观和手感•制作PU合成革的工艺主要分为干法和湿法两种2. 干法工艺•干法工艺是指在制作过程中不使用水•主要步骤包括原料配方调制、混合搅拌、涂覆、干燥等•干法工艺的优点是生产效率高、能耗低、成本较低•然而,干法工艺的制品常常比湿法工艺的制品硬度较高,柔软度和透气性较差3. 湿法工艺•湿法工艺是指在制作过程中使用水•主要步骤包括原料浸泡、混合搅拌、涂覆、干燥等•湿法工艺的优点是制品柔软度好、透气性好•然而,湿法工艺的制作过程中使用水,可能会对环境造成一定污染4. 干法工艺与湿法工艺的比较•干法工艺适用于对产品硬度要求较高的领域,如汽车座椅、箱包等•湿法工艺适用于对产品柔软度和透气性要求较高的领域,如衣物、鞋子等•干法工艺一般成本较低,适合大批量生产•湿法工艺一般成本较高,适合小批量或定制生产5. 总结•PU合成革的干法和湿法工艺各有优劣•在使用PU合成革材料时,需要根据具体的产品要求选择合适的工艺•干法和湿法工艺的选择将直接影响产品的硬度、柔软度和透气性以上是对PU合成革的干法与湿法工艺进行简要介绍,希望对您有所帮助。
6. 干法工艺的具体步骤•原料配方调制:根据产品需求,将PU树脂、溶剂、助剂等按照一定比例进行配制•混合搅拌:将原料放入搅拌机中进行均匀搅拌,使各种成分充分混合•涂覆:将混合好的材料均匀涂覆于底布或网布上,形成涂层•干燥:将涂层的材料放入干燥室中进行干燥,使其固化和去除残余溶剂7. 湿法工艺的具体步骤•原料浸泡:将PU树脂等原料浸泡在大容器中的水溶液中一段时间,使其吸水膨胀•混合搅拌:将浸泡好的原料放入搅拌机中进行均匀搅拌,使各种成分充分混合•涂覆:将混合好的材料均匀涂覆于底布或网布上,形成涂层•干燥:将涂层的材料放入干燥室中进行干燥,使其固化和去除余水8. 干法工艺的优缺点•优点:–生产效率高,适合大批量生产–能耗低,成本较低•缺点:–制品硬度较高,柔软度和透气性较差9. 湿法工艺的优缺点•优点:–制品柔软度好,透气性好•缺点:–制作过程中使用水,可能会对环境造成一定污染–成本较高,适合小批量或定制生产10. 结论•干法工艺适用于对产品硬度要求较高的领域,如汽车座椅、箱包等•湿法工艺适用于对产品柔软度和透气性要求较高的领域,如衣物、鞋子等•在产品制作过程中,需要根据具体要求选择合适的工艺,以获得理想的产品性能和外观。
聚氨酯合成工艺

200万米/年聚氨酯合成革厂的工艺设计摘要聚氨酯(PU)合成革属于聚氨酯弹性体的一类,其工业化工艺生产方法主要有干法和湿法两大类。
通过对PU合成革的发展历史、性能、应用市场的了解,确定年产200万米聚氨酯合成革的生产工艺设计。
主要从其生产配方、生产工艺流程开始设计,进一步进行PU合成革生产中的物料衡算和能量衡算。
从而确定聚氨酯合成革生产的技术参数、工艺流程和主要设备的选择。
同时还对聚氨酯合成革生产企业的三废处理和安全技术进行设计。
关键词:聚氨酯(PU)合成革干法湿法AbstractPolyurethane synthetic leather (PU) belongs to a class of polyurethane elastomer, the industrialized production method mainly has two kinds of dry and wet. Through the synthetic leather development history, performance, application market understanding of PU, determine the design process with an annual output of 2000000 meters of polyurethane synthetic leather. Mainly from the production formula, process design; further PU synthetic leather material balance in production and energy balance. In order to ,determine the parameters of polyurethane synthetic leather technology, production process and main equipment selection. At the same time also synthesis design leather waste treatment and safety technology production enterprise of polyurethane.Keywords:polyurethane (PU) Synthetic leather dry process wet process第一章综述1.1聚氨酯聚氨酯合成革的原料——聚氨酯(以下简称为PU)树脂是聚氨基甲酸酯的简称。
- 1、下载文档前请自行甄别文档内容的完整性,平台不提供额外的编辑、内容补充、找答案等附加服务。
- 2、"仅部分预览"的文档,不可在线预览部分如存在完整性等问题,可反馈申请退款(可完整预览的文档不适用该条件!)。
- 3、如文档侵犯您的权益,请联系客服反馈,我们会尽快为您处理(人工客服工作时间:9:00-18:30)。
聚氨酯湿法合成革聚氨酯浆料用作涂层制备聚氨酯合成革、人造革。
聚氨酯合成革具有光泽柔和、自然,手感柔软,真皮感强的外观,具有与基材粘接性能优异、抗磨损、耐挠曲、抗老化、抗霉菌性好等优异的机械性能,同时还具备耐寒性好、透气、可洗涤、加工方便、价格优廉等优点,是天然皮革的最为理想的替代品,广泛应用于服装、制鞋、箱包、家具、体育等行业。
凡是真皮应用的领域,它都可替代,而且还可应用于真皮无法应用的领域,真皮的行情很容易受动物(牛、羊、猪等行情的影响,疯牛病)。
湿法聚氨酯浆料——由于加工过程采用的是将DMF用水抽提(原因是DMF与水有无限的溶解性),比较环保,而且生产出的合成革具有良好的透湿、透气性能,手感柔软、丰满、轻盈,更富于天然皮革的风格和外观,因此发展速度极为惊人。
湿法聚氨酯合成革是新—代天然皮革的最佳替代产品,它的生产方法是将聚氨酯树脂的DMF溶液添加各种助剂,制成浆料,浸渍或徐覆于基布上,然后放入与溶剂(DMF)具有亲和性、而与聚氨酯树脂不亲相的液体(如水)中,溶剂(DMF)被水置换,聚氨酯树脂逐渐凝固,从而形成多孔性的皮膜,即微孔聚氨酯粒面层。
习惯上称为贝斯(英文Bass的译音),其含意是基材的意思,也就是指湿法聚氨酯半成品革,贝斯表面经整饰后.才能成为聚氨酯合成革成品。
湿法聚氨酯合成革具有卓越的性能.有良好的透气、透湿性,滑爽丰满的手感,优良的机械强度,特别是从结构上近似天然皮革.所以其产品用途与天然皮革相同.可以做服装、鞋、箱包、球类等。
而且花色品种比天然皮革多样、美观,用途广泛,发展迅速。
湿法聚氨酯合成革贝斯的生产工艺可分为单涂覆法、浸渍法和含浸涂覆法3种,所用基布有纺织布和无纺布两类,本文首先介绍单涂覆法的工艺流程。
单涂覆法聚氨酯贝斯通常以下织布、单面起毛巾、无纺布为底基.表面涂覆聚氨酯配合液,经凝固、水洗、烘干而成。
单涂覆法贝斯常常再以干法转移贴面形成产品,或经磨皮机打磨形成产品。
主要用于、轻便鞋、皮包、钱夹等方面。
特别是经过干法转移贴面的单涂覆贝斯制成的合成革,花色品种繁多,既可以生产普通的花纹革,又可以生产镜面革、内花纹革、珠光革、彩印镜面革等,极大地拓宽了产品的用途,向市场提供了丰富多彩的产品。
一、主要原料:1、聚氨酯树脂单涂覆贝斯常用的树脂为普通湿法聚氨酯树脂、磨皮专用树脂及耐寒型树脂等。
树脂的100%模量从1.5MPa到30.0MPa不等。
要求贝斯软时,选用低模量牌号树脂;要求贝斯硬时,选用高模量型号树脂。
单涂覆贝斯由于泡孔小,密度较大.而且往往加入大量木质粉及其他填料.故当产品用于寒冷地区时,要充分考虑产品的耐寒性能,采用耐寒性能好的树脂。
常用单涂覆聚氨酯树脂名词含义品名Name of Product ;固体份Solid(%) ;粘度Viscosity(pa.s/25 );溶剂Viscosity Solvent;100%模量Modulus(Mpa) ;抗拉强度T/S(Mpa) ;伸长率E/L(%) ;特性及用途Characteristics&Application2.木质粉在单涂覆贝斯配方中使用一定量的木质粉,既能降低产品成本.又能在凝固过程中起到骨架的作用。
木质粉的细度一般在400目以上。
3.阴离子表面活性剂OT—70 阴离子表面活性剂主要起加快DMF与水的交换速度.提高凝固速度的作用,同时,使泡孔细密化。
阴离子表面活性剂可生成球形泡孔结构。
4.非离了表面活性剂S—80 非离子表面活性剂由于其具有疏水性,可推迟表面的凝固速度,因面可使内部的DMF与水更快更充分地交换,非离子表面活性剂可生成针状的泡孔结构。
5.二甲基甲酰胺(DMF) DMF用于溶解及稀释聚氨酯树脂,用于单涂覆贝斯时,纯度要求不很高,达到98%以上即可满足工艺要求,但甲酸含量应小于0. 01%(PH值大于4),以防止引起DMF的分解。
6.基布单涂覆贝斯所用基布主要以平织布、单面起毛布为基布,也可以采用高分于材料浸渍过的无纺布。
二、配方设计原则1、树脂聚氨酯树脂仍然是决定湿法聚氨酯贝斯性能的主要因素之一。
为了满足不同的使用要求.使贝斯具有不同的性能,就需要认真地选择树脂牌号。
如用于服装或包袋等要求较软的贝斯时,应选择低模量树脂,100%模量在5.0—7.5MPa,甚至更低的树脂,以使手感柔软,比如模量为20、15树脂等,一般从每年10月中旬开始,服装革开始进入旺季,市场对低模量树脂的需求也随之加大。
为了使贝斯更柔软,也可适当加大DMF的用量,这样,可使泡孔变大,增加肉厚感。
非离子表面活性剂用量的增加,也可降低泡孔层的密度,使手感更加丰满。
但是.由于低模量树脂分子间的内聚力较弱,故凝固速度较慢,在生产中要有足够的时间使树脂凝固;另一方面,低模量树脂耐热性能较差,在设计工艺条件时也必需加以考虑。
用于制鞋而要求贝斯较硬时,应选择模量高的树脂,如100%模量在15.0MPa以上其至为24.0MPa的树脂,为了增加产品的硬度,使泡孔细密,贝斯表面褶纹细小.应适当加大阴离子表面活性剂的用量。
同时.DMF的用量也小于柔软贝斯中的用量,其目的都是为了使泡孔细密。
2、填料在单涂覆贝斯配方中,允许使用较多的填料,其中以木质粉应用最为普遍,其次是碳酸钙、硫酸钙、硅灰石、白炭黑等。
木质粉的微观形态呈树叶状空心结构,也有的木质粉呈短圆柱状。
因此,尽管木质粉的细度都在400目以上,但配制出的浆料仍显粗糙,原因就是因为木质粉并非球形结构,加之相对密度小,故在配制浆料时,增粘效果非常大。
而碳酸钙、硅灰石等呈球形结构、且相对密度大.它们的增粘效果很小。
木质粉的用量一般为树脂质量的20%左右.最高可达40%。
碳酸钙、硅灰石在配方中的用量一般不宜超过15%否则会导致浆料中的填料沉淀。
另外,不论填料是木质粉还是碳酸钙.若配制好的浆料存放时间超过24小时后都会发生不同程度的沉淀。
3、助剂助剂在湿法聚氨配合成革配方中占有重要地位,通常在配制浆料时添加两种表面活性剂,即阴离子表面活性剂和非离子表面活性别。
在一般的单涂覆贝斯配方中,阴离子表面活性剂用l份左右,非离子表面活性剂用0.5份左右即可。
但用于柔软的服装革和磨皮革时,非离子表面活性剂的用量可以适当加大,以便贝斯产生针状泡孔,手感柔软,磨皮后增加绒感。
4、DMF除了起到溶解及稀释聚氨酯树脂的作用外,还对贝斯的泡孔大小有较大影响。
DMF用量大时,贝斯的泡孔则大,DMF用量小时、贝斯的泡孔则小,而且,适当加大DMF的用量,还可以降低成本。
为了满足不同用户的使用要求,DMF的用量要合理,一般在单涂覆贝斯的配方中用量为65份左右,做服装革时也可增到100份以上。
5、着色剂着色剂的用量因色泽不同差异很大,在普通贝斯中一般用量为5—10份左右,但在磨皮革配方中.着色剂用量较大,高达25—30份。
着色剂用量小时.色泽不鲜艳.所以通常选用稳定性高、着色力强的着色剂,如有机颜料、高色素炭黑等。
由于湿法贝斯的生产工艺是在水中凝固,故着色剂在水中的溶解性是一项重要技术指标。
在水中溶解性大的着色剂不能用于湿法贝斯的生产,否则会影响贝斯的色泽及废水的回收处理。
粘度是配方设计时应考虑的一个重要指标。
贝斯所配制的浆料的粘度为7000—9000Pa•s,用于单涂覆粘度过高,则流动性差,过滤困难;粘度过低,容易透底,造成革面不平整等缺陷,而且还浪费浆料。
另外.应注意在设计磨皮革配方时,由于没有填料,且要控制上述要求的粘度,就必须选用本身具有较高粘度的树脂,才能达到工艺要求。
三、生产工艺技术单涂覆聚氨酯贝斯主要使用起毛布为底基,也可使用平织布和无纺布。
但用无纺布作底基时.首先必须用橡胶胶乳或其他高分子材料进行预处理.必要时,用磨皮机将表面打磨平整。
现在国内行场上,可以采购到经过橡胶胶乳浸渍处理的无纺布,其表面平整,弹性好,可以直接用于湿法聚氨酯单涂覆使用。
无论使用起毛布,还是平织布或无纺布为基布流程是一样的,所用配方也基本相同。
1、生产工艺流程简述:基布开卷经储布架进入浸水槽浸湿,再通过挤压辊将水挤出大部分,通过烫平轮一方面除去部分水分,同时将基布烫平(如果使用橡胶胶乳预处理过的无纺布基材,则可不必浸水),然后在涂料台上涂覆聚氨酯配合浆料,再进入凝固槽,使聚氨酯凝固成皮膜,而后再水洗、烘干、冷却卷成大卷贝斯。
2、生产工艺操作要点单涂覆贝斯所要求的浆料粘度较高,一般控制在7000—9000mPa.s,因此,配科时的加科顺序更为重要,以免影响产品质量。
一般在容器内先加入DMF而后加入木质粉,并用搅拌机充分搅拌,约10min左右,确保木质粉充分分散到DMF里。
若先把DMF和聚氨酯混合在一起搅拌,而后加入木质粉,则会使木质粉结团,不能充分地分散到树脂溶液中.即使过滤.结团的木质粉也极易堵塞过滤网,严重时造成浆料无法使用。
助剂添加的顺序对普通贝斯来说,影响要小一些。
一般在木质粉加入到DMF中分散均匀后加入即可,搅拌数分钟后停止搅拌.按配方要求加入聚氨酯树脂,用高速搅拌机搅拌20min后,测量浆料的粘度,使其在工艺要求范围内。
配制磨皮贝斯浆料时,助剂的加入顺序非常重要。
先在配料罐内加入阴离子表面活性剂(比如OT—70)与DMF搅拌至少5min后,再加入非离子表面活性剂(比如S—80),搅拌均匀后再加入聚氨酯树脂和色料,并搅拌至均匀一致为止。
如将OT—70与S—80同时加入,则无论浆料搅拌多长时间,生产的贝斯在磨皮时极易出现亮斑。
磨皮贝斯配方一般不使用木质粉,以免出现空壳等疵点。
生产磨皮贝斯时着色剂用量较大,着色剂的细度要求很高,若用色粉,则应事先将其用DMF溶解过滤后.再加入到浆中。
若使用色浆也应过滤后使用。
粘度是配料工序的一个重要工艺参数,一般单涂覆贝斯所用配合聚氨酯浆料的粘度为7000—9000 mPa.s.为了保证产品的稳定,浆料的粘度必须控制在一定的范围内。
而配制的浆料的粘度既与树脂的生产日期、批号、品种有关,又与木质粉等填料的性质有关。
为了使粘度稳定,有时DMF的用量就不能严格按配方执行。
相比较而言,维持粘度的稳定比维持配方中DMF用量的准确性更为重要。
配制的浆料粘度符合要求后,将之移至真空脱泡机内脱泡。
脱泡时,先进行低真空度脱泡,以避免脱泡初期涌起的大量气泡把浆料带入真主管道或真空泵中造成事故。
随着脱泡时间的加长,逐渐加大真空度,同时,用手电观察料面的气泡情况。
气泡脱除干净后,停止真空泵运转,完全卸压后出料。
脱泡时间一般为40min左右。
若浆料粘度偏高时,可适当延长脱泡时间。
脱泡后的浆料用60—100目的滤网过滤,装在不锈钢桶内备用。
配制好的浆料要及时加盖密封,尤其是在潮湿的夏季更要注意浆料的吸湿问题,否则料桶内上部分的料因吸水会在使用中引起涂层不均、产生坑点等缺陷。