化工工艺 加氢与脱氢过程
第三章第二节:氢化和脱氢

4
氢解示例
粉煤和重油氢解制轻质油
下午11时25分
化学工艺学
5
脱氢示例
① 乙烷脱氢制乙烯
C2H6 C2H4
+
H2
② 丁烷或丁烯脱氢制丁二烯
C4H10 or C4H8 H2C C H C H CH2
+
H2
③ 甲醇脱氢制甲醛
CH3OH HCHO
+
H2
④ 异丙醇脱氢制丙酮
CH3CHOHCH3
下午11时25分 化学工艺学
3.2氢化和脱氢 氢化和脱氢
一、基本概念 二、氢气来源 三、NH3合成 苯加H制环己烷 四、苯加 制环己烷
下午11时25分
化学工艺学
1
一、基本概念
氢化和脱氢的概念 氢化 脱氢
下午11时25分
化学工艺学
2
1.氢化和脱氢的概念 氢化和脱氢的概念
氢化:氢气和化合物间进行的化学反应。 氢化 加氢:氢气进入化合物使之还原或提高不饱和有 加氢 机物的饱和度。 氢解:在加氢的同时有机物分解,氢分子一部分 氢解 进入生成物大分子中,另一部分进入裂解所得小 分子中。 (氢解:破坏加氢,含N、S、O的有机化合物经 氢解变为烃、S化物,H2O、NH3等) 脱氢:从化合物除去氢原子的过程。 脱氢
பைடு நூலகம்
下午11时25分
化学工艺学
3
氢化示例
(1). H2、N2合成NH3 (2). CO、H2合成CH3OH (CO + 2 H 2 → CH 3 OH ) (3). 苯(苯酚)加氢生成环己烷(环己醇)
+ 3 H2
(4).硝基苯加氢生成苯胺
NO2 NH2
+ 3 H2
化工工艺加氢与脱氢过程

化工工艺加氢与脱氢过程化工工艺是为了提高产品质量和生产效率而进行的一系列生产过程。
其中,加氢和脱氢是常见的化工反应过程,主要用于原料的转化和产品的改性。
以下将对加氢和脱氢过程进行详细介绍。
一、加氢过程加氢是指在反应中向化合物中加入氢气的过程。
该过程通常涉及氢气与有机物之间的反应,目的是将有机物中的不饱和键加氢饱和,或是将有机物中的官能团与氢气反应生成其他目标化合物。
1.加氢工艺的原理加氢工艺主要依靠催化剂来实现。
通常使用的催化剂是金属催化剂,如铜、镍、铱等。
这些催化剂能够吸附氢气分子,并为氢气分子提供吸附位点,从而促使氢气与有机物发生反应。
在反应中,催化剂可以提供活化能,使加氢反应得以进行。
2.加氢反应的应用加氢反应在化工工艺中具有广泛的应用。
常见的应用有:加氢脱气、重整反应、加氢裂化和加氢脱硫等。
(1)加氢脱气:将氢气加入原料中,去除其中的气体成分,从而降低气体浓度,达到控制反应环境的目的。
(2)重整反应:通过加氢反应,将低碳烃转化为高碳烃,从而提高产物的价值。
(3)加氢裂化:将高碳烃加氢后进行裂化,得到较小分子量的产物。
这样做不仅能提高燃料的质量,也能减少环境污染。
(4)加氢脱硫:将含硫化合物加氢后,使其转化为易于处理和回收的化合物,从而达到脱除硫化物的目的。
二、脱氢过程脱氢是指在化学反应中去除化合物中的氢原子的过程。
通常涉及碳氢化合物与氧化剂反应,形成不饱和化合物或氧化产物。
1.脱氢工艺的原理脱氢工艺主要依靠高温、高压和催化剂来实现。
脱氢反应需要高温和高压来提供足够的能量,以克服反应的活化能。
同时,催化剂的存在可以加速反应速率,降低反应温度和压力等条件。
2.脱氢反应的应用脱氢反应在化工工艺中也具有广泛的应用。
常见的应用有:脱氢加氢反应、脱氢氧化反应和脱氢重排等。
(1)脱氢加氢反应:通过去除部分氢原子,将饱和化合物转化为不饱和化合物,从而改变产物的性质和用途。
(2)脱氢氧化反应:通过去除氢原子和加入氧原子,使得有机物部分氧化为醛、酮或羧酸,从而提高产品的氧化潜能。
加氢与脱氢过程
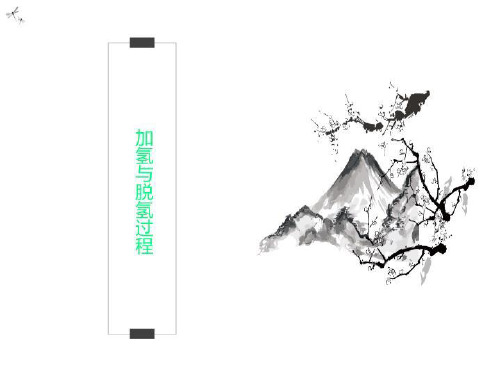
建成投产。
催化加氢
合成甲醇
1923年,BASF公司实现工业化生产,高压法 (T>380℃ ,P=30MPa)
1966年,ICI, 低压法 1972年,ICI, 中压法 1973年,Lurgi,低压法
6.4.1 合成甲醇的基本原理
― 1~25 10~50
6.4.3 合成甲醇工艺条件
(1)温度
a.可逆放热反应,存在最适宜温度。 b.因催化剂种类而异。
活性→最低进料温度 稳定性→最高出口温度
(2)压力
P ↑,r ↑
P=f (T),T↓ ,P↓ ;T↑ ,P ↑。
高压: 30 MPa ZnO-Cr2O3 中压:10 ~ 15MPa , CuO-ZnO-Al2O3 低压:5 ~10MPa,CuO-ZnO-Al2O3
H 2
活F e 性3 O 组4 分 H H 2 2 O
F e 2 O 3
3. 动力学
催化脱氢
催化剂 粒度的影响 催化剂粒度小,反应速率和选择性增加.
催化剂催的化颗剂粒的度颗对粒乙度苯对脱乙氢苯反脱应氢速选度择的性影的响影响
6.4 甲醇的合成
我国甲醇产销现状及分析
我国现有甲醇生产企业约150家。
2004年国内甲醇企业产量前五位的企业
(11)中国石油集团青海油田30万吨/年甲醇装置于2004年8 月在格尔木炼油厂开工建设。于2006年8月投产。
(12)重庆长寿85万吨/年甲醇装置,2007年上半年建成投产.
(13)上海焦化公司在宁夏建设30万吨/年煤基甲醇装置2006 年建成.
(14)中国石油集团公司玉门油田年产10万吨甲醇2006年一季 度投产。
4.3加氢与脱氢过程

②反应压力
A乙苯脱氢反应是体积增大的反应,降低压 力对反应有利。B反应温度随着压力的降低可 适当降低。如表,压力从0.1降到0.01MPa,达 到相同转化率所需要的温度降低100 ℃。
③水蒸气用量
工业上降低物料分压的方法有两种:
一,减压操作(高温减压不安全,环境气体容
易进入)
二,采用惰性气体做稀释剂。
物中加入适量的氧或空气,使上步生成的氢气转 化为水,使脱氢反应朝正向进行。
(1)反应原理
苯 甲苯 乙苯 焦油
(2)催化剂
A 活性组分 B 颗粒影响
(3) 工艺条件选择
①反应温度
乙苯脱氢是强吸热反应。故升温对脱氢 反应有利。 但是,副反应活化能高,高温有利于副 反应发生,同时由于烃类物质在高温下不稳 定,所以脱氢不能在太高温度下进行。 580-600℃。
采用水蒸气作为稀释剂来减压。
高温水蒸气作用:(1)惰性载体,降低反
应产物平衡分压,提高转化率和选择性。 (2)反应热载体,为反应提高热量。(3) 消炭剂,高温条件下与炭反应,避免催化剂 结焦。 绝热反应器 n(水蒸气)/ n(乙苯)=14:1 等温多管反应器为一半。
(4) 工艺流程 乙苯催化脱氢是吸热反应,供热方式
△ H0298 = - 90.8KJ/mol
副反应
选择催化剂,抑制副反应。
操作条件
(1)催化剂
催化剂的活性低
压力
操作温度高
加大
ZnO-Cr2O3,380 ~ 400℃,30MPa,活性低,有毒,
机械强度和耐热性能好,寿命长.
CuO-ZnO-Al2O3,230 ~ 270℃,5-10MPa,活性高,
热稳定性
化学稳定性:金属氧化物不被还原为金属
加氢操作规程

加氢操作规程第⼀章装置概况第⼀节装置简介⼀、装置概况:装置由中国⽯化集团公司北京设计院设计,以重油催化裂化装置所产的催化裂化柴油、顶循油,常减压装置⽣产的直馏柴油和焦化装置所产的焦化汽油、焦化柴油为原料,经过加氢精制反应,使产品满⾜新的质量标准要求。
新《轻柴油》质量标准要求柴油硫含量控制在0.2%以内,部分⼤城市车⽤柴油硫含量要求⼩于0.03%。
这将使我⼚的柴油出⼚⾯临严重困难,本装置可对催化柴油、直馏柴油、焦化汽柴油进⾏加氢精制,精制后的柴油硫含量降到0.03%以下,满⾜即将颁布的新《轻柴油》质量标准,缩⼩与国外柴油质量上的差距,增强市场竞争⼒。
该项⽬与50万吨/年延迟焦化装置共同占地⾯积为217m×103m即22351m2;装置建设在140万吨/年重油催化裂化装置东侧,与50万吨/年延迟焦化装置建在同⼀个界区内,共⽤⼀套公⽤⼯程系统和⼀个操作室。
本装置由反应(包括新氢压缩机、循环氢压缩机部分)、分馏两部分组成。
装置设计规模:120×104t/a。
⼆、设计特点:1、根据⼆次加⼯汽、柴油的烯烃含量较⾼,安定性差,胶质沉渣含量多的特点,本设计选⽤了三台⼗五组⾃动反冲洗过滤器,除去由上游装置带来的悬浮在原料油中的颗粒。
2、为防⽌原料油与空⽓接触氧化⽣成聚合物,减少原料油在换热器、加热炉炉管和反应器中结焦,原料缓冲罐采⽤氮⽓或燃料⽓保护。
3、反应器为热壁结构,内设两个催化剂床层,床层间设冷氢盘。
4、采⽤国内成熟的炉前混氢⼯艺,原料油与氢⽓在换热器前混合,可提⾼换热器的换热效果,减少进料加热炉炉管结焦,同时可避免流体分配不均,具有流速快、停留时间短的特点。
5、为防⽌铵盐析出堵塞管路与设备,在反应产物空冷器和反应产物/原料油换热器的上游均设有注⽔点。
6、分馏部分采⽤蒸汽直接汽提,脱除H2S、NH3,并切割出付产品⽯脑油。
7、反应进料加热炉采⽤双室⽔平管箱式炉,炉底共设有32台附墙式扁平焰⽓体燃烧器,⼯艺介质经对流室进⼊辐射室加热⾄⼯艺所需温度,并设有⼀套烟⽓余热回收系统,加热炉总体热效率可达90%。
加氢与脱氢过程
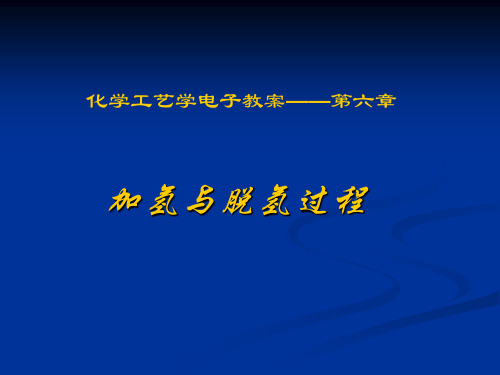
脱氢催化剂应满足下列要求:首先是具有良 好的活性和选择性,能够尽量在较低的温度条 件下进行反应。其次催化剂的热稳定性好,能 耐较高的操作温度而不失活。第三是化学稳定 性好,金属氧化物在氢气的存在下不被还原成 金属态,同时在大量的水蒸气下催化剂颗粒能 长期运转而不粉碎,保持足够的机械强度。第 四是有良好的抗结焦性能和易再生性能。
二、催化脱氢反应的一般规律
3 脱氢反应动力学 脱氢反应的速率控制步骤是表面化学反应,都可按双位吸附理 论来描述其动力学方程,其速率方程可用双曲模型来表示。
铁系催化剂脱氢反应时催化剂颗粒大小对反应速率和选择性都 有影响,图6-2是催化剂颗粒度反应速率的影响,而图6-3是催化剂 颗粒度对选择性的影响。
化学工艺学电子教案——第六章
加氢与脱氢过程
第六章 加氢与脱氢过程
内容提要:
加氢与脱氢反应的一般规律;乙苯和苯乙烯 的性质、用途、主要生产方法和工艺流程; 乙苯脱氢制苯乙烯的主副反应、操作参数 等。
第一节 概 述
通常催化加氢系指有机化合物中一个或几个不炮和的 官能团在催化剂的作用下与氢气加成。H2和N2反应生成 合成氨以及CO和H2反应合成甲醇及烃类亦为加氢反应。 而在催化剂作用下,烃类脱氢生成两种或两种以上的新物 质称为催化脱氢。催化加氢和催化脱氢在有机化工生产中 得到广泛应用。如合成氨、合成甲醇、丁二烯的制取,苯 乙烯的制取等都是极为重要的化工产品。催化加氢反应分 为多相催化加氢和均相催化加氢两种,相比之下,多相催 化加氢的选择性较低,反应方向不易控制,而均相催化加 氢采用可溶性催化剂,选择性较高,反应条件较温和。
一、加氢反应的类型
1 不饱和炔烃、烯烃重键的加氢
2 芳烃加氢
一、加氢反应的类型
加氢基本工艺流程

加氢基本工艺流程
《加氢基本工艺流程》
加氢是一种重要的化工工艺,用于将不饱和化合物转化为饱和化合物,主要用于石油加工、炼油、化工生产等领域。
加氢基本工艺流程是指在加氢反应装置中,通过一系列的操作步骤将原料化合物加氢转化为目标产物的过程。
首先,原料化合物经过预处理,去除其中的硫、氮、氧等杂质物质,避免对反应催化剂的影响。
然后,原料进入加氢反应器,与催化剂接触进行反应。
在反应器内,通常会施加高温高压条件,以促进加氢反应的进行。
催化剂通常是以金属或金属氧化物为主,如镍、钼、钴等。
反应结束后,产生的产物需要进行分离和提纯。
通常通过升温升压脱气以及减压分馏等操作来分离产物和副产物。
对产物进行提纯,可以通过吸附剂吸附、蒸馏、结晶、结晶析出等工艺进行。
最终得到高纯度的目标产物。
加氢基本工艺流程中,需要考虑的关键因素包括温度、压力、催化剂的选择与再生、反应器结构和操作、分离技术等方面。
这些因素的合理运用和优化设计,可以提高加氢反应的产率和产物纯度,降低生产成本,保证生产过程的安全和稳定。
总的来说,加氢基本工艺流程是一项复杂而重要的化工工艺,在石油加工、炼油以及化工生产中具有广泛的应用。
随着技术
的进步和发展,加氢工艺的研究和应用将继续向更高效、更环保、更节能方向发展。
第3章_催化加氢与脱氢

●甲醇是仅次于三烯和三苯的重要基础有机化工原料, 广泛用于有机合成、染料、合成纤维、合成橡胶、涂料 和国防等工业。甲醇大量用于生产甲醛和对苯二甲酸二 甲酯; ●以甲醇为原料经羰基化反应直接合成醋酸已经工业化; ●近年来,随着技术的发展的能源结构的改变,甲醇又开 辟了许多新的用途,是合成人工蛋白的重要原料; ●以甲醇为原料生产烯烃和汽油已实现工业化。因此,甲 醇的生产具有十分重要的意义。
进塔气体的组成有关 20000 50.1
ZnO-Cr2O3: 20000-40000h-1 30000 41.5 26.1 -1 40000 CuO-ZnO-Al2O3: 10000h 32.2 28.4
●增加空速在一定程度上能够增加甲醇产量 ●增加空速有利于反应热的移出,防止催化剂过热 ●空速太高:转化率降低,循环气量增加,从而增加能量消耗;
8.杂环化合物加氢
9.甲苯加氢制苯
(2)加氢精制
裂解气中乙烯和丙烯的精制
※从烃类裂解气分离得到的乙烯和丙烯中含有少
量乙炔、丙炔和两二烯等有害杂质,可利用催化 加氢方法,使炔烃和二烯烃进行选择加氢,转化 为相应的烯烃而除去。
(3)精制氢气
氢气中含有一氧化碳杂质,在加氢反应时能使催化 剂中毒。可通过催化加氢反应,使一氧化碳转化为 甲烷,达到精制的目的。其反应式如下:
催化剂活化
低压合成甲醇的催化剂,其化学组成是CuO-ZnOAl2O3 ,只有还原成金属铜才有活性。 还原过程为活化:氮气流升温、还原
CuO-ZnO-Al2O3
还原性气体 0.4MPa,99%N2 缓慢地升温, 20℃/h
催化剂
CuO-ZnO-Al2O3
160~170℃
化工工艺学完美打印版

第一章绪论1化工生产的起始原料主要有矿物资源,生物资源,空气和水四类。
2化学工业中,设备投资所占比例最大的是产品提纯设备。
3一个化学生产过程,可分为原料预处理,化学反应,产品分离与精制三个步骤。
4天然气主要由甲烷,乙烷,丙烷和丁烷组成。
第二章化学工艺基础1用原油炼制燃料油,一次加工时,原油首先经过的加工设备是常压塔。
2常压蒸馏和减压蒸馏是对石油的一次加工。
3汽油品质最重要的指标是辛烷值。
4在石油催化裂化中,正碳离子中最容易断裂的键是β键。
5石油一次加工过程的主要任务是将原油分离成不同沸点范围的馏分,所用的设备是常压蒸馏塔,减压蒸馏塔。
6常,减压蒸馏塔获得的产品都是混合物。
7原油经过初馏塔,从初馏塔塔顶蒸出的轻汽油,也称石脑油。
8原油在蒸馏前,一般经过脱盐脱水处理。
第三章烃类热裂解1石油中所含烃类有烷烃,环烷烃和芳香烃。
2石油裂解制取乙烯等所用的反应器是管式裂解炉。
3按顺序深冷分离法分离裂解气,裂解气首先进入的设备(塔)是甲烷塔。
4烃类热裂解的后续深冷分离工序之前,要进行裂解气的净化,主要包括:脱除酸性气体,脱水和脱炔三步。
5工业上控制石油深度的措施是控制停留时间。
6裂解气分离的工艺采用用深冷分离法,其中甲烷塔技术含量最高。
7裂解原料的含氢量越高,裂解产物中乙烯收率越高。
第四章芳烃转化过程1工业上已用于苯烷基化工艺的催化剂是酸性催化剂。
第五章合成气的生产过程1合成气的CO变换的主要目的是使CO变成CO2便于除去。
2通过CO变换可产生更多氢气和降低CO含量.3干法脱硫中,能把大部分有机硫转化为无机硫的方法是钴—钼加氢法。
4合成气净化过程中的脱碳是指去除CO25为了脱除合成气中极少的残渣,最适合的脱硫法措施是氯化锌法。
第六章加氢与脱氢过程1可使合成氨催化剂永久性中毒的是二氧化硫。
2N2与H2合成氨所用的催化剂是Fe3O4。
3用于氨合成的熔铁催化剂,必须升温还原活化。
4不论是脱氢反应或是断链反应,都是热效应很大的吸热反应。
催化剂制备原理 第五六七章 加氢、脱氢、氧化催化剂的制备

腈的还原
OH
O
Pd
Ni, Pt
Rh, Ru OH
苯酚加氢 OH
OH
OH
OH
OH
+ 3 H2 phenol
+ 2 H2
+
+
cyclohex-1-enol cyclohex-2-enol cyclohex-3-enol
O OH
+ 2 H2
+ H2
OH
+ 2 H2O
cyclohexanol
cyclohexanone
Regioselective hydrogenation of p-phenylphenol (p-PP) to p-cyclohexylphenol (p-CP) was performed over 10 wt.% Pd/C catalyst in THF solvent. The selectivity of pCP was up to 92.3% at 413 K under 3.5 MPa with 100% conversion of p-PP. The desired product could be easily separated from the reaction mixture by washing with aqueous NaOH following extraction by toluene.
化工工艺学第四章4.3催化加氢与脱氢过程

+
CH4ห้องสมุดไป่ตู้
+
H2O
260~300℃ 3.0MPa
甲烷化反应
CH4
+
CO2
+
4 H2
Ni
Al2O3
2 H2O
(4)精制苯 从焦炉气或煤焦油中分离得到的苯,含有硫化 物杂质,通过催化加氢,可以比较干净地将它 们脱除掉。例如噻吩的脱除,其反应如下式。
4.3.3 CO加氢合成甲醇
4.3.2 催化加氢、脱氢反应的一般规律
• 二、催化脱氢反应的一般规律 • 1、热力学分析 • ①温度的影响 • 与烃类加氢反应相反,烃类脱氢反应是吸热反应, ⊿H>0,其吸热量与烃类的结构有关。
T↑ , KP ↑,xe ↑
4.3.2 催化加氢、脱氢反应的一般规律
• ②压力的影响 • 脱氢反应,分子数增多,P↓ ,Xe↑ • 工业上高温下减压操作不安全。 加稀释剂,常用水 • 表4-34是压力与脱氢反应转化率及其反应温度的关系。
• 研究结果表明:无论是丁烷、丁烯、乙苯或二乙 苯,其脱氢反应的速率控制步骤都是表面化学反应, 都可按双位吸附理论来描述其动力学速率方程,其动 力学速率方程可用双曲模型来表示。
正 逆
(动力学项)(推动) 力 2 (吸附项)
催化加氢在石油化工工业中的应用
催化加氢用于合成有机产品外,还用于精制过程。 (1)合成有机产品
温度对不同单一反应速率的影响
△H0 > 0
不可逆反应:T ↑, k1↑,反应速率增大 可逆吸热反应: T ↑, k1↑,KP ↑,反应速率增大 可逆放热反应: T ↑, k1↑,KP ↓ ,反应速率
△H0 < 0
第五章 加氢脱氢过程-ppt课件
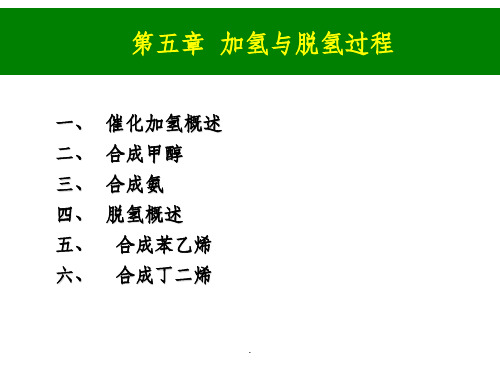
国外:天然气80%,重油、渣油10%,石脑油5%,煤2 %。国内:以煤、重油为主
.
4. 操作条件
(1)催化剂及温度、压力 ZnO-Cr2O3,380 ~ 400℃,30MPa,活性低,有毒,机械强度和耐热
性能好,寿命长. CuO-ZnO-Al2O3,230 ~ 270℃,5-10MPa,活性高,容易S、 As 、
优点:可调节蒸汽压力控制
壳程温度,径向温度均匀, 循环气量小,节能
缺点:由于管内外传热温差 小,所需传热面大;催化 剂装在数千根管内,触媒 装填量只占反应器总体积 的30%;投资大。
(3)材质
因氢蚀及Fe(CO)5,选 用Ni-Cr钢,
1Cr18Ni9Ti
.
6. 工艺流程
(1)造气
合成气为了延长甲醇合成催化剂的使用寿命,提高 粗甲醇的质量,必须对原料气进行净化处理,净化的任务 是清除油、水、尘粒、羰基铁、氯化物及硫化物等,其中 特别重要的是清除硫化物及油。
C H C H C H 2 = C H 2 C H 3 C H 3
.
3. 氢的来源
(1)电解法制氢
• 多采用铁为阴极面,镍为阳极面的串联电解槽 (外形似压滤机)来电解苛性钾或苛性钠的水 溶液。阳极出氧气,阴极出氢气。该方法成本 较高,但产品纯度大,可直接生产99.7%以上 纯度的氢气。这种纯度的氢气常供:①电子、 仪器、仪表工业中用的还原剂、保护气和对坡 莫合金的热处理等,②粉末冶金工业中制钨、 钼、硬质合金等用的还原剂,③制取多晶硅、 锗等半导体原材料,④油脂氢化,⑤双氢内冷 发电机中的冷却气等。
ZnO-Cr2O3: 380 ~ 400℃ ,30 MPa(高压) CuO-ZnO-Al2O3: 230 ~ 270℃ ,5 ~10MPa(低压) CuO-ZnO-Al2O3 :230 ~350 ℃,10 ~15MPa(中压) 为何无低温高压法?
炼油厂采用的主流石油加工工艺——催化加氢工艺详解

3、反应空速
空速的大小反映了反应器的处理能力和反应时间。空速越大,装置的 处理能力越大,但原料与催化剂的接触时间则越短,相应的反应时间 也就越短。因此,空速的大小最终影响原料的转化率和反应的深度。
1、加氢处理催化剂 加氢处理催化剂中常用的加氢活性组分有铂、钯、镍等金属和钨、钼、 镍、钴的混合硫化物,它们对各类反应的活性顺序为: 加氢饱和 Pt,Pb﹥Ni﹥W-Ni﹥Mo-Ni﹥Mo-Co﹥W-Co 加氢脱硫 Mo-Co﹥Mo-Ni﹥W-Ni﹥W-Co 加氢脱氮 W-Ni﹥Mo-Ni﹥Mo-Co﹥W-Co 加氢活性主要取决于金属的种类、含量、化合物状态及在载体表面的 分散度等。 活性氧化铝是加氢处理催化剂常用的载体。
目前炼油厂采用的加氢过程主要分为两类:一类是加氢处理,一 类是加氢裂化。
用这种技术的目的在于脱除油品中的硫、氮、氧及金属等杂质, 同时还使烯烃、二烯烃、芳烃和稠环芳烃选择加氢饱和,从而改善原 料的品质和产品的使用性能。此外,加氢裂化的目的在于将大分子裂 化为小分子以提高轻质油收率,同时还除去一些杂志。其特点是轻质 油收率高,产品饱和度高,杂质含量少。 作用机理 吸附在催化剂上的氢分子生成活泼的氢原子与被催化剂削弱了键的 烯、炔加成。烯烃在铂、钯或镍等金属催化剂的存在下,可以与氢加 成而生成烷烃。加氢过程可分为两大类:
4、催化剂再生 国内加氢装置一般采用催化剂器内再生方式,有蒸汽-空气烧焦法和 氮气-空气烧焦法两种。 再生过程包括以下两个阶段: ①再生前的预处理 在反应器烧焦之前,需先进行催化剂脱油与加热炉清焦。 ②烧焦再生 通过逐步提高烧焦温度和降低氧浓度,并控制烧焦过程分三个阶段完 成。
加氢工艺规程
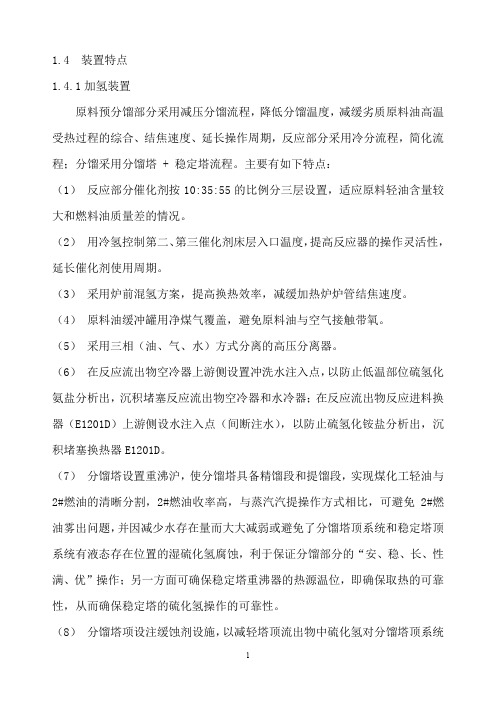
1.4 装置特点1.4.1加氢装置原料预分馏部分采用减压分馏流程,降低分馏温度,减缓劣质原料油高温受热过程的综合、结焦速度、延长操作周期,反应部分采用冷分流程,简化流程;分馏采用分馏塔 + 稳定塔流程。
主要有如下特点:(1)反应部分催化剂按10:35:55的比例分三层设置,适应原料轻油含量较大和燃料油质量差的情况。
(2)用冷氢控制第二、第三催化剂床层入口温度,提高反应器的操作灵活性,延长催化剂使用周期。
(3)采用炉前混氢方案,提高换热效率,减缓加热炉炉管结焦速度。
(4)原料油缓冲罐用净煤气覆盖,避免原料油与空气接触带氧。
(5)采用三相(油、气、水)方式分离的高压分离器。
(6)在反应流出物空冷器上游侧设置冲洗水注入点,以防止低温部位硫氢化氨盐分析出,沉积堵塞反应流出物空冷器和水冷器;在反应流出物反应进料换器(E1201D)上游侧设水注入点(间断注水),以防止硫氢化铵盐分析出,沉积堵塞换热器E1201D。
(7)分馏塔设置重沸沪,使分馏塔具备精馏段和提馏段,实现煤化工轻油与2#燃油的清晰分割,2#燃油收率高,与蒸汽汽提操作方式相比,可避免2#燃油雾出问题,并因减少水存在量而大大减弱或避免了分馏塔顶系统和稳定塔顶系统有液态存在位置的湿硫化氢腐蚀,利于保证分馏部分的“安、稳、长、性满、优”操作;另一方面可确保稳定塔重沸器的热源温位,即确保取热的可靠性,从而确保稳定塔的硫化氢操作的可靠性。
(8)分馏塔项设注缓蚀剂设施,以减轻塔顶流出物中硫化氢对分馏塔顶系统的腐蚀。
(9)分馏塔顶油进入稳定塔,脱除硫化氢和戊烷以下轻组分,塔底得到脱除硫化氢的稳定油,塔顶设注缓蚀剂设施,以减轻塔顶流出物中硫化氢对稳定塔系统的腐蚀。
(10)2#燃油产品先作稳定塔重沸器热源,然后作低分油热源,充分回收其热量。
(11)新氢及循环联合压缩机采用电动往复式,设一台备机。
(12)催化剂预硫化采用液相硫化方法。
(湿法)(13)催化剂再生方式为器外再生。
环己酮的生产工艺及技术进展

环己酮的生产工艺及技术进展2.1 环己酮传统生产工艺世界上传统的环己酮生产工艺主要有苯酚加氢法、苯加氢氧化法、环己烷液相氧化法,生产环己酮的原材料是苯和氢。
2.1.1 苯酚加氢法苯酚合成环己酮工艺是最早应用于工业化生产环己酮的工艺, 该工艺早期分为两步: 第一步苯酚加氢为环己醇, 第二步环己醇脱氢生成环己酮:20世纪70年代开发成功了一步加氢法合成环己酮的新工艺。
苯酚一步加氢有气相和液相两种方式。
工业上主要是采用气相法,该工艺采用3--5个反应器串联,温度为140--170℃、压力为0.1MPa,收率可达95%。
苯酚加氢法生产的环己酮质量较好,安全性高, 但因为苯酚价格昂贵, 并使用了贵金属催化剂, 使环己酮的生产成本较高, 因此该工艺的应用受到了很大的限制。
2.1.2 苯加氢氧化法苯加氢氧化法工艺中苯与氢气在镍催化剂存在下, 在120--180℃下加氢反应生成环己烷, 环己烷于空气中在150--160℃、0.908Mpa下发生氧化反应生成环己醇和环己酮的混合物:混合物经分离后得环己酮, 副产品环己醇在锌、钙催化剂存在下脱氢生成环己酮:2.1.3 环己烷液相氧化法目前90%以上的环己酮是采用环己烷氧化法生产的。
工业生产中环己烷液相氧化法有两条氧化工艺路线,一种为催化氧化工艺,另一种为无催化氧化工艺。
……2.2 现有工艺技术的改进针对上述环己酮生产工艺存在的不足,许多生产企业与研究部门对环己酮生产技术进行了多方面的改进。
<1)延长开车周期。
钴盐法的优点是反应条件温和、温度低、压力低、停留时间短,对设备要求不严格。
但钴盐法最大的难题是反应过程中生成的羧酸钴盐残留在设备及管道上,结渣堵塞管道和阀门。
为了解决此难题,各国都进行了大量的研究。
工艺方面,氧化后未反应的环己烷被分离后循环使用,在氧化前的水用共沸蒸馏等方法除去,避免了反应器的结渣。
反应器方面,捷克斯洛伐克专利提出环己烷液相氧化采用卧式反应器,以垂直挡板将其分割成几个反应器。
化学工艺学知识点(氢化、脱氢、电解、无机化工反应单元工艺)终75
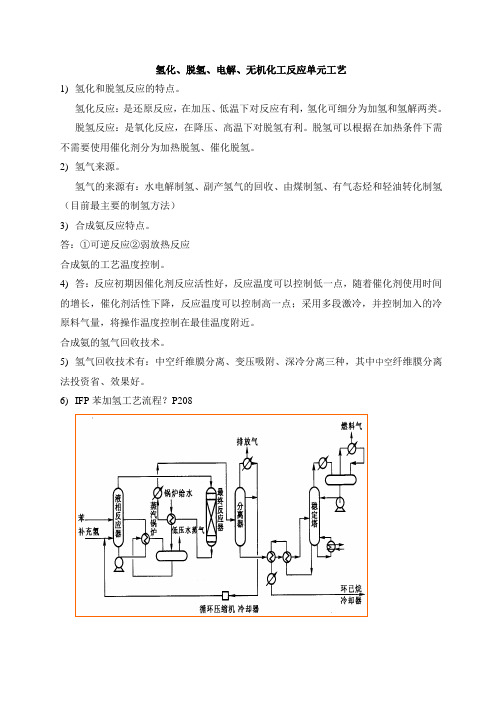
氢化、脱氢、电解、无机化工反应单元工艺1)氢化和脱氢反应的特点。
氢化反应:是还原反应,在加压、低温下对反应有利,氢化可细分为加氢和氢解两类。
脱氢反应:是氧化反应,在降压、高温下对脱氢有利。
脱氢可以根据在加热条件下需不需要使用催化剂分为加热脱氢、催化脱氢。
2)氢气来源。
氢气的来源有:水电解制氢、副产氢气的回收、由煤制氢、有气态烃和轻油转化制氢(目前最主要的制氢方法)3)合成氨反应特点。
答:①可逆反应②弱放热反应合成氨的工艺温度控制。
4)答:反应初期因催化剂反应活性好,反应温度可以控制低一点,随着催化剂使用时间的增长,催化剂活性下降,反应温度可以控制高一点;采用多段激冷,并控制加入的冷原料气量,将操作温度控制在最佳温度附近。
合成氨的氢气回收技术。
5)氢气回收技术有:中空纤维膜分离、变压吸附、深冷分离三种,其中中空纤维膜分离法投资省、效果好。
6)IFP苯加氢工艺流程?P2087)苯加氢制备环己烷过程中,原料精制的目的是什么?P205目的:避免催化剂中毒;甲烷化产生的水分,超过反应温度下在环己烷的溶解度,会导致催化剂聚结和失活。
氢气中的的硫太高,需用碱液吸收精制。
8)电解的定义。
P230电流通过电解质溶液或熔融电解质时,在两个电极上所引起的化学变化。
9)隔膜法电解食盐水的原理及电极反应、产物。
P236原理:利用电解槽内隔膜将阳极产物(氯气)和阴极(氢气和烧碱)分开的电解生产工艺10)离子交换膜法电解食盐水过程,食盐水二次精制的原因。
P242在膜的微孔中挂着磺酸基上的Na+交换下来,后者通过微孔,进入阴极电解液,而带负电的Cl和OH-因受磺酸根基团的静电排斥排斥作用,很难通过微孔。
精制盐水含有较多的多价阳离子,由于他们很容易占有多个磺酸基团,增加了精制盐水中的Na+进行离子交换以及渗过膜微孔的难度。
因此,需要二次精制处理。
11)典型的可通过电解获得的产品有哪些?NaOH、Cl2 、H2、己二腈、葵二酸、12)化学矿的固相化学加工过程及其分类。
金属催化的加氢和脱氢反应
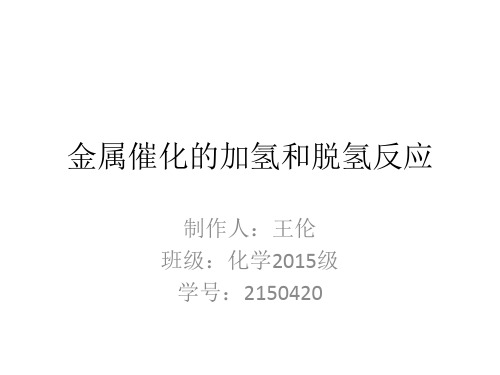
参考文献
[1] Highly Enantioselective Hydrogenation of β-Ketoenamides with the Rh-Zhang Phos Catalyst.Kexuan Huang,Xiaowei Zhang,Huiling Geng,Sheng-kun Li,and Xumu Zhang. ACS Catal. 2012, 2, 1343−1345
O
O
O
Zn-Hg,浓盐酸
O O
Pt/C
上述过程在常压下就可进行,why???
菲的芳构化同上,但萘环和蔻环的芳构化所用的催化剂为Se
Se
三、金属催化加氢的最新研究进展
该种催化剂是基于Grubbs催化剂 开发的一种廉价金属的催化剂
NHC卡宾,用于催化烯烃的复分解反应 单线态卡宾 Renyuan Pony Yu, Jonathan M. Darmon, Jordan M. Hoyt, Grant W. Margulieux,ZoeR.Turner,and Paul J. Chirik.ACS Catal. 2012, 2, 1760−1764
PF6
OH
Ir
N 2.5mol%
H+
CH3 CH2Cl2,H2(1atm),r.t
CH3
64:1
Crabtree,JOC,1986(51)2655
选择性满足不对称合成的要求
OH
H CH3
除上述铱催化剂外,还有如下一系列的催化剂
均相金属催化的机理举例:
三、金属催化的脱氢反应
工业上,脱氢反应中重要的过程主要是芳构化。 芳构化是指含六元环的脂环族化合物在Pt、Pd、Ni等 催化剂的存在下加热脱氢生成芳香族化合物的过程。一般 的芳构化的过程都是伴随重整过程的。重要的重整过程就 是Pt重整(或称为临氢重整),下图为异庚烷通过临氢重 整与芳构化制备甲苯的过程。 另外在傅-克酰基化反应合成稠环芳烃时也有脱氢过 程,这个过程的催化剂一般是Pt/C。
- 1、下载文档前请自行甄别文档内容的完整性,平台不提供额外的编辑、内容补充、找答案等附加服务。
- 2、"仅部分预览"的文档,不可在线预览部分如存在完整性等问题,可反馈申请退款(可完整预览的文档不适用该条件!)。
- 3、如文档侵犯您的权益,请联系客服反馈,我们会尽快为您处理(人工客服工作时间:9:00-18:30)。
★对反应选择性影响 T↑,S↓ ,因为副反应的活化能大。如:
H2
C + CH4
◆压力的影响(与反应物级数有关)
□ 级数负值: P加大,r下降。 □ 0级: P与反应速度无关。 □ 0~1级: P加大,r加大。 □ 对于液相加氢: 高压增加氢溶解度, r增大
◆H2用量的影响
□ H2适度过量,反应速度加快; □ H2过量,产物浓度降低,有时选择性也降低。 □ 考虑抑制结焦,传热,能耗,
■UOP/Hydro、ExxonMobil的MTO技术: 流化床反应器,甲醇转化率99.8%,丙烯产率45%, 乙烯产率34%,丁烯产率13%
■鲁奇(Lurgi )的MTP技术: 甲醇制单一丙烯新工艺,采用中间冷却的绝热固定床反应 器,使用南方化学公司提供的专用沸石催化剂。
甲醇与水蒸气转化制氢
甲醇与水蒸气在一定的温度、压力条件下通过催化剂, 在催 化剂的作用下, 发生甲醇裂解反应和一氧化碳的变换反应, 生成氢和二氧化碳, 这是一个多组份、 多反应的气固催化 反应系统。转化为 75%H2和 24%CO2、极少量的CO、CH4
氢解(hydrogenolysis)
6.1.1 加氢反应类型
●不饱和炔烃、烯烃的加氢 ★烯烃加氢,乙烯反应速度最快。
C原子数↑ ,加氢速度↓ 。 ★同C数有取代基的加氢速度慢, ★二烯烃无取代基双键先加氢。
R-CH=CH2 +H2
RCH2CH3
R-CH=CH-CH-CH2 + 2H2
RCH2CH2CH2CH3
+ H2
+ 2H2
●芳烃加氢
苯核加氢、苯核外的双键加氢、或二者兼有
●含氧化合物加氢
醛、酮、酸、酯
加氢
醇
加氢能力:醛>酮,酸>酯;醇和酚加氢困难
●含氮化合物加氢 -CN,-NO2 加氢 -NH2
●氢解
指加氢过程有裂解,产生小分子混合物。酸、酯、 醇、烷基芳烃加氢时可产生氢解。
COOC2H5cat.●甲醇的用途①甲醇+酸 → 酯+水 ②甲醇+氧气→甲醛 ③甲醇+NH3 → 甲胺、二甲胺、三甲胺 ④甲醇 →醋酸(羰基合成) ⑤甲醇合成人造蛋白是很好的禽畜饲料。 ⑥合成汽油(美国Mobil公司,ZSM-5催化剂,发现了甲醇制汽油
(Methanol to Gasoline,MTG)反应), 1979年新西兰政府利用天然气建 成了全球首套MTG装置
低温对反应有利
◆压力对平衡常数的影响
分子减少反应,高压对反应有利
◆副反应
2CO+4H2 → (CH3)2O+H2O CO+3H2 → CH4+H2O 4CO+8H2 → C4H9OH+3H2O CO2+H2 → CO+H2O
选择催化剂,抑制副反应。
●合成甲醇反应动力学
◆甲醇合成的反应机理:
(1)CO直接加氢生成,CO2通过逆变换生成CO再合成 甲醇
2010年我国甲醇产能将达4500万吨/年的,甚至有一位化 工分析师算出在未来几年我国甲醇产能将达6400万吨/年。 相对中国本土市场对甲醇的消化能力,这个数字难免让人恐 惧。
2012年甲醇产能达到5149.1万吨,
2013年有效产能为5590万吨,
2013年全年进口能在490-500万吨
●甲醇的合成
②因反应放热,反应热应及时移出,否则副反应增 加,活性降低。严格控制温度,及时有效地移走
反应热是合成塔设计、操作之关键。
●压力:
加压有利于反应平衡。压力过大,会使能耗增加, 设备材质要求提高,受反应温度限制。
Zn-Cr催化剂:30MPa ; Cu-Zn-Al催化剂:5-10MPa
●H2与CO比:
●合成甲醇反应热力学 ◆化学反应
主反应:
CO+2H2 CH3OH(g)+90.8kJ/mol
CO2+3H2
CH3OH(g)+H2O(g)+ 58.6kJ/mol
反应热随温度和压力变化而变化,
反应温度越低,压力越高,反应热越大
★反应温度低、压力高, 放热大
★高压,同时采用高温 ★低压,同时采用低温 ★20MPa,300-400℃, 反
Cu-Zn-Al
●金属硫化物催化剂
MoS2、WS2、Ni2S3等。 抗毒性好,但活性低,需高温反应。
●金属络合物催化剂
多为贵重金属Ru、Rh、Pd等的络合物。 优点:活性高,选择性好,反应条件缓和。 缺点:反应为均相进行,催化剂分离难。
马来酸一苯乙烯一钯络合物(简称 (PMS·Pd) 硝基化合物,芳香族醛酮的催化加氢反应
(2)CO2直接加氢生成,CO通过变换生成CO2再合成 甲醇
(3)CO和CO2直接加氢
◆活性中心的吸附类型
■ Cu0是活性中心 ■ Cu+是活性中心 ■ Cu0- Cu+是活性中心 ■ CO与CO2的吸附中心与Cu有关 ■ H2与H2O的吸附中心与ZnO有关
●合成甲醇催化剂
◆Zn-Cr催化剂: 机械强度好,耐热性好,寿命2-3年, 用于高温、高 压法合成甲醇,380-400℃,30MPa。 ◆Cu-Zn-Cr催化剂或Cu-Zn-Al: 活性高,低温性能良好,副产物量少,用于中低压法 合成甲醇。易中毒,寿命为1-2年, 230-270℃,510MPa。S、As中毒,精脱硫 使用前需活化,将氧化铜还原为金属铜或低价铜
共同存在: r炔烃> r二烯烃> r烯烃> r芳烃
□含氧化合物:
醛﹥酮;酯﹥酸;醇与酚较慢,需较高温度
□有机硫化物 R-S-S-R>R-SH>R-S-R>C4H8S>C4H4S
6.1.3 催化加氢催化剂
●金属催化剂
活性金属:Ni、Pd、Pt 常用载体:氧化铝、硅胶、硅藻土。 优点:活性高,低温性能好。 缺点:易中毒,原料杂质要求高。 如 S、As、P、N、Cl等。
第三节 甲醇的合成
●概述 ●合成甲醇的基本原理 ●合成甲醇工艺条件 ●合成甲醇工艺流程 ●合成甲醇主要设备----反应器
6.3.1 合成甲醇概述 ●甲醇性质
工业甲醇是无色、类似酒味的挥发性液体。相对密 度0.7914;熔点-93.9℃;沸点65℃;折光率 1.3288;动力粘度(120℃时)0.56cp;膨胀系数 (20℃时)0.001031;蒸汽压12.8KPa;蒸汽密度 1.1kg/m3. 能与水、乙醇、醚、苯酮类和其它有机溶剂混合; 能与多种化合物形成共沸物。
7、合成MTBE
甲醇制烯烃技术(MTO/MTP) 技术
■Mobil公司以ZSM-5催化剂为基础,最早研究甲醇转化为乙烯 和其它低碳烯烃的工作。 ■UOP和Norsk Hydro合作开发的以UOP MTO-100(SAPO-34)为 催化剂的UOP/Hydro的MTO工艺。 ■中科院大连化物所开发的合成气经二甲醚制低碳烯烃的工艺 路线(SDTO)具独创性,与传统合成气经甲醇制低碳烯烃的 MTO相比较,CO转化率高,达90%以上,建设投资和操作费用节 省50%~80%。采用D0123催化剂时产品以乙烯为主,当使用 D0300催化剂是产品以丙烯为主。
学平衡成为关键因素。如CO加氢制甲醇。
◆压力影响
分子减少反应,加压有利。
◆氢气与原料的用量比
A +H2
B
KN
yB yA yH2
KN
yH2
yB yA
X
H2↑,优点:X↑,有利于移走反应热。 缺点:分离、循环量大,能耗大
●动力学分析 ◆反应机理:不同烃的加氢反应机理不同
★多位吸附 苯在催化剂表面发生多位吸附,然后加氢得产物
+ 4 H2
COOC2H5
CH2OH CH2OH + 2 C2H5OH
●选择性加氢
◆同一化合物有2个可加氢官能团如:
CH=CH2 Cu Ni
C2H5 C2H5
◆催化体系中有多个加氢物质:个别或几个物质加氢 如:裂解汽油加氢
◆炔烃或二烯烃加氢:加氢深度不同
CH CH
CH2 = CH2
CH3CH3
6.1.2 催化加氢反应的一般规律 ●热力学分析(催化加氢皆为放热反应)
H2适当过量
◆溶剂的影响
常用乙醇、甲醇、环己烷等。 作用:
①作稀释剂,带走反应热。 ②原料或产物为固体时,溶于液体溶剂,
利于反应进行。 因溶剂对加氢反应速度有影响,对选择性也有影响, 故应选择好溶剂。萘加氢
◆加氢物质结构的影响(空间位阻,影响吸附) □烯烃加氢
□芳烃
□不同类型烃类加氢
单独加氢: r烯烃>r炔烃 ; r烯烃>r芳烃, r二烯烃>r烯烃
应热变化小,易于控制
◆温度对平衡常数的影响
高温高压,非理想气体,逸度表示Kf只与温度有关
K f exp(13.1652 9263.26 / T 5.92839ln T 0.352404102T 0.102264104T 2 0.769446108T 3 0.238531011T 4 ) 0.1013252
CO过量能引起羰基铁在催化剂上积聚,使催化剂失 活;副反应增加。故常用氢气过量的反应。 氢气过量 ①抑制Fe(CO)5在催化剂表面沉积而造成的失活, ②导热,③ 加快反应速度 工业上 Zn-Cr2O3催化剂时,H2与CO比为4.5左右; 铜基催化剂,H2与CO比为2.2- 3.0。
●空速:
合成甲醇空速大小能影响选择性和转化率,直接关 联到催化剂的生产能力和单位时间的反应放热量。 Zn-Cr催化剂:20000-40000h-1 Cu-Zn-Al催化剂:1000h-1
◆温度影响
( d ln K P dT
)P
-H 0
RT 2
△H<0,∴T↑,KP↓