钢铁生产中的脱磷技术ppt(84张)
转炉脱磷造渣工艺课件(PPT 42张)

东大冶金
3. 氧气转炉各期脱磷
www.emti .cn , 110004
3.1 吹炼初期
吹炼初期。熔池温度较低,这是有利于去磷的 ①(FeO) 高。可以大量生成3FeO· P2O5,从而为生成 一个方面。但是更重要的,是在熔池温度逐渐提高的 3CaO· P2O5创造了必不可少的前提。 过程中,抓紧时机尽快在前期造成具有一定碱度和氧 ②(FeO)有利于石灰的迅速熔化。有效地提高前期渣的碱度, 化铁较高、流动性好的炉渣。只有这样才具备了从铁 为把3CaO· P2O5生成之后,稳定在炉渣内创造了必要的条件。 水中快速脱磷的充分条件。一般说来,前期渣的脱磷 ③有利于泡沫渣的生成,使铁水和炉渣更好地乳化。因而,增 效率是很高的, 60~80%。 加铁水和炉渣的接触表面,当然有利于脱磷。 前期渣中的(FeO)含量对脱磷反应的进行有重要 作用,这是因为:
37生产中脱磷实例73转炉冶炼工艺的优化通过对正常铁水与低硅铁水炉渣熔化过程和各反应期炉渣组成的分析认为在现有装备条件下解决低硅铁水冶炼首先要保证前期有快速足够的熔剂来熔化第一批石灰完成前期脱磷任务
EMTI
ShenyangNEUMetallurgicalTechnologyCorporationLimited
东大冶金
www.emti .cn , 110004
2.3 温度的影响 脱磷反应是放热反应: 3FeO+P2O5=3(FeO)· P2O5 3CaO+P2O5=3(CaO)· P2O5 △H=-384KJ/mol △H=-678KJ/mol
故低温对去磷有利,实际炼钢过程中,为保 证去磷应抓住前期早化渣,低温去磷,中期温 度不过高,终点应采用下限温度出钢。
转炉冶炼低磷钢的控制技术PPT课件

FeO 35
FetO 42.3
CaF2 5
CaF2 19.2
CaCl2 5
-
FetO 39
CaF2 11
Na2CO3 11
FetO 62.2
CaF2 4
CaCl2 3.3
2019版一轮复习物理课件
实验 规模 290t 混铁车 50t,250t 铁水包
15t 实验炉
100t 铁水包
加入量, kg/t铁水
气搅拌。 • 根据所用容器不同,脱磷工艺可分为2种: 一种是在盛铁水的铁水包或鱼雷罐车中进行脱磷。如日本新日铁 ORP,住友的SARP预处理工艺。我国的太钢二炼钢厂20世纪80年 代引进住友主体设备建成铁水罐喷吹三脱工艺。
/08:40:44
2019版一轮复习物理课件
另一种是在转炉内进行铁水预处理。转炉内脱磷具有石灰消耗少 , 渣量少,脱磷效果好,复吹搅拌强,处理时间短,热损少以及 锰回收率增高等优点,而且也解决了敞口罐和鱼雷罐车脱磷中的 泡沫渣问题。 神户制钢的H炉、住友金属的SRP、新日铁的LD-ORP,NKK福 山少渣冶炼技术,新日铁的MURC法等都是采用的这种转炉内脱 磷的预处理工艺。
( 2)
/08:40:44
2019版一轮复习物理课件
• 氧分压的高低决定了脱磷产物的类别。下图给出1823K时 41%CaO-Al2O3系炉渣,渣中磷浓度与气相氧分压的关系。
/08:40:44
1823K时,CaO-Al2O3渣系中磷浓度与氧分压的关渣成分变化对炉渣脱磷能力的影响,对 于炼钢过程,脱磷反应可以写为:
/08:40:44
2019版一轮复习物理课件
4 转炉冶炼脱磷
• 4.1 转炉铁水预处理脱磷 • 转炉炼钢过程的脱磷是一个氧化脱磷过程,保证转炉内的有效脱磷
钢铁生产中的脱磷

❖ 磷是表面活性杂质,易在晶界上偏析引起裂纹。 ❖ 磷在晶界的偏析度随回火温度的升高而降低;
磷在晶界偏析对钢材的危害 ❖ 随磷含量的增加而上升; ❖ 随着晶界中磷含量的增加,钢材脆性转变温度线性提高; ❖ 提高钢中Ti含量可以减轻甚至消除晶界上磷的偏析,抑制磷的危害。
钢铁生产中的脱磷
北京 2007.7
❖ 磷在钢中的危害
❖ 脱磷反应
提纲 ❖ 转炉脱磷工艺
❖ 铁水预处理脱磷工艺
❖ 钢水炉外脱磷工艺
❖ 杂质与钢水的纯净度
❖ 磷对钢材韧性的危害
磷❖ 磷在对钢钢材低中温冲的击危韧性害的危害 ❖ 磷在晶界偏析对钢材的危害
❖ 磷对钢材断裂韧性的危害
❖ 不同钢种对磷含量的要求
质杂量。质ห้องสมุดไป่ตู้质元元素素对钢对材的钢性材能影性响主能要包的括强影度、响塑性 、耐蚀性等,如表所示。
下两表给出钢中不同杂质元素对钢材性能的影响。从表中可以看出 ,磷的危害是:
杂质元素❖对❖降低降钢钢低材钢材的材热的性变韧形性能性 的影响
❖ 降低钢材的浇铸性 同时,磷可以提高钢材的强度,提高钢材的耐磨性和抗腐蚀能力。
• 低温
• 高碱度渣
❖炼钢过程的脱磷反应在渣—金属间进 行,渣中(CaO)高的碱性操作可以脱磷
。据此脱磷反应可以按下式进行: ❖(1)分子论形式的表达式
脱磷反应热力学 ❖2[P]+5(FeO)+3(CaO)=(3CaO·P2O5)+5 Fe(l) ❖2[P]+5(FeO)+4(CaO)=(4CaO·P2O5)+5
❖顶吹超音速纯氧射流 ❖吹炼后期熔池搅拌减弱 ❖后期渣—钢反应偏离平衡 ❖热效率高
钢水脱磷工艺

钢水脱磷工艺磷在钢中是以[Fe3P]或[Fe2P]形式存在,为方便起见,均用[P]表示。
炼钢过程的脱磷反应是在金属液与熔渣界面进行的,首先是[P]被氧化成(P2O5),而后与(CaO )结合成稳定的磷酸钙,其反应式可表示为:2[P]+5(FeO)+4(CaO)=(4CaO ·P2O5)+5[Fe]2[P]+5(FeO)+3(CaO)=(3CaO ·P2O5)+5[Fe]从CaO-P2O5相图中可以看出3CaO ·P2O5为最稳定,4CaO ·P2O5次之。
可以认为存在于碱性渣中的应是3CaO ·P2O5。
由于3CaO ·P2O5和4CaO ·P2O5的反应生成自由能值很相近,在热力学分析时,有两种磷酸盐得出的结论基本上是一致的。
在实验室条件下,达到平衡时的反应产物通常是4CaO ·P2O5。
脱磷反应平衡常数可表示为:4455225.45.4.).(.).(.][%).(22CaO CaO FeO FeO P O P CaO O P CaO N N f P N γγγ=552.4..52CaO FeO P O P CaO P a a a a K = 9.4296600][%][%1lg 1lg 5252-=⋅=⋅T O P a a O P1,1524==⋅CaO O P CaO a a 17.2939060lg 525252-=⋅⋅Ta a N O P O P O P γ390.92078002.1lg 52+-⋅∑=TN A j j O P γ2252.2317833132026a g e a n a j j C O M O F tO N O M O C F P O A N N N N N N N N =+++++-∑j N 表示的是炉渣中某成分的摩尔分数。
将[%P],[%O]分别代替P a 、O a ,可得52lg 56.385984002.1][%]lg[%52O P j j N TN A O P ++-⋅∑=⋅)lg(%5.2)lg(%70.2422350][%)(%lg Fe CaO TP P ++-=24)(%>CaOLP 主要取决于熔渣成分和温度。
金属冶炼中的脱硫与脱磷技术
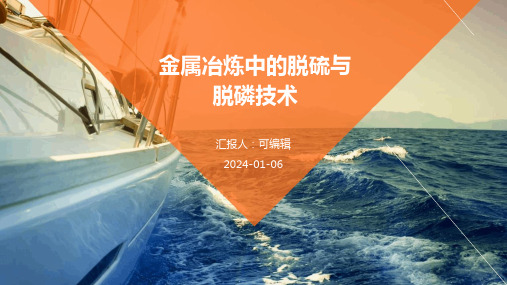
常用方法
生物浸出法和生物吸附法。
优点
环保友好,操作简便,成本低廉。
02
01
缺点
微生物培养条件较为苛刻,且对某些金属冶 炼过程的应用尚在研究阶段。
04
03
04 脱硫与脱磷技术的比较与选择
技术比较
脱硫技术
主要采用物理或化学方法,将金 属矿石中的硫化物去除,常用的
技术包括浮选法、焙烧法等。
脱磷技术
通常采用化学方法,通过添加适 当的还原剂或酸,将矿石中的磷 氧化物还原或溶解,再将其去除 ,常用的技术包括还原焙烧法、
重力脱硫
利用矿物密度不同,通过重选将 硫化物与其它矿物分离,如摇床 、溜槽等。
化学脱硫技术
焙烧脱硫
通过高温氧化作用将硫化物转化为硫 酸盐或硫氧化物,再用水或酸进行浸 出,从而达到脱硫的目的。
化学沉淀法
向含硫溶液中加入适当的沉淀剂,使 硫化物沉淀下来,从而实现脱硫。
生物脱硫技术
生物浸出法
利用微生物的氧化作用将硫化物转化为可溶性的硫酸盐,再通过洗涤、过滤等 手段去除。
生物堆浸法
将矿石堆积在特定的场地,通过自然界的微生物氧化作用将硫化物转化为硫酸 盐,再用水冲洗去除。
03 金属冶炼中的脱磷技术
氧化脱磷技术
原理
通过向熔融金属中加入 氧化剂,将磷氧化成磷 氧化物,从而降低金属 中的磷含量。
常用方法
熔融氧化法和炉渣处理 法。
优点
操作简单,适用于大多 数金属冶炼过程。
02
对金属材料性能的影响
硫和磷的存在会影响金属材料的机械性能,如硬度、韧 性和耐腐蚀性等。的存在会导致金属表面出现斑点、锈蚀等现象, 影响金属制品的外观质量。
硫与磷的来源
脱磷
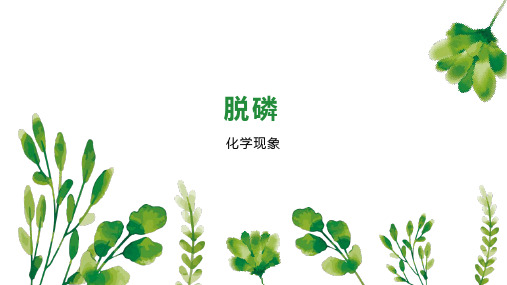
化学现象
01 变化规律
03 炼钢反应
目录
02 反应方程式
磷在钢中的存在形式通常认为是以磷化物的形式存在。 在液态钢中,一般以〔P〕表示,磷使钢产生“冷脆”。 所以脱磷反应常应用于炼钢中,为了除去有害杂质P。
变化规律
在吹炼的最初阶段(约4分钟),由于硅、锰与氧的结合力大,所以要等硅锰氧化到较低时磷才开始氧化,而 且磷的氧化速度也不大,约0.007-0.016%/分,此时脱碳速度也不大,吹炼中期,硅锰已基本氧化,此时进入碳、 磷氧化阶段,磷的氧化速度约0.0013-0.021%/分,一般吹炼到一定时间,磷可达到规格之下,而且由于炉内温度 还不太高,所以只要化渣高R、高FeO、大渣量、低温,增大渣量的目的是稀释(4CaO·P2O5)的浓度。
另:造粘度较大的泡沫渣有利于脱磷,但粘度不宜过大。在一般情况下当炉渣碱度2.5~3.0,(FeO)控制在 15-20%脱磷最佳。为实现炼钢中的脱磷目的,以FeO为氧化剂,以CaO为磷氧化产物的稳定剂,在酸性炉渣条件下 是不可能进行脱磷操作的。
实验研究证明,磷在钢凝固过程中偏析聚集在晶界处,很少量的磷,例如0.01%(100ppm)即可使钢呈现低温 脆性。冶炼普通钢要求将磷降到0.030%~0.040%,而低温用钢如寒冷地带钻井平台用钢、液化气体储存和输送用 钢等要求含磷低到0.002%~0.003%(即20~30ppm)。因此,脱磷是炼钢过程的主要任务之一。
感谢观看
炼钢反应
dephosphorization in steelmaking
脱除钢液中有害杂质磷的物理化学过程。在高炉连续铸钢炼铁时,原料中的磷几乎全部还原到生铁中,随着 铁矿石磷含量的不同,生铁中的磷可达0.1%~1.0%,特殊的可高达2.0%以上。铁合金中同理也含有相当多磷。磷 使钢材在低温下变脆,即产生“冷脆”现象。
钢铁的磷化PPT课件
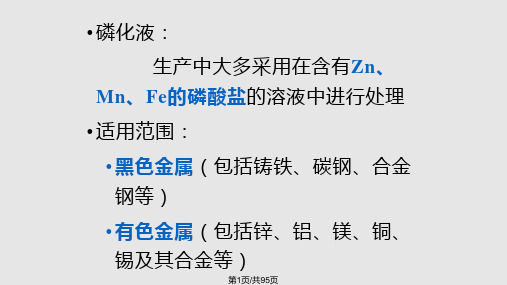
• 伪转化型磷化:膜中主要阳离子(锌、锰、铬)由溶液提供的磷化
第24页/共95页
基本组成: • 碱金属或重金属磷酸二氢盐 Me(H2PO4)2 (Me为Zn2+、Mn2+、Fe2+ 、Ca2+等) • 氧化性促进剂 • 游离磷酸
第25页/共95页
• 微阳极区反应: Fe - 2e- → Fe2+ Fe+ 2ZnPO4 - → FeZn2(PO4)2↓ +2e- ( Zn(H2PO4)2 ⇌ ZnPO4— +2H+ ) • 微阴极区反应: 2H+ + 2e → H2↑
• 避免H+浓度太高 • 避免促进剂氧化能力过强
第35页/共95页
条件: →
• 基体材料 • 工件的表面状态 • 磷化液组成 • 工艺条件
磷化膜:
• 种类 • 厚度 • 表面密度 • 结构 • 颜色
第36页/共95页
分类 锌系 锌钙系
磷化液主要 成分
磷化膜主要组成
Zn(H2PO4)2
Zn3(PO4)2·4H2O Zn2Fe(PO4)2·4H2O
第26页/共95页
Edward Ghali Laval University Canada
磷化膜成膜的电位-时间曲线示意图
Crrosion Science, 1972, 12 (7): 583-594
第27页/共95页
• A段:开始的瞬间,电势快速负移,对 应基体金属的溶解 Me + 2H3PO4→Me(H2PO4)2 + H2↑
• 精密钢管拉拔,磷化膜的质量为 4~10 g/m2
• 钢铁工件冷挤压成型,磷化膜的质
第212页/共95页
脱磷工艺

1.3脱磷工艺钢水炉外脱磷的同时要氧化钢中的合金元素,因此脱磷一般在合金化以前进行。
目前,钢水脱磷的主要方法有:出钢过程中的加脱磷剂脱磷,利用出钢过程中的强烈搅拌以及高的氧分压,冲混脱磷;顶渣加喷粉脱磷,通过吹气使得渣金能够充分混合,达到有效脱磷;出钢后直接将脱磷剂加入钢包中脱磷等方式。
脱磷后要将脱磷渣扒除(以防止回磷和合金元素的损失)再合金化,LF升温,脱硫,RH脱气等操作。
其巾日本NKK采用钢包中喷吹转炉渣和偏硅酸钠脱磷,生产成品钢w(P)为20×10-6“的钢,如图所示。
图5 日本超低磷钢生产的工艺流程1.3.1脱磷冶炼工艺的发展国家正在大力发展高炉炉铁水预处理技术和精炼钢水炉技术后,分享最初的冶炼到炼钢炉完成任务的一部分,炼钢炉的功能越来越多地集中在一个简单的关碳变暖。
当初的承诺变暖的炼钢炉,脱硅,脱硫,脱磷,脱氧,脱碳合金,调整提炼的成分和温度的任务是在时间和空间的分离,分别执行不同的炼油设备线。
解放的炼钢炉,钢决策过程分解成更多更细的子进程和亚单位,转换器的效率大大提高。
钢铁生产过程中磷的去除主要是在铁水预处理,转炉或电炉氧化期,二次精炼三个阶段进行,三个阶段脱磷的特点如表1.1所示表 1.1 各工序脱磷特点比较低磷钢生产分低磷钢[%,P<0.01和超低磷钢[%,P <0.003生产两个过程。
低磷钢生生产能力主要依靠铁水脱磷预处理和氧气转炉炼钢去除钢中磷100410%×下面。
超低磷钢铁冶炼两种方式:其一是在欧洲和北美的崛起,没有铁水预处理转炉冶炼低温钢钢包精炼后,高碱度,高氧化残留物的使用激起脱磷,然后改变包,LF炉加热,在RH的再利用。
使用这种方法,60至70钢水磷含量410%×左右。
另一种方法是在日本的崛起,完整的铁水预处理,在铁水中的磷含量降低到0.02%左右,因此,钢水有不少于20410%×钢的磷含量,然后进行二次精炼处理,以非常低的硫,磷的生产,H,O,钢的N-水平。
转炉脱磷造渣工艺课件
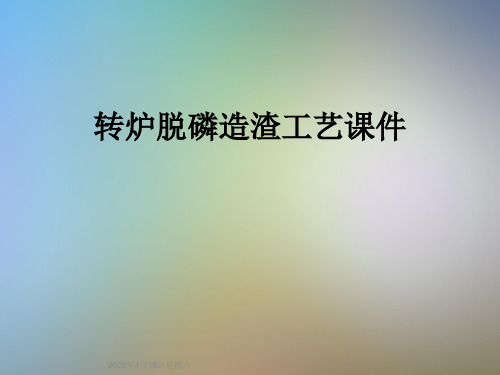
2.3 温度的影响
脱磷反应是放热反应:
3FeO+P2O5=3(FeOO5
△H=-384KJ/mol △H=-678KJ/mol
故低温对去磷有利,实际炼钢过程中,为保
证去磷应抓住前期早化渣,低温去磷,中期温度 不过高,终点应采用下限温度出钢。
2. 影响脱磷的因素分析 2.4 渣量的影响
综氧上气所转述炉,初为期了,含使硅脱量磷高反,应吹进炼初行期完脱全磷,时必间要后移, 需将的铁热水力含学硅条量件降至是0:.10炉%渣~0的.15碱%度时,较P大才(能R=大3量~4氧)化。 铁水,中碳氧的化影铁响含:量较高((FeO)≈15~20%),熔
池温度合适(不过高),适当的渣量。
在氧气转炉冶炼过程中,主要的反应是2[C]+O2=2CO ,在冶炼初期,T<1470℃,磷可以优先氧化,当T> 1470℃,碳开始大量氧化,若想磷与碳同时氧化或优先氧 化应优先形成碱性氧化渣。
去P的基本条件:高(FeO)、高(CaO) 高碱度,大渣量和较低温度及良好搅拌的 动力学条件。
2. 影响脱磷的因素分析
2.1熔渣碱度的影响
从CaO-然Fe而O,-SCiOaO2-的含 P2O5系渣量同过含高磷将铁使液炉的渣变平黏 衡试验及,生这产并研不究利中于均脱可磷。 发现,增熔加渣渣碱中度C的aO影或响石还可 灰 量的或用使量钢以碱会中由度提[P图C]高a降2O.P2低/2S得O,iO到5的如2证越含图明高,, 2.1所示。磷(分图配2比.1越是大。 1600℃条件下的情况。如 果温度高于1600℃,则曲
增加渣量可以降低钢中[P],因渣的增加意味着P2O5 浓度的稀释,从而使Ca3P2O8的含量也相应地减小,所 以对脱磷有利。但是渣量大会使铁损和热损失增大。一 般渣量≈10~15%,在保证去磷条件下,采用最小渣量。
钢铁生产中的脱磷工艺教材课件

高碳钢种对碳含量要求较高,脱磷过程中需控制好温度和 氧势,避免过度氧化,同时保证脱磷效果。
不锈钢种脱磷
不锈钢种对磷、硫含量及夹杂物要求严格,需采用特殊脱 磷剂和工艺,结合后期精炼处理,达到超低磷、硫含量及 纯净度要求。
脱磷工艺的节能减排技术
01
02
03
高效脱磷剂
研发高效脱磷剂,降低脱 磷剂消耗,减少副产物的 生成,降低能耗和生产成 本。
02
脱磷工艺原理
Chapter
化学脱磷反应
01
02
03
化学脱磷反应是利用碱 性氧化物与磷的化合物 之间的反应,将钢液中
的磷去除的过程。
在高温下,碱金属氧化 物与磷的化合物反应生 成磷酸盐和氧气,从而 将磷从钢液中脱去。
常用的碱性氧化物包括 氧化钙、氧化镁等,它 们与磷的反应可表示为 :3CaO + P2O5 ->
环保要求提高
随着环保意识的增强,钢铁企业需要采取更加环保的脱磷工艺,减少对
环境的污染。
新型脱磷剂的开发与应用
复合脱磷剂的研究
针对高磷铁水处理难题,研究开发新型复合脱磷剂,以提高脱磷 效率和降低脱磷成本。
高效脱磷剂的应用
将新型高效脱磷剂应用于实际生产中,提高脱磷效果和降低能耗。
脱磷剂的再生与循环利用
05
脱磷工艺的挑战与未来发展
Chapter
高磷铁水的处理难题
01
高磷铁水成分复杂
高磷铁水中的磷含量较高,同时含有其他多种杂质元素,这增加了脱磷
的难度。
02
高效脱磷技术缺乏
目前,钢铁生产中常用的脱磷技术主要是机械搅拌法和喷吹法,但这些
技术在实际应用中存在一定的局限性,难以满足高磷铁水处理的需求。
钢铁冶金原理第五章 钢铁冶金原理-脱磷

5 4 K P a FeO aCaO
脱磷反应的热力学分析:
H 384kJ mol1 , T K P LP (1)脱磷反应为强放热反应, 故低温有利于脱磷;但在低温下石灰难于熔化,因而应 保持较高的脱磷温度,通过改善其他条件使 LP 。
(2)炉渣成分的影响:
23CaO P2O5 3SiO2 32CaO SiO2 P2O5 2P2 O5 10C 4P 10CO
23CaO P2O5 3SiO2 10C 32CaO SiO2 4P 10CO g
P是钢液中的有害元素,在炼钢过程中,尽可能除去P。P溶于 铁液中放出大量的热,形成 Fe2P、 Fe3P,说明 P、 Fe 原子有较 强的亲和力,在固态铁中形成置换固溶体。 P 在 γ-Fe 中的溶解 度0.5%,在α-Fe中的溶解度2.8%。P会使钢的强度、硬度增大, 塑性、韧性变坏,钢水凝固时, P原子富集在晶界处,使钢产 生冷脆,从室温降到0℃以下时,产生脆裂。
km ks L P,则(P O )在渣中的传质为限制性环节。 2 5
%PLP %P2O5 vP k s
加速脱磷的因素:
(1)迅速造成高碱度、高氧化性、低粘度的熔渣,使脱磷的热力
学条件改善,从而使LP升高。使
%FeO
%CaO
适当。
(2)增大km、ks与钢渣的界面积A/Vm,氧气顶吹转炉形成的熔
§5.2.1 炼钢过程中P的氧化反应 (1)4P 5O2 2P2O5g (2)2P 5O P2O5g
G 0 2651859 890.34TJ mol1 G 0 742032 532.71 TJ mol1
(3)2P 8FeO 3FeO P2O5 5Fe G 0 413575 245.46TJ mol1
转炉脱磷少渣炼钢工艺技术发展与现状概述(PPT 92页).ppt

高(CaO),脱磷产物 (3FeO•P2O5)
(4CaO• P2O5)。
高(FeO),一般经常采用的脱磷剂如铁矿石、烧结矿、氧化铁皮、 转炉炉渣等,要求其(FeO)含量不低于20%。
低温度,温度为1250℃~1400℃对脱磷有利。
4
国外转炉脱磷少渣炼钢技术的发展与现状
第二部分 国外转炉脱磷少渣炼钢技术的
15Biblioteka 国外转炉脱磷少渣炼钢技术的发展与现状
转炉铁水脱磷工艺技术的开发
由于在鱼雷车和铁水包中脱磷存在一些问题,许多厂家纷纷研究 在转炉内进行脱磷的预处理方法,最早的是日本神户制钢神户厂 采用的H炉,随后住友金属、新日铁、日本钢管也纷纷研究开发 并采用了这一技术。
1983年,神户制钢神户厂H炉脱磷脱硫工艺。 1987年,住友金属鹿岛厂SRP工艺。 1989年,新日铁名古屋厂LD-ORP工艺。 1995年,NKK福山厂LD-NRP工艺。 其它转炉铁水脱磷工艺。
9
国外转炉脱磷少渣炼钢技术的发展与现状
SARP工艺(Sumitomo Alkati Refining Process)
住友金属进行可用于工业性生产的脱磷工艺的研究始于1970年。 到1982年5月住友金属鹿岛厂建立了SARP系统,其处理能力为 2000t/d铁水。
既在铁水沟中脱硅,又在混铁车内进行脱硅,最终的硅含量大约 为0.1%。然后在混铁车内采用喷吹苏打灰进行脱磷、脱硫,渣子 用真空吸渣法排出。
由于转炉采用小渣量操作工艺,有助于生产费用的降低。
表2-1 脱磷剂组成及粒度
组成
生石灰 氧化铁屑 萤石
氯化钙
粒度
%
30~40
50~55
5~10
0~5
第六章 钢铁冶金原理脱磷

∆G 0 = −338600 + 142.05 J ⋅ mol −1
lg K 1873 = 8.46
∆G 0 = −343000 + 143.35 J ⋅ mol −1
2[P ] + 5[O ] + 3(CaO ) = (3CaO ⋅ P2 O5 )
lg K = 74970 − 31.33 T
,
lg K 1873 = 8.70
3CaO ⋅ P2O5
:1983K的异分熔点化合物。因而高温下
4CaO ⋅ P2 O5
更稳定,一般认为碱性炼钢渣下的脱磷产物为
3CaO ⋅ P2O5 ,有时也可写成
4CaO ⋅ P2 O5
,因它们的稳定性接近。
2[P ] + 5[O ] + 4(CaO ) = (4CaO ⋅ P2 O5 )
lg K = 74000 − 31.05 T
(3)熔渣适当泡沫化,加强对熔池搅拌时vP增加。如果保持适当的枪 位,增加底吹或侧吹气体进行搅拌等。
k s = (0.47 ~ 4.3) × 10 −3 cm ⋅ s −1;
k m = (3.3 ~ 10.9 ) × 10 −3 cm ⋅ s −1
因此可以认为渣中(PO43-)或(P2O5)的传质为过程的限制性环节。 当认为P在渣及金属液中的传质为混合限制环节时,据双膜理论分析脱磷 的速率为: (% P2 O5 ) k m ⋅ LP d [% P ] v[ P ] = − = × (% P ) − (k m / k S ) + LP dτ LP 式中:
2(3CaO ⋅ P2 O5 ) + 3SiO2 = 3(2CaO ⋅ SiO2 ) + P2 O5
脱磷转炉脱磷PPT课件

第10页/共30页
§3 转炉脱磷工艺
二、吹炼过程中磷含量的变化规律 1.枪位变化对脱磷反应的影响
相反,如果枪位控制得较低,碳氧反应激烈,脱 碳速度快,易使渣中的(FeO)含量不足,并且易 出现炉渣返干现象,这对脱磷极为不利。
合成稳定的磷酸钙: 2[P]+5(FeO)+4(CaO)=(4CaO·P2O5)+5[Fe] 2[P]+5(FeO)+3(CaO)=(3CaO·P2O5)+5[Fe] 因此铁水预脱磷的条件同样是:高碱度、高氧化铁 含量(氧化性)、适当的低温。
第22页/共30页
§3 转炉脱磷工艺
四、铁水预脱磷
1.脱磷剂
第12页/共30页
§3 转炉脱磷工艺
二、吹炼过程中磷含量的变化规律 2.吹炼过程中磷含量的变化规律及分析 A 吹炼初期
吹炼初期熔池温度较低,这对于脱磷是一个有利 条件,如果能保证迅速形成高碱度、高氧化铁含量、 流动性良好的炉渣,可以使脱磷过程快速进行。
因此,该阶段应适当提高枪位,使渣中氧化铁含 量达到18%~25%,可使脱磷速度迅速提高。
第15页/共30页
§3 转炉脱磷工艺
二、吹炼过程中磷含量的变化规律 2.吹炼过程中磷含量的变化规律及分析 C 吹炼后期
此阶段钢液中磷含量已比较低,熔池温度已升高, 脱磷速度较低。 综合上述分析,在化渣良好,碱度适当的情况下,转 炉吹炼初期、吹炼中期及吹炼后期脱磷速度的变化规 律为:较慢——快——慢。
目前常用的脱磷剂有苏打系和石灰系脱磷剂。
- 1、下载文档前请自行甄别文档内容的完整性,平台不提供额外的编辑、内容补充、找答案等附加服务。
- 2、"仅部分预览"的文档,不可在线预览部分如存在完整性等问题,可反馈申请退款(可完整预览的文档不适用该条件!)。
- 3、如文档侵犯您的权益,请联系客服反馈,我们会尽快为您处理(人工客服工作时间:9:00-18:30)。
北京 2007.7
提纲
❖ 磷在钢中的危害 ❖ 脱磷反应 ❖ 转炉脱磷工艺 ❖ 铁水预处理脱磷工艺 ❖ 钢水炉外脱磷工艺
磷在钢中的危害
❖ 杂质与钢水的纯净度 ❖ 磷对钢材韧性的危害 ❖ 磷对钢材低温冲击韧性的危害 ❖ 磷在晶界偏析对钢材的危害 ❖ 磷对钢材断裂韧性的危害 ❖ 不同钢种对磷含量的要求
碳素钢和低合金钢对夹杂物含量和尺寸的要求
钢 铁 生 产 中 的脱磷 技术(P PT84页 )
钢 铁 生 产 中 的脱磷 技术(P PT84页 )
特殊钢对夹杂物含量和尺寸的要求
钢 铁 生 产 中 的脱磷 技术(P PT84页 )
钢 铁 生 产 中 的脱磷 技术(P PT84页 )
优质管线钢对杂质元素的要求
磷对钢材低温冲击韧性的危害
❖磷直接影响钢的脆性转变温度,例如: STE690钢,当磷含量从0.017%降到 0.006%时,转变温度下降25K。因此, 寒冷地区用的高强度钢材对磷含量要求特 别严格。
磷在晶界偏析对钢材的危害
❖ 磷是表面活性杂质,易在晶界上偏析引起裂纹。 ❖ 磷在晶界的偏析度随回火温度的升高而降低; ❖ 随磷含量的增加而上升; ❖ 随着晶界中磷含量的增加,钢材脆性转变温度线性提高; ❖ 提高钢中Ti含量可以减轻甚至消除晶界上磷的偏析,抑制磷的危害。
❖
KP=(aP2O5)/([aP]2[aO]5) ❖ lgKP=36850/T-29.07 ❖渣中磷的活度 aP2o5= P2o5NP2o5
杂质与钢水的纯净度
❖ 杂质元素是钢材发生各种裂纹和脆性的根源,提高钢的洁 净度对改善材质和提高加工性能极为有效。 ❖ 表给出钢中杂质对钢材造成的缺陷及对性能的影响。
磷作为表面活性杂质易在晶界偏析,造成低温脆性,降低 钢材韧性。
杂质元素对钢材性能的影响
❖钢中杂质元素即使在很低的浓度下,因偏析和在晶界 析出或在原子间游动,可以改变钢材性能,降低钢材的 质量。杂质元素对钢材的性能影响主要包括强度、塑性、 耐蚀性等,如表所示。
钢 铁 生 产 中 的脱磷 技术(P PT84页 )
钢 铁 生 产 中 的脱磷 技术(P PT84页 )
脱磷反应
❖ 钢中磷的来源 ❖ 磷在钢中的溶解度 ❖ 脱磷反应热力学 ❖ 炉渣的脱磷能力 ❖ 渣—钢间磷分配系数的计算方法 ❖ 两种脱磷工艺的比较 ❖ 脱磷反应动力学
钢 铁 生 产 中 的脱磷 技术(P PT84页 )
钢 铁 生 产 中 的脱磷 技术(P PT84页 )
钢 铁 生 产 中 的脱磷 技术(P PT84页 )
磷在钢中的溶解度
❖炼钢炉内脱磷反应属于氧化反应,在渣—钢界面 上反应生成的P2O5与渣中CaO结合,生成磷酸钙。 因此,炼钢脱磷反应又是渣—钢反应。钢中磷的溶 解度可以用气体—金属间反应,由下式求出:
钢 铁 生 产 中 的脱磷 技术(P PT84页 )
钢中磷的来源
❖钢中的磷主要来源于矿石。 在高炉炼铁过程中,矿石 中的磷被还原到铁水中。 铁水中的磷含量不仅决定 于矿石的含磷量,也决定 于高炉渣的组成。右图给 出不同成份的高炉渣与铁 水磷平衡的条件。从图中 可以看出,随着铁的还原, 铁水中磷含量逐渐增高。
钢 铁 生 产 中 的脱磷 技术(P PT84页 )
钢 铁 生 产 中 的脱磷 技术(P PT84页 )
脱磷反应热力学
❖炼钢过程的脱磷反应在渣—金属间进 行,渣中(CaO)高的碱性操作可以脱 磷。据此脱磷反应可以按下式进行: ❖(1)分子论形式的表达式 ❖2[P]+5(FeO)+3(CaO)=(3Ca O·P2O5)+5Fe(l) ❖2[P]+5(FeO)+4(CaO)=(4Ca O·P2O5)+5Fe(l) ❖(2)离子形式表达式 ❖ 2[P]+5[O]+3(O2)=2(PO3-4) ❖脱磷反应平衡常数KP可以简化为:
杂质元素对钢材性能的影响
下两表给出钢中不同杂质元素对钢材性能的影响。从表中可以看 出,磷的危害是: ❖ 降低钢材的韧性 ❖ 降低钢材的热变形性 ❖ 降低钢材的浇铸性
同时,磷可以提高钢材的强度,提高钢材的耐磨性和抗腐蚀能力。
磷对钢材韧性的危害
磷使钢变脆,可以提高钢的抗拉强度, 但使韧性降低。如建筑用钢磷含量从 0.02%降到0.005%,性能会进一 步改善。磷从0.014%降到 0.002%,转变温度可下降40K。
杂质与钢水的纯净度
❖ 钢中杂质对钢材性能有多种影响。钢种用处不同,对钢材中杂 质的要求也有很大差别,通常钢中杂质可分为两大类:
(1)表面活性杂质:O、P、S、As、Se、Sb、Te等。 (2)间隙型杂质:H、C、N、O、(B) ❖ 从元素周期表看,表面活性杂质是周期表中Vb和VIb族元素, 此类元素容易在晶界或异向界面上偏析聚集,造成钢的脆化,其 偏析程度有时可达到平均浓度几千倍。间隙型夹杂在铁结晶间的 原子间隙内运动,在400℃以下的低温区域危害极大。
钢 铁 生 产 中 的脱磷 技术(P PT84页 )
钢 铁 生 产 中 的脱磷 技术(P PT84页 )
磷在钢中的溶解度
❖右图给出不同元素 对铁水中磷的活度系 数的影响,其中C、 Si、S等元素提高磷 的活度系数,有利于 脱磷;而Cr、Nb、 Mn、V、Ti等元素 降低磷的活度系数, 不利于炼钢脱磷。
磷对钢材断裂韧性的危害
❖ 高强钢或超高强钢的一种重要的 失效方式—低应力脆性破断。这种 失效,是在施于材料上的载荷小于 σs或许用应力时,由材料内裂纹逐 步扩展造成的。许多因素会影响钢 的断裂韧性,其中磷是引起冷脆的 元素,其含量每增加0.01%会使 钢材临界脆化温度上升7~10K, 并使钢材的冲击值显著降低。产生 这种影响的原因之一是熔于钢基体 中的磷限制了交叉滑移,使钢的塑 性变形能力下降所致。
钢 铁 生 产 中 的脱磷 技术(P PT84页 )
不同用途钢种所允许的杂质含量的上限(%)
钢 铁 生 产 中 的脱磷 技术(P PT8T84页 )
钢种、服役条件对钢材纯净度的要求
钢 铁 生 产 中 的脱磷 技术(P PT84页 )
钢 铁 生 产 中 的脱磷 技术(P PT84页 )