螺纹-车削(2)
螺 纹 加 工

金属切削方法
❖ 螺纹加工
4. 螺纹滚压
图8.118 螺纹滚压
金属切削方法
❖ 螺纹加工
5. 螺纹磨削
根据所用砂轮形状,外螺纹有以下两种磨削方法:
1)单线砂轮磨削,如图8.119(a)所示 2)多线砂轮磨削,如图8.119(b)所示
金属切削方法
❖ 螺纹加工
5. 螺纹磨削
图8.119 螺纹磨削
金属切削方法
1)盘形铣刀铣削螺纹(如图8.115所示) 2)梳形螺纹铣刀铣削螺纹(如图8.116所示) 3)旋风法铣削螺纹(如图8.117所示)
金属切削方法
❖ 螺纹加工
2. 螺纹铣削
图8.115 盘形铣刀加工螺纹
金属切削方法
❖ 螺纹加工
2. 螺纹铣削
图8.116 梳形螺纹铣刀加工螺纹
金属切削方法
❖ 螺纹加工
❖ 螺纹加工
6. 螺纹加工方法的选择
螺纹加工方法的选择,主要取决于螺纹的种类、精度等级、生产批 量及螺纹件的结构特点,如书中表8.7所示。
机械制造基础
2. 螺纹铣削图8.117 Nhomakorabea旋风法铣削螺纹
金属切削方法
❖ 螺纹加工
3. 攻螺纹和套螺纹
攻螺纹是用丝锥加工内螺纹 套螺纹是用板牙加工外螺纹 攻螺纹和套螺纹加工精度较低,主要用于精度要求不高的、直径较 小的普通连接螺纹
金属切削方法
❖ 螺纹加工
4. 螺纹滚压
螺纹滚压方法有搓丝板滚压和滚丝轮滚压两种
1)搓丝板滚压,如图8.118(a)所示 2)滚丝机滚压,如图8.118(b)所示
机械制造基础
金属切削方法
❖ 螺纹加工
螺纹的应用非常广泛,根据其用途不同,可分为两大类:
车螺纹的方法

车螺纹简介(图)将工件表面车削成螺纹的方法称为车螺纹。
螺纹按牙型分有三角螺纹、梯形螺纹、方牙螺纹等(图1)。
其中普通公制三角螺纹应用最广。
图1 螺纹的种类1. 普通三角螺纹的基本牙型普通三角螺纹的基本牙型如图2所示,各基本尺寸的名称如下:图2 普通三角螺纹基本牙型D—内螺纹大径(公称直径);d—外螺纹大径(公称直径);D2 —内螺纹中径;d2—外螺纹中径;D1 —内螺纹小径;d1—外螺纹小径;P—螺距;H-原始三角形高度。
决定螺纹的基本要素有三个:牙型角α 螺纹轴向剖面内螺纹两侧面的夹角.公制螺纹α=60o,英制螺纹α=55o。
螺距P 它是沿轴线方向上相邻两牙间对应点的距离.螺纹中径D2(d2)它是平螺纹理论高度H的一个假想圆柱体的直径。
在中径处的螺纹牙厚和槽宽相等。
只有内外螺纹中径都一致时,两者才能很好地配合.从图上可以看出:车削外螺纹时,应该将外径车削为:车削外螺纹外径=公称直径-2*H/8其中H为螺纹原始三角形高度,计算公式为H=0.866*P(P为螺距,根据手册可以查出)车削内螺纹时,孔径应为:车削内螺纹孔径=公称直径-2*5/8H *5/8=0。
625 1/8=0。
125以车削方式制作M20X2.5的粗牙螺纹为例:螺栓坯料外径=20—2*((0。
866*2.5)/8)=19.46螺母坯料内径=20-2*((0。
866*2.5)*5/8)=17。
29这样车制出来的螺纹仅仅是牙面配合,不会出现牙顶与牙底干涉的情况。
使用板牙、丝锥做作螺纹时,由于加工时的挤压作用,因此上述公式不能适合(根据材料不同而选择另外的公式2. 车削外螺纹的方法与步骤(1)准备工作1)安装螺纹车刀时,车刀的刀尖角等于螺纹牙型角α=60o,其前角γo=0o才能保证工件螺纹的牙型角,否则牙型角将产生误差。
只有粗加工时或螺纹精度要求不高时,其前角可取γo=5o~20o。
安装螺纹车刀时刀尖对准工件中心,并用样板对刀,以保证刀尖角的角平分线与工件的轴线相垂直,车出的牙型角才不会偏斜。
数控车床循环指令详解
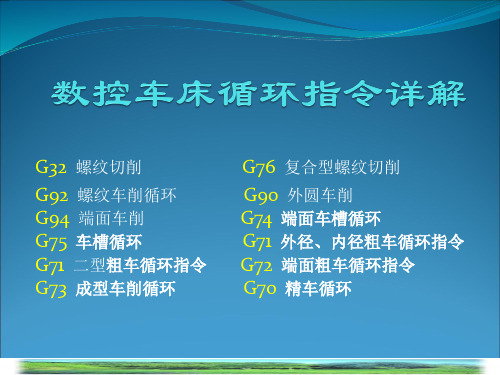
(4)Q nf是指定精加工路线的最后一个程序段的段号; (5)U u是X方向上的精加工余量,直径值; (6)W w是Z方向上的精加工余量。 (7)粗车过程中从程序段号Pns~Qnf之间的任何F 只有G71指令中指定的F、S、T功能有效。
图16.6
G71有两种情况,也就是一型和二型。
一型:也就是沿X轴同一方向递增或递减。一型
工序3 精车加工 精车
G00 X150; Z150; N4; S300 M03 T0303; G00 X48 Z-64; G01 X2 F0.05; G00 X150; Z150; M05; M30;
工序4 切断 程序结束
地址 内容
说明
1851
X向间隙数值。数值为半径值。
1852
Z向间隙数值
3204 0/1 PAR设置0是为中括号[ ]。 设置1是为小括号( )
G32 螺纹切削
G92 螺纹车削循环 G94 端面车削 G75 车槽循环 G71 二型粗车循环指令 G73 成型车削循环
G76 复合型螺纹切削
G90 外圆车削 G74 端面车槽循环 G71 外径、内径粗车循环指令 G72 端面粗车循环指令 G70 精车循环
该指令用于车削等螺距直螺纹、锥螺纹。
格式:G32 X(U)__ Z(W)__ F__
格式:G92 X(U) Z(W) R F
XZ螺纹终点坐标,R表示螺纹起始点与终点在X 向的坐标增量值(半径值),圆柱螺纹切削R为0可 省略。一般外锥螺纹R为负值,内锥螺纹R为正值。
T0202 (螺纹刀) M3 S400 G0 X22 Z5 G92 X20 Z-15 R-0.625 I14 F2 X19.6 I14 X19.2 I14 X18.9 14 X18.75 14 X18.631 I14 X18.631 I14 (精车) G0 X100 Z100 M5 M30
车工第六章3螺纹加工

z1 z3 P工 z2 z4 P丝
3)调整机床间隙 间隙大,车削螺纹时容 易产生“扎刀”现象。所以在车螺纹之前, 应调整中、小滑板的镶条间隙,使之松紧适 当。间隙过小,则操作不灵活,摇动滑板费 力。
4)如果车削的是左旋螺纹,则变换三星轮 的位置
螺纹车削调整项: ①调整主轴转速;
②调整螺距;
③脱开光杠进给机构,改由丝杠进给。
例如:P=2.5mm的米制螺纹,进给手柄如何 交换? 按图(铭牌表)6-30并找到手柄所属的位置 手柄Ⅰ置于B上,将手Ⅱ柄2置于Ⅱ处,将手轮3 拉出转到6与 相对的位置后,便可。 交换齿轮箱的齿轮分别是:A=63,B=100,
弹性刀杆螺纹刀
低速车三角形螺纹进给次数进刀格数表
M24 P=3mm
进刀 次数
中滑板进 刀 格 数
小滑板赶刀格数
左
右
1
30
0
中滑板进 刀 格 数
M20 P=2.5mm 小滑板赶刀格数
左
右
30
0
2
15
6
15
6
3
13
6
13
6
4
10
4
8
4
5
8
4
5
2
6
7
2
3
2
7
5
2
2
0
8
3
1
1
1
M16 P=2mm
中滑板 进 刀 格 数
C=75.
2)调整交换齿轮 某些车床需要调整交换齿 轮,根据要求进行调整,
① 切断机床电源,车头变速手柄放在空挡位 置;
车削螺纹时常见故障及解决方法

车削螺纹时常见故障及解决方法螺纹车削是机械加工中的一项重要工艺,常用于制作螺栓、螺母等产品。
在车削螺纹过程中,有时会遇到一些常见的故障,如螺纹断裂、螺纹毛刺等问题。
本文将针对这些常见故障,给出相应的解决方法。
一、螺纹断裂螺纹断裂是车削螺纹中最常见的故障之一,主要原因有以下几点:1. 切削量过大。
车削螺纹时,如果一次性切削量过大,容易导致螺纹切削力过大,从而造成螺纹断裂。
2. 车削速度过高。
车削速度过高,会使螺纹材料在车削过程中产生过热现象,从而影响螺纹强度,导致断裂。
3. 切削刃磨损严重。
切削刃磨损严重会导致螺纹车削时切削力不均匀,从而容易引起断裂。
解决方法:1. 合理控制切削量。
在车削螺纹时,应根据工件的材料和尺寸,选择合适的切削量,避免一次性过大的切削力。
2. 控制切削速度。
根据螺纹材料的硬度和热处理情况,选择合适的切削速度,避免过高的车削速度造成螺纹断裂。
3. 及时更换刀具。
定期检查和更换切削刃,保证切削刃的锐利度,避免因刀具磨损产生过大的切削力。
二、螺纹毛刺螺纹毛刺是车削螺纹常见的表面缺陷之一,主要原因有以下几点:1. 加工精度不高。
车削螺纹时,如果刀具偏斜、工件夹紧不稳定等,容易导致精度不高,从而产生毛刺。
2. 切削液不合适。
切削液在车削螺纹时起到冷却、润滑的作用,选用不合适的切削液容易造成毛刺。
3. 刀具磨损严重。
刀具磨损严重会导致切削力不均匀,从而产生毛刺。
解决方法:1. 提高加工精度。
在车削螺纹前,检查刀具和夹持装置,确保工艺参数设置正确,以提高加工精度。
2. 合理选择切削液。
根据螺纹材料的特性和切削条件,选择合适的切削液,保证切削液的冷却和润滑效果,减少毛刺。
3. 及时更换刀具。
定期检查和更换刀具,保证刀具的切削锋利度,减少切削力不均匀引起的毛刺问题。
三、螺纹尺寸不准确螺纹尺寸不准确是车削螺纹常见的质量问题之一,主要原因有以下几点:1. 刀具磨损不均匀。
刀具磨损不均匀会导致切削力不均匀,从而影响螺纹尺寸的精度。
螺纹加工方法详细讲解
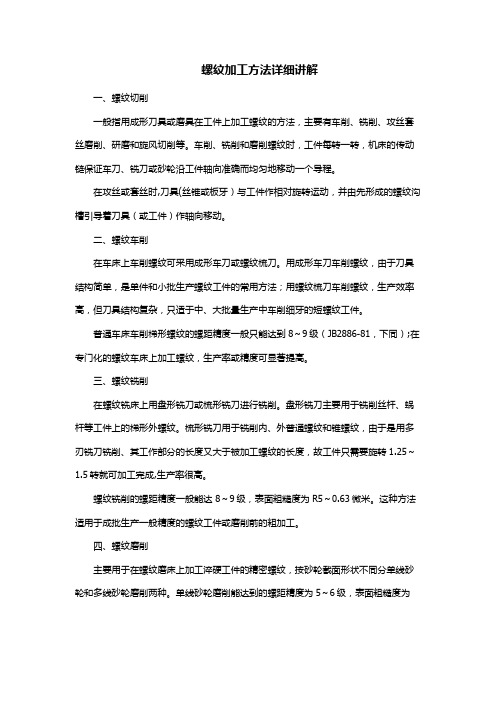
螺纹加工方法详细讲解一、螺纹切削一般指用成形刀具或磨具在工件上加工螺纹的方法,主要有车削、铣削、攻丝套丝磨削、研磨和旋风切削等。
车削、铣削和磨削螺纹时,工件每转一转,机床的传动链保证车刀、铣刀或砂轮沿工件轴向准确而均匀地移动一个导程。
在攻丝或套丝时,刀具(丝锥或板牙)与工件作相对旋转运动,并由先形成的螺纹沟槽引导着刀具(或工件)作轴向移动。
二、螺纹车削在车床上车削螺纹可采用成形车刀或螺纹梳刀。
用成形车刀车削螺纹,由于刀具结构简单,是单件和小批生产螺纹工件的常用方法;用螺纹梳刀车削螺纹,生产效率高,但刀具结构复杂,只适于中、大批量生产中车削细牙的短螺纹工件。
普通车床车削梯形螺纹的螺距精度一般只能达到8~9级(JB2886-81,下同);在专门化的螺纹车床上加工螺纹,生产率或精度可显著提高。
三、螺纹铣削在螺纹铣床上用盘形铣刀或梳形铣刀进行铣削。
盘形铣刀主要用于铣削丝杆、蜗杆等工件上的梯形外螺纹。
梳形铣刀用于铣削内、外普通螺纹和锥螺纹,由于是用多刃铣刀铣削、其工作部分的长度又大于被加工螺纹的长度,故工件只需要旋转1.25~1.5转就可加工完成,生产率很高。
螺纹铣削的螺距精度一般能达 8~9级,表面粗糙度为R5~0.63微米。
这种方法适用于成批生产一般精度的螺纹工件或磨削前的粗加工。
四、螺纹磨削主要用于在螺纹磨床上加工淬硬工件的精密螺纹,按砂轮截面形状不同分单线砂轮和多线砂轮磨削两种。
单线砂轮磨削能达到的螺距精度为5~6级,表面粗糙度为R1.25~0.08微米,砂轮修整较方便。
这种方法适于磨削精密丝杠、螺纹量规、蜗杆、小批量的螺纹工件和铲磨精密滚刀。
多线砂轮磨削又分纵磨法和切入磨法两种。
纵磨法的砂轮宽度小于被磨螺纹长度,砂轮纵向移动一次或数次行程即可把螺纹磨到最后尺寸。
切入磨法的砂轮宽度大于被磨螺纹长度,砂轮径向切入工件表面,工件约转1.25转就可磨好,生产率较高,但精度稍低,砂轮修整比较复杂。
切入磨法适于铲磨批量较大的丝锥和磨削某些紧固用的螺纹。
车削螺纹的步骤

车削螺纹的步骤车削螺纹是机械加工中常见的一种操作,用于在工件上加工出螺纹结构。
螺纹结构广泛应用于各种机械设备中,能够实现零部件的连接和固定。
下面将介绍车削螺纹的步骤。
1. 准备工作在进行车削螺纹之前,首先需要准备好相应的工具和设备。
常用的工具包括车床、刀具、卡盘等。
此外,还需要准备好待加工的工件和螺纹规格的要求。
2. 安装工件将待加工的工件安装在车床上,确保其夹紧牢固。
根据工件的形状和尺寸,选择合适的夹具进行固定。
在安装时,要注意保持工件的水平和垂直度,以确保后续加工的准确性。
3. 选择合适的刀具根据螺纹规格和工件材料的不同,选择合适的刀具进行车削。
常用的刀具有螺旋铣刀、内螺纹刀等。
刀具的选择要考虑到切削力、切削速度和切削深度等因素,以保证加工效果和刀具寿命。
4. 设置车床参数在进行车削螺纹之前,需要设置好车床的参数。
主要包括主轴转速、进给速度和刀具进给量等。
这些参数的设置要根据具体的工件材料和螺纹规格来确定,以保证加工质量和效率。
5. 调整刀具位置根据螺纹规格和刀具形状,调整刀具的位置和角度。
确保刀尖与工件表面接触,并且与螺纹轮廓相吻合。
调整刀具位置时要小心谨慎,避免碰撞和损坏刀具或工件。
6. 开始车削确认所有准备工作完成后,可以开始进行车削操作了。
根据车床上的操作面板或控制系统,启动车床并逐步加工螺纹。
在车削过程中,要保持稳定的进给速度和切削速度,并及时清理切屑。
7. 检查加工质量在完成车削后,需要对加工质量进行检查。
主要包括螺纹轮廓的尺寸、形状和表面质量等方面。
可以使用测量仪器如千分尺、外径规等进行检测,并与螺纹规格进行对比。
8. 清洁和保养在完成车削螺纹后,要对车床和刀具进行清洁和保养。
清除切屑和废料,并对刀具进行润滑和磨损检查。
及时更换磨损严重的刀具,并做好防锈措施,以延长其使用寿命。
总结:车削螺纹是一项精密而复杂的机械加工操作,需要严格按照步骤进行,并注意安全和质量控制。
通过合理选择刀具、设置车床参数和调整刀具位置,能够实现高效、精确的螺纹加工。
普通车床螺纹车削常见故障及解决方法(三篇)

普通车床螺纹车削常见故障及解决方法1. 放松刀夹:在车削过程中,如果刀夹没有固定好,会导致刀具松动或者偏位,从而造成螺纹不良。
解决方法是检查刀夹固定螺母是否紧固,如果松动则重新固定。
2. 刀具磨损:长时间使用刀具会磨损,导致刀尖变钝,从而无法进行正常的车削。
解决方法是更换刀具,保持刀具的锐利度。
3. 机床不稳定:如果机床本身存在不稳定的问题,例如床身变形、主轴不平衡等,会导致螺纹加工时产生偏差。
解决方法是定期检测和调整机床,确保其稳定性。
4. 刀具与工件匹配不良:在螺纹车削过程中,刀具与工件的匹配也非常重要。
如果选用的刀具尺寸不合适,就会导致螺纹加工结果不理想。
解决方法是选择合适尺寸的刀具,确保刀具与工件的配合良好。
5. 刀具进给速度不恰当:刀具进给速度过快或者过慢都会影响螺纹加工的质量。
解决方法是根据不同的工件材料和螺纹规格,调整刀具的进给速度,确保加工的质量。
6. 冷却液不适用:在螺纹车削过程中,适当使用冷却液可以降低温度,减少摩擦,提高切削润滑效果,从而改善加工质量。
如果使用的冷却液性质不合适,也会影响螺纹加工结果。
解决方法是选择合适的冷却液,根据加工工件的要求进行选择。
7. 机床刚度不足:机床刚度不足会导致在螺纹车削过程中产生振动和共振,造成螺纹不良。
解决方法是增加机床的刚度,例如加强机床床身的结构,增加加工时的稳定性。
8. 机床零件磨损:长时间使用机床,有些零部件会磨损,例如导轨、导向轨等,会导致加工误差。
解决方法是定期检查和更换机床零部件,保证机床的准确性和稳定性。
总之,普通车床螺纹车削常见故障的解决方法就是:确保刀具的固定和锐利度,稳定机床的结构和性能,选择合适尺寸和质量的刀具,调整进给速度和冷却液的使用,定期检查和维护机床零部件,确保加工质量和效果。
普通车床螺纹车削常见故障及解决方法(二)车床螺纹车削是机械加工中常见的一种加工方式,常用于制作螺纹零件。
然而,在车削过程中,可能会遇到一些常见的故障。
机床数控技术第二(2)版课后答案

第一章绪论简答题答案,没有工艺题的1 什么是数控机床答:简单地说,就是采用了数控技术(指用数字信号形成的控制程序对一台或多台机床机械设备进行控制的一门技术)的机床;即将机床的各种动作、工件的形状、尺寸以及机床的其他功能用一些数字代码表示,把这些数字代码通过信息载体输入给数控系统,数控系统经过译码、运算以及处理,发出相应的动作指令,自动地控制机床的道具与工件的相对运动,从而加工出所需要的工件。
2 数控机床由哪几部分组成?各组成部分的主要作用是什么?答:(1)程序介质:用于记载机床加工零件的全部信息。
(2)数控装置:控制机床运动的中枢系统,它的基本任务是接受程序介质带来的信息,按照规定的控制算法进行插补运算,把它们转换为伺服系统能够接受的指令信号,然后将结果由输出装置送到各坐标的伺服系统。
(3)伺服系统:是数控系统的执行元件,它的基本功能是接受数控装置发来的指令脉冲信号,控制机床执行元件的进给速度、方向和位移量,以完成零件的自动加工。
(4)机床主体(主机):包括机床的主运动、进给运动部件。
执行部件和基础部件。
3 数控机床按运动轨迹的特点可分为几类?它们特点是什么?答:(1)点位控制数控机床:要求保证点与点之间的准确定位(它只能控制行程的终点坐标,对于两点之间的运动轨迹不作严格要求;对于此类控制的钻孔加工机床,在刀具运动过程中,不进行切削加工)。
(2)直线控制数控机床:不仅要求控制行程的终点坐标,还要保证在两点之间机床的刀具走的是一条直线,而且在走直线的过程中往往要进行切削。
(3)轮廓控制数控机床:不仅要求控制行程的终点坐标值,还要保证两点之间的轨迹要按一定的曲线进行;即这种系统必须能够对两个或两个以上坐标方向的同时运动进行严格的连续控制。
4 什么是开环、闭环、半闭环伺服系统数控机床?它们之间有什么区别?答:(1)开环:这类机床没有来自位置传感器的反馈信号。
数控系统将零件程序处理后,输出数字指令后给伺服系统,驱动机床运动;其结构简单、较为经济、维护方便,但是速度及精度低,适于精度要求不高的中小型机床,多用于对旧机床的数控化改造。
车螺纹的步骤与方法
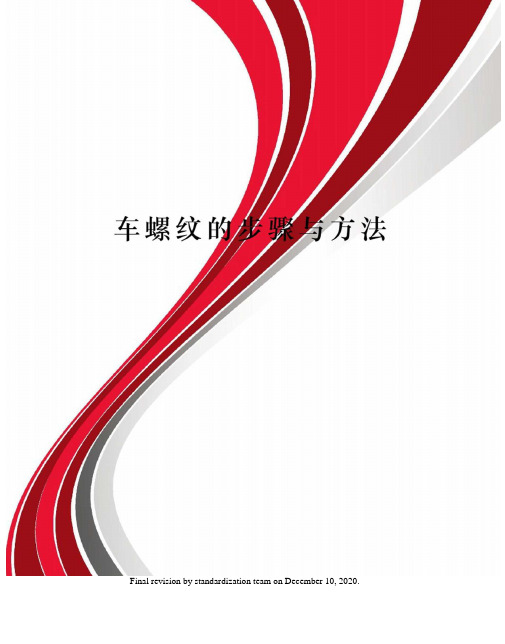
Final revision by standardization team on December 10, 2020.车螺纹的步骤与方法:(低速车削三角形螺纹V < 5米/分)1、车螺纹前对工件的要求:1)螺纹大径:理论上大径等于公称直径,但根据与螺母的配合它存在有下偏差(一),上偏差为0;因此在加工中,按照螺纹三级精度要求。
螺纹外径比公称直径小。
螺纹外径D二公称直径一2)退刀槽:车螺纹前在螺纹的终端应有退刀槽,以便车刀及时退出。
3)倒角:车螺纹前在螺纹的起始部位和终端应有倒角,且倒角的小端直径C螺纹底径。
4)牙深高度(切削深度):hl二2、调整车床:先转动手柄接通丝杠,根据工件的螺距或导程调整进给箱外手柄所示位置。
调整到各手柄到位。
3、开车、对刀记下刻度盘读数,向右退出车刀。
4、合上开合螺母,在工件表面上车出一条螺旋线,横向退出车刀,并开反车把车刀退到右端,停车检查螺距是否正确(钢尺)。
5、开始切削,利用刻度盘调整切深(逐渐减小切深)。
注意操作中,车刀将终了时应做好退刀、停车准备,先快速退出车刀,然后开反车退回刀架。
吃刀深度控制,粗车时t「,精车时t < O六、螺纹的测量:1、单向测量法:1)顶径的测量:螺纹顶径的尺寸,一般都允许有较大的误差,外螺纹顶径可用游标卡尺或千分尺测量,内螺纹顶径可用游标卡尺测量。
2)螺距的测量:螺距一般可用钢尺测量,3)中径的测量:(1)用螺纹千分尺测量螺纹中径。
(2)用三针法测量螺纹中径。
三针法测量螺纹中径是一种比较精密的测量方法。
2、综合测量法:综合测量法就是对螺纹的各项尺寸用螺纹量规进行综合性的测量七、安全生产:1)车螺纹前检查车床正反车操纵机构及开合螺母等,以防操作失灵。
2)在吃刀时注意不要多摇进一圈,否则会发生车刀撞坏,工件顶弯或飞出等事故。
3)不能用手模螺纹表面,更不能用棉纱去擦正在旋转的螺纹工件,以防发生事故。
车螺纹的步骤与方法:(低速车削三角形螺纹V C 5米/分)1、车螺纹前对工件的要求:1)螺纹大径:理论上大径等于公称直径,但根据与螺母的配合它存在有下偏差(一),上偏差为0;因此在加工中,按照螺纹三级精度要求。
螺纹车削_单一固定形状车削(G92指令)

新课巩固
1. G92指令的格式 2. G92指令的动作演示(视频) 3. G92指令的编程(实例) 4. 在数控车床上加工螺纹时的注意事项
布置作业
1.课堂作业:
(1)复习课上内容。
(2)讲义练习:做在作业本上
2.实习任务:
用G92指令编写如下图所示工件的程序,并进行加工。
新课导入
G32 指令主要用于一些单一、特殊高精度螺纹 ( 圆柱 螺纹、等螺距的锥螺纹和端面螺纹)的切削加工,为了适 应一些多加工元素(有圆柱面、圆锥面、圆弧面、螺纹面 等等)零件的切削加工,则引入了另一类加工指令——称为 螺纹切削固定循环指令 G92 。另一方面, G32 指令加工 时,车刀的切入、切出、返回均需编入程序,程序量较 长且易出错。所以从减少程序段的长度,提高程序编制 正确率的角度出发,亦引入 G92 指令。那么,本次课我 们就共同来学习该指令的一些知识。
螺纹的总切深量为18mm背吃刀量分别为11mm05mm01mm和01mmgg3232指令主要用于一些单一指令主要用于一些单一特殊高精度螺纹特殊高精度螺纹圆柱圆柱螺纹螺纹等螺距的锥螺纹和端面螺纹等螺距的锥螺纹和端面螺纹的切削加工的切削加工为了适为了适应一些多加工元素应一些多加工元素有圆柱面有圆柱面圆锥面圆锥面圆弧面圆弧面螺纹面螺纹面等等等等零件的切削加工零件的切削加工则引入了另一类加工指令则引入了另一类加工指令称为称为螺纹切削单一固定循环指令螺纹切削单一固定循环指令gg9292
新课讲授
一、 G92指令的格式
1.功能:用于小螺距圆柱、圆锥螺纹的切削循环加工
2. 指令格式:
G92 X(U)
各参数的含义:
Z(W)
F
;
怎样用车床车螺纹车螺纹的步骤与方法

怎样用车床车螺纹(包括正反丝) 车螺纹的步骤与方法问题:怎样用车床车螺纹(包括正反丝)车螺纹的步骤与方法:(低速车削三角形螺纹 Vく5米∕分) 1、车螺纹前对工件的要求: 1)螺纹大径:理论上大径等于公称直径,但根据与螺母的配合它存在有下偏差(—),上偏差为0;因此在加工中,按照螺纹三级精度要求。
螺纹外径比公称直径小。
螺纹外径D=公称直径—2)退刀槽:车螺纹前在螺纹的终端应有退刀槽,以便车刀及时退出。
3)倒角:车螺纹前在螺纹的起始部位和终端应有倒角,且倒角的小端直径く螺纹底径。
4)牙深高度(切削深度):h1= 2、调整车床:先转动手柄接通丝杠,根据工件的螺距或导程调整进给箱外手柄所示位置。
调整到各手柄到位。
3、开车、对刀记下刻度盘读数,向右退出车刀。
4、合上开合螺母,在工件表面上车出一条螺旋线,横向退出车刀,并开反车把车刀退到右端,停车检查螺距是否正确(钢尺)。
5、开始切削,利用刻度盘调整切深(逐渐减小切深)。
注意操作中,车刀将终了时应做好退刀、停车准备,先快速退出车刀,然后开反车退回刀架。
吃刀深度控制,粗车时t=~0.3mm,精车时tく0.05mm。
六、螺纹的测量: 1、单向测量法: 1)顶径的测量:螺纹顶径的尺寸,一般都允许有较大的误差,外螺纹顶径可用游标卡尺或千分尺测量,内螺纹顶径可用游标卡尺测量。
2)螺距的测量:螺距一般可用钢尺测量, 3)中径的测量:(1)用螺纹千分尺测量螺纹中径。
(2)用三针法测量螺纹中径。
三针法测量螺纹中径是一种比较精密的测量方法。
2、综合测量法:综合测量法就是对螺纹的各项尺寸用螺纹量规进行综合性的测量七、安全生产: 1)车螺纹前检查车床正反车操纵机构及开合螺母等,以防操作失灵。
2)在吃刀时注意不要多摇进一圈,否则会发生车刀撞坏,工件顶弯或飞出等事故。
3)不能用手模螺纹表面,更不能用棉纱去擦正在旋转的螺纹工件,以防发生事故。
普通车床上加工螺纹一般是用螺纹车刀进行加工。
(螺纹车削尺寸表)

44.520 45.003 44.845 45.245 56.558 57.067 56.656 57.125 67.619 68.342 72.226 72.801 83.528 84.217 84.926 85.501 96.236 96.916 97.372 97.947 108.893 109.617 110.072 110.722 135.872 136.617 135.472 136.191 162.712 163.562 160.872 163.431
11.5 11 11.5 11 8 11 8 11 8 11 8 11 8 11 8 11
2.209 2.309 2.209 2.309 3.175 2.309 3.175 2.309 3.175 2.309 3.175 2.309 3.175 2.309 3.175 2.309
60 55 60 55 60 55 60 55 60 55 60 55 60 55 60 55
18.377 19.100 19.215 23.400 28.892 26.700 30.480 29.800 31.750 31.400 33.020 35.800 35.720 40.100 38.418 40.100
48.054 48.537 47.803 48.203 60.092 60.601 59.614 60.083 72.699 73.422 75.184 75.759 88.608 89.297 87.884 88.459 101.316 101.996 100.330 100.905 113.973 114.697 113.030 113.680 140.952 141.697 138.430 139.149 167.792 168.672 163.830 164.549
车工技术教程-车削梯形螺纹

车削梯形螺纹学习目标1.了解梯形螺纹车刀的形状,掌握梯形螺纹车刀的刃磨和检测方法。
2.掌握外梯形螺纹的尺寸计算、车削和检测方法。
梯形螺纹相关知识一、梯形螺纹牙型及相关参数计算牙型如图图图梯形螺纹计算公式如表表梯形螺纹各参数及计算公式名称代号计算公式牙型角αα=30°螺距P 由螺纹标准确定牙顶间隙a cP(mm) 1.5~5 6~12 14~44 ac(mm)0.25 0.5 1外螺纹大径 d 公称直径中径d2d2=d-0.5P 小径d3d3=d-2h3 牙高h3h3=0.5P+ ac内螺纹大径D4D4=d+2ac中径D2D2= d2小径D1D1=d-P牙高H4H4= h3牙顶宽f,f= f’=0.366P牙槽底宽W,W’W=W’=0.336P-0.536a c轴向齿厚Sx Sx=0.5P法向尺厚Sn Sn==0.5Pcos二、梯形螺纹基本标注1.外螺纹2.内螺纹三、螺纹车刀梯形螺纹车刀分为硬质合金和高速钢两种。
常用的是高速钢材料的车刀。
1.高速钢梯形外螺纹车刀(1)粗车刀刀尖宽度要小于齿根槽宽,径向前角为10°~15°,两侧后角进刀方向为(3°~5°)+φ,背进刀方向为(3°~5°)-φ。
如图图高速钢梯形外螺纹粗车刀(2)精车刀精车径向前角为0°,两侧后角进刀方向为(5°~8°)+φ,背进刀方向为(5°~8°)-φ进刀,可适当磨出卷些槽,增大前角。
如图图高速钢梯形外螺纹精车刀2.硬质合金梯形螺纹车刀适合于车削一般精度的梯形螺纹,效率提高。
几何角度如图图硬质合金梯形外螺纹车刀3.梯形内螺纹车刀几何角度如图图梯形内螺纹车刀四、梯形螺纹车刀的刃磨方法和检测(1)刃磨步骤:①粗磨两侧后面,刃磨出两侧后角、刀尖角。
②精磨两侧后面,控制好刀头宽度,使其小于牙槽底宽0.5mm左右。
③粗磨前刀面,刃磨出径向前角。
车削管螺纹的尺寸规格
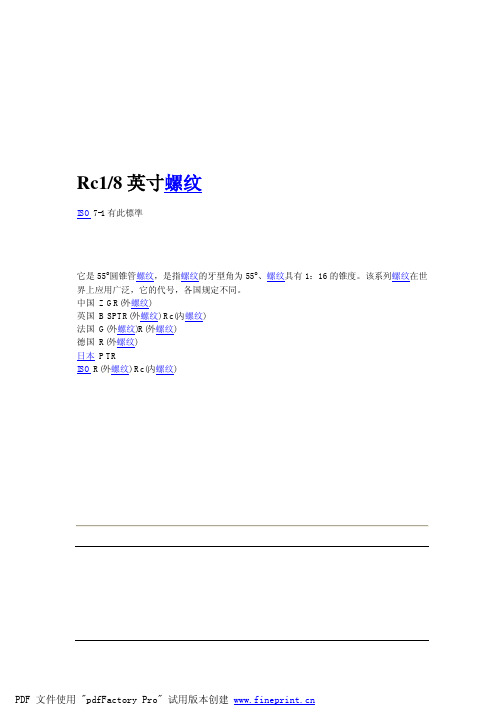
大径 9.728 13.157 16.662 20.955 26.411 33.249 41.910 47.803
中径 9.147 12.301 15.806 19.793 25.279 31.770 40.431 46.324
小径 8.566 11.445 14.950 18.631 24.117 30.291 38.952 44.845
3.1. 3.1. 常用米制普通粗牙螺纹的螺距如下表(螺纹底孔直径:碳钢φ=公称直径-P;铸铁φ=公称
直径-1.05~1.1P;加工外螺纹光杆直径取φ=公称直径-0.13P):
表 1 常用米制普通粗牙螺纹的直径/螺距
公称 直径 M5 M6 M8螺 P0.8 1 1.25
铸铁 底孔 4.1 4.9 6.6
M10 1.5 8.3 8.5
9.8
M12 1.75 10.3 10.4 11.8
M14 2
11.7 12
13.7
M16 2
13.8 14
15.7
M18 2.5 15.3 15.5 17.7
M20 2.5 17.3 17.5 19.7
M33 3.5 M36 4 M42 4.5 M48 5 M56 5.5 M64 6
1-1/4
11.5
1-1/2
11.5
13.616 17.055 21.223 26.568 33.228 41.985 48.054
12.487 15.926 19.772 25.117 31.461 40.218 46.287
11.358 14.797 18.321 23.666 29.694 38.451 44.520
27,30,33,36,39,42,45,48,52,56,60
三角螺纹车削(P=2
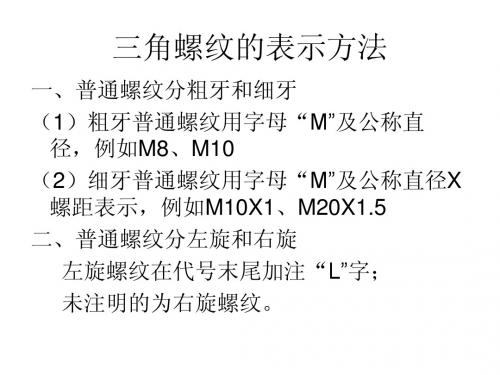
四、螺纹的测量与检查
1.螺纹的大径:游标卡尺或千分尺测量 2.螺距:游标卡尺或钢直尺 3.中经:螺端进止端不进) 或标准螺母
• 采用螺纹千分尺测量
d2=d-0.6495P=φ(d-1.3)
_0.2 0
课堂总结
本节课,我们主要学习了三角螺纹的车削方法。 本节课,我们主要学习了三角螺纹的车削方法。在车削注意 以下几个问题: 以下几个问题:
二、车床调整
1、调整小滑板镶条间隙 调 紧 一些 2、根据名牌表,调整进给箱手柄
Ⅰ
Ⅱ
丝 杆
光 杆
3、调整溜板箱手柄
三、车 削 方 法
车床开正反转车削
正转车削 退 刀 进 刀
反转
1、采用中滑板直进法车削 、 即每次切削由中滑板作径向进给 2、进刀格数计算 、 进刀格数=牙型高度 中滑板每格深度 进刀格数 牙型高度/中滑板每格深度 牙型高度 牙型高度=0.5413P(标准) 牙型高度 (标准) CA6136中滑板每格深度 中滑板每格深度=0.02mm 中滑板每格深度 p=2时,进刀格数为54格 格
3.牙顶宽 牙顶宽=P/8,牙底宽 牙底宽=P/4 牙顶宽 牙底宽
4、分刀方法 、 粗车(转速 转速104—165转/分) 粗车 转速 转分 5-5-5-4-4-4-3-3-3……-2-2(到50格) ( 格 精车(42—68转/分) 精车 转分 51-52-52.5-53-53.5-54-原刻度 原刻度 原则上随着深度的加深每次进刀的格数越少) (原则上随着深度的加深每次进刀的格数越少)
三角螺纹车削 (P=2) )
张家港工贸职业高级中学
任 务 书
工艺分析: 工艺分析:
1、车端面 、
−0 10 2、车削外圆至大径尺寸 d −0..20 、
车削螺纹的计算

8-2【1】三角螺纹的计算一、三角螺纹的尺寸计算1 .普通三角螺纹的尺寸计算普通三角螺纹牙形如图、尺寸计算公式参看下表。
例:试计算三角螺纹 M20 xZ 的牙形高2 .英制三角螺纹的尺寸计算英制三角螺纹的牙形如图 6 一 10 ,尺寸计算公式见表6 一3 。
二、三角形螺纹车刀1 .对螺纹车刀的要求螺纹车刀属于成形刀具,要保证螺纹牙形精度,必须正确刃磨和安装车刀。
对螺纹车刀的要求主要有以下几点:( 1 )车刀的刀尖角一定要等于螺纹的牙形角。
( 2 )精车时车刀的纵向前角应等于零度;粗车时允许有 5 o一15o的纵向前角。
( 3 )因受螺纹升角的影响,车刀两侧面的静止后角应刃磨得不相等,进给方向后面的后角较大,一般应保证两侧面均有 3o一 5o的工作后角。
( 4 )车刀两侧刃的直线性要好。
2 .普通三角螺纹车刀车刀从材料上分有高速钢螺纹车刀和硬质合金螺纹车刀两种。
( l )高速钢螺纹车刀高速钢螺纹车刀刃磨方便、切削刃锋利、韧性好,能承受较大的切削冲击力,车出螺纹的表面粗糙度小。
但它的耐热性差,不宜高速车削,所以常用来低速车削或作为螺纹精车刀。
高速钢螺纹车刀的几何形状如图8-10所示。
高速钢三角螺纹车刀的刀尖角一定要等于牙形角。
当车刀的纵向前角0o时,车刀两侧刃之间夹角等于牙形角;若纵向前角不为O o时,车刀两侧刃不通过工件轴线,车出螺纹的牙形不是直线而是曲线。
当车削精度要求较高的三角螺纹时,一定要考虑纵向前角对牙形精度的影响。
为车削顺利,纵向前角常选在 5 o一 15o之间,这时车刀两侧刃的夹角不能等于牙形角,而应当比牙形角小 30 ’一1o30’。
应当注意.纵向前角不能选得过大,若纵向前角过大,不仅影响牙形精度,而且还容易引起扎刀现象。
车螺纹时,由于螺纹升角的影响,造成切削平面和基面的位置变化,从而使车刀工作时的前角和后角与车刀静止时的前角和后角不相等。
螺纹升角越大,对工作时的前角和后角影响越明显。
零件图螺纹的详细画法

“M10”表示
公称直径为10 mm、螺距1.5 mm的单线 粗牙普通螺纹。
“M10×1”表示
公称直径为10mm、螺距为1 mm的单线细牙普通螺纹。
公差带代号
由公差等级(数字)和基本偏差(外螺纹用小写字母、 内螺纹用大写字母表示)所组成,例如5g6g、6g、6H、7H。 当螺纹中径公差带与顶径公差带代号不同时,需分别注 出,如: M10 ― 5g 6g 顶径公差带代号 中径公差带代号
(2)内螺纹
丝锥攻丝的方法:先用钻头钻孔,再 用丝锥攻丝,钻孔深度较深于螺纹长度
车削内螺纹的情况:工件绕轴线作等速回 转运动,刀具沿轴线作等速移动且切入工 件一定深度
车削螺纹
车外螺纹
点击播放
车内螺纹
加工螺纹的方法和工具示例
攻丝演示
点击播放
螺纹的牙顶和牙底
在螺纹加工中,由于刀具的切入(或压入)构成了凸起 和沟槽两部分,凸起的顶端称为 螺纹的牙顶 ,沟槽的底部称 为螺纹的牙底。
三角形螺纹: 普通螺纹和管螺纹 梯形螺纹 锯齿形螺纹
a. 普通螺纹
普通螺纹,牙型为三角形,牙型角为60°,螺纹特征代号为M。
普通螺纹又分为粗牙和细牙两种同。一般连接都用粗牙螺纹。 当螺纹的大径相同时,细牙螺纹的螺距和牙型高度比粗牙小,
细牙螺纹适用于薄壁零件的连接。
b. 英制管螺纹
管螺纹主要用于连接管子,牙型为三角形,牙型角为55°。
55°密封管螺纹的标记示例:
Rp3/4LH:尺寸代号为3/4的单线左旋圆柱内螺纹; Rc3/4: 尺寸代号为3/4的单线右旋圆锥内螺纹; Rp/R13/4 LH和Rc/R23/4:内螺纹与外螺纹旋合构成螺纹副。 Rp :密封圆柱内螺纹的螺纹特征代号; Rc :密封圆锥内螺纹的螺纹特征代号; R1 :与圆柱内螺纹相配合的圆锥外螺纹的特征代号; R2 :与圆锥内螺纹相配合的圆锥外螺纹的特征代号;
- 1、下载文档前请自行甄别文档内容的完整性,平台不提供额外的编辑、内容补充、找答案等附加服务。
- 2、"仅部分预览"的文档,不可在线预览部分如存在完整性等问题,可反馈申请退款(可完整预览的文档不适用该条件!)。
- 3、如文档侵犯您的权益,请联系客服反馈,我们会尽快为您处理(人工客服工作时间:9:00-18:30)。
车圆锥面的方法
(教案)
定
州
职
教
中
心
张晓晖
教案用纸附页
<一>、组织教学:(1分钟)
<二>、1、新课导入:(1分钟)
2、复习提问:(4分钟)
圆锥参数及计算共五个问题(每组一个必答题)<三>、讲授新课:(81分钟)
一:圆锥面车削方法
圆锥角度
1、技术要求:
尺寸精度
转动小滑板法
偏移尾座法
2.主要方法仿形法
宽刃刀车削法
铰内圆锥法
二:转动小滑板法(视频,板书)
1.小滑板转动的方
向
2.小滑板转过的角
度
正锥:逆时针转α/2
倒锥:顺时针转α/2 查看出勤情况
分组
目的:为讲解新课打基础。
答对者为本组加分
导入新课。
在大屏幕上展示图6—14。
用车刀模型向同学们展示图中的剖面在车刀中的断面位置。
对讨论中不准确的地方,不直接否定,通过其他同学的补充发言予以充实和纠正。
然后点击课件演示。
通过讲解,启发、引导学生得
到左侧★结论。
请一位学生上讲台来计算,其他同学在下面计算。
教 案 用 纸 附 页
教 学 内 容、 方 法 和 过 程
附 记
解:由oL α=(30 ~ 50)+ ψ⇒oL α=30+4030′ = 7030′
oR α=(30 ~ 50)—ψ⇒oR α=30- 4030′ = -1030′
总结: (约1分钟) 螺纹升角ψ越大,对车刀后角的影响也越大。
这种影响会在车削梯形螺纹或螺距较大的螺纹时反映的更加明显。
2、螺纹升角ψ对车刀两侧前角的影响(22分钟) 还是以6人为一组,每组一把外螺纹车刀。
让学生将大屏幕上的图片和车刀作联系,分析两种不同的装刀法,车刀前刀面和前角的变化。
(约4分钟)
图6-15 螺纹升角对车刀前角的影响
讨论1:为什么车螺纹时,车刀轴向装刀时两侧前角数值不相同?(约6分钟)
由于螺纹升角的影响,使车刀前刀面在截面上的投影与基面不重合,从而使车刀轴向装刀时前角的数值不相同,即左侧为正,右侧为负。
车削右旋螺纹时,★①左刀刃在工作时是正前角,切削刃比较锋利,切削顺利;★②右刀刃在
工作时是负前角,切削刃处于挤刮状态,不仅切削费力,且排屑也困难。
讨论2:轴向装刀有弊端,如何改善? (约7分钟)
为了改善上述状况,我们可以★①采用图6-15b 所示的方法,即采用法向装刀法安装车刀,将车刀两侧切削刃组成的平面垂直于螺旋线装夹。
这时两侧刀刃的工作前角都为00;★②在前刀面上沿两侧切削刃上磨有较大的卷屑槽(图6-15c 、d ),使切削顺利,并有利于排屑。
通过例题来巩固新知识,运用新知识。
为讲授车削梯形螺纹
和蜗杆打下伏笔。
介绍轴向装刀和法向装刀的方法。
在大屏幕上展示图6—
15。
点击课件演示。
分组讨论,引导学生得到左侧★结论。
在整个讨论过程中切
忌轻易否定不同的、甚
至是错误的意见和见
解!
切削平面
基面
(轴向装刀) 基面(法向装刀)
教案用纸附页
总结:
(约2分钟)
① 车刀轴向装刀工作时两侧前角
γ
工作L
= -γ
工作R
≠0
② 车刀法向装刀工作时、静止时两侧前角
γ0L =γ
0R
= 00
★③ 粗车时采用法向装刀,精车时采用轴向装刀。
这样既能顺利的进行粗车,又能保证精车后螺纹牙型的准确性。
3、径向前角γP 对车削螺纹牙型的影响(20分钟)
当径向前角γP = 00
时,螺纹车刀的刀尖角
εr 应等于螺纹的牙型角α。
(1)解释:什么是径向前角? (约1分钟) (2)指出:径向前角在车刀模型上的具体位置。
(约2分钟)
在实际工作中,我们一般采用γP = 50 ~ 150高速钢螺纹车刀。
图6-16 螺纹升角对车刀前角的影响
a )γP = 00
b )γP > 00
c )θ/2 > εr /2
引导学生得到左侧结论。
为讲授修正螺纹牙型埋下伏笔
教具:车刀模型。
注意看图b )、图c)
在大屏幕上展示图6-16。
教 案 用 纸 附 页
教 学 内 容、 方 法 和 过 程
附 记
课间休息
(3)径向前角γP 对车削螺纹牙型的影响 (约9分钟) 由于螺纹车刀两侧切削刃不与工件轴向重合,刀刃不通过工件轴心线,使
得车出工件的螺纹牙型角α大于车刀的刀尖角εr ,因此,被切削的螺纹牙型在轴向剖面内不是直线,而是曲线,会影响螺纹副的配合质量。
径向前角γP 越大,牙型角的误差也越大。
若车削精度要求不高的螺纹,其车刀允许磨有较大的径向前角(50~150
),但必须对车刀两刃夹角εr 进行修正,其修正值可参见表6-12,也可根据图6-16
按下式进行修正计算:(表6-12及公式见教材)
(4)用样板检验刀尖角 (约7分钟) 用计算方法或通过查表,虽然可以得到比较正确的修正后的刀尖角度,但
在现场工作中还是比较麻烦。
我们可以用一种但厚度较厚的特制的螺纹样板(样
板的角度等于牙型角)来测量刀尖角。
图6-23 用样板修正两刃夹角
a) 正确 b) 错误 c) 测量示意
1——样板 2——螺纹车刀
注意:刀尖角是在基面..内测得的。
应将样板与车....刀底平面平行......,再用透光法...
检查,图6-23a )。
这样测出来角度,车削时已是投影角度。
总结: (约1分钟)
①γ
P = 0
,
εr = α ; ②γ
P > 0
,
εr < α,要修正εr 。
订正:教材P164页倒
数第3段第2行少一
“刃”字。
γP >00会导致牙型角
误差。
引用教材原文
在大屏幕上展示图
6-23。
先请同学们把左手假
想成样板,来测量手头
的车刀。
再请一位做的比较好
的同学作示范。
引导同学们得到左侧结论。
教案用纸附页
教学内容、方法和过程附记4、常用各种形式三角形螺纹车刀(20分钟)
图6-18 常用三角形螺纹车刀
a)、b)整体式内螺纹车刀c)、d) 装配式内螺纹车刀
e) 装配式外螺纹车刀f) 整体式外螺纹车刀
(1)看大屏幕分辨内、外螺纹车刀形状。
(约2分钟)(2)提问:展示各种实物内、外螺纹车刀,请同学们将内螺纹车刀分辨出来。
(约2分钟)(3)常见的高速钢外螺纹车刀。
(约4分钟)请同学们注意看车刀角度(图6-19),找到它们的区别。
然后提问某位同学,让其指出。
(区别:γP不同;刀尖圆弧半径不等。
)
图6-19 高速钢三角形外螺纹车刀
a)粗车刀 b)精车刀
讨论:为什么粗、精车刀的径向前角不同且刀尖圆弧半径不等?(约5分钟)(先让同学们回忆所学外圆车刀内容,以及本节课所讲内容,然后启发、引导同学们找到答案。
)在大屏幕上展示图6-18,分辨内、外螺纹车刀形状。
演示课件,找到区别。
在大屏幕上展示图6-19。
还是先前的分组,请一到两位代表回答。
教案用纸附页
(4)常见的硬质合金外螺纹车刀。
(约5分钟)
图6-20 硬质合金三角形外螺纹车刀
请同学们注意看车刀角度:
γ
P
= 0 0;α0 = 4 0~ 6 0;0.2~ 0.4mm宽,γ01 = -5 0的倒棱;εr = 59030′。
思考:为什么硬质合金螺纹车刀要磨出-50的倒楞?
①与硬质合金本身的性质有关;②增强车刀刀体强度。
注意:在高速切削时,牙型角会扩大,所以刀尖角要适当减少30′,另外车刀的前刀面及后刀面的表面粗糙度值必须很小。
(5)内螺纹车刀。
(约2分钟)关于内螺纹车刀,要注意以下几点:
①根据所加工内孔的结构特点来选择合适的内螺纹车刀,内螺纹车刀刀体的径向尺寸应比螺纹孔径小3 ~ 5mm;
②要提高内螺纹车刀的刚性和解决排屑问题;
③内螺纹车刀的刀刃几何形状应具有外螺纹刀尖的几何形状特点。
其余请同学们在下课后自己看书,这里不再赘述。
在大屏幕上展示图6 - 20。
让同学们自己分析原因,然后启发、引导同学们找到答案。
教案用纸附页。