冷轧板制管麻点缺陷成因及其预防措施
冷轧不锈钢质量控制及常见缺陷预防论述

冷轧不锈钢质量控制及常见缺陷预防论述随着工业化进程的加快,不锈钢的需求越来越大,而冷轧不锈钢由于具有优良的耐腐蚀性、耐热性、美观性等特点,因此在各行各业得到广泛应用。
但是,不锈钢在生产过程中容易出现各种缺陷,影响质量,因此,研究冷轧不锈钢的质量控制及常见缺陷预防是十分必要的。
本文将从以下几个方面进行探讨:一、冷轧不锈钢质量控制不锈钢生产过程中的质量控制主要包括原料控制、生产过程控制、检验控制和质量管理等四个方面。
其中,原料控制的关键是对原料的化学成分进行检查,以确保原材料符合国家标准。
在生产过程中,需要对生产环境、生产设备、人员素质和生产流程进行控制,确保机器运行稳定,环境整洁卫生,工人操作规范等。
同时,在检验和质量管理方面,需要严格把控各个环节,遵循标准化的检验流程,以保证成品质量可靠。
二、冷轧不锈钢常见缺陷1. 表面缺陷表面缺陷是较为常见的一种不锈钢缺陷。
主要是指钢板表面出现坑洼、斑点、伤痕、起泡、杂质等问题。
2. 化学成分不合格化学成分不合格通常指钢板中的元素含量不符合标准,如钼、钴、铝等成分的含量不足或超标,这会导致不锈钢耐腐蚀性不佳、强度及硬度差等问题。
3. 热处理不当不锈钢的热处理涉及温度、时间、冷却速率等因素,如果问题出现,则会引起不锈钢的形状不稳定,脆性增加等现象。
4. 噪音过大钣金加工过程中,耳膜损伤是一个不容忽视的问题,噪音过大会促进物理变化的发生,从而影响不锈钢板的质量。
三、常见缺陷预防措施为预防冷轧不锈钢的各类缺陷,需要采取以下几种措施:1. 严格执行生产流程,确保各环节质量稳定;2. 对生产过程进行盲审,以防止环境污染和机器故障等因素影响不锈钢质量;3. 严格按照标准化检验流程进行检验,防止不合格不锈钢流入市场;4. 在制造过程中注意产品匹配,任何一级产品的质量问题都可能影响到最终的成品质量。
总之,冷轧不锈钢的质量控制和缺陷预防是十分重要的。
只有严格管控各个环节、严格遵循标准化检验流程,才能保证不锈钢板质量稳定,并在市场上取得更好的竞争优势。
冷轧板表面缺陷成因及预防措施

还是塑性水平都不十分均匀 , 以上述缺陷只是 所
局 部表 现 出来 。 3 3 对 冷轧 生 产的建 议 .
为避免 冷轧 板 表 面 出 现块 状 和亮 线 缺 陷 , 冷 轧 生产 首先 应 把道 次 最 大 轧 制 力 减小 , 以避 免产 生 过 大 的剪 切 力 , 致 轧 材 被 破 坏 。 当这 一 改进 导 不 能起 到应 有 作用 时 , 考 虑在 轧 制 中间 增加 一 可 次 中间退火 , 以使轧 材 的塑性 得 以 回复 , 就完全 这 可 以避免此 类 事故 。
亮线的边缘部位用刀片划线标记 , 以便于观察。1 号试样 电镜分析后沿纵 向磨制进行金相分析 , 4
号试 样 沿横 向磨 制 。
送 检 的两块 钢板 编 号 分 别 是 00 06 8575规 格
0 6 m ×8 0 i 0 0 0 5 规 格 0. m × .m O h m和 8 5 7 9 5 m
4 结 论
位错密集形成的亚裂纹线条。这些都证明 , 钢板
表 面的缺 陷是 冷轧 裂纹 。
长度较大的裂纹存在变形痕迹 , 裂纹两侧的 晶粒 度完 全不 同 , 明裂 纹两 侧 的变形 量 不一样 。 说
也就 是说 , 纹形 成后 , 裂 钢板 仍 旧继续 变形 。通 过 以上 分析 可 以推 测 , 部 分 裂纹 并 不 是 冷 轧 的最 大 后道 次形 成 , 而是 发生 在前几 道 次 。
通 过 以上分 析 可 知 , 轧 板 表 面 的块 状 缺 陷 冷 和 条状亮 线 属 于 同一 种 缺 陷 , 即冷 轧 板表 面 的局 部破 损 , 只是 严重 程度 和密 集程 度有 差别 。
2 3
N . o4
De e e 0 8 c mb r2 0
退火冷轧钢带产品表面缺陷、产生部位及预防措施
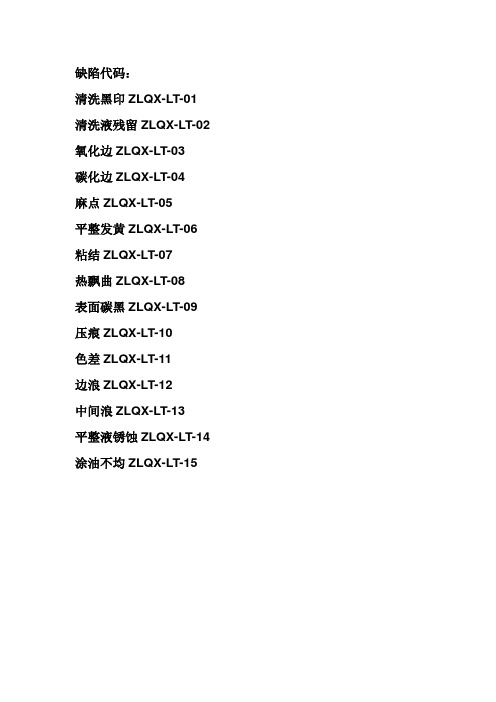
缺陷代码:清洗黑印ZLQX-LT-01 清洗液残留ZLQX-LT-02 氧化边ZLQX-LT-03碳化边ZLQX-LT-04麻点ZLQX-LT-05平整发黄ZLQX-LT-06 粘结ZLQX-LT-07热飘曲ZLQX-LT-08表面碳黑ZLQX-LT-09 压痕ZLQX-LT-10色差ZLQX-LT-11边浪ZLQX-LT-12中间浪ZLQX-LT-13平整液锈蚀ZLQX-LT-14 涂油不均ZLQX-LT-15缺陷代码ZLQX-LT-01缺陷名称清洗黒印缺陷特征钢带经过清洗机组后,沿带钢轧制方向有表面残留黑色痕迹产生部位板带表面任何部位原因分析沉没辊表面衬胶脱落,胶质粘在带钢表面,产生黑色痕迹。
处理措施及时定期更换沉没辊。
质检判定标准备注缺陷代码ZLQX-LT-02缺陷名称清洗液残留缺陷特征经过清洗机组后,钢带表面残留的清洗液,呈片状,退火前不明显,退火后呈现白色斑迹。
产生部位板带表面任何部位原因分析刷辊或挤干辊故障,及漂洗段电导率高处理措施刷辊或挤干辊定期更换。
漂洗段电导率及时调整质检判定标准备注缺陷代码ZLQX-LT-03缺陷名称氧化边缺陷特征从边部向中间部位逐渐变淡的黄褐色或蓝色痕迹,无明显的轮廓线产生部位一般在版带的边部原因分析出炉温度过高,罩式炉快速冷却水漏水,保护气体露点过高处理措施严格工艺规程规定的出炉温度,保证保护气体的露点温度。
出现氧化边可回罩式炉进行返修退火质检判定标准备注缺陷代码ZLQX-LT-04缺陷名称碳化边缺陷特征颜色呈黑灰色,用手擦不掉,碳与基板发生化学反应,不溶于酸,又称蛇形迹。
连续或间断分布。
产生部位一般分布在钢卷(退过火)的两边原因分析轧制油挥发温度过高或乳液系统调整不当,在退火过程中碳与氢分解成自由碳析出。
露点过高。
工艺润滑系统设备运行不正常。
处理措施根据原因分心采取相应的对策。
重新调整乳化液的温度浓度。
可以考虑换新的轧制油。
质检判定标准备注缺陷代码ZLQX-LT-05缺陷名称麻点缺陷特征带钢表面有局部或者连续的粗糙面,有些呈桔子皮状凹麻点,在灯光下呈亮晶晶小凹坑。
热、冷轧板带材质量缺陷类别、原因及措施

1.粉末烧结板坯密度不均匀;2.由于热轧开坯时道次加工率小造成不均匀变形,致使产生分层,带入冷轧。3.中间退火不均匀。
1.保证板坯质量;2.控制好热轧工艺;3.改进退火工艺
10
针孔
由于环境卫生不好,粉尘颗粒落到轧件表面,轧制时致使压透箔材而形成微波孔眼
保持良好的环境卫生,加强文明生产。轧前坯料要认真清洗和检查
冷轧板、带材常见缺陷及消除方法
序号
缺陷名称
产生原因
消除方法
1
表面裂纹
1.来料表面裂纹未清除干净,冷轧时继续扩展;
2.来料表面脆性吸气层未清除,轧制时表面层与内层金属变形不一致,使表面被拉裂;
3.压下规程不合理,道次加工率过小,道次太多,使表面硬化太快,轧制时开裂;
4.道次加工率分配不均,造成严重地不均匀变形使局部拉裂。
11
表面粗晶和条状组织
经挤压、锻造的钼及其合金板坯,如果加工率不足或以后退火时,未能达到充分再结晶,轧时易出现此类缺陷
开坯时要给予足够的变形,提高退火温度或增长保温时间,使再结晶充分进行
12
厚度超差
1.量尺寸时不精确或量具不准确,误差过大;2.压下装置未调整好或指针不准确。
1.测量应细心,量具要准确;2.调整好压下装置,校正压下指针。
7
裂边
1.来料裂边未除净,轧制扩展了;2.冷轧加工率过大,边部被拉裂;
3.轧辊曲线配置不当;4.退火不均匀。
1.来料剪裂边要除净;2.调整压下规程;
3.配置好轧辊曲线;4.改进退火工艺。
8
表面起皮
1.道次加工率过小,轧制道次过多;
2.粉末烧结板坯,烧结密度偏低。
1.调整压下规程;2.保证板坯质量。
9
冷轧板夹杂类表面缺陷成因分析及控制
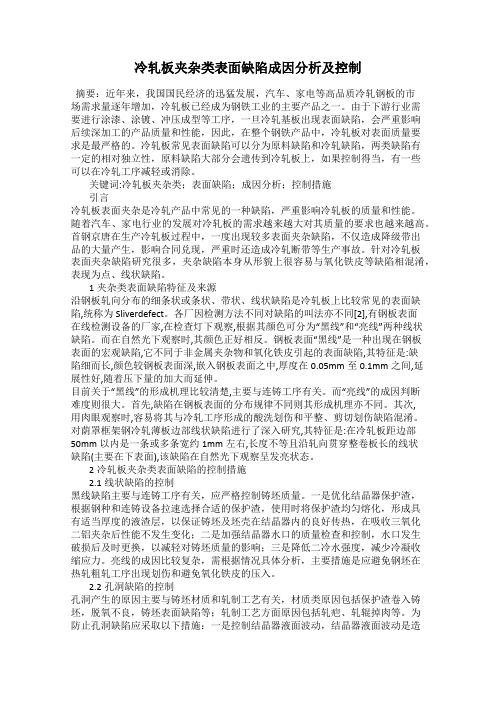
冷轧板夹杂类表面缺陷成因分析及控制摘要:近年来,我国国民经济的迅猛发展,汽车、家电等高品质冷轧钢板的市场需求量逐年增加,冷轧板已经成为钢铁工业的主要产品之一。
由于下游行业需要进行涂漆、涂镀、冲压成型等工序,一旦冷轧基板出现表面缺陷,会严重影响后续深加工的产品质量和性能,因此,在整个钢铁产品中,冷轧板对表面质量要求是最严格的。
冷轧板常见表面缺陷可以分为原料缺陷和冷轧缺陷,两类缺陷有一定的相对独立性,原料缺陷大部分会遗传到冷轧板上,如果控制得当,有一些可以在冷轧工序减轻或消除。
关键词:冷轧板夹杂类;表面缺陷;成因分析;控制措施引言冷轧板表面夹杂是冷轧产品中常见的一种缺陷,严重影响冷轧板的质量和性能。
随着汽车、家电行业的发展对冷轧板的需求越来越大对其质量的要求也越来越高。
首钢京唐在生产冷轧板过程中,一度出现较多表面夹杂缺陷,不仅造成降级带出品的大量产生,影响合同兑现,严重时还造成冷轧断带等生产事故。
针对冷轧板表面夹杂缺陷研究很多,夹杂缺陷本身从形貌上很容易与氧化铁皮等缺陷相混淆,表现为点、线状缺陷。
1夹杂类表面缺陷特征及来源沿钢板轧向分布的细条状或条状、带状、线状缺陷是冷轧板上比较常见的表面缺陷,统称为Sliverdefect。
各厂因检测方法不同对缺陷的叫法亦不同[2],有钢板表面在线检测设备的厂家,在检查灯下观察,根据其颜色可分为“黑线”和“亮线”两种线状缺陷。
而在自然光下观察时,其颜色正好相反。
钢板表面“黑线”是一种出现在钢板表面的宏观缺陷,它不同于非金属夹杂物和氧化铁皮引起的表面缺陷,其特征是:缺陷细而长,颜色较钢板表面深,嵌入钢板表面之中,厚度在0.05mm至0.1mm之间,延展性好,随着压下量的加大而延伸。
目前关于“黑线”的形成机理比较清楚,主要与连铸工序有关。
而“亮线”的成因判断难度则很大。
首先,缺陷在钢板表面的分布规律不同则其形成机理亦不同。
其次,用肉眼观察时,容易将其与冷轧工序形成的酸洗划伤和平整、剪切划伤缺陷混淆。
冷轧产品缺陷及预防介绍
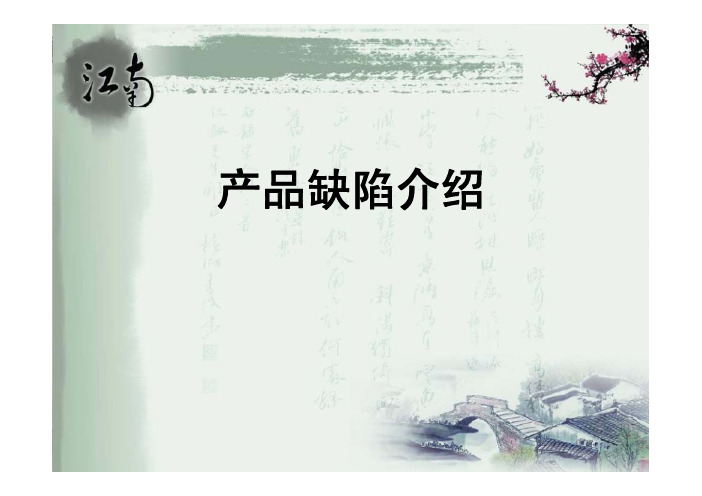
产品缺陷介绍一、冷轧产品缺陷1、表面夹层1、缺陷特征表面夹层形状不规则,呈片状折叠并伴有非金属夹杂物。
2、产生原因表面夹层是由连铸工序中非金属夹杂导致,开始存在与皮下,加工后暴露于外。
2、孔洞1、缺陷特征孔洞是材料非连续的、贯穿带钢上下表面的缺陷。
2、产生原因材料撕裂产生孔洞。
钢质不纯,有非金属夹杂物,轧制后会出现孔洞。
带钢越薄,其现象越明显。
3、氧化铁皮1、缺陷特征氧化铁皮压入是由热轧中被轧入带钢表面的氧化铁皮引起的,氧化铁皮可在酸洗工序中去除,但留下的印点在冷轧过程中也不能完全消除,这种缺陷的外观可为麻点、线痕或大面积的压痕。
2、产生原因氧化铁皮压入是由于热轧除鳞高压水压力不够,氧化铁皮被轧入带钢。
4 、乳化液斑1、缺陷特征乳化液斑是残留在带钢表面的裂化乳化液。
它们随机地分布在带钢表面,形状不规则,颜色发暗。
2、产生原因乳化液斑是残留在带钢表面的乳化液发生裂化作用。
由于在退火过程中残余的乳化液没有被完全蒸发,带钢上多余的乳化液没有被吹净。
5、辊印(凸起)1、缺陷特征凸起辊印是在带钢表面周期性的点状凸起。
2、产生原因凸起辊印是由于冷轧或平整过程中工作辊上有压痕造成的。
6、辊印(凹入)1、缺陷特征凹入辊印在带钢表面呈一定周期性的压痕或印痕。
2、产生原因由工作辊粘有杂物引起。
7、边浪、中浪1、缺陷特征边浪和中浪是沿轧制方向产生的波浪,未扩展到整个带钢宽度。
2、产生原因由辊缝形状与轧件入口形状不匹配造成。
可能是入口轧件有凸度或辊缝设置不合理;也可能是支撑辊凸度或支撑辊位置不合适。
边浪也可能由于园盘剪刀片位置不合理造成。
8、隆起1、缺陷特征隆起是沿轧制方向带状增厚,特别是当带钢被卷起时,可导致不均匀的程度增加;在极端情况下,隆起可能导致波浪、厚度起伏、带卷破裂。
2、产生原因隆起主要发生在热轧机上,而且一旦发生,则在随后的冷轧中也不能消除。
因为钢卷取时,厚度增加会因放大效应而变的越来越明显。
9、氧化色1、缺陷特征氧化色发生在退火后的冷轧带卷上。
冷轧卷表面麻点缺陷分析及防治

作 者:李宗强,硕士研究 生,工程 师,现 主要从 事
炼钢 工 艺研 发 工作 。
量均值 ,W ( A 1 2 0 ) :
9 . 9 % ;W ( C a O ) :1 7 . 8 % ;W ( K 2 0 ) :1 2 . 6 %。参
的原 因 ,提 出相 应 的防治 措施 。
形 状 为 圆形 或 椭 圆形 , 目视 麻 点 较 深 。 某 钢 卷
麻 点孔 径 范 围 3 0 0 9 0 0 m,最 大 深 度 为 8 l m,用 扫描 电镜 检 测麻 点 缺 陷部 位 、基 体部 位
表 面 。麻 点 微 观 呈 凹 凸 不 平 状 ,质 地 粗 糙 ( 见
一
冷轧卷表 面麻 点缺陷分析及 防治
李 宗强 樊 雷
( 技术 中心 )
摘
要 :柳钢冷轧卷常见表 面麻点缺 陷主要是 夹杂物、氧化铁皮压入 、擦 伤 ,介 绍缺 陷形貌 ,
分析 产 生原 因 ,提 出防 治措施 。
关键 词 :冷轧卷 ;麻 点 ;夹杂物 ;氧 化铁 皮 ;擦 伤
Ana l ys i s a nd Tr e a t me n t f o r t he Pi t t i n g De f e c t o n t he
缺 陷宏 观 描 述 :对 冷 轧 板 进 行 切 块 、高 速 旋 压 成型 后 ,麻 点缺 陷暴 露 ( 见图 1 a ) ,仅 出现 在 钢 卷 一 面 局 部 区 域 ,为 黑 灰 色 呈 簇 状 分 布 ,
形成皮下夹杂 ,在使用旋压加工过程脱 落形成
孔 洞【 ” 。
假设 麻 点 部 位 检测 的夹 杂 物全 部 由 A l 、s i 、 K、C a等 非 金 属 氧 化 物 构 成 ,计 算 4种 物 质 含
冷加工缺陷

冷轧时钢管的缺陷、产生原因及消除办法一、二辊式冷轧管机轧管缺陷二辊式冷轧管机轧管时最常出现的产品缺陷有:折叠,凹陷,过大的波纹,内表面上的凹陷和擦伤,直径和壁厚的超差以及壁厚不均,等。
1.1 折叠在机架的正行程中,金属进到了扎槽块之间的间隙中,在工作锥的侧表面上形成了耳子。
在机架的返行程时,这些耳子被轧槽块压到工作锥的表面中去。
所形成的缺陷就是折叠。
由于轧制时管料在一个轧制周期中要回转一次,所以折叠在管子表面呈螺旋分布。
轧槽块之间的间隙太大,间隙分布不均匀,孔型各部分的宽度不够,芯棒尺寸同孔型形状不相符合,送进量大小不均匀或者管料猛进以及管料停止回转等,这些原因都会促使在工作锥上形成侧面耳子和在管子表面上形成折叠。
如果轧槽块之间的间隙大大,应该重新调整间隙。
当孔型各个部分的宽度不够时,可以找出金属被孔型凸缘“啃掉”的地方,并用风动砂轮研磨孔型,加大孔型宽度较小部分的开口度。
芯棒尺寸同孔型形状不符会引起金属的集中压下而出现耳子。
为了消除这种现象,可换上芯棒圆锥母线斜度较大的芯棒。
在送进量大小不均匀或者在管料猛进的情况下,应该消除它们产生的原因。
如果管料停止了回转可调整一下前卡盘。
1.2 凹陷管子表面上的凹陷多发生在孔型的预精整段部分以及当机架返行程时管子不在芯棒上辊轧的情况下。
形成凹陷的原因是:轧槽块之间的间隙太大和孔型预精整部分侧壁的开口太陡,轧槽块在水平面内互相错开以及轧槽块表面上有缺陷等。
凹陷多半出现在轧制薄壁管时。
当轧槽块之间的间隙太大和孔型预精整部分侧壁开口太陡时,在机架的正行程中金属充满了孔型的侧壁开口部分并被孔型的凸缘切割,被切割部分的金属在返行程轧制时被压到管子的表面下而形成凹陷。
由于管子回转,管子表面上的凹陷一般呈螺旋分布。
当轧槽块两侧的间隙不等时,凹陷可能只出现在管子的一侧。
为了避免凹陷的产生必须减小出现凹陷处的轧槽块之间的间隙,同时研磨孔型预精整部分的侧壁开口,减小它的陡度。
冷拔管常见缺陷、产生原因及预防和消除方法

[选取日期]冷拔无缝钢管常见的缺陷特征产生的原因及预防和消除方法2010年10月08日孟相欣冷拔无缝钢管常见的缺陷特征产生的原因及预防和消除方法一、折迭拔制后,钢管内外表面呈现直线或螺旋方向的折迭,局部或通长的出现在钢管上。
产生的原因:管料表面有折迭或夹杂物,有严重擦伤和裂纹,管料磨修处有棱角或深宽比(H/b)不够。
预防和消除方法:严格把好穿孔热轧质量关。
二、尺寸超差(包括壁厚超差,壁厚不均,直径超差,椭圆偏心)直径超过了标准的偏差,在同一截面上管壁一边薄,一边厚,直径不等,长短轴之差超出标准规定。
产生的原因:1、拔制模具选择不当,或芯棒(内模)调整不当。
2、内外模设计制造不合理或磨损严重,或硬度不够造成变形磨损。
3、热处理时间长,温度高,或热处理性能不均匀。
4、增减壁的规律控制不当。
5、拔制表编制不合格。
6、钢管矫直时被压扁,造成误差较大。
预防和消除方法:1、正确设计和选配拔管模具。
2、正确执行热处理制度,均匀加热。
3、正确调制矫直机,经常校对拔管机各部件和量具。
4、掌握不同钢种、不同规格钢管的增减壁规律。
5、正确合理编制拔制表。
6、椭圆度出格可重新矫直,局部椭圆度出格可切除。
三、划道钢管表面上呈现纵向直线的划痕称为划道,划道长短不一,宽窄不等,多为沟状,可见沟底。
产生的原因:1、拔模表面不光滑,有裂纹或粘结金属。
2、锤头过度部分有棱角,工具磨损。
3、欠酸洗或毛管上残存氧化铁皮。
4、磷化、皂化工序操作不当。
5、内外模以损坏或磨损严重。
6、中间退火不均,变形量不足。
预防和消除方法:1、提高拔管模具的表面质量。
2、钢管酸洗后,氧化铁皮要冲洗干净。
3、锤头过度部分要圆滑无棱角。
4勤检查模具和钢管的表面,发现问题及时处理。
四、斗纹钢管表面沿长度方向呈高低不平的环形波浪或波浪逐个相同排列,局部或通长出现在钢管内外表面上。
产生的原因:1、热处理后的性能不均,热轧时低温钢造成性能不均。
2、酸洗后冲洗不干净,磷化不良导致皂化不均。
冷轧镀锌板典型表面质量缺陷成因及控制措施

冷轧镀锌板典型表面质量缺陷成因及控制措施摘要:冷轧镀锌板表面质量缺陷有常规缺陷和非常规缺陷,常规缺陷其原理没有非常规缺陷那么复杂,比较容易去判断和掌握这门工艺。
冷轧板原料缺陷很大一部分源于炼钢,常见微观检验,发现内部有异常高含量的Na、Mg、Al的深冲、超深冲用的外来成分。
冷轧产品的质量是决定市场的主要原因,想要占领更加广阔的市场就要解决产品夹杂缺陷的问题,提高生产产品的质量,而有效措施主要是钢质种、纯净化、精炼工艺优化、连铸横拉速操作、铸坯表、夹杂面清理等。
关键词:冷轧镀锌板典型案例质量缺陷原因和解决方法采用了一系列高科技试验手段,如SEM、EDS等,研究了冷轧镀锌板典型的表面质量缺陷成因以及相对应的控制措施。
根据调查结果显示:油脂类物质残留可导致冷轧镀锌板表面漏镀缺陷,氧化铁颗粒压入机器会引起表面黑点缺陷,机械划伤可造成表面线状缺陷,保护渣卷入致使镀锌板表面出现孔洞缺陷,这些缺陷不仅在很大程度上影响了冷轧镀锌板的技术,而且大大降低降低了工作效率,因此本文阐述了镀锌板各类表面缺陷的形成机理,并提出了相应缺陷的控制处理措施和解决方案。
一、冷轧镀锌板生产中的缺陷及原因1.1锌粒缺陷锌锅中锌渣粘到钢板表面引起了有关于锌粒缺陷的许多繁琐问题。
这项缺陷是热镀锌产品所具有的质量缺陷中比较常见的一项,它在一定程度上对热镀锌产品的外观和质量造成了影响。
因为气刀气流的影响,容易产生一定的吸引力吸着周围的灰尘从而产生了浮渣,锌液发生氧化造成了锌粒缺陷。
底渣之所以产生主要是因为铁在锌液中超过饱和浓度,出现铁与锌结合生成铁锌合金的现象,随之就会产生沉淀。
在带钢表面分散着多种多样的颗粒,米粒状或不规则的形状,这是锌粒缺陷的主要特征。
这样的缺陷在降低锌镀层美观度的同时光学表面造成了一定程度的伤害,加快了镀层表面的腐蚀程度,根据一系列的实验数据结果,分析得到了导致锌粒缺陷产生的很大一部分原因是,锌液中只含有少量的铝,但是却含有大量的铁,因此游离渣和面渣会在锌液中大面积存在。
冷轧产品缺陷及预防

12孔洞 英:Holes
【定义与特征】 钢带表面非连续的、贯穿钢带上下表面的缺陷。一般 位于钢带的中部或边部,大多呈串状分布。 【原因分析】 材料撕裂产生孔洞,在轧制过程中,带钢断面局部 疏松,该处的应力超过材料的变形极限。带钢越薄, 其现象越明显。由于浇铸中夹杂、气泡、缩孔等,在 以后的轧制过程中虽着厚度的减薄使带钢局部破裂; 由于轧制不均而导致局部周期性韧性撕裂。 【鉴别与判定】 可用肉眼判定,引起孔洞的原因可用金相方法查明, 不易与其他缺陷混淆。
【鉴别与判定】 可用肉眼判定,不易与其他缺陷 混淆 【消除对策】 设备故障排除时间缩短。 严格控制酸洗工艺,按规程要求控制好 酸液浓度、温度、工艺段速度。
7停车斑 英:Stoppage marks
【定义与特征】 停车斑是酸洗线停车时,由于化学物质沾在钢带表面 形成大片斑迹。可分布在钢带的任何位置。 【原因分析】 在酸洗线上,如果带钢停留或在太低速度下运行,则 可能发生停车痕迹。 【鉴别与判定】 可用肉眼判定,不易与其他缺陷混淆。
2.破鳞机操作不当,使铁皮未经充分疏松剥离。 3.酸洗工艺不适当,酸浓度偏低,温度低、酸液中亚 铁成份高或速度太快所致。 4.带钢有较大浪型或张力过大时钢板露出酸液面。 5.带钢在原料库存放时间过长,使带钢头尾腐蚀严 重
【鉴别与判定】 可用肉眼判定,不易与其他缺陷混淆。 【消除对策】 1.按酸洗工艺规程控制好酸洗液的浓度、 温度、速度。 2.根据热轧终轧温度的高低,选择合理 的工艺速度。 3.热轧要控制好终轧温度、卷取温度。
6过酸洗 英:Over pickled
麻点钢板文档 (2)

钢材表面缺陷之一,表现为产品表面呈凹凸不平的粗糙面,又称为麻面。
多连续成片,也有局部的或呈周期性分布的。
麻点是允许存在的缺陷,但其深度不得超过产品的厚度偏差的范围。
麻点产生的原因是:
(1)成品孔或成品前孔轧槽磨损,或粘有破碎的氧化铁皮等物;
(2)破碎的氧化铁皮被压入轧件表面后又脱落;
(3)轧辊锈蚀;
(4)坯料在加热过程中,表面被严重氧化。
1)换辊时,先检查轧辊,不使用严重锈蚀的轧辊,及时更换磨损的轧辊或孔型;
2)改进轧辊材质,保持轧槽冷却良好,采用工艺润滑剂(见塑性加工工艺润滑)以提高轧槽耐磨性能;
3)控制坯料加热操作,使炉内保持正压并减少氧化性气体。
对某些易氧化且氧化铁皮不易脱落的合金钢,应在钢坯表面加盖铁皮,保护加热;
4)在粗轧机前用高压水、压缩空气或铁刷子清除轧件表面的氧化铁皮.
板预处理、喷砂清理、耗用量、硬度、覆盖率、速度、效率
一、概述。
轧制缺陷及质量控制

轧制缺陷及质量控制一、引言轧制是金属加工过程中的重要环节之一,对于确保产品质量具有重要意义。
本文将详细介绍轧制过程中常见的缺陷类型及其产生原因,并探讨如何通过质量控制手段来预防和解决这些缺陷问题。
二、轧制缺陷类型及原因1. 表面缺陷表面缺陷是指轧制产品表面出现的瑕疵,如麻点、划痕、氧化皮等。
其主要原因包括:- 轧辊表面粗糙度不合格:轧辊表面粗糙度过高或过低都会导致产品表面出现缺陷;- 轧辊表面污染:轧辊表面存在杂质、油污等污染物会直接影响产品表面质量;- 轧制过程中的热裂纹:高温下,金属材料容易发生热裂纹,进而导致表面缺陷。
2. 尺寸偏差尺寸偏差是指轧制产品的尺寸与设计要求之间存在的差异。
常见的尺寸偏差包括过大或过小的厚度、宽度、长度等。
尺寸偏差的原因主要有:- 轧机设备调整不当:轧机设备的调整不当会导致产品尺寸偏差;- 材料厚度不均匀:原材料的厚度不均匀会直接影响轧制产品的尺寸;- 轧机辊系磨损:轧机辊系磨损会导致轧制压力不均匀,进而影响产品尺寸。
3. 内部缺陷内部缺陷是指轧制产品内部存在的缺陷,如气孔、夹杂物等。
内部缺陷的主要原因包括:- 原材料质量问题:原材料中存在气孔、夹杂物等缺陷;- 轧机设备故障:轧机设备的故障会导致轧制产品内部出现缺陷;- 轧制过程中的温度控制不当:温度控制不当会导致金属材料内部产生缺陷。
三、质量控制手段1. 轧辊表面处理为了避免表面缺陷的产生,可以采取以下措施:- 定期对轧辊进行磨削和抛光,确保其表面粗糙度符合要求;- 加强轧辊的清洁工作,防止污染物附着在轧辊表面;- 对轧辊进行定期检测,及时发现并修复轧辊表面的磨损和裂纹。
2. 轧机设备调整与维护为了控制尺寸偏差,需要进行轧机设备的调整与维护工作:- 对轧机设备进行定期的检查和维护,确保其工作状态良好;- 对轧机设备进行精确的调整,确保产品尺寸与设计要求一致;- 定期检测轧机辊系的磨损情况,及时更换磨损严重的辊子。
轧制缺陷及质量控制

轧制缺陷及质量控制一、引言轧制是金属加工中的一种重要工艺,用于将金属块材变形成所需的形状和尺寸。
然而,在轧制过程中,由于材料的特性和操作条件的不同,会产生一些缺陷,如裂纹、气泡、夹杂物等,这些缺陷会降低产品的质量和性能。
因此,进行轧制缺陷的控制和质量的监控是非常重要的。
二、轧制缺陷的分类1. 表面缺陷:包括划痕、麻点、皮膜剥离等。
2. 内部缺陷:包括裂纹、气泡、夹杂物等。
三、轧制缺陷的原因1. 材料因素:材料的化学成分、结构和纯度等会影响轧制过程中的缺陷形成。
2. 设备因素:轧机的结构、参数设置、润滑和冷却等条件会对轧制缺陷产生影响。
3. 操作因素:操作人员的技术水平、操作规程的执行等也会对轧制缺陷产生影响。
四、轧制缺陷的控制方法1. 材料选择:选择质量好、纯度高的原材料,减少缺陷的可能性。
2. 设备维护:定期对轧机进行维护和保养,确保设备的正常运行。
3. 工艺控制:控制轧制的温度、速度、压力等参数,减少缺陷的产生。
4. 检测方法:使用先进的无损检测技术,如超声波检测、磁粉检测等,及时发现和修复轧制缺陷。
5. 培训与管理:加强操作人员的培训,提高其技术水平和质量意识,严格执行操作规程。
五、质量控制体系建立完善的质量控制体系对于轧制过程中的缺陷控制至关重要。
以下是一个典型的质量控制体系的组成部分:1. 质量目标:明确轧制产品的质量要求,包括物理性能、化学成分等指标。
2. 质量计划:制定轧制过程中的质量控制计划,包括检测方法、检测频率等。
3. 质量检测:通过各种检测方法对轧制产品进行全面的检测,及时发现缺陷并采取措施修复。
4. 不良品处理:对于出现缺陷的产品,及时进行分类、记录和处理,以防止不良品流入市场。
5. 过程改进:根据质量检测结果和不良品处理情况,对轧制过程进行改进和优化,提高产品质量。
6. 内部审核:定期进行内部审核,评估质量控制体系的有效性和符合性。
7. 外部认证:通过第三方机构的认证,证明质量控制体系符合相关标准和要求。
冷拔管常见缺陷、产生原因及预防和消除方法

[选取日期]冷拔无缝钢管常见的缺陷特征产生的原因及预防和消除方法2010年10月08日孟相欣冷拔无缝钢管常见的缺陷特征产生的原因及预防和消除方法一、折迭拔制后,钢管内外表面呈现直线或螺旋方向的折迭,局部或通长的出现在钢管上。
产生的原因:管料表面有折迭或夹杂物,有严重擦伤和裂纹,管料磨修处有棱角或深宽比(H/b)不够。
预防和消除方法:严格把好穿孔热轧质量关。
二、尺寸超差(包括壁厚超差,壁厚不均,直径超差,椭圆偏心)直径超过了标准的偏差,在同一截面上管壁一边薄,一边厚,直径不等,长短轴之差超出标准规定。
产生的原因:1、拔制模具选择不当,或芯棒(内模)调整不当。
2、内外模设计制造不合理或磨损严重,或硬度不够造成变形磨损。
3、热处理时间长,温度高,或热处理性能不均匀。
4、增减壁的规律控制不当。
5、拔制表编制不合格。
6、钢管矫直时被压扁,造成误差较大。
预防和消除方法:1、正确设计和选配拔管模具。
2、正确执行热处理制度,均匀加热。
3、正确调制矫直机,经常校对拔管机各部件和量具。
4、掌握不同钢种、不同规格钢管的增减壁规律。
5、正确合理编制拔制表。
6、椭圆度出格可重新矫直,局部椭圆度出格可切除。
三、划道钢管表面上呈现纵向直线的划痕称为划道,划道长短不一,宽窄不等,多为沟状,可见沟底。
产生的原因:1、拔模表面不光滑,有裂纹或粘结金属。
2、锤头过度部分有棱角,工具磨损。
3、欠酸洗或毛管上残存氧化铁皮。
4、磷化、皂化工序操作不当。
5、内外模以损坏或磨损严重。
6、中间退火不均,变形量不足。
预防和消除方法:1、提高拔管模具的表面质量。
2、钢管酸洗后,氧化铁皮要冲洗干净。
3、锤头过度部分要圆滑无棱角。
4勤检查模具和钢管的表面,发现问题及时处理。
四、斗纹钢管表面沿长度方向呈高低不平的环形波浪或波浪逐个相同排列,局部或通长出现在钢管内外表面上。
产生的原因:1、热处理后的性能不均,热轧时低温钢造成性能不均。
2、酸洗后冲洗不干净,磷化不良导致皂化不均。
冷轧薄板质量缺陷图谱

性能问题预防: 提出预防性能 问题的措施和
方法
04
冷轧薄板质量缺陷预防 措施
原料控制
选用优质原料,保证原料质量
严格控制原料的化学成分和物料的纯净度和均匀性
定期对原料进行检验和测试, 确保原料质量稳定可靠
轧制工艺优化
优化轧制速度:提 高轧制速度,减少 缺陷产生
案例分析方法
观察缺陷特征:观察缺陷的外观、尺寸、位置等特征 分析缺陷原因:根据缺陷特征分析可能原因,如材料、工艺、设备等 制定改进措施:根据分析结果制定改进措施,如更换材料、调整工艺参数、维修设备等 验证改进效果:实施改进措施后,验证改进效果,确保缺陷得到解决
案例分析结果
缺陷类型:表面划 伤、凹坑、麻点等
02
冷轧薄板质量缺陷产生 原因
原料因素
原料质量:原料的纯净度、均匀性等对冷轧薄板的质量产生影响 原料处理:原料的加热、冷却、轧制等工艺过程对冷轧薄板的质量产生影响 原料成分:原料中的元素含量、合金元素等对冷轧薄板的质量产生影响 原料来源:不同来源的原料可能对冷轧薄板的质量产生影响
轧制工艺
轧制温度:影响薄板硬度和 韧性
凸起:表面出现凸起,影响 美观和使用性能
凹坑:表面出现凹坑,影响 美观和使用性能
划痕:表面出现划痕,影响 美观和使用性能
裂纹:表面出现裂纹,影响 美观和使用性能
腐蚀:表面出现腐蚀,影响 美观和使用性能
氧化:表面出现氧化,影响 美观和使用性能
尺寸偏差图谱
尺寸偏差的定义和分类 尺寸偏差产生的原因和影响因素 尺寸偏差的检测方法和标准 尺寸偏差的预防和控制措施
操作规范与培训
制定严格的操作规 范,确保员工按照 规范进行操作
对员工进行定期的 培训,提高员工的 操作技能和意识
冷加工缺陷

冷轧时钢管的缺陷、产生原因及消除办法一、二辊式冷轧管机轧管缺陷二辊式冷轧管机轧管时最常出现的产品缺陷有:折叠,凹陷,过大的波纹,内表面上的凹陷和擦伤,直径和壁厚的超差以及壁厚不均,等。
1.1 折叠在机架的正行程中,金属进到了扎槽块之间的间隙中,在工作锥的侧表面上形成了耳子。
在机架的返行程时,这些耳子被轧槽块压到工作锥的表面中去。
所形成的缺陷就是折叠。
由于轧制时管料在一个轧制周期中要回转一次,所以折叠在管子表面呈螺旋分布。
轧槽块之间的间隙太大,间隙分布不均匀,孔型各部分的宽度不够,芯棒尺寸同孔型形状不相符合,送进量大小不均匀或者管料猛进以及管料停止回转等,这些原因都会促使在工作锥上形成侧面耳子和在管子表面上形成折叠。
如果轧槽块之间的间隙大大,应该重新调整间隙。
当孔型各个部分的宽度不够时,可以找出金属被孔型凸缘“啃掉”的地方,并用风动砂轮研磨孔型,加大孔型宽度较小部分的开口度。
芯棒尺寸同孔型形状不符会引起金属的集中压下而出现耳子。
为了消除这种现象,可换上芯棒圆锥母线斜度较大的芯棒。
在送进量大小不均匀或者在管料猛进的情况下,应该消除它们产生的原因。
如果管料停止了回转可调整一下前卡盘。
1.2 凹陷管子表面上的凹陷多发生在孔型的预精整段部分以及当机架返行程时管子不在芯棒上辊轧的情况下。
形成凹陷的原因是:轧槽块之间的间隙太大和孔型预精整部分侧壁的开口太陡,轧槽块在水平面内互相错开以及轧槽块表面上有缺陷等。
凹陷多半出现在轧制薄壁管时。
当轧槽块之间的间隙太大和孔型预精整部分侧壁开口太陡时,在机架的正行程中金属充满了孔型的侧壁开口部分并被孔型的凸缘切割,被切割部分的金属在返行程轧制时被压到管子的表面下而形成凹陷。
由于管子回转,管子表面上的凹陷一般呈螺旋分布。
当轧槽块两侧的间隙不等时,凹陷可能只出现在管子的一侧。
为了避免凹陷的产生必须减小出现凹陷处的轧槽块之间的间隙,同时研磨孔型预精整部分的侧壁开口,减小它的陡度。
冷拔管常见缺陷产生原因及预防和消除方法
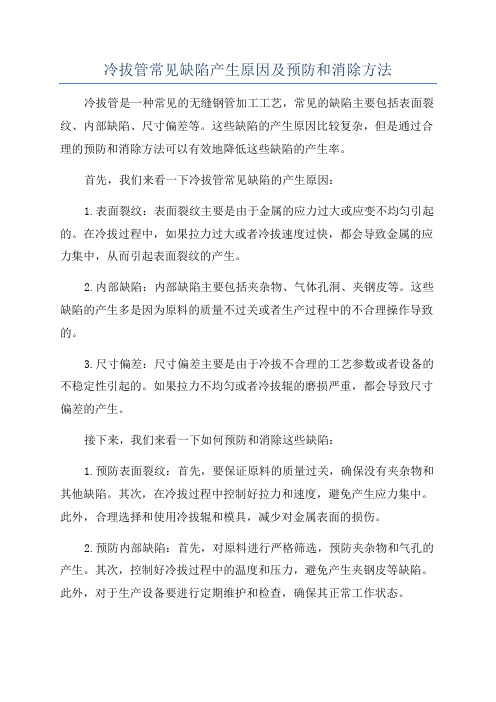
冷拔管常见缺陷产生原因及预防和消除方法冷拔管是一种常见的无缝钢管加工工艺,常见的缺陷主要包括表面裂纹、内部缺陷、尺寸偏差等。
这些缺陷的产生原因比较复杂,但是通过合理的预防和消除方法可以有效地降低这些缺陷的产生率。
首先,我们来看一下冷拔管常见缺陷的产生原因:1.表面裂纹:表面裂纹主要是由于金属的应力过大或应变不均匀引起的。
在冷拔过程中,如果拉力过大或者冷拔速度过快,都会导致金属的应力集中,从而引起表面裂纹的产生。
2.内部缺陷:内部缺陷主要包括夹杂物、气体孔洞、夹钢皮等。
这些缺陷的产生多是因为原料的质量不过关或者生产过程中的不合理操作导致的。
3.尺寸偏差:尺寸偏差主要是由于冷拔不合理的工艺参数或者设备的不稳定性引起的。
如果拉力不均匀或者冷拔辊的磨损严重,都会导致尺寸偏差的产生。
接下来,我们来看一下如何预防和消除这些缺陷:1.预防表面裂纹:首先,要保证原料的质量过关,确保没有夹杂物和其他缺陷。
其次,在冷拔过程中控制好拉力和速度,避免产生应力集中。
此外,合理选择和使用冷拔辊和模具,减少对金属表面的损伤。
2.预防内部缺陷:首先,对原料进行严格筛选,预防夹杂物和气孔的产生。
其次,控制好冷拔过程中的温度和压力,避免产生夹钢皮等缺陷。
此外,对于生产设备要进行定期维护和检查,确保其正常工作状态。
3.预防尺寸偏差:首先,要合理选择冷拔工艺参数,尽量保证拉力的均匀分布。
其次,定期检查和更换冷拔辊和模具,减少磨损对尺寸的影响。
此外,对于冷拔设备要进行定期维护和校准,确保其稳定性。
除了以上措施外,还可以通过加热退火、自动控制系统、成品质量检测等方法来预防和消除冷拔管的常见缺陷。
加热退火可以降低冷拔过程中的应力,提高内部结构的均匀性;自动控制系统可以实时监测冷拔过程中的各项参数,并进行调整;成品质量检测可以及时发现和修复缺陷,确保产品的合格率。
综上所述,冷拔管常见缺陷的产生原因比较复杂,但是通过合理的预防和消除方法可以有效地降低这些缺陷的产生率。
- 1、下载文档前请自行甄别文档内容的完整性,平台不提供额外的编辑、内容补充、找答案等附加服务。
- 2、"仅部分预览"的文档,不可在线预览部分如存在完整性等问题,可反馈申请退款(可完整预览的文档不适用该条件!)。
- 3、如文档侵犯您的权益,请联系客服反馈,我们会尽快为您处理(人工客服工作时间:9:00-18:30)。
图2b
1
93.63
6.37
2
97.23
2.77
3
69.66
30.34
——
4
62.60
31.18
1.47
3
100.00
4
—
82.46
15.95
1.59
—— —— ——
2.65
—— ——
2.10
——
缺陷管0.007
合格管0.054
Stl2标准要求
≤0.10
0.01 0.02 ≤0.05
0.15 0.27 ≤0.50
冷板在辊弯成型制成(I)22mm×1.Omm、垂22mm ×1.2ram、圣30mm×1.5ram钢管过程中,钢管外
表面金属发生的应变分别为4.55%、5.45%、 5.00%(曲率半径分别为11、11、15mm)。 2.4.3去应力退火材料再结晶过程分析
经完全再结晶退火的冷轧板在制管辊弯成型 过程中经历冷变形后再加热到再结晶温度(去应 力退火,温度800℃,退火时间40~50min)时,又 会发生相变。其再结晶晶粒的大小在很大程度上 取决于冷变形程度的大小[1],当钢板在临界变形 范围内加工时,材料的性能会恶化。金属材料的 临界变形量一般为2%~10%,但其具体的临界 变形量还受材料的化学成分、合金成分、原始晶粒 尺寸及第二相粒子等的影响。
1刮伤缺陷问题 某热轧带钢生产线轧制过程中带钢下表面出
现刮伤缺陷,形貌好似带钢表面被刮掉了一层皮 (见图1),被刮去部分充满了氧化铁皮,而缺陷表 面摸上去没有手感,但经酸洗后形成深浅不一的 小坑。生产中,需停轧较长时间打磨精轧入口/出 口夹送辊或检查轧线辊道表面,从而大大影响了 日历作业率和轧制产量。同时,由于停轧时间较 长,造成轧辊热凸度变化,导致开轧后前几块带钢
(武汉钢铁集团公司热轧带钢总厂。湖北武汉430080)
摘要:针对某热轧带钢生产线带钢下表面存在刮伤缺陷的问题,对轧制线标高、后滑系数、导卫标高进行了
优化计算,消除了热轧带钢下表面的刮伤缺陷,保证了带钢表面质量。
关键词:热轧带钢;刮伤缺陷;轧制线标高f后滑系数;导卫标高
中图分类号:TG335.5
文献标识码:B 文章编号:1003—9996(2010 J05一0052一03
万方数据
·52 ·
轧
料的临界变形区域,防止因晶粒粗大而导致麻点 缺陷的产生,具体措施如下:
(1)限定制管用Stl2冷轧板的碳含量下限, 避免由IF钢改判坯生产的Stl2冷轧板进入该类 制管用户,从而避免制管加工变形量正好位于材 料临界变形区域。
(2)采用由IF钢改判坯生产的Stl2冷轧板 生产其他直径规格的钢管,如采用厚1.0mm冷 板生产圣25mm以上或016mm以下规格钢管,
Abstract:The causes and preventive measures of pockmark in the process of making tube with cold rolled sheet were investigated.Results show that deformation degree in making tube with Stl2 produced by substandard IF steel is jUst in its critical deformation region,which causes extraordinary coarse grains after annealing and fi— nally forms the pockmark in drawing.Pockmark is effectively prevented by making deformation degree avoid critical deformation region. Key words:cold rolled sheet;welded tube;pockmark;critical deformation
0.010 0.016 ≤0.025
0.012 0.010 ≤0.025
0.04 0.08 0.01t0.10
此外,对所有出现麻点缺陷的Stl2冷轧卷冶 炼炉次进行了追溯性调查分析,结果表明其均为 由IF钢改判坯生产,碳含量均较低,属于超低碳 钢。钢厂在IF钢冶炼过程中,因某些因素的影响 导致其熔炼成分不能满足IF钢成分标准要求时, 若其符合Stl2成分要求,则一般均改判为Stl2
凸度、楔形超标。因此,为消除热轧带钢下表面刮 伤缺陷开展了大量改进工作。 2解决措施
热轧带钢下表面划伤缺陷与轧制线标高、轧 件后滑、导卫标高等有关,为此,对这些参数计算 进行了优化。 2.1轧线标高优化计算
该厂采用下阶梯垫调整轧线高度,使其在偏 差范围内,下阶梯垫结构示意图见图2。
收稿日期:2009—12一01 作者简介:昊进(1980一)。男(汉族).湖北大冶人,工程师。
对麻点缺陷及合格成品管均取样进行了化学 成分分析,其结果见表2。由表2可见,麻点缺陷 试样中碳含量很低,属于超低碳钢。
收稿日期:2010—02—24 作者简介:郭太雄(1972一),男(汉族),四川南部人,高级工程师,硕士。
万方数据
·50·
轧
钢
2010年10月出版
图2缺陷区域微观形貌
微观区域——i_———_表百l—缺—陷微 —观 —区下域—成』分堑分生析气结}果塑塑塑里菩鳖坚堑—1F———1i—T
钢
2010年10月出版
以减小或增大制管时的冷变形量,从而避开该类 材料的临界变形区域。
该精密焊管公司通过采用上述预防措施,基 本消除了Stl2冷轧板制管麻点缺陷的产生。
参考文献:
[17崔忠圻.金属学与热处理[M].北京:机械工业出版社,
1990.
热轧带钢刮伤缺陷的消除
吴 进,徐再新,周云松,蔡延擘,冉珠峰
Abstract:In view of the scratch defect of bottom surface of hot rolled strip,some calculation.settings were op- timized,including the rolling line elevation,backward creep coefficient,level of guide and guard.Based on it, the surface quality of strip can be assured. Key words:hot rolled strip;scratch defect;rolling line elevation;backward creep coefficient;level of guide and guard
万方数据
冷轧板制管麻点缺陷成因及其预防措施
作者: 作者单位:
刊名: 英文刊名: 年,卷(期):
郭太雄, 邓函, 赵孝章, GUO Tai-xiong, DENG Han, ZHAO Xiao-zhang 郭太雄,GUO Tai-xiong(攀钢集团,研究院有限公司,四川,成都,611731), 邓函,DENG Han(攀钢集团,攀枝花钢钒有限公司,四川,攀枝花,617022), 赵孝章,ZHAO Xiao-zhang(南 京钢铁股份有限公司,江苏,南京,330000)
攀枝花
617022;
摘要:通过对Stl2冷轧板制管过程中出现麻点缺陷处的形貌、微观化学成分和组织的分析.得出其原因是
制管加工变形量正好位于钢坯(由IF钢改判Stl2)的临界变形区域,因此钢管退火后晶粒异常粗大,拉拔时形
成了麻点缺陷。采取使制管加工变形量避开材料临界变形区域的措施,可有效预防麻点缺陷的产生。
在Stl2冷板制管的辊弯成型过程中,其中性 层纤维既不伸长,也不缩短,中性层以下的材料则 受拉而伸长,中性层以上的材料则受压而缩短。 断面上各层纤维的应变与其至中性层的距离成直 线关系,则钢管外表面的应变为:
厶
(p+姜)dO—pd口 ,
式中,P为中性层的曲率半径;^为钢板厚度。 由此可计算出厚度h=1.0、1.2、1.5ram的
钢种。 2.3金相组织分析
对麻点缺陷及合格成品管均取样进行了金相 组织及夹杂物分析,其结果见表3、图3。可见,出 现麻点缺陷的钢管其晶粒均异常粗大(仅局部表 层正常)。
试样
缺陷管 合格管
警—F—{幽型警—下 表3金相组织及夹杂物分析结果
金相组织
F
8.0(表层)0.5
0.5
0.5
0.5
F+P(少)8.5
GUO Tai—xiong“,DENG Han”。ZHAO Xiao-zhan92
(1.Pangang Group,a.Research Institute Co.,Ltd.,Chengdu 611731,China; b.Panzhihua Steel&Vanadium Co.,Ltd.,Panzhihua 617022,China: 2.Nanjing Iron&Steel Co.,Ltd.,Nanjing 330000,China)
1 前言 某精密焊管公司在使用Stl2冷轧板进行制
管的冷拔过程中出现麻点缺陷,缺陷宏观形貌如 图1所示。为此,对Stl2冷轧板制管冷拔麻点缺 陷成因进行了分析研究,并在此基础上提出了该 缺陷的预防措施。
图1缺陷管宏观形貌
2缺陷成因分析 2.1缺陷微观特征分析
将麻点缺陷样在JSM一5600LV扫描电镜下 观察,缺陷微观形貌如图2所示,采用INCA能谱 仪对微区成分分析的结果见表1。发现缺陷区域 较为粗糙,其成分主要是Fe、O元素,以及少量的 P、Zn、S、C1、Cu、T.i元素。图2a试样是铁基体及 其局部氧化形成,图2b试样是磷化膜残留或试样 局部被污染所致。缺陷区域成分未见异常。 2.2化学成分分析
因此,在该精密焊管公司制管加工工艺条件 下(变形量为4%~5%),正常的Stl2冷轧板制 管时避开了该材料的临界变形区域,而由IF钢改 判坯生产的Stl2冷轧板制管时则正好位于材料 的临界变形区域,致使去应力退火后材料晶粒异 常粗大,拉拔时形成了麻点缺陷,即麻面管。 3预防措施及实施效果