射线检测中铸件常见缺陷特征辨析
无损检测射线常见缺陷图集及分析 ppt

2、折痕
折痕(曝光后)1 折痕(曝光后)2
折痕(曝光后)3
1、折痕(曝光后)的表面现象是什么? 折痕的表征为黑月牙显示,其密度高于邻近的胶片区域(黑度较 高)。 2、折痕(曝光后)产生的原因是什么? 曝光后或冲洗过程中过度(或用力)弯曲胶片都会使胶片出现折痕。 3、这些现象何时可能发生? 折痕(曝光后)通常出现在卸下暗袋或洗片夹时处理胶片不当的情 况下发生。 4、如何检测曝光后的折痕? 将一些胶片曝光,然后有意识地将其卷曲或扭折,冲洗胶片,然后 通过反射光检验胶片,您有可能见到一个或多个月牙状的黑痕。 5、如何可以避免折痕(曝光后)? 严格遵守暗室操作规程,始终小心处理胶片,特别避免手指对胶片 施以任何类型的压 力。
折 痕 曝 光 前
1、折痕的表面现象是什么? 折痕(曝光前)的表征为白月牙状显示,其密度低于邻近的胶片区域(黑度较低)。 2、它们产生的原因是什么? 曝光前弯曲胶片用力过大或过猛都会导致这种类型的折痕。 3、这些现象何时可能发生? 通常出现在从包装盒取出胶片或在曝光前装入暗袋时处理不当的情况下。 4、如何检验曝光前的折痕? 有意识地将某些胶片卷曲或扭折,使其曝光,然后按正常方法冲洗。检验胶片,这时您可 能会在胶片处理不当的地方风到一些颜色较淡的折痕。 5、如何可以避免它们? 严格遵守暗室操作规程,始终小心处理胶片,特别避免手指对胶片施以任何类型的压力。
到静电放电现象。如果您看到冲洗的胶片有锯齿状线条或黑色斑 点,则极有可能是出现了静电曝光斑点。 5、如何可以避免? 在相对湿度大于40%的环境下保存胶片,从包装盒取出胶片时避免 快速滑动或移动胶片。
定 影 液 斑 点
1、它们的表面现象是什么? 由定影液产生的斑点表征为一些小白圆点,其密度较周围胶片区域的密度底。 2、它们产生的原因是什么? 在显影之前,溅出的定影液滴,即使极其微量,都有可能导致产生白色斑点。 3、这些现象何时可能发生? 无论何时,只要有化学污染的存在,都可能会发生这种现象。通常发生最多的 是由于暗室布局不当或冲洗不小心引起。 4、如何可以避免它们? 保证胶片装卸区域的安全干燥清洁,不能让定影液溅在胶片上。
无损检测射线常见缺陷图集及分析
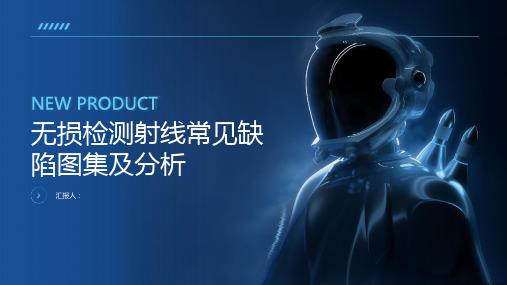
气孔缺陷定义:在金属材料中气孔是由于熔炼或 浇注过程中气体在金属内部未能全部逸出而形成 的空穴。
气孔缺陷图集展示:展示不同类型的气孔缺陷图 谱包括圆形气孔、椭圆形气孔、链状气孔等。
气孔缺陷产生原因:主要由于金属材料熔 炼或浇注过程中气体在金属内部未能全部 逸出或者由于金属材料中含有易形成气体 的元素所致。
无损检测射线常见缺 陷图集及分析
汇报人:
目录
添加目录标题
无损检测射线技术 简介
常见缺陷图集展示
缺陷图集分析
无损检测射线技术 发展趋势
结论
添加章节标题
无损检测射线技术 简介
通过检测衰减后射线的强度 或透射后的影像进行分析
利用射线穿透物质时产生的 衰减作用进行检测
可用于检测各种材料和产品 内部缺陷
降低维护成本:及时发现设备故障 避免重大事故发生降低维护成本。
添加标题
添加标题
添加标题添ຫໍສະໝຸດ 标题提高生产效率:通过快速检测减少 生产过程中的停机时间提高生产效 率。
促进工业发展:无损检测技术的应 用提高了工业生产的可靠性和安全 性推动了工业的发展。
提高检测精度和可 靠性
降低漏检和误检率
促进缺陷识别和分 类标准化
常见缺陷图集展示
裂纹缺陷定义:裂纹是一种常见的缺陷类型通常是由于材料受到外力作用或内部应力过大而产生的断裂现象。
裂纹缺陷图集展示:展示不同材料、不同形状和尺寸的裂纹缺陷图像以便更好地了解裂纹的形成和分布情况。
裂纹缺陷分析:对裂纹缺陷进行详细分析包括裂纹的形态、走向、大小等方面以便更好地了解裂纹的性质和产生 原因。
缺点:无损检测 射线技术需要使 用放射性物质存 在一定的安全风 险同时检测成本 较高设备也较为 昂贵。
焊缝、铸件缺陷及伪缺陷在X射线底片上影像特征的分析

焊缝、铸件缺陷及伪缺陷在X 射线底片上影像特征的分析樊星明一 .单个气孔 (分散气孔 )1.特征和分布状态单个气孔缺陷在焊接内部多呈单一状态均匀分布,在焊缝上部,气孔体积不大 ,呈球状或椭圆形,外表光滑。
2.X 射线检测单个气孔与 X 射线底片上能清晰地显示出气孔的球状,椭圆状轮廓,由于经常采用射线方向与焊缝纵向垂直的透照方法,我们在底片上看到的都是气孔的正投影图象,所以,在 X 射线底片上都不能反映单个气孔缺陷在焊缝横向所处位置,即不能说明单个气孔是在焊缝的上部、中部或下部。
3.形成原因A焊接前未将焊缝坡口处金属上的铁锈、油污和油漆等清理干净。
B电焊条潮湿,水分在电弧高温作用下分解成氢气和氧气等气体,溶解于液态金属中,此时假设焊缝中液态金属凝固过快,熔解气休不能及时自焊缝中逸出。
C由于电弧加热母材温度不够高,焊接速度又过快等不合理工艺因素影响。
二 .链式气孔缺陷1.特征与分布状态链式乞孔在焊缝中呈一直线分布,气孔边沿相互衔接,状如链条,链的中心与焊缝轴线平行。
在埋弧焊中带出现在母材与焊缝之间。
在单面对接焊缝中常出现在焊接底部,链式乞孔缺陷很容易和未焊透缺陷混淆。
为了与未焊透缺陷区别,链状乞孔又称细线气孔。
在焊缝边沿的纵剖面上可以看到链状气孔,在母材与焊缝分界面上呈链环状影像。
在焊缝横剖面上链状气孔是呈单个分布,并有一定距离。
链状气孔之所以有以上所述的分布状态是由于母材与焊缝边界处冷却速度大,液态金属在此处受母材激冷,首先在此处凝固。
而氢气泡在固相外表上形成时消耗的功又小,因此氢气在熔池中析出即在此处元集形成气泡,来不及逸出。
2.X 射线检测链式气孔缺陷在X 射线底片上能清晰地显示出来,有的链环状分布,连续长度有30mm 以上有的那么呈断链状。
一段一段分布在焊缝与母材边沿部位底片上呈暗色图像,在链的边沿可清楚扯到气孔圆形轮廓。
3.形成原因主要是由氢引起的,氢来源于潮湿的助熔剂和没有充分枯燥的焊条涂料中的水分。
海绵状疏松 铸件射线评定
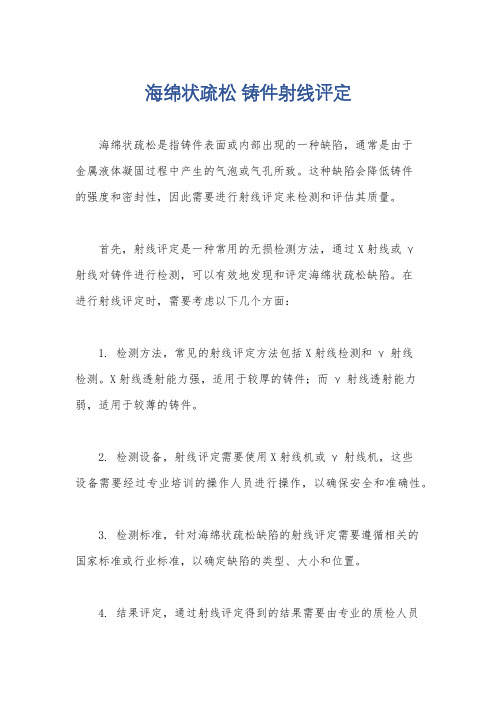
海绵状疏松铸件射线评定
海绵状疏松是指铸件表面或内部出现的一种缺陷,通常是由于
金属液体凝固过程中产生的气泡或气孔所致。
这种缺陷会降低铸件
的强度和密封性,因此需要进行射线评定来检测和评估其质量。
首先,射线评定是一种常用的无损检测方法,通过X射线或γ
射线对铸件进行检测,可以有效地发现和评定海绵状疏松缺陷。
在
进行射线评定时,需要考虑以下几个方面:
1. 检测方法,常见的射线评定方法包括X射线检测和γ射线
检测。
X射线透射能力强,适用于较厚的铸件;而γ射线透射能力弱,适用于较薄的铸件。
2. 检测设备,射线评定需要使用X射线机或γ射线机,这些
设备需要经过专业培训的操作人员进行操作,以确保安全和准确性。
3. 检测标准,针对海绵状疏松缺陷的射线评定需要遵循相关的
国家标准或行业标准,以确定缺陷的类型、大小和位置。
4. 结果评定,通过射线评定得到的结果需要由专业的质检人员
进行评定,判断铸件是否符合质量要求,是否需要修复或报废。
此外,海绵状疏松缺陷的产生可能与铸造工艺、材料选择等因素有关,因此在进行射线评定时,还需要综合考虑这些因素,以找出缺陷产生的原因,并提出改进措施,以避免类似缺陷再次发生。
总的来说,射线评定是一种重要的质量检测方法,对于评定海绵状疏松缺陷具有重要意义,通过科学的检测和评定,可以保证铸件的质量和安全性。
射线检测典型缺陷

射线检测典型缺陷
缺陷名称:裂纹
焊接裂纹是指金属在焊接应力及其它致脆因素共同作用下,焊接接头中局部地区金属结合力遭到破坏,形成的新界面所产生的缝隙, 有尖锐的缺口和长宽比大的特征, 是焊接结构(件)中最危险的缺陷。
裂纹缺陷X射线底片
缺陷名称:气孔
焊接时熔池中的气泡在凝固时未能逸出而残留下来所形成的空穴称为气孔。
气孔有时以单个出现,有时以成堆的形式聚集在局部区域,其形状有球形、条虫形等。
密集气孔缺陷X射线底片
缺陷名称:夹渣
焊后残留在焊缝中的熔渣称为夹渣,形状较复杂,一般有线状、长条状、颗粒状等。
主要发生在坡口边缘和
每层焊道之间非圆滑过渡的部位,焊道形状发生突变或存在深沟的部位也容易产生夹渣。
条状夹渣缺陷X射线底片
缺陷种类:未熔合
在焊缝金属和母材之间或焊道金属与焊道金属之间末完全熔化结合的部分称为未熔合,常出现在坡口的侧壁、多层焊的层间及焊缝的根部。
这种缺陷有的间隙很大,与熔渣难以区别,未熔合区末端易产生微裂纹。
未熔合缺陷X射线底片
缺陷种类:未焊透
焊接时,母材金属之间应该熔合而末焊上的部分称为末焊透。
出现在单面焊的坡口根部及双面焊的坡口钝边处。
末焊透易造成较大的应力集中,往往从端部产生裂纹。
未焊透缺陷X射线底片中心指示器未收起造成的底片错误曝光,如下图所示。
铝铸件常见缺陷及分析
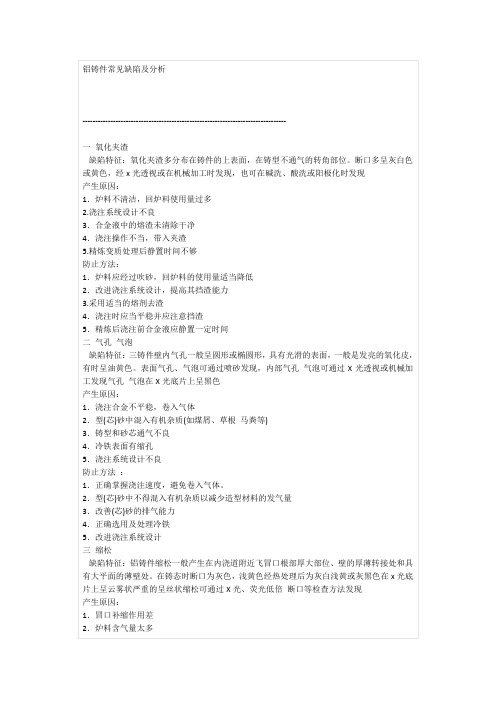
铝铸件常见缺陷及分析--------------------------------------------------------------------------------一氧化夹渣缺陷特征:氧化夹渣多分布在铸件的上表面,在铸型不通气的转角部位。
断口多呈灰白色或黄色,经x光透视或在机械加工时发现,也可在碱洗、酸洗或阳极化时发现产生原因:1.炉料不清洁,回炉料使用量过多2.浇注系统设计不良3.合金液中的熔渣未清除干净4.浇注操作不当,带入夹渣5.精炼变质处理后静置时间不够防止方法:1.炉料应经过吹砂,回炉料的使用量适当降低2.改进浇注系统设计,提高其挡渣能力3.采用适当的熔剂去渣4.浇注时应当平稳并应注意挡渣5.精炼后浇注前合金液应静置一定时间二气孔气泡缺陷特征:三铸件壁内气孔一般呈圆形或椭圆形,具有光滑的表面,一般是发亮的氧化皮,有时呈油黄色。
表面气孔、气泡可通过喷砂发现,内部气孔气泡可通过X光透视或机械加工发现气孔气泡在X光底片上呈黑色产生原因:1.浇注合金不平稳,卷入气体2.型(芯)砂中混入有机杂质(如煤屑、草根马粪等)3.铸型和砂芯通气不良4.冷铁表面有缩孔5.浇注系统设计不良防止方法:1.正确掌握浇注速度,避免卷入气体。
2.型(芯)砂中不得混入有机杂质以减少造型材料的发气量3.改善(芯)砂的排气能力4.正确选用及处理冷铁5.改进浇注系统设计三缩松缺陷特征:铝铸件缩松一般产生在内浇道附近飞冒口根部厚大部位、壁的厚薄转接处和具有大平面的薄壁处。
在铸态时断口为灰色,浅黄色经热处理后为灰白浅黄或灰黑色在x光底片上呈云雾状严重的呈丝状缩松可通过X光、荧光低倍断口等检查方法发现产生原因:1.冒口补缩作用差2.炉料含气量太多3.内浇道附近过热4.砂型水分过多,砂芯未烘干5.合金晶粒粗大6.铸件在铸型中的位置不当7.浇注温度过高,浇注速度太快防止方法:1.从冒口补浇金属液,改进冒口设计2.炉料应清洁无腐蚀3.铸件缩松处设置冒口,安放冷铁或冷铁与冒口联用4.控制型砂水分,和砂芯干燥5.采取细化品粒的措施6.改进铸件在铸型中的位置降低浇注温度和浇注速度四裂纹缺陷特征:1.铸造裂纹。
无损检测射线常见缺陷图集及分析.
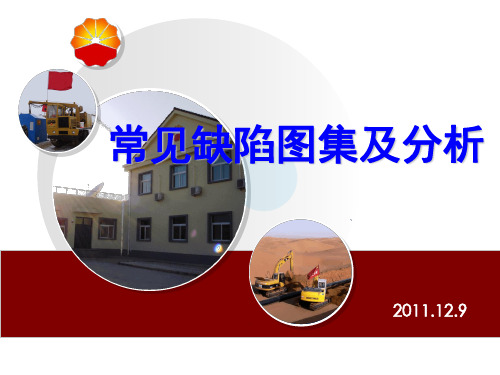
折 痕 曝 光 前
1、折痕的表面现象是什么? 折痕(曝光前)的表征为白月牙状显示,其密度低于邻近的胶片区域(黑度较低)。 2、它们产生的原因是什么? 曝光前弯曲胶片用力过大或过猛都会导致这种类型的折痕。 3、这些现象何时可能发生? 通常出现在从包装盒取出胶片或在曝光前装入暗袋时处理不当的情况下。 4、如何检验曝光前的折痕? 有意识地将某些胶片卷曲或扭折,使其曝光,然后按正常方法冲洗。检验胶片,这时您可 能会在胶片处理不当的地方风到一些颜色较淡的折痕。 5、如何可以避免它们? 严格遵守暗室操作规程,始终小心处理胶片,特别避免手指对胶片施以任何类型的压力。
未融合
边缘未融合
注意:砂轮片磨伤痕迹(不是未融合)
5、裂纹
定义:裂纹是指材料局部断裂形成的缺陷。 影像特征:底片上裂纹和典型影像是轮廓分明的黑线或黑丝。其细节 特征包括:黑线或黑丝上有微小的锯齿,有分叉,粗细和黑度有时有 变化,有些裂纹影像呈较粗的黑线与较细的黑丝相互缠绕状;线的端 部尖细,端头前方有时有丝状阴影延伸。
纵向裂纹
根部裂纹
横向裂纹
6、咬边
一、常见缺陷及示意图
二、其他几种缺陷 三、常见伪缺陷
表 面 内 边
内 咬 边
错 口
接 头 凹 坑
一、常见缺陷及示意图
二、其他几种缺陷 三、常见伪缺陷
1、压痕
1、压痕的表面现象是什么? 压痕的表征为密度明显低于邻近区域的密度。 2、它们产生的原因是什么? 在曝光前某个胶片区域局部受力严重。 3、这些现象何时可能发生? 产生压痕的主要原因在于暗袋准备过程中胶片处理的 方式不当。在处理过程中,胶片某处可能被压(夹)紧 在暗袋中。掉落到暗袋上的物体同样可能造成压痕。 4、如何检验压痕? 直接从同一包装盒中小心准备另一暗袋胶片,曝光并冲 洗胶片,如果未见到与第一次所见一样的暇疵,则第一次所 见的斑痕很可能就是压痕。 5、如何可以避免压痕? 严格遵守暗室操作规程,始终小心处理胶片,避免对胶 片施以任何类型的压力。
焊缝、铸件缺陷及伪缺陷在X射线底片上影像特征的分析

焊缝、铸件缺陷及伪缺陷在X射线底片上影像特征的分析樊星明一.单个气孔(分散气孔)1.特征和分布状态单个气孔缺陷在焊接内部多呈单一状态均匀分布,在焊缝上部,气孔体积不大,呈球状或椭圆形,表面光滑。
2. X射线检测单个气孔与X射线底片上能清晰地显示出气孔的球状,椭圆状轮廓,由于经常采用射线方向与焊缝纵向垂直的透照方法,我们在底片上看到的都是气孔的正投影图象,所以,在X射线底片上都不能反映单个气孔缺陷在焊缝横向所处位置,即不能说明单个气孔是在焊缝的上部、中部或下部。
3.形成原因A焊接前未将焊缝坡口处金属上的铁锈、油污和油漆等清理干净。
B电焊条潮湿,水分在电弧高温作用下分解成氢气和氧气等气体,溶解于液态金属中,此时若焊缝中液态金属凝固过快,熔解气休不能及时自焊缝中逸出。
C由于电弧加热母材温度不够高,焊接速度又过快等不合理工艺因素影响。
二.链式气孔缺陷1.特征与分布状态链式乞孔在焊缝中呈一直线分布,气孔边沿相互衔接,状如链条,链的中心与焊缝轴线平行。
在埋弧焊中带出现在母材与焊缝之间。
在单面对接焊缝中常出现在焊接底部,链式乞孔缺陷很容易和未焊透缺陷混淆。
为了与未焊透缺陷区别,链状乞孔又称细线气孔。
在焊缝边沿的纵剖面上可以看到链状气孔,在母材与焊缝分界面上呈链环状影像。
在焊缝横剖面上链状气孔是呈单个分布,并有一定距离。
链状气孔之所以有以上所述的分布状态是由于母材与焊缝边界处冷却速度大,液态金属在此处受母材激冷,首先在此处凝固。
而氢气泡在固相表面上形成时消耗的功又小,因此氢气在熔池中析出即在此处元集形成气泡,来不及逸出。
2. X射线检测链式气孔缺陷在X射线底片上能清晰地显示出来,有的链环状分布,连续长度有30mm以上有的则呈断链状。
一段一段分布在焊缝与母材边沿部位底片上呈暗色图像,在链的边沿可清楚扯到气孔圆形轮廓。
3.形成原因主要是由氢引起的,氢来源于潮湿的助熔剂和没有充分干燥的焊条涂料中的水分。
焊条地程中在电弧高温作用下水被分解成氢和氧。
无损检测 焊件中常见的缺陷
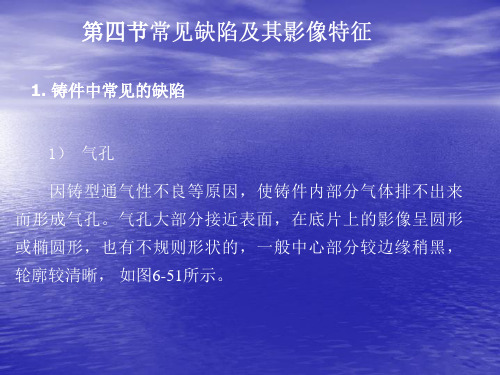
中子射线照相检测与X射线照相检测、γ 射线照相检测相类似, 都是利用射线对物体有很强的穿透能力,来实现对物体的无损检
测。对大多数金属材料来说,由于中子射线比X射线和γ 射线具有
更强的穿透力,对含氢材料表现为很强的散射性能等特点,从而 成为射线照相检测技术中又一个新的组成部分。
第四节常见缺陷及其影像特征
1. 铸件中常见的缺陷
1) 气孔
因铸型通气性不良等原因,使铸件内部分气体排不出来
而形成气孔。气孔大部分接近表面,在底片上的影像呈圆形 或椭圆形,也有不规则形状的,一般中心部分较边缘稍黑, 轮廓较清晰, 如图6-51所示。
2) 疏松
浇铸时局部温差过大,在金属收缩过程中,邻近金属补 缩不良,产生疏松。疏松多产生在铸件的冒口根部、厚大部 位、厚薄交界处和具有大面积的薄壁处。在底片上的影像呈 轻微疏散的浅黑条状或疏散的云雾状,严重的呈密集云雾状
第五节 γ 射线检测及中子射线检测简介
1. γ 射线检测的特点
γ 射线与X射线检测的工艺方法基本上是一样的, 但是γ
射线检测有其独特的地方。 (1) γ 射线源不像X射线那样,可以根据不同检测厚度来
调节能量(如管电压),它有自己固定的能量,所以要根据材料 厚度、精度要求合理选取γ 射线源。
周每人控制在最大容许剂量0.1rem以内时,则应有D≤0.1rem;
如果人体在每透照一次时所接受到的射线剂量为时,则控制每 周内的透照次数N≤0.1,亦可以达到防护的目的。
4. 中子防护 1)减速剂的选择 快中子减速作用,主要依靠中子和原子核的弹性碰撞,因 此较好的中子减速剂是原子序数低的元素如氢、水、石蜡等含 氢多的物质,它们作为减速剂使用减速效果好,价格便宜,是 比较理想的防护材料。
金属铸件x射线缺陷

金属铸件的X射线缺陷
金属铸件的X射线缺陷主要有以下几种:
1. 气孔:在铸件中出现的圆形、椭圆形或不规则形状的孔洞,有时多个气孔会形成气团。
气孔可能是由于模具预热温度过低,液态金属通过浇注系统冷却太快,模具排气设计不良,涂层不好等因素造成的。
2. 缩松:铸件表面或内部的一种粗糙的孔洞,通常发生在铸件的流道附近、冒口的根部、厚壁部分、壁厚过渡部分以及大平面的厚薄部分之间。
这可能是由于模具的工作温度控制不满足定向凝固的要求,涂层选择不当,铸件在模具中位置的设计不当等因素造成的。
3. 渣孔:铸件中的开孔或黑洞,孔完全或部分充满熔渣。
渣孔主要由合金熔炼过程和浇注过程(包括浇注系统设计不当)引起。
4. 裂纹:铸件中出现的直线或不规则曲线状的缺陷,可能是由于不合理的结构设计和制作工艺不达标,或者热处理不当等原因造成。
裂纹在X射线检测图像中呈浅色线条状。
5. 气泡:由于铸件在铸造过程中通气不顺,掺杂了空气或杂质等原因造成的。
工件表面的气泡/气孔可以通过喷砂处理发现,工件内部的气泡/气孔可采用X射线透视检测发现。
这些缺陷的存在会严重影响铸件的质量和性能,因此在生产过程中应通过优化工艺、加强质量控制等措施避免这些缺陷的产生。
铸件缺陷特征和检验标准

铸件缺陷特征和检验标准
铸件缺陷这事儿,其实就是铸造过程中不小心留下的“小毛病”,这些毛病会影响铸件的质量和使用。
咱们来聊聊常见的几种问题和怎么检查它们:
多出来的部分:就像做蛋糕时不小心多抹了一层奶油,铸件有时也会有些地方厚了或者不该有的凸起。
检查时,我们就得仔细瞧瞧,量量尺寸,看看有没有哪里鼓起来了,超出标准。
表面不平整:想象一下,如果你的新手机壳上有划痕、小坑或者脏东西嵌在里面,肯定不乐意。
铸件也一样,裂纹、小坑、杂质这些,得通过专业的“照妖镜”——磁粉检查或渗透检测来找,确保表面干净、光滑。
藏起来的小洞:气孔和针孔就像是面包里的小气泡,不过在铸件里可就不受欢迎了。
要用X光或者超声波这样的高科技手段,像给铸件做CT扫描一样,找出这些隐藏的问题。
缩水和疏松:就像冬天衣服没穿够会缩成一团,铸件也可能因为金属冷却时收缩,留下大洞或者密密麻麻的小孔。
得用水压测试或者高级的无损检测,确保这些洞洞不会让铸件“体质”变差。
脏东西留下的痕迹:渣眼就像是衣服上的污渍,得仔细找找。
通过破坏性检测或者非常精细的检查,把这些不干净的痕迹揪出来。
没填满的地方:冷隔和浇不足就像是倒茶时杯子没倒满,铸件里面或者表面也有没填满的情况。
还是得靠X光或超声波这些“透视眼”来发现。
性能不达标:铸件不仅要长得好看,还得结实能用。
通过拉拉扯扯的力学实验和化学分析,确保它既硬朗又成分合适,符合规定的“身体素质”。
每个国家或行业都有自己的标准,就像是老师给的考试大纲,告诉厂家铸件得达到什么水平。
厂家自己也会有一套更细致的检查办法,确保生产出来的铸件都是“优等生”。
无损检测射线常见缺陷图集及分析-精选文档
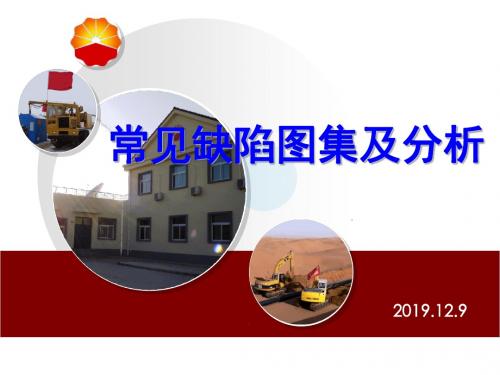
纵向裂纹
根部裂纹
横向裂纹
6、咬边
一、常见缺陷及示意图
二、其他几种缺陷 三、常见伪缺陷
表 面 内 凹
根 部 内 凹
表 面 咬 边
内 咬 边
错 口
接 头 凹 坑
一、常见缺陷及示意图
二、其他几种缺陷 三、常见伪缺陷
1、压痕
1、压痕的表面现象是什么? 压痕的表征为密度明显低于邻近区域的密度。 2、它们产生的原因是什么? 在曝光前某个胶片区域局部受力严重。 3、这些现象何时可能发生? 产生压痕的主要原因在于暗袋准备过程中胶片处理的 方式不当。在处理过程中,胶片某处可能被压(夹)紧 在暗袋中。掉落到暗袋上的物体同样可能造成压痕。 4、如何检验压痕? 直接从同一包装盒中小心准备另一暗袋胶片,曝光并冲 洗胶片,如果未见到与第一次所见一样的暇疵,则第一次所 见的斑痕很可能就是压痕。 5、如何可以避免压痕? 严格遵守暗室操作规程,始终小心处理胶片,避免对胶 片施以任何类型的压力。
折 痕 曝 光 前
1、折痕的表面现象是什么? 折痕(曝光前)的表征为白月牙状显示,其密度低于邻近的胶片区域(黑度较低)。 2、它们产生的原因是什么? 曝光前弯曲胶片用力过大或过猛都会导致这种类型的折痕。 3、这些现象何时可能发生? 通常出现在从包装盒取出胶片或在曝光前装入暗袋时处理不当的情况下。 4、如何检验曝光前的折痕? 有意识地将某些胶片卷曲或扭折,使其曝光,然后按正常方法冲洗。检验胶片,这时您可 能会在胶片处理不当的地方风到一些颜色较淡的折痕。 5、如何可以避免它们? 严格遵守暗室操作规程,始终小心处理胶片,特别避免手指对胶片施以任何类型的压力。
2、折痕
折痕(曝光后)1
折痕(曝光后)2
折痕(曝光后)3
铸件缺陷分析

4、防止方法 :
1.均匀混砂和紧实,提高砂型和砂芯的强度和 紧实度,在砂型和砂芯的凸出部位应插钉加固
2.调整型、芯烘干规范,防止烘干过度。防止 型、芯在存放时返潮 3.改进浇注系统设计,分散布置内浇道,避免内 浇道直冲型壁、芯子和型腔转角,降低金属液注入 型腔时的液流速度 4.改进涂料配方,在型、芯易冲砂部位及直浇 道和内浇道处采用耐火管、耐火砖和抗冲刷涂料。
4、防止方法 :
1.非铁合金熔炼时,炉料、熔剂、工具、坩埚和浇包要充分预热和烘干,去锈去油污, 多次重熔炉料的加入量要适当限制 2.防止金属液在熔炼过程中过度氧化和吸气,加强脱氧、除气和除渣。在坩埚和浇包内 的金属熔池表面加覆盖熔剂,防止金属液二次氧化、吸气和有害杂质返回熔池。对球墨铸铁, 应加强脱硫,降低原铁液的含硫量,在保证球化前提下,尽量减少球化剂加入量,降低铸铁 的残留镁量,并加强孕育处理。 3.浇注时金属液不得断流,充型速度不宜过高,铸件浇注位置和浇注系统的设置应保证 金属液平稳地充满型腔,并利于型腔内气体能畅通地排出。 4.砂型铸造时,应保证型和芯排气畅通。砂芯内要开排气通道,合型时要填补芯头间隙, 以免钻人金属液堵塞通气道;型腔最高处及易窝气的部位应设置出气冒口;大平面铸件可倾 斜浇注.并在型腔最商处设置出气冒口;芯撑和冷铁应干燥、无锈、无油污;砂型要扎足够 多的出气孔;型砂中不得混人铁豆、煤粒、粘土等杂物,并控制水分及碳质材料的含量,减 少粘土含量,提高型砂的透气性;涂料要烘干并不含易发气物质。 7.增加直浇道高度以提高充型金属液静压力,保证金属液连续平稳地充型
二、胀砂 1、定义和特征: 铸件表面局部胀大,形成不 规则瘤状金属突起物 2、检验与鉴别 : 肉眼外观检查。注意与冲砂、掉 砂缺陷相区别。胀砂一般不伴生其他 缺陷,缺陷内不裹含砂粒和砂块。冲 砂和掉砂在铸件其他部位或冒口中常 伴有砂眼,冲砂与浇注系统位置及充 型金属液流向有关。 a)外表面胀砂
铸造铸件常见缺陷分析报告
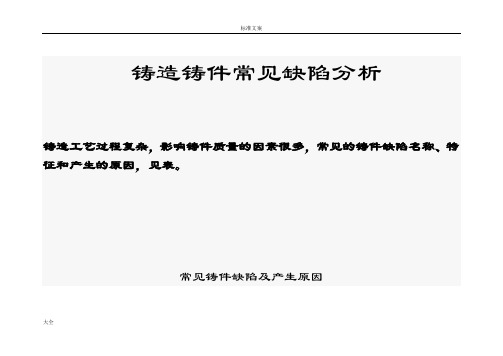
铸造铸件常见缺陷分析铸造工艺过程复杂,影响铸件质量的因素很多,常见的铸件缺陷名称、特征和产生的原因,见表。
常见铸件缺陷及产生原因大全缺陷名称特征产生的主要原因气孔在铸件部或表面有大小不等的光滑孔洞①炉料不干或含氧化物、杂质多;②浇注工具或炉前添加剂未烘干;③型砂含水过多或起模和修型时刷水过多;④型芯烘干不充分或型芯通气孔被堵塞;⑤春砂过紧,型砂透气性差;⑥浇注温度过低或浇注速度太快等缩孔与缩松缩孔多分布在铸件厚断面处,形状不规则,孔粗糙①铸件结构设计不合理,如壁厚相差过大,厚壁处未放冒口或冷铁;②浇注系统和冒口的位置不对;③浇注温度太高;④合金化学成分不合格,收缩率过大,冒口太小或太少砂眼在铸件部或表面有型砂充塞的孔眼①型砂强度太低或砂型和型芯的紧实度不够,故型砂被金属液冲入型腔;②合箱时砂型局部损坏;③浇注系统不合理,浇口方向不对,金属液冲坏了砂大全型;④合箱时型腔或浇口散砂未清理干净粘砂铸件表面粗糙,粘有一层砂粒①原砂耐火度低或颗粒度太大;②型砂含泥量过高,耐火度下降;③浇注温度太高;④湿型铸造时型砂中煤粉含量太少;⑤干型铸造时铸型未刷涂斜或涂料太薄夹砂铸件表面产生的金属片状突起物,在金属片状突起物与铸件之间夹有一层型砂①型砂热湿拉强度低,型腔表面受热烘烤而膨胀开裂;②砂型局部紧实度过高,水分过多,水分烘干后型腔表面开裂;③浇注位置选择不当,型腔表面长时间受高温铁水烘烤而膨胀开裂;④浇注温度过高,浇注速度太慢错型铸件沿分型面有相对位置错①模样的上半模和下半模未对准;②合箱时,上下砂箱错位;③上下砂箱未夹紧或上箱未加足够压大全移铁,浇注时产生错箱冷隔铸件上有未完全融合的缝隙或洼坑,其交接处是圆滑的①浇注温度太低,合金流动性差;②浇注速度太慢或浇注中有断流;③浇注系统位置开设不当或浇道横截面积太小;④铸件壁太薄;⑤直浇道(含浇口杯)高度不够;⑥浇注时金属量不够,型腔未充满浇不足铸件未被浇满裂纹铸件开裂,开裂处金属表面有氧化膜①铸件结构设计不合理,壁厚相差太大,冷却不均匀;②砂型和型芯的退让性差,或春砂过紧;③落砂过早;④浇口位置不当,致使铸件各部分收缩不均匀大全铸件质量与气孔的关系1)合理选定铸造合金和铸件结构。
射线检测中铸件常见缺陷特征辨析
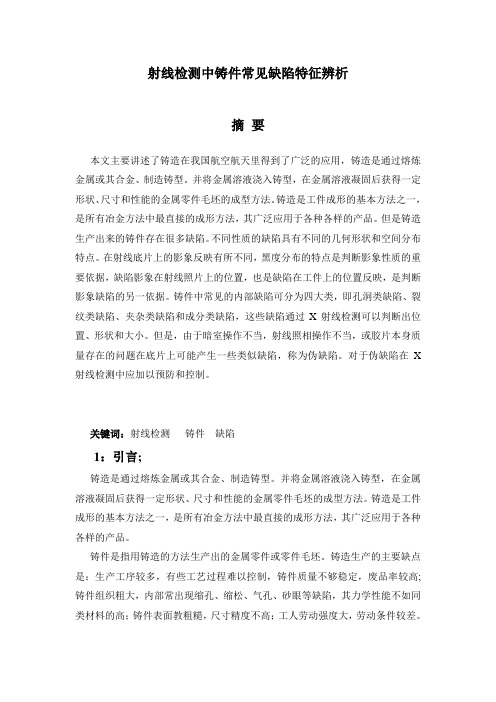
射线检测中铸件常见缺陷特征辨析摘要本文主要讲述了铸造在我国航空航天里得到了广泛的应用,铸造是通过熔炼金属或其合金、制造铸型。
并将金属溶液浇入铸型,在金属溶液凝固后获得一定形状、尺寸和性能的金属零件毛坯的成型方法。
铸造是工件成形的基本方法之一,是所有冶金方法中最直接的成形方法,其广泛应用于各种各样的产品。
但是铸造生产出来的铸件存在很多缺陷。
不同性质的缺陷具有不同的几何形状和空间分布特点。
在射线底片上的影象反映有所不同,黑度分布的特点是判断影象性质的重要依据,缺陷影象在射线照片上的位置,也是缺陷在工件上的位置反映,是判断影象缺陷的另一依据。
铸件中常见的内部缺陷可分为四大类,即孔洞类缺陷、裂纹类缺陷、夹杂类缺陷和成分类缺陷,这些缺陷通过X射线检测可以判断出位置、形状和大小。
但是,由于暗室操作不当,射线照相操作不当,或胶片本身质量存在的问题在底片上可能产生一些类似缺陷,称为伪缺陷。
对于伪缺陷在X 射线检测中应加以预防和控制。
关键词:射线检测铸件缺陷1:引言;铸造是通过熔炼金属或其合金、制造铸型。
并将金属溶液浇入铸型,在金属溶液凝固后获得一定形状、尺寸和性能的金属零件毛坯的成型方法。
铸造是工件成形的基本方法之一,是所有冶金方法中最直接的成形方法,其广泛应用于各种各样的产品。
铸件是指用铸造的方法生产出的金属零件或零件毛坯。
铸造生产的主要缺点是:生产工序较多,有些工艺过程难以控制,铸件质量不够稳定,废品率较高;铸件组织粗大,内部常出现缩孔、缩松、气孔、砂眼等缺陷,其力学性能不如同类材料的高;铸件表面教粗糙,尺寸精度不高;工人劳动强度大,劳动条件较差。
目前,我厂铸造生产出的工件大多数都是铸件,但是其存在很多的缺陷,因此我们常采用x射线检测,其特点:第一,对工件无特殊要求,检验结果显示直观;第二,检验技术和检验工作质量可以自我检测。
2:缺陷识别概述正确地识别射线照片上的影象,判断影象所代表的缺陷性质的基础是:(1)具有一定的材料和工艺方面的知识,掌握缺陷的可能形成和发生规律。
射线检测的缺陷影像分析

射线检测的缺陷影像分析
缺陷性质分为: 1.裂纹、 2.未熔合、 3.未焊透、 4.条形缺陷 5.圆形缺陷,
射线检测的缺陷影像分析—————裂纹①
1. 裂纹 定义:裂纹是指材料局部断裂形成的缺陷。 裂纹有多种分类方法:按延伸方向可分为
纵向裂纹、横向裂纹、辐射状裂纹等;按发生 部位可分为焊缝裂纹、热影响区裂纹、熔合区 裂纹、焊趾裂纹、焊道下裂纹、弧坑裂纹等; 按发生条件和时机可分为热裂纹、冷裂纹、再 热裂纹等。
对于低碳钢和低合金钢,大致在300℃~200℃以 下。冷裂纹可以焊后立即出现,也有可能在几个 小时,几天甚至更长时间以后发生,这种冷裂纹 称为延迟裂纹,具有更大的危害性。
射线检测的缺陷影像分析—————裂纹⑥
冷裂纹 延迟裂纹多发生在热影响区,少数发生在
焊缝上,沿纵向和横向都有发生。焊趾裂纹、 焊道下裂纹、根部裂纹都是延迟裂纹常见的形 态。
射线检测的缺陷影像分析
————裂纹
射线检测的缺陷影像分析
————裂纹
射线检测的缺陷影像分析
————裂纹
射线检测的缺陷影像分析
————裂纹
射线检测的缺陷影像分析
————裂纹
射线检测的缺陷影像分析
————裂纹
射线检测的缺陷影像分析—————裂纹⑤
冷裂纹 一般在焊后冷却至马氏体转变温度以下产生,
线或其他不规则的。气孔的轮廓比较圆滑,其黑 度中心较大,至边缘减小。
射线检测的缺陷影像分析
————气孔
射线检测的缺陷影像分析
————气孔
射线检测的缺陷影像分析
————气孔
射线检测的缺陷影像分析
————气孔
射线检测的缺陷影像分析
————气孔
铸件中常见缺陷

铸件中常见的主要缺陷有:1.气孔这是金属凝固过程中未能逸出的气体留在金属内部形成的小空洞,其内壁光滑,内含气体,对超声波具有较高的反射率,但是又因为其基本上呈球状或椭球状,亦即为点状缺陷,影响其反射波幅。
钢锭中的气孔经过锻造或轧制后被压扁成面积型缺陷而有利于被超声检测所发现,如图2.2所示。
2.缩孔与疏松铸件或钢锭冷却凝固时,体积要收缩,在最后凝固的部分因为得不到液态金属的补充而会形成空洞状的缺陷。
大而集中的空洞称为缩孔,细小而分散的空隙则称为疏松,它们一般位于钢锭或铸件中心最后凝固的部分,其内壁粗糙,周围多伴有许多杂质和细小的气孔。
由于热胀冷缩的规律,缩孔是必然存在的,只是随加工工艺处理方法不同而有不同的形态、尺寸和位置,当其延伸到铸件或钢锭本体时就成为缺陷。
钢锭在开坯锻造时如果没有把缩孔切除干净而带入锻件中就成为残余缩孔(缩孔残余、残余缩管),如图2.3、2.4、2.5所示。
如果铸件的型模设计不当、浇注工艺不当等,也会在铸件与型模接触的部位产生疏松,如图2.28所示。
断口照片中的黑色部分即为疏松部位,其呈现黑色是因为该工件已经过退火处理,使得疏松部位被氧化和渗入机油所致。
图2.28 W18钢铸件-用作铣刀齿,采用超声纵波垂直入射多次底波衰减法发现的疏松断口照片3.夹渣熔炼过程中的熔渣或熔炉炉体上的耐火材料剥落进入液态金属中,在浇注时被卷入铸件或钢锭本体内,就形成了夹渣缺陷。
夹渣通常不会单一存在,往往呈密集状态或在不同深度上分散存在,它类似体积型缺陷然而又往往有一定线度。
4.夹杂熔炼过程中的反应生成物(如氧化物、硫化物等)-非金属夹杂,如图2.1和2.6,或金属成分中某些成分的添加料未完全熔化而残留下来形成金属夹杂,如高密度、高熔点成分-钨、钼等,如图2.29,也有如图2.24所示钛合金棒材中的纯钛偏析。
(a)(b)(c)(d)(e)图2.29 BT9钛合金锻制饼坯中的钼夹杂:(a)剖面低倍照片;(b)X射线照相底片;(c)C扫描显示(图中四个白色点状显示为同一个缺陷,是使用水浸点聚焦探头以不同灵敏度检测的结果,其他分散细小的白色点状为与该缺陷无关的杂波显示);(d)B扫描显示;(e)3D显示5.偏析铸件或钢锭中的偏析主要指冶炼过程中或金属的熔化过程中因为成分分布不均而形成的成分偏析,有偏析存在的区域其力学性能有别于整个金属基体的力学性能,差异超出允许标准范围就成为缺陷,如图2.23和2.24、2.27所示。
- 1、下载文档前请自行甄别文档内容的完整性,平台不提供额外的编辑、内容补充、找答案等附加服务。
- 2、"仅部分预览"的文档,不可在线预览部分如存在完整性等问题,可反馈申请退款(可完整预览的文档不适用该条件!)。
- 3、如文档侵犯您的权益,请联系客服反馈,我们会尽快为您处理(人工客服工作时间:9:00-18:30)。
目前,我厂铸造生产出的工件大多数都是铸件,但是其存在很多的缺陷,因此我们常采用x射线检测,其特点:第一,对工件无特殊要求,检验结果显示直观;第二,检验技术和检验工作质量可以自我检测。
2:缺识别概述
正确地识别射线照片上的影象,判断影象所代表的缺陷性质的基础是:
(1)具有一定的材料和工艺方面的知识,掌握缺陷的可能形成和发生规律。
3.3缩孔和缩松(图) 铸件在冷却和凝固过程中,合金将发生液态收缩和固态收缩,由于铸件设计的特点和铸型设计存在的不足、浇注操作不当,造成补缩不足,在铸件中产生孔洞。集中的大孔洞称为缩孔,分散而细小的孔洞称为缩松。缩孔与缩松在底片上呈现的形态常见的是集中性孔洞、纤维状缩孔、海绵状缩松三种状态。
集中性孔洞常称为缩孔,在底片上它呈现为形状不规则、黑度比背景高出很多的暗斑影象,其分布没有确定的方向,面积较大,轮廓一般清晰。纤维状(树枝状)缩孔在底片上它呈现为树枝状黑度较大的影象,影象具有主干、主枝、次枝等形貌,整个影象都显示较大的黑度,特别是主干和主枝。由于其形态的特殊性,这种缺陷影象容易识别。海绵状缩松由相互连接的小孔洞系构成,在底片上呈现为云雾状影象,它总有一定的面积分布。
射线检测中铸件常见缺陷特征辨析
———————————————————————————————— 作者:
———————————————————————————————— 日期:
ﻩ
射线检测中铸件常见缺陷特征辨析
摘要
本文主要讲述了铸造在我国航空航天里得到了广泛的应用,铸造是通过熔炼金属或其合金、制造铸型。并将金属溶液浇入铸型,在金属溶液凝固后获得一定形状、尺寸和性能的金属零件毛坯的成型方法。铸造是工件成形的基本方法之一,是所有冶金方法中最直接的成形方法,其广泛应用于各种各样的产品。但是铸造生产出来的铸件存在很多缺陷。不同性质的缺陷具有不同的几何形状和空间分布特点。在射线底片上的影象反映有所不同,黑度分布的特点是判断影象性质的重要依据,缺陷影象在射线照片上的位置,也是缺陷在工件上的位置反映,是判断影象缺陷的另一依据。铸件中常见的内部缺陷可分为四大类,即孔洞类缺陷、裂纹类缺陷、夹杂类缺陷和成分类缺陷,这些缺陷通过X射线检测可以判断出位置、形状和大小。但是,由于暗室操作不当,射线照相操作不当,或胶片本身质量存在的问题在底片上可能产生一些类似缺陷,称为伪缺陷。对于伪缺陷在X射线检测中应加以预防和控制。
(2)识别影象和判断缺陷性质的丰富经验。
(3)必须了解射线照相过程,特别是透照的具体位置,以分析影象的形成和变化特点。
总之,对工件的材料、工艺知识掌握的越多,对工件射线照相过程了解的越清楚,具有的经验越丰富,就越容易正确的识别射线照片上的缺陷影象。不同性质的缺陷具有不同的几何形状和空间分布特点,例如,气孔一般呈球形,裂纹多为宽度很小、且有变化的缝隙等。由于射线照片上缺陷的影象是缺陷的几何形状按照一定规律在平面上投影形成的图形,因此,射线照片上的缺陷影象的几何形状及射线的照射方向密切相关。影象的几何形状常常是判断缺陷性质的最重要依据。影象的黑度分布是判断影象性质的另一个主要依据,黑度分布的特点是判断影象性质的重要依据。
3.1.2析出气孔是溶解在金属溶液中的气体,在冷却和凝固过程中,由于温度降低或外界压力降低,使溶解度降低,而从金属溶液中析出,这些析出的气体由于受到型芯的阻挡,或因金属溶液温度降低黏度增大而难以上浮排出,便被留在铸件内形成气孔。析出气孔多为分散的小圆孔。
3.1.3反应气孔是金属溶液与铸型或金属溶液中的某些元素之间发生化学反应产生的气体所造成的气孔。它一般均匀分布,主要集中在铸件皮下。
关键词:射线检测铸件缺陷
1:引言;
铸造是通过熔炼金属或其合金、制造铸型。并将金属溶液浇入铸型,在金属溶液凝固后获得一定形状、尺寸和性能的金属零件毛坯的成型方法。铸造是工件成形的基本方法之一,是所有冶金方法中最直接的成形方法,其广泛应用于各种各样的产品。
铸件是指用铸造的方法生产出的金属零件或零件毛坯。铸造生产的主要缺点是:生产工序较多,有些工艺过程难以控制,铸件质量不够稳定,废品率较高;铸件组织粗大,内部常出现缩孔、缩松、气孔、砂眼等缺陷,其力学性能不如同类材料的高;铸件表面教粗糙,尺寸精度不高;工人劳动强度大,劳动条件较差。
3.2针孔(图) 针孔是铸件中 比较均匀散布的细小气孔,它或者出现在整个铸件,或者集中出现在铸件的某个区域。在射线照片上它呈现为均匀散布的暗点状影象,在铸件截面厚度较小时,影象清晰;在截面厚度较大时,影象模糊,这时候由于气孔在厚度方向上的迭加,影象可转化为尖点状(苍蝇脚状)或近于圆点状。如果厚度大,影象将变成模糊的云状形貌。
3.1气孔(图) 在射线照片上呈现为孤立的或成群的圆形、椭圆形和梨形的暗班,轮廓光滑,影象鲜明,整个影象黑度较大,无明显变化。较大的气孔很容易识别。按照产生原因,气孔可分为三类,即侵入气孔、析出气孔和反应气孔。
3.1.1侵入气孔是在浇注的过程中,铸型和型心由于急剧加热挥发出的气体和黏接剂等有机物燃烧产生的气体和型腔中未逸出的气体等进入到金属溶液中形成的气孔。侵入气孔的体积一般较大,多分布在铸件上表面附近。
铸件中常见的内部缺陷可分为四类,即
(1)孔洞类缺陷,如气孔、针孔、缩孔、缩松和缩松。
(2)裂纹类缺陷,如热烈纹、冷裂纹、白点和冷隔。
(3)夹杂类缺陷,如夹杂物、夹渣(渣孔)和砂眼。
(4)成分类缺陷,如偏析。
3孔洞类缺陷
气孔是铸件中常见的缺陷之一,在铸件的废品中,由气孔造成的约占1/3。气孔是气体在铸件中形成的孔洞。它存在破坏了铸件金属的连续性,减少了承载截面,造成了局部应了集中,降低了铸件的性能,特别是降低铸件的冲击韧度和疲劳强度。气孔在射线照片上常见的形态主要有两种: