铸铁件的时效处理及方法
固溶处理与时效处理的区别

固溶处理固溶处理(solution treatment):指将合金加热到高温单相区恒温保持,使过剩相充分溶解到固溶体中后快速冷却,以得到过饱和固溶体的热处理工艺。
目录序言固溶处理是为了溶解基体内碳化物、γ’相等以得到均匀的过饱和固溶体,便于时效时重新析出颗粒细小、分布均匀的碳化物和γ’等强化相,同时消除由于冷热加工产生的应力,使合金发生再结晶。
其次,固溶处理是为了获得适宜的晶粒度,以保证合金高温抗蠕变性能。
固溶处理的温度范围大约在980~1250℃之间,主要根据各个合金中相析出和溶解规律及使用要求来选择,以保证主要强化相必要的析出条件和一定的晶粒度。
对于长期高温使用的合金,要求有较好的高温持久和蠕变性能,应选择较高的固溶温度以获得较大的晶粒度;对于中温使用并要求较好的室温硬度、屈服强度、拉伸强度、冲击韧性和疲劳强度的合金,可采用较低的固溶温度,保证较小的晶粒度。
高温固溶处理时,各种析出相都逐步溶解,同时晶粒长大;低温固溶处理时,不仅有主要强化相的溶解,而且可能有某些相的析出。
对于过饱和度低的合金,通常选择较快的冷却速度;对于过饱和度高的合金,通常为空气中冷却。
不锈钢固溶热处理碳在奥氏体不锈钢中的溶解度与温度有很大影响。
奥氏体不锈钢在经400℃~850℃的温度范围内时,会有高铬碳化物析出,当铬含量降至耐腐蚀性界限之下,此时存在晶界贫铬,会产生晶间腐蚀,严重时能变成粉末。
所以有晶间腐蚀倾向的奥氏体不锈钢应进行固溶热处理或稳定化处理。
固溶热处理:将奥氏体不锈钢加热到1100℃左右,使碳化物相全部或基本溶解,碳固溶于奥氏体中,然后快速冷却至室温,使碳达到过饱和状态。
这种热处理方法为固溶热处理。
固溶热处理中的快速冷却似乎象普通钢的淬火,但此时的‘淬火’与普通钢的淬火是不同的,前者是软化处理,后者是淬硬。
后者为获得不同的硬度所采取的加热温度也不一样,但没到1100℃。
淬火钢的淬火是将钢加热到临界温度Ac3或Ac1以上某一温度,保温一段时间,使之全部或部分奥氏体化,然后以大于临界冷却速度的冷速快冷到Ms以下进行马氏体转变的热处理工艺。
铸铁件的时效处理及方法

铸造实习报告范文一、实习目的和任务本次实习的目的是为了让我更加深入地了解铸造工艺,并掌握一定的铸造技术。
实习期间,我主要任务是学习和实践各种铸造方法,包括砂型铸造、金属型铸造等,并参与一定的铸造工艺实践操作。
二、实习内容和过程在实习的第一周,我主要学习了铸造的基本知识和标准。
了解了铸造过程的基本流程和操作要点。
通过观看相关视频和听取老师的讲解,我逐渐掌握了铸造所需要的基本知识。
在实习的第二周,我开始进行实际操作。
首先,我学习了砂型铸造的方法和工艺流程。
在老师的指导下,我学会了如何制作一个完整的砂模。
从选料到模具制作,再到最后的砂心制作,我都一步一步地进行了实践操作。
在这个过程中,我遇到了一些困难,比如掌握砂模的制作时间和砂心的制作难度。
但通过不断练习和改进,我逐渐掌握了这些技巧。
接下来的几天,我开始学习金属型铸造。
这是一种相对复杂的铸造方法,要求对金属的性质和金属型的制作有一定的了解。
通过观看一些实际操作的视频,我对金属型的制作和融化金属的处理有了初步的了解。
然后,我在实验室内进行了一次实际的金属型铸造操作。
在老师的指导下,我完成了一个简单的产品,并成功获得了合格品。
在整个实习的过程中,我还参观了一家大型铸造企业,并观摩了他们的生产线。
通过这次参观,我深刻地认识到铸造工艺在实际生产中的重要性和广泛应用。
三、实习收获和体会通过这次实习,我收获了很多实践技能和经验。
首先,我掌握了基本的铸造知识和技术,了解了铸造工艺的原理和流程。
其次,在实际操作中,我不仅加深了对理论知识的理解,还培养了自己的动手能力和耐心。
我学会了如何根据产品要求进行材料选择和模具制作,并掌握了一些操作技巧和注意事项。
同时,通过参观大型企业的生产线,我对铸造工业有了更加全面的认识。
我认识到铸造工艺在汽车、机械制造、建筑以及石油化工等许多领域都有广泛的应用。
铸造工艺的发展和改进对于提高产品质量和生产效率具有重要意义。
总结起来,这次铸造实习对我来说是一次很有意义的经历。
灰铁、球铁热处理工艺指导书

铸件热处理工艺指导书1.灰铸铁的退火、正火热处理工艺1.1消除内应力退火(人工时效)工艺灰铸铁消除内应力退火(人工时效)热处理工艺适用范围1.较薄、故冷却速度较快的灰铁件;2.形状复杂、截面变化较大的铸件;3。
需进行机加工的大型铸件;4。
经过少量焊修,因而局部积累些许焊应力的铸件.*加热温度越高,应力消除越快。
但温度过高,则易发生石墨化与珠光体球化而使性能降低,尤其是含Si 量较高时;*保温时间一般按炉内铸件平均壁厚的5min/mm计算。
形状复杂的铸件,要以75~100℃/h的速率缓慢加热;*保温时间终了,以30~50℃/h的速率在炉内缓冷,冷却至150~200℃出炉冷却(空冷).1.2软化退火和正火工艺灰铸铁软化退火和正火热处理工艺适用范围*保温时间一般按炉内铸件平均壁厚的5min/mm计算。
形状复杂的铸件,要以75~100℃/h的速率缓慢加热.2.球墨铸铁的退火、正火(+回火)和调质热处理工艺2.1 高温退火当铸态组织为铁素体+珠光体+渗碳体+石墨时,必须采用高温退火工艺:适用范围1。
获得铁素体球墨铸铁;2.分解渗碳体和珠光体,提高机械性能;3.改善加工性能,使工件容易加工且不易变形。
*退火温度越高,渗碳体组织分解速度越快,白口现象越易消除.但温度过高将使铸件机械性能反而变坏,发生变形和表面氧化失碳,故须严格控制温度上限。
* 保温时间也可按炉内铸件每15mm的有效厚度、需要保温1~2h计算,铸件白口深度大、渗碳体组织成分多时,应适当增加保温时间。
*形状复杂的铸件,要以75~100℃/h的速率缓慢加热。
保温终了,以60~80℃/h的速率在炉内缓冷,至600℃后出炉空冷。
2.2 低温退火当铸态组织为铁素体+珠光体+石墨(没有渗碳体)时,只需采用低温退火工艺:球墨铸铁低温退火热处理工艺适用范围1。
获得铁素体球墨铸铁;2。
分解渗碳体和珠光体,提高机性能;3。
改善加工性能。
* 保温时间也可按炉内铸件每15mm的有效厚度、需要保温1~2h计算;*形状复杂的铸件,要以75~100℃/h的速率缓慢加热。
关于铸铁加工的工艺流程及参数
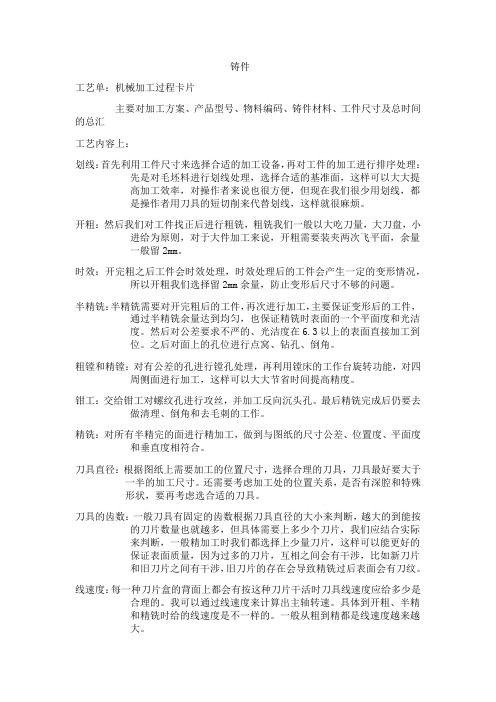
铸件工艺单:机械加工过程卡片主要对加工方案、产品型号、物料编码、铸件材料、工件尺寸及总时间的总汇工艺内容上:划线:首先利用工件尺寸来选择合适的加工设备,再对工件的加工进行排序处理:先是对毛坯料进行划线处理,选择合适的基准面,这样可以大大提高加工效率,对操作者来说也很方便,但现在我们很少用划线,都是操作者用刀具的短切削来代替划线,这样就很麻烦。
开粗:然后我们对工件找正后进行粗铣,粗铣我们一般以大吃刀量,大刀盘,小进给为原则,对于大件加工来说,开粗需要装夹两次飞平面,余量一般留2mm。
时效:开完粗之后工件会时效处理,时效处理后的工件会产生一定的变形情况,所以开粗我们选择留2mm余量,防止变形后尺寸不够的问题。
半精铣:半精铣需要对开完粗后的工件,再次进行加工,主要保证变形后的工件,通过半精铣余量达到均匀,也保证精铣时表面的一个平面度和光洁度。
然后对公差要求不严的、光洁度在6.3以上的表面直接加工到位。
之后对面上的孔位进行点窝、钻孔、倒角。
粗镗和精镗:对有公差的孔进行镗孔处理,再利用镗床的工作台旋转功能,对四周侧面进行加工,这样可以大大节省时间提高精度。
钳工:交给钳工对螺纹孔进行攻丝,并加工反向沉头孔。
最后精铣完成后仍要去做清理、倒角和去毛刺的工作。
精铣:对所有半精完的面进行精加工,做到与图纸的尺寸公差、位置度、平面度和垂直度相符合。
刀具直径:根据图纸上需要加工的位置尺寸,选择合理的刀具,刀具最好要大于一半的加工尺寸。
还需要考虑加工处的位置关系,是否有深腔和特殊形状,要再考虑选合适的刀具。
刀具的齿数:一般刀具有固定的齿数根据刀具直径的大小来判断,越大的到能按的刀片数量也就越多,但具体需要上多少个刀片,我们应结合实际来判断,一般精加工时我们都选择上少量刀片,这样可以能更好的保证表面质量,因为过多的刀片,互相之间会有干涉,比如新刀片和旧刀片之间有干涉,旧刀片的存在会导致精铣过后表面会有刀纹。
线速度:每一种刀片盒的背面上都会有按这种刀片干活时刀具线速度应给多少是合理的。
时效处理

时效处理 (1)固溶热处理: (1)热处理工艺中请问什么是人工时效? (3)什么是时效处理 (3)锻压:超塑成形 (3)预合金粉末与金刚石的扩散连接 (4)异种金属扩散连接技术研究 (7)时效处理金属结构件在铸造、焊接、锻压和机械切削加工过程中,由于热胀冷缩和机械力造成的变形,在工件内部产生残余应力,致使工件处于不稳定状态,降低工件的尺寸稳定性和机械物理性能,使工件在成品后使用过程中因残余应力的释放而产生变形和失效。
为消除残余应力,传统的工艺方法是采用自然时效和热时效。
自然时效是将工件长时间露天放置(一般长达六个月至一年左右),利用环境温度的不断变化和时间效应使残余应力释放。
热时效(TSR)工艺是目前广泛采用的传统机械加工方法,其原理是用炉窑将金属结构件加热到一定温度,保温后控制降温,达到消除残余应力的目的,可以保证加工精度和防止裂纹产生。
振动时效(VSR)工艺是一种可完全取代TSR和NSR的工艺,其原理是用振动消除残余应力,可达到TSR 工艺的同样效果,并在许多性能指标上超过TSR。
固溶热处理:将合金加热至高温单相区恒温保持,使过剩相充分溶速冷却,以得到过饱和固溶体的热处理工艺时效处理可分为自然时效和人工时效两种自然时效是将铸件置于露天场地半年以上,便其缓缓地发生形,从而使残余应力消除或减少,人工时效是将铸件加热到550~650℃进行去应力退火,它比自然时效节省时间,残余应力去除较为彻底.根据合金本性和用途确定采用何种时效方法。
高温下工作的铝合金适宜用人工时效,室温下工作的铝合金有些采用自然时效,有些必须人工时效。
从合金强化相上来分析,含有S相和CuAl2等相的合金,一般采用自然时效,而需要在高温下使用或为了提高合金的屈服强度时,就需要采用人工时效来强化。
比如LY11和LY12,40度以下自然时效可以得到高的强度和耐蚀性,对于150度以上工作的LY12和125-250度工作的LY6铆钉用合金则需要人时效。
铸造残余应力

铸造残余应力及时效方法牟行辉(陕西秦川机床工具集团有限公司,陕西宝鸡721009)铸件在凝固和冷却过程中,由于各部分的冷却速度差异、收缩受阻、及组织转变引起体积变化等因素,不可避免的会产生铸造应力。
如果铸造应力未得到释放,将会以残余应力的形式保留在铸件内。
铸件的残余内应力越大,会使零件在放置、运转、加工和使用过程产生变形,尺寸精度降低严重时会发生开裂。
1,铸造残余应力的形成铸造残余应力是由铸造应力未得到释放而存在于铸件内部的,铸造应力是热应力、相变应力、机械阻碍应力的代数和。
[1]1.1,热应力:铸件各部分冷却速度不同,造成各部分的收缩量不一样,但是铸件的各部分连成一个整体,因此在彼此之间会产生制约而产生应力。
这种由线收缩受热阻碍引起的热应力,一般会成为铸件的残余应力。
其大小与铸件的壁厚差异大小有关,铸件壁厚差异越大,残余应力就越大。
1.2,相变应力:铸件冷却过程发生固态相变的时间和程度不同,其体积变化也不一样,各处相互制约,由此会形成相变应力。
相变应力一般会形成铸件的残余内应力。
1.3,机械阻碍应力:铸件冷却到弹性状态,由于受到机械阻碍而产生应力。
如型砂的退让性太差,阻碍铸件收缩,会使铸件产生机械阻碍应力。
这种应力当机械阻碍消除后,部分应力会消失,但不会完全的消失,部分会形成铸件的残余内应力。
2,减少铸件产生残余应力尽管铸件残余应力可以通过时效处理等方式进行消除和降低,但是时效处理并不能完全消除铸件的残余内应力。
残余内应力的大小取决于原始残余应力的大小。
分析铸件残余应力的成因,可以认为,凡是能够减少体积变化(收缩),降低阻碍的因素,均有利于降低铸件残余应力的产生。
具体可以有以下措施:2.1,在铸造工艺设计时可以通过分型面选择、浇注系统分布、冷铁和保温材料的应用等方式,使铸件实现同时凝固,以减少因铸件结构造成的冷却不均匀;提高砂型的退让性,减少铸型对铸件收缩的阻碍;适当增加铸件在铸型内的冷却时间减弱因空冷造成的各部分冷却不均匀。
球墨铸铁的热处理分析及解决方法
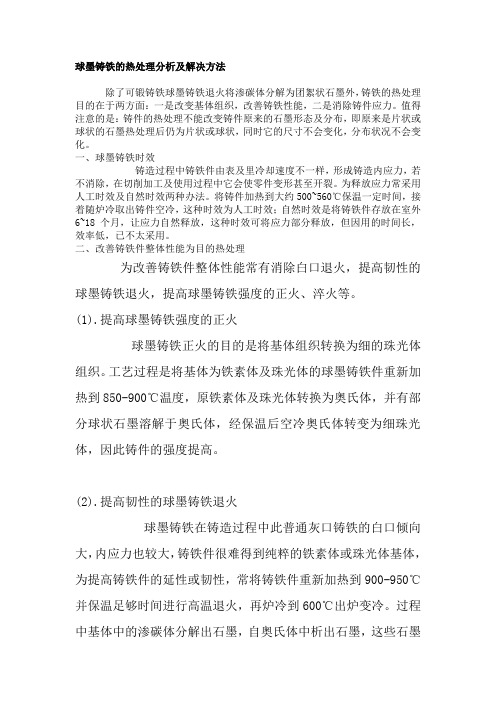
球墨铸铁的热处理分析及解决方法除了可锻铸铁球墨铸铁退火将渗碳体分解为团絮状石墨外,铸铁的热处理目的在于两方面:一是改变基体组织,改善铸铁性能,二是消除铸件应力。
值得注意的是:铸件的热处理不能改变铸件原来的石墨形态及分布,即原来是片状或球状的石墨热处理后仍为片状或球状,同时它的尺寸不会变化,分布状况不会变化。
一、球墨铸铁时效铸造过程中铸铁件由表及里冷却速度不一样,形成铸造内应力,若不消除,在切削加工及使用过程中它会使零件变形甚至开裂。
为释放应力常采用人工时效及自然时效两种办法。
将铸件加热到大约500~560℃保温一定时间,接着随炉冷取出铸件空冷,这种时效为人工时效;自然时效是将铸铁件存放在室外6~18个月,让应力自然释放,这种时效可将应力部分释放,但因用的时间长,效率低,已不太采用。
二、改善铸铁件整体性能为目的热处理为改善铸铁件整体性能常有消除白口退火,提高韧性的球墨铸铁退火,提高球墨铸铁强度的正火、淬火等。
(1).提高球墨铸铁强度的正火球墨铸铁正火的目的是将基体组织转换为细的珠光体组织。
工艺过程是将基体为铁素体及珠光体的球墨铸铁件重新加热到850-900℃温度,原铁素体及珠光体转换为奥氏体,并有部分球状石墨溶解于奥氏体,经保温后空冷奥氏体转变为细珠光体,因此铸件的强度提高。
(2).提高韧性的球墨铸铁退火球墨铸铁在铸造过程中此普通灰口铸铁的白口倾向大,内应力也较大,铸铁件很难得到纯粹的铁素体或珠光体基体,为提高铸铁件的延性或韧性,常将铸铁件重新加热到900-950℃并保温足够时间进行高温退火,再炉冷到600℃出炉变冷。
过程中基体中的渗碳体分解出石墨,自奥氏体中析出石墨,这些石墨集聚于原球状石墨周围,基体全转换为铁素体。
若铸态组织由(铁素体+珠光体)基体,以及球状石墨组成,为提高韧性,只需将珠光体中渗碳体分解转换为铁素体及球状石墨,为此将铸铁件重新加热到700-760℃的共析温度上下经保温后炉冷至600℃出炉变冷。
铸件释放应力的工艺规程

铸件释放应力的工艺规程
铸件在凝固和冷却过程中,由于收缩受阻,各部位冷却速度不同以及组织转变引起体积变化等原因,不可避免地会在铸件内产生内应力。
铸件内应力会使铸件在存放、后续加工及使用过程中产生裂纹或变形,降低铸件的尺寸精度和使用性能,甚至使铸件报废。
因此,对于有较大铸造残留应力的铸件,尤其是形状复杂的大型铸件,应在机械加工前进行消除内应力处理。
铸件在焊补时也会产生内应力,因此,焊补后的铸件也应进行消除内应力处理。
最常采用的铸件消除内应力处理方法是自然时效和人工时效。
自然时效是将铸件平稳地放置在空地上,一般放置6-18个月,最好经过夏季和冬季。
大型铸铁件,如床身,机架等一般采用这种时效方法。
自然时效稳定铸件尺寸的效果比人工时效好,但周期长,因此中小铸件甚至大铸件通常都采用人工时效方法来消除内应力。
人工时效通常指对铸件进行消除内应力回火,即将铸件加热到塑性变形温度范围保持一段时间,使铸件各部位温度均匀化,从而释放铸件内应力,使铸件尺寸趋于稳定,然后使铸件在炉内缓慢冷却到弹性变形温度范围后出炉空冷。
此外,振动时效作为一种消除铸件内应力的新工艺,由于其能耗和处
理成本较低,且在消除内应力及保证铸件尺寸稳定性方面效果显著,也越来越受到重视。
cr20高铬铸铁热处理工艺
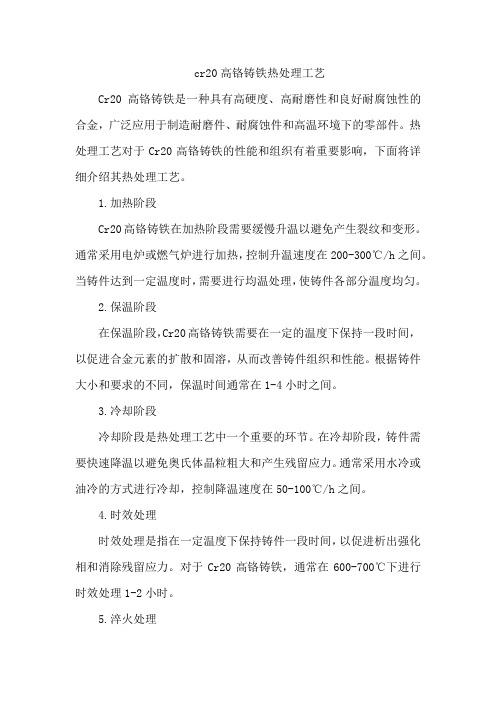
cr20高铬铸铁热处理工艺Cr20高铬铸铁是一种具有高硬度、高耐磨性和良好耐腐蚀性的合金,广泛应用于制造耐磨件、耐腐蚀件和高温环境下的零部件。
热处理工艺对于Cr20高铬铸铁的性能和组织有着重要影响,下面将详细介绍其热处理工艺。
1.加热阶段Cr20高铬铸铁在加热阶段需要缓慢升温以避免产生裂纹和变形。
通常采用电炉或燃气炉进行加热,控制升温速度在200-300℃/h之间。
当铸件达到一定温度时,需要进行均温处理,使铸件各部分温度均匀。
2.保温阶段在保温阶段,Cr20高铬铸铁需要在一定的温度下保持一段时间,以促进合金元素的扩散和固溶,从而改善铸件组织和性能。
根据铸件大小和要求的不同,保温时间通常在1-4小时之间。
3.冷却阶段冷却阶段是热处理工艺中一个重要的环节。
在冷却阶段,铸件需要快速降温以避免奥氏体晶粒粗大和产生残留应力。
通常采用水冷或油冷的方式进行冷却,控制降温速度在50-100℃/h之间。
4.时效处理时效处理是指在一定温度下保持铸件一段时间,以促进析出强化相和消除残留应力。
对于Cr20高铬铸铁,通常在600-700℃下进行时效处理1-2小时。
5.淬火处理淬火处理是将铸件加热到奥氏体化温度后快速冷却,以获得马氏体组织。
对于Cr20高铬铸铁,淬火温度通常为1000-1100℃,冷却方式为水冷或油冷。
6.回火处理回火处理是在淬火后将铸件加热到一定温度并保持一段时间,以降低残留应力和提高韧性。
对于Cr20高铬铸铁,回火温度通常为500-600℃,回火时间根据铸件大小和要求而定。
7.马氏体转变淬火后的Cr20高铬铸铁中存在大量马氏体组织,马氏体是一种硬脆相,具有高硬度和高耐磨性。
在马氏体转变过程中,碳原子从奥氏体中迅速析出并形成碳化物,导致奥氏体转变为马氏体。
8.奥氏体转变奥氏体转变是指Cr20高铬铸铁在加热过程中从马氏体转变为奥氏体。
在奥氏体转变过程中,部分马氏体分解并形成奥氏体组织。
奥氏体是一种软相,具有较好的韧性和塑性。
铸铁件常见铸造缺陷的防止方法

铸铁件经常会发生各种不同的铸造缺陷,如何防止这些缺陷发生,一直是铸件生产厂关注的问题。
本文介绍了笔者在这方面的一些认识和实践经验。
1 气孔特征:铸件中的气孔是指在铸件内部,表面或接近表面处存在的大小不等的光滑孔洞。
孔壁往往还带有氧化色泽,由于气体的来源和形成原因不同,气孔的表现形式也各不相同,有侵入性气孔,析出性气孔,皮下气孔等。
1.1 侵入性气孔这种气孔的数量较少,尺寸较大,多产生在铸件外表面某些部位,呈梨形或圆球形。
主要是由于铸型或砂芯产生的气体侵入金属液的未能逸出而造成。
防止措施:(1)减少发气量:控制型砂或芯砂中发气物质的含量,湿型砂的含水量不能过高,造型与修模时脱模剂和水用量不宜过多。
砂芯要保证烘干,烘干后的砂芯不宜存放太长时间,隔天使用的砂芯在使用前要回炉烘干,以防砂芯吸潮,不使用受潮、生锈的冷铁和芯撑等。
(2)改善型砂的透气性,选择合适的型空紧实度,合理安排出气眼位置以利排气,确保砂芯通气孔道畅通。
(3)适当提高浇注温度,开排气孔和排气冒口等,以利于侵入金属液的气体上浮排出。
1.2 析出性气孔这种气孔多而分散,一般位于铸件表面往往同批浇注的铸件大部分都发现有。
这种气孔主要是由于在熔炼过程中,金属液吸收的气体在凝固前未能全部析出,便在铸件中形成许多分散的小气孔。
防止措施:(1)采用洁净干燥的炉料,限制含气量较多的炉料使用。
(2)确保“三干”:即出铁槽、出铁口、过桥要彻底烘干。
(3)浇包要烘干,使用前最好用铁液烫过,包中有铁液,一定要在铁液表面放覆盖剂。
(4)各种添加剂(球化剂、孕育剂、覆盖剂)一不定期要保持干燥,湿度高的时候,要烘干后才能使用。
1.3 皮下气孔这种气孔主要出现在铸件的表层皮下2~3mm处,直径为1~3mm左右。
而且数量较多,铸件经热处理或粗加工去除外皮后,就会清晰地显露出来。
防止措施;(1)适当提高浇注温度,严格控制各种添加剂的加入量,尽可能缩短浇注时间。
(2)孕育剂的加入量最好控制在(质量分数)0.4%~0.6%,同时要严格控制孕育剂中A1的质量分数,w(Al)偏高容易和型腔表面的水分发生反应:2Al+3H2O=Al2O3+3H2↑,一般情况下孕育剂含Al量不宜超过1.5%。
灰铸铁件的微量自变形

灰铸铁件的微量自变形合金材料中,灰铸铁件最容易发生微量自变形。
灰铸铁件落砂清理后,存在着残余余力,主要是残余热应力,残余热应力除了会使铸件产生冷裂、铸态变形等缺陷外,也是使灰铸铁件产生微量自变形的主要原因。
残余应力即使没有超过屈服强度,但在其作用下灰铸铁随着时间的延续,也会缓慢地发生微量塑性变形(即残余应变),这种变形成为微量自变形。
随着这种变形的发生,残余应力得到松弛,故微量自变形亦称为应力松弛变形。
灰铸铁发生这种变形会使尺寸发生变化,导致机械加工后的灰铸铁尺寸不稳定,谓之尺寸失稳。
形成原因:宏观塑性变形基本上是均不于受力件的整个截面积上,而微量自变形分布是不均匀的,它主要形成于灰铸铁组织中有大量的片状石墨,每片石墨的尖端就是应力集中之处,应力集中处的最大应力值可达到受力件平均应力的8-15倍,当最大应力值超过σmys时,片状石墨的尖端处的基体组织发生微量自变形。
灰铸铁件的微量自变形的应力松弛过程是具有随时间延续而产生连续的、缓慢的塑性变形的特点。
危害:钳工划线台,机密机床基础零件(车床、工作台、立柱等)都用灰铸铁件制作,如果这些基础铸件在使用过程中尺寸失稳,就会导致精密用具、精密机床精度下降,丧失其使用价值。
海钺铸造厂经过多年的生产经验,总结了灰铸铁微量自变形的防止对策:1、灰铸铁牌号的选择,应选择硅/碳比值较高(0.8左右)的,HT250牌号以上的灰铸铁件,制作尺寸稳定性要求高的基础铸件。
2、采取工艺措施,使铸件实现同时凝固和同时冷却,以减小铸件的残余应力,降低微量变形而有利于尺寸稳定。
3、时效处理,获得铸态灰铸铁后,为了使机械加工后的铸件尺寸稳定所进行的尺寸稳定化处理,称之为时效处理,有热时效处理、自然时效处理和共振时效处理等。
机床铸件为什么需要时效处理

机床铸件为什么需要时效处理?
机床铸件时效热处理:为使和机床铸件有所需要的力学性能,物理性能和化学性能,除合理选用材料和各种成形工艺外,热处理工艺是必不可少的.钢铁是机械工业中应用最广的材料,钢铁显微组织复杂,可以通过热处理予以控制,所以钢铁的热处理是金属热处理的主要内容.
机床铸件回火时应严格遵守回火工艺,筋板密集或易变形部位应加支撑筋,防止应回火温度导致变形和断裂.应有专人看管回火炉温度计,及时控制温度,防止温度过高或过低,这样会对回火工件有很大的影响.
机床床身铸件产品作为一种大型铸件必须要经过时效处理才能提高本身的使用性能,改善床身铸件的内在质量.金属热处理是机械制造中的重要工艺环节,与其它加工工艺相比,热处理一般不改变工件的形状和整体的化学成分,而是通过改变工件内部的显微组织,或改变铸铁平台和机床铸件表面的化学成分,赋予或改善工件的使用性能.其特点是改善铸铁平台和机床铸件的内在质量.
温馨提示:沧州同和重工机械公司专业生产精密铸件,球墨铸铁件、灰铁件、大型机床铸件、平板量具系列(平台量具)、机床床身铸件、覆膜砂铸件、铸铁平板、基础平台,我厂工艺精湛,生产和检测设备齐全,技术力量雄厚。
铸造试题4(答案)

铸造试题4(答案)铸造试题4 ⼀、填空题(每⼩题1分共20分)1、碳溶解在α-Fe 中形成的间隙固溶体称为(铁素体)在727℃温时α-Fe中的最⼤溶碳量仅为(0.0218﹪)。
2、渗碳体是含碳量为(6.69﹪)的铁与碳的⾦属化合物,其分⼦式为Fe3C,其熔点为1227℃,(不发⽣)同同素异构体转变。
3、振动落砂机是利⽤铸型与落砂机之间的振动来实现落砂的,按其振动⽅式不同分(偏⼼)振动式惰性振动式和(电磁)振动式。
4、在铸型内储存供补缩铸件⽤的熔融⾦属的空腔成为(冒⼝),通常位于铸型的(顶部)或热节附近。
5、⽤⾼温⾦属液冲浸,使铸件缺陷部位的(本体⾦属)表⾯熔化并与填补的⾦属熔合,以修补缺陷的⽅法叫(⾦属熔补)。
6、铸件的裂纹、⽓孔、砂眼、缩孔、冷隔等缺陷可进⾏(焊接)修补,常⽤的修补⽅法有(⽓焊和电焊)两种。
7、对铸件上不太重要部位的(孔眼)类缺陷,在(技术条件)许可时,可⽤腻⼦修补。
8、向⾼模数的⽔玻璃中加⼊适量的(氢氧化钠),以中和⼀部分游离的(⼆氧化硅)可使其模数值降低。
9、往低模数的⽔玻璃中加⼊适量(氯化铵)或盐酸,中和⼀部分(氢氧化钠),从⽽降低碱度,提⾼模数。
10、对铸铁件进⾏时效处理是为了消除铸造(应⼒);进⾏正⽕、淬⽕是为了提⾼铸铁件的(硬度和耐磨性)。
11、对于灰铸铁⽽⾔,Mn、S都是铁液的(表⾯活性元素),当含量超标时都会产⽣众多的(⽪下⽓孔)。
12、在灰铸铁液中加⼊稀⼟元素碲或铋能脱氧脱硫提⾼铁液的(表⾯张⼒),因此能有效的防⽌湿型灰铸铁产⽣(⽪下⽓孔)。
13、浇注时,煤粉在⾦属铸型界⾯形成(还原性⽓膜),不仅可防⽌铸件粘砂,⽽且还能抑制界⾯的还原反应,也能有效防⽌(⽪下⽓孔)。
14、⾚铁矿粉是⼀种(助熔剂),能降低型砂的烧结温度⽽形成玻璃层,抑制了⾦属—铸型界⾯的化学反应,能够有效体防⽌(⽪下⽓孔)。
15、砂芯在⾦属液的热作⽤和(浮⼒)作⽤下,其位臵发⽣偏移导致铸件内腔或外形与图样要求不符合,这种缺陷叫(偏⼼或漂芯)。
工程材料-第八章_铸铁

灰口铸铁的性能: 灰口铸铁的性能:
主要铸铁具有与钢相近的力学性能,可部分替代钢制造承受震动、 球墨铸铁具有与钢相近的力学性能,可部分替代钢制造承受震动、 载荷大的零件,如曲轴、传动齿轮等。 载荷大的零件,如曲轴、传动齿轮等。 铸铁曲轴
轧辊与辊环
球 墨 铸 铁 制 品
管道接口
核燃料贮存运输容器
第八章 铸铁-§8.2 常用铸铁的组织和性能 三、蠕墨铸铁(Vermicular Graphite iron) )
1.冷却(结晶) 1.冷却(结晶)时的石墨化 冷却
(1)从液相中析出石墨 L → GⅠ 共晶反应) L → γ + G (共晶反应) (2)从奥氏体中析出石墨
特别提示: 特别提示:
灰铸铁、球墨铸铁、蠕墨铸铁 灰铸铁、球墨铸铁、 在冷却时通过析出石墨而获得。 在冷却时通过析出石墨而获得。
γ → GⅡ
(3)由共析反应生成石墨
举例:QT 5 0 0-05 举例: -
延伸率不低于5% 延伸率不低于5% 抗拉强度不小于500MPa 抗拉强度不小于500MPa “球铁”之汉语拼音字头 球铁”
第八章 铸铁-§8.2 常用铸铁的组织和性能
2.球墨铸铁的组织 2.球墨铸铁的组织
电 镜 下 的 石 墨 球
第八章 铸铁-§8.2 常用铸铁的组织和性能
本章介绍灰口铸铁
第八章 铸铁 灰口铸铁的种类: 灰口铸铁的种类:
按石墨的形态,灰口铸铁分为四类: 按石墨的形态,灰口铸铁分为四类: 灰铸铁: 灰铸铁:石墨呈片状
铸件热处理工艺及作业指导书主
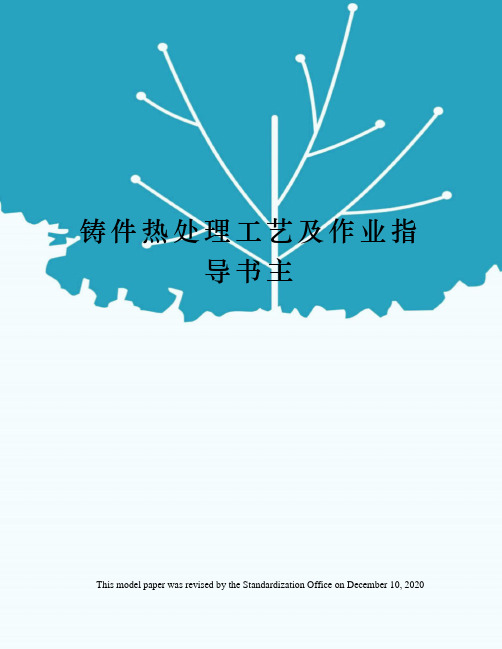
铸件热处理工艺及作业指导书主This model paper was revised by the Standardization Office on December 10, 2020前提:本作业指导书系建蓓铸造有限公司的核心工艺文件之一。
它针对公司产品实现的第三个特殊过程(见《公司质量手册》章节号之4.1.7)提出了系统完整的操作、控制规定,必须得到充分严格贯彻执行。
本作业指导书所取参数,主要源于化工出版社的《钢铁热处理实用技术》。
* 本作业指导书中打“*”并用楷体注明的文字,是警/提示内容,也可作为执行条款。
1.灰铸铁的退火、正火热处理工艺1.1消除内应力退火(人工时效)工艺灰铸铁消除内应力退火(人工时效)热处理工艺适用范围1.较薄、故冷却速度较快的灰铁件;2.形状复杂、截面变化较大的铸件;3.需进行机加工的大型铸件;4.经过少量焊修,因而局部积累些许焊应力的铸件。
* 加热温度越高,应力消除越快。
但温度过高,则易发生石墨化与珠光体球化而使性能降低,尤其是含Si量较高时;* 保温时间一般按炉内铸件平均壁厚的5min/mm计算。
形状复杂的铸件,要以75~100℃/h的速率缓慢加热;* 保温时间终了,以30~50℃/h的速率在炉内缓冷,冷却至150~200℃出炉冷却(空冷)。
1.2软化退火和正火工艺灰铸铁软化退火和正火热处理工艺适用范围3.正火工艺适用于对材质有硬度要求的铸件,退火工艺适用于对材质有韧性要求的铸件;4.经过较多焊修,因而积累较大焊应力的铸件。
* 保温时间一般按炉内铸件平均壁厚的5min/mm计算。
形状复杂的铸件,要以75~100℃/h的速率缓慢加热。
2.球墨铸铁的退火、正火(+回火)和调质热处理工艺高温退火当铸态组织为铁素体+珠光体+渗碳体+石墨时,必须采用高温退火工艺:适用范围1.获得铁素体球墨铸铁;2.分解渗碳体和珠光体,提高机械性能;3.改善加工性能,使工件容易加工且不易变形。
铸造工艺知识及对产品设计的要求
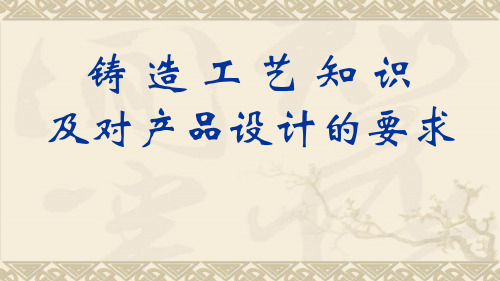
1、铸造工艺流程
2、铸造工艺方案
铸造合金的种类、零件的结构与技术要求、生 产批量的大小和生产条件是确定铸造工艺方案的 依据。
确定铸造工艺方案主要是选择合理的浇注位置 和分型面。
分型面的选择应尽量与浇注位置一致,以避免 合型后翻转砂型。但平做立浇的铸件除外,如压 力机导套。
❖ 使用上表时的几点规定: ❖ ①当铸件尺寸公差等级和铸件机械加工余量等级确定后,其
加工余量数值应按有加工要求的表面上最大基本尺寸和该表 面距它的加工基准间尺寸两者中较大的尺寸所在范围,从表 2中选取加工余量数值。 ❖ ②确定旋转体加工余量时,铸件基本尺寸取其直径或高度 (长度)中较大的尺寸。 ❖ ③当砂型铸件底、侧面所采用的加工余量等级选定后,其顶 面的加工余量等级原则上采用降一级所对应的数值。 ❖ ④砂型铸造孔的加工余量等级由铸造工艺的保证性确定,可 适当加大。原则上降一级。 ❖ ⑤一般情况下一种铸件只能选取一个尺寸公差等级,当有特 殊要求时,可由供需双方商定采用非标准的加工余量。 ❖ 检验与评定时,当铸件实际测量尺寸位于铸件基本尺寸的公
用途是:制造模样、模板、芯盒等,并作为生 产准备和模样验收依据;是用于生产的指导性技 术文件及铸件尺寸验收依据。
铸造工艺卡片
三、铸铁件的热时效处理
对于不进行特殊热处理的重要铸铁件,特别是 机床铸件都要进行低温退火以降低或去除残余应 力,从而保持零件的尺寸精度,这种热处理又称 为热时效。
热时效是将铸件加热至弹塑性温度范围,为使 铸件各部分温度均匀和残余应力在此区间得到松 弛和稳定化而予以保温,然后缓慢冷却至弹性变 形的温度范围内,出炉空冷。
②有色金属铸件:主要生产铜合金铸件和 铝合金铸件。铜合金铸件以压力机铜套为主, 采用电炉熔炼、离心铸造工艺。铝合金铸件 采用砂型(红砂)、电炉熔炼工艺。
球墨铸铁热处理方法
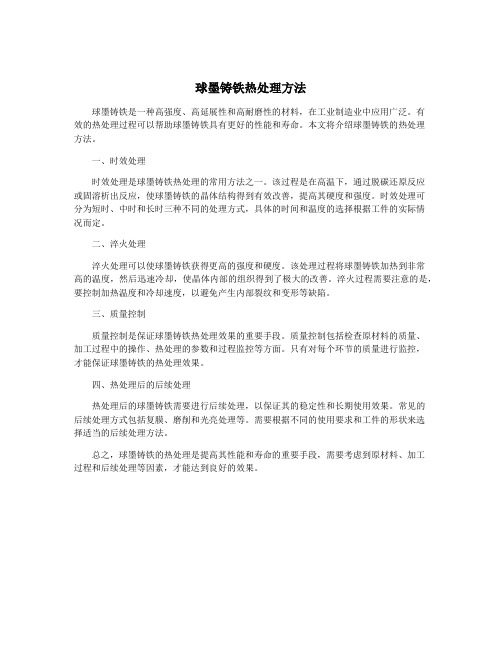
球墨铸铁热处理方法
球墨铸铁是一种高强度、高延展性和高耐磨性的材料,在工业制造业中应用广泛。
有
效的热处理过程可以帮助球墨铸铁具有更好的性能和寿命。
本文将介绍球墨铸铁的热处理
方法。
一、时效处理
时效处理是球墨铸铁热处理的常用方法之一。
该过程是在高温下,通过脱碳还原反应
或固溶析出反应,使球墨铸铁的晶体结构得到有效改善,提高其硬度和强度。
时效处理可
分为短时、中时和长时三种不同的处理方式,具体的时间和温度的选择根据工件的实际情
况而定。
二、淬火处理
淬火处理可以使球墨铸铁获得更高的强度和硬度。
该处理过程将球墨铸铁加热到非常
高的温度,然后迅速冷却,使晶体内部的组织得到了极大的改善。
淬火过程需要注意的是,要控制加热温度和冷却速度,以避免产生内部裂纹和变形等缺陷。
三、质量控制
质量控制是保证球墨铸铁热处理效果的重要手段。
质量控制包括检查原材料的质量、
加工过程中的操作、热处理的参数和过程监控等方面。
只有对每个环节的质量进行监控,
才能保证球墨铸铁的热处理效果。
四、热处理后的后续处理
热处理后的球墨铸铁需要进行后续处理,以保证其的稳定性和长期使用效果。
常见的
后续处理方式包括复膜、磨削和光亮处理等。
需要根据不同的使用要求和工件的形状来选
择适当的后续处理方法。
总之,球墨铸铁的热处理是提高其性能和寿命的重要手段,需要考虑到原材料、加工
过程和后续处理等因素,才能达到良好的效果。
铸件、锻件、焊接件残余应力的产生和时效方法
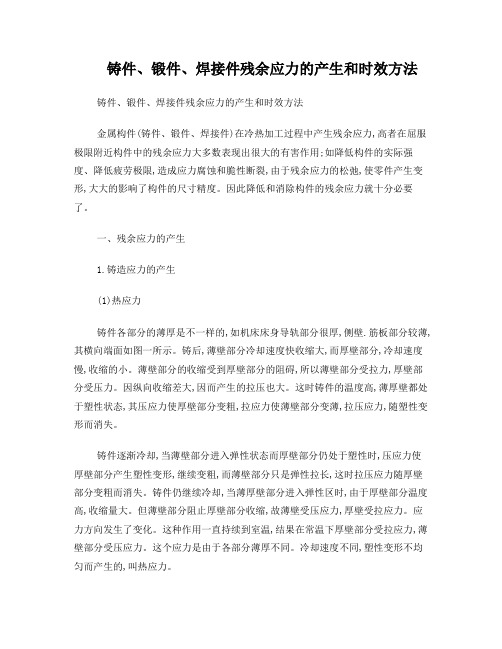
铸件、锻件、焊接件残余应力的产生和时效方法铸件、锻件、焊接件残余应力的产生和时效方法金属构件(铸件、锻件、焊接件)在冷热加工过程中产生残余应力,高者在屈服极限附近构件中的残余应力大多数表现出很大的有害作用;如降低构件的实际强度、降低疲劳极限,造成应力腐蚀和脆性断裂,由于残余应力的松弛,使零件产生变形,大大的影响了构件的尺寸精度。
因此降低和消除构件的残余应力就十分必要了。
一、残余应力的产生1.铸造应力的产生(1)热应力铸件各部分的薄厚是不一样的,如机床床身导轨部分很厚,侧壁.筋板部分较薄,其横向端面如图一所示。
铸后,薄壁部分冷却速度快收缩大,而厚壁部分,冷却速度慢,收缩的小。
薄壁部分的收缩受到厚壁部分的阻碍,所以薄壁部分受拉力,厚壁部分受压力。
因纵向收缩差大,因而产生的拉压也大。
这时铸件的温度高,薄厚壁都处于塑性状态,其压应力使厚壁部分变粗,拉应力使薄壁部分变薄,拉压应力,随塑性变形而消失。
铸件逐渐冷却,当薄壁部分进入弹性状态而厚壁部分仍处于塑性时,压应力使厚壁部分产生塑性变形,继续变粗,而薄壁部分只是弹性拉长,这时拉压应力随厚壁部分变粗而消失。
铸件仍继续冷却,当薄厚壁部分进入弹性区时,由于厚壁部分温度高,收缩量大。
但薄壁部分阻止厚壁部分收缩,故薄壁受压应力,厚壁受拉应力。
应力方向发生了变化。
这种作用一直持续到室温,结果在常温下厚壁部分受拉应力,薄壁部分受压应力。
这个应力是由于各部分薄厚不同。
冷却速度不同,塑性变形不均匀而产生的,叫热应力。
在导轨或侧壁的同一个截面内,表层与内心部,由于冷却快慢不同,也产生相互平衡拉压的应力,用类似与上述方法分析,可知在室温下表层受压应力,心部受拉应力,并且截面越大,应力越大,此应力也叫热应力。
(2)相变应力常用的铸铁含碳量在2.8-3.5%,属于亚共晶铸铁,由结晶过程可知①:厚壁部分在1153℃共晶结晶时,析出共晶石墨,产生体积膨胀,薄壁部分阻碍其膨张,厚壁部分受压应力,薄壁部分受拉应力,薄辟部分受拉应力。
- 1、下载文档前请自行甄别文档内容的完整性,平台不提供额外的编辑、内容补充、找答案等附加服务。
- 2、"仅部分预览"的文档,不可在线预览部分如存在完整性等问题,可反馈申请退款(可完整预览的文档不适用该条件!)。
- 3、如文档侵犯您的权益,请联系客服反馈,我们会尽快为您处理(人工客服工作时间:9:00-18:30)。
铸铁件的时效处理
时效处理可分为自然时效和人工时效两种。
自然时效是将铸件置于露天场地半年以上,便其缓缓地发生形,从而使残余应力消除或减少,人工时效是将铸件加热到550~650℃进行去应力退火,它比自然时效节省时间,残余应力去除较为彻底.
振动时效技术发展史
使用振动处理方法消除或均化金属件的残余应力,以代替热时效(焖火)。
这种新技术在国外被称作:“Vibratory Stress Relief Method”(简称VSR)引进我国后又称“振动时效”该技术源于美国发展和应用于英国、法国、前苏联。
据统计,目前世界上正在使用的VSR 设备有一万台以上,许多国家都已将振动时效定为某些机械构件必须采用的标准工艺,我国的振动时效技术经过科研人员的不懈努力在机理和应用上取得了突破性的进展,一些技术指标已达到或超过国外同类设备的先进水平。
人工时效是退火吗?
对于铸铁件来说,人工时效就是热时效。
也就是一种能够快速降低铸件内应力的退火工艺。
时效现在有三种方式:自然时效、人工时效、振动时效。
自然时效和热时效,即工件露天长时间放置,由于温度的自然变化以及其它环境变化使工件的尺寸日趋稳定。
一般说来这需长达两年的时间。
用木锤敲击工件,用风握直接振动等,在实际生产中都有应用,有人认为用机械施加工件即相当于加速自然时效,这种方法在国外早有专刊。
它的基本原理就是采用激振器的周期外力-激振力的作用下,使之与工件发生共振(激振器产生与工件本征频率相一致的振动频率)。
从而获得相当大的振动能量,这种能量可以和热能相比的、共振中交变的初应力与残余应力相叠加,驱使工件产生更大的振动,发生局部屈服,使晶体内部错位和晶界产生微观滑移,引起微量塑性变形,促使大量错位一部分钉轧在杂质上,另一部分聚集到晶粒间界上,另外还有一部分错位获得足够大的能量,可以穿过晶界而进入另一个晶粒内,这样从总体看工件的残余应力得到松弛或均化,在宏观上表现为尺寸稳定、刚度、耐腐蚀性、耐疲劳性提高,金属内耗下降,塑性得到改善。
由于晶粒内位错大量聚集在晶界和杂志上,所以造成各个晶粒内应力的完全不均匀性,使微观应力提高。
由此错位处在更大的大型应力场内,滑移阻尼增大,所以位错再滑移是非常困难的。
振动时效消除残余应力就是将激振器紧紧固定于工件上施加机械振动,工件放置于橡胶块或者其他弹性支撑上,以防止地面对振动的阻尼作用,振动频率通过控制器控制调节电机转速获得,频率通常在167HZ以内,整个设备消耗电能很低,一般不超过1KW,对于大多数工件,15分钟振动即可消除或均化应力,使工件尺寸稳定精度提高,处理的工件重量从几十公斤到上百吨。
时效三种方式:
对于铸铁件来说,人工时效就是热时效。
也就是一种能够快速降低铸件内应力的退火工艺。
时效现在有三种方式:自然时效、人工时效、振动时效。
自然时效和热时效,即工件露天长时间放置,由于温度的自然变化以及其它环境变化使工件的尺寸日趋稳定。
一般说来这需长达两年的时间。
用木锤敲击工件,用风握直接振动等,在实际生产中都有应用,有人认为用机械施加工件即相当于加速自然时效,这种方法在国外早有专刊。
它的基本原理就是采用激振器的周期外力-激振力的作用下,使之与工件发生共振(激振器产生与工件本征频率相一致的振动频率)。
从而获得相当大的振动能量,这种能量可以和热能相比的、共振中交变的初应力与残余应力相叠加,驱使工件产生更大的振动,发生局部屈服,使晶体内部错位和晶界产生微观滑移,引起微量塑性变形,促使大量错位一部分钉轧在杂质上,另一部分聚集到晶粒间界上,另外还有一部分错位获得足够大的能量,
可以穿过晶界而进入另一个晶粒内,这样从总体看工件的残余应力得到松弛或均化,在宏观上表现为尺寸稳定、刚度、耐腐蚀性、耐疲劳性提高,金属内耗下降,塑性得到改善。
由于晶粒内位错大量聚集在晶界和杂质上,所以造成各个晶粒内应力的完全不均匀性,使微观应力提高。
由此错位处在更大的大型应力场内,滑移阻尼增大,所以位错再滑移是非常困难的。
振动时效消除残余应力就是将激振器紧紧固定于工件上施加机械振动,工件放置于橡胶块或者其他弹性支撑上,以防止地面对振动的阻尼作用,振动频率通过控制器控制调节电机转速获得,频率通常在167HZ以内,整个设备消耗电能很低,一般不超过1KW,对于大多数工件,15分钟振动即可消除或均化应力,使工件尺寸稳定精度提高,处理的工件重量从几十公斤到上百吨。
振动时效技术又称“振动消除应力法”,国外简称“VSR”技术。
它的实施过程是通过振动时效装置的控制系统控制激振器的转数和偏心作用在工件上产生离心力,使工件发生共振(谐振),让工件需时效部位产生一定幅度、一定周期的交变运动,并吸收能量,经过一定时间的振动引起工件微小塑性变形及晶粒内部位错逐渐滑移,并重新缠绕钉扎使得残余应力被消除和均化,防止工件变形和开裂,从而达到提高工件尺寸精度稳定性,增强工件的抗变形能力和提高疲劳寿命。
◆从宏观角度分析振动时效使零件产生塑性变形,降低和均化残余应力并提高材料的抗变形能力,无疑是导致零件尺寸精度稳定的基本原因。
从分析残余应力松驰和零件变形中可知,残余应力的存在及其不稳定性造成了应力松驰和再分布,使零件发生永久塑性变形。
故通常采用热时效方法以消除和降低残余应力,特别是危险的降值应力,振动时效同样可以降低残余应力,零件在振动处理后残余应力通常可降低30—80%,同时也使峰值应力降低使应力分布均匀化。
◆从微观方面分析振动时效可视为一种以循环载荷的形式施加于零件上的一种附加动应力,众所周知工程上采用的材料都不是理想的弹性体,其内部存在着不同类型的微观缺陷,铸铁中更是存在着大量形状各异的切割金属基体的石墨。
故而无论是钢、铸铁或其他金属,其中的微观缺陷附近都存在着不同程度的应力集中,当受到振动时,施加于零件上的交变应力与零件中的残余应力叠加。
当应力叠加的结果到一定的数值时,在应力集中最严重的部位就会超过材料的屈服极限而发生塑性变形。
这种塑性变形降低了该处残余应力降值,并强化了金属基体,而后振动又在一些应力集中较严重的部位上产生同样作用,直至振动附加应力与残余应力叠加的代数和不能引起任何部位的塑性变形为止,此时振动便不再产生消除和均化残余应力及强化金属的作用。
◆实践证明振动时效替代热时效后可节约能源90%以上,提高抗变形能力30%以上,尺寸稳定性提高30%以上,疲劳寿命提高20%以上。
处理时效通常只需15—45分钟,不分场地,不受工件尺寸、形状、重量等限制,可处理几公斤至几百吨的工件。
便携工件不需运输可就地处理,可插在任何工序之间进行处理。
采用振动时效可提高工效几十倍,它具有减少环境污染、缩短生产周期、改善劳动条件、工艺简便等优点,是一项投资少、见效快、综合效益显著的工艺。
◆振动时效适应于碳素结构钢、低合金钢、不锈钢、铸铁、有色金属(铜、铝、锌及其合金)等铸件、锻件和焊接件。