制程设计和开发程序
浅谈APQP(量产之前的质量计划)

浅谈APQP(量产之前的质量计划)2008年12月18日AM 09:11APQP (Advanced Product Quality Planning):量产之前的质量计划~~定义:产品从研发到生产应该有一套完整的质量规划及管制计划,制定各阶段的作业方式与质量活动,以确保产品在研发、初期样品、小批量试作、量产,等阶段之管理活动有效运作。
APQP参考手册经QS9000条文的引用,字句中有Shall、Will、Must是具有强制性,的其他并不强制,窗体中示范仅供参考用不强制性。
APQP规划时程:5个阶段1.企划及开发阶段。
2.产品开发设计验证。
3.制程设计开发阶段。
4.产品及制程确认。
5.回馈稽查及矫正措施。
APQP的PDSA:P-plan,D-do,S-study,A-act∙企划及开发阶段(第一阶段):Plan and Define Program 从概念提出到开发计划核准。
1.确保客户需求与期望被充分了解。
2.投入因素:1.来自客户反应的讯息:a.市场研究 b.客诉记录与质量履历数据 c.小组经验。
2.经营计划/营销3.产品或制程的标竿。
4.产品或制程描诉。
5.产品可靠度研究。
6.客户需求与期望(满意度指标)。
3. 产出项目:1.设计目标(概念之具体化与量化)。
2.可靠度与质量目标。
3.初期材料清单(含分包商名单)。
4.初期制程流程图。
5.初期制造与产品之管制特性列表。
:决定特殊特性因素有:a.客户或图面指定 b.A级或AR及 c.跨功能小组决定 d.过去质量履历 e.严重度较高者或成本较高者。
6.产品保证计划。
7.管理阶层之支持。
∙产品开发设计验证(第二阶段):Production Define &Development verification 从计划到原型产品建立。
1.以原型产品(Prototype)确认产品或服务是否符合客户要求或期望。
2.有效考虑产能、开发时机时程要求、工程要求、质量要求、投资成本、与单位成本。
软件开发流程的具体内容

软件开发流程的具体内容软件开发是一个复杂而又精细的过程,需要经历多个阶段和环节。
下面将介绍软件开发的具体流程,以便更好地了解软件开发的全貌。
1. 需求分析阶段。
软件开发的第一步是需求分析阶段。
在这个阶段,开发团队与客户进行沟通,了解客户的需求和期望。
通过讨论和调研,确定软件的功能和特性,明确软件的用户群体和使用场景,为后续的开发工作奠定基础。
2. 设计阶段。
在需求分析的基础上,开发团队进行软件的设计工作。
包括系统架构设计、数据库设计、界面设计等。
设计阶段的目标是确定软件的整体结构和各个模块的功能,为后续的编码工作提供指导。
3. 编码阶段。
编码阶段是软件开发的核心阶段,开发团队根据需求和设计文档,进行具体的编码工作。
根据需求文档和设计文档,开发团队使用相应的编程语言和开发工具,编写软件的源代码。
4. 测试阶段。
编码完成后,软件需要进行测试。
测试阶段包括单元测试、集成测试、系统测试等多个环节。
测试人员根据测试计划和测试用例,对软件进行全面的测试,确保软件的质量和稳定性。
5. 部署和维护阶段。
软件通过测试后,进入部署和维护阶段。
开发团队将软件部署到目标环境中,并进行相关的配置和优化。
同时,开发团队需要对软件进行维护和更新,确保软件的稳定性和安全性。
总结。
软件开发流程包括需求分析、设计、编码、测试、部署和维护等多个阶段。
每个阶段都有其独特的任务和目标,需要开发团队的密切合作和高效协调。
只有经过严格的流程管理和质量控制,才能保证软件开发的顺利进行和最终的成功交付。
新产品开发流程和基本工艺
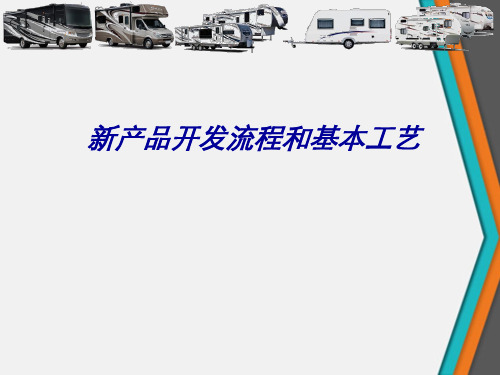
一、新产品设计开发分成五个阶段:
项目立项阶段
客户技阶段
1 • 项目立项 2 • 客户技术要求转化及产品初期分析 3 • 产品过程开发阶段 4 • 试生产阶段 5 • 批量生产
Page 4
1、1项目立项阶段
整车开发日程 灯具A面、效果图、车身钣金 产品规范:外观、性能、配光、 品质要求、配合尺寸 试验要求:环境及试验条件
形成书面文件
间隙 高低差
样灯
产出相关文件
装车后产出相关文件
认证报告 试验报告 装车记录 测量系统分析报告 PPK 生产控制计划
5、小批量生产阶段
90 80 70 60 50 40 30 20 10
0 第一季度 第二季度 第三季度 第四季度
东部 西部 北部
8
7
6
5
4
3
2
1
0
1
2
3
4
5
6
7
系列1 系列2
1 2 3 4 5 6 7
QC小组
技术部
生产部
产出相关文件
OK
✓— ✓—
3、产品过程开发阶段
产品要求
型腔材料 模板材料
冷却水路 浇口位置
顶出装置 模面处理
模穴数
团队
① 评估供应商的质量系统 质量部
② 评估供应商的技术力量、检 测能力、环境条件、生产能力
技术部 ② 评估供应商的服务态度
采购部
团队
外协件开发 技术协议
工装夹具制作
产出相关文件
1 产品特性清单
1、2新产品分析
材料
性能
外观
尺寸
模具 生产技术 设备 开发周期
公司技术部全体成员:
HSF产品设计开发控制程序
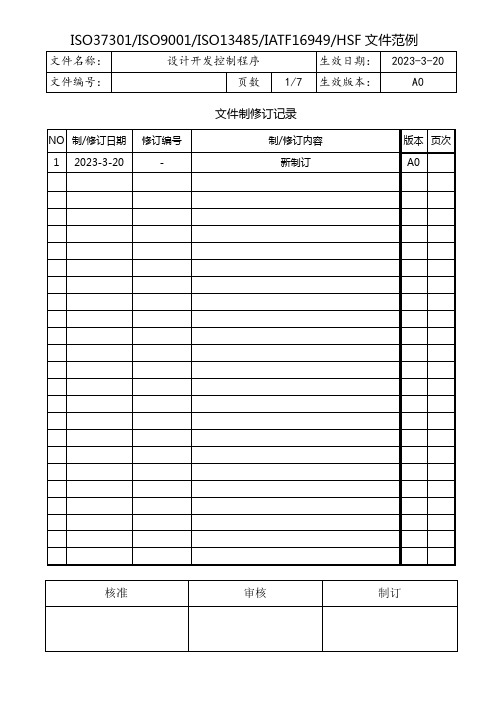
文件制修订记录1.0目的使开发设计作业的各阶段能够依照设计规格及客户要求事项施以管制及验证,以确保开发设计的质量。
2.0适用范围开发部门职掌包括HSF在内产品设计开发作业程序。
3.0权责3.1.总经理:产品继续开发与否的审查及各阶段审查结果的总裁决。
3.2.设计审查会:针对开发各阶段实施设计审查,力求设计内容合乎各种规定,确保设计结果的正当性。
3.3.市场部:协助设计单位取得对于产品开发的注意事项及情报分析数据。
3.4.技术:管理监督指导自己单位负责的产品开发设计作业,由单位主管依《人力资源作业程序》实施指派合格人员主办设计开发计划。
3.5.生产部:生产部执行试作及生产作业,将试作过程中不良状况随时回馈开发部并提供改善意见。
3.6.品质:负责依据《产品验证作业程序》,对完成试作品的质量验证流程,以作为产品生产之依据,并将质量状况随时回馈给开发部。
3.7.技术:负责针对新产品承接,做好技术转移工作以及参与开发各阶段审查工作。
4.0定义4.1关键特性:影响国家、行业法规要求或产品功能安全性、环境保护等,包括需要特殊生产、装配、发运或的产品要求或参数。
4.2特殊特性:指由顾客指定的产品和过程特性,包括显著影响政府法规和安全特性及显著影响顾客满意的产品和过程特性,和/或由公司通过产品和过程的了解选出的特性。
4.3 APQP:产品质量先期策划和控制计划。
4.4 PPAP:生产件批准程序。
4.5 DFMEA:设计失效模式及后果分析;是一种动态文件,随顾客需要和期望不断更新。
4.6 PFMEA:过程失效模式及后果分析;是一种动态文件,当发现新的失效模式时则需要对现有的PFMEA进行评审和更新。
5.0作业程序5.1.产品企划阶段(C0)5.1.1市场部依市场或客户需求提出《产品开发规格需求书》并给开发部,如未通过则退回市场部重新企划。
5.1.2由总经理(副总)、技术主管、市场主管组成产品企划审查小组,审查内容为:1.市场行销及需求的可行性-《产品开发规格需求书》。
APQP第三阶段01
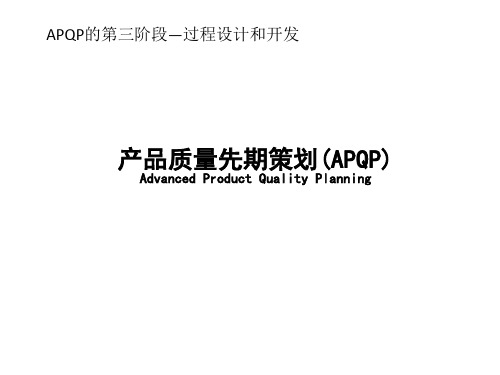
•试生产控制计划: (1)对试生产所用材料/试生产产品的尺寸和功能/性能所安排的检 验和试验活动,为验证/确认提供所需的可靠数据 (2)在样件控制计划(如已有)基础上编制 (3)是编制批量生产控制计划的基础 (4)仍需按流程图编制,在试生产前完成 •作业指导书: (1)是具体指导作业人员实施作业控制的文件 (2)是控制计划的展开 (3)过程指导书通常有:作业指导书,检验指导书,返工指导书,作 业准备调整指导书等,还有其他叫法,如:操作规程,工序卡等,格 式由组织确定 (4)作业指导书应使操作者易于得到
(Pp,Ppk):过程性能指数:
是根据采集到的数据对当前过程性能的估计,PPK是衡量不稳定或不知道是否稳 定的过程(如初始过程)的性能的一个指标(过程不受控),一般试生产时(模具 维修时,新模具验收时等)实施,表示的是过程在过去一段时间内的表现。比如: 一个人的工作表现
备注:一切以顾客要求为准,顾客可以提供表格和内容要求
DFMEA和PFMEA的关系
•DFMEA:是设计阶段对产品自身的材质和性能的失效分析并作出预防 措施。 •PFMEA:是产品可能在生产过程中的材质、性能、操作流程或手段的 失效分析并作出预防措施。
PPAP中过程流程图、PFMEA、控制计划的关系
二、过程设计和开发的输出
•包装标准
•产品/过程质量体系评
审 •过程流程图 •场地平面布置图 •特性矩阵图 •PFMEA
•试生产控制计划 •作业指导书 •测量系统分析计划 •初始过程能力研究计 划
•包装规范
•管理者支持
•包装标准: 系指顾客对包装提出的要求,包装主要的功能有:产
品防护;便于搬运,贮存管理,所以通常顾客会提出对包 装的相关要求 •产品/过程质量体系评审: (1)对象:现有的产品/过程/质量体系对新产品/新过 程的适合程度 (2)目的:寻求对现有过程/质量体系的改进 (3)结果:文件变更,作为过程其后开发活动的输入
五大手册简介-APQP、PPAP、MSA、FMEA、SPC简介

五大手册简介-APQP、PPAP、MSA、FMEA、SPC简介16949五大手册简介-APQP、PPAP、MSA、FMEA、SPC简介ISO/TS 16949:2009参考手册的应用与案例目录前言一、产品质量先期策划和控制计划(A P Q P) 11.产品质量先期策划的由来 12.产品质量策划责任矩阵图 13.产品品质规划的基本原则 14.产品质量策划的基本步骤 25.A P Q P的主要内容 4 案例:先期产品质量策划控制程序13二、生产性零组件核准程序(P P A P)161.范围、定义和目的162.何时要求提交163.生产件核准的要求174.提交等级175.过程要求196.记录和原型样品的保存207.零组件提交状态20案例:生产件核准程序21三、失效模式与效应分析(F M E A)221.F M E A简介222.实施重点233.设计的D F M E A(D e s i g n F M E A)234.分析方式(A n a l y s i s A p p r o a c h)245.F M E A程序(F M E A P r o c e s s)246.F M E A表格内容说明25案例:F M E A制作办法30 附件:F M E A软件30四、测量系统分析(M S A—M e a s u r e m e n t S y s t e m s A n a l y s i s)311.测量系统变差的类型312.测量系统分析33附件:M S A软件46五、统计过程控制(S P C—S t a t i s t i c P r o c e s s C o n t r o l)471.控制图47案例X—R控制图应用案例58 案例P控制图(不合格品率控制图)58 案例缺陷数控制图(C图)61 案例工序能力指数计算68 案例:S P C控制程序683附件:SPC系统实施步骤 694前言ISO/TSl6949:2009并未指定其核心工具的具体内容,故组织在推行ISO/TSl6949:2009时,对核心工具的选择有较大的自由度。
apqp开发流程

apqp开发流程APQP(Advanced Product Quality Planning,先进产品质量计划)是一种用来指导新产品开发过程的方法论,旨在确保产品在设计和制造阶段都能达到预期的质量要求。
下面将介绍APQP的开发流程。
APQP的开发流程共有五个主要阶段:计划和定义、产品设计和开发、制程设计和开发、产品和过程验证、生产开始。
第一阶段:计划和定义在这个阶段中,制定一个明确的计划,确定产品的性能目标和相应的质量标准。
同时,明确产品各个阶段的开发与验证任务,并制定项目时间表和资源分配计划。
第二阶段:产品设计和开发在这个阶段中,进行产品的基本设计、详细设计和样品制作。
同时,进行产品的功能分析、可靠性工程、安全性能评估以及质量风险分析。
最后,制作初样进行验证,包括功能验证和可制造性验证。
第三阶段:制程设计和开发在这个阶段中,设计和开发生产所需的工艺流程和设备,制定操作指导书。
同时,进行制程的可行性评估,并提供工序的质量控制标准。
最后,制作工艺流程示意图和图纸。
第四阶段:产品和过程验证在这个阶段中,通过制作样品和工艺验证,对产品和制程进行验证。
其中,对产品的验证包括性能验证、可靠性验证和安全性能验证;对制程的验证包括制程能力验证和特性验证。
最后,将验证结果进行分析,根据分析结果做出适当的调整和改进。
第五阶段:生产开始在这个阶段中,根据验证结果进行生产准备工作,包括生产设备的调试、员工培训和制程的优化。
同时,建立生产过程中的质量控制机制,确保产品的稳定性。
最后,进行批量生产,并根据质量控制标准进行质量检验和产品发布。
总结来说,APQP的开发流程包括计划和定义、产品设计和开发、制程设计和开发、产品和过程验证以及生产开始等五个阶段。
通过APQP的应用,可以在产品开发过程中制定明确的计划和目标,并通过验证和调整确保产品达到预期的质量要求,最终实现产品的生产和发布。
这一方法论对于提高产品质量、降低生产成本以及满足客户需求具有重要意义。
研发新产品开发流程PPT33页

DR2 阶段的文件产出
DR3 EVT (主导单位: RD)1. EVT (Owner: EE/ME/ F/W /DQA)试做Working Sample, 验证设计概念的可行性及正确性,评估设计开发能力,以提高新产品设计开发技术。2. EVT Evaluation (Owner: PM)PM 召集专案成员针对EVT验证结果进行分析与评估,并对设计问题提出改善方案,解决设计问题。必要时可再次进行EVT, 以确保设计问题处理结果。3. Tooling Start (Owner: RD ME)RD ME依据机构设计的图面,参考上一点的评估后,对图面进行更新。PM填写开模申请单,模具供应商展开模具设计与开发作业。EE/ME/ F/W 准备EVT所需Eng-spec./Panel’s Specifications 的物料与制作Prototype, 由DQA/EE/ME展开Prototype功能性测试验证。
DR3 EVT (主导单位: RD)4. EVT Documentation Release (Owner: RD)ID 工程师针对客户产品规格(需求) 展开外观与使用界面视觉设计(参考[ ID (工业设计)管制作业办法])5. DVT Material Preparation (Owner: PM/ RD)PM协同RD ME/EE根据E-BOM, 准备DVT Sample所需的物料并管控来料状况 (参考[样品制作管制作业办法])6. EVT Test Report (Owner: DQA)DQA整合各Function的EVT各项测试项目的测试报告,制作[EVT TestReport]及[EVT Design Verification Report], 并透过DCC发行。[EVTDesign Verification Report based on Longhorn’s Standard TestPlan]
玻璃设计开发流程
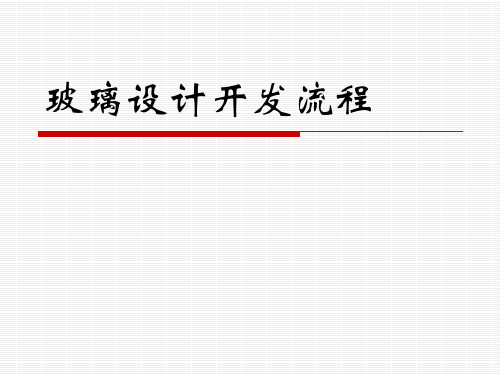
1) 產品規格功能與性能之要求。 2) 現有之技術能力是否能執行此項開發案。
3) 開發進度是否符合公司或客戶要求
4) 討論內容必須包括對產品自身環境影響,生產過程中產生的環境問題,原材 料環境的影響等。
五、量产移移
確認生產後由工程單位召集相關人員實施新產品量 產移轉說明會,並檢附移轉生產前所需之設備、治 具,及規範建立、生產作業標準、及物料需求表, 並以「內部行文單」含移轉清冊通知各單位知悉。
六、图面管理
1.客戶所提供設計之圖面、工程主管在試量产階段分 發給相關單位產品仕樣試作圖面,並蓋「試產 章」,經試作、量試、驗證、承認後分發給相關單 位產品仕樣承認圖面,並蓋上工程單位「工程確認 章」
下墨不均
c.印刷
印刷缺口 刮伤——人员手法、治具周转
常見問題點
d.退镀
退镀不洁——退镀时间、脏污或油墨附着
刮伤——退镀液的选择及退镀时间的管控
e. 清洗: 脏污——擦拭药剂比例、清洗药剂比例、纯水洁净度 (成品)
酒精印——选择挥发性较好的溶剂(IPA、去污水、白电油)
f. 品检
难擦拭脏污——用丙酮擦拭(不能碰到油墨区)
3、試產追蹤:
a、明確統計各站良率狀況,及時解決相關製程問題。 b、完善各站參數,確定各站PPH值。 c、制定各站作業票書。
常見問題點
4. 试产制程:
a. 清洗 (白片) b. 电镀
白点、脏污——水质(欧母值)、水&药水&滤芯更换
刮伤——加强人料检验(黄光)、减少清洗次数 透空——环境落尘、机台保养 电刮——人员手法、治具周转 色差——机台保养、空跑至靶材均匀溅射 透 空 机台参数(刮胶、网距等)、人员检验
设计开发控制程序

1目的本程序旨在建立本公司的新产品设计开发流程和要求,确保新产品的开发过程和结果符合客户以及相关法律法规的要求。
2适用范围本程序适用于本公司所有新产品的设计开发。
3定义(解释特殊简写或概念)3.1BOM - 物料清单3.2FAI –新零件首件检验3.3DFMEA - 设计失效模式分析3.4PFMEA - 生产制造失效模式分析3.5ECN - 工程技术更改通知单3.6T0 - 第一次试模件的试装3.7EB0 - 用T0零件进行工程样板组装3.8EB1 - 第一次试产3.9EB2 - 第二次试产3.10PP - 小批量试生产3.11MP - 大批量生产3.12HSF - 有害物质减免4职责(规范部门或特殊职位在程序中的职责)4.1销售部 - 负责新项目的市场调研,客户需求对接,产品外观评审,发行/更新《新产品立项评估表》,并且在新产品开发过程中与客户沟通所遇到的项目问题;负责新产品价格的更新和维护。
4.2研发部 - 负责《项目计划表》、《产品开发规格书》的制定和更新;负责产品的设计,《BOM》、2D/3D图纸的编制和更新;负责《DFMEA》文件的维护及更新;负责《新产品模具清单》编制和更新,新模具的制作及跟进;负责新零件打样跟进,零件FAI评审;负责安排试产,测试,认证等工作;负责主持和召开项目评审会议,编制和更新《设计开发评审记录》,通过问题点的跟踪及改善方案的实施,确保设计过程及结果符合客户及相关法规的要求。
4.3工程部 - 负责新产品工艺制程的制定及《产品工艺制程表》的编写和维护;负责《新产品生产设备及工装清单》的编写和维护,以及生产装备的购买和制作;负责《标准作业指导书》的编写和维护,以及员工的操作培训;负责《PFMEA》文件的维护及更新;负责生产产能和制成率的跟踪及验证。
4.4品质部 - 负责新产品品质过程控制的制定及《品质控制计划》的编写和维护;负责《检验指导书》的编写和维护,负责《新产品测试设备及工装清单》的编写和维护,以及测试装备的购买和制作;负责《FAI》文件的数据收集,零件/半成品/成品的检测以及检验报告编制,品质问题的跟踪及改善。
msc研发流程及生产工艺

msc研发流程及生产工艺全文共四篇示例,供读者参考第一篇示例:MSC研发流程及生产工艺MSC(Mass Spectrometry Chromatography)质谱色谱技术是一种先进的分析技术,广泛应用于化学、生物、药物等领域。
在MSC 技术的背后,有着复杂的研发流程和精密的生产工艺支持。
本文将介绍MSC研发流程及生产工艺,带领读者深入了解这一技术的发展与运用。
研发流程:MSC技术的研发流程通常包括需求调研、方案设计、实验验证和技术优化等环节。
研发团队需要对市场需求进行深入调研,了解用户对MSC技术的需求和期望,确定研发方向和目标。
在需求调研的基础上,团队将提出具体的方案设计,包括仪器结构、工作原理、分析方法等方面的设计方案。
设计完成后,研发团队将进行实验验证,通过实验数据和结果来验证设计方案的可行性和有效性。
在不断实验验证的基础上,研发团队将对技术进行优化,不断改进和完善技术性能,以满足用户需求并提升技术竞争力。
在MSC技术的研发流程中,仪器设计、分析方法和数据处理是三大核心环节。
仪器设计是整个流程的基础,关系到技术的实现和应用效果。
研发团队需要根据市场需求和技术特点,设计出适合的仪器结构和性能指标,确保仪器能够满足用户需求。
分析方法是技术实现的关键,是将样品转化为数据的桥梁。
研发团队需要确定合适的分析方法,包括样品处理、样品分析、数据处理等步骤,提高分析效率和准确性。
数据处理是技术应用的重要环节,是将实验数据转化为结论和应用价值的过程。
研发团队需要建立合适的数据处理技术,提高数据的可视化和分析能力,为用户提供准确可靠的数据支持。
生产工艺:MSC技术的生产工艺通常包括原材料采购、装配生产、检测调试和质量控制等环节。
生产部门需要对原材料进行采购,确保原材料的质量和供应稳定。
在原材料采购完成后,生产部门将按照设计图纸和生产工艺流程,对零部件进行装配生产。
在装配生产的过程中,生产工人需要严格按照操作规程进行操作,确保产品的装配质量和工艺合格。
开发新产品流程
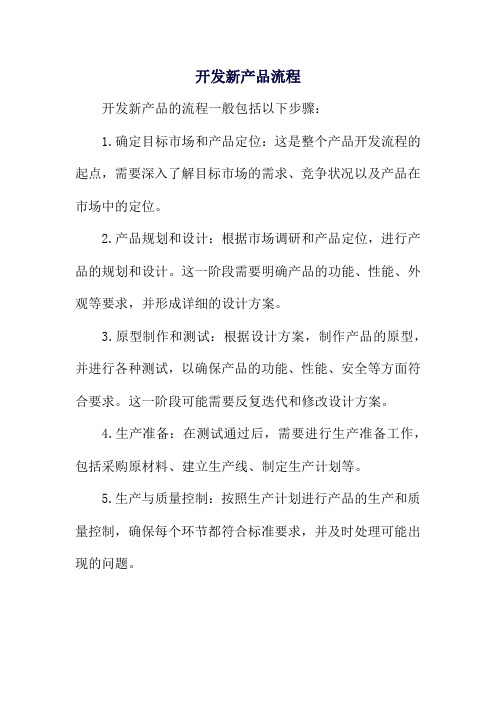
开发新产品流程
开发新产品的流程一般包括以下步骤:
1.确定目标市场和产品定位:这是整个产品开发流程的起点,需要深入了解目标市场的需求、竞争状况以及产品在市场中的定位。
2.产品规划和设计:根据市场调研和产品定位,进行产品的规划和设计。
这一阶段需要明确产品的功能、性能、外观等要求,并形成详细的设计方案。
3.原型制作和测试:根据设计方案,制作产品的原型,并进行各种测试,以确保产品的功能、性能、安全等方面符合要求。
这一阶段可能需要反复迭代和修改设计方案。
4.生产准备:在测试通过后,需要进行生产准备工作,包括采购原材料、建立生产线、制定生产计划等。
5.生产与质量控制:按照生产计划进行产品的生产和质量控制,确保每个环节都符合标准要求,并及时处理可能出现的问题。
6.产品上市和推广:产品上市前需要进行市场推广策划,包括确定目标受众、制定营销策略、设计宣传物料等。
同时,需要制定售后服务计划,保障消费者的权益。
7.持续改进和迭代:上市后需要对产品进行持续的改进和迭代,以满足市场的变化和用户的需求。
同时,也需要不断收集用户反馈和市场信息,为未来的产品开发提供参考。
以上是开发新产品的基本流程,具体实施时可根据实际情况进行调整和优化。
APQP产品质量培训教程

AOQP讲义
44
可制造性和装配设计
–制造和/或装配过程
–尺寸公差(要求到什么程度,分供方是否可 接受,价格是否可接受)
–性能要求(要求到什么程度,是否可接受)
–部件数(多或少)
–过程调整(最佳化)
–材料搬连频(最小化)街
产品质量策划小组的知识、经验、产品/过程
、政府法规和服务要求有可能需要考虑其它因
APQP产品质量培训教 程
课程目的
了解APQP在新产品开发中的重要作用 APQP的主要阶段 APQP的参加部门 APQP各阶段对应的体系要素 APQP的输出--控制计划的编制和实施
AOQP讲义
2
产品品质规划时间表
AOQP讲义
3
产品品质规划时间表
AOQP讲义
4
产品品质规划时间表
AOQP讲义
5
产品质量策划责任矩阵图
14
产品质量策划概述
培训 产品质量计划的成功依赖于有效的培训 方案,它传授所有满足顾客需要和期望 的要求及开发技能
AOQP讲义
15
产品质量策划概述
顾客和供方的参与 主要顾客可与其供方共同进行质量策划 。但供方有义务建立橫向职能小组来管 理产品质量策划过程。供方同样可要求 其分承包方
AOQP讲义
16
AOQP讲义
18
产品质量策划概述
产品质量的进度计划
产品质量策划小组在完成组织活动后的第一项工作是 制定进度计划。在选择需作计划并绘制成图的进度要 素时,应考虑产品的类型、复杂性和顾客的期望。 所有的小组成员都应在每一事项、措施和进度上取得 意见一致。 一个组织良好的进度图应列出任务、分配和或其它事 项 每一事项应具备“起始”和“完成”日期,并记录进 展的实际点。
设计开发控制程序
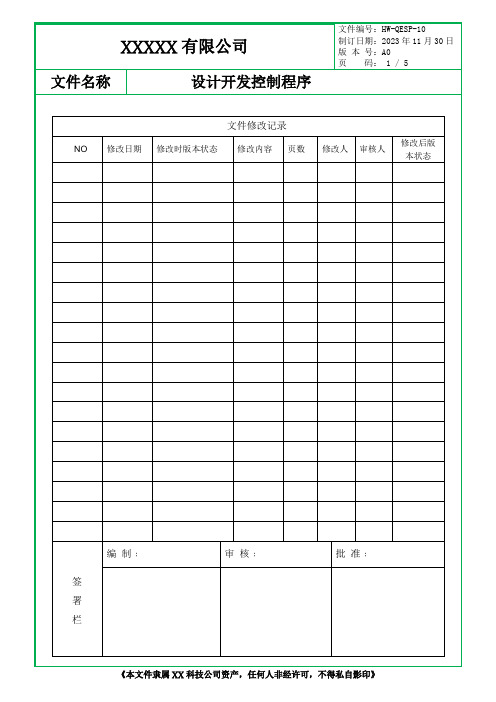
6.5.1设计确认通常针对最终产品,在交付之前完成。试产合格的产品,由业务部负责联系送交顾客试用,提交《设计确认报告》,报告应反映出:顾客对试样符合标准或合同要求的满意程度,及对试样适用性的评价。或由工程部组织召开新产品鉴定会(包括拟参加人员,邀请有关专家,准备任务书、输出文件、评审验证记录、试产报告等相关资料),提交会议进行综合确认。
6.6.2.1 由设计变更申提案人通知工程部,若需要,附上相关资料送工程部审查变更的可行性,若审查不可行,则该提案取消。
6.6.2.2 设计变更提案经专案负责人初步研判其可行性,须对变更内容执行审查,以决定变更内容是否会对下列事项造成影响:
A 变更结果后的产品,其零组件之间的相互影响。
B 公司现有产品和过去已交货之产品的操作
文件修改记录
NO
修改日期
修改时版本状态
修改内容
页数
修改人
审核人
修改后版
本状态
签
署
栏
编制﹕
审核﹕
批准﹕
一、目的:
对设计全过程进行控制,确保产品设计能满足顾客和有关标准、法律、法规的要求。
二、范围:
适用于本公司各类产品设计的全过程,包括产品的技术改进。
三、定义无
四、权责:
4.1业务部负责根据市场调研、分析,依客户提供的样板或技术资料,向工程部提交《项目立项书》。总经理或工程部根据公司的产品规划和行业发展方向,也可以提出《项目立项书》。
6.2设计输出:
6.2.1各设计人员根据《设计规划书》及《设计开发进度日程表》的要求进行设计活动:包括指导采购、生产、检验、包装等活动的图样和文件,如各种形式的测试、产品爆炸图、单体配件图、BOM、零件承认书、成品图、产品检验标准、作业指导书。
SMT十步骤
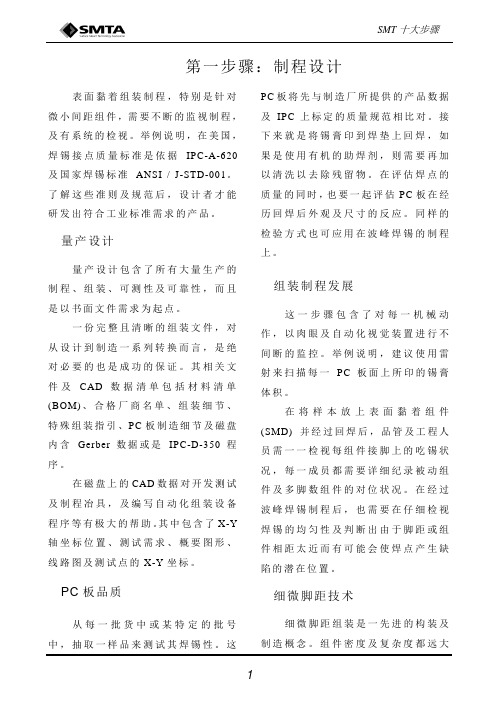
第一步骤:制程设计表面黏着组装制程,特别是针对微小间距组件,需要不断的监视制程,及有系统的检视。
举例说明,在美国,焊锡接点质量标准是依据IP C-A-620及国家焊锡标准A NS I /J-ST D-001。
了解这些准则及规范后,设计者才能研发出符合工业标准需求的产品。
量产设计量产设计包含了所有大量生产的制程、组装、可测性及可靠性,而且是以书面文件需求为起点。
一份完整且清晰的组装文件,对从设计到制造一系列转换而言,是绝对必要的也是成功的保证。
其相关文件及CA D数据清单包括材料清单(BOM)、合格厂商名单、组装细节、特殊组装指引、P C板制造细节及磁盘内含Ge rber数据或是IP C-D-350程序。
在磁盘上的CA D数据对开发测试及制程冶具,及编写自动化组装设备程序等有极大的帮助。
其中包含了X-Y 轴坐标位置、测试需求、概要图形、线路图及测试点的X-Y坐标。
PC板品质从每一批货中或某特定的批号中,抽取一样品来测试其焊锡性。
这PC板将先与制造厂所提供的产品数据及I P C上标定的质量规范相比对。
接下来就是将锡膏印到焊垫上回焊,如果是使用有机的助焊剂,则需要再加以清洗以去除残留物。
在评估焊点的质量的同时,也要一起评估P C板在经历回焊后外观及尺寸的反应。
同样的检验方式也可应用在波峰焊锡的制程上。
组装制程发展这一步骤包含了对每一机械动作,以肉眼及自动化视觉装置进行不间断的监控。
举例说明,建议使用雷射来扫描每一P C板面上所印的锡膏体积。
在将样本放上表面黏着组件(SM D)并经过回焊后,品管及工程人员需一一检视每组件接脚上的吃锡状况,每一成员都需要详细纪录被动组件及多脚数组件的对位状况。
在经过波峰焊锡制程后,也需要在仔细检视焊锡的均匀性及判断出由于脚距或组件相距太近而有可能会使焊点产生缺陷的潜在位置。
细微脚距技术细微脚距组装是一先进的构装及制造概念。
组件密度及复杂度都远大于目前市场主流产品,若是要进入量产阶段,必须再修正一些参数后方可投入生产线。
APQP工作流程及说明

APQP工作流程及说明APQP(Advanced Product Quality Planning,高级产品质量规划)是一种流程化的方法,用于规划并确保产品在设计、工程、制造和服务过程中达到高质量水平。
它在汽车行业得到广泛应用,也适用于其他制造业。
1.规划和定义阶段:在该阶段,制定产品的质量目标和开发计划。
团队成员评估相关需求、法规要求以及潜在风险,并根据这些因素制定APQP计划。
此外,还制定产品设计和制程开发的时间表,并确定APQP团队成员。
2.产品设计和开发阶段:该阶段的关键目标是开发出满足客户需求和规定要求的产品设计。
团队成员使用设计评审、特性矩阵、质量功能展开(QFD)和设计失效模式与影响分析(DFMEA)等工具来完成该目标。
同时,对供应商进行评估和选择,并与供应商建立质量计划。
3.制程设计和开发阶段:在这个阶段,团队成员开发和优化制造工艺,确保产品的质量并满足设计要求。
流程评估、流程失效模式与影响分析(PFMEA)和可行性研究等工具被广泛应用于该阶段。
此外,还进行生产控制计划的制定,并对测量和试验设备进行校准和验证。
4.产品和过程验证阶段:在这个阶段,团队成员验证产品和制程是否达到设计要求和客户期望。
通过样品测试、过程验证和生产试运行,确保产品和制程的稳定性和一致性。
在此阶段还进行了供应商相关的评估,并控制实验和生产的相关文档。
5.生产评估阶段:在生产开始之前的最后一个阶段,团队成员将进行产品质量的最终评估。
通过审查生产和测量数据、统计过程控制技术和上线前检查等,确保产品质量的稳定性和一致性。
任何未解决的问题都将回到之前的阶段进行修正。
值得注意的是,APQP不是一次性的过程,而是一个循环的过程。
如果在各个阶段发现了任何问题或改进的机会,团队将重新回到相应的阶段进行修正。
此外,团队成员应紧密合作,及时沟通并共享信息,以确保项目按时、高质量地完成。
APQP的目标是通过规划和预防活动来确保产品的质量,并在产品开发早期发现和解决潜在问题,以减少后期的成本和风险。
APQP管理程序
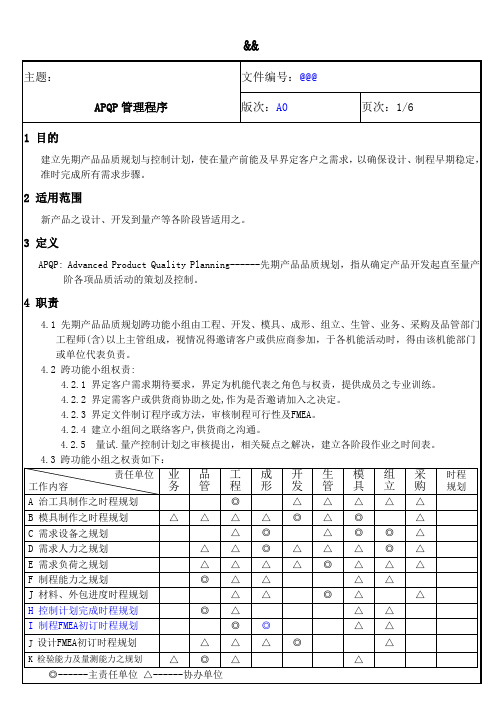
6.3.3管制特性选定:
A工程单位依PFMEA结果与客户要求及<<管制特性选定作业办法>>进行管制特性选定。
6.3.4量试控制计划:
A品管单位依PFMEA结果与管制特性选定结果及「控制计划管理办法」制作量试控制计划;
6.3.5作业指导书
6.2.2客户承认(样品)
A业务单位于收到客户签回之承认书时,须将签回之承认书转予开发单位;如客户未签回承认书仅通知认可并下订单时,亦需通知开发单位。开发单位于接获转回之客户签认承认书或业务通知已获承认,即可进行后续作业,若客户对样品有异议,则开发单位须回复至6.2.1 B项以后之作业。
B开发单位于客户样品承认后,进行工程文件之建立,含BOM、线路图、零件位置图、组立图、包装规范、GERBER FILE、烧录程序、测试软体等数据,并于量试文件制作前转文管中心管制及发行。
&&
主题:
文件编号:@@@
APQP管理程序
版次:A0
页次:1/6
1目的
建立先期产品品质规划与控制计划,使在量产前能及早界定客户之需求,以确保设计、制程早期稳定,准时完成所有需求步骤。
2适用范围
新产品之设计、开发到量产等各阶段皆适用之。
3定义
APQP: Advanced Product Quality Planning------先期产品品质规划,指从确定产品开发起直至量产阶各项品质活动的策划及控制。
6.4.7客户核准/承认(量试):
A.依《PPAP管理程序》进行生产性零组件客户核准作业。
B.接获客户签回之提交保证书或客户正式订单视同客户核准、承认。
新产品开发控制程序文件
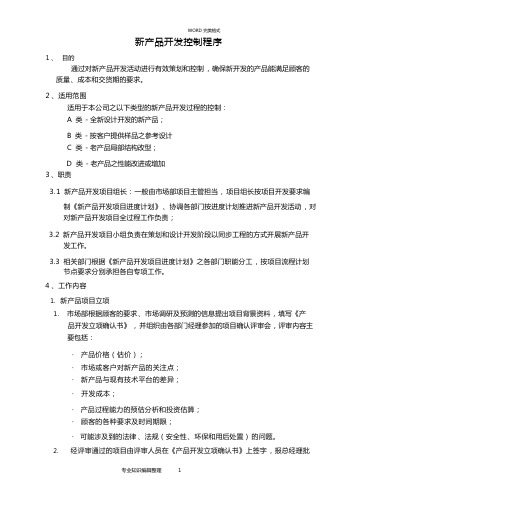
2.
在新产品试生产控制计划 、工艺文件等通过评审后, 工程部根据试生产控
制计划编制初始过程能力研究计划和 MSA 分析计划。
6. 制程设计确认阶段 -试产
1. 工程部负责下达新产品试生产作业计划 ,各部门接受计划后作试产作业准备;
1.
采购部负责准备试产所需用的物料, 品管部 IQC 对外购外协件、材料执
行 检验。
2.
制造部技术课和品管部负 IPQC 负责准备试产品的检验文件 , 需要时由工
程 部对员工进行新产品的新工艺方法培训。
3.
生产部生产车间负责新产品试产的现场准备;
4.
工程部:
· 负责对新产品试产所需的场地进行布置规划 , 必要时采用“车间平面布 置图检查表 ”进行确认;
· 确认试生产所需新设备、工装和试验设备的到位情况 ,适当时采用“新 设备 、工装和试验设备检查表 ”确认;
3.
品管部根据 MSA 计划适用试产品实施 MSA 分析 ,工程部根据初始能力研究
计划对初始过程能力进行计算;
4.
品管部负责组织对新产品之包装进行评价 。顾客有要求时 ,应取得客户的
确认。
4.7.3 试产分析检讨
1.
开发部和工程部在收集试产品实验报告和初始能力分析报告后分别进行产
品设计和制程开发小结 , 并联合初步建立《新产品试产问题改善计划》 。
· 客户产品合同 、技术协议书 、顾客提供的产品外形图或功能图 、产品技
术标准及其它文件;
· 在顾客提供产品样品的情况下 ,样品及其测试数据也作为设计输入的一 部分;
· 公司现有技术平台 · 合同评审结果;
· 适用的国家法令及法规。
3.
开发部项目主管工程师在设计输入评审结果后编制《设计输入评审报告》,
- 1、下载文档前请自行甄别文档内容的完整性,平台不提供额外的编辑、内容补充、找答案等附加服务。
- 2、"仅部分预览"的文档,不可在线预览部分如存在完整性等问题,可反馈申请退款(可完整预览的文档不适用该条件!)。
- 3、如文档侵犯您的权益,请联系客服反馈,我们会尽快为您处理(人工客服工作时间:9:00-18:30)。
GB6017.1-20起重机械安全规程-第1部分
1目的
对制造过程的设计和开发过程进行控制,保证产品和制造过程符合客户的要求。
2适用范围
本程序适用于公司所有产品的制程设计和开发过程控制。
3名词定义
无
4 相关权责
4.1制造技术课负责制程设计和开发的管理。
4.2生产企划课负责收集和记录客户要求。
4.3制造课负责协助制造技术课完成产品的样品制作和试产。
4.4品质管理课负责对产品质量进行检验和试验。
4.5总经理负责审批《新产品立项书》,并对设计各个阶段的评审记录进行审批。
5 作业说明
5.1设计/开发策划
5.1.1新产品导入时,生产企划课根据客户对产品和制程的要求,编制《新
产品立项申请表》交制造技术课。
5.1.2制造技术课根据《先期质量策划管理程序》,组织CFT相关人员,论
证新产品的可行性。
制造技术课应编制初始的生产流程和特殊特性文件提交
给CFT讨论。
5.1.3制造技术课根据论证后的结果及相关事项,编制《新产品立项书》,
交总经理审批。
5.1.4《新产品立项书》应列出主要的设计开发输入,见《先期质量策划
管理程序》的规定。
5.2设计/开发过程
5.2.1制造技术课根据《新产品立项书》组织相关单位共同划分开发阶段与
目标,填写《产品过程设计项目责任矩阵兼进度表》。
其主要包括:
A)开发流程与阶段划分;
B)每一开发阶段的时间与目标;
C)各阶段的目标评审与验证;
D)相关人员的职责与权限。
5.2.2当设计开发完成每一个阶段性目标后,由制造技术课人员列写阶段性
开发输出技术/文件资料(见《先期质量策划管理程序》)。
5.2.3制造技术课主管应依《先期质量策划管理程序》组成CFT相关人员对
所有设计
开发输出文件进行评审。
5.3设计/开发评审
5.3.1当设计开发完成每一阶段性目标后,制造技术课主管均应组织生产
课、品质管理课等相关人员对每一阶段的输出技术、文件资料进行评审与验
证,记录阶段性评审结论。
5.3.2设计审查应指出预测问题点及弱点,同时指出改正措施,以确保最
终产品和制造符合客户要求。
5.3.3设计评审时应考虑的要点有:
A)有关客户需求的项目;
B)有关产品性能需求的项目;
C)有关生产过程需求的项目。
5.3.4评审记录结果必须经总经理审批确认,并送所有相关人员保持以指
导后续开发工作。
5.4设计/开发验证及确认
5.4.1制造技术课按客户要求的信息通知制造课进行样品制作。
5.4.2制造技术课应依《先期质量策划管理程序》进行产品试产并进行确认。
5.5设计/开发文件控制
制造技术课应把相关的工艺文件交给文控中心受控。
文控中心应依《文件及资料管理程序》保存并分发给所有相关人员。
5.6设计/开发的更改
制造技术课需对制程进行设计更改时,应按《工程更改程序》规定执行。
6 作业流程
无
7相关文件
7.1《先期质量策划管理程序》QP-07-02
7.2《文件及资料管理程序》QP-04-01
7.3《工程更改程序》QP-07-22
8附件
8.1《新产品立项书》QF-PP-010
8.2《产品过程设计项目责任矩阵兼进度表》QF-PT-092
8.3《新产品立项申请表》QF-PP-009
计划检查表。