炼铁系统资料
高炉炼铁(附彩图)
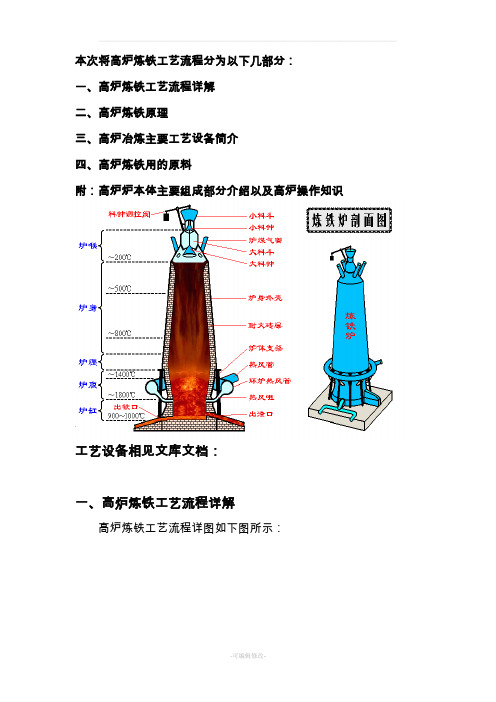
本次将高炉炼铁工艺流程分为以下几部分:一、高炉炼铁工艺流程详解二、高炉炼铁原理三、高炉冶炼主要工艺设备简介四、高炉炼铁用的原料附:高炉炉本体主要组成部分介绍以及高炉操作知识工艺设备相见文库文档:一、高炉炼铁工艺流程详解高炉炼铁工艺流程详图如下图所示:二、高炉炼铁原理炼铁过程实质上是将铁从其自然形态——矿石等含铁化合物中还原出来的过程。
炼铁方法主要有高炉法、直接还原法、熔融还原法等,其原理是矿石在特定的气氛中(还原物质CO、H2、C;适宜温度等)通过物化反应获取还原后的生铁。
生铁除了少部分用于铸造外,绝大部分是作为炼钢原料。
高炉炼铁是现代炼铁的主要方法,钢铁生产中的重要环节。
这种方法是由古代竖炉炼铁发展、改进而成的。
尽管世界各国研究发展了很多新的炼铁法,但由于高炉炼铁技术经济指标良好,工艺简单,生产量大,劳动生产率高,能耗低,这种方法生产的铁仍占世界铁总产量的95%以上。
炼铁工艺是是将含铁原料(烧结矿、球团矿或铁矿)、燃料(焦炭、煤粉等)及其它辅助原料(石灰石、白云石、锰矿等)按一定比例自高炉炉顶装入高炉,并由热风炉在高炉下部沿炉周的风口向高炉内鼓入热风助焦炭燃烧(有的高炉也喷吹煤粉、重油、天然气等辅助燃料),在高温下焦炭中的碳同鼓入空气中的氧燃烧生成的一氧化碳和氢气。
原料、燃料随着炉内熔炼等过程的进行而下降,在炉料下降和上升的煤气相遇,先后发生传热、还原、熔化、脱炭作用而生成生铁,铁矿石原料中的杂质与加入炉内的熔剂相结合而成渣,炉底铁水间断地放出装入铁水罐,送往炼钢厂。
同时产生高炉煤气,炉渣两种副产品,高炉渣铁主要矿石中不还原的杂质和石灰石等熔剂结合生成,自渣口排出后,经水淬处理后全部作为水泥生产原料;产生的煤气从炉顶导出,经除尘后,作为热风炉、加热炉、焦炉、锅炉等的燃料。
炼铁工艺流程和主要排污节点见上图。
三、高炉冶炼主要工艺设备简介高护炼铁设备组成有:①高炉本体;②供料设备;③送风设备;④喷吹设备;⑤煤气处理设备;⑥渣铁处理设备。
高炉炼铁基本原理与工艺
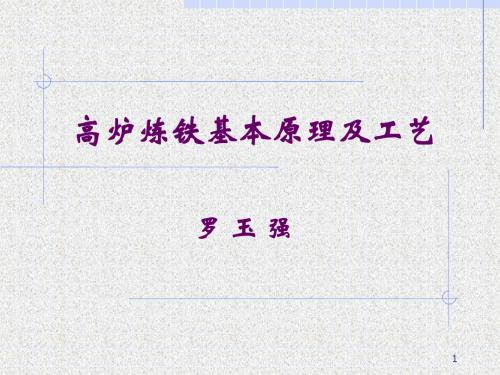
15
2.铁的间接还原与直接还原
(1)间接还原:用CO、H2为还原剂还原铁的氧化物,产物CO2、 H2O的还原反应。 特点:放热反应 反应可逆 (2)直接还原:用C作为还原剂,最终气体产物为CO的还原反应。 特点:强吸热反应 反应不可逆 (3)直接、间接还原区域划分:取决于焦碳的反应性 低温区 <800℃基本为间接还原 中温区 800~1100℃共存 高温区 > 1100℃全部为直接还原 (4)用直接还原度rd、间接还原度ri来衡量高炉C素利用好坏,评价 焦比。
9
2. (助)熔剂
(1)作用: 形成低熔点易流动的炉渣、脱S(碱性熔剂) (2)种类:
使用条件及作用
碱性
酸性
铁矿中脉石为酸性氧化物,包括:石灰石、白云石、石灰
铁矿中脉石为碱性氧化物,主要为:SiO2(只在炉况失常 时使用——(Al2O3)≥18%或排碱时) 高Al熔剂,主要为:含Al2O3高的铁矿(只在降低炉渣流动 性时使用)
24
五、高炉强化冶炼手段与方法
1.大风量 风量增加,炉内传热效果下降,ri降低,K 增加。风量应与还原性相适应 2.高风温 风温增加,传热推动力增加,但利用风温 的同时K势必降低,透气性将下降 3.富氧 富氧将使炉缸温度增加,但煤气总量下降, 不利于全厂能量平衡;富氧达到的效果与提高 风温相比,成本提高10倍。
10
中性
3 焦碳
①主要作用:
作为高炉热量主要来源的60~80%,其它热风提供 提供还原剂C、CO 料柱骨架,保证透气性、透液性
②质量要求:
含炭量:C↑ 灰份:10%左右,灰分低可使渣量↓ 含S量:<0.6% 生铁中[S]80%±来源于焦碳 强 度:M40 (kangsuiqd)、M10 (lmqd) 粒度组成:均匀 60mm 左右的 >80% ,大于 80mm 的 <10% ,大于 80mm的<10% 成分稳定(特指水分): 一般采用干熄焦 焦碳反应性: C+CO2=2CO开始反应的高低快慢→影响间接还原区的 范围从而影响焦比
钢铁生产工艺流程资料

钢铁生产工艺流程资料一、引言钢铁是现代工业中最重要的材料之一,广泛应用于建筑、汽车、航空航天、机械制造等领域。
钢铁的生产过程是一个复杂而精细的工艺流程,需要经过多个步骤才能得到最终的产品。
本文将详细介绍钢铁生产的工艺流程,包括原料准备、炼铁、炼钢和精炼等环节。
二、原料准备钢铁的主要原料是铁矿石、焦炭和石灰石。
首先,铁矿石经过破碎、磨矿和磁选等工艺处理,得到适合炼铁的铁矿石粉末。
焦炭是一种高碳含量的煤炭,经过煤气化和炼焦等工艺处理,得到适合高温炼铁的焦炭块。
石灰石用于调节炼铁过程中的酸碱度,经过破碎和煅烧等工艺处理,得到适合使用的石灰石粉末。
三、炼铁1. 高炉炼铁高炉炼铁是目前主要的炼铁方法之一。
首先,将铁矿石、焦炭和石灰石按一定比例加入高炉中。
然后,通过高炉顶部喷入预热的空气,使焦炭燃烧产生高温和一氧化碳气体。
一氧化碳与铁矿石中的氧化铁反应生成金属铁,并与石灰石反应生成炉渣。
最后,通过高炉底部的出渣口排出炉渣,通过高炉顶部的出铁口收集金属铁。
2. 湿法炼铁湿法炼铁是一种较为环保的炼铁方法。
首先,将铁矿石粉末与还原剂(如煤粉)混合,并加入适量的水。
然后,将混合物放入湿法炼铁炉中进行还原反应。
在高温下,还原剂和水蒸气与铁矿石中的氧化铁反应生成金属铁。
最后,通过湿法炼铁炉底部的出渣口排出炉渣,通过炉顶部的出铁口收集金属铁。
四、炼钢炼铁得到的生铁中含有大量的杂质,需要经过炼钢过程进行精炼。
炼钢的主要方法包括转炉法、电炉法和氧气底吹法等。
1. 转炉法转炉法是一种常用的炼钢方法。
首先,将生铁和适量的废钢放入转炉中。
然后,通过转炉底部喷吹氧气,使废钢和生铁中的杂质被氧化。
氧化反应产生的高温和一氧化碳气体可以提供炉内的热量。
最后,通过转炉底部的出渣口排出炉渣,通过炉顶部的出钢口收集炼钢产品。
2. 电炉法电炉法是一种利用电能进行炼钢的方法。
首先,将生铁和废钢放入电炉中。
然后,通过电极向电炉中通入电流,使炉内的材料加热。
炼钢厂设计复习资料
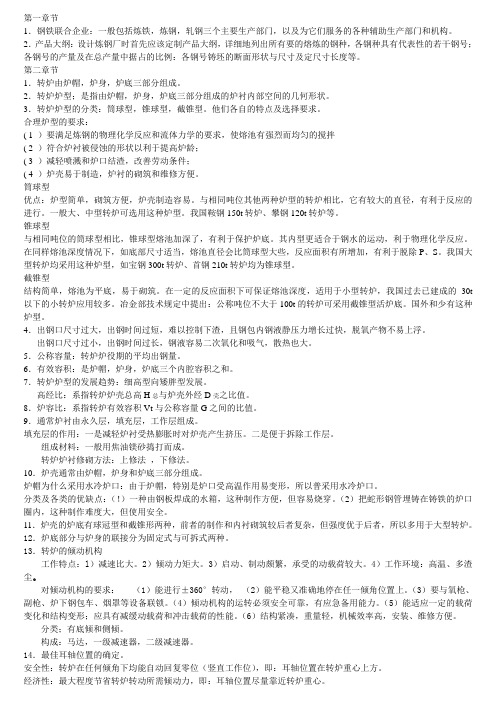
第一章节1.钢铁联合企业:一般包括炼铁,炼钢,轧钢三个主要生产部门,以及为它们服务的各种辅助生产部门和机构。
2.产品大纲:设计炼钢厂时首先应该定制产品大纲,详细地列出所有要的熔炼的钢种,各钢种具有代表性的若干钢号;各钢号的产量及在总产量中据占的比例:各钢号铸坯的断面形状与尺寸及定尺寸长度等。
第二章节1.转炉由炉帽,炉身,炉底三部分组成。
2.转炉炉型;是指由炉帽,炉身,炉底三部分组成的炉衬内部空间的几何形状。
3.转炉炉型的分类:筒球型,锥球型,截锥型。
他们各自的特点及选择要求。
合理炉型的要求:( 1 )要满足炼钢的物理化学反应和流体力学的要求,使熔池有强烈而均匀的搅拌( 2 )符合炉衬被侵蚀的形状以利于提高炉龄;( 3 )减轻喷溅和炉口结渣,改善劳动条件;( 4 )炉壳易于制造,炉衬的砌筑和维修方便。
筒球型优点:炉型简单,砌筑方便,炉壳制造容易。
与相同吨位其他两种炉型的转炉相比,它有较大的直径,有利于反应的进行。
一般大、中型转炉可选用这种炉型。
我国鞍钢150t转炉、攀钢120t转炉等。
锥球型与相同吨位的筒球型相比,锥球型熔池加深了,有利于保护炉底。
其内型更适合于钢水的运动,利于物理化学反应。
在同样熔池深度情况下,如底部尺寸适当,熔池直径会比筒球型大些,反应面积有所增加,有利于脱除P、S。
我国大型转炉均采用这种炉型,如宝钢300t转炉、首钢210t转炉均为锥球型。
截锥型结构简单,熔池为平底,易于砌筑。
在一定的反应面积下可保证熔池深度,适用于小型转炉,我国过去已建成的30t 以下的小转炉应用较多。
冶金部技术规定中提出:公称吨位不大于100t的转炉可采用截锥型活炉底。
国外和少有这种炉型。
4.出钢口尺寸过大,出钢时间过短,难以控制下渣,且钢包内钢液静压力增长过快,脱氧产物不易上浮。
出钢口尺寸过小,出钢时间过长,钢液容易二次氧化和吸气,散热也大。
5.公称容量:转炉炉役期的平均出钢量。
6.有效容积:是炉帽,炉身,炉底三个内腔容积之和。
钢铁冶炼学习资料

钢铁生产工艺一、钢铁生产流程钢铁生产流程大致分为:选矿、烧结、炼焦、高炉(炼铁)、电炉或转炉(炼钢)、连铸、轧制等过程;辅助系统有:制氧/制氮、循环水系统、烟气除尘及煤气回收等。
钢铁生产工艺1.选矿:根据矿石中不同矿物的物理、化学性质,把矿石破碎磨细以后,采用重选法、浮选法、磁选法、电选法等,将有用矿物与脉石矿物分开,并使各种共生(伴生)的有用矿物尽可能相互分离,除去或降低有害杂质,以获得冶炼或其他工业所需原料的过程。
选矿能够使矿物中的有用组分富集,降低冶炼或其它加工过程中燃料、运输的消耗,使低品位的矿石能得到经济利用。
选矿试验所得数据,是矿床评价及建厂设计的主要依据。
过程:破碎、磨碎、筛分等级、选矿。
铁矿石:是主要的炼铁原料,有磁铁矿“Fe3O4”、赤铁矿“Fe2O3”、褐铁矿“2Fe2O3.3H2O”、菱铁矿“FeCO3”。
铁矿石中除铁的化合物外,还含有硅、锰、磷、硫等的化合物。
磁铁矿选矿:主要有多级磁选或干湿磁选联合。
赤铁矿选矿:主要有重选、浮选和强磁选或是多种选矿并用,也有磁化焙烧后弱磁选。
褐铁矿选矿:主要有水洗:如广东韶关大宝山褐铁矿;重选:主要是摇床、跳汰;磁选:电磁或永磁强磁场选矿。
菱铁矿选矿:主要有弱磁—强磁—浮选组合工艺。
2.烧结和炼焦烧结:烧结是钢铁生产工艺中的一个重要环节,它是将铁矿粉、粉(无烟煤)和石灰按一定配比混匀,经烧结而成的有足够强度和粒度的烧结矿可作为炼铁的熟料。
为了保证供给高炉的铁矿石中铁含量均匀,并且保证高炉的透气性,需要把选矿工艺产出的铁精矿制成10-25mm的块状原料。
铁矿粉造块目前主要有两种方法:烧结法和球团法。
球团矿是细磨铁精矿或其它含铁粉料造块的又一方法。
它是将精矿粉、熔剂(有时还有粘结剂和燃料)的混合物,在造球机中滚成直径8~15mm(用于炼钢则要大些)的生球,然后干燥、焙烧,固结成型,成为具有良好冶金性质的优良含铁原料,供给钢铁冶炼需要。
两种方法所获得的块矿分别为烧结矿和球团矿。
炼铁原料复习资料
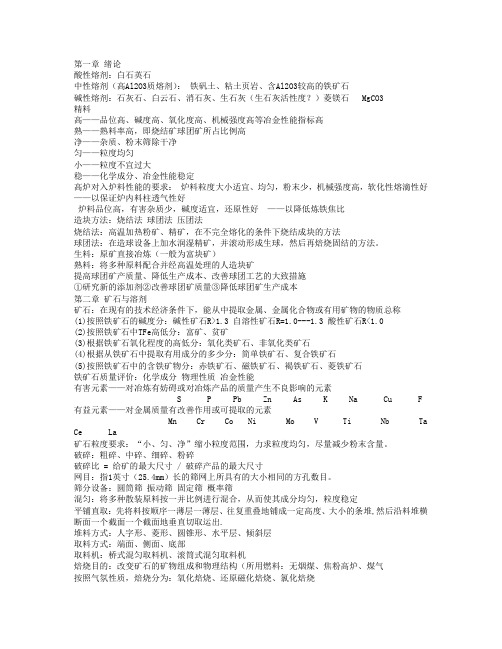
第一章绪论酸性熔剂:白石英石中性熔剂(高Al2O3质熔剂):铁矾土、粘土页岩、含Al2O3较高的铁矿石碱性熔剂:石灰石、白云石、消石灰、生石灰(生石灰活性度?)菱镁石 MgCO3精料高——品位高、碱度高、氧化度高、机械强度高等冶金性能指标高熟——熟料率高,即烧结矿球团矿所占比例高净——杂质、粉末筛除干净匀——粒度均匀小——粒度不宜过大稳——化学成分、冶金性能稳定高炉对入炉料性能的要求:炉料粒度大小适宜、均匀,粉末少,机械强度高,软化性熔滴性好——以保证炉内料柱透气性好炉料品位高,有害杂质少,碱度适宜,还原性好——以降低炼铁焦比造块方法:烧结法球团法压团法烧结法:高温加热粉矿、精矿,在不完全熔化的条件下烧结成块的方法球团法:在造球设备上加水润湿精矿,并滚动形成生球,然后再焙烧固结的方法。
生料:原矿直接冶炼(一般为富块矿)熟料:将多种原料配合并经高温处理的人造块矿提高球团矿产质量、降低生产成本、改善球团工艺的大致措施①研究新的添加剂②改善球团矿质量③降低球团矿生产成本第二章矿石与溶剂矿石:在现有的技术经济条件下,能从中提取金属、金属化合物或有用矿物的物质总称(1)按照铁矿石的碱度分:碱性矿石R>1.3 自溶性矿石R=1.0---1.3 酸性矿石R<1.0(2)按照铁矿石中TFe高低分:富矿、贫矿(3)根据铁矿石氧化程度的高低分:氧化类矿石、非氧化类矿石(4)根据从铁矿石中提取有用成分的多少分:简单铁矿石、复合铁矿石(5)按照铁矿石中的含铁矿物分:赤铁矿石、磁铁矿石、褐铁矿石、菱铁矿石铁矿石质量评价:化学成分物理性质冶金性能有害元素——对冶炼有妨碍或对冶炼产品的质量产生不良影响的元素S P Pb Zn As K Na Cu F有益元素——对金属质量有改善作用或可提取的元素Mn Cr Co Ni Mo V Ti Nb Ta Ce La矿石粒度要求:“小、匀、净”缩小粒度范围,力求粒度均匀,尽量减少粉末含量。
炼铁学习资料
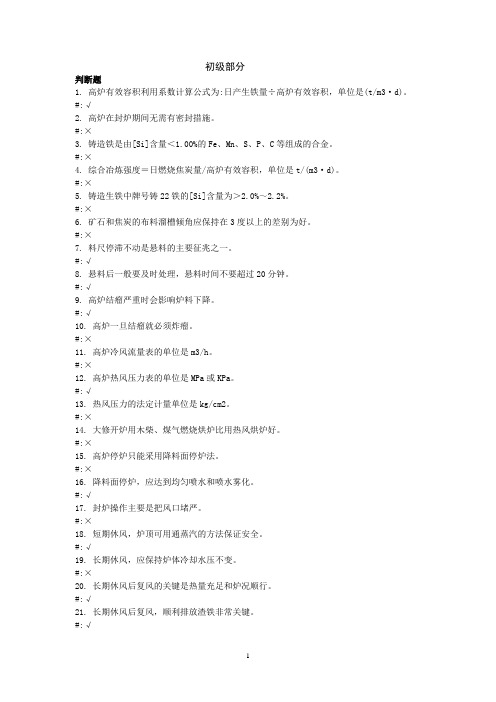
初级部分判断题1. 高炉有效容积利用系数计算公式为:日产生铁量÷高炉有效容积,单位是(t/m3·d)。
#:√2. 高炉在封炉期间无需有密封措施。
#:×3. 铸造铁是由[Si]含量<1.00%的Fe、Mn、S、P、C等组成的合金。
#:×4. 综合冶炼强度=日燃烧焦炭量/高炉有效容积,单位是t/(m3·d)。
#:×5. 铸造生铁中牌号铸22铁的[Si]含量为>2.0%~2.2%。
#:×6. 矿石和焦炭的布料溜槽倾角应保持在3度以上的差别为好。
#:×7. 料尺停滞不动是悬料的主要征兆之一。
#:√8. 悬料后一般要及时处理,悬料时间不要超过20分钟。
#:√9. 高炉结瘤严重时会影响炉料下降。
#:√10. 高炉一旦结瘤就必须炸瘤。
#:×11. 高炉冷风流量表的单位是m3/h。
#:×12. 高炉热风压力表的单位是MPa或KPa。
#:√13. 热风压力的法定计量单位是kg/cm2。
#:×14. 大修开炉用木柴、煤气燃烧烘炉比用热风烘炉好。
#:×15. 高炉停炉只能采用降料面停炉法。
#:×16. 降料面停炉,应达到均匀喷水和喷水雾化。
#:√17. 封炉操作主要是把风口堵严。
#:×18. 短期休风,炉顶可用通蒸汽的方法保证安全。
#:√19. 长期休风,应保持炉体冷却水压不变。
#:×20. 长期休风后复风的关键是热量充足和炉况顺行。
#:√21. 长期休风后复风,顺利排放渣铁非常关键。
#:√22. 长期休风后如果热量损失少,可以全开风口复风。
#:×23. 封炉时间越长,封炉焦比越高。
#:√24. 炉前泥炮的打泥压力与炉缸内压力相等即可。
#:×25. 炉前泥炮堵口操作包括转炮、压炮、打泥三部分#:√26. 一般大型高炉应配备5座热风炉。
#:×27. 生铁合格率是反映生铁质量的指标。
高炉炼铁工艺流程(简介)资料

小钟
溜槽 探尺
导料板
大钟
探尺
高炉概况和工艺流程
高炉喷煤流程
热风炉废 气烟囱
热风炉废 气引风机
BFG Air
干燥炉
COG
原煤仓
给煤机
磨煤
旋风分离器
再循环废气 布袋除尘器
振动筛
流化气
煤粉仓
Distributer 仓顶除尘器
排气系统
主排风机
×18支 管
分配器 ×2
输送压缩 空气
高
喷吹罐
炉
1#
2#
3#
Z-301BC
煤气净化流程简图
洗涤塔 文氏管
重力 除尘
布袋 除尘器
高压 阀组
消音器
公司 管网
TRT
送风系统
鼓风机
热风炉
热风总管 热风围管 高炉
鹅颈管 风口
直吹管
热风炉设备工艺图
B FN
B
GC2 F
N
AO IG
AG I
K
H R
R
R
CC C RG P
BB B PG R
C CC R GP
BB B PG R
BP BG BR
H
CB
AB
BB
H
CB
AB
BB
H
B
M
B
M
B
M
B
M
Sta ck W .G
4HS
3HS
2HS
1HS
H
H
H
H
SII WS W
E
SI
C
SII WS
W
E
SI
C
SII WS
高炉炼铁原理

高炉炼铁原理与工艺知识问答1、高炉原料中的游离水对高炉冶炼有何影响?答:游离水存在于矿石和焦炭的表面和空隙里。
炉料进入高炉之后,由于上升煤气流的加热作用,游离水首先开始蒸发。
游离水蒸发的理沦温度是100℃,但是要料块内部也达到100℃,从而使炉料中的游离水全部蒸发掉,就需要更高的温度。
根据料块大小的不同,需要到100℃,或者对大块来说,甚至要达到200℃游离水才能全部蒸发掉。
一般用天然矿或冷烧结矿的高炉,其炉顶温度为100~300℃,因此,炉料中的游离水进入高炉之后,不久就蒸发完毕,不增加炉内燃料消耗。
相反,游离水的蒸发降低了炉顶温度,有利于炉顶设备的维护,延长其寿命。
另一方面,炉顶温度降低使煤气体积缩小,降低煤气流速,从而减少炉尘吹出量。
2、高炉原料中的结晶水对高炉冶炼有何影响?答:炉料中的结晶水主要存在于水化物矿石(如褐铁矿和高岭土)中间。
高岭土是黏土的主要成分,有些矿石中含有高岭土。
试验表明,褐铁矿中的结晶水从200℃开始分解,到400~500℃才能分解完毕。
高岭土中的结晶水从400℃开始分解,但分解速度很慢,到500~600℃迅速分解,全部除去结晶水要达到800~1000℃。
可见,高温区分解结晶水,对高炉冶炼是不利的,它不仅消耗焦炭,而且吸收高温区热量,增加热消耗,降低炉缸温度。
3、高炉内碳酸盐分解的规律如何?对高炉冶炼有何影响?答:炉料中的碳酸盐主要来自熔剂(石灰石或白云石),有时矿石也带入一少部分。
炉中的碳酸盐在下降过程中逐渐被加热发生吸热分解反应。
它们的开始分解温度和激烈分解温度(即化学沸腾温度)是由各自的分解压(即分解反应达到平衡状态时分压)与高炉内煤气中分压和煤气的总压决定的。
碳酸盐的分压随温度升高而增大的,当分解压超过高炉内煤气的分压时,它们就开始分解,而分解压超过煤气的总压时就激烈分解,即化学沸腾。
由于高炉冶炼条件不同,不同高炉内的总压力和分压也有差别,碳酸盐在不同高炉内开始分解和化学沸腾分解温度也有差别。
炼铁初级工复习资料
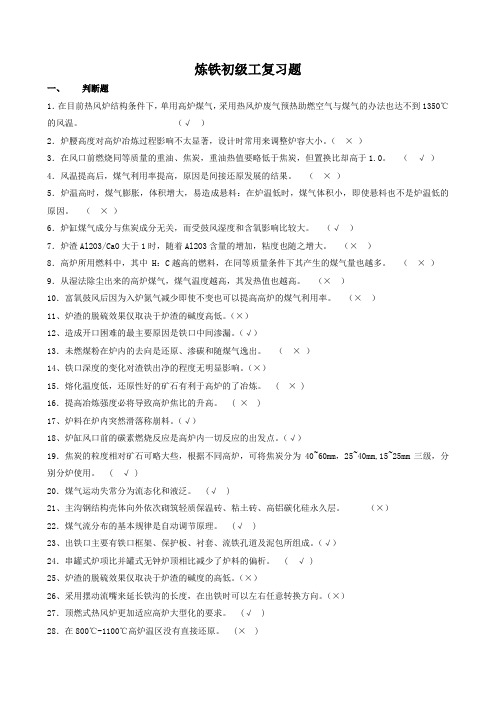
炼铁初级工复习题一、判断题1.在目前热风炉结构条件下,单用高炉煤气,采用热风炉废气预热助燃空气与煤气的办法也达不到1350℃的风温。
(√)2.炉腰高度对高炉冶炼过程影响不太显著,设计时常用来调整炉容大小。
(×)3.在风口前燃烧同等质量的重油、焦炭,重油热值要略低于焦炭,但置换比却高于1.0。
(√)4.风温提高后,煤气利用率提高,原因是间接还原发展的结果。
(×)5.炉温高时,煤气膨胀,体积增大,易造成悬料:在炉温低时,煤气体积小,即使悬料也不是炉温低的原因。
(×)6.炉缸煤气成分与焦炭成分无关,而受鼓风湿度和含氧影响比较大。
(√)7.炉渣Al2O3/CaO大于1时,随着Al2O3含量的增加,粘度也随之增大。
(×)8.高炉所用燃料中,其中 H:C越高的燃料,在同等质量条件下其产生的煤气量也越多。
(×)9.从湿法除尘出来的高炉煤气,煤气温度越高,其发热值也越高。
(×)10.富氧鼓风后因为入炉氮气减少即使不变也可以提高高炉的煤气利用率。
(×)11、炉渣的脱硫效果仅取决于炉渣的碱度高低。
(×)12、造成开口困难的最主要原因是铁口中间渗漏。
(√)13.未燃煤粉在炉内的去向是还原、渗碳和随煤气逸出。
(×)14、铁口深度的变化对渣铁出净的程度无明显影响。
(×)15.熔化温度低,还原性好的矿石有利于高炉的了冶炼。
( × )16.提高冶炼强度必将导致高炉焦比的升高。
( × )17、炉料在炉内突然滑落称崩料。
(√)18、炉缸风口前的碳素燃烧反应是高炉内一切反应的出发点。
(√)19.焦炭的粒度相对矿石可略大些,根据不同高炉,可将焦炭分为40~60mm,25~40mm,15~25mm三级,分别分炉使用。
( √ )20.煤气运动失常分为流态化和液泛。
(√ )21、主沟钢结构壳体向外依次砌筑轻质保温砖、粘土砖、高铝碳化硅永久层。
包钢新体系铁前系统概述-文档资料

17
包钢(集团)公司稀土钢炼铁厂
二、烧结
18
包钢(集团)公司稀土钢炼铁厂
烧结设计效果图
19
包钢(集团)公司稀土钢炼铁厂
烧结鸟瞰图
20
包钢(集团)公司稀土钢炼铁厂
烧结全貌21Fra bibliotek包钢(集团)公司稀土钢炼铁厂
1、烧结主体工艺概述
1.1烧结产能
➢新体系的2台烧结机,由有效烧结面积为500㎡的烧结机及其配套公辅设施构成; ➢年产成品烧结矿1029万吨; ➢是目前国内最大的烧结工程。
22
包钢(集团)公司稀土钢炼铁厂
1.2主体工艺特点
➢由中冶长天国际工程技术有限公司设计; ➢在节能、环保、安全与资源综合利用等方面的经济技术指标也达到国内同行业领先水平; ➢设计特点定位在大型化、自动化、环保化、稳定生产、低耗节能几个方面。
23
包钢(集团)公司稀土钢炼铁厂
1.2主体工艺特点
(1)加强混合料的混匀和制粒,改善混合料的透气性,满足高料层烧结的需要。 (2)采用低温厚料层烧结工艺,料层厚度760毫米(含铺底料),强化料层的蓄热作用,有利于改善产品质 量和减少固体燃料消耗,提高烧结矿的还原性能。 (3)5米宽的烧结台车上部扩展为5.5米。 (4)热风烧结:由鼓风环冷机受料密封罩的热风送至烧 结机的料面,以强化烧结。 (5)采用先进的液密封式鼓风环式冷却机,动密封系统 的漏风率小于1%,静密封系统的漏风率小于5%, 总漏风率小于 10%,冷却后的烧结矿平均温度≤120摄氏度。 (6)烧结矿采用大粒级22.5毫米以上、小粒级22.5毫米至5毫米烧结矿分级入炉方式。 (7)采用进口红外线水分仪,在线检测并自动控制混合料加水,稳定烧结过程。 (8)烧结矿采用高效振动筛,集中筛分,紧凑布置,减少倒运环节,提高作业效率。
炼铁学复习资料
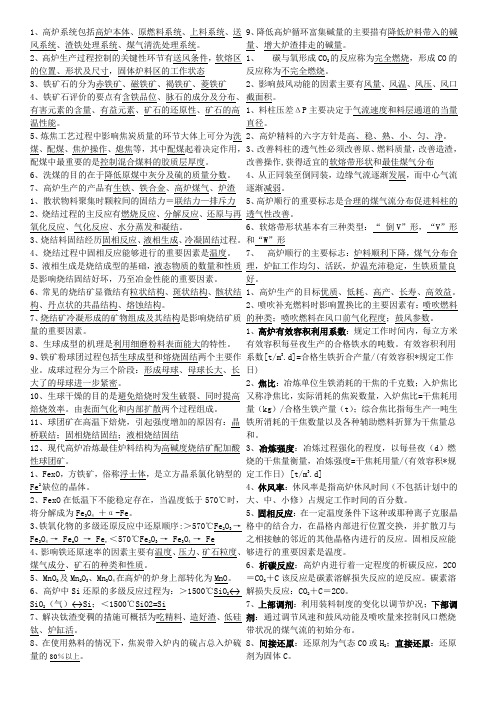
1、高炉系统包括高炉本体、原燃料系统、上料系统、送风系统、渣铁处理系统、煤气清洗处理系统。
2、高炉生产过程控制的关键性环节有送风条件,软熔区的位置、形状及尺寸,固体炉料区的工作状态3、铁矿石的分为赤铁矿、磁铁矿、褐铁矿、菱铁矿4、铁矿石评价的要点有含铁品位、脉石的成分及分布、有害元素的含量、有益元素、矿石的还原性、矿石的高温性能。
5、炼焦工艺过程中影响焦炭质量的环节大体上可分为洗煤、配煤、焦炉操作、熄焦等,其中配煤起着决定作用,配煤中最重要的是控制混合煤料的胶质层厚度。
6、洗煤的目的在于降低原煤中灰分及硫的质量分数。
7、高炉生产的产品有生铁、铁合金、高炉煤气、炉渣1、散状物料聚集时颗粒间的固结力=联结力—排斥力2、烧结过程的主反应有燃烧反应、分解反应、还原与再氧化反应、气化反应、水分蒸发和凝结。
3、烧结料固结经历固相反应、液相生成、冷凝固结过程。
4、烧结过程中固相反应能够进行的重要因素是温度。
5、液相生成是烧结成型的基础,液态物质的数量和性质是影响烧结固结好坏,乃至冶金性能的重要因素。
6、常见的烧结矿显微结有粒状结构、斑状结构、骸状结构、丹点状的共晶结构、熔蚀结构。
7、烧结矿冷凝形成的矿物组成及其结构是影响烧结矿质量的重要因素。
8、生球成型的机理是利用细磨粉料表面能大的特性。
9、铁矿粉球团过程包括生球成型和熔烧固结两个主要作业。
成球过程分为三个阶段:形成母球、母球长大、长大了的母球进一步紧密。
10、生球干燥的目的是避免焙烧时发生破裂、同时提高焙烧效率。
由表面气化和内部扩散两个过程组成。
11、球团矿在高温下焙烧,引起强度增加的原因有:晶桥联结;固相烧结固结;液相烧结固结12、现代高炉冶炼最佳炉料结构为高碱度烧结矿配加酸性球团矿。
1、FexO,方铁矿,俗称浮士体,是立方晶系氯化钠型的Fe2缺位的晶体。
2、FexO在低温下不能稳定存在,当温度低于570℃时,将分解成为Fe3O4+α-Fe。
3、铁氧化物的多级还原反应中还原顺序:>570℃Fe2O3 → Fe3O4 → Fe x O → Fe,<570℃Fe2O3 → Fe3O4 → Fe4、影响铁还原速率的因素主要有温度、压力、矿石粒度、煤气成分、矿石的种类和性质。
冶炼行业的相关知识资料
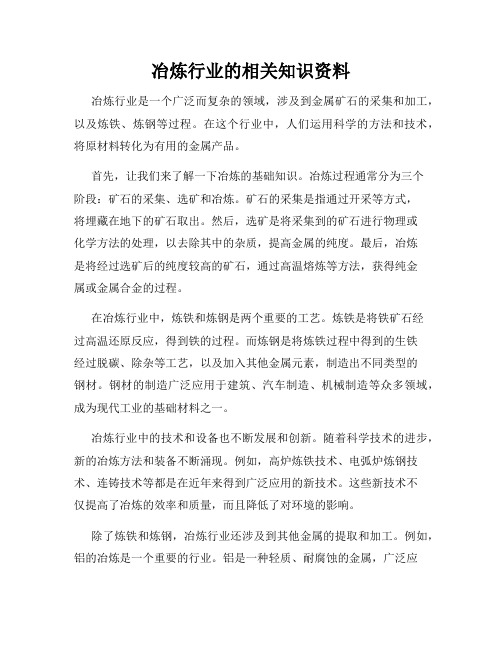
冶炼行业的相关知识资料冶炼行业是一个广泛而复杂的领域,涉及到金属矿石的采集和加工,以及炼铁、炼钢等过程。
在这个行业中,人们运用科学的方法和技术,将原材料转化为有用的金属产品。
首先,让我们来了解一下冶炼的基础知识。
冶炼过程通常分为三个阶段:矿石的采集、选矿和冶炼。
矿石的采集是指通过开采等方式,将埋藏在地下的矿石取出。
然后,选矿是将采集到的矿石进行物理或化学方法的处理,以去除其中的杂质,提高金属的纯度。
最后,冶炼是将经过选矿后的纯度较高的矿石,通过高温熔炼等方法,获得纯金属或金属合金的过程。
在冶炼行业中,炼铁和炼钢是两个重要的工艺。
炼铁是将铁矿石经过高温还原反应,得到铁的过程。
而炼钢是将炼铁过程中得到的生铁经过脱碳、除杂等工艺,以及加入其他金属元素,制造出不同类型的钢材。
钢材的制造广泛应用于建筑、汽车制造、机械制造等众多领域,成为现代工业的基础材料之一。
冶炼行业中的技术和设备也不断发展和创新。
随着科学技术的进步,新的冶炼方法和装备不断涌现。
例如,高炉炼铁技术、电弧炉炼钢技术、连铸技术等都是在近年来得到广泛应用的新技术。
这些新技术不仅提高了冶炼的效率和质量,而且降低了对环境的影响。
除了炼铁和炼钢,冶炼行业还涉及到其他金属的提取和加工。
例如,铝的冶炼是一个重要的行业。
铝是一种轻质、耐腐蚀的金属,广泛应用于航空、建筑、电子等领域。
铜、锌、铅等金属的冶炼也是重要的工艺。
这些金属在电力、通信、交通等现代工业中发挥着重要的作用。
当然,在冶炼过程中也存在一些环境和安全问题。
矿石的开采会破坏地表和地下环境,排放出大量的废渣和废水。
炼铁和炼钢过程中的高温和有害气体,对环境和工人的身体健康也存在潜在风险。
因此,冶炼行业需要严格的环境保护和安全管理措施。
对于冶炼行业的从业人员来说,具备专业的知识和技能尤为重要。
他们需要了解金属材料的物理和化学特性,掌握冶炼工艺和设备的操作技术。
此外,他们还需要关注行业的最新动态和发展趋势,不断学习和提升自己的专业水平。
- 1、下载文档前请自行甄别文档内容的完整性,平台不提供额外的编辑、内容补充、找答案等附加服务。
- 2、"仅部分预览"的文档,不可在线预览部分如存在完整性等问题,可反馈申请退款(可完整预览的文档不适用该条件!)。
- 3、如文档侵犯您的权益,请联系客服反馈,我们会尽快为您处理(人工客服工作时间:9:00-18:30)。
选用符合理化指标的电极石墨颗粒、高纯碳化硅颗粒及细 粉作为主要原料,加入粘土、沥青等粉料,并添加抗氧化剂、烧 结剂等,结合剂采用酚醛树脂,使材料具有良好的施工作业性及 保存期。
项目
体积密度
生
导热系数
SiC
化学成分
F.C Al2O3 SiO2
单位
太钢考 核指标
g/cm3 ≥1.8
W/m.k ≥4
RSSR2碳素泥浆
炉底板
水冷管
RCN-120浇注料
混凝土基墩
RCN-120浇注料、RCN-120G喷涂料
【使用部位】
– 高炉炉底板下部;热风炉蓄热室底部隔热层浇注 – 钢砖空隙处填充料;除尘器煤气出口处铁皮托圈上部
填充料
【特性】
– 强度高,耐火度高,高温性能好 – 导热系数较小,隔热保温效果极佳 – 喷涂性能好,施工反弹率低
RBFD-S9 实测值
98 1.58 ----
12
RBFD-S10 实测值 98 1.54 -26 20 --
RCC-3B碳质泥浆
使用部位:
高炉炉底板上部砌砖前,涂抹在捣打料上;铁 口、炉底炉缸碳砖,炉底高导碳砖的砌筑
作用:方便砌筑
指标 牌号
RCC-3B
挤压缝试验 mm
-
F·C ≥54
化学成分%
灰份 挥发份
目录
• 高炉本体用不定形耐火材料 • 热风炉用不定形耐火材料 • 高炉长寿系列材料
煤气管道
炉
高
喉
炉
炉 身
送风管道
本
体
出铁场
材
炉底
炉缸
料
炉底部分材料
RC-952碳素捣打料
二层粘土保护砖 五层碳砖
炉底一层C-SiC砖
RCC-3B碳素 泥浆
RTJ-1碳素胶泥
RBFD-S10碳 素捣打料
RBFD-S9碳素 捣打料
【作用】
高导热材料,使炉底和捣打料粘紧、利于冷却
【特性】
高导热材料 有良好的粘结性,扩展性 具有一定的保存期
指标 牌号
RSSR-2
体积密度g/cm3 110℃
≥1.3
耐火度 ℃
-
耐压强度MPa 110℃
≥15
导热系数 w/m.k(常温)
≥3.5
RBFD-S9、RBFD-S10碳素捣打料
RBFD-S9: 主要用在炉底、炉缸部位的炉壳与碳砖之间
指标 牌号
使用温度 耐火度 体积密度 抗折强度(Mpa) 烧后线变化(%)化学成份(%)
℃
℃
g/cm3
110℃×24h 1200℃热态
3h
Al2O3
RCN-120 、120G 1200 ≥1540 ≥1.7
≥3.0
≥0.6
1200℃, ±1.0
≥40
RSSR2碳质泥浆
【用途】
用于炉底板和捣打料之间压入
≤6
≤39
水份 ≤1
RTJ-1无水碳素泥浆
用途
用于高导热高炉碳砖的砌泥及高 炉微孔碳砖的砌泥
特点
• 高导热材料 • 有良好的粘结性,扩展性 • 具有一定的保存期
项目
单位
粒度
物理
挤压缝试验
指标
粘结时间
粘结抗折强度 110℃
固定碳
化学成分
水分 灰分
挥发份
mm mm Min MPa %
% % %
太钢考核 指标
环竖缝的填充。
RBFD-S10:主要用在炉底板下、水冷管中心线以上至炉
底板之间及炉底板上找平。
作用:高导热材料,炉底冷却
项目
固定碳 体积密度(g/cm3) 导热系数W/(m.k)
抗压强度 MPa
指标
110℃×24h 100℃
100℃×24h 200℃×24h 1000℃×3h
南钢考核 指标
86 1.5 10 -12(S10) 8(S9)
≤0.5 ≤1.0 2~3 ≥4 ≥50 ≤1.0 ≤10 ≤39
RD 实测值
0.5 0.85 2’40” 4.3 66.2 0.37 9.06 24.71
检验标准 YB/T5164-1993
YB/T5122-1993 YB/T5123-1993
RC-952碳质捣打料
用途:用于炉底上部粘土砖和高铝砖之间捣打 作用:抗渣铁侵蚀
选用特级矾土熟料作为骨料,特级矾土粉、粘土、碳化硅粉等作为粉料, 结合剂使用复合结合剂,使材料具有良好的扩展性。
项目
单位
太钢考 核指标
RD 实测值
检验标准
耐火度
℃
≥1750
1750 YB/T5162-1986
体积密度 110℃×24h
物 理
线变化率
1200℃×3h
指 抗折强度 110℃×24h
标
高温抗折 强度
指 标 牌 体积密度
抗折强度MPa
g/cm3
号
110℃×24h 1400℃×3h
线变化率% 1400℃×3h
化学成分%
SiC
Si3N4
RC-952 ≥1.7
≥2.0
≥2.8
±0.25
≥12
≥20
炉缸冷却壁
RSC-8YK
无水压入泥浆
RSN-13P
碳化硅捣打料
炉皮
RSN-13P捣打料
使用部位
填充炉缸冷却壁之间的间隙
1200℃×0.5h
耐压强度 110℃×24h
化学成分
Al2O3
g/cm3 MPa MPa
MPa
MPa %
≥2.0 ≤±1.0 ≥4.0
≥0.5
≥10.0 ≥55
2.25 -0.58 >11.7
0.53
34 66.4
YB/T5200-1993 YB/T5203-1993
YB/T5201-1993
炼铁系统不定形耐火材料
2014-5-9
宝钢二期工程
包括的项目 1)450m2烧结机; 2)4×50孔焦炉及干熄焦; 3)4063m3高炉、热风炉、混铁车、出铁场; 4)1900mm板坯连铸车间; 5)2050mm热轧板机组; 6)2030mm连续冷轧带钢轧机; 7)石灰石、白云石焙烧车间
所用不定形耐火材料约80多个牌号,均已国产化。
荣大公司消化吸收了大高炉系统80多个牌号的不定形耐火 材料技术,并已在太钢4350m3高炉热风炉上、和南钢 2500m3高炉上应用了一部分材料,例如RCN-140 、 RCL-130、RVL-SG、RZ-2等,这些都是赛迪公司设计的 高炉。
另外太钢3X1000吨石灰窑中所涉及的两条石灰窑用不定 形耐火材料包括45%氧化铝低水泥浇注料、60%氧化铝低水 泥浇注料、70%氧化铝低水泥浇注料、隔热浇注料、耐磨浇 注料和粘土喷涂料。 这些不定形耐火材料主要应用在窑尾 冷却室、窑尾、窑头和窑头罩等部位,并且还有由散料成 型的预制件,这些不定形耐火材料在石灰窑中起着重要的
%
≥20
%
≥40
%
≤5
%
≤15
RD 实测值
1.85 5
21.6 50.9
3.3
12.1
检验标准
YB/T5200-1993 GB/T5990-1986 GB/T1655.1-1996 GB/T13245-1991
GB/T6900-1986
RSC-8YK无水压入泥浆
使用部位填充炉壳与冷却壁源自的缝隙设计方案