富士康制程防呆.ppt
合集下载
防呆法精讲PPT课件

授课:XXX行方法的基本步骤遵循PDCA的 原则
授课:XXX
18
【步骤1】发现人为疏忽
发生何种之人为疏忽,搜集数据进行调查, 重估自己的工作找出疏忽所在。
平常即搜集像异材混入、表示失误、数量 不足、零件遗忘、数据记入错误等,加以 整理即可发现问题点。
调查抱怨情报、工程检查结果、产品检查 结果之数据,掌握发生了何种之问题。
7
狭义“防呆法”
如何设计一个东西,使错误绝不会发生。
授课:XXX
8
广义“防呆法”
如何设计一个东西,而使错误发生的机会 减至最低的程度。
授课:XXX
9
更具体的说明
1.具有即使有人为疏忽也不会发生错误的 构造──不需要注意力。
2.具有外行人来做也不会错的构造──不 需要经验与直觉。
3 具有不管是谁或在何时工作都不会出差 错的构造──不需要专门知识与高度的技 能。
授课:XXX
24
【步骤7】维持管制状态
防呆法是任何人都能使作业不出差错之一 种构造。不断的注意改善状况,若发生新 问题时要能马上处理,贯彻日常的管理乃 是非常重要的事情。
授课:XXX
25
八、基本原理
排除化:剔除会造成错误的要因。 替代化:利用更确实的方法来代替。 容易化:使作业变得更容易、更合适、更独特,
事实上,这句话的积极意义是在鼓励吾人“不 要怕改过,有了错误应该彻底检讨,努力改过 向善”。
授课:XXX
5
二、意义-防呆措施
防呆措施在任何製程或產品上建立安全機 制以預防或減少人為的錯誤
授课:XXX
6
意义-防呆法
其义即是防止呆笨的人做错事。亦即,连 愚笨的人也不会做错事的设计方法
防呆及措施ppt课件

防呆的原则和目标
原则 预防为主,纠正为辅;
全方位、全过程、全员参与;
防呆的原则和目标
简便易行,可操作性强; 持续改进,追求卓越。
目标
防呆的原则和目标
实现零缺陷,减少返工和投诉; 优化生产流程,提升产能;
提高设备综合效率(OEE); 营造安全、健康、环保的工作环境。
防呆在生产和管理中的应用
生产现场防呆
质量防呆工具和技术
FMEA(失效模式与影响分析):一种系统性的 方法,用于识别、评估和优先处理潜在的失效模 式,以预防或减少失效对产品或过程的影响。
SPC(统计过程控制):应用统计技术对生产过 程进行实时监控,发现和纠正过程中的异常波动 ,确保产品质量的稳定和一致。
田口方法:通过设计实验,研究各种因素对产品 或过程性能的影响,找出最佳的设计参数组合, 实现质量的稳健设计。
通过问卷调查和访谈的方式,收集员工对防呆措 施的意见和建议,以便改进和优化措施。
持续改进的思路和方法
定期评估审查
设定合理的时间周期,定期 对防呆措施进行评估审查, 以便及时发现问题,调整和 优化措施。
员工参与改进
鼓励员工提出改进建议,激 发员工的创新意识,让实际 操作者参与到防呆措施的持 续改进中。
数据分析和预测
通过大数据分析,预测设 备可能出现的故障,提前 采取防范措施。
人机交互设计
简洁明了的界面设计
直观的操作提示
确保操作界面简洁、清晰,避免操作人员 因界面复杂而产生混淆或误操作。
提供直观的操作提示,如声音、灯光等, 帮助操作人员准确执行操作。
操作反馈和确认
容错设计
在操作完成后提供明确的反馈和确认信息 ,让操作人员清楚操作结果,避免不确定 性的误操作。
防呆措施培训课件(PPT85页)

l 防呆装置的种类
导轨、模板、微动开关、计数器、顺序限制、标准化、 指示装置、 制止器、感应开关、设计对称、设计非对 称、条件设定(选择)….等。
防呆装置的功能
防呆装置的设计应是简单且不用花太多 钱的,它们是用来: • 避免可能产生的错误,并且 • 侦测错误和导正错误。
迅速的回馈
100%检查
防呆措施预防的层级
定义:错 误
十种最常见的错误
制程遗漏 制程错误 设定工作对象中的
错误 装配遗漏(缺少零件) 包含错误零件/物品
错误的工作对象
操作错误
校正/测量/尺寸上的 错误
在设备保养或维修中 的错误
在叶片,夹具或工具 准备上的错误
常见不良的类型
损坏的零件/产品 倒置的零件/产品 存在异质物品 错装的零件 错排的零件
无法装配 矛盾的测试结果/测
试失败 不良的进货物料 错误的物料/零件 错误或矛盾的尺寸 其他....?
制程中导致不良的情况
调整 工具使用/工具替换 尺寸/规格/临界条件 多种/混合零件 多重步骤 罕见产品 缺乏有效的作业标准
对称/不对称 快速重制 高容积/极高容积 环境状况:
管制计划 (包含 应变计划)
零件 选择灯
站内文件
工具 转换程序
工作 辅助
QPS
QPS 1) Receive block 2) Add bolts 3) Check torque 4) Finish load,
and return
辅助广告牌 极限开关
汽车音响检视站-改善前
从上游操作而来 未测试的电路板
防呆措施概述
5.角色与职责:
圈长
• 小组长成员间的协调 • 提供训练与指导 • 解决问题与障碍
导轨、模板、微动开关、计数器、顺序限制、标准化、 指示装置、 制止器、感应开关、设计对称、设计非对 称、条件设定(选择)….等。
防呆装置的功能
防呆装置的设计应是简单且不用花太多 钱的,它们是用来: • 避免可能产生的错误,并且 • 侦测错误和导正错误。
迅速的回馈
100%检查
防呆措施预防的层级
定义:错 误
十种最常见的错误
制程遗漏 制程错误 设定工作对象中的
错误 装配遗漏(缺少零件) 包含错误零件/物品
错误的工作对象
操作错误
校正/测量/尺寸上的 错误
在设备保养或维修中 的错误
在叶片,夹具或工具 准备上的错误
常见不良的类型
损坏的零件/产品 倒置的零件/产品 存在异质物品 错装的零件 错排的零件
无法装配 矛盾的测试结果/测
试失败 不良的进货物料 错误的物料/零件 错误或矛盾的尺寸 其他....?
制程中导致不良的情况
调整 工具使用/工具替换 尺寸/规格/临界条件 多种/混合零件 多重步骤 罕见产品 缺乏有效的作业标准
对称/不对称 快速重制 高容积/极高容积 环境状况:
管制计划 (包含 应变计划)
零件 选择灯
站内文件
工具 转换程序
工作 辅助
QPS
QPS 1) Receive block 2) Add bolts 3) Check torque 4) Finish load,
and return
辅助广告牌 极限开关
汽车音响检视站-改善前
从上游操作而来 未测试的电路板
防呆措施概述
5.角色与职责:
圈长
• 小组长成员间的协调 • 提供训练与指导 • 解决问题与障碍
防呆防错PPT幻灯片课件

1
利用防错防呆技术设置缺陷探测器 • 接触装置 原理:必须与物体接触,可以由一个小弹片得知
物体的存在 功能:判别物料的大小,放置的位置 例如:限为开关、转换开关(最常 用的)配置传感器, 金属通过传感器
1
利用防错防呆技术设置缺陷探测器 • 非接触装置(光电装置) 原理:不须与物体接触,可藉光线就可得知物体
1
零缺陷的策略 1.及时生产(just-in-time)
若你不需要就不要生产,当产品变成存货时你生产 越多发生瑕疵的机会就越多,以及时生产的原则来 说,当你需要时才生产,需要多少就生产多少. 2.持续改进 使用者是发现瑕疵的专家,因此建立一套具有防护 系统的生产流程,是很重要的,可以确保产品禁的 起任何的使用,经由防错防呆技术、自动化及作业 标准化可以将质量建立于生产 3.若你无法使一项产品禁得起任何的使用,那就确保 在连续的制程中产品能很快的被使用到.
应对防呆点餐法那就是餐票自动贩卖机有很多地方都是采用这种制度在餐厅的入口处会摆上一台餐票自动贩卖机餐票自动贩卖机上当然也是图文并茂决对不会让你发生看不懂你只要投钱再按钮选餐餐票自动贩卖机就会找零并且给你一张餐券进到餐厅后找个位子座下来把餐券放在桌上服务生会先很有礼貌的送上一杯茶水及餐具再过个几分钟就会把你的点送到你面前
1
2.百分之百检验是最好的,在最好的工厂中, 他们所抱持的态度是“我们要规划我们的 生产线,是能够轻易的让我们百分之百的 检验产品”,因为只要一件有瑕疵的产品 就能够破坏顾客对公司的信任,因此要保持 竞争力,公司必须提共质量良好的产品,而 最好的方法就是百分之百检验.
1
3.使用者是最好的检查员,没有人想要犯错, 但是当我们一不注意时错误就发生了,而我 们如何能在错误发生前就发现呢?---在随 后的制程中发现瑕疵.在我们不预期能找到 瑕疵时发现我们要使用一项产品却不能用 时,我们知道这项产品有瑕疵.若我们将下 一个制程当作是上一个制程的使用者时,我 们可以立刻知道产品是否有瑕疵,因此如果 我们的制程是连续的,产品很快的会被送至 下个制程,那么只要产品有瑕疵我们便可以 马上发现
利用防错防呆技术设置缺陷探测器 • 接触装置 原理:必须与物体接触,可以由一个小弹片得知
物体的存在 功能:判别物料的大小,放置的位置 例如:限为开关、转换开关(最常 用的)配置传感器, 金属通过传感器
1
利用防错防呆技术设置缺陷探测器 • 非接触装置(光电装置) 原理:不须与物体接触,可藉光线就可得知物体
1
零缺陷的策略 1.及时生产(just-in-time)
若你不需要就不要生产,当产品变成存货时你生产 越多发生瑕疵的机会就越多,以及时生产的原则来 说,当你需要时才生产,需要多少就生产多少. 2.持续改进 使用者是发现瑕疵的专家,因此建立一套具有防护 系统的生产流程,是很重要的,可以确保产品禁的 起任何的使用,经由防错防呆技术、自动化及作业 标准化可以将质量建立于生产 3.若你无法使一项产品禁得起任何的使用,那就确保 在连续的制程中产品能很快的被使用到.
应对防呆点餐法那就是餐票自动贩卖机有很多地方都是采用这种制度在餐厅的入口处会摆上一台餐票自动贩卖机餐票自动贩卖机上当然也是图文并茂决对不会让你发生看不懂你只要投钱再按钮选餐餐票自动贩卖机就会找零并且给你一张餐券进到餐厅后找个位子座下来把餐券放在桌上服务生会先很有礼貌的送上一杯茶水及餐具再过个几分钟就会把你的点送到你面前
1
2.百分之百检验是最好的,在最好的工厂中, 他们所抱持的态度是“我们要规划我们的 生产线,是能够轻易的让我们百分之百的 检验产品”,因为只要一件有瑕疵的产品 就能够破坏顾客对公司的信任,因此要保持 竞争力,公司必须提共质量良好的产品,而 最好的方法就是百分之百检验.
1
3.使用者是最好的检查员,没有人想要犯错, 但是当我们一不注意时错误就发生了,而我 们如何能在错误发生前就发现呢?---在随 后的制程中发现瑕疵.在我们不预期能找到 瑕疵时发现我们要使用一项产品却不能用 时,我们知道这项产品有瑕疵.若我们将下 一个制程当作是上一个制程的使用者时,我 们可以立刻知道产品是否有瑕疵,因此如果 我们的制程是连续的,产品很快的会被送至 下个制程,那么只要产品有瑕疵我们便可以 马上发现
防呆及措施ppt课件

防呆及措施ppt课件
汇报人: 日期:
目 录
• 防呆概述 • 防呆的常见方法和措施 • 防呆措施在各行各业的应用案例 • 防呆措施的效果评估与持续改进
01 防呆概述
防呆的定义和意义
定义
防呆是一种通过预防、控制和纠 正措施,减少或消除生产过程中 错误、浪费和不良现象的方法。
意义
提高生产效率,降低成本,增强 产品质量,提升客户满意度。
作业指导和标准化操作;
防呆在生产和管理中的应用
生产线布局优化和流程改善。
建立防呆机制和制度体系;
在管理中的应用
防呆在生产和管理中的应用
开展防呆培训和意识 提升;
实施持续改进和创新 管理。
பைடு நூலகம்推行绩效考核和激励 机制;
02 防呆的常见方法和措施
标准化操作
操作规范明确
制定详细且明确的操作规范,确 保操作人员按照统一的标准进行 操作,减少因个人习惯或误解导
致的错误。
培训和认证
对操作人员进行系统的培训,提高 其操作技能和意识水平,并通过认 证确保其具备操作资格。
定期检查和评估
定期对操作过程进行检查和评估, 及时发现问题和不足,进行相应的 改进和优化。
自动化和智能化设备
自动化设备
采用自动化设备,减少人工操作 环节,降低人为错误的可能性,
提高工作效率和准确性。
防呆的原则和目标
原则 预防为主,纠正为辅;
着眼于全局,从源头抓起;
防呆的原则和目标
简化操作,减少人为因素; 标准化、目视化和人性化。
防呆的原则和目标
01
目标
02
03
04
实现零缺陷,减少返工和投诉 ;
提高员工工作积极性和满意度 ;
汇报人: 日期:
目 录
• 防呆概述 • 防呆的常见方法和措施 • 防呆措施在各行各业的应用案例 • 防呆措施的效果评估与持续改进
01 防呆概述
防呆的定义和意义
定义
防呆是一种通过预防、控制和纠 正措施,减少或消除生产过程中 错误、浪费和不良现象的方法。
意义
提高生产效率,降低成本,增强 产品质量,提升客户满意度。
作业指导和标准化操作;
防呆在生产和管理中的应用
生产线布局优化和流程改善。
建立防呆机制和制度体系;
在管理中的应用
防呆在生产和管理中的应用
开展防呆培训和意识 提升;
实施持续改进和创新 管理。
பைடு நூலகம்推行绩效考核和激励 机制;
02 防呆的常见方法和措施
标准化操作
操作规范明确
制定详细且明确的操作规范,确 保操作人员按照统一的标准进行 操作,减少因个人习惯或误解导
致的错误。
培训和认证
对操作人员进行系统的培训,提高 其操作技能和意识水平,并通过认 证确保其具备操作资格。
定期检查和评估
定期对操作过程进行检查和评估, 及时发现问题和不足,进行相应的 改进和优化。
自动化和智能化设备
自动化设备
采用自动化设备,减少人工操作 环节,降低人为错误的可能性,
提高工作效率和准确性。
防呆的原则和目标
原则 预防为主,纠正为辅;
着眼于全局,从源头抓起;
防呆的原则和目标
简化操作,减少人为因素; 标准化、目视化和人性化。
防呆的原则和目标
01
目标
02
03
04
实现零缺陷,减少返工和投诉 ;
提高员工工作积极性和满意度 ;
《防呆法防错法》课件

防呆防错法是一种系统性的方法,通过设计产品和工艺过程,消除或减少潜在 的错误和缺陷。它强调预防错误的发生,而不是依赖检查和测试来发现错误。
目的与意义
总结词
防呆防错法的目的是提高产品质量、降低生产成本、增强生产安全和提升企业竞争力。
详细描述
防呆防错法的实施有助于提高产品质量,减少产品缺陷和客户投诉,降低生产成本,提 高生产效率。同时,它还有助于增强生产安全,保护员工免受因错误操作而导致的伤害 。长期来看,防呆防错法的应用能够提升企业的竞争力,使企业在激烈的市场竞争中保
根据评估结果,制定相应的改进措施,优 化防呆防错法的实施方案。
培训与指导
持续改进
对员工进行定期的培训和指导,提高其对 防呆防错法的应用能力。
不断优化和完善防呆防错法,提高其在实 际生产中的应用效果。
THANKS FOR WATCHING
感谢您的观看
详细描述
在办公室工作中,可以采用电子文档管理、标准化工作流程、定期备份数据等措施,降低错误率,提 高工作效率。
案例三:家庭生活中的防呆防错应用
总结词
通过日常生活中的小细节,避免出现意 外事故。
VS
详细描述
在家庭生活中,可以通过安全警示标识、 正确使用电器设备、定期检查燃气设备等 措施,保障家庭安全。
检测法
总结词
在错误发生后及时检测并纠正,防止错误扩大或重复发生。
详细描述
通过设置检查点、监控系统等手段,及时发现并纠正错误,确保流程的正确执行 。
缓和法
总结词
通过采取措施缓解错误产生的影响, 降低错误造成的损失。
详细描述
在错误发生后采取适当的措施,如备 用方案、应急措施等,以减轻错误造 成的影响,确保流程的顺利进行。
目的与意义
总结词
防呆防错法的目的是提高产品质量、降低生产成本、增强生产安全和提升企业竞争力。
详细描述
防呆防错法的实施有助于提高产品质量,减少产品缺陷和客户投诉,降低生产成本,提 高生产效率。同时,它还有助于增强生产安全,保护员工免受因错误操作而导致的伤害 。长期来看,防呆防错法的应用能够提升企业的竞争力,使企业在激烈的市场竞争中保
根据评估结果,制定相应的改进措施,优 化防呆防错法的实施方案。
培训与指导
持续改进
对员工进行定期的培训和指导,提高其对 防呆防错法的应用能力。
不断优化和完善防呆防错法,提高其在实 际生产中的应用效果。
THANKS FOR WATCHING
感谢您的观看
详细描述
在办公室工作中,可以采用电子文档管理、标准化工作流程、定期备份数据等措施,降低错误率,提 高工作效率。
案例三:家庭生活中的防呆防错应用
总结词
通过日常生活中的小细节,避免出现意 外事故。
VS
详细描述
在家庭生活中,可以通过安全警示标识、 正确使用电器设备、定期检查燃气设备等 措施,保障家庭安全。
检测法
总结词
在错误发生后及时检测并纠正,防止错误扩大或重复发生。
详细描述
通过设置检查点、监控系统等手段,及时发现并纠正错误,确保流程的正确执行 。
缓和法
总结词
通过采取措施缓解错误产生的影响, 降低错误造成的损失。
详细描述
在错误发生后采取适当的措施,如备 用方案、应急措施等,以减轻错误造 成的影响,确保流程的顺利进行。
制程防呆
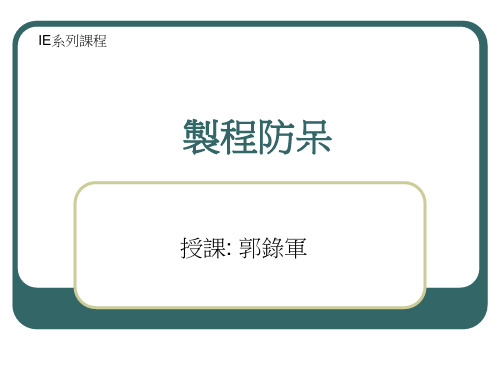
IE系列課程
製程防呆
授課: 郭錄軍
課程大綱
一. 防呆概述 二. 製程防呆應用
一. 防呆概述
防呆的定義
設計一個方法,防止錯誤發生. 或使錯誤發生 的機率降至最低程度. 使事情一次就做好.
也稱愚巧法、防錯法, 起源於日本丰田 公司(日本譯音POKA YOKE)
一. 防呆概述
防呆的改善對象是什么? 防呆的改善對象是什么
防呆法應用實 防呆法應用實例 應用
2.點焊機電極溫度控制改善﹕ 點焊機電極溫度控制改善﹕ 點焊機電極溫度控制改善 改善前﹕由于點焊機電極發熱溫度過 高﹐使工件焊接點發黑﹐造成外觀不良。 防呆改善﹕在電極尾部裝一個溫度傳感 器﹐當溫度超過標准要求上限時﹐溫度傳感 器切斷控制電路﹐使機床無法下壓﹐當電極 在冷卻裝置的作用下恢復正常溫度時﹐方可 正常作業。
提示(五感)的方式
1. 一般性提示
(狀態標識﹔SOP﹔圖示)
2. 重點信息提醒
(安全資訊﹑危險標志﹑使用說明)
二. 製程防呆應用
檢測器
1、判断型检测(Judgment Inspection) 、判断型检测 (1) (1)通过比較判斷方法,發現問題(或不良品)。 , ( ) (2)有問題時停止動作,防止問題發生(不良流出)。
二. 製程防呆應用
檢測器
3﹑溯源檢測(Source Inspection) ﹑溯源檢測 (1)对製程因子进行检测和确认,以保证在作业 之前就满足生产出高品质產品所需的条件。
(2)溯源型检测是预防型检测。通过对源头控制,
从而确保品质要求。
二. 製程防呆應用
警告的方式
對錯誤發出警告信號: 1) 聲音/文字 2) 閃燈 3) 其它(E-mail,短信)
製程防呆
授課: 郭錄軍
課程大綱
一. 防呆概述 二. 製程防呆應用
一. 防呆概述
防呆的定義
設計一個方法,防止錯誤發生. 或使錯誤發生 的機率降至最低程度. 使事情一次就做好.
也稱愚巧法、防錯法, 起源於日本丰田 公司(日本譯音POKA YOKE)
一. 防呆概述
防呆的改善對象是什么? 防呆的改善對象是什么
防呆法應用實 防呆法應用實例 應用
2.點焊機電極溫度控制改善﹕ 點焊機電極溫度控制改善﹕ 點焊機電極溫度控制改善 改善前﹕由于點焊機電極發熱溫度過 高﹐使工件焊接點發黑﹐造成外觀不良。 防呆改善﹕在電極尾部裝一個溫度傳感 器﹐當溫度超過標准要求上限時﹐溫度傳感 器切斷控制電路﹐使機床無法下壓﹐當電極 在冷卻裝置的作用下恢復正常溫度時﹐方可 正常作業。
提示(五感)的方式
1. 一般性提示
(狀態標識﹔SOP﹔圖示)
2. 重點信息提醒
(安全資訊﹑危險標志﹑使用說明)
二. 製程防呆應用
檢測器
1、判断型检测(Judgment Inspection) 、判断型检测 (1) (1)通过比較判斷方法,發現問題(或不良品)。 , ( ) (2)有問題時停止動作,防止問題發生(不良流出)。
二. 製程防呆應用
檢測器
3﹑溯源檢測(Source Inspection) ﹑溯源檢測 (1)对製程因子进行检测和确认,以保证在作业 之前就满足生产出高品质產品所需的条件。
(2)溯源型检测是预防型检测。通过对源头控制,
从而确保品质要求。
二. 製程防呆應用
警告的方式
對錯誤發出警告信號: 1) 聲音/文字 2) 閃燈 3) 其它(E-mail,短信)
生产一线如何做到防错防呆管理讲义(PPT 34页)

----原丰田汽车工业社长渡边捷昭
24
做最专业、最系统化的企业全员培训平台
如何明白浪费
随时检查和防止自己身边的7种浪费。
25
做最专业、最系统化的企业全员培训平台
明确目的
实施清扫的目的就是通过整体某些东西去明白和发现浪费。
26
做最专业、最系统化的企业全员培训平台
排除过于膨胀的工作
在丰田,因为发现组织过于庞大,在决策时要耗费一定 的时间,就发起了“图章3个运动”。就像在七个浪费中最先被 研究的是“生产过剩的浪费”一样,“工作过度”也是同样的 浪费。
7
做最专业、最系统化的企业全员培训平台
第二讲:防止错误的手段
8
做最专业、最系统化的企业全员培训平台
防止错误的手段
提醒装置
纠错装置
一旦发生异常,就会通过蜂鸣 器的声音和红色的灯光发出信号, 提醒操作人员注意的方式
一旦发生异常,就会自动停止 机械和生产线,无法继续工作的方 式。
没有声音:正常运行,绿灯亮
提高人均生产效 率的想法
12
10 不 合 格 率8 (%)
6
4
如果持有危机意识,就会发现改善的主
活用QC手法 题
(基本上能够
消除不合格
①
产品)
活用IE手法 (仔细观察事物,提高生产效率)
通过IE、QC手法 还不能找到改善 对策时,活用V
A/VE手法
具有①实力的企业 和具有②实力的企 业,其人均生产效
4
做最专业、最系统化的企业全员培训平台
原因2—环境恶劣
原因
照明太暗或过于明亮 噪声 粉尘 高温、湿度太大 振动 有气味 有毒气体
事例
在太暗或太亮的照明灯下进行 检查,时间一长,检查的精确度就 会下降。
24
做最专业、最系统化的企业全员培训平台
如何明白浪费
随时检查和防止自己身边的7种浪费。
25
做最专业、最系统化的企业全员培训平台
明确目的
实施清扫的目的就是通过整体某些东西去明白和发现浪费。
26
做最专业、最系统化的企业全员培训平台
排除过于膨胀的工作
在丰田,因为发现组织过于庞大,在决策时要耗费一定 的时间,就发起了“图章3个运动”。就像在七个浪费中最先被 研究的是“生产过剩的浪费”一样,“工作过度”也是同样的 浪费。
7
做最专业、最系统化的企业全员培训平台
第二讲:防止错误的手段
8
做最专业、最系统化的企业全员培训平台
防止错误的手段
提醒装置
纠错装置
一旦发生异常,就会通过蜂鸣 器的声音和红色的灯光发出信号, 提醒操作人员注意的方式
一旦发生异常,就会自动停止 机械和生产线,无法继续工作的方 式。
没有声音:正常运行,绿灯亮
提高人均生产效 率的想法
12
10 不 合 格 率8 (%)
6
4
如果持有危机意识,就会发现改善的主
活用QC手法 题
(基本上能够
消除不合格
①
产品)
活用IE手法 (仔细观察事物,提高生产效率)
通过IE、QC手法 还不能找到改善 对策时,活用V
A/VE手法
具有①实力的企业 和具有②实力的企 业,其人均生产效
4
做最专业、最系统化的企业全员培训平台
原因2—环境恶劣
原因
照明太暗或过于明亮 噪声 粉尘 高温、湿度太大 振动 有气味 有毒气体
事例
在太暗或太亮的照明灯下进行 检查,时间一长,检查的精确度就 会下降。
- 1、下载文档前请自行甄别文档内容的完整性,平台不提供额外的编辑、内容补充、找答案等附加服务。
- 2、"仅部分预览"的文档,不可在线预览部分如存在完整性等问题,可反馈申请退款(可完整预览的文档不适用该条件!)。
- 3、如文档侵犯您的权益,请联系客服反馈,我们会尽快为您处理(人工客服工作时间:9:00-18:30)。
零缺陷战略
用户得到 的是什么?
为什么?
•每个厂外和厂内用户都期望着从他的“供货商”那里得 到无缺陷的产品。每个“供货商”对此负责!
拥护不希望遇到问题(用户至上)
•链锁中的每个单元都有自己的工作任务。 后续单元没 有义务并且无法在前面单元提供的产品中寻找和消除缺 陷。
•遗忘或没有集中注意力 •误解、或没有获得全部信息就跳到结论 •培训、或缺少培训 •忽视规则故意出错 •由于分心或疲惫引起的疏忽 •迟钝或判断延误 •缺少标准 •当事情没有如计划运行是,惊慌失措 •故意破坏捣乱
人为差错
遗漏工序 加工错误 安装错误 遗漏零件 错误零件 加工错误工件 操作错误 调整错误 不适当工具
条形码
理想的价值创造过程 真实的,实际的价值创造过程
“非质量”总是意味 着损失:
附加成本,返修工 时,惹气;这些都 意味着生产率的损
失,都是浪费。
由下列原因产生的损失: -材料报废 -工作报废 -外购件不合格 -过程运转不均衡 高库存
零缺陷战略
整个过程的各步骤都不 产生缺陷。成品合格率 为100%(一次合格率 =100%
扭矩和角度监视
•测试机床模仿总装在汽车上 的功能 •使用非常精确的感应技术和 电脑技术
功能测试
•在线检验可以检查和防止错误发生
在线检验
•用油漆记号指出操作完成的简 单系统 •到位记号是由下一位操作员检 查是否存在 •和检验卡相似
接触记号
•当错误发生时音频警报便发出讯号 •当错误发生时提醒操作员和工作领导 •比灯号更容易识别 •将会使用在所有的工序上
生产率最高,用户满意 度最高。
一次合格率<100%。 由下列原因产生的损失: -返修工时 -合格与不合格品分类工时 -缺陷分析 -索赔 -等待 -特殊措施 -故障
最终不合 格品份额
合格
零缺陷战略:
全过程中每道工序都应制造出100%合格品(规划)。 每道工序都应该确保实现这一要求(实施和检验)。
为什么?
缺陷的种类
过程需要人干预 体力性的重复劳动 知道会发生错误 预测会发生错误
防错的使用情况
识别问题
顾客反馈、缺陷零件分析、错误报告、FMEA
问题分优先级
根据问题的频率和成本分优先级。 确定浪费的材料,返工的时间,检测时 间,考虑检查成本
寻找根本原因
一直往下追溯,直到真正理解错误的来源,在源头改正错误
刀具破损/刀具磨损检测
•利用邻近/限位或压力开关检查不正确零 件的安装 •邻近和限位开关主要用在到位零件 •定位器气孔和压力开关能检查零件位置 是否正确
零件到位传感器
•电脑数控刀具管理程序定期指示操作员换 刀和检查工件 •提供讯号和灯号警报系统 •防止刀具破损和确保质量检查频率
换刀和质量检测计数器
富士康科技公司 基础IE培训
中北大学工业工程
内容之三 制程防呆
防错的定义 错误发生的原因 人为差错以及缺陷种类 加工中的防错策略 装配线上的防错策略
为尽量减少制造过程出现错误或缺陷而 采用的一种工艺或机构装置:
•帮助操作工: 防错必须以消除操作工的体力或脑力负担为设计原
则,前提是操作工主观上想把工作做好; •简单
零件装配箱
•光幕放在零件箱上检查操作 员的手挑选零件
光幕
•利用开关检查零件到位和刀具使用
零件和刀具到位检查
•电子仪器检查压床压力和泄露
压力感应器/验漏
•电子监视螺纹连接操作 •监视扭矩和角度,如果任何一项超出 限制工件也会报废 •扭矩枪和灯号警报系统以及无线电频 率标签连在一起 •计数器可以使用在单轴枪多紧固件上
灯号音频警报系统
•在托盘上书写或记录质量和错误防止的信息 •资料输入电脑配合零件顺序号码因此能够调查和预 防将废品给客户 •使用在变速箱和发动机装配线上
无线电频率标签
•工件的设计可以防止错误 •现有产品很难进行设计改进
产品设计
•视觉讯号指出正确物料,工件和旗 号问题
视觉控制
•分辨不同型号的零件 •用条形码扫描来分辨正确的装配件或 工序
实施和保养简单的成本低 •重复性
重复性防错大大提高了发现缺陷的可能性,同时体现 了简单、成本低的理念,降低了检查工序停机造成的影响。
防错的定义
•步骤不正确或遗漏,步骤不能与任务、环 境、设备、材料、测量或劳动力匹配 •过程中的变化太多 •原材料中的变化太多 •测量设备出错 •人为差错
错误发生的原因
产生解决办法
使做错是不可能的。做成本效益分析,看多久能收回投资,产生解决方法 时有创造性
衡量结果
错误消除了吗? 影响是什么?
防错的五个步骤
•PFMEA(工艺失效模式和效果分析) •用优先顺序号码的排列来决定优先顺序 •目标是防止错误发生 •在工艺过程中建立一种廉价的100%检验 •成功率超过60%便可立即采用 •是不断改进过程的一部分 •Process Wall 策略的一部分,用图表显示计 划的进度
•在滚道上装上工件样板可以防止工件 装反,不到位和不合格工件
仿行样板
•零件装配箱 •光幕 •零件或刀具到位检查 •压力感应器/验漏 •扭距和角度监视 •最后测试 •接触记号 •灯号警报音频系统 •无线电频率标签 •产品设计 •视觉控制 •条形码
装配线上的防错策略
•正确零件数量安放在特殊设计的装配 零件盘 •遗漏和剩余零件给操作员视觉讯号显 示错误发生 •并有人体工程学的利益
PFMEA(工艺失效模式和效果分析)
•夹具设计 •刀具破损/刀具磨损检测 •零件到位传感器 •换刀具和质量检查计数器 •仿行样板
加工中防错的策略
•夹具的设计是为了防止零件放在错误的位 置上 •使用销钉防止装反零件或零件方向错误 •选择使用卡盘和定位器设计是为了防止装 反零件
夹具设计
•利用振动监视,开关,动力监视或其它方 法检测破损或磨损刀具 •技术能够检测到刀具破坏,但检测刀具磨 损不够有效 •同时能够检查由于不适当的安装或电脑程 序引起的破坏
防错设计的发展
•参考DFMEA(设计失效模式和效果分析)识 别出来的设计失效模式 •在应用之前分析工艺过程来减少废品 •应该是包括多个部门的小组工作 •失败模式根据优先顺序号码排列 •RPN优先顺序号码的排列=严重程度*发生频率 *查出原因机率 •所有优先顺序号码的排列,超过40便采用防错 设计减少到40以下
用户得到 的是什么?
为什么?
•每个厂外和厂内用户都期望着从他的“供货商”那里得 到无缺陷的产品。每个“供货商”对此负责!
拥护不希望遇到问题(用户至上)
•链锁中的每个单元都有自己的工作任务。 后续单元没 有义务并且无法在前面单元提供的产品中寻找和消除缺 陷。
•遗忘或没有集中注意力 •误解、或没有获得全部信息就跳到结论 •培训、或缺少培训 •忽视规则故意出错 •由于分心或疲惫引起的疏忽 •迟钝或判断延误 •缺少标准 •当事情没有如计划运行是,惊慌失措 •故意破坏捣乱
人为差错
遗漏工序 加工错误 安装错误 遗漏零件 错误零件 加工错误工件 操作错误 调整错误 不适当工具
条形码
理想的价值创造过程 真实的,实际的价值创造过程
“非质量”总是意味 着损失:
附加成本,返修工 时,惹气;这些都 意味着生产率的损
失,都是浪费。
由下列原因产生的损失: -材料报废 -工作报废 -外购件不合格 -过程运转不均衡 高库存
零缺陷战略
整个过程的各步骤都不 产生缺陷。成品合格率 为100%(一次合格率 =100%
扭矩和角度监视
•测试机床模仿总装在汽车上 的功能 •使用非常精确的感应技术和 电脑技术
功能测试
•在线检验可以检查和防止错误发生
在线检验
•用油漆记号指出操作完成的简 单系统 •到位记号是由下一位操作员检 查是否存在 •和检验卡相似
接触记号
•当错误发生时音频警报便发出讯号 •当错误发生时提醒操作员和工作领导 •比灯号更容易识别 •将会使用在所有的工序上
生产率最高,用户满意 度最高。
一次合格率<100%。 由下列原因产生的损失: -返修工时 -合格与不合格品分类工时 -缺陷分析 -索赔 -等待 -特殊措施 -故障
最终不合 格品份额
合格
零缺陷战略:
全过程中每道工序都应制造出100%合格品(规划)。 每道工序都应该确保实现这一要求(实施和检验)。
为什么?
缺陷的种类
过程需要人干预 体力性的重复劳动 知道会发生错误 预测会发生错误
防错的使用情况
识别问题
顾客反馈、缺陷零件分析、错误报告、FMEA
问题分优先级
根据问题的频率和成本分优先级。 确定浪费的材料,返工的时间,检测时 间,考虑检查成本
寻找根本原因
一直往下追溯,直到真正理解错误的来源,在源头改正错误
刀具破损/刀具磨损检测
•利用邻近/限位或压力开关检查不正确零 件的安装 •邻近和限位开关主要用在到位零件 •定位器气孔和压力开关能检查零件位置 是否正确
零件到位传感器
•电脑数控刀具管理程序定期指示操作员换 刀和检查工件 •提供讯号和灯号警报系统 •防止刀具破损和确保质量检查频率
换刀和质量检测计数器
富士康科技公司 基础IE培训
中北大学工业工程
内容之三 制程防呆
防错的定义 错误发生的原因 人为差错以及缺陷种类 加工中的防错策略 装配线上的防错策略
为尽量减少制造过程出现错误或缺陷而 采用的一种工艺或机构装置:
•帮助操作工: 防错必须以消除操作工的体力或脑力负担为设计原
则,前提是操作工主观上想把工作做好; •简单
零件装配箱
•光幕放在零件箱上检查操作 员的手挑选零件
光幕
•利用开关检查零件到位和刀具使用
零件和刀具到位检查
•电子仪器检查压床压力和泄露
压力感应器/验漏
•电子监视螺纹连接操作 •监视扭矩和角度,如果任何一项超出 限制工件也会报废 •扭矩枪和灯号警报系统以及无线电频 率标签连在一起 •计数器可以使用在单轴枪多紧固件上
灯号音频警报系统
•在托盘上书写或记录质量和错误防止的信息 •资料输入电脑配合零件顺序号码因此能够调查和预 防将废品给客户 •使用在变速箱和发动机装配线上
无线电频率标签
•工件的设计可以防止错误 •现有产品很难进行设计改进
产品设计
•视觉讯号指出正确物料,工件和旗 号问题
视觉控制
•分辨不同型号的零件 •用条形码扫描来分辨正确的装配件或 工序
实施和保养简单的成本低 •重复性
重复性防错大大提高了发现缺陷的可能性,同时体现 了简单、成本低的理念,降低了检查工序停机造成的影响。
防错的定义
•步骤不正确或遗漏,步骤不能与任务、环 境、设备、材料、测量或劳动力匹配 •过程中的变化太多 •原材料中的变化太多 •测量设备出错 •人为差错
错误发生的原因
产生解决办法
使做错是不可能的。做成本效益分析,看多久能收回投资,产生解决方法 时有创造性
衡量结果
错误消除了吗? 影响是什么?
防错的五个步骤
•PFMEA(工艺失效模式和效果分析) •用优先顺序号码的排列来决定优先顺序 •目标是防止错误发生 •在工艺过程中建立一种廉价的100%检验 •成功率超过60%便可立即采用 •是不断改进过程的一部分 •Process Wall 策略的一部分,用图表显示计 划的进度
•在滚道上装上工件样板可以防止工件 装反,不到位和不合格工件
仿行样板
•零件装配箱 •光幕 •零件或刀具到位检查 •压力感应器/验漏 •扭距和角度监视 •最后测试 •接触记号 •灯号警报音频系统 •无线电频率标签 •产品设计 •视觉控制 •条形码
装配线上的防错策略
•正确零件数量安放在特殊设计的装配 零件盘 •遗漏和剩余零件给操作员视觉讯号显 示错误发生 •并有人体工程学的利益
PFMEA(工艺失效模式和效果分析)
•夹具设计 •刀具破损/刀具磨损检测 •零件到位传感器 •换刀具和质量检查计数器 •仿行样板
加工中防错的策略
•夹具的设计是为了防止零件放在错误的位 置上 •使用销钉防止装反零件或零件方向错误 •选择使用卡盘和定位器设计是为了防止装 反零件
夹具设计
•利用振动监视,开关,动力监视或其它方 法检测破损或磨损刀具 •技术能够检测到刀具破坏,但检测刀具磨 损不够有效 •同时能够检查由于不适当的安装或电脑程 序引起的破坏
防错设计的发展
•参考DFMEA(设计失效模式和效果分析)识 别出来的设计失效模式 •在应用之前分析工艺过程来减少废品 •应该是包括多个部门的小组工作 •失败模式根据优先顺序号码排列 •RPN优先顺序号码的排列=严重程度*发生频率 *查出原因机率 •所有优先顺序号码的排列,超过40便采用防错 设计减少到40以下