电机组装过程PFMEA分析表
FMEA 分析模板
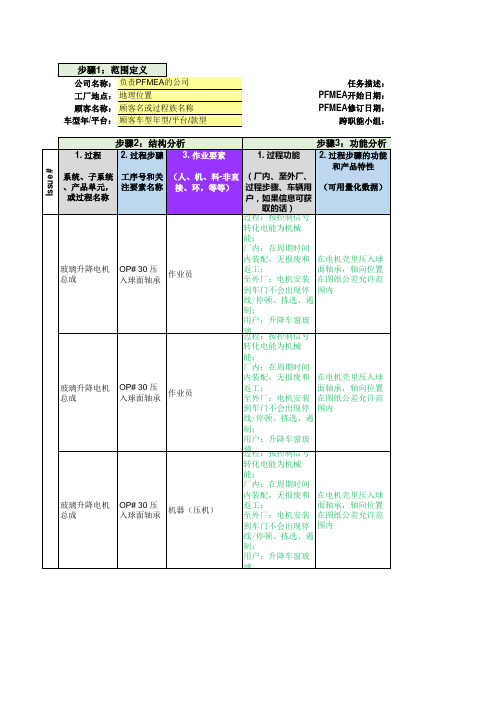
和产品特性
系统、子系统 工序号和关 (人、机、料-非直 (厂内、至外厂、
、产品单元, 注要素名称 接、环,等等) 过程步骤、车辆用 (可用量化数据)
或过程名称
户,如果信息可获
取的话) 过程:按控制信号
转化电能为机械
能;
厂内:在周期时间
内装配,无报废和 在电机壳里压入球
玻璃升降电机 总成
OP# 30 压 入球面轴承
制;
用户:升降车窗玻
璃
过程失效模式及影响分析 - PFMEA
PFMEA项目名称 PFMEA开始日期 最新修订日期 小组名单
:功能分析
3. 作业要素的功 能和过程特性
1. 失效影响 (FE)
(厂内、至外厂、过程步骤、 车辆用户,如果信息可获取的
话)
步骤4:失效分析
2. 过程步骤的失效模式 (FM)
3. 作业要素的失效原因 (FC)
据
进行 中
更新严重度 (S) 更新发生度 (O) 更新探测度 (D) 更新DFMEA AP
备注
持续改进
历史/变更授权 (如适用)
至外厂:无;
用户:车窗玻璃升降困难 (7)
手册(草案)中例子不清晰
8
轴承轴向位置没有达 到,间距过小
压机在还没压到位就停止 了(压力太小)
- PFMEA
PFMEA编号: 按公司内部规定 过程负责人: 即PFMEA负责人
保密等级: 例如:对外/机密/内部使用
当前针对FC的 预防性控制措施
(PC)
步骤5:PFMEA 风险分析
过程:机械能损失,因为球面
轴承与转子间摩擦过大,球面
作业员从料箱拿取 正确型号的清洁的 球面轴承,并放到 压机的上止位
BDM电机-PFMEA
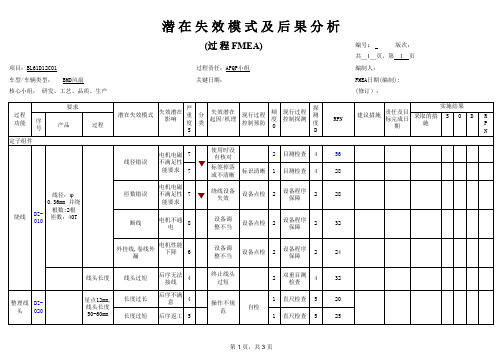
(过 程 FMEA)
项目:BL61D12C01 车型/车辆类型: BMD风扇 核心小组: 研发、工艺、品质、生产
过程责任:APQP小组 关键日期:
过程 功能 序
号 定子组件
要求
产品
过程
绕线
线径:φ
0.36mm 并绕
DZ010
根数:2根 匝数:40T
潜在失效模式
失效潜在 影响
严 重 度
冷装配, 且存在过
盈量
再次平缓 压装
1
检确认
7
42
操作不规 加强作业
范
培训
1 目测检查
4
28
操作不规 加强作业
范
培训
2 目测检查
2
28
第 2 页,共 3 页
压装支 ZC架 020
焊三相 ZC线 030
端盖压 含油轴
承
ZC040
转子组 件、前 ZC后端盖 050
铆合
装销钉
ZP 不满足性 7
设备点检
2
设备程序 保障
2
编号:
版次:
共__1__页,第__1__页
编制人:
FMEA日期(编制):
(修订):
实施结果
RPN
建议措施
责任及目 标完成日
采取的措
S
O
D
R
期
施
P
N
56 28
28
32
外挂线,卷线外 漏
电机性能 下降
6
设备调 整不当
设备点检
2
设备程序 保障
2
24
整理线 DZ头 020
线头长度
星点12mm, 线头长度 50-60mm
1、PFMEA表格(新版填写范例)
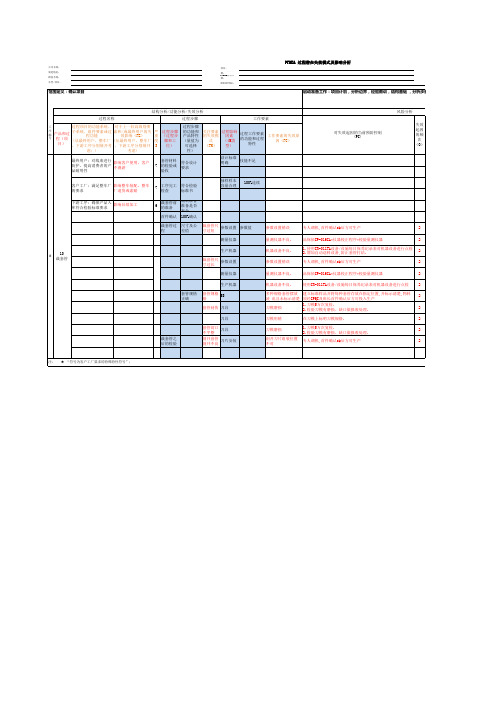
测量仪器
生产机器
裁套管尺 寸过长
参数设置
测量仪器
参数设置错误 量测仪器不良. 机器设备不良. 参数设置错误 量测仪器不良.
专人调机,首件确认ok后方可生产
2
品保依CP-016CA«仪器校正程序»校验量测仪器
2
1.使用CR-011FA设备/设施每日保养纪录表对机器设备进行点检 2.增加自动送料设备,防止套管打结.
式 (FM)
过程影响 因素 (4M类 型)
过程工作要素 的功能和过程
特性
工作要素的失效原 因(FC)
最终用户:对线束进行 防护,提高消费者的产 品耐用性
影响客户使用,客户 不漫游
套管材料 7 的检验或
验收
符合设计 要求
设计标准 明确
技能不足
对失效起因的当前预防控制 (PC)
风险分析
失效 起因 的频
次 (O)
客户工厂:满足整车厂 影响整车装配,整车
的要求
厂退货或索赔
7
工序完工 检查
符合检验 标准书
抽样样本 容量合理
100%连续
下游工序:确保产品入 库符合检验标准要求
影响后续加工
10 # 裁套管
6
裁套管前 的准备
首件确认
确认准备 准备是否 充分
100%确认
裁套管过 寸及公
程
差值
裁套管尺 寸过短
参数设置
参数值
教训,结构基础 ,分析步骤
PMEA编号: 过程职责: 保密级别:
版本号:
页 码:
第
页,共
页
编制者/日期:
批准/日期:
风险分析
改进措施
失效
起因/ 行动
PFMEA第五版表格
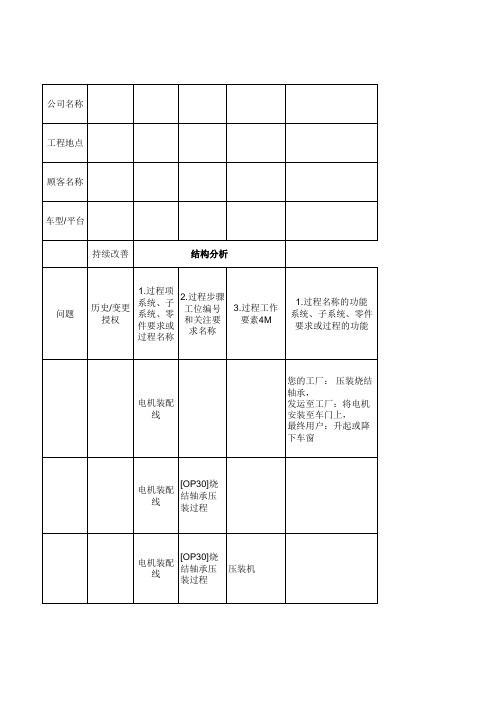
特殊特 性
筛选器 代码
预防措施
探措施
根据规范
MRKJ503
根据数据表调整力的大 小
5
8对电机性 能曲线进
2
M
行完全检
测
带位置控 制传感器 的选择性
压装
带压力监 测的选择 性压装
P
改进措施
责任人
目标完成 日期
状态: 尚未确认/ 决策/执行
已完成 不执行
采取基于 证据的措
施
完成日期
严 重 度
发 生 度
电机装配 线
[OP30]烧 结轴承压 装过程
电机装配 线
[OP30]烧 结轴承压 装过程
压装机
功能分析
项目 开始日期 修订日期 职能团队
失效分析
PFMEA
2.过程步骤的功能 3.过程工作要 1.对于上一较高级别要素和
和产品特性 素的功能和 I或最终用户的失效影响(
(量值为可选项) 过程特性
FE)
不能实现 烧结轴承 的轴向定 位
机器将烧结 轴承压入电 机壳,实现 轴向定位
设备在达 到最终位 置前停止
PFMEA
系统/子系 统/组件/部
件
DFMEA编 号
设计职责
保密等级
风险分析
当前的对失效起因的预 防措施( PC)
频 度 (0 )
FC /FM 的当前探
测措施 (DC)
FC
/F
M 的 AP(行 探 动优先 测 级) 度 (
公司名称
工程地点
顾客名称
车型/平台 持续改善
结构分析
功能分析
问题
历史/变更 授权
1.过程项 系统、子 系统、零 件要求或 过程名称
整车总装过程pfmea分析
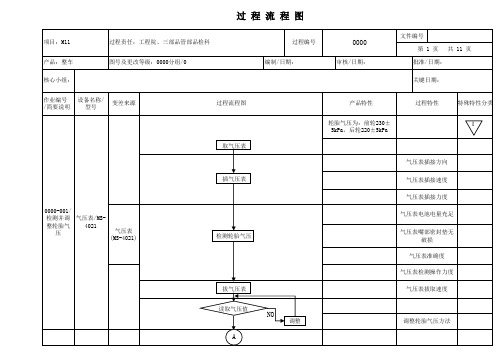
0000
审核/日期:
文件编号 M16-8092-7008 第 6 页 共 11 页
批准/日期:
核心小组:
关键日期:
作业编号 /简要说明
设备名称/ 型号
变差来源
0000-004/ 检测并调 整四轮定
位
0000-005/ 检测前照
灯灯光
大灯检测仪 /X-light
大灯检测 仪/Xlight
环境
过程流程图
长城标
检BCDCB验DA A 过 程NO流 程 图
项目:M11 产品:整车 核心小组:
过程责任:工程院、三部品管部品检科 图号及更改等级:0000分组/0
过程编号 编制/日期:
0000
审核/日期:
文件编号 第 1 页 共 11 页
批准/日期:
关键日期:
作业编号 /简要说明
设备名称/ 型号
变差来源
0000-001/
E
打印检测数据 车辆驶离
检测前照灯灯
F
NO
调整
NO
产品特性
过程特性
特殊特性分类
打印数据清晰
远光灯发光强度 水平偏差、垂直偏差 前照灯基准中心高度H
车速 车辆定位 前照灯距检测镜面距
离 设备开关、按钮
镜面清洁度 显示器
灯光检测顺序 检测方法
前照灯检测仪准确度 调整方法
环境温度5-40度,空 气湿度0-90%
检测整车侧滑量
0000-007/ 安装转向 定扭力扳手 定扭力扳 盘六角法 /100N•m 手/100N•m 兰面螺母
安装转向盘六角法兰面螺母
G
0000
审核/日期:
产品特性
文件编号 M16-8092-7008 第 7 页 共 11 页
pfmea分析表
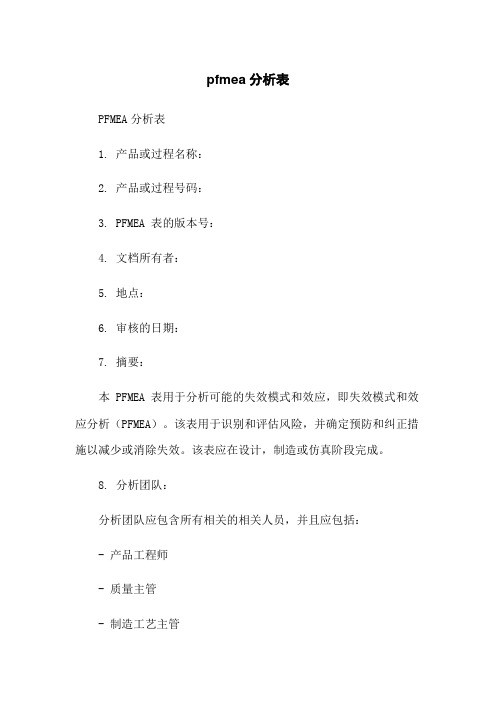
pfmea分析表PFMEA分析表1. 产品或过程名称:2. 产品或过程号码:3. PFMEA 表的版本号:4. 文档所有者:5. 地点:6. 审核的日期:7. 摘要:本 PFMEA 表用于分析可能的失效模式和效应,即失效模式和效应分析(PFMEA)。
该表用于识别和评估风险,并确定预防和纠正措施以减少或消除失效。
该表应在设计,制造或仿真阶段完成。
8. 分析团队:分析团队应包含所有相关的相关人员,并且应包括:- 产品工程师- 质量主管- 制造工艺主管- 安全主管- 故障分析师- 设计负责人- 制造工程师- 客户服务代表9. 步骤:步骤1:识别过程、组件或子组件- 识别过程、组件或子组件,该过程对产品性能,质量和可靠性的影响最大- 如果有多个过程,组件或子组件,请在单独的表中进行分析步骤2:确定失效模式- 对于每个识别的过程、组件或子组件,列出可能的失效模式步骤3:确定失效效应- 确定每种失效模式的影响,包括可能导致的产品或过程故障、风险和/或安全问题步骤4:确定失效严重性(S)- 确定失效对于产品功能和可靠性的影响严重性级别为S步骤5:确定失效发生概率(O)- 确定失效的发生概率级别为O步骤6:确定失效检出度(D)- 确定失效的检出度级别为D步骤7:计算风险优先级数(RPN)- 计算风险优先级数(RPN),即 RPN = S × O × D步骤8:制定预防和纠正措施- 针对高优先级数(RPN)的失效模式制定预防和纠正措施步骤9:跟踪措施有效性- 跟踪预防和纠正措施的实施,以确保其有效性。
10. 列举本文档所涉及简要注释如下:- 失效模式和效应分析(PFMEA):用于确定可能的失效模式和效应并采取纠正措施的过程。
- 风险优先级数(RPN): PFMEA 表中计算风险的指标。
RPN = S × O × D。
11. 列举如下本文档所涉及的法律名词及注释:无总结本文介绍了 PFMEA 分析表,该表用于识别和评估风险,并确定预防和纠正措施以减少或消除失效。
PFMEA表格(第四版)

措施结果action results R P N
必备条件 requirement
S
O
D
潜在失效模式及后果分析表(PFMEA) RE MODE AND EFFECTS ANALYSIS(PROCESS FMEA)
系统item: 子系统/部件model year(S)/program(s): 核心小组 core team:
级别 classification 项目 process step 功能 function 严重度Severity 潜在失效模式 potential failure mode 潜在失效的后 果potential effect(s) failure 现行过程current process 潜在失效的 起因/机理 频 potential cause(S) 现行过程预防控制 度 现行过程探测控制 controls of failure 数 controls detection prevention 0
FMEA编号 : 过程责任process responsibility 关键日期key date 页码 第 页,共 页 编制人 prepared by: PFMEA 日期(版本) date(Orig)
风险 建议 顺序 措施 探 测 数 recommended action 度 RPN D
责任和目 标完成日 措施实 期 responsibili 施描述 ty&target 及完成 completion 日期
制程PFMEA分析表格
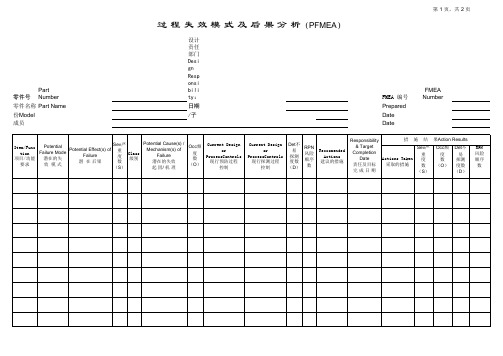
Occ频 度 数
(O)
Current Design or
ProcessControls 现行预防过程 控制
Current Design or
ProcessControls 现行探测过程 控制
Det不
易 探测 度数 (D)
RPN 风险 顺序 数
Reccomended Actions
建议的措施
Responsibility
措 施 结 果Action Results
& Target Completion
Date 责任及目标 完成日期
Actions Taken 采取的措施
Sev严 重 度 数
(S)
Occ频 度 数
(O)
Det不 易 探测 度数
(D)
RPN 风险 顺序
数
Part 零件号 Number
建议的措施
Responsibility
措 施 结 果Action Results
& Target Completion
Date 责任及目标 完成日期
Actions Taken 采取的措施
Sev严 重 度 数
(S)
Occ频 度 数
(O)
Det不 易 探测 度数
(D)
RPN 风险 顺序
数
FMEA Number
Item/Func tion
项目/功能 要求
Potential
Failure Mode 潜在的失 效 模式
Sev严
Potential Effect(s) of Failure
潜 在 后果
重 度 数
Class 级别
PFMEA分析范例

PFMEA分析范例1. 引言PFMEA(Process Failure Mode and Effects Analysis)是一种常用的质量管理工具,用于识别和评估制造过程中存在的潜在故障模式及其对产品质量的影响。
本文将通过一个实例来展示PFMEA分析的过程和方法。
2. 实例描述假设我们正在开发一种新型电动汽车电池组装工艺,并希望通过PFMEA分析来发现潜在的故障模式并采取相应的措施预防。
3. PFMEA步骤3.1 选择分析范围首先,我们需要确定要分析的工艺范围。
在本例中,我们选择了电动汽车电池组装工艺中的关键步骤:电池包装、电池连接和充电检测。
3.2 收集工艺信息接下来,我们收集与每个工艺步骤相关的信息,包括工艺流程、设备、材料和人员等。
针对电池包装步骤,我们列出了以下信息: - 工艺流程:电芯装载、包装封装- 设备:电芯装载机、包装机- 材料:电芯、包装材料- 人员:操作工、质检员3.3 识别故障模式在此步骤中,我们识别潜在的故障模式,即制造过程中可能发生的问题。
针对电池包装步骤,我们列出了以下故障模式: - 电芯装载不准确- 包装封装不牢固3.4 评估故障影响在此步骤中,我们评估每个故障模式对产品质量的影响程度。
针对电芯装载不准确这一故障模式,我们评估了以下影响: - 电池运行时间缩短- 电池性能下降3.5 评估故障原因在此步骤中,我们分析导致每个故障模式出现的可能原因。
针对电芯装载不准确这一故障模式,可能的原因包括:- 操作工技能不熟练- 设备故障3.6 识别和实施控制措施在此步骤中,我们确定并实施控制措施以防止故障模式的发生。
针对电芯装载不准确这一故障模式,可能的控制措施包括: - 培训操作工,提高技能水平- 定期维护设备,确保其正常运行3.7 重新评估和更新PFMEA最后,我们重新评估已实施的控制措施并更新PFMEA表格。
如果控制措施有效,我们将确认问题得到了解决。
如果问题仍存在,我们需要重新评估并采取进一步的纠正措施。
PFMEA_PWB装配分析案例
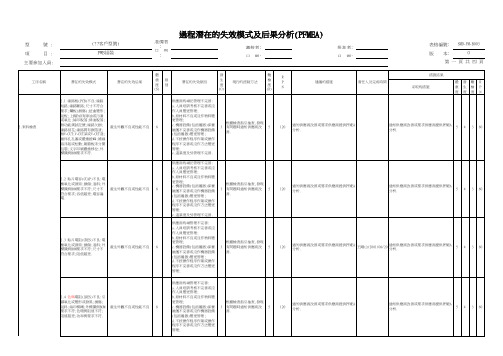
產生外觀不良或性能不良
8
3
根據檢查指引抽查,發現 有問題時通知供應商改 善.
3
根據檢查指引抽查,發現 有問題時通知供應商改 善.
5
120
通知供應商改善或要求供應商提供PFMEA 分析.
通知供應商改善或要求供應商提供PFMEA 分析.
5
4
3
60
2.2 貼片電容(CCAP)不良:電 極氧化或發黑;損傷;混料;外 標識與BOM要求不符;尺寸不 符合要求;容值超差;電容漏 電.
產生外觀不良或性能不良
產生外觀不良或性能不良
8
供應商的4M管理不完善: a.人員培訓考核不完善或沒 作人員變更管理; b.或原材料不良或沒作物料 變更管理; c.或機器設備(包括儀器)保 養維護不完善或沒作機器設 備(包括儀器)變更管理; d.或不按操作程序作業或操 作程序不完善或沒作方法變 更管理; 供應商的4M管理不完善: a.人員培訓考核不完善或沒 作人員變更管理; b.原材料不良或沒作物料變 更管理; c.機器設備(包括儀器)保養 維護不完善或沒作機器設備 (包括儀器)變更管理; d.不按操作程序作業或操作 程序不完善或沒作方法變更 管理; 供應商的4M管理不完善: a.人員培訓考核不完善或沒 作人員變更管理; b.或原材料不良或沒作物料 變更管理; c.或機器設備(包括儀器)保 養維護不完善或沒作機器設 備(包括儀器)變更管理; d.或不按操作程序作業或操 作程序不完善或沒作方法變 更管理; 供應商的4M管理不完善: a.人員培訓考核不完善或沒 作人員變更管理; b.或原材料不良或沒作物料 變更管理; c.或機器設備(包括儀器)保 養維護不完善或沒作機器設 備(包括儀器)變更管理; d.或不按操作程序作業或操 作程序不完善或沒作方法變 更管理; 供應商的4M管理不完善: a.人員培訓考核不完善或沒 作人員變更管理; b.或原材料不良或沒作物料 變更管理; c.或機器設備(包括儀器)保 養維護不完善或沒作機器設 備(包括儀器)變更管理; d.或不按操作程序作業或操 作程序不完善或沒作方法變 更管理;
3-1 PFMEA 表格-P16

探测措施
失效起因的频度(O)
过程FMEA措施优先级 特殊特性
筛选器代码(可选) 预防措施
负责人姓名 目标完成日期
状态 采取基于证据的措施
完成日期 (S)严重度 (O)发生度 (D) 探测度 特殊特性 措施优先级
备注
PFMEA 优化(步骤六)
过程失效模式及影响分析(PFMEA)表格
过程 FMEA 风险分析 (步骤五)
压装机
过程失效模式及影响分析(PFMEA)表格
功能分析 (步骤三)
1. 过程项的功能系统、 子系统、零件要素或过程 的功能
2. 过程步骤的功能和产 品特性(量值为可选)
3. 过程工作要素的功能 和过程特性
您的工厂:
运至工厂: 最终用户:
过程失效模式及影响分析(PFMEA)表格
功能分析 (步骤三)
最终用户:
升起和降下车窗
过程失效模式及影响分析(PFMEA)表格
失效分析(步骤四)
1.对于上一较高级别要素和/或最终用户 的失效影响(FE)
2.关注要素的失效模式(FM) 3.工作要素的失效原因(FC)
1.失效影响
2.过程步骤的失效模式 3.工作要素的失效原因(FC)
您的工厂: 发运至工厂: 最终用户:
1. 过程项的功能系统、 子系统、零件要素或过程 的功能
2. 过程步骤的功能和产 品特性(量值为可选)
3. 过程工作要素的功能 和过程特性
您的工厂:
将轴安装至电机壳总成内 发运至工厂: 将电机安装至车门上
压装烧结轴承,在每次压 装时实现 电机壳内的轴 向定位保留最大间隙
机器将烧结轴承压入电机 壳,实现轴向定位
PFMEAID编号:
顾客名称:
23、PFMEA检查使用表

项目预备过程流程图表头描绘 / 目的故障模式故障结果故障原由 /机理P F M E A 检查表问题Yes No ●组织了 PFMEA 小组● 背景资料已检查● 准备了过程流程图● 在每道工序产生了部件特征或评定● 每道工序过程特征列出了● 进货资源的变差明确● 填好●每道工序的目的或功能列出了● 目的或功能可胸怀● 能否利用“什么使部件被拒收”的原则列出全部的故障模式●假如某一部件特征高出技术规范会造成拒收,故障模式中能否列出这些制造工序的部件特征● 故障模式中能否包含检测工序的故障,即接受坏部件拒收好部件● 假如故障模式对后边的工序有不利影响,● —该故障模式是不是下游工序的故障原由● —下游故障模式能否可辨别● 能否考虑了对机器、工厂员工以及最后用户潜伏的危害成效● 故障模式成效的描绘能否考虑了下述各项:● —本工序、下一工序、后来工序● —直接顾客(制造或装置厂)最后顾客● —车辆● —政府法例● 过程中可能犯错的细节能否明确● 可能致使犯错的特征能否可确立或控制● 能否考虑了过程特征● 能否考虑了设计缺点● 能否考虑了每步工序进入的资料和部件● 能否考虑了操作者的要素项目当前采纳的过程控制严重度数频度数探测度数分类风险次序数建议举措追踪问题Yes No ● 将要采纳的控制能否用于检测坏部件●控制能否在部件走开加工/ 组装厂前检测出坏部件● 控制是用于检测或是用于预防能否明确● 能否依据故障模式的最严重结果打分顾客结果打分与设计FMEA 中的打分能否一致● 该频度数能否考虑了预防控制可减少某个故障模式发生的能力● 该探测度数能否依据当前采纳的控制方法,在部件走开制造或装置工位前检出某一故障模式的能力确立● 特别特征及其控制能否明确● 临界特征能否用规定的符号注明● 特别特征能否作为过程(或部件)特征注明● 特别特征及其控制能否已通知责任设计师●风险次序数( RPN)摆列能否由高到低摆列● 过程举措能否考虑了降低临界特征的临界值●特别加工 / 装置控制能否明确用于特别特征● 能否考虑了全部的特别特征●能否考虑了纠正举措以降低列最高位的故障模式的RPN值● 建议举措的责任和达成日期能否列出● 能否在适合的地点标出预防(而不是检测)举措●能否考虑在适合的状况下采纳了除去/ 减少故障模式的潜伏危害发生的举措● RPN 序号能否由高到低摆列。
PFMEA分析表
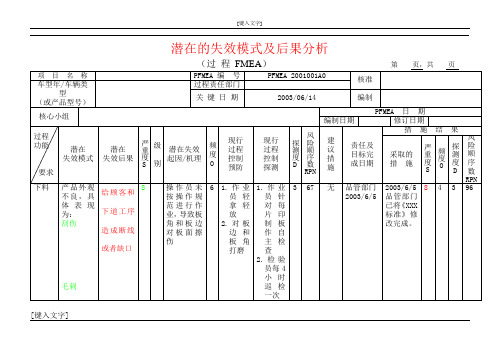
120
无
PP-705-2-01A0
XXX 有 限 公 司
过 程 F M E A 检 查 表
制定部门: 制定日期: 年 月 日
产品名称
规格/型号
顾客零件编号
问 题
是
否
所要求的意见 / 措施
负责部门/负责人
完成日期
1
是否使用克莱斯勒、福特和通用汽车公司的指南制定过程ห้องสมุดไป่ตู้MEA
2
所有影响配合、功能、耐久性、政府法规和安全性的操作是否已被识别并按顺序列出
潜在的失效模式及后果分析
(过程FMEA)第页,共页
项 目 名 称
PFMEA 编 号
PFMEA2001001A0
核准
车型年/车辆类型
(或产品型号)
过程责任部门
关 键 日 期
2003/06/14
编制
核心小组
PFMEA 日 期
编制日期
修订日期
过程
功能
要求
潜在
失效模式
潜在
失效后果
严
重
度
S
级
别
潜在失效
起因/机理
频
度
O
现行
过程
控制
预防
现行
过程
控制
探测
探测
度
D
风险
顺序
数RPN
建 议
措 施
责任及
目标完
成日期
措 施 结 果
采取的
措 施
严
重
度
S
频
度
O
探测
度
D
风险
顺序数
RPN
下料
产品外观不良,具体表现为:
PFMEA检查表

● 该频度数是否考虑了预防控制可减少某个故障模式发生的能力
探测度数
● 该探测度数是否根据目前采用的控制方法,在零件离开制造或装配工
位前检出某一故障模式的能力确定
分类
● 特殊特性及其控制是否明确
● 临界特性是否用规定的符号标明
● 特殊特性是否作为过程(或零件)特性标明
● 特殊特性及其控制是否已通知责任设计师
故障后果
● 是否考虑了对机器、工厂职工以及最终用户潜在的危害效果
● 故障模式效果的描述是否考虑了下述各项:
● — 本工序、下一工序、其后工序
● — 直接顾客(制造或装配厂)最终顾客
● — 车辆
● — 政府法规
故障原因/
机理
● 程中可能出错的细节是否明确
● 可能导致出错的特性是否可确定或控制
● 是否考虑了过程特性
风险顺序数
● 风险顺序数(RPN)排列是否由高到低排列
建议措施
● 过程措施是否考虑了降低临界特性的临界值
● 特殊加工/装配控制是否明确用于特殊特性
● 是否考虑了所有的特殊特性
● 是否考虑了纠正措施以降低列最高位的故障模式的RPN值
● 建议措施的责任和完成日期是否列出
● 是否在适当的位置标出预防(而不是检测)措施
23、PFMEA检查表(通用)(共2页)
PFMEA检查表
项目
问题
Yes
No
预 备
● 组织了PFMEA小组
● 背景资料已检查
过程
流程图
● 准备了过程流程图
● 在每道工序产生了零件特性或评定
● 每道工序过程特性列出了
● 进货资源的变差明确
表 头
● 填好
PFMEA分析表

(过 程 FMEA)第 页,共 页
项 目 名 称
PFMEA 编 号
PFMEA2001001A0
核准
车型年/车辆类型
(或产品型号)
过程责任部门
关 键 日 期
2003/06/14
编制
核心小组
PFMEA 日 期
编制日期
修订日期
过程
功能
要求
潜在
失效模式
潜在
失效后果
严
重
度
S
级
别
潜在失效
起因/机理
频
度
O
现行
过程
控制
预防
现行
过程
控制
探测
探测
度
D
风险
顺序
数RPN
建 议
措 施
责任及Leabharlann 目标完成日期措 施 结 果
采取的
措 施
严
重
度
S
频
度
O
探测
度
D
风险
顺序数
RPN
下料
产品外观不良,具体表现为:
刮伤
毛刺
给顾客和下道工序造成断线或者缺口
8
操作员未按操作规范进行作业,导致板角和板边对板面擦伤
6
1.作业员轻拿轻放
3
是否考虑了类似零件的FMEA?
4
是否对已发生事件和保修数据进行了评审?
5
对高风险顺序数的项目是否已计划并采取了适当的纠正措施?
6
对严重度数高的项目是否已计划并采取了适当的纠正措施?
7
当纠正措施完成后,风险顺序数是否作了修改?
8
当完成设计更改时,是否修改了高严重度数?
制程PFMEA分析表格

第 1 页,共 1 页
FMEA 编号 FMEA Number 编制Prepared by: 编制日期Date (Orig.): 修订日期Date (Rev.):
Item/Func tion
项目/功能 要求
Potential
Failure Mode 潜在的失 效 模式
Sev严
Potential Effect(s) of Failure
Sev严 重 度 数
(S)
Occ频 度 数
(O)
Det不 易Βιβλιοθήκη 探测 度数(D)RPN 风险 顺序
数
潜 在 后果
重 度 数
Class 级别
(S)
Potential Cause(s) / Mechanism(s) of
Failure 潜在的失效 起 因/ 机 理
Occ频 度 数
(O)
Current Design or
ProcessControls 现行预防过程 控制
Current Design or
零件号 Part Number 零件名称 Part Name 车型/年份Model Year(s)/Vehicle(s) 核心小组成员Core Team Member
过 程 失 效 模 式 及 后 果 分 析(PFMEA)
设计责任部门Design Responsibility: 关键日期Key Date: 系统/子系统/部件System/Subsystem/Component
ProcessControls 现行探测过程 控制
Det不 易 探测 度数
(D)
RPN 风险 顺序 数
Reccomended Actions
建议的措施
Responsibility
PFMEA表格汇总

D
7-10 5-6 2-4
1 7-10 5-6 2-4
1 7-10 5-6 2-4
1 7-10 5-6 2-4
1
措施优先级 AP
H H H H H H H H H H H M H M L L
备注
非常低 非常高
1 8-10
高
6-7
对产品或工厂的 7-8
影响高
中
4-5
对产品或工厂的 4-6
影响中等
低 非常低 非常高
生产线没有停工
缺陷产品会触发重大应对计划的启
100%的产品可能需要在工位上返
外观、声音、震动、粗糙度或触感
4
动;可能不会出现额外的瑕疵产品,
工后才能继续加工
令人感觉非常不舒服。
不需要分拣
缺陷产品会触发次要应对计划的启
部分产品可能需要在工位上返工后
外观、声音、震动、粗糙度或触感
3
动;可能不会出现额外的缺陷产品,
测量可重复性和再现性结果可
5
的半自动化方式),或使用可以探测失效模式或失效
以接受)。
起因的检验设备,例如坐标测量机。
以设备为基础的自动化探测方法,其可以在下游探测
到失效模式,进而避免进一步加工、或系统可以识别
4
已经过实践证明为有效和可靠 差异产品,并允许其在过程中自动前进,直至到达指
的系统(例如工厂在关于相同 定的不合格品卸载去。差异产品将在一个有效的系统
技术控制
预防控制
没有预防控制 预防控制在防止失效起因出现的方面起
到的作用很小。 预防控制在防止失效起因出现的方面可
以起到一定的作用。 预防控制在防止失效起因出现的方面可
以起到有效的作用。
PWB组装PFMEA分析
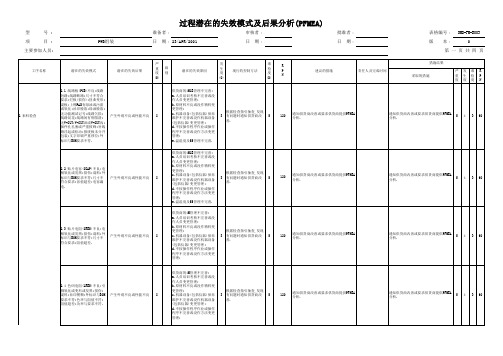
现行的控制方法
检 度
(O)
(D)
R P N
建议的措施
责任人及完成时间
措施结果 采取的措施
严发难 R 重生检 P 度度度 N
2.1 线路板(PCB)不良:线路
短路;线路断路;尺寸不符合
要求;烂板(损伤);扭曲变形;
混板;上锡PAD有绿油或污渍
或氧化;丝印脱落;绿油脱落;
无功能测试记号;线路欠损; 线路刮花;线路间有铜箔渣;
根据检查指引抽查,发现 3 有问题时通知供货商改 5
善.
120
通知供货商改善或要求供货商提供PFMEA 分析.
120
通知供货商改善或要求供货商提供PFMEA 分析.
通知供货商改善或要求供货商提供PFMEA 分析.
5
4
3 60
通知供货商改善或要求供货商提供PFMEA 分析.
5
4
3 60
2.4 色码电阻(LRES)不良:引 脚氧化或变形或发黑;损伤; 混料;丝印模糊;外标识与BOM 产生外观不良或性能不良 8 要求不符;色环与阻值不符; 阻值超差;功率与要求不符.
型
号:
项
目:
主要参加人员:
PWB组装
过程潜在的失效模式及后果分析(PFMEA)
准备者﹕
审核者﹕
日 期﹕ 23/APR/2001
日 期﹕
批准者﹕ 日 期﹕
表格编号﹕ SMD-FM-B003
版 本﹕
0
第一页共四页
工序名称 2.来料检查
潜在的失效模式
潜在的失效后果
严 重级 度别 (S)
潜在的失效原因
发
难
生 度
善.
供货商的4M1E管理不完善: a.人员培训考核不完善或没 作人员变更管理; b.原材料不良或没作物料变 更管理; c.机器设备(包括仪器)保养 维护不完善或没作机器设备 (包括仪器)变更管理; d.不按操作程序作业或操作 程序不完善或没作方法变更 管理; e.温湿度及5S管理不完善.
- 1、下载文档前请自行甄别文档内容的完整性,平台不提供额外的编辑、内容补充、找答案等附加服务。
- 2、"仅部分预览"的文档,不可在线预览部分如存在完整性等问题,可反馈申请退款(可完整预览的文档不适用该条件!)。
- 3、如文档侵犯您的权益,请联系客服反馈,我们会尽快为您处理(人工客服工作时间:9:00-18:30)。
频 度 (O)
现行过程控制 预防
现行过程探测
探测 度 (D)
R P N
责任人和 建议的措施 预期完成 检验文件依据
日期
措施执行结果
采取的措施
R SODP
N
放珠垫
漏放或多 放
产生噪音
3
员工工作疏 忽
2
员工自检和巡 由噪音测试岗
检员抽检
位检测
2
12
/
1.工序首检记
/
录 2.车间巡检
/
3 2 2 12
记录
定子入机 壳
刮断漆包 线
电机断路
员工没按工 6 艺要求进行
操作
2
加强员工增培 由自动检测线
训
进行检测
1
12
/
/
自动检测线数 据
/
6 2 1 12
电机过自 动检测线
漏检/误判
影响电机 性能
生产设备 维护修理
所使用的 润滑油残 留
污染产品 外观
5
自动检测线 故障
6 工人疏忽
2
员工发现生产 线异常及时报 告
录
5.虫鼠等防治
控制记录
过程潜在失效模式及后果分析(PFMEA)
PFMEA编号:
项目:电机组装
过程责任:电机部
共1页,第 1 页
类别或产品型号:
关键日期:2016-5-26
PFMEA日期(编制)2017-5-26 修订:2017-7-4
核心小组
工序功能/ 要求
潜在的失 效模式
严 潜在的失 重
效后果 度 (S)
潜在的失效 起因/机理
品中
工人身上 异物污染 产品
影响到产 品的清洁 状况,影 响接触者 (包括使 用者)的
健康
6
1.工人长头发 没戴工作帽 2.员工没做好 个人卫生 3.私人物品没 按规定存放
4
1.包装车间员 工戴帽工作 2.长头发需盘 起,保持个人 清洁卫生 3.私人物品不 带入工作区
1.检查工人的 着装佩戴 2.检查工人的 卫生注意事项 3.检查私人物 品安全存放
无法精准 的测量不
良点
1.工具校正后
使用不当出
现错误
1.建立工具保 1.核查设备校
5
2.工具校正误 差太大,不
3
养维护制度 正清单 2.培训正确使 2.考核设备使
适用
用工具
校正清单更 新 2.设备使用 75 维护培训考 核 3.设备编号 特定授权管 理
员工装饰 物、头发 掉落到产
计划并实际实
施
5
4. 所有车间、
QC检验测试工
具设备必须按
要求送第三方
3
5 75
年度校正,保
留校正记录、
报告
5. 所有车间、
QC检验测试工
具必须按规定
收发、存储、
保养
1.个人卫生状 况记录表 2.QC 检验记 录表
1.员工工作帽 佩戴检查 2.检查员工的 上班卫生状况 3.确保清洁生 产
6 4 3 72
3
1.员工工作
帽佩戴检查
2.员工的穿
72
着卫生再上 班
3.固定安全
存放私人物
品
1. 制定工具设
备台账清单
2. 所有检验测
试工具设备管
理程序制度文
件及实施,受
控发行
3. 制定更新检
验测试工具设
1.工具设备清 单 2.设备校正计 划表 3.设备校正报 告 4.工具维修保 养记录
备清单,工具
编号正确使
用,制定校正
1.制定异物 控制程序制
度, 90 2.记录利器
、玻璃、微 生物管理、
监督
1. 制定利器管
制规定
1.利器清单 2. 对利器的领
2.利器收发记 用、发放进行
录
记录
3.玻璃易碎品 3. 管理人员巡
清单
查是否有落实 6 3 3 54
4.玻璃易碎品 4.制作玻璃易
核查记录
碎品清单以及
5.虫鼠防治记 核查记录
利器、玻
璃、微生
物害虫、 外来物品
异物污染
掉落到成
品中
造成不明 物体、脏 污物混入 产品中, 导致生产 产品部件
污染
1.利器、玻璃 1.利器、易碎 1.监督异物控
易碎品微生
品、微生物监 制程序执行
6 物管控不良 3 控管理
2.检查利器玻 5
2.外来物品管 2.记录异物控 璃微生物的控
控不良
制过程
制记录
OQC抽检成 品
1
3 目视检测
设备维护人员
按设备维护修 理的程序完成
2
作业
10
/
1.设备人员
36
做自检检查. 2.使用部门
班长使用前
1.工序首检记
/
录 2.车间巡检
/
5 2 1 10
记录
1.设备人员做
设备操作规程
自检检查. 2.使用部门班
6 3 2 36
长使用前确认
检测工具 检测设备 、设备 校正错误