PWB组装PFMEA分析案例
pfmea过程潜在失效模式及后果分析案例(从原材料-加工-出货整套案例分析)

1、注射压力大 2、锁模力不够 3.模具分型面有异物
4 调节注射压力 作业准备验证,适当调
整,并进行工艺监控 清理模具分型面
产品不合格
2
C 4.塑料温度太高
调节 56
5
制品质量符合 要求
气泡
1.原料含水分、溶剂或 易挥发物
3
原料检验
2.塑料温度太高或受热 时间长,易降聚或分解
标签贴错 漏检 纸箱受潮变形 数量不准确
产品型号错
误,顾客不满 2
意
不良品混入, 影响客户使用
5
纸箱变形破损 3
顾客不满意
1
C 包装人员粗心 C 检验人员操作失误 C 纸箱堆积太高 C 仓库计数错误
3 检查、更正 3 检验、及时标记 3 检查、更正 3 检查、更正
2 42
1 21
3 18 4 60 3 27 26
3.注射压力太小
调节注射压力
4.注射柱塞退回太早 产品不合格 7 A
5.模具温度太低
调节注射温度
6.注射速度快
调节注射速度
2 42
7.在料筒加料端混入空 气
6
制品质量符合 要求
凹痕、缩水
产品不合格 7
1、流道浇口太小
4
2、塑料件太厚或厚薄 不均
3、浇口位置不当
4、注射保压时间太短 A 5、加料量不夠
过程潜在失效模式及后果分析 (PFMEA)
类型/部件: 车型年:
核心小组:
设计责任: 关键日期:
RPN DETECT
OCCUR CLASS SEV
项目
设计功能/要 求
潜在失效模式
潜在失效后果
1 原材料采购 原材料不合格
装配过程 PFMEA实例(中英文)

80
CPK requirement on shaft OD對轉子內徑要求CPK
130
1
Pulley Press壓皮帶輪
Wrong Assembly Dimension組裝尺寸錯誤
Not Meet Customer Unit和客戶的部件不相配
8
Wrong Machine Setup
機器設定錯誤
2
100% Visual Check目視全檢
壓軸承
Distance Between 2 Bearings too Long
両軸承間距太長
1)No Axial Play沒有軸向遊隙
2) Motor Not Meet Performance Spec電機不符合性能要求
3) Noise / Vibration噪音/振動
5
6
8
Wrong Machine Setup
Broken Magnet磁環破裂
1) Noise / Vibration噪音/振動
2) Motor Not Meet Performance Spec電機不符合性能要求
8
6
Wrong Machine Setup
機器設定錯誤
2
Visual Check 100%目視全檢
Check setup 1time/day or before re-supply每天一次檢查設定或換型時
2
3
32
48
110
1
Rotor Coin轉子上壓環形痕
No Coin沒有環形痕
Loose coin壓環太鬆
Noise/Vibration噪音/振動
Inoperable motor電機無法動作
新版PFMEA案例

新版PFMEA案例
过程失
面无锈蚀、磕碰
、划痕
清洗洁度,机体安装
后,能够降低发动
机产生异响的概率
过程失效模式及后果分析(PFMEA)
2.每季度对维护保养计划的执行情况进行检查确认。
3.每月度对清洗剂的更换频次进行检查确认。
量异常;
对最终用户影响:无
点;
料:清洗剂不能满足除污、防锈要求,清洗剂过期,未得到监控法:超声波清洗机内的液体未及时更换,液体变质:
进行维护保养;3.确定清洗剂液体更换周期,并明确在作业标准中。
对机体表面100%检查针对失效起因:
1.每半年对人员的能力评影响交付或交付后顾客投诉;
对主机厂影响:表面存在锈斑、有磕碰点和划痕人员取放工件
时与传输带表面碰撞;
机:传输带长时间训,提高质量意识。
2.制定维护保养
措施。
六步法pfmea案例

六步法pfmea案例全文共四篇示例,供读者参考第一篇示例:案例背景:某家汽车零部件制造公司在生产过程中发现了一个频繁出现的问题:某零部件的尺寸偏差过大,导致装配时无法完全契合,进而影响产品的性能和质量。
为了解决这一问题,公司决定使用六步法PFMEA 进行分析和改进。
步骤一:确定分析范围团队确定了分析的范围为某零部件的生产工艺。
他们明确了问题的具体表现,以及对产品性能和质量的影响。
团队还确定了分析的目的是为了找出可能引起零部件尺寸偏差的潜在故障模式,并制定相应的控制措施。
步骤二:收集相关信息团队开始收集相关信息,包括零部件的设计图纸、生产工艺流程、设备参数、材料性质等。
他们还对生产现场进行实地考察,观察生产过程中的关键环节,并与相关工程师和操作人员进行沟通交流,了解他们对问题的认识和看法。
步骤三:识别潜在故障模式通过分析收集到的信息,团队识别出了可能导致零部件尺寸偏差的潜在故障模式。
包括:材料供应质量不稳定、设备操作不规范、工艺参数设置不当等。
每个故障模式都被赋予一个风险等级,以确定其重要性和优先级。
步骤四:确定故障影响团队分析每个故障模式的影响范围,包括对产品性能、质量、交付时间等方面的影响。
他们还评估了每个故障模式的可能性和频率,以确定其潜在风险。
步骤五:制定改进控制措施基于对故障模式和影响的分析,团队制定了一系列改进控制措施,以降低潜在风险。
加强材料供应商管理、优化生产工艺流程、规范设备操作规程等。
每个控制措施都被赋予一个责任人和执行时间表,以确保实施和落实。
步骤六:跟踪和持续改进团队制定了一个跟踪和持续改进计划,以监控改进控制措施的执行情况和效果。
他们定期对实施情况进行评估和审查,继续识别和解决可能存在的风险和问题,确保质量和性能的持续提升。
通过六步法PFMEA的分析和改进,该汽车零部件制造公司成功解决了零部件尺寸偏差的问题,提高了产品的质量和性能,降低了生产过程中的风险和损失,进一步提升了企业的竞争力和市场地位。
PFMEA分析案例

项目名称:F507 M31814002电源接插件支架核心小組:项目名称:F507 M31814002电源接插件支架车辆/年度:潜在失效模式及后Failure Mode and Ef(过程F吴为、易军林(技术部);张茂科、漆敏(品质部);谭红军、敖顺洲(生产车辆/年度:Failure Mode and Ef(过程F核心小組:项目名称:F507 M31814002电源接插件支架核心小組:吴为、易军林(技术部);张茂科、漆敏(品质部);谭红军、敖顺洲(生产车辆/年度:Failure Mode and Ef(过程F吴为、易军林(技术部);张茂科、漆敏(品质部);谭红军、敖顺洲(生产项目名称:F507 M31814002电源接插件支架核心小組:车辆/年度:Failure Mode and Ef(过程F吴为、易军林(技术部);张茂科、漆敏(品质部);谭红军、敖顺洲(生产项目名称:F507 M31814002电源接插件支架核心小組:车辆/年度:Failure Mode and Ef(过程F吴为、易军林(技术部);张茂科、漆敏(品质部);谭红军、敖顺洲(生产项目名称:F507 M31814002电源接插件支架核心小組:车辆/年度:Failure Mode and Ef(过程F吴为、易军林(技术部);张茂科、漆敏(品质部);谭红军、敖顺洲(生产47±0.2超差项目名称:F507 M31814002电源接插件支架核心小組:产品成型后尺Failure Mode and Ef(过程F吴为、易军林(技术部);张茂科、漆敏(品质部);谭红军、敖顺洲(生产车辆/年度:FMEA编号:过程责任部门:供销部、品质部关键日期:编制者:FMEA日期:FMEA编号:过程责任部门:生产部冲压二组关键日期:编制者:页码: 第 1 页 共 7 页2015.7.25张茂科式及后果分析d Effect Analasis 过程FMEA)CD/PFMLH-005(生产部);仲伟成(供销部)2015.7.252015.7.25张茂科d Effect Analasis 过程FMEA)CD/PFMLH-005页码: 第 2 页 共 7 页FMEA日期:FMEA编号:过程责任部门:生产部冲压二组关键日期:编制者:FMEA日期:(生产部);仲伟成(供销部)2015.7.25页码: 第 3 页 共 7 页2015.7.25张茂科d Effect Analasis 过程FMEA)CD/PFMLH-005(生产部);仲伟成(供销部)2015.7.25FMEA编号:过程责任部门:生产部加工组关键日期:编制者:FMEA日期:页码: 第 4 页 共 7 页2015.7.25张茂科d Effect Analasis 过程FMEA)CD/PFMLH-0052015.7.25(生产部);仲伟成(供销部)FMEA编号:过程责任部门:生产部冲压二组关键日期:编制者:FMEA日期:页码: 第 5 页 共 7 页2015.7.25张茂科d Effect Analasis 过程FMEA)CD/PFMLH-0052015.7.25(生产部);仲伟成(供销部)FMEA编号:过程责任部门:生产部冲压二组关键日期:编制者:FMEA日期:页码: 第 6 页 共 7 页2015.7.25张茂科d Effect Analasis 过程FMEA)CD/PFMLH-005(生产部);仲伟成(供销部)2015.7.25FMEA编号:过程责任部门:生产部加工组关键日期:编制者:FMEA日期:d Effect Analasis 过程FMEA)CD/PFMLH-005(生产部);仲伟成(供销部)2015.7.25页码: 第 7 页 共 7 页2015.7.25张茂科。
PFMEA分析范例
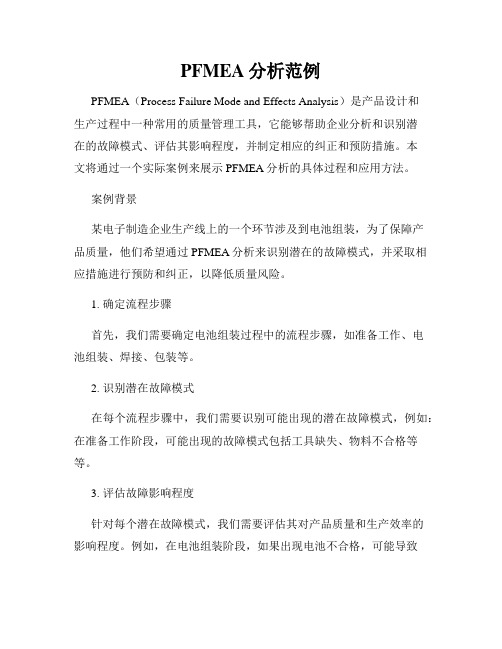
PFMEA分析范例PFMEA(Process Failure Mode and Effects Analysis)是产品设计和生产过程中一种常用的质量管理工具,它能够帮助企业分析和识别潜在的故障模式、评估其影响程度,并制定相应的纠正和预防措施。
本文将通过一个实际案例来展示PFMEA分析的具体过程和应用方法。
案例背景某电子制造企业生产线上的一个环节涉及到电池组装,为了保障产品质量,他们希望通过PFMEA分析来识别潜在的故障模式,并采取相应措施进行预防和纠正,以降低质量风险。
1. 确定流程步骤首先,我们需要确定电池组装过程中的流程步骤,如准备工作、电池组装、焊接、包装等。
2. 识别潜在故障模式在每个流程步骤中,我们需要识别可能出现的潜在故障模式,例如:在准备工作阶段,可能出现的故障模式包括工具缺失、物料不合格等等。
3. 评估故障影响程度针对每个潜在故障模式,我们需要评估其对产品质量和生产效率的影响程度。
例如,在电池组装阶段,如果出现电池不合格,可能导致产品连接不可靠,影响产品性能,同时还会增加后续检测和返工的工作量。
4. 确定风险等级结合故障模式的影响程度,我们可以根据一定的评估标准来确定每个故障模式的风险等级。
例如,可以设定高、中、低三个等级,将电池不合格列为高风险等级。
5. 制定预防和纠正措施对于高风险等级的故障模式,我们需要制定相应的预防和纠正措施,以降低潜在风险。
例如,对于电池不合格的风险,可以建立严格的供应商管理制度,提高物料检测的精度和效率。
6. 实施和跟踪制定好预防和纠正措施后,我们需要将其纳入到生产实践中,并建立相应的跟踪机制,及时评估其实施效果,并根据需要对措施进行调整和改进。
通过以上几个步骤的分析和实施,电子制造企业可以在电池组装过程中减少故障发生的概率,并及时采取纠正措施,以确保产品质量和生产效率的稳定性和可持续性。
总结PFMEA作为一种常用的质量管理工具,可以帮助企业在产品设计和生产过程中识别潜在故障模式,并制定相应的预防和纠正措施。
pfmea的案例

pfmea的案例哎哟喂,各位看官,今天咱们来摆一摆PFMEA(过程失效模式与影响分析)的案例。
咱们四川人说话直来直去,陕西朋友说话豪爽,再加上北京大哥的实在,咱们一起来把这个案例给讲明白了。
先说咱四川这边的例子。
咱们四川有个做电子产品的厂家,那厂里的生产线可是热火朝天。
有天,他们发现产品中的某个小零件老是出问题,导致整批产品都得返工。
这一下,工人们忙得团团转,老板也急得像热锅上的蚂蚁。
后来,他们用了PFMEA,把每个生产环节都仔细分析了一遍,最后发现是那个零件的供应商出了问题。
换了供应商之后,问题就迎刃而解了。
你看,这就是PFMEA的妙处,能帮我们找到问题的根源。
再说说陕西的例子。
咱们陕西的兄弟做事可是讲究个实在。
有个做机械加工的厂家,他们发现机器在加工过程中经常出现误差,导致产品质量不稳定。
他们用了PFMEA,从人、机、料、法、环、测六个方面进行分析,最后发现是操作工人的技能不够熟练。
于是,他们加强了对工人的培训,问题也就迎刃而解了。
你看,PFMEA不仅能找到问题,还能帮我们找到解决问题的方法。
最后说说北京的例子。
咱们北京的大哥做事可是有条不紊。
有个做食品的厂家,他们发现产品在储存过程中容易变质。
于是,他们用了PFMEA,对每个可能导致变质的因素都进行了详细的分析。
最后,他们发现是储存环境的温度控制不够精确。
于是,他们改进了温度控制系统,问题也就解决了。
你看,PFMEA就像是个指南针,能帮我们找到前进的方向。
这三个例子,虽然地方不同,但都用到了PFMEA这个方法。
它就像是个万金油,哪里有问题就往哪里抹一抹,问题就迎刃而解了。
所以呀,咱们在工作中,也得学会用这种方法,才能事半功倍,把工作做得更好。
仿真车玩具装配pfmea分析范例 (1)

发错货
产品退回
7
◇
仓管员不明要 求/仓管员粗心
3
1.相关资料及时发 放仓库人员
业务人员监柜
2
42
现行过程控制
预防
探测
探R 测P 度N
建议措施
措施结果
职责&目标 完成日期 采取措施及 生效日期
严发探 重生测 度率度
R P N
成品入库
存放位置符合要 求
1.存放位置错误
发错货
1.仓管员不具 7 ◇ 备相关岗位技
能
2
1.仓管员进行岗位 培训
公司内审 /仓库稽查
2 28
存放方式符合要 求
2.存放方式不符 要求
1.打开左/右车门,依次触发两种音乐,同时前车灯发白光,尾车灯发红光,表板灯发蓝光. 2.按压车前轮触发引擎声,同时前车灯发白光,尾车灯发红光,表板灯发蓝光. 使用方式说明
3.轮子贴地后拉上满发条,松手产品向前行驶.
过程/功能
要求
潜在失效模式
潜在失效 模式后果
严级 重 度别
潜在失效 模式要因
发 生 率
产品名称/型号 项目名称 生产过程 核心小组
潜在失效模式及后果分析 P-FMEA
过程职责
关键日期
FMEA 编 号
页
次
编
制
FMEA编制日期
FMEA修订日期
产品适用年龄
3岁及以上
产品销售地区/适用法规 国内及国外销售,全球玩具安全技术法规均适用
设计理念/功能 仿真车之模型玩具,具有声光功能及回力驱动行驶功能
物料损坏
6
1.仓管员不具 备相关岗位技 能
1.仓管员进行岗位 2 培训
公司内审 /仓库稽查
PFMEA分析范例

PFMEA分析范例1. 引言PFMEA(Process Failure Mode and Effects Analysis)是一种常用的质量管理工具,用于识别和评估制造过程中存在的潜在故障模式及其对产品质量的影响。
本文将通过一个实例来展示PFMEA分析的过程和方法。
2. 实例描述假设我们正在开发一种新型电动汽车电池组装工艺,并希望通过PFMEA分析来发现潜在的故障模式并采取相应的措施预防。
3. PFMEA步骤3.1 选择分析范围首先,我们需要确定要分析的工艺范围。
在本例中,我们选择了电动汽车电池组装工艺中的关键步骤:电池包装、电池连接和充电检测。
3.2 收集工艺信息接下来,我们收集与每个工艺步骤相关的信息,包括工艺流程、设备、材料和人员等。
针对电池包装步骤,我们列出了以下信息: - 工艺流程:电芯装载、包装封装- 设备:电芯装载机、包装机- 材料:电芯、包装材料- 人员:操作工、质检员3.3 识别故障模式在此步骤中,我们识别潜在的故障模式,即制造过程中可能发生的问题。
针对电池包装步骤,我们列出了以下故障模式: - 电芯装载不准确- 包装封装不牢固3.4 评估故障影响在此步骤中,我们评估每个故障模式对产品质量的影响程度。
针对电芯装载不准确这一故障模式,我们评估了以下影响: - 电池运行时间缩短- 电池性能下降3.5 评估故障原因在此步骤中,我们分析导致每个故障模式出现的可能原因。
针对电芯装载不准确这一故障模式,可能的原因包括:- 操作工技能不熟练- 设备故障3.6 识别和实施控制措施在此步骤中,我们确定并实施控制措施以防止故障模式的发生。
针对电芯装载不准确这一故障模式,可能的控制措施包括: - 培训操作工,提高技能水平- 定期维护设备,确保其正常运行3.7 重新评估和更新PFMEA最后,我们重新评估已实施的控制措施并更新PFMEA表格。
如果控制措施有效,我们将确认问题得到了解决。
如果问题仍存在,我们需要重新评估并采取进一步的纠正措施。
PFMEA_PWB装配分析案例
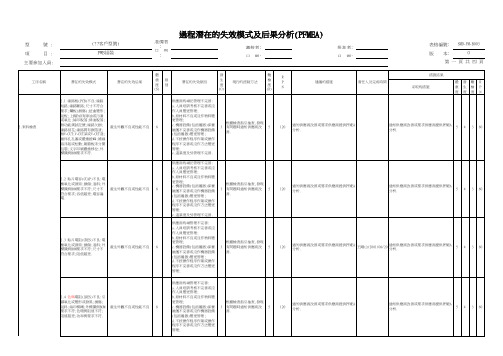
產生外觀不良或性能不良
8
3
根據檢查指引抽查,發現 有問題時通知供應商改 善.
3
根據檢查指引抽查,發現 有問題時通知供應商改 善.
5
120
通知供應商改善或要求供應商提供PFMEA 分析.
通知供應商改善或要求供應商提供PFMEA 分析.
5
4
3
60
2.2 貼片電容(CCAP)不良:電 極氧化或發黑;損傷;混料;外 標識與BOM要求不符;尺寸不 符合要求;容值超差;電容漏 電.
產生外觀不良或性能不良
產生外觀不良或性能不良
8
供應商的4M管理不完善: a.人員培訓考核不完善或沒 作人員變更管理; b.或原材料不良或沒作物料 變更管理; c.或機器設備(包括儀器)保 養維護不完善或沒作機器設 備(包括儀器)變更管理; d.或不按操作程序作業或操 作程序不完善或沒作方法變 更管理; 供應商的4M管理不完善: a.人員培訓考核不完善或沒 作人員變更管理; b.原材料不良或沒作物料變 更管理; c.機器設備(包括儀器)保養 維護不完善或沒作機器設備 (包括儀器)變更管理; d.不按操作程序作業或操作 程序不完善或沒作方法變更 管理; 供應商的4M管理不完善: a.人員培訓考核不完善或沒 作人員變更管理; b.或原材料不良或沒作物料 變更管理; c.或機器設備(包括儀器)保 養維護不完善或沒作機器設 備(包括儀器)變更管理; d.或不按操作程序作業或操 作程序不完善或沒作方法變 更管理; 供應商的4M管理不完善: a.人員培訓考核不完善或沒 作人員變更管理; b.或原材料不良或沒作物料 變更管理; c.或機器設備(包括儀器)保 養維護不完善或沒作機器設 備(包括儀器)變更管理; d.或不按操作程序作業或操 作程序不完善或沒作方法變 更管理; 供應商的4M管理不完善: a.人員培訓考核不完善或沒 作人員變更管理; b.或原材料不良或沒作物料 變更管理; c.或機器設備(包括儀器)保 養維護不完善或沒作機器設 備(包括儀器)變更管理; d.或不按操作程序作業或操 作程序不完善或沒作方法變 更管理;
PFMEA分析范例
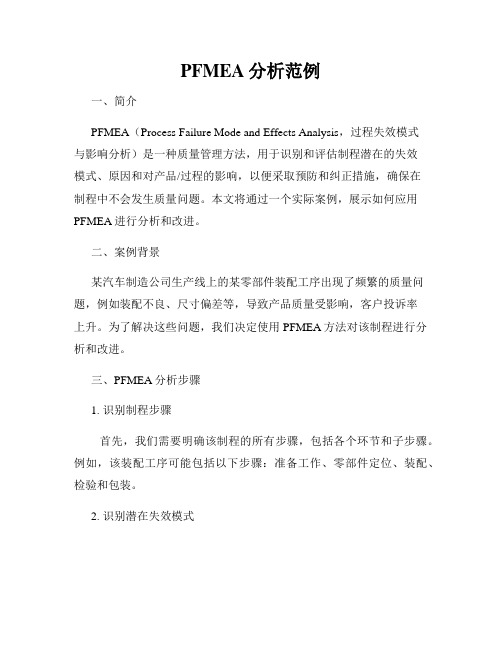
PFMEA分析范例一、简介PFMEA(Process Failure Mode and Effects Analysis,过程失效模式与影响分析)是一种质量管理方法,用于识别和评估制程潜在的失效模式、原因和对产品/过程的影响,以便采取预防和纠正措施,确保在制程中不会发生质量问题。
本文将通过一个实际案例,展示如何应用PFMEA进行分析和改进。
二、案例背景某汽车制造公司生产线上的某零部件装配工序出现了频繁的质量问题,例如装配不良、尺寸偏差等,导致产品质量受影响,客户投诉率上升。
为了解决这些问题,我们决定使用PFMEA方法对该制程进行分析和改进。
三、PFMEA分析步骤1. 识别制程步骤首先,我们需要明确该制程的所有步骤,包括各个环节和子步骤。
例如,该装配工序可能包括以下步骤:准备工作、零部件定位、装配、检验和包装。
2. 识别潜在失效模式对于每个制程步骤,我们需要识别可能的失效模式。
例如,在零部件定位步骤中可能出现的失效模式包括零部件定位不准确、零部件磨损等。
3. 评估失效影响针对每个失效模式,我们需要评估其对产品和制程的影响程度。
这可以通过制程图、统计数据和客户反馈等信息获得。
例如,零部件定位不准确可能导致装配不良、产品外观缺陷等问题。
4. 评估失效原因对于每个失效模式,我们需要分析其潜在原因。
这可以通过对制程参数、操作方法和设备条件等进行分析和检查来确定。
例如,零部件定位不准确的潜在原因可能是装配夹具磨损、工人技能不足等。
5. 评估当前控制措施针对每个失效模式和原因,我们需要评估当前是否有相应的控制措施。
如果有,需要评估其有效性和可靠性。
如果没有,需要考虑引入相应的控制措施。
例如,对于装配夹具磨损的失效原因,当前可能存在定期保养清洁措施,但其有效性需要进一步评估。
6. 制定改进措施基于对失效模式、影响、原因和控制措施的评估,我们可以制定相应的改进措施。
例如,针对装配夹具磨损的问题,我们可以考虑定期更换夹具、提供更好的保养指导等措施。
PFMEA案例
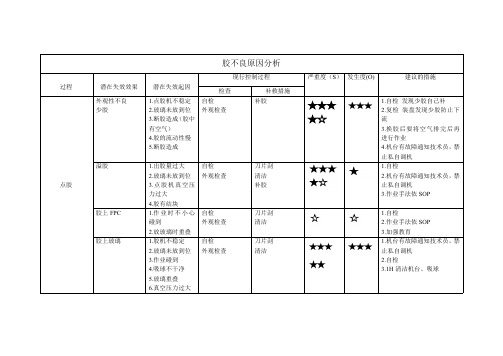
作业手法不对碰 自检
到胶
外观检查
刀片刮 清洁
棉签挑
刀片刮 清洁
1.自检 2.吸球吸玻璃的中间位置 3.1H 清洁吸球
1.现场 5S、成品盘装玻璃前 抖一抖 2.作业自检 1.自检 2.胶未干,禁止贴易撕贴 3.作业手法严格按照 SOP
1.自检 2.作业手法依 SOP 3.加强教育 1.机台有故障通知技术员,禁 止私自调机 2.自检 3.1H 清洁机台、吸球
胶上玻璃
装盘
胶异物
贴 易 撕 贴 / 电 测 / 胶上玻璃 外观
1.作业碰到 2.玻璃重叠 3.吸球不干净 4.胶未干,玻璃倾 斜 成品盘上异物掉 落
自检 外观检查
自检 外观检查
胶不良原因分析
过程 点胶
潜在失效效果
外观性不良 少胶
潜在失效起因
1.点胶机不稳定 2.玻璃未放到位 3.断胶造成(胶中 有空气) 4.胶的流动性慢 5.断胶造成
现行控制过程
检查 自检 外观检查
补救措施 补胶
溢胶
胶上 FPC 胶上玻璃
1.出胶量过大 2.玻璃未放到位 3. 点 胶 机 真 空 压 力过大 4.胶有结块 1.作 业 时 不 小 心 碰到 2.放玻璃时重叠 1.胶机不稳定 2.玻璃未放到位 3.作业碰到 4.吸球不干净 5.玻璃重叠 6.真空压力过大
自检 外观检查
自检 外观检查 自检 外观检查
刀片刮 清洁 补胶
刀Байду номын сангаас刮 清洁
刀片刮 清洁
严重度(S) 发生度(O)
建议的措施
1.自检 发现少胶自己补 2.复检 装盘发现少胶防止下 流 3.换 胶 后 要 将 空 气 排 完 后 再 进行作业 4.机台有故障通知技术员,禁 止私自调机 1.自检 2.机台有故障通知技术员,禁 止私自调机 3.作业手法依 SOP
PFMEA分析范例
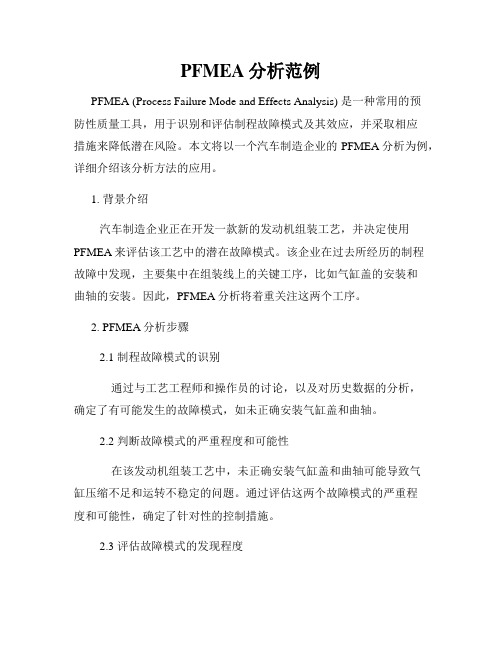
PFMEA分析范例PFMEA (Process Failure Mode and Effects Analysis) 是一种常用的预防性质量工具,用于识别和评估制程故障模式及其效应,并采取相应措施来降低潜在风险。
本文将以一个汽车制造企业的PFMEA分析为例,详细介绍该分析方法的应用。
1. 背景介绍汽车制造企业正在开发一款新的发动机组装工艺,并决定使用PFMEA来评估该工艺中的潜在故障模式。
该企业在过去所经历的制程故障中发现,主要集中在组装线上的关键工序,比如气缸盖的安装和曲轴的安装。
因此,PFMEA分析将着重关注这两个工序。
2. PFMEA分析步骤2.1 制程故障模式的识别通过与工艺工程师和操作员的讨论,以及对历史数据的分析,确定了有可能发生的故障模式,如未正确安装气缸盖和曲轴。
2.2 判断故障模式的严重程度和可能性在该发动机组装工艺中,未正确安装气缸盖和曲轴可能导致气缸压缩不足和运转不稳定的问题。
通过评估这两个故障模式的严重程度和可能性,确定了针对性的控制措施。
2.3 评估故障模式的发现程度考虑到设备和操作员的现有检测手段,确定了对未正确安装气缸盖和曲轴的发现程度。
如采用视觉检测和质量控制人员的检验。
2.4 计算RPN值通过将故障模式的严重程度、可能性和发现程度相乘,得到Risk Priority Number (RPN) 值,用于确定哪些故障模式需要优先处理。
2.5 制定预防和改善措施针对具有较高RPN值的故障模式,制定预防和改善措施,如提供培训、改进工艺规程、增加检测设备等。
2.6 实施和验证措施的有效性实施制定的措施,并通过监控和验证来确保其有效性。
比如设立关键工序的抽样检验,并对不合格品进行追踪分析。
3. 结果与总结通过PFMEA分析,汽车制造企业识别出了发动机组装工艺中的关键故障模式,并相应制定了有效的控制措施。
这些措施将有助于降低潜在的质量风险,提高发动机组装的可靠性和稳定性。
4. 心得体会通过本次PFMEA分析,我们深刻认识到了预防性质量工具的重要性。
PFMEA分析范例
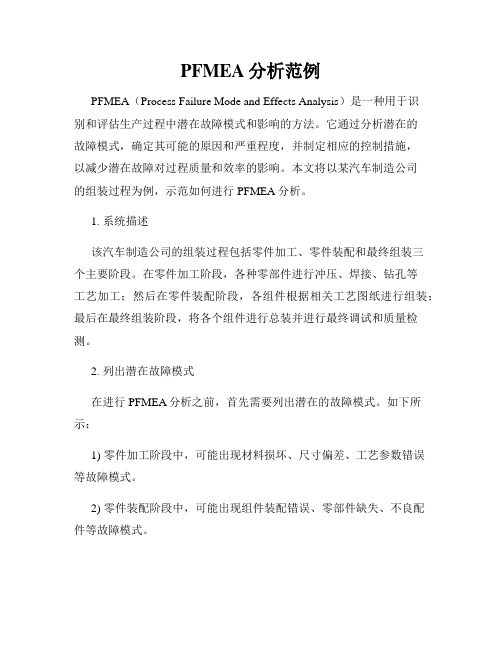
PFMEA分析范例PFMEA(Process Failure Mode and Effects Analysis)是一种用于识别和评估生产过程中潜在故障模式和影响的方法。
它通过分析潜在的故障模式,确定其可能的原因和严重程度,并制定相应的控制措施,以减少潜在故障对过程质量和效率的影响。
本文将以某汽车制造公司的组装过程为例,示范如何进行PFMEA分析。
1. 系统描述该汽车制造公司的组装过程包括零件加工、零件装配和最终组装三个主要阶段。
在零件加工阶段,各种零部件进行冲压、焊接、钻孔等工艺加工;然后在零件装配阶段,各组件根据相关工艺图纸进行组装;最后在最终组装阶段,将各个组件进行总装并进行最终调试和质量检测。
2. 列出潜在故障模式在进行PFMEA分析之前,首先需要列出潜在的故障模式。
如下所示:1) 零件加工阶段中,可能出现材料损坏、尺寸偏差、工艺参数错误等故障模式。
2) 零件装配阶段中,可能出现组件装配错误、零部件缺失、不良配件等故障模式。
3) 最终组装阶段中,可能出现组装错误、传动系统故障、电子系统故障等故障模式。
3. 评估故障原因在列出潜在故障模式之后,需评估每种故障模式的可能原因。
具体评估过程如下:1) 零件加工阶段中,材料损坏的原因可能是供应商提供的原材料质量不合格,尺寸偏差的原因可能是机床设备调整不当,工艺参数错误的原因可能是人工操作失误。
2) 零件装配阶段中,组件装配错误的原因可能是工人操作不规范,零部件缺失的原因可能是供应链管理不善,不良配件的原因可能是供应商提供的配件质量不合格。
3) 最终组装阶段中,组装错误的原因可能是工人操作失误,传动系统故障的原因可能是组装过程中零部件配合不良,电子系统故障的原因可能是控制芯片质量问题。
4. 评估故障严重程度在评估故障原因后,需要评估每种故障模式的严重程度,即故障发生时可能造成的影响程度。
具体评估过程如下:1) 零件加工阶段中,材料损坏可能导致后续组装工序无法进行,尺寸偏差可能导致产品性能下降,工艺参数错误可能导致产品质量问题。
PFMEA分析范例

PFMEA分析范例PFMEA(Potential Failure Mode and Effects Analysis)是一种常用于产品设计和生产过程中的风险评估工具。
它通过系统地识别潜在的失效模式,并评估这些失效对产品性能、生产效率和客户满意度的影响,从而帮助企业采取相应的措施来预防和降低潜在失效的风险。
本文将以汽车制造业为例,介绍PFMEA分析的具体步骤和相关应用。
1. 背景介绍汽车制造业面临着严格的质量要求和市场竞争压力。
在生产过程中,如果存在失效模式而未能及时发现或纠正,将会导致产品质量问题、客户投诉以及生产效率下降等严重后果。
因此,采用PFMEA分析方法能够帮助企业降低失效风险,提高产品质量和生产效率。
2. PFMEA分析步骤2.1 制定团队PFMEA分析需要跨职能团队共同参与,包括设计工程师、生产工程师、供应商等相关人员。
团队成员应根据其专业知识和经验来确定潜在失效模式及其影响因素。
2.2 识别失效模式团队成员根据产品设计和制造过程,逐一识别可能存在的失效模式。
例如,在汽车制造过程中,可能存在供应商提供零部件质量不合标准、零部件装配不准确等失效模式。
2.3 评估失效影响针对每个失效模式,团队成员评估其对产品性能、生产效率和客户满意度的影响程度。
评估指标可以根据实际情况进行确定,如利用5W1H法(What、When、Where、Why、How)来进行细致拆解。
2.4 评估失效原因团队成员分析导致每种失效模式的潜在原因,可以运用鱼骨图(也称因果图)或5W1H法来帮助识别。
例如,失效模式为零部件装配不准确,潜在原因可能包括操作员技能不足、装配工具磨损等。
2.5 制定控制措施团队成员针对每个失效模式及其原因,制定相应的控制措施,以预防或降低失效风险。
控制措施可以包括提高操作员培训、更换装配工具等。
2.6 评估控制效果实施控制措施后,团队成员应不定期进行监控和评估,以确定措施的有效性。
如果控制措施无效,需要重新进行评估并采取其他措施。
PFMEA案例

30
检查与评估现有的操纵方法
生产部
7﹑
装扣钩
漏装扣钩/扣钩装的位置不正确
线束装入车辆时困难或者安装失败
6
操作员未依规定操作
3
培训操作人员并重点标注图面要求
依照图面规定操作/100%外观检验
2
54
检查与评估现有的操纵方法
生产部
6
扣钩插入的深度不充分
2
培训操作人员并重点标注图面要求
依照图面规定操作/100%外观检验
装线盆入线不正确
3
用正确的装线盆/架
操作员检验
3
36
绝缘破皮,导线断线
端子铆线困难/导通测试不良
4
*裁线机故障/刀片设置太低/刀片用旧;*短路或者开路
5
保护保养/点检
100%检查
2
40
2﹑
压端子
端子变形
铆线端子插入壳仔困难
6
送料爪的变化导致端子经导流板时不正确
2
加大清洁/润滑端子机活动部门的频次
PQC每小时巡检/操作员自检
3
பைடு நூலகம்36
检查与评估现有的操纵方法
工程部
铆线端子插入壳仔后不合格
6
端子在导流板卡住而被硬拉出铆线
2
加大清洁/润滑端子机活动部位的频次
PQC每小时巡检/操作员自检
3
36
检查与评估现有的操纵方法
工程部/品管部/生产部
拉力不够
端子铆线不正确
8
▲
模座/刀座松动
2
保护保养/操纵正确的C/H
每小时拉力测试;巡检
3
48
灯炮装配线束时困难
5
检查图面脏污或者褪色未及时更换
PFMEA案例(从原材料-加工-出货整套案例分析)

3
注塑成型
产品缺料
影响产品质量、 制造进度
7
影响产品质量、 制造进度
7
影响外观与装 配,使顾客不满 7
意
A 供应商没有严格控制
1、优先使用顾客认可供应商 2 2. 选择有质量保证能力和良 到货验收
好信誉的供应商
3 42
A
检测及对供方的控制手段不 够
2
1.不定期进行供应商审核2.使 用外部认可实验室进行检测
8 包装 9 最终检验 10 入库存储 11 出货交付
标签贴错 漏检 纸箱受潮变形 数量不准确
产品型号错误, 顾客不满意
2
C 包装人员粗心
不良品混入,影 响客户使用
5
C 检验人员操作失误
纸箱变形破损
3 C 纸箱堆积太高
顾客不满意
1 C 仓库计数错误
3 检查、更正 3 检验、及时标记 3 检查、更正 3 检查、更正
过程潜在失效模式及后果分析 (PFMEA)
类型/部件: 车型年:
核心小组:
设计责任: 关键日期:
RPN DETECT
OCCUR CLASS SEV
项目 设计功能/要求
潜在失效模式
潜在失效后果
失效的潜在原因 /机理
现行设计控制防范
现行设计控制探测
建议措施
1 原材料采购
原材料不合格
2 原材料检验
质量不合格流入
4 调节注射压力 作业准备验证,适当调整,并 进行工艺监控 清理模具分型面
调节注射温度
1.原料含水分、溶剂或易挥 发物 2.塑料温度太高或受热时间 长,易降聚或分解 3.注射压力太小
3 原料检验 调节注射压力
4.注射柱塞退回太早
PCB干膜外层前处理PFMEA分析范例
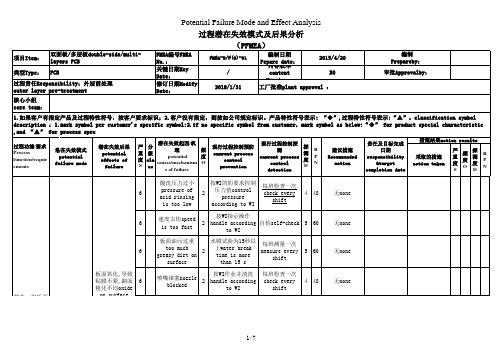
项目Item:FMEA编号FMEANo.:编制日期Pepare date:类型Type:关键日期KeyDate:内容版本contentVersion:修订日期ModifyDate:核心小组core team:采取的措施action taken 严重度S频度O探测度DRPN6酸洗压力过小pressure ofacid rinsingis too low2按WI的的要求控制压力值controlpressureaccording to WI每班检查一次check everyshift448无none6速度太快speedis too fast2按WI指示操作handle accordingto WI自检self-check560无none6板面油污过重too muchgreasy dirt onsurface2水膜试验为15秒以上water breaktime is morethan 15 s每班测量一次measure everyshift560无none6喷嘴堵塞nozzleblocked2按WI作业并清洗handle accordingto WI每班检查一次check everyshift448无noneRPN建议措施Recommendedaction责任及目标完成日期responsibility&targetcompletion date措施结果action results 潜在失效起因/机理potentialcauses/mechanisms of failure频度O现行过程控制预防current processcontrolprevention现行过程控制探测current processcontroldetection探测度D过程责任Responsibility:外层前处理outer layer pre-treatment2018/1/31工厂批准plant approval :1.如果客户有指定产品及过程特性符号,按客户要求标识;2.客户没有指定,则按如公司规定标识。
PCB表面处理沉金PFMEA分析范例

2
温度校正 The temperature
calibration
温度计对比校正
Comparison correction of
5 70
thermometers
烘干温度控制在80±5℃ 设备自动控制
control temperature
Automatic
3 42
within 80±5℃
equipment control
现行过程 控制探测current process detection
探 测 度
D
R P N
每班测量微蚀速率控制
在0.1-0.5um。
每班化验分析
2 The microerosion chemical analysis 5 70
rate is controlled
every shift
at 0.1-0.5um.
copper ion: 5-20g/l
无none 无none
3/9
unadequate micro-
漏镍金Skip plating
7
etching
过程
潜在失
功能process function
效模式
要求
potential
requirement failure mode 微蚀micro-etching
FMEA编号 FMEA No.:
关键日期 Key Date:
修订日期 Modify Date:
FMEA-IG-01 /
2020/3/26
编制日期Pepare date:2015/8/28 内容版本content Version:B3 工厂批准plant approval :
编制 Prepareby:
- 1、下载文档前请自行甄别文档内容的完整性,平台不提供额外的编辑、内容补充、找答案等附加服务。
- 2、"仅部分预览"的文档,不可在线预览部分如存在完整性等问题,可反馈申请退款(可完整预览的文档不适用该条件!)。
- 3、如文档侵犯您的权益,请联系客服反馈,我们会尽快为您处理(人工客服工作时间:9:00-18:30)。
8
3
根据检查指引抽查,发 现有问题时通知供货商 改善.
5
120
通知供货商改善或要求供货商提供 PFMEA分析.
通知供货商改善或要求供货商提供 PFMEA分析.
5
4
3
2.4 色码电阻(LRES)不良:引 脚氧化或变形或发黑;损伤; 混料;丝印模糊;外标识与BOM 要求不符;色环与阻值不符; 阻值超差;功率与要求不符.
主要参加人员:
工序名称
潜在的失效模式
潜在的失效后果
级 别
潜在的失效原因
现行的控制方法
R P N
2.来料检查
2.1 线路板(PCB)不良:线路 短路;线路断路;尺寸不符合 要求;烂板(损伤);扭曲变形; 混板;上锡PAD有绿油或污渍 或氧化;丝印脱落;绿油脱落; 无功能测试记号;线路欠损; 线路刮花;线路间有铜箔渣; 无V-CUT;V-CUT深或V-CUT浅; 插件孔孔塞或严重披峰;补线 路浮起或松动;报废板未分开 包装;文字印刷严重移位;外 标识与BOM要求不符.
3
根据检查指引抽查,发 现有问题时通知供货商 改善.
5
120
通知供货商改善或要求供货商提供 PFMEA分析.
通知供货商改善或要求供货商提供 PFMEA分析.
5
4
3
2.8直插式IC不良:引脚氧化 或变形或发黑;封装形式不符 要求;损伤;混料;丝印模糊; 丝印内容与BOM要求不符;外 标识与BOM要求不符;尺寸不 符合要求;电气性能不良.
3
根据检查指引抽查,发 现有问题时通知供货商 改善.
5
120
通知供货商改善或要求供货商提供 PFMEA分析.
通知供货商改善或要求供货商提供 PFMEA分析.
5
4
3
2.2 贴片电容(CCAP)不良:电 极氧化或发黑;损伤;混料;外 标识与BOM要求不符;尺寸不 符合要求;容值超差;电容漏 电.
产生外观不良或性能不良
5
120
通知供货商改善或要求供货商提供 PFMEA分析.
通知供货商改善或要求供货商提供 PFMEA分析.
5
4
3
2.5插脚二极管(DIODE)不良: 引脚氧化或变形或发黑;损 伤;混料;丝印模糊;极性标识 错误;实物丝印内容与BOM要 求不符.外标识与BOM要求不 符;尺寸不符合要求;电气性 能不良.
产生外观不良或性能不良
8
供货商的4M1E管理不完善: a.人员培训考核不完善或没 作人员变更管理; b.原材料不良或没作物料变 更管理; c.机器设备(包括仪器)保养 维护不完善或没作机器设备 (包括仪器)变更管理; d.不按操作程序作业或操作 程序不完善或没作方法变更 管理; e.温湿度及5S管理不完善. 供货商的4M1E管理不完善: a.人员培训考核不完善或没 作人员变更管理; b.原材料不良或没作物料变 更管理; c.机器设备(包括仪器)保养 维护不完善或没作机器设备 (包括仪器)变更管理; d.不按操作程序作业或操作 程序不完善或没作方法变更 管理; e.温湿度及5S管理不完善. 供货商的4M管理不完善: a.人员培训考核不完善或没 作人员变更管理; b.原材料不良或没作物料变 更管理; c.机器设备(包括仪器)保养 维护不完善或没作机器设备 (包括仪器)变更管理; d.不按操作程序作业或操作 程序不完善或没作方法变更 管理;
8
3
根据检查指引抽查,发 现有问题时通知供货商 改善.
5
120
通知供货商改善或要求供货商提供 PFMEA分析.
通知供货商改善或要求供货商提供 PFMEA分析.
5
4
3
2.3 贴片电阻(CRES)不良:电 极氧化或发黑;损伤;混料;外 标识与BOM要求不符;尺寸不 符合要求;阻值超差.
产生外观不良或性能不良
8
供货商的4M管理不完善: a.人员培训考核不完善或没 作人员变更管理; b.原材料不良或没作物料变 更管理; c.机器设备(包括仪器)保养 维护不完善或没作机器设备 (包括仪器)变更管理; d.不按操作程序作业或操作 程序不完善或没作方法变更 管理;
3
根据检查指引抽查,发 现有问题时通知供货商 改善.
5
120
通知供货商改善或要求供货商提供 PFMEA分析.
通知供货商改善或要求供货商提供 PFMEA分析.
5
4
3
2.6插脚三极管(TRAN)不良: 引脚氧化或变形或发黑;损 伤;混料;丝印模糊.实物丝印 内容与BOM要求不符;外标识 与BOM要求不符;尺寸不符合 要求;极性错误;电气性能不 良.
产生外观不良或性能不良
过程潜在的失效模式及后果分析(PFMEA)
型 项 号 : 目 : PWB组装 准备者﹕ 日 期﹕ 审核者﹕ 日 期﹕ 批准者﹕ 日 期﹕ 表格编号﹕ 版 本﹕ 第 一 页 共 四 页
严 重 度 (S) 发 生 度 (O) 难 检 度 (D) 措施结果 建议的措施 责任人及完成时间 采取的措施 严 重 度 发 生 度 难 检 度
产生外观不良或性能不良
8
供货商的4M管理不完善: a.人员培训考核不完善或没 作人员变更管理; b.或原材料不良或没作物料 变更管理; c.或机器设备(包括仪器)保 养维护不完善或没作机器设 备(包括仪器)变更管理; d.或不按操作程序作业或操 作程序不完善或没作方法变 更管理;
3
根据检查指引抽查,发 现有问题时通知供货商 改善.
5
120
通知供货商改善或要求供货商提供 PFMEA分析.
通知供货商改善或要求供货商提供 PFMEA分析.
5
4
3
2.7贴片三极管(TRAN)不良: 电极氧化或变形或发黑;混 料;损伤;丝印模糊;实物丝印 内容与BOM要求不符;外标识 与BOM要求不符;电气性能不 良.
产生外观不良或性能不良
8
供货商的4M管理不完善: a.人员培训考核不完善或没 作人员变更管理; b.或原材料不良或没作物料 变更管理; c.或机器设备(包括仪器)保 养维护不完善或没作机器设 备(包括仪器)变更管理; d.或不按操作程序作业或操 作程序不完善或没作理不完善: a.人员培训考核不完善或没 作人员变更管理; b.原材料不良或没作物料变 更管理; c.机器设备(包括仪器)保养 维护不完善或没作机器设备 (包括仪器)变更管理; d.不按操作程序作业或操作 程序不完善或没作方法变更 管理;
3
根据检查指引抽查,发 现有问题时通知供货商 改善.