五原则表培训教材PPT课件
合集下载
广本5原则培训资料

☆集体创造性思考 ☆特性要因图
• 调查结果总结、变化点和推断原因总结
4、现在的対応状况(緊急処置後的)
• 用X-R管理图 、矩形图、CP值等
可以说问题一定源于变化点(人、物、设备等,4M1E)
1、老七种工具: 调查表 分层法 排列图 因果图 直方图 控制图 散布图 2、新七种工具 亲和图 树图 关联图 矩阵图 箭条图 PDPC法(过程决策程序图法) 矩阵数据分析法
・可用于解决开发、生产、销售、供应、管理等 所有领域发生的问题。
来自顾客的意见、投诉产品、服务不好 设备、机械、机器的问题 精确度与效率不高的工作
解决问题、防止再发
五原则工作表
重要度的决定及处置判断
• 重要度、麻烦度、重要保安部品判断
零件品质科
重要度
麻烦度
重要保安部品
A 不良时判断为危害人身安 A 已进行整车的检测、修理 HS
17 240±5 +7 +8 +9
P21
10 270 SET SET SET
(工序概要) No 工程名 1 来料仓库 2 端末加工 3 弯管加工 4 最終検査 5 出荷
加工機種名 起因 西岛端末加工机 T型弯管机 ★ -
*根据现品确认,弯管形状有同样倾向
■ 5原则工作表(解析报告)
是指从发生问题的初期对应到彻底解决问题,防止再发的问题解 决手法。是本田特有的问题解决手法。
目的:通过对不良问题进行有条理的、理论性的分析(三现主 义) ,查找真正的原因,采取适当的对策,防止问题再发。
・解析报告要将解决问题流程的结果用1张纸(A3)总结后进行报告。
■ 使用范围
集、整理)
• 工序中现正生产的零部件的品质状况、良品批次确认(根据X-R管理图、工程
三现五原则ppt课件
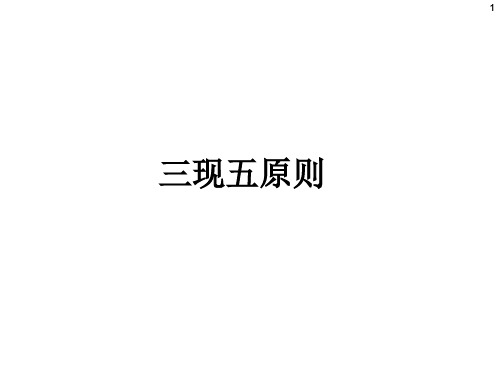
关部门传达。
6、减少问题再次发生的次数
五原则的填写说明-发 生 状 况(现象、投诉内容、发生件数、处置内容)
6
填写目标: 1、为体现到下一个行动、目标 2、为更鲜明体现部品、部位, 应直接写下事实现象,并如实写 明该时的动机、变化
见下页
五原则的填写说明-发 生 状 况(现象、投诉内容、发生件数、处置内容)
亲自 接触 实物 (现 物)
調总和の是と以れ事た 仕实事の为流基れ础を 作り而あげ行る动こと
“干部应一天洗两次手”、 “高高在上三个月也未弄 懂的问题,深入基层三天
便能马上明嘹”
有下列想法、行动的人才能搞好现场 管理工作:
〇 喜欢接触现场的人 〇 每天深入了解现场的人 〇 理解深入现场的好处的人
三现主义在中国用得很早:远点,“捉贼捉脏, 捉奸捉双”;近点,毛主席的“没有调查研究 就没有发言权”;再近点,;新闻工作者不也是 天天在掌握第一手材料么?谁和谁有拍拖之 嫌呀,哪个和哪个出现在某酒店啊,这都是三 现主义的运用,可是中国的三现主义只用于 政治或只用于整人,很少用于品质管理。
为什么呢?原因是出在这家冰淇淋店的内部设置的问题。因为,香草冰淇淋是所有冰淇淋口味中最畅销的口味,店家为了 让顾客每次都能很快的取拿,将香草口味特别分开陈列在单独的冰柜,并将冰柜放置在店的前端;至于其它口味则放置在距离 收银台较远的后端。
现在,工程师所要知道的疑问是,为什么这部车会因为从熄火到重新激活的时间较短时就会不能发动?原因很清楚,绝对 不是因为香草冰淇淋的关系,工程师很快地由心中浮现出,答案应该是“ 蒸气锁”。因为当这位仁兄买其它口味时,由于时 间较久,引擎有足够的时间散热,重新发动时就没有太大的问题。但是买香草口味时,由于花的时间较短,引擎太热以至于还 无法让“ 蒸气锁 ”有足够的散热时间。
6、减少问题再次发生的次数
五原则的填写说明-发 生 状 况(现象、投诉内容、发生件数、处置内容)
6
填写目标: 1、为体现到下一个行动、目标 2、为更鲜明体现部品、部位, 应直接写下事实现象,并如实写 明该时的动机、变化
见下页
五原则的填写说明-发 生 状 况(现象、投诉内容、发生件数、处置内容)
亲自 接触 实物 (现 物)
調总和の是と以れ事た 仕实事の为流基れ础を 作り而あげ行る动こと
“干部应一天洗两次手”、 “高高在上三个月也未弄 懂的问题,深入基层三天
便能马上明嘹”
有下列想法、行动的人才能搞好现场 管理工作:
〇 喜欢接触现场的人 〇 每天深入了解现场的人 〇 理解深入现场的好处的人
三现主义在中国用得很早:远点,“捉贼捉脏, 捉奸捉双”;近点,毛主席的“没有调查研究 就没有发言权”;再近点,;新闻工作者不也是 天天在掌握第一手材料么?谁和谁有拍拖之 嫌呀,哪个和哪个出现在某酒店啊,这都是三 现主义的运用,可是中国的三现主义只用于 政治或只用于整人,很少用于品质管理。
为什么呢?原因是出在这家冰淇淋店的内部设置的问题。因为,香草冰淇淋是所有冰淇淋口味中最畅销的口味,店家为了 让顾客每次都能很快的取拿,将香草口味特别分开陈列在单独的冰柜,并将冰柜放置在店的前端;至于其它口味则放置在距离 收银台较远的后端。
现在,工程师所要知道的疑问是,为什么这部车会因为从熄火到重新激活的时间较短时就会不能发动?原因很清楚,绝对 不是因为香草冰淇淋的关系,工程师很快地由心中浮现出,答案应该是“ 蒸气锁”。因为当这位仁兄买其它口味时,由于时 间较久,引擎有足够的时间散热,重新发动时就没有太大的问题。但是买香草口味时,由于花的时间较短,引擎太热以至于还 无法让“ 蒸气锁 ”有足够的散热时间。
五原则表培训教材
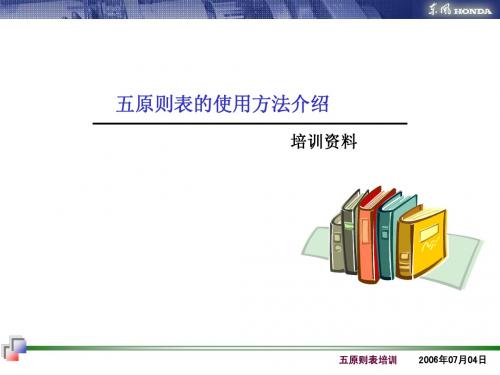
27.3333
11000-PWC-0202
零件名称 零件号
问题零件的名称 对应于部品表的零件编号
日期
批准日期
提出部门 批准 审核
管理科 自制品质系
审核
发现区域检技
自制品质不良主要由管理科提出五原则对策要求及跟踪推进!
日期
编制日期 科 长
批准
副 科 长
编制部门 检技
检技
系长
系长
班长
班长
编制
担当
责任部门负责五原则表的编制,由检查技术者审核后,交由科长批准!
不良发生对策 ・加工设备内铁屑清扫
对策人:刘×× 对策时间:5月6日
《恒久对策》
不良发生对策 ・在护板上安装吹气装置
・在作业标准书里,追加吹起 装置的确认项目.
对策人:刘×× 对策时间:6月6日
不良流出对策 ・车削QA机判定为不良品后的处理
对策人:王×× 对策时间:5月7日
不良流出对策 ・QA机排出不良品的处理方法明确化. ・车削QA机不良品处理台帐的作成 ・车削QA机不良品的处理作业标准书 作成.
再现品的不良现象和现品一样。从这样的结果 来看,这次的不良是由于铁屑的残留,工件在偏心的 状态在被加工所致的。
五原则表培训
2006年07月04日
【 为何-为何分析】
1-对主要原因进行五次为何为何分析,将问题反馈到源流进行改善。 2-对不良发生的为何-为何分析。 3-对不良流出的为何-为何分析。
记录查明原因的过程
五原则表培训
2006年07月04日
【 把握事实】 例
①
③
Y 方 向
測定箇所
① 中心孔深度 ② 小端面位置 ③ 螺纹上部轴径 ④ 螺纹大径 ⑤ 花键大径 ⑥ OP径 ⑦ 导向径 ⑧ 外圆直径 φ93.7 φ90.7
5原则解析报告培训教材

始业及每加工500件用卡尺测量并记录数据。
品质科 11/23
·在设备上明确标示辅助滚轮所在正确位置的尺寸。
工务科 11/25
(流出対策)
·检查治具的改善对策
(改造至和实车装配有相同的异常判定能力)
·标明判断标准及作业方法。
对策前
对策后
品质科 11/30 品质科 11/30
洞穴
溶接固定 实车 同条件
实车
POINT23曲率不良
(和其
方向)
它部
品间 隙过 小)
流出 原因
虽用过检具确认,但未发 现异常,不良品符合检 具,被判定为OK。
·端末部的检具槽为可动 式设计,容许最大的偏差 量为23mm·检具槽没有 设置限位
3
在对辅助滚轮进行了调 整后,锁紧时滚轮位置 偏移,造成POINT23偏 离基准
可动式设计容易忽略其 活动量,而导致错误的 判断
2、流出原因 检具
A
· 端末部的检具槽为可动式设计, 最大容许的活动量为 23 mm ,如下图所示:
·通过检具进行零件的确认时 容易忽略上述活动量, 而导致错误的判断。 误将NG品判定为合格
A部放大 6
17
Step
1
2
因Point17~22偏离基准值
形 不
状 良
发生 原因
过大,和其它部品的间隙 就会过小(尺寸偏向H+
最终检查
把零件放置在检具上,上紧定 忽略了可动式检具槽的活动量,
作业方法 位端螺栓,管件不能和检具槽 误将NG品判定为合格
×
干涉及超出基准面。
对策效果要的因确认和(效事果实实绩的) 分析
五原则表培训
零件品质科
2、查明原因(发生的原因・重现测试)
三现五原则最终版PPT课件
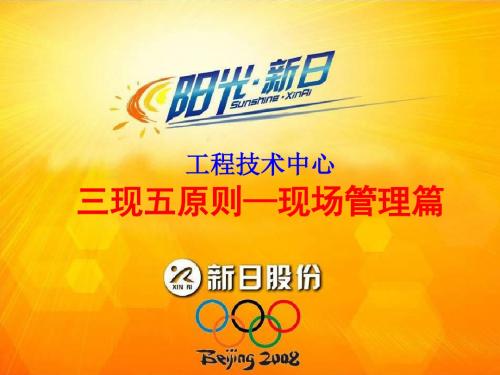
工程技术中心
三现五原则—现场管理篇
质 量 ● 创 新 ● 服 务
一、背
景
1、生产现场是组织内部所有工作成效的检验地、集成 地,是内部工作的终点。另一方面,从现场入手,可 以拉动组织内部其他部门的工作,所以,现场又是一
个内部改善的起点。
2、品质经常发生不良,导致交期不正常。
3、返修过多,导致工作时间过长,员工士气低落。
临时对策之执行成效
对策内容之 执行成效
永久对策之有效性
效果确认
•零件之品质特性 (制程能力的改善) •完成品之品质水准 •耐久品质水准确认 •市场品质状况确认
实际品质水 准效果确认
质 量 ● 创 新 ● 服 务
4、效果确认
1、对于实行的对策,实施追踪。 2、在进行效果确认检查时,取 样数量可参考实际问题发生 率,数据方面可以灵活使用 统计手法。
质 量 ● 创 新 ● 服 务
5、源流回馈
标准类反应 源流回馈
S.O.P修订
质 量 ● 创 新 ● 服 务
•图面 •零件检验标准 •QC工程表 •作业标准 •试验规范 •限度样品
1、无科学根据数据
疑 问 点:常发生的直觉判断 ~ 焊接强度不足对策:焊道加长2mm.正确吗? ~ 模温不足变形对策:模温提高10℃.没问题吗? 考:加长2mm、提高10℃如何得到的? 思
质 量 ● 创 新 ● 服 务
分析方法:利用品管统计学来掌握解析手法之可靠 性。问题解析与效果确认, 皆可使用品 管统计手法。 1. 掌握品质的准确程度 a.平均数X b.中位数 c.众数。 2.掌握品质的均匀程度 a .全距 R b .最大值最小值 Max 、 Min c.标准差。 3. 掌握制程品质能力
质 量 ● 创 新 ● 服 务
三现五原则—现场管理篇
质 量 ● 创 新 ● 服 务
一、背
景
1、生产现场是组织内部所有工作成效的检验地、集成 地,是内部工作的终点。另一方面,从现场入手,可 以拉动组织内部其他部门的工作,所以,现场又是一
个内部改善的起点。
2、品质经常发生不良,导致交期不正常。
3、返修过多,导致工作时间过长,员工士气低落。
临时对策之执行成效
对策内容之 执行成效
永久对策之有效性
效果确认
•零件之品质特性 (制程能力的改善) •完成品之品质水准 •耐久品质水准确认 •市场品质状况确认
实际品质水 准效果确认
质 量 ● 创 新 ● 服 务
4、效果确认
1、对于实行的对策,实施追踪。 2、在进行效果确认检查时,取 样数量可参考实际问题发生 率,数据方面可以灵活使用 统计手法。
质 量 ● 创 新 ● 服 务
5、源流回馈
标准类反应 源流回馈
S.O.P修订
质 量 ● 创 新 ● 服 务
•图面 •零件检验标准 •QC工程表 •作业标准 •试验规范 •限度样品
1、无科学根据数据
疑 问 点:常发生的直觉判断 ~ 焊接强度不足对策:焊道加长2mm.正确吗? ~ 模温不足变形对策:模温提高10℃.没问题吗? 考:加长2mm、提高10℃如何得到的? 思
质 量 ● 创 新 ● 服 务
分析方法:利用品管统计学来掌握解析手法之可靠 性。问题解析与效果确认, 皆可使用品 管统计手法。 1. 掌握品质的准确程度 a.平均数X b.中位数 c.众数。 2.掌握品质的均匀程度 a .全距 R b .最大值最小值 Max 、 Min c.标准差。 3. 掌握制程品质能力
质 量 ● 创 新 ● 服 务
品质管理的三现五原则 ppt课件
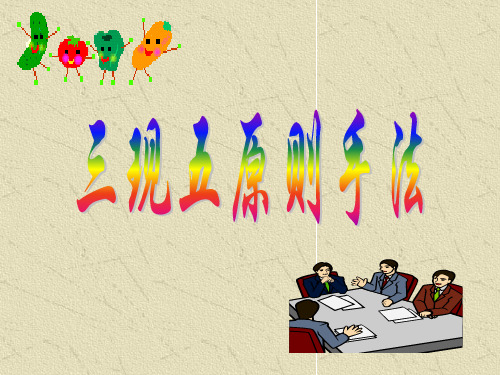
2-A 查明原因(WHY WHY 分析)
2-B 查明原因(发生的途径、问题再现试验WHY WHY分析)
3 采取)适当的对策 (对策内容、效果预测PPA) 4确认(对策)效果(效果实绩) 5对(问题)源头的反馈(需落实到体制、组织的内容)
品质管理的三现五原则
右腕受伤
1- A 发生状况(现象、申诉内容、发生次数、5W1H处置内容)
笨,没有学问无颜见爹娘 ……” • “太阳当空照,花儿对我笑,小鸟说早早早……”
4
1、了解并运用三现五原则解析 手法,真正改善重要品质问 题
2、解决问题→持续有效解决问 题→不再是问题
3、解决客诉品质问题挑战“零不良”
品质管理的三现五原则
现物
三现
现状
现场
品质管理的三现五原则
1、机种、零件名称/号码 2、发生场所/环境/使用条件 3、发生的现象/问题 4、发生日期 5、引擎号码
记入要领
1-B 对事实的把握(对零部件的确认结果、原因分析、现在正在生产的该零部件的品质状况)
1、在确认事故发生时,也发现了
同样汽缸倒下来的情况,作业
人
设备
人员每一次都是同样地用手把 它扶起来(还了解到一般9个 里会倒1个)
疲劳
注意 不够
没有反馈 不知道方法
作业标准不完善
2、在事故发生时,作业人员的健
汽缸倒下来这 一情况未反馈
与特性要因图(鱼刺图),利用系统的、有条理的Q&A(提 问和回答)方法,抓住找出真正的原因 2-A 查明原因( WHY WHY 分析)
1
2
3
4
5
内
检验: 为何会检测不出来。
品质管理的三现五原则
意义:为什么之五层分析是一个形容 词,代表追根究底的意思,其目 的在寻求真正的原因,并不是一 次要作五次为什么分析,可以比 五次少,也可以比五次多,只要 能寻求出真正的原因。
五原则表
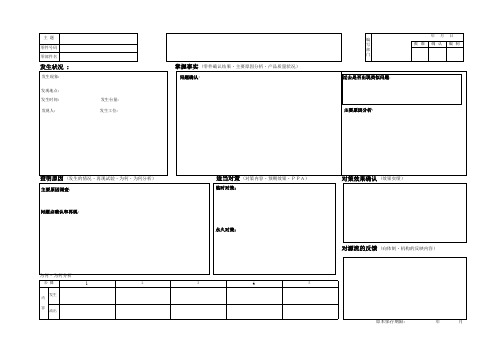
主 题 零件号码
年
月
日
零部件名ห้องสมุดไป่ตู้
编 写 部 门
批 准
确 认
编 制
发生状况 :
发生现象: 发现地点: 发生时间: 发现人: 发生台量: 发生工位:
掌握事实
(零件确认结果・主要原因分析・产品质量状况) 过去是否出现类似问题:
问题确认:
主要原因分析:
查明原因
(发生的情况・再现试验・为何・为何分析)
适当对策
临时对策:
(对策内容・预期效果・PPA)
对策效果确认
(效果实绩)
主要原因调查:
问题点确认和再现:
永久对策:
对源流的反馈
(向体制・机构的反映内容)
为何・为何分析
步 骤
发生
1
2
3
4
5
内 容
流出
原本保存期限:
年
月
年
月
日
零部件名ห้องสมุดไป่ตู้
编 写 部 门
批 准
确 认
编 制
发生状况 :
发生现象: 发现地点: 发生时间: 发现人: 发生台量: 发生工位:
掌握事实
(零件确认结果・主要原因分析・产品质量状况) 过去是否出现类似问题:
问题确认:
主要原因分析:
查明原因
(发生的情况・再现试验・为何・为何分析)
适当对策
临时对策:
(对策内容・预期效果・PPA)
对策效果确认
(效果实绩)
主要原因调查:
问题点确认和再现:
永久对策:
对源流的反馈
(向体制・机构的反映内容)
为何・为何分析
步 骤
发生
1
2
3
4
5
内 容
流出
原本保存期限:
年
月
SMART五大原则ppt课件
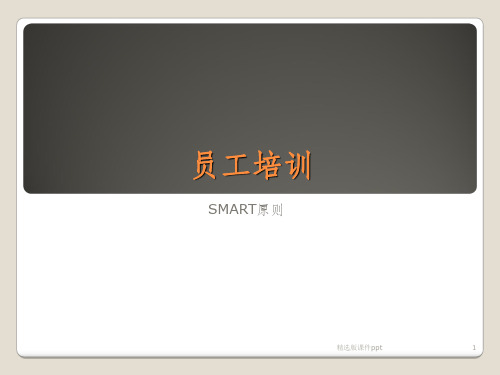
A:(Attainable)实现性
精选版课件ppt
12
提供示例:
例: 本周我要完成某某餐饮街的立项、前期拜访、厨师 联谊会、小区推广、开发进货、生动化宣传、维护巩固全 过程,造就月销量5万元的首条餐饮样板街。
工作量太大,无法一个人在一周内保质保量的完成, 单条餐饮街的月销售平台5万元可能难以在一周内达成。
明确性;
M:(Measurable) 衡量性;
A:(Attainable)
实现性;
R:(Relevant)
相关性;
T:(Time bound) 时限性。
SMART原则
精选版课件ppt
5
目标要清晰、明确,让考核者与被考核者能 够准确的理解目标。
明确的目标几乎是所有成功团队的一致特点。很多团队不成 功的重要原因之一就因为目标定的模棱两可,或没有将目标有效的传 达给相关成员。
精选版课件ppt
18
提供示例:
例:餐饮部在今后很长一段时间内,还是会把餐饮开发 作为工作的重点,切实有效地提升销售平台。
很长一段时间,有时间限制,但没有明确的时间限制。
修改:餐饮部会把餐饮开发作为工作的重点,每月新增 销售平台3万元,截止9月30日,餐饮部整体月销售平台 达到115万元。
T:(Time bound)时限性
既要使工作内容饱满,也要具有可达性。
可以制定出跳起来“摘桃”的目标,不能制定出跳起 来“摘星星”的目标。
A:(Attainable)实现性
精选版课件ppt
14
目标要和工作有相关性,不是被考核者 的工作,别设定目标。
个人目标与组织目标达成认识一致,目标一致, 要考虑达成目标所需要的条件,这些条件包括人力资源、硬件 条件、技术条件、系统信息条件、团队环境因素等 目标要有实际意义和效果, 定目标要考虑成本和结果的效益,要取得成本和结果的平衡点。
中文五原则表教材培训讲学
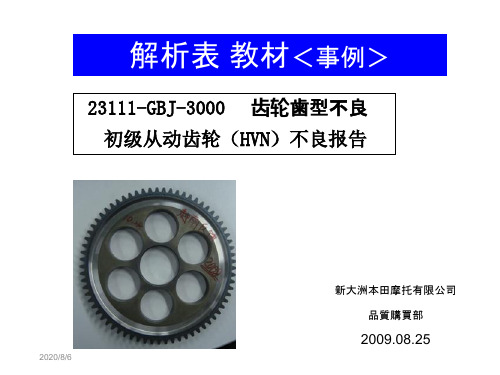
再現试验概要 上冲
上冲
阴模
倾斜的产品
阴模 再現
产品
Sizing机器
下冲
2.0φ異物 (如碎等)
<图1>
<图2>
图1为待精整产品,上、下冲处于停止状态,产品放置在阴模型腔内的导向段内;
图2为产品精整过程示意图,上冲单向压制,从上方开始对产品施压。当有杂物存在时,产品会倾斜,被垫起 部分将与上冲首先接触,且所受到的压力逐渐增加;当产品进入阴模有效段后,产品的外径尺寸是略大于模 具尺寸20的20,/8/6因此产品的齿尖锐处会作用与阴模型腔,将阴模拉伤。
5-2.查明原因-发生(再現试验条件)
2.<再現試験>・・・以特性要因図、
現場検証的因素为基础,实施再現试 验,找出原因。 ・・・①.試験条件、方法的明確化
过程再现:再現試験状態
当上冲向下运动时,被异物垫起的 齿尖部分损伤阴模。
标记点
齿顶处与阴模内腔接触
2020/8/6
上冲
齿轮 ● 下冲
鉄異物 2φmm
对此两尺寸控制,控制提高,分别为:
左、右齿形:0~0.007mm
左、右齿向:0~0.007mm
左图为初始的精整工序检查记录表,只对齿形、向在数值 上做出规定,忽略了齿形、齿向的曲线形状波动问题。
2.精整工序现场作业情况
碎齿大小约 为2x3mm
精整工序对齿形、齿向要求
2020/8/6
如上图,制造现场,模具表面发现产品碎齿的颗粒现場缺
再现试验产品齿形
试验件测量结果 1 2 3 4 5 6 7 8 9 10 11 0.004 0.004 0.003 0.006 0.005 0.004 0.004 0.003 0.003 0.002 0.002
中文五原则表教材
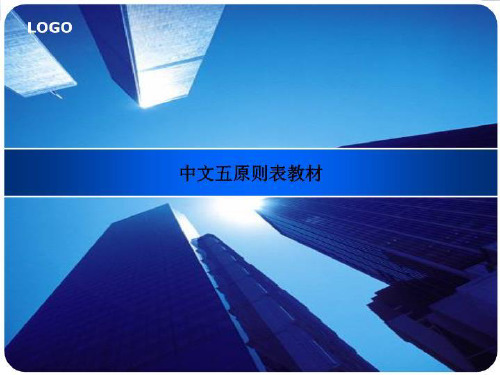
LOGO
4-4.把握事实-制造现场检证(sizing和浸油)
1.整型油塗布
浸油後临时放在鉄板上
5.<現場確認>・・・基準、標準的妥当性和实际作業 对照 对①.作標 ②.点検表 ③.検基 ④.条件表 の妥 当性及⑤.基準、標準的作業遵守状態进行確認
3.工程検証結果
油 2.临时放置鉄板
工程名
・型内有鉄異物的付着
鉄板上附有鉄屑異物
3.歯形 検査
× 歯型0.007 ・歯形的歯顶塌边基準未明記
㎜以内
(検基不恰当) ・歯顶塌边基準有図面指示
忽略了
4-5.把握事实-制造现场检证( sizing)
6.<現場確認>・・・基準、標準的妥当性和实际作業
1.精整工序现场检查记录表 对照
①.作標 ②.点検表 ③.記録 ④.検査 与作業対
图2为产品精整过程示意图,上冲单向压制,从上方开始对产品施压。当有杂物存在时,产品会倾斜,被垫起 部分将与上冲首先接触,且所受到的压力逐渐增加;当产品进入阴模有效段后,产品的外径尺寸是略大于模 具尺寸的,因此产品的齿尖锐处会作用与阴模型腔,将阴模拉伤。
5-2.查明原因-发生(再現试验条件)
2.<再現試験>・・・以特性要因図、
2
WRONG PART SHIPPED 寄误品
0
UBLE PART Q'TY / TOTAL PART Q'TY
数量 / 总数 1,630/30,240
REPAIRABLE 理可能
歯 形
3
DAMAGE 伤痕
RUST 4 生锈
NOT REPAIRABLE 可修理
5
DEFECTIVE PART 故障件
歯先上り側
ITION OF NEXT LOT 现状
4-4.把握事实-制造现场检证(sizing和浸油)
1.整型油塗布
浸油後临时放在鉄板上
5.<現場確認>・・・基準、標準的妥当性和实际作業 对照 对①.作標 ②.点検表 ③.検基 ④.条件表 の妥 当性及⑤.基準、標準的作業遵守状態进行確認
3.工程検証結果
油 2.临时放置鉄板
工程名
・型内有鉄異物的付着
鉄板上附有鉄屑異物
3.歯形 検査
× 歯型0.007 ・歯形的歯顶塌边基準未明記
㎜以内
(検基不恰当) ・歯顶塌边基準有図面指示
忽略了
4-5.把握事实-制造现场检证( sizing)
6.<現場確認>・・・基準、標準的妥当性和实际作業
1.精整工序现场检查记录表 对照
①.作標 ②.点検表 ③.記録 ④.検査 与作業対
图2为产品精整过程示意图,上冲单向压制,从上方开始对产品施压。当有杂物存在时,产品会倾斜,被垫起 部分将与上冲首先接触,且所受到的压力逐渐增加;当产品进入阴模有效段后,产品的外径尺寸是略大于模 具尺寸的,因此产品的齿尖锐处会作用与阴模型腔,将阴模拉伤。
5-2.查明原因-发生(再現试验条件)
2.<再現試験>・・・以特性要因図、
2
WRONG PART SHIPPED 寄误品
0
UBLE PART Q'TY / TOTAL PART Q'TY
数量 / 总数 1,630/30,240
REPAIRABLE 理可能
歯 形
3
DAMAGE 伤痕
RUST 4 生锈
NOT REPAIRABLE 可修理
5
DEFECTIVE PART 故障件
歯先上り側
ITION OF NEXT LOT 现状
中文五原则表教材ppt课件

①、生产设备:无变化
②、制造条件:精整工序模具出现不良 ③、生产要员:无变化(考勤)
④、检验要员:成品检验要员无变化 ⑤、作业标准:检验基准书、限度封样精没品有课件变化(检验基准书有疏漏)
4-3.把握事实-現物检证
4.<現物的確認>・・・不具合現物与基準、標準的 对照
1.不良品检查结果 与①.図面 ②.SPEC ③.HES ④.法規 検査対比
数量 / 总数 1,630/30,240
REPAIRABLE 理可能
歯 形
3
DAMAGE 伤痕
RUST 4 生锈
NOT REPAIRABLE 可修理
5
DEFECTIVE PART 故障件
歯先上り側
+11μ
ITION OF NEXT LOT 现状
HEAD
紧要
7
SARY
需要
ECESSARY 未需要
UNDIRO), Q'TY:
在不適合発生時,如不认真找出真正的原因的话,就无法取得有效的対策, 无法做到再発防止。
查明原因,并且为去除不適合的真正的発生原因,探讨为什么为什么, 到体制、体質、组织架构为止做调整,为做源流改善实施根据五原則的問題 解決。
精品课件
2.問題解決的流程
問題解決的五原則
1.发生状况: 発生状況
2.把握事实:
4-1.把握事实-推定要因
特性要因図 設備
型材質不適 型カジリ傷
作動不良
模具拉伤
油量少い
人
产品附着杂物未检查
检查不 仔细
责任心不强
工件放置未检查
材料成分不適 異材
检查作业指导书不完善
流出不良没跟踪控制
工艺流程变化
精益生产五大原则培训课件PPT(共 47张)

三、价值流
价值流为精益生产中最精彩的部分。经过第 二步的价值流分析,对于保留下来的创造价值的 活动和一型浪费活动应策划使其流动起来。
传统的观点认为应该将各种活动按类型分组 而利于管理,比如在生产现场将所有的车床布置 在一起,将所有的刨床布置在一起,从事相同工 作的人形成一个班组,如车床班、刨床组。这种 观点在传统的职能制组织结构下表现为分工明确 的几个部门:财务部、设计部、采购部、检验部 等。
创造的。来自欧洲,尤其是德国的大多数企业的 高层管理者通常持有此种想法,认为产品的价值 是生产者创造的,生产者的劳动是产品价值形成 的原因,也是生产者之存在的理由,所以他们热 衷于提高他们产品的性能和生产工艺的水平,然 后向他们的顾客去介绍和推销自己的产品,虽然 他们的产品功能在用户看来并不实用。生产者创 造了产品的价值,但并不是定义了产品的价值, 德国企业的这种想法是供小于求、以产定销时代 的缩影。
福特将轿车总装生产转变为连续流动 生产,使福特的T型车的总装工作量减少了 90%,同样,将产品从接到订单到发货中 的活动按照流水线的原理设计也将大大提 高效率,保证按期向顾客交货。
精益生产方式的价值流动原则要求企 业重新定义职能、部门和企业的作用,使 他们能对创造价值做出积极的贡献;说明 价值流上每一点的员工的真正需要,因此, 使价值流动起来才真正符合员工的利益。 这不仅要求为每种产品建立精益企业,还 应该重新思考传统的企业、职能、职业, 重新考虑精益战略的发展。
运 输
来 料 检 验
原 料 存 储
搬 运 和 等 待
加 工
检 验 及 返 工
成 品 存 储
成 品 发 运
货 款 回 收
制造周期
交付周期
精益生产方式依存于五大基本原则: • 价值 • 价值流 • 价值流动 • 需求拉动 • 尽善尽美
精益生产五大原则PPT课件

在一旁监视这种高速度的机器,一看到不
正常的情况时,立即停止机器。为了拥有
一部高速度的机器,就必须指定专人为其
服务。像这样的设计,至少应装设有不合
格品一旦产生时,就能立即停止下来的机
构。
精选ppt
27
供应商经常抱怨与顾客交易时,有太多 的文书及设计变更的工作。就广义而言,此 两种问题也是浪费。减少官僚作风、作业流 线化、剔除不必要的流程及加速决策制订时 间,是可以剔除文书作业的浪费。过多的设 计变更,产生重修的浪费。如果人员第一次 就把工作做对—假如他们对顾客、供应商及 自己的现场有较佳的了解,就可以消除设计 变更的浪费。改善可以有效地实用于工程项 目上,就如同在现场的工作改善一样。
采 购 下 单
供 应 商 备 料
运 输
来 料 检 验
原 料 存 储
搬 运 和 等 待
加 工
检 验 及 返 工
成 品 存 储
成 品 发 运
货 款 回 收
制造周期
交付周期
精选ppt
4
精益生产方式依存于五大基本原则: • 价值 • 价值流 • 价值流动 • 需求拉动 • 尽善尽美
精选ppt
5
精选ppt
精益生产五大基本原则 和七大浪费
精选ppt
1
精益生产方式是继单件生产方式和大量生 产方式之后在日本丰田汽车公司诞生的全 新生产方式。这种生产方式与传统的生产 方式相比,具有非常卓越的模式,是具有 几千年历史的工业生产方式的巨大变革。 同时精益生产的思想又被广泛的应用于传 统制造业之外的行业,如服务业、物流运 输业、饮食业等,并且推行十分成功。
精选ppt
17
为什么如此呢?企业满足上述四个原则后,愈想 真正的满足用户的要求,让价值流动的更快一些, 就越能暴露出价值流过程中的瓶颈和障碍,企业就 会不断的改善这些瓶颈,去除障碍,满足用户的要 求。
- 1、下载文档前请自行甄别文档内容的完整性,平台不提供额外的编辑、内容补充、找答案等附加服务。
- 2、"仅部分预览"的文档,不可在线预览部分如存在完整性等问题,可反馈申请退款(可完整预览的文档不适用该条件!)。
- 3、如文档侵犯您的权益,请联系客服反馈,我们会尽快为您处理(人工客服工作时间:9:00-18:30)。
规格
±0.15
±0.1
21.0
0 -0.5
24.0 29.0 31.444
-0.1
-0.28 +0.05
-0.25 0
-0.06
29.44
0 -0.03
93.7 ±0.1
93.0 ±0.1
0.03以内
0.06以内
实测值
X方向 Y方向 -0.17 -0.13
-0.09 -0.17 -0.28 -0.75 -0.25 -0.75 -0.026 -0.140 -0.02 -0.025 -0.07 -0.08 -0.05 -0.06
3.杯部C位置也有黑皮残留.
五原则表培训
8 2006年07月04日
【 查明原因】
1.不良发生的过程及其原因: 不良现象的出现过程进行分析
2.不良流出的过程及其原因: 对不良流出的过程进行分析
3.真正原因的确认:
最终确认不良发生及流出的主要原因
4.再现试验结果:
安排主要原因的再现试验及记录其结果
五原则表培训
0.15 不能测量
判定
NG NG NG NG NG NG OK OK OK NG NG
*能够得出的结论:
1.在A部位有宽20mm,长 24mm的黑皮残留
4.各个部分的黑皮在同一水平线上. 5.不良品是SDC-A500的D级.
2.在花键B部位,有宽24mm, 长33mm的黑皮残留.
6.该不良品不能装进轮毂.
五原则表培训
6 2006年07月04日
【 把握事实】
1.不良品的确认结果: 与标准的材质和尺寸进行比较 2.问题点的主要原因分析和结果:
从人、机、料、法、环等方面进行分析,确定变化点(鱼刺图) 3.工艺调查:对当时的加工工艺条件进行调查,确定变化点
4.不良原因推测: 根据变化点分析,推测出导致不良的主要原因
对应于部品表的零件编号
日期
批准日期
提出部门
批准
审核
管理科
自制品质系
审核
发现区域检技
自制品质不良主要由管理科提出五原则对策要求及跟踪推进!
日期
批准
编制部门 检技 系长
班长
编制
编制日期 科 长 副 科 长 检技
系长
班长
担当
责任部门负责五原则表的编制,由检查技术者审核后,交由科长批准!
五原则表培训
4 2006年07月04日
9 2006年07月04日
要因分析・…(轴部黑皮不良要因调查)
从工件的加工精度上分析,球道沟槽跳动大的问题,只有可能发生在以球道沟槽为基准,进 行中心孔加工的工程上. 中心孔加工工程要因調査
項 目
发 机种切换 生 设备故障
不 良 记录
要因 机 种切换有问题 夹具的定位 夹具压力的设定 夹有铁屑
調 査 結 果 无 机 种切换 要 求 值为设定为1.0mm以 上 , 实绩值为1.9mm,ok 设定值为4~ 6kg/cm2, 实绩值为5 k g / c m 2 , o k 5月 13日 ,有 因 夹有铁屑造成的不良记录
车削 040506-010-003 5月06日 4号线 第三批次 1s
8.不良对象机种 车削4号线在流动的全机种
SDC-A500/SJK-3000/SX0-9500/S7S-9500/S2A-9500
9.全检处理 ・5/28 在库品实行全检 11955个
(Assy完成5113套 COMP品5326个 单品1516个)不良品 0个
2004年05月27日 铃鹿工厂
3.不良内容 4.发生件数
在螺纹部发现有黑皮残留的不良品 1件
5.发生机种
44150-SDC-A500
6.零件等级
D等级
7.发生批次
装配卡箍号 453033812
研削 040524-010-003 5月24日 2号线 第三个批次 1s
热处理 040524-010-002 5月24日 2号线 第二个批次 3s
4
对策效果确认(效果实绩)
效果验证
对策制定
5
对问题源头的反馈
步骤
1
内 发生 容 流出
2
3
4
为何,为何分析
5
源流反馈
五原则表培训
3 2006年07月04日
【 标题栏填写说明 】
发生的问题:
缸体变速箱侧 定位销孔偏紧源自零件名称 PWC缸体 零件号 11000-PWC-0202
对发生的问题进行简要的描述 问题零件的名称
发生的问题:
零件名称 零件号
提出部门
标题栏日期 批准 审核 审核
日期
批准
编制部门 检技 系长
班长
编制
1-A
发生状况(现象、申诉内容、发生次数、处置内容)
1-B 把握事实(对零部件的确认结果、原因分析、现在正在生产的零件的品质状况)
发生状况
把握事实
2
查明原因(“WHY
WHY”分析)
查明原因
3
采取适当的对策(对策内容、效果预测PPA)
五原则表的使用方法介绍
培训资料
五原则表培训
1 2006年07月04日
目
录
《五原则表》填写概要说明 《发生状况》的目填写要领
《把握事实》的填写要领 《查明原因》的填写要领 《采取适当对策》的填写要领 《对策效果确认》的填写要领 《对源头的反馈》的填写要领
五原则表培训
2 2006年07月04日
解解决决问问题题的的5原五则原工则作表表
【 发生状况】
1.发生地:
不良现象发现的地理位置
2.发生年月日: 不良现象的发生日期
3.对象零件部位: 出现不良的零部件的具体位置及不良内容
4.批次号码:
不良品所在的不良批次号码
5.不良现象的发生条件: 在什么条件下出现了不良 6.不良是如何被发现的: 正常检查/偶然发现/设备发现/人发现/作业标准有无要求
5.不良品范围:可能出现的不良品批次范围和数量
五原则表培训
7 2006年07月04日
【 把握事实】 例
A部
①
Y
方
向
③
④ X方向
⑤
B部 ⑥
⑦
C部
⑩
⑧
⑨
測定箇所
① 中心孔深度
② 小端面位置
③ 螺纹上部轴径
④ 螺纹大径
⑤ 花键大径
⑥ OP径
⑦ 导向径
⑧ 外圆直径 φ93.7
⑨
φ90.7
⑩ 沟槽震动
⑪ 两针距
关联 × × × ○
再现性试验1…让球道内夹上铁粉进行加工. 在轴部出现有同样的黑皮 (球道内残留有铁屑的伤痕)
再现性试验2…让支撑块夹有铁屑进行加工
没有出现轴部黑皮 (即使夹有铁屑,工件的芯位置还是没有倾斜)
7.里程/时间: 对应市场的不良反馈,需要明确整车的里程和时间
8.曾经处理该车/零件的方法和程序: 简要的描述过往该类问题的处理经验
9.紧急对策:
发现问题后采用了哪些紧急对策
10.前后批次的确认结果:对不良问题的前后批次全检结果的描述
五原则表培训
5 2006年07月04日
【 发生状况】例
1.发生日期 2.发生场所