方壳型底座铸造工艺设计开题报告
罩壳压铸模 开题报告

国内外研究现状:
如今压铸已成为最先进的金属成型方法之一。近年来我国在压铸模设计、制造方面均有明显提高,能满足汽车行业部分需求及基本上满足摩托车、家电、电机、仪表、轻工等行业的需要。但是我国的压铸模存在使用寿命偏短,可靠性较差以及在压铸模的设计和制造方面进展较为缓慢,目前仍主要依靠设计人员的经验进行等缺陷。
3.按学校论文文本标准编写毕业设计说明书(8000字以上),翻译3000字以:表中一至六栏由学生填写
[5]赖华清主编.压铸工艺及模具.机械工业出版社,2005.
[6]械设计手册编写组.机械设计手册(1~5册).[M] 北京:机械工业出版社,1998.
七、指导教师意见:
1..按论文设计题目要求,查阅搜集、使用相关资料设计手册等,进行毕业设计;
2.绘制模具装配图、型芯及镶块等重要零件图,至少完成3张零号图的工作量;
发展趋势:
现代压铸模具的主要发展趋势是向精密、复杂、大型模具方向发展,缩短模具的制造周期,提高模具的加工质量,努力延长压铸模使用寿命,降低生产成本,提高产品竞争力。
三、本课题研究内容:
1、研究目标:
在指导老师的指导下,设计出一套结构简单、制造精度高的上盖压铸模具。
2、研究内容:
(1)、对压铸件进行工艺性分析,并绘制产品毛坯图。
(3)、根据有关模具的知识,设计模具总装图方案。
(4)、比较方案,最后确定方案。
(5)、绘制总装图和零件图。
(6)、成型零件的造型设计。
(7)、编制技术说明书。
五、主要特色及工作进度:
起止时间:2010 年 11 月 1 日至 2011 年 5 月 20 日
序号
工作内容
起止日期
备注
方壳型底座铸造工艺与设计
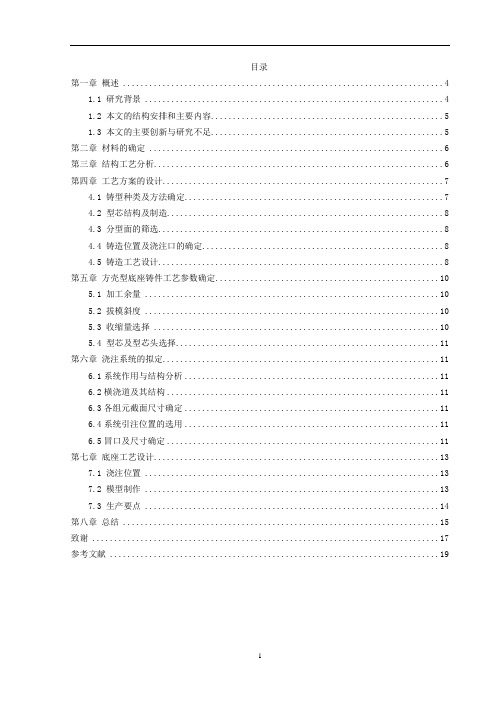
目录第一章概述 (4)1.1 研究背景 (4)1.2 本文的结构安排和主要内容 (5)1.3 本文的主要创新与研究不足 (5)第二章材料的确定 (6)第三章结构工艺分析 (6)第四章工艺方案的设计 (7)4.1 铸型种类及方法确定 (7)4.2 型芯结构及制造 (8)4.3 分型面的筛选 (8)4.4 铸造位置及浇注口的确定 (8)4.5 铸造工艺设计 (8)第五章方壳型底座铸件工艺参数确定 (10)5.1 加工余量 (10)5.2 拔模斜度 (10)5.3 收缩量选择 (10)5.4 型芯及型芯头选择 (11)第六章浇注系统的拟定 (11)6.1系统作用与结构分析 (11)6.2横浇道及其结构 (11)6.3各组元截面尺寸确定 (11)6.4系统引注位置的选用 (11)6.5冒口及尺寸确定 (11)第七章底座工艺设计 (13)7.1 浇注位置 (13)7.2 模型制作 (13)7.3 生产要点 (14)第八章总结 (15)致谢 (17)参考文献 (19)论文版面格式:方壳型底座铸造工艺设计摘要:在中华文明5000多年的历史的创造过程中,铸造生产做出了巨大的贡献。
方壳型铸造在机械制造业中的地位是特别的重要的。
她不会因为质量、尺寸、材料种类及生产批量而受到限制。
而用于装轴瓦的部分总称壳件,轴承盖是它的上半部分,滑动轴承座是她的下半部分。
滑动轴承座设计。
滑动轴承座主要由材料为HT200或Zg200~Zg400的铸铁制成。
大面积运用于冶金、矿山、运输系统、环保设备。
滑动轴承座在铸造过程中的技术要求特别的严苛。
通过对滑动轴承座的研究,获得了滑动轴承座的铸造工艺。
根据铸件和生产数量的要求,复杂薄壁基础铸件的结构特点和技术难点得到了分析,并进一步优化了工艺措施。
经过我们的实验证明:选择对的浇注位置,使用合理的冒口,工艺补贴及冷铁、砂芯等多种工艺措施生产,能有效解决基础型腔加工面尺寸变小的问题,大大提高铸件的合格率。
铸造工艺模拟设计开题报告

铸造工艺模拟设计开题报告一、研究背景与意义1.1 研究背景铸造是一种制造工艺,通过将熔化的金属或合金注入模具中并使其冷却凝固,用于制造各种形状的零部件。
铸造工艺的优化对于提高产品质量、提高生产效率以及节约资源具有重要意义。
随着计算机技术的发展,仿真软件开始在铸造工艺中得到广泛应用,通过数值模拟可以准确预测铸造工艺的各种参数以及最终产品的性能,从而指导实际生产。
1.2 研究意义本项目旨在利用现代数值模拟技术,并结合实际工艺参数和实验数据,对铸造工艺进行模拟设计。
通过对铸造过程的数值仿真,可以降低试验次数和试验成本,提高产品质量,优化工艺参数,同时减少环境污染。
二、研究目标和研究内容2.1 研究目标•建立铸造工艺的模拟设计方法;•通过数值仿真,预测铸造过程中的温度分布、相变、应力和变形等关键参数;•优化工艺参数,提高产品质量和生产效率。
2.2 研究内容1.收集和整理铸造工艺相关的文献资料;2.借助仿真软件,建立铸造工艺数值模型;3.定义模型中的物理参数,包括材料属性和工艺参数;4.进行铸造过程的数值模拟,预测温度、相变、应力和变形等参数;5.分析模拟结果,优化工艺参数;6.验证模型的准确性和可靠性。
三、研究方法和技术路线3.1 研究方法本项目主要采用以下研究方法:1.文献调研:收集和整理与铸造工艺模拟设计相关的文献资料,了解当前研究状况和存在的问题;2.数值模拟:借助专业仿真软件,建立数值模型并模拟铸造过程,预测关键参数;3.实验验证:通过对比模拟结果与实际铸造结果进行验证,评估模型的准确性和可靠性。
3.2 技术路线1.数据收集:收集铸造工艺的相关数据,包括材料性能、工艺参数等;2.建立数值模型:利用仿真软件建立铸造工艺的数值模型,并进行网格划分;3.定义物理参数:根据实际情况,设置材料属性和工艺参数;4.数值模拟:运用数值方法求解模型,并得到预期结果;5.分析优化:对模拟结果进行分析和优化,调整工艺参数;6.实验验证:与实际铸造结果进行对比,评估模型的准确性和可靠性。
壳型铸造可行性研究报告

壳型铸造可行性研究报告一、研究背景壳型铸造是一种常用的铸造工艺,通过使用砂型和壳型来制造金属铸件。
它具有精度高、表面光滑、成型周期短等优点,在航空航天、汽车制造、机械制造等领域有广泛应用。
在进行壳型铸造工艺时,需要对铸造工艺参数、材料性能、成本效益等进行全面分析和研究,以保证产品质量和生产效率。
因此,本报告旨在深入分析壳型铸造的可行性,为企业的生产提供决策支持。
二、研究目的1. 研究壳型铸造工艺的优劣势,为企业提供技术支持和决策参考。
2. 分析壳型铸造中涉及的各项工艺参数和材料特性,探索其对产品质量的影响。
3. 研究壳型铸造在成本方面的优势,评估其在生产中的经济效益。
4. 提出相应的建议,为企业在进行壳型铸造时提供参考。
三、研究内容1. 壳型铸造工艺综述(1)壳型铸造工艺流程分析(2)壳型铸造工艺优劣势分析2. 壳型铸造工艺参数分析(1)铸造温度、压力、速度等工艺参数对产品质量的影响(2)涂料、抗蚀剂等材料性能对壳型铸造工艺的影响3. 壳型铸造成本分析(1)壳型材料成本和使用寿命分析(2)壳型铸造与其他铸造工艺的成本对比4. 壳型铸造工艺优化方案(1)工艺参数优化建议(2)材料选择和使用建议(3)成本降低建议四、研究方法1. 文献综述法:通过查阅大量文献,了解壳型铸造工艺的发展历程和应用情况。
2. 实地调研法:走访多家壳型铸造企业,了解其生产工艺和经验做法。
3. 数据分析法:收集各类壳型铸造工艺参数、材料性能和成本数据,进行统计分析。
4. 专家访谈法:邀请行业专家进行深入访谈,获得对壳型铸造工艺的专业见解。
五、研究成果1. 壳型铸造工艺的优劣势分析:壳型铸造工艺优势在于成型精度高、表面光滑,但也存在周期长、成本高等劣势。
2. 壳型铸造工艺参数分析:铸造温度、压力、速度等工艺参数对产品质量的影响较大,需精细调控。
3. 壳型铸造成本分析:壳型材料成本占比较大,但在长期使用中成本效益较高。
4. 壳型铸造工艺优化方案:建议在工艺参数、材料选择和成本控制方面进行优化,提高生产效率和经济效益。
铸造方案设计

铸造方案设计铸造工艺方案设计,是整个铸造工艺及工装设计中最基本而又最重要的部分之一。
正确的铸造工艺方案,可以提高铸件质量,简化铸造工艺,提高劳动生产率。
铸造工艺方案设计的内容主要有:铸造工艺方法的选择;铸件浇注位置及分型面的选择;铸件初加工基准面的选择;铸造工艺设计有关工艺参数的选择,型芯的设计等。
一、铸造工艺方法的选择目前铸造方法的种类繁多,按生产方法可分为砂型铸造和特种铸造两大类,而砂型铸造按浇注时砂型是否经过了烘干又分为湿型、干型、表面干型和自硬型铸造。
特种铸造可分为金属型铸造、压力铸造、低压铸造、离心铸造、壳型铸造,熔模铸造、陶瓷型铸造,等等。
各种铸造方法都有其特点和应用范围,究竟应该采用哪一种方法,应根据零件特点、合金种类、批量大小、铸件技术要求的高低以及经济性加以综合考虑。
1.零件结构特点零件的结构特点主要包括铸件的壁厚大小、形状及重量大小等,应根据不同铸件的结构特点选择合适的铸造工艺方法。
(1)砂型铸造的特点①由于内部砂芯、活块模样、气化模及其他特殊的造型技术等有利条件,可以生产结构形状比较复杂的铸件。
②铸件的大小和重量几乎不受限制,铸件重量一般是几十克到几百千克。
③砂型铸造对铸件最小壁厚有一定限制。
(2)熔模铸造的特点①可以铸出形状极为复杂的铸件,其复杂程度是任何其他方法难以达到的。
虽然一个压型所能制出的熔模形状较简单,但可用几个压型分别制出复杂零件的不同部分,然后焊合在一起,组成复杂零件的熔模。
②熔模铸造可铸出清晰的花纹、文字。
③能铸出孔的最小直径可达0.5mm,铸件的最小壁厚为0.3mm,但不宜铸造壁厚大的铸件。
其比较适宜生产的铸件重量为几十克至几千克,但它能生产的铸件重量为几克至几十千克。
(3)金属型铸造的特点①金属型铸造的铸件重量范围一般为0.1~135kg,个别可达225kg。
②由于金属型的型腔是用机械加工方法制出的,所以铸件的结构形状不能很复杂,更应考虑从铸型中取出铸件的可能性。
壳型铸造工艺

壳型铸造工艺壳型铸造工艺壳型铸造工艺是一种常见的金属铸造工艺,广泛应用于各个领域的制造业中。
它以其高精度和良好的表面质量而受到重视。
在本文中,我将深入探讨壳型铸造工艺的原理、应用和发展前景,并分享我对该工艺的观点和理解。
作为一种近几十年来发展迅猛的铸造工艺,壳型铸造工艺通过制作具有空腔的模具来实现金属制品的生产。
其基本原理是在充填模腔的过程中,通过模具表面上的壳层材料固化形成壳体。
待模具内的金属液体冷却凝固后,壳体即可被拆除,从而得到所需的金属制品。
值得一提的是,壳型铸造工艺在铸造精度方面有着较大的优势。
相比传统的砂型铸造工艺,壳型铸造能够制造出更为精细的铸件。
这得益于壳型铸造工艺中所使用的耐高温的耐火材料,它们能够承受高温条件下的熔融金属,并保持壳体的稳定性。
另外,由于模具外壳较为坚硬,不易变形,壳型铸造还能够生产出具有较高表面质量和复杂结构的零件。
相较于其他几种常见的铸造工艺,壳型铸造工艺在这些方面具有明显的优势。
壳型铸造工艺在各个行业有着广泛的应用。
例如在航空航天领域,壳型铸造工艺常被用来生产高温合金零件、涡轮叶片等。
由于这些零件通常需要具备高强度和耐腐蚀性能,而壳型铸造工艺能够提供高精度和高质量的铸造件,因此成为了最佳选择。
在汽车制造领域,壳型铸造工艺可以用于生产发动机零部件、变速箱外壳等。
壳型铸造工艺还被广泛应用于船舶、军事装备、工程机械等领域。
随着科技的不断进步,壳型铸造工艺也在不断改善和创新。
近年来,随着数控(Computer Numerical Control, CNC)技术的发展,壳型铸造工艺与CNC技术的结合越来越紧密。
通过CNC技术,可以实现对铸型的精确加工和控制,进一步提高铸件的精度和质量。
3D打印技术的快速发展也为壳型铸造工艺提供了新的可能性。
通过3D打印技术,可以快速制作出复杂形状的铸型,减少模具制作的时间和成本。
壳型铸造工艺在金属制品制造领域具有广泛的应用前景和发展潜力。
底座铸造毕业设计

底座铸造毕业设计底座铸造毕业设计毕业设计是每个大学生的重要任务,它不仅是对所学知识的综合运用,更是对个人能力和专业素养的一次全面检验。
作为一名机械工程专业的学生,我选择了底座铸造作为我的毕业设计课题。
底座是机械设备的重要组成部分,它承载着整个设备的重量,并提供稳定的支撑。
底座的质量和结构设计直接影响着设备的稳定性和使用寿命。
因此,我决定通过铸造的方式来制造底座,以确保其质量和性能。
首先,我进行了底座的结构设计。
通过对不同类型设备的分析和研究,我确定了底座的形状和尺寸。
底座需要具备足够的强度和刚性,以承受设备的重量和外部力的作用。
同时,底座还需要考虑到设备的布线和维修保养的便利性。
在结构设计中,我采用了CAD软件进行三维建模和仿真,以确保底座的结构合理性和稳定性。
接下来,我进行了底座的材料选择。
底座需要具备高强度、耐磨损和耐腐蚀等特性。
在材料选择上,我综合考虑了铸造工艺的可行性和材料的性能要求。
最终,我选择了一种高强度铸铁材料作为底座的材料。
这种材料具有良好的铸造性能和机械性能,能够满足底座的使用要求。
然后,我进行了底座的铸造工艺设计。
铸造是将熔融金属注入到模具中,经过冷却凝固形成所需零件的一种制造方法。
在底座的铸造过程中,我需要考虑到金属的熔化温度、浇注温度和冷却速度等因素。
通过合理控制这些参数,可以获得高质量的底座铸件。
为了提高铸件的表面质量和减少缺陷,我还采用了一些先进的铸造技术,如真空铸造和气体保护铸造。
最后,我进行了底座的加工和装配。
铸造得到的底座铸件需要进行后续的加工和装配,以满足设备的安装和使用要求。
在加工过程中,我采用了数控加工技术和精密测量设备,以确保底座的尺寸和形状的精度。
在装配过程中,我还进行了一系列的功能测试和质量检验,以确保底座的性能和可靠性。
通过这次底座铸造的毕业设计,我不仅学到了很多有关铸造工艺和机械设计的知识,更锻炼了自己的实践能力和解决问题的能力。
我深刻体会到了工程实践的重要性和挑战性,也更加明确了自己未来的发展方向。
浇铸模具开题报告

浇铸模具开题报告一、选题背景浇铸模具是金属铸造过程中使用的一种关键设备,它用于将熔化的金属液倒入模具中,经冷却后获得所需形状的金属制品。
浇铸模具的设计和制造对于金属铸造工艺的质量和效率起着至关重要的作用。
如何设计出结构合理、制造工艺优良的浇铸模具,是当前金属铸造领域的研究重点之一。
因此,我们选取了浇铸模具设计和制造作为开题研究的课题。
二、研究目的本项目旨在通过对浇铸模具设计和制造技术的研究,探索出一种能够提高金属铸造工艺质量和效率的浇铸模具设计方法,为金属铸造行业的发展做出贡献。
三、研究内容本研究将从以下几个方面展开:1. 浇铸模具的结构设计通过分析金属铸造工艺的要求,研究浇铸模具的结构设计原理和方法。
探究不同材料、不同形状的金属制品所需的浇铸模具结构设计特点,寻找出最优的设计方案。
2. 浇铸模具材料的选择研究不同材料的特性和适用范围,选择合适的材料作为浇铸模具的制造材料。
考虑到浇铸模具在使用过程中遇到的高温、高压等工况,需保证所选材料具有良好的耐热、耐压性能。
3. 浇铸模具制造工艺研究浇铸模具的制造工艺,包括模具的制造流程、工艺参数的调整以及制造设备和工具的选取。
通过改进制造工艺,提高浇铸模具的质量和效率。
4. 浇铸模具质量控制与检测方法研究浇铸模具的质量控制方法和检测技术。
通过建立一套完善的质量控制体系,对浇铸模具进行质量检测和评估,确保浇铸模具的稳定性和可靠性。
四、预期成果通过本项目的研究,我们期望能够获得以下成果:1.提出一种能够满足金属铸造工艺要求的浇铸模具设计方法。
2.确定一种适用于不同工况的浇铸模具制造材料。
3.优化浇铸模具的制造工艺,提高制造效率和成品质量。
4.建立一套完善的浇铸模具质量控制体系,提供有效的质量检测方法。
五、研究方法及进度安排为完成上述研究目标,我们将采用以下研究方法:1.文献资料的查阅和分析:对已有的浇铸模具设计和制造相关的文献进行综述,总结归纳已有成果和方法。
(完整word版)铸造工艺课程设计说明书

铸造工艺课程设计说明书目录1 前言 (4)1。
1本设计的意义 (4)1.1.1 本设计的目的 (4)1.1。
2 本设计的意义 (5)1.2本设计的技术要求 (5)1。
3本课题的发展现状 (5)1.4本领域存在的问题 (6)1.5本设计的指导思想 (6)1。
6本设计拟解决的关键问题 (7)2 设计方案 (7)2。
1零件的材质分析 (8)2.2支座工艺设计的内容和要求 (9)2.3造型造芯方法的选择 (11)2。
4浇注位置的选择与分型面的选择 (12)2。
4.1 浇注位置的选择 (12)2.4.2 分型面的确定 (14)2.4.3 砂箱中铸件数目的确定 (15)3 设计说明 (17)3。
1工艺设计参数确定 (17)3。
1.1 最小铸出的孔和槽 (17)3.1.2 铸件的尺寸公差 (18)3。
1.3 机械加工余量 (19)3。
2铸造收缩率 (19)3。
2。
1 起模斜度 (20)3.2。
2 浇注温度和冷却时间 (21)3。
3砂芯设计 (22)3.3。
1 芯头的设计 (22)3。
3。
2 砂芯的定位结构 (23)3。
3.3 芯骨设计 (23)3.3.4 砂芯的排气 (23)3。
4浇注系统及冒口,冷铁,出气孔的设计 (24)3。
4.1 浇注系统的类型和应用范围 (24)3。
4。
2 确定内浇道在铸件上的位置、数目、金属引入方向 (24)3.5决定直浇道的位置和高度 (25)3.5.1 计算内浇道截面积 (25)3.5.2 计算横浇道截面积 (26)3。
5。
3 计算直浇道截面积 (27)3。
5.4 冒口的设计 (27)4 铸造工艺装备设计 (28)4。
1模样的设计 (28)4。
1.1 模样材料的选用 (28)4.1。
2 金属模样尺寸的确定 (29)4。
1。
3 壁厚与加强筋的设计 (29)4。
1。
4 金属模样的技术要求 (29)4.1。
5 金属模样的生产方法 (29)4.2模板的设计 (30)4。
2。
1 模底板材料的选用 (30)4.2。
壳型铸造工艺及装备研发生产方案(一)

壳型铸造工艺及装备研发生产方案一、实施背景随着制造业的不断发展,高效、环保、节能已成为铸造行业的重要发展方向。
壳型铸造工艺作为一种先进的铸造技术,具有较高的生产效率、较低的能耗和良好的产品质量,因此受到广泛关注。
然而,国内壳型铸造工艺及装备研发生产方面仍存在一定的问题,如技术水平不高、生产效率低下、产品质量不稳定等,难以满足市场需求。
因此,开展壳型铸造工艺及装备研发生产具有重要的现实意义和市场需求。
二、工作原理壳型铸造工艺是一种利用覆膜砂或其他类似材料制成的壳型进行浇铸的工艺方法。
其主要工作原理包括以下几个方面:1.覆膜砂制壳:利用覆膜砂材料,通过喷射、流化等手段制成具有一定厚度的壳型,其内部为空心结构。
2.熔融金属浇铸:将熔融的金属液体通过浇口注入到壳型中,待金属液体冷却凝固后形成铸件。
3.脱壳、清理:经过一定时间的冷却后,打开壳型,取出铸件,进行表面清理及处理。
三、实施计划步骤1.需求分析:对市场需求进行调研,明确产品类型、规格、质量要求等。
2.技术研究:开展覆膜砂材料、制壳技术、熔融金属浇铸技术等方面的技术研究。
3.装备设计:根据实际需要,设计相应的制壳设备、浇铸设备等。
4.生产调试:对所研发的设备进行调试,确保其正常运行并逐步优化生产工艺。
5.批量生产:在确保产品质量和稳定性的前提下,逐步扩大生产规模,实现批量生产。
四、适用范围壳型铸造工艺及装备适用于各种大中小型铸件的生产,尤其适用于复杂形状、高精度要求的铸件。
在汽车、航空航天、船舶、机械制造等领域得到广泛应用。
五、创新要点1.采用新型覆膜砂材料:通过选用高性能的覆膜砂材料,提高壳型强度和耐高温性能,从而提高产品质量和生产效率。
2.制壳工艺优化:改进制壳工艺流程,实现自动化、智能化制壳,降低劳动强度,提高生产效率。
3.熔融金属高效浇铸:研究高效浇铸技术,提高金属熔融温度和浇注速度,减少能源消耗和废品率。
4.集成化装备设计:将制壳、浇铸、脱壳等工艺流程集成在一台或多台设备上,实现流水线生产,提高生产效率。
铸造开题报告
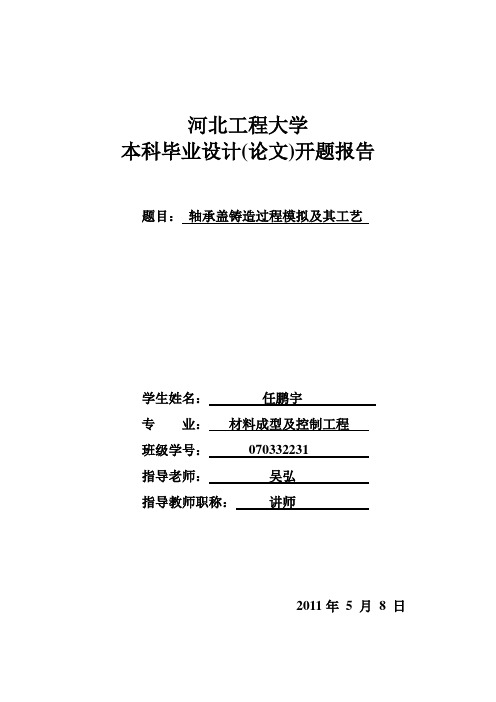
经过30多年的不断发展,铸造模拟在工程应用已是一项十分成熟的技术,已有很多商品软件,并已在生产中取得显著的经济及社会效益。目前,模拟仿真技术已能用在压力铸造、熔模铸造等精确成型制造工艺,而焊接过程的模拟仿真研究也取得可喜的进展。
本课题通过改变其浇注温度的高低和浇注速度的快慢,来观察对其内部的缩松缩孔的影响。从而为改进工艺方案提供意见。使铸件成品率能得以提高。
预期结果:
结合工艺设计,铸造过程数值模拟和实际的试验结果来完成产品的开发,从而建立一种新的开发产品的过程和方法。以便更好地对铸型结构及其配方进行设计,改进和提高,以适应时代的要求。铸造工艺CAD的发展和应用对铸造生产具有重大的意义和价值。但必须清楚地认识到铸造工艺CAD不是目的,而是手段。应用和加速发展铸造工艺CAD是为了铸造工艺的最优化设计、提高设计的质量和科学性、缩短设计的周期、保证铸件质量和提高经济效益。所以,从应用的角度上讲,各种数值模拟最终要服务于铸造工艺的优化设计。
4月2日至4月12日
4月14日至4月23日
4月25日至5月3日
5月5日至5月15日
5月17日至5月26日
指导教师意见:
签名:
年月日
系审核意见:
负责人签名:
年月日
阶段进度计划
序号
主要工作内容
起止日期
备注
第1、2周
第3、4周
第5、6周
第7、8周
第9、10周
第11、12周
第13、14周
参观实习,查看文献;
学习Pro/E;
学习华铸CAE;
铸造开题报告
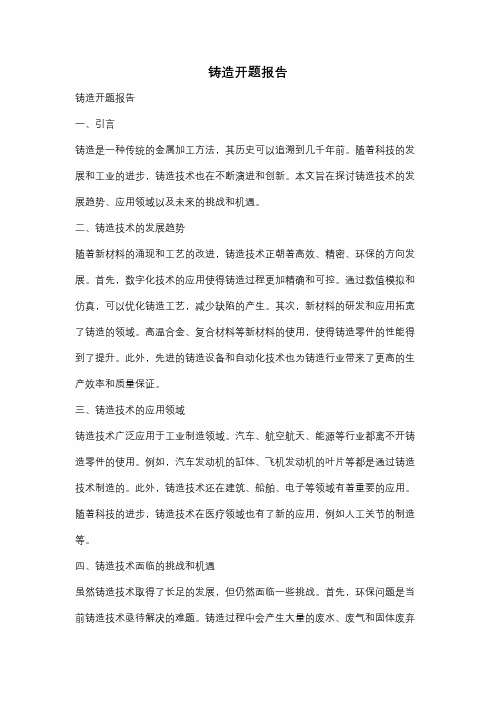
铸造开题报告铸造开题报告一、引言铸造是一种传统的金属加工方法,其历史可以追溯到几千年前。
随着科技的发展和工业的进步,铸造技术也在不断演进和创新。
本文旨在探讨铸造技术的发展趋势、应用领域以及未来的挑战和机遇。
二、铸造技术的发展趋势随着新材料的涌现和工艺的改进,铸造技术正朝着高效、精密、环保的方向发展。
首先,数字化技术的应用使得铸造过程更加精确和可控。
通过数值模拟和仿真,可以优化铸造工艺,减少缺陷的产生。
其次,新材料的研发和应用拓宽了铸造的领域。
高温合金、复合材料等新材料的使用,使得铸造零件的性能得到了提升。
此外,先进的铸造设备和自动化技术也为铸造行业带来了更高的生产效率和质量保证。
三、铸造技术的应用领域铸造技术广泛应用于工业制造领域。
汽车、航空航天、能源等行业都离不开铸造零件的使用。
例如,汽车发动机的缸体、飞机发动机的叶片等都是通过铸造技术制造的。
此外,铸造技术还在建筑、船舶、电子等领域有着重要的应用。
随着科技的进步,铸造技术在医疗领域也有了新的应用,例如人工关节的制造等。
四、铸造技术面临的挑战和机遇虽然铸造技术取得了长足的发展,但仍然面临一些挑战。
首先,环保问题是当前铸造技术亟待解决的难题。
铸造过程中会产生大量的废水、废气和固体废弃物,对环境造成严重污染。
其次,传统的铸造工艺存在一定的局限性,无法满足一些特殊零件的需求。
此外,铸造技术在高温合金、复合材料等新材料的应用上还有待突破。
然而,这些挑战也带来了机遇。
环保问题的解决将推动铸造技术向更加环保和可持续的方向发展。
新材料的研发和应用将为铸造技术带来更多的发展空间。
此外,数字化技术和自动化技术的进一步应用,将提高铸造过程的效率和质量,为铸造行业带来更多的机遇。
五、结论铸造技术作为一种传统的金属加工方法,经过几千年的发展,已经成为现代工业制造的重要环节。
随着科技的进步和工业的发展,铸造技术正朝着高效、精密、环保的方向发展。
铸造技术的应用领域广泛,涉及汽车、航空航天、能源等多个行业。
压铸开题报告模板
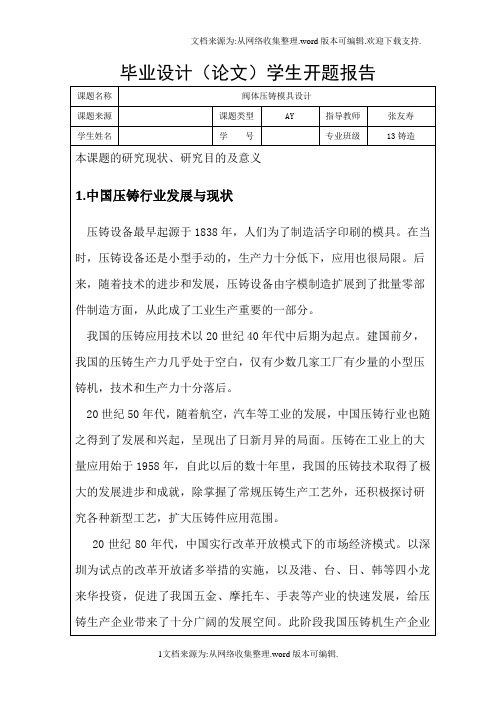
进度安排,共6周
第一周:分析零件结构工艺性,确定成型工艺和成型方案。
第二周:画出模具总装草图
第三周:选择压铸机并进行参数校核,对成型零部件尺寸进行计算。
第四周:模具结构计算
第五周:绘制模具总装图和零件图
第六周:撰写说明书.
开题报告(2)
已查阅的主要L].2017(03)
[2]杨裕国.压铸工艺与模具设计[M].北京:机械工业出版社,1993.
[3]中国压铸业发展历程与进步[J].耿鑫明.金属加工(热加工). 2010(19)
[4]邹剑佳.压铸产业发展战略研究[J].特种铸造及有色合金,2012,(12):1107-1110.
13铸造
本课题的研究现状、研究目的及意义
压铸设备最早起源于1838年,人们为了制造活字印刷的模具。在当时,压铸设备还是小型手动的,生产力十分低下,应用也很局限。后来,随着技术的进步和发展,压铸设备由字模制造扩展到了批量零部件制造方面,从此成了工业生产重要的一部分。
我国的压铸应用技术以20世纪40年代中后期为起点。建国前夕,我国的压铸生产力几乎处于空白,仅有少数几家工厂有少量的小型压铸机,技术和生产力十分落后。
[9]《陈金城,彭余恭.压铸机的发展[J].铸造,2005,(01):6-15.
[10]黄晓锋,谢锐,田载友,朱凯,曹喜娟.压铸技术的发展现状与展望[J].新技术新工艺,2008,(07):50-55+3.
[11]宋才飞.中国压铸市场分析与和谐发展[J].世界有色金属,2007,(05):42-44.
[12]周健波,田福祥.压力铸造的现状与发展[J].铸造设备研究,2006,(02):48-51.
铸造综合实验报告摘要
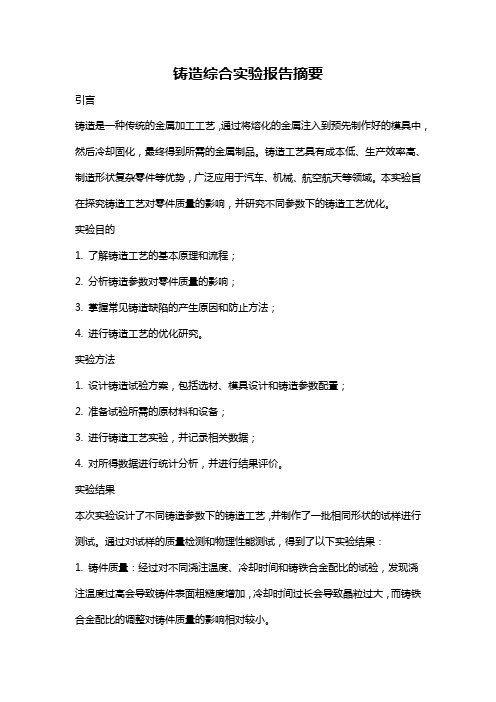
铸造综合实验报告摘要引言铸造是一种传统的金属加工工艺,通过将熔化的金属注入到预先制作好的模具中,然后冷却固化,最终得到所需的金属制品。
铸造工艺具有成本低、生产效率高、制造形状复杂零件等优势,广泛应用于汽车、机械、航空航天等领域。
本实验旨在探究铸造工艺对零件质量的影响,并研究不同参数下的铸造工艺优化。
实验目的1. 了解铸造工艺的基本原理和流程;2. 分析铸造参数对零件质量的影响;3. 掌握常见铸造缺陷的产生原因和防止方法;4. 进行铸造工艺的优化研究。
实验方法1. 设计铸造试验方案,包括选材、模具设计和铸造参数配置;2. 准备试验所需的原材料和设备;3. 进行铸造工艺实验,并记录相关数据;4. 对所得数据进行统计分析,并进行结果评价。
实验结果本次实验设计了不同铸造参数下的铸造工艺,并制作了一批相同形状的试样进行测试。
通过对试样的质量检测和物理性能测试,得到了以下实验结果:1. 铸件质量:经过对不同浇注温度、冷却时间和铸铁合金配比的试验,发现浇注温度过高会导致铸件表面粗糙度增加,冷却时间过长会导致晶粒过大,而铸铁合金配比的调整对铸件质量的影响相对较小。
2. 物理性能:通过对铸件的硬度、抗拉强度和冲击韧性等性能的测试发现,不同铸造参数下的铸件性能有所差异,但无明显规律可言。
可能是由于实验条件和样品数量有限的原因导致结果的不确定性。
实验讨论通过对实验结果的分析,我们可以得出以下结论:1. 浇注温度的控制对铸件表面质量有重要影响,应该根据具体铸件形状和材料进行合理选择;2. 冷却时间对铸件金相组织结构有影响,应根据所需物理性能进行优化;3. 铸铁合金配比对铸件质量的影响相对较小,应优先考虑其他参数的调整。
实验结论通过本次实验,我们对铸造工艺的基本原理和流程有了更深入的了解,探究了铸造参数对零件质量的影响,并研究了铸造工艺的优化方法。
然而,本次实验的样本数量和条件有限,实验结果还需进行更多验证和优化。
希望以后能进一步完善实验设计,提高实验数据的可靠性和可重复性。
低压铸造工艺设计毕业论文

摘要本文运用反重力铸造技术—低压铸造来对铝合金铸件带轮的铸造工艺进行方案设计,包括分型面、浇注位置的选择、各项铸造工艺参数的确定以及浇注系统的设计。
根据铸件形状较复杂的特点,在进行实验浇注时设计了两个浇注方案即两个内浇道或者一个内浇道,并同时进行调压和重力铸造浇注,以方便比较。
根据实际零件建立了铸件的三维模型,并用View-cast铸造模拟软件对铝合金铸件带轮的充型过程进行了模拟计算。
模拟结果显示,充型过程平稳,没有明显的液相起伏、飞溅。
根据数值模拟结果并结合理论分析,铸件中没有缩孔、缩松等缺陷,铸造工艺方案和浇注工艺参数的设计合理。
关键词:低压铸造;铸造工艺;实验浇注;充型过程;数值模拟AbstractIn this paper, anti-gravity casting technology, low pressure casting technology was used to complete the design of the casting of an aluminum alloy casting wheel, which include choice of Sub-surface and casting position, determining all of the parameters of the casting process, and the design of the casting system. For the complex shape of the casting, when conducting experiments was designed to use two runners and one ingate for casting in one time, and at the same time, surge and gravity casting was used to make it easier to compare. For sand shell moulding, the mode of same time freezing was generally used. Build the Three-dimensional model of the casting, then simulate and calculate the filling process of casting. Form the results, it was saw that the process was steady without apparent phase fluctuations or splash. From the result we can see that there was no defect such as shrinkage, so the design was perfect.Keywords:Low pressure die casting; casting process; experimental cast; filling process; numerical simulation.目录摘要 (I)ABSTRACT (II)第1章绪论 0低压铸造概述 0低压铸造的工艺过程 0低压铸造的工艺特点 (1)低压铸造的工艺分类 (3)国外低压铸造行业的发展概况 (4)我国低压铸造行业现状、存在的问题和发展趋势 (5)低压铸造的数值模拟 (7)计算机数值模拟的优点 (7)低压铸造与计算机数值模拟 (8)选题意义及本文的主要研究内容 (9)课题的意义 (9)课题的任务和内容 (10)第2章低压铸造工艺设计 (11)低压铸造铸型工艺参数的选择 (11)铸件凝固方式的选择 (12)浇注系统的选择 (13)浇注系统的选择 (14)机械加工余量的选择 (15)低压铸造浇注工艺参数的选择 (16)升液速度的确定 (16)充型压力和充型速度的选择 (16)充型增压值的选择 (17)保压增压值的选择 (17)保压时间的确定 (17)浇注温度的确定 (17)第3章实验材料、内容及过程 (19)实验材料 (19)实验设备 (19)反重力铸造设备主体 (19)反重力铸造多功能气路控制系统 (20)反重力铸造电控系统 (21)实验过程 (21)砂型制造 (21)浇注前的准备 (24)铸件的金相观察 (28)第4章充型过程数值模拟 (28)V IEW C AST的实现过程 (28)充型过程的计算机模拟 (29)前处理 (29)凝固过程模拟结果及分析 (32)结论 (34)参考文献 (35)致谢 (36)第1章绪论低压铸造概述低压铸造的工艺过程低压铸造是一种特种铸造工艺,它是巴斯加原理在铸造生产中的应用。
壳型铸造工艺
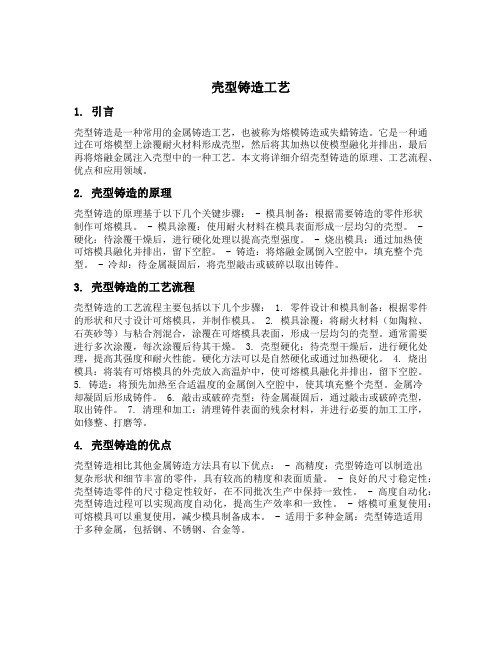
壳型铸造工艺1. 引言壳型铸造是一种常用的金属铸造工艺,也被称为熔模铸造或失蜡铸造。
它是一种通过在可熔模型上涂覆耐火材料形成壳型,然后将其加热以使模型融化并排出,最后再将熔融金属注入壳型中的一种工艺。
本文将详细介绍壳型铸造的原理、工艺流程、优点和应用领域。
2. 壳型铸造的原理壳型铸造的原理基于以下几个关键步骤: - 模具制备:根据需要铸造的零件形状制作可熔模具。
- 模具涂覆:使用耐火材料在模具表面形成一层均匀的壳型。
- 硬化:待涂覆干燥后,进行硬化处理以提高壳型强度。
- 烧出模具:通过加热使可熔模具融化并排出,留下空腔。
- 铸造:将熔融金属倒入空腔中,填充整个壳型。
- 冷却:待金属凝固后,将壳型敲击或破碎以取出铸件。
3. 壳型铸造的工艺流程壳型铸造的工艺流程主要包括以下几个步骤: 1. 零件设计和模具制备:根据零件的形状和尺寸设计可熔模具,并制作模具。
2. 模具涂覆:将耐火材料(如陶粒、石英砂等)与粘合剂混合,涂覆在可熔模具表面,形成一层均匀的壳型。
通常需要进行多次涂覆,每次涂覆后待其干燥。
3. 壳型硬化:待壳型干燥后,进行硬化处理,提高其强度和耐火性能。
硬化方法可以是自然硬化或通过加热硬化。
4. 烧出模具:将装有可熔模具的外壳放入高温炉中,使可熔模具融化并排出,留下空腔。
5. 铸造:将预先加热至合适温度的金属倒入空腔中,使其填充整个壳型。
金属冷却凝固后形成铸件。
6. 敲击或破碎壳型:待金属凝固后,通过敲击或破碎壳型,取出铸件。
7. 清理和加工:清理铸件表面的残余材料,并进行必要的加工工序,如修整、打磨等。
4. 壳型铸造的优点壳型铸造相比其他金属铸造方法具有以下优点: - 高精度:壳型铸造可以制造出复杂形状和细节丰富的零件,具有较高的精度和表面质量。
- 良好的尺寸稳定性:壳型铸造零件的尺寸稳定性较好,在不同批次生产中保持一致性。
- 高度自动化:壳型铸造过程可以实现高度自动化,提高生产效率和一致性。
- 1、下载文档前请自行甄别文档内容的完整性,平台不提供额外的编辑、内容补充、找答案等附加服务。
- 2、"仅部分预览"的文档,不可在线预览部分如存在完整性等问题,可反馈申请退款(可完整预览的文档不适用该条件!)。
- 3、如文档侵犯您的权益,请联系客服反馈,我们会尽快为您处理(人工客服工作时间:9:00-18:30)。
学生姓名
王坤岳
学号
班级
所属院系专业
指导教师1
职称
所在部门
指导教师2
职称
所在部门
毕业设计(论文)题目
方壳型底座铸造工艺设计
题目类型
工程设计(项目)□
论文类□
作品设计类□
其他□
一、选题简介、意义
21世纪的中国,要想实现经济上的巨大飞跃,实现中华民族的伟大复兴,就必须把信息化的建设放在首位,信息化是我国加快实现工业化和现代化的必然选择。坚持以信息化带动工业化、以工业化促进信息化,走出一条科技含量高、经济效益好、资源消耗低、环境污染少、人力资源优势得到充分发挥的新型工业化道路。从工业发展角度来看,方壳型底座铸造工艺设计最重要的战略资源之一,因为方壳型底座铸造工艺设计几乎可以涉及整个企业的生产经营活动,对企业的经营、效率和战略的变化有直接而深远的影响。因此,研究开发适合我国工业发展所需的方壳型底座,是实行企业信息化战略的重大课题。
(2)分析结构工艺
滑动轴承座主要由上盖,底座,轴瓦组成。由任务书知上方小孔过小不铸出,铸件图样如图1。滑动轴承座的中心孔距地尺寸为132mm;圆通外径22mm,长24mm;支撑板厚6mm;地板高25mm。为小型铸件。主要承受径向载荷,使用简单不需要安装轴承,且轴瓦内表面不承担载荷的部分有油槽,这样润滑油可以通过油孔和油沟进入间隙,起到润滑保养作用。由于其经常处于压应力和摩擦状态,故要求能抗压和耐磨损。通过查找《金属成型工艺设计》比较分析得到,故选择灰铸铁HT200作为铸件材料。
方法及措施:
(1)确定材料
灰铸铁件主要应用于可铸造壁较薄且形状复杂的铸件。灰铸铁有良好的耐磨性,液态流动性好,凝固收缩性小,抗压强度高,吸震性好动轴承座工作要求。因此,选用灰铸铁件。在灰铸铁中,常用的HT2OO性能良好,便于加工和铸造,故选HT200做为铸造材料。
解决的问题:
抓住一种向高性能、高速度、数字化、智能型、网络化方向发展的理念,来实现高层次的应用要求,并重点研究方壳型底座铸造工艺设计。
预期目标:
设计并实现一个方壳型底座,根据系统配置,完成实验,规范、标准化实现控制模块;实现多模式的调试;完成毕业设计论文,通过论文答辩。
研究步骤:
通过设计一个可以在多种操作模式下运行的方壳型底座的实例,详细介绍如何把方壳型底座区分开来。充分利用所拥有的硬件进行测试,重点介绍如何设计出符合项目设计要求的方壳型底座铸造工艺设计。
三、设计(论文)体系、结构(大纲)
1 概述
1.1研究背景
1.2本文的结构安排和主要内容
1.3本文的主要创新与研究不足
2 材料的确定
3 结构工艺分析
4 工艺方案的设计
4.1铸型种类及方法确定
4.2型芯结构及制造
4.3分型面的筛选
4.4铸造位置及浇注口的确定
5 方壳型底座铸件工艺参数确定
5.1加工余量
5.2拔模斜度
5.3收缩量选择
5.4型芯及型芯头选择
6 总结
参考文献
致谢
指导教师意见:
签字:
年月日
分院审批意见:
签章:
年月日
2、课题综述(课题研究,主要研究的内容,要解决的问题,预期目标,研究步骤、方法及措施等)
课题研究:
方壳型底座铸造工艺设计
主要研究的内容:
介绍方壳型底座铸造工艺设计的国内外现状和发展趋势的基础上,提出了本课题的系统集成方案,详细论述了方壳型底座铸造工艺设计的方法。最后通过实际的演示实验证明本设计的系统能够完成预先设定的技术要求,系统运行稳定、精度高,并且操作方便。
(3)设计工艺方案
滑动轴承座在工程中的应用是比较广泛常见的。滑动轴承支座内部结构简单,主要由内腔和小孔等组成,表面形状相对复杂,但无特殊表面质量要求:从尺寸上来讲,属于较小尺寸造型;由于选用了灰铸铁材料且生产批量不大,技术要求不太高,综合分析考虑选用砂型铸造成型,铸型种类为湿型,采用手工分模,这样在满足要求的同时,操作灵活,工艺装备简单,成本低,生产率高,必要时易于采用机械自动化操作。