壳型铸造是采用覆膜砂制壳
壳型铸造
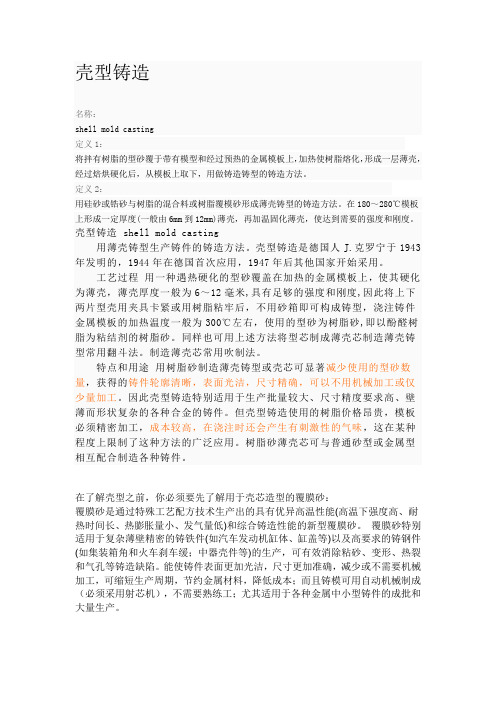
壳型铸造名称:shell mold casting定义1:将拌有树脂的型砂覆于带有模型和经过预热的金属模板上,加热使树脂熔化,形成一层薄壳,经过焙烘硬化后,从模板上取下,用做铸造铸型的铸造方法。
定义2:用硅砂或锆砂与树脂的混合料或树脂覆模砂形成薄壳铸型的铸造方法。
在180~280℃模板上形成一定厚度(一般由6mm到12mm)薄壳,再加温固化薄壳,使达到需要的强度和刚度。
壳型铸造 shell mold casting用薄壳铸型生产铸件的铸造方法。
壳型铸造是德国人J.克罗宁于1943年发明的,1944年在德国首次应用,1947年后其他国家开始采用。
工艺过程用一种遇热硬化的型砂覆盖在加热的金属模板上,使其硬化为薄壳,薄壳厚度一般为6~12毫米,具有足够的强度和刚度,因此将上下两片型壳用夹具卡紧或用树脂粘牢后,不用砂箱即可构成铸型,浇注铸件金属模板的加热温度一般为300℃左右,使用的型砂为树脂砂,即以酚醛树脂为粘结剂的树脂砂。
同样也可用上述方法将型芯制成薄壳芯制造薄壳铸型常用翻斗法。
制造薄壳芯常用吹制法。
特点和用途用树脂砂制造薄壳铸型或壳芯可显著减少使用的型砂数量,获得的铸件轮廓清晰,表面光洁,尺寸精确,可以不用机械加工或仅少量加工。
因此壳型铸造特别适用于生产批量较大、尺寸精度要求高、壁薄而形状复杂的各种合金的铸件。
但壳型铸造使用的树脂价格昂贵,模板必须精密加工,成本较高,在浇注时还会产生有刺激性的气味,这在某种程度上限制了这种方法的广泛应用。
树脂砂薄壳芯可与普通砂型或金属型相互配合制造各种铸件。
在了解壳型之前,你必须要先了解用于壳芯造型的覆膜砂:覆膜砂是通过特殊工艺配方技术生产出的具有优异高温性能(高温下强度高、耐热时间长、热膨胀量小、发气量低)和综合铸造性能的新型覆膜砂。
覆膜砂特别适用于复杂薄壁精密的铸铁件(如汽车发动机缸体、缸盖等)以及高要求的铸钢件(如集装箱角和火车刹车缓;中器壳件等)的生产,可有效消除粘砂、变形、热裂和气孔等铸造缺陷。
铸造中覆膜砂制芯工艺的应用
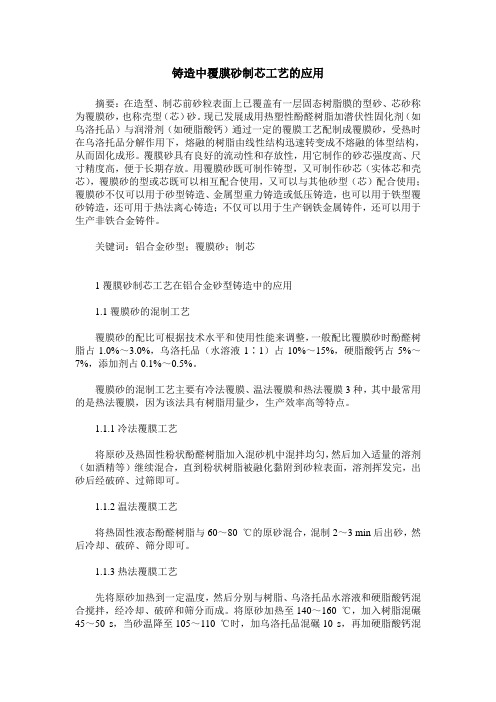
铸造中覆膜砂制芯工艺的应用摘要:在造型、制芯前砂粒表面上已覆盖有一层固态树脂膜的型砂、芯砂称为覆膜砂,也称壳型(芯)砂。
现已发展成用热塑性酚醛树脂加潜伏性固化剂(如乌洛托品)与润滑剂(如硬脂酸钙)通过一定的覆膜工艺配制成覆膜砂,受热时在乌洛托品分解作用下,熔融的树脂由线性结构迅速转变成不熔融的体型结构,从而固化成形。
覆膜砂具有良好的流动性和存放性,用它制作的砂芯强度高、尺寸精度高,便于长期存放。
用覆膜砂既可制作铸型,又可制作砂芯(实体芯和壳芯),覆膜砂的型或芯既可以相互配合使用,又可以与其他砂型(芯)配合使用;覆膜砂不仅可以用于砂型铸造、金属型重力铸造或低压铸造,也可以用于铁型覆砂铸造,还可用于热法离心铸造;不仅可以用于生产钢铁金属铸件,还可以用于生产非铁合金铸件。
关键词:铝合金砂型;覆膜砂;制芯1覆膜砂制芯工艺在铝合金砂型铸造中的应用1.1覆膜砂的混制工艺覆膜砂的配比可根据技术水平和使用性能来调整,一般配比覆膜砂时酚醛树脂占1.0%~3.0%,乌洛托品(水溶液1∶1)占10%~15%,硬脂酸钙占5%~7%,添加剂占0.1%~0.5%。
覆膜砂的混制工艺主要有冷法覆膜、温法覆膜和热法覆膜3种,其中最常用的是热法覆膜,因为该法具有树脂用量少,生产效率高等特点。
1.1.1冷法覆膜工艺将原砂及热固性粉状酚醛树脂加入混砂机中混拌均匀,然后加入适量的溶剂(如酒精等)继续混合,直到粉状树脂被融化黏附到砂粒表面,溶剂挥发完,出砂后经破碎、过筛即可。
1.1.2温法覆膜工艺将热固性液态酚醛树脂与60~80 ℃的原砂混合,混制2~3 min后出砂,然后冷却、破碎、筛分即可。
1.1.3热法覆膜工艺先将原砂加热到一定温度,然后分别与树脂、乌洛托品水溶液和硬脂酸钙混合搅拌,经冷却、破碎和筛分而成。
将原砂加热至140~160 ℃,加入树脂混碾45~50 s,当砂温降至105~110 ℃时,加乌洛托品混碾10 s,再加硬脂酸钙混碾45~50 s,当砂温降至70 ℃以下时,卸砂——冷却——破碎10 s,然后进行筛分即可。
覆膜砂相关知识培训.
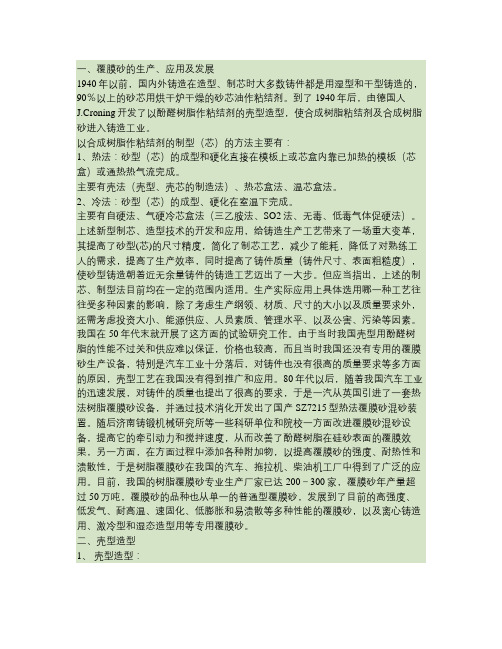
一、覆膜砂的生产、应用及发展1940年以前,国内外铸造在造型、制芯时大多数铸件都是用湿型和干型铸造的,90%以上的砂芯用烘干炉干燥的砂芯油作粘结剂。
到了1940年后,由德国人J.Croning开发了以酚醛树脂作粘结剂的壳型造型,使合成树脂粘结剂及合成树脂砂进入铸造工业。
以合成树脂作粘结剂的制型(芯)的方法主要有:1、热法:砂型(芯)的成型和硬化直接在模板上或芯盒内靠已加热的模板(芯盒)或通热热气流完成。
主要有壳法(壳型、壳芯的制造法)、热芯盒法、温芯盒法。
2、冷法:砂型(芯)的成型、硬化在室温下完成。
主要有自硬法、气硬冷芯盒法(三乙胺法、SO2法、无毒、低毒气体促硬法)。
上述新型制芯、造型技术的开发和应用,给铸造生产工艺带来了一场重大变革,其提高了砂型(芯)的尺寸精度,简化了制芯工艺,减少了能耗,降低了对熟练工人的需求,提高了生产效率,同时提高了铸件质量(铸件尺寸、表面粗糙度),使砂型铸造朝着近无余量铸件的铸造工艺迈出了一大步。
但应当指出,上述的制芯、制型法目前均在一定的范围内适用。
生产实际应用上具体选用哪一种工艺往往受多种因素的影响,除了考虑生产纲领、材质、尺寸的大小以及质量要求外,还需考虑投资大小、能源供应、人员素质、管理水平、以及公害、污染等因素。
我国在50年代末就开展了这方面的试验研究工作。
由于当时我国壳型用酚醛树脂的性能不过关和供应难以保证,价格也较高,而且当时我国还没有专用的覆膜砂生产设备,特别是汽车工业十分落后,对铸件也没有很高的质量要求等多方面的原因,壳型工艺在我国没有得到推广和应用。
80年代以后,随着我国汽车工业的迅速发展,对铸件的质量也提出了很高的要求,于是一汽从英国引进了一套热法树脂覆膜砂设备,并通过技术消化开发出了国产SZ7215型热法覆膜砂混砂装置。
随后济南铸锻机械研究所等一些科研单位和院校一方面改进覆膜砂混砂设备,提高它的牵引动力和搅拌速度,从而改善了酚醛树脂在硅砂表面的覆膜效果,另一方面,在方面过程中添加各种附加物,以提高覆膜砂的强度、耐热性和溃散性,于是树脂覆膜砂在我国的汽车、拖拉机、柴油机工厂中得到了广泛的应用。
铸造中覆膜砂制芯工艺的应用
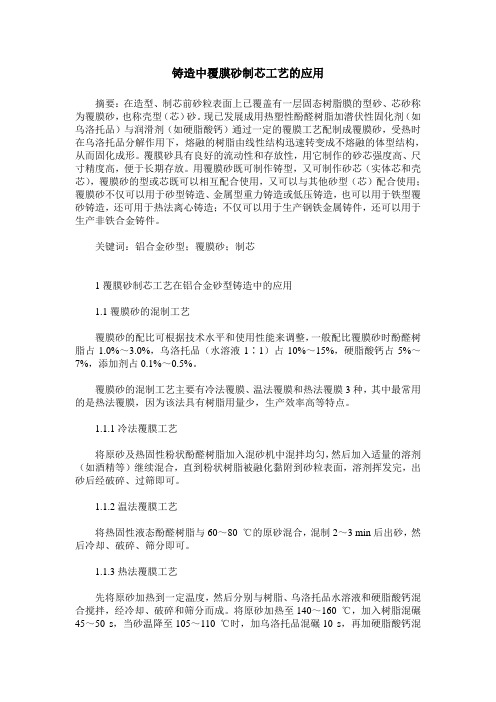
铸造中覆膜砂制芯工艺的应用摘要:在造型、制芯前砂粒表面上已覆盖有一层固态树脂膜的型砂、芯砂称为覆膜砂,也称壳型(芯)砂。
现已发展成用热塑性酚醛树脂加潜伏性固化剂(如乌洛托品)与润滑剂(如硬脂酸钙)通过一定的覆膜工艺配制成覆膜砂,受热时在乌洛托品分解作用下,熔融的树脂由线性结构迅速转变成不熔融的体型结构,从而固化成形。
覆膜砂具有良好的流动性和存放性,用它制作的砂芯强度高、尺寸精度高,便于长期存放。
用覆膜砂既可制作铸型,又可制作砂芯(实体芯和壳芯),覆膜砂的型或芯既可以相互配合使用,又可以与其他砂型(芯)配合使用;覆膜砂不仅可以用于砂型铸造、金属型重力铸造或低压铸造,也可以用于铁型覆砂铸造,还可用于热法离心铸造;不仅可以用于生产钢铁金属铸件,还可以用于生产非铁合金铸件。
关键词:铝合金砂型;覆膜砂;制芯1覆膜砂制芯工艺在铝合金砂型铸造中的应用1.1覆膜砂的混制工艺覆膜砂的配比可根据技术水平和使用性能来调整,一般配比覆膜砂时酚醛树脂占1.0%~3.0%,乌洛托品(水溶液1∶1)占10%~15%,硬脂酸钙占5%~7%,添加剂占0.1%~0.5%。
覆膜砂的混制工艺主要有冷法覆膜、温法覆膜和热法覆膜3种,其中最常用的是热法覆膜,因为该法具有树脂用量少,生产效率高等特点。
1.1.1冷法覆膜工艺将原砂及热固性粉状酚醛树脂加入混砂机中混拌均匀,然后加入适量的溶剂(如酒精等)继续混合,直到粉状树脂被融化黏附到砂粒表面,溶剂挥发完,出砂后经破碎、过筛即可。
1.1.2温法覆膜工艺将热固性液态酚醛树脂与60~80 ℃的原砂混合,混制2~3 min后出砂,然后冷却、破碎、筛分即可。
1.1.3热法覆膜工艺先将原砂加热到一定温度,然后分别与树脂、乌洛托品水溶液和硬脂酸钙混合搅拌,经冷却、破碎和筛分而成。
将原砂加热至140~160 ℃,加入树脂混碾45~50 s,当砂温降至105~110 ℃时,加乌洛托品混碾10 s,再加硬脂酸钙混碾45~50 s,当砂温降至70 ℃以下时,卸砂——冷却——破碎10 s,然后进行筛分即可。
浅析斗齿类铸件壳型铸造常见缺陷与防止
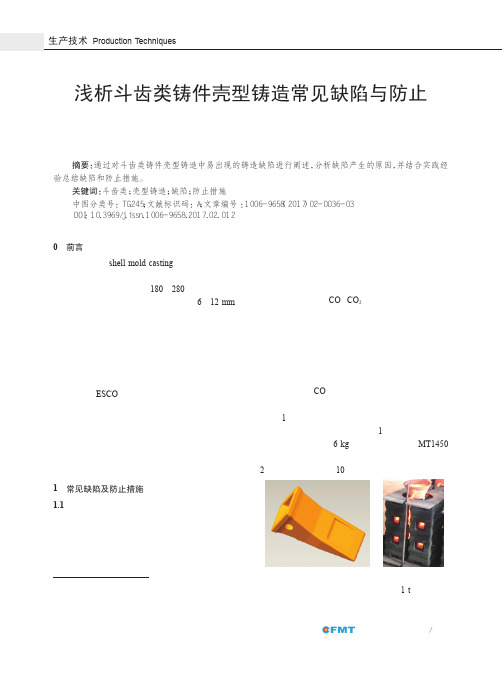
收稿日期 :2016-08-21 稿件编号 :1608-1478 作者简介:郜刚强(1985—),男, 工程师 . 主要从事铸造生产工艺技
(1)机械粘砂 金属液渗入型砂的空隙中,冷凝后在铸件的表
面上粘附一层不易清除的金属液和型壳材料的机 械混合物。机械粘砂常常产生在铸件的内角、窄槽、 小孔、厚壁、表面、浇冒口附近或铸件的下部等(图 6 所示)。
பைடு நூலகம்
图 5 钢液熔炼品质引起的气孔
防止措施: a)在熔炼过程中,严格控制金属液的含气量, 确保所用原材料符合要求,规范熔炼操作,选择合 适的熔炼设备。 b)出钢前采用铝锭进行脱氧处理,并采用定氧 仪测定钢液中的含氧量,使钢液含氧量 <15×10-6%。 加铝脱氧后的钢液不应停留时间过长,应在 2~3
图 3 卷气机理图 图 4 侵入性气孔
防止措施: a)增加浇口盆,采用 1 t 的转包浇注,遵循“慢— 快—慢”原则,保持浇口盆内充满钢液,以保证直浇 道始终处于充满状态,充型时金属液流动平稳,不 卷气。合理控制浇注速度,浇注时间控制在 18 s/ 串。 b)设计工艺时,合理安排壳型及砂芯的排气位 置,以便顺畅排出浇注过程中卷入的气体。 (2)析出性气孔 钢 液 熔 炼 过 程 中 含 有 气 体,需 要 进 行 预 脱 氧 处理和终脱氧处理,如果脱氧不充分容易形成气孔 (图 5 所示),此类气孔体积较小,直径一般< 3 mm, 且随机分布在铸件各处。
1 常见缺陷及防止措施
1.1 气孔缺陷 气孔是铸件最常见的缺陷之一,根据形成机理
铸钢工艺之:精铸覆膜砂壳型工艺代替熔模精密铸造生产复杂铸钢件的稳定化应用
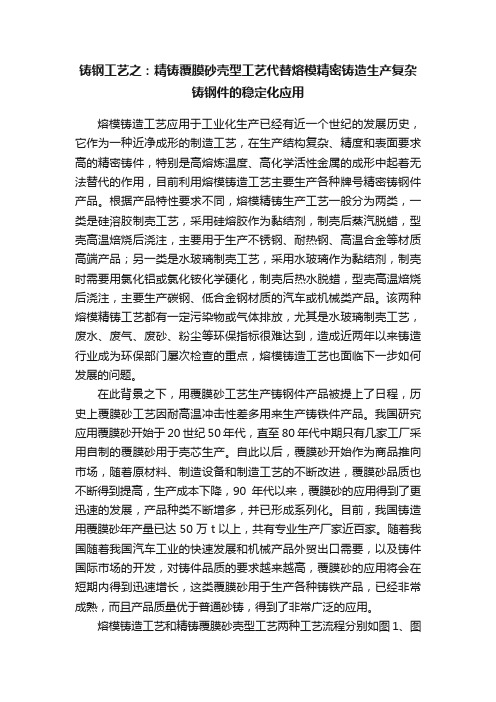
铸钢工艺之:精铸覆膜砂壳型工艺代替熔模精密铸造生产复杂铸钢件的稳定化应用熔模铸造工艺应用于工业化生产已经有近一个世纪的发展历史,它作为一种近净成形的制造工艺,在生产结构复杂、精度和表面要求高的精密铸件,特别是高熔炼温度、高化学活性金属的成形中起着无法替代的作用,目前利用熔模铸造工艺主要生产各种牌号精密铸钢件产品。
根据产品特性要求不同,熔模精铸生产工艺一般分为两类,一类是硅溶胶制壳工艺,采用硅熔胶作为黏结剂,制壳后蒸汽脱蜡,型壳高温焙烧后浇注,主要用于生产不锈钢、耐热钢、高温合金等材质高端产品;另一类是水玻璃制壳工艺,采用水玻璃作为黏结剂,制壳时需要用氯化铝或氯化铵化学硬化,制壳后热水脱蜡,型壳高温焙烧后浇注,主要生产碳钢、低合金钢材质的汽车或机械类产品。
该两种熔模精铸工艺都有一定污染物或气体排放,尤其是水玻璃制壳工艺,废水、废气、废砂、粉尘等环保指标很难达到,造成近两年以来铸造行业成为环保部门屡次检查的重点,熔模铸造工艺也面临下一步如何发展的问题。
在此背景之下,用覆膜砂工艺生产铸钢件产品被提上了日程,历史上覆膜砂工艺因耐高温冲击性差多用来生产铸铁件产品。
我国研究应用覆膜砂开始于20世纪50年代,直至80年代中期只有几家工厂采用自制的覆膜砂用于壳芯生产。
自此以后,覆膜砂开始作为商品推向市场,随着原材料、制造设备和制造工艺的不断改进,覆膜砂品质也不断得到提高,生产成本下降,90年代以来,覆膜砂的应用得到了更迅速的发展,产品种类不断增多,并已形成系列化。
目前,我国铸造用覆膜砂年产量已达50万t以上,共有专业生产厂家近百家。
随着我国随着我国汽车工业的快速发展和机械产品外贸出口需要,以及铸件国际市场的开发,对铸件品质的要求越来越高,覆膜砂的应用将会在短期内得到迅速增长,这类覆膜砂用于生产各种铸铁产品,已经非常成熟,而且产品质量优于普通砂铸,得到了非常广泛的应用。
熔模铸造工艺和精铸覆膜砂壳型工艺两种工艺流程分别如图1、图2所示。
壳型铸造工艺及装备研发生产方案(一)

壳型铸造工艺及装备研发生产方案一、实施背景随着制造业的不断发展,高效、环保、节能已成为铸造行业的重要发展方向。
壳型铸造工艺作为一种先进的铸造技术,具有较高的生产效率、较低的能耗和良好的产品质量,因此受到广泛关注。
然而,国内壳型铸造工艺及装备研发生产方面仍存在一定的问题,如技术水平不高、生产效率低下、产品质量不稳定等,难以满足市场需求。
因此,开展壳型铸造工艺及装备研发生产具有重要的现实意义和市场需求。
二、工作原理壳型铸造工艺是一种利用覆膜砂或其他类似材料制成的壳型进行浇铸的工艺方法。
其主要工作原理包括以下几个方面:1.覆膜砂制壳:利用覆膜砂材料,通过喷射、流化等手段制成具有一定厚度的壳型,其内部为空心结构。
2.熔融金属浇铸:将熔融的金属液体通过浇口注入到壳型中,待金属液体冷却凝固后形成铸件。
3.脱壳、清理:经过一定时间的冷却后,打开壳型,取出铸件,进行表面清理及处理。
三、实施计划步骤1.需求分析:对市场需求进行调研,明确产品类型、规格、质量要求等。
2.技术研究:开展覆膜砂材料、制壳技术、熔融金属浇铸技术等方面的技术研究。
3.装备设计:根据实际需要,设计相应的制壳设备、浇铸设备等。
4.生产调试:对所研发的设备进行调试,确保其正常运行并逐步优化生产工艺。
5.批量生产:在确保产品质量和稳定性的前提下,逐步扩大生产规模,实现批量生产。
四、适用范围壳型铸造工艺及装备适用于各种大中小型铸件的生产,尤其适用于复杂形状、高精度要求的铸件。
在汽车、航空航天、船舶、机械制造等领域得到广泛应用。
五、创新要点1.采用新型覆膜砂材料:通过选用高性能的覆膜砂材料,提高壳型强度和耐高温性能,从而提高产品质量和生产效率。
2.制壳工艺优化:改进制壳工艺流程,实现自动化、智能化制壳,降低劳动强度,提高生产效率。
3.熔融金属高效浇铸:研究高效浇铸技术,提高金属熔融温度和浇注速度,减少能源消耗和废品率。
4.集成化装备设计:将制壳、浇铸、脱壳等工艺流程集成在一台或多台设备上,实现流水线生产,提高生产效率。
壳型背丸工艺生产康明斯排气管铸件

Q 40 3 0 T 2 . 9
—
≤ ≤ ≤ 04 O0 00 . 0 .6 . 4
O. 02~ 0. O3~
1 5
29~3 . _ 4
O5
0.5 0
炉 后
( ) 采 用 一 次 大 孕 育 量 和 二 次 随 流 孕 育 技 2
术 ,提高球 化效果 ,降低珠 光体量 ,增加 铁素 体 量 ,即稀土 镁球化剂加入 量14 .%~1 %,同时加 . 6
壳 型 背丸 工 艺是 一 种 采 用 覆 膜 砂制 壳 型 ,并 在
传 热 较快 ,导 致 铸 件 的冷 却 速 度快 ,极 易形 成 珠 光
壳型内腔浇注铁液、壳型背面装填钢九 ( 铁丸 )冷 却铸件的铸造工艺方法 ,这种新的工艺方法生产 的 铸件 尺寸精度和表面质量高 ( T 级 ),消耗砂量 C 8 少 ,生产成本较低 ,生产机械化 、自动化程度高 ,
一
层 粒度 1 ~2 mm的7 e 育 剂 ,加 入 量 按 终 0 0 5S F 孕 i
硅量W =33 . %~3 0 . %计算 加 入 。随 流孕 育剂加 入 4 量 为01 . %, 同时 设计 适 宜 的 浇注 系统 ,以保 证 孕 育
压头高 (7 rm),铸件极易形成粘砂缺陷。 90 a ( )生产的壳型易变形 ,影响铸件尺寸精度。 3
易获得铁素体基体组织,因此 ,恰 当的材料壳型厚 度 就成 为能否获 得铸态铁 素体基 体材 质排 气管
的 另一 重 要 因素 。 通 过 试 验 研 究 ,当 壳 型 厚 度 为
压头不超过6 0 0 mm ( 加上下箱2 0 0 mm的压头 ),
而 由于 壳 型背 丸 工艺 采 用 立 浇方 式 ,铁 液 压头 达 到 90 7 mm,比一 般 覆膜 砂 芯使 用 条 件 下的 铁 液压 头 大 近 一 倍 ,过 高 的 高温 铁 液 压 头将 显 著 增 加 高温 铁 液 的渗 透性 ( 多 数铸 件 使 用 的 覆膜 砂 芯 不 上涂 料 , 大