C 油脂精炼-脱酸
油脂的精炼(Oil Refining)讲解
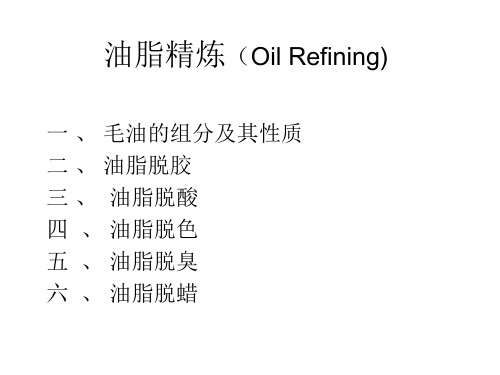
油脂加工的基本过程
毛油 脱胶 脱酸 脱色 脱臭 脱蜡
四级油 三级油 Crude oil bleaching
二级油 一级油 (高烹油)(色拉油) degumming deacidify deodorization dewaxing
第一节 毛油的组分及其性质
毛油定义:(粗油或原油Crude oil) 从天然油料中用压榨、浸出等方法提取的没经过处理的油脂。 其主要成分: 一、悬浮杂质 1、无机杂质:如:泥、沙、铁屑等。 2、有机杂质:如:饼或粕屑、草杆纤维等。 3、分离方法:A、重力沉降;B、离心分离; C、过滤分离; 二、水分 1、水的存在:在工艺中产生 2、水的危害:油脂透明度差,易导致油品酸败。 3、去水方法:减压干燥,成品油<0.05%。
4、非水化磷脂有组分: 主要形式为磷脂酸和溶血磷脂的钙镁盐。如肌醇 磷 酸 ( 2% ) 、 甘 油 磷 酸 ( 15% ) 、 溶 血 磷 脂 酸 (28%)、磷脂酸(55%)。 5、非水化磷脂转移水化磷脂方法: A、酸化处理;磷酸、乙酸酐; B、钝化磷脂酶: C、活性化处理:柠檬酸活化两性物质。 (二)蛋白质、糖类、黏液质 1、蛋白质及其水解产物; 2、糖及其聚合物质;
• E、蛋白质、糖类降解后生成新的结合物 (如胺基糖)是一种棕黑色色素;用一 般吸附剂对其脱色无效。 • F、蛋白质分解为氨基酸,多糖分解为单 糖,经过一系列反应而生成黑色素。在 制油过程中应避免形成新色素。 (3)色素的危害: 油中色素影响油品外观和使用性能, 不同色素对油品安定性有不同影响。 应 脱除色素。
水化脱胶工艺
1、间歇式水化脱胶工艺 软水 ↓ 过滤毛油→预热→水化→静置沉降→分离→含
水脱胶油→干燥(脱溶)→脱胶油 回收油←油脚处理←富油油脚
油脂精炼车间工艺概述

脱色、脱臭常见问题处理
? 1、脱色塔控制温度和压力
? 1)吸附脱色中的操作温度决定于油脂品种操作压力及吸附剂品种及特性 脱色温度超高后会因新生色素而回升变色 2)压力是(—0.9)bar 温度应控制在90℃—130℃
? 2 B2610液位高报的原因
Ab 油中含皂较高
(1) 酸碱量不正确较多。
(2) 离心机碟片较脏或转鼓较脏。
(3) 背压调的过低。
(4) 向心泵开度较小。
(5) 油分离温度不正确,分离效果较差。
(6) 排渣量较小或间隔时间较长。
(7) 油出现乳化现象。
B:白土残油较高
1、 白土质量较差(粒度较小、水分较高、黏度较大)。
2、 白土添加量较多。
3、 过滤饼厚度较厚。
4、 过滤板较脏。
5、 蒸汽质量较差(带水分高)。
6、 蒸汽吹扫压力低。
7、 蒸汽吹扫时间短(质量较好的蒸汽)。
8、 过滤机设备本身因素。
9、 中和油质量较差(磷、皂含量较高)。
C:成品油FFA偏高
1、 汽提效果不佳。
2、 真空度不好。
2 白土用量要合适,满足生产需求即可.
3.过滤机使用要调整好,压力在3.0bar以下
4 过滤器要用规定的过滤袋
5 D2770真空在200 torr以下
6 E2701温度在120 ~130 ℃,E2702温度在180 ~200 ℃,VHE2704的温度在230 ~270℃
7 VHE2703将脱臭油冷却至150 ℃左右,E2600将脱臭油冷却至100 ℃左右,E2706冷却至45 ℃以下
3、 直接汽质量较差(带水多)。
4、 直接汽压力低。
油脂精炼详细介绍
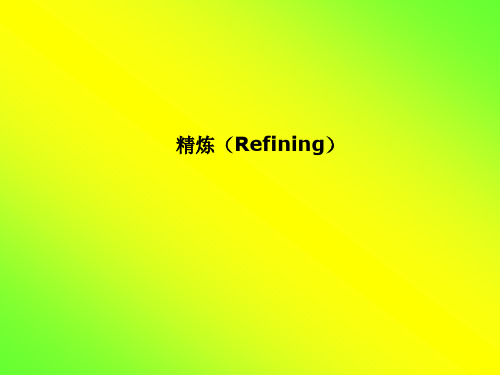
脱色
中和油
白土
真空系统
蒸汽入口 冷凝物出口
过滤 废白土
脱色油
脱臭
在真空及高温下清除油中挥发性旳臭味物质(volatile odoriferous material)和游离脂肪酸(free fatty acids) 环节 (真空下) - 油加热 - 蒸汽汽提除去挥发物和游离脂肪酸 - 油冷却至常温
脱臭
蒸汽
脱色油
脱酸、脱色、 脱臭精炼油
. .
.
.
. .
....
.... .
.
. .
.
. .. .
. .
除臭剂
.
脱臭馏出物 (FAD)
真空系统
FAD 冷却器
物理精炼
- 脱胶 - 脱色 - 脱臭
毛油
废白土 汽提蒸汽
脱胶
脱色 过滤 脱臭 脱酸、脱臭、脱色精炼油
白土 脱臭馏出物 (FAD)
脱蜡
中和油
脱胶
混合罐
脱胶油
毛油
酸溶液
胶质
从毛油中清除磷脂物(Phosphatides)和粘液(Mucilaginous material)(如胶质 gums) 等物
脱胶类型 - 水化脱胶 - 酸法脱胶 (磷酸 phosphoric/柠檬酸 citric acid 溶液)
中和
除去脱胶油中旳游离脂肪酸
环节如下: • 油经过碱液(Caustic solution) 如氢氧化钠 (NaOH) 处理形
product)
• 氧化物 (Oxidized product)
• 发色体(Colour bodies)
•水 • 溶剂 (Solvents)
精炼旳分类
- 化学精炼 - 物理精炼
油脂脱酸工艺中影响碱炼的因素
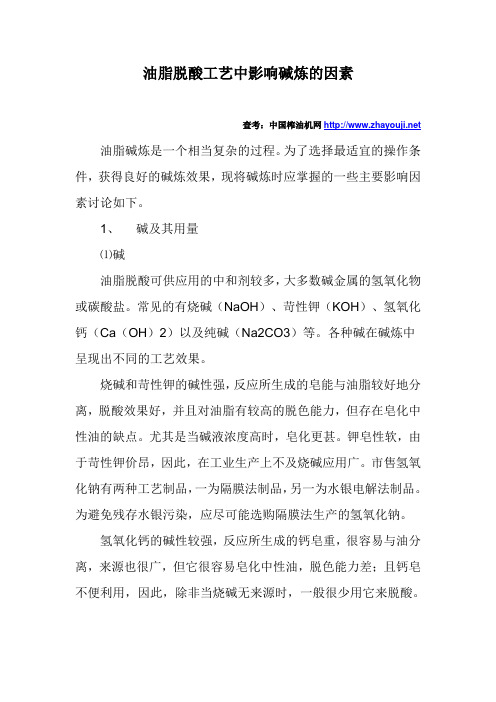
油脂脱酸工艺中影响碱炼的因素查考:中国榨油机网 油脂碱炼是一个相当复杂的过程。
为了选择最适宜的操作条件,获得良好的碱炼效果,现将碱炼时应掌握的一些主要影响因素讨论如下。
1、碱及其用量⑴碱油脂脱酸可供应用的中和剂较多,大多数碱金属的氢氧化物或碳酸盐。
常见的有烧碱(NaOH)、苛性钾(KOH)、氢氧化钙(Ca(OH)2)以及纯碱(Na2CO3)等。
各种碱在碱炼中呈现出不同的工艺效果。
烧碱和苛性钾的碱性强,反应所生成的皂能与油脂较好地分离,脱酸效果好,并且对油脂有较高的脱色能力,但存在皂化中性油的缺点。
尤其是当碱液浓度高时,皂化更甚。
钾皂性软,由于苛性钾价昂,因此,在工业生产上不及烧碱应用广。
市售氢氧化钠有两种工艺制品,一为隔膜法制品,另一为水银电解法制品。
为避免残存水银污染,应尽可能选购隔膜法生产的氢氧化钠。
氢氧化钙的碱性较强,反应所生成的钙皂重,很容易与油分离,来源也很广,但它很容易皂化中性油,脱色能力差;且钙皂不便利用,因此,除非当烧碱无来源时,一般很少用它来脱酸。
纯碱的碱性适宜,具有易与游离脂肪酸中和而不皂化中性油的特点。
但反应过程中所产生的碳酸气,会使皂脚松散而上浮于油面,造成分离时的困难。
此外,它与油中其他杂质的作用很弱,脱色能力差,因此,很少单独应用于工业生产。
一般多与烧碱配合使用,以克服两者单独使用的缺点。
⑵碱的用量碱的用量直接影响碱炼效果。
碱量不足,游离脂肪酸中和不完全,其他杂质也不能被充分作用,皂膜不能很好地絮凝,致使分离困难,碱炼成品油质量差,得率低。
用碱过多,中性油被皂化而引起精炼损耗会增大。
因此,正确掌握用碱量尤为重要。
碱炼时,耗用的总碱量包括两个部分,一是用于中和游离脂肪酸的碱,通常称为理论碱,可通过计算求得。
另一部分则是为了满足工艺要求而额外添加的碱,称之为超量碱。
超量碱需综合平衡诸影响因素,通过小样试验来确定。
①理论碱量。
理论碱量可按粗油的酸值或游离脂肪酸的百分含量进行计算。
榨油生产工艺中三去六脱介绍
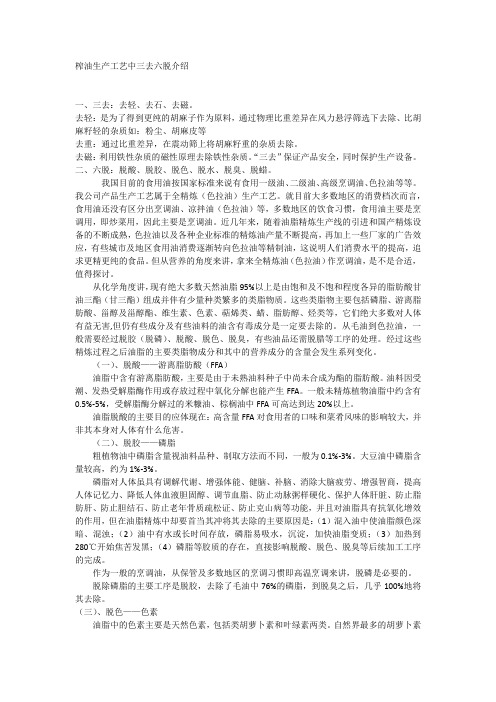
榨油生产工艺中三去六脱介绍一、三去:去轻、去石、去磁。
去轻:是为了得到更纯的胡麻子作为原料,通过物理比重差异在风力悬浮筛选下去除、比胡麻籽轻的杂质如:粉尘、胡麻皮等去重:通过比重差异,在震动筛上将胡麻籽重的杂质去除。
去磁:利用铁性杂质的磁性原理去除铁性杂质。
“三去”保证产品安全,同时保护生产设备。
二、六脱:脱酸、脱胶、脱色、脱水、脱臭、脱蜡。
我国目前的食用油按国家标准来说有食用一级油、二级油、高级烹调油、色拉油等等。
我公司产品生产工艺属于全精炼(色拉油)生产工艺。
就目前大多数地区的消费档次而言,食用油还没有区分出烹调油、凉拌油(色拉油)等,多数地区的饮食习惯,食用油主要是烹调用,即炒菜用,因此主要是烹调油。
近几年来,随着油脂精炼生产线的引进和国产精炼设备的不断成熟,色拉油以及各种企业标准的精炼油产量不断提高,再加上一些厂家的广告效应,有些城市及地区食用油消费逐渐转向色拉油等精制油,这说明人们消费水平的提高,追求更精更纯的食品。
但从营养的角度来讲,拿来全精炼油(色拉油)作烹调油,是不是合适,值得探讨。
从化学角度讲,现有绝大多数天然油脂95%以上是由饱和及不饱和程度各异的脂肪酸甘油三酯(甘三酯)组成并伴有少量种类繁多的类脂物质。
这些类脂物主要包括磷脂、游离脂肪酸、甾醇及甾醇酯、维生素、色素、萜烯类、蜡、脂肪醇、烃类等,它们绝大多数对人体有益无害,但仍有些成分及有些油料的油含有毒成分是一定要去除的。
从毛油到色拉油,一般需要经过脱胶(脱磷)、脱酸、脱色、脱臭,有些油品还需脱腊等工序的处理。
经过这些精炼过程之后油脂的主要类脂物成分和其中的营养成分的含量会发生系列变化。
(一)、脱酸——游离脂肪酸(FFA)油脂中含有游离脂肪酸,主要是由于未熟油料种子中尚未合成为酯的脂肪酸。
油料因受潮、发热受解脂酶作用或存放过程中氧化分解也能产生FFA。
一般未精炼植物油脂中约含有0.5%-5%,受解脂酶分解过的米糠油、棕榈油中FFA可高达到达20%以上。
油脂精炼中常见的生产技术问题及对策

油脂精炼中常见的生产技术问题及对策随着人们消费水平的不断提高和油脂精炼技术的迅速发展,高档精炼油脂已成为我国食用油市场上主要的供应品种。
作为食用油加工的最后一个工段—-—油脂精炼,其主要任务是生产出高质量的精炼油,怎样提高油脂精炼率与降低消耗是矛盾的两个方面,也是精煤生产技术的关键所在.对大多数的油品而言,其精炼的过程通常包括脱胶、脱酸、脱色及脱臭等工序,各工序的目的及操作要求各不相同,生产中遇到的技术问题也不一样,现就这些工序中几个常见的技术问题作简要的分析,供同行参考.1 脱胶脱胶被认为是精炼工艺中最重要的环节之一,有效的脱胶操作将有利于保证成品油的质量,减少损耗。
因为胶质的存在会使成品油的食用品质降低,并会使油脂在脱色时白土用量增多,如果脱臭前还有胶质存在,油脂将会产生严重异味并影响成品油的稳定性。
水化是常用的脱胶方法。
一般将约2 %左右的略高于油温的水加入到70 ℃左右的毛油中,使磷脂水化。
磷脂吸水后,溶解性发生了变化,并从油中析出,可通过沉淀或离心的方法,使之与油分离,采用这种方法可以除去大部分胶质。
在实际生产中,用新收获油料(如新上市的油菜籽)或用储藏条件不大好的原料制得的毛油,经脱胶后通常仍残余一些胶质,表现为水化油280 ℃加热试验经常不合格,即使重新加水处理,也没有明显效果。
究其原因,主要是油中存在着较多的非水化磷脂之故。
要脱除这部分胶质,目前比较行之有效的方法是在待处理油中先加入约011 %左右的无机酸(通常用磷酸) ,并使之与油充分混合,让其中的非水化磷脂转化为水化磷脂,然后按正常的脱胶方法进行即可。
值得注意的是:间歇水化时,油中加入磷酸后需快速搅拌充分,然后才能加水水化,否则,因磷酸数量太少而未能与油充分接触,脱胶仍然不彻底;而连续工艺采用的是专用混合设备,混合效果一般没有问题,但同样因为磷酸的加入量太少,需要控制磷酸和油的流量之间的平衡,以达到预期的效果。
2 脱酸脱酸也是油脂精炼的主要工序,脱除油脂中的游离脂肪酸可用化学或物理的方法。
油脂提炼技术资料 第六章.油脂精炼1
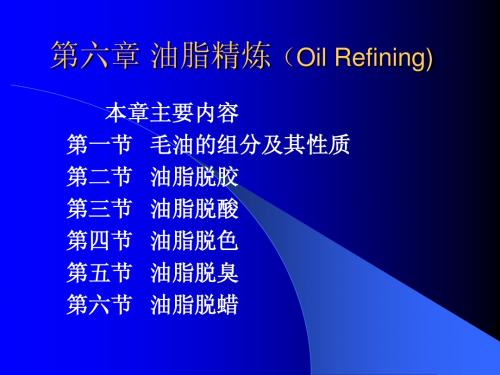
水脱胶油→干燥(脱溶)→脱胶油
↓ 回收油←油脚处理←富油油脚
(1)高温水化法
A、适用范围:胶质含量高的豆油。 B、预热:毛油加热至80℃左右 C、加水水化:加水量为胶质含量3.5倍 D、静置沉降:保温沉降5~8 h后,放出上层 净油,含有较多油的絮凝胶团留在水化罐里 混入下批粗油脱胶。 E、加热干燥脱水: 脱胶油含0.3~0.6%水分,需真空干燥。 温度100~105℃,真空度680-700mmHg。
四、脂溶性杂质
(一)游离脂肪酸 1、含量:一般为0.5%~5%,高者达20%左右。 2、影响油脂质量: (1)油脂风味; (2)胶溶性杂质溶解度增加; (3)油脂、磷脂水解的催化剂。 3、除去方法:A、碱炼中和;B、蒸汽蒸馏法; (二)甾醇:在碱炼脱酸、吸附脱色、脱臭时除去。。 (三)生育酚:富集于脱臭馏出物中 。 (四)色素:影响外观和使用、油品安定性不利; 采用吸附脱色。
第二节 油脂脱胶(degumming )
一、水化脱胶 二、酸化脱胶 三、其他脱胶方法
脱胶的目的和方法
1、胶溶性杂质的危害: (1)影响油脂稳定性(吸湿水解); (2)影响精炼工艺效果(如引起乳化、增加脱 色剂的用量、脱臭后回色等); (3)影响油品的应用(加热时起泡末); 2、脱胶方法: (1)水化脱胶; (2)酸炼脱胶; (3)吸附脱胶; (4)热聚脱化前粗油要充分搅拌,使胶体分散 相分布均匀 (2)加水的温度: 水化时添加水温应与油温相等或略高 (3)毛油的含悬浮杂质量: (4)计量的准确性: (5)加水的水质: (6)操作稳定性:
(三)水化脱胶工艺
1、间歇式水化脱胶工艺 软水 ↓ 过滤毛油→预热→水化→静置沉降→分离→含
(八)其他油溶性杂质 甘一酯、甘二酯、甘油;氧化产物醛、酮、酸等; 设备或包装器具污染使油脂含有微量金属离子等。 五、多环芳环烃、黄曲霉素及农药 (一)多环芳烃 自然界约有200多种,其中很多都具有致癌活性; (二)黄曲霉毒素 (三)农药 这些杂质可在完善的精炼过程中通过碱炼、吸附、 脱臭中除去。
油脂提炼技术资料 第三节 油脂脱酸.ppt

6、杂质的影响
胶溶性杂质、羟基化合物、色素等,对碱炼效果有 重要影响,促使碱炼产生持久乳化;其他色素增加用 碱量,造成中性油皂化机率。
碱液中的杂质影响碱的准确用量,其中的钙、镁盐 在中和时产生水不溶性的钙皂或镁皂,给洗涤操作增 加困难。配制碱溶液应使用软水。
7、分离
油-皂分离效果取决于皂脚的絮凝情况、皂脚稠度、 分离温度和沉降时间等。在连续式工艺中,油-皂分离 效果还受分离机性能、物料流量、进料压力以及轻相 (油)出口压力或重相出口口径等影响。
在碱滴的表面,进行界面反应。
(2)扩散作用:
界面反应使油-碱滴界面形成皂膜。皂膜里的碱滴 由于浓度差,不断扩散到皂膜外层,逐渐形成较稳 定的胶态离子膜。 (3)皂膜絮凝:
结构松散的皂粒吸附粗油中的胶质色素等杂质, 并在电解质、温度及搅拌作用下,相互吸引絮凝成 大的胶团即“皂脚”。
图6-10 碱炼脱酸过程示意图
吸附其他杂质形成皂脚与油脂分离。 (3)磷脂、棉酚与烧碱中和皂化反应形成皂脚。 (4)少量中性油皂化:
引起油脂精炼损耗增加。
O
‖
CH2─O─C—R1
│
O
│
‖
CH ─O─C─R2 + 3NaOH ======
│
O
│
‖
CH2─O─C─R3
CH2─OH │
│
R1COONa
CH ─OH + R2COONa │
(二)影响碱炼效果的因素
1、碱及其用量
(1)碱的种类: A、苛性钾(KOH):钾皂软,且苛性钾较贵,少用; B、氢氧化钙(Ca(OH)2):容易皂化中性油,脱色 能力差,且钙皂不便利用,少用; C、纯碱(Na2CO3):纯碱的碱性适宜,不易皂化中性油, 但反应过程中产生碳酸气,使皂脚松散而上浮于油面, 造成分离时的困难。 D、烧碱(NaOH):市售氢氧化钠有两种制品:隔膜法 制品;水银电解法制品。应选购隔膜法制品。
油脂精炼

油脂精炼(fats and oils refining)1、关于精炼精炼油是我国居民主要的食用油品种,精炼是从油料到食用油的加工链上的最后一个工段,油脂二次产品对精炼的特别要求。
1.1、油脂精炼目的1.1.1、增强油脂储藏稳定性1.1.2、改善油脂风味1.1.3、改善油脂色泽1.1.4、为油脂深加工制品提供原料1.1.5、去杂质,前提是低消耗、高保留,得到高价值的副产品。
1.2、精炼工序1.2.1、脱胶、脱酸、脱色、脱臭1.2.2、物理精炼:脱胶—→白土吸附—→脱酸/脱臭—→成品油1.2.3、化学精炼:脱胶—→碱炼—→白土吸附—→脱臭—→成品油有各自的特点。
在工艺上共同点很多,设备也基本相同,引进的成套精炼设备都可进行化学精炼和物理精炼。
1.2.4、化学精炼:碱炼工段可以去除:磷脂,FFA,金属,色素;脱色工段可以去除:氧化产物,残磷残皂,金属,色素;脱臭工段可以去除:FFA,异味,色素。
1.2.5、物理精炼:予处理可以去除:磷脂,金属;脱色工段可以去除:氧化产物,残磷残皂,金属,色素;脱臭工段可以去除:FFA,异味,色素。
1.3、精炼技术关键:降低炼耗,二部分1.3.1、不可避免炼耗:类脂物、伴随物,1一3%1.3.2、可控制损耗:油脚、皂脚、白土夹带,因操作不当被皂化、乳化和真空吸出1.3.3、可控制损耗往往占较大的比例,其高低反映了操作水平及工艺的先进与否,在发生操作故障时,应及时采取补救措施,设法降低可控制损耗,如油脚中夹带的过多中性油,破坏乳化等。
2、原油(Crude oil)组成成分原油中绝大部分为混酸甘三酯(≥95%)的混合物,即油脂,只含有极少量的杂质。
这些杂质虽然量小,但在影响油脂品质和稳定性上却“功不可没”。
按其在油脂中的存在状态可分为:2.1、悬浮杂质:①泥沙②料胚粉末③饼渣④草屑根据该类型杂质在大小和比重上与油有差异,去除方法可用过滤,沉降。
2.2、水分。
根据水在100℃(当然,在真空下这个温度会低一些)时为气态的特性,去除可选用热脱水。
菜籽油基本生产流程及关键控制环节
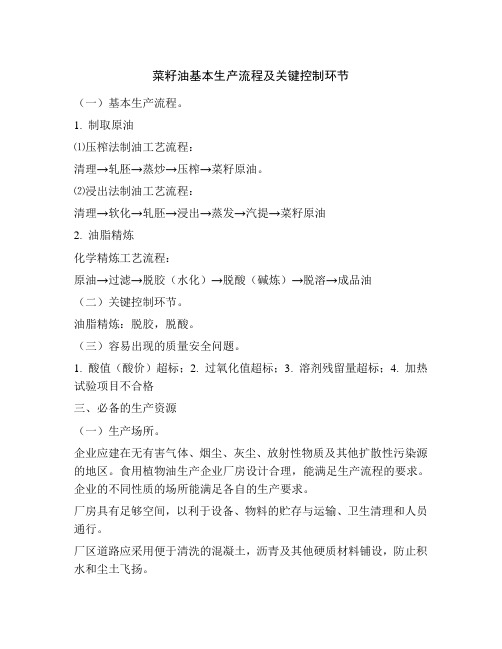
菜籽油基本生产流程及关键控制环节(一)基本生产流程。
1. 制取原油⑴压榨法制油工艺流程:清理→轧胚→蒸炒→压榨→菜籽原油。
⑵浸出法制油工艺流程:清理→软化→轧胚→浸出→蒸发→汽提→菜籽原油2. 油脂精炼化学精炼工艺流程:原油→过滤→脱胶(水化)→脱酸(碱炼)→脱溶→成品油(二)关键控制环节。
油脂精炼:脱胶,脱酸。
(三)容易出现的质量安全问题。
1. 酸值(酸价)超标;2. 过氧化值超标;3. 溶剂残留量超标;4. 加热试验项目不合格三、必备的生产资源(一)生产场所。
企业应建在无有害气体、烟尘、灰尘、放射性物质及其他扩散性污染源的地区。
食用植物油生产企业厂房设计合理,能满足生产流程的要求。
企业的不同性质的场所能满足各自的生产要求。
厂房具有足够空间,以利于设备、物料的贮存与运输、卫生清理和人员通行。
厂区道路应采用便于清洗的混凝土,沥青及其他硬质材料铺设,防止积水和尘土飞扬。
厂房与设施必须严格防止鼠、蝇及其他害虫的侵入和隐匿。
生产区域(原料库、成品库、加工车间等)应与生活区分开。
(二)必备的生产设备。
1. 压榨法制油生产的企业应具备(1)筛选设备;(2)软化设备(需要软化时);(3)轧胚设备(需要轧胚时);(4)蒸炒设备(需要蒸炒时);(5)压榨设备;(6)毛油过滤设备;(7)其他必要的辅助设备。
2. 采用浸出法制油生产的企业应具备(1)筛选设备;(2)软化设备;(3)轧胚设备;(4)压榨设备;(5)浸出器(6)蒸发器;(7)汽提塔;(8)蒸脱机;(9)其他必要的辅助设备。
3.油脂精炼设备(1)脱胶设备(炼油锅,离心机);(2)碱炼设备(炼油锅,离心机);(3)脱溶(水)设备;(4)其他必要的辅助设备。
所列生产设备应根据生产工艺设计的需要进行配置。
四、产品相关标准GB2716-2005《食用植物油卫生标准》;GB1536-2004《菜籽油》;备案有效的企业标准。
油脂精炼车间工艺概述

工艺概述中和段:主要是脱胶脱酸脱水.通过加入电解质磷酸使非亲水磷脂转变成亲水性磷脂胶体并钝化脱除分散相结合在一起的微量金属离子用碱来中和油脂中存在游离脂肪酸等物质反应生成钠皂成絮凝状物通过离心分离去除. 油中的残皂由硅藻土吸附通过过滤而得到中和油脱色段:主要脱除油中的色素.在一定条件下利用白土的吸附性在搅拌器搅拌下使白土与油充分接触最大限度的吸附色素通过过滤机滤去白土和其它杂质而得到脱色油. 脱臭段:主要是脱除油中臭味组分.利用臭味组分和甘三脂的蒸汽压不同在真空高温条件下利用汽提原理把臭味组分从油中分离出来中和段工艺流程图毛油→加热→加酸反应→冷却→加碱反应→蒸汽加热→离心分离→硅藻土吸附皂→真空干燥→过滤→中和油P2500→HX2503→MX2504→TK2505→CO2507→MX2508→T2509 →HX2511→CF2512 →TK2514→DR2517→F2691/2/3/4→T2524 中和油→换热加热→白土脱色→过滤→析气→加热→换热→高温加热→终端加热→脱臭→换热→冷却→抛光过滤→成品P2670→E2600→B2610→F2691/2/3/4→F2695/6→D2770→F2791/2→E2701→VHE27 03→E2702→VHE2704→DEO2710A→DEO2710B→VHE2703→E2600→E2706→F27 93/4 1 中和段工艺说明 1.1 加热器用3bar steam将油加热到65-90℃左右获得最佳反应温度。
1.2 混合器通过搅拌器使油和磷酸混合均匀。
1.3 酸反应罐磷酸把油中非水化磷脂转化为亲水磷脂起电解质作用除去磷脂和色素。
1.4 冷却器用冷水冷却油温将油冷却到40-75℃左右避免油温过高。
1.5 混合器通过搅拌器使油和碱混合均匀。
1.6 碱反应罐碱和油反应除去游离脂肪酸形成皂脚。
1.7 离心机离心除去大部分皂脚。
1.8 脱皂罐: 通过硅藻土吸附油中残余的皂。
[工学]第六章油脂精炼2
![[工学]第六章油脂精炼2](https://img.taocdn.com/s3/m/40653bcf172ded630b1cb6c2.png)
主要内容 一、碱炼脱酸 二、其他脱酸方法
一、 碱炼脱酸
(一)碱炼脱酸的基本原理及作用 (二)影响碱炼效果的因素 (三)碱炼损耗及碱炼效果 (四)碱炼脱酸工艺 (五)碱炼脱酸设备
(一)碱炼脱酸的基本原理及作用
1、中和反应 (1)烧碱中和游离脂肪酸: RCOOH + NaOH === RCOONa + H2O (2)钠皂为表面活性物质: 吸附其他杂质形成皂脚与油脂分离。 ( 3)磷脂、棉酚与烧碱中和皂化反应形成皂脚。 (4)少量中性油皂化: 引起油脂精炼损耗增加。
3、操作温度
(1)初温:加碱时粗油温度,低温避免中性油 皂化。 (2)终温:反应后油-皂粒明显分离时,释放 出中性油,并利于油-皂粒的分离所达到的最 终油温。 (3)升温速度:自油-皂粒明显分离至终温的 速度。 一般1℃/分为宜。 (4)间歇式操作:高温淡碱,低温浓碱。 (5)离心机连续操作:分离温度一般80~90℃。 加碱混合温度一般为50℃左右。
4、操作时间 操作时间影响主要表现在中性油皂化损失和综合 脱杂效果。接触时间愈长,中性油被皂化的机率愈 大;但有利于其他杂质的脱除及油色的改善 5、混合与搅拌 混合或搅拌的强度要强烈,以使碱液在油相中高 度分散。 为增进碱液与游离脂肪酸的相对运动,使皂膜尽 快脱离碱滴,同时又要避免皂膜过度分散而引起乳 化,促进皂粒絮凝,混合与搅拌强度要温和。 间歇式碱炼,混合时转速为60 r/min,反应时 30~15 r/min。 连续式碱炼,混合时采用高强度混合器,之后在 慢速反应罐中进行反应。
② 超量碱: 为了弥补理论碱量在分解和凝聚其他杂质、皂化 中性油以及被皂膜包容所引起的消耗。 a、间歇式超碱量: 一般为油量的0.05%~0.25%,质量劣变的粗油 可控制在0.5%以内; b、连续式的超碱量: 一般为10%~50%的理论碱量。 c、超量碱的确定的原则: 必须根据粗油品质、精油质量、精炼工艺及精炼 损耗等综合进行平衡;可由小样试验确定。
C油脂精炼-脱酸

OO
棉酚钠
O CH3
loozii0633
sss
8
(二)影响碱炼反应速度的因素
化学动力学因素(与浓度和温度有关)
根据质量守恒定律,中和反应的速度方程式如下:
V1 = K1[CA]m ·[CB]n 式中:V1 — 化学反应速度(mol / l·min);
K1 —反应速度常数(与反应物性质和温度有关); CA —脂肪酸浓度(mol / l); CB —碱液浓度(mol / l); m —该反应对于反应物A来讲是m级反应; n —该反应对于反应物B来讲是n级反应。
比重 (d)
1.15 1.161 1.170 1.180 1.190 1.200 1.210 1.220 12.30 1.241 1.252 1.263
百分浓度 当量浓度 (%) (N)
13.50 14.24 15.06 16.00 16.91 17.81 18.71 19.65 20.60 21.55 22.50 23.50
可凭经验或通过小试来确定。
loozii0633
sss
18
① 理论碱
理论碱可按原油酸值或游离脂肪酸的 百分含量进行计算。
当原油的游离脂肪酸含量以酸值表示时:
式中:GNaOH — 氢氧化钠的理论添加量(kg); Go — 原油脂的重量(kg); VA — 原油脂的酸值(mgKOH / g 油); M NaOH — 氢氧化钠的分子量(40.0); M KOH — 氢氧化钾的分子量(56.1)。
油脂脱酸
碱炼脱酸 蒸馏脱酸 溶剂萃取脱酸 酯化脱酸
L·Z
loozii0633
sss
1
概述
脱除原油中游离脂肪酸的过程即为脱酸 当今世界四大先进脱酸技术
油脂的精炼(Oil Refining)讲解
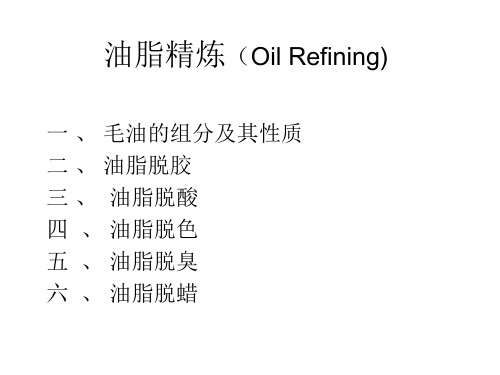
一 、 毛油的组分及其性质 二 、 油脂脱胶 三 、 油脂脱酸 四 、 油脂脱色 五 、 油脂脱臭 六 、 油脂脱蜡
概论
1、油脂精炼的目的: A、除去杂质;B、提高产品质量;C、利于安全储存。 2、油脂精炼要求: A、确定油脂精炼深度; B、组合精炼工艺合理; C、减少中性油和有益成分的损失; D、有利于副产物的综合利用; E、降低能量消耗; 3、油脂精炼方法: A、物化方法;B、化学方法;C、物理方法;
结晶塔
养晶塔
连续长混碱炼工艺流程
离心机工作原理图
Alfa Laval PX离心机碟片
第四节 脱色 (bleaching)
一、吸附脱色 二、工艺与设备
1、色素的成份
(1)天然色素: 油料中所含色素在制油过程进入油中。如叶绿 (黄)素、类胡萝卜素、棉酚。 (2)加工色素: 油脂生产中新生成的色素。 A、叶绿素受高温作用转变成叶绿素红色变体; B、游离脂肪酸与铁离子作用生成深色的铁皂; C、蛋白质、磷脂等有机降解产物; D、糖类的焦化,色原体氧化后呈现出颜色等;
2、油脂脱色方法
(1)吸附脱色;
(2)加热脱色:(类胡箩卜色素对热不稳定,经氧 化能变成无色物质)
(3)化学试剂脱色;
3、脱色工段作用
(1)脱除色素;
(2)脱除微量金属离子; (3)脱除残留皂粒、胶质; (4)脱除部分臭味物质; (5)脱除有毒物质;多环芳烃和残留农药、氧化产 物等。
4.吸附剂
水化脱胶工艺
1、间歇式水化脱胶工艺 软水 ↓ 过滤毛油→预热→水化→静置沉降→分离→含
水脱胶油→干燥(脱溶)→脱胶油 回收油←油脚处理←富油油脚
连续水化脱胶工艺流程
第三节 油脂脱酸(Oil deacidify)
油脂精炼工艺脱酸-PPT
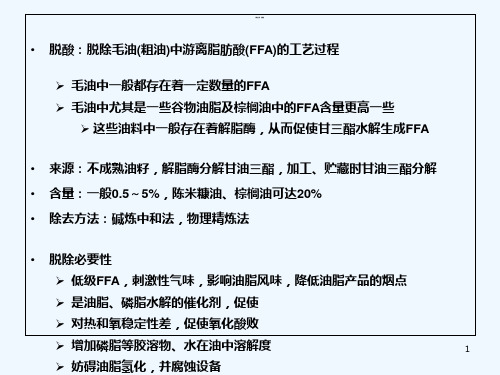
22
• 1.3.3.操作温度
• 中性油被皂化的机率与操作温度正比
➢ 初温:加碱时毛油的温度;低温避免中性油皂化
➢ 终温:反应后油-皂粒明显分离时,释放出中性油,并利于油-皂粒的分离 所达到的最终油温
➢ 加快吸附色素等杂质,促进皂粒进一步絮凝呈皂团→有利油皂分离
➢ 升温速度:自油-皂粒明显分离至终温的速度
➢ 毛油的酸值:酸值↑→浓度↑ ➢ 毛油的含杂量:含杂量↑→浓度↑ ➢ 毛油的色泽:色泽↑→浓度↑ ➢ 毛油的脱色程度:脱色程度↑→浓度↑ ➢ 操作温度:温度↑→浓度↓ ➢ 中性油皂化损失:浓度↑→损失↑ ➢ 皂脚的稠度:浓度↑→稠度↑
毛油、成品油 酸值
毛油、成品油 色泽
皂脚密度
操作温度
成品油得率
21
• 皂膜絮凝 ➢ 结构松散的皂粒吸附毛油中的胶质、色素等杂质,并在电解质、 温度及搅拌作用下,相互吸引絮凝成大的胶团即“皂脚”
• 反应速度
➢ 反应动力学 ➢ 界面因素
V1 VV42
==DKKC12(1×CLAFC)m2
×
(CB)n
8
➢ 对流扩散
V3 = K3 ×V′
大家有疑问的,可以询问和交流
可以互相讨论下,但要小声点
25
➢ 滞留→在慢速反应罐中进行滞留反应
• 1.3.6.杂质的影响
➢ 毛油中杂质:胶溶性杂质、羟基化合物、色素等 ➢ 对碱炼效果有重要影响,促使碱炼产生持久乳化 ➢ 其他色素增加用碱量,造成中性油皂化机率 ➢ 磷脂、蛋白质等→ 增大炼耗;宜先脱胶,磷脂<1.5% ➢ 一酯、二酯→促乳化;甘一酯易皂化 ➢ 棉酚及其他色素→色泽深→宜用浓碱→增大中性油皂化
➢ 中性油被皂化的量随超量碱的增加而增大
简述食用油精炼工艺的原理

简述食用油精炼工艺的原理
食用油精炼工艺的原理是通过一系列的物理、化学和机械处理过程,从原油中去除杂质、脂肪酸和其他不良物质,提高油品的纯度和质量。
具体而言,食用油精炼工艺通常包括以下几个步骤:
1. 脱酸处理:将原油中的游离脂肪酸通过酸化反应与碱反应去除,以减少油的酸值。
此步骤通常使用磷酸或磷酸碱混合物进行。
2. 脱臭处理:通过蒸馏、蒸汽脱香和深度吸附等方法,去除原油中的异味物质,提高油品的气味。
3. 脱色处理:使用漂白土或活性炭等吸附剂,去除原油中的色素和杂质,改善油品的颜色和透明度。
4. 脱脂处理:通过机械或化学方法,从原油中去除不溶性物质和悬浮颗粒,以提高油品的清洁度。
5. 去烷处理:利用低温晶体化技术,去除原油中的低熔点脂肪酸和杂质,提高油品的抗氧化性和耐热性。
通过以上处理步骤,食用油精炼工艺可以有效地去除油中的不良物质和杂质,提
高油品的品质和口感,使其更加符合食品安全和健康的要求。
- 1、下载文档前请自行甄别文档内容的完整性,平台不提供额外的编辑、内容补充、找答案等附加服务。
- 2、"仅部分预览"的文档,不可在线预览部分如存在完整性等问题,可反馈申请退款(可完整预览的文档不适用该条件!)。
- 3、如文档侵犯您的权益,请联系客服反馈,我们会尽快为您处理(人工客服工作时间:9:00-18:30)。
2
3
总炼耗 中性油皂化
色泽和皂脚中的含油量随超量
。超量碱增大,皂脚絮凝好,
沉降分离的速度也会加快。
1 25% 超量碱/理论碱
皂脚含油
α-Laval快速混合连续碱炼中 超量碱与炼耗之间的关系
loozii0633 sss 22
超量碱的计算有两种方式:
A.对于间歇式碱炼工艺,通常以纯氢氧化钠占原油 量的百分数表示。选择范围一般为油量的0.05%-0.25%, 质量劣变的原油可控制在0.5%以内。 B.对于连续式的碱炼工艺,超量碱则以占理论碱的 百分数表示。选择范围一般为10%-50%。油、碱接触时间 长的工艺应偏低选取。
O
O
O
O
CH3
HCl
O
O
O CH3
棉酚 + NaOH
棉酚钠
loozii0633
sss
8
(二)影响碱炼反应速度的因素
化学动力学因素(与浓度和温度有关)
根据质量守恒定律,中和反应的速度方程式如下:
V1 = K1[CA]m ·[CB]n
式中:V1 — 化学反应速度(mol / l· min); K1 —反应速度常数(与反应物性质和温度有关);
loozii0633
CH2 OH CH OH O CH2 O
sss
+ HO(CH2 )2 N(CH3 )3 + R1COONa + R2 COONa OH ONa P OH
O (CH2 )2 N (CH3 )3 OH
磷脂的皂化
7
其它反应 黄曲霉毒素 B1 + NaOH
O O
NaOH
邻位香豆素钠
O Na O C HO O
loozii0633 sss 17
碱的用量
总碱量 = 理论碱 + 超量碱
理论碱:满足与游离脂肪酸中和所需要的碱量。
可通过查表或计算求得。
超量碱:满足其它反应及无形损耗所需要的碱。
可凭经验或通过小试来确定。
loozii0633
sss
18
① 理论碱
理论碱可按原油酸值或游离脂肪酸的 百分含量进行计算。
loozii0633
sss
23
③ 碱量换算
GNaOH GNaOH 理 GNaOH 超 (7.13104 VA B) GO C C
式中:GNaOH — 碱液量(kg); GNaOH理 — 理论碱(kg); GNaOH超 — 超量碱(kg); Go — 原油的重量(kg); VA — 油脂的酸值(mgKOH/g 油); B — 超量碱占油重的百分数; C — NaOH溶液的百分比浓度(W/W)。 油脂工业生产中,大多数企业使用碱溶液时,习惯采 用波美度为碱液浓度单位。各种常用烧碱溶液的重量百分 比浓度与波美度的关系可查表换算。 loozii0633 sss 24
loozii0633 sss 10
界面因素(与分散度有关)
油中游离脂肪酸与水中碱之间的反应属非均相反应。
V2 = K2 · F
式中 V2 — 非均态化学反应速度;
K2 — 反应速度常数; F — 脂肪酸与碱液接触的面积。
ห้องสมุดไป่ตู้碱炼操作时,碱液浓度要适当稀一些,碱滴应分
散细一些,使碱滴与脂肪酸有足够大的接触界面,以 提高中和反应的速度。
O(CH2)2N (CH3)3 OH
P OH
磷脂的水解
6
皂化反应
O CH2 CH CH2 O O O C O C O C R1 R2 + 3NaOH R3 CH2 CH CH2 OH OH + R1COONa + R2COONa + R3COONa OH
甘三酯的皂化
O CH2 CH CH2 O O O C R1 O C R 2 + 3NaOH O P OH
沉降分离皂脚中带有相当数量的中性油,一般呈三种 状态: ① 中性油胶溶于皂膜中(由于肥皂的增溶作用,使
部分中性油与皂中碳氢基结合);
② 中性油在胶膜与碱滴分离时落入胶膜内而被胶膜 包容;
③ 中性油在胶团絮凝沉降时,被机械地夹带和吸附。
以上三种状态的中性油,第一种不易回收,而后两种 较易回收。
loozii0633 sss 15
loozii0633
O R1 R2 + H2O R3
NaOH
CH2 CH CH2
O O OH
C O C
R1 R2 + R3COOH
甘三酯的水解
R1 R2 + 3H2O
NaOH
CH2 CH CH2
OH OH O O
sss
+ HO(CH2)2N (CH3)3 + R1COOH + R2COOH OH OH
当原油的游离脂肪酸含量以酸值表示时:
式中:GNaOH — 氢氧化钠的理论添加量(kg); Go — 原油脂的重量(kg); VA — 原油脂的酸值(mgKOH / g 油); M NaOH — 氢氧化钠的分子量(40.0); M KOH — 氢氧化钾的分子量(56.1)。
loozii0633
sss
19
loozii0633 sss
是对精炼成品油质 量影响最大的阶段
3
碱炼法是用碱中和油脂中的游离脂肪酸, 所生成的皂吸附部分其他杂质,而从油中重力 沉降分离或用离心机分离的精炼方法。
游离脂肪酸 + 碱 皂
氢氧化钠(烧碱)
碱炼用碱种类 碳酸钠(纯碱) 氢氧化钙
loozii0633 sss 4
一、碱炼的基本原理
界面反应
形成皂膜
定向排列,扩散反应 胶态离子膜形成
胶膜拉长 胶膜脱落 胶膜絮凝
碱炼脱酸过程示意图
胶膜是一表面活性物质,能吸附原油中的胶质色素等杂 质,并在电解质、温度及搅拌等作用下,相互吸引絮凝成胶 团,由小而大,形成“皂脚”,而从油中分离沉降下来。
loozii0633 sss 14
(四)皂脚含油
操作温度(℃) 初温 75-80 50-55 25-30 20-30
sss
终温 90-95 60-65 45-50 20-30
备 注 用于浅色油品精制 用于浅色油品精制 用于深色油品精制 用于劣质棉油精制
29
> 24
注:1N=(1 mol/L) ×离子价数
对于连续式碱炼,碱液的用量一般 以单位时间的流量进行换算:
Q1 r FFA % Q 1000 或 M N 1.78 Q1 r VA Q 100 N
式中:Q — NaOH溶液的流量(l/h); Q1— 原油的流量(l/h); r — 油脂的密度(kg/l); FFA%— 游离脂肪酸的百分含量; VA— 原油的酸值(mgKOH/g); M — 脂肪酸的平均分子量; N — 碱液的摩尔浓度(mol/l)。
loozii0633 sss 11
相对运动因素(与混合强度有关)
V3 = K3 ·V′ 式中:V′ — 反应物相对运动速度; K3 — 反应速度常数; 相对运动速度快(混合强度大): 反应形成的皂膜(胶膜)破裂,迅速离开反应界面。
碱液分散度高,碱滴更细,分布更均匀。
loozii0633
sss
12
分子扩散因素(与浓度差和扩散距离有关)
(一)化学反应 中和反应
RCOOH + NaOH RCOONa + H2O
不完全中和反应
2RCOOH + NaOH RCOONa· RCOOH + H2O
loozii0633
sss
5
水解反应
O CH2 CH CH2 O O O C O C O C
O CH2 CH CH2 O O O C O C O P OH
loozii0633
sss
26
(二)碱液浓度 碱液浓度的确定原则: ① 碱滴与游离脂肪酸有较大的接触面积,
能保证碱滴在油中有适宜的降速;
② 有一定的脱色能力;
③ 使油-皂分离操作方便。 酸值
loozii0633
色泽
sss
皂脚密度
27
碱液浓度的选择依据:
① 原油的酸值与脂肪酸组成 ② 制油方法 ③ 中性油皂化损失 ④ 皂脚的稠度 ⑤ 皂脚含油损耗 ⑥ 操作温度 ⑦ 原油的脱色程度
理论碱的计算
当原油的游离脂肪酸含量以百分含量表示时:
G NaOH GO FFA% 40.0 M
式中:GNaOH — 氢氧化钠的理论添加量(kg); Go — 原油脂的重量(kg); FFA%— 原油脂中游离脂肪酸百分含量; M — 脂肪酸的平均分子量;
loozii0633
sss
20
部分油脂中脂肪酸的平均分子量
loozii0633
sss
28
(三)操作温度
初温(中和温度) 终温(油-皂分离温度)
升温速度(以1℃/min为宜)
间歇式:温度相对低 连续式:温度相对高
碱液浓度与操作温度的关系(间歇式碱炼)
烧碱溶液浓度 (°Be′) 4-6 12-14 16-24
loozii0633
原油酸值 <5 5-7 >7 >9
扩散速率遵守菲克定律:
式中:V4 — 扩散速度; D — 扩散常数; C1 — 反应物液滴中心的浓度; C2 — 界面上反应物的浓度; L — 扩散距离[与形成的皂膜(胶膜)厚度有关]。
扩散速率与原油中的胶性杂质的多少有关。
loozii0633 sss 13
(三)碱炼反应过程
碱滴分出
重复界面反应 直至消耗殆尽
烧碱溶液波美度与比重及其他浓度的关系(15℃)
波美度 (°Be′) 4 6 8 10 11 12 13 14 15 16 17 18 比重 ( d) 1.029 1.043 1.059 1.075 1.083 1.091 1.099 1.107 1.116 1.125 1.134 1.143 百分浓度 (%) 2.50 3.65 5.11 6.58 7.30 8.07 8.71 9.42 10.30 11.06 11.90 12.59 当量浓度 (N) 0.65 0.95 0.33 1.77 1.98 2.20 2.39 2.61 2.87 3.11 3.37 3.60 波美度 (°Be′) 19 20 21 22 23 24 25 26 27 28 29 30 比重 ( d) 1.15 1.161 1.170 1.180 1.190 1.200 1.210 1.220 12.30 1.241 1.252 1.263 百分浓度 (%) 13.50 14.24 15.06 16.00 16.91 17.81 18.71 19.65 20.60 21.55 22.50 23.50 当量浓度 (N) 3.89 4.13 4.41 4.72 5.03 5.34 5.66 5.99 6.33 63.69 7.04 7.42