模具动静态验收表
模具动静态检查表

硬度计
打印去清晰无凸起
目视
高于型面0.1-0.2mm,工作面清晰 是否产生压痕 排气通畅 管理面95%准管理面90%凹模>80% 符合图纸,工件表面平整 带料冲压检查轮廓线是否清晰、顺畅 最经济下料尺寸
目视 目视 目视 目视 红丹粉 目视 目视 卷尺
贴合率≥80
目视 红丹粉
不能过紧或过松
目视 目视
目视.8,支撑面1.6
目视
无单边接触、无损伤、无松动现象
红丹粉
大型<0.1,中型<0.08,反侧导板≤0.0塞1 尺
≥85%,着色均匀
红丹粉
间隙<0.03
塞尺
扒钩间隙 侧冲0.5-1 吊冲<0.3
塞尺
粗糙度0.8
目视
按图纸要求
硬度计
≤0.03mm
塞尺
垂直于刃口≤100以内不允许超过3条裂纹目视
沧州瑞恒模具动、静态检查表
项目名称 工序名称 调试设备 630T
类别 序号
1
外 观 检 查
2 3 4 5 6
7
8
1
导
2
向
3
装
4
置
5
6
冲
1
载
2
落
3
料
4
、
5
冲
6
孔
7
、
8
切
9
边
10
部
11
分
12
13
前防撞梁左吸能盒内板
主压力
20
检查项目
静
模具颜色
模具铭牌
模具倒角、出气槽
刀块非工作面倒角、孔倒角
F标记、模具号
≤0.01mm
塞尺
模具动静态检验标准

镶
材质是否与图纸
17 块 刃口吃入量
积料不超过 3 片。刃口吃入量 3-5mm。
18 与 接刀缝
间隙规测量 0.05mm 以下
19 刀 镶块补焊
补焊光顺,横向裂纹无,纵向裂纹 100 mm 内允许 3 条
20 口 镶块与安装底面
自由状态,贴合间隙小于 0.02mm/与基体或背托贴合率大于 90%
21 冲 标准异形冲头
凹模套在斜面上要有防转措施,小于等于¢8 的冲头采用快换冲头 材质、编号与实物一一对应;字体工整,醒目,内容齐全
15kg 以上或难于取出的镶块应有起吊螺纹孔,并有标示
检查时看导柱、导板间隙;如果是钢板变形量大,涂红丹看导柱间隙。
除压(托)料面,其他地方都要倒角
压(托)料板与刃口配合间隙 0.5-0.8mm 单边至少有两处定位,进料方向有导入角,并且刚性良好。 压料板上要有导正销,导正销突出压料板时要有退料销 活动部分必须有安全护板。 沉孔深度一致,正反面要倒角。螺钉拧入直径 2 倍以上。 工作时不起作用,但位置分布要合理,孔四周用黄漆标注 与沉孔一致,正反面倒角,螺钉紧入量是螺钉直径的 2 倍
8
上、下模型面 R 角光顺,棱线清晰,油石抛光
上
9
压边圈
下
压料面油石抛光;拉延筋(槽)圆顺光滑。
10 模 排气孔
钻孔¢6 应在凹处不影响制件外观
11
防尘管
紧固可靠,通畅
12
材质与硬度 材质依技术协议及图纸,硬度不低于 HRC50
13
拉延成型标记 标记深度 0.3mm,左右件用“L、R”代替, 压印不得留在 A 表上
型 型面及压料面
14 面 空研
上下模空研。平面着色
模具验收检查表(动态)

全 5 压料圈的限位螺钉要对角固定(限位螺钉保证2个以上、起重孔应保证4个)
部
份
6
施压时聚胺脂缓冲器变形后不能与模具本体发生干涉,并且安装面面积应大 于变形后聚胺脂面积
7 聚胺脂安装螺钉要紧固
产品名称
2 判定 标记
合格 不合格 未装配 未确认
○
×
序号
△
——
检查时间
检查员
备注
无此项 /
1 拉延筋部位的间隙取(板厚+0.15mm以上)
车型
令号
模具图号
分类 NO
检查项目
1 导板及Ф60以上衬套应用铜基自润结构,不允许拉毛
2 导板导向间隙<0.12mm,间隙均匀
模 3 导滑面研合率的确认(红丹粉研合70%以上)
具 导
4 导板的垂直度要求应在0.03/150mm以内
向 5 上下模导向面中心有无错位 部
位 6 凸模和压边圈的导向间隙单边<0.12以下,两边保持均匀
7 导柱的导向间隙<0.03mm
模具检查专用表——模具动态(拉延序用)
模具名称
自 检
1
2
分 类
NO
1
检查项目 压料圈上升时,应与上底板无干涉(与上模应有50mm)
自检 1
2 气垫防护板要稳定,可靠(防护板高度=气垫行程+20mm)
3 到下死点时,聚胺脂防护板应有2-5mm间隙
安4
压料圈限位螺钉长度要比其它安装面长23-30mm
2 定位板有效导向部位高度应合适(导向高度=板料厚度+30mm)
定 位
3
定位板与安装面空开处间隙要满足使用要求,防止间隙过大使板 料变形或起皱
钢板模具动静态检查表
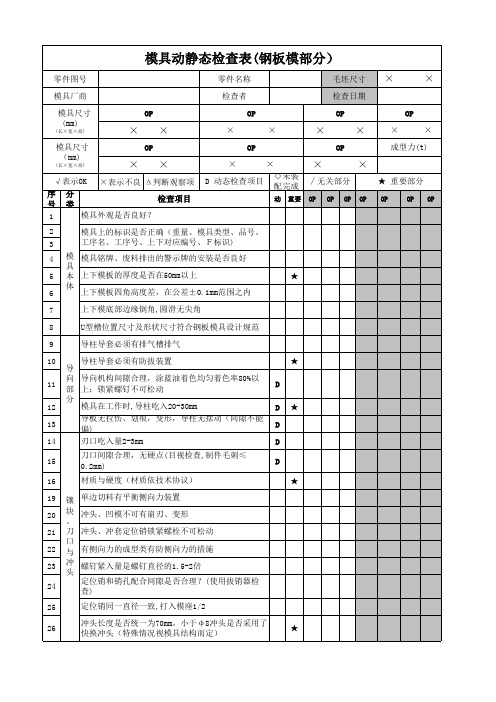
D D
D D
★ ★
64 65 66 67 68
标准件全部按协议要求使用 模柄需采用法兰式模柄 其 到底标记深度0.3mm,不易辨别左右件用L、R代替 它 制件无起皱、压伤、隐裂、棱线清晰,符合数模 制件毛刺≤0.2mm
★
D D
验收结论
ห้องสมุดไป่ตู้
确认人
动 重要 OP OP OP OP
★ 重要部分
OP OP OP
1 2 3 4 5 6 7 8 9 10 11 12 13 14 15 16 19 20 21 22 23 24 25 26 镶 块 、 刀 口 与 冲 头
模具外观是否良好? 模具上的标识是否正确(重量、模具类型、品号、 工序名、工序号、上下对应编号、F标识) 模 模具铭牌、废料排出的警示牌的安装是否良好 具 本 上下模板的厚度是否在50mm以上 体 上下模板四角高度差,在公差±0.1mm范围之内 上下模底部边缘倒角,圆滑无尖角 U型槽位置尺寸及形状尺寸符合钢板模具设计规范 导柱导套必须有排气槽排气 导柱导套必须有防拔装置 导 向 导向机构间隙合理,涂蓝油着色均匀着色率80%以 部 上;锁紧螺钉不可松动 分 模具在工作时,导柱吃入20-30mm 导板无拉伤、划痕,变形,导柱无摆动(间隙不能 偏) 刃口吃入量2-3mm 刀口间隙合理,无硬点(目视检查,制件毛刺≤ 0.2mm) 材质与硬度(材质依技术协议) 单边切料有平衡侧向力装置 冲头、凹模不可有崩刃、变形 冲头、冲套定位销锁紧螺栓不可松动 有侧向力的成型类有防侧向力的措施 螺钉紧入量是螺钉直径的1.5-2倍 定位销和销孔配合间隙是否合理?(使用拔销器检 查) 定位销同一直径一致,打入模座1/2 冲头长度是否统一为70mm,小于φ 8冲头是否采用了 快换冲头(特殊情况视模具结构而定) ★ ★ D D D D D ★ ★
模具静态验收单
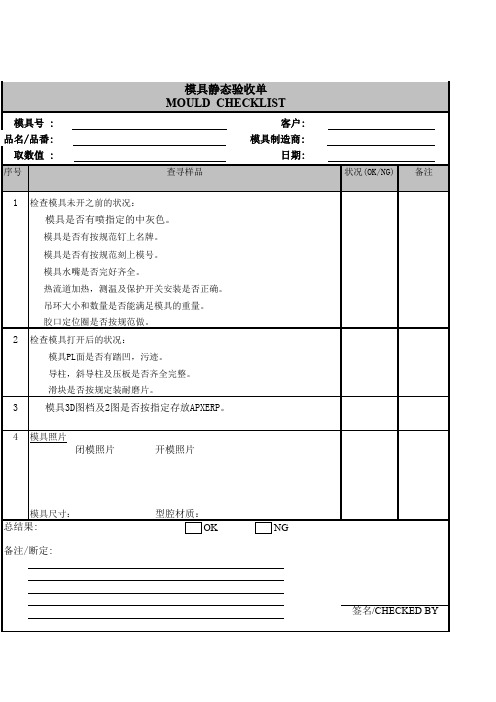
胶口定位圈是否按规范做。
2 检查模具打开后的状况:
模具PL面是否有踏凹,污迹。
导柱,斜导柱及压板是否齐全完整。
滑块是否按规定装耐磨片。
3
模具3D图档及2图是否按指定存放APXERP。
4 模具照片 闭模照片
开模照片
状况(OK/NG) 备注
模具尺寸: 总结果:
备注/断定:
型腔材 BY
模具号 : 品名/品番:
取数值 : 序号
模具静态验收单 MOULD CHECKLIST
客户: 模具制造商:
日期: 查寻样品
1 检查模具未开之前的状况:
模具是否有喷指定的中灰色。
模具是否有按规范钉上名牌。
模具是否有按规范刻上模号。
模具水嘴是否完好齐全。
热流道加热,测温及保护开关安装是否正确。
吊环大小和数量是否能满足模具的重量。
模具验收通过判定标准

3)顶杆端部固定台阶为标准尺寸,
不允许有打磨痕,顶杆台阶下部不允
许安装垫圈
顶杆及孔
17
4)顶杆尾部的防转销按标准制作
检查
5)顶杆及顶杆固定板的对应编号规
范、清晰、不混淆
6)顶杆与型腔固定孔的配合长度在 30mm~50mm 之间
7)型腔顶杆固定孔与顶杆的配合尺 寸保证设计要求,保证成型时不漏塑 料
1)导柱、导套同心
4
内滑块检查
利取件
2)内滑块不转动和上下摆动
导柱、导套
5
保证生产过程中导柱、导套不单边和拉伤
检查
冷却水和抽
6
工作时不漏水、不漏油
芯油检查
模具喷嘴检
7
保证成型时不漏塑料
查
脱模性好、不用脱模剂,顶出时制品不自由
8
脱模性检查
下坠
5 件连续成
9
成型正常、不发生异常
型检查
30 件连续成
10
成型正常、不发生异常
25
检查
中不变形
1)使用规定材质,并出具材质报告
模具材质
26 检查
2)模具型腔、型芯必须进行探伤,并
出具探伤报告
标准件检
符合技术要求规定的标准件种类、数
27
查
量
综合判定:
甲方:
乙方:
签字: 日期:
签字: 日期:
2、模具动态验收标准见表 2
工装模具验收报告书 (动态检查)
类别:模具
名称:
序 检查项目
号
2)皮纹无锈蚀、无针眼
芯表观
要求,保证制品脱模时皮纹不拉伤
质量检查
4)无皮纹模具型腔表面粗糙度在 0.2
[过程验收]模具静检标准表
![[过程验收]模具静检标准表](https://img.taocdn.com/s3/m/b5f4183af111f18583d05a5f.png)
1 压料板缓冲的滑动行程良好吗? 2 压料板和切刀,曲刃的间隙良好吗? 3 弹簧,优力胶的装配良好吗? 4 5 6 7 压料板吊挂螺丝孔位置良好吗? 压料板与下模接触率是否良好? 模具有局部脆弱部位吗? 缓冲的逃孔良好吗?
H 切 刀 曲 刃 冲 8 冲孔衬套防止转良好吗? 孔 9 快换凸凹模的锁紧可靠,拆卸方便. 10 刃口无咬合、崩刃. 11 1 I 2 3 刃口镶块接合面间隙是否良好? 废料长度在指定尺寸以内吗? 废料滑槽的长、宽、高、度适当吗? 废料滑槽的倾斜角度有利于废料滑出?
K 钣 件 品 质
1 破裂,裂痕 2 重叠,皱纹 3 咬伤,刮伤 4 毛边,翻边 5 模具的接触率
模具合格证
发运 返工 × √
与机能无关的尖角是否有倒角? 安全防护板的安装.(气垫行程+20) 模具翻转处设置翻转R角?(保护起吊钢丝) 吊耳或吊棒大小合适?铸入吊柄紧固? 吊耳周围无铸造缺陷.
废 4 周围落料、切边废料排出是否良好? 料 5 废料落下孔与废料盒位置是否良好? 落 6 废料滑槽的安装与肋的逃隙良好吗?制品形状的配合好吗? 投 2 定位器的调整量及逃隙好吗? 入 3 制品会附着在上模或下模吗? 取 4 定位器类的固定良好吗? 出 5 制品手取空间良好吗? 1 模具重量及尺寸适当吗? 2 模具定位用快速定位块的安装良好吗? 3 模具定位键槽良好吗?
不良 × 检未装配,未加工 ◇ 查 判定保存 △ 记 良好 ○ 号 无关部分 检查日期: 年月
日
特记事项:
7 上模/下模/压料芯具有翻转孔? 8 起吊棒必须自锁. 9 模具导向有防反? 1 2 C 3 型 面 4 5 6 D 压 料 与 缓 冲 制品与下模基准面的接触率良好吗?(85%) 模具的基准面钣厚确认? 制品与压料板接触好吗? 透油,透气良好吗?(防尘管) 上下模平衡块、墩靠块是否贴合? 模具型面的表面粗糙度良好吗?
模具验收计划表格模板

[人员姓名 3]
4
模具材料
使用指定的材料,材质符合要求
材料检验报告审 核
[具体时间 4]
[人员姓名 4]
5
试模产品质量
产品无飞边、毛刺、缺料等缺 陷,尺寸精度符合要求
抽样检测产品
[具体时间 5]
[人员姓名 5]
6
模具标识
模具编号、名称、生产日期等标 识清晰准确
目视检查
[具体时间 6]
[人员姓名 6]
模具验收计划表格模板
序号
验收项目
验收标准
验收方法
验收时间
验收人员
1
模具外观
无明显划痕、锈迹、变形等缺陷 目视检查
[具体时间 1]
[人员姓名 1]
2
模具尺寸
符合设计图纸要求,公差在允许 范围内
ห้องสมุดไป่ตู้量具测量
[具体时间 2]
[人员姓名 2]
3
模具结构
结构稳固,运动部件灵活,无干 涉现象
手动操作检查
[具体时间 3]
备注
7
模具文件
提供完整的模具设计图纸、使用 说明书、维护手册等
文件审核
[具体时间 7]
[人员姓名 7]
模具动、静检验收表

合格/不合格
合格/不合格
合格/不合格 合格/不合格 合格/不合格
合格/不合格
合格/不合格
合格/不合格 合格/不合格 合格/不合格 合格/不合格 合格/不合格 合格/不合格 合格/不合格 合格/不合格 合格/不合格 合格/不合格
合格/不合格
48
废料滑道,防飞 溅
49
ቤተ መጻሕፍቲ ባይዱ
废料盒、轨道式 滑道 废料处理(废料 滑道)
制造加工
50
51 冲孔冲头、凹模 52 压料圈(单动)
53
导向面(铸造本 体)
54 导板
55
限制器、平衡垫 块
56 调整垫片、垫块 57 弹性件(汽缸、 弹簧、橡胶)
58 氮气缸 装配 59 气路安装座 60 节流阀 61 管子 气动废料托起装 置
62
63 顶件器
废料是否满足每一片都滑出。宽度、滑道间隙 是否合理。滑槽的板厚是否合理。第二节滑道 的固定。2次滑槽是否是一触动就能轻便操作。 第一节本体色,第二节黄色。圆形滑道、滚轮 、镶入滑道、挂钩等是否合理。 有防止轨道式滑道飞溅措施。盒子是否有限制 器,排泄孔。把手的强度是否足够。废料盒的 取出搬运是否容易。四周立壁排水孔。取送是 否干涉。全部涂黄色(表示位置)。 挂废料原因(安装板确认、铸件出毛刺、孔偏 移、不贯通)、镶入。 凸模安装、拆卸的方便性。有防止脱落的限位 压板。防转、镶嵌、形状加工。 分型面间隙:0.5±0.3。不允许干涉出现的划 痕、擦痕等。强度足够。锐角处倒R。托杆接触 均匀。 初始接触部位R5。不允许有铸造缺陷、划痕等 缺陷,倒角C2(吊楔接触面R10)。加工光洁度 要好。螺钉紧固可靠,(沉头深度不小于2mm) (钢绳接触处R5)。斜楔、吊楔导向接触平 稳,导向面接触均匀。 安装面倒角C1,厚度必须为标准值。不得有滑 伤。受力一侧有反侧,高度不低于厚度1/2,间 隙0。安装螺钉沉入深度至少2mm。板导入处R5 、标准件,无研磨痕迹。 安装面必须是加工面。周边倒角C2。不能有压 痕划伤。作为合模标记(合模0间隙)。刻印标 记。是否有位置偏移(上下不对中),红色。 压料板的平衡块使用锥形平衡块。 采用钢质垫片或钢板。使用螺钉紧固在模具本 体上。 要有防护板。有窝座的是否有座面偏移。无窝 座的是否有防倒伏措施。压力表外露可见。强 度是否满足要求。氮气缸接触面布置垫片。 空载时:上模活动元件氮气缸不允许受力;下 模活动元件只允许承受活动元件本身重力。 安装位置是否满足要求。安装座或气路接头涂 标志色。装置名称标识、工作性能。不突出模 具轮廓以外。 操作空间、安装方向合适。固定在模具本体上 。 下垂(用手拉下不允许出模外)。分管接头是 否有漏气现象,用管夹子固定在模具本体。外 露部分设置防护套。 动作情况、功能是否满足需要(顶件器的位置 、形状)。对操作者有无危险。动作部位涂黄 色、防转、防脱落,废料无飞溅。 功能满足要求,动作平稳。对操作者有无危险 性。活动部位涂黄色。对制件的压痕处理。推 件器、有无干涉现象。制件攒动量在1mm内。
冲压模具验收动静态检查表

A
√
/
/
87
安全护板
厚度22∙Omm,操作安全
C
√
/
/
88
销钉
松紧合适,上下各销•半,安装防脱落装置
C
√
√
√
√
89
侧销孔
船销直径+0∙2mm=侧销孔宜径,无兄动
A
/
√
√
Z
90
侧销固定长度
原则上固定25mm根据直径大小现场判定
A
/
√
√
/
91
侧销锁板销钉
锁板按要求安装摞钉孔不允许人工打磨或加工
65
翻边整形刃口面
顺滑,无凸凹不平等缺陷
B
/
/
/
√
66
翻边整形块安装
间隙W0.05mm,无台阶,圆角顺滑一致
B
/
/\
/
√
67
翻边顶出器顶杆
螺钉孔与顶杆壁厚保证3-5M
B
/
/
/
√
冲压模具静态验收检查表
项目
CN200
零件名称
螺母片
备注:符合要求填写,不符合要求填写“X”,不适用填写
*7”具体问题填入“模具问题记录表”
目视
B
/
7
4
/
102
防护板涂黄色
目视
C
√
Z
/
Z
103
取出压料芯前需要先拆除的镶块涂红色
目视
A
/
√
/
/
104
模具存放块外周边涂红色.
目视
A
√
√
模具动静态检查表--

目视
2 导柱与导套配合间隙 向 3 导板面配合间隙 装 4 滑动导板接触面接合率
▲ 无单边接触,无损伤 大型<0.1,中型<0.08,反侧导板≤
▲
0.01 ▲ ≥85%,分布均匀
5 斜楔机构运动导滑面
▲ 间隙<0.03mm
置
6
各种斜楔机构运动灵活,扒钩间隙合 理
扒钩间隙侧冲0.5~1mm, ▲ 吊冲<0.03mm
目视 目视 目视
5 起吊孔的螺纹规格 检 6 压板槽位置、尺寸及数量
● 按用户和图纸要求 ▲ 按图纸尺寸
目视 直尺
查 7 模具定位键或定位孔 8 空气管接头座及电气安装位置
▲ 按图纸尺寸 ▲ 按图纸尺寸,不能超出模体
直尺 目视
9 闭合高度检查
▲ 按图纸尺寸
卷尺
导 1 导向面粗糙度
●
工作面和导入圆角粗糙度0.8,支承面 粗糙度1.6
︶ 部
11
10°~30°斜面冲裁时,冲孔及修边凸 模处理
工作刃口提前切入深度按2个料厚处 ▲ 理,冲头是否防转
直尺 目视
分 12 刃口切入量
▲ 按图纸规定
直尺
13
退料板与凸模,压料板与凹模的导正 间隙
▲ 间隙0.3~0.5mm
成 1 镶块接缝间隙 形 ︵ 2 工作面粗糙度
拉 延 3 工作表面无缺陷 、
● ≤0.01mm
成 7 凸凹模镶块材料牌号及件号标记
● 打印清晰,无凸起
形 8 上模销孔加丝堵
● 是否防止上模销子松动脱落
、 9 拉延模到底标记
整 形
10
卸料板型面与工件接触面
高于型面 ▲ 0.3mm,工件表 ▲ 是否产生压痕
模具动静态检验标准

上模销孔有防落措施,销不过紧过松,同一直径长度一致打入模座 1/2
深度一致,倒角 3×45 角,弹簧与面接触平稳、可靠,力量足够。
导
31
导柱、导套及间隙 向
32
废料处理
操
33 作 废料
34 性 废料装置
35
制件操作性与定位
36
防呆
37 安 安全护板
38 全 加垫
39
防反
40 41 外
观 42
43 44 其 45 他 试模次
8
上、下模型面 R 角光顺,棱线清晰,油石抛光
上
9
压边圈
下
压料面油石抛光;拉延筋(槽)圆顺光滑。
10 模 排气孔
钻孔¢6 应在凹处不影响制件外观
11
防尘管
紧固可靠,通畅
12
材质与硬度 材质依技术协议及图纸,硬度不低于 HRC50
13
拉延成型标记 标记深度 0.3mm,左右件用“L、R”代替, 压印不得留在 A 表上
5
检 中心键、快速 与(所选压机)图纸一致,机床精加工。中心槽为通槽(双动模除外) 查 定位
6
三销刻印
准确、齐全、工整、清晰
7
铸件外观
无夹砂、裂痕、变形和大的铸造缺陷、所有非工作面棱角倒角
承制 厂商 NO1 NO2
8
模具的标识 对于零件号、车型号、模具名称、工序号、模具号、模具铭牌、F、其他技术要求标识等
体
4 检 U 槽位置、数量
与图纸一致;L≥1500mm 6-8 个,L<1500 mm4-6 个
36 观 位颜色
客户指定颜色
37
铭牌、顶杆图 内容填写齐全、准确、清晰,顶杆顶出高度与图纸相符
福锐静动态验收表 (2)
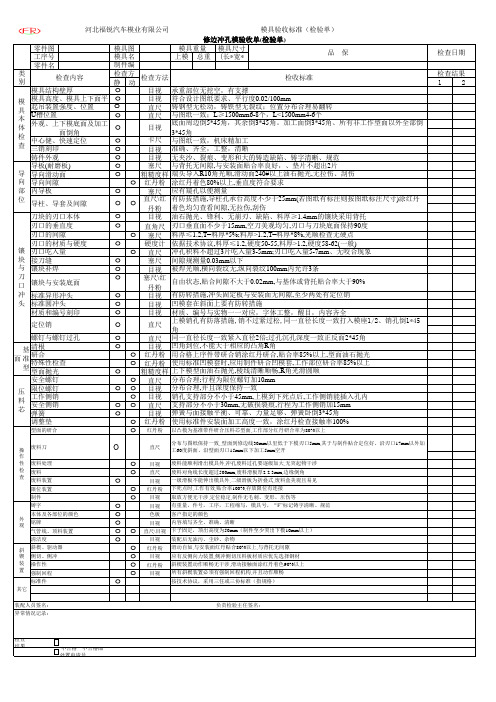
零件图模具尺寸工序号上模总重(长*宽*零件名静动12目视目视直尺直尺卡尺目视目视塞尺粗糙度样红丹粉塞尺目视直角尺塞尺硬度计直尺塞尺目视塞尺\红丹粉目视目视目视直尺目视红丹粉红丹粉粗糙度样直尺目视目视直尺目视红丹粉红丹粉目视直尺目视红丹粉目视目视色板目视直尺\目视目视红丹粉目视红丹粉目视检查结果 不合格 不合格品处置申请号废料刀直尺制件编检查方铸钢型无松动,铸铁型无裂纹;位置分布合理易翻转与图纸一致;L ≥1500mm6-8个,L<1500mm4-6个检收标准定位销上模销孔有防落措施,销不过紧过松,同一直径长度一致打入模座1/2、销孔倒1*45角直尺导板(耐磨板)与背托无间隙,与安装面贴合率良好,、垫片不超出2片三销刻印检查结果检查内容检查方法目视U 槽位置起吊装置强度、位置用合格上序件带研合销涂红丹研合,贴合率85%以上,型面油石抛光有防拔措施,导柱孔承台高度不少于25mm(若图纸有标注则按图纸标注尺寸)涂红丹着色均匀查看间隙,无拉伤,刮伤刀块的刃口本体油石抛光、锋利、无崩刃、缺陷、料厚≥1.4mm 的镶块采用背托刃口的垂直度刃口垂直面不少于15mm,空刀美观均匀,刃口与刀块底面保持90度刃口的间隙镶块与安装底面料厚≤1.2,T=料厚*5%;料厚>1.2,T=料厚*8%,光顺检查无硬点分布与图纸保持一致,,型面到修边线30mm 以里低于下模刃口5mm,其于与制件贴合定位好、沿刃口17mm 以外加工60度斜面、沿型面刃口15mm 以下加工5mm 空开自由状态,贴合间隙不大于0.02mm,与基体或背托贴合率大于90%标准异形冲头有防转措施,冲头固定板与安装面无间隙,至少两处有定位销凹模套在斜面上要有防转措施螺钉与螺钉过孔同一直径长度一致紧入直径2倍;过孔沉孔深度一致正反面2*45角清根凹角到位,不能大于相应的凸角R 角研合使用标准凹模套时,应用制件研合凹模套,工作部位研合率85%以上型面抛光上下模型面油石抛光,棱线清晰顺畅,R 角光滑圆顺型面的研合以凸模为基准带件研合压料芯型面,工作部分红丹研合率为80%以上特殊性检查废料装置一级滑板不能伸出模具外,二级滑板为折叠式,废料盒美观且易见限位装置下死点时,工作有效,贴合率100%,存放限位有连接废料处理废料能顺利滑出模具外,冲孔废料过孔要逐级加大,无突起物干涉废料制件取放方便无干涉,定位稳定,制件无毛刺、变形、压伤等斜楔、驱动器侧切、侧冲操作性强制回程模具名内容填写齐全、准确、清晰清洁度装配后无油污、尘砂、杂物标准件按技术协议,采用三住或三协标准(指规格)滑动自如,与安装面红丹贴合80%以上,与背托无间隙材质、编号与实物一一对应,字体工整,醒目,内容齐全河北福锐汽车模业有限公司模具验收标准(检验单)修边冲孔模验收单(检验单)模具图模具重量品 保检查日期承重部位无挖空,有支撑准确、齐全,工整,清晰铸件外观无夹沙、裂痕、变形和大的铸造缺陷、铸字清晰、规范与图纸一致,机床精加工外观、上下模底面及加工面倒角类别底面周边倒5*45角,其余倒3*45角。
静态检查表
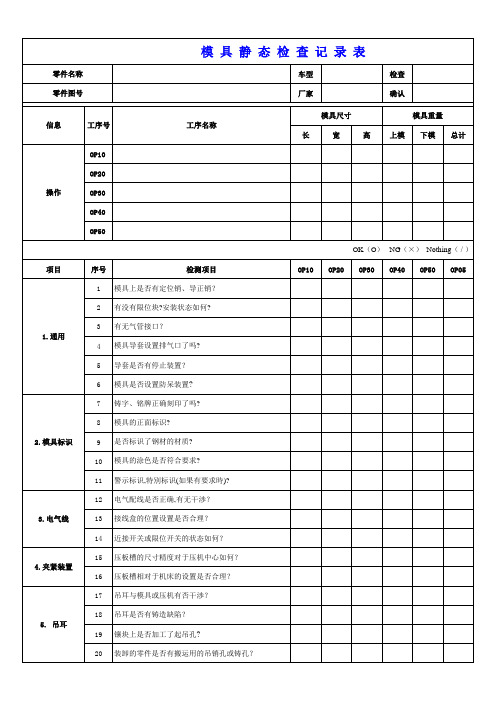
模具静态检查记录表
零件名称 零件图号
车型 厂家
检查 确认
信息 操作
工序号
OP10 OP20 OP30 OP40 OP50
工序名称
项目 1.通用
2.模具标识 3.电气线
4.夹紧装置 5. 吊耳
序号
检测项目
1 模具上是否有定位销、导正销?
2 有没有限位块?安装状态如何?
3 有无气管接口?
4 模具导套设置排气口了吗?
5 导套是否有停止装置?
6 模具是否设置防呆装置?
7 铸字、铭牌正确刻印了吗?
8 模具的正面标识?
9 是否标识了钢材的材质?
41 衬套的周围有充分保证强度的壁厚吗?
10.切边冲孔模 42 切刀是否取了剪切角度?
43 刃口的状态好吗?
44 堆焊后的刃口有没有横裂口竖裂口堆焊部有否针孔?
11. 翻边整形模
45 模具有无到底标识? 46 翻边、整形后模腔表面是否有凹痕?
47 斜契块彻底返回情况如何?
12. 斜契块
48 飞转斜契的强制返回如何?
31 模具是否有排气管,空气流通状态如何?
32 模具有无到底标识?
33 模具是否有顶料装置?
34 压边圈是否有拉紧螺栓?
9. 拉延模
35 加强筋,压边圈,凹凸的成形部表面状态如何?
36 与产品接触的表面状态如何?
37 圆角半径处的光顺情况?
38 平衡块正确地安装了吗?
39 平衡块下是否设置了竖筋?
华泰汽车模具验收标准

2 回程键和回程扒钩起始部位的圆角及安装
斜 3 斜楔滑动面研合率 楔 4 斜楔弹簧的状态 机 5 滑块、压板的间隙 构 6 滑块、导轨、压板 部 7 斜楔与上下模压料器 分 8 斜楔应有强制返回
9 斜楔运动功能
检查 静动
※ 应退磁处理
操作者 检查要领
※ 保持等高 钢块接缝方向应垂直于修边口,翻边口方向,
目视、直角尺
允许垂直于刃口的微裂纹应控制在100mm≤3条 (长<2mm,宽<0.02mm,深度≤1mm)
目视
13 刃口硬度
应符合图纸要求,不允许有软点,烧伤,裂纹 ※ 等,淬火面积型面≥3mm深,端面≥5mm宽
目视
第 2 页,共 6 页
华泰汽车模具动静态检查表
制号 用户设备 类别序号
零件名称 工序名称 检查项目
目视 目视 直尺 厚薄规 厚薄规 目视 目视
形
压形模,整形模压力检测是否到位,压印标记,
模 28 制件棱线凸台清晰
※ 符合图纸技术要求
目视
部 29 气缸卸料机构状态
有强度,行程合适,托件平稳,无干涉现象, ※ 托料面与制件接触面无压伤,划痕,尺寸按设
目视
分
计技术要求制作
30 压弯模间隙
※ 间隙合理,弯曲工作表面平整
12 废料滑板和托板盒的强度
※ 应符合要求,料厚≥2mm
13 一级废料滑板和二级滑板
※ 要平整、顺滑,有强度
14 折叠式滑板槽
要用链条固定在下模,不允许固定在上模,并 ※ 且折叠后,不能超出上模平面
15 废料盒
※ 应有固定装置,防止模具起吊过程中脱落
16 废料盒与模具腔壁或托板壁
※ 贴合,并且抽拉灵活
模具动静态验收标准

模具动静态检查表冲压模具动静态检查表(一)项目:零件名称工序号/名称调试设备模具号类序检查项目查检检查要领检查方法验收别号静动 1 2一外观检查1 模具铭牌及顶杆位置示意牌●按图纸规定目视2 模具颜色●按用户要求目视3铸字(“F”标记、模具重量、箭头标记、模具号等)●按用户要求目视4 模体无明显铸造缺陷●按图纸目视5 起吊孔的螺纹规格●按用户要求目视6 压板槽位置、尺寸及数量▲按图纸尺寸直尺7 模具定位键或定位孔▲按图纸尺寸直尺8 空气管接头座及电气安装位置▲按图纸尺寸,不能超出模体目视9 闭合高度检查▲按图纸尺寸卷尺二导向装置1 导向面粗糙度●工作面和导入圆角粗糙度0.8,支承面粗糙度1.6目视2 导柱与导套配合间隙▲无单边接触,无损伤红丹粉3 导板面配合间隙▲大型<0.1,中型<0.08,反侧导板≤0.02厚薄规4 滑动导板接触面接合率▲≥85%,分布均匀红丹粉5 斜楔机构运动导滑面▲间隙<0.03mm厚薄规6各种斜楔机构运动灵活,扒钩间隙合理▲扒钩间隙侧冲0.5~1mm,吊冲<0.03mm目视厚薄规三冲裁︵落料、冲孔、切边︶部1 剪切面刃口粗糙度●端面粗糙度1.6,侧面粗糙度0.8目视2 刃口硬度●按图纸规定硬度计3 刃口镶块接合面间隙●≤0.05mm厚薄规4焊接刃口无气孔、夹渣、横向裂纹●垂直于刃口≤100mm的微裂纹≤3条目视5 镶块与安装座或键与窝座配合●≤0.02mm厚薄规6凸凹模镶块材料牌号及件号标记●打印清晰,无凸起目视7 凹模镶块高度不小于80MM ●应有足够的空间、便于装配冲头直尺8 刃口无咬合、擦黑▲空车下压4-5次目视分9 压料面贴合率、压料面粗糙度▲管理面贴合率>80%,沿周15mm粗糙度<0.8红丹粉10 刃口间隙▲按图纸规定;是制件料厚的<10% 。
目视厚薄规11 10°~30°斜面冲裁时,冲孔及修边凸模处理▲工作刃口提前切入深度按2个料厚处理,冲头是否防转直尺目视12 刃口切入量▲按图纸规定直尺13 退料板与凸模,压料板与凹模的导正间隙▲间隙0.3~0.5mm厚薄规四成形︵拉延、1 镶块接缝间隙●≤0.05mm厚薄规2 工作面粗糙度●主要工作面及R处粗糙度0.8,辅助工作面及R处粗糙度1.6目视3工作表面无缺陷●无划伤、裂纹、波纹、磕碰伤、夹渣、气孔4 工作面硬度●按图纸要求硬度计冲压模具动静态检查表(二)类序检查项目检查检查要领检查方法验收别号静动 1 2五成形、整形) 部分5 C/N基准孔●孔的座标值是否打印清晰(各序通用)目视6 镶块与安装座或键与窝座配合●≤0.02mm厚薄规7凸凹模镶块材料牌号及件号标记●打印清晰,无凸起目视8 上模销孔加丝堵●加丝堵目视9 拉延模到底标记▲高于型面0.3mm,工件表面清晰目视10 卸料板型面与工件接触面▲是否产生压痕目视11 拉延模、成形模排气孔▲排气通畅目视12 压边圈与凹模研合面检查▲管理面95%、准管理面90% 凹模>80%红丹粉13 整形模压力检查▲制件凸台清晰,符合图纸目视14 压弯模的间隙▲间隙符合图纸,弯曲工件表面平整目视15 型面精度(R角、棱线、台阶)▲带料冲压检查轮廓线是否清晰目视直尺16 气垫位置及顶出高度检查▲符合图纸要求直尺六制1 顶出器结构强度●目视2 工件是否有防反措施▲目视件投入与取出3 制件与贴合面配合状态▲贴合率≥70%红丹粉4 顶出器工作平稳▲无干涉目视5 制件投入、取出顺利▲目视6 定位板、定位销与工件配合间隙▲不能过紧,配合间隙0.4mm 目视七废料1 废料长度和数量●按设计要求目视2废料溜料板强度及粗糙度和尺寸●手感直尺3 折叠式废料槽要求●折叠后不能超出上模平面目视4 冲孔检查▲废料能否落入废料盒或槽内顺利排出,积存数量<4片目视5 周围废料,切边废料排出▲排出顺利,无阻碍目视八安全1 铸入吊柄,螺栓紧固式吊柄●坚固,无松动、破损、毛刺目视2 安全防护板、护罩●目视3 防止弹簧弹出、倒伏装置●无松动目视4 模具上下模座连接板●符合图纸目视5 非工作面倒角●按图纸要求目视6 镶块加起吊孔●一般≥15kg,具体按用户要求目视7侧销、安全销及退料螺钉、安全螺钉▲符合图纸,灵活可靠目视九其它1 模具各部分清洁,无锈蚀●目视2 配件齐全●符合图纸目视验收标记:合格√不合格×无此项目/ 验收1:表示第一次验收2:表示第二次验收第一次验收人员:验收日期:第二次验收人员:验收日期:冲压件验收单产品号:产品名称:检查项目检查方式是否合格备注1 裂纹目视2 缩颈目视、测量3 坑包目视、手感4 麻点(群)目视、手感5 毛刺目视、测量6 拉毛目视、手感、测量7 压痕目视、测量8 叠料目视、测量9 波浪目视、手感10 起皱目视11 棱线目视手感12 R角目视手感13 带料塌边目视测量14 其它检查人员:模具品质鍳定表编号:产品型号产品名称零件图号零件名称工装编号工装名称使用单位使用设备工序号工序名称检验问题记录修改后状况结论冲压件制造公司编制审核批准年月日。
模具静检记录表

间
料厚间隙
18
隙
拼缝
19
挡墙零间隙
20
凹模口、棱线
21
成形圆角
22
硬
刃口
23
冲头
24
导柱、导套
25
度
定位件
26
卸料板
27
固定板
序号
检验项目
检验内容
自检结果
专检结果
结论
整改后检验
28
研合率
凸、凹模
29
退、圧件器
30
废料
刃口高度
31
排出
漏料孔
32
废料盒
33
排气孔
34
闭合高度
35
限位
36
侧销
37
顶杆孔
模具静检记录表
模具名称
装配钳工
检验员
模具图号
完成日期检验日期序号检验项H检验内容
自检结果
专检结果
结论
整改后检验
1
光顺,棱线清晰
2
工
成形圆角
3
作
刃「1
4
型
砂眼、裂纹等
5
面
磕碰、划伤现象
6
表面粗糙度
7
间隙
8
导
表面粗糙度
9
向
垂直度
10
止退台
11
错位、偏斜、
12
大小
13
定
位置
14
位
高度
15
运行可靠
16
冲裁间隙
检测内容
尺寸精度
左件
右件
检验方法
1
2
3
1
2
14 模具动静检查表

★
123
斜楔必须设置背托或底部镶键,滑动自如,与背托无间隙
重量15kg以上或难于取出的斜楔应有起吊螺纹孔,起重孔统一设置
124
M20、M16;
125
废料滑板的安装位置不得影响螺栓以及废料刀的拆卸与安装
★
126
侧冲必须有观察孔,排废料孔。
D
127
废料必须100%能滑落到模具以外(自动化模具必须100%滑出工作 台)
118
斜楔和驱动导向接触时上、下模导向在50mm以上
D
斜楔
119
机构 斜楔滑动前必须保证斜楔驱动装置先接触接触面的40%,其工作时斜 楔驱动装置之间至少80%充分接触
D
120
斜楔压料芯必须是上模压料板压住后才开始工作
D
121
斜楔滑动体在下模时,必须保证斜楔不得与送件、取件动作干涉
D
122
大型斜楔在上模时,必须考虑其安全性
94
多状态模具的切换工具需要运动自如,操作方便,并有相应操作说 D ★
95
氮明气缸相对应压料芯底部必须设置垫块
96
模具要考虑防反措施,对称零件要考虑定位的防反;
D★
97
模具安全平台尺寸符合要求
D
98
拉延工序的压边圈安全限位的A≥10mm,模座上的限位平台必须等 D
安高全限位螺钉分布合理,过孔支撑不小于30mm,深度为限位螺钉行
★
40
侧冲孔时,冲头需采用带顶针的结构,同时,有废料防堵塞装置
所有拼块,镶块都有销钉,且有防反,防错设计,销钉吃入其长度
41
的1/2,销钉的松紧程度通过拔销器来测定
易折断的凸模或使用球锁止凸模时,冲孔凸模周围的压料装置采用
- 1、下载文档前请自行甄别文档内容的完整性,平台不提供额外的编辑、内容补充、找答案等附加服务。
- 2、"仅部分预览"的文档,不可在线预览部分如存在完整性等问题,可反馈申请退款(可完整预览的文档不适用该条件!)。
- 3、如文档侵犯您的权益,请联系客服反馈,我们会尽快为您处理(人工客服工作时间:9:00-18:30)。
零件图号工序号上模总重零件名称闭合高度主: 顶:动
12○
红丹粉目视目视○
操作演示○
红丹粉○
目视○
目视卡尺检测目视○
目视○
目视○
目视○
目视○
目视○
目视细铁丝检查是否通透目视/手感硬度计○
红丹粉○
A4纸/塞尺扳手/拔销器○
红丹粉目视/手感无松动目视○
目视○
目视○
手感○
目视○
目视目视○
目视/手动○
目视目视、量尺S :检查合格
G:检查不合格
∕:所检查的模具无此项制件简图:编写(供应商工程师)
审核(供应商品质经理)
操作性压料板、型面、压边圈研合率○
制件滑块运动斜楔机构与其它机构协调性弹簧是否有导正销;弹簧窝座要锪平,深浅一致○
限位柱/平衡块等高检查板件与凸模贴合情况○
滑块强制复位○
斜楔、滑块滑合面接触率排气孔位置及数量○
导套要有止转、防拉托措施弹簧与窝座间隙是否有破裂、暗裂/缩颈导板导向面接触率红丹率≥90%导柱要有防拔措施○
安装锁紧螺丝模具导向弹性元件及斜楔机构成形型面零件手感平顺符合图纸要求符合图纸要求安装压板、丝堵等锁紧装置零件无暗裂,手感平顺零件板材表面光滑清晰可见,标记处不会凸出是否有压伤、拉毛拉伸/整形到底标记、零件号平稳、无窜动、无干涉返楔拉块强度刚性好、滑块能强制复位、无蛇形摆动直径大于1mm 动作协调、无干涉要求着色面3/4以上符合图纸要求,加工平整,弹簧放入后不会偏斜检查结果静 天 益 模 具 动 静 态 检 查 表
模具图号模具重量模具尺寸(长*宽*高)实际压力(吨)检查日期工序名称制件编号
类别检查内容检查方式检查方法检收标准直径为外板工作区域4mm,其他6mm,有防尘管贴合率≧85%是否有凹凸、皱、叠料现象型面是否有变形翻孔、边高度均匀一致工作部分、凸R角硬度符合要求着色率≧90%,略大于一个料厚,零件不能有皱焊接表面光顺度○
焊接处不得有气孔塌角不平沙眼,修整后外观质量良好○
硬度不小于HRC50拉伸模到底块间隙合理0.02-0.05mm 镶块螺钉、销钉○
螺钉锁附直径两倍,销钉循序渐进,松紧OK 间隙小于1MM 定位销垂直部位长度○
超过板料1.5倍料厚,上部做成锥度模具工作前压边圈(压料板)先压住板料查看成型零件走料翻边先后次序正确,不会带来零件缺陷查看零件符合型面板件是否需要防反放件确认定位要有可调整量最少10MM 板件是否需加抠手槽或顶出器板件可顺利取出说明:其中检查“1”由供应商进行自检,检查“2”由敏实SQE检查操作方便,制件的投入与取出顺利无干涉移动部件(压料体等)是否有安全及限位装置○一般4个工作、2个安全装置,高度相差5-10mm
镶块标记 (对照记号)○
打印出材料牌号,硬度,匹配记号,打印清晰无凸起卸、顶料装置顶料平稳、无晃动、无阻滞卸、顶料装置工作时上下升降动作合理、顺畅生产过程中投取料操作
批准(敏实SQE)。