接插件镀金层常见质量问题分析
耳机插座电镀不良原因分析及对策(品质异常改善报告)

耳机插座电镀不良原因分析及对策(品质异常改善报告)耳机插座电镀不良对策镀层质量不良的发生半为电镀条件.电镀设备或电镀药水异常.及人为疏失所造成.通常在现发生不良时比较容易找出原因予以克服.但电镀后经过一段时间才发不良就比较棘手.然而日后与环境中之酸气.氧气,水分等接触,加速氧化腐蚀作用也是必需注意.以下将对电镀不良之发生原因以及改善对策加以探讨说明:一. 表面粗糙:指不平整,不光亮之表面,通常成粗白状.可能发生的原因:1. 素材表面严重粗糙,电镀层无法复盖平整.2. 传动轮表面粗糙,且压合过紧,以致于压伤.3. 电流密度稍微偏高,部分表面不亮粗糙(尚未烧焦)4. 药温高低,一般镀镍才会发生.5. PH值过高或过低,一般镀镍或镀金(过低不会)皆会发生.改善对策:1. 若为素材严重粗糙,立即停产并通知客户.2. 若传动轮粗糙,可换备品使用并检查压合紧度.3. 计算电流密度是否操作过高,若是应降低电流.4. 待温度回升再开机,或降低电流,并立即检查温控系统.5. 立即调整PH至标准范围.6. 查核前处理药剂,稀释药剂或更药剂.二..沾附异物:指端子表面附着之污物.可能发生的原因:1. 水洗不干净或水质不良.2. 沾到放料系统之机械油污.3. 素材带有类似胶状物,于前处理流程无法去除.4. 收料时落地沾到泥污物.5. 锡铅活晶物沾附.改善对策:1. 清洗水槽并更换新水.2. 将有油污处做以遮敝3. 领先以溶剂浸泡处理.4. 避免落地,若已沾附泥土可用吹气清洁,数量很多时,建议重新清洗一次.5. 立即去除结晶物.三.密着不良:指镀层有剥落,起皮,起泡等现象.可能发生的原因:1. 前处理不良,如剥镍.2. 阴极接触不良放电,如剥镍,镍剥镍,镍剥金,镍剥锡铅.3. 镀液受严重污染.4. 产速太慢,底层再次氧化,如镍层在金槽氧化(或金还原).剥锡铅.5. 水洗不干净.6. 素材氧化严重,如氧化斑,热处理后氧化膜.7. 停机化学置换反应造成.8. 操作电压太高,阴极导电头及镀件发热,造成镀层氧化.9. 底层电镀不良(如烧焦),造成下一层剥落.10. 严重烧焦所形成剥落.改善对策:1. 加强前处理.2. 检查阴极是否接触不良适时调整.3. 更换药水.4. 电镀前须再次活化.5. 更换新水,必要时清洗水槽.6. 必须先做除锈及去氧化膜处理,一般使用化学抛光或电解抛光.7. 避免停机或剪除不良品8. 降低操作电压或检查导线接触状况.9. 改善底层电镀质量.10. 参考NO12处理对策.四. 露铜:可清楚看见铜色或黄黑色于低电流处可能发生的原因:1.前处理不良,油脂,氧化物,异物尚未除去,镀层无法析出.1. 操作电流密度太低,导致低电流区镀层无法析出.2. 镍光泽剂过量,导致低电流区镀层无法析出.3. 严重刮伤导致露铜5.未镀到.改善对策:1.加强前处理或降低产速.1. 重新计算电镀条件.2. 处理药水,去除过多光泽剂或更新.3. 检查电镀流程.5.调整电镀位置.五. 刮伤:指水平线条状,一般在锡铅镀层经较容易发生可能发生的原因:1. 素材本身在冲床时,即造成刮伤.2. 被电镀设备中之金属治具刮伤,如阴极头,烤箱定位器,导轮等.3. 被电镀结晶物刮伤.改善对策:1. 停止生产,待与客户联系.2. 检查电镀流程,适时调整设备及治具.3. 停止生产,立即去除晶物更多资讯请登录:()。
有关电镀中所产生品质不良之原因分析

有关电镀中所产生品质不良之原因分析镀层发黄镀层脱落镀层龟裂主要讲镀锡,镀镍镀层发黄1.镀层中,金属之间结合会有空隙,当然这个用肉眼很难看得见,空隙之间会残留有镀槽中的药水和添加剂,而药水大多分为酸性和碱性,所电镀产品暴露在空气中,会随着气温的变化产生一些物理性质,热胀冷缩。
致使其内部残留药水和添加剂外吐,而所电镀附着上的锡层,极易被这些物质所腐蚀。
造成表面氧化,产生镀层发黄。
2.后处理不充分,电镀过程中,附着在产品表面上的药水,必须经过水洗之后,清除表面大部分药水,再以弱碱对其表面所残留少量药水进行中和处理,以确保其表面清洁,这样对以后的存贮有很大的帮助。
在中和的过程中,会对所电镀的锡层进行封孔处理,防止过多的药水进入电镀层中。
所以说,水洗越充分对电镀层越好。
采用超声波进行水洗其效果会更好。
3.产品的烘干,水也是一种氧化剂。
虽然反应缓慢,但是长时间的腐蚀也是会造成镀层发黄。
所以在后处理的过程中,要将水吹干,并在烘干的时候注意温度的控制。
4.导电不良,在电镀过程中,对导电的要求很严格,不可以产生间断性的导电效果,这样会给产品的表面造成不规则的电镀黄斑,导电不良也可以造成整个表面发黄,发黑的一种现象。
这种不良的情况可以从现场上看出来,只要针对其的导电进行这方面的改善便可以得到改善。
5.四价锡的附着,在电镀的过程中,槽中的药水会电解,产品表面产生高温,二价锡离子会部分被氧化成四价锡离子,四价锡离子不溶于水,会使电镀浴混浊,电镀产品在电镀的过程中,如果水洗不充分,其会沾染在产品上面,形成一种泥状的固态现象。
造成产品外观显黄色。
6.添加剂过量,添加剂在药水中含量偏高,这种情况在电镀的过程中不易看出来,它大大缩短了电镀产品的保质期。
添加剂都是一些有机物质,有机物质的化学性质极为不稳定。
7.镀浴中有锌杂质污染,这种可能性不会很大,有可能的话是某些素材上是锌的合金。
这个只要在素材的表面上打铜底和镍底便可以解决。
连接器镀金层结合力差的可能原因

连接器镀金层结合力差的可能原因
2016-04-12 12:57来源:内江洛伯尔材料科技有限公司作者:研发部
镀金插头在镀后检验接插件的镀层结合力时,有时会遇到部份插针的针端前部在折弯时或针孔件的焊线孔在压扁时镀层有起皮现象,有时在高温检测试验发现金层有极细小的鼓泡现象发生。
具体归纳可能有如下几种原因:
1、镀前处理不彻底
对于小型针孔件来说,如果在机加工序完毕后不能立即采用三氯乙烯超声波除油清洗,那么接下来的常规镀前处理很难将孔内干涸的油污除净,这样孔内的镀层结合力就会大大降低.
2、基体镀前活化不完全
在接插件基体材料中大量使用各类铜合金,这些铜合金中的铁铅锡铍等微量金属在一般的活化液中很难使其活化,如果不采用对应的酸将其活化,在进行电镀时,这些金属的氧化物跟镀层很难结合,于是就造成了镀层高温起泡的现象.
3、镀液浓度偏低
在使用氨磺酸镍镀液镀镍时,当镍含量低于工艺范围时,小型针孔件的孔内镀层质量要受到影响.如果是预镀液的金含量过低,那么在镀金时孔内就有可能镀不上金,当镀件进入加厚金镀液时,孔内五金层的镀件孔内的镍层已钝化其结果是孔内的金层结合力自然就差.
4、细长状插针电镀时未降低电流密度
在镀细长形状插针时,如果按通常使用遥电流密度电镀时,针尖部位的镀层会比针杆上厚许多,在放大镜下观察针尖有时会旦火柴头形状.其头颈部的镀层即插针前端顶部靠后一点部位的金镀层检验结合力就不合格.这种现象在振动镀金时易出现.
5、振动镀金振频调整不正确
采用振动电镀镀接插件时,如果在镀镍时振动频率调整不正确镀件跳动太快,易开成双层镍对镀层结合力影响甚大.。
镀层常见故障的分析和纠正

常见故障的分析和纠正(酸锌)常见故障的分析和纠正(1)镀层起泡,结合力不好。
镀前处理不良;镀液中添加剂过多;硼酸含量过低同时阴极电流密度过大等会使镀层起泡,造成结合力不好。
镀液中添加剂含量过多,则阴极表面上吸附了较多的有机添加剂,导致阴极表面憎水,同时它还会夹附于镀层内,造成镀层与基体金属间晶格不连续而结合不牢;镀液中硼酸含量低,阴极膜中pH容易升高,同时电流密度过大,阴极膜中pH更高,容易造成金属的氢氧化物或碱式盐夹附于镀层内,影响镀层晶格的正常排列,从而造成镀层结合不牢。
硼酸含量低,电流密度大造成的结合力不好较多地出现在零件的尖端和边缘,出现这类现象时,一方面检查电流,另一方面分析硼酸含量,然后按检查和分析结果进行纠正。
在排除了硼酸含量和电流密度的影响后,再加强镀前处理或用良好的镀前处理与原来的操作进行对比,检查镀前处理是否有问题。
另外用赫尔槽试验检查添加剂的含量。
当发现添加剂含量过高,可用电解或活性炭处理降低其含量。
(2)镀层粗糙。
镀液中锌含量过高;添加剂含量偏低;温度过高或镀液中有固体微粒等都会使镀层粗糙。
镀液中锌含量和温度升高,添加剂含量降低,都是降低阴极极化,导致镀层粗糙。
假使在电镀过程中,镀液温度有升高的趋势,那么最好装置冷却设备。
假使温度略微偏高而没有冷却设备,也可加入适量的苯甲酸钠,以改善镀层的结晶组织。
添加剂含量的多少,可用前述的赫尔槽试验确定,同时还可以从一些现象进行观察,因为添加剂含量偏低时,不但镀层粗糙,同时镀层的光泽差,电流密度的范围比较狭小,低电流密度处镀层色暗,当同时出现这些现象时,再在赫尔槽试验的溶液中,加入适量的添加剂后进行试验,观察阴极样板上的镀层状况,若有好转,可向镀液中补充添加剂。
镀液中的锌含量,可按分析进行调整。
发现锌含量过高时,一方面要稀释镀液,将其浓度调节在工艺范围内,另一方面要减少阳极面积,防止锌含量继续升高。
确定镀液中是否有固体微粒,一种方法是在搅拌镀液的情况下,用500mL(或1000mL)的量杯取一杯镀液,将它放置在强烈的光线下观察;另一方法是用定量滤纸过滤少量镀液,然后观察滤纸上同体微粒的多少,从而估计镀液中固体微粒的含量,若镀液中固体杂质较多,就应过滤镀液,除去这类杂质。
连接器插针电镀的质量问题

连接器插针电镀的质量问题1前言在插针电镀中,由于接触对有着较高的电气性能要求,镀金工艺在插针电镀中占有明显重要的地位.目前除部分的带料插针采用选择性电镀金工艺外,其余大量的针孔散件的孔内镀金仍采用滚镀和振动镀来进行.近几年,插针体积发展到越来越小型化,其针孔散件的孔内镀金质量问题日趋突出,用户对金层的质量要求也越来越高,一些用户对金层的外观质量甚至达到了十分挑剔的程度.为了保证插针镀金层质量结合力这几类常见质量问题总是提高插针镀金质量的关键.下面就这些质量问题产生的原因进行逐一分板提供大家探讨。
2镀金层质量问题的产生原因2.1金层颜色不正常插针镀金层的颜色与正常的金层颜色不一致,或同一配套产品中不同零件的金层颜色出现差异,出现这种问题的原因是:2.1.1镀金原材料杂质影响当加入镀液的化学材料带进的杂质超过镀金液的忍受程度后会很快影响金层的颜色和亮度.如果是有机杂质影响会出现金层发暗和发花的现象,郝尔槽试片检查发暗和发花位置不固定.若是金属杂质干扰则会造成电流密度有效范围变窄,郝尔槽试验显示是试片电流密度低端不亮或是高端镀不亮低端镀不上.反映到镀件上是镀层发红甚至发黑,其孔内的颜色变化较明显。
2.1.1镀金电流密度过大由于镀槽零件的总面积计算错误其数值大于实际表面积,使镀金电流量过大,或是采用振动电镀金时其振幅过小,这样槽中全部或部分镀件金镀层结晶粗糙,目视金层发红。
2.1.3镀金液老化镀金液使用时间太长则镀液中杂质过度积累必然会造成金层颜色不正常。
2.1.4硬金镀层中合金含量发生变化为了提高插针的硬度和耐磨程度,插针镀金一般采用镀硬金工艺.其中使用较多的是金钴合金和金镍合金.当镀液中的钴和镍的含量发生变化时会引起金镀层颜色改变.若是镀液中钴含量过高金层颜色会偏红;若是镀液中这镍含量过高金属颜色会变浅;若是镀液中这种变化过大而同一配套产品的不同零件又不在同一槽镀金时,这样就会出现提供给用户的同一批次产品金层颜色不相同的现象。
电镀件常见不良原因分析
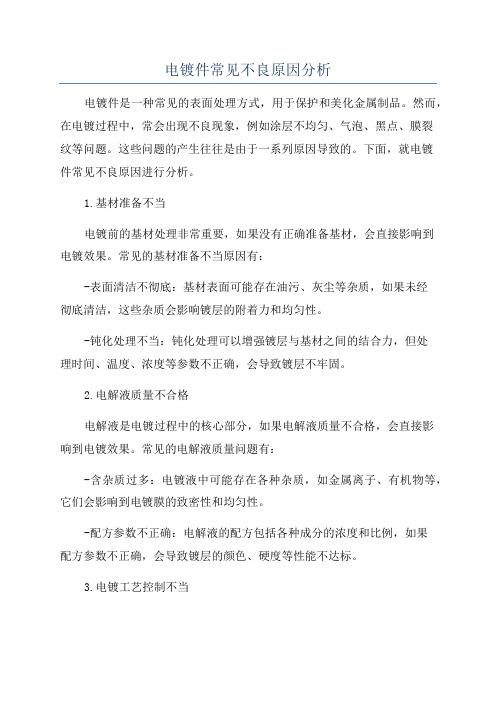
电镀件常见不良原因分析电镀件是一种常见的表面处理方式,用于保护和美化金属制品。
然而,在电镀过程中,常会出现不良现象,例如涂层不均匀、气泡、黑点、膜裂纹等问题。
这些问题的产生往往是由于一系列原因导致的。
下面,就电镀件常见不良原因进行分析。
1.基材准备不当电镀前的基材处理非常重要,如果没有正确准备基材,会直接影响到电镀效果。
常见的基材准备不当原因有:-表面清洁不彻底:基材表面可能存在油污、灰尘等杂质,如果未经彻底清洁,这些杂质会影响镀层的附着力和均匀性。
-钝化处理不当:钝化处理可以增强镀层与基材之间的结合力,但处理时间、温度、浓度等参数不正确,会导致镀层不牢固。
2.电解液质量不合格电解液是电镀过程中的核心部分,如果电解液质量不合格,会直接影响到电镀效果。
常见的电解液质量问题有:-含杂质过多:电镀液中可能存在各种杂质,如金属离子、有机物等,它们会影响到电镀膜的致密性和均匀性。
-配方参数不正确:电解液的配方包括各种成分的浓度和比例,如果配方参数不正确,会导致镀层的颜色、硬度等性能不达标。
3.电镀工艺控制不当电镀工艺过程中的各个环节都需要精确控制,否则会产生不良现象。
常见的电镀工艺控制不当原因有:-电流密度不均匀:电镀过程中,电流密度分布不均匀会导致镀层厚度不均匀,甚至出现孔洞等问题。
-温度控制不准确:电镀过程中的温度控制对于镀层的质量和均匀性非常重要,如果温度控制不准确,会影响到电解液的反应速率和镀层的结构。
4.设备维护不当电镀设备的维护工作也是保证电镀质量的关键。
常见的设备维护不当原因有:-阴极和阳极污染:设备内部的阴极和阳极可能会受到电解液的腐蚀,长期使用后会产生污染物,需要定期清洗和更换。
-设备参数不稳定:设备的电流、温度、电压等参数需保持稳定,如果设备参数不稳定,会导致镀层质量下降。
综上所述,电镀件常见的不良现象往往由基材准备不当、电解液质量不合格、电镀工艺控制不当和设备维护不当等原因导致。
为确保电镀质量,操作人员应遵循正确的工艺流程,提高工作细致性和耐心性,严格控制每个环节的参数和条件,以及定期维护设备,确保设备的正常运行。
连接器端子镀层脱落原因

连接器端子镀层脱落的原因主要有以下几个方面:
1. 生产工艺问题:生产过程中如果温度和时间的控制不准确,可能导致镀层过薄或镀层不均匀,出现脱落现象。
2. 材质问题:连接器端子材料可能含有不利于镀层的杂质,导致镀层与端子表面结合不牢。
3. 腐蚀或电化学作用:如果连接器端子接触其他腐蚀性物质或处于潮湿、腐蚀性环境,可能会对端子表面造成破坏,导致镀层脱落。
4. 冲击或振动:连接器在使用过程中可能会受到冲击或振动,如果端子镀层不耐冲击或振动,可能会脱落。
5. 不当操作:如果操作人员在进行镀层工艺时,操作不当,如用力过大或速度过快,可能导致镀层出现裂纹或脱落。
6. 老化过程:连接器端子在长期使用过程中,可能会因老化而变形,导致镀层与端子表面脱离。
为了解决连接器端子镀层脱落的问题,可以采取以下措施:
1. 对生产工艺进行严格控制,确保温度和时间都控制在最佳范围内,以保证镀层的厚度和均匀性。
2. 选用优质的连接器端子材料,以减少镀层与端子表面结合不牢的风险。
3. 避免连接器端子接触腐蚀性物质或处于潮湿、腐蚀性环境,以减少镀层被破坏的可能性。
4. 对连接器进行定期检查和维护,发现镀层脱落及时修补或更换新的连接器。
5. 对操作人员进行培训,使其掌握正确的镀层工艺操作方法。
6. 对于老化导致的镀层脱落,可以在维修时对端子进行重新镀层,以确保其耐腐蚀性和使用寿命。
总之,连接器端子镀层脱落的原因可能是生产工艺、材质、腐蚀、冲击、振动、不当操作和老化等因素导致的。
通过采取相应的措施,可以有效地解决这个问题,提高连接器的可靠性和使用寿命。
接插件镀金、镀银层变色原因及防变色措施

接插件镀金、镀银层变色原因及防变色措施摘要:分别探讨了接插件镀金和镀银层变色的原因。
镀金层的变色原因如下:基体质量不符合要求,产品的设计及电镀工艺存在缺陷(包括产品前处理工艺、金阻挡层镀液体系的选择、镀液的维护、电镀工艺参数的选择和电镀方式等的不妥当),镀后处理不力,产品使用环境的差异等镀银层变色的原因如下:基体形状复杂且其表面粗糙度高,电镀工艺不完善,包装方式不当,产品使用环境差异等。
提出了镀层的防变色措施:提高基体质量,减少设计缺陷,改进电镀工艺,加强镀后工序管理,根据产品的使用环境对其制定不同的质量要求等关键词:接插件;镀金;镀银;变色;措施;1 前言在接插件的制造工艺中,为了保证产品的导电性能和可靠性,大部分产品的接触件以及部分产品的壳体均采用了镀金或镀银进行表面处理。
由于在产品的加工和使用过程中受到各种因素的影响,部分产品的镀层表面会在较短时间内出现变色现象。
而一旦镀层表面开始变色,产品的电气性能也会随之下降。
为了避免这种现象发生,针对金、银镀层的变色机理,人们采取了各种措施尽力延缓镀层在规定的时间内出现的颜色变化。
以下为目前在接插件制造行业中发生镀层变色原因的分析以及常用的解决镀金、镀银层变色问题的一些基本方法。
2 金镀层的变色原因金是一种比较稳定的金属元素,在大气环境中几乎不与其它物质反应,因此不会受到各种腐蚀气体侵袭而发生化学变化。
接插件金镀层变色的原因主要是受到基体金属(铜及铜合金)通过金层孔隙向镀层表面迁移的影响。
因为金层与基体金属之间存在着电位差,在遇到腐蚀介质时这种电位差会导致基体金属被腐蚀,当腐蚀物富集在金层表面时金层就改变了颜色。
在接插件的制造行业中导致金层很快变色的原因主要还体现在以下几个方面。
2.1 基体质量达不到要求基材杂质含量和基体表面光洁度是两项衡量电接触体基体质量的重要指标。
近几年来,由于市场竞争加剧,加上金属材料涨价因素,使得一些基体制造厂为了降低生产成本,采用一些不合规格的材料,甚至采用回收铜加工制造基体。
镀金镀银件变色原因及对策

接插件镀金、镀银层变色原因及防变色措施镀金层的变色原因如下:基体质量不符合要求,产品的设计及电镀工艺存在缺陷(包括产品前处理工艺、金阻挡层镀液体系的选择、镀液的维护、电镀工艺参数的选择和电镀方式等的不妥当),镀后处理不力,产品使用环境的差异等镀银层变色的原因如下:基体形状复杂且其表面粗糙度高,电镀工艺不完善,包装方式不当,产品使用环境差异等。
1 前言在接插件的制造工艺中,为了保证产品的导电性能和可靠性,大部分产品的接触件以及部分产品的壳体均采用了镀金或镀银进行表面处理。
由于在产品的加工和使用过程中受到各种因素的影响,部分产品的镀层表面会在较短时间内出现变色现象。
而一旦镀层表面开始变色,产品的电气性能也会随之下降。
为了避免这种现象发生,针对金、银镀层的变色机理,人们采取了各种措施尽力延缓镀层在规定的时间内出现的颜色变化。
以下为目前在接插件制造行业中发生镀层变色原因的分析以及常用的解决镀金、镀银层变色问题的一些基本方法。
2 金镀层的变色原因金是一种比较稳定的金属元素,在大气环境中几乎不与其它物质反应,因此不会受到各种腐蚀气体侵袭而发生化学变化。
接插件金镀层变色的原因主要是受到基体金属(铜及铜合金)通过金层孔隙向镀层表面迁移的影响。
因为金层与基体金属之间存在着电位差,在遇到腐蚀介质时这种电位差会导致基体金属被腐蚀,当腐蚀物富集在金层表面时金层就改变了颜色。
在接插件的制造行业中导致金层很快变色的原因主要还体现在以下几个方面。
2.1 基体质量达不到要求基材杂质含量和基体表面光洁度是两项衡量电接触体基体质量的重要指标。
近几年来,由于市场竞争加剧,加上金属材料涨价因素,使得一些基体制造厂为了降低生产成本,采用一些不合规格的材料,甚至采用回收铜加工制造基体。
由于杂质超标,基材脆性增大,在机加工时部分镀件的基体会产生不易察觉的微裂纹(有时也会因电镀时的渗氢作用产生这种微裂纹)。
我厂2000年初在电镀某种高频电连接器外壳时,由于外壳的基体材料是采用回收铜制作,故经振动电镀金后,盛镀件的振筛底部会留下一层铜粉,其中部分镀件的4只插脚仅剩下3只,镀件的凹下部位的金层几天就变成了褐色。
镀金层常见故障和纠正方法

镀金层常有故障和纠正方法故障可能原由纠正方法低电流区发雾①温度太低① 调整温度到正常值②增补剂不足② 增加增补剂③有机污染③ 活性炭办理④ PH太高④ 用酸性调整盐调低PH中电流区发雾,高电流区呈①温度太高① 降低操作温度暗褐色②阴极电流密度太高② 降低电流密度③ PH太高③ 用酸性调整盐调低PH④增补剂不够④ 增加增补剂⑤搅拌不够⑤ 增强搅拌⑥有机污染⑥ 活性炭过滤高电流区烧焦①金含量不足① 增补金盐② PH太高② 用酸性调整盐调低PH③电流密度太高③ 调低电流密度④镀液比重太低④ 用导电盐提升比重⑤搅拌不够⑤ 增强搅拌镀层颜色不平均①金含量不足① 增补金盐②比重太低② 用导电盐调高比重③搅拌不够③ 增强搅拌④镀液被 Ni , Cu等污染④除去金属离子污染 , 必需时更换溶液板面金变色(特别是在潮热①镀金层冲刷不完全① 增强镀后冲刷季节)②镀镍层厚度不够② 镍层厚度不小于微米③镀金液被金属或有机物污染③ 增强金镀液净化④镀镍层纯度不够④ 增强除去镍镀液的杂质⑤镀金板存放在有腐化性的环⑤ 镀金层应远离腐化氛围环境保存, 其变色境中层可浸 5-15%HSO除去24镀金板可焊性不好①低应力镍镀层太薄①低应力镍层厚度不小于微米②金层纯度不够②增强镀金液监控 , 减少杂质污染③表面被污染,如手印③增强冲刷和板面洁净④包装不合适④需较长时间存放的印制板 , 应采纳真空包装镀层结合力不好①铜镍间结合力不好①注意镀镍前铜表面洁净和活化②镍金层结合力不好②注意镀金前的镍表面活化③镀前冲刷办理不良③增强镀前办理④镀镍层应力大④净化镀镍液,通小电流或炭办理LY-955 中性镀金工艺一、工艺特色:LY-955 中性镀金,其镀层为 24K 纯金色,色彩金黄,颜色娇艳平均,镀液稳固,操作简单,因为含金量低,可作为面层,也可作为厚金的预镀层,大大降低了镀金的成本。
LY-955 中性镀金合用于在镍,铜及铜合金上直接镀金。
广泛用于金饰,工艺品及制板整板镀金。
电镀金问题分析与解决方案

电镀金问题分析与解决方案一、前言市场上常见电镀金的种类有:酸性/中性薄金(俗名水金、软金、纯金)及酸性/中性厚金,而厚金又包含了:镀薄金、镀厚金、镀耐磨金。
电镀金虽工艺成熟,但仍有部分厂家因所选择的电镀金产品系列不当,导致难达到品质要求,常出现品质上的一些问题(如,厚度不够、不耐磨、不抗盐雾试验、不抗硝酸蒸汽试验、分布不均、氧化变色、甩金、针孔、发黑及色差等)。
一、镀镍层去镀金的关系及工艺选择的常见问题。
1、电镀金前选择硫酸镍或氨基磺酸镍镀液也至关重要,电镀金表面要求镀镍层为哑色、镀层外观要求高或镀层要求内应力低等均可采用氨基磺酸镍哑镍光剂最好;电镀金面要求盐雾试验、镀层内应力低及小孔可焊性要佳等均可采用氨基磺酸镍半光亮镍光剂最好;电镀金面要求耐磨度高的板或直接单双面大铜箔面上通过前处理直接镀镍,没有特别要求的单双面板可在短时间内获得镍层均匀光亮等均可采用硫酸镍高速镍光剂最好(光亮程度可以通过控制添加量来达到品质要求,此单双面板通常镀薄金或厚金工艺)。
有关电镀镍方面的内容另外详细介绍!2. 采用电镀金产品不当导致的问题。
①选择酸性中性薄金药水来镀厚金产品,镀板时间越长越容易产生金面发红、发雾、发黑、氧化及色差等问题;②选择中性厚金药水来镀厚金产品,因中性厚金药水电流密度操作范围窄,电流稍大就出现金镀层粗糙、疏松、发红、发黑、氧化甚至甩金等问题。
采用中性厚金适宜电流密度越小越对品质有利,但上金速率慢,前处理后铜上镀金结合力基本正常,但镍上镀金就会常出现结合力差等问题。
二、电镀金分类薄金:版面镀金层是24K纯金,它有良好的导电性和可焊性,镀层均匀细致、纯度高且内应力低,此产品适应于打线(Bonding)。
镀层厚度0.01~0.05μm。
厚金:版面合金元素含量≤0.2%,用于高稳定、高可靠、低接触电阻、耐磨、耐腐蚀及可焊性佳等特殊用途。
镀薄厚金(0.1~0.5μm);镀厚金(0.5~5μm)。
电镀金分为薄金和厚金,薄金要求没有厚金品质要求高,薄金基本印制板厂家都能做到并达到要求,但厚金呢?根据产品性能要求,针对高频板往往市场上没有多少厂家能做好。
接插件镀金、镀银层变色原因及防变色措施

【经验交流】!!收稿日期:"##$%#&%"’!!修回日期:"##$%#(%"#!!作者简介:沈涪()*$’%),男,高级工程师,主要从事电镀工艺研究工作。
作者联系方式:(+,-./)01-2345236-578.2-9:5,。
接插件镀金、镀银层变色原因及防变色措施沈涪(四川绵阳华丰企业集团公司,绵阳!&")###)摘!要:分别探讨了接插件镀金和镀银层变色的原因。
镀金层的变色原因如下:基体质量不符合要求,产品的设计及电镀工艺存在缺陷(包括产品前处理工艺、金阻挡层镀液体系的选择、镀液的维护、电镀工艺参数的选择和电镀方式等的不妥当),镀后处理不力,产品使用环境的差异等。
镀银层变色的原因如下:基体形状复杂且其表面粗糙度高,电镀工艺不完善,包装方式不当,产品使用环境差异等。
提出了镀层的防变色措施:提高基体质量,减少设计缺陷,改进电镀工艺,加强镀后工序管理,根据产品的使用环境对其制定不同的质量要求等。
关键词:接插件;镀金;镀银;变色;措施;中图分类号:;<)$’9)&;;<)$’9)=!!!!!文献标识码:>文章编号:)##?%""(@("##$))#%##)(%#’!"#$%&’%$()"*&+&"$,-"#$%&’%$(#+&%&-"$-.+"&*#+&/0(/1,"$,&%12+#341"-+,)/$$+)-/#&A A BC+D E156&-#")-:;0F :-18F85G H-I2.80.2335/6-268./JFIKL/-HF6:522F:H5I8MFIF 8H16.F6IF8LF:H.JF/49;0F :-18F85G H-I2.8K 0.2335/6F/F:HI56FL58.H MFIF -8G5//5M8:H0F 81N8HI-HF O1-/.K H4.825H 1L H5H0F 8H-26-I69PFGF:H8FQ.8H .26F8.325G LI56K 1:H -26F/F:HI5L/-H.23LI5:F88(.2:/16.23LI561:H LIFHIF-HK ,F2H ,H0F 5LH.525G N-H0848HF,G5I 35/6N-II.FI ,N-H0,-.2K HF2-2:F ,5LH.525G F/F:HI5L/-H.23LI5:F88L-I-,FHFI -26M-485G F/F:HI5L/-H.23,FH:9)9R58HKHIF-H,F2H8MFIF .2-6FO1-HF -26 6.GGFIF2:F 5G LI561:H -LL/.:-H.52F2J.I52,F2H8,FH:9S-18F85G 8./JFI F/F:HI56FL58.H H-I2.80.23MFIF -8G5//5M8::5,L/.:-HF680-LF 5G 81N8HI-HF8-260.30I51302F885G 81IK G-:F ,.2:5,L/FHF F/F:HI5L/-H.23LI5:F88,1281.H-N/F M-45G L-:T.23-266.GGFIF2:F 5G LI561:H -LL/.:-H.52F2J.I52,F2H8,FH:9;0F LIFJF2H.JF ,F-81IF8-3-.28H H-I2.80.23.2:/16F .,K LI5JF,F2H 5G 81N8HI-HF O1-/.H4,6F:IF-8.236FGF:H 5G 6F8.32,.,LI5J.23F/F:HI5L/-H.23LI5:F88,8HIF23H0F2.23H0F ,-2-3FK ,F2H 5G L58HKHIF-H,F2H -26.28H.H1H.236.GGFIF2H O1-/.H4IFK O1F8H8-::5I6.23H5H0F LI561:H -LL/.F6.2J-I.518F2J.I52K ,F2H8,FH:97+89/#,&::522F:H5I ;35/6F/F:HI5L/-H.23;8./JFI F/F:HI5KL/-H.23;H-I2.80.23;,F-81IF5*-’/#:&",,#+&&:C1-GF23+2HFILI.8F UI51L S59,V.-2K 4-23&")###,S0.2-;<前言!!在接插件的制造工艺中,为了保证产品的导电性能和可靠性,大部分产品的接触件以及部分产品的壳体均采用了镀金或镀银进行表面处理。
接插件镀金镀层常见质量问题分析

I电流、h板厚、k电导率、d孔径 上式说明电流越小电位差越小,降低电流密度 可使孔内镀层均匀。 我们通过生产实践:在加厚镀铜时我们延长时 间至35分钟,电流密度为1.7A/dm2,使铜层厚度为 12微米左右,图形镀铜把电流密度降至1.3A/din2, 电镀时间延长至90分钟,板厚为1.6毫米、孔径为 0.3毫米的印制电路板,经金相剖析厚度均为25~28 微米之间。
2.镀金层质量问题的产生原因
2 1金层颜色不正常 接插件镀金层的零件的金层颜色出现差 异,出现这种问题的原因是: 2.1 I镀金原材料杂质影响
当加入镀液的化学材料带进的杂质超过镀金液 的忍受程度后会很快影响金层的颜色和亮度。如果
是有机杂质影响会出现金层发暗和发花现象,郝尔 槽试片检查发暗和发花位置不固定。若是金属杂质 干扰则会造成电流密度有效范围变窄,郝尔槽试验 显示是试片电流密度低端镀不亮或是高端镀不亮低 端镀不上。反映到镀件上是镀层发红甚至发黑,其 孔内的颜色变化较明显。 2.1.2镀金电流密度过大
2.会议论文 沈涪 电镀质量问题分析处理案例 2008
对电镀质量问题的分析,首先应从电镀工序查找自身的原因,在排除了电镀所有条件(电镀设备、操作方式、工艺参数)的影响后,要向上工序逐级倒推一直查到镀件使用的基体材料的质量。近些年来,由于市场竞争激烈,而各种原材料又在不断涨价的情况下,镀件的基材加工厂会在降低材料等级和减少生产工序上想办法,实际上现在好多电镀质量问题也 确实跟基材质量有关。对于产品用户提出的电镀质量问题,除了要在电镀上工序查找原因外,还要在电镀的下工序查找原因,例如大家关注的镀金层变色问题就跟镀件的装配、运输、包装有一定的关系。
1)综合评述了国内军用电子设备中电接触元件在质量上存在的一些问题和镍打底镀金工艺的发展与应用,提出了与国外电连接器行业存在的差距,总结了电连接器接触体镀金常见质量问题并对其产生原因和解决办法进行了分析探讨,并论述电连接器接触体镍打底镀金工艺的宗旨和思想。 2)详细论述了镍打底镀金工艺的理论和方法。首先,介绍了镍打底镀金工艺研究的目的和理论依据;其次,对镀镍工艺进行了选择与优化,对镀镍机理、低应力镍机理和镀金阻挡层的选择原则进行了阐述。通过几种不同镀镍溶液中所获得镍镀层的物理性质及镀层孔隙率的对比,得出氨基磺酸盐镀镍是电连接器接触体镀镍的理想镀镍体系,并通过氨基磺酸 盐镀镍层内应力的影响因素分析及试验,对镀镍工艺进行了优化,得到了最佳电解液组成和工艺条件,同时对镀液的配制、维护和控制进行了阐述;最后对镀金机理和常用镀金工艺进行了分析,确定了适合本研究的镀金工艺,同时介绍了镀液的配制及镀液组成对镀液性能的影响。 3)介绍了镍打底镀金工艺流程,并从化学除油、酸洗、活化I、中和、预镀铜、活化II、氨盐镀镍、浸柠檬酸、柠檬酸盐镀金、镀后处理共10个方面对其主要工序进行了详细说明。 4)阐述了镀金层的质量检验与性能测试。从镀金层的质量要求、镀金层的质量检验和性能测试方法及试验结果3个方面进行了详细介绍,并对本章进行了小结。 5)阐述了镀金溶液的维护纯化和故障分析。从镀金溶液的维护和控制、镀金溶液的纯化和镀金溶液的常见故障及排除方法共3个方面进行了详细介绍。 6)最后,对全文进行总结。
连接器行业端子电镀不良8D报告案例样板

连接器行业端子电镀不良8D报告案例样板8D报告案例:连接器行业端子电镀不良1.情况描述:在连接器的生产过程中,发现一批端子的电镀存在不良情况。
问题主要集中在电镀层的厚度不均匀和存在气泡、麻点等缺陷。
该批次端子属于高精度产品,质量要求较高。
2.问题分析:2.1工艺参数分析:通过检查工艺参数记录发现,电镀温度、时间等参数都在正常范围内,且符合工艺规范。
因此,问题并不是由于工艺参数调整不当导致的。
2.2原材料分析:经过对原材料进行抽样分析,未发现原材料存在质量问题。
因此,问题并不是由于原材料问题导致的。
2.3设备状态分析:检查设备运行状态,包括电镀槽、电镀设备、输送带等。
未发现设备故障或异常情况。
因此,问题并不是由于设备问题导致的。
2.4操作人员分析:对操作人员进行培训,强调操作规范,并检查其操作流程。
发现一部分操作人员操作不规范,导致端子的镀层不均匀,存在气泡、麻点等缺陷。
因此,问题主要是由于操作人员操作不规范导致的。
3.问题解决:3.1培训操作人员:针对操作不规范的操作人员进行培训,并制定详细的操作规范,确保每个环节的操作正确执行。
3.2质量控制检查:增加质量控制检查的频率和强度,对端子进行严格的质量检查,保证产品质量符合要求。
3.3镀层监控:对电镀设备进行定期的维护和保养,确保电镀液的浓度和温度等参数稳定,并设置自动报警装置,确保电镀液参数异常时及时发现并处理。
4.效果验证:经过上述措施的实施,端子电镀不良情况得到有效改善。
经过多批次产品的质量检查,端子的电镀层厚度均匀,且无气泡、麻点等缺陷。
5.预防措施:5.1制定操作规范:对操作人员进行详细的培训,制定操作规范,确保每个环节的操作正确执行。
5.2强化质量控制:增加质量控制检查的频率和强度,对产品进行严格的质量检查,及时发现和纠正问题。
5.3定期维护设备:定期对电镀设备进行维护和保养,确保设备的稳定运行,避免设备故障对产品质量造成影响。
以上是连接器行业端子电镀不良的8D报告案例样板,详细阐述了问题的分析过程、解决措施以及效果验证和预防措施。
金手指镀金质量问题及措施

金手指镀金质量问题及措施1前言在接插件电镀中,由于接触对有着较高的电气性能要求,镀金工艺在接插件电镀中占有明显重要的地位.目前除部分的带料接插件采用选择性电镀金工艺外,其余大量的针孔散件的孔内镀金仍采用滚镀和振动镀来进行.近几年,接插件体积发展到越来越小型化,其针孔散件的孔内镀金质量问题日趋突出,用户对金层的质量要求也越来越高,一些用户对金层的外观质量甚至达到了十分挑剔的程度.为了保证接插件镀金层质量结合力这几类常见质量问题总是提高接插件镀金质量的关键.下面就这些质量问题产生的原因进行逐一分板提供大家探讨.2镀金层质量问题的产生原因2.1金层颜色不正常接插件镀金层的颜色与正常的金层颜色不一致,或同一配套产品中不同零件的金层颜色出现差异,出现这种问题的原因是:2.1.1镀金原材料杂质影响当加入镀液的化学材料带进的杂质超过镀金液的忍受程度后会很快影响金层的颜色和亮度.如果是有机杂质影响会出现金层发暗和发花的现象,郝尔槽试片检查发暗和发花位置不固定.若是金属杂质干扰则会造成电流密度有效范围变窄,郝尔槽试验显示是试片电流密度低端不亮或是高端镀不亮低端镀不上.反映到镀件上是镀层发红甚至发黑,其孔内的颜色变化较明显.2.1.1镀金电流密度过大由于镀槽零件的总面积计算错误其数值大于实际表面积,使镀金电流量过大,或是采用振动电镀金时其振幅过小,这样槽中全部或部分镀件金镀层结晶粗糙,目视金层发红.2.1.3镀金液老化镀金液使用时间太长则镀液中杂质过度积累必然会造成金层颜色不正常.2.1.4硬金镀层中合金含量发生变化为了提高接插件的硬度和耐磨程度,接插件镀金一般采用镀硬金工艺.其中使用较多的是金钴合金和金镍合金.当镀液中的钴和镍的含量发生变化时会引起金镀层颜色改变.若是镀液中钴含量过高金层颜色会偏红;若是镀液中这镍含量过高金属颜色会变浅;若是镀液中这种变化过大而同一配套产品的不同零件又不在同一槽镀金时,这样就会出现提供给用户的同一批次产品金层颜色不相同的现象.2.2孔内镀不上金接插件的插针或插孔镀金工序完成后镀件外表面厚度达到或超过规定厚度值时,其焊线孔或插孔的内孔镀层很薄甚至无金层.2.2.1镀金时镀件互相对插为了保证接插件的插孔在插孔在插拔使用时具有一定弹性,在产品设计时大多数种类的插孔都有是在口部设计一道劈槽.在电镀过程中镀件不断翻动部份插孔就在开口处互相插在一起致使对插部位电力线互相屏敝造成孔内电镀困难.2.2.2镀金时镀件首尾相接有些种类的接插件其插针在设计时其针杆的外径尺寸略小于焊线孔的孔径尺寸,在电镀过程中部份插针就会形成首尾相接造成焊线孔内镀不进金.(见图示)以上两种现象在振动镀金时较容易发生.2.2.3盲孔部位浓度较大超过电镀工艺深镀能力由于在插孔的劈槽底部距孔底还有一段距离,这段距离客观上形成了一段盲孔.同样在插针和插孔的焊线孔里也有这样一段盲孔,它是提供导线焊接时的导向作用.当这些孔的孔径较小(往往低于1毫米甚至低于0.5毫米)而盲孔浓度超过孔径时镀液很难流进孔内,流进孔内的镀液又很难流出,所以孔内的金层质量很难保证.2.2.4镀金阳极面积太小当接插件体积较小时相对来说单槽镀件的总表面积就较大,这样在镀小型针孔件时如果单槽镀件较多.原来的阳极面积就显得不够.特别是当铂钛网使用时间过长铂损耗太多时,阳极的有效面积就会减少,这样就会影响镀金的深镀能力,镀件的孔内就会镀不进.2.3镀层结合力差在镀后检验接插件的镀层结合力时,有时会遇到部份插针的针端前部在折弯时或针孔件的焊线孔在压扁时镀层有起皮现象,有时在高温(2001小时)检测试验发现金层有极细小的鼓泡现象发生.2.3.1镀前处理不彻底对于小型针孔件来说,如果在机加工序完毕后不能立即采用三氯乙烯超声波除油清洗,那么接下来的常规镀前处理很难将孔内干涸的油污除净,这样孔内的镀层结合力就会大大降低.2.3.2基体镀前活化不完全在接插件基体材料中大量使用各类铜合金,这些铜合金中的铁铅锡铍等微量金属在一般的活化液中很难使其活化,如果不采用对应的酸将其活化,在进行电镀时,这些金属的氧化物跟镀层很难结合,于是就造成了镀层高温起泡的现象.2.2.3镀液浓度偏低在使用氨磺酸镍镀液镀镍时,当镍含量低于工艺范围时,小型针孔件的孔内镀层质量要受到影响.如果是预镀液的金含量过低,那么在镀金时孔内就有可能镀不上金,当镀件进入加厚金镀液时,孔内五金层的镀件孔内的镍层已钝化其结果是孔内的金层结合力自然就差.2.3.4细长状插针电镀时未降低电流密度在镀细长形状插针时,如果按通常使用遥电流密度电镀时,针尖部位的镀层会比针杆上厚许多,在放大镜下观察针尖有时会旦火柴头形状.(见图3)其头颈部的镀层即插针前端顶部靠后一点部位的金镀层检验结合力就不合格.这种现象在振动镀金时易出现.2.3.5振动镀金振频调整不正确采用振动电镀镀接插件时,如果在镀镍时振动频率调整不正确镀件跳动太快,易开成双层镍对镀层结合力影响甚大.3解决质量问题的方法有些种类的接插件其插针在设计时其针杆的外径尺寸略小于焊线孔的孔径尺寸,在电镀过程中部份插针就会形成首尾相接造成焊线孔内镀不进金.(见图示)以上两种现象在振动镀金时较容易发生.2.2.3盲孔部位浓度较大超过电镀工艺深镀能力由于在插孔的劈槽底部距孔底还有一段距离,这段距离客观上形成了一段盲孔.同样在插针和插孔的焊线孔里也有这样一段盲孔,它是提供导线焊接时的导向作用.当这些孔的孔径较小(往往低于1毫米甚至低于0.5毫米)而盲孔浓度超过孔径时镀液很难流进孔内,流进孔内的镀液又很难流出,所以孔内的金层质量很难保证.2.2.4镀金阳极面积太小当接插件体积较小时相对来说单槽镀件的总表面积就较大,这样在镀小型针孔件时如果单槽镀件较多.原来的阳极面积就显得不够.特别是当铂钛网使用时间过长铂损耗太多时,阳极的有效面积就会减少,这样就会影响镀金的深镀能力,镀件的孔内就会镀不进.2.3镀层结合力差在镀后检验接插件的镀层结合力时,有时会遇到部份插针的针端前部在折弯时或针孔件的焊线孔在压扁时镀层有起皮现象,有时在高温(2001小时)检测试验发现金层有极细小的鼓泡现象发生.2.3.1镀前处理不彻底对于小型针孔件来说,如果在机加工序完毕后不能立即采用三氯乙烯超声波除油清洗,那么接下来的常规镀前处理很难将孔内干涸的油污除净,这样孔内的镀层结合力就会大大降低.2.3.2基体镀前活化不完全在接插件基体材料中大量使用各类铜合金,这些铜合金中的铁铅锡铍等微量金属在一般的活化液中很难使其活化,如果不采用对应的酸将其活化,在进行电镀时,这些金属的氧化物跟镀层很难结合,于是就造成了镀层高温起泡的现象.2.2.3镀液浓度偏低在使用氨磺酸镍镀液镀镍时,当镍含量低于工艺范围时,小型针孔件的孔内镀层质量要受到影响.如果是预镀液的金含量过低,那么在镀金时孔内就有可能镀不上金,当镀件进入加厚金镀液时,孔内五金层的镀件孔内的镍层已钝化其结果是孔内的金层结合力自然就差.2.3.4细长状插针电镀时未降低电流密度在镀细长形状插针时,如果按通常使用遥电流密度电镀时,针尖部位的镀层会比针杆上厚许多,在放大镜下观察针尖有时会旦火柴头形状.(见图3)其头颈部的镀层即插针前端顶部靠后一点部位的金镀层检验结合力就不合格.这种现象在振动镀金时易出现.2.3.5振动镀金振频调整不正确采用振动电镀镀接插件时,如果在镀镍时振动频率调整不正确镀件跳动太快,易开成双层镍对镀层结合力影响甚大.3解决质量问题的方法3.3.3目前国内已有许多家公司提供专利型的电镀金工艺,象希普励公司、安格凯隆公司和乐思公司的镀金工艺用于接插件镀金镀层质量比较稳定。
常见电镀缺陷和原因分析

常见电镀缺陷和原因分析电镀缺陷是指在电镀过程中(包括准备工作和电镀工艺)出现的不良现象或问题。
下面我将介绍一些常见的电镀缺陷以及可能的原因分析。
1. 镀层不均匀:电镀层在部分区域厚度不均匀或出现斑点、斑纹等现象。
可能的原因包括:- 温度控制不准确:电镀液的温度不稳定、过高或过低,导致镀液在镀件表面的分布不均匀。
- 电镀液流动不均匀:电镀液在镀件上的流动速度不同,导致电流分布不均,进而影响镀层的均匀性。
- 镀液成分不稳定:电镀液中的添加剂、盐类等成分浓度不稳定,导致镀层的形成不均匀。
2. 黑斑或黄斑:镀层表面出现黑色或黄色的斑点。
可能的原因包括:- 杂质污染:电镀液中的杂质(如氧化物、铁离子等)进入镀液中,被还原到镀层表面形成斑点。
- 温度控制不当:电镀液的温度过高,导致镀层表面出现黄色或黑色反应物。
- 电流密度不均匀:镀件表面的电流密度不均匀,导致镀层表面出现黑斑或黄斑。
3. 镀层剥落:镀层与基材之间出现脱落现象。
可能的原因包括:- 镀液准备不当:电镀液的配方和浓度不正确,导致镀液附着力不足。
- 清洗不彻底:镀件在电镀前未进行彻底的清洗,导致表面存在杂质或脱脂剂,影响镀液与基材的结合。
- 电镀时间过短:电镀时间不足,镀层与基材之间的结合力不强,易剥离。
4. 镀层起泡:镀层表面出现气泡现象。
可能的原因包括:- 水分污染:电镀液中存在水分,经电解反应后生成氢气,导致镀液中产生气泡。
- 剧烈搅拌:电镀液在搅拌过程中引入大量气体,导致镀液中产生气泡。
- 电流密度不均匀:镀件表面的电流密度分布不均匀,导致一些区域出现过高的电流密度,进而引发气泡。
5. 镀层色差:镀层表面出现色差现象,包括颜色不均匀、色泽深浅不一等。
可能的原因包括:- 镀液浓度不均:电镀液中添加剂或盐类的浓度不均匀,导致镀层颜色不均匀。
- 电镀液PH值不稳定:电镀液中PH值变化较大,会影响镀层的色泽。
- 镀液渗染:电镀液渗透到基材中,与基材反应产生色差。
镀金层常见故障和纠正方法

镀金层常见故障和纠正方法
LY-955中性镀金工艺
一、工艺特点:
LY-955中性镀金,其镀层为24K纯金色,色泽金黄,颜色鲜艳均匀,镀液稳定,操作简单,由于含金量低,可作为面层,也可作为厚金的预镀层,大大降低了镀金的成本。
LY-955中性镀金适用于在镍,铜及铜合金上直接镀金。
广泛用于首饰,工艺品及制板整板镀金。
二、溶液配方及操作条件:
金属金克/升
LY-955开缸剂( M) 600毫升/升
PH值6-7
溶液温度 60-70℃
溶液比重(波美度) 12-140Be
阴极电流密度安/分米2
阳极材料 316不锈钢或铂钛网
搅拌阴极移动或净化空气搅拌
过滤定期或连续过滤
三、溶液配制方法:
1.充分清洗镀槽,加入1/3体积的纯水,加热至60℃
2.在搅拌下加入LY-955开缸剂(M)。
3.加入预先在热纯水中溶解的所需量氰化金钾,充分搅拌并加纯水至工作
体积。
4.测定溶液比重、PH值、温度后即可试镀。
四、溶液维护:
1.保持溶液中的金含量,应及时补充氰化金钾,每补充1克金(克的氰化金
钾)需加入LY-955补充剂(R)1ml。
2 .PH值高时可用10%KOH;调底时用10%的H
3PO
4。
3.升高溶液比重可用LY-955导电盐,每提高10Be约需加入20-30 g/L 。
4 .应避免异金属的带入,有机杂质污染可用活性炭处理。
金手指镀金质量问题及措施

金手指镀金质量问题及措施1前言在接插件电镀中,由于接触对有着较高的电气性能要求,镀金工艺在接插件电镀中占有明显重要的地位.目前除部分的带料接插件采用选择性电镀金工艺外,其余大量的针孔散件的孔内镀金仍采用滚镀和振动镀来进行.近几年,接插件体积发展到越来越小型化,其针孔散件的孔内镀金质量问题日趋突出,用户对金层的质量要求也越来越高,一些用户对金层的外观质量甚至达到了十分挑剔的程度.为了保证接插件镀金层质量结合力这几类常见质量问题总是提高接插件镀金质量的关键.下面就这些质量问题产生的原因进行逐一分板提供大家探讨.2镀金层质量问题的产生原因2.1金层颜色不正常接插件镀金层的颜色与正常的金层颜色不一致,或同一配套产品中不同零件的金层颜色出现差异,出现这种问题的原因是:2.1.1镀金原材料杂质影响当加入镀液的化学材料带进的杂质超过镀金液的忍受程度后会很快影响金层的颜色和亮度.如果是有机杂质影响会出现金层发暗和发花的现象,郝尔槽试片检查发暗和发花位置不固定.若是金属杂质干扰则会造成电流密度有效范围变窄,郝尔槽试验显示是试片电流密度低端不亮或是高端镀不亮低端镀不上.反映到镀件上是镀层发红甚至发黑,其孔内的颜色变化较明显.2.1.1镀金电流密度过大由于镀槽零件的总面积计算错误其数值大于实际表面积,使镀金电流量过大,或是采用振动电镀金时其振幅过小,这样槽中全部或部分镀件金镀层结晶粗糙,目视金层发红.2.1.3镀金液老化镀金液使用时间太长则镀液中杂质过度积累必然会造成金层颜色不正常.2.1.4硬金镀层中合金含量发生变化为了提高接插件的硬度和耐磨程度,接插件镀金一般采用镀硬金工艺.其中使用较多的是金钴合金和金镍合金.当镀液中的钴和镍的含量发生变化时会引起金镀层颜色改变.若是镀液中钴含量过高金层颜色会偏红;若是镀液中这镍含量过高金属颜色会变浅;若是镀液中这种变化过大而同一配套产品的不同零件又不在同一槽镀金时,这样就会出现提供给用户的同一批次产品金层颜色不相同的现象.2.2孔内镀不上金接插件的插针或插孔镀金工序完成后镀件外表面厚度达到或超过规定厚度值时,其焊线孔或插孔的内孔镀层很薄甚至无金层.2.2.1镀金时镀件互相对插为了保证接插件的插孔在插孔在插拔使用时具有一定弹性,在产品设计时大多数种类的插孔都有是在口部设计一道劈槽.在电镀过程中镀件不断翻动部份插孔就在开口处互相插在一起致使对插部位电力线互相屏敝造成孔内电镀困难.2.2.2镀金时镀件首尾相接有些种类的接插件其插针在设计时其针杆的外径尺寸略小于焊线孔的孔径尺寸,在电镀过程中部份插针就会形成首尾相接造成焊线孔内镀不进金.(见图示)以上两种现象在振动镀金时较容易发生.2.2.3盲孔部位浓度较大超过电镀工艺深镀能力由于在插孔的劈槽底部距孔底还有一段距离,这段距离客观上形成了一段盲孔.同样在插针和插孔的焊线孔里也有这样一段盲孔,它是提供导线焊接时的导向作用.当这些孔的孔径较小(往往低于1毫米甚至低于0.5毫米)而盲孔浓度超过孔径时镀液很难流进孔内,流进孔内的镀液又很难流出,所以孔内的金层质量很难保证.2.2.4镀金阳极面积太小当接插件体积较小时相对来说单槽镀件的总表面积就较大,这样在镀小型针孔件时如果单槽镀件较多.原来的阳极面积就显得不够.特别是当铂钛网使用时间过长铂损耗太多时,阳极的有效面积就会减少,这样就会影响镀金的深镀能力,镀件的孔内就会镀不进.2.3镀层结合力差在镀后检验接插件的镀层结合力时,有时会遇到部份插针的针端前部在折弯时或针孔件的焊线孔在压扁时镀层有起皮现象,有时在高温(2001小时)检测试验发现金层有极细小的鼓泡现象发生.2.3.1镀前处理不彻底对于小型针孔件来说,如果在机加工序完毕后不能立即采用三氯乙烯超声波除油清洗,那么接下来的常规镀前处理很难将孔内干涸的油污除净,这样孔内的镀层结合力就会大大降低.2.3.2基体镀前活化不完全在接插件基体材料中大量使用各类铜合金,这些铜合金中的铁铅锡铍等微量金属在一般的活化液中很难使其活化,如果不采用对应的酸将其活化,在进行电镀时,这些金属的氧化物跟镀层很难结合,于是就造成了镀层高温起泡的现象.2.2.3镀液浓度偏低在使用氨磺酸镍镀液镀镍时,当镍含量低于工艺范围时,小型针孔件的孔内镀层质量要受到影响.如果是预镀液的金含量过低,那么在镀金时孔内就有可能镀不上金,当镀件进入加厚金镀液时,孔内五金层的镀件孔内的镍层已钝化其结果是孔内的金层结合力自然就差.2.3.4细长状插针电镀时未降低电流密度在镀细长形状插针时,如果按通常使用遥电流密度电镀时,针尖部位的镀层会比针杆上厚许多,在放大镜下观察针尖有时会旦火柴头形状.(见图3)其头颈部的镀层即插针前端顶部靠后一点部位的金镀层检验结合力就不合格.这种现象在振动镀金时易出现.2.3.5振动镀金振频调整不正确采用振动电镀镀接插件时,如果在镀镍时振动频率调整不正确镀件跳动太快,易开成双层镍对镀层结合力影响甚大.3解决质量问题的方法3.1从产品设计开始消除影响电镀质量的因素首先在接插件进行产品设计时就要考虑到对电镀工序可能带来的影响,尽量避免因设计考虑不当给电镀质量留下隐患.3.1.1对一字形开口的插孔,采用在劈槽时先从口部边缘向口部中央斜向45度角开口,然后再顺着口部中央垂直向下进行.若是十字形开口的插孔,可以先将插孔收口使劈槽口部的链宽度小于插孔壁厚度,这样就可减少和避免镀金时产生插孔互相对插现象.(见图4)3.1.2设计时插针的针杆尺寸应始终略大于焊线孔孔尺寸或是延长焊线孔铣弧长度避免电镀时插针首尾相接.3.1.3在盲孔部位的底部设计一横向通孔使电镀时镀液能在孔内顺利出入.(见图5)3.2采用科学的电镀工艺管理方法3.2.1加强对电镀质量控制,特别是对金盐的质量要重点关注.对使用的每一批金盐除了必须经过常规的理化检验外均要取样作郝尔槽试验,试验认定合格后再用于镀槽.郝尔槽试验方法:取样品中金盐十二克,加入柠檬酸钾100克配制成1升镀液,加温至50℃调整PH5.4-5.8作]郝尔槽试验.正常结果为250毫升郝尔槽试验样片在0.SA电流电镀1分钟时光亮范围应在靠电流密度低端二分之一以上面积,整块试片上应是均匀的金黄色,否则应判定金盐不能正常使用.3.2.2对每槽镀件的数量、表面积、总电流量在电镀前进行计算并作好记录,以便在出现质量问题后查找原因。
- 1、下载文档前请自行甄别文档内容的完整性,平台不提供额外的编辑、内容补充、找答案等附加服务。
- 2、"仅部分预览"的文档,不可在线预览部分如存在完整性等问题,可反馈申请退款(可完整预览的文档不适用该条件!)。
- 3、如文档侵犯您的权益,请联系客服反馈,我们会尽快为您处理(人工客服工作时间:9:00-18:30)。
接插件镀金层常见质量问题分析
摘要本文针对接插件的针孔散件电镀金中常见的镀层质量问题从产品设计和电镀工艺以及电镀设备等方面进行了原因分析,并提出了相应的解决方法.
关键词镀金质量问题措施
1前言
在接插件电镀中,由于接触对有着较高的电气性能要求,镀金工艺在接插件电镀中占有明显重要的地位.目前除部分的带料接插件采用选择性电镀金工艺外,其余大量的针孔散件的孔内镀金仍采用滚镀和振动镀来进行.近几年,接插件体积发展到越来越小型化,其针孔散件的孔内镀金质量问题日趋突出,用户对金层的质量要求也越来越高,一些用户对金层的外观质量甚至达到了十分挑剔的程度.为了保证接插件镀金层质量结合力这几类常见质量问题总是提高接插件镀金质量的关键.下面就这些质量问题产生的原因进行逐一分板提供大家探讨.
2镀金层质量问题的产生原因
2.1金层颜色不正常
接插件镀金层的颜色与正常的金层颜色不一致,或同一配套产品中不同零件的金层颜色出现差异,出现这种问题的原因是:
2.1.1镀金原材料杂质影响
当加入镀液的化学材料带进的杂质超过镀金液的忍受程度后会很快影响金层的颜色和亮度.如果是有机杂质影响会出现金层发暗和发花的现象,郝尔槽试片检查发暗和发花位置不固定.若是金属杂质干扰则会造成电流密度有效范围变窄,郝尔槽试验显示是试片电流密度低端不亮或是高端镀不亮低端镀不上.反映到镀件上是镀层发红甚至发黑,其孔内的颜色变化较明显.
2.1.2镀金电流密度过大
由于镀槽零件的总面积计算错误其数值大于实际表面积,使镀金电流量过大,或是采用振动电镀金时其振幅过小,这样槽中全部或部分镀件金镀层结晶粗糙,目视金层发红.
2.1.3镀金液老化
镀金液使用时间太长则镀液中杂质过度积累必然会造成金层颜色不正常.
2.1.4硬金镀层中合金含量发生变化
为了提高接插件的硬度和耐磨程度,接插件镀金一般采用镀硬金工艺.其中使用较多的是金钴合金和金镍合金.当镀液中的钴和镍的含量发生变化时会引起金镀层颜色改变.若是镀液中钴含量过高金层颜色会偏红;若是镀液中这镍含量过高金属颜色会变浅;若是镀液中这种变化过大而同一配套产品的不同零件又不在同一槽镀金时,这样就会出现提供给用户的同一批次产品金层颜色不相同的现象.
2.2孔内镀不上金
接插件的插针或插孔镀金工序完成后镀件外表面厚度达到或超过规定厚度值时,其焊线孔或插孔的内孔镀层很薄甚至无金层.
2.2.1镀金时镀件互相对插
为了保证接插件的插孔在插孔在插拔使用时具有一定弹性,在产品设计时大多数种类的插孔都有是在口部设计一道劈槽.在电镀过程中镀件不断翻动部份插孔就在开口处互相插在一起致使对插部位电力线互相屏敝造成孔内电镀困难.
2.2.2镀金时镀件首尾相接
有些种类的接插件其插针在设计时其针杆的外径尺寸略小于焊线孔的孔径尺寸,在电镀过程中部份插针就会形成首尾相接造成焊线孔内镀不进金.(见图示)以上两种现象在振动镀金时较容易发生.
2.2.3盲孔部位浓度较大超过电镀工艺深镀能力
由于在插孔的劈槽底部距孔底还有一段距离,这段距离客观上形成了一段盲孔.同样在插针和插孔的焊线孔里也有这样一段盲孔,它是提供导线焊接时的导向作用.当这些孔的孔径较小(往往低于1毫米甚至低于0.5毫米)而盲孔浓度超过孔径时镀液很难流进孔内,流进孔内的镀液又很难流出,所以孔内的金层质量很难保证.
2.2.4镀金阳极面积太小
当接插件体积较小时相对来说单槽镀件的总表面积就较大,这样在镀小型针孔件时如果单槽镀件较多.原来的阳极面积就显得不够.特别是当铂钛网使用时间过长铂损耗太多时,阳极的有效面积就会减少,这样就会影响镀金的深镀能力,镀件的孔内就会
镀不进.
2.3镀层结合力差
在镀后检验接插件的镀层结合力时,有时会遇到部份插针的针端前部在折弯时或针孔件的焊线孔在压扁时镀层有起皮现象,有时在高温(2001小时)检测试验发现金层有极细小的鼓泡现象发生.
2.3.1镀前处理不彻底
对于小型针孔件来说,如果在机加工序完毕后不能立即采用三氯乙烯超声波除油清洗,那么接下来的常规镀前处理很难将孔内干涸的油污除净,这样孔内的镀层结合力就会大大降低.
2.3.2基体镀前活化不完全
在接插件基体材料中大量使用各类铜合金,这些铜合金中的铁铅锡铍等微量金属在一般的活化液中很难使其活化,如果不采用对应的酸将其活化,在进行电镀时,这些金属的氧化物跟镀层很难结合,于是就造成了镀层
高温起泡的现象.
2.3.3镀液浓度偏低
在使用氨磺酸镍镀液镀镍时,当镍含量低于工艺范围时,小型针孔件的孔内镀层质量要受到影响.如果是预镀液的金含量过低,那么在镀金时孔内就有可能镀不上金,当镀件进入加厚金镀液时,孔内五金层的镀件孔内的
镍层已钝化其结果是孔内的金层结合力自然就差.
2.3.4细长状插针电镀时未降低电流密度
在镀细长形状插针时,如果按通常使用遥电流密度电镀时,针尖部位的镀层会比针杆上厚许多,在放大镜下观察针尖有时会旦火柴头形状.(见图3)其头颈部的镀层即插针前端顶部靠后一点部位的金镀层检验结合力就不合格.这种现象在振动镀金时易出现.
2.3.5振动镀金振频调整不正确
采用振动电镀镀接插件时,如果在镀镍时振动频率调整不正确镀件跳动太快,易开成双层镍对镀层结合力影响甚大.
3解决质量问题的方法
3.1从产品设计开始消除影响电镀质量的因素
首先在接插件进行产品设计时就要考虑到对电镀工序可能带来的影响,尽量避免因设计考虑不当给电镀质
量留下隐患.
3.1.1对一字形开口的插孔,采用在劈槽时先从口部边缘向口部中央斜向45度角开口,然后再顺着口部中央
垂直向下进行.若是十字形开口的插孔,可以先将插孔收口使劈槽口部的链宽度小于插孔壁厚度,这样就可
减少和避免镀金时产生插孔互相对插现象.(见图4)
3.1.2设计时插针的针杆尺寸应始终略大于焊线孔孔尺寸或是延长焊线孔铣弧长度避免电镀时插针首尾相接.
3.1.3在盲孔部位的底部设计一横向通孔使电镀时镀液能在孔内顺利出入.(见图5)
3.2采用科学的电镀工艺管理方法
3.2.1加强对电镀质量控制,特别是对金盐的质量要重点关注.对使用的每一批金盐除了必须经过常规的理化检验外均要取样作郝尔槽试验,试验认定合格后再用于镀槽.
郝尔槽试验方法:取样品中金盐十二克,加入柠檬酸钾100克配制成1升镀液,加温至50℃调整PH5.4-5.8作]
郝尔槽试验.正常结果为250毫升郝尔槽试验样片在0.SA电流电镀1分钟时光亮范围应在靠电流密度低端二分
之一以上面积,整块试片上应是均匀的金黄色,否则应判定金盐不能正常使用.
3.2.2对每槽镀件的数量、表面积、总电流量在电镀前进行计算并作好记录,以便在出现质量问题后查找原因。
3.2.3根据镀金生产情况及时分析调整镀液,保证镀液成份在最佳期工艺范围,镀镍溶液每月至少应用活性炭处理。
当镀金液使用到70个周期以上时应考虑重新配制新镀液,将旧镀液回收金后废弃。
3.2.4保证镀金时有足够的阳极面积,当电镀过程中使用的铂钛网上经常出现大量气泡而镀金久镀不上时
应考虑更换新的铂钛阳极。
3.2.5对小型针孔件在镀前增加一道超声波除油清洗工序。
3.2.6对铍青铜接插件在镀前用1:1盐酸溶液煮沸10--30分钟,充分除净氧化物后再进入常规电镀工序.对于黄铜件应在镀镍前的活化液中加入一定量的氢氟酸或直接使用带氟化物的氟酸盐配制活化液,以保证基材铜合金中的微量金属活化.
3.3采用先进的电镀设备和先进的镀金工艺进行电镀
3.3.1在消除了产品设计的不利因素后,采用振动电镀设备进行接插件镀金镀层质量明显强于滚镀.
3.3.2(1)采用换向脉冲电镀电源作镀金电镀电源,其深孔件的内孔质量比直流电镀效果明显.(2)在使用这种PPR(Periodic Pulse Peverse)电源时,关键是正反向电流的大小比值,时间长短比值一定要选择好,否则体现不出最佳效果.(3)目前宝迪公司提供的电镀生产线上大多配置了这种电源,我厂使用该公司的振动电镀自动线用于接插件镀金,我厂使用该公司的振动电镀自动线用于接插件镀金,镀层质量效果有明显增长.
3.3.3目前国内已有许多家公司提供专利型的电镀金工艺,象希普励公司、安格凯隆公司和乐思公司的镀金工艺用于接插件镀金镀层质量比较稳定。
另外我国许多老一辈的电镀工作都他们利用自己丰富的电镀经验在国外先进镀金配方基础上研制出了一些更加具有实用价值的镀金工艺。
建议国内的用户在认同使用效果后不妨俦使用他们的镀金工艺。
4结论
在接插件镀金过程中,影响镀层质量的因素较多,随着我国电子工业的迅速发展,一些新质量问题又会产生。
但是只要我们从接插件制造成的各个环节入手,找到产生这些问题的根本原因,对各个生产工序采用科学的管理手段,同时尽可能采用先进的电镀设备和技术,这些质量问题就会迎刃而解。