刀具路径生成算法
多轴加工无干涉刀具路径生成算法研究
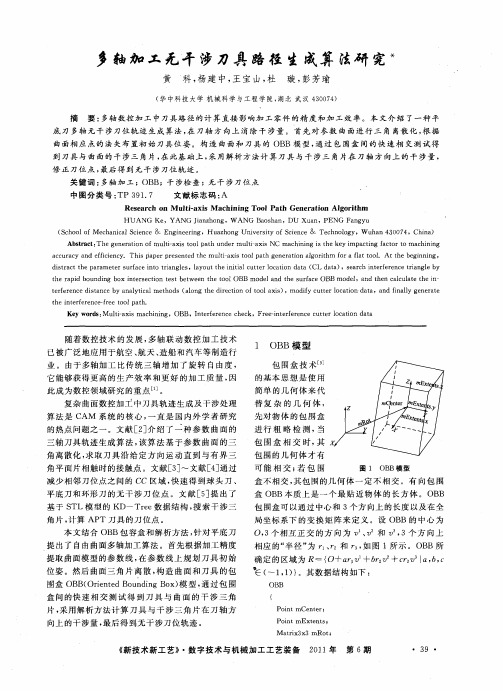
将坐 标 系 X y z 变换 到 全 局坐 标 系 xⅣ Ⅵ y, z
下 的变换 矩 阵记 为 T : 。
1 0 0 — 0x 0 1 0
CI C1 1 2
C2 C2 1 2
— Oy —
图 2 刀 具 OBB模 型
T2 = = 0 0
OB B
提 出 了 自由 曲面 多轴 加 工算 法 。首先 根据 加 工精 度 提取 曲面模 型 的参 数 线 , 参 数 线 上 规 划 刀 具初 始 在
位姿 。然后 曲面 三 角 片 离 散 , 造 曲面 和 刀 具 的 包 构 围盒 O B Or n e o n igB x 模 型 , 过 包 围 B ( i tdB u dn o ) e 通 盒 间 的快 速 相 交 测 试 得 到 刀 具 与 曲 面 的 干 涉 三 角
t e r p d b u d n o n e s c in t s e we n t e t o h a i o n i g b x i t r e t e tb t e h o l o OBB mo e n h u f c d l d t e s ra e OBB mo e ,a d t e ac l t h n a d l n h n c lu a e t e i — t re e c i t n e b n l t a t o s( l n h ie to ft o x s e f r n e d s a c y a ay i l c me h d a o g t e d r c i n o o l i),mo i u t r lc to a a n i al e e a e a d f c te o a i n d t ,a d f l g n r t y n y
数控车削加工刀具轨迹自动生成的算法

数控车削加工刀具轨迹自动生成的算法本文针对数控车削加工的特点,结合被加工零件的特征,提出了数控车削加工刀具轨迹自动生成的算法。
该算法在实际应用中,取得了理想的效果。
1 零件图的预处理根据数控车削加工的特点,零件的加工工艺分为:孔加工(包括打中心孔),外(内)表面加工、退刀槽及螺纹加工,根据表面质量的要求,又分为粗加工、半精加工和精加工等工艺。
数控车削加工刀具轨迹的规划,重点外(内)表面粗加工时刀具轨迹的规划处理。
对退刀槽、螺纹样的零件特征在进行表面粗加工时将其用表面代替,如图1。
数控加工中为减少多次安装带来的安装误差,一般采用一次装夹,对那些需要调头加工的部位则采取右偏刀反向走刀切削。
此外,对端面的加工有时选取向下的切削方向。
因此加工时的切削方向分为向左、向右和向下的切削方向。
图1对于倒角和倒圆角等工艺的处理在算法上将其作为表面处理。
对反向走刀切削时的刀具轨迹规划的算法与正向切削时类似,对内表面加工时刀具轨迹规划的算法与外表面切削时也相类似。
另外对精加工时的刀具轨迹规划,以及退刀槽和螺纹加工的刀具轨迹规划处理也较为容易。
一般,为减少刀具轨迹生成算法的复杂性,在刀具轨迹生成前对零件进行刀具干涉处理(刀具干涉处理的算法另文讨论)。
本文仅讨论正向切削外表面时粗加工刀具轨迹生成的算法。
2 刀具轨迹生成的算法图2由于粗加工刀具轨迹规划是从毛坯开始的,因此生成刀具轨迹时必须考虑毛坯的形状,并且随着工步的不同,其毛坯的形状也是不同的,此即工艺毛坯。
由于在轨迹生成前已经进行过刀具干涉的处理,所在刀具轨迹生成时主要考虑的是零件图形的特征。
经过零件图的预处理后,零件图形是由直线和圆弧所构成的连续表面,其中的关键是对图形中凹槽的识别和处理。
如图2所示,零件图形经过处理后,其粗加工的外表面轮廓为ABCDEPFGHIQJKM,经刀具切削方向为左时干涉处理后,其轮廊为ABCDPEFGHQJKM,其阴影部分为欠切削部分,在下一工步加工时,反向走刀切削时的刀具的起点分别为P点和Q点,通过反向向右走切切除其残留部分,从而形成所要求的零件轮廓QIH和PED。
改进的等残余高度加工自由曲面刀具路径生成算法
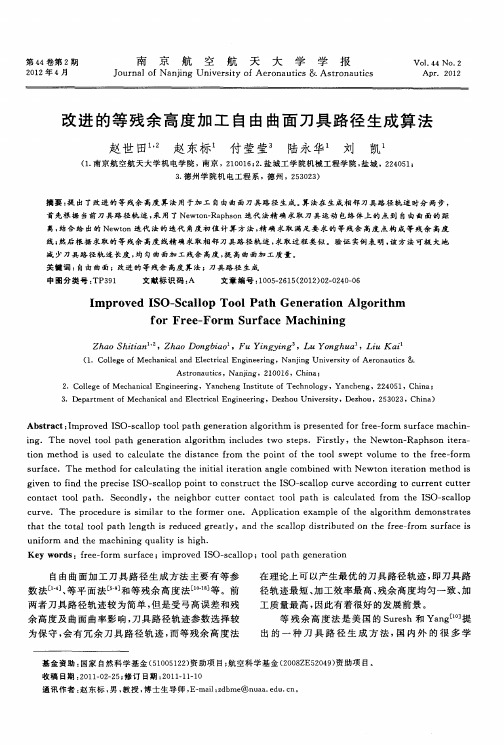
21 0 2年 4月
南 京 航 空
航
天
大
学
学报 Vo .来自4 No 2 14 . A p . 20 r 12
to a t c J u n lo ni g Un v riy o e o a tc & Asr n u is o r a fNa j ie st fA r n u is n
摘 要 : 出 了改进 的 等 残 余 高度 算 法 用 于加 工 自由 曲 面 刀 具 路 径 生 成 。 法在 生 成 相 邻 刀 具路 径 轨 迹 时分 两 步 , 提 算 首 先 根 据 当 前 刀 具 路 径 轨 迹 , 用 了 Ne o — a ho 采 wtn R p sn迭 代 法精 确 求 取 刀 具 运 动 包络 体 上 的 点 到 自由 曲 面 的 距 离, 结合 给 出 的 Ne tn迭 代 法 的 迭 代 角 度 初 值 计 算 方 法 , 确 求取 满 足 要 求 的 等 残 余 高度 点 构 成 等 残 余 高 度 wo 精 线; 然后 根 据 求取 的 等 残 余 高度 线 精 确 求 取 相 邻 刀 具路 径 轨 迹 , 取 过 程 类 似 。验 证 实例 表 明 , 方 法 可极 大 地 求 该
3 .De a t n fM e h n c l n e tia g n e i g,De h u Un v r iy,De h u,2 3 2 p r me to c a ia d El c rc l a En i e rn z o i e st zo 5 0 3,Ch n ) ia
Abs r t:mpr e SO— c lop t ol t e e a i n a g ih i e e t d f rf e — o m ur a e ma hi — t ac I ov d I s a l o h g n r to l ort m s pr s n e o r e f r s f c c n pa i g. Th v lt o t n r to g rt n e no e o lpa h ge e a i n al o ihm nc u s t t p . Fis l i l de wo s e s r ty,t wt n- p o t r — he Ne o Ra hs n ie a to t od i s d t a c a e t i t nc r m h i t o he t o we t v l m e t he f e —or i n me h s u e o c lul t he d s a e f o t e po n f t o ls p o u o t r e f m s f c .The me h orc l ul tng t nii lie a i n e c ur a e t od f a c a i he i ta t r ton a gl ombi e t wt t r to t d i n d wih Ne on ie a i n me ho S gi e o fnd t e ie I v n t i he pr cs SO- c lop po ntt ons r tt SO— c lo u ve a c d ng t u r n ut e - a l i o c s t uc he I — a l p c r c or i o c r e t c t r s c nt c t o a h. Se o l o a t o lp t c nd y,t i hb u t r c t c t o t i c l u a e fom t e SO— c lo he ne g or c t e on a t o l pa h s a c l t d r h I s a lp c r e The pr c dur s sm ia o t o m e ne Ap i a i x m p e o he a g rt uv . oe e i i l r t he f r r o . plc ton e a l f t l o ihm mo t a e de ns r t s t t t o a oo at e ha he t t lt lp h l ngt s r duc d g e ty,a d he s a l p d s r b e he f e — r h i e e ral n t c lo i t i ut d on t r e fom ur a e i s f c s u f r a d t c ni g qu lt s h gh. nio m n he ma hi n a iy i i
雕刻机刀具路径轨迹算法
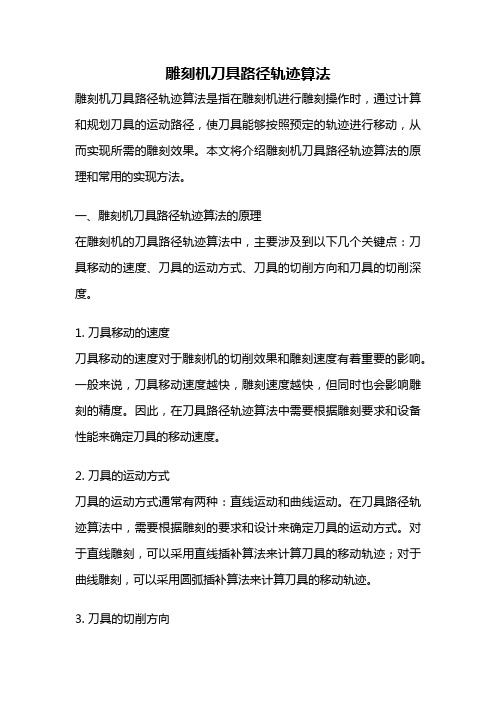
雕刻机刀具路径轨迹算法雕刻机刀具路径轨迹算法是指在雕刻机进行雕刻操作时,通过计算和规划刀具的运动路径,使刀具能够按照预定的轨迹进行移动,从而实现所需的雕刻效果。
本文将介绍雕刻机刀具路径轨迹算法的原理和常用的实现方法。
一、雕刻机刀具路径轨迹算法的原理在雕刻机的刀具路径轨迹算法中,主要涉及到以下几个关键点:刀具移动的速度、刀具的运动方式、刀具的切削方向和刀具的切削深度。
1. 刀具移动的速度刀具移动的速度对于雕刻机的切削效果和雕刻速度有着重要的影响。
一般来说,刀具移动速度越快,雕刻速度越快,但同时也会影响雕刻的精度。
因此,在刀具路径轨迹算法中需要根据雕刻要求和设备性能来确定刀具的移动速度。
2. 刀具的运动方式刀具的运动方式通常有两种:直线运动和曲线运动。
在刀具路径轨迹算法中,需要根据雕刻的要求和设计来确定刀具的运动方式。
对于直线雕刻,可以采用直线插补算法来计算刀具的移动轨迹;对于曲线雕刻,可以采用圆弧插补算法来计算刀具的移动轨迹。
3. 刀具的切削方向刀具的切削方向决定了雕刻的效果和切削力的大小。
在刀具路径轨迹算法中,需要根据雕刻要求和材料特性来确定刀具的切削方向。
常见的切削方向有:顺时针切削、逆时针切削和双向切削。
根据切削方向的不同,刀具的路径轨迹也会有所差异。
4. 刀具的切削深度刀具的切削深度决定了雕刻的深度和切削力的大小。
在刀具路径轨迹算法中,需要根据雕刻要求和材料特性来确定刀具的切削深度。
切削深度可以通过控制刀具的下降速度和切削轨迹的设计来实现。
在实际应用中,有多种算法可以用来计算和规划雕刻机刀具的路径轨迹。
下面介绍几种常用的算法:1. 直线插补算法直线插补算法是一种简单而常用的刀具路径规划算法。
该算法通过计算直线的起点和终点坐标,并结合刀具的移动速度和切削深度,确定刀具的移动轨迹和切削速度。
2. 圆弧插补算法圆弧插补算法是一种用于计算和规划刀具路径的常用算法。
该算法通过计算圆弧的起点、终点和半径,并结合刀具的移动速度和切削深度,确定刀具的移动轨迹和切削速度。
UG编程中的自动化刀具路径生成技巧介绍

UG编程中的自动化刀具路径生成技巧介绍自动化刀具路径生成是现代数控编程中的关键技术之一。
UG软件作为一款功能强大的CAD/CAM软件,具备高度的自动化刀具路径生成功能,为数控加工提供了便利。
本文将介绍UG编程中的一些自动化刀具路径生成的技巧,帮助读者更好地应用UG软件进行刀具路径生成。
一、刀具路径生成的基础概念在了解UG编程中的自动化刀具路径生成技巧之前,首先需要了解一些基础概念。
刀具路径生成是指根据加工零件的形状和加工要求,自动创建合理的刀具路径,使刀具能够按照预定的轨迹进行加工。
刀具路径生成的目标是提高加工效率、保证加工质量和节省加工成本。
二、自动化刀具路径生成技巧1. 使用合适的刀具尺寸和类型选择合适的刀具尺寸和类型是自动化刀具路径生成的第一步,影响着后续的刀具路径生成和加工效果。
根据加工零件的形状、材料以及加工要求,选择合适的刀具尺寸和类型,能够减少切削力、降低刀具磨损,提高加工效率和质量。
2. 合理设置切削参数切削参数的设置对于刀具路径生成和加工效果至关重要。
合理设置切削速度、进给速度、切削深度等参数,能够避免刀具过热、过载和振动等问题,提高切削效果和刀具寿命。
3. 使用合适的切削方式不同的加工任务需要采用不同的切削方式。
根据加工零件的形状和材料特性,选择合适的切削方式,包括立铣、侧铣、面铣等,能够更好地适应加工需求,并提高加工效率和表面质量。
4. 合理划分刀具路径将加工零件划分为不同的区域,并合理划分刀具路径,可以提高加工效率和质量。
根据零件的几何特征和加工要求,将加工刀具路径分为粗加工、精加工和清角等不同的阶段,并合理安排刀具路径的顺序和方向。
5. 设定合理的过切量和过切角过切量和过切角是自动化刀具路径生成中的重要参数,对于加工效果和刀具磨损有较大影响。
合理设定过切量和过切角,能够减少切削载荷和刀具振动,提高加工质量和刀具寿命。
6. 使用自动化刀具选用功能UG软件提供了自动化刀具选用功能,能够根据加工要求自动选择合适的刀具。
刀具切屑路径长度计算公式
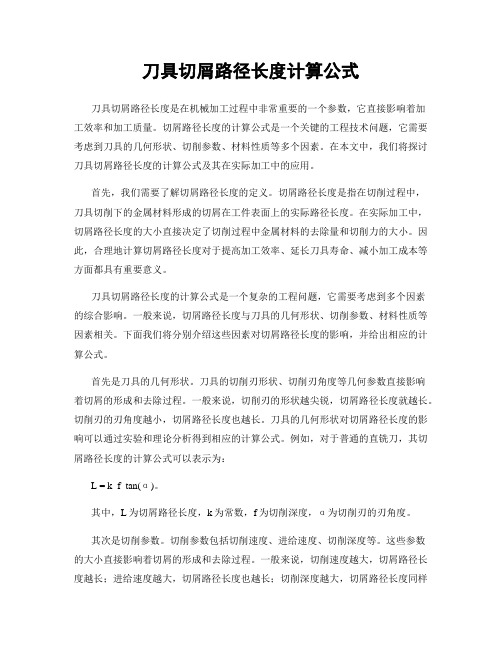
刀具切屑路径长度计算公式刀具切屑路径长度是在机械加工过程中非常重要的一个参数,它直接影响着加工效率和加工质量。
切屑路径长度的计算公式是一个关键的工程技术问题,它需要考虑到刀具的几何形状、切削参数、材料性质等多个因素。
在本文中,我们将探讨刀具切屑路径长度的计算公式及其在实际加工中的应用。
首先,我们需要了解切屑路径长度的定义。
切屑路径长度是指在切削过程中,刀具切削下的金属材料形成的切屑在工件表面上的实际路径长度。
在实际加工中,切屑路径长度的大小直接决定了切削过程中金属材料的去除量和切削力的大小。
因此,合理地计算切屑路径长度对于提高加工效率、延长刀具寿命、减小加工成本等方面都具有重要意义。
刀具切屑路径长度的计算公式是一个复杂的工程问题,它需要考虑到多个因素的综合影响。
一般来说,切屑路径长度与刀具的几何形状、切削参数、材料性质等因素相关。
下面我们将分别介绍这些因素对切屑路径长度的影响,并给出相应的计算公式。
首先是刀具的几何形状。
刀具的切削刃形状、切削刃角度等几何参数直接影响着切屑的形成和去除过程。
一般来说,切削刃的形状越尖锐,切屑路径长度就越长。
切削刃的刃角度越小,切屑路径长度也越长。
刀具的几何形状对切屑路径长度的影响可以通过实验和理论分析得到相应的计算公式。
例如,对于普通的直铣刀,其切屑路径长度的计算公式可以表示为:L = k f tan(α)。
其中,L为切屑路径长度,k为常数,f为切削深度,α为切削刃的刃角度。
其次是切削参数。
切削参数包括切削速度、进给速度、切削深度等。
这些参数的大小直接影响着切屑的形成和去除过程。
一般来说,切削速度越大,切屑路径长度越长;进给速度越大,切屑路径长度也越长;切削深度越大,切屑路径长度同样越长。
切削参数对切屑路径长度的影响也可以通过实验和理论分析得到相应的计算公式。
例如,对于普通的直铣刀,其切屑路径长度的计算公式可以表示为:L = k v f。
其中,L为切屑路径长度,k为常数,v为切削速度,f为进给速度。
UG编程在CNC加工中的快速刀具路径生成技巧
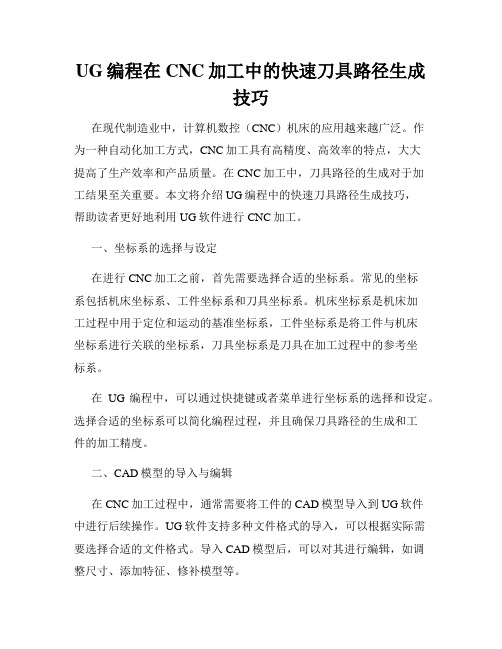
UG编程在CNC加工中的快速刀具路径生成技巧在现代制造业中,计算机数控(CNC)机床的应用越来越广泛。
作为一种自动化加工方式,CNC加工具有高精度、高效率的特点,大大提高了生产效率和产品质量。
在CNC加工中,刀具路径的生成对于加工结果至关重要。
本文将介绍UG编程中的快速刀具路径生成技巧,帮助读者更好地利用UG软件进行CNC加工。
一、坐标系的选择与设定在进行CNC加工之前,首先需要选择合适的坐标系。
常见的坐标系包括机床坐标系、工件坐标系和刀具坐标系。
机床坐标系是机床加工过程中用于定位和运动的基准坐标系,工件坐标系是将工件与机床坐标系进行关联的坐标系,刀具坐标系是刀具在加工过程中的参考坐标系。
在UG编程中,可以通过快捷键或者菜单进行坐标系的选择和设定。
选择合适的坐标系可以简化编程过程,并且确保刀具路径的生成和工件的加工精度。
二、CAD模型的导入与编辑在CNC加工过程中,通常需要将工件的CAD模型导入到UG软件中进行后续操作。
UG软件支持多种文件格式的导入,可以根据实际需要选择合适的文件格式。
导入CAD模型后,可以对其进行编辑,如调整尺寸、添加特征、修补模型等。
在编辑CAD模型时,需要注意保持模型的完整性和准确性。
避免出现缺陷和错误,以免影响后续的刀具路径生成和加工过程。
三、刀具路径生成的基本原理刀具路径生成是CNC加工中的核心过程,它决定了加工效率和加工质量。
UG软件通过算法和规则来生成刀具路径,以确保刀具能够按照预定的轨迹进行加工。
在刀具路径生成过程中,需要考虑多个因素,如加工精度要求、切削力和切削液的情况、刀具磨损和工件的形状等。
通过合理设置参数和选择算法,可以生成满足需求的刀具路径。
四、快速刀具路径生成技巧1. 合理选择刀具路径类型:UG软件提供了多种刀具路径类型,如等间距切削、连续切削、螺旋切削等。
在选择刀具路径类型时,需要根据具体的加工要求进行合理选择。
例如,对于平面加工,可以选择等间距切削;对于曲面加工,可以选择螺旋切削。
曲面数控加工中面向NURBS刀具路径生成的刀位点分段算法
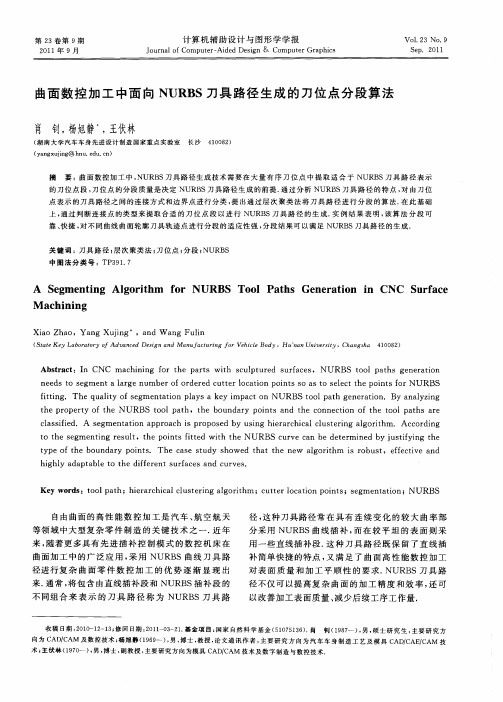
点 表 示 的刀 具 路 径 之 间 的连 接 方 式 和 边 界 点 进 行 分 类 , 出通 过 层 次 聚 类 法 将 刀 具 路 径 进 行 分 段 的算 法 . 此 基 础 提 在
上 , 过 判 断 连 接 点 的 类 型 来 提 取 合 适 的 刀 位 点 段 以进 行 NUR S刀 具 路 径 的 生 成 . 例 结 果 表 明 , 算 法 分 段 可 通 B 实 该 靠 、 捷 , 不 同 曲线 曲面 轮 廓 刀 具 轨 迹 点 进 行 分 段 的适 应性 强 , 段 结 果 可 以满 足 N 快 对 分 URB S刀 具 路 径 的生 成 .
曲面 数 控 加 工 中面 向 N R S刀具 路 径 生成 的刀位 点分 段算 法 U B
肖 钊, 杨旭静 王伏林 ,
( 南 大 学 汽 车 车 身 先 进 设 计 制造 国家 重 点 实 验 室 长 沙 湖
( a g uig h u e u c ) y n x j @ n . d .n n
408) 1 0 2
摘
要 :曲 面 数 控 加 工 中 , URB N S刀 具 路 径 生 成 技 术 需 要 在 大 量 有 序 刀 位 点 中 提 取 适 合 于位 点 段 , 位 点 的 分 段 质 量 是 决 定 NUR S刀 具 路 径 生 成 的 前 提 . 过 分 析 NUR S刀 具 路 径 的 特 点 , 由 刀 位 刀 B 通 B 对
UG编程中的刀具路径生成技巧介绍

UG编程中的刀具路径生成技巧介绍UG软件是一种先进的三维建模和机械制造软件,广泛应用于机械设计和制造领域。
在UG编程中,刀具路径生成是非常重要的一环,它关乎着产品质量和生产效率。
本文将介绍UG编程中的刀具路径生成技巧,帮助读者更好地应用UG软件进行刀具路径生成,提高加工效率。
一、刀具路径生成概述刀具路径生成是指在数控机床上完成加工任务时,通过UG软件自动生成刀具在工件表面的移动轨迹。
它是实现自动化加工的关键过程,直接影响着零件的加工质量和生产效率。
刀具路径生成技巧的应用,可以有效地减少加工时间、提高加工精度和降低加工成本。
二、UG编程中的刀具路径生成技巧1.合理设置切削参数在进行刀具路径生成前,需要合理设置切削参数。
切削参数包括进给速度、进给量、切削深度等。
合理设置切削参数可以保证切削过程的稳定性,减少切削振动和切削力,提高切削效率和工件表面质量。
2.选择合适的刀具类型根据加工零件的特点和要求,选择合适的刀具类型。
UG软件提供了多种刀具类型,如钻头、铣刀、镗刀等。
选择合适的刀具类型可以提高加工效率和质量。
3.使用高级刀路生成功能UG软件提供了丰富的刀路生成功能,如平面加工、轮廓加工、螺旋加工等。
这些高级刀路生成功能可以根据加工要求,生成更加高效和精确的刀具路径。
4.利用刀具半径补偿功能刀具半径补偿是指根据刀具半径大小,自动调整刀具路径的位置,保证切削轮廓准确。
利用UG软件的刀具半径补偿功能,可以有效地保证加工零件的精度和质量。
5.优化刀具路径规划在进行刀具路径生成时,可以通过优化刀具路径规划来减少刀具的移动距离和切削时间,提高加工效率。
常见的优化方法包括合并相邻刀具路径、降低刀具移动速度等。
6.避免干涉检测和修复刀具路径生成过程中,需要进行干涉检测,以确保刀具路径不与其他零件或夹具发生碰撞。
如果发现干涉问题,需要及时进行修复。
UG软件提供了强大的干涉检测和修复功能,可以方便地进行操作。
7.灵活应用UG编程技巧除了以上几点技巧外,UG编程中还有许多灵活应用的技巧。
基于单调链的行切刀具路径生成算法
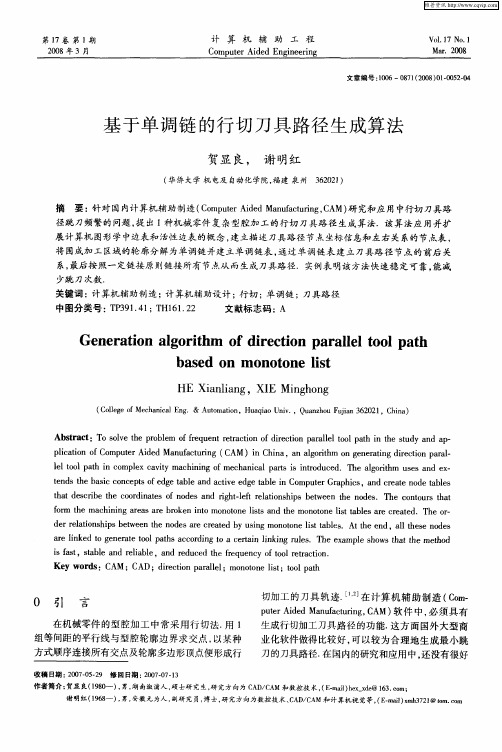
fr t e ma h n n r a r o e n o mo o o e lss a d te mo oo els a l sa e c e t d Th r o m h c i i g a e sa ebrk n i t n tn it n h n t n ittb e r r ae eo -
pi t no o p t i dMauatr g( A l a o f m u r d nfc i ci C eA e u n C M)i C ia a l rh ngn rt gdrc o a 1 n hn , na o tm o eea n i t npr . gi i ei a
Absr c t a t:T o v h r b e o o s le t e p o lm f ̄e u n e r cin o ie to a allto ah i h t v a d a - q e tr ta to fd r cin p rle o lp t n te sud n p
,
t a e c b h o r iae fn d s a d rg t1f eai n his b t e h o s Th 0 tur h t h td s r e t e c o dn ts o o e n h .e rl t s p ewe n te n de i i t o e c n 0 s t a
.
tn s t eb sc c n e t fe g a l n c ie e g a l n Co u e a h c a d c e t o e tb e e d a i o c p so d e tb e a d a tv d e tb e i mp trGr p is n r aen d a ls h
曲面数控加工中面向NURBS刀具路径生成的刀位点分段算法
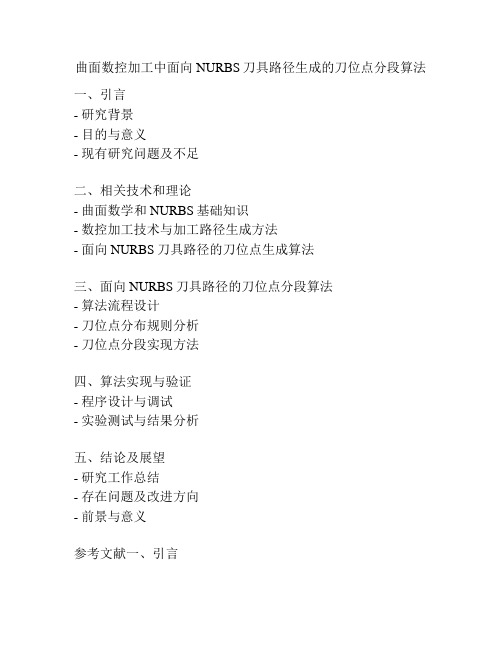
曲面数控加工中面向NURBS刀具路径生成的刀位点分段算法一、引言- 研究背景- 目的与意义- 现有研究问题及不足二、相关技术和理论- 曲面数学和NURBS基础知识- 数控加工技术与加工路径生成方法- 面向NURBS刀具路径的刀位点生成算法三、面向NURBS刀具路径的刀位点分段算法- 算法流程设计- 刀位点分布规则分析- 刀位点分段实现方法四、算法实现与验证- 程序设计与调试- 实验测试与结果分析五、结论及展望- 研究工作总结- 存在问题及改进方向- 前景与意义参考文献一、引言随着现代制造技术的不断发展和进步,数控加工技术越来越广泛地应用于各种工业制造领域。
其中,曲面数控加工技术是一种常见的高精度零件加工方式,具有加工精度高、加工效率高、加工自动化程度高等特点。
因此,曲面数控加工技术在航空、机械、模具等制造领域广泛应用。
曲面数控加工的基本任务是将 CAD 三维模型数据转化为数控加工机床的 G 代码,控制刀具轨迹实现加工操作。
在曲面数控加工中,生成高效、准确的刀具路径非常重要,可以直接影响加工质量和效率。
因此,如何将 CAD 三维模型数据转化为高效的数控加工机床 G 代码,逐渐成为曲面数控加工技术中的研究热点。
NURBS(Non-Uniform Rational B-Splines)是一种常用的曲面表达方法,它在现代制造技术中得到了广泛应用。
针对NURBS 接口的刀具路径生成是曲面数控加工的一项重要研究内容。
目前,如何在计算机中精确地表示和绘制 NURBS 刀具路径已成为数控技术中需研究的关键。
在曲面数控加工中,如何实现高效的刀位点分段成为研究领域之一。
本论文将针对面向 NURBS 刀具路径生成的刀位点分段算法进行研究,为曲面数控加工机床提供高精度的 G 代码生成方案。
本文将从以下几个方面展开研究:首先,简要介绍曲面数控加工技术的发展背景、研究现状及存在问题。
随后,探讨本研究所需要用到的相关技术和理论,包括曲面数学和NURBS基础知识、数控加工技术与加工路径生成方法、面向NURBS刀具路径的刀位点生成算法等。
刀具路径生成算法
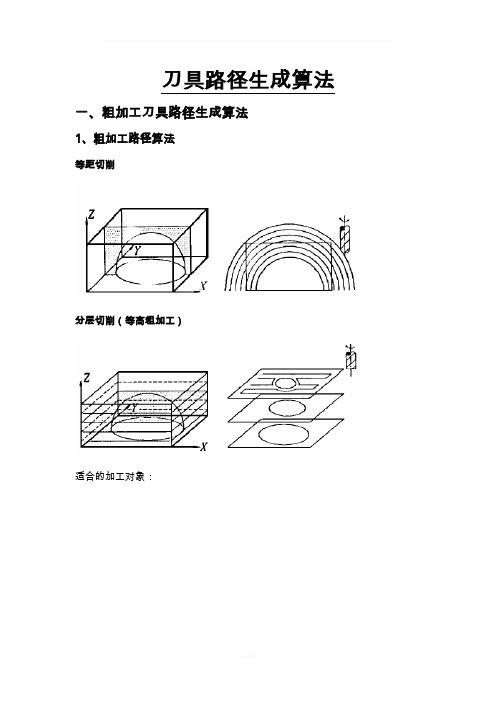
刀具路径生成算法一、粗加工刀具路径生成算法1、粗加工路径算法等距切削分层切削(等高粗加工)适合的加工对象:单元切削截面线法插铣加工2、粗加工算法中要解决的主要问题●切削边界提取●边界偏置形成刀具路径(针对环切而言)3、粗加工走到方式行切环切4、构型空间(Configuration Space, C-Space)将物体中心放在障碍物的边缘,通过Minkowski sum后,物体可作为点来处理。
示意图入下:5、粗加工刀具路径生成算法—G-buffer方法1)G-buffer模型生成●G-buffer模型:被加工零件的Configuration Space模型,也是CL Surface ●构造方法:刀具遍历曲面、反转刀具形成G-buffer模型的示意图:2)G-buffer模型的构造●在工件上方构造一网格平面,网格交点为点集{Pij}●将刀具放在网格平面中的网格点P(i, j)上●刀具向下移动(投影)直到触碰到工件停止,记录该网格点P(i, j)对应的Z坐标值Zij●重复上述步骤,直到得到所有网格点的Z坐标值●所有网格点的Z值构成了工件的G-buffer模型3)G-buffer模型与Z-buffer模型的区别4)切削区域边界用等高面Zc与G-buffer求交,形成切削区域边界●Zij < Zc,记录该网格点P(i, j)●Zij > Zc,不记录该网格点P(i, j)●这些被记录的网格点集合{Pij}构成切削区域无干涉边界点见下图:切削区域边界追踪利用图像处理中轮廓算法,顺序连接位于切削区域边界上的网格点5)切削区域判定(从外到内:一层加工,一层不加工)边界描述树:用来保存切削区域的边界,并识别切削区域边界拓扑结构的一种树状结构,边界之间的包容关系决定了边界在边界描述树中的位置。
6)刀具路径生成环切法环切加工刀具路径生成:利用等距线计算方法,对每个切削区域的边界按走刀步距的数值计算等距线,不断循环偏置,从而产生环切加工刀具轨迹。
五轴数控加工中的算法研究
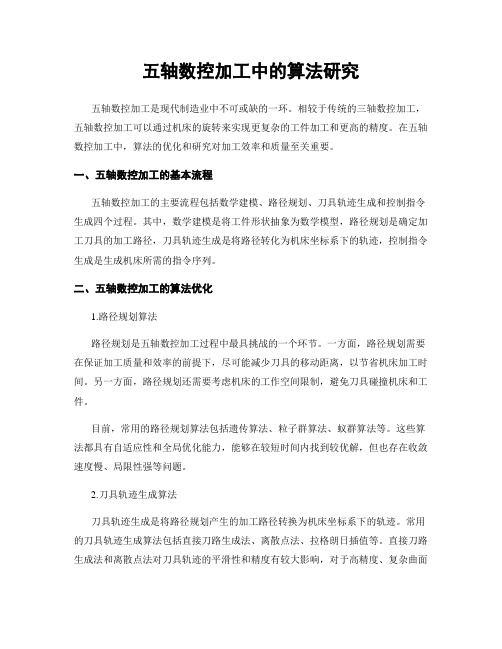
五轴数控加工中的算法研究五轴数控加工是现代制造业中不可或缺的一环。
相较于传统的三轴数控加工,五轴数控加工可以通过机床的旋转来实现更复杂的工件加工和更高的精度。
在五轴数控加工中,算法的优化和研究对加工效率和质量至关重要。
一、五轴数控加工的基本流程五轴数控加工的主要流程包括数学建模、路径规划、刀具轨迹生成和控制指令生成四个过程。
其中,数学建模是将工件形状抽象为数学模型,路径规划是确定加工刀具的加工路径,刀具轨迹生成是将路径转化为机床坐标系下的轨迹,控制指令生成是生成机床所需的指令序列。
二、五轴数控加工的算法优化1.路径规划算法路径规划是五轴数控加工过程中最具挑战的一个环节。
一方面,路径规划需要在保证加工质量和效率的前提下,尽可能减少刀具的移动距离,以节省机床加工时间。
另一方面,路径规划还需要考虑机床的工作空间限制,避免刀具碰撞机床和工件。
目前,常用的路径规划算法包括遗传算法、粒子群算法、蚁群算法等。
这些算法都具有自适应性和全局优化能力,能够在较短时间内找到较优解,但也存在收敛速度慢、局限性强等问题。
2.刀具轨迹生成算法刀具轨迹生成是将路径规划产生的加工路径转换为机床坐标系下的轨迹。
常用的刀具轨迹生成算法包括直接刀路生成法、离散点法、拉格朗日插值等。
直接刀路生成法和离散点法对刀具轨迹的平滑性和精度有较大影响,对于高精度、复杂曲面加工常常不适用。
而拉格朗日插值法能够在一定程度上保持轨迹的平滑性和精度,是目前应用广泛的一种刀具轨迹生成算法。
3.控制指令生成算法控制指令生成算法是将刀具轨迹转化为机床控制器所需的指令序列。
常用的控制指令生成算法包括基于G代码的程序生成法、数字化控制器固件生成法、基于NC语言表示的程序生成法等。
三、五轴数控加工的应用五轴数控加工广泛应用于航空航天、汽车、模具等制造领域。
其中,航空航天领域对五轴数控加工的精度和效率要求较高,尤其是航空发动机涡轮叶片等高精度、复杂曲面零部件的加工对五轴数控加工的技术水平和算法优化提出了更高挑战。
MasterCAM的三维刀具路径生成
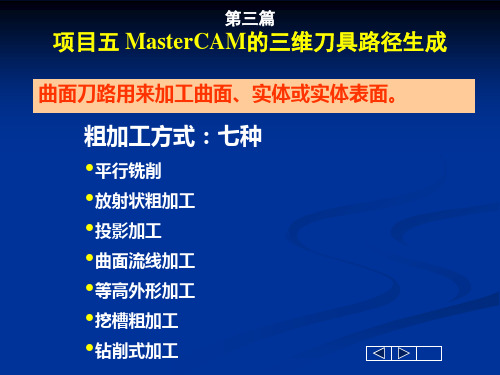
四、曲面加工综合实例
曲面挖槽粗加工→等高外形半精修 平行式曲面精修 曲面挖槽粗加工 等高外形半精修→平行式曲面精修 等高外形半精修
2、等高外形方式: 、等高外形方式:
为主切削面,紧挨着曲面边廓产生刀路, 以 XY 为主切削面,紧挨着曲面边廓产生刀路,一层一层地往下推 进。 和挖槽式的区别:它仅产生紧贴曲面边廓的刀路。 和挖槽式的区别:它仅产生紧贴曲面边廓的刀路。挖槽式更适合于块 状毛坯的粗切加工, 状毛坯的粗切加工,而等高外形方式则适合于那些已经铸锻成型的加 工余量少而均匀的坯料。 工余量少而均匀的坯料。
6、残料清角方式 、
残料清角刀路通常也发生于一些曲面交接处, 残料清角刀路通常也发生于一些曲面交接处,它不仅产生于非圆滑过 渡的曲面交接处,也发生在曲面倒圆的部位。 渡的曲面交接处,也发生在曲面倒圆的部位。 当曲面交接部位的转角较小,粗加工时刀具无法切削到,那么, 当曲面交接部位的转角较小,粗加工时刀具无法切削到,那么,就需 要更换较小的刀具进行清角修整, 要更换较小的刀具进行清角修整,这时就可选用残料清角曲面精修方 式。
3、陡斜面式 、
陡斜面式主要用于在粗加工或精加工后对一些相对较陡峭的曲面部 位做进一步的精修。 位做进一步的精修。 选用陡斜面加工方式时, 选用陡斜面加工方式时,系统将在众多的曲面中自动地筛选出符合 斜角范围的部位,并生成精修刀路。 斜角范围的部位,并生成精修刀路。
50° 90° 50°~90°度范围陡斜面加工刀路 0°~50°度范围斜面加工的刀路 50°
4、浅平面式 、
选用浅平面方式, 选用浅平面方式,则系统会在众多的曲面中自动地筛选出那 些比较浅的平面、平坦的曲面、浅坑等部位,并产生刀路。 些比较浅的平面、平坦的曲面、浅坑等部位,并产生刀路。
- 1、下载文档前请自行甄别文档内容的完整性,平台不提供额外的编辑、内容补充、找答案等附加服务。
- 2、"仅部分预览"的文档,不可在线预览部分如存在完整性等问题,可反馈申请退款(可完整预览的文档不适用该条件!)。
- 3、如文档侵犯您的权益,请联系客服反馈,我们会尽快为您处理(人工客服工作时间:9:00-18:30)。
刀具路径生成算法一、粗加工刀具路径生成算法1、粗加工路径算法等距切削分层切削(等高粗加工)适合的加工对象:单元切削截面线法插铣加工2、粗加工算法中要解决的主要问题切削边界提取边界偏置形成刀具路径(针对环切而言)3、粗加工走到方式行切环切4、构型空间(Configuration Space, C-Space )将物体中心放在障碍物的边缘,通过Minkowski sum 后,物体可作为点来处理。
示意图入下:5、粗加工刀具路径生成算法—G-buffer 方法1)G-buffer 模型生成G-buffer 模型:被加工零件的Configuration Space 模型,也是CL Surface 构造方法:刀具遍历曲面、反转刀具形成G-buffer 模型的示意图:2)G-buffer 模型的构造在工件上方构造一网格平面,网格交点为点集{Pij}将刀具放在网格平面中的网格点P(i, j) 上刀具向下移动(投影)直到触碰到工件停止,记录该网格点P(i, j)对应的Z 坐标值Zij重复上述步骤,直到得到所有网格点的Z 坐标值所有网格点的Z 值构成了工件的G-buffer 模型3)G-buffer 模型与Z-buffer 模型的区别4)切削区域边界用等高面Zc 与G-buffer 求交,形成切削区域边界Zij < Zc ,记录该网格点P(i, j)Zij > Zc ,不记录该网格点P(i, j)这些被记录的网格点集合{Pij} 构成切削区域无干涉边界点见下图:切削区域边界追踪利用图像处理中轮廓算法,顺序连接位于切削区域边界上的网格点5)切削区域判定(从外到内:一层加工,一层不加工)边界描述树:用来保存切削区域的边界,并识别切削区域边界拓扑结构的一种树状结构,边界之间的包容关系决定了边界在边界描述树中的位置。
6)刀具路径生成环切法环切加工刀具路径生成:利用等距线计算方法,对每个切削区域的边界按走刀步距的数值计算等距线,不断循环偏置,从而产生环切加工刀具轨迹。
等距线计算:直接偏置法和Voronoi 方法。
行切法行切加工刀具路径生成:从刀具路径角度方向,用一组平行于刀具路径角度的平行线分别与切削区域边界求交,得到交点,生成各切削行的刀具轨迹线段;下图表达了行切法的示意图:刀具轨迹线段的有序串联。
6、粗加工刀具路径生成算法—Z-map 方法1)Z-map 模型方法简介Z-map 模型:被加工零件的近似模型,利用网格点逼近被加工曲面构造方法:线面求交2)Z-map 模型与G-buffer 模型的区别3)切削区域边界用等高面Zc 与Z-map 模型求交Zij< Zc ,记录该网格点P(i, j)Zij > Zc ,不记录该网格点P(i, j)这些被记录的网格点集合{Pij} 构成切削区域初始边界点切削区域确定示意图:切削区域初始边界点筛选(比G-buffer 要多的一步检查)切削区域的初始边界点可能是干涉点对每个初始边界点,搜索其邻域的非边界点沿初始边界点邻域的每个非边界点方向,利用投影法进行干涉检查如果干涉,则删除该边界点;否则,保留切削区域边界追踪、切削区域判定和刀具路径生成(行切和环切)均可参照G-buffer 方法。
7、粗加工刀具路径生成算法—直接求交法1)直接求交法简介直接求交法:根据等高面与被加工零件表面的交线,规划刀具路径。
构造方法:面面求交直接求交法示意图:2)具体方法被加工零件与平面交线:被加工曲面集合{Si}(i = 1, 2, , n),切削层平面Zc,则交线集合Curi = Si ∩Zc计算曲面Si位于切削层平面Zc 上方的轮廓线Profi为每张被加工曲面规划切削区域:交线Curi 与曲面Si 的位于切削层平面Zc 上方的轮廓线Profi 在平面上的投影Prji 构成曲面Si 的非切削区域边界Non CutBndi 。
给定刀具半径D,对每个曲面Si 的非切削区域边界Non CutBndi 按照距离D/2 偏置,获得偏置边界Non CutBndOffi边界裁剪合并形成非切削区域。
切削区域判定、刀具路径生成都可以直接参照G-buffer 方法。
二、精加工刀具路径生成算法1、多面体法1)概述多面体法就是采用曲面的离散三角片模型计算刀具轨迹,它是目前各商业CAM 系统中应用最广泛、计算最稳定的刀具轨迹生成方式之一。
2)算法思想在初始刀位点处,判断刀具表面与多面体中每个三角片的顶点、边和三角面片的干涉关系,计算干涉量并根据干涉量调整刀具,生成无干涉的刀位点。
即刀具竖直由上向下运动(平行于Z 轴),当与多面体模型发生接触时刀具所在的位置。
3)算法步骤被加工曲面的多面体模型(UV 参数域法)上图表示了对于参数曲面的三角片离散过程,不停给的细分。
干涉量计算为了提高计算速度,在刀具投影域内搜索干涉检查三角片;在每个初始刀位点处,计算刀具到每个干涉检查三角片的顶点、边和面的距离,得到抬刀量。
刀具与三角片顶点、边和面的关系:无干涉刀位点刀具以计算得到的最大抬刀量进行抬刀,从而生成无干涉的刀位点。
刀位轨迹生成顺序连接无干涉刀位点生成刀位轨迹。
2、投影法1)概述投影法是UG CAM 中使用的三轴刀具轨迹生成算法。
投影法与多面体法的算法思想相同,区别在于:多面体法在消除干涉时,刀具沿着Z 轴运动;而投影法在消除干涉时,刀具可以沿着指定的投影矢量运动,从而增加了算法的灵活性。
2)算法内容给定投影矢量Vector将刀具放在Vector 的反方向,且与工件不发生碰撞的初始位置刀具沿着投影方向向工件移动当刀具碰到工件的时候停止,则刀具停止的位置为初始位置的Projection这里的“刀具”可包括:刀具本体、Holder 和主轴3)投影法刀具路径生成示意图4)投影(Projection )计算计算工件的离散模型Primitives ,如Facet (三角片法)、Finite-difference (UV 参数域法)、Discrete volume (空间离散法)等将工件离散模型存放在空间数据结构中(Spatial directory ),如Kd-tree 、Octree 、Surface-patch tree 、3D Grid 、OBBTree 、AABBTree 、Convex hull 等在tree 中搜索计算输入:工件模型、刀具形状,刀具在空间的初始位置,投影矢量输出:投影位置5) 三角片离散方式的投影计算(目的是用于干涉检查)将工件离散为三角片(Facet ),将三角片保存在Tree 结构中,每个树节点保存了其对应了Bounding Volume (BV )。
示意图:计算步骤及示意图:将刀具放在Tree 中最上层节点的BV 上,计算Z1将刀具放在Tree 中第二层节点的BV 上,计算Z1 和Z2将刀具放在Tree 中第三层节点的BV 上,计算各节点对应的Z 值以此类推,直到Tree 中所有叶子节点的BV 都计算了Z 值搜索最底层叶子节点,选择其中Z 最大值为最终位置2、偏置面法偏置面法思想:是最近几年研究比较多的一种方法。
直接在曲面的广义偏置面上生成刀具轨迹。
用三角片表示被加工曲面,分别偏置三角片的顶点、边和面,形成偏置元素(点偏置成球面、边偏置成柱面和面偏置成偏置面),这些偏置元素的包络面就是刀位面,用导动面与这些偏置元素求交得到交线,最后排序、裁剪和连接交线生成无干涉的刀具轨迹。
刀具轨迹由曲线段组成。
三、补加工(清根)刀具路径生成算法1、概述清根加工目的是去除精加工过程的残余体积,一般通过刀位曲面的清根曲线实现。
球头刀的球心沿工件表面的凹边区域滑动的轨迹称为铅笔曲线(Pencil curve )。
示意图如下图:清根曲线跟踪问题可以认为是一个边缘融合(Edge blending )问题,清根曲线可以用“滚动球”和“球位置采样”方法计算。
清根曲线生成算法可以基于Z-map 模型、多面体模型和STL 模型等多种方法。
2、补加工刀具路径生成算法_基于Z-map 模型基本思想:在Z-map 模型的各行和各列中寻找凹点(称为铅笔点,pencil-points ),然后通过跟踪这些铅笔点构造笔式曲线。
计算铅笔点输入:CL Z-map 模型输出:铅笔点、行进方向、质量过程在X 方向的CVS 曲线中寻找最大凹点设置行进方向为+Y 或-Y ;计算X 向CVS 上最大凹点处且垂直于行进方向的有效凹角αi;用质量等级规则确定铅笔的质量;如果满足栅格条件,则将MCP 定义为铅笔点;在Y 方向的CVS 曲线中寻找最大凹点设置行进方向为+X 或-X ;计算Y 向CVS 上最大凹点处且垂直于行进方向的有效凹角αi;用质量等级规则确定铅笔的质量;如果满足栅格条件,则将MCP 定义为铅笔点;如果铅笔点的X 向质量比Y 向质量好,则返回X 方向的初始铅笔点和质量,初始行进方向为+Y 或-Y ;反之亦然。
3、补加工刀具路径生成算法_基于多面体模型算法思想:利用多面体模型构造网格,利用网格计算补加工区域,从而生成补加工刀具路径。
算法步骤输入:多面体模型,刀具形状和尺寸输出:清根刀具路径过程:根据多面体模型计算刀触点网格(CC net )根据给定的间距采样刀触点网格计算干涉检查边界在干涉检查边界内产生清根路径Welcome To Download !!!欢迎您的下载,资料仅供参考!。