发泡模具排气装置设计
模具排气之设计

1.在分模度為 按鍵孔的靠破面設計排氣槽及排氣孔,排氣槽的寬度為2~3 ㎜。
排 氣 槽 深 度 為 : 0 .2 ~ 0 .5 m m . 排 氣 槽 深 度 如 附 表 所 示 .
排氣二
32~3㎜ m m ~4
排氣三
2~3㎜
說明結束 謝謝
3.抽真空排氣槽尺寸的基本要求
2~3㎜ DEEP 0.5~0.6㎜ ∮6㎜
3.5~4.0㎜ DEEP 如附表所示
(例如 注:當有其它原因無法製作O RING時,則不作O RING. (例如 SLIDE) 當有其它原因無法製作O RING時 則不作O
4.抽真空O型環結構之設計標準
V=
此種O型環的設計方式可以避免O 此種O型環的設計方式可以避免O型環掉落
=H
5.薄片Insert排氣方式
成品面 排氣槽只製作單面,深度 為塑膠原料對應排氣槽 的深度,離成品面應為 整面排氣
除客戶特別 指定, 指定,一般 不採用透氣 性鋼材
Depth:0.2 mm
在局部充填困難(成品肉厚較小處),可採用薄片 在局部充填困難(成品肉厚較小處),可採用薄片 ), Insert的方式,在薄片 的方式, 的方式 在薄片Insert上建立排氣槽 上建立排氣槽
在充填的末端及包風處 設計排氣, 設計排氣,排氣的基本 方式有: 方式有: 分割入子、設計頂針、 分割入子、設計頂針、 設計排氣槽等。 設計排氣槽等。
2.各種塑膠原料不發生毛邊的排氣孔深度明細
(排氣深度應先以最小值製作)
塑膠原料 PE PP PS SB ABS PC PBT 排氣孔深度(MM) 0.02 0.01~0.02 0.02 0.03 0.03 0.01~0.03 0.005~0.015 塑膠原料 SAN PPO POM PMMA PA PPS PC+ABS 排氣孔深度(MM) 0.03 0.03 0.01~0.03 0.03 0.005~0.015 0.01~0.03 0.015~0.02
排气对模具设计的影响
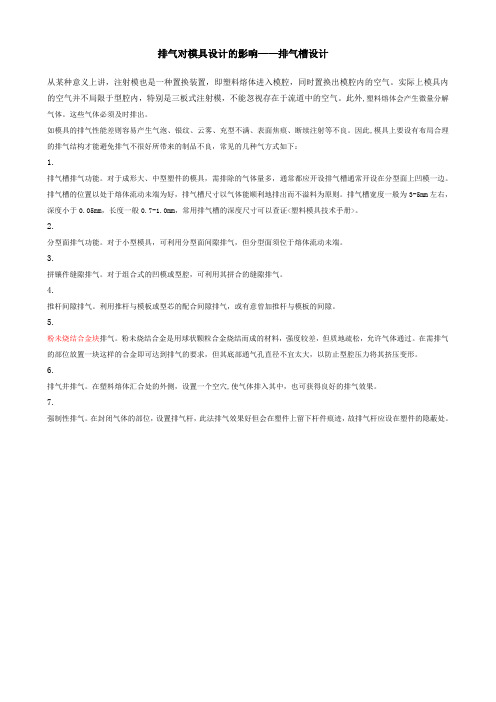
排气对模具设计的影响——排气槽设计从某种意义上讲,注射模也是一种置换装置,即塑料熔体进入模腔,同时置换出模腔内的空气。
实际上模具内的空气并不局限于型腔内,特别是三板式注射模,不能忽视存在于流道中的空气。
此外,塑料熔体会产生微量分解气体。
这些气体必须及时排出。
如模具的排气性能差则容易产生气泡、银纹、云雾、充型不满、表面焦痕、断续注射等不良。
因此,模具上要设有布局合理的排气结构才能避免排气不很好所带来的制品不良,常见的几种气方式如下:1.排气槽排气功能。
对于成形大、中型塑件的模具,需排除的气体量多,通常都应开设排气槽通常开设在分型面上凹模一边。
排气槽的位置以处于熔体流动未端为好,排气槽尺寸以气体能顺利地排出而不溢料为原则。
排气槽宽度一般为3-5mm左右,深度小于0.05mm,长度一般0.7-1.0mm,常用排气槽的深度尺寸可以查证<塑料模具技术手册>。
2.分型面排气功能。
对于小型模具,可利用分型面间隙排气,但分型面须位于熔体流动未端。
3.拼镶件缝隙排气。
对于组合式的凹模或型腔,可利用其拼合的缝隙排气。
4.推杆间隙排气。
利用推杆与模板或型芯的配合间隙排气,或有意曾加推杆与模板的间隙。
5.粉未烧结合金块排气。
粉未烧结合金是用球状颗粒合金烧结而成的材料,强度较差,但质地疏松,允许气体通过。
在需排气的部位放置一块这样的合金即可达到排气的要求,但其底部通气孔直径不宜太大,以防止型腔压力将其挤压变形。
6.排气井排气。
在塑料熔体汇合处的外侧,设置一个空穴,使气体排入其中,也可获得良好的排气效果。
7.强制性排气。
在封闭气体的部位,设置排气杆,此法排气效果好但会在塑件上留下杆件痕迹,故排气杆应设在塑件的隐蔽处。
模具排气系统设计

12
13
(2) 设排气槽
❖ 因为合模间隙很小,在强大的合模力作用下, 模板产生一定的变形,合模间隙更小。所以, 对于型腔容积较大的模具,仅仅利用合模间隙 排气,排气速率一般达不到要求。这时需要专 门开设排气槽。
❖ 当充模料流末端不在分 型面上,又没有配合间 隙可用时,一般难以开 设排气槽。
❖ 此时可在与料流末端接 触的成型零件上镶嵌可 透气的烧结金属块,并 用排气孔与外界或真空 系统连通,构成排气系 统。
19
小
结
排气系统设计主要考虑: ❖ 位置:一般设在料流的末端。 ❖ 尺寸:排气而不漏料。 ❖ 实施方式:
❖ 为有效排除模腔内的气体,排气系统的入口位置 (即排气系统在型腔内的开口)必须设在充模料 流的汇集处(料流末端)。
❖ 排气系统的出口位置可根据模具结构灵活安排, 但应注意采用排气槽等大截面排气系统时出口不 要正对操作者,以避免因工艺波动导致高温高压 熔体喷出时,可能造成的工伤事故。
8
2.排气系统尺寸
(1)利用分型面间隙排气。 (2)设排气槽。 (3)利用成型零件配合间隙排气。 (4)专设排气系统。
20
度w,根据缝隙深度h及在充模时间内排出模
腔内气体所需的排气通道截面积A确定
(w≥A/h)。
9
❖ 排气通道截面积A产下式计算 : A=0.05V/n
式中:A——排气通道截面积,mm2; V——型腔及浇注系统总容积,cm3; n——排气槽的数量
[说明:溢边值即物料能流入的最小缝隙,成型用 物料的溢边值取决于由物料特性和工艺条件决定 的物料流动性,流动性越好,溢边值越小。常用 塑料、常规成型条件下的溢边值如下表所示。]
聚氨酯发泡流动性,排气孔设计问题
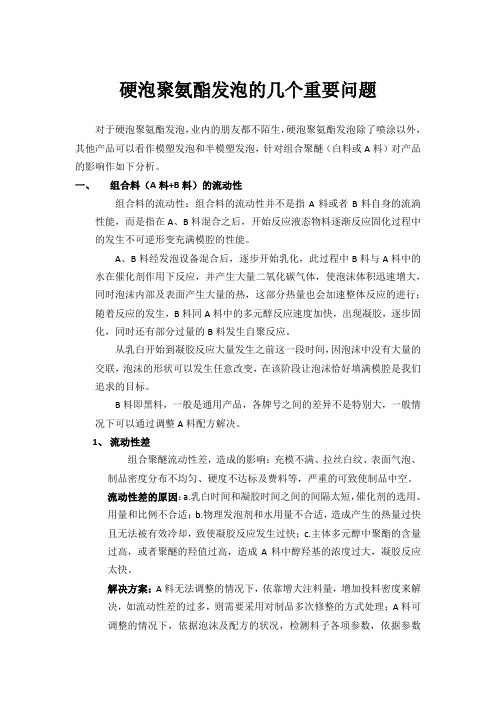
硬泡聚氨酯发泡的几个重要问题对于硬泡聚氨酯发泡,业内的朋友都不陌生,硬泡聚氨酯发泡除了喷涂以外,其他产品可以看作模塑发泡和半模塑发泡,针对组合聚醚(白料或A料)对产品的影响作如下分析。
一、组合料(A料+B料)的流动性组合料的流动性:组合料的流动性并不是指A料或者B料自身的流淌性能,而是指在A、B料混合之后,开始反应液态物料逐渐反应固化过程中的发生不可逆形变充满模腔的性能。
A、B料经发泡设备混合后,逐步开始乳化,此过程中B料与A料中的水在催化剂作用下反应,并产生大量二氧化碳气体,使泡沫体积迅速增大,同时泡沫内部及表面产生大量的热,这部分热量也会加速整体反应的进行;随着反应的发生,B料同A料中的多元醇反应速度加快,出现凝胶,逐步固化,同时还有部分过量的B料发生自聚反应。
从乳白开始到凝胶反应大量发生之前这一段时间,因泡沫中没有大量的交联,泡沫的形状可以发生任意改变,在该阶段让泡沫恰好填满模腔是我们追求的目标。
B料即黑料,一般是通用产品,各牌号之间的差异不是特别大,一般情况下可以通过调整A料配方解决。
1、流动性差组合聚醚流动性差,造成的影响:充模不满、拉丝白纹、表面气泡、制品密度分布不均匀、硬度不达标及费料等,严重的可致使制品中空。
流动性差的原因:a.乳白时间和凝胶时间之间的间隔太短,催化剂的选用、用量和比例不合适;b.物理发泡剂和水用量不合适,造成产生的热量过快且无法被有效冷却,致使凝胶反应发生过快;c.主体多元醇中聚酯的含量过高,或者聚醚的羟值过高,造成A料中醇羟基的浓度过大,凝胶反应太快。
解决方案:A料无法调整的情况下,依靠增大注料量,增加投料密度来解决,如流动性差的过多,则需要采用对制品多次修整的方式处理;A料可调整的情况下,依据泡沫及配方的状况,检测料子各项参数,依据参数对症下药。
2、流动性过好组合料流动性好的正面影响在此不谈,负面影响主要有:泡沫内部气泡甚至断层、漏料、模具承压过大等。
流动性过好的原因:与流动性差相反。
模具抽真空排气设计方案

优点:结构简单,实施方便,效 果显著。
总结词:简单、高效、适用于小 型模具
优缺点
缺点:对于大型模具,需要更多 的时间和能量来抽真空,且可能 需要更高的维护成本。
方案二:间接抽真空法
01
02
背景
在塑料模具、压铸模具等高分子材料成型模具中,残留气体 和挥发物常常会引发许多问题,如气孔、翘曲、变形等,严 重影响产品的质量和生产效率。因此,模具抽真空排气设计 成为了解决这些问题的必要手段。
模具抽真空排气设计的意义
提高产品质量
通过排除模具内部的残留气体和 挥发物,可以减少气孔、翘曲、 变形等问题,从而提高产品的质
THANK YOU
问题三
管道和阀门连接不牢固,导致漏气或真空度不足 。
解决方案三
在连接管道和阀门时,应确保连接处紧固、密封性好, 检查管道和阀门的完好性。
控制:抽真空排气效果的监测和控制方法
01
02
03
方法一
使用压力表监测模具内的 压力变化,判断抽真空排 气效果。
方法二
观察模具表面情况,检查 是否有气孔、气泡等缺陷 ,判断排气效果。
不足
本次研究虽然取得了一定的成果,但在实验过程中发现,该方案对于一些特殊材料的排气效果还有待进一步提高 。
结论二:对未来研究方向的展望
深入研究不同材料对模具抽真空 排气效果的影响,找出更加普遍
适用的解决方案。
进一步优化模具抽真空排气的设 计方案,提高其使用效率和稳定
性。
结合其他先进的制造技术,研究 更加智能化的模具抽真空排气方 案,提高生产效率和产品质量。
汽车座椅聚氨酯发泡模具排气系统的新设计

汽车座椅发泡采用聚氨酯体系一般会根据主机工厂(OEM )的需求,可分为MDI(二苯基甲烷二异氰酸酯),TDI(甲苯二异氰酸酯)、MDT(二苯基甲烷二异氰酸酯)/TDI(甲苯二异氰酸酯)混合体系的聚氨酯冷熟化发泡工艺,该发泡材质具有良好的物化性能以及高回弹性。
该体系使用的发泡剂主要是利用水与异氰酸酯反应,放出的二氧化碳作为发泡剂。
所以模具内需要排出的气体多为空气与发泡反应种产生的二氧化碳。
如果在发泡过程中排气不顺畅,泡沫产品就会出现表面或内部空洞等质量缺陷,从而造成一定的产品残次和报废,增加了产品的成本。
模具的排气系统的分布和产品的形状,浇注方式有密切的联系,廖元国对排气的设计提出三种典型的案例,分别为模具下模带有横筋,模具上方凸起,平直产品排气设计方式。
李宇锋提出了分型面增开溢流槽,排气槽的解决方案。
虽然方案解决了产品缺陷问题,但后道仍然需要员工大量的修补。
目前市场上标准的排气装置,此结构存在三种问题:一是单个气缸大,在模具上不能完全按工艺要求位置放置,导致产品排气不良,报废和修补高;二是此结构不能放置于模具分型面边缘,需开气槽,导致产品蘑菇头多;三是此结构的气管、三通等易损件多,容易造成设备停机率的上升。
本文主要设计全新排气结构,采用单气缸集成式控制模具上所有排气钢针的运动。
单根钢针占有空间小,可在模具上模面自由布置,极大的满足工艺布置钢针的自由度,从而优化模具排气方式,模具不需开气槽,减少产品报废和缺陷,提升产品质量,并降低修补人工。
1集成式顶针排气结构1.1集成式顶针排气结构定义集成式顶针排气结构是通过保证所有排气顶针的运动轨迹与驱动机构的运动轨迹相互平行的情况下,通过一块覆盖所有需要设置排气点区域的铝板连接固定顶针和驱动机构后,通过气缸驱动在设定的行程内做直线往复运动的一种机械机构。
其结构由气缸驱动机构(驱动气缸,滚珠导柱(线性轴承),固定板,固定座,连接座,铝板,紧固件)和排气机构(司筒顶针)组成。
模具系列8-模具排气系统
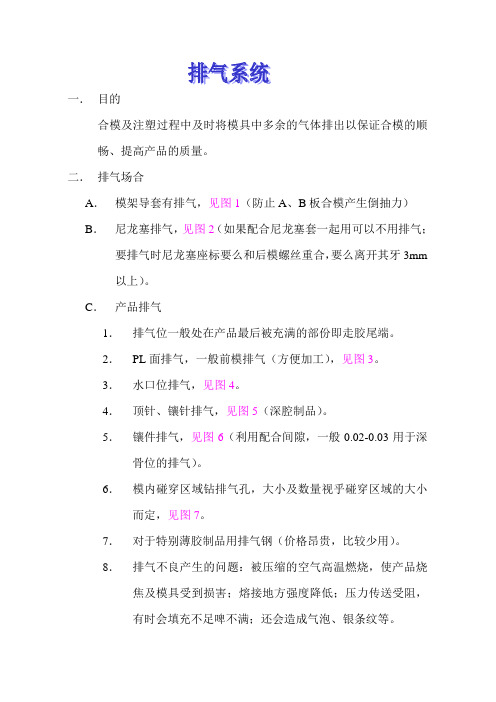
一.目的
合模及注塑过程中及时将模具中多余的气体排出以保证合模的顺畅、提高产品的质量。
二.排气场合
A.模架导套有排气,见图1(防止A、B板合模产生倒抽力)
B.尼龙塞排气,见图2(如果配合尼龙塞套一起用可以不用排气;
要排气时尼龙塞座标要么和后模螺丝重合,要么离开其牙3mm
以上)。
C.产品排气
1.排气位一般处在产品最后被充满的部份即走胶尾端。
2.PL面排气,一般前模排气(方便加工),见图3。
3.水口位排气,见图4。
4.顶针、镶针排气,见图5(深腔制品)。
5.镶件排气,见图6(利用配合间隙,一般0.02-0.03用于深骨位的排气)。
6.模内碰穿区域钻排气孔,大小及数量视乎碰穿区域的大小而定,见图7。
7.对于特别薄胶制品用排气钢(价格昂贵,比较少用)。
8.排气不良产生的问题:被压缩的空气高温燃烧,使产品烧焦及模具受到损害;熔接地方强度降低;压力传送受阻,
有时会填充不足啤不满;还会造成气泡、银条纹等。
模具排气设计

圖18.6及18.7是疏氣鋼鑲件設計的參考方法:
序號
修訂內容
批準/日期
審核/日期
制訂/修訂
2.6盡可能用銑床加工,然后省去刀紋.因為用磨床加工,往往平位太長,使空氣不能直接排出
2.7排氣坑兩旁可做45斜邊及拋光(用#320沙紙)。
3.
4.水口的排氣
4.1水口的排氣深度
5.頂針及司筒排氣設計
5.1 “X”闊度為膠料排氣坑深度的1/2陪,排氣坑深度可參考表12.1
5.2哥針亦可用同樣排氣設計。
8.7.檢查疏氣的方法,可塗_少量液體如脫模劑在疏氣鋼工件表面上,再由出氣位吹入高
壓風,檢查泡沫湧起的情況便可知道疏氣性能的情度。
8.8.清潔阻塞疏氣孔的方法:
(i)加熱工件至500F,維時最少一小時。
(ii)冷卻至室溫後,浸入丙酮(acetone),維時最少十五分鐘。
(iii)取出工件,用高壓風從工件底部吹出阻塞物。
模具排氣設計
1.
作為一通道給型腔內的空氣及塑料被注射時所產生的氣體,在注塑時可流出型腔。
2.
2.1尺寸依膠料,不同膠料排氣尺寸不同.
2.2所有流道及冷膠位要加排氣.
2.3所有成品要加排氣,位置在入水對面.死角位.最后走到的.
2.4 CORE針及司筒有需要加排氣.
2.5排氣針要銑坑駁通模胚பைடு நூலகம்排氣,或駁通頂針孔.
8.2.疏氣鋼須疏氣的部份在幼加工時(膠位及底部)除電蝕外,不可作任何機械加工(磨床或
鑼床);粗加工時可作任何機械加工。
8.3.鑲件底要做疏氣坑。
8.4.疏氣鋼可直接修螺絲。
8.5.疏氣鋼如要開運水,運水孔要作鍍Dichtol處理。
模具抽真空排气设计方案

管路连接
采用可靠的连接方式,确保管路连接紧密,防止 气体泄漏。
排气效果评估方法
观察法
通过观察制品表面质量、气泡分布等情况,评估排气效果。
称重法
通过对比制品排气前后的重量差异,评估排气效果。
仪器检测法
使用真空度计、压力传感器等仪器,检测模具内真空度或气体压 力,评估排气效果。源自05安全防护与环保措施
以避免产生气泡、烧焦等问题。
排气效率
02 要求模具抽真空排气系统具有较高的排气效率,以缩
短生产周期,提高生产效率。
操作便捷性
03
模具抽真空排气系统应设计简洁、操作方便,以降低
操作难度和减轻工人负担。
设计方案目标与期望
实现自动化控制
01
通过引入自动化控制技术,实现模具抽真空排气过程的自动化
,提高生产效率和生产质量。
防止模具因内外气压差导致变形或损坏。
快速抽真空
缩短成型周期,提高生产效率。
关键部件选型及依据
真空泵
选择高效、稳定的真空泵,确保快速抽真空 及排气效果。
真空管道
选用耐腐蚀、低阻力的真空管道,确保气体 顺畅排出。
真空阀门
选择密封性好、操作灵活的真空阀门,实现 模腔内外气压的快速平衡。
传感器与控制系统
通过传感器实时监测模腔内真空度,配合控 制系统实现自动化控制。
导柱导套
确保模具合模时的精确定位, 提高模具寿命。
模具底座
承载模具各部件,确保整体稳 定性。
顶针
用于推出成型后的产品,保证 产品顺利脱模。
冷却系统
通过循环冷却液降低模腔温度 ,确保产品质量和成型效率。
抽真空排气功能需求
排除模腔内空气
在注射成型过程中,确保模腔内无气泡,提高产品质量。
发泡模具排气装置设计

2.3 排气孔排气
排气孔形状:排 气孔设计形式多 种多样,但既要 有利于排气,又 要便于清理气孔, 常见的排气孔有 如下三种结构, 其中结构C最理 想。
2.2 排气槽排气
注射模具的排气槽应设置在塑料流动 的末端,一般常开设在分型面型腔一 侧,排气槽深可取,宽,以塑料不进 入排气槽为宜,其出口不要对着操作 工人,以防熔融塑料喷出造成事故, 有的厂推荐将分型面上的排气槽做成 弯形且逐步增宽,以降低塑料溢出的 可能。小型制件的排气量不大,如排 气点正好在分型面上,一般可以利用 分型面闭合时的微小间隙排气。
CLICK HERE TO ADD A TITLE
泡模具排气系统设计
此处添加副标题
冯
加
和
2
0
16Biblioteka 0913
1、概述
1、概述
在设计发泡成型模具时必须考虑排气问题。如果模具型腔内的气体不能 顺利排出,将造成制品的气泡、疏松、冲模不满、焊接不牢、制件表面 发乌或者在注射时由于气体被压缩所产生的高温制品底部碳化、烧焦, 而且型腔内气体被压缩产生的反压力会降低冲模速度,影响注射周期和 产品质量。
PM-35排气钢是一种优质透气性钢材,内部由微细的小孔相连构成,使空气 或任何气体能顺利渗透及穿过。因此,于注塑模具之适当位置镶上PM-35 排气钢,由气体所形成的注塑问题,可以完全清除,使成型加工更加完美。
2.3 排气钢排气
特性:1.降低注射压力,减少成型和保压时间。2.降低和消除成型件的内应力, 防止产品的变形和曲翘。3.表面皮纹的塑料零件,由于高温高压产生的亮光 皮纹,能解决要求亚光的表面。4.由于模具分型面的紧密配合,可以解决开模 困难等情况。解决通常利用顶针、镶件等无法提供足够表面区域以容纳可 能产生的大量气体等诸多问题,避免了利用分型面或其他排气系统而产生的 飞边及其他瑕疵。5.可使由于浇口偏位、壁厚不匀、壁薄产品等较难成型问 题得到解决和缓解。6.由于成型材料高温产生的气体和模具腔内快速聚压产 生的烧焦、流痕、缺料、吸气造成的零件变形等缺陷能得到充分解决。7.提 高成型生产效率,节约生产成本。
【CN209794380U】聚氨酯发泡模具自动排气装置【专利】
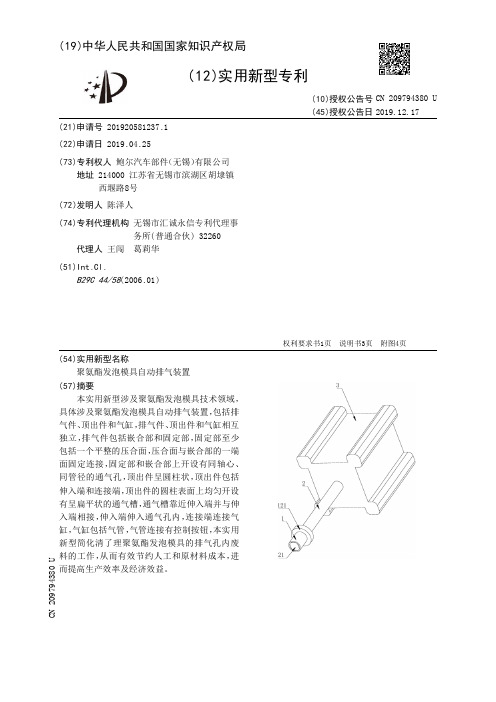
(19)中华人民共和国国家知识产权局(12)实用新型专利(10)授权公告号 (45)授权公告日 (21)申请号 201920581237.1(22)申请日 2019.04.25(73)专利权人 鲍尔汽车部件(无锡)有限公司地址 214000 江苏省无锡市滨湖区胡埭镇西堰路8号(72)发明人 陈泽人 (74)专利代理机构 无锡市汇诚永信专利代理事务所(普通合伙) 32260代理人 王闯 葛莉华(51)Int.Cl.B29C 44/58(2006.01)(54)实用新型名称聚氨酯发泡模具自动排气装置(57)摘要本实用新型涉及聚氨酯发泡模具技术领域,具体涉及聚氨酯发泡模具自动排气装置,包括排气件、顶出件和气缸,排气件、顶出件和气缸相互独立,排气件包括嵌合部和固定部,固定部至少包括一个平整的压合面,压合面与嵌合部的一端面固定连接,固定部和嵌合部上开设有同轴心、同管径的通气孔,顶出件呈圆柱状,顶出件包括伸入端和连接端,顶出件的圆柱表面上均匀开设有呈扁平状的通气槽,通气槽靠近伸入端并与伸入端相接,伸入端伸入通气孔内,连接端连接气缸,气缸包括气管,气管连接有控制按钮,本实用新型简化清了理聚氨酯发泡模具的排气孔内废料的工作,从而有效节约人工和原材料成本,进而提高生产效率及经济效益。
权利要求书1页 说明书3页 附图4页CN 209794380 U 2019.12.17C N 209794380U权 利 要 求 书1/1页CN 209794380 U1.聚氨酯发泡模具自动排气装置,其特征在于:包括排气件(1)、顶出件(2)和气缸(3),所述排气件(1)、顶出件(2)和气缸(3)相互独立;所述排气件(1)包括嵌合部(11)和固定部(12),所述嵌合部(11)的形状大小与聚氨酯发泡模具的排气孔相匹配,所述固定部(12)至少包括一个平整的压合面(121),所述压合面(121)与所述嵌合部(11)的一端面固定连接,所述固定部(12)和所述嵌合部(11)上开设有同轴心、同管径的通气孔(13);所述顶出件(2)呈圆柱状,所述顶出件(2)的管径与所述通气孔(13)的管径相同,所述顶出件(2)包括伸入端(21)和连接端(22),所述顶出件(2)的圆柱表面上均匀开设有呈扁平状的通气槽(23),所述通气槽(23)靠近所述伸入端(21)并与所述伸入端(21)相接,所述伸入端(21)伸入所述通气孔(13)内,所述连接端(22)连接所述气缸(3);所述气缸(3)包括气管,气管连接有控制按钮(32)。
- 1、下载文档前请自行甄别文档内容的完整性,平台不提供额外的编辑、内容补充、找答案等附加服务。
- 2、"仅部分预览"的文档,不可在线预览部分如存在完整性等问题,可反馈申请退款(可完整预览的文档不适用该条件!)。
- 3、如文档侵犯您的权益,请联系客服反馈,我们会尽快为您处理(人工客服工作时间:9:00-18:30)。
2.4 配合间隙排气
当由于型腔结构限制充模料流末端不在分型面上时,可利用
成型零件间的配合间隙排气。 构成型腔的成型零件中的某些零件,如顶杆、顶管、活动成 型零件等,与型腔或型芯之间多采用间隙配合,配合间隙较大, 若将其设计在料流末端,可兼起排气作用。 此时也可不专设排气系统。当排气速率不能满足要求时,可 在相应零件上设置排气结构,增大排气速率(参见下图)。
构成,使空气或任何气体能顺利渗透及穿过。因此,于注塑模具之 适当位置镶上PM-35排气钢,由气体所形成的注塑问题,可以完全 清除,使成型加工更加完美。 特点:1.比重小,比强度大。2.能量吸收性好。3.制振效果好。4.比
表面积大。有1/4的组织是通孔。
2.3 排气钢排气
特性:1.降低注射压力,减少成型和保压时间。2.降低和消除成型件
气孔之间气泡两侧受力,且所受之力相对于同一区域内一个排
气孔时物料对气泡的作用力小,最终造成气泡不能顺利排除, 而残存在泡沫中,小气泡逐渐碰撞融合,成为大气泡。
2.3 排气孔排气 排气孔形状:排气孔设计形式多种多样,但既要有利于排气, 又要便于清理气孔,常见的排气孔有如下三种结构,其中结
构C最理想。
2.2 排气槽排气 注射模具的排气槽应设置在塑料流动的末端,一般常开设在分型
面型腔一侧,排气槽深可取0.025-0.1mm,宽1.5-1.6mm,以塑
料不进入排气槽为宜,其出口不要对着操作工人,以防熔融塑料 喷出造成事故,有的厂推荐将分型面上的排气槽做成弯形且逐步 增宽,以降低塑料溢出的可能。小型制件的排气量不大,如排气
发泡模具排气系统设计
冯加和 20160913
1、概述
1、概述
在设计发泡成型模具时必须考虑排气问题。如果模
具型腔内的气体不能顺利排出,将造成制品的气泡、 疏松、冲模不满、焊接不牢、制件表面发乌或者在注 射时由于气体被压缩所产生的高温制品底部碳化、烧 焦,而且型腔内气体被压缩产生的反压力会降低冲模 速度,影响注射周期和产品质量。
的内应力,防止产品的变形和曲翘。3.表面皮纹的塑料零件,由于 高温高压产生的亮光皮纹,能解决要求亚光的表面。4.由于模具分 型面的紧密配合,可以解决开模困难等情况。解决通常利用顶针、 镶件等无法提供足够表面区域以容纳可能产生的大量气体等诸多
问题,避免了利用分型面或其他排气系统而产生的飞边及其他瑕
疵。5.可使由于浇口偏位、壁厚不匀、壁薄产品等较难成型问题 得到解决和缓解。6.由于成型材料高温产生的气体和模具腔内快 速聚压产生的烧焦、流痕、缺料、吸气造成的零件变形等缺陷能 得到充分解决。7.提高成型生产效率,节约生产成本。
2.4 配合间隙排气
2、总结
排气系统设计主要考虑: • 位置:一般设在料流的末端。 • 尺寸:排气而不漏料。 • 实施方式: (1)利用分型面间隙排气。 (2)设排气槽。 (3)利用成型零件配合间隙排气。 (4)专设排气系统。
2.2 排气孔排气 排气孔的位置选择:排气孔的位置并不是单纯的选择在制品 的最上端,要依据原料流动状态,选择在原料固化前最后留 到的位置,既要对模具进行整体考虑,也要对模具局部形态 进行分割考虑。
2.2 排气孔排气 排气孔的数量:排气孔的数量并不是越多越好,大家都知道在 排气过程中,最后残余的少量大泡会集中向排气孔位置成椭圆 形或者水滴形排列,可以看出,排气孔的数量越多,最终可能 残存的大气泡越多,如果同一区域内过多的开排气孔,两个排
1.概述
模腔中存 在的空气 模腔中气 体的来源
浇注系统 中存在的 空气
塑料中添 加剂挥发 反应产生 气体来自塑料原料 中水分蒸 发
塑料分解 生成气体
2、排气系统
排气孔排气
模具型腔中的 空气如何排出
排气槽排气
排气系统 排气钢排气 配合间隙排气 ……
作用 保证塑料熔体在填充过 程中型腔中的气体能完 全顺利排出
点正好在分型面上,一般可以利用分型面闭合时的微小间隙排气。
2.2 排气槽排气
低发泡模具必须设置排气槽,由于模腔内的压力低,排气槽
深度可达0.3mm左右,并不会发生溢边,不过根据经验,排气槽 的深度可达0.1-0.2mm(长5mm,宽10mm),对于大型塑件的 排气排气槽应设置在塑料流动的末端或两股料流熔之处。
MATERIAL
ABS
X(mm)
0.025-0.038
MATERIAL
PP
X(mm)
0.013-0.025
ACETAL
HIPS P.C
0.025-0.038
0.1 0.05
PS
PMMA PE
0.013-0.025
0.013-0.038 0.013-0.025
2.3 排气钢排气
PM-35排气钢是一种优质透气性钢材,内部由微细的小孔相连