发泡模具设计详解
发泡模具工艺流程

发泡模具工艺流程发泡模具工艺流程是制作发泡模具的一种常见工艺流程,它的主要目的是通过加热和冷却的过程来使原材料膨胀成为所需形状的模具。
下面将详细介绍发泡模具工艺流程的步骤和注意事项。
第一步:原材料准备在进行发泡模具工艺流程之前,首先需要准备好适宜的原材料。
常用的原材料有聚氨酯、聚苯乙烯等。
根据实际需要选择合适的原材料,并确保其质量符合要求。
原材料通常以颗粒或块状形式存在。
第二步:模具准备在开始制作发泡模具之前,需要准备好模具。
模具的制作可以使用不同材料,如铝、钢等。
根据实际需要选择合适的模具材料,并进行相关的加工和处理。
模具的设计和制造需要考虑到产品的形状和尺寸,以保证发泡模具的质量和精度。
第三步:注塑在进行注塑之前,需要将原材料加热至一定的温度。
加热的方式可以是直接加热或间接加热。
加热后的原材料会变得粘稠,可以通过注射机将其注入到已经准备好的模具中。
注塑过程需要控制注射时间、注射速度等参数,以确保注入的原材料均匀分布并填充整个模具。
第四步:发泡注塑完成后,需要对模具中的原材料进行发泡处理。
发泡的过程中需要控制好温度和时间,确保原材料可以膨胀成为所需的模具形状。
温度的控制可以通过加热或冷却来实现,时间的控制可以根据原材料的特性和制品的要求来确定。
经过发泡处理后,原材料会膨胀成为模具的形状。
第五步:冷却发泡完成后,需要对模具中的制品进行冷却。
冷却的方式可以是自然冷却或强制冷却。
冷却时间的长短取决于材料的类型和厚度,一般较薄的制品冷却时间较短,而较厚的制品冷却需要较长的时间。
通过冷却,制品可以固化和形成稳定的结构。
第六步:脱模与修整在冷却完成后,就可以将制品从模具中取出。
脱模需要注意不要造成模具和制品的损坏。
取出后,可以对制品进行修整和加工,以使其达到最终的要求和标准。
修整的方式包括切割、打磨、修边等。
根据制品的具体要求,选择适当的修整方法,使制品的表面光滑、边缘整齐。
总结:发泡模具工艺流程是一种常见的制作模具的工艺流程。
汽车发泡模具的设计开发浅析
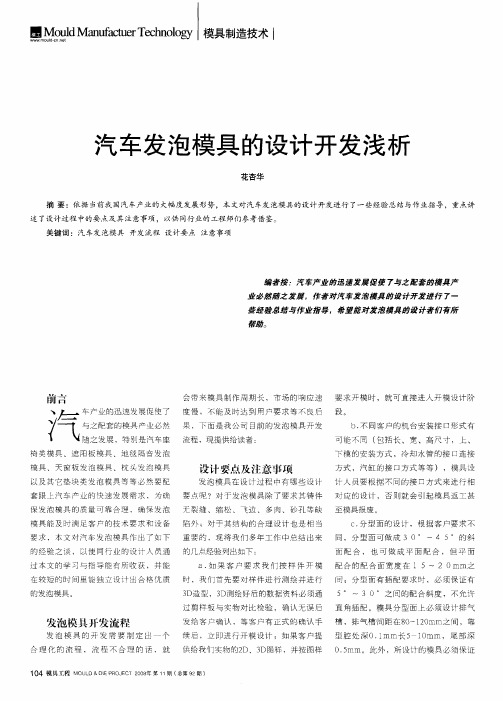
经 验总 结与 作业 指导 ,应 该能 对发泡 模 具的设计者们有所帮助 。 国 在机 台旋转 中心旋 转 时模具 不会 出现 干 润 滑油 槽 ,且 导柱 末 段必 须设 计限 位装
涉现 象 , 以保 证 旋 转 开 模 顺 利 进 行 。 置 ,导 向 零 件 与 模 具 滑 块 的 连 接 必 须 可
发 泡 模 具 的 开 发 需 要 制 定 出 一 个 续后 ,立 即进行 开模 设计 ;如果 客户 提 型 腔 处 深 0 1 . mm 长 5 1 m m , 尾 部 深 0 合 理 化 的 流 程 , 流 程 不 合 理 的 话 , 就 供给我们实物 的2 D、3 D图样 ,并按 图样 0 5 m 。此 外 ,所 设 计 的 模 具 必 须 保 证 .r a
1 - 0 m之 间 。 6 2r a
i. " 模具必 须 设计 吊环孔 ,以 保证模 1
具 的 加 工 、 运 输 方 便 ,且 能 顺 利 地 在 用
旦…里一旦耱 f ; 旦
士 _." t - J 劓 I }
|L ,
户 处装 上机 台 。
结 束 语
汽 车 产 品 的 日新 月 异 ,汽 车 模 具 行
发 泡 模 具 在 设 计 过 程 中 有 哪 些 设 计 计 人 员 要 根 据 不 同 的 接 口 方 式 来 进 行 相
套 跟 上 汽 车 产 业 的 快 速 发 展 需 求 , 为 确 要 点 呢 ? 对 于 发 泡 模 具 除 了 要 求 其 铸 件 对 应 的 设 计 , 否 则 就 会 引 起 模 具 返 工 甚 保 发 泡 模 具 的 质 量 可 靠 合 理 ,确 保 发 泡 无 裂 缝 、缩 松 、 飞 边 、 多 肉 、砂 孔 等 缺 至 模 具 报 废 。 模 具 能 及 时 满 足 客 户 的 技 术 要 求 和 设 备 陷 外 ;对 于 其 结 构 的 合 理 设 计 也 是 相 当
泡沫模具产品设计方案模板
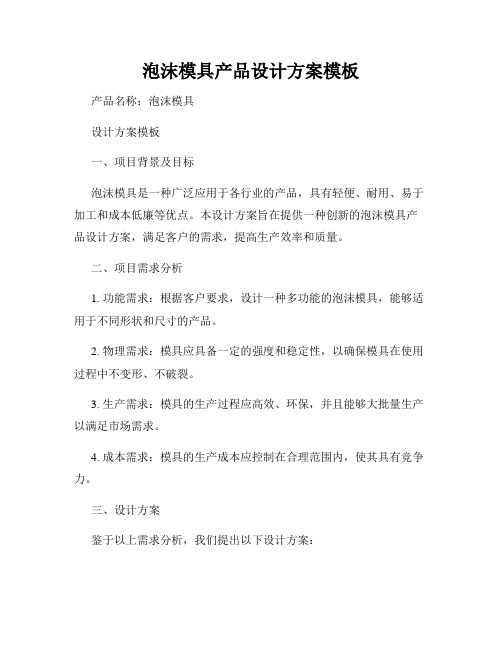
泡沫模具产品设计方案模板产品名称:泡沫模具设计方案模板一、项目背景及目标泡沫模具是一种广泛应用于各行业的产品,具有轻便、耐用、易于加工和成本低廉等优点。
本设计方案旨在提供一种创新的泡沫模具产品设计方案,满足客户的需求,提高生产效率和质量。
二、项目需求分析1. 功能需求:根据客户要求,设计一种多功能的泡沫模具,能够适用于不同形状和尺寸的产品。
2. 物理需求:模具应具备一定的强度和稳定性,以确保模具在使用过程中不变形、不破裂。
3. 生产需求:模具的生产过程应高效、环保,并且能够大批量生产以满足市场需求。
4. 成本需求:模具的生产成本应控制在合理范围内,使其具有竞争力。
三、设计方案鉴于以上需求分析,我们提出以下设计方案:1. 材料选择:选择高密度泡沫材料作为模具的主要材料,具有轻便、耐用和隔热等特性。
2. 结构设计:采用模块化设计,使模具可以快速组装和拆卸,以适应不同形状和尺寸的产品需求。
3. 强度优化:通过对模具的内部结构进行优化设计,提高其强度和稳定性,以防止变形和破裂。
4. 加工技术:采用先进的数控加工技术,提高生产效率,并保证模具的精度和质量。
5. 环保性考虑:在模具的生产过程中,采用环保的生产工艺和材料,减少对环境的影响。
6. 成本控制:在材料选择和加工工艺上进行合理的控制,降低生产成本,使产品具有竞争力。
四、实施计划1. 阶段一:进行需求调研和材料筛选,确定模具的基本设计方案。
2. 阶段二:制定详细的设计方案,包括结构设计、加工工艺和环保考虑等。
3. 阶段三:制造样品模具进行测试和优化,确保设计方案的可行性和稳定性。
4. 阶段四:扩大生产规模,提高生产效率,并进行市场推广。
五、预期效果与成果评估1. 预期效果:设计方案的实施将使得泡沫模具具备更好的适应性、强度和稳定性,提高生产效率和产品质量。
2. 成果评估:根据客户的反馈和市场份额的增长来评估设计方案的实施效果和经济效益。
六、风险与对策1. 技术风险:可能遇到材料性能不符合预期、结构设计困难等问题,需密切跟踪技术发展和进行技术优化。
《发泡成型模具》课件
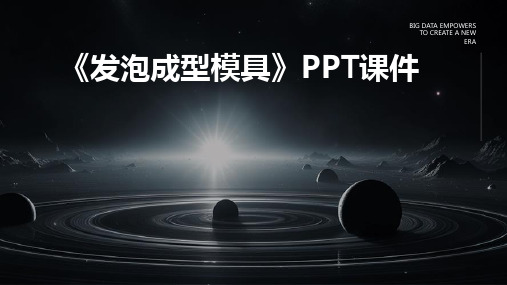
05
发泡成型模具案例分析
BIG DATA EMPOWERS TO CREATE A NEW
ERA
案例一:某品牌汽车座椅发泡模具设计
总结词
汽车座椅发泡模具设计
详细描述
介绍某品牌汽车座椅发泡模具的设计理念、结构特点、材料选择以及制造工艺流程,重点阐述模具设计对座椅性 能和品质的影响。
案例二:某品牌鞋底发泡模具制造工艺
温度控制
根据生产需要,将模具温度调整到适宜范围 ,以获得最佳的发泡效果。
冷却与脱模
确保模具在充分冷却后进行脱模,以避免产 品变形或损坏。
常见问题与解决方案
填充不均
表面粗糙
调整物料填充速度和流量,确保均匀填充 。
检查模具温度和物料温度,确保两者匹配 ,避免表面粗糙。
产品变形
模具损坏
优化冷却系统,使产品均匀冷却,防止变 形。
BIG DATA EMPOWERS TO CREATE A NEW ERA
04
发泡成型模具的发展趋势与展望
技术创新与进步
01
3D打印技术的应用
02
新型材料的应用
03
智能化技术的引入
通过3D打印技术,实现模具的快 速原型制造,缩短产品开发周期 。
采用高强度、轻质、耐高温的新 型材料,提高模具的使用寿命和 性能。
建筑领域
发泡成型模具可用于生产建筑保温材 料、装饰材料等,具有保温、隔热、 隔音、美观等优点。
包装领域
发泡成型模具可用于生产包装材料、 缓冲材料等,具有轻便、环保、耐用 等优点。
02
发泡成型模具的设计与制造
BIG DATA EMPOWERS TO CREATE A NEW
ERA
发泡聚苯乙烯成型模具
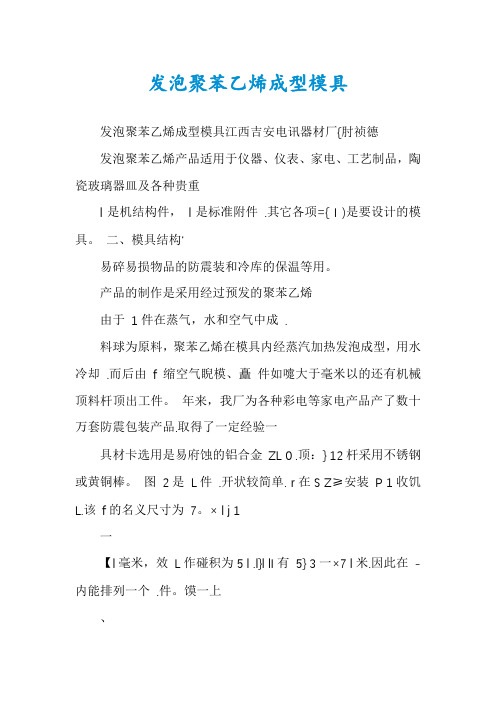
发泡聚苯乙烯成型模具发泡聚苯乙烯成型模具江西吉安电讯器材厂{肘祯德发泡聚苯乙烯产品适用于仪器、仪表、家电、工艺制品,陶瓷玻璃器皿及各种贵重l是机结构件,l是标准附件 .其它各项={ I )是要设计的模具。
二、模具结构‘易碎易损物品的防震装和冷库的保温等用。
产品的制作是采用经过预发的聚苯乙烯由于1件在蒸气,水和空气中成 .料球为原料,聚苯乙烯在模具内经蒸汽加热发泡成型,用水冷却 .而后由f缩空气睨模、矗件如嚏大于毫米以的还有机械顶料杆顶出工件。
年来,我厂为各种彩电等家电产品产了数十万套防震包装产品.取得了一定经验一具材卡选用是易府蚀的铝合金ZL 0 .顶:} 12杆采用不锈钢或黄铜棒。
图2是L件 .开状较简单. r在S Z≥安装P 1收饥L.该f的名义尺寸为7。
× l j 1一【l毫米,效L作碰积为5 l .l}l lI有5} 3一×7 l米.因此在-内能排列一个 .件。
馍一上、模具工艺要求聚苯乙烯发泡成型机.不象注塑成型机那样技工件重量尺寸大小选用适当的设备.而发泡聚苯乙烯模是按设备给定的组合尺、l设计j‘米的奠l I. I u刘l l2、架3.芯模框l组成一个封闭的宅问。
料3枪口l把料l满后、卡枪口天闭 .由蒸I}进:}气管9进汽加热熔接成型。
腔模6、芯板u和模芯l, I上有气隙 .使蒸气能通过进入2 J1内。
图1中项l、2, ', 5、H、I 5 l 、为l便于加工,省时和不受设备大小的『制.我J采用钉体拼装式模具。
图3中模芯L左右各二件 .模芯1四件,分型板 1 2 l二件均?f芯板l I I l I芯f。
生产时与戊 c !芯艇1连接。
r Iq模芯1,顶出杆7和 .{纠I l .复位蚪簧装在腔模上 .这二个腔模装在:I【为卡、{ 成( !接. .f I II均' j :时腔连l1排污Ⅱ 2腔模框3框架1顶板5进 . . . . .气管6腔模7顶料杆和弹簧8冷却水管 . . .9进气管 . 1 .枪口l .板 1 .芯O料1芯2模訇:{43 U1. 3志稹稚1. 4模芯1. 5原料粒1. 6分型板(具工业1 9‘模9 0. N O.2总1 8 0维普资讯3◇ O一0望、8――:圈圈目囹0 t . 。
PVC与聚氨酯发泡模具设计

PVC与聚氨酯发泡模具设计PVC(聚氯乙烯)与聚氨酯都是常见的材料,广泛用于模具制造。
在设计PVC和聚氨酯发泡模具时,需要考虑材料特性、模具结构和制造工艺等因素。
下面将详细介绍PVC和聚氨酯发泡模具设计的一些关键考虑因素。
1.PVC发泡模具设计:PVC是一种热塑性塑料,具有良好的可加工性和成型性。
在制造PVC发泡模具时,需要注意以下几点:(1)高温耐受性:PVC在加热融化过程中需要承受较高的温度。
因此,模具的材料选择和设计必须能够耐受高温。
(2)冷却系统设计:PVC发泡过程中需要快速冷却,以保证产品形状的稳定性。
模具应考虑冷却水系统的设计,以加速冷却过程。
(3)材料选择:模具材料应具有较好的耐高温性能,并且具有较好的耐磨性,以确保模具的长期使用寿命。
2.聚氨酯发泡模具设计:聚氨酯是一种合成材料,具有良好的耐磨性和高强度。
在制造聚氨酯发泡模具时,需要考虑以下几点:(1)耐腐蚀性:聚氨酯发泡时需要使用一些化学药剂,这些药剂可能对模具材料产生腐蚀作用。
因此,模具材料选择应具有较好的耐腐蚀性。
(2)高强度设计:聚氨酯发泡时需要较高的压力,以确保发泡成型过程中产生的气泡可以均匀分布在产品中。
因此,模具的结构设计应具有足够的强度,以承受高压力。
(3)润滑剂:聚氨酯泡沫的发泡需要使用润滑剂,以减少摩擦力和摩擦热。
模具的设计应考虑润滑剂的使用和清洁问题。
以上是关于PVC和聚氨酯发泡模具设计的一些考虑因素。
模具设计需要综合考虑材料特性、工艺要求和产品要求,以确保模具的质量和长期可靠性。
除了上述因素外,设计师还需要根据具体的产品要求和制造工艺进行更多的细节设计。
发泡模具设计详解

发泡模具设计详解发泡模具是一种用于制造发泡产品的模具,广泛应用于各个行业。
通过设计合理的发泡模具,可以大大提高产品质量和生产效率。
本文将详细介绍发泡模具的设计要点和设计流程。
发泡模具的设计要点如下:1.产品尺寸:首先需要根据产品的尺寸要求确定发泡模具的尺寸,包括长度、宽度和高度等。
同时需要考虑产品的形状和结构,以及模具的分型线和倒角等。
2.模具材料:选择合理的模具材料非常重要。
常见的模具材料有铝合金、钢材和塑料等。
根据产品的要求和生产数量,选择不同的模具材料,以实现最佳的生产效果和成本控制。
3.模具结构:合理的模具结构可以提高生产效率和产品质量。
通常,发泡模具包括上模和下模两部分。
下模用来容纳产品的发泡,上模用来形成产品的外形和结构。
模具还需要考虑产品的脱模方式和气路设计,以确保产品质量。
4.模具制造:根据设计图纸,进行模具的制造工艺。
制造过程包括数控加工、车削、铣削和电火花等。
十分严格的制造工艺可以保证模具的精度和质量。
5.模具上手操作:在使用模具之前,需要对模具进行调试和上手操作。
这包括安装模具、调整模具的开合间隙和压力等。
只有合理的上手操作,才能保证模具生产出合格的产品。
1.产品要求分析:了解产品的尺寸要求、用途和特殊要求等。
根据产品要求,确定合理的模具尺寸和材料。
2.模具结构设计:设计模具的基本结构,包括上模和下模的形状和尺寸。
需要考虑产品的形状、结构和脱模要求等。
同时,要注意模具之间的分型线和倒角等。
3.模具零件设计:根据模具结构设计,细化各个模具零件的形状和尺寸。
这包括上模和下模的芯轴、拉杆、动模板和定模板等。
4.模具图纸设计:根据模具结构和零件设计,绘制详细的模具图纸。
图纸需要包括模具的三视图、分解图和装配图等。
5.模具制造:根据设计图纸,进行模具的制造。
制造过程中需要进行数控加工、车削、铣削和电火花等制造工艺。
6.模具调试:在模具制造完成后,需要对模具进行调试和上手操作。
调试包括安装模具、调整模具的开合间隙和压力等。
发泡成型模具

1.3.2普通注射机低发泡注射成型
在普通注射机上也可以进行低发泡注射成型。一般 有两种方法:一是减量注射法,二是瞬间开模注射 法。两种方法都必须对原有模具进行适当改造。改 造的内容如下:
(1)增加排气通路 把原来分型面上的排气槽增加 ,把通过拼缝和推杆排气的气隙增大。
(2)增加推杆数量 在试模后观察,发现有推杆处 受力过大的现象时,再适当增加推杆数量,或加大 推杆直径。
(3)加强冷却水流量。
2、模具设计
2.1模具制造材料
2.2模具分型面选择
分型面尽量选用平面、避用曲面 结构力求简单、易于制模和操作方便 便于设置加料口 便于取模 尽量不影响模样形状和尺寸精度
分模线:根据产品的最大外形做分模线,再做压 料,分出凹凸模腔,分析加工工艺,方便加工,打
气芯、 抛光等;不好做到位的地方做拼块,拼块最好 能做限位,方便安装;产品有倒扣的、侧面有穿孔的 ,做滑块抽芯;根据凹、凸模腔,做模具壁厚,根据 客户要求的壁厚来做,把型腔背面多余的料去掉,尽 量做到壁厚均匀,背面尽量做脱模斜度,方便木样在 翻砂时好脱模,做好造型后,考虑顶杆、料枪位置、 背面的加强筋、支柱位置,可以先做2D排模图,设计
2.3加料口
料枪孔,比料枪嘴大0.2~0.5mm之间
2.4模具壁厚
EPP模具的壁厚一般在15 mm左右; EPS模具、EPO模具的壁厚在8~10 mm之间; EPE模具的壁厚一般在15 mm,除客户特别说明要求。
2.5泡沫塑料收缩率与尺寸精 度
缩水: 一般EPS模具材料的缩水为0.3%,倍率低的客户要求
提供0.25%、0.2%等; EPO材料一般在0.9%~1.0%之间; EPP、EPE材料根据倍率的不同,缩水也不同; EPP、EPE材料又分JSP/KANEKA原料等,4、∮6、∮8、∮10、∮12等规格,有条 型式和针式两种类型。
挤出发泡模具设计及制造
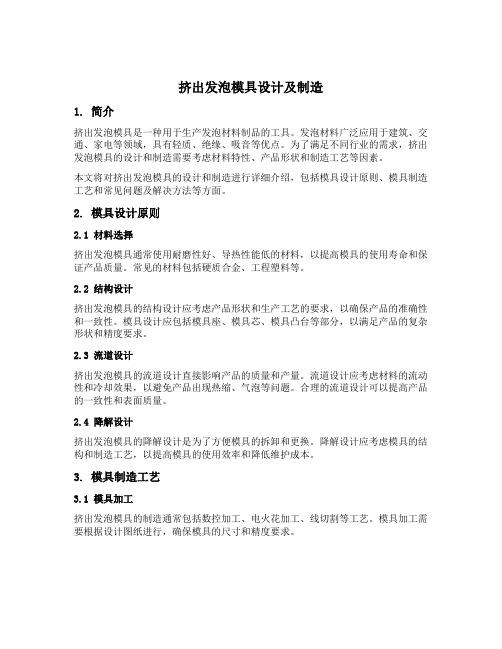
挤出发泡模具设计及制造1. 简介挤出发泡模具是一种用于生产发泡材料制品的工具。
发泡材料广泛应用于建筑、交通、家电等领域,具有轻质、绝缘、吸音等优点。
为了满足不同行业的需求,挤出发泡模具的设计和制造需要考虑材料特性、产品形状和制造工艺等因素。
本文将对挤出发泡模具的设计和制造进行详细介绍,包括模具设计原则、模具制造工艺和常见问题及解决方法等方面。
2. 模具设计原则2.1 材料选择挤出发泡模具通常使用耐磨性好、导热性能低的材料,以提高模具的使用寿命和保证产品质量。
常见的材料包括硬质合金、工程塑料等。
2.2 结构设计挤出发泡模具的结构设计应考虑产品形状和生产工艺的要求,以确保产品的准确性和一致性。
模具设计应包括模具座、模具芯、模具凸台等部分,以满足产品的复杂形状和精度要求。
2.3 流道设计挤出发泡模具的流道设计直接影响产品的质量和产量。
流道设计应考虑材料的流动性和冷却效果,以避免产品出现热缩、气泡等问题。
合理的流道设计可以提高产品的一致性和表面质量。
2.4 降解设计挤出发泡模具的降解设计是为了方便模具的拆卸和更换。
降解设计应考虑模具的结构和制造工艺,以提高模具的使用效率和降低维护成本。
3. 模具制造工艺3.1 模具加工挤出发泡模具的制造通常包括数控加工、电火花加工、线切割等工艺。
模具加工需要根据设计图纸进行,确保模具的尺寸和精度要求。
3.2 表面处理挤出发泡模具的表面处理可以提高模具的耐磨性和防腐性。
常见的表面处理方法包括镀铬、喷涂、电镀等。
3.3 装配调试挤出发泡模具的装配调试是确保模具正常运行的重要环节。
装配调试包括模具部件的安装、调整和测试等步骤,以保证模具的稳定性和性能。
4. 常见问题及解决方法4.1 模具磨损模具在使用过程中会出现磨损,影响产品的质量和产量。
解决模具磨损问题的方法包括定期维护、更换磨损部件等。
4.2 模具温度过高模具温度过高会导致产品收缩不均匀、表面粗糙等问题。
解决模具温度过高问题的方法包括增加冷却系统、调整挤出温度等。
SRIM发泡模具设计技术在汽车内饰件中的应用分析
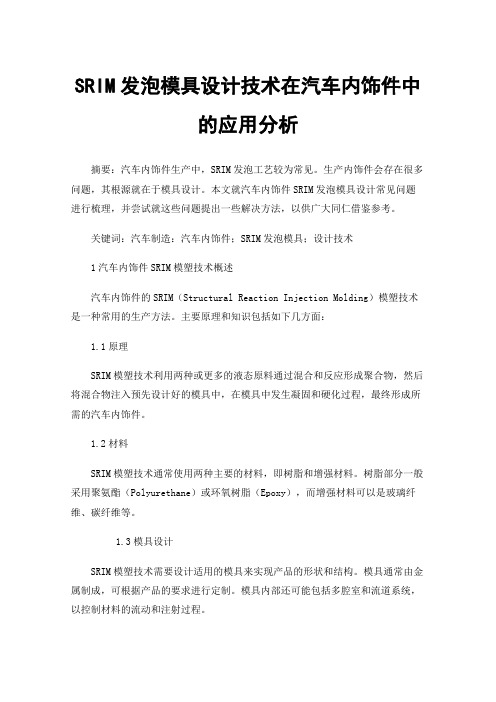
SRIM发泡模具设计技术在汽车内饰件中的应用分析摘要:汽车内饰件生产中,SRIM发泡工艺较为常见。
生产内饰件会存在很多问题,其根源就在于模具设计。
本文就汽车内饰件SRIM发泡模具设计常见问题进行梳理,并尝试就这些问题提出一些解决方法,以供广大同仁借鉴参考。
关键词:汽车制造:汽车内饰件;SRIM发泡模具;设计技术1汽车内饰件SRIM模塑技术概述汽车内饰件的SRIM(Structural Reaction Injection Molding)模塑技术是一种常用的生产方法。
主要原理和知识包括如下几方面:1.1原理SRIM模塑技术利用两种或更多的液态原料通过混合和反应形成聚合物,然后将混合物注入预先设计好的模具中,在模具中发生凝固和硬化过程,最终形成所需的汽车内饰件。
1.2材料SRIM模塑技术通常使用两种主要的材料,即树脂和增强材料。
树脂部分一般采用聚氨酯(Polyurethane)或环氧树脂(Epoxy),而增强材料可以是玻璃纤维、碳纤维等。
1.3模具设计SRIM模塑技术需要设计适用的模具来实现产品的形状和结构。
模具通常由金属制成,可根据产品的要求进行定制。
模具内部还可能包括多腔室和流道系统,以控制材料的流动和注射过程。
1.4制造过程(1)前处理。
材料准备、模具准备和表面处理等;(2)混合注射。
树脂和增强材料按照一定比例混合,然后通过喷头或喷嘴注入模具中;(3)充填。
混合物在模具中充填,填满所需的形状和结构;(4)凝固和硬化。
混合物在模具中发生凝固和硬化过程,形成产品的实体部分;(5)取出和后处理:将成品从模具中取出,并进行去除余料、修整、清洁和表面处理等工序;(6)优势。
SRIM模塑技术能够生产出具有较高强度、刚性和耐用性的汽车内饰件。
此外,它还可以实现复杂的几何形状、薄壁结构和一体成型,提高生产效率和产品质量。
2 SRIM制件成型缺点与控制措施2.1气泡与气穴缺陷与控制(1)缺陷问题第一,气泡缺陷。
第17章 发泡成型工艺与模具设计

(3) 按密度或发泡倍率分类 泡沫塑料按其密度或发泡倍率可分为低
发泡、中发泡与高发泡三种类型。
3
17.1 发泡成型工艺
1.泡沫塑料的特性 泡沫塑料的品种很多,性能也多种多样,因为它含有大量气泡,因此 具有以下共同的特性:
(1) 具有吸收冲击载荷的能力 泡沫塑料受到冲击载荷时,泡沫中的 气体通过滞流和压缩,使外来作用的能量被消耗、散逸。泡体以较小 的负加速度,逐步终止冲击载荷。
R(t) =KDC0 tn (3) 气泡的稳定和固化过程
5
17.1 发泡成型工艺
17.1.2 可发性聚苯乙烯的制备 聚苯乙烯泡沫塑料成型方法主要有模压法、可发性珠粒法和挤出发 泡法。 目前大量使用的方法是可发性珠粒法和挤出发泡法,我国主要使用 可发性珠粒法。
(1) 预发泡 预发泡分为间隙法和连续法两种 (2) 熟化
(2) 隔热性能好。
4
17.1 发泡成型工艺
17.1.1 泡沫塑料的成型原理 1.气发泡沫的成型过程 (1) 泡沫的气泡核形成阶段 (2) 泡沫的气泡核增长 (3) 泡沫的稳定固化 2.成型机理 (1) 气泡核的形成 形成气泡核必须满足以下条件:
1) 作为泡沫塑料基体的聚合物,其分子架中应有足够量的自由 空间,以供聚集足够量的发泡剂,形成气泡核。 2) 发泡剂一般采用低沸点的有机液体 3) 含有低沸点发泡剂的聚合物不应在大气中久放。 (2) 气泡的膨胀过程 气泡增长的近似计算式如下:
高等教育出版社 高等教育电子音像出版社
塑料成型工艺与模具设计电子教案
第17章 发泡成型工艺与模具设计
1 .
第17章 发泡成型工艺与模具设计
17.1 发泡成型工艺 17.2 发泡成型模具设计
2
17.1 发泡成型工艺
四锥聚氨酯硬质泡沫发泡模的设计
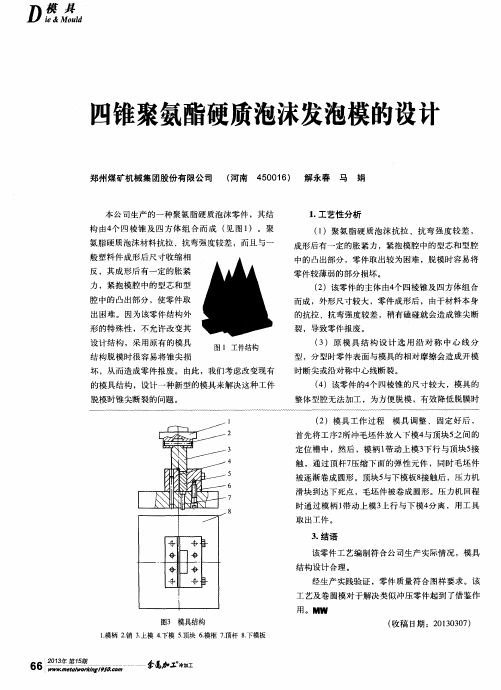
坏 ,从而造成零件报废。由此 ,我们考虑改变现有 的模具结构 ,设计一种新型的模具 来解决这种工件 脱模时锥尖断裂的问题 。
一
首 先 将 工 序2 所 冲毛 坯 件 放 入 下 模 4 与顶块5 之 间的
‘ \
\
—
/
定位槽中 ,然后 ,模柄 1 带动上模3 下行与顶块5 接
触 ,通 过 顶 杆 7 压 缩 下 面 的 弹 性 元件 ,同时 毛 坯 件
图3 型芯l 2
保证两个锥齿轮 的运动 灵活 ,本 机构特 设置了3 个
轴 向推 力轴 承4 。 模 具 工 作 时 ,因加 料 过 程 时 间 短 ,要 求 动 作 准
确 、迅速 ,但堵头是采用手工安装操作 ,堵头与盖 板之间的配合间隙小则不易装入 ,而配合 间隙太大
又 会 进料 产 生 飞 边 ,从 而 导 致 下一 次 装料 时 很 难 取
ห้องสมุดไป่ตู้
匡 /
\
\
被 逐 渐卷 成 圆形 。顶块 5 与 下 模板 8 接 触后 ,压 力机 滑 块 到达 下 死 点 ,毛 坯件 被 卷成 圆形 。 压 力机 回程 时通过模柄 1 带动上模3 上 行 与 下 模4 分 离 ,用 工具
/
取 出工 件 。
岳 每 一 }
杏 杏
形 和 一 个 正 方 彤 组 成 , 角
构的型腔设计。镶拼结构的型腔设计不仅有利于排 气 ,更有利于零件尖部尺寸成形 。
度关 系较复杂 ,其加工质 量的好坏直接关 系到该模
2 . 模具 结构
( 1 )模具结 构及加工难 点 综合考虑 了该 工
件 材 料 的机 械 性 能 、成 形 工艺 特 性 及 外形 结 构 设 计
发泡模具设计详解

一、发泡模成型机的原理1、发泡原材料的种类:EPS,EPP,EPE,EPO等。
2、成型原理:合模,加料,利用蒸汽加热成型,再冷却,脱模。
二、EPS模具总体结构根据机型的种类来设计模具,与机台配套。
1、一体模:台湾机、方圆机、等机台没有标准水箱,必须根据产品排模来定水箱(蒸汽室),又叫一体模。
2、三片式模具:都具有三片板:凸模板、凹模板、枪板凸模板来固定连接凸模型腔;凹模板用来固定连接凹模型腔;枪板也叫做后封板、背板、主要装顶杆套和料枪。
3、压料:为凸模与凹模配合,方便预开加料成型而设计的一种结构,起到预开加料时不漏料。
根据水箱的合模台阶、模板来计算;压料有离空和没有离空两种。
没有离空的,凹凸模的压料相同;有离空的,凹模压料加离空等于凸模压料,凹模压料不少于10 mm。
4、法兰边:也就是凹模与凹模板连接处的空间,方便安装螺丝钉。
根据水箱合模台阶和模板来定,一般做到15 mm左右为宜,不能少于10mm;还有一种,从模板下面往上面套,叫反托,反托高度根据模板的厚度来定,如库尔特机型,一般采用反托式,日本机型一般采用正面安装,有法兰边。
5、壁厚:EPP模具的壁厚一般在15 mm左右;EPS模具、EPO模具的壁厚在8~10 mm之间;EPE模具的壁厚一般在15 mm,除客户特别说明要求。
6、缩水:一般EPS模具材料的缩水为0.3%,倍率低的客户要求提供0.25%、0.2%等;EPO材料一般在0.9%~1.0%之间;EPP、EPE材料根据倍率的不同,缩水也不同;EPP、EPE材料又分JSP/KANEKA原料等,缩水又不同7、气眼:∮4、∮6、∮8、∮10、∮12等规格,有条型式和针式两种类型。
EPS原材料模具,采用针式气眼比较多,EPP、EPE等原材料模具采用条型式(平面)比较多、侧面一般用针式;气芯按材质分,有铝气芯,铜气芯、不锈钢气芯,常用的是铝气芯。
针孔:一些死角地方,加针孔在∮0.6~0.8mm之间。
发泡模具设计详解
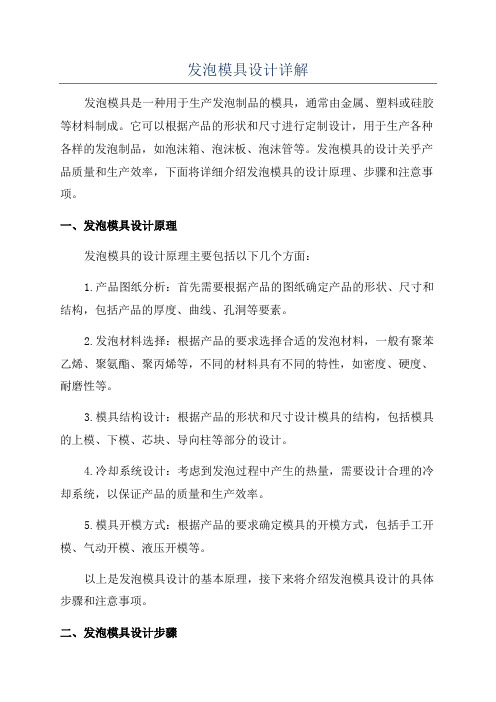
发泡模具设计详解发泡模具是一种用于生产发泡制品的模具,通常由金属、塑料或硅胶等材料制成。
它可以根据产品的形状和尺寸进行定制设计,用于生产各种各样的发泡制品,如泡沫箱、泡沫板、泡沫管等。
发泡模具的设计关乎产品质量和生产效率,下面将详细介绍发泡模具的设计原理、步骤和注意事项。
一、发泡模具设计原理发泡模具的设计原理主要包括以下几个方面:1.产品图纸分析:首先需要根据产品的图纸确定产品的形状、尺寸和结构,包括产品的厚度、曲线、孔洞等要素。
2.发泡材料选择:根据产品的要求选择合适的发泡材料,一般有聚苯乙烯、聚氨酯、聚丙烯等,不同的材料具有不同的特性,如密度、硬度、耐磨性等。
3.模具结构设计:根据产品的形状和尺寸设计模具的结构,包括模具的上模、下模、芯块、导向柱等部分的设计。
4.冷却系统设计:考虑到发泡过程中产生的热量,需要设计合理的冷却系统,以保证产品的质量和生产效率。
5.模具开模方式:根据产品的要求确定模具的开模方式,包括手工开模、气动开模、液压开模等。
以上是发泡模具设计的基本原理,接下来将介绍发泡模具设计的具体步骤和注意事项。
二、发泡模具设计步骤1.产品分析:根据产品的图纸确定产品的形状、尺寸和结构,分析产品的特点和要求,确定发泡模具的设计方向。
2.模具结构设计:根据产品的形状和尺寸设计模具的结构,包括模具的上模、下模、芯块、导向柱等部分的设计,确保模具的稳定性和精度。
3.模具零部件设计:根据模具结构设计细化设计各个零部件,包括上模板、下模板、芯块、导向柱等部件的设计。
4.冷却系统设计:设计模具的冷却系统,以保证模具在生产过程中不发热变形,同时可以提高生产效率和产品质量。
5.模具装配:将各个零部件按照设计图纸进行装配,保证模具的结构完整和稳定。
6.试模调试:进行试模调试,检查模具的精度和稳定性,对模具进行必要的调整和优化,确保模具可以正常生产。
以上是发泡模具设计的基本步骤,设计师在进行发泡模具设计时需要认真执行每个步骤,确保设计的质量和准确性。
发泡模具排气装置设计

2.3 排气孔排气
排气孔形状:排 气孔设计形式多 种多样,但既要 有利于排气,又 要便于清理气孔, 常见的排气孔有 如下三种结构, 其中结构C最理 想。
2.2 排气槽排气
注射模具的排气槽应设置在塑料流动 的末端,一般常开设在分型面型腔一 侧,排气槽深可取,宽,以塑料不进 入排气槽为宜,其出口不要对着操作 工人,以防熔融塑料喷出造成事故, 有的厂推荐将分型面上的排气槽做成 弯形且逐步增宽,以降低塑料溢出的 可能。小型制件的排气量不大,如排 气点正好在分型面上,一般可以利用 分型面闭合时的微小间隙排气。
CLICK HERE TO ADD A TITLE
泡模具排气系统设计
此处添加副标题
冯
加
和
2
0
16Biblioteka 0913
1、概述
1、概述
在设计发泡成型模具时必须考虑排气问题。如果模具型腔内的气体不能 顺利排出,将造成制品的气泡、疏松、冲模不满、焊接不牢、制件表面 发乌或者在注射时由于气体被压缩所产生的高温制品底部碳化、烧焦, 而且型腔内气体被压缩产生的反压力会降低冲模速度,影响注射周期和 产品质量。
PM-35排气钢是一种优质透气性钢材,内部由微细的小孔相连构成,使空气 或任何气体能顺利渗透及穿过。因此,于注塑模具之适当位置镶上PM-35 排气钢,由气体所形成的注塑问题,可以完全清除,使成型加工更加完美。
2.3 排气钢排气
特性:1.降低注射压力,减少成型和保压时间。2.降低和消除成型件的内应力, 防止产品的变形和曲翘。3.表面皮纹的塑料零件,由于高温高压产生的亮光 皮纹,能解决要求亚光的表面。4.由于模具分型面的紧密配合,可以解决开模 困难等情况。解决通常利用顶针、镶件等无法提供足够表面区域以容纳可 能产生的大量气体等诸多问题,避免了利用分型面或其他排气系统而产生的 飞边及其他瑕疵。5.可使由于浇口偏位、壁厚不匀、壁薄产品等较难成型问 题得到解决和缓解。6.由于成型材料高温产生的气体和模具腔内快速聚压产 生的烧焦、流痕、缺料、吸气造成的零件变形等缺陷能得到充分解决。7.提 高成型生产效率,节约生产成本。
- 1、下载文档前请自行甄别文档内容的完整性,平台不提供额外的编辑、内容补充、找答案等附加服务。
- 2、"仅部分预览"的文档,不可在线预览部分如存在完整性等问题,可反馈申请退款(可完整预览的文档不适用该条件!)。
- 3、如文档侵犯您的权益,请联系客服反馈,我们会尽快为您处理(人工客服工作时间:9:00-18:30)。
发泡模具设计详解 The latest revision on November 22, 2020
一、发泡模成型机的原理
1、发泡原材料的种类:EPS,EPP,EPE,EPO等。
2、成型原理:合模,加料,利用蒸汽加热成型,再冷却,脱模。
二、EPS模具总体结构
根据机型的种类来设计模具,与机台配套。
1、一体模:
台湾机、方圆机、等机台没有标准水箱,必须根据产品排模来定水箱(蒸汽室),又叫一体模。
2、三片式模具:都具有三片板:凸模板、凹模板、枪板
凸模板来固定连接凸模型腔;
凹模板用来固定连接凹模型腔;
枪板也叫做后封板、背板、主要装顶杆套和料枪。
3、压料:为凸模与凹模配合,方便预开加料成型而设计的一种结构,起到预开加料时不漏料。
根据水箱的合模台阶、模板来计算;
压料有离空和没有离空两种。
没有离空的,凹凸模的压料相同;
有离空的,凹模压料加离空等于凸模压料,凹模压料不少于10 mm。
4、法兰边:也就是凹模与凹模板连接处的空间,方便安装螺丝钉。
根据水箱合模台阶和模板来定,一般做到15 mm左右为宜,不能少于10mm;
还有一种,从模板下面往上面套,叫反托,反托高度根据模板的厚度来定,如库尔特机型,一般采
用反托式,日本机型一般采用正面安装,有法兰边。
5、壁厚:EPP模具的壁厚一般在15 mm左右;
EPS模具、EPO模具的壁厚在8~10 mm之间;
EPE模具的壁厚一般在15 mm,除客户特别说明要求。
6、缩水:一般EPS模具材料的缩水为0.3%,倍率低的客户要求提供0.25%、0.2%等;
EPO材料一般在0.9%~1.0%之间;
EPP、EPE材料根据倍率的不同,缩水也不同;
EPP、EPE材料又分JSP/KANEKA原料等,缩水又不同
7、气眼:∮4、∮6、∮8、∮10、∮12等规格,有条型式和针式两种类型。
EPS原材料模具,采用针式气眼比较多,
EPP、EPE等原材料模具采用条型式(平面)比较多、侧面一般用针式;
气芯按材质分,有铝气芯,铜气芯、不锈钢气芯,常用的是铝气芯。
针孔:一些死角地方,加针孔在∮0.6~0.8mm之间。
8、打气眼:先用钻头打好孔,一般钻头选用比气眼小0.3~0.4 mm,气芯分布均匀。
EPS一般采用气芯与气芯为25×25间距;
EPP、EPE一般采用气芯与气芯为20×20间距,除客户特别要求。
气芯要敲平,气芯必须分三次敲到位,一次敲平的气芯松动,气芯旁边不能有月牙形,抛光把气芯和刀纹抛平,使模具表面光亮、平滑
9、分模线:根据产品的最大外形做分模线,再做压料,分出凹凸模腔,分析加工工艺,方便加工,打
气芯、抛光等;不好做到位的地方做拼块,拼块最好能做限位,方便安装;产品有倒扣的、侧面有穿孔的,做滑块抽芯;根据凹、凸模腔,做模具壁厚,根据客户要求的壁厚来做,把型腔背面多余的料去掉,尽量做到壁厚均匀,背面尽量做脱模斜度,方便木样在翻砂时好脱模,做好造型后,考虑顶杆、料枪位置、背面的加强筋、支柱位置,可以先做2D排模图,设计好顶杆、料枪位置、支柱位置。
10、字牌:按图纸要求制作。
11、离模顶:凹模板与凸模板之间有离空的必须安装离模顶,可用∮30铝棒做成,用螺丝固定,根据离模空间高度来做,分布均匀,差不多在200~250mm的间距为宜,安装到凹模板上。
12、定位销:根据客户要求,安装定位销,方便模具在合模时起到导向作用,防模具撞坏。
13、锁模系统:国外模具,爱仑巴赫机型,常配有模具锁模系统,把凸模板与凹模板固定起来,方便吊装,安装好了再打开锁模杆,国内模具一般不用。
14、料枪:料枪孔,比料枪嘴大0.2~0.5mm之间
15、顶杆:固定规格的顶杆
16、支柱:分凸模支柱和凹模支柱,根据机台的水箱高度来制作,支柱一般排布均匀,间距在150mm
左右,EPP模具间距可以小点,EPS模具间距可以大点,尽量不要超过节200mm,支柱可以用紧钉螺丝和平基、内、外六角螺丝紧固,看模具结构来定,板的厚度;如果支柱与枪板连接用螺丝的,枪板已打了通孔,支柱要有密封圈防漏气,螺丝尽可能的用大螺丝,如M10 mm。
17、水管:根据排模图,让开顶杆、料枪、支柱位来设计水管,水管上的喷头间距100~120 mm,尽量让水喷到模具表面的每个地方,完全冷却,模具很高的,可以加小水管,凸模支柱的排布要让开水管位置,防碰撞水管,水管要固定到枪板上,进水接头按机台资料做。
三.发泡成型机的种类:国内大部分为库尔特日本戴生,日本积水,方圆机、巨馨机、国外大部分为库尔特、爱仑巴赫。
3、新产品仿真方案
三、密度概念、公制、英制、密度换算、体积、重量
1、公制:长度单位、质量单位、、密度单位
体积单位:1升(L)=1立方分米
1毫升(mL)=1立方厘米=1cc
1立方米=1000立方分米(升)
2、英制:长度单位:inft
质量单位:ibs=ib=pound(磅)
密度单位:PCF磅/英尺3
长度单位:1 英寸in=2.5400 厘米
1 英尺ft=12英寸=0.3048 米
重量单位:1 磅=0.4536 千克
重量:M(g)=p(kg/m3)*[L*W*H(mm)]*10-6
3、发泡倍率
倍率=单位体积水的重量/单位体积泡塑颗粒的重量水的密度是1000kg/立方米
1000kg=1吨
4、力的单位:
Kgf千克力
Kgf/cm2 千克力/平方厘米
1MPa=145磅力/英寸2(psi)=10.19(kgf/cm2)
1kgf/cm2=1.019bar
1kgf=9.807牛顿(N)。