发泡模具设计详解
第9章发泡成型模具

泡沫塑料是以树脂为基础内部含有无数微小气孔的塑料,又 称为多孔性塑料。采用不同的树脂和发泡方法可制成性能各 异的泡沫塑料。它具有质轻、防震、防潮、隔热与吸音等优 点,在塑料工业中占有特殊的地位。 泡沫塑料的发泡方法大致有三种:物理发泡法、化学发泡法、 机械发泡法。三种发泡方法的共同点是:待发泡聚合物或复 合物必须处于液态或粘度在一定范围内的塑性状态;泡孔的 形成是依靠添加能产生泡沫结构的固体、液体或气体发泡剂, 或者几种物质混合的发泡剂。针对某种聚合物,应根据其性 质,选择适宜的发泡法与发泡剂,才能制成合格的泡沫塑料。
Hale Waihona Puke 9.4 低发泡注射成型模1.低发泡注射成型模具基本结构 低发泡注射成型模的基本结构与普通注射成型模具 基本相同,其设计方法也与注射成型模具极为类似。 由于发泡材料的物理性质与非发泡料材有所不同, 因此在个别部位的设计上有其特殊要求: (1)浇注系统 (2)型腔排气 (3)冷却系统 (4)脱模机构 (5)型腔数
图9-1 模压发泡成型模具 1-气孔 2-上气室 3-型芯 4-加料管
5-模框
6-下气室
②液压机直接通蒸汽发泡法适宜生产厚度较大的泡 沫板材。成型时常用气送法将粒料加入液压机上的 模具中。模具开有若干个0.1~O.4mm的通气孔(或 槽),当模具型腔装满预胀物后,直接通入O.1~ O.2MPa的蒸汽,并使温度升至11O℃左右,此时 模内预胀物膨胀并粘接成整体。关闭蒸汽,保持一 定时间(1~2min),通水冷却后脱模。此发泡法的优 点是塑化时间短、冷却定型快、塑件内珠粒熔接良 好、质量稳定、生产效率高,能实现机械化与自动 化生产,如图9-1(b)所示。
(2)挤出发泡成型法
挤出发泡成型法适宜生产片材和薄膜。图9-2所示为 可发性聚苯乙烯泡沫塑料纸的挤出吹塑过程。
泡沫模具产品设计方案模板
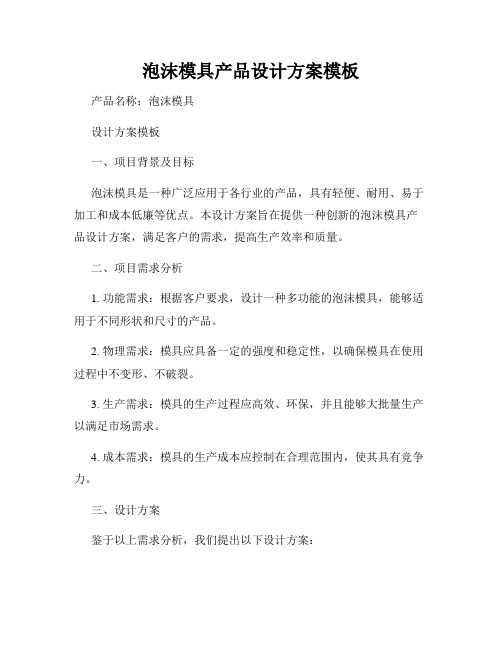
泡沫模具产品设计方案模板产品名称:泡沫模具设计方案模板一、项目背景及目标泡沫模具是一种广泛应用于各行业的产品,具有轻便、耐用、易于加工和成本低廉等优点。
本设计方案旨在提供一种创新的泡沫模具产品设计方案,满足客户的需求,提高生产效率和质量。
二、项目需求分析1. 功能需求:根据客户要求,设计一种多功能的泡沫模具,能够适用于不同形状和尺寸的产品。
2. 物理需求:模具应具备一定的强度和稳定性,以确保模具在使用过程中不变形、不破裂。
3. 生产需求:模具的生产过程应高效、环保,并且能够大批量生产以满足市场需求。
4. 成本需求:模具的生产成本应控制在合理范围内,使其具有竞争力。
三、设计方案鉴于以上需求分析,我们提出以下设计方案:1. 材料选择:选择高密度泡沫材料作为模具的主要材料,具有轻便、耐用和隔热等特性。
2. 结构设计:采用模块化设计,使模具可以快速组装和拆卸,以适应不同形状和尺寸的产品需求。
3. 强度优化:通过对模具的内部结构进行优化设计,提高其强度和稳定性,以防止变形和破裂。
4. 加工技术:采用先进的数控加工技术,提高生产效率,并保证模具的精度和质量。
5. 环保性考虑:在模具的生产过程中,采用环保的生产工艺和材料,减少对环境的影响。
6. 成本控制:在材料选择和加工工艺上进行合理的控制,降低生产成本,使产品具有竞争力。
四、实施计划1. 阶段一:进行需求调研和材料筛选,确定模具的基本设计方案。
2. 阶段二:制定详细的设计方案,包括结构设计、加工工艺和环保考虑等。
3. 阶段三:制造样品模具进行测试和优化,确保设计方案的可行性和稳定性。
4. 阶段四:扩大生产规模,提高生产效率,并进行市场推广。
五、预期效果与成果评估1. 预期效果:设计方案的实施将使得泡沫模具具备更好的适应性、强度和稳定性,提高生产效率和产品质量。
2. 成果评估:根据客户的反馈和市场份额的增长来评估设计方案的实施效果和经济效益。
六、风险与对策1. 技术风险:可能遇到材料性能不符合预期、结构设计困难等问题,需密切跟踪技术发展和进行技术优化。
发泡成型模具

• 1.2.2 图9-4所示为板材手动蒸箱压模,一次可成型三块 板材,模套由件5和件8组成,并通过件12连接。
图9-4 板材手动蒸箱压模 1-铰链螺栓2-螺母3-上模板4-隔板5-模套6-下模板 7-螺母8-模套组合件9-螺母10-销11-轴12-长螺栓
• 1.2.3 图9-5为包装 盒机动发泡模,使用卧 式泡沫塑料成型机。
• 气眼:∮4、∮6、∮8、∮10、 ∮12等规格,有条型式和针式两种类型 。
• 比较多E,PS原材料模具,采用针式气眼
• 式(平E面P)P、比E较PE多等、原侧材面料一模般具用采针用式条;型
•
气芯按材质分,有铝气芯,铜气 芯、不锈钢气芯,常用的是铝气芯。
•
针孔:一些死角地方,加针孔在 ∮0.6~0.8mm之间
•
打气眼:先用钻头打好孔,一般钻 头选用比气眼小0.3~0.4 mm,气芯分布
2.7气室结构、加强筋板、 压料
• 压料:为凸模与凹模配合,方便预 开加料成型而设计的一种结构,起到预
开加料时不漏料。
•
根据水箱的合模台阶、模板来计
算;
•
压料有离空和没有离空两种。没
有离空的,凹凸模的压料相同;
•
有离空的,凹模压料加离空等于
• 蒸汽加热模压法成型模具 和低发泡注射成型模
• 1.1 蒸汽加热模压法成型模具
• 按加热方式又分为蒸缸发泡和液压机直接通蒸汽发泡两种。
• 1.1.1 蒸缸发泡法适宜生产小型、薄壁与形状复杂的塑件 ,即将预胀物填满模具后放入蒸缸中,然后通蒸汽加热成型 。蒸汽压力与加热时间应视塑件大小与厚度而定,一般为 0.05~0.10MPa,10~50min。模内预胀物受热软化,经膨 胀互相熔接而成整体,冷却脱模即制得泡沫塑料产品。此法 所用模具简单,但工人劳动强度较大,难于实现机械与自动 化生产,如图图9-1(a)所示。
《发泡成型模具》课件
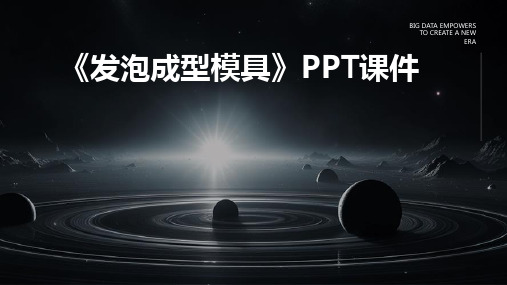
05
发泡成型模具案例分析
BIG DATA EMPOWERS TO CREATE A NEW
ERA
案例一:某品牌汽车座椅发泡模具设计
总结词
汽车座椅发泡模具设计
详细描述
介绍某品牌汽车座椅发泡模具的设计理念、结构特点、材料选择以及制造工艺流程,重点阐述模具设计对座椅性 能和品质的影响。
案例二:某品牌鞋底发泡模具制造工艺
温度控制
根据生产需要,将模具温度调整到适宜范围 ,以获得最佳的发泡效果。
冷却与脱模
确保模具在充分冷却后进行脱模,以避免产 品变形或损坏。
常见问题与解决方案
填充不均
表面粗糙
调整物料填充速度和流量,确保均匀填充 。
检查模具温度和物料温度,确保两者匹配 ,避免表面粗糙。
产品变形
模具损坏
优化冷却系统,使产品均匀冷却,防止变 形。
BIG DATA EMPOWERS TO CREATE A NEW ERA
04
发泡成型模具的发展趋势与展望
技术创新与进步
01
3D打印技术的应用
02
新型材料的应用
03
智能化技术的引入
通过3D打印技术,实现模具的快 速原型制造,缩短产品开发周期 。
采用高强度、轻质、耐高温的新 型材料,提高模具的使用寿命和 性能。
建筑领域
发泡成型模具可用于生产建筑保温材 料、装饰材料等,具有保温、隔热、 隔音、美观等优点。
包装领域
发泡成型模具可用于生产包装材料、 缓冲材料等,具有轻便、环保、耐用 等优点。
02
发泡成型模具的设计与制造
BIG DATA EMPOWERS TO CREATE A NEW
ERA
发泡聚苯乙烯成型模具
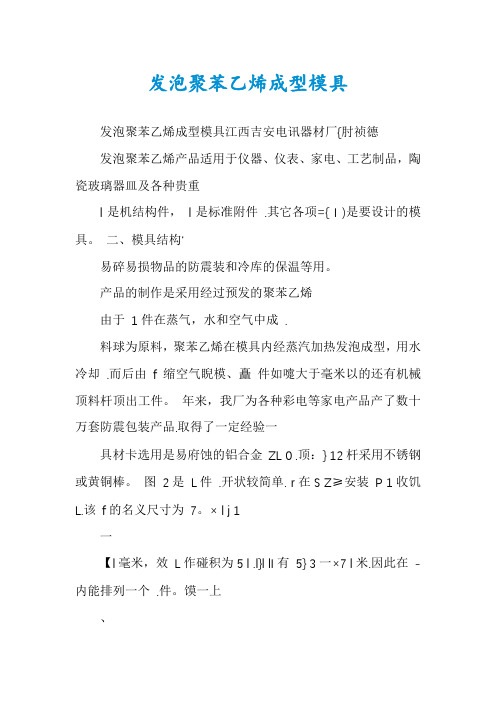
发泡聚苯乙烯成型模具发泡聚苯乙烯成型模具江西吉安电讯器材厂{肘祯德发泡聚苯乙烯产品适用于仪器、仪表、家电、工艺制品,陶瓷玻璃器皿及各种贵重l是机结构件,l是标准附件 .其它各项={ I )是要设计的模具。
二、模具结构‘易碎易损物品的防震装和冷库的保温等用。
产品的制作是采用经过预发的聚苯乙烯由于1件在蒸气,水和空气中成 .料球为原料,聚苯乙烯在模具内经蒸汽加热发泡成型,用水冷却 .而后由f缩空气睨模、矗件如嚏大于毫米以的还有机械顶料杆顶出工件。
年来,我厂为各种彩电等家电产品产了数十万套防震包装产品.取得了一定经验一具材卡选用是易府蚀的铝合金ZL 0 .顶:} 12杆采用不锈钢或黄铜棒。
图2是L件 .开状较简单. r在S Z≥安装P 1收饥L.该f的名义尺寸为7。
× l j 1一【l毫米,效L作碰积为5 l .l}l lI有5} 3一×7 l米.因此在-内能排列一个 .件。
馍一上、模具工艺要求聚苯乙烯发泡成型机.不象注塑成型机那样技工件重量尺寸大小选用适当的设备.而发泡聚苯乙烯模是按设备给定的组合尺、l设计j‘米的奠l I. I u刘l l2、架3.芯模框l组成一个封闭的宅问。
料3枪口l把料l满后、卡枪口天闭 .由蒸I}进:}气管9进汽加热熔接成型。
腔模6、芯板u和模芯l, I上有气隙 .使蒸气能通过进入2 J1内。
图1中项l、2, ', 5、H、I 5 l 、为l便于加工,省时和不受设备大小的『制.我J采用钉体拼装式模具。
图3中模芯L左右各二件 .模芯1四件,分型板 1 2 l二件均?f芯板l I I l I芯f。
生产时与戊 c !芯艇1连接。
r Iq模芯1,顶出杆7和 .{纠I l .复位蚪簧装在腔模上 .这二个腔模装在:I【为卡、{ 成( !接. .f I II均' j :时腔连l1排污Ⅱ 2腔模框3框架1顶板5进 . . . . .气管6腔模7顶料杆和弹簧8冷却水管 . . .9进气管 . 1 .枪口l .板 1 .芯O料1芯2模訇:{43 U1. 3志稹稚1. 4模芯1. 5原料粒1. 6分型板(具工业1 9‘模9 0. N O.2总1 8 0维普资讯3◇ O一0望、8――:圈圈目囹0 t . 。
发泡模具设计详解

发泡模具设计详解 The latest revision on November 22, 2020一、发泡模成型机的原理1、发泡原材料的种类:EPS,EPP,EPE,EPO等。
2、成型原理:合模,加料,利用蒸汽加热成型,再冷却,脱模。
二、EPS模具总体结构根据机型的种类来设计模具,与机台配套。
1、一体模:台湾机、方圆机、等机台没有标准水箱,必须根据产品排模来定水箱(蒸汽室),又叫一体模。
2、三片式模具:都具有三片板:凸模板、凹模板、枪板凸模板来固定连接凸模型腔;凹模板用来固定连接凹模型腔;枪板也叫做后封板、背板、主要装顶杆套和料枪。
3、压料:为凸模与凹模配合,方便预开加料成型而设计的一种结构,起到预开加料时不漏料。
根据水箱的合模台阶、模板来计算;压料有离空和没有离空两种。
没有离空的,凹凸模的压料相同;有离空的,凹模压料加离空等于凸模压料,凹模压料不少于10 mm。
4、法兰边:也就是凹模与凹模板连接处的空间,方便安装螺丝钉。
根据水箱合模台阶和模板来定,一般做到15 mm左右为宜,不能少于10mm;还有一种,从模板下面往上面套,叫反托,反托高度根据模板的厚度来定,如库尔特机型,一般采用反托式,日本机型一般采用正面安装,有法兰边。
5、壁厚:EPP模具的壁厚一般在15 mm左右;EPS模具、EPO模具的壁厚在8~10 mm之间;EPE模具的壁厚一般在15 mm,除客户特别说明要求。
6、缩水:一般EPS模具材料的缩水为0.3%,倍率低的客户要求提供0.25%、0.2%等;EPO材料一般在0.9%~1.0%之间;EPP、EPE材料根据倍率的不同,缩水也不同;EPP、EPE材料又分JSP/KANEKA原料等,缩水又不同7、气眼:∮4、∮6、∮8、∮10、∮12等规格,有条型式和针式两种类型。
EPS原材料模具,采用针式气眼比较多,EPP、EPE等原材料模具采用条型式(平面)比较多、侧面一般用针式;气芯按材质分,有铝气芯,铜气芯、不锈钢气芯,常用的是铝气芯。
发泡模与搪塑模的制备解读

⑤上模吸盘推荐使用3.5褶皱 的硅胶吸盘,根据骨架形状可采 用伸缩气缸辅助吸附
带伸缩气缸 的吸盘 普通吸盘
模具公司
Tool Shop
Φ10 &Φ8 二、发泡模结构及分类 – 密封系统
6、密封系统 ①PU料密封:a、根据排气和 工艺需要,采用分段充气密封策 略,侧壁或陡峭斜面推荐采用充 气密封条;b、平坦区域可采用一 般密封条密封;c、密封边界狭窄 区域采用硬密封。 ②滑块之间、滑块与本体之间 均需要严格密封,形成封闭的真 空缝隙;(为了防止密封条在运 动中磨损,设法放置在垂直碰面 上,至少保证斜面45°
模具公司
Tool Shop
一、发泡模生产流程
开模浇注生产流程: ①顶出机构、滑块复位→②铺设表皮(自动感应抽真空吸附) →③ 上模放置骨架(自动感应,吸盘或真空吸附) →④模架旋转(合适 的浇注位置) →⑤浇注→⑥合模→⑦锁模→⑧气垫顶出(加锁模力) →⑨充气密封条充气(根据排气情况分段充气密封) →⑩气垫下降 或充气密封条放气排气(上模真空或吸盘断)→ ⑾合紧模熟化→⑿ 模架旋转至取件状态→⒀开锁、气垫下降(断真空)→⒁开模→⒂ 开模→⒃滑块、抽芯依次打开→⒄顶块将产品顶出→⒅取件……. (切割) 闭模模浇注生产流程: …… → ⑤放置在⑩前;其它过程相似
15~25mm
充气密封 条截面
60 ° 充气密封条进 气接头方式
滑块、本体之间密 封条形状(4*6)
Tool Shop
二、发泡模结构及分类 – 产品特点2
2、产品特点要求:
L
切割 位置 充气密 封条
骨架:足够的工艺边用于密封 充气密封条工艺边 L>20mm 一般密封条工艺边L>15mm 硬密封L>5mm
pu海棉发泡模具方法

pu海棉发泡模具方法
pu海棉发泡模具方法是一种常用的模具制作技术,它采用了聚氨酯材料的优点,具有高强度、优异的耐磨性、耐化学腐蚀性等特点。
下面是pu海棉发泡模具制作的方法:
1. 准备材料:聚氨酯材料、模具结构材料、发泡剂等。
2. 制作模具结构:根据所需的模具形状和尺寸,选择合适的模具结构材料,如木板、铁板等,制作出模具的骨架。
3. 涂刷隔离层:将隔离层涂刷在模具骨架的表面,以防止聚氨酯泡沫粘附在模具骨架上。
4. 喷涂聚氨酯材料:将聚氨酯材料和发泡剂混合后,通过喷涂方式均匀地喷在模具骨架表面,注意聚氨酯材料不要过度喷涂,以免影响模具的质量。
5. 发泡:将喷涂后的模具放置在恰当的环境中进行发泡,一般需要等待几个小时至24小时左右,直到聚氨酯材料完全发泡成型。
6. 去除模具:发泡结束后,将模具从聚氨酯材料中取出,并进行必要的修整和拼接,最终得到所需的pu海棉发泡模具。
以上是pu海棉发泡模具制作的基本步骤,制作过程需要注意安全,避免液体聚氨酯接触皮肤和眼睛,同时还需要控制好聚氨酯材料的喷涂量和发泡时间,以确保模具的质量。
- 1 -。
发泡成型模具

1.3.2普通注射机低发泡注射成型
在普通注射机上也可以进行低发泡注射成型。一般 有两种方法:一是减量注射法,二是瞬间开模注射 法。两种方法都必须对原有模具进行适当改造。改 造的内容如下:
(1)增加排气通路 把原来分型面上的排气槽增加 ,把通过拼缝和推杆排气的气隙增大。
(2)增加推杆数量 在试模后观察,发现有推杆处 受力过大的现象时,再适当增加推杆数量,或加大 推杆直径。
(3)加强冷却水流量。
2、模具设计
2.1模具制造材料
2.2模具分型面选择
分型面尽量选用平面、避用曲面 结构力求简单、易于制模和操作方便 便于设置加料口 便于取模 尽量不影响模样形状和尺寸精度
分模线:根据产品的最大外形做分模线,再做压 料,分出凹凸模腔,分析加工工艺,方便加工,打
气芯、 抛光等;不好做到位的地方做拼块,拼块最好 能做限位,方便安装;产品有倒扣的、侧面有穿孔的 ,做滑块抽芯;根据凹、凸模腔,做模具壁厚,根据 客户要求的壁厚来做,把型腔背面多余的料去掉,尽 量做到壁厚均匀,背面尽量做脱模斜度,方便木样在 翻砂时好脱模,做好造型后,考虑顶杆、料枪位置、 背面的加强筋、支柱位置,可以先做2D排模图,设计
2.3加料口
料枪孔,比料枪嘴大0.2~0.5mm之间
2.4模具壁厚
EPP模具的壁厚一般在15 mm左右; EPS模具、EPO模具的壁厚在8~10 mm之间; EPE模具的壁厚一般在15 mm,除客户特别说明要求。
2.5泡沫塑料收缩率与尺寸精 度
缩水: 一般EPS模具材料的缩水为0.3%,倍率低的客户要求
提供0.25%、0.2%等; EPO材料一般在0.9%~1.0%之间; EPP、EPE材料根据倍率的不同,缩水也不同; EPP、EPE材料又分JSP/KANEKA原料等,4、∮6、∮8、∮10、∮12等规格,有条 型式和针式两种类型。
SRIM发泡模具设计技术在汽车内饰件中的应用分析
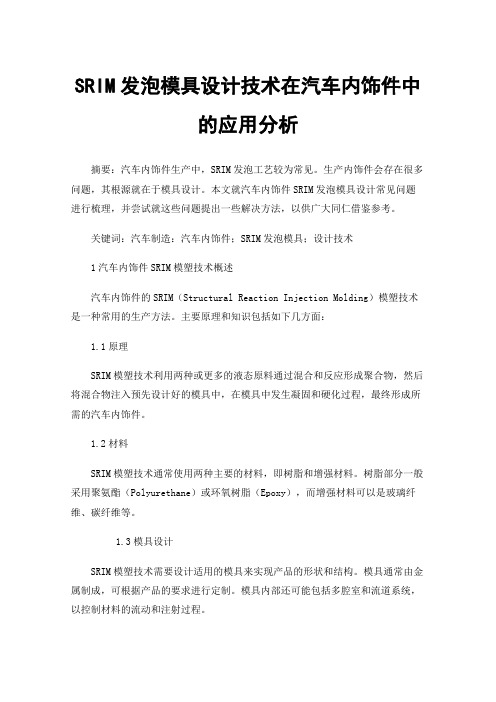
SRIM发泡模具设计技术在汽车内饰件中的应用分析摘要:汽车内饰件生产中,SRIM发泡工艺较为常见。
生产内饰件会存在很多问题,其根源就在于模具设计。
本文就汽车内饰件SRIM发泡模具设计常见问题进行梳理,并尝试就这些问题提出一些解决方法,以供广大同仁借鉴参考。
关键词:汽车制造:汽车内饰件;SRIM发泡模具;设计技术1汽车内饰件SRIM模塑技术概述汽车内饰件的SRIM(Structural Reaction Injection Molding)模塑技术是一种常用的生产方法。
主要原理和知识包括如下几方面:1.1原理SRIM模塑技术利用两种或更多的液态原料通过混合和反应形成聚合物,然后将混合物注入预先设计好的模具中,在模具中发生凝固和硬化过程,最终形成所需的汽车内饰件。
1.2材料SRIM模塑技术通常使用两种主要的材料,即树脂和增强材料。
树脂部分一般采用聚氨酯(Polyurethane)或环氧树脂(Epoxy),而增强材料可以是玻璃纤维、碳纤维等。
1.3模具设计SRIM模塑技术需要设计适用的模具来实现产品的形状和结构。
模具通常由金属制成,可根据产品的要求进行定制。
模具内部还可能包括多腔室和流道系统,以控制材料的流动和注射过程。
1.4制造过程(1)前处理。
材料准备、模具准备和表面处理等;(2)混合注射。
树脂和增强材料按照一定比例混合,然后通过喷头或喷嘴注入模具中;(3)充填。
混合物在模具中充填,填满所需的形状和结构;(4)凝固和硬化。
混合物在模具中发生凝固和硬化过程,形成产品的实体部分;(5)取出和后处理:将成品从模具中取出,并进行去除余料、修整、清洁和表面处理等工序;(6)优势。
SRIM模塑技术能够生产出具有较高强度、刚性和耐用性的汽车内饰件。
此外,它还可以实现复杂的几何形状、薄壁结构和一体成型,提高生产效率和产品质量。
2 SRIM制件成型缺点与控制措施2.1气泡与气穴缺陷与控制(1)缺陷问题第一,气泡缺陷。
第17章 发泡成型工艺与模具设计

(3) 按密度或发泡倍率分类 泡沫塑料按其密度或发泡倍率可分为低
发泡、中发泡与高发泡三种类型。
3
17.1 发泡成型工艺
1.泡沫塑料的特性 泡沫塑料的品种很多,性能也多种多样,因为它含有大量气泡,因此 具有以下共同的特性:
(1) 具有吸收冲击载荷的能力 泡沫塑料受到冲击载荷时,泡沫中的 气体通过滞流和压缩,使外来作用的能量被消耗、散逸。泡体以较小 的负加速度,逐步终止冲击载荷。
R(t) =KDC0 tn (3) 气泡的稳定和固化过程
5
17.1 发泡成型工艺
17.1.2 可发性聚苯乙烯的制备 聚苯乙烯泡沫塑料成型方法主要有模压法、可发性珠粒法和挤出发 泡法。 目前大量使用的方法是可发性珠粒法和挤出发泡法,我国主要使用 可发性珠粒法。
(1) 预发泡 预发泡分为间隙法和连续法两种 (2) 熟化
(2) 隔热性能好。
4
17.1 发泡成型工艺
17.1.1 泡沫塑料的成型原理 1.气发泡沫的成型过程 (1) 泡沫的气泡核形成阶段 (2) 泡沫的气泡核增长 (3) 泡沫的稳定固化 2.成型机理 (1) 气泡核的形成 形成气泡核必须满足以下条件:
1) 作为泡沫塑料基体的聚合物,其分子架中应有足够量的自由 空间,以供聚集足够量的发泡剂,形成气泡核。 2) 发泡剂一般采用低沸点的有机液体 3) 含有低沸点发泡剂的聚合物不应在大气中久放。 (2) 气泡的膨胀过程 气泡增长的近似计算式如下:
高等教育出版社 高等教育电子音像出版社
塑料成型工艺与模具设计电子教案
第17章 发泡成型工艺与模具设计
1 .
第17章 发泡成型工艺与模具设计
17.1 发泡成型工艺 17.2 发泡成型模具设计
2
17.1 发泡成型工艺
发泡模具设计详解

一、发泡模成型机的原理1、发泡原材料的种类:EPS,EPP,EPE,EPO等。
2、成型原理:合模,加料,利用蒸汽加热成型,再冷却,脱模。
二、EPS模具总体结构根据机型的种类来设计模具,与机台配套。
1、一体模:台湾机、方圆机、等机台没有标准水箱,必须根据产品排模来定水箱(蒸汽室),又叫一体模。
2、三片式模具:都具有三片板:凸模板、凹模板、枪板凸模板来固定连接凸模型腔;凹模板用来固定连接凹模型腔;枪板也叫做后封板、背板、主要装顶杆套和料枪。
3、压料:为凸模与凹模配合,方便预开加料成型而设计的一种结构,起到预开加料时不漏料。
根据水箱的合模台阶、模板来计算;压料有离空和没有离空两种。
没有离空的,凹凸模的压料相同;有离空的,凹模压料加离空等于凸模压料,凹模压料不少于10 mm。
4、法兰边:也就是凹模与凹模板连接处的空间,方便安装螺丝钉。
根据水箱合模台阶和模板来定,一般做到15 mm左右为宜,不能少于10mm;还有一种,从模板下面往上面套,叫反托,反托高度根据模板的厚度来定,如库尔特机型,一般采用反托式,日本机型一般采用正面安装,有法兰边。
5、壁厚:EPP模具的壁厚一般在15 mm左右;EPS模具、EPO模具的壁厚在8~10 mm之间;EPE模具的壁厚一般在15 mm,除客户特别说明要求。
6、缩水:一般EPS模具材料的缩水为0.3%,倍率低的客户要求提供0.25%、0.2%等;EPO材料一般在0.9%~1.0%之间;EPP、EPE材料根据倍率的不同,缩水也不同;EPP、EPE材料又分JSP/KANEKA原料等,缩水又不同7、气眼:∮4、∮6、∮8、∮10、∮12等规格,有条型式和针式两种类型。
EPS原材料模具,采用针式气眼比较多,EPP、EPE等原材料模具采用条型式(平面)比较多、侧面一般用针式;气芯按材质分,有铝气芯,铜气芯、不锈钢气芯,常用的是铝气芯。
针孔:一些死角地方,加针孔在∮0.6~0.8mm之间。
发泡模模具结构

发泡模模具结构
发泡模模具结构是由上模板、下模板、热板、隔板、顶压板、顶压板杆、顶压气缸、顶底板、顶底板杆、顶底板气缸、挤出头、挤出头底板、挤出头底板杆、挤出头气缸等组成的。
上模板和下模板之间加装有热板和隔板,隔板用于将上下模板隔开,使发泡材料在加热膨胀时只向上膨胀,在下模板受到顶压时,又能保持稳定的模具高度。
顶压板、顶压板杆和顶压气缸用于控制模具高度和压力,保证发泡材料能够充满整个模具。
顶底板、顶底板杆和顶底板气缸则是用于控制模具的开合和固定模具位置的。
挤出头、挤出头底板、挤出头底板杆和挤出头气缸则是用于将发泡材料挤出到模具中,并控制挤出量和速度的。
发泡模模具结构的设计和制造有着相当高的技术和工艺要求,需要考虑到发泡材料的物理性质、操作的方便性和安全性等多方面因素,以确保模具的稳定性、可靠性和使用寿命。
- 1 -。
发泡模具设计详解
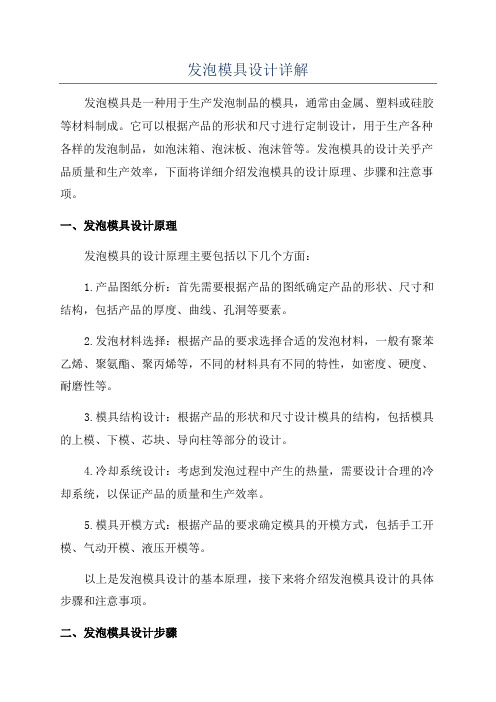
发泡模具设计详解发泡模具是一种用于生产发泡制品的模具,通常由金属、塑料或硅胶等材料制成。
它可以根据产品的形状和尺寸进行定制设计,用于生产各种各样的发泡制品,如泡沫箱、泡沫板、泡沫管等。
发泡模具的设计关乎产品质量和生产效率,下面将详细介绍发泡模具的设计原理、步骤和注意事项。
一、发泡模具设计原理发泡模具的设计原理主要包括以下几个方面:1.产品图纸分析:首先需要根据产品的图纸确定产品的形状、尺寸和结构,包括产品的厚度、曲线、孔洞等要素。
2.发泡材料选择:根据产品的要求选择合适的发泡材料,一般有聚苯乙烯、聚氨酯、聚丙烯等,不同的材料具有不同的特性,如密度、硬度、耐磨性等。
3.模具结构设计:根据产品的形状和尺寸设计模具的结构,包括模具的上模、下模、芯块、导向柱等部分的设计。
4.冷却系统设计:考虑到发泡过程中产生的热量,需要设计合理的冷却系统,以保证产品的质量和生产效率。
5.模具开模方式:根据产品的要求确定模具的开模方式,包括手工开模、气动开模、液压开模等。
以上是发泡模具设计的基本原理,接下来将介绍发泡模具设计的具体步骤和注意事项。
二、发泡模具设计步骤1.产品分析:根据产品的图纸确定产品的形状、尺寸和结构,分析产品的特点和要求,确定发泡模具的设计方向。
2.模具结构设计:根据产品的形状和尺寸设计模具的结构,包括模具的上模、下模、芯块、导向柱等部分的设计,确保模具的稳定性和精度。
3.模具零部件设计:根据模具结构设计细化设计各个零部件,包括上模板、下模板、芯块、导向柱等部件的设计。
4.冷却系统设计:设计模具的冷却系统,以保证模具在生产过程中不发热变形,同时可以提高生产效率和产品质量。
5.模具装配:将各个零部件按照设计图纸进行装配,保证模具的结构完整和稳定。
6.试模调试:进行试模调试,检查模具的精度和稳定性,对模具进行必要的调整和优化,确保模具可以正常生产。
以上是发泡模具设计的基本步骤,设计师在进行发泡模具设计时需要认真执行每个步骤,确保设计的质量和准确性。
发泡模具设计详解
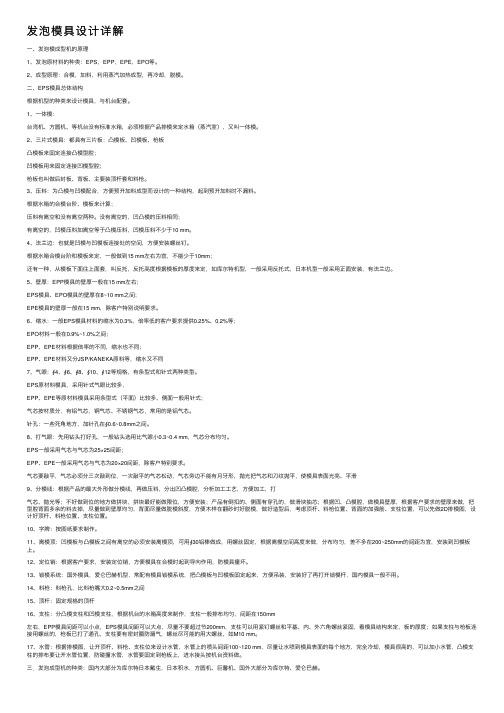
发泡模具设计详解⼀、发泡模成型机的原理1、发泡原材料的种类:EPS,EPP,EPE,EPO等。
2、成型原理:合模,加料,利⽤蒸汽加热成型,再冷却,脱模。
⼆、EPS模具总体结构根据机型的种类来设计模具,与机台配套。
1、⼀体模:台湾机、⽅圆机、等机台没有标准⽔箱,必须根据产品排模来定⽔箱(蒸汽室),⼜叫⼀体模。
2、三⽚式模具:都具有三⽚板:凸模板、凹模板、枪板凸模板来固定连接凸模型腔;凹模板⽤来固定连接凹模型腔;枪板也叫做后封板、背板、主要装顶杆套和料枪。
3、压料:为凸模与凹模配合,⽅便预开加料成型⽽设计的⼀种结构,起到预开加料时不漏料。
根据⽔箱的合模台阶、模板来计算;压料有离空和没有离空两种。
没有离空的,凹凸模的压料相同;有离空的,凹模压料加离空等于凸模压料,凹模压料不少于10 mm。
4、法兰边:也就是凹模与凹模板连接处的空间,⽅便安装螺丝钉。
根据⽔箱合模台阶和模板来定,⼀般做到15 mm左右为宜,不能少于10mm;还有⼀种,从模板下⾯往上⾯套,叫反托,反托⾼度根据模板的厚度来定,如库尔特机型,⼀般采⽤反托式,⽇本机型⼀般采⽤正⾯安装,有法兰边。
5、壁厚:EPP模具的壁厚⼀般在15 mm左右;EPS模具、EPO模具的壁厚在8~10 mm之间;EPE模具的壁厚⼀般在15 mm,除客户特别说明要求。
6、缩⽔:⼀般EPS模具材料的缩⽔为0.3%,倍率低的客户要求提供0.25%、0.2%等;EPO材料⼀般在0.9%~1.0%之间;EPP、EPE材料根据倍率的不同,缩⽔也不同;EPP、EPE材料⼜分JSP/KANEKA原料等,缩⽔⼜不同7、⽓眼:∮4、∮6、∮8、∮10、∮12等规格,有条型式和针式两种类型。
EPS原材料模具,采⽤针式⽓眼⽐较多,EPP、EPE等原材料模具采⽤条型式(平⾯)⽐较多、侧⾯⼀般⽤针式;⽓芯按材质分,有铝⽓芯,铜⽓芯、不锈钢⽓芯,常⽤的是铝⽓芯。
针孔:⼀些死⾓地⽅,加针孔在∮0.6~0.8mm之间。
发泡模具排气系统设计
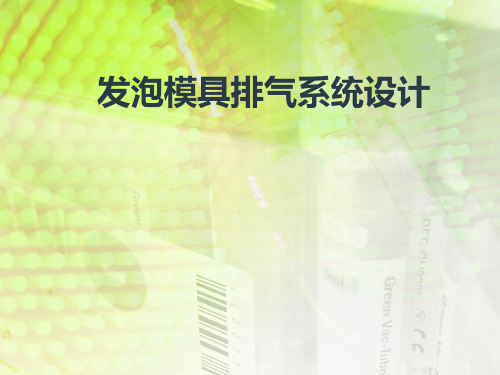
实用文档
1
1、概述
实用文档
2
1、概述
在设计发泡成型模具时必须考虑排气问题。如果模 具型腔内的气体不能顺利排出,将造成制品的气泡、 疏松、冲模不满、焊接不牢、制件表面发乌或者在注 射时由于气体被压缩所产生的高温制品底部碳化、烧 焦,而且型腔内气体被压缩产生的反压力会降低冲模 速度,影响注射周期和产品质量。
实用文档
13
2.4 配合间隙排气
实用文档
14
2、总结
排气系统设计主要考虑: • 位置:一般设在料流的末端。 • 尺寸:排气而不漏料。 • 实施方式:
(1)利用分型面间隙排气。 (2)设排气槽。 (3)利用成型零件配合间隙排气。 (4)专设排气系统。
实用文档
15
实用文档
16
X(mm) 0.025-0.038 0.025-0.038
0.1 0.05
MATERIAL PP PS
PMMA PE
实用文档
X(mm) 0.013-0.025 0.013-0.025 0.013-0.038 0.013-0.025
10
2.3 排气钢排气
PM-35排气钢是一种优质透气性钢材,内部由微细的小孔相 连构成,使空气或任何气体能顺利渗透及穿过。因此,于注塑模具 之适当位置镶上PM-35排气钢,由气体所形成的注塑问题,可以完 全清除,使成型加工更加完美。 特点:1.比重小,比强度大。2.能量吸收性好。3.制振效果好。4.比 表面积大。有1/4的组织是通孔。当由于型腔结构限制充模料流末端不在分型面上时,可利用 成型零件间的配合间隙排气。
构成型腔的成型零件中的某些零件,如顶杆、顶管、活动成 型零件等,与型腔或型芯之间多采用间隙配合,配合间隙较大, 若将其设计在料流末端,可兼起排气作用。
发泡成型模具讲解
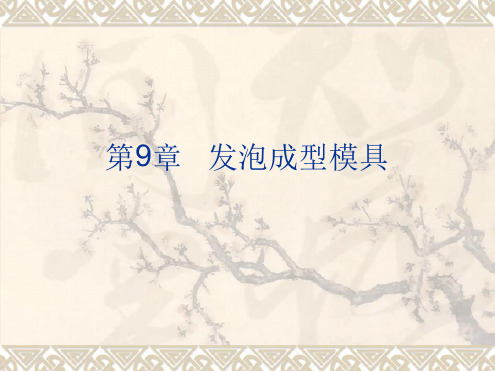
9.1 概述
? 泡沫塑料是以树脂为基础内部含有无数微小气孔的塑料,又 称为多孔性塑料。采用不同的树脂和发泡方法可制成性能各 异的泡沫塑料。它具有质轻、防震、防潮、隔热与吸音等优 点,在塑料工业中占有特殊的地位。
? 泡沫塑料的发泡方法大致有三种:物理发泡法、化学发泡法、 机械发泡法。三种发泡方法的共同点是:待发泡聚合物或复 合物必须处于液态或粘度在一定范围内的塑性状态;泡孔的 形成是依靠添加能产生泡沫结构的固体、液体或气体发泡剂, 或者几种物质混合的发泡剂。针对某种聚合物,应根据其性 质,选择适宜的发泡法与发泡剂,才能制成合格的泡沫塑料。
机直接通蒸汽发泡两种。
? ①蒸缸发泡法适宜生产小型、薄壁与形状复杂的塑件,即将 预胀物填满模具后放入蒸缸中,然后通蒸汽加热成型。蒸汽 压力与加热时间应视塑件大小与厚度而定,一般为0.05~ 0.10MPa,10~50min。模内预胀物受热软化,经膨胀互相 熔接而成整体,冷却脱模即制得泡沫塑料产品。此法所用模 具简单,但工人劳动强度较大,难于实现机械与自动化生产, 如图图9-1(a)所示。
点是塑化时间短、冷却定型快、塑件内珠粒熔接良
好、质量稳定、生产效率高,能实现机械化与自动 化生产,如图9-1(b)所示。
(2)挤出发泡成型法 ? 挤出发泡成型法适宜生产片材和薄膜。图 9-2所示为
可发性聚苯乙烯泡沫塑料纸的挤出吹塑过程。
图9-2 可发性泡沫塑料纸的生产过程 1-挤出机 2-机头 3-泡沫塑料纸 4-卷筒
? (2)图9-4所示为板材手动蒸箱压模,一次可成型三块板材, 模套由件5和件8组成,并通过件12连接。
图9-4 板材手动蒸箱压模 1-铰链螺栓2-螺母3-上模板4-隔板5-模套6-下模板 7-螺母8-模套组合件9-螺母10-销11-轴12-长螺栓
- 1、下载文档前请自行甄别文档内容的完整性,平台不提供额外的编辑、内容补充、找答案等附加服务。
- 2、"仅部分预览"的文档,不可在线预览部分如存在完整性等问题,可反馈申请退款(可完整预览的文档不适用该条件!)。
- 3、如文档侵犯您的权益,请联系客服反馈,我们会尽快为您处理(人工客服工作时间:9:00-18:30)。
发泡模具设计详解
经验交流2010-04-12 14:15:39 阅读477 评论0 字号:大中小订阅
一、发泡模成型机的原理
1、发泡原材料的种类:EPS,EPP,EPE,EPO等。
2、成型原理:合模,加料,利用蒸汽加热成型,再冷却,脱模。
二、EPS模具总体结构
根据客户机型的种类来设计模具,与客户机台配套。
1、水箱(汽室):三片式模具,客户有标准水箱。
台湾机、方圆机、等机台没有标准水箱,必须
根据产品的排模来定水箱,又叫一体模。
2、三片式模具,都具有三片板,分别叫凸模板、凹模板、枪板,凸模板来固定连接凸模型腔,凹
模板用来固定连接凹模型腔,枪板也叫做后封板、背板、主要装顶杆套和料枪。
3、压料:为凸模与凹模配合,方便预开加料成型而设计的一种结构,起到预开加料时不跑料。
根据水箱的合模台阶、模板来计算,压料有离空和没有离空两种,没有离空的,凹凸模的压料相同,有离空的,凹模压料加离空等于凸模压料,凹模压料不少于10 mm。
4、法兰边:也就是凹模与凹模板连接处的空间,方便安装螺丝钉,根据水箱合模台阶和模板来定,一般做到15 mm左右为宜,不能少于10mm,还有一种,从模板下面往上面套,叫反托,反托高度根据模板的厚度来定,如库尔特机型,一般采用反托式,日本机型一般采用正面安装,有法兰边。
5、壁厚:EPP模具的壁厚一般在15 mm左右,EPS模具、EPO模具的壁厚在8~10 mm之间,
EPE模具的壁厚一般在15 mm,除客户特别说明要求。
6、缩水:一般的发泡模具EPS材料的缩水为0.3%(国内)国外0.4%,倍率低的客户要求提供0.25%、0.2%等,EPO材料一般在0.9%~1.0%之间;EPP、EPE材料根据倍率的不同,缩水也不同;EPP、EPE 材料又分JSP原料、卡内卡原料等,缩水又不同,所以EPP、EPE等材料的缩水是客户提供,也可以叫生产原材料厂家提供,如国内两家原料公司,JSP、卡内卡;
7、气芯:气芯∮4、∮6、∮8、∮10、∮12等规格,有条型和针孔两种类型,还有一种叫无孔气芯,闷气芯;根据要求分一般气芯,特殊气芯,如条型的,条型直缝为0.25mm~0.4mm的为特殊气芯,一般用线切割加工制作;普通的条型直缝为0.8 mm ~0.7mm;EPS原材料模具,采用针孔气芯比较多,EPP、EPE等原材料模具采用条型气芯比较多,指平面、侧面一般用针孔;气芯按材质分,有铝气芯,铜气芯、不锈钢气芯,常用的是铝气芯,其它根据客户要求来定。
8、打气芯:先用钻头打好孔,一般钻头选用比气芯小0.3~0.4 mm,气芯分布均匀,EPS一般采用气芯与气芯为25×25间距,EPP、EPE一般采用气芯与气芯为20×20间距,除客户特别要求。
气芯要敲平,气芯必须分三次敲到位,一次敲平的气芯松动,气芯旁边不能有月牙形,抛光把气芯和刀纹抛平,使模具表面光亮、平滑,一些死角地方,加针孔在∮0.6~0.8mm之间。
9、找分模线,要根据产品的最大外形做分模线,再做压料,分出凹凸模腔,分析加工工艺,方便加工,打气芯、抛光等;不好做到位的地方做拼块,拼块最好能做限位,方便安装;产品有倒扣的、侧面有穿孔的,做滑块抽芯;根据凹、凸模腔,做模具壁厚,根据客户要求的壁厚来做,把型腔背面多余的料去
掉,尽量做到壁厚均匀,背面尽量做脱模斜度,方便木样在翻砂时好脱模,做好造型后,考虑顶杆、料枪位置、背面的加强筋、支柱位置,可以先做2D排模图,设计好顶杆、料枪位置、支柱位置。
10、字牌:按图纸要求制作。
11、离模顶:凹模板与凸模板之间有离空的必须安装离模顶,可用∮30铝棒做成,用螺丝固定,根
据离模空间高度来做,分布均匀,差不多在200~250mm的间距为宜,安装到凹模板上。
12、定位销:根据客户要求,安装定位销,方便模具在合模时起到导向作用,防模具撞坏。
13、锁模系统:国外模具,爱仑巴赫机型,常配有模具锁模系统,把凸模板与凹模板固定起来,方
便吊装,安装好了再打开锁模杆,国内模具一般不用。
14、料枪:一般客户配有,模具根据客户的料枪,做好料枪孔,比料枪嘴大0.2~0.5mm之间,有的
要做限位,有的不需要,根据客户要求做。
15、顶杆:一般客户有固定规格的顶杆,根据客户要求制作设计模具,如果客户要配顶杆,我们可
以配成套的顶杆,如顶杆套,密封圈、推杆、弹簧、插销、顶杆头。
16、支柱:分凸模支柱和凹模支柱,根据客户机台的水箱高度来制作,支柱一般排布均匀,间距在150mm左右,EPP模具间距可以小点,EPS模具间距可以大点,尽量不要超过节200mm,支柱可以用紧钉螺丝和平基、内、外六角螺丝紧固,看模具结构来定,板的厚度;如果支柱与枪板连接用螺丝的,枪板已打了通孔,支柱要有密封圈防漏气,螺丝尽可能的用大螺丝,如M10 mm。
17、水管:根据排模图,让开顶杆、料枪、支柱位来设计水管,水管上的喷头间距100~120 mm,尽量让水喷到模具表面的每个地方,完全冷却,模具很高的,可以加小水管,一般配凹模水管,凸模水管一般客户机台上就有,凸模支柱的排布要让开水管位置,防碰撞水管,水管要固定到枪板上,进水接头按客户机台资料做。
发泡模具的结构大致这样,要根据客户机台来设计模具,设计好的模具一定要方便客户
装机。
三.发泡成型机的种类:国内大部分为库尔特日本戴生,日本积水,方圆机、巨馨机、台湾机、国
外大部分为库尔特、爱仑巴赫。