发泡成型模具 PPT
第9章发泡成型模具

泡沫塑料是以树脂为基础内部含有无数微小气孔的塑料,又 称为多孔性塑料。采用不同的树脂和发泡方法可制成性能各 异的泡沫塑料。它具有质轻、防震、防潮、隔热与吸音等优 点,在塑料工业中占有特殊的地位。 泡沫塑料的发泡方法大致有三种:物理发泡法、化学发泡法、 机械发泡法。三种发泡方法的共同点是:待发泡聚合物或复 合物必须处于液态或粘度在一定范围内的塑性状态;泡孔的 形成是依靠添加能产生泡沫结构的固体、液体或气体发泡剂, 或者几种物质混合的发泡剂。针对某种聚合物,应根据其性 质,选择适宜的发泡法与发泡剂,才能制成合格的泡沫塑料。
Hale Waihona Puke 9.4 低发泡注射成型模1.低发泡注射成型模具基本结构 低发泡注射成型模的基本结构与普通注射成型模具 基本相同,其设计方法也与注射成型模具极为类似。 由于发泡材料的物理性质与非发泡料材有所不同, 因此在个别部位的设计上有其特殊要求: (1)浇注系统 (2)型腔排气 (3)冷却系统 (4)脱模机构 (5)型腔数
图9-1 模压发泡成型模具 1-气孔 2-上气室 3-型芯 4-加料管
5-模框
6-下气室
②液压机直接通蒸汽发泡法适宜生产厚度较大的泡 沫板材。成型时常用气送法将粒料加入液压机上的 模具中。模具开有若干个0.1~O.4mm的通气孔(或 槽),当模具型腔装满预胀物后,直接通入O.1~ O.2MPa的蒸汽,并使温度升至11O℃左右,此时 模内预胀物膨胀并粘接成整体。关闭蒸汽,保持一 定时间(1~2min),通水冷却后脱模。此发泡法的优 点是塑化时间短、冷却定型快、塑件内珠粒熔接良 好、质量稳定、生产效率高,能实现机械化与自动 化生产,如图9-1(b)所示。
(2)挤出发泡成型法
挤出发泡成型法适宜生产片材和薄膜。图9-2所示为 可发性聚苯乙烯泡沫塑料纸的挤出吹塑过程。
《发泡成型模具》课件
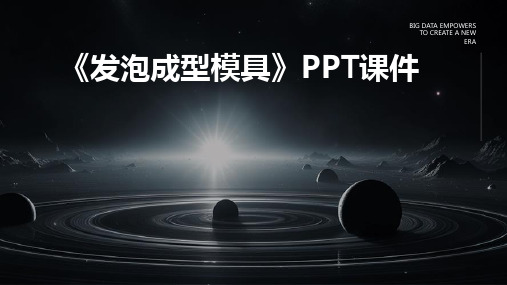
05
发泡成型模具案例分析
BIG DATA EMPOWERS TO CREATE A NEW
ERA
案例一:某品牌汽车座椅发泡模具设计
总结词
汽车座椅发泡模具设计
详细描述
介绍某品牌汽车座椅发泡模具的设计理念、结构特点、材料选择以及制造工艺流程,重点阐述模具设计对座椅性 能和品质的影响。
案例二:某品牌鞋底发泡模具制造工艺
温度控制
根据生产需要,将模具温度调整到适宜范围 ,以获得最佳的发泡效果。
冷却与脱模
确保模具在充分冷却后进行脱模,以避免产 品变形或损坏。
常见问题与解决方案
填充不均
表面粗糙
调整物料填充速度和流量,确保均匀填充 。
检查模具温度和物料温度,确保两者匹配 ,避免表面粗糙。
产品变形
模具损坏
优化冷却系统,使产品均匀冷却,防止变 形。
BIG DATA EMPOWERS TO CREATE A NEW ERA
04
发泡成型模具的发展趋势与展望
技术创新与进步
01
3D打印技术的应用
02
新型材料的应用
03
智能化技术的引入
通过3D打印技术,实现模具的快 速原型制造,缩短产品开发周期 。
采用高强度、轻质、耐高温的新 型材料,提高模具的使用寿命和 性能。
建筑领域
发泡成型模具可用于生产建筑保温材 料、装饰材料等,具有保温、隔热、 隔音、美观等优点。
包装领域
发泡成型模具可用于生产包装材料、 缓冲材料等,具有轻便、环保、耐用 等优点。
02
发泡成型模具的设计与制造
BIG DATA EMPOWERS TO CREATE A NEW
ERA
泡沫塑料成型办法与模具
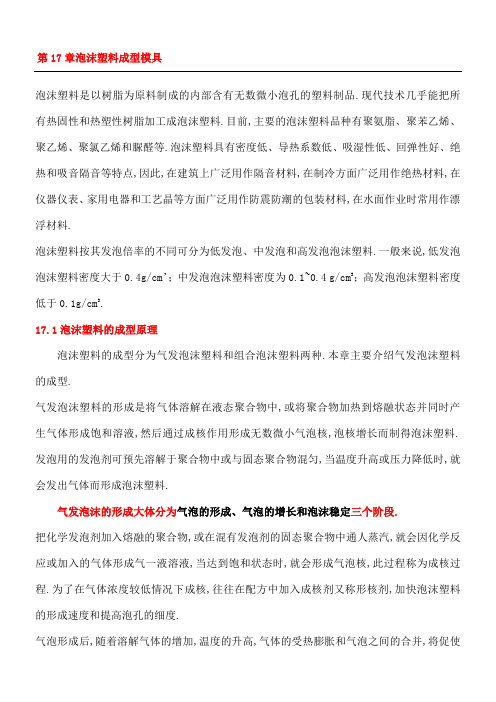
第17章泡沫塑料成型模具泡沫塑料是以树脂为原料制成的内部含有无数微小泡孔的塑料制品.现代技术几乎能把所有热固性和热塑性树脂加工成泡沫塑料.目前,主要的泡沫塑料品种有聚氨脂、聚苯乙烯、聚乙烯、聚氯乙烯和脲醛等.泡沫塑料具有密度低、导热系数低、吸湿性低、回弹性好、绝热和吸音隔音等特点,因此,在建筑上广泛用作隔音材料,在制冷方面广泛用作绝热材料,在仪器仪表、家用电器和工艺晶等方面广泛用作防震防潮的包装材料,在水面作业时常用作漂浮材料.泡沫塑料按其发泡倍率的不同可分为低发泡、中发泡和高发泡泡沫塑料.一般来说,低发泡泡沫塑料密度大于0.4g/cm’;中发泡泡沫塑料密度为0.1~0.4 g/cm3;高发泡泡沫塑料密度低于0.1g/cm3.17.1泡沫塑料的成型原理泡沫塑料的成型分为气发泡沫塑料和组合泡沫塑料两种.本章主要介绍气发泡沫塑料的成型.气发泡沫塑料的形成是将气体溶解在液态聚合物中,或将聚合物加热到熔融状态并同时产生气体形成饱和溶液,然后通过成核作用形成无数微小气泡核,泡核增长而制得泡沫塑料.发泡用的发泡剂可预先溶解于聚合物中或与固态聚合物混匀,当温度升高或压力降低时,就会发出气体而形成泡沫塑料.气发泡沫的形成大体分为气泡的形成、气泡的增长和泡沫稳定三个阶段.把化学发泡剂加入熔融的聚合物,或在混有发泡剂的固态聚合物中通人蒸汽,就会因化学反应或加入的气体形成气一液溶液,当达到饱和状态时,就会形成气泡核,此过程称为成核过程.为了在气体浓度较低情况下成核,往往在配方中加入成核剂又称形核剂,加快泡沫塑料的形成速度和提高泡孔的细度.气泡形成后,随着溶解气体的增加,温度的升高,气体的受热膨胀和气泡之间的合并,将促使气泡不断地增长.同时,通过成核剂的作用大大增加了气泡的数量,再加上气泡膨胀使孔直径扩大,因此泡沫塑料将不断胀大.由于气泡的不断生成和增长,使得泡沫体系的体积和表面积增大,因此气壁的厚度会不断减薄,使泡沫体系不稳定.通常采用加入表面活性剂以减少气体扩散的作用来促使泡沫的稳定,也可通过提高聚合物熔体、对物料冷却或增加聚合物交联作用来达到稳定的目的.本章主要以聚苯乙烯树脂为例,介绍泡沫塑料的成型工艺及模具设计.17.2聚苯乙烯泡沫塑料的成型工艺聚苯乙烯泡沫塑料成型方法主要有模压法、可发性珠粒法和挤出发泡法.模压法是采用乳液法聚苯乙烯和热分解型发泡剂的方法制得泡沫塑料,是早期使用的方法,现在很少使用.目前大量使用的方法是可发性珠粒法和挤出发泡法,我国主要使用可发性珠粒法.17.2.1可发性聚苯乙烯珠粒的制备在成型泡沫塑料之前,必须先将发泡剂与聚苯乙烯制成易于流动的珠状半透明的可发性聚苯乙烯珠粒.1预发泡预发泡有间隙歇法和连续法两种,目前多用连续法,其主要设备是连续蒸汽预发泡机,如图16.1所示.预发泡前,发泡剂通常为石油醚、正戊烷、异戊烷、季戊烷等在聚苯乙烯合成时或聚合后加入,含量约为6%—8%.将含有发泡剂的珠粒状聚苯乙烯加入发泡机,利用蒸汽将其加热到90-1050C,使树脂软化,同时发泡剂汽化造成压力,促使珠粒膨胀40~80倍.2熟化预发泡后的颗粒在环境温度下自然冷却,贮存一段时间,具体时间可由实验确定.泡孔内的发泡气体和水蒸汽凝成液态,珠内压力减小,形成局部真空状态,这时周围的空气通过泡孔膜渗透入泡中,使气泡内的压力与环境压力达到平衡,这一过程称为熟化.由于发泡剂与空气组合,进一步发泡时,预发泡颗粒将会产生更大的膨胀力.通常熟化处理在布袋或大型网状料仓中进行,最适宜的熟化温度为22~260C下熟化8~24h后就可放入模具中成型.一般室温17.2.2聚苯乙烯泡沫塑料的成型工艺聚苯乙烯泡沫塑料在模具内通入蒸汽加热成型,故称为蒸汽加热成型法.按照加热方式与使用设备的不同,可分为蒸箱发泡成型和泡沫塑料成型机一种专用液压机直接通蒸汽发泡成型两种.1蒸箱发泡对于生产小型、薄壁和复杂的塑件,大多采用蒸箱发泡成型.将填满可发性聚苯乙烯原料的模具合模后放进蒸箱通人蒸汽加热,蒸汽压力和加热时间视塑件大小和厚度而定.一般蒸汽压力控制在0.05~0.25MPa,加热时间为2~3min,根据需要也可长达10min以上.模内的预发泡颗粒受热软化和膨胀就互相熔结在一起,从蒸箱内取出模具,冷却脱模后即可得到泡沫塑料制件.2泡沫塑料成型机发泡泡沫塑料成型机是国内普遍使用的聚苯乙烯泡沫塑料成型设备,该设备可分为包装成型机和板材成型机两种.厚度较大的泡沫塑料制件或大中型的泡沫塑料制件常采用泡沫塑料成型机直接发泡成型.在模具上开有供通气用的0.1~0.4mm直径的通气孔,在成型前先通入0.1~0.2MPa的加热蒸汽,将模具预热0.5min后,打开出气口,用气送法将预发泡颗粒注入模具型腔中,闭合出气口,在蒸汽室中通入0.1~0.2MPa的蒸汽,使温度升至1100C左右,型腔内的预发泡颗粒就膨胀粘接为一体,关闭蒸汽阀门并保持1~2min,然后通冷却水,最后脱模.17.2.3聚苯乙烯泡沫塑料成型模具泡沫塑料成型模具的结构比较简单.对于小型、薄壁和复杂的泡沫塑料制件或者小批量生产的泡沫塑料制件,常采用蒸箱发泡的手工操作模具;对于大型厚壁或者大批量生产的泡沫塑料制件,常采用带有蒸汽室的泡沫塑料成型机直接通蒸汽发泡模具.17.2.3.1手工操作模具手工操作模具本身没有蒸汽室,而是将整个模具放在蒸箱中通蒸汽加热,成型后移出箱外冷却.图16.2所示是包装盖手动蒸箱发泡模,一次成型一件.合模时,模套1和下模板3以圆周定位.为了开模方便,在模具的四周设有撬口8.上模板2、下模板3和模套1上均设有直径为1~1.8mm的通气小孔,孔距为15-20mm.整副模具靠铰链螺栓6和蝶形螺母5锁紧,铰链螺栓摆动要灵活,并要有足够的强度.17.2.3.2泡沫塑料成型机直接通蒸汽模具泡沫塑料成型机上的发泡模本身带有蒸汽室,其模具一般由两部分组成.立式成型机上设有上下模,上下模均设有蒸汽室.合模后,经预发泡的珠粒状聚苯乙烯由喷枪或用气送法从进料口输送到模具型腔内,料满后关闭气阀,然后在动、定模汽室内通人一定蒸汽压力的蒸汽,保持一定时间,接着再保温一段时间,然后在蒸汽室内通冷却水,冷却后脱模取件.图16.3为包装盒机动发泡模,适合于在卧式泡沫塑料成型机上生产.为了保证模具的良好密封,在动、定模板及分型面处设有密封环,在定模汽室板5、动模汽室板2和成型套10上均设有孔径8mm的通气小孔,孔距为20mm.17.2.3.3模具设计应注意的问题1型腔壁厚应尽量均匀虽然泡沫塑料成型模具一般都并不复杂,但是,由于每一次生产循环都会使模具受热受冷各一次,这样频繁的膨胀与收缩引起的热交变应力对模具的寿命会产生较大的影响,若模具壁厚不均匀,则影响就会更大,因此,泡沫塑料成型模具要求壁厚尽量均匀,一般约10 mm左右.2型腔应考虑脱模斜度一般型腔深度在100mm以内时,脱模斜度取10~1.50;型腔深度100mm 以上时,脱模斜度取20~30.手工操作的模具一般用手工脱模,因此,脱模斜度应取上限.有蒸汽室的机动泡沫塑料成型模具常采用在蒸汽室内通人压缩空气脱模的方法,受力比较均匀,故脱模斜度可取下限.另外,蒸汽室一定要考虑密封的问题,同时,为了使蒸汽室能均匀冷却,冷却水的通人与排出应能保证型腔均匀地得到冷却,且在蒸汽室中不应积水.3模具材料发泡成型的工艺特点决定了泡沫塑料的成型模具必须具有良好的导热性和能够长期经受由热胀冷缩产生的交变应力,还要具有耐蚀性能.在中小批量生产中,一般采用铝合金铸件来制造模具;在大批量生产中,可采用青铜等材料.为了保护模具型腔不受腐蚀以及脱模方便,通常型腔表面抛光后应涂脱模剂,最常用的脱模剂是硅油.17.3聚四氟乙烯塑料成型工艺与冷压成型模具聚四氟乙烯树脂的大分子链中,由于碳键的存在,增加了链的刚性.聚四氟乙烯是结晶型聚合物,其晶区熔点很高3270C,加上分子量很大和分子链的密集堆积等,使得其在高温下的熔融粘度很高,甚至加热到分解温度4150C时仍然不能变为粘流态.虽然聚四氟乙烯是热塑性塑料,但不能用一般热塑性塑料的成型方法成型,只能用类似粉末冶金烧结成型方法来成型,这种方法通常称为冷压烧结成型.成型时,先将,‘定量的聚四氟乙烯放人常温的模具型腔中,在压力的作用下压成密实的型坯,然后送至烧结炉亦称烘室内进行烧结,冷却后成为塑料制件.成型冷压成型的过程包括聚四氟乙烯粒度的选择、加料及其控制、压制及其工艺参数的选择压制过程中排气以及脱模等.1粒度冷压烧结成型大多采用通过悬浮法聚合的聚四氟乙烯粉料,如果成型薄壁塑件,亦可选用分散法聚合的聚四氟乙烯.聚四氟乙烯树脂是一种纤维状的粉末,在贮存或运输过程中,由于受压和震动,容易结块成团,致使冷压时加料发生困难或者所压制成的型坯密度不均匀,甚至出现开裂现象,所以在使用前必须将已结成块的树脂捣碎,并用20目的筛子过筛,过筛后的树脂粉料的颗粒直径一般为20~600μm.2加料聚四氟乙烯冷压成型的设备是立式压机,模具的型腔固定在压机的下工作台上,压头也是模具塑件的成型部分固定在压机的上工作台上.压制时,需将符合要求的粉料按塑料制件所需的量由试验确定均匀地加入到敞开的型腔内,然后用刮刀刮平.树脂的加入量也可由模具结构的调试来确定,即在压机上把模具结构调试到模具型腔的原料加入量正好是成型塑件所要加入的定量,则加料后只需要用刮刀将上平面刮平即町,这对定量及加料的操作将会带来极大的方便.加料时应特别注意,一个型坯应一次加料完毕,否则就有可能在各次加料的界面上产生分层或开裂.3压制加料完毕应立即进行压制,加压宜缓慢进行,防止冲击.预压型坏的成型压力选择十分重要,它与树脂的粒度、是否含有填充剂及型坯要求的密度有关.压力过低,型坯内部不紧密,密度不高,会使塑件的物理和力学性能显着下降;压力过高,树脂的颗粒在模内容易相互滑动,以致型坯内部出现裂纹.预压成型的压力一般取25—50MPa,如果采用带有填充剂的树脂,成型压力可适当增大,甚至可达到100MPa.为了使高度较大的塑件型坯能获得尽可能一致的密度,应采取从型腔上下双向同时加压的压制方法加压.加压的速度是指压头接触加料腔中粉料后的下降速度,也就是压机上工作台下降的速度.。
PU发泡工艺介绍解析

20
聚氨酯化学:A料跟B料之比
对于座椅泡沫而言(TDI系统及TDI&MDI系统)来说, 其对应关系为:
A料 P1:100
B料(软泡) 30-50
B料(硬泡)
根据实际羟值和水份计算,通常要 远高于软泡
21
聚醚组合料
2、新制的泡沫需在自然状态下熟化72小时方可取 样,取样应放在恒温恒湿内(GB/T2918规定的温 度是23±2℃,相对湿度50±5%)。
31
发泡测试标准
硬度:压陷硬度(ILD)、压缩硬度(CLD) 这两种测试方法的主要区别是泡沫塑料的加载面积,在ILD试验中
样件受压面积是323CM2,而CLD是将整个样件进行压缩。在此,我 们只讨论ILD试验方法。 在ILD试验中,试样大小是38*38*50mm,试验的压头直径200mm (压头底边有R=10的圆角),支撑板开有6mm的孔,孔间距20mm。 压头加压速度(100±20)mm/min,首先以5N的压力作为下压零点, 从零点开始下压试样厚度的70%,再以同样的速度卸荷,重复加压、 卸荷三次,作为预压,重复预压三次后立即以相同的速度压陷试样, 压头压入试样的厚度分别为25±1%、65±1%,到达变形量之后保持 30±1s记录相对压陷值,记下的值即为该压陷变量下的压陷硬度。
3
聚氨酯定义
➢主链上含有--NHCO-- 基团聚合物通称为聚 氨酯甲酸酯简称为聚氨酯。
➢简称PU。
4
聚氨酯分类
➢根据原料不同和配方的变化,分为软质、 半硬质和硬质泡沫。
软质:座椅,头枕,海绵… 半硬质:扶手,方向盘; 硬质:方向盘芯、冷库保温防水。
发泡模具
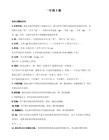
1kgf = 9.807牛顿(N)
气芯要敲平,气芯必须分三次敲到位,一次敲平的气芯松动,气芯旁边不能有月牙形,抛光把气芯和刀纹抛平,使模具表面光亮、平滑
9、分模线:根据产品的最大外形做分模线,再做压料,分出凹凸模腔,分析加工工艺,方便加工,打
气芯、 抛光等;不好做到位的地方做拼块,拼块最好能做限位,方便安装;产品有倒扣的、侧面有穿孔的,做滑块抽芯;根据凹、凸模腔,做模具壁厚,根据客户要求的壁厚来做,把型腔背面多余的料去掉,尽量做到壁厚均匀,背面尽量做脱模斜度,方便木样在翻砂时好脱模,做好造型后,考虑顶杆、背面的加强筋、支柱位置,可以先做2D排模图,设计好顶杆、支柱位置。
2、三片式模具:都具有三片板:凸模板、凹模板
凸模板来固定连接凸模型腔;
凹模板用来固定连接凹模型腔;
3、压料:为凸模与凹模配合,方便预开加料成型而设计的一种结构,起到预开加料时不漏料。
根据水箱的合模台阶、模板来计算;
压料有离空和没有离空两种。没有离空的,凹凸模的压料相同;
10、字牌:按图纸要求制作。
11、离模顶:凹模板与凸模板之间有离空的必须安装离模顶,可用∮30铝棒做成,用螺丝固定,根据离模空间高度来做,分布均匀,差不多在200~250mm的间距为宜,安装到凹模板上。
12、定位销:根据客户要求,安装定位销,方便模具在合模时起到导向作用,防模具撞坏。
一、发泡模成型机的原理
1、发泡原材料的种类:EPS,EPP,EPE,EPO等。
2、成型原理:合模,加料,利用蒸汽加热成型,再冷却,脱模。
二、EPS模具总体结构
根据机型的种类来设计模具,与机台配套。
1、一体模:
台湾机、方圆机、等机台没有标准水箱,必须根据产品排模来定水箱(蒸汽室),又叫一体模。
塑料发泡成型工艺:第四章 通用泡沫塑料

操作步骤 ➢ 先从模腔通入0.1~0.2MPa蒸汽,预热30s ➢ 将脱模剂涂在模腔表面,通入压缩空气,将
珠粒吹入并填满型腔 ➢ 模具装在液压机上,控制蒸汽压力
0.15~0.2MPa,110~130℃加热约1min后,通 入冷却水。
二、乳液法泡沫塑料的生产工艺
原理:以乳液法聚合的PS粉状树脂为原料,与发 泡剂混合,加热加压使混合物熔结成毛坯,然 后加热发泡制成泡沫塑料。
EPS制品的制备
使用可发性PS粒料制造泡沫制品的生产过 程,通常分为预发泡、熟化与模塑三道工序。
2. EPS的预发泡
按加热方式不同,可分为: ➢ 红外线预发泡 ➢ 热空气预发泡 ➢ 热水预发泡 ➢ 蒸汽预发泡:密度大于0.012g/cm3 ➢ 真空预发泡:可生产密度小于0.012g/cm3的
EPS
烷、异戊烷 ➢ 阻燃剂 ➢ 其他助剂
2.工艺流程
浸渍工艺参数:体系内压力不超过1MPa;料温 80~90℃,恒温4~12小时(由颗粒大小决定), 降温至40℃以下出料,冷却后用自来水清洗、吹 干。注意:不要烘干。
EPS珠粒要求:发泡剂含量约为6%(5.5~7.5%), 表观密度0.68g/cm3,颗粒的直径范围0.25~2mm。 制造密度偏小的泡沫塑料制品时,宜用直径偏大 的珠粒。注意可发性聚苯乙烯珠粒储存时,一定 要密封包装,低温储存。
案例:EPS包装制品的制造
(1)主要设备 ➢ 包装成型机:液压机 ➢ 模具:材料为铝合金
➢ 加料喷枪
利用压缩空气通过束节增加压力,然后体积膨 胀,产生负压,使PS珠粒借压缩空气带入模 腔。
(2)操作步骤 ➢ 模具先通入0.1~0.2MPa蒸汽,预热30s ➢ 开启上下气箱板的出气口,用加料喷枪将珠粒
结构发泡成型浅悉

结构发泡成型浅悉结构发泡工序从注塑工艺演变而来,生产出的零件外表完整,模芯呈蜂窝状,强重比相当高,能应用于承重材料。
要生产出发泡内芯,可以将惰性气体(通常是氮)直接射入熔融物,也可以用化学发泡剂(氮和二氧化碳)产生的气体,预先与树脂混合。
这一工艺需要在模具一部分内注入熔体,或进行“缺料”填充。
气压致使熔体膨胀,从而填满整个模穴。
当树脂与冷模面接触时,就形成坚固的外表层,而内核的发泡气体则发泡膨胀,在零件内部形成多泡孔结构。
完成后的是产品内层为蜂窝状结构,外表则坚硬稳固。
通过增加横截面的坚硬度,坚固的外表层使结构发泡零件具备独有的强度和硬度。
可采用多种工序来生产结构发泡部件。
低压法最为常见。
在这一方法中,通过氮气或化学发泡剂释放的气体(氮或二氧化碳)使熔融物发泡膨胀。
熔融物中能产生2.1至3.4兆帕的气压,足以膨胀树脂来填满整个模穴。
运用低压法填注并填满模具所需的压力仅为注塑法的10%。
需要特殊设备才能使用氮气。
蓄能器就是用来在压力下储存氮气/混合气体,直至将其注入模穴。
采用化学发泡剂需先用机械将其与树脂混合,再注入铸模机。
这个过程中,还要用到带截流装置喷头的标准注塑机或其他特殊设计的机器另两种可选来生产结构发泡部件的方法是高压法和气体反压法,但应用较少。
高压法是将含有气体的熔融物完全注满整个模穴。
既可以在留有膨胀空间的特殊模具内通过收缩其内芯来制造发泡内芯,也可以使发泡剂膨胀,将原料推回至热流道系统,从而产生发泡内芯。
气体反压法将在下一期栏目中介绍。
优点选择结构发泡成型的主要原因是,部件具有外表层坚固而内芯呈蜂窝状的结构(如图1所示),具有较高的强重比。
这一结构能在需要增加硬度时增加零件厚度,但重量不会随之增加。
其他优点包括:• 降低内应力• 提升空间稳定性• 增强零部件的坚固性• 可在零件中加入高性能设计• 能达到不同的模壁厚度• 可减少/消除缩痕• 对铸模机锁模吨位的要求较低• 能制造大型零部件缺点主要缺点为零件表面呈旋涡状纹理,必须加以修整才能获得满意的外观。
PU发泡工艺介绍PPT课件

• 伯羟基含量:伯羟基含量越高则聚醚多元醇的反 应活性越高;
• 粘度:粘度越低则原料的流动性越好,加工性能 就越好,及混合程度;
. 16
聚氨酯原材料-聚醚组合料
• 固含量: 固含量越高则泡沫产品硬度越高;
• 粘度: 与固含量相关,固含量越高则粘度越高; 粘度越低则原料的流动性越好,加工性能 就越好;
C-225
三乙醇胺 (85%)
水
称量 搅 拌
进料罐
P1
M
计量泵
P2
M
计量泵
高压 混合
P3
M
计量泵
ISO
M
计量泵
.
聚醚组合料
• 将聚醚,水,催化剂和稳定剂按一定的比例配制后搅拌均匀的体系; 也称为A料
• 常见的配方:
. 22
工艺流程
• 原料检验
•
羟值,含水量,固含量,NCO含量等原材料性能;
• 配料
•
按配方配制聚醚组合料;
• 浇注
•
按一定的轨迹,一定的流量,一定的浇注时间向模具
中进行投料并控制原料的温度,模具的温度以及浇注时的
. 1
课程目标
• 介绍聚氨酯发泡工艺基础原理 • 发泡设备、模具的基础知识 • 工业生产安全防范
. 2
课 程 目录
• 聚氨酯的发展史 • 聚氨酯的分类 • 原料的介绍 • 聚氨酯的发泡原理 • 影响发泡的因素 • 配方制作基本要素 • 脱模剂原理及选择 • 发泡设备简单介绍
.
• 发泡模具简单介绍 • 生产工艺流程解析 • 常见问题分解 • 工业生产安全防范 • 聚氨酯发展趋势 • 知识要点回顾 • 持续改进(发泡工艺) • 经验分享
模具结构图示(1)
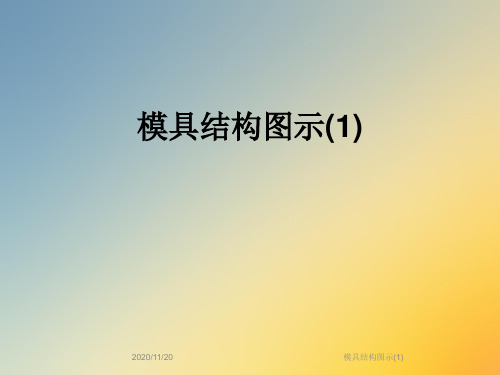
4.2 注塑模具标准模架
• 4.2.1 标准模架分类 • 按进料口(浇口)的形式模架分为大水口模架和小水口模
架两大类,香港地区将浇口称为水口,大水口模架指采用 除点浇口外的其他浇口形式的模具(二板式模具)所选用的 模架,小水口模架指进料口采用点浇口模具(三板式模具) 所选用的模架。
以上的工作位置。分为单注塑头多模位、多注塑头单模位 和多注塑头多模位注塑机三种。 ‘
• 如图5—5所示为单注塑头多模位注塑机,图5—6所示
为多注塑头单模位注塑机,图5—7所示为多注塑头多模 位注塑机。这些注塑机主要用来成型两种以上颜色或物料 的制品,可实现多模注塑,适应大批量生产,能提高生产 效率。
• (5)顶出机构 • 顶出机构是指模具分型以后将塑件顶出的装置(又称脱
模机构)杆、复位杆、顶杆固定扳、顶板、主流道拉料杆 等组成。
模具结构图示(1)
• (6)冷却和加热系统 • 为了使熔融塑料在模具型腔内尽快固化成型,提高生
产效率,一些塑料成型时必须对模具进行冷却,通常是在 模具上开设冷却水道,当塑料充满型腔并经一定的保压时 间后,水道通以循环冷水对模具进行冷却。
• 注塑成型设备主要是用来成型塑料制品,所以注塑成
型设备俗称注塑机。如图所示为一台往复螺杆式注塑机、 主要由合模装置、注塑装置、液压传动系统和电气控制系 统组成。
模具结构图示(1)
模具结构图示(1)
模具结构图示(1)
模具结构图示(1)
5.1 注塑成型设备的分类
•
近年来注塑机发展很快,种类日益增多,分类方式也
• 形式,设计的模具大致结构如图所示(B形式模架)。其模
架型号为:
• 1520—B—I一40—40—60,该代码表示规格为大水口、
发泡模具设计详解

一、发泡模成型机的原理1、发泡原材料的种类:EPS,EPP,EPE,EPO等。
2、成型原理:合模,加料,利用蒸汽加热成型,再冷却,脱模。
二、EPS模具总体结构根据机型的种类来设计模具,与机台配套。
1、一体模:台湾机、方圆机、等机台没有标准水箱,必须根据产品排模来定水箱(蒸汽室),又叫一体模。
2、三片式模具:都具有三片板:凸模板、凹模板、枪板凸模板来固定连接凸模型腔;凹模板用来固定连接凹模型腔;枪板也叫做后封板、背板、主要装顶杆套和料枪。
3、压料:为凸模与凹模配合,方便预开加料成型而设计的一种结构,起到预开加料时不漏料。
根据水箱的合模台阶、模板来计算;压料有离空和没有离空两种。
没有离空的,凹凸模的压料相同;有离空的,凹模压料加离空等于凸模压料,凹模压料不少于10 mm。
4、法兰边:也就是凹模与凹模板连接处的空间,方便安装螺丝钉。
根据水箱合模台阶和模板来定,一般做到15 mm左右为宜,不能少于10mm;还有一种,从模板下面往上面套,叫反托,反托高度根据模板的厚度来定,如库尔特机型,一般采用反托式,日本机型一般采用正面安装,有法兰边。
5、壁厚:EPP模具的壁厚一般在15 mm左右;EPS模具、EPO模具的壁厚在8~10 mm之间;EPE模具的壁厚一般在15 mm,除客户特别说明要求。
6、缩水:一般EPS模具材料的缩水为0.3%,倍率低的客户要求提供0.25%、0.2%等;EPO材料一般在0.9%~1.0%之间;EPP、EPE材料根据倍率的不同,缩水也不同;EPP、EPE材料又分JSP/KANEKA原料等,缩水又不同7、气眼:∮4、∮6、∮8、∮10、∮12等规格,有条型式和针式两种类型。
EPS原材料模具,采用针式气眼比较多,EPP、EPE等原材料模具采用条型式(平面)比较多、侧面一般用针式;气芯按材质分,有铝气芯,铜气芯、不锈钢气芯,常用的是铝气芯。
针孔:一些死角地方,加针孔在∮0.6~0.8mm之间。
发泡成型原理概论
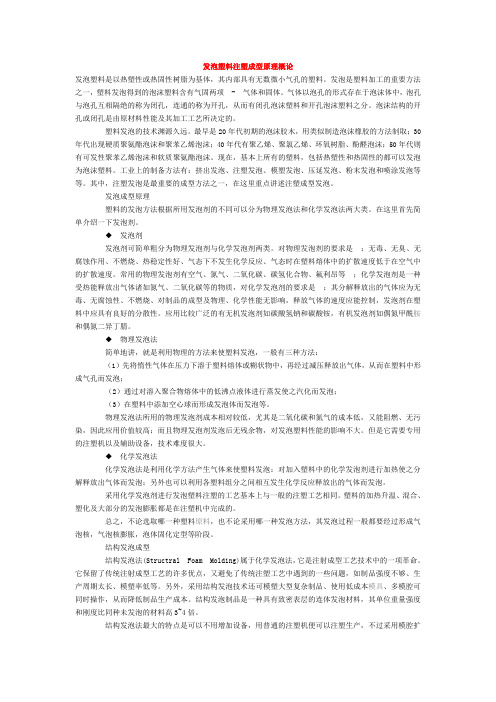
发泡塑料注塑成型原理概论发泡塑料是以热塑性或热固性树脂为基体,其内部具有无数微小气孔的塑料。
发泡是塑料加工的重要方法之一,塑料发泡得到的泡沫塑料含有气固两项- 气体和固体。
气体以泡孔的形式存在于泡沫体中,泡孔与泡孔互相隔绝的称为闭孔,连通的称为开孔,从而有闭孔泡沫塑料和开孔泡沫塑料之分。
泡沫结构的开孔或闭孔是由原材料性能及其加工工艺所决定的。
塑料发泡的技术渊源久远。
最早是20年代初期的泡沫胶木,用类似制造泡沫橡胶的方法制取;30年代出现硬质聚氨酯泡沫和聚苯乙烯泡沫;40年代有聚乙烯、聚氯乙烯、环氧树脂、酚醛泡沫;50年代则有可发性聚苯乙烯泡沫和软质聚氨酯泡沫。
现在,基本上所有的塑料,包括热塑性和热固性的都可以发泡为泡沫塑料。
工业上的制备方法有:挤出发泡、注塑发泡、模塑发泡、压延发泡、粉末发泡和喷涂发泡等等。
其中,注塑发泡是最重要的成型方法之一,在这里重点讲述注塑成型发泡。
发泡成型原理塑料的发泡方法根据所用发泡剂的不同可以分为物理发泡法和化学发泡法两大类。
在这里首先简单介绍一下发泡剂。
◆发泡剂发泡剂可简单粗分为物理发泡剂与化学发泡剂两类。
对物理发泡剂的要求是:无毒、无臭、无腐蚀作用、不燃烧、热稳定性好、气态下不发生化学反应、气态时在塑料熔体中的扩散速度低于在空气中的扩散速度。
常用的物理发泡剂有空气、氮气、二氧化碳、碳氢化合物、氟利昂等;化学发泡剂是一种受热能释放出气体诸如氮气、二氧化碳等的物质,对化学发泡剂的要求是:其分解释放出的气体应为无毒、无腐蚀性、不燃烧、对制品的成型及物理、化学性能无影响,释放气体的速度应能控制,发泡剂在塑料中应具有良好的分散性。
应用比较广泛的有无机发泡剂如碳酸氢钠和碳酸铵,有机发泡剂如偶氮甲酰胺和偶氮二异丁腈。
◆物理发泡法简单地讲,就是利用物理的方法来使塑料发泡,一般有三种方法:(1)先将惰性气体在压力下溶于塑料熔体或糊状物中,再经过减压释放出气体,从而在塑料中形成气孔而发泡;(2)通过对溶入聚合物熔体中的低沸点液体进行蒸发使之汽化而发泡;(3)在塑料中添加空心球而形成发泡体而发泡等。
微孔发泡成型技术
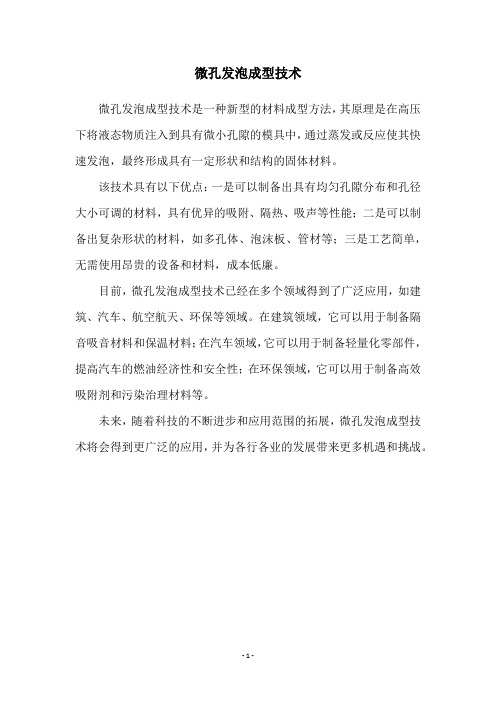
微孔发泡成型技术
微孔发泡成型技术是一种新型的材料成型方法,其原理是在高压下将液态物质注入到具有微小孔隙的模具中,通过蒸发或反应使其快速发泡,最终形成具有一定形状和结构的固体材料。
该技术具有以下优点:一是可以制备出具有均匀孔隙分布和孔径大小可调的材料,具有优异的吸附、隔热、吸声等性能;二是可以制备出复杂形状的材料,如多孔体、泡沫板、管材等;三是工艺简单,无需使用昂贵的设备和材料,成本低廉。
目前,微孔发泡成型技术已经在多个领域得到了广泛应用,如建筑、汽车、航空航天、环保等领域。
在建筑领域,它可以用于制备隔音吸音材料和保温材料;在汽车领域,它可以用于制备轻量化零部件,提高汽车的燃油经济性和安全性;在环保领域,它可以用于制备高效吸附剂和污染治理材料等。
未来,随着科技的不断进步和应用范围的拓展,微孔发泡成型技术将会得到更广泛的应用,并为各行各业的发展带来更多机遇和挑战。
- 1 -。
- 1、下载文档前请自行甄别文档内容的完整性,平台不提供额外的编辑、内容补充、找答案等附加服务。
- 2、"仅部分预览"的文档,不可在线预览部分如存在完整性等问题,可反馈申请退款(可完整预览的文档不适用该条件!)。
- 3、如文档侵犯您的权益,请联系客服反馈,我们会尽快为您处理(人工客服工作时间:9:00-18:30)。
• 1.1 蒸汽加热模压法成型模具
• 按加热方式又分为蒸缸发泡和液压机直接通蒸汽发泡两种。
• 1.1.1 蒸缸发泡法适宜生产小型、薄壁与形状复杂的塑 件,即将预胀物填满模具后放入蒸缸中,然后通蒸汽加热成 型。蒸汽压力与加热时间应视塑件大小与厚度而定,一般为 0.05~0.10MPa,10~50min。模内预胀物受热软化,经膨 胀互相熔接而成整体,冷却脱模即制得泡沫塑料产品。此法 所用模具简单,但工人劳动强度较大,难于实现机械与自动 化生产,如图图9-1(a)所示。
• (3)加强冷却水流量。
2、模具设计
• 2.1模具制造材料
2.2模具分型面选择
• 分型面尽量选用平面、避用曲面 • 结构力求简单、易于制模和操作方便 • 便于设置加料口 • 便于取模 • 尽量不影响模样形状和尺寸精度
•
分模线:根据产品的最大外形做分模线,再做压料,分
出凹凸模腔,分析加工工艺,方便加工,打
1.2 可发性聚苯乙烯泡沫塑料典型模具
• 1.2.1 图9-3所示为成 型某防震包装用发泡体 的模具,用于水平开模 式的发泡成型设备。
图9-3 水平开模模具结构 1-阴模体 2-进料管 3-阴模腔壁 4-螺钉 5,14-蒸汽进口 6-阳模体 7,12-压缩空气进口 8-阳模底板 9-模座 10,11-冷水出口 13-阴模底板
•
EPP、EPE一般采用气芯与气芯为20×20间距,除客
户特别要求。
•
气芯要敲平,气芯必须分三次敲到位,一次敲平的气
0.25%、0.2%等; • EPO材料一般在0.9%~1.0%之间; • EPP、EPE材料根据倍率的不同,缩水也不同; • EPP、EPE材料又分JSP/KANEKA原料等,缩水又不同
2.6气孔和气塞设置
•
气眼:∮4、∮6、∮8、∮10、∮12等规格,有条型式和针
式两种类型。
•
EPS原材料模具,采用针式气眼比较多,
大家应该也有点累了,稍作休息
大家2 图9-4所示为板材手动蒸箱压模,一次可成型三块 板材,模套由件5和件8组成,并通过件12连接。
图9-4 板材手动蒸箱压模 1-铰链螺栓2-螺母3-上模板4-隔板5-模套6-下模板 7-螺母8-模套组合件9-螺母10-销11-轴12-长螺栓
• 气芯、 抛光等;不好做到位的地方做拼块,拼块最好能做限 位,方便安装;产品有倒扣的、侧面有穿孔的,做滑块抽芯 ;根据凹、凸模腔,做模具壁厚,根据客户要求的壁厚来做 ,把型腔背面多余的料去掉,尽量做到壁厚均匀,背面尽量 做脱模斜度,方便木样在翻砂时好脱模,做好造型后,考虑 顶杆、料枪位置、背面的加强筋、支柱位置,可以先做2D排 模图,设计好顶杆、料枪位置、支柱位置。
1.3.2普通注射机低发泡注射成型
• 在普通注射机上也可以进行低发泡注射成型。一般 有两种方法:一是减量注射法,二是瞬间开模注射 法。两种方法都必须对原有模具进行适当改造。改 造的内容如下:
• (1)增加排气通路 把原来分型面上的排气槽增加 ,把通过拼缝和推杆排气的气隙增大。
• (2)增加推杆数量 在试模后观察,发现有推杆处 受力过大的现象时,再适当增加推杆数量,或加大 推杆直径。
2.3加料口
• 料枪孔,比料枪嘴大0.2~0.5mm之间
2.4模具壁厚
• • EPP模具的壁厚一般在15 mm左右; • EPS模具、EPO模具的壁厚在8~10 mm之间; • EPE模具的壁厚一般在15 mm,除客户特别说明要求。
2.5泡沫塑料收缩率与尺寸精度
• 缩水: • 一般EPS模具材料的缩水为0.3%,倍率低的客户要求提供
发泡成型模具
目录
• 1、消失模成型模具种类 • 1.1 蒸汽加热模压法成型模具 • 1.2 低发泡注射成型模 • 2、模具设计 • 2.1 模具制造材料和参数设计 • 2.2 蒸缸模具设计 • 2.3 压机气室模具设计 • 2.4 低发泡注射成型模具设计
• 1、发泡成型模具种类
•
• 生产中常用有:
• (1)发泡时胀模 • (2)填充不足 • (3)发泡不完全 • (4)脱模时局部膨胀或变形 • (5)脱模时有冷却水从型腔中喷出 • (6)脱模困难
1.3 低发泡注射成型模
• 1.3.1低发泡注射成型模具基本结构 • 低发泡注射成型模的基本结构与普通注射成型模具
基本相同,其设计方法也与注射成型模具极为类似 。由于发泡材料的物理性质与非发泡料材有所不同 ,因此在个别部位的设计上有其特殊要求: • (1)浇注系统 • (2)型腔排气 • (3)冷却系统 • (4)脱模机构 • (5)型腔数
图9-1 模压发泡成型模具 1-气孔 2-上气室 3-型芯 4-加料管 5-模框 6-下气室
• 1.1.2 液压机直接通蒸汽发泡法适宜生产厚度较 大的泡沫板材。成型时常用气送法将粒料加入液压 机上的模具中。模具开有若干个0.1~O.4mm的通 气孔(或槽),当模具型腔装满预胀物后,直接通入 O.1~O.2MPa的蒸汽,并使温度升至11O℃左右, 此时模内预胀物膨胀并粘接成整体。关闭蒸汽,保 持一定时间(1~2min),通水冷却后脱模。此发泡法 的优点是塑化时间短、冷却定型快、塑件内珠粒熔 接良好、质量稳定、生产效率高,能实现机械化与 自动化生产,如图9-1(b)所示。
•
EPP、EPE等原材料模具采用条型式(平面)比较多、
侧面一般用针式;
•
气芯按材质分,有铝气芯,铜气芯、不锈钢气芯,常
用的是铝气芯。
• 针孔:一些死角地方,加针孔在∮0.6~0.8mm之间
•
打气眼:先用钻头打好孔,一般钻头选用比气眼小
0.3~0.4 mm,气芯分布均匀。
•
EPS一般采用气芯与气芯为25×25间距;
• 1.2.3 图9-5为包装盒 机动发泡模,使用卧式 泡沫塑料成型机。
图9-5 包装盒机动发泡模 1,4,12,15-螺钉 2-回汽水管 3,5-定模汽室板 6-料塞 7-挡销 8-动模汽室板 9,17-密封环
10-成型套 11-外套 13,14-型芯 16-料套
1.3 由于模具原因而使制品出现的缺陷