焦炉
焦炉的工艺流程

焦炉的工艺流程
焦炉是用于将煤炭等原料加热至高温,使其发生化学反应生成焦炭的设备。
其工艺流程主要包括以下几个步骤:
1. 原料准备:将煤炭进行粉煤打散、混匀等处理,以便于均匀加热和反应。
2. 装料:将准备好的煤炭原料通过装料设备送入焦炉的装料皮带或装料斗,分层装料,保持炉内良好的通风和燃烧条件。
3. 加热:在焦炉内点火燃烧,同时通过给煤料注入空气使之燃烧,通过内部燃烧释放的高温使煤料升温,使其发生干馏反应,生成焦炭。
4. 脱硫:焦炉内的煤料在高温反应过程中会产生气体,其中含有硫化物等有害物质。
因此,在焦炉顶部设置脱硫设备,将煤气中的硫化物进行脱硫处理,减少环境污染。
5. 焦炭收集:焦炉产生的焦炭经过冷却后,通过焦炉底部的排焦设备将焦炭推出焦炉,经过输送装置收集和储存。
6. 煤气收集:焦炉反应产生的煤气经过冷却除尘处理,收集其中的可燃气体。
这些煤气可以用于发电、供热、供气等。
7. 余热利用:在焦炉操作过程中会产生大量的余热,该余热可以通过余热锅炉等设备进行回收利用,用于提供热能或发电。
需要注意的是,焦炉是高温高压设备,操作过程需要严格控制温度、压力以及煤气和烟尘的排放。
同时,焦炉操作过程中会产生大量的气体、灰尘和有害物质,需要进行处理,以减少对环境的影响。
精选第三章炼焦炉及生产过程
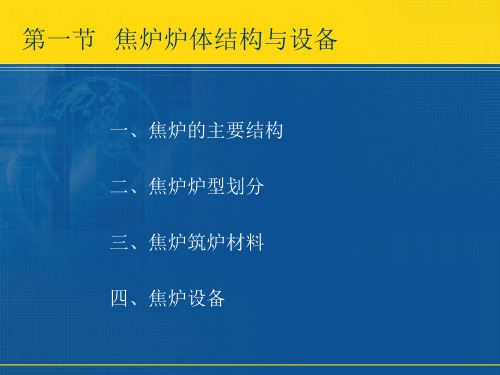
4、炉顶区
炭化室盖顶砖以上部位为炉顶区(图3-5),该区砌有装 煤孔、上升管孔、看火孔、烘炉孔以及拉条沟等。为减少炉 项散热,炉顶不受压部位砌有隔热砖。炉顶区的实体部位设 置平行于抵抗墙的膨胀缝,烘炉孔在焦炉转为正常加热投产 时用塞子砖堵死。为防止雨水对焦炉表面的侵蚀,炉顶表面 用耐磨性好的缸砖砌筑。
4、炉顶区
图3-5 JN型焦炉炉顶区构造图 1-装煤孔;2-看火孔;3-烘炉孔;4-挡火砖
5、焦炉基础和烟道
焦炉的基础位于炉体的底部,支承整个炉体、炉体设备 和焦炉机械的重量,并把重量传到地基上。焦炉基础的结构 形式随炉型和加热煤气供入方式而不同,下喷式焦炉的基础 有地下室(参见图3-1),它是由底板、顶板和支柱组成, 整个焦炉砌在焦炉顶板平台上。浇顶板时,按焦炉膨胀后的 尺寸埋设好下喷煤气管接口。
目前国内建设的焦炉,火道主要采用双联和两分结构。 大型焦炉均采用双联火道结构。
2、按对加热用煤气种类的适应性划分
焦炉加热用的煤气通常分成两大类:富煤气即焦炉煤气和 贫煤气。贫煤气主要包括高炉煤气、发生炉煤气等。焦炉煤 气的热值高,供焦炉加热时不需经蓄热室预热。而高炉煤气 或发生炉煤气加热焦炉时,必须经蓄热室预热。
5、焦炉基础和烟道
为了降低基础顶板的温度。在焦炉砌体与基础顶板之 间,一般砌有4~6层红砖隔热,由于焦炉砌体没有预留横 向的膨胀缝,这样当焦炉烘炉时,顶板上的焦炉砌体必然 向两侧膨胀而产生滑动,为了利于这种膨胀产生的滑动, 在砌筑焦炉之前,在隔热层上沿机焦两侧向中心铺置一定 宽度的滑动层,然后再进行炉体砌砖。
焦炉的加热系统若只能使用富煤气加热,这种焦炉称为 单热式焦炉。加热系统既可用富煤气加热,又可用贫煤气加 热,这样的焦炉称为复热式焦炉。复热式焦炉有两套煤气供 入系统,分别提供焦炉煤气和贫煤气。当采用贫煤气加热时, 煤气须经蓄热室预热。国内的大中型炼焦厂在建设焦炉时, 一般选择建设复热式焦炉,通过向焦炉提供低热值煤气加热, 顶替出焦炉煤气,增加城市煤气供应。对于冶金企业焦化厂, 为了回收利用高炉煤气加热,同样推荐建设复热式焦炉 。
焦炉炉型分类

焦炉炉型分类焦炉是冶金和化工行业中常见的设备,用于生产高质量的焦炭。
根据不同的生产需求和工艺特点,焦炉可以分为多种类型。
本文将就焦炉炉型分类进行详细介绍。
一、按照结构形式分类1.立式焦炉立式焦炉是指筒体与地面垂直的一种结构形式。
它主要由筒体、加料装置、出料装置、风道系统、冷却系统等组成。
立式焦炉具有结构简单、操作方便等优点,但因其筒体高度较大,会增加生产难度和安全风险。
2.水平焦炉水平焦炉是指筒体与地面平行的一种结构形式。
它主要由筒体、加料装置、出料装置、风道系统、冷却系统等组成。
水平焦炉相对于立式焦炉来说,具有占地面积小、操作方便等优点,但因其筒体长度较大,会增加生产难度和安全风险。
3.倾斜式焦炉倾斜式焦炉是指筒体与地面呈倾斜状态的一种结构形式。
它主要由筒体、加料装置、出料装置、风道系统、冷却系统等组成。
倾斜式焦炉相对于立式焦炉和水平焦炉来说,具有结构紧凑、操作方便等优点,但因其筒体倾斜角度较大,会增加生产难度和安全风险。
二、按照工艺特点分类1.非恒压焦炉非恒压焦炉是指在生产过程中,筒体内部的压力不稳定,并且无法控制的一种类型。
它主要用于生产低质量的焦炭,具有生产效率高、成本低等优点。
2.恒压焦炉恒压焦炉是指在生产过程中,筒体内部的压力稳定,并且可以通过调整风量和排气量来控制的一种类型。
它主要用于生产高质量的焦炭,具有产品品质好、节能环保等优点。
3.间歇式焦炉间歇式焦炉是指在生产过程中,每次只加入一定数量的原料,在原料完全转化为焦后再进行出炉,然后再加入下一批原料的一种类型。
它主要用于生产高质量的焦炭,具有产品品质好、能耗低等优点。
4.连续式焦炉连续式焦炉是指在生产过程中,原料不断地加入和转化为焦,同时焦炭不断地出炉的一种类型。
它主要用于生产大量的焦炭,具有生产效率高、成本低等优点。
三、按照操作方式分类1.手工操作焦炉手工操作焦炉是指在生产过程中,需要人工进行加料、出料等操作的一种类型。
它主要用于小型冶金企业或者在资源匮乏地区使用,具有投资成本低、操作简单等优点。
焦炉工艺流程

焦炉工艺流程
焦炉工艺流程是将煤炭进行加热、干馏和碳化的过程,主要用于
生产焦炭和煤焦油。
焦炉工艺流程包括以下几个主要步骤:
1. 进料:将煤炭通过煤气管道送入焦炉内。
进料的方式可以有
多种,常见的有上料斗、上料车等。
2. 预热:在焦炉顶部设有预热炉,用于对进料进行预热。
预热
有助于提高煤炭的热解效率。
3. 碳化:将预热后的煤炭送入焦炉的碳化室。
碳化室内温度通
常在1000℃左右,煤炭在高温下进行热解,产生焦炭和煤焦油。
4. 焦炭收集:焦炭通过焦炉底部的焦渣窖排出,在焦渣窖中进
行冷却和固化。
焦渣中还含有焦煤油,可以通过相应的工艺进行回收。
5. 煤焦油收集:焦炉中产生的煤焦油通过管道输送至相应的收
集设备中,进行冷凝和分离,得到煤焦油和其它副产品。
6. 煤气的处理和利用:焦炉中产生的煤气含有一定的燃烧热值,可以通过煤气净化、加热和回收等工艺,进行利用或回收。
7. 尾气处理:焦炉尾气中含有一定的有害物质,需要进行脱硫、脱尘等处理,以达到环保要求。
总的来说,焦炉工艺流程包括煤炭进料、预热、碳化、焦炭收集、煤焦油收集、煤气处理和利用、尾气处理等步骤,通过这些步骤可以
将煤炭转化为焦炭和煤焦油,并对煤气和尾气进行全面处理,实现资
源的利用和环境的保护。
国内外焦炉现状及其发展

国内外焦炉现状及其发展焦炉是冶金炼焦的关键设备,广泛应用于钢铁、化工、煤炭等行业。
其主要功能是将煤炭进行高温热解反应,得到焦炭和含有大量有机物的煤气。
本文将从国内外焦炉的现状及发展方向两个方面进行探讨。
一、国内焦炉现状及问题国内焦炉行业起步较早,以大型钢铁企业为主要用户。
2000年以来,国内焦炉产能逐年增加,2019年全国总产能达到3.6亿吨。
然而,国内焦炉产业存在一些问题。
1.能耗高:传统焦炉存在高温热量的浪费现象,能耗较高。
此外,焦炉的调温技术相对落后,无法实现精确控制,进一步增加了能耗。
2.环境污染:焦炉炼焦过程会排放大量有害气体和颗粒物,对环境产生严重污染。
尽管国内采取了一系列措施来减少焦炉排放污染,但仍然面临严峻挑战。
3.技术水平不高:国内焦炉设备普遍过时,技术水平相对滞后。
相比于国外的先进技术,国内焦炉的自动化程度低、控制精度不高,影响了炼焦效率和产品质量。
二、国内焦炉发展方向为了解决上述问题,国内焦炉行业正朝着以下几个方向进行发展:1.提高能源利用效率:通过改进煤气回收和利用技术,提高焦炉能源利用效率,降低能耗。
采用先进的煤气净化技术,可以将高热值煤气转化为燃料或电力,实现能源的综合利用。
2.推广清洁炼焦技术:发展低排放、零排放的焦炉技术,减少炼焦过程中的排放污染物。
采用干法炼焦技术、焦炉脱硫装置等,可以有效控制二氧化硫、颗粒物等污染物的排放。
3.提高焦炉自动化程度:引进国外先进的自动化控制系统,提高焦炉的自动化水平。
通过自动化控制,可以实现煤气的精确配比和温度的精确控制,提高炼焦效率和产品质量。
4.创新型焦炉技术:国内一些高校和科研机构正在开展创新型焦炉技术的研究。
比如,高温氧化炉技术、微波炉技术等,这些新技术有望在未来几年内得到商业化应用。
三、国际焦炉现状及发展方向国际焦炉行业发展较为成熟,主要集中在发达国家和地区,例如中国、日本、美国和欧洲等。
国际焦炉行业的发展主要表现在以下几个方面:1.推广先进的清洁炼焦技术:国际焦炉行业对环境保护的要求较高,通过采用先进的清洁炼焦技术,减少污染物排放。
焦炉分析报告

焦炉分析报告1. 研究背景焦炉是冶金炼铁过程中至关重要的设备之一。
它用于将焦炭转化为高温下的可燃气体,为铁矿石还原提供热量和还原剂。
对焦炉进行分析可以帮助我们了解其工作状态、优化操作以及改善炼铁过程。
本报告旨在通过对焦炉进行分析,提供有关其性能和操作的详尽评估。
2. 分析方法为了对焦炉进行全面的分析,我们采用了以下方法:2.1 数据收集与处理我们收集了焦炉操作过程中的相关数据,包括温度、压力、流量等。
通过对这些数据进行统计分析和处理,我们获得了焦炉在不同时间点的运行状态和性能指标。
2.2 热力学模型我们基于热力学原理建立了一个简化的热力学模型来描述焦炉的工作过程。
该模型考虑了焦炉内部的燃烧反应、传热和质量平衡等因素,可以预测焦炉在不同操作条件下的性能。
2.3 数值仿真基于上述热力学模型,我们进行了数值仿真来模拟焦炉的工作过程。
通过改变不同的操作参数,我们评估了这些参数对焦炉性能的影响,并找到了最佳的操作条件。
3. 焦炉性能评估3.1 燃烧效率燃烧效率是评估焦炉性能的关键指标之一。
我们通过分析焦炉内的燃烧反应过程,计算了焦炉的燃烧效率。
根据我们的分析结果,焦炉的燃烧效率达到了XX%。
3.2 热能利用率热能利用率是另一个重要的评估指标。
我们通过计算焦炉输入和输出的热能量,确定了焦炉的热能利用率。
结果表明,焦炉的热能利用率为XX%。
3.3 炉渣质量炉渣质量对焦炉的工作稳定性和铁矿石还原有重要影响。
我们分析了焦炉内的炉渣成分并评估了其质量。
根据我们的分析结果,焦炉的炉渣质量符合标准要求。
3.4 排放物浓度焦炉在运行过程中会产生一些有害气体,例如二氧化硫和氮氧化物。
我们测量了这些排放物的浓度,并分析了其对环境的潜在影响。
根据我们的测量结果,焦炉的排放物浓度在国家排放标准范围内。
4. 优化建议基于对焦炉的分析和评估,我们提出了以下优化建议:•调整燃料配比:通过调整焦炭、煤和空气的配比,可以提高焦炉的燃烧效率和热能利用率。
焦炉的生产原理

焦炉的生产原理焦炉是一种用来生产焦炭的设备,一般是由高炉、焦炉和焦风机三部分组成。
它的生产原理是通过在高炉中冶炼铁矿石时,将煤炭加热到高温,使其分解、燃烧产生煤气和固体残渣,然后通过冷却、净化获得质量较好的焦炭。
焦炉的主要生产原理如下:1. 炼焦煤的分解:炼焦煤中含有较高的固定碳和挥发分,以及少量的纯煤气。
在高温下,炼焦煤会分解成焦炭和煤气。
同时,分解过程中还会有一部分气体在炉内燃烧,释放出大量的热能。
2. 炉内气体生成:在焦炉中,炼焦煤在高温下分解时,会产生大量的煤气。
煤气的成分主要包括一氧化碳、二氧化碳、氮气、水蒸气和一些其他成分。
其中一氧化碳和水蒸气是重要的还原剂,可以在高炉内促进铁矿石的还原反应。
而二氧化碳则是高炉燃烧过程中的主要产物,对环境有一定的污染。
3. 炉渣生成:在焦煤的分解过程中,产生的固体残渣称为炉渣。
炉渣主要由非挥发分和灰分组成,其作用是吸收和净化高炉内的杂质和冶炼渣,以保证高炉冶炼过程的正常进行。
4. 焦炭的生成:在焦炉内,炼焦煤的分解过程中生成的煤气主要用于高炉内的还原反应,同时也用于加热炼焦煤。
在高温下,炼焦煤中的碳元素会重新排列和结构重组,形成质量较好的焦炭。
焦炭是冶炼铁矿石时的主要原料,它具有高强度、高燃烧性、高储存性等优点,对提高高炉冶炼效率和降低成本有重要作用。
5. 煤气的净化:在焦炉中产生的煤气含有一定量的不可燃和有害物质,如烟尘、硫化物和氨等。
为了减少环境污染和提高资源利用率,需要对煤气进行净化处理。
常见的净化方法包括除尘、脱硫和脱氮等。
除尘主要利用物理方法将煤气中的颗粒物去除,脱硫则利用化学方法将煤气中的硫化物去除,脱氮则通过化学吸收剂将煤气中的氮气去除。
总之,焦炉的生产原理主要在于将炼焦煤加热到高温,分解产生煤气和固体残渣,再通过冷却、净化等处理获得焦炭。
焦炭是冶炼铁矿石时的重要原料,对高炉冶炼效率和产品质量具有重要影响,同时焦炉的运行也对环境保护和资源利用起着重要作用。
焦炉、高炉、转炉煤气的区别
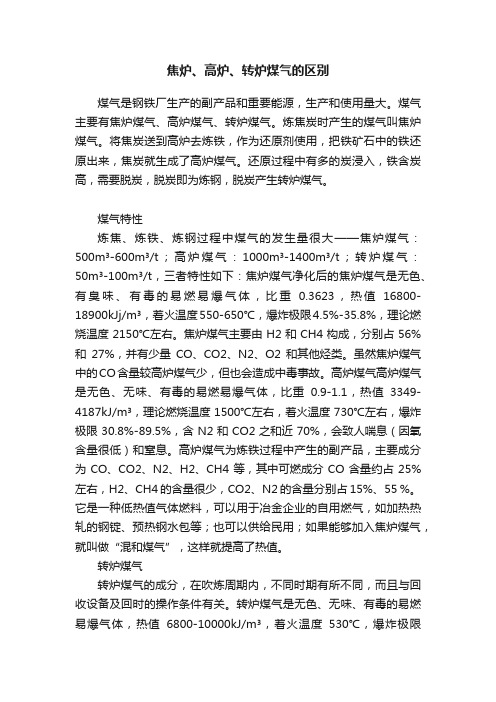
焦炉、高炉、转炉煤气的区别煤气是钢铁厂生产的副产品和重要能源,生产和使用量大。
煤气主要有焦炉煤气、高炉煤气、转炉煤气。
炼焦炭时产生的煤气叫焦炉煤气。
将焦炭送到高炉去炼铁,作为还原剂使用,把铁矿石中的铁还原出来,焦炭就生成了高炉煤气。
还原过程中有多的炭浸入,铁含炭高,需要脱炭,脱炭即为炼钢,脱炭产生转炉煤气。
煤气特性炼焦、炼铁、炼钢过程中煤气的发生量很大——焦炉煤气:500m³-600m³/t;高炉煤气:1000m³-1400m³/t;转炉煤气:50m³-100m³/t,三者特性如下:焦炉煤气净化后的焦炉煤气是无色、有臭味、有毒的易燃易爆气体,比重0.3623,热值16800-18900kJj/m³,着火温度550-650℃,爆炸极限4.5%-35.8%,理论燃烧温度2150℃左右。
焦炉煤气主要由H2和CH4构成,分别占56%和27%,并有少量CO、CO2、N2、O2和其他烃类。
虽然焦炉煤气中的CO含量较高炉煤气少,但也会造成中毒事故。
高炉煤气高炉煤气是无色、无味、有毒的易燃易爆气体,比重0.9-1.1,热值3349-4187kJ/m³,理论燃烧温度1500℃左右,着火温度730℃左右,爆炸极限30.8%-89.5%,含N2和CO2之和近70%,会致人喘息(因氧含量很低)和窒息。
高炉煤气为炼铁过程中产生的副产品,主要成分为CO、CO2、N2、H2、CH4等,其中可燃成分CO含量约占25%左右,H2、CH4的含量很少,CO2、N2的含量分别占15%、55 %。
它是一种低热值气体燃料,可以用于冶金企业的自用燃气,如加热热轧的钢锭、预热钢水包等;也可以供给民用;如果能够加入焦炉煤气,就叫做“混和煤气”,这样就提高了热值。
转炉煤气转炉煤气的成分,在吹炼周期内,不同时期有所不同,而且与回收设备及回时的操作条件有关。
转炉煤气是无色、无味、有毒的易燃易爆气体,热值6800-10000kJ/m³,着火温度530℃,爆炸极限18.2%-83.2%。
焦炉温度和焦炉压力制度

1、焦炉温度制度1.1标准温度与直行温度焦炉燃烧室的火道数量较多,为了均匀加热和便于检查、控制,每一个燃烧室的机、焦侧各选择一个火道作为测温火道,其温度分别代表机、焦两侧温度,这两个火道称为测温火道和标准火道。
其所测得的实际温度称为直行温度。
为保证全炉各燃烧室温度均匀,各测温火道温度与同侧直行温度的平均值不应超过±20℃,边炉相差不超过±30℃,超过此值的测温火道为温度不合格火道,并以均匀系数K均表示:K均二[(M—A机)+(M-A焦)]/2M;M焦炉燃烧室数;A机、A焦:机、焦侧测温火道温度不合格数。
直行温度不但要求均匀,还要求直行温度的平均值保持稳定,并用安定系数K安考核。
K安二(2N-(A,机+A'焦))/2N;N直行温度的测量次数;A,机、A,焦:全炉机、焦测直行平均温度与加热制度规定的该测标准温度相差超过±7℃的测量次数。
1.2横排温度同一燃烧室的各火道温度,称为横排温度θ每一个燃烧室各火道温度,应当由机侧向焦侧逐渐增高,要求从机侧第2火道至焦侧第2火道的温度均匀上升。
横排温度均匀系数二(考核火道数-不合格火道数)/考核火道数。
1.3边火道温度燃烧室两端的炉头火道,由于散热量大,温度较低。
为防止炉头焦炭不熟,以及装煤后炭化室头部降温过多,引起炉砖开裂变形,一般要求边火道温度低于标准温度的值在100°C以内。
为评定炉头温度的好坏,要求每一个炉头温度与该侧炉头平均温度差不超过±50℃。
1.4蓄热室顶部温度为防止因蓄热室高温而将格子砖烧熔,应严格控制蓄热室温度。
对于硅砖蓄热室,其顶部温度应控制在1320°C以下。
在一般情况下,蓄热室的高温事故应不容易发生,但是,当炭化室窜漏,荒煤气被抽到蓄热室内燃烧,砖煤气道煤气漏入蓄热室内燃烧,立火道煤气燃烧不充分,继续到蓄热室燃烧以及废气循环发生短路等,仍可能引起蓄热室高温事故,特别是当炉体衰老时容易出现上述情况。
焦炉工艺流程
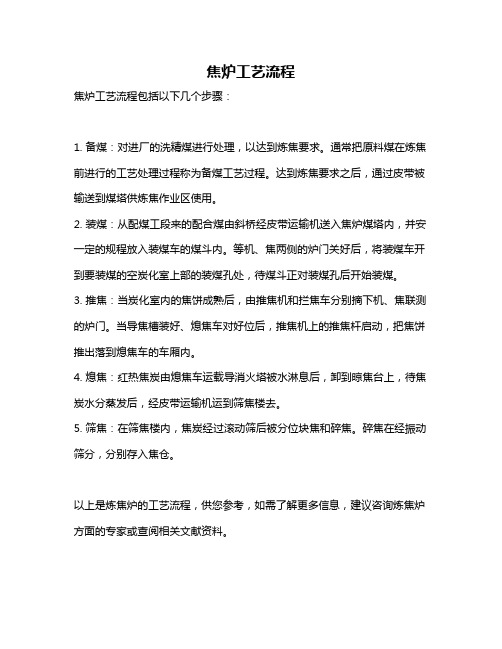
焦炉工艺流程
焦炉工艺流程包括以下几个步骤:
1. 备煤:对进厂的洗精煤进行处理,以达到炼焦要求。
通常把原料煤在炼焦前进行的工艺处理过程称为备煤工艺过程。
达到炼焦要求之后,通过皮带被输送到煤塔供炼焦作业区使用。
2. 装煤:从配煤工段来的配合煤由斜桥经皮带运输机送入焦炉煤塔内,并安一定的规程放入装煤车的煤斗内。
等机、焦两侧的炉门关好后,将装煤车开到要装煤的空炭化室上部的装煤孔处,待煤斗正对装煤孔后开始装煤。
3. 推焦:当炭化室内的焦饼成熟后,由推焦机和拦焦车分别摘下机、焦联测的炉门。
当导焦槽装好、熄焦车对好位后,推焦机上的推焦杆启动,把焦饼推出落到熄焦车的车厢内。
4. 熄焦:红热焦炭由熄焦车运载导消火塔被水淋息后,卸到晾焦台上,待焦炭水分蒸发后,经皮带运输机运到筛焦楼去。
5. 筛焦:在筛焦楼内,焦炭经过滚动筛后被分位块焦和碎焦。
碎焦在经振动筛分,分别存入焦仓。
以上是炼焦炉的工艺流程,供您参考,如需了解更多信息,建议咨询炼焦炉方面的专家或查阅相关文献资料。
炼焦炉规格

炼焦炉规格一、炼焦炉概述炼焦炉是一种用于将煤炭转化为焦炭的工业设备,广泛应用于钢铁、化工、建材等行业。
炼焦炉在我国的发展历史悠久,经过多次技术改造,现已具备较高的生产水平。
二、炼焦炉的规格分类1.按容量分炼焦炉按容量可分为小型、中型和大型。
小型炼焦炉容量一般在100吨/日以下,中型炼焦炉容量在100-300吨/日,大型炼焦炉容量在300吨/日以上。
2.按热工制度分炼焦炉按热工制度可分为室式炼焦炉和窑式炼焦炉。
室式炼焦炉采用间断式加热,窑式炼焦炉采用连续式加热。
3.按燃烧方式分炼焦炉按燃烧方式可分为气体燃烧、固体燃烧和混合燃烧。
气体燃烧主要用于气体燃料,固体燃烧主要用于固体燃料,混合燃烧则结合了气体和固体燃料的燃烧。
4.按焦炭用途分炼焦炉按焦炭用途可分为冶金焦炉、化工焦炉和建材焦炉。
冶金焦炉主要用于钢铁工业,化工焦炉用于生产焦油、氨等化工产品,建材焦炉用于生产水泥、陶瓷等建材产品。
三、炼焦炉的主要结构1.炉体炼焦炉炉体通常由炉墙、炉顶、支撑系统等组成。
炉墙和炉顶采用耐火材料砌筑,以确保炉内高温环境的稳定性。
2.炉衬炉衬是炼焦炉内部的一层保护层,通常采用硅酸盐耐火砖、高铝砖等材料制成。
炉衬的作用是保护炉体免受高温、高压等恶劣环境的侵蚀。
3.炉门及炉口炉门和炉口是炼焦炉进行装煤、出焦等操作的关键部件。
炉门设有观察窗、调节阀等装置,以便于观察炉内情况和调节焦炭质量。
4.烟道及通风系统烟道和通风系统是炼焦炉排放废气和调节炉内气氛的重要通道。
烟道设有除尘器、脱硫器等环保设施,以减少废气对环境的污染。
四、炼焦炉的工作原理炼焦炉在工作过程中,煤炭在高温条件下进行干馏,将煤中的挥发分去除,形成焦炭。
同时,煤中的有机物分解产生煤气、焦油等副产品。
煤气用于燃烧供给热量,焦油则作为化工原料回收。
五、炼焦炉的操作与维护1.装煤与出焦装煤时,应确保煤料均匀分布于炉内,避免局部过热或过焦。
出焦时,应根据焦炭质量要求,控制出炉温度和炭化时间。
焦炉资料

《焦炉结构与设备》焦炉是以煤为原料,经过高温干馏生产焦炭,同时获得煤气、煤焦油并回收其他化工产品,包括安、粗苯、硫、硫氰化合物等,它是一种结构复杂、长期连续生产的热工设备,生产温度950-1050℃。
一、焦化厂主要系统及设备备煤车间:煤仓、配煤室、粉碎机室、皮带机运输系统、煤制样室炼焦车间:煤塔、焦炉、装煤设施、推焦设施、拦焦设施、熄焦塔、筛运焦工段(包括焦台、筛焦楼)煤气净化车间:冷鼓工段(包括风机房、初冷器、电捕焦油器等设施);脱氨工段(包括洗氨塔、蒸氨塔、氨分解炉等设施);粗苯工段(包括终冷器、洗苯塔、脱苯塔等设施)公辅设施:废水处理站、供配电系统、给排水系统、综合水泵房、备煤除尘系统、筛运焦除尘系统、化验室等设施、制冷站等二、焦炉炉体的结构:炭化室、燃烧室、斜道区、蓄热室、小烟道、炉顶区、焦炉基础平台、烟道、烟囪三、炼焦炉的机械与设备:护炉铁件:保护板和炉门框、炉柱、拉条、弹簧和炉门焦炉加热设备:加热煤气设备、焦炉的煤气管系、交换设备、废气设备荒煤气导出设备:高压氨水及水封上升管盖装置、上升管与桥管、集气管与吸气管焦炉机械:装煤车、拦焦车、推焦车、熄焦车和电机车附属设备和修理装置:炉门修理站、余煤单斗机和埋刮板提升机、悬臂式起重机和电动葫芦、推焦杆更换装置第一章焦炉整体结构一、焦炉炉型的分类:现代焦炉因火道结构,加热煤气种类及其入炉方式,实现高向加热均匀性的方法不同等分成许多型式。
因火道结构形式的不同,焦炉可分为二分式焦炉,双联火道焦炉及少数的过顶式焦炉。
根据加热煤气种类的不同,焦炉可分为单热式焦炉和复热式焦炉。
根据煤气入炉的方式不同,焦炉可分为下喷式焦炉和侧入式焦炉。
二、现代焦炉的结构:(一)、现代焦炉虽有多种炉型,但都有共同的基本要求:1)焦并长向和高向加热均匀,加热水平适当,以减轻化学产品的裂解损失。
2)劳动生产率和设备利用率高。
3)加热系统阻力小,热工效率高,能耗低。
4)炉体坚固、严密、衰老慢、炉龄长。
焦炉生产工艺流程

焦炉生产工艺流程焦炉是将煤炭经过高温加热,使其分解产生焦炭和煤气的设备。
焦炉生产工艺流程如下:第一步:原料准备首先,需要准备好煤炭作为原料。
煤炭应选择质量好、热值高、灰分低的优质煤,通常使用粉煤。
第二步:煤粉制备将煤炭送入煤磨机中进行破碎,并通过给煤磨加入适量的热风和燃烧辅助空气,以提高研磨效率。
经过煤磨机研磨后,得到所需的细煤粉。
第三步:煤气准备煤气准备分为预热、干燥和干馏三个过程。
首先,在干燥塔中,将细煤粉与预热的空气进行混合,并以适当的速度送入大炉。
煤粉与空气在干燥塔中加热至一定温度,使水分得到蒸发。
然后,将干燥后的煤粉送入干馏炉中,通过高温加热,使煤粉分解产生煤气和焦炭。
煤气主要由一氧化碳、氢气和甲烷组成。
第四步:焦炭产生煤粉在干馏炉中高温分解后,生成焦炭和煤气。
焦炭沉积在焦炉底部,通过焦炉底部的出焦口取出。
取出的焦炭可进一步进行处理和筛分,得到不同粒径的焦炭产品。
第五步:煤气处理经过干馏炉分解的煤气进入煤气洗涤塔,在洗涤塔中进行洗涤。
洗涤塔中,煤气与洗涤液进行接触,去除其中的煤砂和其他杂质。
经过洗涤后的煤气经过冷却,得到可用于燃料的洁净煤气。
第六步:废气处理煤炭焦化过程中产生的废气需要进行处理,以减少对环境的污染。
常见的废气处理方式包括:利用煤气洗涤塔中洗涤液中的碱性成分吸收并中和酸性气体,利用除尘器去除固体颗粒物,以及利用脱硫装置去除硫化氢等硫化物。
第七步:灰渣处理煤炭焦化过程中产生的固体废弃物被称为灰渣。
灰渣在焦炉中积累一定量后,需要进行清理。
通常将灰渣运出焦炉,并在灰渣堆场进行储存和处理,以减少对环境的影响。
以上就是焦炉生产工艺流程的主要步骤。
焦炉生产工艺的完善可以提高焦炭质量,减少环境污染,提高生产效率和经济效益。
同时,需要严格控制炉内温度、通风等参数,以确保焦炉运行的稳定和安全。
焦炉简介介绍

焦炉的热效率可以达到70%以上 ,这是由于焦炉采用先进的燃烧 技术和余热回收技术,能够有效
地利用能源。
焦炉的燃烧效率也非常高,可以 达到98%以上,这得益于焦炉采 用先进的燃烧器和控制技术,能
够实现精准控制Байду номын сангаас烧。
提高焦炉能效的措施
采用先进的燃烧技术和余热回 收技术,提高热效率和能源利 用率。
按照生产能力,焦炉 可分为常规焦炉、大 型焦炉和超大型焦炉 。
02 焦炉的工作原理
煤气发生过程
干馏
焦炉煤气主要由来自煤料 干馏的煤气组成,包括一 氧化碳、二氧化碳、甲烷 、乙烯、乙炔等。
气化反应
在高温下,煤料与氧气和 水蒸气反应生成煤气,其 中一氧化碳是主要的可燃 组分。
热解
煤料在受热过程中会发生 热解反应,释放出挥发性 组分和焦油等物质。
粉尘防治措施
粉尘来源
焦炉生产过程中,装煤、出焦等环节会产生大量 的粉尘。
粉尘防治措施
为降低粉尘对环境和人员的影响,通常采取多种 措施,如密闭尘源、干法除尘、湿法除尘等。
效果评估
定期对粉尘防治措施进行效果评估,及时调整和 完善,确保达到良好的防治效果。
安全操作规程与应急预案
安全操作规程
为确保焦炉生产过程的安全,需要制定并执行严格的安全操作规程 ,包括装煤、出焦、加热等环节的操作要求和注意事项。
04 焦炉的环保与安 全措施
废气处理与排放控制
废气来源
焦炉在生产过程中会产生大量的废气,主要来源于焦炉烟囱和炉 内燃烧过程。
废气处理技术
针对不同来源的废气,通常采用不同的处理技术,如烟气脱硫、脱 硝等,以降低废气中污染物排放。
排放标准
焦炉炉体结构课件

03
焦炉内部结构
燃烧室结构
炉墙
燃烧室的两侧由耐火砖砌成的炉 墙,用于隔绝燃烧室和焦炭室,
承受高温烟气冲刷。
燃烧器
位于燃烧室顶部的燃烧器,将煤 气和空气混合后点燃,产生高温
烟气。
拱顶
燃烧室的顶部由耐火材料砌成的 拱形结构,起到支撑和分散烟气
压力的作用。
焦炭室结构
炭化室墙
焦炭室的四周由耐火砖砌成,用于将炼焦煤隔绝成独立的空间, 承受高温和压力。
焦炉发展历程
01
02
03
初创阶段
早期的焦炉结构简单,效 率低下,产量有限。
改进阶段
随着技术的发展,焦炉结 构不断优化,提高了热效 率和产量。
现代化阶段
引入先进的自动化技术和 环保措施,使得焦炉生产 更加高效可分为顶装式焦炉和侧装 式焦炉,主要区别在于装 煤方式的不同。
位于炉顶盖板下方,是燃烧室的一 部分,通常设有看火孔,以供操作 人员观察火焰状况。
炉顶保温层
用于减少热量损失,提高焦炉热效 率。
炉墙结构
耐火砖层
焦炉炉墙主要由耐火砖砌成,承受高温,保证炉 体的稳定性和寿命。
保温层
减少热量损失,提高热效率。
金属结构层
用于支撑和固定耐火砖层,保证炉墙的稳定性。
炉底结构
燃烧不充分
燃烧不充分会导致能源浪费和污染物排放增加。处理方法 为清理燃烧器、喷嘴,调整燃气和空气比例,确保燃烧充 分。
温度控制失灵
温度控制失灵会影响焦炭质量和产量。处理方法为检查温 度控制系统元件,更换损坏部件,重新标定温度探头。
THANKS
感谢观看
根据结构形式分类
可分为单室式焦炉和多室 式焦炉,多室式焦炉又可 进一步分为连续式、半连 续式和间歇式。
焦炉简介
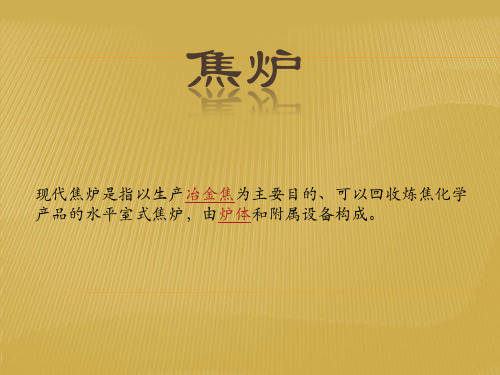
按炉高可分为:4米、5米、6米、7米焦炉。
按装煤方式可分为:顶装式或侧装式(捣固 焦)。
顶 装 式 焦 炉
结构
现代炼焦炉由炭化室、燃烧室、蓄热室、斜道 区、炉顶、基础、烟道等组成。
工作原理
炭化室中煤料在隔绝空气条件下受热变成焦炭。一座焦炉 有几十个炭化室和燃烧室相间配置,用耐火材料(硅砖)隔开。 每个燃烧室有20~30个立火道。来自蓄热室的经过预热的 煤气(高热值煤气不预热)和空气在立火道底部相遇燃烧, 从侧面向炭化室提供热量。蓄热室位于焦炉的下部,利用 高温废气来预热加热用的煤气和空气。斜道区是连接蓄热 室和燃烧室的斜通道。炭化室、燃烧室以上的炉体称炉顶, 其厚度按炉体强度和降低炉顶表面温度的需要确定。炉顶 区有装煤孔和上升管孔通向炭化室,用以装入煤料和导出 煤料干馏时产生的荒煤气。还设有看火孔通向每个火道, 供测温、检查火焰之用,根据检测结果,调节温度和压力。 整座焦炉砌筑在坚固平整的混凝土基础上,每个蓄热室通 过废气盘与烟道连接,烟道设在基础内或基础两侧,一端 与烟囱连接。
焦炉用耐材
顶盖层 炭化室的顶部 炭化室底部 炭化室和燃烧室的隔墙 炭化室两端的炉头 燃烧室 蓄热室 用粘土砖或硅砖砌筑 硅砖 硅砖 硅砖 优质高铝砖,硅线石砖或红柱石砖 硅砖 格子砖,一般用黏土砖
蓄热室侧墙
小烟道烟囱 斜道
优质黏土砖,保持整体性,也采用硅砖
粘土砖 小型焦炉用粘土砖,大中型焦炉普遍使用硅砖砌 筑
焦炉
现代焦炉是指以生产冶金焦为主要目的、可以回收炼焦化学 产品的水平室式焦炉,由炉体和附属设备构成。
类
按加热系统的结构不同,可分为:①双联火道 式,上升气流火道和下降气流火道成对组合, 整个燃烧室由若干组双联火道组成;②两分火 道式,整个燃烧室的半侧火道均走上升气流, 另半侧火道均走下降气流;③上跨焰道式,整 个燃烧室的各火道分为若干组,通过上跨焰道 与相邻燃烧室的火道组相联。炼焦炉的生产能 力决定于炭化室的尺寸和结焦时间。
焦炉炉型的分类与应用

焦炉炉型的分类与应用焦炉是冶金工业中常用的设备,用于生产焦炭,是钢铁生产过程中不可或缺的环节之一。
而焦炉的炉型决定了其热工性能和操作特点,因此对于不同的工业需求和生产要求,需要使用不同型号的焦炉。
在本文中,我们将探讨焦炉炉型的分类及其应用。
一、按燃料分类根据焦炉的燃料不同,可以将焦炉分为煤气炉、重油炉和天然气炉三种类型。
1. 煤气炉:煤气炉是以煤气作为燃料的焦炉。
煤气炉主要有焦炉煤气发生炉、蒸汽煤气发生炉和高炉煤气发生炉等。
其中,焦炉煤气发生炉是最常见的一种煤气炉,它通过加热煤炭产生煤气,然后通过管道输送到其他部分进行利用。
煤气炉具有燃烧效率高、温度均匀等特点,广泛应用于钢铁行业。
2. 重油炉:重油炉是以重油作为燃料的焦炉。
重油炉主要有高炉重油炉、液态燃料炉和喷燃器式炉等。
重油炉的燃烧效率较高,能够提供高温的热能,适用于一些对热能要求较高的工业生产。
3. 天然气炉:天然气炉是以天然气作为燃料的焦炉。
天然气炉主要有直接燃烧天然气炉和煤气-天然气复合燃烧炉等。
天然气炉具有环保、高效、无污染等优点,被广泛应用于钢铁、化工等行业。
二、按炉型分类根据焦炉的炉型不同,可以将焦炉分为立式焦炉和水平焦炉两种类型。
1. 立式焦炉:立式焦炉是煤气炉中常见的炉型之一。
立式焦炉具有结构简单、操作方便等特点,适用于一些小型钢铁企业。
2. 水平焦炉:水平焦炉是传统的焦炉炉型之一,其主要特点是炉身呈水平布置。
水平焦炉具有炉容大、生产能力强等优点,广泛应用于大型钢铁企业。
三、按结构分类根据焦炉的结构不同,可以将焦炉分为焦炉炉腔直径和炉腔高度均匀的均质炉、炉腔具有高度温差的非均质炉和炉腔具有比较大高度温差的跌差炉三种类型。
1. 均质炉:均质炉是指炉腔直径和炉腔高度均匀的焦炉。
均质炉具有热工性能稳定、操作简单等特点,对于生产一致品质的焦炭有着重要作用。
2. 非均质炉:非均质炉是指炉腔具有高度温差的焦炉。
非均质炉能够实现不同位置的温度控制,适用于一些特殊需要的焦炭生产。
焦炉的组成部分
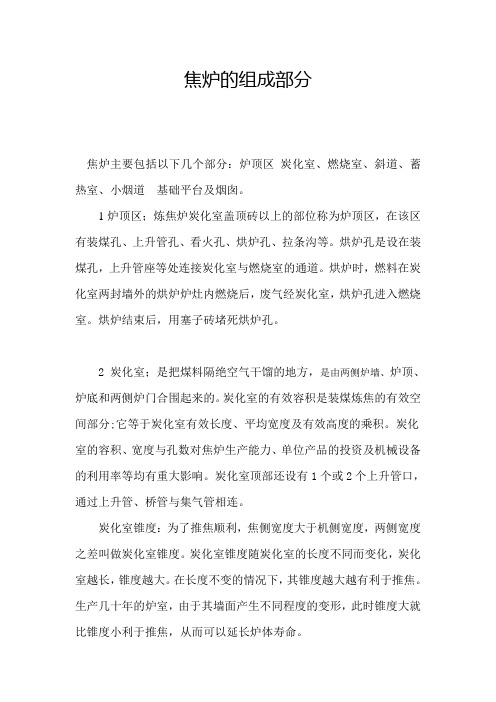
焦炉的组成部分焦炉主要包括以下几个部分:炉顶区炭化室、燃烧室、斜道、蓄热室、小烟道基础平台及烟囱。
1炉顶区;炼焦炉炭化室盖顶砖以上的部位称为炉顶区,在该区有装煤孔、上升管孔、看火孔、烘炉孔、拉条沟等。
烘炉孔是设在装煤孔,上升管座等处连接炭化室与燃烧室的通道。
烘炉时,燃料在炭化室两封墙外的烘炉炉灶内燃烧后,废气经炭化室,烘炉孔进入燃烧室。
烘炉结束后,用塞子砖堵死烘炉孔。
2 炭化室;是把煤料隔绝空气干馏的地方,是由两侧炉墙、炉顶、炉底和两侧炉门合围起来的。
炭化室的有效容积是装煤炼焦的有效空间部分;它等于炭化室有效长度、平均宽度及有效高度的乘积。
炭化室的容积、宽度与孔数对焦炉生产能力、单位产品的投资及机械设备的利用率等均有重大影响。
炭化室顶部还设有1个或2个上升管口,通过上升管、桥管与集气管相连。
炭化室锥度:为了推焦顺利,焦侧宽度大于机侧宽度,两侧宽度之差叫做炭化室锥度。
炭化室锥度随炭化室的长度不同而变化,炭化室越长,锥度越大。
在长度不变的情况下,其锥度越大越有利于推焦。
生产几十年的炉室,由于其墙面产生不同程度的变形,此时锥度大就比锥度小利于推焦,从而可以延长炉体寿命。
3燃烧室、是煤气与空气混合并燃烧的空间。
双联式燃烧室每相邻火道连成一对,一个是上升气流,另一个是下降气流。
双联火道结构具有加热均匀、气流阻力小、砌体强度高等优点,但异向气流接触面较多,结构较复杂,砖形多,我国大型焦炉均采用这种结构。
每个燃烧室有28个或32个立火道。
相邻两个为一对,组成双联火道结构。
每对火道隔墙上部有跨越孔,下部除炉头一对火道外都有废气循环孔。
砖煤气道顶部灯头砖稍高于废气循环孔的位置,使焦炉煤气火焰拉长,以改善焦炉高向加热均匀性和减少废气氮氧化物含量,还可防止产生短路。
4斜道、燃烧室与蓄热室相连接的通道称为斜道。
蓄热室位子斜道下部,通过斜道与燃烧室相通,是废气与空气进行热交换的部位。
蓄热室预热煤气与空气时的气流称为上升气流,废气称为下降气流。
焦炉操作时间
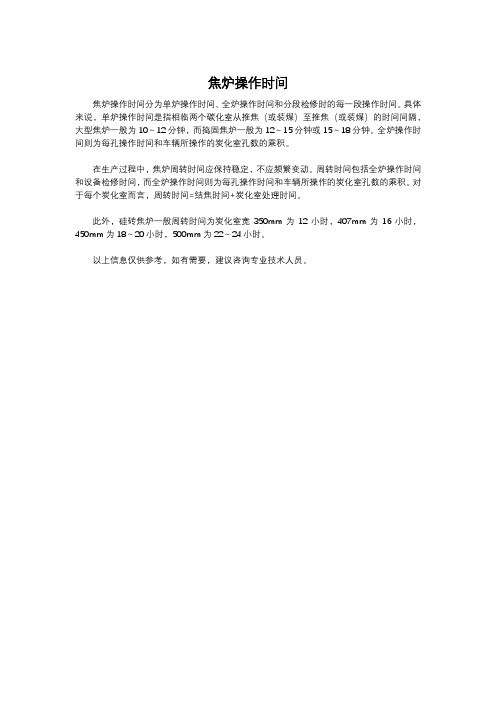
焦炉操作时间
焦炉操作时间分为单炉操作时间、全炉操作时间和分段检修时的每一段操作时间。
具体来说,单炉操作时间是指相临两个碳化室从推焦(或装煤)至推焦(或装煤)的时间间隔,大型焦炉一般为10~12分钟,而捣固焦炉一般为12~15分钟或15~18分钟。
全炉操作时间则为每孔操作时间和车辆所操作的炭化室孔数的乘积。
在生产过程中,焦炉周转时间应保持稳定,不应频繁变动。
周转时间包括全炉操作时间和设备检修时间,而全炉操作时间则为每孔操作时间和车辆所操作的炭化室孔数的乘积。
对于每个炭化室而言,周转时间=结焦时间+炭化室处理时间。
此外,硅砖焦炉一般周转时间为炭化室宽350mm为12小时,407mm为16小时,450mm为18~20小时,500mm为22~24小时。
以上信息仅供参考,如有需要,建议咨询专业技术人员。
焦炉生产工艺

焦炉生产工艺
焦炉生产工艺是指将煤炭加工转化成焦炭的过程。
焦炭是冶金行业重要的燃料和还原剂,广泛应用于钢铁生产等领域。
在焦炉生产工艺中,主要包括煤炭预处理、热解焦化和焦炭冷却等环节。
首先,在焦炉生产工艺中,煤炭预处理是非常重要的一步。
这主要是通过煤炭的粉碎和干燥等工艺,将煤炭转化成适合于焦化的颗粒状物料。
粉碎是将煤炭进行机械破碎,使其粒度适度,以提高热解焦化的效果。
而干燥则是通过对湿煤进行烘干,减少焦炉煤气处理中的水蒸气含量,防止结焦和沾污等问题的发生。
其次,煤炭进入焦炉后,经历热解焦化过程。
这是通过高温下,将煤炭内部结构发生改变的过程。
在焦炉中,煤炭被加热至高温后开始热解,通过热解产生的煤气和焦炉煤气进行热交换,进行煤气净化和冷却。
在这个过程中,煤炭中的挥发分被分解释放出来,形成煤气;而固定碳则不断聚焦,形成焦炭。
最后,焦炭冷却是焦炉生产工艺的最后一环节。
焦炭冷凝过程采用水冷却,将焦炭表面的热量迅速带走,使其迅速降温至常温,并使焦炭均匀冷却。
这有助于提高焦炭的机械强度和耐久性,提高其燃烧效率和还原能力。
总的来说,焦炉生产工艺是一个复杂的过程,需要通过不同的环节来完成焦炭的制备。
其中煤炭的预处理,热解焦化和焦炭冷却是三个关键的环节。
通过对煤炭的预处理,可以提高煤炭
的焦化效果;而热解焦化过程则是焦炉生产工艺的核心环节,是焦炭形成的关键步骤;最后的焦炭冷却,则可以提高焦炭的品质和使用性能。
因此,在焦炉生产工艺中,各个环节的配合和控制,对焦炭的质量和生产效率有着重要的影响。
- 1、下载文档前请自行甄别文档内容的完整性,平台不提供额外的编辑、内容补充、找答案等附加服务。
- 2、"仅部分预览"的文档,不可在线预览部分如存在完整性等问题,可反馈申请退款(可完整预览的文档不适用该条件!)。
- 3、如文档侵犯您的权益,请联系客服反馈,我们会尽快为您处理(人工客服工作时间:9:00-18:30)。
焦炉选型一、焦炉选型原则焦炉的选型的原则:首先考虑焦炉生产的焦炭是否满足高炉生产的需要,其次再从焦炉工艺技术、投资、生产成本、环保等方面进行综合比较选择最适合匹配高炉生产的型号。
高炉容积越大,冶炼周期就越长,对焦炭反应后强度要求就越高;而且随着高炉为降低成本追求高煤比、低焦比,焦炭在高炉内的“骨架”作用就越来越重要。
这些都要求焦炭的冷、热强度处于合理的范围,才能满足高炉运行对焦炭质量的要求。
以下表1是大高炉对焦炭热性能要求;表2是国内大、中型焦化焦炭质量统计。
表1:大高炉对焦炭热性能要求(资料来源:世界金属导报2008-10-21第10-11版)表2:国内大、中型焦化焦炭质量统计(资料来源:万方数据)我厂现用焦炭70%左右是鑫跃焦化厂焦炭,鑫跃焦化厂是典型的4.3m焦炉,其2008年指标状况如表3:表3:鑫跃焦化2008年质量指标(资料来源:炼铁厂技术分析)从上表可以看出鑫跃焦化4.3m焦炉热反应性能CRI在29.1—34.13,热反应后强度CSR在46.25—53.4。
冷态强度也较大、中型焦炉有一定差距,而且它的单孔容积较小,推焦次数较多,使其质量较差的机头焦较多,质量稳定性差,生产成本高。
因此1000m3及以上高炉为保持高炉的稳定顺行,新建系统不采用4.3m焦炉与之匹配。
二、国内焦炉的现状国内与1000m3及以上高炉配套的焦炉现在主要是6m焦炉、7m焦炉、7.63m 焦炉三种。
(国外有8m焦炉),另外有一部分大型捣鼓焦炉也在兴建中。
几种焦炉的基本情况如表4:表4:国内焦炉现状(资料来源:世界金属导报第46卷总第1904期)2007年我国新建焦炉投产41座,新增产能2163万吨。
其中炭化室大于6米(含5.5米捣固焦炉)23座,产能1435万吨,占新增产能的66.3%,主要匹配1000 m3以上高炉的投产。
三、6m焦炉(一)、6m焦炉的技术特点宝钢分别于1985年、1991年、1997年建设的第一、二、三期共12座6m 焦炉比较典型的反映了6m焦炉的发展及特点:。
(二)6m焦炉分析1、6m焦炉1985年开始从日本引进,经过两到三年时间消化、吸收实现国产化,现运行或在建100座,设计、制造、安装技术比较普及和成熟。
2、与7m焦炉、7.63m焦炉比较6m焦炉燃烧方式相对简单只是异位燃烧,燃料利用率低,生产成本相对较高。
3、由于燃烧方式造成废气中NOx的含量较7m焦炉、7.63m焦炉高,环保压力较大。
4、6m焦炉操作工艺及操作技术研究比较多,与7m焦炉、7.63m焦炉比较是各种工艺技术最成熟的一种焦炉。
四、7m焦炉(一)7米焦炉的开发和投产1、2005年中冶焦耐工程技术有限公司开发了JNX70-2型(炭化室宽450毫米)7米焦炉。
JNX70-2型7米焦炉是双联火道、废气循环、焦炉煤气下喷、高炉煤气侧入、下调的复热式焦炉。
2、2007年为适应严格控制烟道废气中NOx量的要求降低污染物排放,开发了JNX3-70-1型。
它也是是双联火道、废气循环、多段加热、焦炉煤气下喷、贫煤气和空气侧入、下调的复热式焦炉。
它比JNX70-2型增加了多段加热措施,降低废气中NOx的排放。
JNX3-70-1型加热时贫煤气和空气侧入分三段供给,焦炉煤气加热时空气分三段供给,降低燃烧强度进而降低燃烧温度,减少NOx的生成。
JNX3-70-1型焦化室500毫米,炉墙厚度减薄为950毫米,提高烧结速度、改善结焦性能、减少焦煤配比、降低炼焦煤成本。
7m焦炉技术参数如表5:表5:7m焦炉技术参数(资料来源:世界金属导报)JNX70-2型JNX3-70-1型焦炉技术参数(二)7米焦炉分析1、年产150万吨7米焦炉比6米焦炉泄漏口数量减少20%,密封面长度减少13.3%,每天打开泄漏口次数分别减少21%和28.6%。
从而大大减少有害气体的排放量。
(资料来源:世界金属导报)2、能满足强粘结性煤缺乏的国家和地区生产大型高炉用焦炭的质量要求。
3、降低了污染物的排放量,能显著改善焦炉生产的环保水平。
4、为保证7m焦炉高向和长向加热的均匀性,采取了以下几项措施:① 采用了双联火道、废气循环的加热方式,在总结JN60型焦炉、8m试验焦炉以及国外大容积焦炉高向加热经验的基础上,不仅加大了废气循环量,而且还设置了焦炉煤气高灯头,保证了高向加热的均匀性。
② 在总结国外大容积焦炉的斜道口大小及其排列方式和国内下调焦炉生产经验的基础上,计算确定了斜道口的开度和排列,保证了焦炉长向加热的均匀性。
③ 蓄热室采用分格和篦子砖可调的结构,可使气流在蓄热室内合理地分配,大大减少了气流的偏析,增加了格子砖的冲刷系数,降低了废气的温度,提高了焦炉的热工效率。
④ 为了确保边火道的加热符合要求,边蓄热室、蓄热室封墙、炉头斜道出口和炉头立火道都采取了特殊的结构,以确保焦饼的均匀成熟。
⑤ 蓄热室设有可调节的篦子砖,斜道口设置了可更换的调节砖,焦炉的调节简单易行、准确可靠,保证了高向加热的均匀性。
5、为延长焦炉炉龄,提高环保水平,在焦炉结构上采取了如下的改进措施:① 改进了蓄热室主墙、单墙、隔墙和封墙的结构,保证了墙的严密性和整体性,减少了一氧化碳的排放量,提高了焦炉的热工效率。
② 新设计焦炉的炭化室墙面砖在继承了JN系列焦炉优点的基础上,提高了炭化室墙面砖的抗剪强度,降低了炭化室墙面砖损坏的可能性, 提高了炭化室墙面砖的严密性,减少了炭化室和燃烧室之间的窜漏,尽可能地减少了炭化室墙面砖的砖型数量,以节省投资和便于维修。
③ 改善了燃烧室立火道隔墙的结构,以保证燃烧室的整体性和立火道之间的严密性。
④ 采用加大废气循环量和设置焦炉煤气高灯头的措施后,既可保证炭化室高向加热的均匀性,又可减少NOx的产生量。
⑤ 重新设计的炉顶结构可减少炉顶的散热,改善炉顶的操作环境。
合理的装煤孔布置和装煤孔结构,既可减少装煤时阵发性污染物的排放量,又可保证均匀装煤,以达到减少平煤操作次数、减少污染物排放的目的。
⑥ 蓄热室采用两个火道为一格的结构,斜道高度增加到900mm,避免了立火道火焰对蓄热室顶部格子砖的直射,有效降低了蓄热室顶部格子砖的温度。
6、为提高煤的结焦性能,炭化室采用了宽度为450mm的窄炭化室,炉墙厚度也减薄到95mm ,以达到提高炭化室结焦速度、减少焦煤配比、降低炼焦煤成本和提高经济效益的目的。
7、燃烧室墙具有足够的稳定性和强度。
计算表明,7m焦炉炉墙的极限侧负荷为9066Pa,比国内现有的6m焦炉有了较大的提高。
8、焦炉所用材料的选用和砖型图的设计都进行了精心的考虑,60孔的7m焦炉炉体用耐火材料具有易采购、制砖成品率高、便于施工等特点,完全称得上是适合中国国情、技术先进的新型焦炉。
(以上2—8条资料来源中冶焦耐网页)五、7.63m焦炉(一)7.63米焦炉的建设和运行1、建设情况:兖矿引进德国Kaiserstuh焦化厂2×60孔7.63米焦炉(年产200万吨);太钢、马钢、武钢、首钢曹妃甸和沙钢分别从德国Uhde公司和Schalke 公司引进13座7.63米焦炉和四大车技术,与4000立方米以上高炉配套。
2、运行情况:兖矿、太钢、马钢、武钢的8座7.63米焦炉已分别于2006—2007年投产;炭化室宽度平均590毫米;适用于粘结性好,挥发分较低的配煤,当入炉煤配入65%-70%强粘结性焦煤或肥煤时可生产出4000立方米高炉所需的冷态和热态强度较好的优质焦炭;当入炉焦煤挥发份24±1%、水分﹤10%时实现无烟装煤。
(以上(一)资料来源:世界金属导报)(二)7 .63 m焦炉分析1、 7 .63 m焦炉炉体严密性好,但异型砖多,有些砖的成品率极低,甚至不到50%。
焦炉加热水平设计不合适,炉顶空间温度高,Proven(单个上升管压力控制)系统很复杂,这对焦油质量有一定影响。
高向加热设计的调节手段较多,但可操作性较差并使得炉体结构复杂等问题皆值得讨论或有待于改进。
2、 7 .63 m焦炉使用了许多新技术,但是这些新技术有的值得借鉴,有的尚需讨论其有效性和必要性,而复杂的炉体结构对焦炉生产操作和寿命是否有影响也需要进一步实践验证。
太钢 7 .6 3m焦炉机械硬件由大重制造,关键控制设备以及控制软件由德国SCHALKE公司提供。
(以上(二)资料来源:万方数据)六、捣鼓焦炉以下焦炉部分为第46卷总第1905期(一)捣鼓焦炉的特点及发展1、上世纪我国只在大连、抚顺、镇江等地有炭化室高3.2米和3.8米小型搗固焦炉,总计不到20座,2000年我国开发了炭化室高4.3米、宽500毫米搗固焦炉。
现在我国投产的搗固焦炉已超过360座,炼焦生产能力接近0.8亿吨,相当于每年少用强粘结性炼焦煤2400万吨。
2、我国自行开发了 5.5米搗固焦炉,中冶焦耐开发了JNDK55-05型和JNDK55-07型。
至2008年5月我国已有云南曲靖(4座)、山东铁雄(2座)、河南金马(1座)和河北旭阳(2座)共9座5.5米搗固焦炉。
我国已投产的360座搗固焦炉几乎都是建在独立的焦化厂,只有十几座建在中小型钢铁企业内。
3、2006年中冶焦耐开发了世界最高的6.25米搗固焦炉,在河北唐山佳华设计施工,预计2008年9月投产。
该工程为新建4*46孔炭化室高度6.25米,年产干全焦220万吨。
2008年昆钢、莱钢、旭阳也已决定建设6.25米搗固焦炉。
(二)捣鼓焦炉分析搗固焦炉寿命不如顶装焦炉,搗固焦炉的稳定生产不如顶装焦炉;搗固焦炉装煤除尘效果不如顶装焦炉;国内外几乎还没有3000立方米以上高炉长期全部使用搗固焦炭的生产经验。
因此大高炉在主要工艺配置上选择捣鼓焦炉不是合适的选择。
七、焦炉新技术的应用(一)、干熄焦技术的推广和大型化1、干熄焦技术基本原理是:利用冷惰性气体在干熄焦炉中与红焦直接换热,从而冷却焦炭。
采用干熄焦可回收80%红焦显热,平均每熄1吨红焦可回收3.9MPa、450度蒸汽0.45—0.58吨,采用全凝机组发电,平均每熄1吨红焦净发电95—105kWh。
2、采用干熄焦可提高焦炭质量,降低高炉焦比。
在保持焦炭质量不变的情况下,采用干熄焦可在配煤中多用15%的弱粘结性煤。
采用干熄焦可以节水,宝钢的实践数据是平均每吨焦节水0.440吨以上,采用干熄焦技术可降低炼焦能耗50—60kgce/t焦。
3、我国最大的干熄焦200t/h2008年7月31日在唐山钢铁公司顺利投入运行。
我国在建和已投产的干熄焦装置126套,相当于和12012吨焦炭能力配套,相当于我国2007年机焦总量3.0537亿吨的39.3%,相当于我国2007年钢铁工业耗焦总量的41.7%。
世界各国正在施工和设计的干熄焦装置已超过300套。
(二)、煤调湿技术的推广1、煤调湿技术是将炼焦煤料在装炉之前去除一部分水份,保持装炉煤水分稳定在6%左右然后进行装炉炼焦。