磁硫铁矿制酸净化污酸固液分离工艺改造实践
硫铁矿制酸工艺范文

硫铁矿制酸工艺范文
一、硫铁矿制酸工艺
1、原料准备
制酸原料主要为硫铁矿(FeS2),是一种可以制成氢氧化铁的硫酸盐
矿物。
硫铁矿要求细度适中,杂质少,颜色均一,所以要经过粉碎、筛选
等粗加工后才能作为制酸原料。
2、生膳熔化
经过粉碎和筛选的硫铁矿,经过生膳熔化后,释出其中的硫,得到氧
化铁和硫酸熔液(硫酸熔液是由硫、氢氧化铁、氢氧化硫和水组成)。
3、氢氧化铁沉淀
将硫酸熔液进行蒸馏,以除去硫、硫酸熔液中的水分、氢氧化硫,剩
余的氢氧化铁形成沉淀,经过洗涤和干燥即可得到氢氧化铁,以备来制酸。
4、电解氢氧化铁
将氢氧化铁放入电解桶中,加入少量盐酸以调节液体的pH值,再加
入碱性的电解液,再由电解装置提供电流,氢氧化铁会被电解分解成氢气、氧气、氢氧化铁溶液中还含有少量的氢氧化铁固溶物。
5、氢氧化铁溶液精炼
将氢氧化铁溶液透过精炼设备,去除其中的杂质及水,所得溶液称为
酸液,为制酸的最终产物,可以用来制造各种硫酸系列产品。
6、废液处理。
磁分离净化技术在矿井污水处理中的应用研究

磁分离净化技术在矿井污水处理中的应用研究发表时间:2020-04-09T02:56:05.983Z 来源:《防护工程》2020年1期作者:李耀耀[导读] 能否通过合理的技术应用来净化煤矿矿井水,在很大程度上决定了煤矿企业的资源利用率及其节能减排情况。
安徽途晟规划设计咨询有限公司安徽合肥 230051摘要:能否通过合理的技术应用来净化煤矿矿井水,在很大程度上决定了煤矿企业的资源利用率及其节能减排情况。
很多矿井为了更加合理充分的利用资源,通过建设污水处理站的形式对矿井污水进行综合的净化处理,其中应用了磁分离水体净化技术。
大量实践结果表明,将该技术运用在水体净化过程中,能够有效实现泥水分离,以较低的运行成本节省更多的能源,不仅实现了对矿区污染的控制,同时煤泥经处理后可流通入市,产生二次经济效益。
鉴于此,本文围绕磁分离净化技术在矿井污水处理中的应用展开探究。
首先简述了超磁分离净化技术工艺流程、水质及排放指标,然后介绍了在矿井污水处理中磁分离净化技术应用的主要构筑物及工艺系统,最后分析了磁分离净化技术在矿井污水处理中的应用效果。
关键词:煤矿污水;煤泥资源;磁分离;净化节能 1工艺简述1.1工艺流程由巷道沟渠对矿井污水进行引流和收集,最终集中于近水渠,在其中布置机械格栅来进行初次过滤,接下来引入预沉池中。
过一段时间的沉积,水中比较大的颗粒会沉淀到底部形成污泥,由下方的潜水渣浆泵将其倒入泥池中,在污泥泵的带动下转送至压滤机,经过脱水后再进入下一阶段处理。
超磁分离净化技术具体的工艺流程显示在图1中。
图1 超磁分离净化技术工艺流程图超磁分离混凝系统接收来自预沉处理后的污水,该系统中含有大量的混凝剂和磁种,其中混凝剂主要是PAM和PAC,在三分钟到六分钟的时间内悬浮在水面上的物质会在磁种的吸引下团聚形成微絮团。
经过此过程后水再次进入超磁分离机,在这里进行固液分离的净化过程。
之后经检测达到相关标准后实现清水入仓,在排水泵的加压提升下运送至水面进行综合运用。
硫铁矿制酸净化工序废酸回用的探讨

I N D U S T R I A L W A T E R & W A S T E W A T E R
工业用水与废水
V o 1 . 4 5 N o . 1 F e b . . 2 0 1 4
硫铁矿 制酸净化 工序废 稀酸 回用 的探讨
李 旺 旺 ,牟林 琳 ,毕 亚 凡
( 武 汉 工 程 大 学 环 境 与 城 市 建 设 学 院 ,武 汉 4 3 0 0 7 4 ) 摘 要 : 为 了考 察 硫 铁 矿 制 酸净 化 工序 产 生 的 废 稀 酸 回用 于湿 法磷 酸 萃取 系统 的 可 行 性 问题 .将 u s s i o n on r e u s e o f wa s t e di l u t e a c i d f r O m p u r i f i c a t i o n p r o c e s s
d u r i n g p r o d u c i n g s u l f u r i c a c i d b y p y r i t e
科技成果——硫铁矿制酸厂酸性含砷废水循环利用技术

科技成果——硫铁矿制酸厂酸性含砷废水循环利用技术技术开发单位湘潭大学适用范围各种规模的硫铁矿制酸装置以及冶炼烟气制酸装置的酸性含重金属废水处理,实现废水循环利用。
成果简介该技术由硫酸废水分步脱氟除砷铅和二氧化碳脱钙回用两部分组成,其中第一部分先用氢氧化钙对废水进行中和脱氟(生成氟化钙),再加入铁盐并曝气,使As(Ⅲ)、Fe(Ⅱ)氧化和生成砷酸铁沉淀,而过量的Fe(Ⅲ)能够把废水中的砷铅氟等不溶物充分絮凝,然后被滤除;第二部分是用二氧化碳对所生成的碱性钙盐过饱和废水进行脱钙处理,由于碱性是氢氧化钙所致,用含二氧化碳的压缩空气曝气能够生成碳酸钙晶粒,并使溶解态Fe(Ⅱ)被氧化成Fe(Ⅲ)析出,使得过饱和硫酸钙的稳定性降低,再加入絮凝剂混凝后能够形成共沉淀效应,使沉淀池出水钙浓度降低为不饱和状态。
由于硫酸钙在硫酸溶液中溶解度增大,该废水可全部返回酸洗工序循环利用。
工艺流程工艺流程为:硫酸废水进入搅拌反应池,加入氢氧化钙进行中和脱氟反应;废水再进入曝气反应池,加入铁盐并用压缩空气曝气,使As(Ⅲ)、Fe(Ⅱ)被氧化和生成砷酸铁;曝气反应池的悬浮液进入压滤机分离;压滤机的出水进入二级反应池,加入少量铁盐并用压缩空气曝气,使残留的砷与铁进一步反应;其出水进入脱钙反应池,用废气二氧化碳掺混的压缩空气曝气,生成碳酸钙晶种;该废水再进入混凝反应池,加入絮凝剂进行混凝;混凝液进入沉淀池发生碳酸钙、硫酸钙与絮凝物的共沉淀,废水钙浓度降低至不饱和状态;废水进入pH调整池,用废气二氧化碳调整pH值,然后进入回用水储水池待用。
工艺流程图关键技术硫铁矿制酸废水分步脱氟除砷铅新方法,改变了传统两级石灰铁盐中和曝气法存在的反应池结垢淤塞和处理后废水不能回用的弊端,使污染物去除更彻底、能耗降低、运行稳定。
碱性高钙废水二氧化碳脱钙回用新方法,能够将所生成的钙盐过饱和废水通过二氧化碳反应和混凝共沉淀降低至不饱和状态,并且实现废水循环利用。
硫铁矿制酸工艺

硫铁矿制酸工艺硫铁矿是一种常见的金属矿石,在现代工业生产中有着广泛的应用。
硫铁矿中含有大量的金属元素,如铜、铅、锌等,但同时也含有大量的硫化物。
这些硫化物在自然环境中难以分解,而且具有一定的腐蚀性,常常给环境带来一定的危害。
而通过硫铁矿制酸工艺的研究和应用,可以将硫化物分解转化为有用的化学品,同时也能够减少对环境的污染,对于促进产业结构升级和环境保护都具有重要意义。
硫铁矿制酸工艺是指通过对含硫铁矿进行氧化反应,将硫化物转化为硫酸,同时产生水。
这个反应过程可以用化学方程式表示为:FeS2 + 7O2 + 2H2O → Fe2(SO4)3 + 2H2SO4其中,FeS2为硫铁矿,O2为氧气,H2O为水,Fe2(SO4)3和H2SO4分别为硫酸铁和硫酸。
此外,在反应中还需要一定的催化剂和温度控制。
硫铁矿制酸工艺主要应用于提取铜、锌、铅等金属元素的生产过程中。
在这个过程中,需要大量消耗硫酸,而通过硫铁矿制酸工艺,可以使得硫化物转化为硫酸,不仅可以减少废弃物的排放,而且可大幅降低生产成本。
同时,硫铁矿制酸工艺还可以用于环境治理和回收利用废水处理中的氧化作用。
将高浓度的有机物和重金属离子转化为无害的水和二氧化硫,并从中收集到有用的硫酸和其他化学物质。
在硫铁矿制酸工艺中,实际生产中会遇到一些问题。
例如,硫铁矿制酸过程中产生较多的气体,导致环境污染和资源浪费。
此外,工艺涉及到的化学物质和催化剂也可能对环境造成一定的污染和危害。
因此,需要在工艺的研究和应用中注重环境保护,尽可能地减少废弃物的产生和对环境的负面影响。
总的来说,硫铁矿制酸工艺具有重要的意义和应用前景。
通过研究和发展这一技术,可以实现有效生产和资源利用,同时也有利于环境保护和治理。
在实际应用中,应注重技术创新和环境保护,从而更好地推进工艺的应用和发展。
硫铁矿制酸工艺控制方案
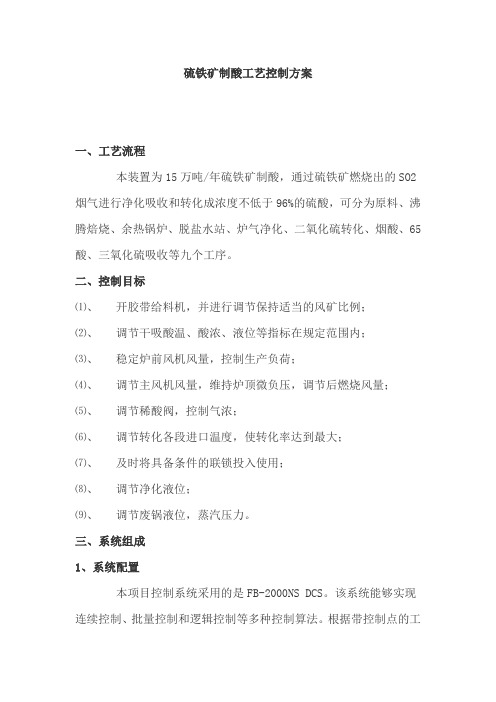
硫铁矿制酸工艺控制方案一、工艺流程本装置为15万吨/年硫铁矿制酸,通过硫铁矿燃烧出的SO2烟气进行净化吸收和转化成浓度不低于96%的硫酸,可分为原料、沸腾焙烧、余热锅炉、脱盐水站、炉气净化、二氧化硫转化、烟酸、65酸、三氧化硫吸收等九个工序。
二、控制目标⑴、开胶带给料机,并进行调节保持适当的风矿比例;⑵、调节干吸酸温、酸浓、液位等指标在规定范围内;⑶、稳定炉前风机风量,控制生产负荷;⑷、调节主风机风量,维持炉顶微负压,调节后燃烧风量;⑸、调节稀酸阀,控制气浓;⑹、调节转化各段进口温度,使转化率达到最大;⑺、及时将具备条件的联锁投入使用;⑻、调节净化液位;⑼、调节废锅液位,蒸汽压力。
三、系统组成1、系统配置本项目控制系统采用的是FB-2000NS DCS。
该系统能够实现连续控制、批量控制和逻辑控制等多种控制算法。
根据带控制点的工艺流程图,与工艺技术人员认真细致地分析了生产工艺对控制的要求,合理地设计了方便于操作工监视、操作的流程图画面。
由于湖北楚源鑫慧化工公司十五车间的十五万吨/ 年硫酸生产DCS分为制酸站和焙烧站,制酸站是两机两柜,焙烧站上是两机一柜,既要各自独立工作又要相互监视,因此我们采用在四台操作站上同时建立以太网进行连接,现场控制站网络结构图如下:其DCS的硬件配置为:制酸站:FB-2001NS2块,FB-2005NS网卡2块,FB-2010NS-13块,FB-SC14NS-13块;FB-2020NS-6块,FB-SC20NS -6块; FB-2030NS-7块,FB-SC30NS-7块; FB-2040NS-4块,FB-SC43NS -4块。
这样就构成了一套分布式数据采集与控制系统。
另外现场有一台10KVA和一台3KVA一共两台在线式不间断电源UPS,备品备件有:FB-2001NS主控制器2块。
焙烧站:FB-2001NS2块,FB-2005NS网卡2块,FB-2010NS-6块,FB-SC14NS-6块;FB-2020NS-3块,FB-SC20NS -3块; FB-2030NS-3块,FB-SC30NS-3块; FB-2040NS-2块,FB-SC43NS -2块。
新硫铁矿制酸工艺流程精编版
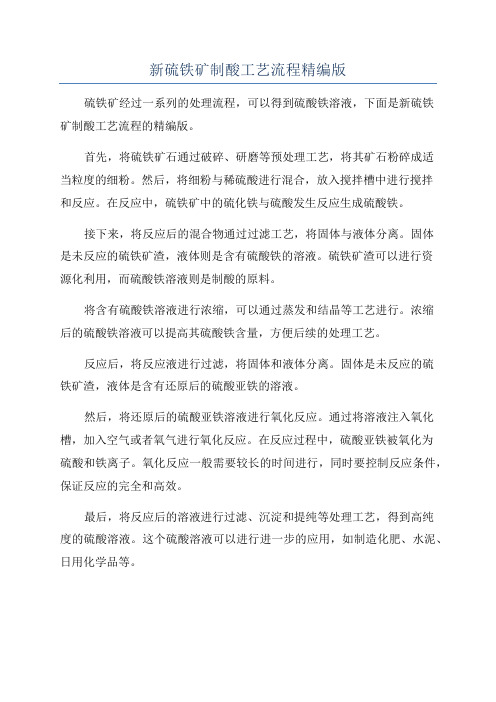
新硫铁矿制酸工艺流程精编版
硫铁矿经过一系列的处理流程,可以得到硫酸铁溶液,下面是新硫铁
矿制酸工艺流程的精编版。
首先,将硫铁矿石通过破碎、研磨等预处理工艺,将其矿石粉碎成适
当粒度的细粉。
然后,将细粉与稀硫酸进行混合,放入搅拌槽中进行搅拌
和反应。
在反应中,硫铁矿中的硫化铁与硫酸发生反应生成硫酸铁。
接下来,将反应后的混合物通过过滤工艺,将固体与液体分离。
固体
是未反应的硫铁矿渣,液体则是含有硫酸铁的溶液。
硫铁矿渣可以进行资
源化利用,而硫酸铁溶液则是制酸的原料。
将含有硫酸铁溶液进行浓缩,可以通过蒸发和结晶等工艺进行。
浓缩
后的硫酸铁溶液可以提高其硫酸铁含量,方便后续的处理工艺。
反应后,将反应液进行过滤,将固体和液体分离。
固体是未反应的硫
铁矿渣,液体是含有还原后的硫酸亚铁的溶液。
然后,将还原后的硫酸亚铁溶液进行氧化反应。
通过将溶液注入氧化槽,加入空气或者氧气进行氧化反应。
在反应过程中,硫酸亚铁被氧化为
硫酸和铁离子。
氧化反应一般需要较长的时间进行,同时要控制反应条件,保证反应的完全和高效。
最后,将反应后的溶液进行过滤、沉淀和提纯等处理工艺,得到高纯
度的硫酸溶液。
这个硫酸溶液可以进行进一步的应用,如制造化肥、水泥、日用化学品等。
以上就是新硫铁矿制酸工艺流程的精编版。
通过这个工艺流程,可以将硫铁矿转化为硫酸铁溶液,实现资源的有效利用和二氧化硫的减排。
同时,对于工艺条件的控制和能源消耗的优化也是工艺设计和改进的重点。
硫铁矿制酸装置净化流程改造及运行

2 0 1 3年 1 2月
广
州
化
工
Vo 1 . 41 No . 23 De c e mb e r . 2 01 3
Gu a n g z h o u Ch e mi c a l I n d u s t r y
硫 铁 矿 制 酸 装 置 净 化 流 程 改 造 及 运 行
Ab s t r a c t : As s o c i a t e d p y r i t e t r a n s f o r ma t i o n p r o c e s s p u if r ic a t i o n s u l p h u r i c a c i d p l a n t , b e f o r e a nd a f t e r t h e t r a n s f o ma r t i o n o f o pe r a t i o n i n d e x we r e c o mpa r e d .I t s h o we d t ha t t h e i mp r o v e d o p e r a t i o n,p u if r i c a t i o n p r o c e s s u s i n g h e a t e x c h a n g e r h a d s i g n i ic f a n t a d v a n t a g e s ,g o o d h e a t e x c h a n g e e f f e c t ,a n d s ma l l s y s t e m r e s i s t a n c e, s i g n i ic f a n t l y r e du c e d e n e r g y c o n s u mpt i o n,b u t a l s o t o t h e p r o d uc t i o n ma n a g e me n t d e v i c e . At t h e s a me t i me,b y wa y o f c i r c u l a r g r o o v e t wo s e t t l e me n t s c a n a c hi e v e p u if r y d i l ut e a c i d p u if r ic a t i o n a nd me e t t h e r e q u i r e me n t s o f pr o d u c t i o n, wh i c h wa s wo r t hy o f
硫铁矿制酸工艺流程 PDF

硫铁矿制酸工艺流程 PDF
硫铁矿制酸工艺流程是一种重要的工艺流程,可以将硫铁矿中的硫酸盐和其他有价值的金属元素转化为高品质的硫酸和其他有价值的化学品。
下面是硫铁矿制酸工艺流程的详细介绍。
首先,硫铁矿经过破碎和磨粉等前处理工艺之后,被送入浸出器中进行浸出。
在浸出器中,硫铁矿与硫酸和水混合,形成硫酸浸出液。
浸出液经过离心分离和赤泥分离等处理之后,进入溶液处理工艺环节。
在溶液处理工艺中,浸出液中的硫酸盐、铜、铁等有价值金属元素得以被还原、分离和提纯。
具体地,溶液经过还原-中和、蒸发结晶、萃取、脱铜、脱铁、浊度调节等环节的处理,得到含有高品质硫酸和其他有价值化学品的溶液。
最后,溶液经过过滤、包装等后处理工艺,得到市场销售所需的高品质硫酸和其他化学品。
总的来说,硫铁矿制酸工艺流程是一种高效、环保的工艺流程,可以将硫铁矿中的有价值元素充分利用,减少对环境的影响,提高资源利用率。
硫铁矿制酸实施方案
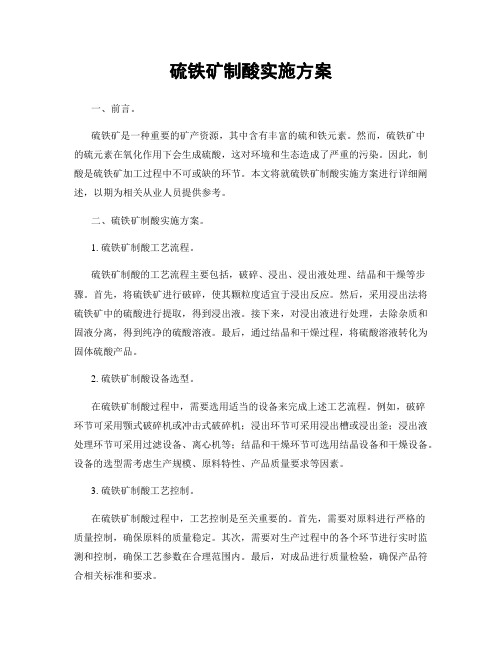
硫铁矿制酸实施方案一、前言。
硫铁矿是一种重要的矿产资源,其中含有丰富的硫和铁元素。
然而,硫铁矿中的硫元素在氧化作用下会生成硫酸,这对环境和生态造成了严重的污染。
因此,制酸是硫铁矿加工过程中不可或缺的环节。
本文将就硫铁矿制酸实施方案进行详细阐述,以期为相关从业人员提供参考。
二、硫铁矿制酸实施方案。
1. 硫铁矿制酸工艺流程。
硫铁矿制酸的工艺流程主要包括,破碎、浸出、浸出液处理、结晶和干燥等步骤。
首先,将硫铁矿进行破碎,使其颗粒度适宜于浸出反应。
然后,采用浸出法将硫铁矿中的硫酸进行提取,得到浸出液。
接下来,对浸出液进行处理,去除杂质和固液分离,得到纯净的硫酸溶液。
最后,通过结晶和干燥过程,将硫酸溶液转化为固体硫酸产品。
2. 硫铁矿制酸设备选型。
在硫铁矿制酸过程中,需要选用适当的设备来完成上述工艺流程。
例如,破碎环节可采用颚式破碎机或冲击式破碎机;浸出环节可采用浸出槽或浸出釜;浸出液处理环节可采用过滤设备、离心机等;结晶和干燥环节可选用结晶设备和干燥设备。
设备的选型需考虑生产规模、原料特性、产品质量要求等因素。
3. 硫铁矿制酸工艺控制。
在硫铁矿制酸过程中,工艺控制是至关重要的。
首先,需要对原料进行严格的质量控制,确保原料的质量稳定。
其次,需要对生产过程中的各个环节进行实时监测和控制,确保工艺参数在合理范围内。
最后,对成品进行质量检验,确保产品符合相关标准和要求。
4. 硫铁矿制酸安全与环保。
在硫铁矿制酸过程中,安全生产和环境保护是企业的重要责任。
因此,需要建立健全的安全管理制度和环保措施,确保生产过程安全稳定,减少对环境的影响。
同时,对生产人员进行安全培训和环保意识教育,提高员工的安全意识和环保意识。
5. 硫铁矿制酸技术改进。
随着科技的不断进步,硫铁矿制酸技术也在不断改进。
例如,采用先进的浸出设备和新型的浸出剂,可以提高硫铁矿的浸出率和硫酸的纯度;采用自动化控制系统,可以提高生产效率和产品质量;采用节能环保的干燥设备,可以减少能源消耗和环境污染。
某硫铁矿制酸厂废水处理现状

某硫铁矿制酸厂废水处理现状某硫铁矿制酸厂废水处理现状近年来,随着工业化进程的不断加快,环境污染问题日益严重。
尤其是在硫铁矿制酸工业领域,废水处理问题已成为亟待解决的难题。
本文就某硫铁矿制酸厂废水处理现状展开探讨。
硫铁矿制酸厂是指以硫铁矿为原料,通过酸化反应产生酸性废水的工厂。
常见的酸性废水成分包括硫酸铁、硫酸、硫酸氢铁等。
这些废水不仅酸度高,还含有大量的有害物质,如重金属离子、氨氮等,对环境和人体健康造成严重威胁。
目前,某硫铁矿制酸厂废水处理工艺主要包括物化方法与生物方法。
物化方法主要利用化学药剂进行沉淀、吸附、中和等处理过程;生物方法则利用微生物对废水中污染物进行降解分解。
但是,由于硫铁矿制酸废水的复杂性以及成本问题,传统的废水处理工艺存在一定的局限性。
首先,对于物化方法而言,传统的沉淀法处理废水存在效率低、处理量小、生成大量污泥等问题。
而吸附法仅针对特定有机物或金属离子具有良好的去除效果,很难应对废水中复杂组分的处理。
中和法虽然可以将废水中的酸碱度进行中和调节,但却无法解决其他有毒物质的去除问题。
其次,生物方法可以较好地对废水中的有机物进行降解,具有高效、环保的特点。
但由于硫铁矿制酸废水中存在大量硫酸根等有毒物质,抑制了微生物的生长,降低了处理效果。
同时,硫酸根的存在也使得废水处理过程中释放出大量硫化氢气体,给环境和人体带来安全隐患。
所以,为了改善某硫铁矿制酸厂废水处理现状,亟需引入先进的处理技术和方法。
一种可行的方式是采用化学生物联合处理工艺。
化学方法可以利用先进的药剂技术,如高分子吸附剂、氧化剂等,对废水中的有害物质进行深层去除。
生物方法可以利用改良后的微生物菌种,提高其对废水中硫酸根等有毒物质的耐受能力,实现高效降解。
此外,在硫铁矿制酸厂废水处理过程中,应加强对废水的前处理环节,避免其大量进入处理系统,减轻工艺设施的负担。
通过合理的预处理,如沉淀除杂、调节pH值等,可以有效降低废水中有机物和重金属离子的浓度,提高后续处理的效果。
硫铁矿制酸装置废水“零”排放的生产实践

硫铁矿制酸装置废水“零”排放的生产实践陈火木;胡春丽【摘要】介绍了云浮联发化工有限公司400 kt/a硫铁矿制酸装置通过工艺技术改进、环保设施完善、资源综合利用等措施推进废水“零”排放实践.技改后每年可以减少污水处理量30 000 m3以上,减少外排水量约9600 m3,减少石灰消耗约2500t,减少用电2.4×105 kWh,降低烧碱用量180 t,节约运行费用超过150万元,降低了环保和生产成本,提高了经济效益和社会效益.【期刊名称】《硫酸工业》【年(卷),期】2017(000)006【总页数】3页(P21-23)【关键词】硫铁矿;硫酸生产;废水;压滤;回用;技术改造【作者】陈火木;胡春丽【作者单位】云浮联发化工有限公司,广东云浮527343;云浮联发化工有限公司,广东云浮527343【正文语种】中文【中图分类】TQ111.16云浮联发化工有限公司(以下简称联发公司)是国产化产能最大的硫铁矿制酸装置,产能为400 kt/a,装置位于云浮市云安区硫化工产业园区内。
随着《中华人民共和国环境保护法》、《广东省环境保护条例》等相关环保法律法规及政策的出台,对企业环保工作的要求也越来越严格。
为了降低环保和生产成本,提高清洁生产水平,实现废水“零”排放,联发公司于2015年底通过工艺技术改进、环保设施改善、资源综合利用等手段推进废水”零”排放技改工作,通过一年多的实践运行,基本实现了硫酸生产装置的废水”零”排放。
1.1 技改前运行状况技改前硫酸装置水平衡如图1所示。
技改前配套了污水处理站,生产系统向污水处理站排放污水总量为96 m3/d。
其中酸性废水来自净化工序w(H2SO4)约15%的稀硫酸,为72 m3/d;一般工业废水则来自于装置锅炉及配套制水系统、生活污水等,为24 m3/d。
硫酸装置于2013年技改配套了尾气脱硫系统,脱硫采用双碱法撞击流吸收工艺,脱硫过程主要是NaOH与SO2反应生成Na2SO3,再生过程为石灰粉制乳后Ca(OH)2与Na2SO3反应再生成NaOH和CaSO3沉淀[1]。
硫铁矿制酸装置污酸脱砷生产实践

硫铁矿制酸装置污酸脱砷生产实践摘要:硫铁矿制酸污酸,就是指一些会给周遭环境带来极大污染的重金属,形状复杂的污染物等。
目前虽然我国正在大力地进行各类改造,增添排污口增加相关设施以及人员处理这些有害物质,但是仍然会有很多疏漏。
这些疏漏导致的结果,就是有些工厂能力有限,没有办法或者是没有资金去对污染物进行一个很好的处理。
处理污染物的时候,简单粗暴,将他们直接排进土壤和污水中。
这非常不利于人类赖以生存的环境。
用硫铁矿制酸时硫铁矿中含有重金属砷,某公司生产硫酸使用的硫铁矿一般w(As)为0.1%左右,经净化洗涤后污酸中ρ(As)最大约为1050mg/L,如果这部分砷不除掉,不能满足环保要求且给污水处理和后序使用带来不便。
现以某公司为例,介绍将污酸中砷去除后稀酸供工厂使用的生产实践。
关键词:硫铁矿制酸;污酸;脱砷装置;节能减排1污酸来源介绍了某公司硫铁矿制酸装置污酸处理系统工艺流程、脱砷装置及运行情况。
由于硫铁矿中含有重金属砷,制酸装置产生的污酸未除砷而直接用石灰中和,不利于稀酸的循环利用,同时产生大量中和渣。
该公司现有3套系统200kt/a硫铁矿制酸装置,一、二系统净化采用空塔+填料塔+电除雾器流程,三系统净化采用动力波洗涤器+填料塔+电除雾器流程,污酸排出量为6m3/h。
原来这部分污酸直接进污水处理站用石灰中和,产生大量中和渣,也造成资源浪费,现将其处理达标后供工厂使用。
2污酸处理的必要性工艺流程2.1必要性任何化工厂,在运作的过程中,都不可避免地会排出有毒有害的物质或者气体。
如果化工厂将这些污染物排放在了土地、河流中,它不仅仅会影响植物的生长繁殖发育,还会影响整个生物链。
如果最终有毒有害的物体流入了水中,最终被人们饮用,将会给人们的身体带来不可恢复的伤害。
其实污染物也是很好区分的。
在处理废水的过程中,通过一定时间的静置,水会沉淀下去,这些有害、有毒的金属物质会漂浮上来,可以将这一部分漂浮上来的物质分离出来单独进行处理。
硫铁矿制酸工艺流程

硫铁矿制酸工艺流程硫铁矿制酸工艺流程硫铁矿(FeS2)是一种常见的含有硫和铁的矿石,通过对硫铁矿的处理可以提取出硫酸。
硫酸在工业生产中有广泛的应用,可用于制造肥料、废水处理、金属加工等。
以下是硫铁矿制酸的一般工艺流程。
首先,硫铁矿通常需要经过破碎、磨矿和浮选等过程进行预处理。
这些过程的目的是将矿石的粒度减小,并通过浮选将金属硫化物从其他杂质中分离出来。
磨矿过程通常使用球磨机进行,将硫铁矿矿石磨成粉末。
然后,磨碎后的硫铁矿经过浸出处理。
浸出是将硫铁矿与稀硫酸溶液进行接触,使硫铁矿中的硫化物反应生成硫酸。
浸出可以使用浸出罐或酸浸塔来进行,硫铁矿和稀硫酸溶液逆流而上接触,反应生成硫酸并溶解于溶液中。
接下来,溶液经过过滤或沉淀工艺,将固体硫铁渣从溶液中分离出来。
过滤通常使用压滤机进行,将硫铁渣分离出来后,压滤机会将溶液流出。
硫铁渣可以作为生铁冶炼的回收利用。
随后,分离出的溶液需要进行浓缩。
浓缩可以使用多效蒸发器实现,通过多次蒸发和冷凝循环,将溶液中的水分逐渐蒸发,使得硫酸得以浓缩。
多效蒸发器具有高效、连续化的特点,能够达到高浓度硫酸的制备要求。
最后,浓缩后的溶液需要进行脱水处理,使得硫酸得以进一步浓缩。
脱水可以使用蒸汽脱水器或其他脱水设备实现,将溶液中的水分蒸发掉,使硫酸浓度进一步提高。
脱水后的溶液即为浓硫酸。
综上所述,硫铁矿制酸的工艺流程包括破碎、磨矿、浮选、浸出、过滤、浓缩和脱水等过程。
这些过程通过物理和化学反应将硫铁矿转化为硫酸,得到高浓度的硫酸用于工业生产中的各种应用。
硫铁矿制酸工艺流程的优化可以提高硫酸的产率和品质,降低生产成本,提高工艺效益。
60万吨年硫铁矿制酸污酸污水系统升级改造及其再利用

60万吨/年硫铁矿制酸污酸污水系统升级改造及其再利用铜陵市华兴化工有限公司 张健 陈银根 王晓颜【摘 要】 本文重点讨论了硫酸污酸污水的再优化设计及其处理后的中和水回用,真正做到了硫铁矿制酸系统的污水零排放。
【关键词】 硫酸 污酸 污水 再利用铜陵市华兴化工有限公司现有三套硫铁矿制酸系统,装置设计能力200kt /a ×3(实际生产能达到660kt/a)。
随着硫酸污水排放标准越来越严格,尤其氨氮等指标越来越苛刻,为此必须要求将原来的污水系统升级改造,同时要求处理后的中水要再循环利用。
华兴化工的污水处理系统于2014年6月投用,投资少,见效大。
现将该系统总结如下,以便给以后的硫铁矿制酸系统污水处理系统设计以启迪。
1 概述华兴公司现有硫酸厂、精细化工公司、磁选车间、动力车间四个生产单位。
硫酸净化排出的稀酸及全公司总污水检测如下:表一污水检测结果表水源pHAs(mg/L)NH3-N(mg/L)悬浮物(mg/L)COD(mg/L)F-水量(m3/h)硫酸厂污水 6.31 0.78 17.8 105 未检出9.6 46.95 硫酸厂污酸 2.60% 69.78 215.6 340 397 1050.8 5 磁选车间污水 2.4 6.4 5.62 243 1350 26.9 9.8 同时要求的出水水质要达到国家规定的排放标准如下:表二国家规定出水水质排放标准表序号项目标准1 COD(mg/L) 602 F-(mg/L) 103 SS(mg/L) 504 pH 6~95 A s (mg/L) 0.3※※:根据《硫酸工业污染物排放标准》(GB26132-2010)的相关要求,现有装置污水As含量2013年9月30日前为0.5mg/L,2013年10月1日起为0.3mg/L。
226硫酸厂废水、净化稀酸中含有硫酸、亚硫酸、As3+、As 5+、F-、Fe2+、Fe3+等, 当加入氢氧化钙时,会发生下列反应:(1)中和反应Ca(OH )2+H2SO4 =CaSO4↓+2H2OCa(OH )2+H2SO3 =CaSO3↓+2H2O(2) 脱砷反应3Ca(OH)2+2A sO43- =Ca3(AsO4)2↓+6OH-Ca(OH)2+As2O3 =Ca3(AsO2)2↓+H2OCa(OH)2+Fe2+=Fe(OH)2↓+Ca2+3Ca(OH)2+2Fe3+=2F e ( O H ) 3↓+3Ca2+As2O3+2Fe(OH)2= Fe2 As2O5↓+2H2O3A s2O3+2Fe (OH)3= 2Fe (AsO2)3↓+3H2O2AsO43-+3Fe ( OH ) 2 =Fe3 (AsO4)2↓+6OH-AsO43-+Fe(OH)3=FeAsO4↓+3OH-通过反复多次实验得出结论:利用石灰石、电石渣对净化稀酸进行中和、除砷,将pH调节至6.8~7.3,即可到达溶液中As含量<0.3mg/L的目标。
硫铁矿制酸工艺

硫铁矿制酸工艺1. 简介硫铁矿是一种常见的含有硫化铁矿物的矿石,其在工业生产中具有重要的应用价值。
硫铁矿制酸工艺是通过处理硫铁矿矿石,将其中的硫化铁转化为硫酸铁,从而实现硫铁矿的资源利用。
2. 工艺流程硫铁矿制酸工艺一般包括以下几个主要的步骤:2.1 矿石选矿在硫铁矿的制酸工艺中,首先需要将原始的硫铁矿矿石进行选矿处理。
选矿的目的是通过物理或化学方法去除矿石中的杂质,提高硫铁矿的品位,减少后续工艺处理的困难度。
2.2 矿石破碎经过选矿处理后的硫铁矿矿石需要进行破碎,以满足后续的工艺要求。
破碎方法可以采用机械破碎、磨碎或者化学溶解等不同的方式。
2.3 矿石浸取硫铁矿的制酸工艺中,矿石浸取是其中一个关键步骤。
通过将破碎后的硫铁矿矿石与酸性溶液接触,使硫化铁发生氧化反应,从而转化为硫酸铁。
此过程需要控制浸取的温度、酸浓度等因素,以提高反应的效率。
2.4 硫酸铁的制备经过矿石浸取后,得到的溶液中含有硫酸铁。
为了获得高纯度的硫酸铁产品,还需要进行进一步的提纯和加工。
一般经过沉淀、过滤、蒸发等工艺步骤,最终得到纯度较高的硫酸铁。
2.5 产品后处理制备好的硫酸铁产品可能还存在一定的杂质,因此需要进行后处理工艺。
后处理工艺可包括过滤、热处理等步骤,以获得符合工业标准的硫酸铁产品。
3. 工艺优化和问题解决在硫铁矿制酸工艺中,为了提高工艺效率和产品品质,常常需要进行工艺优化和问题解决。
以下是一些建议和措施:•通过选择合适的选矿方法,去除矿石中的杂质,提高硫铁矿的品位。
•优化矿石破碎的工艺参数,以获得符合要求的破碎度。
•控制矿石浸取的温度、酸浓度等因素,以提高浸取效率。
•加强对硫酸铁制备过程中反应条件的监控,避免产生不合格的产品。
•配备先进的设备和控制系统,提高工艺的自动化和智能化程度。
•进行定期的设备维护和保养,确保工艺设备的正常运行。
•提高工作人员的技能和工艺水平,以便更好地处理工艺中出现的问题。
4. 应用和前景展望硫铁矿制酸工艺作为一种重要的资源利用和化工生产方法,在冶金、化工、环保等领域具有广泛的应用前景。
磁铁矿的矿石脱硫和酸性废水处理技术

磁铁矿的矿石脱硫和酸性废水处理技术磁铁矿是一种重要的铁矿石资源,被广泛应用于钢铁制造和其他工业领域。
然而,在磁铁矿开采和加工过程中,常常伴随着脱硫和产生大量酸性废水的问题。
因此,磁铁矿的脱硫和酸性废水处理技术成为了矿石加工过程中的关键环节。
一、磁铁矿的脱硫技术磁铁矿中通常含有硫化物矿物,如黄铁矿(FeS2)等,当这些硫化物与氧气接触时,会生成二氧化硫(SO2)等气体物质,造成矿产环境的污染,同时也对工人的健康产生危害。
因此,实现磁铁矿的脱硫是十分重要的。
目前,磁铁矿脱硫技术主要包括物理破碎和化学法两种方式。
物理破碎法是利用机械设备将磁铁矿石进行破碎,使硫化物矿物与空气充分接触,加速氧化反应,以降低磁铁矿中硫化物的含量。
然而,该方法破碎过程中容易造成细微颗粒的产生,进一步造成环境污染,并且处理过程中由于破碎机的振动和噪音也会对环境和工作人员产生影响。
化学法是利用化学试剂对磁铁矿进行处理,主要包括浸出法、浮选法和熔融法等。
浸出法是指将化学试剂浓度高的溶液与磁铁矿接触,使其中的硫化物溶解,然后通过分离步骤将溶液中的硫化物去除。
浮选法是利用特定的药剂和气泡将硫化物矿物与其他矿物分离。
熔融法则是将磁铁矿与熔融剂一同熔化,通过熔融剂对硫化物矿物进行提取。
二、酸性废水处理技术磁铁矿的开采和加工常常伴随着产生大量的酸性废水,这些废水中通常含有大量的金属离子和酸性物质,对环境造成严重的污染。
酸性废水处理技术主要包括中和法和沉淀法两种方式。
中和法是通过加入碱性物质,如石灰、纯碱等,将酸性废水中的酸中和为中性或碱性。
中和反应会生成一些沉淀物,通过沉淀物的分离可以达到废水处理的目的。
中和法是一种常见且有效的酸性废水处理技术,但在处理过程中需要注意控制反应的速率,避免剧烈反应引发的溅射和气体释放等安全问题。
沉淀法是通过加入沉淀剂将酸性废水中的金属离子沉淀下来形成固体沉淀物,进而分离。
常用的沉淀剂包括氢氧化钙、氢氧化镁等。
硫铁矿制酸项目污染治理及环境影响的分析
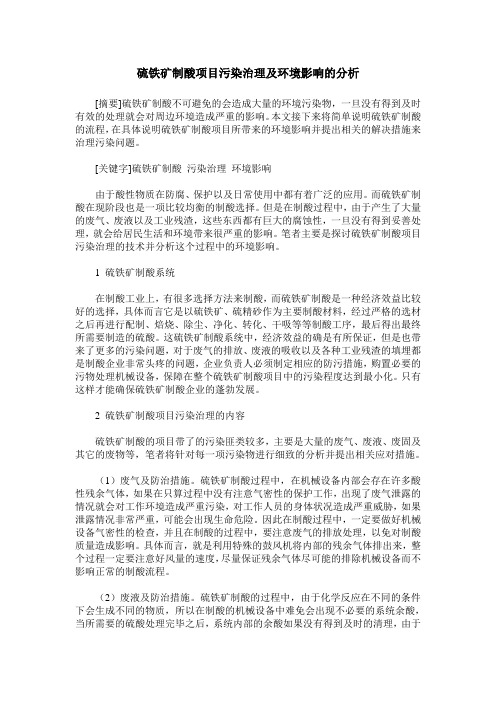
硫铁矿制酸项目污染治理及环境影响的分析[摘要]硫铁矿制酸不可避免的会造成大量的环境污染物,一旦没有得到及时有效的处理就会对周边环境造成严重的影响。
本文接下来将简单说明硫铁矿制酸的流程,在具体说明硫铁矿制酸项目所带来的环境影响并提出相关的解决措施来治理污染问题。
[关键字]硫铁矿制酸污染治理环境影响由于酸性物质在防腐、保护以及日常使用中都有着广泛的应用。
而硫铁矿制酸在现阶段也是一项比较均衡的制酸选择。
但是在制酸过程中,由于产生了大量的废气、废液以及工业残渣,这些东西都有巨大的腐蚀性,一旦没有得到妥善处理,就会给居民生活和环境带来很严重的影响。
笔者主要是探讨硫铁矿制酸项目污染治理的技术并分析这个过程中的环境影响。
1 硫铁矿制酸系统在制酸工业上,有很多选择方法来制酸,而硫铁矿制酸是一种经济效益比较好的选择,具体而言它是以硫铁矿、硫精砂作为主要制酸材料,经过严格的选材之后再进行配制、焙烧、除尘、净化、转化、干吸等等制酸工序,最后得出最终所需要制造的硫酸。
这硫铁矿制酸系统中,经济效益的确是有所保证,但是也带来了更多的污染问题,对于废气的排放、废液的吸收以及各种工业残渣的填埋都是制酸企业非常头疼的问题,企业负责人必须制定相应的防污措施,购置必要的污物处理机械设备,保障在整个硫铁矿制酸项目中的污染程度达到最小化。
只有这样才能确保硫铁矿制酸企业的蓬勃发展。
2 硫铁矿制酸项目污染治理的内容硫铁矿制酸的项目带了的污染匪类较多,主要是大量的废气、废液、废固及其它的废物等,笔者将针对每一项污染物进行细致的分析并提出相关应对措施。
(1)废气及防治措施。
硫铁矿制酸过程中,在机械设备内部会存在许多酸性残余气体,如果在只算过程中没有注意气密性的保护工作,出现了废气泄露的情况就会对工作环境造成严重污染,对工作人员的身体状况造成严重威胁,如果泄露情况非常严重,可能会出现生命危险。
因此在制酸过程中,一定要做好机械设备气密性的检查,并且在制酸的过程中,要注意废气的排放处理,以免对制酸质量造成影响。
硫铁矿制酸酸洗封闭净化实践的体会

硫铁矿制酸酸洗封闭净化实践的体会
吴世有
【期刊名称】《化学工业与工程技术》
【年(卷),期】1993(000)001
【总页数】2页(P53-54)
【作者】吴世有
【作者单位】无
【正文语种】中文
【中图分类】TQ111.14
【相关文献】
1.全封闭酸洗净化工艺及污水处理的应用 [J], 郭梁;茹江林;等
2.硫铁矿制酸装置净化工序炉气除氟实践 [J], 赵信刚
3.76%酸洗净化工艺改为稀酸洗的设计与实践 [J], 何明安;左永伟
4.封闭酸洗净化技术总结 [J], 陈富生;周汉斌
5.铜冶炼烟气制酸半封闭稀酸洗净化工艺探讨 [J], 蒋蕴华
因版权原因,仅展示原文概要,查看原文内容请购买。
- 1、下载文档前请自行甄别文档内容的完整性,平台不提供额外的编辑、内容补充、找答案等附加服务。
- 2、"仅部分预览"的文档,不可在线预览部分如存在完整性等问题,可反馈申请退款(可完整预览的文档不适用该条件!)。
- 3、如文档侵犯您的权益,请联系客服反馈,我们会尽快为您处理(人工客服工作时间:9:00-18:30)。
s。
板框系统仍可保持良好的固液分离效果,每天压 滤出来的烧渣滤饼约20 m3,最高可达35 m3,滤 饼成形,无表面水分(如图4所示),运输出售都 比较方便,滤液基本清澈,为后续的石膏和中和处 理系统减轻了压力。板框压滤系统经试验可以运 用在硫铁矿制酸净化污酸的固液分离方面,且处 理量可调。 本公司在焙烧制酸烟气含尘净化在电除尘器 几乎失效的情况下,出电除尘器烟尘含量最高达 到10 g/m3。电除尘器在工艺应用过程中,特别 是烟气中含SO,,粉尘细黏,形成硫酸盐状物质, 电除尘器难以长期高效运行,电除尘器壳体、极板 腐蚀,泄漏气体,极间搭桥短路,每次周期大修都 属重点维修设备,维修周期长,费用昂贵,其运行 除尘效果较差时,给湿式后续烟气净化带来灾难 性压力。 本公司通过对烟气湿法净化污酸固液分离系 统改造及运行经验,在烟气粉尘干法净化过程中 取消传统的电收尘器成为可能,笔者认为焙烧烟
一般通过进料时间的延时可以降低滤饼的含 水率,使滤饼干爽,易于成型。但是延时的时间过 长又会增加过滤的时间周期,降低系统的过滤效 率,这就我们需要寻找一个既能保证滤饼的干爽 成型,又不影响过滤周期的时间节点。目前我们 控制延时1
800
s。
2.3.5延长风干时间 滤饼在经过压榨后,往往需要通人压缩空气
・106・
2012年全国硫酸工业技术交流会论文集
对空腔内的滤饼进行进一步的吹干,适当延长风 干的时间,可以进一步减少滤饼中的含水量,j亨便 滤饼的卸渣。目前我们将风干时间控制在150 2.3.6加强工艺指标的控制 焙烧制酸过程中难免会产生单质硫,在设备 中发现升华硫,易造成设备的堵塞,特别是在.±lttd, 的管道或孔眼中,其影响更大。在硫铁矿制酸系 统中,控制好焙烧过程中的烟气含氧量,抑制j十华 硫的出现,减少系统中升华硫的存在,对于提高过 滤的通畅性、提高设备的过滤效率有着重要的影 响。 2.3.7更换滤布 滤布使用一段时间后,一些细小的物料颗粒 会在滤布的表面堆积,堵塞滤布的孔隙。在浆液 浓度未发生明显变化时,当发现过滤时间偏长、滤 饼含水量、卸料困难时,则需要对滤布进行清洗, 若经清洗后过滤效率没有明显提高,则需要对滤 布进行更换,更换周期一般在28 d左右。 2.4净化稀酸固液分离改造存在的问题及改进 措施
£——板框压滤机空腔距离,在这里取4
10~rn。
X
过滤的有效性,提高了滤布的自动清洗频率,平均 两个周期约4 h,进行高压在线自动清洗1次,为 节省滤布,运行1周左右再拆下通过工业彻底洗 涤一次,延长滤布使用寿命。
2.3.4进料延时时间
则,由公式(1)得A=158.73 m2,故板框压滤 机面积应选160 m2。考虑到设备的体积及现有空 间的位置,在实际生产中选用两台80 m2的设备。 滤布在过滤过程中起关键的作用,其性能的 好坏直接影响过滤的效果,因此滤布的选择也很 重要。为了达到比较理想的过滤效果和速度,我 们需要根据物料的颗粒大小、密度、黏度、化学成 分以及过滤工艺条件来选择合适的滤布。 2.3影响板框压滤机过滤效果的因素 我们所选用的板框压滤机为增强聚丙烯厢式 压滤机,过滤面积为160 rn2,过滤压力为0.6
和工序 处理
滤饼
图3改造后石膏工艺流程 2。2主要设备的选型 2.2.1膜过滤器的选型 在正常的状态下,净化动力波的循环酸含尘 量约为4 g/L,根据厂方提供的参数,含尘量在
3~5
g/L范围内,膜的过滤系数为0.8 m3/(h・
m2)。
沈涛等.
磁硫铁矿制酸净化污酸固液分离工艺改造实践
・105・
按照设计要求,动力波的循环酸量为1
X103 kg/m3;
rn3。
则,所需板框压滤机的容积为V=2.86 根据经验公式: V=0.9‰论=0.9 X{(A/2)×L} 式中:‰论——板框压滤机理论容积; A——板框压滤机的面积;
2.3.3介质黏性 过滤介质的黏度的大小,也会影响到过滤的
(1)
效果。黏性越大,过滤时的阻力也就越大,而且容 易堵塞滤布的孔眼。我们的浆液中含有焙烧过程 中形成的细尘及土灰,脱水时的黏性大;为了保持
考虑到设备空间、场地及设备维护等方面的因 素,故采用2台过滤面积为62.5 m2的膜过滤器。 2.2.2板框压滤机的选型 压滤机作为一种固液分离设备,应用于:工业 生产已有较长的历史,但在稀酸过滤中的使用尚 不多见。因此针对我们的工况,需要工业化试验 的验证。 据调查,国内常用压滤机的过滤面积为1~
电石渣
图2原设计中和工艺流程
1.2污水处理存在问题 在实际的生产过程中,大量使用低硫高铁精 砂与高硫精砂进行搭配,使得平均入炉伽(S)只 有约30%,W(Fe)约48%,原设计使用原料为 训(S)≥36.5%,为保证硫酸生产负荷,需提高投 料量和焙烧强度。由于原料性质的影响,焙烧产 生的残渣量大,粉尘的粘性也大,致使电收尘器的 运行困难,收尘效果差,从而导致大量粉尘带人净 化系统,大大超过设计值200 mg/m3,最高可:达10 g/m3。大量粉尘进入动力波循环酸内,CN过滤 器基本失效,排出废酸含尘量高达50 g/L,结果导 致石膏离心机堵塞频繁。废酸若直接打到中和调 节池,由于酸浓和含尘量远高于原设计值,致使污 水中和系统的压力大增,但在提高烧渣综合利用 率的前提下,不能改变原料配比和焙烧工艺,需要 从污酸的固液分离方面人手,设法减少污酸中的 含固量,提高环保设施的运行效率。
表1磁黄铁矿成分
全S
22.76
磁S
19.10
SOi
0.18
S2一
全Fe
56.22
Fe304
Fe203
3.02
Fe。S。+l 29.2
FeC03 2.15
FeS2 0.1l
FeSi03
O.54
21.90
21.56
和工序 处理
滤饼
图1
原设计石膏工艺流程
・104・
2012年全国硫酸工业技术交流会论文集
电石渣
焙烧炉烟气一余热锅炉H旋风除尘器H燃l
卜雾器H除湿塔H曩嚣l
图4烟气除尘净化工艺 将原三级电除尘器、动力波除尘洗涤工艺改
为多管除尘器、动力波洗涤,对净化污酸进行固液 分离,设备空间布置相对简洁,烟气净化效果也能 达到要求,烟气除尘净化系统可以避免传统电除 尘器的诸多问题及昂贵的周期性大修费用。对动 力波循环液进行固液分离(图5):
4结束语
铜陵有色铜冠冶化分公司2012年3月完成 对磁硫铁矿烟气净化污酸固液分离工艺的改造, 经过采用膜过滤器、浓密机、板框压滤机的应用对 循环酸高固含量进行液固分离预处理,通过5个 月的运行实践证明,对处理硫铁矿制酸净化工序 较高含固量的污酸进行分离是可行的:
000
MPa。根据其实际运行情况,对影响板框压滤机 过滤效果的以下因素进行了控制:
2.3.1
m3/h,引W(H:SO。)10%的稀酸进膜过滤器过滤 后回净化系统,则需要处理的酸量为100 通过计算可得需要的膜过滤面积125
n13/h。 m2。
浆液浓度
在设备状况稳定的条件下,滤饼产量主要取决 于浆液浓度的大小。随着浆液浓度的提高滤饼形 成速度加快,因为压滤机的空腔体积是一定的,浆 液浓度越高,所需的进料时间越短,而且浆液浓度 的提高,有利于滤饼在滤布上的生成,提高了设备 的生产率,将固含量(训)控制在10%一15%比较合 适。 膜过滤器初步浓缩过程中需选用超高分子量 阳离子型絮凝剂进行絮凝,以克服超细粉尘难以 过滤的影响,选择合适孔径的膜及防堵措施,稳定 膜过滤器正常运行。 2.3.2滤布性能 压滤机的过滤过程主要靠滤布的过滤形成 的,滤布性能的好坏直接影响到过滤的效果和效 率,因此要根据过滤物料的pH值或酸浓度、固体 粒径等因素选用合适的滤布,以保证过滤的效率。 通过与滤布厂家的团结协作,不断试验摸索,我们 最终选择了黑达斯较为致密耐蚀滤布。
3烟气除尘可以不使用电除尘器
铜冠冶化公司的2台板框压滤系统于2011 年底投入试用,运行至今已有半年多时间,目前2 套硫酸系统每天通过膜过滤器排放含固污酸量约
500
干滤渣
m3,将其全部通过浓密机和板框压滤机处理,
图5净化循环酸分离工艺
洗涛等
醋硫铁矿制酸净化污酸固液分离工艺改造实践
・107
率有适度提高,有利于环保治理。 b循环酸应用膜过滤器进行初步浓缩需选 用合适的絮凝剂,选择合适孔径的膜,在运行过程 中需有膜防堵措施,可以达到初步浓缩长周期运 行的II标。 C从硫酸净化循环酸固液分离工艺改造实 践中受到启发,电除尘器运行不适应的除尘烟气, 图6压滤出来的烧渣滤饼 完全可以取消电除尘器,在电除尘器的位置改设 冶金行业普遍使用的高效低阻耐磨多管除尘器,
滤布故障
气粉尘分离采用以下工艺流程(图4)可能更适用 更经济:
在改造装置的试运行中,最常见的问题是滤布 堵塞和破损的问题,滤布小孔堵塞也影响了过滤效 率和滤饼的成型,曾出现过最长6 h才完成一个周 期的运行,且滤饼黏结,不易卸料。经过分析对比 多种滤布使用周期、过滤效果等数据,最终确定适 合于我们物料的滤布型号,该型号滤布过滤效果 好,不易破损,且效率较高(平均周期为2 h)。 2.4.2管道堵塞 通过调节浓密机底流泵频率控制回流量,回 流量低,管道容易堵塞,影响生产,回流量大,没有 浓密效果,经多次摸索确定了泵的高速进液转速 和低速回流转速,管道没有再出现堵塞的情况。
W,%
1.1原料及生产概况 铜陵有色铜冠冶化分公司目前有2套生产能 力为400 kt/a的硫酸生产线,焙烧制酸所采用的 原料为铜尾矿磁黄铁矿精砂。原料矿性质较为特 殊(见表1),粒度细(精矿粒度为325目的约占 75.3%,见表2)、磁硫铁矿含量高(黄铁矿中s 与磁黄铁矿中的S质量比为51.71:48.29)、发热 量大,对装置及设备的要求较高。根据浮选后原 料矿中S、Fe的品位和性质不同,可将原料矿分为 两2种:一种为高硫精砂,含有效硫W(s)约44 %,铁W(Fe)约42%;一种为低硫高铁精砂,含有