复合模设计说明书
倒装复合模设计说明书
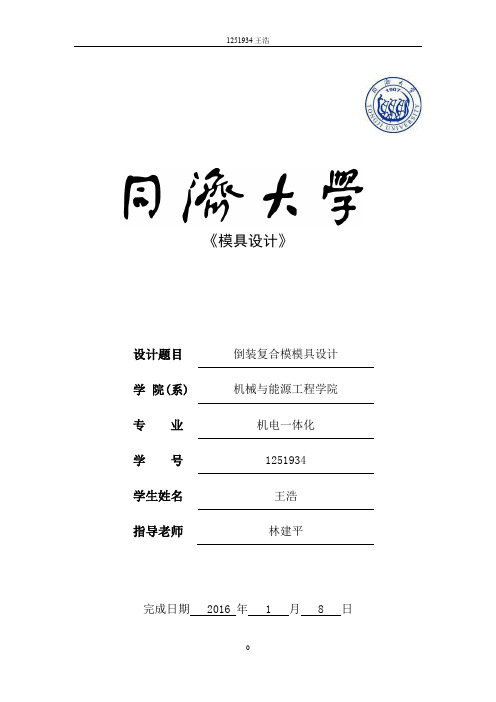
《模具设计》设计题目倒装复合模模具设计学院(系) 机械与能源工程学院专业机电一体化学号1251934学生姓名王浩指导老师林建平完成日期 2016 年 1 月 8 日目录引言 (3)一.分析零件工艺性 (4)1.冲裁件造型 (4)2.冲裁件工艺分析 (4)3.冲压工艺方案的确定 (4)二.毛坯排样方案设计及材料利用率计算 (5)1.排样方法的确定 (5)2.布置方式的确定 (5)三.冲裁力及压力中心计算 (6)1.冲裁力的计算 (6)2.其他冲压力计算 (6)四.选择压力设备 (6)五.模具总体结构设计 (7)1.送料方式 (7)2.卸料和出件方式 (7)3.凹模板外形尺寸的计算 (8)4.其他模板尺寸的确定 (8)5.模架的选择 (9)六.主要零件设计 (10)1.凸、凹模零件设计 (10)2.卸料和顶件装置设计 (12)七.其他零件设计 (14)1.模柄的设计 (14)2.螺钉的选择 (14)3.圆柱销的选择 (14)八.校核模具高度 (14)九.课程总结 (15)参考文献 (16)附录 (17)1.下模座 (17)2.下模垫板 (18)3.凸凹模固定板 (19)4.卸料板 (20)5.凹模板 (21)6.空心垫板 (22)7.凸模固定板 (23)8.上模垫板 (24)9.上模座 (25)10.凸凹模 (26)11.推块 (27)12.冲孔凸模 (28)13.总装图 (28)引言随着我国科学技术的进步、社会经济快速发展,模具成型技术及模具设计与制造已成为当代工业生产的重要手段。
近十几年来,中国模具工业发展十分迅速,特别是高新技术企业的快速发展加大了用于技术进步的投资力度,技术进步已成为企业发展的重要动力。
虽然我国的模具工业和技术得到了快速发展,但与国外工业发达的国家相比仍存在较大差距,未来的中国模具工业和技术的发展空间是巨大的。
冷冲压式利用安装在压力机上的冲模对材料施加压力,使其产生分离或塑形变形,从而获得所需要零件(俗称冲压件或冲件)的一种压力加工方法。
落料冲孔复合模设计说明书

摘要我的毕业设计是落料冲孔复合模的设计,冲压模具主要是将板料分离或成形而得到制件的加工方法。
因为模具的生产主要是大批量的生产,而且模具可以保证冲压产品的尺寸精度和产品质量,模具的设计与制造主要考虑到模具的设计能否满足工件的工艺性设计,能否加工出合格的零件,以及后来的维修和存放是否合理等。
在本次设计中,不仅要考虑要使做出的零件能满足工作要求,还要保证它的使用寿命。
其次设计中还要考虑到它的实际工作环境和必须完成的设计任务,采用倒装复合模,凸凹模的外形和内型孔、凹模型孔采用数控线切割机床加工,在设计中我要考虑到很多关于我所设计模具的知识,包括它的使用场合、外观要求等,从这里可以知道模具设计是一项很复杂的工作,所以在设计要不断的改进直到符合要求。
关键词:落料;工艺性;凸凹模;复合模;AbstractMy graduation project is the blanking piercing die, stamping die mainly to isolated or forming the sheet metal processing methods are workpiece. Because molds are mainly high volume production, and stamping die products can ensure the dimensional accuracy and quality, mold design and manufacture of primary consideration to the mold design can meet the design process the workpiece, can process a qualified parts, and, later, maintenance and storage is reasonable. In this design, not only to consider making the parts to make to meet the job requirements, but also to ensure its service life.Second, the design should also take into account the actual work environment and must complete the design task, using inverse compound die, the shape of main punch the holes, die hole model used CNC Cutting Machine, I have to take into account in the design a lot on my knowledge of mold design, including its use of occasions, appearance requirements, from here you can know that mold is a very complex task, so to continuous improvement in the design until it meets the requirements.Keyword: blanking; Technological efficiency;main punch;compound die;前言随着科学技术的发展需要,模具已成为现代化不可缺少的工艺装备,模具设计是机械专业一个最重要的教学环节,是一门实践性很强的学科,是我们对所学知识的综合运用,通过对专业知识的综合运用,使学生对模具从设计到制造的过程有个基本上的了解,为以后的工作及进一步学习深造打下了坚实的基础。
落料拉伸复合模设计说明书.
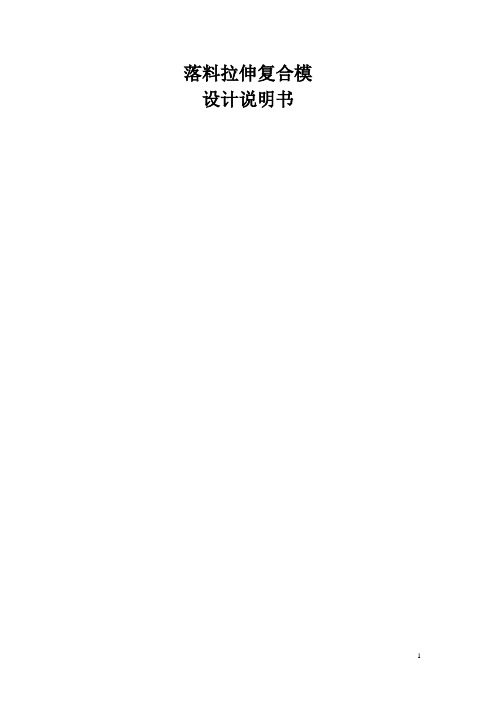
落料拉伸复合模设计说明书目录第一部分冲压成形工艺设计 (4)1.冲裁件的工艺性分析 (4)1.1材料分析 (4)1.2结构分析 (4)1.3精度分析 (5)2.确定冲裁工艺方案 (5)2.1工序性质和数量 (5)2.1.1工序性质的确定 (5)2.1.2工序数量的确定 (5)2.2工序顺序和组合 (5)2.2.1工序顺序 (5)2.2.2工序组合方式的选择 (6)2.3冲压工艺方案 (6)2.3.1工艺方案 (6)2.3.2工艺方案分析 (7)3.必要的工艺计算 (7)3.1确定零件修边余量 (7)3.2预算坯料尺寸D (7)3.3用逼近法确定第一次拉深直径 (9)3.4判断是否采用压边圈 (10)3.5确定拉深次数 (10)3.6预算各次拉深直径 (10)4.排样计算 (11)4.1排样方法 (11)4.2搭边与料宽 (11)4.2.1搭边 (11)4.2.2条料宽度 (12)第二部分冲压模具设计 (13)1.确定冲模类型机型结构形式 (13)2.计算工序压力 (13)3.落料、拉深、复合模工艺计算 (14)3.1凸、凹模刃口尺寸的确定 (14)3.2凸、凹模配合加工时的工作部分尺寸 (14)3.2.1落料凸、凹模刃口尺寸计算 (14)3.2.2首次拉深凸、凹模尺寸计算 (15)3.2.3二次拉深凸、凹模尺寸计算 (15)参考文献 (15)绘制CAD图 (16)小结 (22)第一部分冲压成形工艺设计1.冲裁件的工艺性分析如图1-1,材料为10钢,大量生产。
试制定工件冲压工艺规程,设计其模具,编制零件的加工工艺规程。
图1-1有凸缘圆筒件1.1材料分析10钢为优质碳素结构钢。
具有较好的拉深性能。
冷应变塑性高,板材正火或高温回后性能及佳,切削性,冷拉正火较退火态好。
1.2结构分析零件为一有凸缘筒形件,结构简单,底部圆锥半径r=5,满足筒形件试音圆角半径大于一倍料厚的要求,因此,零件具有良好的结构工艺性。
冲压模具设计说明书复合模

冲压模具设计说明书班级:G08 模具(3)班姓名:楼小波学号:19卢鹏程20工件名称:传动片工件见图:如图(1)生产批量:大批量A3材料:厚度:2mm1•此工件只有落料和冲孔两个工序。
材料为Q235—A钢,具有良好的冲性能,适合冲裁。
抗剪图(,抗310~380 t/MPa度为工件结构相。
240 6 b/MPa 6 b拉强度为380~470 /MPa ,屈服强度为的孔,孔与孔,孔与边缘之间的距离也满足10个①对简单,有2127MM,工件除了为IT11级外,其余都是要求,最小壁厚为0-0.11IT14级。
尺寸精度较低,普通冲裁完全能满足要求。
2. 冲裁工艺方案的确定该工件包括落料、冲孔两个基本工序,可有以下三种工艺方案:方案一:先落料,后冲孔。
采用单工序模生产。
方案二:落料—冲孔复合冲模。
采用复合模生产。
方案三:冲孔—落料级进冲模。
采用级进模生产。
方案一结构简单,但需要两道工序两副模具,成本高生产效率低,难以满足大批量生产的要求。
方案二只需要一副模具,工件精度及生产效率都教高,工件最小壁厚为7MM 模具强度较好。
方案三也只需要一副模具,生产效率高,操作方便,但是制造精度.不如复合模。
通过对上述三种方案的分析比较,该件的冲压声场采用方案二为佳,即复合模。
3. 主要设计计算(1)排样方式的确定及其计算传动片的形状为左右对称,下端水平,采用直对排效率较高。
如图(2)所示的排样方法。
查(《冲压工艺与模具设计》表2.5.2 )所得,工件间a1=2MM ,沿边a2=2.2MM ,条料宽度为70MM ,步距S=32MM ,一个步距的材料利用率为56% 。
计算部分见表(1)。
32图(2)(2)冲压力的计算该模具采用复合模,拟选用弹性卸料,结构采用倒装式复合模。
(1)冲压力的相关计算见表.表(1)公称压力:250KN发生公称压力时滑块离下极点距离:6MM滑块周边行程80MM调节行程10MM标准行程均数:100次/MIN最大闭合高度最低360MM,最高160MM闭合高度调节是70MM滑块中心到机身距离190MM工作台左右尺寸560MM 前后尺寸300MM工作台孔尺寸左右260 MM(3)压力中心工件为几何对称形状,则复合模的压力中心定位工件的几何中心。
落料复合模具设计说明书

落料复合模具设计说明书1. 引言本文档旨在对落料复合模具的设计进行详细说明,以便于设计师、工程师和制造商在模具设计和制造过程中了解设计要求和技术规范。
落料复合模具是一种用于生产复杂形状产品的模具,具有高度的精度和耐用性。
本文档将从设计原则、结构介绍、材料选择和加工工艺等方面对落料复合模具进行详细阐述。
2. 设计原则在设计落料复合模具时,需要遵循以下原则:2.1. 完整性原则落料复合模具应该能够一次性完成产品的制造过程,减少生产中的工序,提高生产效率。
2.2. 精确性原则落料复合模具应能够精确地实现产品的复杂形状和尺寸要求,确保产品质量。
2.3. 可维护性原则落料复合模具的设计应考虑到日常维护和维修的便捷性,减少停机时间和维护成本。
2.4. 可扩展性原则落料复合模具应具备一定的可扩展性,可以根据产品设计变化或批量生产需求进行调整和改进。
3. 结构介绍落料复合模具通常由以下部分组成:3.1. 上模上模是用于决定产品外形的部分,在设计上应考虑形状复杂度、翻边和压纹等工艺要求,并根据产品尺寸和材料的特性确定材料选择。
3.2. 下模下模是上模的补充部分,在设计上应考虑产品的精度和稳定性要求,以及导向和定位的需求。
3.3. 滑块机构滑块机构是实现产品复杂凸台或切削结构的关键部分,在设计上应考虑滑块的移动规律、导向、润滑和固定等问题。
3.4. 定位销定位销是确保上模和下模的准确定位的重要元素,在设计上应考虑定位销的材料选择、密封性和可调性等要素。
4. 材料选择对于落料复合模具的材料选择,应综合考虑以下因素:•强度和硬度要求:模具应具备足够的强度和硬度,以抵御高压和高温的工作条件。
•耐磨性要求:模具应具备良好的耐磨性能,以延长使用寿命并提高生产效率。
•导热性要求:模具应具备良好的导热性能,以便于热补偿和降低加工温度。
•腐蚀性要求:模具应具备良好的抗腐蚀性能,以应对工作环境中的腐蚀性介质。
综合考虑上述因素,可以选择常见的模具材料,如工具钢、硬质合金和高速钢等。
罩盖拉深胀形复合模的设计说明书

#######大学毕业设计说明书设计题目:罩盖拉深胀形复合模的设计学生姓名:学院:专业及班级:学号:指导教师:目录罩盖落料拉深复合模的设计摘要:冷冲模是冲压生产中不可缺少的工艺装置,深入了解冷冲模的设计,以及运用现代计算机技术来完善冷冲模设计对增强企业的竞争能力和应变能力有着很大的助推力。
模具作为产品加工的工具,设计时要求结构合理、简单且有利于提高产品质量,延长模具寿命。
本文设计了罩盖拉深胀形复合模的整体精细结构,以及部分重要零件的精细结构。
阐述了该工件在拉深胀形过程中的重点难点。
制定出了合理的工艺方案,采取了有效的工艺措施。
准确的计算了工件的毛坯尺寸,凸凹模的刃口尺寸以及工艺压力的大小。
同时在设计过程中合理的设计了零件加工的排样图,准确的校核了凸模的拉压强度,合理的选用了橡胶、弹簧并进一步精确校核。
通过对工件的综合分析,最后设计了2 张装配图和10 张零件图,制作了冲压工艺过程卡和机加工工艺卡。
关键词:冷冲模;凸凹模;拉深;胀形。
THE COVER DESIGN OF DRAWING ANDBULGING COMPOUND DIEABSTRACT:Cold stamping die is an indispensable process device .It is beneficial for the enterprises to improve their competiveness and the ability to cope with changes to get an in-depth understa nding of Die design and then improve the design of Die by modern computer technology. The Die as a tool for production process is required that the design of its structure is reasonable 、simple which is advantageoous to improve its quantity as well as to prolong its longevity. In this paper, it designed an overa ll fine structure of The Cover Design of Drawing And Bulging Compound Die overa ll, and the fine structure of some of the important parts.The impotance and the difficulties that arises when the Die is made in the process of drawing and bulging are both stated in this paper.Meanwhile this article has utilized effective measures to work out a reasonable processing program by accurate calculation of the rough workpiece size, convex, the edge die size and the size of the pressure process.Besides, it has reasonably designed the processing components la yout map, exactly calibrated the tension and compression strength of the punch , rationally chosed the rubber,a nd further calibrated the spring precisely.Through comprehensive analysis of the workpiece, it has finally designed two assembly drawings and ten maps of the parts and made the production process of the stamping machine cards and the processingcard.Key words: Cold Stamping Die ; Convex and carve mold ; bulging; Drawing.1 绪论1.1 国内外模具行业的现状和发展趋势1.1.1 冲压模具发展现状模具生产技术水平的高低,已成为衡量一个国家产品制造水平高低的重要标志,因为模具在很大程度上决定着产品的质量、效益和新产品的开发能力。
冲孔落料复合模设计说明书

冲孔落料倒装复合模设计说明书班级:姓名:学号:日期:目录一.工艺设计1、工艺分析1.1材料分析1.2结构分析1.3精度分析2、冲裁方案确定3、排样设计4、工艺计算4.1刃口尺寸计算4.2冲压力计算4.3模具压力中心计算二.模具零件设计1.凹模外形结构、尺寸确定2. 凸模外形结构、尺寸确定3. 凸凹模外形结构、尺寸确定3.1卸料弹簧设计3.2凸凹模长度3.3凸凹模外刃口三.设备选用1.模座2.导套、导柱3. 冲压设备四.模具装配图1.装配图及相关数据五.参考资料一.工艺设计1、工艺分析工件为的落料冲孔件,材料为10钢,材料厚度1.5mm,生产批量为大批量。
零件图(单位:mm):1.1材料分析10钢为优质碳素结构钢(表4-5),具有较好的冲裁成形性能。
1.2结构分析零件结构不对称,有一个Ø6孔一个Ø12孔,最小孔d=6>t=1.5(表5-10),最小孔边距c=3>1.5t=2.25(图5-27),交线处的圆弧R>0.5t=0.75取R=1(设计大典图2-17),故该零件的外形结构满足冲裁的要求。
(单位:mm)1.3精度分析对于普通冲裁件,其经济精度为IT12~IT14,零件外形为自由公差可选IT14,冲孔精度比落料高一级,所以,冲孔所选精度为IT13,孔间距为0.12mm(表5-12)的公差属于11级精度,故孔间距选择IT11。
2、冲裁方案确定零件为落料冲孔件,可提出的加工方案如下:方案一:先落料,后冲孔。
采用两套单工序模生产。
方案二:落料—冲孔复合冲压,采用复合模生产。
方案三:冲孔—落料连续冲压,采用级进模生产。
方案一模具结构简单,但需两道工序、两副模具,生产效率低,零件精度较差,在生产批量较大的情况下不适用。
方案二只需一副模具,冲压件的形位精度和尺寸精度易保证,且生产效率高。
尽管模具结构较方案一复杂,但由于零件的几何形状较简单,模具制造并不困难。
方案三也只需一副模具,生产效率也很高,但与方案二比生产的零件精度稍差。
复合模设计说明书
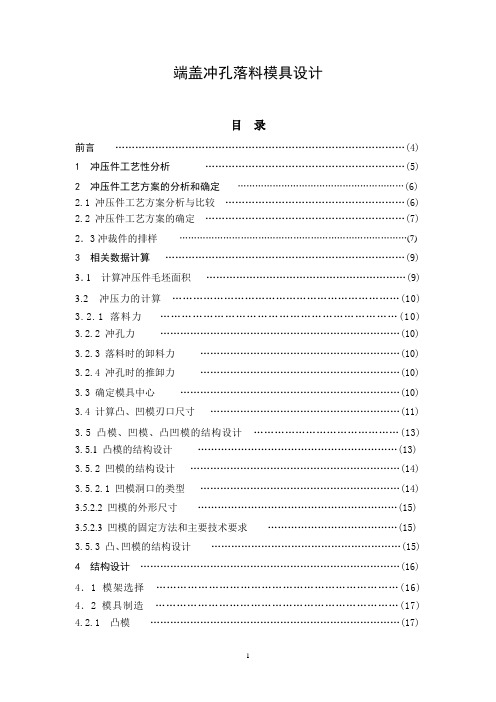
端盖冲孔落料模具设计目录前言 (4)1 冲压件工艺性分析 (5)2 冲压件工艺方案的分析和确定 (6)2.1 冲压件工艺方案分析与比较 (6)2.2冲压件工艺方案的确定 (7)2.3冲裁件的排样 (7)3 相关数据计算 (9)3.1 计算冲压件毛坯面积 (9)3.2 冲压力的计算 (10)3.2.1 落料力 (10)3.2.2 冲孔力 (10)3.2.3 落料时的卸料力 (10)3.2.4 冲孔时的推卸力 (10)3.3 确定模具中心 (10)3.4 计算凸、凹模刃口尺寸 (11)3.5 凸模、凹模、凸凹模的结构设计 (13)3.5.1 凸模的结构设计 (13)3.5.2凹模的结构设计 (14)3.5.2.1凹模洞口的类型 (14)3.5.2.2 凹模的外形尺寸 (15)3.5.2.3 凹模的固定方法和主要技术要求 (15)3.5.3凸、凹模的结构设计 (15)4 结构设计 (16)4.1 模架选择 (16)4.2模具制造 (17)4.2.1 凸模 (17)4.2.2 凹模 (17)4.2.3 凸、凹模 (17)4.2.4 垫板、凸模固定板,推件块,卸料 (18)4.2.5上下模座 (18)5 冲压设备的选择 (18)6 其他零部件的设计 (19)6.1 定位零件的设计 (19)6.1.1挡料销 (19)6.1.2定位板和定位钉 (20)6.1.3送进方向的控制 (20)6.2 卸料和推料零件的设计 (20)6.2.1歩距和定距方式 (20)6.2.2卸料零件 (20)6.2.3推料和顶件装置 (21)6.3模具的固定零件 (21)7 模具的总装图 (21)致谢 (22)参考文献 (23)附录一工艺卡片 (24)附录二模具装配图和零件图 (25)前言任何事物都有一个从出生到成熟的成长过程。
一个全面的毕业设计是一个合格大学生对大学学习生活的总结和灵活运用。
它是学生结合自身能力在单位实实习之后的情况下,把理论和实际相结合的一次飞跃。
方垫片复合模设计说明书

模具CAD/CAM课程设计说明书方垫片1复合模设计(CAD/CAM)摘要本次课程设计的内容为方形垫片1复合模,完成冲孔、落料两道工序。
模具为倒装结构,由打杆顶出制件,弹簧驱动的卸料板卸除条料。
排样方式为单排,由固定挡料销和导料销定位、导料。
模架为中间导柱模架,凸缘式模柄。
使用CATIA生成零件实体并完成装配,进而生成装配工程图和相关的零件图。
关键词:冲孔落料倒装单排CATIA目录1. 概论 (1)1.1 CAD/CAM概论 (1)1.2 CAD/CAM系统组成 (1)1.3 CATIA简介 (1)2.工艺方案分析及确定 (2)2.1 垫片冲压工艺分析 (2)2.2垫片冲压工艺的确定 (3)3.模具结构的确定 (4)3.1 模具的形式 (4)3.2 定位装置 (4)3.3 卸料装置 (4)3.4 导向零件 (4)3.5 模架 (5)4.工艺计算 (6)4.1 排样 (6)4.2 计算冲压力 (7)4.3 计算模具压力中心 (8)4.4 计算模具刃口尺寸 (8)5.主要工作零件的设计 (9)5.1 落料凹模 (9)5.2 冲孔凸模长度及强度校核 (11)5.3 凸凹模长度,壁厚校核 (12)6.其他零件的设计 (14)6.1 卸料弹簧 (14)6.2 凸凹模固定板 (14)6.3 垫板 (15)6.4 卸料板 (15)6.5 模座 (16)6.5 压力机校核 (16)7.CATIA实体建模 (17)7.1 模具的设计顺序 (17)7.2 零件的实体建模 (17)7.3 装配模具实体 (17)7.4 工程图 (20)结束语 (21)参考文献 (21)一、概论1.1 CAD/CAM概论随着计算机计算有关技术的不断发展和计算机技术应用领域的日益扩大,涌现出许多以计算机技术为基础的新兴科学。
CAD/CAM技术便是其中之一。
CAD/CAM,即计算机辅助制造技术与计算机辅助制造,是一门基于计算机技术而发展起来的、与机械设计和制造技术相互渗透、型号结合的、多学科综合性的技术。
冲孔落料复合模设计说明书

目录一、冲压模具发展现状及技术趋势 (1)二、制件工艺性分析 (4)1、材料分析 (4)2、结构分析 (4)3、精度分析 (4)三、冲裁工艺方案的确定 (5)四、制件工艺计算 (5)1、刃口尺寸计算 (6)2、排样计算 (7)3、冲压力计算 (9)4、压力中心计算 (9)五、冲压设备的选用 (10)1、冲压设备的选则原则 (10)2、选择压力机及相关参数 (10)六、模具零部件结构的确定 (11)1、标准模架的选用 (11)2、卸料装置中弹性元件的计算 (11)七、模具装配图 (12)八、模具零件图 (14)九、小结 (19)十、参考文献 (20)冲孔落料复合模设计一、冲压模具发展现状及技术趋势改革开放以来,随着国民经济的高速发展,市场对模具的需求量不断增长。
近年来,模具工业一直以15%左右的增长速度快速发展,模具工业企业的所有制成分也发生了巨大变化,除了国有专业模具厂外,集体、合资、独资和私营也得到了快速发展。
浙江宁波和黄岩地区的“模具之乡”;广东一些大集团公司和迅速崛起的乡镇企业,科龙、美的、康佳等集团纷纷建立了自己的模具制造中心;中外合资和外商独资的模具企业现已有几千家。
随着与国际接轨的脚步不断加快,市场竞争的日益加剧,人们已经越来越认识到产品质量、成本和新产品的开发能力的重要性。
而模具制造是整个链条中最基础的要素之一。
近年许多模具企业加大了用于技术进步的投资力度,将技术进步视为企业发展的重要动力。
一些国内模具企业已普及了二维CAD,并陆续开始使用Pro/E、PDX、UG NX、NX Progressive Die Design、I-DEAS、Euclid-IS、Logopress3、3DQuickPress等国际通用软件,个别厂家还引进了C-Flow、DYNAFORM和MAGMASOFT等CAE软件,并成功应用于冲压模的设计中。
以汽车覆盖件模具为代表的大型冲压模具的制造技术已取得很大进步,东风汽车公司模具厂、一汽模具中心等模具厂家已能生产部分轿车覆盖件模具。
模具毕业设计8冲裁冲孔复合模设计说明书

冲裁冲孔复合模学校:班级:组别:学号:姓名:指导老师:冲压工艺设计复合模具如图1所示零件:钢板生产批量:中小批量材料:08F 料厚t=1.2mm公差按IT14级制造本零件为落料冲孔模设计该零件的冲压工艺与模具。
图1 钢板设计该零件的冲压工艺与模具(一)冲压工艺分析设计冲裁件的工艺性是指从冲压工艺方面来衡量设计是否合理。
一般的讲,在满足工件使用要求的条件下,能以最简单最经济的方法将工件冲制出来,就说明该件的冲压工艺性好,否则,该件的工艺性就差。
当然工艺性的好坏是相对的,它直接受到工厂的冲压技术水平和设备条件等因素的影响。
以上要求是确定冲压件的结构,形状,尺寸等对冲裁件工艺的实应性的主要因素。
根据这一要求对该零件进行工艺分析。
零件尺寸部分公差已经给出,其余未标注公差,属自由尺寸,可按IT14级确定工件尺寸的公差,经查公差表,各尺寸公差为:500-0.62、24.70-0.52、70-0.36、6.50-0.36、10±0.18、150+0.43以根据图纸要求进行设计并画图,利用普通冲裁方式可达到图样要求。
材料为08F钢板是优质碳素结构钢,具有良好的可冲压性能。
材料的厚度为1.2mm。
由于该件外形简单,形状规则,适于落料冲孔加工。
(二)确定工艺方案及模具结构形式确定方案就是确定冲压件的工艺路线,主要包括冲压工序数,工序的组合和顺序等。
确定合理的冲裁工艺方案应在不同的工艺分析进行全面的分析与研究,比较其综合的经济技术效果,选择一个合理的冲压工艺方案。
经分析,该零件属于中小批量生产,工艺性较好,冲压件尺寸精度不高,形状简单。
根据现有冲模制造条件与冲压设备,采用冲裁冲孔复合模,模具制造周期短,价格低廉,工人操作安全,方便可靠。
(三)模具设计计算1.排样因为矩形边长L=50mm 查表1可知两工件间按矩形取搭边值a=1.8,工件与边缘搭边值a1=1.5.条料宽度按相应的公式计算:B=(D+2a+δ)-δ查表2 ⊿=0.5 C=0.2B=(50+2×2+0.5)0-0.5B=54.50-0.5 mm表1 搭边值和侧边值的数值材料厚度t (mm)圆件及r>2t圆角矩形边长l≤50 矩形边长l>50或圆角r≤2 工件间a1 侧边a 工件间a 侧边a1 工件间a1侧边a0.25以下 1.8 2.0 2.2 2.5 2.8 3.0 0.25~0.5 1.2 1.5 1.8 2.0 2.2 2.5 0.5~0.8 1.0 1.2 1.5 1.8 1.8 2.00.8~1.2 0.8 1.0 1.2 1.5 1.5 1.81.2~1.5 1.0 1.2 1.5 1.8 1.92.0 1.6~2.0 1.2 1.5 2.0 2.2 2.0 2.2表2 剪裁下的下偏差△(mm)条料宽度b(mm)条料厚度t(mm)≤50>50~100 >100~200 >200 ≤10.5 0.5 0.7 1.0 >1~30.5 1.0 1.0 1.0 >3~4 1.0 1.0 1.0 1.5 >4~6 1.0 1.0 1.0 2.0根据上述数据可知图形搭边值和条料宽度,如图2可示:图2 排样图2.计算冲裁力若采用平刃冲裁模,其冲裁力P p按下式计算:P—冲裁力;L—冲裁周边长度;t—材料厚度;τ—材料抗剪强度;K—系数;系数K是考虑到实际生产中,模具间隙值的波动和不均匀,刃口磨损、板料力学性能和厚度波动等原因的影响而给出修正系数,一般取K=1.3。
复合模具设计说明(doc 24页)

班级:机械05-6班姓名:马仲举指导教师:刘宏梅完成日期:2009年1月8日指导教师评语成绩:指导教师日期摘要本设计内容为复合模具的设计,并绘制出模具装配图、凸模和凹模的零件图以及编制课程设计说明书。
此模具是落料、拉深和冲孔相结合的复合模具。
在设计的过程中,首先对零件进行了工艺分析,接着对工艺方案进行了比较,最终确定采用先落料,再拉深,最后冲孔的工艺方案,然后画工序图、经过计算选择冲压设备。
然后选择冲模类型以及结构形式,接着是一些模具设计的相关数据计算,包括一些基本力的计算。
对模具的凸模、凹模加工工艺过程以及加工工艺方案的确定,最后编写凸凹模加工工艺规程。
本次设计分析和解决了零件的制造工艺和凸、凹模制造的工艺及工序安排的问题。
关键词:复合模具;装配;工艺方案;工序安排AbstractThe design content for composite mold design and mo ld assembly to map out plans, punch and die parts plans and the preparation of curriculum design specification. This mold is blanking, drawing and punching a combination of composite mold. In the design process, the first parts of the process analysis, and then on the technology programs are compared, and ultimately adopt the first blank, and then drawing the final punch of technology programs, and then painting process maps, calculated choice stamping equipment . Then select the type of die structure, foll owed by a number of die design of the relevant data, including some of the basic computing power. Punch on the mold, die machining process, as well as processing program to determine the final preparation of convexity modulus of order processing. The design of the analysis and solution of the parts manufacturing process and convex and concave mold manufacturing technology and processes arrangements.Key words:Composite mold;assembly;technology programs;process arrangements目录1 冲压工艺设计 (1)1.1零件的工艺分析 (1)1.2制定工艺方案 (2)1.2.1计算毛坯尺寸 (2)1.2.2确定工艺方案 (2)1.2.3确定拉深次数 (2)1.3排样图的确定 (2)1.4初选冲压设备 (3)1.4.1落料力的计算 (3)1.4.2拉深力的计算 (3)1.4.3冲孔力的计算 (3)1.5编制冲压工艺卡 (4)2 复合模具的设计 (5)2.1复合模具的类型及结构形式的选择 (5)2.2模具设计计算 (6)2.2.1拉深凹模(落料凸模)尺寸的确定 (6)2.2.2拉深凸模(冲孔凹模)尺寸的确定 (6)2.2.3冲孔凸模和冲孔凹模刃口尺寸的确定 (7)2.2.4顶出器尺寸的确定 (7)3 模具主要零件加工工艺设计 (8)3.1落料凸模(拉深凹模)加工工艺过程 (9)3.2拉深凸模(冲孔凹模)加工工艺过程 (11)3.3冲孔凸模加工工艺过程 (11)3.4落料凹模加工工艺过程 (12)4 模具的工作过程 (14)5 设计体会 (15)参考文献 (16)1 冲压工艺设计1.1零件的工艺分析通过对零件图的观察,知零件的形状、尺寸及板料的材料和厚度。
复合模说明书
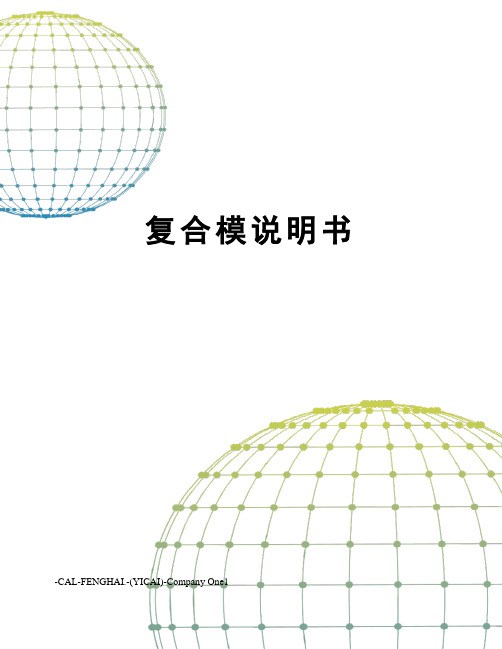
复合模说明书-CAL-FENGHAI.-(YICAI)-Company One1一、零件设计零件简图:如图所示成产批量:大批量材料:Q235钢材料厚度:2mm零件简图二、冲压件的工艺分析、结构分析该零件形状简单、对称,由两段Φ20圆弧、两个Φ10的圆和直线组成t=(t 为材料厚度)。
、材料分析材料为Q235普通碳素结构钢,由于含碳适中,综合性能较好,强度、塑性和焊接等性能得到较好配合,抗拉强度(σb/MPa):375-500。
、精度分析由于图中没明确标出公差尺寸,所以冲裁件内外形的经济精度为IT14,可以根据GB1800—79标准公差数值表查得。
标注如下图:三、确定冲裁工艺方案该冲裁件包括落料和冲孔两个基本工序,因此,工艺上可采用的工艺冲裁方案有五种:方案一:单工序模生产,先落料,后冲孔,需要两副模具。
方案二:级进模生产,一模两件,如图(A)。
方案三:复合模生产,一模两件如图(B)。
方案四:级进模生产,一模一件,如图(C)。
方案五:复合模生产,一模一件,如图(D)。
以上五种工艺方案,从生产率方面看,第一、四、五方案较低,与大批量生产不相符,因此应予淘汰。
现比较二、三方案,级进模生产时,导料板导料便于送进操作,但搭边需略增大,料耗增加;若以挡料销和始用挡料销定距,对生产率略有影响,若以侧刃定距,料耗更为增加。
而且在级进模中,零件的中心距不好保证。
而由于零件的结构简单,复合模的结构并不比级进模复杂,中心距能够更好保证,材料利用率更高。
因此决定采用第三种方案,用复合模生产,一模两件。
A BC D四、工艺计算(1)排样图及坯料尺寸由于条料送进采用有侧刃导料板送进,搭边按正常情况选取。
完整排样图如图所示。
根据常用钢板规格表,选择650mm X1300mm的板材余料最少,每张板可以裁成64mmX1300mm的条料十条,每个条料可生产零件59件。
A≈2xπx102+(40-16)x12-2xπx52=759mm2则材料总利用率为:η=Na/BL=59x759/(64x1300)x100%≈54%(2)冲压力计算与压力中心落料力:根据零件图可算得一个零件的落料轮廓线长为L1=,F1=2KL1tτb =(K是修正系数取;τb是材料抗剪切强度根据常用冲压金属材料力学性能表查得在304~373间取350τ/MPa)冲孔力:单个零件内孔周长L2=,则冲孔力为:F2=2KL2tτb =卸料力:根据课本表3—17查得K X=,K T=,F D=,则:F X=K X F1==推件力:F T=K T F1== N顶件力:F D=K D F1= x219492=总冲压力:F∑= F1+ F2 +F X +F T=219492+85722++=压力中心(3)刃口尺寸及公差表1 工作零件刃口尺寸计算(1)将零件图尺寸全部按入体原则标注,未注公差按IT14,可以根据GB1800—79标准公差数值表查得。
- 1、下载文档前请自行甄别文档内容的完整性,平台不提供额外的编辑、内容补充、找答案等附加服务。
- 2、"仅部分预览"的文档,不可在线预览部分如存在完整性等问题,可反馈申请退款(可完整预览的文档不适用该条件!)。
- 3、如文档侵犯您的权益,请联系客服反馈,我们会尽快为您处理(人工客服工作时间:9:00-18:30)。
端盖冲孔落料模具设计目录前言 (4)1 冲压件工艺性分析 (5)2 冲压件工艺方案的分析和确定 (6)2.1 冲压件工艺方案分析与比较 (6)2.2冲压件工艺方案的确定 (7)2.3冲裁件的排样 (7)3 相关数据计算 (9)3.1 计算冲压件毛坯面积 (9)3.2 冲压力的计算 (10)3.2.1 落料力 (10)3.2.2 冲孔力 (10)3.2.3 落料时的卸料力 (10)3.2.4 冲孔时的推卸力 (10)3.3 确定模具中心 (10)3.4 计算凸、凹模刃口尺寸 (11)3.5 凸模、凹模、凸凹模的结构设计 (13)3.5.1 凸模的结构设计 (13)3.5.2凹模的结构设计 (14)3.5.2.1凹模洞口的类型 (14)3.5.2.2 凹模的外形尺寸 (15)3.5.2.3 凹模的固定方法和主要技术要求 (15)3.5.3凸、凹模的结构设计 (15)4 结构设计 (16)4.1 模架选择 (16)4.2模具制造 (17)4.2.1 凸模 (17)4.2.2 凹模 (17)4.2.3 凸、凹模 (17)4.2.4 垫板、凸模固定板,推件块,卸料 (18)4.2.5上下模座 (18)5 冲压设备的选择 (18)6 其他零部件的设计 (19)6.1 定位零件的设计 (19)6.1.1挡料销 (19)6.1.2定位板和定位钉 (20)6.1.3送进方向的控制 (20)6.2 卸料和推料零件的设计 (20)6.2.1歩距和定距方式 (20)6.2.2卸料零件 (20)6.2.3推料和顶件装置 (21)6.3模具的固定零件 (21)7 模具的总装图 (21)致谢 (22)参考文献 (23)附录一工艺卡片 (24)附录二模具装配图和零件图 (25)前言任何事物都有一个从出生到成熟的成长过程。
一个全面的毕业设计是一个合格大学生对大学学习生活的总结和灵活运用。
它是学生结合自身能力在单位实实习之后的情况下,把理论和实际相结合的一次飞跃。
所以说它不仅仅是一份毕业答卷,同时还是一个学生对知识的系统、深入的认识和学习过程。
它不仅表现了一个学生从事实际工作的基本能力和基本技能,更重要的是如何把理论应用在实际工作当中。
随着科学技术的迅猛发展,各种产品的更新换代的速度愈来愈快,而产品的更新换代是以新产品的造型设计和模具的设计、制造与更新为前提的。
模具的设计是模具更新的基础,模具设计工作与产品的更新息息相关。
传统的单工序模具已经不能够满足产品批量生产的需要,这就为复合模和级进模的出现奠定了基础。
本次毕业设计所采用的模具即是冲孔落料复合模。
复合模:只有一个工位,在压力机的一次行程中能完成两道或两道以上的冲压工艺。
复合模广泛应用于大批量生产,尤其适合于制造形状复杂,对精度和表面质量要求较高的零件。
1.冲压件工艺性分析:工件名称:端盖模具名称:冲孔落料复合模生产批量:大批量工件材料:20钢材料厚度:1mm尺寸精度:IT14级零件外形尺寸:135,88,84,100,1.5,2.5,9零件内形尺寸:φ35零件图如图1-1所示,零件尺寸图如图1-2所图1-1 图1-2复合模的特点:具有一个落料凸模,又是冲孔凹模的凸凹模(这是在复合模中必有得零件,其外形是落料凸模,其内孔是冲孔凹模,故称此零件为凸凹模)。
而在另一个方,则装着凸模和凹模,当上、下模两部分嵌合时,就能同时完成冲孔与落料,因此,它不存在连续模冲压时的定位误差问题。
复合模冲压的优点:(1)、生产率高。
复合模具属于单工位、多工序模具,在一副模具中包括冲裁、弯曲、拉深、成形等多道冲压工序,因而具有高的劳动生产率。
(2)、适用于生产批量大、精度要求高的冲裁件,冲裁件的内孔与外缘的相对位置精度高,板料的定位精度要求比级进模低,冲模的轮廓尺寸小,冲出的冲件平直度高。
复合模冲压的缺点:结构复杂,冲件容易被嵌入边料中影响操作,制造精度要求高,成本高。
本工件需要采用的模具为倒装复合模,即落料凹模在上模上,称为倒装式复合模。
其结构特点是有两套除料、除件装置。
倒装复合模的优点是结构简单,缺点是不宜冲制孔边距离较小的冲裁件。
2.冲压件工艺方案的分析与确定:冲压生产的模具制造费用比较高,往往占冲压件总成本的10%~30%,甚至高达40%。
因此选用哪种生产方法,必须首先估算生产成本。
即使必须采用冲压加工的方式,也须视生产批量决定采用何种模具形式进行生产。
该件属于大批量生产,比较合适的模具形式是级进模和复合模。
但是,在此工件中只有一个冲孔,因此使用连续跳步模会增大结构尺寸,制造也复杂,成本较高。
用侧刃定距的连续冲裁模,还对带料、板料宽度的尺寸精度有一定要求,材料有额外的浪费。
2.1冲压件工艺方案分析与比较:该零件包括落料,冲孔两个基本工序,可以采用以下三种工艺方案:方案一:先落料,再冲孔,采用单工序模生产。
方案二:冲孔—落料连续冲压,采用级进模生产。
方案三:落料—冲孔复合冲压,采用复合模生产。
2.2冲压件工艺方案的确定:方案1,模具结构简单,但需要两道工序,两套模具才能完成零件的生产加工,生产效率较低,难以满足零件大批量生产的需要,操作也不安全,故不宜采用。
方案2,此半径规工件中只有一个冲孔,因此使用连续跳步模会增大结构尺寸,制造也复杂,成本较高。
用侧刃定距的连续冲裁模,还对带料、板料宽度的尺寸精度有一定要求,材料有额外的浪费。
方案3,可以节约模具制造材料,节省成本,可以结合方案1和方案2的优缺点,选择方案3是最佳的。
2.3冲裁件的排样:条料排样图设计的好坏,直接影响模具设计的质量。
当条料排样图确定了,则零件材料的利用率、模具步距的基本尺寸、定距方式、条料载体形式、条料宽度、模具结构、导料方式等都得到了确定。
排样图设计错误,会导致制造出来的模具无法冲压零件。
因此,在排样设计分析时要考虑以下原则:(1)材料的合理利用;(2)操作方便、安全,减轻工人的劳动强度。
(3)尽量按少、无废料排序;(4)使模具结构简单、模具寿命长;(5)排样应保证冲裁件的质量;在做条料排样设计时,不仅要考虑它的设计原则,还要考虑各种实际因素,比如:(1)企业的实际生产能力和零件的生产批量;(2)零件的形状;(3)冲裁力的平衡(冲压力中心与模具中心尽可能平衡);(4)模具结构的合理性;(5)被加工材料(材料供料状态、加工材料的物理性能、材料的毛刺方向、材料的利用率);(6)冲压件的毛刺方向;(7)注意条料在送进过程中的阻碍;排样图如图3-1所示在冲压零件的成本中,材料费用约占60﹪,因此材料的经济利用具有非常重要的意义。
同时为了补偿定位误差,保持条料有一定的刚度,以保证零件质量和送料方便。
我们还需要查出其搭边值查表2-16得最小搭边值两工件之间的搭边:1a = 0.8mm工件边缘搭边:2a = 1.0mm3. 相关数据的计算:3.1计算冲压件毛坯面积:经计算零件展开尺寸为165.8mm步距:0B = 168+0.8=168.8 mm条料宽度:查标准取B=170 mm冲压件毛坯面积:经计算A = 22686.52m m排样图如图3-1所示在冲压零件的成本中,材料费用约占60﹪,因此材料的经济利用具有非常重要的意义。
一个步距内的材料利用率η为:η= BSA × 100﹪ = 22686.5/28526=79.5% 3.2冲压力的计算:为了选用合适的压力机、设计模具和检验模具的强度。
压力机的吨位必须大于所计算的冲裁力,以适应冲裁的需求,我们必须计算出相应的冲压力。
该模具我们采用弹性卸料和下出料方式。
查《模具设计指导》表4-12得:b σ=430a MP3.2.1冲裁力:落F = Lt b σ=2*π*170*430=459068(N )查《冲压模具设计指导书》29面得Kx=0.04,Kt=0.055,Kd=0.063.2.2推件力:Ft=n*Kt*F=126243.7N3.2.3顶件力:Fd=Kd*F=27544.08(N)如图9-1所示的凹模的刃口形式:采用弹性卸料上出料方式则F总=F+Fx+Fd=504.97(KN)3.3确定模具压力中心:冲裁模的压力中心就是冲裁力合力的作用点。
为了确保压力机和模具正常工作,应使冲模的压力中心与压力机滑块的中心相重合。
对于带有模柄的冲压模,压力中心应通过模柄的轴心线,否则会使冲模和压力机滑块产生偏心载荷,使滑块和导轨之间产生过大的磨损,模具导向零件加速磨损,降低模具和压力机的使用寿命。
根据图形分析,由于工件为圆形且对称,所以压力中心就是工件圆心。
3.4计算凸凹模刃口尺寸:冲裁件的尺寸精度主要决定于模具刃口的尺寸精度,模具的合理间隙值也要靠模具刃口尺寸及制造精度来保证。
在确定冲模刃口制造公差时,应考虑制件的公差要求。
如果对刃口精度要求过高( 即制造公差过小 ),会使模具制造困难,增加成本,延长生产周期;如果对刃口精度要求过低(即制造公差过大 ),则生产出来的制件可能不合格,会使模具的寿命降低。
在计算冲孔模刃口尺寸时,应以凸模为基准,凹模尺寸按凸模实际尺寸配制,保证双面间隙为0.04~0.06mm。
查《冲压模具及设备》92面4-9得max Z =0.07mmmin Z =0.05mm即:max Z -min Z = 0.02 mm由工件制造公差表知:落料的制造公差d δ =4∆ ,冲孔的制造公差p δ = 4∆ ,孔距的制造公差为8∆ 。
工件的制件精度为IT14,故磨损系数X=0.5根据计算原则,落料时以凹模为设计基准,凹模制造偏差取正偏差,凸模偏差取负偏差。
3.4.1落料:φ1680 -111d D =(Dmax-X*△)+δd 0Dp=(Dd-min Z )0 -δp因为δp+δd=0.07>max Z -min Z =0.02 故不能满足δp+δd ≤max Z -min Z 条件,所以可调整为 δp=0.4*(max Z -min Z )=0.008,δd=0.6×(m a x Z -min Z )=0.012 代入数值得:2d D = (168-0.5×1.1)+δd 0=167.45+0.012 0mm Dp=(167.45-0.05)=167.40 -0.008 mm根据计算原则,冲孔时以凸模设计为基准,凸模制造偏差取负偏差,凹模取正偏差。
3.4.2冲孔:Φ35+0.1 0p d = (d min +X △)0 -δpDd=(d p +Z min )+δd查《冲压模具及设备》97面4-13得 δd=0.03 δp=0.02 X=0.75 校核间隙 因为δp+δd=0.05>max Z -min Z =0.02不能满足 所以可以调整为:δp=0.4×(max Z -min Z )=0.008mm δd=0.6×(max Z -min Z )=0.012mm代入数值有:p d =35.0750 -0.008 Dd=35.125+0.012 0mm3.5凸模、凹模、凸凹模的结构设计:3.5.1凸模的结构设计:3.5.1.1凸模形式 : 凸模的结构形式,主要根据冲裁件的形状和尺寸而定。