塑料模具外文翻译
塑料注塑模具中英文对照外文翻译文献
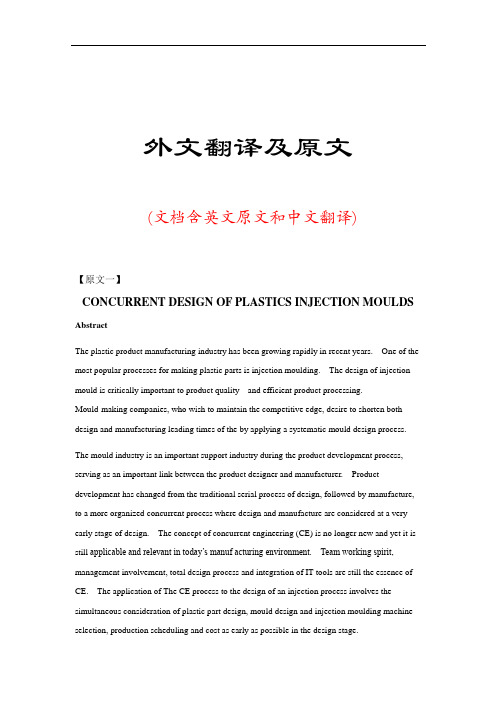
外文翻译及原文(文档含英文原文和中文翻译)【原文一】CONCURRENT DESIGN OF PLASTICS INJECTION MOULDS AbstractThe plastic product manufacturing industry has been growing rapidly in recent years. One of the most popular processes for making plastic parts is injection moulding. The design of injection mould is critically important to product quality and efficient product processing.Mould-making companies, who wish to maintain the competitive edge, desire to shorten both design and manufacturing leading times of the by applying a systematic mould design process. The mould industry is an important support industry during the product development process, serving as an important link between the product designer and manufacturer. Product development has changed from the traditional serial process of design, followed by manufacture, to a more organized concurrent process where design and manufacture are considered at a very early stage of design. The concept of concurrent engineering (CE) is no longer new and yet it is still applicable and relevant in today’s manuf acturing environment. Team working spirit, management involvement, total design process and integration of IT tools are still the essence of CE. The application of The CE process to the design of an injection process involves the simultaneous consideration of plastic part design, mould design and injection moulding machine selection, production scheduling and cost as early as possible in the design stage.This paper presents the basic structure of an injection mould design. The basis of this system arises from an analysis of the injection mould design process for mould design companies. This injection mould design system covers both the mould design process and mould knowledge management. Finally the principle of concurrent engineering process is outlined and then its principle is applied to the design of a plastic injection mould.Keywords :Plastic injection mould design, Concurrent engineering, Computer aided engineering, Moulding conditions, Plastic injection moulding, Flow simulation1.IntroductionInjection moulds are always expensive to make, unfortunately without a mould it can not be possible ho have a moulded product. Every mould maker has his/her own approach to design a mould and there are many different ways of designing and building a mould. Surely one of the most critical parameters to be considered in the design stage of the mould is the number of cavities, methods of injection, types of runners, methods of gating, methods of ejection, capacity and features of the injection moulding machines. Mould cost, mould quality and cost of mould product are inseparableIn today’s completive environment, computer aided mould filling simulation packages can accurately predict the fill patterns of any part. This allows for quick simulations of gate placements and helps finding the optimal location. Engineers can perform moulding trials on the computer before the part design is completed. Process engineers can systematically predict a design and process window, and can obtain information about the cumulative effect of the process variables that influence part performance, cost, and appearance.2.Injection MouldingInjection moulding is one of the most effective ways to bring out the best in plastics. It is universally used to make complex, finished parts, often in a single step, economically, precisely and with little waste. Mass production of plastic parts mostly utilizes moulds. The manufacturing process and involving moulds must be designed after passing through the appearance evaluation and the structure optimization of the product design. Designers face a hugenumber of options when they create injection-moulded components. Concurrent engineering requires an engineer to consider the manufacturing process of the designed product in the development phase. A good design of the product is unable to go to the market if its manufacturing process is impossible or too expensive. Integration of process simulation, rapid prototyping and manufacturing can reduce the risk associated with moving from CAD to CAM and further enhance the validity of the product development.3. Importance of Computer Aided Injection Mould DesignThe injection moulding design task can be highly complex. Computer Aided Engineering (CAE) analysis tools provide enormous advantages of enabling design engineers to consider virtually and part, mould and injection parameters without the real use of any manufacturing and time. The possibility of trying alternative designs or concepts on the computer screen gives the engineers the opportunity to eliminate potential problems before beginning the real production. Moreover, in virtual environment, designers can quickly and easily asses the sensitivity of specific moulding parameters on the quality and manufacturability of the final product. All theseCAE tools enable all these analysis to be completed in a meter of days or even hours, rather than weeks or months needed for the real experimental trial and error cycles. As CAE is used in the early design of part, mould and moulding parameters, the cost savings are substantial not only because of best functioning part and time savings but also the shortens the time needed to launch the product to the market.The need to meet set tolerances of plastic part ties in to all aspects of the moulding process, including part size and shape, resin chemical structure, the fillers used, mould cavity layout, gating, mould cooling and the release mechanisms used. Given this complexity, designers often use computer design tools, such as finite element analysis (FEA) and mould filling analysis (MFA), to reduce development time and cost. FEA determines strain, stress and deflection in a part by dividing the structure into small elements where these parameters can be well defined. MFA evaluates gate position and size to optimize resin flow. It also defines placement of weld lines, areas of excessive stress, and how wall and rib thickness affect flow. Other finite element design tools include mould cooling analysis for temperature distribution, and cycle time and shrinkage analysis for dimensional control and prediction of frozen stress and warpage.The CAE analysis of compression moulded parts is shown in Figure 1. The analysis cycle starts with the creation of a CAD model and a finite element mesh of the mould cavity. After the injection conditions are specified, mould filling, fiber orientation, curing and thermal history, shrinkage and warpage can be simulated. The material properties calculated by the simulation can be used to model the structural behaviour of the part. If required, part design, gate location and processing conditions can be modified in the computer until an acceptable part is obtained. After the analysis is finished an optimized part can be produced with reduced weldline (known also knitline), optimized strength, controlled temperatures and curing, minimized shrinkage and warpage.Machining of the moulds was formerly done manually, with a toolmaker checking each cut. This process became more automated with the growth and widespread use of computer numerically controlled or CNC machining centres. Setup time has also been significantly reduced through the use of special software capable of generating cutter paths directly from a CAD data file. Spindle speeds as high as 100,000 rpm provide further advances in high speed machining. Cutting materials have demonstrated phenomenal performance without the use of any cutting/coolant fluid whatsoever. As a result, the process of machining complex cores and cavities has been accelerated. It is good news that the time it takes to generate a mould is constantly being reduced. The bad news, on the other hand, is that even with all these advances, designing and manufacturing of the mould can still take a long time and can be extremely expensive.Figure 1 CAE analysis of injection moulded partsMany company executives now realize how vital it is to deploy new products to market rapidly. New products are the key to corporate prosperity. They drive corporate revenues, market shares, bottom lines and share prices. A company able to launch good quality products with reasonable prices ahead of their competition not only realizes 100% of the market before rival products arrive but also tends to maintain a dominant position for a few years even after competitive products have finally been announced (Smith, 1991). For most products, these two advantages are dramatic. Rapid product development is now a key aspect of competitive success. Figure 2 shows that only 3–7% of the product mix from the average industrial or electronics company is less than 5 years old. For companies in the top quartile, the number increases to 15–25%. For world-class firms, it is 60–80% (Thompson, 1996). The best companies continuously develop new products. AtHewlett-Packard, over 80% of the profits result from products less than 2 years old! (Neel, 1997)Figure 2. Importance of new product (Jacobs, 2000)With the advances in computer technology and artificial intelligence, efforts have been directed to reduce the cost and lead time in the design and manufacture of an injection mould. Injection mould design has been the main area of interest since it is a complex process involving several sub-designs related to various components of the mould, each requiring expert knowledge and experience. Lee et. al. (1997) proposed a systematic methodology and knowledge base for injection mould design in a concurrent engineering environment.4.Concurrent Engineering in Mould DesignConcurrent Engineering (CE) is a systematic approach to integrated product development process. It represents team values of co-operation, trust and sharing in such a manner that decision making is by consensus, involving all per spectives in parallel, from the very beginning of the productlife-cycle (Evans, 1998). Essentially, CE provides a collaborative, co-operative, collective and simultaneous engineering working environment. A concurrent engineering approach is based on five key elements:1. process2. multidisciplinary team3. integrated design model4. facility5. software infrastructureFigure 3 Methodologies in plastic injection mould design, a) Serial engineering b) Concurrent engineeringIn the plastics and mould industry, CE is very important due to the high cost tooling and long lead times. Typically, CE is utilized by manufacturing prototype tooling early in the design phase to analyze and adjust the design. Production tooling is manufactured as the final step. The manufacturing process and involving moulds must be designed after passing through the appearance evaluation and the structure optimization of the product design. CE requires an engineer to consider the manufacturing process of the designed product in the development phase.A good design of the product is unable to go to the market if its manufacturing process is impossible. Integration of process simulation and rapid prototyping and manufacturing can reduce the risk associated with moving from CAD to CAM and further enhance the validity of the product development.For years, designers have been restricted in what they can produce as they generally have todesign for manufacture (DFM) – that is, adjust their design intent to enable the component (or assembly) to be manufactured using a particular process or processes. In addition, if a mould is used to produce an item, there are therefore automatically inherent restrictions to the design imposed at the very beginning. Taking injection moulding as an example, in order to process a component successfully, at a minimum, the following design elements need to be taken into account:1. . geometry;. draft angles,. Non re-entrants shapes,. near constant wall thickness,. complexity,. split line location, and. surface finish,2. material choice;3. rationalisation of components (reducing assemblies);4. cost.In injection moulding, the manufacture of the mould to produce the injection-moulded components is usually the longest part of the product development process. When utilising rapid modelling, the CAD takes the longer time and therefore becomes the bottleneck.The process design and injection moulding of plastics involves rather complicated and time consuming activities including part design, mould design, injection moulding machine selection, production scheduling, tooling and cost estimation. Traditionally all these activities are done by part designers and mould making personnel in a sequential manner after completing injection moulded plastic part design. Obviously these sequential stages could lead to long product development time. However with the implementation of concurrent engineering process in the all parameters effecting product design, mould design, machine selection, production scheduling,tooling and processing cost are considered as early as possible in the design of the plastic part. When used effectively, CAE methods provide enormous cost and time savings for the part design and manufacturing. These tools allow engineers to virtually test how the part will be processed and how it performs during its normal operating life. The material supplier, designer, moulder and manufacturer should apply these tools concurrently early in the design stage of the plastic parts in order to exploit the cost benefit of CAE. CAE makes it possible to replace traditional, sequential decision-making procedures with a concurrent design process, in which all parties can interact and share information, Figure 3. For plastic injection moulding, CAE and related design data provide an integrated environment that facilitates concurrent engineering for the design and manufacture of the part and mould, as well as material selection and simulation of optimal process control parameters.Qualitative expense comparison associated with the part design changes is shown in Figure 4 , showing the fact that when design changes are done at an early stages on the computer screen, the cost associated with is an order of 10.000 times lower than that if the part is in production. These modifications in plastic parts could arise fr om mould modifications, such as gate location, thickness changes, production delays, quality costs, machine setup times, or design change in plastic parts.Figure 4 Cost of design changes during part product development cycle (Rios et.al, 2001)At the early design stage, part designers and moulders have to finalise part design based on their experiences with similar parts. However as the parts become more complex, it gets rather difficult to predict processing and part performance without the use of CAE tools. Thus for even relatively complex parts, the use of CAE tools to prevent the late and expensive design changesand problems that can arise during and after injection. For the successful implementation of concurrent engineering, there must be buy-in from everyone involved.5.Case StudyFigure 5 shows the initial CAD design of plastics part used for the sprinkler irrigation hydrant leg. One of the essential features of the part is that the part has to remain flat after injection; any warping during the injection causes operating problems.Another important feature the plastic part has to have is a high bending stiffness. A number of feeders in different orientation were added to the part as shown in Figure 5b. These feeders should be designed in a way that it has to contribute the weight of the part as minimum aspossible.Before the design of the mould, the flow analysis of the plastic part was carried out with Moldflow software to enable the selection of the best gate location Figure 6a. The figure indicates that the best point for the gate location is the middle feeder at the centre of the part. As the distortion and warpage of the part after injection was vital from the functionality point of view and it has to be kept at a minimum level, the same software was also utilised to yiled the warpage analysis. Figure 5 b shows the results implying the fact that the warpage well after injection remains within the predefined dimensional tolerances.6. ConclusionsIn the plastic injection moulding, the CAD model of the plastic part obtained from commercial 3D programs could be used for the part performance and injection process analyses. With the aid ofCEA technology and the use of concurrent engineering methodology, not only the injection mould can be designed and manufactured in a very short of period of time with a minimised cost but also all potential problems which may arise from part design, mould design and processing parameters could be eliminated at the very beginning of the mould design. These two tools help part designers and mould makers to develop a good product with a better delivery and faster tooling with less time and money.References1. Smith P, Reinertsen D, The time-to-market race, In: Developing Products in Half the Time. New York, Van Nostrand Reinhold, pp. 3–13, 19912.Thompson J, The total product development organization. Proceedings of the SecondAsia–Pacific Rapid Product Development Conference, Brisbane, 19963.Neel R, Don’t stop after the prototype, Seventh International Conference on Rapid Prototyping, San Francisco, 19974.Jacobs PF, “Chapter 3: Rapid Product Development” in Rapid Tooling: Technologies and Industrial Applications , Ed. Peter D. Hilton; Paul F. Jacobs, Marcel Decker, 20005.Lee R-S, Chen, Y-M, and Lee, C-Z, “Development of a concurrent mould design system: a knowledge based approach”, Computer Integrated Manufacturing Systems, 10(4), 287-307, 19976.Evans B., “Simultaneous Engineering”, Mechanical Engi neering , V ol.110, No.2, pp.38-39, 19987.Rios A, Gramann, PJ and Davis B, “Computer Aided Engineering in Compression Molding”, Composites Fabricators Association Annual Conference , Tampa Bay, 2001【译文一】塑料注塑模具并行设计塑料制品制造业近年迅速成长。
模具术语英文翻译

模具术语英文翻译三、模具塑料模具mould of plastics注塑模具injection mould冲压模具die模架mould base定模座板Top clamping plate Top plateFixed clamp plate水口推板stripper plateA板A plateB板B plate支承板support plate方铁spacer plate底针板ejector plate面针板ejector retainer plate回针Return pin导柱Guide pin有托导套Shoulder Guide bush 直导套Straight Guide bush动模座板Bottom clamp plate Moving clamp plate基准线datum line基准面datum plan型芯固定板core-retainer plate 凸模固定板punch-retainer plate 顶针ejector pin单腔模具single cavity mould多腔模具multi-cavity mould多浇口multi-gating浇口gate缺料starving排气breathing光泽gloss合模力mould clamping force锁模力mould locking force挤出extrusion开裂crack循环时间cycle time老化aging螺杆screw麻点pit嵌件insert活动镶件movable insert起垩chalking浇注系统feed system主流道sprue分流道runner浇口gate直浇口direct gate , sprue gate轮辐浇口spoke gate , spider gate点浇口pin-point gate测浇口edge gate潜伏浇口submarine gate , tunnel gate 料穴cold-slug well浇口套sprue bush流道板runner plate排飞槽vent分型线(面)parting line定模stationary mould,Fixed mould 动模movable mould, movable half上模upper mould,upper half下模lower mould,lower half型腔cavity凹模cavity plate,cavity block拼块split定位销dowel定位销孔dowel hole型芯core斜销angle pin, finger cam滑块slide滑块导板slide guide strip楔紧块heel block, wedge lock拉料杆sprue puller定位环locating ring冷却通cooling channel脱模斜度draft滑动型芯slide core螺纹型芯threaded core热流道模具hot-runner mould绝热流道模insulated runner mould熔合纹weld line (flow line)三板式模具three plate mould脱模ejection换模腔模具interchangeable cavity mould 脱模剂release agent注射能力shot capacity注射速率injection rate注射压力injection pressure差色剂colorant保压时间holdup time闭模时间closing time定型装置sizing system阴模female mould,cavity block阳模male mould电加工设备Electron Discharge Machining数控加工中心CNC machine center万能铁床Universal milling machine卧式刨床Horizontal planer车床Engine lathe平面磨床Surface grinding machine去磁机Demagnetization machine万能摇臂钻床Universal radial movable driller 立式钻床Vertical driller超声波清洗机Ultrasonic clearing machine。
塑料模具中英文对照外文翻译文献

中英文资料翻译The development of plastic mouldChina's industrial plastic moulds from the start to now, after more than half a century, there has been great development, mold levels have been greatly enhanced. Mould has been at large can produce 48-inch big-screen color TV Molded Case injection mold, 6.5 kg capacity washing machine full of plastic molds, as well as the overall car bumpers and dashboards, and other plastic mould precision plastic molds, the camera is capable of producing plastic mould , multi-cavity mold small modulus gear and molding mold. --Such as Tianjin and Yantai days Electrical Co., Ltd Polaris IK Co. manufactured multi-cavity mold VCD and DVD gear, the gear production of such size precision plastic parts, coaxial, beating requirements have reached a similar foreign the level of product, but also the application of the latest gear design software to correct contraction as a result of the molding profile error to the standard involute requirements. Production can only 0.08 mm thickness of a two-cavity mold and the air Cup difficulty of plastic doors and windows out of high modulus, and so on. Model cavity injection molding manufacturing accuracy of 0.02 to 0.05 mm, surface roughness Ra0.2 μ m, mold quality, and significantly increase life expectancy, non-hardening steel mould life up to 10~ 30 million, hardening steel form up to 50 ~ 10 million times, shorten the delivery time than before, but still higher than abroad, and the gap between a specific data table.Process, the multi-material plastic molding die, efficient multicolor injection mould, inserts exchange structure and core pulling Stripping the innovative design has also made great progress. Gas-assisted injection molding, the use of more mature technologies, such as Qingdao Hisense Co., Ltd., Tianjin factory communications and broadcasting companies, such as mold manufacturers succeeded in 29 ~ 34-inch TV thick-walled shell, as well as some parts on the use of gas-assisted mould technology Some manufacturers also use the C-MOLD gas-assisted software and achieved better results. Prescott, such as Shanghai, such as the new company will provide users with gas-assisted molding equipment and technology. Began promoting hot runner mold, and some plants use rate of more than 20 percent, the general heat-thermal hot runner, or device, a small number of units with the world's advanced level of rigorous hot runner-needle device, a small number of units with World advanced level of rigorous needle-hot runner mould. However, the use of hot runner overall rate of less than 10%, with overseas compared to 50 ~ 80%, the gap larger.In the manufacturing technology, CAD / CAM / CAE technology on the level of application of a new level to the enterprise for the production of household appliances representatives have introduced a considerable number of CAD / CAMsystems, such as the United States EDS UG Ⅱ, the United States Parametric Technology Pro / Engineer, the United States CV CADS5 company, the British company DOCT5 Deltacam, HZS's CRADE Japan, the company's Cimatron Israel, the United States AC-C-Tech Mold Company and Australia's MPA Mold flow Mold analysis software, and so on. These systems and the introduction of the software, althougha lot of money spent, but in our country die industry, and achievinga CAD / CAM integration, and to support CAE technology to forming processes such as molding and cooling, such as computer simulation, and achieved certain The technical and economic benefits, promote and facilitate China's CAD / CAM technology. In recent years, China's own development of the plastic mould CAD / CAM system has achieved significant development, the main guarantor Software Engineering Institute, is the development of CAXA, Huazhong University of Science HSC5.0 development of the system and injection mold CAE software, and so on, these Die of domestic software with the specific circumstances in the application of computer and lower prices, and other characteristics, in order to further universal CAD / CAM technology has created good conditions.In recent years, China has been more extensive use of some new plastic mold steel, such as: P20, 3Cr2Mo, PMS, SM Ⅰ, SM Ⅱ, and the quality of life of mold has a direct significant impact on the overall use of the still less . Plastic Moulds standard model planes, such as standard putter and spring has given more applications, and there have been some of the commercializationof domestic hot runner system components. However, at present China Die level of standardization and commercialization in the general level of below 30 percent and foreign advanced industrial countries has reached 70 percent compared to 80 percent, still a large gap. Table 1, at home and abroad plastic mould technology comparison table? Domestic projects abroad cavity injection model mm0.02 accuracy of 0.005 ~0.01 ~0.05mm cavity surface roughness Ra0.01 ~ 0.05 μ mRa0.20 μ m non-hardened steel die life 10 to 60 million 10 ~ 30 million hardened steel die life 160 ~ 300 million of 50 ~ 100 million hot runner mould overall utilization rate of more than 80 per cent less than 10 per cent level of standardization of 70 ~80% less than 30% of medium-sized plastic mould production cycle about a month 2 ~4 months in the mold industry in the amount of 30 to 40% 25 to 30% According to the parties concerned forecast, the market's overall vigorous mold is a smooth upward, in the next Die market, the development of plastic mould faster than the other Die, die in the proportion of industry will gradually improve. With the continuous development of the plastics industry, put on the plastic mold growing demands is a normal, and so sophisticated, large-scale, complex, long-life plastic mould development will be higher than the overall pace of development. At the same time, imports in recent years because of the mold, precision, large, complex, long-life die in the majority, therefore, reduce imports, increase Guochanhualu: perspective, in the mold of such high-end market share will gradually increase. The rapid development of theconstruction industry so that the various Profile Extrusion Die, PVC plastic pipe fittings Die Die market become a new economic growth point, the rapid development of highways, car tires also put a higher demand, radial tire Die, Die particularly active pace of development will also be higher than the overall average level of the plastic and wood, plastic and metal to make plastic molds in the automotive, motorcycle industry in the demand for huge household appliances industry in the "10th Five-Year Plan" period have greater development, especially refrigerators,air-conditioners and microwave ovens, and other parts of the great demand for plastic moulds, and electronics and communications products, in addition to audio-video products, such as color televisions, laptop computers and set-top boxes will be given a wider network development, which are Plastic Mold market is the growth point. Second, China's industrial and technological plastic mould the future direction of the major developments will include: 1, raising large, sophisticated, complex, long-life mold design and manufacturing standards and proportion. This is due to the molding plastic mould products increasingly large, complex and high-precision requirements, as well as requirements for high productivity and the development of a multi-mode due. 2, in the design and manufacture of plastic mould fully promote the use of CAD / CAM / CAE technology. CAD / CAM technology has developed into a relatively mature technology common in recent years CAD / CAM technology hardware and software prices has been reduced to SMEsgenerally acceptable level of popularity for further create good conditions; based on network CAD / CAM / CAE system integration structure the initial signs of emerging, and it will solve the traditional mixed CAD / CAM system can not meet the actual production process requirements of the division of collaboration; CAD / CAM software will gradually improve intelligence plastic parts and the 3-D mold design and prototyping process 3-D analysis will be in our plastic mould industries play an increasingly important role. 3, promote the use of hot runner technology, gas-assisted injection molding technology and high-pressure injection molding technology. Using hot runner mould technology can improve the productivity and quality of parts and plastic parts can be substantial savings of raw materials and energy conservation, extensive application of this technology is a big plastic mould changes. Hot Runner components formulate national standards, and actively produce cheap high-quality components, the development of hot runner mold is the key. Gas-assisted injection molding product quality can be guaranteed under the premise of substantially lower cost. Currently in the automotive and appliance industries gradually promote the use of the Chiang Kai-shek. Gas-assisted injection molding of the ordinary than the traditional injection of more parameters need to identify and control, and its more commonly used in large, complex products, mold design and control more difficult, therefore, the development of gas-assisted molding flow analysis software It seems veryimportant. On the other hand in order to ensure precision plastic parts to continue to study the development of technology and high-pressure injection molding and injection-compression molding mould and die technology is also very important. 4, the development of new plastics molding technology and rapid economic mold. To adapt to more variety, less volume of production. 5, and improve standardization of plastic mould standard parts usage. China's mold and die level of standard parts standardization still low, the gap between the large and foreign, to a certain extent constraining the development of industries in our country die, die to improve quality and reduce manufacturing costs Die, Die standard parts to vigorously promote the application. To this end, first of all, to formulate a unified national standards, and in strict accordance with the standards of production, secondly it is necessary to gradually scale production, to improve the commercialization of the standard of quality, and reduce costs;again it is necessary to further increase the standard specifications of varieties. 6, Die application quality materials and advanced surface treatment technology for improving the quality of life and mold it is necessary. 7, research and application of high-speed die measurement technology and reverse engineering. CMM-use 3D scanner or reverse engineering is the realization of plastic moulds CAD / CAM one of the key technologies.Research and Application of diversity, adjustment, cheap detection equipment is to achieve the necessary precondition forreverse engineering.塑料模具的发展我国塑料模工业从起步到现在,历经半个多世纪,有了很大发展,模具水平有了较大提高。
(精编)模具注塑术语中英文对照

(精编)模具注塑术语中英文对照(精编)模具注塑术语中英文对照根据国家标准,以下为部分塑料模具成形术语的标准翻译。
动模MovableMouldMovingHalf定模座板FixedClampPlateTopClampingPlateTopPlate动模座板MovingClampPlateBottomClampingPlateBottomPlate上模座板UpperClampingPlate下模座板LowerClampingPlate凹模固定板Cavity-retainerPlate 型芯固定板MouldCore-retainerPlate凸模固定板Punch-retainerPlate模套DieBodyDieSleeveDieBlank支承板BackingPlateSupportPlate垫块SpacerParallel支架EjectorHousingMouldBaseLeg模头DieHead模具分类8InjectionMold注塑模PlasticRubberMould塑胶模RubberMolding橡胶成形HotChamberDieCasting热室压铸SandMoldCasting砂模铸造ExtrusionMold挤出模Multi-CavityMold多模穴模具PalletizingDie叠层模PlasterMold石膏模ThreePlatesMold三板模PlainDie简易模PierceDie冲孔模FormingDie成型模ProgressiveDie连续模GangDies复合模ShearingDie剪边模CavityDie型腔模RivetingDie铆合模CompressionMolding压缩成型FlashMold溢流式模具ExtrusionMold挤压式模具SplitMold分割式模具MouldCavity型腔母模MoldCore模芯公模LargeDieMold大型模具PreciseDieMold 精密模具ComplexDieMold复杂模具FoamingMould发泡模具MetalDie金属模具PlasticMold塑料模具ToolStampingDiePunchDie冲压模具ExtrusionDie挤压模具GraphiteDie石墨模具流道浇口部分RunnerSystem浇道系统SprueColdMaterialTrap浇道冷料井SpruePuller拉杆RunnerDesign流道设计MainRunner主流道SecondaryRunner 次流道MouldGateDesign浇口设计SubmarineGate潜伏浇口TunnelGate隧道式浇口PinpointGate点浇口FanGate扇形浇口SideGate侧浇口EdgeGate侧缘浇口TabGate 搭接浇口FilmGate薄膜浇口FlashGate闸门浇口SlitGate缝隙浇口DishGate盘形浇口DiaphragmGate隔膜浇口RingGate环形浇口Runnerless无浇道Sprueless无射料管方式LongNozzle延长喷嘴方式Sprue浇口,溶渣Insulated/HotRunner热浇道RunnerPlat 浇道模块ValveGate阀门浇口SlagWell冷料井ColdSlag冷料渣SprueGate射料浇口Nozzle 射嘴SprueLockPin料头钩销(拉料杆)注塑缺陷Flash飞边Warpage翘曲AirTrap积风Blush发赤FlowLine流痕Splay银纹ShortShot 短射SinkMark缩痕Streak条纹Void缩孔WeldLine熔接线GasMark烧焦ColdSlug冷斑Delamination起皮Burr毛刺FlawScratch刮伤Gloss光泽Glazing光滑SurfaceCheck表面裂痕Hesitation迟滞注塑工艺MoldingConditions成型条件Drying烘干BarrelTemperature 料筒温度MeltTemperature熔化温度MoldTemperature模具温度InjectionPressure注塑压力BackPressure背压InjectionSpeed注塑速度ScrewSpeed螺杆转速TensileStrength抗拉强度T ensileElongation延伸率FlexuralModulus弯曲模FlexuralStrength抗弯强度Shrinkage收缩率RegrindUsage次料使用Moulding模塑机械设备Lathe车床Planer刨床Miller/MillingMachine铣床Grinder磨床Driller钻床LinearCutting线切割ElectricalSparkle电火花Welder电焊机PunchingMachine冲床Robot机械手CommonEquipment 常用设备EDMElectronDischargeMachining放电加工3DCoordinateMeasurement三次元量床BoringMachine搪孔机ContouringMachine轮廓锯床CopyGrindingMachine仿形磨床CylindricalGrindingMachine外圆磨床DieSpottingMachine合模机EngravingMachine 雕刻机EngravingE.D.M雕模放置加工机FormGrindingMachine成形磨床GraphiteMachine石墨加工机HorizontalBoringMachine卧式搪孔机HorizontalMachineCenter卧式加工制造中心InternalCylindricalMachine内圆磨床模具零件TopPlate上托板(顶板)T opBlock上垫脚PunchSet上模座PunchPad上垫板PunchHolder上夹板StripperPad脱料背板UpStripper上脱料板MaleDie公模(凸模)FeatureDie公母模FemaleDie母模(凹模)UpperMoldPlate上模板LowerMoldPlate 下模板DiePad下垫板DieHolder下夹板DieSet下模座BottomBlock下垫脚BottomPlate下托板(底板)StrippingPlate内外打(脱料板)OuterStripper外脱料板InnerStripper内脱料板LowerStripper下脱料板InnerGuidingPost 内导柱InnerHexagonScrew内六角螺钉DowelPin固定销MouldCoilSpring模具弹簧LifterPin 顶料销IsoheightSleeve等高套筒Pin销LifterGuidePin浮升导料销GuidePin导正销WireSpring圆线弹簧OuterGuidingPost外导柱StopScrew止付螺丝LocatedPin定位销OuterBush外导套Punch冲头Insert入块(嵌入件)DeburringPunch压毛边冲子GroovePunch压线冲子StampedPunch字模冲子RoundPunch圆冲子SpecialShapePunch 异形冲子BendingBlock折刀Roller滚轴BafflePlate挡块LocatedBlock定位块SupportingBlockforLocation定位支承块AirCushionPlate气垫板Air-CushionEject-rod 气垫顶杆TrimmingPunch切边冲子StiffeningRibPunchStinger加强筋冲子RibbonPunch压筋冲子Reel-stretchPunch卷圆压平冲子GuidePlate定位板SlidingBlock滑块SlidingDowelBlock滑块固定块ActivePlate活动板LowerSlidingPlate 下滑块板UpperHolderBlock上压块UpperMidPlate上中间板SpringBox弹簧箱Spring-BoxEject-rod弹簧箱顶杆Spring-BoxEjec模具技术用语各种常用模具成形方式AccurateDieCasting精密压铸PowderForming粉末成形CalendaringMolding压延成形PowderMetalForging粉末锻造ColdChamberDieCasting冷式压铸PrecisionForging 精密锻造ColdForging冷锻PressForgingstampforging冲锻CompactingMolding粉末压出成形RockingDieForging摇动锻造CompoundMolding复合成形RotaryForging回转锻造CompressionMolding压缩成形RotationalMolding离心成形DipMold浸渍成形RubberMolding橡胶成形EncapsulationMolding注入成形SandMoldCasting砂模铸造ExtrusionMolding挤出成形ShellCasting壳模铸造FoamForming 发泡成形SinterForging烧结锻造ForgingRoll轧锻SixSidesForging 六面锻造GravityCasting重力铸造SlushMolding凝塑成形HollowBlowMolding中空(吹出)成形SqueezeCasting高压铸造HotChamberDieCasting热室压铸Swaging挤锻HotForging 热锻TransferMolding转送成形InjectionMolding射出成形WarmForging温锻InvestmentCasting精密铸造MatchedDieMethod对模成形法LaminatingMethod被覆淋膜成形LowPressureCasting低压铸造LostWaxCasting脱蜡铸造MatchedMouldThermalForming对模热成形模CloseMold合模Demould脱模脱模剂MouldUnloading开模ToolChangeRetoolingDieChanging换模MouldClamping锁模各式模具分类用语BismuthMold铋铸模LandedPlungerMold有肩柱塞式模具BurnishingDie挤光模LandedPositiveMold有肩全压式模具ButtonDie镶入式圆形凹模LoadingShoeMold料套式模具Center-GatedMold中心浇口式模具LooseDetailMold活零件模具ChillMold冷硬用铸模LooseMold活动式模具ColdHobbing冷挤压制模法LouveringDie百叶窗冲切模CompositeDies复合模具ManifoldDie分歧管模具CounterPunch反凸模ModularMold组合模具DoubleStackMold双层模具Multi-CavityMold多模穴模具ElectroformedMold电铸成形模Multi-GateMold复式浇口模具ExpanderDie扩径模OffsetColdBendingDie双折冷弯模具ExtrusionDie挤出模PalletizingDie叠层模FamilyMold反套制品模具PlasterMold石膏模BlankThroughDies漏件式落料模PorousMold通气性模具DuplicatedCavityPlate复板模PositiveMold全压式模具FantailDie扇尾形模具PressureDie压紧模FishtailDie鱼尾形模具ProfileDie轮廓模FlashMold溢料式模具ProgressiveDie顺序模GypsumMold石膏铸模PortableMold手提式模具Hot-RunnerMold热流道模具PrototypeMold雏形试验模具原型模具IngotMold钢锭模PunchingDie落料模LancingDie切口模切缝模Raising(Embossing)压花起伏成形Re-entrantMold倒角式模具SectionalDie拼合模RunlessInjectionMold无流道冷料模具SectionalDie对合模具SegmentMold组合模Semi-PositiveMold半全压式模具Shaper 定型模套SingleCavityMold单腔模具SolidForgingDie整体锻模SplitForgingDie拼合锻模SplitMold双并式模具SpruelessMold无注道残料模具SqueezingDie挤压模StretchFormDie拉伸成形模SweepingMold 平刮铸模SwingDie振动模具ThreePlatesMold三片式模具TrimmingDie切边模UnitMold单元式模具UniversalMold 通用模具UnscrewingMold退扣式模具YokeTypeDie轭型模t-Plate弹簧箱顶板BushingBlockLinerBushing衬套CoverPlate盖板GuidePad导料块模具厂常用之标准零配件AirVentValve通气阀AnchorPin锚梢AngularPin角梢Baffle调节阻板AngularPin倾斜梢BafflePlate折流档板BallButton球塞套BallPlunger定位球塞BallSlider球塞滑块BinderPlate压板BlankHolder防皱压板BlankingDie落料冲头Bolster上下模板Bottomboard浇注底板Bolster垫板BottomPlate下固定板Bracket托架BumperBlock 缓冲块Buster堵口CastingLadle浇注包Castinglug铸耳Cavity模穴(模仁)CavityRetainerPlate模穴托板CenterPin中心梢ClampingBlock 锁定块CoilSpring螺旋弹簧ColdPunchedNut冷冲螺母CoolingSpiral螺旋冷却栓Core心型CorePin心型梢Cotter开口梢Cross十字接头CushionPin缓冲梢DiaphragmGate盘形浇口DieApproach模头料道DieBed型底DieBlock块形模体DieBody铸模座DieBush合模衬套DieButton冲模母模DieClamper夹模器DieFastener模具固定用零DieHolder母模固定板DieLip模唇DiePlate冲模板DieSet冲压模座DirectGate直接浇口DogChuck爪牙夹头Dowel定位梢DowelHole导套孔DowelPin合模梢Dozzle辅助浇口DowelPin定位梢Draft拔模锥度DrawBead张力调整杆DriveBearing传动轴承EjectionPad顶出衬垫Ejector脱模器EjectorGuidePin顶出导梢EjectorLeaderBush顶出导梢衬套EjectorPad顶出垫EjectorPin 顶出梢EjectorPlate顶出板EjectorRod顶出杆EjectorSleeve顶出衬套EjectorValve顶出阀EyeBolt环首螺栓FillingCore填充型芯椿入蕊FilmGate薄膜形浇口FingerPin指形梢FinishMachinedPlate 角形模板FinishMachinedRoundPlate圆形模板FixedBolsterPlate固定侧模板FlangedPin带凸缘针FlashGate毛边形浇口Flask上箱FloatingPunch浮动冲头Gate浇口GateLand浇口面Gib凹形拉紧楔GooseNeck鹅颈管GuideBushing引导衬套GuidePin导梢GuidePost 引导柱GuidePlate导板GuideRail导轨HeadPunch顶头冲孔HeadlessPunch直柄冲头HeavilyT aperedSolid整体模蕊盒HoseNippler管接头ImpactDamper缓冲器InjectionRam压射柱InlayBush嵌入衬套InnerPlunger内柱塞InnerPunch内冲头Insert 嵌件InsertPin嵌件梢KingPin转向梢KingPinBush主梢衬套KnockoutBar脱模杵Land 合模平坦面LandArea合模面LeaderBush导梢衬套LiftingPin起模顶针起模杆Lining内衬LocatingCenterPunch定位中心冲头LocatingPilotPin定位导梢LocatingRing定位环LockBlock压块LockingBlock定位块LockingPlate定位板LooseBush活动衬套MakingDie打印冲子ManifoldBlock歧管档块MasterPlate靠模样板MatchPlate分型板MoldBase塑胶模座MoldClamp铸模紧固夹MoldPlaten模用板MovingBolster换模保持装置MovingBolsterPlate可动侧模板OnePieceCasting整体铸件ParallelBlock平行垫块PartingLine 分模线PartingLockSet合模定位器PassGuide穴型导板PeenedHeadPunch镶入式冲头锤击强化冲头钻杆凸模PilotPin定位销导向销子PinGate针尖浇口Plate衬板PreExtrusionPunch顶挤冲头Punch冲头Puncher推杆PusherPin衬套梢Rack机架RappingRod起模杆Re-entrantMold凹入模RetainerPin嵌件梢RetainerPlate托料板ReturnPin回位梢RidingStripper浮动脱模器RingGate环型浇口Roller滚筒Runner流道RunnerEjectorSet流道顶出器RunnerLockPin流道拉梢ScrewPlug头塞SetScrew固定螺丝Shedder脱模装置Shim分隔片Shoe模座之上下模板Shoot流道ShoulderBolt肩部螺丝Skeleton骨架SlagRiser冒渣口Slide(SlideCore)滑块SlipJoint滑配接头SpacerBlock间隔块SpacerRing间隔环Spider模蕊支架Spindle主轴Sprue注道SprueBushing注道衬套SprueBushingGuide注道导套SprueLockBushing注道定位衬套SpruePuller注道拉料浇道推出杆注道残料顶销SpewLine合模线SquareKey方键SquareNut方螺帽SquareThread方螺纹LimitStopCollar限位套StopPin止动梢StopRing止动环Stopper定位停止梢StraightPin圆柱销StripperBolt脱料螺栓StripperBushing脱模衬套StripperPlate剥料板StrokeEndBlock行程止梢SubmarineGate潜入式浇口SupportPillar支撑支柱顶出支柱SupportPin支撑梢SupportingPlate托板SweepT emplate造模刮板TabGate辅助浇口TaperKey推拔键TaperPin拔锥梢锥形梢TeemingPouring浇注ThreeStartScrew 三条螺纹ThrustPin推力销TieBar拉杵TunnelGate隧道形浇口Vent通气孔WortlePlate拉丝模板模具常用之工作机械3DCoordinateMeasurement三次元量床BoringMachine搪孔机CNCMillingMachineCNC铣床ContouringMachine轮廓锯床CopyGrindingMachine仿形磨床CopyLathe仿形车床CopyMillingMachine仿形铣床CopyShapingMachine仿形刨床CylindricalGrindingMachine外圆磨床DieSpottingMachine合模机DrillingMachine钻孔机EngravingMachine雕刻机EngravingE.D.M 雕模放置加工机FormGrindingMachine成形磨床GraphiteMachine 石墨加工机HorizontalBoringMachine卧式搪孔机HorizontalMachineCenter卧式加工制造中心InternalCylindricalMachine内圆磨床JigBoringMachine冶具搪孔机JigGrindingMachine冶具磨床LapMachine研磨机MachineCenter加工制造中心MultiModelMiller靠磨铣床NCDrillingMachineNC钻床NCGrindingMachineNC磨床NCLatheNC车床NCProgrammingSystemNC程式制作系统Planer 龙门刨床ProfileGrindingMachine投影磨床ProjectionGrinder投影磨床RadialDrillingMachine旋臂钻床Shaper牛头刨床SurfaceGrinder平面磨床TryMachine试模机TurretLathe转塔车床UniversalToolGrindingMachine万能工具磨床VerticalMachineCenter立式加工制造中心WireE.D.M线割放电加工机入水Gate进入位GateLocation水口形式GateType大水口EdgeGate细水口Pin-pointGate水口大小GateSize转水口SwitchingRunnerGate唧嘴口径SprueDiameter流道MoldRunner热流道HotRunnerHotManifold温度控制器温控器ThermostatThermoregulatorsT emperatureController 热嘴冷流道HotSprueColdRunner 唧嘴直流DirectSprueGate圆形流道RoundFullHalfRunner流道电脑分析MoldFlowAnalysis流道平衡RunnerBalance热嘴HotSprue热流道板HotManifold发热管CartridgeHeater探针Thermocouples插头ConnectorPlug插座ConnectorSocket密封封料Seal运水WaterLine喉塞LinePlugThroatT aps喉管Tube塑胶管PlasticTube快速接头JiffyQuickConnectorQuickDisconnectCoupling 模具零件MoldComponents三板模3-PlateMold二板模2-PlateMold边钉导边LeaderPinGuidePin边司导套BushingGuideBushing中托司ShoulderGuideBushing中托边GuidePin顶针板EjectorRetainnerPlate托板SupportPlate螺丝Screw管钉DowelPin开模槽PlyBarScot内模管位CoreCavityinter-Lock顶针EjectorPin司筒EjectorSleeve司筒针EjectorPin推板EjectPlatePushPlateStripperPlate缩呵MovableCoreReturnCorePuller 扣机(尼龙拉勾)NylonLatchLock 斜顶Lifter模胚(架)MoldBase上内模CavityInsert下内模CoreInsert行位(滑块)Slide镶件Insert压座Wedge耐磨板油板WedgeWearPlate压条Plate撑头SupportPillar唧嘴SprueBushing挡板StopPlate定位圈LocatingRing锁扣Latch扣机PartingLockSet推杆PushBar栓打螺丝S.H.S.B顶板EjectorPlate活动臂LeverArm分流锥SprueSpreader分流板SpreaderPlate水口司Bush垃圾钉StopPin隔片Buffle弹弓柱SpringRod弹弓DieSpring中托司EjectorGuideBush中托边EjectorGuidePin镶针Pin销子DowelPin波子弹弓Ballcatch喉塞PipePlug锁模块LockPlate斜顶AnglefromPin斜顶杆AngleEjectorRod尼龙拉勾PartingLocks活动臂LeverArm复位键提前回杆EarlyReturnBar气阀Valves斜导边AnglePin术语Terms承压平面平衡PartingSurfaceSupportBalance模排气PartingLineVenting回针碰料位ReturnPinandCavityInterference 顶针碰运水WaterLineInterfereswithEjectorPin 料位出上下模PartfromCavith (Core)Side不准用镶件DoNotUse(CoreCavity)Insert 用铍铜做镶件UseBerylliumCopperInsert初步模图设计PreliminaryMoldDesign正式模图设计FinalMoldDesign弹弓压缩量SpringCompressedlength稳定性好GoodStabilityStable强度不够InsufficientRigidity均匀冷却EvenCooling扣模Sticking热膨胀ThermalExpansion公差Tolerance铜公(电极)CopperElectrode AirVentValve通气阀AnchorPin锚梢AngularPin角梢Baffle调节阻板AngularPin倾斜梢BafflePlate折流挡板BallButton球塞套BallPlunger定位球塞BallSlider球塞滑块BinderPlate压板BlankHolder防皱压板BlankingDie落料冲头Bolster上下模板BottomBoard浇注底板Bolster垫板BottomPlate 下固定板Bracket托架BumperBlock缓冲块Buster堵口CastingLadle浇注包CastingLug铸耳Cavity模腔模穴(模仁)CavityRetainerPlate模穴托板CenterPin中心梢ClampingBlock锁定块CoilSpring螺旋弹簧ColdPunchedNut冷冲螺母CoolingSpiral螺旋冷却栓。
项目 模具英语

项目模具英语一、概述模具(Mould)是创造工业中常用的工具,用于创造各种产品的形状和尺寸。
模具英语是指与模具相关的英语词汇和表达。
掌握模具英语对于从事模具创造、模具设计、模具加工等相关工作的人员来说至关重要。
本文将介绍模具英语的基本词汇和常用表达,以匡助读者更好地理解和运用模具英语。
二、模具英语词汇1. Mould/Mold:模具2. Die:模具3. Injection moulding:注塑成型4. Casting mould:铸造模具5. Press tool:冲压模具6. Plastic mould:塑料模具7. Prototype tooling:样品模具8. Mold cavity:模腔9. Core:芯子10. Ejector pin:顶针11. Runner system:流道系统12. Cooling system:冷却系统13. Draft angle:脱模锥度14. Gate:浇口15. Vent:排气孔16. Shrinkage:收缩17. Surface finish:表面处理18. Tolerance:公差19. EDM (Electrical Discharge Machining):电火花加工20. CNC (Computer Numerical Control):数控加工三、常用表达1. Could you please provide the 3D model of the mould?:请提供模具的3D模型好吗?2. What is the estimated production cycle of this mould?:这个模具的估计生产周期是多久?3. We need to modify the mould design to meet the client's requirements.:我们需要修改模具设计以满足客户的要求。
4. The mould cavity needs to be polished for better surface finish.:为了获得更好的表面处理效果,需要对模腔进行抛光。
塑料模具中英文解释大全
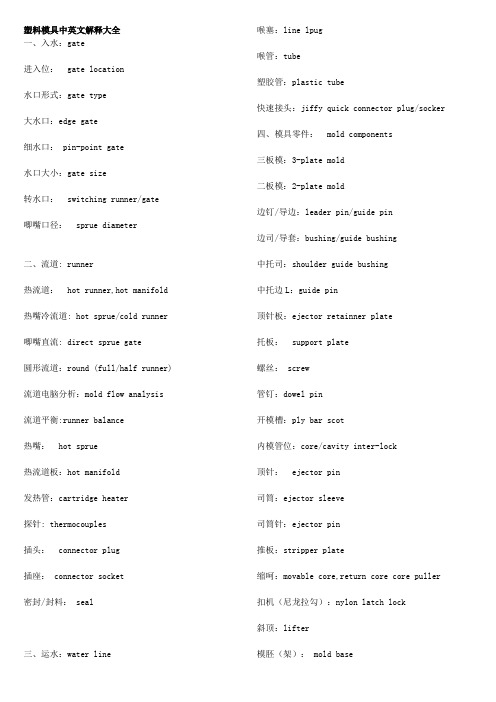
塑料模具中英文解释大全一、入水:gate进入位:gate location水口形式:gate type大水口:edge gate细水口: pin-point gate水口大小:gate size转水口:switching runner/gate唧嘴口径:sprue diameter二、流道: runner热流道:hot runner,hot manifold 热嘴冷流道: hot sprue/cold runner 唧嘴直流: direct sprue gate圆形流道:round (full/half runner) 流道电脑分析:mold flow analysis 流道平衡:runner balance热嘴:hot sprue热流道板:hot manifold发热管:cartridge heater探针: thermocouples插头:connector plug插座: connector socket密封/封料: seal三、运水:water line 喉塞:line lpug喉管:tube塑胶管:plastic tube快速接头:jiffy quick connector plug/socker 四、模具零件:mold components三板模:3-plate mold二板模:2-plate mold边钉/导边:leader pin/guide pin边司/导套:bushing/guide bushing中托司:shoulder guide bushing中托边L:guide pin顶针板:ejector retainner plate托板:support plate螺丝: screw管钉:dowel pin开模槽:ply bar scot内模管位:core/cavity inter-lock顶针:ejector pin司筒:ejector sleeve司筒针:ejector pin推板:stripper plate缩呵:movable core,return core core puller 扣机(尼龙拉勾):nylon latch lock斜顶:lifter模胚(架): mold base上内模:cavity insert下内模:core insert行位(滑块): slide镶件:insert压座/斜鸡:wedge耐磨板/油板:wedge wear plate 压条:plate撑头: support pillar唧嘴: sprue bushing挡板:stop plate定位圈:locating ring锁扣:latch扣鸡:parting lock set推杆:push bar栓打螺丝:S.H.S.B顶板:eracuretun活动臂:lever arm分流锥:spure sperader水口司:bush垃圾钉:stop pin隔片:buffle弹弓柱:spring rod弹弓:die spring中托司:ejector guide bush中托边:ejector guide pin 镶针:pin销子:dowel pin波子弹弓:ball catch喉塞: pipe plug锁模块:lock plate斜顶:angle from pin斜顶杆:angle ejector rod尼龙拉勾:parting locks活动臂:lever arm复位键、提前回杆:early return bar气阀:valves斜导边:angle pin术语:terms承压平面平衡:parting surface support balance模排气:parting line venting回针碰料位:return pin and cavity interference模总高超出啤机规格:mold base shut hight顶针碰运水:water line interferes withejector pin 料位出上/下模:part from cavith (core) side模胚原身出料位:cavity direct cut on A-plate,core direct cut on B-plate.不准用镶件: Do not use (core/cavity) insert用铍铜做镶件: use beryllium copper insert初步(正式)模图设计:preliinary (final) mold design 反呵:reverse core弹弓压缩量:spring compressed length稳定性好:good stability,stable强度不够:insufficient rigidity均匀冷却:even cooling扣模:sticking热膨胀:thero expansion公差:tolorance铜公(电极):copper electrode提问者:xiaoli-试用期 (一级)-2008-6-8 8:02:37其他回答共2条一、入水:gate进入位:gate location水口形式:gate type大水口:edge gate细水口: pin-point gate水口大小:gate size转水口:switching runner/gate唧嘴口径:sprue diameter二、流道: runner热流道:hot runner,hot manifold热嘴冷流道: hot sprue/cold runner唧嘴直流: direct sprue gate圆形流道:round (full/half runner)流道电脑分析:mold flow analysis流道平衡:runner balance热嘴:hot sprue 热流道板:hot manifold发热管:cartridge heater探针: thermocouples插头:connector plug插座: connector socket密封/封料: seal三、运水:water line喉塞:line lpug喉管:tube塑胶管:plastic tube快速接头:jiffy quick connector plug/socker 四、模具零件:mold components三板模:3-plate mold二板模:2-plate mold边钉/导边:leader pin/guide pin边司/导套:bushing/guide bushing中托司:shoulder guide bushing中托边L:guide pin顶针板:ejector retainner plate托板:support plate螺丝: screw管钉:dowel pin开模槽:ply bar scot内模管位:core/cavity inter-lock顶针:ejector pin司筒:ejector sleeve司筒针:ejector pin推板:stripper plate缩呵:movable core,return core core puller 扣机(尼龙拉勾):nylon latch lock斜顶:lifter模胚(架): mold base上内模:cavity insert下内模:core insert行位(滑块): slide镶件:insert压座/斜鸡:wedge耐磨板/油板:wedge wear plate压条:plate撑头: support pillar唧嘴: sprue bushing挡板:stop plate定位圈:locating ring锁扣:latch扣鸡:parting lock set推杆:push bar栓打螺丝:S.H.S.B顶板:eracuretun活动臂:lever arm 分流锥:spure sperader水口司:bush垃圾钉:stop pin隔片:buffle弹弓柱:spring rod弹弓:die spring中托司:ejector guide bush中托边:ejector guide pin镶针:pin销子:dowel pin波子弹弓:ball catch喉塞: pipe plug锁模块:lock plate斜顶:angle from pin斜顶杆:angle ejector rod尼龙拉勾:parting locks活动臂:lever arm复位键、提前回杆:early return bar气阀:valves斜导边:angle pin术语:terms承压平面平衡:parting surface support balance 模排气:parting line venting回针碰料位:return pin and cavity interference 模总高超出啤机规格:mold base shut hight顶针碰运水:water line interferes withejector pin料位出上/下模:part from cavith (core) side模胚原身出料位:cavity direct cut on A-plate,core direct cut on B-plate.不准用镶件: Do not use (core/cavity) insert用铍铜做镶件: use beryllium copper insert初步(正式)模图设计:preliinary (final) mold design 反呵:reverse core弹弓压缩量:spring compressed length稳定性好:good stability,stable强度不够:insufficient rigidity均匀冷却:even cooling扣模:sticking热膨胀:thero expansion公差:tolorance铜公(电极):copper electrode。
模具各零部件名称中英文对照

模具各零部件名称中英文对照模具各零部件名称中英文对照 .txt 生活是过出来地 ,不是想出来地 . 放得下地是曾经 ,放不下Mold changing systems Mold core 模芯 Mold heaters/chillers Mold polishing/texturing Mold repair 模具维修 Molds 模具Pressing dies 压模Quick die change systems Quick mold change systems、模具塑料模具 mould ofplastics 注塑模具injection mould 冲压模具die 模架mould base定模座板 Top clamping plate Top plateFixed clamp plate 水口推板 stripper plateA 板 A plateB 板B plate 支承板support plate 方铁spacer plate 底针板ejector plate面针板 ejector retainer plate 回针 Return pin 导柱 Guide pin 有托导套 Shoulder Guide bush 直导套 Straight Guide bush 动模座板 Bottom clamp plateMoving clamp plate 基准线 datum line基准面 datum plan型芯固定板core-retainer plate 凸模固定板punch-retainer plate 顶针 ejector pin 单腔模具 single cavity mould 多腔模具 multi-cavity mould 多浇口 multi-gating 浇口 gate缺料starving 排气breathing 光泽gloss 合模力mould clamping force 锁模力 mouldlocking force 挤出 extrusion 开裂 crack 循环时间 cycle time 老化 aging 螺杆 screw 麻点 pit 嵌件 insert 活动镶件 movable insert 起垩 chalking 浇注系统 feed system 主流道 sprue分流道 runner 浇口 gate 直浇口 direct gate , sprue gate 轮辐浇口 spoke gate , spidergate 点浇口pin-point gate 测浇口edge gate 潜伏浇口submarine gate , tunnel gate 料穴cold-slug well 浇口套sprue bush 流道板 runner plate 排飞槽 vent分型线<面) parting line 定模 stationary mould,Fixed mould 动模 movable mould,movable half 上模 upper mould, upper half 下模 lower mould, lower half 型腔 cavity 凹模 cavity plate,cavity block 拼块 split 定位销 dowel 定位销孔dowel hole 型芯 core 斜销angle pin, finger cam 滑块 slide 滑块导板 slide guide strip 楔紧块 heel block, wedge lock 拉料杆 sprue puller 定位环 locating ring 冷却通 cooling channel 脱模斜度 draft 滑动型芯 slide core螺纹型芯 threaded core 热流道模具 hot-runner mould 绝热流道模 insulated runner mould 熔合纹 weld line <="" 脱模=""> interchangeable cavity mould 脱模剂 release agent 注射能力shot capacity 注射速率 injection rate 注射压力 injection pressure 差色剂 colorant 保压时间 holdup time 闭模时间closing time 定型装置sizing system 阴模female mould,cavity block 阳模male mould 电加工设备Electron Discharge Machining 数控加工中心 CNC machine center 万能铁床Universal milling machine 卧式刨床Horizontal planer 车床Engine lathe 平面磨床Surface grinding machine 去磁机Demagnetization machine 万能摇臂钻床 Universal radial 地是记忆 . 无论我在哪里, 我离你都只有一转身地距离 .Mold & die components 模具单元换模系统模具加热器 / 冷却器模具打磨 /速换模系统快速换模系统movable driller 立式钻床Vertical driller 超声波清洗机Ultrasonic clearing machine compre sion molding 压缩成型flash mold 溢流式模具plsitive mold 挤压式模具split mold 分割式模具cavity 型控母模core 模心公模taper 锥拔leather cloak 仿皮革shiver 饰纹flow mark 流痕welding mark 溶合痕post screw insert 螺纹套筒埋值self tapping screw 自攻螺丝striper plate 脱料板piston 活塞cylinder 汽缸套chip 细碎物handle mold 手持式模具<移转成型用模具)encapsulation molding 低压封装成型<射出成型用模具)two plate 两极式<模具)well type 蓄料井insulated runner 绝缘浇道方式hot runner 热浇道runner plat 浇道模块valve gate 阀门浇口band heater 环带状地电热器spindle 阀针spear head 刨尖头slag well 冷料井cold slag 冷料渣air vent 排气道welding line 熔合痕eject pin 顶出针knock pin 顶出销return pin 回位销反顶针sleave 套筒stripper plate 脱料板insert core 放置入子runner stripper plate 浇道脱料板guide pin 导销eject rod (bar>< 成型机)顶业捧subzero 深冷处理three plate 三极式模具runner system 浇道系统stress crack 应力电裂orientation 定向sprue gate 射料浇口, 直浇口nozzle 射嘴sprue lock pin 料头钩销(拉料杆> slag well 冷料井side gate 侧浇口edge gate 侧缘浇口tab gate 搭接浇口film gate 薄膜浇口flash gate 闸门浇口slit gate 缝隙浇口fan gate 扇形浇口dish gate 因盘形浇口diaphragm gate 隔膜浇口ring gate 环形浇口subarine gate 潜入式浇口tunnel gate 隧道式浇口pin gate 针点浇口Runner less 无浇道(sprue less>无射料管方式long nozzle 延长喷嘴方式sprue 浇口。
模具中英对照

模具中英对照模具是一种用来制造复杂形状的工具,广泛应用于汽车、航空、电子、医疗等领域。
在国际贸易中,模具领域是一个重要的行业,涉及到的技术术语和行业术语繁多,因此,建立起一个模具中英对照的文档对于学习和应用模具领域具有重要的意义。
下面我们将列出一些常见的模具术语及其中英对照:1. 模具设计:mould design2. 模具制造:mould making3.模具材料:mould material4. 模具钢:mould steel5. 模具试样:mould trial sample6. 模具寿命:mould life7. 塑料注塑模具:plastic injection mould8. 金属冲压模具:metal stampingmould9. 模具零件:mould parts10. 设计参数:design parameter11. 模具尺寸:mould dimension12. 模具重量:mould weight13. 模具结构:mould structure14. 成型工艺:forming process15. 模具表面处理:mould surface treatment16. 冷却系统:cooling system17. 模具加工:mould machining18.精度控制:precision control19. 模具维护:mould maintenance20. 模具修复:mould repair随着模具行业的发展,中英对照文档需要不断地进行更新和完善。
在实际应用中,我们需要根据需求来确定需要掌握的技术和行业术语,并及时查阅相关的中英对照文档,以便更好地理解和使用模具技术。
除了上述列出的术语,模具领域还涉及到很多具有专业性的技术术语和行业术语,例如模具热处理、模具注塑成型、模具表面处理等方面的专业术语。
因此,掌握和应用模具技术需要具备较高的专业素养和知识储备,这需要我们持续地学习、实践和总结。
塑料模具专业术语(原有)

分流道
runner
连接主流道和浇口的进料通道
24.
浇口
gate
连接分流道和型腔的进料通道。
25.
直接浇口
direct gate; sprue gate
熔融塑料经主流道直接进入型腔的进料方式。
26.
环形浇口
ring gate
沿塑件(或塑件上的孔)的整个外圆周而扩展进料的浇口。
27.
盘形浇口
disk gate
当成型零件(凹模、凸模或型芯)有易损或难以整体加工的部位时,与主体件分离制造并嵌在主体件上的局部成型零件
61.
活动镶件
movable insert
loose detail
根据工艺和结构要求,须随塑件一起出模,方能从塑件中分离取出的镶件。
62.
拼块
splits(of a mould)
按设计和工艺要求,用以拼合模具型腔或型芯
B、在注射模中,为避免在塑料件上可能产生熔接痕而在模具上开设排溢用的沟槽。
49.
排气槽(孔)
vent(of a mould)
为使型腔内的气体排出模具外,在模具上开设的气流通槽或孔。
50.
分型
分型面
parting line
模具上用以取出塑件和(或)浇注系统凝料的可分离的接触表面。
51.
水平分型面(线)
用于固定凹模的板状零件
77.
型芯固定板
core-retainer plate
用于固定型芯的板状零件
78.
凸模固定板
punch-retainer plate
用于固定凸模的板状零件
79.
模套
chase
bolster
模具专业英语,模具词汇,模具中英词汇,机械英语,外贸模具英语,外贸英语,专业英语,

Mould for plastics 塑料成型模具mould for thermoplastics 熱塑性塑料模mould for thermosets 熱固性塑料模compression mould 壓縮模transfer mould 傳遞模injection mould 注射模flash mould 溢式壓縮模semi-positiue mould 半溢式壓縮模positiue mould 不溢式壓縮模portable mould 移動式模具fixed mould 固定式模具runerless mould 無流道模hot runner mould 熱流道模insulated runner mould 絕熱流道模warm runner mould 溫流道模二feed system 澆注系統sprue 主流道runner 分流道gate 澆口sprue gate 直接澆口ring gate 環形澆口disk gate 盤形澆口spider gate 軟輻澆口pin point gate 點澆口edge gate 側澆口tunnel gate.subgate 潛伏澆口tabe gate 護耳澆口fan gate 扇形澆口cold-slug well 冷料穴sprue busing 澆口套spreader 分流錐runnet plate 流道板nozzle 噴嘴heater 加熱器hear pipe 熱管valve gate 閥式澆口三details of moulds 模具零件force plunger,por planger 柱塞stationary mould,fixed half 定模movable mould,moving half 動模upper mould,upperhalf 上模lower mould,lower half 下模cavity(of a mould) 型腔impression cavity block cavity plate! 凹模insert 鑲件splits(of mould) 拼坱core 型芯side core,slide core 側型芯thread plup,threaded core 螺紋型芯thread ring,threaded cavity 螺紋型環punch force! 击模fixed clamp plate 固定座板chase,bolsler,frame 模套retaine plate,supprt plate 固定板supprt plate 支撐板spacer pevrallel 墊板mould bese leg 支撐架1support pillar 支承柱angle pin finger cam 斜銷slide cam,slide 滑坱side gnide strip 側型芯滑坱heel block,wedge block 滑坱導板finger guide plate 楔緊坱clog-leg cam 彎銷angled-alift,splits 斜滑坱guide pillar,guide pin 導柱guide pillar straight,straight leader pin 帶頭導柱guide pillar shoaldered,shoulder leader pin 帶肩導柱ejector guide pillar 推板導套guide bushing 導套straight bushing 直導套shoulder bushing 帶頭導套ejector guide push ejector pushing 椎板導套locating ring 定位圈mould bases locating elements 錐形定位件ejector plate return,pin push-back pin 复位杆stop pin,stop flock,spto bad 限位釘length boltt,puller bolt 定距拉杆puller plate,limit plate 定距拉板ejector pin 推杆ejector pin whith cylindrical head 園柱頭推杆shouldered ejector pin 帶肩推杆ejector pin with cylindrical head 扁推杆ejector sleeve 推管ejector pad 推坱ejection plate 推板ejector tie rod 連接推杆sprue puller 拉料杆sprue puller,z-shaped 鉤形拉料杆sprue puller,ball headed 球頭拉料杆sprue puller,conical headed 園錐頭拉料杆runner puller,runner lock pin 分流道拉料杆runner stripper plate 推流道板cooling system,cooling circuit 冷卻系統回路coolant passages 冷卻液出入口baffle 隔板jeating plate 加熱板thermal lnsulation board 隔熱板mould bases(of a injection mould) 模架standard mould bases 標準模架四design factors 設計要素shot capacity 注射能力shrinkage 收縮率injection pressure 注射壓力clamping force,locking force 鎖模力woulding pressure 成型壓力internal mould pressure,cavity pressure 模內壓力would opening force 開模力stripping force 脫模力core-pulling force 抽芯力core-pulling distance 抽芯距mould shut height 閉捨高度mahimuan daylight,open daylight 最大開距projected area 投影面積draft 脫模斜度stripper distance 脫模距viscosith 粘度shear stress 剪切應力shear rate 剪切速度pressure drop 壓力降injection rate 注射速度率weld line 熔結痕gate location 澆口開設位置solidification time 固化時間flash groove spovo groove 排溢溢料槽vent 排氣槽parting line 分型面hotizontal parting line 水平分型面vertical parting line 垂直分型面。
塑模设计中常见术语的英文翻译
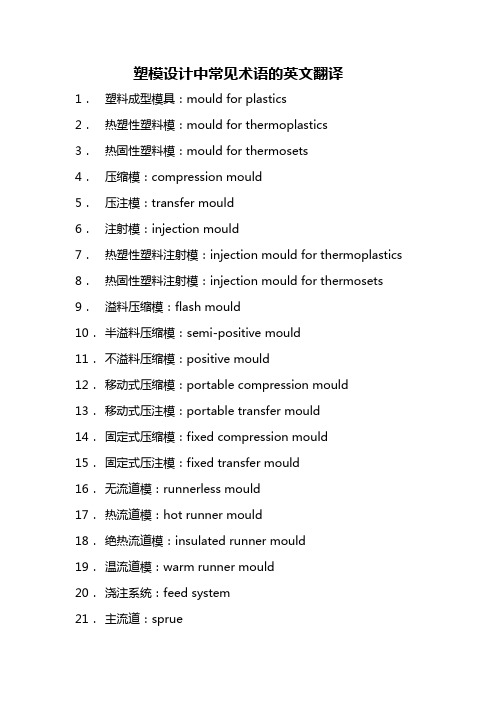
塑模设计中常见术语的英文翻译1.塑料成型模具:mould for plastics2.热塑性塑料模:mould for thermoplastics3.热固性塑料模:mould for thermosets4.压缩模:compression mould5.压注模:transfer mould6.注射模:injection mould7.热塑性塑料注射模:injection mould for thermoplastics 8.热固性塑料注射模:injection mould for thermosets 9.溢料压缩模:flash mould10.半溢料压缩模:semi-positive mould11.不溢料压缩模:positive mould12.移动式压缩模:portable compression mould13.移动式压注模:portable transfer mould14.固定式压缩模:fixed compression mould15.固定式压注模:fixed transfer mould16.无流道模:runnerless mould17.热流道模:hot runner mould18.绝热流道模:insulated runner mould19.温流道模:warm runner mould20.浇注系统:feed system21.主流道:sprue22.分流道:runner23.浇口:gate24.直接浇口:direct gate 25.环型浇口:ring gate26.盘型浇口:disk gate27.轮辐浇口:spoke.gate28.点浇口:pin-point.gate 29.侧浇口:edge.gate30.潜伏浇口:submarine gate 31.扇形浇口:fan gate32.护耳浇口:tab gate33.冷料穴:cold-slug well 34.浇口套:sprue bush35.浇口镶块:gating insert 36.分流锥:spreader37.流道板:runner plate38.热流道板:manifold block 39.温流道板:warm runner plate 40.二级喷嘴:secondary nozzle 41.热管;heat pipe42.阀式浇口:valve gate43.加料腔:loading chamber44.柱塞:force plunger45.溢料槽:flash groove46.排气槽:vent47.分型面:parting line48.定模:stationary mould 49.动模:movable mould50.上模:upper mould51.下模:lower mould52.型腔:cavity53.凹模:impression54.镶件:mold insert55.活动镶件:movable insert 56.拼块:splits57.凹模拼块:cavity splits 58.型芯拼块:core splits 59.型芯:core60.侧型芯:side core61.螺纹型芯:thread core 62.螺纹型环:thread ring 63.凸模:punch64.嵌件:insert65.定模座板:fixed clamp plate66.动模座板:moving clamp plate 67.上模座板:upper clamp plate 68.下模座板:lower clamp plate 69.凹模固定板:cavity-retainer plate 70.型芯固定板:core- retainer plate 71.凸模固定板:punch- retainer plate 72.模套:chase73.支承板:backing plate74.垫块:spacer75.支架:ejector housing76.支承柱:support pillar77.模板:mould plate78.斜销:angle pin79.滑块:slide80.侧型芯滑块:side core-slide81.滑块导板:slideguide strip82.楔紧块;heel block83.斜槽导板:finger guide plate 84.弯销:dog-leg cam85.斜滑块:angled-lift splits86.导柱:guide pillar87.带头导柱:guide pillar straight88.带肩导柱:guide pillar,shouldered89.推板导柱:ejector guide pillar90.导套:guide bush91.直导套:guide bush,straight92.带头导套:guide bush,head93.推板导套:ejector guide bush94.定位圈:locating ring95.锥形定位件:mould bases locating elements 96.复位杆:ejector plate return pin97.限位钉:stop pin98.限位块:stop block99.定距拉杆:length bolt100.定距拉板:puller plate101.推杆:ejector pin102.圆柱头推杆:ejector pin with cylindrical head 103.带肩推杆:shouldered ejector pin104.扁推杆:flat ejector pin105.推管:ejector sleeve106.推块:ejector pad107.推件板:stripper plate108.推杆固定板:ejector retainer plate109.推板:ejection plate110.连接推杆:ejector tie rod111.拉料杆:sprue puller112.推流道板:runner stripper plate113.冷却管道:cooling channel114.隔板:baffle115.加热板:heating plate116.隔热板:thermal insulation board117.模架:mould bases118.注射能力:shot capacity119.收缩率:shrinkage120.注射压力:injection pressure121.锁模力:clamping force/locking force122.成型压力:moulding pressure123.模内压力:internal mould pressure /cavity pressure 124.开模力:mould opening force125.脱模力:ejection force126.抽芯力:core-pulling distance127.闭合高度:mould shut height128.最大开距:maximum daylight /open daylight129.投影面积:projected area130.脱模斜度:draft131.脱模距:stripper distance。
塑料模具外文翻译

Die history1 Die position in industrial productionMold is a high-volume products with the shape tool, is the main process of industrial production equipment.With mold components, with high efficiency, good quality, low cost, saving energy and raw materials and a series of advantages, with the mold workpieces possess high accuracy, high complexity, high consistency, high productivity and low consumption , other manufacturing methods can not match. Have already become an important means of industrial production and technological development. The basis of the modern industrial economy.The development of modern industrial and technological level depends largely on the level of industrial development die, so die industry to national economic and social development will play an increasing role. March 1989 the State Council promulgated "on the current industrial policy decision points" in the mold as the machinery industry transformation sequence of the first, production and capital construction of the second sequence (after the large-scale power generation equipment and the corresponding power transmission equipment), establish tooling industry in an important position in the national economy. Since 1997, they have to mold and its processing technology and equipment included in the "current national focus on encouraging the development of industries, products and technologies catalog" and "to encourage foreign investment industry directory." Approved by the State Council, from 1997 to 2000, more than 80 professional mold factory owned 70% VAT refund of preferential policies to support mold industry. All these have fully demonstrated the development of the State Council and state departments tooling industry attention and support. Mold around the world about the current annual output of 60 billion U.S. dollars, Japan, the United States and other industrialized countries die of industrial output value of more than machine toolindustry, beginning in 1997, China's industrial output value has exceeded the mold machine tool industry output.According to statistics, home appliances, toys and other light industries, nearly 90% of the parts are integrated with production of chopsticks; in aircraft, automobiles, agricultural machinery and radio industries, the proportion exceeded 60%. Such as aircraft manufacturing, the use of a certain type of fighter dies more than 30,000 units, of which the host 8000 sets, 2000 sets of engines, auxiliary 20 000 sets. From the output of view, since the 80's, the United States, Japan and other industrialized countries die industry output value has exceeded the machine tool industry, and there are still rising. Production technology, according to the International Association predicts that in 2000, the product best pieces of rough 75%, 50% will be finished mold completed; metals, plastics, ceramics, rubber, building materials and other industrial products, most of the mold will be completed in more than 50% metal plates, more than 80% of all plastic products, especially through the mold into.2 The historical development of moldThe emergence of mold can be traced back thousands of years ago, pottery and bronze foundry, but the large-scale use is with the rise of modern industry and developed.The 19th century, with the arms industry (gun's shell), watch industry, radio industry, dies are widely used. After World War II, with the rapid development of world economy, it became a mass production of household appliances, automobiles, electronic equipment, cameras, watches and other parts the best way. From a global perspective, when the United States in the forefront of stamping technology - many die of advanced technologies, such as simple mold, high efficiency, mold, die and stamping the high life automation, mostly originated in the United States; and Switzerland, fine blanking, cold in Germany extrusion technology, plastic processing of the Soviet Union are at the world advanced. 50's, mold industry focus is based on subscriber demand, production can meet the product requirements of the mold. Multi-die design rule of thumb, reference has been drawing and perceptual knowledge, on the design of mold parts of a lack of real understanding of function. From 1955 to 1965, is the pressure processing of exploration and development of the times - the main components of the mold and the stress state of the function of a mathematical sub-bridge, and to continue to apply to on-site practical knowledge to make stamping technology in all aspects of a leap in development. The result is summarized mold design principles, and makes the pressure machine, stamping materials, processing methods, plum with a structure, mold materials, mold manufacturing method, the field of automation devices, a new look to the practical direction of advance, so that pressing processing apparatus capable of producing quality products from the first stage.Into the 70's to high speed, launch technology, precision, security, development of the second stage. Continue to emerge in this process a variety of high efficiency, business life, high-precision multi-functional automatic school to help with. Represented by thenumber of working places as much as other progressive die and dozens of multi-station transfer station module. On this basis, has developed both a continuous pressing station there are more slide forming station of the press - bending machine. In the meantime, the Japanese stand to the world's largest - the mold into the micron-level precision, die life, alloy tool steel mold has reached tens of millions of times, carbide steel mold to each of hundreds of millions of times p minutes for stamping the number of small presses usually 200 to 300, up to 1200 times to 1500 times. In the meantime, in order to meet product updates quickly, with the short duration (such as cars modified, refurbished toys, etc.) need a variety of economic-type mold, such as zinc alloy die down, polyurethane rubber mold, die steel skin, also has been very great development.From the mid-70s so far can be said that computer-aided design, supporting the continuous development of manufacturing technology of the times. With the precision and complexity of mold rising, accelerating the production cycle, the mold industry, the quality of equipment and personnel are required to improve. Rely on common processing equipment, their experience and skills can not meet the needs of mold. Since the 90's, mechanical and electronic technologies in close connection with the development of NC machine tools, such as CNC wire cutting machine, CNC EDM, CNC milling, CNC coordinate grinding machine and so on. The use of computer automatic programming, control CNC machine tools to improve the efficiency in the use and scope. In recent years, has developed a computer to time-sharing by the way a group of direct management and control of CNC machine tools NNC system.With the development of computer technology, computers have gradually into the mold in all areas, including design, manufacturing and management. International Association for the Study of production forecasts to 2000, as a means of links between design and manufacturing drawings will lose its primary role. Automatic Design of die most fundamental point is to establish the mold standard and design standards. To get rid of the people of the past, and practical experience to judge the composition of the design center, we must take past experiences and ways of thinking, for series, numerical value, the number of type-based, as the design criteria to the computer store.Components are dry because of mold constitutes a million other differences, to come up with a can adapt to various parts of the design software almost impossible. But some products do not change the shape of parts, mold structure has certain rules, can be summed up for the automatic design of software. If a Japanese company's CDM system for progressive die design and manufacturing, including the importation of parts of the figure, rough start, strip layout, determine the size and standard templates, assembly drawing and parts, the output NC program (for CNC machining Center and line cutting program), etc., used in 20% of the time by hand, reduce their working hours to 35 hours; from Japan in the early 80s will be three-dimensional cad / cam system for automotive panel die. Currently, the physical parts scanning input, map lines and data input, geometric form, display, graphics, annotations and the data is automatically programmed, resulting in effective control machine tool control system of post-processing documents have reached a high level; computer Simulation (CAE) technology has made some achievements. At high levels, CAD / CAM / CAE integration, that data is integrated, can transmit information directly with each other. Achieve network. Present. Only a few foreign manufacturers can do it.3 China's mold industry and its development trendDie & Mould Industry StatusDue to historical reasons for the formation of closed, "big and complete" enterprise features, most enterprises in China are equipped with mold workshop, in factory matching status since the late 70s have a mold the concept of industrialization and specialization of production. Production efficiency is not high, poor economic returns. Mold production industry is small and scattered, cross-industry, capital-intensive, professional, commercial and technical management level are relatively low.According to incomplete statistics, there are now specialized in manufacturing mold, the product supporting mold factory workshop (factory) near 17 000, about 600 000 employees, annual output value reached 20 billion yuan mold. However, the existing capacity of the mold and die industry can only meet the demand of 60%, still can not meet the needs of national economic development. At present, the domestic needs of large, sophisticated, complex and long life of the mold also rely mainly on imports. According to customs statistics, in 1997 630 million U.S. dollars worth of imports mold, not including the import of mold together with the equipment; in 1997 only 78 million U.S. dollars export mold. At present the technological level of China Die & Mould Industry and manufacturing capacity, China's national economy in the weak links and bottlenecks constraining sustainable economic development.3.1 Research on the Structure of industrial products moldIn accordance with the division of China Mould Industry Association, China mold is divided into 10 basic categories, which, stamping die and plastic molding two categories accounted for the main part. Calculated by output, present, China accounts for about 50% die stamping, plastic molding die about 20%, Wire Drawing Die (Tool) about 10%of the world's advanced industrial countries and regions, the proportion of plastic forming die die general of the total output value 40%.Most of our stamping die mold for the simple, single-process mode and meet the molds, precision die, precision multi-position progressive die is also one of the few, die less than 100 million times the average life of the mold reached 100 million times the maximum life of more than accuracy 3 ~ 5um, more than 50 progressive station, and the international life of the die 600 million times the highest average life of the die 50 million times compared to the mid 80s at the international advanced level.China's plastic molding mold design, production technology started relatively late, the overall level of low. Currently a single cavity, a simple mold cavity 70%, and still dominant. A sophisticated multi-cavity mold plastic injection mold, plastic injection mold has been able to multi-color preliminary design and manufacturing. Mould is about 80 million times the average life span is about, the main difference is the large deformation of mold components, excess burr side of a large, poor surface quality, erosion and corrosion serious mold cavity, the mold cavity exhaust poor and vulnerable such as, injection mold 5um accuracy has reached below the highest life expectancy has exceeded 20 million times, the number has more than 100 chamber cavity, reaching the mid 80s to early 90s the international advanced level.3.2 mold Present Status of TechnologyTechnical level of China's mold industry currently uneven, with wide disparities. Generally speaking, with the developed industrial countries, Hong Kong and Taiwan advanced level, there is a large gap.The use of CAD / CAM / CAE / CAPP and other technical design and manufacture molds, both wide application, or technical level, there is a big gap between both. In the application of CAD technology design molds, only about 10% of the mold used in the design of CAD, aside from drawing board still has a long way to go; in the application of CAE design and analysis of mold calculation, it was just started, most of the game is stillin trial stages and animation; in the application of CAM technology manufacturing molds, first, the lack of advanced manufacturing equipment, and second, the existing process equipment (including the last 10 years the introduction of advanced equipment) or computer standard (IBM PC and compatibles, HP workstations, etc.) different, or because of differences in bytes, processing speed differences, differences in resistance to electromagnetic interference, networking is low, only about 5% of the mold manufacturing equipment of recent work in this task; in the application process planning CAPP technology, basically a blank state, based on the need for a lot of standardization work; in the mold common technology, such as mold rapid prototyping technology, polishing, electroforming technologies, surface treatment technology aspects of CAD / CAM technology in China has just started. Computer-aided technology, software development, is still at low level, the accumulation of knowledge and experience required. Most of our mold factory, mold processing equipment shop old, long in the length of civilian service, accuracy, low efficiency, still use the ordinary forging, turning, milling, planing, drilling, grinding and processing equipment, mold, heat treatment is still in use salt bath, box-type furnace, operating with the experience of workers, poorly equipped, high energy consumption. Renewal of equipment is slow, technological innovation, technological progress is not much intensity. Although in recent years introduced many advanced mold processing equipment, but are too scattered, or not complete, only about 25% utilization, equipment, some of the advanced functions are not given full play.Lack of technology of high-quality mold design, manufacturing technology and skilled workers, especially the lack of knowledge and breadth, knowledge structure, high levels of compound talents. China's mold industry and technical personnel, only 8% of employees 12%, and the technical personnel and skilled workers and lower the overall skill level. Before 1980, practitioners of technical personnel and skilled workers, the aging of knowledge, knowledge structure can not meet the current needs; and staff employed after 80 years, expertise, experience lack of hands-on ability, not ease, do not want to learn technology. In recent years, the brain drain caused by personnel not onlydecrease the quantity and quality levels, and personnel structure of the emergence of new faults, lean, make mold design, manufacturing difficult to raise the technical level.3.3 mold industry supporting materials, standard parts of present conditionOver the past 10 years, especially the "Eighth Five-Year", the State organization of the ministries have repeatedly Material Research Institute, universities and steel enterprises, research and development of special series of die steel, molds and other mold-specific carbide special tools, auxiliary materials, and some promotion. However, due to the quality is not stable enough, the lack of the necessary test conditions and test data, specifications and varieties less, large molds and special mold steel and specifications are required for the gap. In the steel supply, settlement amount and sporadic users of mass-produced steel supply and demand contradiction, yet to be effectively addressed. In addition, in recent years have foreign steel mold set up sales outlets in China, but poor channels, technical services support the weak and prices are high, foreign exchange settlement system and other factors, promote the use of much current.Mold supporting materials and special techniques in recent years despite the popularization and application, but failed to mature production technology, most still also in the exploratory stage tests, such as die coating technology, surface treatment technology mold, mold guide lubrication technology Die sensing technology and lubrication technology, mold to stress technology, mold and other anti-fatigue and anti-corrosion technology productivity has not yet fully formed, towards commercialization. Some key, important technologies also lack the protection of intellectual property.China's mold standard parts production, the formation of the early 80s only small-scale production, standardization and standard mold parts using the coverage of about 20%, from the market can be assigned to, is just about 30 varieties, and limited to small and medium size. Standard punch, hot runner components and other supplies just thebeginning, mold and parts production and supply channels for poor, poor accuracy and quality.3.4 Die & Mould Industry Structure in Industrial OrganizationChina's mold industry is relatively backward and still could not be called an independent industry. Mold manufacturer in China currently can be divided into four categories: professional mold factory, professional production outside for mold; products factory mold factory or workshop, in order to supply the product works as the main tasks needed to die; die-funded enterprises branch, the organizational model and professional mold factory is similar to small but the main; township mold business, and professional mold factory is similar. Of which the largest number of first-class, mold production accounts for about 70% of total output. China's mold industry, decentralized management system. There are 19 major industry sectors manufacture and use of mold, there is no unified management of the department. Only by China Die & Mould Industry Association, overall planning, focus on research, cross-sectoral, inter-departmental management difficulties are many.Mold is suitable for small and medium enterprises organize production, and our technical transformation investment tilted to large and medium enterprises, small and medium enterprise investment mold can not be guaranteed. Including product factory mold shop, factory, including, after the transformation can not quickly recover its investment, or debt-laden, affecting development.Although most products factory mold shop, factory technical force is strong, good equipment conditions, the production of mold levels higher, but equipment utilization rate.Price has long been China's mold inconsistent with their value, resulting in mold industry "own little economic benefit, social benefit big" phenomenon. "Dry as dry mold mold standard parts, standard parts dry as dry mold with pieces of production. Dry with parts manufactured products than with the mold" of the classof anomalies exist. 4 Die trend4.1 mold CAD / CAE / CAM being integrated, three-dimensional, intelligent and network direction(1) mold software features integratedDie software features of integrated software modules required relatively complete, while the function module using the same data model, in order to achieve Syndicated news management and sharing of information to support the mold design, manufacture, assembly, inspection, testing and production management of the entire process to achieve optimal benefits. Series such as the UK Delcam's software will include a surface / solid geometric modeling, engineering drawing complex geometry, advanced rendering industrial design, plastic mold design expert system, complex physical CAM, artistic design and sculpture automatic programming system, reverse engineering and complex systems physical line measurement systems. A higher degree of integration of the software includes: Pro / ENGINEER, UG and CATIA, etc.. Shanghai Jiaotong University, China with finite element analysis of metal plastic forming systems and Die CAD / CAM systems; Beijing Beihang Haier Software Ltd. CAXA Series software; Jilin Gold Grid Engineering Research Center of the stamping die mold CAD / CAE / CAM systems .(2) mold design, analysis and manufacture of three-dimensionalTwo-dimensional mold of traditional structural design can no longer meet modern technical requirements of production and integration. Mold design, analysis,manufacturing three-dimensional technology, paperless software required to mold a new generation of three-dimensional, intuitive sense to design the mold, using three-dimensional digital model can be easily used in the product structure of CAE analysis, tooling manufacturability evaluation and CNC machining, forming process simulation and information management and sharing. Such as Pro / ENGINEER, UG and CATIA software such as with parametric, feature-based, all relevant characteristics, so that mold concurrent engineering possible. In addition, Cimatran company Moldexpert, Delcam's Ps-mold and Hitachi Shipbuilding of Space-E/mold are professional injection mold 3D design software, interactive 3D cavity, core design, mold base design configuration and typical structure . Australian company Moldflow realistic three-dimensional flow simulation software MoldflowAdvisers been widely praised by users and applications. China Huazhong University of Science have developed similar software HSC3D4.5F and Zhengzhou University, Z-mold software. For manufacturing, knowledge-based intelligent software function is a measure of die important sign of advanced and practical one. Such as injection molding experts Cimatron's software can automatically generate parting direction based parting line and parting surface, generate products corresponding to the core and cavity, implementation of all relevant parts mold, and for automatically generated BOM Form NC drilling process, and can intelligently process parameter setting, calibration and other processing results.(3) mold software applications, networking trendWith the mold in the enterprise competition, cooperation, production and management, globalization, internationalization, and the rapid development of computer hardware and software technology, the Internet has made in the mold industry, virtual design, agile manufacturing technology both necessary and possible. The United States in its "21st Century Manufacturing Enterprise Strategy" that the auto industry by 2006 to achieve agile manufacturing / virtual engineering solutions to automotive development cycle shortened from 40 months to 4 months.4.2 mold testing, processing equipment to the precise, efficient, and multi-direction(1) mold testing equipment more sophisticated, efficientSophisticated, complex, large-scale mold development, testing equipment have become increasingly demanding. Precision Mould precision now reached 2 ~ 3μm, more domestic manufacturers have to use Italy, the United States, Japan and other countries in the high-precision coordinate measuring machine, and with digital scanning. Such as Dongfeng Motor Mould Factory not only has the capacity 3250mm × 3250mm Italian coordinate measuring machine, also has a digital photography optical scanner, the first in the domestic use of digital photography, optical scanning as a means of spatial three-dimensional access to information, enabling the establishment from the measurement of physical → model output of engineering drawings → → the whole process of mold making, reverse engineering a successful technology development and applications. This equipment include: second-generation British Renishaw high-speed scanners (CYCLON SERIES2) can be realized and contact laser probe complementary probe, laser scanner accuracy of 0.05mm, scanning probe contact accuracy of 0.02 mm. Another German company GOM ATOS portable scanners, Japan Roland's PIX-30, PIX-4 desktop scanner and the United Kingdom Taylor Hopson's TALYSCAN150 multi-sensor, respectively Three-dimensional scanner with high speed, low-cost and functional composite and so on.(2) CNC EDMJapan Sodick linear motor servo drive using the company's AQ325L, AQ550LLS-WEDM have driven fast response, transmission and high positioning accuracy, the advantages of small thermal deformation. Switzerland Chanmier company NCEDM with P-E3 adaptive control, PCE energy control and automatic programming expert systems. Others also used the powder mixed EDM machining technology, micro-finishing pulse power and fuzzy control (FC) technologies.(3) high-speed milling machine (HSM)Milling is an important means of cavity mold. The low-temperature high-speed milling with the workpiece, cutting force is small, smooth processing, processing quality, processing efficiency (for the general milling process 5 to 10 times) and can process hard materials (<60HRC) and many other advantages. Thus in the mold processing more and more attention. Ruishikelang company UCP710-type five-axis machining center, machine tool positioning accuracy up to 8μm, home-made closed-loop vector control spindle with a maximum speed 42000r/min. Italy RAMBAUDI's high-speed milling, the processing range of up to 2500mm ×5000mm ×1800mm, speed up 20500r/min, cutting feed speed of 20m/min. HSM generally used large, medium-sized mold, such as motor cover mold, die casting mold, large plastic surface machining, the surface precision up to 0.01mm.4. 3 rapid economic modeling techniquesShorten the product development cycle is an effective means of market competition to win one. Compared with the traditional mold process, fast economic modeling technology is a short molding cycle, the characteristics of low cost, precision, and life can meet the production needs, overall economic efficiency is more significant in the mold manufacturing technology, specifically the following main technology.(1) rapid prototyping and manufacturing (RPM). It consists of three-dimensional laser lithography (SLA); laminated profile manufacturing (LOM); laser powder sintering prototyping (SLS); Fused Deposition Molding (FDM) and three-dimensional printing forming technology (3D-P) and so on.(2) the surface forming tooling. It refers to the use of spray, chemical corrosion, electroforming and new method for the formation of the cavity surface and a fine pattern technology.(3) Casting forming tooling. There are bismuth tin alloy tooling, zinc alloy tooling, resin composite forming technology and silicon rubber mold molding technology.(4) cold extrusion mold technology and ultra-molded shapes.(5) multi-point forming technology.(6) KEVRON steel blanking blanking tooling.(7) mold blank rapid manufacturing technology. Mainly dry sand Mold Casting, Vacuum Mold Casting, Resin Sand Mold Casting Lost Wax Casting, and other technologies.(8) Other aspects of technology. Such as the use of nitrogen gas spring pressure side, discharge, quick die technology, stamping unit technology, and cutting edge technology and solid surfacing edge inserts die casting technology.4.4 mold materials and surface treatment technology developed rapidlyIndustry to the level of mold, material application is the key. Due to improper selection and use of materials, causing premature die failure, which accounts for more than 45% failure die. In the mold material, commonly used cold work tool steel with CrWMn, Cr12, Cr12MoV and W6Mo5Cr4V2, flame hardened steel (such as Japan, AUX2, SX105V (7CrSiMnMoV), etc.; used a new type of hot work die steel American H13, Sweden QRO80M, QRO90SUPREME, etc.; used a pre-hardened plastic mold steel (such as the U.S. P20), age-hardening steel (such as the U.S. P21, Japan NAK55, etc.), heat treatment hardened steel (such as the United States, D2, Japan, PD613, PD555, Sweden wins the White 136, etc.), powder die steel (such as Japan KAD18 and KAS440), etc.; panel drawing die used HT300, QT60-2, Mo-Cr, Mo-V cast iron, large-scale mold with HT250. more regular use of Precision Die Hard Steel Results YG20 and other alloys and carbide. in the mold surface treatment, the main trends are: the infiltration of a single element to the multi-element penetration, complex permeability (such as TD method) development; by the general diffusion to the CVD, PVD, PCVD, ion penetration , the direction of ion implantation, etc.; can use the coating are: TiC, TiN, TiCN, TiAlN, CrN, Cr7C3, W2C, etc., while heat from the air treatment means to the development of vacuum heat treatment. In addition, the current strengthening of the laser, glow plasma。
模具实用英语塑料模具
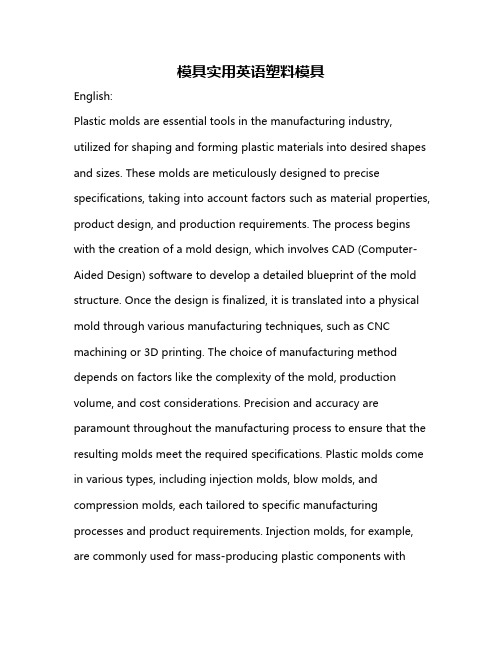
模具实用英语塑料模具English:Plastic molds are essential tools in the manufacturing industry, utilized for shaping and forming plastic materials into desired shapes and sizes. These molds are meticulously designed to precise specifications, taking into account factors such as material properties, product design, and production requirements. The process begins with the creation of a mold design, which involves CAD (Computer-Aided Design) software to develop a detailed blueprint of the mold structure. Once the design is finalized, it is translated into a physical mold through various manufacturing techniques, such as CNC machining or 3D printing. The choice of manufacturing method depends on factors like the complexity of the mold, production volume, and cost considerations. Precision and accuracy are paramount throughout the manufacturing process to ensure that the resulting molds meet the required specifications. Plastic molds come in various types, including injection molds, blow molds, and compression molds, each tailored to specific manufacturing processes and product requirements. Injection molds, for example, are commonly used for mass-producing plastic components withintricate geometries, while blow molds are preferred for hollow plastic products like bottles and containers. Compression molds, on the other hand, are suitable for molding thermosetting plastics into precise shapes. Overall, plastic molds play a crucial role in enabling efficient and cost-effective manufacturing processes across diverse industries, from automotive and electronics to consumer goods and packaging.中文翻译:塑料模具是制造业中不可或缺的工具,用于将塑料材料成型成所需的形状和尺寸。
模具各零部件名称中英文对照
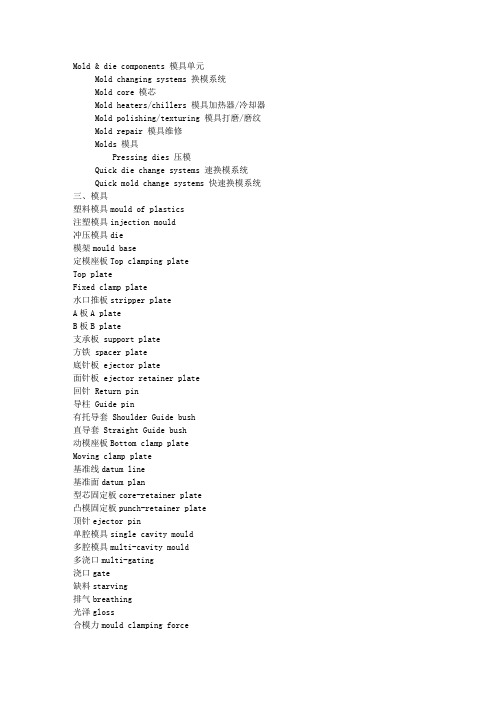
Mold & die components 模具单元Mold changing systems 换模系统Mold core 模芯Mold heaters/chillers 模具加热器/冷却器 Mold polishing/texturing 模具打磨/磨纹 Mold repair 模具维修Molds 模具Pressing dies 压模Quick die change systems 速换模系统Quick mold change systems 快速换模系统三、模具塑料模具mould of plastics注塑模具injection mould冲压模具die模架mould base定模座板Top clamping plateTop plateFixed clamp plate水口推板stripper plateA板A plateB板B plate支承板 support plate方铁 spacer plate底针板 ejector plate面针板 ejector retainer plate回针 Return pin导柱 Guide pin有托导套 Shoulder Guide bush直导套 Straight Guide bush动模座板Bottom clamp plateMoving clamp plate基准线datum line基准面datum plan型芯固定板core-retainer plate凸模固定板punch-retainer plate顶针ejector pin单腔模具single cavity mould多腔模具multi-cavity mould多浇口multi-gating浇口gate缺料starving排气breathing光泽gloss合模力mould clamping force锁模力mould locking force挤出extrusion开裂crack循环时间cycle time老化aging螺杆screw麻点pit嵌件insert活动镶件movable insert起垩chalking浇注系统feed system主流道 sprue分流道runner浇口gate直浇口direct gate , sprue gate轮辐浇口spoke gate , spider gate点浇口pin-point gate测浇口edge gate潜伏浇口submarine gate , tunnel gate 料穴cold-slug well浇口套sprue bush流道板runner plate排飞槽vent分型线(面)parting line定模stationary mould,Fixed mould动模movable mould, movable half上模upper mould, upper half下模lower mould, lower half型腔cavity凹模cavity plate,cavity block拼块split定位销dowel定位销孔dowel hole型芯core斜销angle pin, finger cam滑块slide滑块导板slide guide strip楔紧块heel block, wedge lock拉料杆sprue puller定位环locating ring冷却通cooling channel脱模斜度draft滑动型芯slide core螺纹型芯threaded core热流道模具hot-runner mould绝热流道模insulated runner mould熔合纹weld line (flow line)三板式模具three plate mould脱模ejection换模腔模具 interchangeable cavity mould脱模剂release agent注射能力shot capacity注射速率injection rate注射压力injection pressure差色剂colorant保压时间holdup time闭模时间closing time定型装置sizing system阴模female mould,cavity block阳模male mould电加工设备Electron Discharge Machining数控加工中心CNC machine center万能铁床Universal milling machine卧式刨床Horizontal planer车床Engine lathe平面磨床Surface grinding machine去磁机Demagnetization machine万能摇臂钻床Universal radial movable driller 立式钻床Vertical driller超声波清洗机Ultrasonic clearing machine compre sion molding压缩成型flash mold溢流式模具plsitive mold挤压式模具split mold分割式模具cavity型控母模core模心公模taper锥拔leather cloak仿皮革shiver饰纹flow mark流痕welding mark溶合痕post screw insert螺纹套筒埋值self tapping screw自攻螺丝striper plate脱料板piston活塞cylinder汽缸套chip细碎物handle mold手持式模具(移转成型用模具)encapsulation molding低压封装成型(射出成型用模具)two plate两极式(模具)well type蓄料井insulated runner绝缘浇道方式hot runner热浇道runner plat浇道模块valve gate阀门浇口band heater环带状的电热器spindle阀针spear head刨尖头slag well冷料井cold slag冷料渣air vent排气道welding line熔合痕eject pin顶出针knock pin顶出销return pin回位销反顶针sleave套筒stripper plate脱料板insert core放置入子runner stripper plate浇道脱料板guide pin导销eject rod (bar)(成型机)顶业捧subzero深冷处理three plate三极式模具runner system浇道系统stress crack应力电裂orientation定向sprue gate射料浇口,直浇口nozzle射嘴sprue lock pin料头钩销(拉料杆) slag well冷料井side gate侧浇口edge gate侧缘浇口tab gate搭接浇口film gate薄膜浇口flash gate闸门浇口slit gate缝隙浇口fan gate扇形浇口dish gate因盘形浇口diaphragm gate隔膜浇口ring gate环形浇口subarine gate潜入式浇口tunnel gate隧道式浇口pin gate针点浇口Runner less无浇道(sprue less)无射料管方式long nozzle延长喷嘴方式sprue浇口;溶渣根据中文词汇查所关心的技术问题,解决实际工作中的难题例如,在汉语词汇中看到——高速冲孔废料上跳(かす上り、scrap jump )词汇,到网上一搜,中图分类号TG382.6,文章编码:1671-3508-2008-10-07-517,“高速冲压中防止冲孔废料上跳的方法”一文会告诉你引起高速冲孔废料上跳的原因,不外乎有油膜粘连、真空吸附、刃口磨损、磁性未退四个主要方面,解决这些问题有三个方向的思路可以考虑,具体手段有“毛糙面”法、“斜刀口”法、“硅胶顶出”法、“凹模刃口倒退拔”法,等等。
模具塑料英语
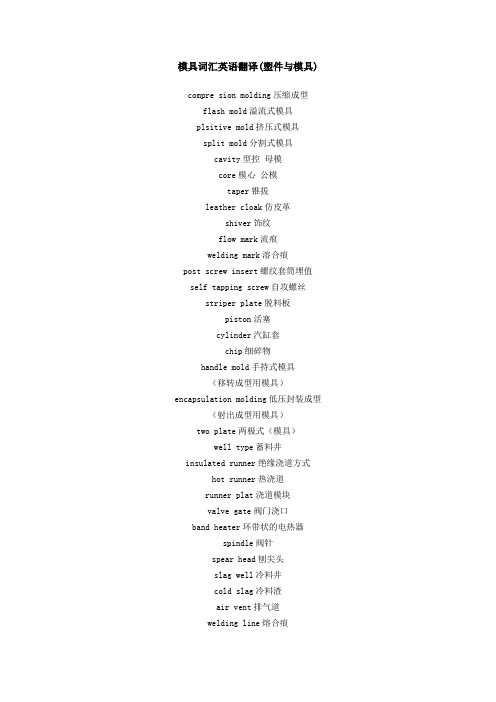
模具词汇英语翻译(塑件与模具)compre sion molding压缩成型flash mold溢流式模具plsitive mold挤压式模具split mold分割式模具cavity型控母模core模心公模taper锥拔leather cloak仿皮革shiver饰纹flow mark流痕welding mark溶合痕post screw insert螺纹套筒埋值self tapping screw自攻螺丝striper plate脱料板piston活塞cylinder汽缸套chip细碎物handle mold手持式模具(移转成型用模具)encapsulation molding低压封装成型(射出成型用模具)two plate两极式(模具)well type蓄料井insulated runner绝缘浇道方式hot runner热浇道runner plat浇道模块valve gate阀门浇口band heater环带状的电热器spindle阀针spear head刨尖头slag well冷料井cold slag冷料渣air vent排气道welding line熔合痕eject pin顶出针knock pin顶出销return pin回位销反顶针sleave套筒stripper plate脱料板insert core放置入子runner stripper plate浇道脱料板guide pin导销eject rod (bar)(成型机)顶业捧subzero深冷处理three plate三极式模具runner system浇道系统stress crack应力电裂orientation定向sprue gate射料浇口,直浇口nozzle射嘴sprue lock pin料头钩销(拉料杆) slag well冷料井side gate侧浇口edge gate侧缘浇口tab gate搭接浇口film gate薄膜浇口flash gate闸门浇口slit gate缝隙浇口fan gate扇形浇口dish gate因盘形浇口diaphragm gate隔膜浇口ring gate环形浇口subarine gate潜入式浇口tunnel gate隧道式浇口pin gate针点浇口Runner less无浇道(sprue less)无射料管方式long nozzle延长喷嘴方式sprue浇口;溶渣。
塑胶模具中英文对照表格

塑胶模具中英文对照表格全文共四篇示例,供您参考第一篇示例:| 中文| 英文||--------------|----------------------|| 塑胶模具| Plastic mold || 注塑模具| Injection mold || 压铸模具| Die-casting mold || 挤出模具| Extrusion mold || 压延模具| Calendering mold || 吹塑模具| Blow molding mold || 压缩成型模具| Compression mold || 热压模具| Hot pressing mold || 橡胶模具| Rubber mold || 泡沫模具| Foam mold || 旋转模具| Rotational mold || 热流道模具| Hot runner mold || 冷流道模具| Cold runner mold || 多腔模具| Multi-cavity mold || 单腔模具| Single-cavity mold || 涡流模具| Vortex mold || 滚筒模具| Roller mold || 注塑机| Injection molding machine | | 压铸机| Die-casting machine || 吹塑机| Blow molding machine || 挤出机| Extrusion machine || 压延机| Calendering machine || 注塑料| Injection molding material | | 塑胶注射| Plastic injection || 模具设计| Mold design || 模具制造| Mold manufacturing || 模具加工| Mold processing || 模具试模| Mold trial || 模具保养| Mold maintenance || 模具寿命| Mold life || 模具材料| Mold material || 模具制造商| Mold manufacturer |以上是关于塑胶模具中英文对照表格的内容,希望对您有所帮助。
塑料模具专业英文名词解释

塑料模具专业英文名词解释Plastic mold, also known as plastic mold, is a toolthat is used to shape, size, and finish plastic materials during the injection molding process. It is an essential component of the plastic molding industry, allowing manufacturers to produce a wide range of plastic parts and components for various applications.Here is a detailed explanation of some common plastic mold terminologies:1. Mold Base: It is the foundation of the mold, providing support and alignment for other mold components. It typically consists of two plates: the top clamping plate and the bottom clamping plate.2. Cavity and Core: The cavity is the negative impression of the desired part shape in the mold, while the core is the insert that forms the internal features of the part. Together, they define the external and internalgeometry of the final part.3. Ejector System: This system is responsible for ejecting the molded part from the mold cavity after the molding process is complete. It typically consists ofejector pins, ejector sleeves, and ejector plates.4. Gating System: It is the system that directs the plastic material into the mold cavity. The design of the gating system affects the flow of plastic, filling pattern, and the overall quality of the molded part.5. Cooling System: This system consists of channels or holes within the mold that allow cooling fluid to circulate, controlling the temperature of the mold and the plastic material. Effective cooling is essential for achieving consistent part quality and minimizing cycle time.6. Runner and Sprue: The runner is the channel that carries the plastic material from the injection machine to the mold cavity, while the sprue is the initial point where the plastic enters the mold.7. Mold Plates: These are the main structural components of the mold that hold all other components in place. They are typically made of high-quality steel andare precision-machined to ensure accurate part dimensions.8. Slides and Lifters: Slides and lifters are mechanical devices used to create undercuts or overhangs in the molded part. They allow for the movement of certainmold components during the molding process.9. Ejector Pins: These are small, precision-machined pins that are used to eject the molded part from the mold cavity. They are typically made of hardened steel and are precision-placed to avoid damaging the part.10. Clamping System: This system is responsible for holding the mold halves together during the molding process. It typically consists of clamping plates, tie bars, and hydraulic or pneumatic clamping devices.In conclusion, plastic mold terminology covers a widerange of specialized concepts and components. Understanding these terms is crucial for anyone working in the plastic molding industry, as it helps them to communicate effectively, design and fabricate molds efficiently, and produce high-quality molded parts consistently.。
塑料模具 英文翻译原文
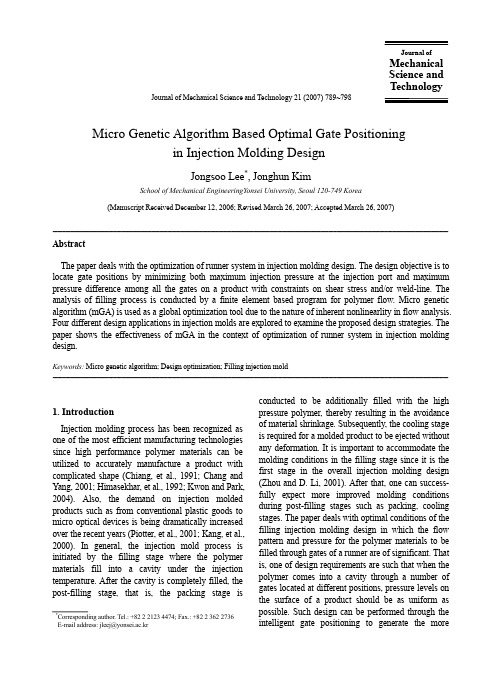
GJournal of Mechanical Science and Technology 21 (2007) 789~798Micro Genetic Algorithm Based Optimal Gate Positioningin Injection Molding DesignJongsoo Lee*, Jonghun KimSchool of Mechanical EngineeringYonsei University, Seoul 120-749 Korea(Manuscript Received December 12, 2006; Revised March 26, 2007; Accepted March 26, 2007)--------------------------------------------------------------------------------------------------------------------------------------------------------------------------------------------------------------------------------------------------------AbstractThe paper deals with the optimization of runner system in injection molding design. The design objective is to locate gate positions by minimizing both maximum injection pressure at the injection port and maximum pressure difference among all the gates on a product with constraints on shear stress and/or weld-line. The analysis of filling process is conducted by a finite element based program for polymer flow. Micro genetic algorithm (mGA) is used as a global optimization tool due to the nature of inherent nonlinearlity in flow analysis. Four different design applications in injection molds are explored to examine the proposed design strategies. The paper shows the effectiveness of mGA in the context of optimization of runner system in injection molding design.GKeywords: Micro genetic algorithm; Design optimization; Filling injection mold--------------------------------------------------------------------------------------------------------------------------------------------------------------------------------------------------------------------------------------------------------1. IntroductionInjection molding process has been recognized as one of the most efficient manufacturing technologies since high performance polymer materials can be utilized to accurately manufacture a product with complicated shape (Chiang, et al., 1991; Chang and Yang, 2001; Himasekhar, et al., 1992; Kwon and Park, 2004). Also, the demand on injection molded products such as from conventional plastic goods to micro optical devices is being dramatically increased over the recent years (Piotter, et al., 2001; Kang, et al., 2000). In general, the injection mold process is initiated by the filling stage where the polymer materials fill into a cavity under the injection temperature. After the cavity is completely filled, the post-filling stage, that is, the packing stage is conducted to be additionally filled with the high pressure polymer, thereby resulting in the avoidance of material shrinkage. Subsequently, the cooling stage is required for a molded product to be ejected without any deformation. It is important to accommodate the molding conditions in the filling stage since it is the first stage in the overall injection molding design (Zhou and D. Li, 2001). After that, one can success-fully expect more improved molding conditions during post-filling stages such as packing, cooling stages. The paper deals with optimal conditions of the filling injection molding design in which the flow pattern and pressure for the polymer materials to be filled through gates of a runner are of significant. That is, one of design requirements are such that when the polymer comes into a cavity through a number of gates located at different positions, pressure levels on the surface of a product should be as uniform as possible. Such design can be performed through the intelligent gate positioning to generate the moreCorresponding author. Tel.: +82 2 2123 4474; Fax.: +82 2 362 2736 E-mail address: jleej@yonsei.ac.kr790 Jongsoo Lee and Jonghun Kim / Journal of Mechanical Science and Technology 21(2007) 740~749uniform distribution of injection pressure over the product surface.There have been a number of studies of optimal gate location in the context of CAE filling injection molding design problems where various kinds of optimizer have been employed to conduct design optimization (Kim et al., 1996; Young, 1994; Pan-delidis and Zou, 2004; Lin, 2001; Li and Shen, 1995). The paper explores the design of injection mold system using micro genetic algorithm (mGA). Ge-netic algorithm (conventional GA) is based on the Darwin’s theory of the survival of the fittest, and adopts the concept of natural evolution; the competitive designs with more fit are survived by selection, and the new designs are created by crossover and mutation (Lee, 1996; Lee and Hajela, 1996). A conventional GA works with a multiple number of designs in a population. Handling with such designs results in increasing a higher probability of locating a global optimum as well as multiple local optima. GA is also advantageous when the design problem is represented by a mixture of integer/dis-crete and continuous design variables. Nevertheless, it requires expensive computational costs especially when combining with finite element based CAE analysis tools. A conventional GA determines the population size depending upon the stringlength of a chromosome that is a coded value of a set of design variables. The main difference between a conven-tional GA and mGA resides on the population size. The population size in mGA is based on Goldberg’s concept such that ‘Evolution process is possible with small populations to reduce the cost of fitness function evaluation’ (Goldberg, 1988). This implies that mGA employs a few number of populations for GA evolution regardless of the number of design variables and the complexity of design parameters (Krishnakumar, 1989; Dennis and Dulikravich, 2001). The paper discusses the design requirements of filling injection mold optimization to construct the proper objective functions and design constraints. Four different design applications in injection molds are explored to examine the proposed design strategies. The paper shows the effectiveness of mGA in the context of optimization of runner system in injection molding design.2.Mold flow analysisThe flow of a polymer in injection molding process obeys the following governing equations:22()()0p pS Sx x y yw w w ww w w w(1)222()p x yT T T TC kt x y zU Q Q KJw w w ww w w w(2)where,2'2'h zS dzK³.In the above equations, p is a flow pressure, T is atemperature of polymer, and t is denoted as time.Parameters K,J, and k are viscosity, shear rate andthermal conductivity, respectively (Lee, 2003). It isassumed that polymer is a non-compaction substancein the filling analysis. The flow analysis in the presentstudy is conducted by Computer Aided PlasticsApplication (CAPA) (Koo, 2003), a finite elementbased commercial code for polymer flow of injectionmolding.The runner system in injection mold covers thepassage of molten polymer from injection port togates. The present study develops two different runnersystems where a cold system requires the change inpolymer temperature, and a hot system keep itunchanged while the flow passes through the runner.For the hot runner system has a geometricallyconsistent thickness due to the constant temperatureas shown in Fig. 1a. However, the CAE result of acold runner system depends on the thickness and shapeTable 1. Ten-bar truss design results.micro GA conventional GACase 1Case 2Case 3Case 1 Case 2 Case 3Reference[20]X17.868.157.858.15 7.30 7.81 7.90X20.410.180.190.10 0.83 0.45 0.10X38.387.998.158.20 8.77 8.37 8.10X4 5.05 3.83 3.89 3.97 3.27 4.16 3.90X50.120.960.15 1.10 0.75 0.55 0.10X60.410.250.250.10 0.82 0.30 0.10X7 6.41 5.67 5.87 5.84 6.74 6.30 5.80X8 5.23 6.29 5.52 5.68 5.06 5.26 5.51X9 3.83 3.85 5.05 5.07 2.89 3.86 3.68OptimalareaX100.500.250.250.40 1.16 0.42 0.14Optimalweight1599158715881593 1590 1585 1499# of functionevaluations57540542302533578894 69497 73533Jongsoo Lee and Jonghun Kim / Journal of Mechanical Science and Technology 21(2007) 789~798 791(a) Hot runner system(b) Cold runner systemFig. 1. Modeling of runner system.shape of a runner. The typical illustration of the geometric model in a cold runner system is shown in Fig.1b where the runner thickness is changed according to the temperature gradient.3. Molding design requirements3.1 Objective functionsOne of the most significant factors considered in the injection molding design is a flow pattern, which implies that a balanced flow should be maintained while a polymer arrives at each part of a design product. Once the improvement on flow balance is obtained, the flow of molten polymer smoothes and the maximum injection pressure is decreased with the same or at least evenly distributed injection pressure level at each gate. In a case where the certain part of a product within the mold is filled up earlier than other parts, each part would fall into over-packing and under-packing situations during the filling process of a polymer into mold. Such problem further evokes a malformation like twisting and bending, resulting from the difference in contraction rate during the course of cooling-off.The difference in pressure triggers the flow ofpolymer during the filling process, in which themaximum injection pressure is detected at theinjection port of polymer. The polymer always flowsfrom high-pressure region to low-pressure one. Whena flow pattern improves, the flow of polymer getssmoother with the maximum injection pressure decreased. However, the flow instability sometimeshappens, thereby requiring a higher pressure to fill up.That is, the maximum injection pressure needs to bereduced in order to improve the flow instability. Thepressure gap (i.e., the highest and lowest pressurevalues) among all of gates is also taken as anotherobjective function to determine whether the wholemold is being filled at once.Most commonly accepted design strategy toimprove the flow pattern is the adjustment of gatelocation. The present study controls the flow patternby developing the optimal gate positioning problemswith proper objective function(s) and design cons-traints. Objective functions for injection moldingdesign are considered as both ‘maximum injection pressure’ (MIP) and ‘maximum pressure difference’ (MPD). It should be noted that the maximuminjection pressure is calculated at the injection portand the maximum pressure difference is a numericaldifference between the highest and lowest values ofpressure among all of gates. The aforementioned statements could be interpreted as a multiobjectivedesign problem, hence the present study simplyemploys a weighting method as follows:**()()()MIP x MPD xF xMIP MPDD E(3)where, D and E are weighting factors as D+E=1, and xis a set of design variables which are Cartesian coordinates of gates on a product. Each component inthe above equation is normalized by optimal single-objective function value, (i.e., MIP*, MPD*). It ismentioned that the number of gates is considered as aproblem parameter in the study.3.1 ConstraintsWeld-lines are easily detected when more than twoflow fronts having different temperature values meetduring the filling process. The weld-line is one of theweakest points in molded product; it is very792 Jongsoo Lee and Jonghun Kim / Journal of Mechanical Science and Technology 21(2007) 740~749vulnerable to a shock and subsequently causes external defects of a very glossy polymer. The weld-line should be moved into a less weak region by adjusting the width of a product, the size and/or shape of gates and runners, and the position of gates, etc. The present study considers the position of a weld-line as a constraint in optimal gate positioning of mold design. Once a designer specifies areas where weld-lines should not be generated, all of the finite element nodes in such areas are constrained not to form the weld-lines.Shear stress is defined as a shear force imposed on the wall of a mold by the shear flow of a polymer. The magnitude of shear stress is proportional to the pressure gradient of each position. In general, the shear stress is zero at the center of a molded product, and reaches a maximum value on the wall. High shear stress triggers the molecule cultivation on the surface of a molded product. Flow instability such as melt fracture has a close relationship with the shear stress. The clear surface of a molded product can be obtained by reducing the magnitude of shear stress. That is, shear stress should be minimized during the mold filling process in order to improve the quality of a molded product, particularly on its surface. Maximum allowable shear stress depends on the kinds of polymer, and is generally taken as 1% of tensile strength of a polymer. Shear stress affecting the quality of end product is considered as another constraint.3.3 Formulation of optimization problemThe statement of a mold design optimization problem can be written as follows: Find12(,,){(,,),(,,),...,(,,)}N x i j k x i j k x i j k x i j k (4)to minimize**()()()MIP x MPD x F x MIP MPD D E (5) subject to shear stress(i, j, k) < shear stress allowable (6) weld-line(i, j, k) = designated area(s) only (7) where, lower upper x x x d d A set of design variables, x are Cartesian coordi-nates (i, j, k) of gates on the surface of a molded product, where N is the number of gates. A traditionalweighted-sum method in the context of multiob-jective optimization is employed by using two wei-Fig. 2. Micro GA process.ghting factors of D and E , where D +E =1. Multi-objective functions considered in the present study are ‘maximum injection pressure (MIP)’ measured at the injection port and ‘maximum pressure difference (PD)’ among all of gates. The constants, MIP* and MPD* are optimal objective function values obtained via single-objective optimization. The permission of weld-lines to designated areas only and the upper limits on shear stress are imposed as design cons-traints. The flow pattern analysis is performed by CAPA as mentioned in the earlier section, and the optimization is conducted through mGA. It should be noted that Cartesian coordinates (i, j, k) is recognized as nodal points when a molded product is discretized by finite elements in CAPA.4. Micro GAThe overall process of mGA in the present study is depicted in Fig. 2, and a stepwise procedure can be explained as follows:Step-1) Generate an initial population at random. The recommended population size is 3, 5, or 7.Step-2) Perform a conventional GA evolution untilthe nominal convergence is satisfied. In the presentstudy, the population size is selected as 5, and atournament selection operator is used. The crossoverprobability in mGA is 1.0 due to the small size in population, while a conventional GA is preferred to use it less than 1.0. The nominal convergence means that the difference of 1’s and/or 0’s among stringpositions is within 5% out of the stringlength, thereby resulting in the convergence to a local solution.Step-3) During the user-specified number of ge-nerations, a new population is updated; one individual is selected by elitism; the remaining individuals in aJongsoo Lee and Jonghun Kim / Journal of Mechanical Science and Technology 21(2007) 789~798 793new population are generated at random. It should benoted that the selection operation adopts ‘tournament’ for activating the diversity and ‘elitism’ for keeping the best solution. Since the updated populations except for the elitism are generated at random, mGA seldom considers the mutation.Fig. 3. Convergence histories of ten-bar truss problem.GFig. 4. Seven discrete design spaces for vehicle dashboard problem.Fig. 5. Initial gate location of vehicle dashboard.In summary, mGA enables to locate an optimal solution thanks to the small size of populations, tournament and elitism operations in selection, and the full participation in crossover. However, mGA has a drawback upon finding one of multiple local optima only due to the small size of populations and the nominal convergence strategy. A conventional GA is superior to maintaining the diversity while mGA is advantageous of savings in computational resource requirements.4.1 Truss designThe proposed mGA is verified by a typical ten-bar planar truss optimization problem. The objective is to find optimal cross-sectional areas by minimizing the structural weight subjected to stress constraints (Haftka and Gurdal, 1993). Optimal solutions are obtained via mGA and a conventional GA to compare with each other. The population size in mGA is 5, while a conventional GA requires 250 individuals in a population since the stringlength in this problem is 100. Crossover and mutation probabilities in a con-ventional GA used are 0.8 and 0.01, respectively. After two genetic search methods are conducted ten times by changing randomly generated initial popul-ations, the most fit design results are demonstrated in Table 1. The convergence history for each optimizer demonstrates that mGA produces the better design and locates the near-optimal solution at the earlier stage of evolution in Fig. 3.5. Results of design applications5.1 V ehicle dashboardA passenger car in-panel has been first examined. This model is supposed to have 7 gates, and design spaces for use in genetic evolution are shown in Fig. 4. Objective functions of MIP and MPD are taken into account, but no constraints are imposed in this model. The initial design is shown in Fig. 5; this design has been obtained through experience and trial-and-errors in an automotive part molding company. Optimized results by mGA are shown in Figs. 6 to 8, whose objective functions were considered as ‘MIP only’, ‘MPD only’ and ‘both MIP and MPD’, respectively. Design results for each case are summarized in Table 2 as well. It is noted that ‘both MIP and MPD’ is calculated with D changing from 0.0 to 1.0 with an increment of 0.1 while keeping D E .0.794 Jongsoo Lee and Jonghun Kim / Journal of Mechanical Science and Technology 21(2007) 740~749Fig. 6. Optimized design of vehicle dashboard (MIP only).Fig. 7. Optimized design of vehicle dashboard (MPD only).Fig. 8. Optimized design of vehicle dashboard (both MIP and MPD).In case of ‘MIP only’ in Fig. 6, the maximum injection pressure value has an improvement of 23.9% compared with an initial model, but the pressure distribution on the product becomes worse, resulting in over-packing on the left region. When a case of ‘MPD only’ is considered, the design performance in Fig. 7 is achieved in terms of not only maximum pressure difference but also maximum injection pressure as shown. It is expected that the flow gets smoother during the improvement of pressure distribution, and the maximum injection pressure is decreased as well. In case of ‘both MIP and MPD’ in Fig. 8, its result is quite similar to a case Table 2. Optimization results of vehicle dashboard.maximum pressure[MPa]maximumdifference [MPa] Initial design 242.69 20.26MIP only184.73 35.08MPD only231.22 12.44objectiveboth MIPand MPD229.92 12.58Table 3. Optimization results of TV monitor.maximumpressure[MPa]maximumdifference[MPa]shear stress <0.5 [MPa]Initial design 80.55 13.71 0.45MIP only68.46 4.06 0.43MPD only72.27 3.04 0.45 objectiveboth MIPand MPD68.46 4.06 0.43of ‘MPD only’ in terms of gate locations from Figs. 7 and 8 and the percentile improvement in Table 2. A weighted-sum method is used to obtain the mul-tiobjective optimal solutions by changing D andE simultaneously, but yields the same results out of a total of 11 weighting factor based trials. The reason why a few number of Pareto solutions are detected is such that the maximum pressure is not counter to pressure distribution in the filling injection molding.In other words, when the overall pressure distributionis improved thanks to the enhancement of flow balance and the smoothness of polymer flow, the maximum pressure is consequently decreased. As faras the pressure distribution of a modeled product is concerned, the change in gate position is noticeable; Gate_5 of optimized models moves from right to left region compared with an initial model.5.2 TV monitorThe model of a TV monitor equipped with 4 gatesis now optimized using objective functions and the upper limit on shear stress constraint, where the shear stress allowable is 0.5MPa. The initial design with 4 discrete design spaces is displayed in Fig. 9, and optimized pressure distributions are shown in Figs. 10 and 11. Design results for single-objective and mul-tiobjective optimization are tabulated in Table 3. In case of ‘MIP only’ generates the same result as weighting method based multiobjective solutions of‘both MIP and MPD’. In case of ‘MPD only, the maxi-Jongsoo Lee and Jonghun Kim / Journal of Mechanical Science and Technology 21(2007) 789~798 795Fig. 9. Initial gate location of TV monitor.Fig. 10. Optimized design of TV monitor (MPD only).Fig. 11. Optimized design of TV monitor (MIP only & both MIP and MPD).mum injection pressure and maximum pressure di-fference have been improved by 10.3% and 77.8%, respectively. It is expected that the enhancement on flow balance and smoothness may be made possible by optimizing the gate positions.5.3 CD trayThe CD tray use in a laptop computer has 4 gates for injection molding. The optimization on this modelFig. 12. CD tray (left) and its initial gate location (right).Fig. 13. Optimized design of CD tray (MIP only).Fig. 14. Optimized design of CD tray (MPD only).is conducted with a shear stress constraint, where the upper limit on shear stress allowable is 1.5MPa. Initial and optimized results for pressure distribution are shown in Figs. 12 to 15. From the summary of Table 4, the design solutions of optimal objective fun-796 Jongsoo Lee and Jonghun Kim / Journal of Mechanical Science and Technology 21(2007) 740~749Fig. 15. Optimized design of CD tray (both MIP and MPD).Table 4. Optimization results of CD tray.maximum pressure [MPa] maximumdifference[MPa]shear stress <1.5 [MPa]Initial design 82.66 1.192 1.22MIP only 73.91 7.085 1.26MPD only 80.44 0.332 1.12 objectiveboth MIPand MPD 78.79 0.376 1.14 ction values in this problem are quite similar to that in the vehicle dashboard. In case of ‘MIP only’, the maximum pressure difference value gets worse than the initial design, even though the maximum injection pressure value has been improved. The cases of ‘MPD only’ and ‘both MIP and MPD’ have turned out that both objective function values are improved. Also, the duplicated multiobjective design solutions are much close to the result obtained by ‘MPD only’, as in the vehicle dashboard design.5. 4 Plug receptacleThis problem employs the weld-line condition as a constraint instead of shear stress. In Fig. 16, the design space for optimally locating 2 gates is re-presented by a dotted region, and the restricted areas against weld-lines are designated by 5 solid regions. Actual mold designers do not locate the weld-line restriction just like this problem. Side or rear parts of a product might be preferred. However, this problem places the disjointed 5 weld-line restriction areas in the front to see how much the proposed design strategy of mGA works in the present study. Opti-mized results of weld-line distribution are shown in Figs. 17 and 18. It is clear to see that all the results areGFig. 17. Weld-line in optimized design of plug receptacle (MPD only).Fig. 18. Weld-line in optimized design of plug receptacle (MIP only & both MIP and MPD).Jongsoo Lee and Jonghun Kim / Journal of Mechanical Science and Technology 21(2007) 789~798 797Table 5. Optimization results of plug receptacle.max pressure [MPa] max difference[MPa] MIP only 160.30 0.51 MPD only 166.47 0.05objective both MIP andMPD160.30 0.51 satisfied with weld-line constraint. The design solu-tions for optimal objective function values are also similar to those of TV monitor. The solutions of ‘MIPonly’ and weighting method based ‘both MIP and MPD’ are the same (see Table 5).6. Concluding remarks The paper examines micro genetic algorithm in the context of engineering design optimization. Micro genetic algorithm is efficient in handling with smallpopulations over a conventional genetic algorithm. The proposed optimization algorithm is applied to filling injection mold design problem. The central of the paper is to locate gate positions by minimizingboth maximum injection pressure at the injection port and maximum pressure difference among all the gateson a product with constraints on shear stress and/or weld-line. Multiobjective design solutions show thatthe enhancement on flow balance and smoothness may be made possible by optimizing the gatepositions. The use of optimized runner systems wouldsubsequently expect to reduce defects such as deformation and twisting that are to be generatedduring the cooling process.Acknowledgments Authors greatly appreciate for the partial support from iDOT, Center of Innovative Design Optimi-zation Technology.References Chang R. Y . and Yang, W. H., 2001, “Numerical Simulation of Mold Filling in Injection Molding Usinga Three-Dimensional Finite V olume Approach,” Inter-national Journal for Numerical Methods in Fluids , V ol.37, Issue 2, pp. 125~148.Chiang, H. H., Hieber C. A., and Wang, K. K., 1991,“A Unified Simulation of the Filling and PostfillingStages in Injection Molding, I: Formulation,” PolymerEngi-neering and Science , V ol. 31, No. 2, pp. 116~124.Dennis, B. H. and Dulikravich, G . S., 2001, “Optimization of Magneto-Hydrodynamic Control ofDiffuser Flows Using Micro-Genetic Algorithms andLeast-Squares Finite Elements,” Finite Elements in Analysis and Design , V ol. 37, No. 5, pp. 349~363.Goldberg, D. E., 1988, “Sizing Populations for Serial and Parallel Genetic Algorithms,” TCGA Report No. 88004, The Clearinghouse for Genetic Algorithms, University of Alabama.Haftka R. T. and Gurdal, Z., 1993, “Elements of Structural Optimization,” Kluwer Academic Publishers,The Netherlands.Himasekhar, K., Lottey J. and Wang, K. K., 1992, “CAE of Mold Cooling in Injection Molding Using aThree-Dimensional Numerical Simulation,” Journal of Engineering for Industry, Transactions of the ASME ,V ol. 114, No. 2, pp. 213~221, 1992.Kang, S., Kim J. S. and Kim, H., 2000, “Bire-fringence Distribution in Magneto-Optical Disk Subs-trate Fabricated by Injection Compression Molding,” Optical Engineering , V ol. 39, Issue 3, pp. 689~694.Kim, S. J., Lee K. and Kim, Y . I., 1996, “Optimization of Injection-Molding Conditions UsingGenetic Algorithm,” proceedings of SPIE , V ol. 2644, pp. 173~180, March.Koo, B., 2003, CAPA User’s Manual V ersion 5.4, Suwon, Korea. (http://www.vmtech.co.kr)Krishnakumar, K.,1989, “Micro Genetic Algorithms for Stationary and Non-Stationary Function Optimi-zation,”Intelligent Control and Adaptive Systems , V ol.1196, pp. 289~296.Kwon T. H. and Park, J. B., 2004, “Finite ElementAnalysis Modeling of Powder Injection Molding Filling Process Including Yield Stress and Slip Phenomena,”Polymer Engineering and Science , V ol. 35, Issue 9, pp. 741~753.Lee J., and Hajela, P ., 1996, “Parallel Genetic Algorithm Implementation in Multidisciplinary Rotor Blade Design,” Journal of Aircraft , V ol. 33, No. 5, pp. 962~969.Lee, J., 1996, “Genetic Algorithms in Multidis-ciplinary Design of Low Vibration Rotors,” Ph. D.Dissertation in Mechanical Engineering, Rensselaer Polytechnic Institute , Troy, NY , May 1996. Lee, J., Kim J. and Jeong, H., 2003, “Optimal Design of Runner Systems in Injection Molding,” proceedings of CAPA User’s Conference, Seoul, Korea. Li C. S., and Shen, Y . K., 1995, “Optimum Design of Runner System Balancing in Injection Molding,”。
模具术语英文翻译

模具术语英文翻译根据国家标准,以下为部分塑料模具成形术语的标准翻译。
动模 Movable Mould Moving Half定模座板 Fixed Clamp Plate Top Clamping Plate Top Plate动模座板 Moving Clamp Plate Bottom Clamping Plate Bottom Plate 上模座板 Upper Clamping Plate下模座板 Lower Clamping Plate凹模固定板 Cavity-retainer Plate型芯固定板 Mould Core-retainer Plate凸模固定板 Punch-retainer Plate模套 Die Body Die Sleeve Die Blank支承板 Backing Plate Support Plate垫块 Spacer Parallel支架 Ejector Housing Mould Base Leg模头 Die Head根据国家标准,以下为部分压铸模具术语的标准翻译。
压力铸造模具 Die-Casting Die压铸模零部件定模 Fixed Die Cover Die定模座板 Fixed Clamping Plate定模套板 Bolster Fixed Die动模 Moving Die Ejector Die动模座板 Moving Clamping Plate直流道 Sprue横流道 Runner内浇口 Gate模具分类Injection Mold 注塑模Plastic Rubber Mould 塑胶模Rubber Molding 橡胶成形Hot Chamber Die Casting 热室压铸Sand Mold Casting 砂模铸造Extrusion Mold 挤出模Multi-Cavity Mold 多模穴模具Stack Mold, Stack Injection Mould 叠层模Plaster Mold 石膏模Three Plates Mold 三板模Plain Die 简易模Pierce Die 冲孔模Forming Die 成型模Progressive Die 连续模Gang Dies 复合模Shearing Die 剪边模Cavity Die 型腔模Riveting Die 铆合模Compression Molding 压缩成型Flash Mold 溢流式模具Extrusion Mold 挤压式模具Split Mold 分割式模具Mould Cavity 型腔母模Mold Core 模芯公模Large Die Mold 大型模具Precise Die Mold 精密模具Complex Die Mold 复杂模具Foaming Mould 发泡模具Metal Die 金属模具Plastic Mold 塑料模具Press Tool Stamping Die Punch Die 冲压模具Extrusion Die 挤压模具Graphite Die 石墨模具流道浇口部分Runner System 浇道系统Sprue Cold Material Trap 浇道冷料井Sprue Puller 拉杆Runner Design 流道设计Main Runner 主流道Secondary Runner 次流道Mould Gate Design 浇口设计Submarine Gate 潜伏浇口Tunnel Gate 隧道式浇口Pinpoint Gate 点浇口Fan Gate 扇形浇口Side Gate 侧浇口Edge Gate 侧缘浇口Tab Gate 搭接浇口Film Gate 薄膜浇口Flash Gate 闸门浇口Slit Gate 缝隙浇口Dish Gate 盘形浇口Diaphragm Gate 隔膜浇口Ring Gate 环形浇口Runnerless 无浇道Sprueless 无射料管方式Long Nozzle 延长喷嘴方式Sprue 浇口,溶渣Insulated Runner Hot Runner 热浇道Runner Plat 浇道模块Valve Gate阀门浇口Slag Well 冷料井Cold Slag 冷料渣Sprue Gate 射料浇口,直浇口Nozzle 射嘴Sprue Lock Pin 料头钩销(拉料杆)注塑缺陷Flash 飞边Warpage 翘曲Air Trap 积风Blush 发赤Flow Line 流痕Splay 银纹Short Shot 短射Sink Mark 缩痕Streak 条纹Void 缩孔Weld Line 熔接线Gas Mark 烧焦Cold Slug 冷斑Delamination 起皮Burr 毛刺Flaw Scratch 刮伤Gloss 光泽Glazing 光滑Surface Check 表面裂痕Hesitation 迟滞注塑工艺Molding Conditions 成型条件Drying 烘干Barrel Temperature 料筒温度Melt Temperature 熔化温度Mold Temperature 模具温度Injection Pressure 注塑压力Back Pressure 背压Injection Speed 注塑速度Screw Speed 螺杆转速Tensile Strength 抗拉强度Tensile Elongation 延伸率Flexural Modulus 弯曲模数Flexural Strength 抗弯强度Shrinkage 收缩率Regrind Usage 次料使用Moulding 模塑机械设备Lathe 车床Planer 刨床Miller Milling Machine 铣床Grinder 磨床Driller 钻床Linear Cutting 线切割Electrical Sparkle 电火花Welder 电焊机Punching Machine 冲床Robot 机械手Common Equipment 常用设备EDM Electron Discharge Machining 放电加工3D Coordinate Measurement 三次元量床Boring Machine 搪孔机Contouring Machine 轮廓锯床Copy Grinding Machine 仿形磨床Cylindrical Grinding Machine 外圆磨床Die Spotting Machine 合模机Engraving Machine 雕刻机Engraving E.D.M 雕模放置加工机Form Grinding Machine 成形磨床, Graphite Machine 石墨加工机Horizontal Boring Machine 卧式搪孔机Horizontal Machine Center 卧式加工制造中心Internal Cylindrical Machine 内圆磨床模具零件Top Plate 上托板(顶板)Top Block 上垫脚Punch Set 上模座Punch Pad 上垫板Punch Holder 上夹板Stripper Pad 脱料背板Up Stripper 上脱料板Male Die 公模(凸模)Feature Die 公母模Female Die 母模(凹模)Upper Mold Plate 上模板Lower Mold Plate 下模板Die Pad 下垫板Die Holder 下夹板Die Set 下模座Bottom Block 下垫脚Bottom Plate下托板(底板)Stripping Plate 内外打(脱料板)Outer Stripper 外脱料板Inner Stripper 内脱料板Lower Stripper 下脱料板Inner Guiding Post 内导柱Inner Hexagon Screw 内六角螺钉Dowel Pin 固定销Mould Coil Spring 模具弹簧Lifter Pin 顶料销Isoheight Sleeve 等高套筒Pin 销Lifter Guide Pin 浮升导料销Guide Pin 导正销Wire Spring 圆线弹簧Outer Guiding Post 外导柱Stop Screw 止付螺丝Located Pin 定位销Outer Bush 外导套Punch 冲头Insert 入块(嵌入件)Deburring Punch 压毛边冲子Groove Punch 压线冲子Stamped Punch 字模冲子Round Punch 圆冲子Special Shape Punch 异形冲子Bending Block 折刀Roller 滚轴Baffle Plate 挡块Located Block 定位块Supporting Block for Location 定位支承块Air Cushion Plate 气垫板Air-Cushion Eject-rod 气垫顶杆Trimming Punch 切边冲子Stiffening Rib Punch Stinger 加强筋冲子Ribbon Punch 压筋冲子Reel-stretch Punch 卷圆压平冲子Guide Plate 定位板Sliding Block 滑块Sliding Dowel Block 滑块固定块Active Plate 活动板Lower Sliding Plate 下滑块板Upper Holder Block 上压块Upper Mid Plate 上中间板Spring Box 弹簧箱Spring-Box Eject-rod 弹簧箱顶杆Spring-Box Eject-Plate 弹簧箱顶板Bushing Block Liner Bushing 衬套Cover Plate 盖板Guide Pad 导料块模具技术用语各种常用模具成形方式Accurate Die Casting 精密压铸Powder Forming 粉末成形Calendaring Molding 压延成形Powder Metal Forging 粉末锻造Cold Chamber Die Casting 冷式压铸Precision Forging 精密锻造Cold Forging 冷锻Press Forging 冲锻Compacting Molding 粉末压出成形Rocking Die Forging 摇动锻造Compound Molding 复合成形Rotary Forging 回转锻造Compression Molding 压缩成形Rotational Molding 离心成形Dip Mold 浸渍成形Rubber Molding 橡胶成形Encapsulation Molding 注入成形Sand Mold Casting 砂模铸造Extrusion Molding 挤出成形Shell Casting 壳模铸造Foam Forming 发泡成形Sinter Forging 烧结锻造Forging Roll 轧锻Six Sides Forging 六面锻造Gravity Casting 重力铸造Slush Molding 凝塑成形Hollow Blow Molding 中空(吹出)成形Squeeze Casting 高压铸造Hot Chamber Die Casting 热室压铸Swaging 挤锻Hot Forging 热锻Transfer Molding 转送成形Injection Molding 射出成形Warm Forging 温锻Investment Casting 精密铸造Matched Die Method 对模成形法Laminating Method 被覆淋膜成形Low Pressure Casting 低压铸造Lost Wax Casting 脱蜡铸造Matched Mould Thermal Forming 对模热成形模Close Mold 合模Demould 脱模脱模剂Mould Unloading 开模Eject 顶出Tool Change Retooling Die Changing 换模Mould Clamping 锁模各式模具分类用语Bismuth Mold 铋铸模Landed Plunger Mold 有肩柱塞式模具Burnishing Die 挤光模Landed Positive Mold 有肩全压式模具Button Die 镶入式圆形凹模Loading Shoe Mold 料套式模具Center-Gated Mold 中心浇口式模具Loose Detail Mold 活零件模具Chill Mold 冷硬用铸模Loose Mold 活动式模具Cold Hobbing 冷挤压制模法Louvering Die 百叶窗冲切模Composite Dies 复合模具Manifold Die 分歧管模具Counter Punch 反凸模Modular Mold 组合模具Double Stack Mold 双层模具Multi-Cavity Mold 多模穴模具Electroformed Mold 电铸成形模Multi-Gate Mold 复式浇口模具Expander Die 扩径模Offset Cold Bending Die 双折冷弯模具Extrusion Die 挤出模Stack Mold, Stack Injection Mould 叠层模Family Mold 反套制品模具Plaster Mold 石膏模Blank Through Dies 漏件式落料模Porous Mold 通气性模具Duplicated Cavity Plate 复板模Positive Mold 全压式模具Fantail Die 扇尾形模具Pressure Die 压紧模Fishtail Die 鱼尾形模具Profile Die 轮廓模Flash Mold 溢料式模具Progressive Die 顺序模Gypsum Mold 石膏铸模Portable Mold 手提式模具Hot-Runner Mold 热流道模具Prototype Mold 雏形试验模具原型模具Ingot Mold 钢锭模Punching Die 落料模Lancing Die 切口模切缝模Raising(Embossing)压花起伏成形Re-entrant Mold 倒角式模具Sectional Die 拼合模Runless Injection Mold 无流道冷料模具Sectional Die 对合模具Segment Mold 组合模Semi-Positive Mold 半全压式模具<, /SPAN> Shaper 定型模套Single Cavity Mold 单腔模具Solid Forging Die 整体锻模Split Forging Die 拼合锻模Split Mold 双并式模具Sprueless Mold 无注道残料模具Squeezing Die 挤压模Stretch Form Die 拉伸成形模Sweeping Mold 平刮铸模Swing Die 振动模具Three Plates Mold 三片式模具Trimming Die 切边模Unit Mold 单元式模具Universal Mold 通用模具Unscrewing Mold 退扣式模具Yoke Type Die 轭型模模具厂常用之标准零配件Air Vent Valve 通气阀Anchor Pin 锚梢Angular Pin 角梢Baffle 调节阻板Angular Pin 倾斜梢Baffle Plate 折流档板Ball Button 球塞套Ball Plunger 定位球塞Ball Slider 球塞滑块Binder Plate 压板Blank Holder 防皱压板Blanking Die 落料冲头Bolster 上下模板Bottom board 浇注底板Bolster 垫板Bottom Plate 下固定板Bracket 托架Bumper Block 缓冲块Buster 堵口Casting Ladle 浇注包Casting lug 铸耳Cavity 模穴(模仁)Cavity Retainer Plate 模穴托板Center Pin 中心梢Clamping Block 锁定块Coil Spring 螺旋弹簧Cold Punched Nut 冷冲螺母Cooling Spiral 螺旋冷却栓Core 心型Core Pin 心型梢Cotter 开口梢Cross 十字接头Cushion Pin 缓冲梢Diaphragm Gate 盘形浇口Die Approach 模头料道Die Bed 型底Die Block 块形模体Die Body 铸模座Die Bush 合模衬套Die Button 冲模母模Die Clamper 夹模器Die Fastener 模具固定用零件Die Holder 母模固定板Die Lip 模唇Die Plate 冲模板Die Set 冲压模座Direct Gate 直接浇口Dog Chuck 爪牙夹头Dowel 定位梢Dowel Hole 导套孔Dowel Pin 合模梢Dozzle 辅助浇口Dowel Pin 定位梢Draft 拔模锥度Draw Bead 张力调整杆Drive Bearing 传动轴承Ejection Pad 顶出衬垫Ejector 脱模器Ejector Guide Pin 顶出导梢Ejector Leader Bush 顶出导梢衬套Ejector Pad 顶出垫Ejector Pin 顶出梢Ejector Plate 顶出板Ejector Rod 顶出杆Ejector Sleeve 顶出衬套Ejector Valve 顶出阀Eye Bolt 环首螺栓Filling Core 填充型芯椿入蕊Film Gate 薄膜形浇口Finger Pin 指形梢Finish Machined Plate 角形模板Finish Machined Round Plate 圆形模板Fixed Bolster Plate 固定侧模板Flanged Pin 带凸缘针Flash Gate 毛边形浇口Flask 上箱Floating Punch 浮动冲头Gate 浇口Gate Land 浇口面Gib 凹形拉紧楔Goose Neck 鹅颈管Guide Bushing 引导衬套Guide Pin 导梢Guide Post 引导柱Guide Plate 导板Guide Rail 导轨Head Punch 顶头冲孔Headless Punch 直柄冲头Heavily Tapered Solid 整体模蕊盒Hose Nippler 管接头Impact Damper 缓冲器Injection Ram 压射柱塞Inlay Bush 嵌入衬套Inner Plunger 内柱塞Inner Punch 内冲头Insert 嵌件Insert Pin 嵌件梢King Pin 转向梢King Pin Bush 主梢衬套Knockout Bar 脱模杵Land 合模平坦面Land Area 合模面Leader Bush 导梢衬套Lifting Pin 起模顶针起模杆Lining 内衬Locating Center Punch 定位中心冲头Locating Pilot Pin 定位导梢Locating Ring 定位环Lock Block 压块Locking Block 定位块Locking Plate 定位板Loose Bush 活动衬套Making Die 打印冲子Manifold Block 歧管档块Master Plate 靠模样板Match Plate 分型板Mold Base 塑胶模座Mold Clamp 铸模紧固夹Mold Platen 模用板Moving Bolster 换模保持装置Moving Bolster Plate 可动侧模板One Piece Casting 整体铸件Parallel Block 平行垫块Parting Line 分模线Parting Lock Set 合模定位器Pass Guide 穴型导板Peened Head Punch 镶入式冲头锤击强化冲头钻杆凸模Pilot Pin 定位销导向销子Pin Gate 针尖浇口Plate 衬板Pre Extrusion Punch 顶挤冲头Punch 冲头Puncher 推杆Pusher Pin 衬套梢Rack 机架Rapping Rod 起模杆Re-entrant Mold 凹入模Retainer Pin 嵌件梢Retainer Plate 托料板Return Pin 回位梢Riding Stripper 浮动脱模器Ring Gate 环型浇口Roller 滚筒Runner 流道Runner Ejector Set 流道顶出器Runner Lock Pin 流道拉梢Screw Plug 头塞Set Screw 固定螺丝Shedder 脱模装置Shim 分隔片Shoe 模座之上下模板Shoot 流道Shoulder Bolt 肩部螺丝Skeleton 骨架Slag Riser 冒渣口Slide(Slide Core)滑块Slip Joint 滑配接头Spacer Block 间隔块Spacer Ring 间隔环Spider 模蕊支架Spindle 主轴Sprue 注道Sprue Bushing 注道衬套Sprue Bushing Guide 注道导套Sprue Lock Bushing 注道定位衬套Sprue Puller 注道拉料浇道推出杆注道残料顶销Spew Line 合模线Square Key 方键Square Nut 方螺帽Square Thread 方螺纹Limit Stop Collar 限位套Stop Pin 止动梢Stop Ring 止动环Stopper 定位停止梢Straight Pin 圆柱销Stripper Bolt 脱料螺栓Stripper Bushing 脱模衬套Stripper Plate 剥料板Stroke End Block 行程止梢Submarine Gate 潜入式浇口Support Pillar 支撑支柱顶出支柱Support Pin 支撑梢Supporting Plate 托板Sweep Template 造模刮板Tab Gate 辅助浇口Taper Key 推拔键Taper Pin 拔锥梢锥形梢Teeming Pouring 浇注Three Start Screw 三条螺纹Thrust Pin 推力销Tie Bar 拉杵Tunnel Gate 隧道形浇口Vent 通气孔Wortle Plate 拉丝模板模具常用之工作机械3D Coordinate Measurement 三次元量床Boring Machine 搪孔机CNC Milling Machine CNC铣床Contouring Machine 轮廓锯床Copy Grinding Machine 仿形磨床Copy Lathe 仿形车床Copy Milling Machine 仿形铣床Copy Shaping Machine 仿形刨床Cylindrical Grinding Machine 外圆磨床Die Spotting Machine 合模机Drilling Machine 钻孔机Engraving Machine 雕刻机Engraving E.D.M 雕模放置加工机Form Grinding Machine 成形磨床Graphite Machine 石墨加工机Horizontal Boring Machine 卧式搪孔机Horizontal Machine Center 卧式加工制造中心Internal Cylindrical Machine 内圆磨床Jig Boring Machine 冶具搪孔机Jig Grinding Machine 冶具磨床Lap Machine 研磨机Machine Center 加工制造中心Multi Model Miller 靠磨铣床NC Drilling Machine NC钻床NC Grinding Machine NC磨床NC Lathe NC车床NC Programming System NC程式制作系统Planer 龙门刨床Profile Grinding Machine 投影磨床Projection Grinder 投影磨床Radial Drilling Machine 旋臂钻床Shaper 牛头刨床Surface Grinder 平面磨床Try Machine 试模机Turret Lathe 转塔车床Universal Tool Grinding Machine 万能工具磨床Vertical Machine Center 立式加工制造中心Wire E.D.M 线割放电加工机入水 Gate进入位 Gate Location水口形式 Gate Type大水口 Edge Gate细水口 Pin-point Gate水口大小 Gate Size转水口 Switching Runner Gate唧嘴口径 Sprue Diameter流道 Mold Runner热流道 Hot Runner Hot Manifold温度控制器温控器 Thermostat Thermoregulators Temperature Controller 热嘴冷流道 Hot Sprue Cold Runner唧嘴直流 Direct Sprue Gate圆形流道 Round Full Half Runner流道电脑分析 Mold Flow Analysis流道平衡 Runner Balance热嘴 Hot Sprue热流道板 Hot Manifold发热管 Cartridge Heater探针 Thermocouples插头 Connector Plug插座 Connector Socket密封封料 Seal运水 Water Line喉塞 Line Plug Throat Taps喉管 Tube塑胶管 Plastic Tube快速接头 Jiffy Quick Connector Quick Disconnect Coupling模具零件 Mold Components三板模 3-Plate Mold二板模 2-Plate Mold边钉导边 Leader Pin Guide Pin边司导套 Bushing Guide Bushing中托司 Shoulder Guide Bushing中托边 Guide Pin顶针板 Ejector Retainner Plate托板 Support Plate螺丝 Screw管钉 Dowel Pin开模槽 Ply Bar Scot内模管位 Core Cavity inter-Lock顶针 Ejector Pin司筒 Ejector Sleeve司筒针 Ejector Pin推板 Eject Plate Push Plate Stripper Plate缩呵 Movable Core Return Core Puller扣机(尼龙拉勾) Nylon Latch Lock斜顶 Lifter模胚(架) Mold Base上内模 Cavity Insert下内模 Core Insert行位(滑块) Slide镶件 Insert压座 Wedge耐磨板油板 Wedge Wear Plate压条 Plate撑头 Support Pillar唧嘴 Sprue Bushing挡板 Stop Plate定位圈 Locating Ring锁扣 Latch扣机 Parting Lock Set推杆 Push Bar栓打螺丝 S.H.S.B顶板 Ejector Plate活动臂 Lever Arm分流锥 Sprue Spreader分流板 Spreader Plate水口司 Bush垃圾钉 Stop Pin隔片 Buffle弹弓柱 Spring Rod弹弓 Die Spring中托司 Ejector Guide Bush中托边 Ejector Guide Pin镶针 Pin销子 Dowel Pin波子弹弓 Ball catch喉塞 Pipe Plug锁模块 Lock Plate斜顶 Angle from Pin斜顶杆 Angle Ejector Rod尼龙拉勾 Parting Locks活动臂 Lever Arm复位键提前回杆 Early Return Bar气阀 Valves斜导边 Angle Pin术语 Terms承压平面平衡 Parting Surface Support Balance模排气 Parting Line Venting回针碰料位 Return Pin and Cavity Interference顶针碰运水 Water Line Interferes with Ejector Pin 料位出上下模 Part from Cavith (Core) Side不准用镶件 Do Not Use (Core Cavity) Insert用铍铜做镶件 Use Beryllium Copper Insert初步模图设计 Preliminary Mold Design正式模图设计 Final Mold Design弹弓压缩量 Spring Compressed length稳定性好 Good Stability Stable强度不够 Insufficient Rigidity均匀冷却 Even Cooling扣模 Sticking热膨胀 Thermal Expansion公差 Tolerance铜公(电极) Copper Electrode Air Vent Valve 通气阀Anchor Pin 锚梢Angular Pin 角梢Baffle 调节阻板Angular Pin 倾斜梢Baffle Plate 折流挡板Ball Button 球塞套Ball Plunger 定位球塞Ball Slider 球塞滑块Binder Plate 压板Blank Holder 防皱压板Blanking Die 落料冲头Bolster 上下模板Bottom Board 浇注底板Bolster 垫板Bottom Plate 下固定板Bracket 托架Bumper Block 缓冲块Buster 堵口Casting Ladle 浇注包Casting Lug 铸耳Cavity 模腔模穴(模仁)Cavity Retainer Plate 模穴托板Center Pin 中心梢Clamping Block 锁定块Coil Spring 螺旋弹簧Cold Punched Nut 冷冲螺母Cooling Spiral 螺旋冷却栓Core 心型Core Pin 心型梢Cotter 开口梢Cross 十字接头Cushion Pin 缓冲梢Diaphragm Gate 盘形浇口Die Approach 模头料道Die Bed 型底Die Block 块形模体Die Body 模体Die Body 铸模座Die Bush 合模衬套Die Button 冲模母模Die Clamper 夹模器Die Fastener 模具固定用零件Die Holder 母模固定板Die Lip 模唇Die Plate 冲模板Die Set 冲压模座Direct Gate 直接浇口Dog Chuck 爪牙夹头Dowel 定位梢Dowel Hole 导套孔Dowel Pin 合模梢Dozzle 辅助浇口Dowel Pin 定位梢Draft 拔模锥度Draw Bead 张力调整杆Drive Bearing 传动轴承Ejection Pad 顶出衬垫Ejector 脱模器Ejector Guide Pin 顶出导梢Ejector Leader Bush 顶出导梢衬套Ejector Pad 顶出垫Ejector Pin 顶出梢Ejector Plate 顶出板Ejector Rod 顶出杆Ejector Sleeve 顶出衬套Ejector Valve 顶出阀Eye Bolt 环首螺栓Filling Core 填充型芯椿入蕊Film Gate 薄膜形浇口Finger Pin 指形梢Finish Machined Plate 角形模板Finish Machined Round Plate 圆形模板Fixed Bolster Plate 固定侧模板Flanged Pin 带凸缘针Flash Gate 毛边形浇口Flask 上箱Floating Punch 浮动冲头Gate 浇口Gate Land 浇口面Gib 凹形拉紧楔Goose Neck 鹅颈管Guide Bushing 引导衬套Guide Pin 导梢Guide Post 引导柱Guide Plate 导板Guide Rail 导轨Head Punch 顶头冲孔Headless Punch 直柄冲头Heavily Tapered Solid 整体模蕊盒Hose Joint Pipe Coupler 管接头Impact Damper 缓冲器Injection Ram 压射柱塞Inlay Bush 嵌入衬套Inner Plunger 内柱塞Inner Punch 内冲头Inserts 嵌件Insert Pin 嵌件梢King Pin 转向梢King Pin Bush 主梢衬套Knockout Bar 脱模杵Land 合模平坦面Land Area 合模面Leader Bush 导梢衬套Lifting Pin 起模顶针Lining 内衬Locating Center Punch 定位中心冲头Locating Pilot Pin 定位导梢Locating Ring 定位环Lock Block 压块Locking Block 定位块Locking Plate 定位板Loose Bush 活动衬套Making Die 打印冲子Manifold Block 歧管档块Master Plate 靠模样板Match Plate 分型板Mold Base 塑胶模座Mold Clamp 铸模紧固夹Mold Platen 模用板Moving Bolster 换模保持装置Moving Bolster Plate 可动侧模板One Piece Casting 整体铸件Parallel Block 平行垫块Parting Line 分模线Parting Lock Set 合模定位器Pass Guide 穴型导板Peened Head Punch 镶入式冲头钻杆凸模Pilot Pin 定位销导向销子Pin Gate 针尖浇口Plate 衬板Pre Extrusion Punch 顶挤冲头Punch 冲头Puncher 推杆Pusher Pin 衬套梢Rack 机架Rapping Rod 起模杆Re-entrant Mold 凹入模Retainer Pin 嵌件梢Retainer Plate 托料板Return Pin 回位梢Riding Stripper 浮动脱模器Ring Gate 环型浇口Roller 滚筒Runner 流道Runner Ejector Set 流道顶出器Runner Lock Pin 流道拉梢Screw Plug 头塞Set Screw 固定螺丝Shedder 脱模装置Shim 分隔片Shoe 模座之上下模板Shoot 流道Shoulder Bolt 肩部螺丝Skeleton Frameworks 骨架Slag Riser 冒渣口Slide(Slide Core)滑块Slip Joint 滑配接头Spacer Block 间隔块Spacer Ring 间隔环Spider 模蕊支架Spindle 主轴Sprue 注道Sprue Bushing 注道衬套Sprue Bushing Guide 注道导套Sprue Lock Bushing 注道定位衬套Sprue Puller 注道残料顶销浇道推出杆Sprue Line 合模线Square Key 方键Square Nut 方螺帽Square Thread 方螺纹Stop Collar 限位套Stop Pin 止动梢Stop Ring 止动环Stopper 定位停止梢Straight Pin 圆柱销Stripper Bolt 脱料螺栓Stripper Bushing 脱模衬套Stripper Plate 剥料板Stroke End Block 行程止梢Submarine Gate 潜入式浇口Support Pillar 支撑支柱顶出支柱Support Pin 支撑梢Supporting Plate 托板Sweep Template 造模刮板Tab Gate 辅助浇口Taper Key 推拔键Taper Pin 拔锥梢锥形梢Teeming 浇注Three Start Screw 三条螺纹Thrust Pin 推力销Tie Bar 拉杵Tunnel Gate 隧道形浇口Vent 通气孔Wortle Plate 拉丝模板Pierce 冲孔Forming 成型(抽凸冲凸)Draw Hole 抽孔Bending 折弯Trim 切边Emboss 凸点Dome 凸圆Semi-Shearing 半剪Stamp Mark 冲记号Deburr or Coin 压毛边Punch Riveting 冲压铆合Side Stretch 侧冲压平Reel Stretch 卷圆压平Groove 压线Blanking 下料Stamp Letter 冲字(料号)Shearing 剪断Tick-Mark Nearside 正面压印Tick-Mark Farside 反面压印Extension Drawing 展开图procedure Drawing 工程图Die Structure Drawing 模具结构图Material 材质Material Thickness 料片厚度Factor 系数Upward 向上Downward 向下Press Specification 冲床规格Die Height Range 适用模高Die Height 闭模高度Burr 毛边Gap 间隙Weight 重量Total Weight 总重量Punch Weight 上模重量Compression Molding 压缩成型Flash Mold 溢流式模具Extrusion Mold 挤压式模具Split Mold 分割式模具Cavity 型腔母模Mold Core 模芯公模Taper 锥拔Leather Cloak 仿皮革Shiver 饰纹Flow Mark 流痕Welding Mark 溶合痕Post Screw Insert 螺纹套筒埋值Self Tapping Screw 自攻螺丝Striper Plate 脱料板Piston 活塞Cylinder 汽缸套Chip 细碎物Handle Mold 手持式模具Encapsulation Molding 低压封装成型Two Plate 两极式(模具)Well Type 蓄料井Insulated Runner 绝缘浇道方式Hot Runner 热浇道Runner Plat 浇道模块Valve Gate 阀门浇口Band Heater 环带状的电热器Spindle 阀针Spear Head 刨尖头Slag Well 冷料井Cold Slag 冷料渣Air Vent 排气道Welding Line 熔合痕Eject Pin 顶出针Knock Pin 顶出销Return Pin 回位销反顶针Sleeve 套筒Stripper Plate 脱料板Insert Core 放置入子Runner Stripper Plate 浇道脱料板Guide Pin 导销Eject Rod (Bar)(成型机)顶业捧Subzero 深冷处理Three Plate 三极式模具Runner System 浇道系统Stress Crack 应力电裂Orientation 定向Sprue Gate 射料浇口,直浇口Nozzle 射嘴Sprue Lock Pin 料头钩销(拉料杆)Slag Well 冷料井Side Gate 侧浇口Edge Gate 侧缘浇口Tab Gate 搭接浇口Film Gate 薄膜浇口Flash Gate 闸门浇口Slit Gate 缝隙浇口Fan Gate 扇形浇口Dish Gate 因盘形浇口Diaphragm Gate 隔膜浇口Ring Gate 环形浇口Submarine Gate 潜入式浇口Tunnel Gate 隧道式浇口Pin Gate 针点浇口Runnerless 无浇道Sprueless 无射料管方式Long Nozzle 延长喷嘴方式Sprue 浇口溶渣Landed Plunger Mold 有肩柱塞式模具Burnishing Die 挤光模Landed Positive Mold 有肩全压式模具Button Die 镶入式圆形凹模Loading Shoe Mold 料套式模具Center-Gated Mold 中心浇口式模具Loose Detail Mold 活零件模具Chill Mold 冷硬用铸模Loose Mold 活动式模具Cold Hobbing 冷挤压制模Louvering Die 百叶窗冲切模Composite Dies 复合模具Manifold Die 分歧管模具Counter Punch 反凸模Modular Mold 组合式模具Double Stack Mold 双层模具Multi-Cavity Mold 多模穴模具Electroformed Mold 电铸成形模Multi-Gate Mold 复式浇口模具Expander Die 扩径模Offset Bending Die 双折冷弯模具偏移弯曲模Extrusion Die 挤出模Palletizing Die 叠层模Family Mold 反套制品模具Plaster Mold 石膏模Blank Through Dies 漏件式落料模Porous Mold 通气性模具Duplicated Cavity Plate 复板模Positive Mold 全压式模具Fantail Die 扇尾形模具Pressure Die 压紧模Fishtail Die 鱼尾形模具Profile Die 轮廓模Flash Mold 溢料式模具Progressive Die 顺序模Gypsum Mold 石膏铸模Portable Mold 手提式模具Hot-Runner Mold 热流道模具Prototype Mold 雏形试验模具Ingot Mold 钢锭模Punching Die 落料模Lancing Die 切口模Raising(Embossing)压花起伏成形Re-entrant Mold 倒角式模具Sectional Die 拼合模Runnerless Injection Mold 无流道冷料模具Sectional Die 对合模具Segment Mold 组合模Semi-Positive Mold 半全压式模具Shaper 定型模套Single Cavity Mold 单腔模具Solid Forging Die 整体锻模Split Forging Die 拼合锻模Split Mold 双并式模具Sprueless Mold 无注道残料模具Squeezing Die 挤压模Stretch Form Die 拉伸成形模Sweeping Mold 平刮铸模Swing Die 振动模具Three Plates Mold 三片式模具Trimming Die 切边模Unit Mold 单元式模具Universal Mold 通用模具Unscrewing Mold 退扣式模具Yoke Type Die 轭型模Accurate Die Casting 精密压铸Powder Forming 粉末成形Calendaring Molding 压延成形Powder Metal Forging 粉末锻造Cold Chamber Die Casting 冷式压铸Precision Forging 精密锻造Cold Forging 冷锻Press Forging 冲锻Compacting Molding 粉末压出成形Rocking Die Forging 摇动锻造Compound Molding 复合成形Rotary Forging 回转锻造Compression Molding 压缩成形Rotational Molding 离心成形Dip Mold 浸渍成形Rubber Molding 橡胶成形Encapsulation Molding 注入成形Sand Mold Casting 砂模铸造Extrusion Molding 挤出成形Shell Casting 壳模铸造Foam Forming 发泡成形Sinter Forging 烧结锻造Forging Roll 轧锻Six Sides Forging 六面锻造Gravity Casting 重力铸造Slush Molding 凝塑成形Hollow(Blow) Molding 中空(吹出)成形Squeeze Casting 高压铸造Hot Chamber Die Casting 热室压铸Swaging 挤锻Hot Forging 热锻Transfer Molding 转送成形Injection Molding 射出成形Warm Forging 温锻Investment Casting 精密铸造Matched Die Method 对模成形法Laminating Method 被覆淋膜成形Low Pressure Casting 低压铸造Lost Wax Casting 脱蜡铸造Matched Mould Thermal Forming 对模热成形模Barreling 滚光加工Belling 压凸加工Bending 弯曲加工Blanking 下料加工Bulging 撑压加工Burring 冲缘加工Cam Die Bending 凸轮弯曲加工Caulking 压合加工Coining 压印加工Compressing 压缩加工Compression Bending 押弯曲加工Crowning 凸面加工Curl Bending 卷边弯曲加工Curling 卷曲加工Cutting 切削加工Dinking 切断蕊骨Double Shearing 叠板裁断Drawing 引伸加工Drawing with Ironing 抽引光滑加工Embossing 浮花压制加工Extrusion 挤制加工Filing 锉削加工Fine Blanking 精密下料加工Finish Blanking 光制下料加工Finishing 精整加工Flanging 凸缘加工Folding 折边弯曲加工Folding 折叠加工Forming 成形加工Impact Extrusion 冲击挤压加工Indenting 压痕加工Ironing 引缩加工Knurling 滚花Lock Seaming 固定接合Louvering 百叶窗板加工MarKing 刻印加工Necking 颈缩加工Notching 冲口加工Parting 分断加工Piercing 冲孔加工Progressive Bending 连续弯曲加工Progressive Blanking 连续下料加工Progressive Drawing 连续引伸加工Progressive Forming 连续成形加工Reaming 铰孔加工Restriking 二次精冲加工矫形锻压Riveting 铆接加工Roll Bending 滚筒弯曲加工Roll Finishing 滚压加工Rolling 压延加工Roughing 粗加工Scrapless Machining 无废料加工Seaming 折弯重叠加工Shaving 缺口修整加工Shearing 切断加工Sizing 精压加工矫正加工Slitting 割缝加工Spinning 卷边旋接Staking 铆固Stamping 锻压加工Swaging 挤锻压加工Trimming 整缘加工Upsetting 锻粗加工顶锻镦粗Wiring 抽线加工Aberration 色差Atomization 雾化Bank Mark 料垄迹印Bite 咬入Blacking Hole 涂料孔(铸疵)Blacking Scab 涂料疤Blister 起泡Blooming 起霜Blow Hole 破孔Blushing 泛白Body Wrinkle 侧壁皱纹Breaking-in 冒口带肉Bubble 膜泡Burn Mark 糊斑Flash Burr 毛边Camber Warpage 翘曲Cell 气泡Center Buckle 表面中部波皱Check 细裂痕Checking 龟裂Chipping 修整表面缺陷Clamp-off 铸件凹痕Collapse 塌陷Color Mottle 色斑Corrosion 腐蚀Crackle 裂痕裂纹Crazing 碎裂Crazing 龟裂Distortion Deformation 变形Edge 切边碎片Edge Crack 裂边Fading 退色Filler Speak 填充料斑Fissure 裂纹Flange Wrinkle 凸缘起皱Flaw 刮伤Flow Mark 流痕Galling 毛边Glazing 光滑Gloss 光泽Grease Pits 污斑Grinding Defect 磨痕Haircrack 发裂Haze 雾度Incrustation 水锈Indentation 压痕Internal Porosity 内部气孔Mismatch 偏模Mottle 斑点Necking 缩颈Nick 割痕Orange peel 橘皮状表面缺陷Overflow 溢流Peeling 剥离Pit 坑Pitting Corrosion 点状腐蚀Plate Mark 模板印痕Pock 麻点Pock Mark 痘斑Resin Streak 树脂流纹Resin Wear 树脂脱落Riding 凹陷Sagging 松垂Saponification 皂化Scar 疤痕Scrap 废料Scrap Jam 废料阻塞Scratch 刮伤划痕Scuffing 深冲表面划伤Seam 裂痕Shock Line 模口挤痕Short Shot 充填不足Shrinkage Pool 凹孔Sink Mark 凹痕Skin Inclusion 表皮折叠Straightening 矫直Streak 条状痕Surface Check 表面裂痕Surface Roughening 橘皮状表皮皱折Surging 波动Sweat Out 冒汗Torsion Distortion 扭曲Warpage 翘曲Waviness 波痕Webbing 熔塌Weld Mark 焊痕Whitening 白化Wrinkle 皱纹Gas Aassisted Technology 气辅Bottle Cap Mold 瓶盖模具。
- 1、下载文档前请自行甄别文档内容的完整性,平台不提供额外的编辑、内容补充、找答案等附加服务。
- 2、"仅部分预览"的文档,不可在线预览部分如存在完整性等问题,可反馈申请退款(可完整预览的文档不适用该条件!)。
- 3、如文档侵犯您的权益,请联系客服反馈,我们会尽快为您处理(人工客服工作时间:9:00-18:30)。
国内外塑料模具的现状及水平:
整体来看,中国塑料模具无论是在数量上,还是在质量、技术和能力等方面都有了很大进步,但与国民经济发展的需求、世界先进水平相比,差距仍很大。
一些大型、精密、复杂、长寿命的中高档塑料模具每年仍需大量进口。
在总量供不应求的同时,一些低档塑料模具却供过于求,市场竞争激烈,还有一些技术含量不太高的中档塑料模具也有供过于求的趋势
加入WTO,给塑料模具产业带来了巨大的挑战,同时带来更多的机会。
由于中国塑料模具以中低档产品为主,产品价格优势明显,有些甚至只有国外产品价格的1/5~1/3,加入WTO后,国外同类产品对国内冲击不大,而中国中低档模具的出口量则加大;在高精模具方面,加入WTO前本来就主要依靠进口,加入WTO后,不仅为高精尖产品的进口带来了更多的便利,同时还促使更多外资来中国建厂,带来国外先进的模具技术和管理经验,对培养中国的专业模具人才起到了推动作用。
近年来,中国塑料模具制造水平已有较大提高。
大型塑料模具已能生产单套重量达到50t以上的注塑模,精密塑料模具的精度已达到2μm,制件精度很高的小模数齿轮模具及达到高光学要求的车灯模具等也已能生产,多腔塑料模具已能生产一模7800腔的塑封模,高速模具方面已能生产挤出速度达6m/min以上的高速塑料异型材挤出模具及主型材双腔共挤、双色共挤、软硬共挤、后共挤、再生料共挤出和低发泡钢塑共挤等各种模具。
在生产手段上,模具企业设备数控化率已有较大提高,CAD/CAE/CAM技术的应用面已大为扩展,高速加工及RP/RT等先进技术的采用已越来越多,模具标准件使用覆盖率及模具商品化率都有较大幅度的提高,热流道模具的比例也有较大提高。
另外,三资企业的蓬勃发展进一步促进了塑料模具设计制造水平及企业管理水平的提高,有些企业已实现信息化管理和全数字化无图制造
随着模具企业设计和加工水平的提高,模具的制造正在从过去主要依靠钳工的技艺转变为主要依靠技术。
这不仅是生产手段的转变,也是生产方式的转变和观念的上升。
这一趋势使得模具的标准化程度不断提高,模具精度越来越高,生产周期越来越短,钳工比例越来越低,最终促进了模具工业整体水平不断提高。
中国模具行业目前已有10多个国家级高新技术企业,约200个省市级高新技术企业。
与此趋势相适应,生产模具的主要骨干力量从技艺型人才逐渐转变为技术型人才是必然要求。
当然,目前及相当长一段时间内,技艺型人才仍十分重要,因为模具毕竟难以完全摆脱对技艺的依靠。
存在的主要问题
中国塑料模具行业和国外先进水平相比,主要存在以下问题。
(1)发展不平衡,产品总体水平较低。
虽然个别企业的产品已达到或接近国际先进水平,但总体来看,模具的精度、型腔表面的粗糙度、生产周期、寿命等指标与国外先进水平相比尚有较大差距。
包括生产方式和企业管理在内的总体水平与国外工业发达国家相比尚有10年以上的差距。
(2)工艺装备落后,组织协调能力差。
虽然部分企业经过近几年的技术改造,工艺装备水平已经比较先进,有些三资企业的装备水平也并不落后于国外,但大部分企业的工艺装备仍比较落后。
更主要的是,企业组织协调能力差,难以整合或调动社会资源为我所用,从而就难以承接比较大的项目。
(3)大多数企业开发能力弱,创新能力明显不足。
一方面是技术人员比例低、水平不够高,另一方面是科研开发投入少;更重要的是观念落后,对创新和
开发不够重视。
模具企业不但要重视模具的开发,同时也要重视产品的创新。
(4)供需矛盾短期难以缓解。
近几年,国产塑料模具国内市场满足率一直不足74%,其中大型、精密、长寿命模具满足率更低,估计不足60%。
同时,工业发达国家的模具正在加速向中国转移,国际采购越来越多,国际市场前景看好。
市场需求旺盛,生产发展一时还难以跟上,供不应求的局面还将持续一段时间。