关于P20模具钢的球头铣刀刀轴方向的调查报告
铣刀研究报告
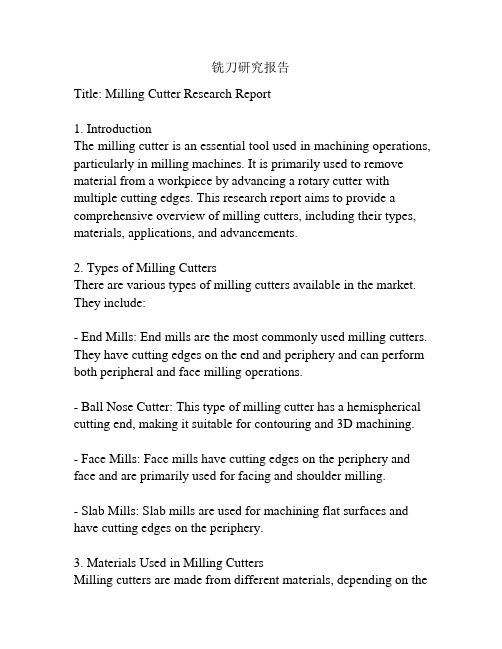
铣刀研究报告Title: Milling Cutter Research Report1. IntroductionThe milling cutter is an essential tool used in machining operations, particularly in milling machines. It is primarily used to remove material from a workpiece by advancing a rotary cutter with multiple cutting edges. This research report aims to provide a comprehensive overview of milling cutters, including their types, materials, applications, and advancements.2. Types of Milling CuttersThere are various types of milling cutters available in the market. They include:- End Mills: End mills are the most commonly used milling cutters. They have cutting edges on the end and periphery and can perform both peripheral and face milling operations.- Ball Nose Cutter: This type of milling cutter has a hemispherical cutting end, making it suitable for contouring and 3D machining.- Face Mills: Face mills have cutting edges on the periphery and face and are primarily used for facing and shoulder milling.- Slab Mills: Slab mills are used for machining flat surfaces and have cutting edges on the periphery.3. Materials Used in Milling CuttersMilling cutters are made from different materials, depending on themachinability, hardness, and desired application. Commonly used materials include:- High-Speed Steel (HSS): HSS cutters are cost-effective and can withstand high temperatures. They are suitable for general-purpose milling.- Carbide: Carbide cutters are extremely hard and can endure high cutting speeds and temperatures. They are perfect for machining hard materials like stainless steel and titanium.- Ceramic: Ceramic cutters offer excellent heat resistance and are ideal for high-speed machining applications in ferrous and non-ferrous materials.4. Applications of Milling CuttersMilling cutters find applications in various industries, including automotive, aerospace, electronics, and mold and die manufacturing. Some common applications include:- Contouring: Milling cutters are used for creating complex shapes and contours on workpieces.- Slotting: They are utilized for cutting slots or grooves in workpieces.- Gear Cutting: Specialized milling cutters are designed for cutting gears.- Roughing and Finishing: Different types of milling cutters areused for roughing and finishing operations on workpieces.5. Advancements in Milling CuttersThe milling cutter industry has witnessed several advancements to enhance performance and efficiency. Some notable advancements include:- Coatings: Various coating technologies have been developed to improve the wear resistance and tool life of milling cutters.- Insert Milling Cutters: Insert milling cutters feature replaceable cutting inserts for ease of use and cost-effectiveness.- High-Speed Machining: Advancements in the manufacturing process now allow for higher cutting speeds, thereby reducing machining time.- Computer Numerical Control (CNC) Integration: Modern milling machines are equipped with CNC systems that allow for precise control of milling cutters.6. ConclusionMilling cutters play a crucial role in various industrial applications, providing efficient and accurate material removal. With advancements in materials, coatings, and machining processes, milling cutters continue to evolve, ensuring increased productivity and cost-effectiveness.。
我国刀具市场发展调研报告
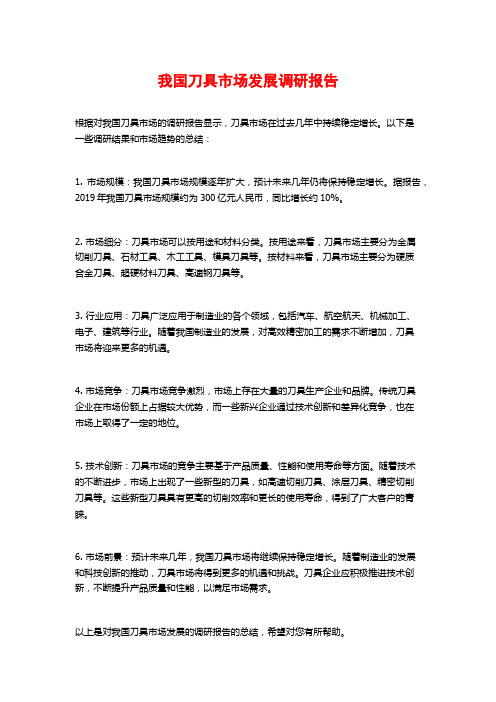
我国刀具市场发展调研报告根据对我国刀具市场的调研报告显示,刀具市场在过去几年中持续稳定增长。
以下是一些调研结果和市场趋势的总结:1. 市场规模:我国刀具市场规模逐年扩大,预计未来几年仍将保持稳定增长。
据报告,2019年我国刀具市场规模约为300亿元人民币,同比增长约10%。
2. 市场细分:刀具市场可以按用途和材料分类。
按用途来看,刀具市场主要分为金属切削刀具、石材工具、木工工具、模具刀具等。
按材料来看,刀具市场主要分为硬质合金刀具、超硬材料刀具、高速钢刀具等。
3. 行业应用:刀具广泛应用于制造业的各个领域,包括汽车、航空航天、机械加工、电子、建筑等行业。
随着我国制造业的发展,对高效精密加工的需求不断增加,刀具市场将迎来更多的机遇。
4. 市场竞争:刀具市场竞争激烈,市场上存在大量的刀具生产企业和品牌。
传统刀具企业在市场份额上占据较大优势,而一些新兴企业通过技术创新和差异化竞争,也在市场上取得了一定的地位。
5. 技术创新:刀具市场的竞争主要基于产品质量、性能和使用寿命等方面。
随着技术的不断进步,市场上出现了一些新型的刀具,如高速切削刀具、涂层刀具、精密切削刀具等。
这些新型刀具具有更高的切削效率和更长的使用寿命,得到了广大客户的青睐。
6. 市场前景:预计未来几年,我国刀具市场将继续保持稳定增长。
随着制造业的发展和科技创新的推动,刀具市场将得到更多的机遇和挑战。
刀具企业应积极推进技术创新,不断提升产品质量和性能,以满足市场需求。
以上是对我国刀具市场发展的调研报告的总结,希望对您有所帮助。
刀具 调研 报告
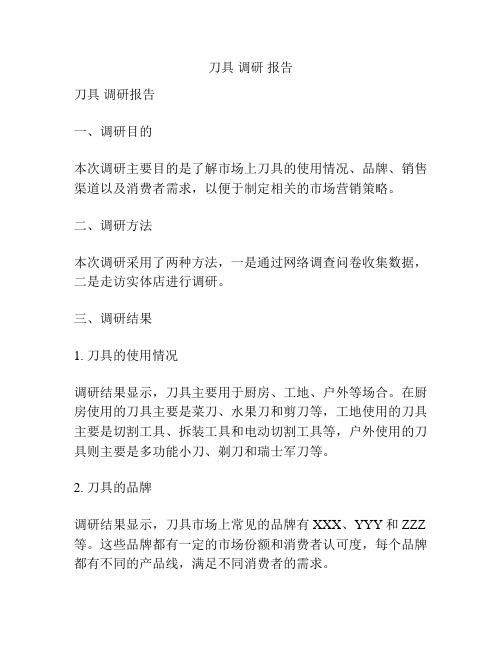
刀具调研报告刀具调研报告一、调研目的本次调研主要目的是了解市场上刀具的使用情况、品牌、销售渠道以及消费者需求,以便于制定相关的市场营销策略。
二、调研方法本次调研采用了两种方法,一是通过网络调查问卷收集数据,二是走访实体店进行调研。
三、调研结果1. 刀具的使用情况调研结果显示,刀具主要用于厨房、工地、户外等场合。
在厨房使用的刀具主要是菜刀、水果刀和剪刀等,工地使用的刀具主要是切割工具、拆装工具和电动切割工具等,户外使用的刀具则主要是多功能小刀、剃刀和瑞士军刀等。
2. 刀具的品牌调研结果显示,刀具市场上常见的品牌有XXX、YYY和ZZZ 等。
这些品牌都有一定的市场份额和消费者认可度,每个品牌都有不同的产品线,满足不同消费者的需求。
3. 刀具的销售渠道调研结果显示,刀具的销售渠道主要有实体店和电商平台。
实体店主要包括大型超市、家居用品店和刀剪专卖店等,而电商平台主要包括淘宝、京东、天猫等。
消费者可以根据自己的需求选择不同的购买渠道。
4. 消费者需求调研结果显示,消费者对于刀具的需求主要包括以下几点:(1)质量和耐用性:消费者希望购买的刀具质量好、耐用性强,能够满足长时间使用的需求。
(2)安全性:刀具的安全性是消费者十分关注的问题,他们希望使用刀具时能够更加安全,避免伤害。
(3)设计和外观:消费者对于刀具的外观设计也有一定的要求,他们希望刀具既能够实用,又能够美观。
(4)价格和性价比:刀具的价格也是消费者考虑购买的重要因素,消费者希望能够购买到价格合理、性价比高的刀具产品。
四、市场营销策略根据以上调研结果,结合市场需求及竞争对手情况,制定以下市场营销策略:1. 产品质量优先:加强产品质量的控制,确保刀具的品质和耐用性,提高消费者的满意度和忠诚度。
2. 安全性保障:在产品设计时注重安全性,提供详细的使用说明,并加强售后服务,以解决消费者的问题和疑虑。
3. 创新设计和外观:推出具有创新设计和独特外观的刀具产品,满足消费者对美观的需求,增加产品辨识度和竞争力。
刀具 调研 报告

刀具调研报告刀具调研报告一、引言刀具是现代社会中广泛应用的一种工具,它在制造、农业、建筑等领域起着重要作用。
为了进一步了解刀具市场的需求和发展趋势,我们进行了一次刀具调研。
本报告将主要介绍我们的调研目的、方法、结果和结论。
二、调研目的1. 了解刀具市场的现状和趋势,包括市场规模、竞争格局等方面信息;2. 分析刀具市场的消费者需求和特点;3. 研究刀具制造商的生产技术和创新方向。
三、调研方法我们通过以下方式获取刀具市场的相关信息:1. 网络调研:通过电子商务平台、行业专业网站等在线渠道,查找关于刀具市场的相关数据和报告。
2. 实地参观:我们前往一些刀具生产企业,实地考察他们的生产工艺和设备。
3. 问卷调查:我们设计了一份针对刀具消费者的问卷,在线和线下发放,以了解他们对刀具品牌、性能和价格等方面的偏好。
四、调研结果1. 市场规模:根据我们的调研数据,刀具市场规模庞大,而且呈稳步增长趋势。
其中,手工刀具和电动刀具是市场上主要的产品类型。
2. 竞争格局:刀具市场竞争激烈,几家大型的刀具制造商占据了市场的主导地位。
他们通过技术研发、品牌营销等手段提升自身竞争力。
3. 消费者需求:刀具消费者普遍注重产品的质量和性能。
在价格合理的前提下,他们更愿意选择具有优质材料和精湛工艺的产品。
4. 生产技术:刀具制造业采用了许多先进的生产技术,如数控加工、电火花加工等。
这些技术的应用提高了刀具的精度和效率。
5. 创新方向:刀具制造商致力于开发更加耐磨、耐用的刀具产品。
同时,一些刀具制造商也在研发智能化刀具,以满足市场的不断变化需求。
五、结论通过本次刀具调研,我们得出以下结论:1. 刀具市场规模庞大,发展潜力巨大,但竞争激烈,需要刀具制造商不断提升产品质量和性能。
2. 消费者对刀具的需求更加注重质量和性能,刀具制造商应该注重产品的工艺和材料选择。
3. 刀具制造业需要不断引入先进的生产技术,提升生产效率和产品质量。
4. 刀具制造商应该加大研发力度,开发更加耐磨、耐用的刀具产品,并关注智能化刀具的市场需求。
数控刀具的研究报告总结
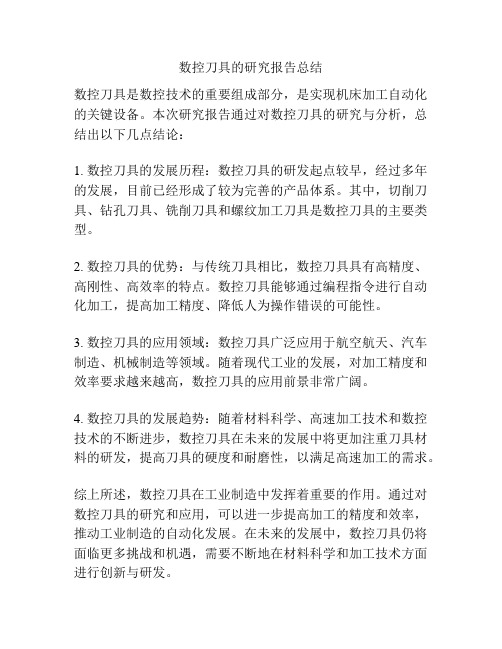
数控刀具的研究报告总结
数控刀具是数控技术的重要组成部分,是实现机床加工自动化的关键设备。
本次研究报告通过对数控刀具的研究与分析,总结出以下几点结论:
1. 数控刀具的发展历程:数控刀具的研发起点较早,经过多年的发展,目前已经形成了较为完善的产品体系。
其中,切削刀具、钻孔刀具、铣削刀具和螺纹加工刀具是数控刀具的主要类型。
2. 数控刀具的优势:与传统刀具相比,数控刀具具有高精度、高刚性、高效率的特点。
数控刀具能够通过编程指令进行自动化加工,提高加工精度、降低人为操作错误的可能性。
3. 数控刀具的应用领域:数控刀具广泛应用于航空航天、汽车制造、机械制造等领域。
随着现代工业的发展,对加工精度和效率要求越来越高,数控刀具的应用前景非常广阔。
4. 数控刀具的发展趋势:随着材料科学、高速加工技术和数控技术的不断进步,数控刀具在未来的发展中将更加注重刀具材料的研发,提高刀具的硬度和耐磨性,以满足高速加工的需求。
综上所述,数控刀具在工业制造中发挥着重要的作用。
通过对数控刀具的研究和应用,可以进一步提高加工的精度和效率,推动工业制造的自动化发展。
在未来的发展中,数控刀具仍将面临更多挑战和机遇,需要不断地在材料科学和加工技术方面进行创新与研发。
铣刀设计实验报告

本科生实验报告实验课程金属切削原理与刀具学院名称核技术与自动化工程学院专业名称学生姓名学生学号指导教师实验地点实验成绩二〇 16 年 11 月——二〇 16 年 11 月填写说明1、适用于本科生所有的实验报告(印制实验报告册除外);2、专业填写为专业全称,有专业方向的用小括号标明;3、格式要求:①用A4纸双面打印(封面双面打印)或在A4大小纸上用蓝黑色水笔书写。
②打印排版:正文用宋体小四号,1.5倍行距,页边距采取默认形式(上下2.54cm,左右2.54cm,页眉1.5cm,页脚1.75cm)。
字符间距为默认值(缩放100%,间距:标准);页码用小五号字底端居中。
③具体要求:题目(二号黑体居中);摘要(“摘要”二字用小二号黑体居中,隔行书写摘要的文字部分,小4号宋体);关键词(隔行顶格书写“关键词”三字,提炼3-5个关键词,用分号隔开,小4号黑体);正文部分采用三级标题;第1章××(小二号黑体居中,段前0.5行)1 ×××××四号黑体×××××(段前、段后0.5行)1.1小四号黑体(段前、段后0.5行)参考文献(黑体小二号居中,段前0.5行),参考文献用五号宋体,参照《参考文献著录规则(GB/T 7714-2005)》。
1课程设计题目:立式铣刀的设计2铣削的定义及应用3课题目的(1)、了解立式铣刀的各参量;(2)、准确的在图中标出各参量;(3)、熟练使用pro/e进行铣刀的三维建模。
立式铣刀的设计一.铣刀简介1.概念铣刀,是用于铣削加工的、具有一个或多个刀齿的旋转刀具。
工作时各刀齿依次间歇地切去工件的余量。
铣刀主要用于在铣床上加工平面、台阶、沟槽、成形表面和切断工件等。
2.分类圆柱形铣刀:用于卧式铣床上加工平面。
刀齿分布在铣刀的圆周上,按齿形分为直齿和螺旋齿两种。
按齿数分粗齿和细齿两种。
数控刀具研究报告-数控刀具产品入市调查研究报告2023年
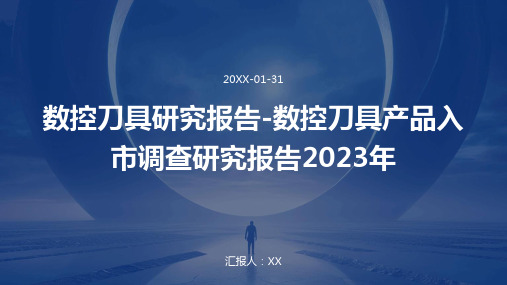
VS
主要问题
当前数控刀具技术面临的主要问题包括刀 具材料性能不足、结构设计不合理、制造 工艺水平不高等。这些问题导致了刀具在 高速、高精度加工中的性能不稳定,难以 满足复杂工件的加工需求。
新技术、新工艺推广应用前景
01
新材料技术
随着新材料技术的不断发展,超硬刀具材料(如PCD、CBN等)的应用
将越来越广泛。这些材料具有更高的硬度、耐磨性和热稳定性,能够显
产品优劣势比较分析
优势
本公司产品采用先进的数控加工技术和高品质材料制造,具有高精度、高耐磨性、高稳定性等优点; 同时,公司注重产品研发和创新,不断推出适应市场需求的新产品,满足客户的多样化需求。
劣势
与国内外知名品牌相比,本公司在品牌知名度、市场渠道建设等方面还存在一定差距;此外,由于公 司规模相对较小,生产成本较高,导致产品价格相对较高,影响了市场竞争力。
合性能。
智能化、自动化发展趋势
智能化刀具
随着人工智能技术的不断发展,智能化刀具将成为未来数控刀具的重要发展方向。智能化 刀具能够实时监测刀具的磨损状态、自动调整切削参数,提高加工效率和加工质量。
自动化换刀系统
自动化换刀系统能够实现刀具的自动更换和调整,减少人工干预和操作时间,提高生产效 率。未来,随着自动化技术的不断发展,自动化换刀系统将更加智能化、柔性化。
完善售后服务体系
建立完善的售后服务体系,提供及时、专业的技术支 持和维修服务,增强客户信任度和满意度。
06
竞争对手分析与优劣势比较
主要竞争对手概况介绍
国内外知名数控刀具品牌
如株洲钻石、华锐精密、欧士机、山特维克等,这些品牌历史悠久,技术实力雄厚,产品线丰富,市场占有率较 高。
新兴数控刀具企业
刀具维护及尺寸测量报告
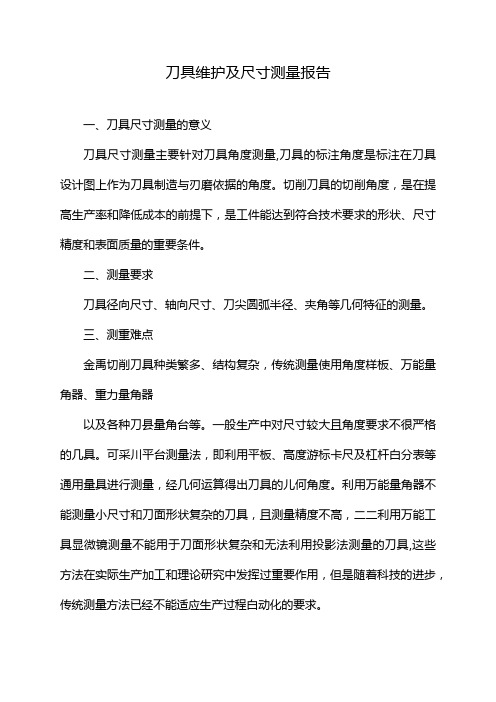
刀具维护及尺寸测量报告一、刀具尺寸测量的意义刀具尺寸测量主要针对刀具角度测量,刀具的标注角度是标注在刀具设计图上作为刀具制造与刃磨依据的角度。
切削刀具的切削角度,是在提高生产率和降低成本的前提下,是工件能达到符合技术要求的形状、尺寸精度和表面质量的重要条件。
二、测量要求刀具径向尺寸、轴向尺寸、刀尖圆弧半径、夹角等几何特征的测量。
三、测重难点金禹切削刀具种类繁多、结构复杂,传统测量使用角度样板、万能量角器、重力量角器以及各种刀县量角台等。
一般生产中对尺寸较大且角度要求不很严格的几具。
可采川平台测量法,即利用平板、高度游标卡尺及杠杆白分表等通用量具进行测量,经几何运算得出刀具的儿何角度。
利用万能量角器不能测量小尺寸和刀面形状复杂的刀具,且测量精度不高,二二利用万能工具显微镜测量不能用于刀面形状复杂和无法利用投影法测量的刀具,这些方法在实际生产加工和理论研究中发挥过重要作用,但是随着科技的进步,传统测量方法已经不能适应生产过程白动化的要求。
四、天准测量解决方案天准精密技术有限公司基于机器视觉技术的几何量测量技术,对于小尺寸刀具的复杂曲面轮廓、圆弧及R角等常见尺寸,可以实现非接触的快速、准确的自动化测量,如需测出更接近于刀具实际情况的界面形状,只需在刀面上选择更多的的点测量即可,同时也可借助于不同检具和夹具协助刀具快速准确测量,因此在工程实践中得到广泛应用和迅速发展。
机器视觉技术应用于刀具几何参数测量,必然会为提高切削生产率和切削技术水平发挥重要作用。
刀具维护一、防止数控刀具生锈的方法1、选择品质优良的防锈油。
2、防锈之前要注意将刀具擦拭干净;保持室内干燥。
3、刀具管理;刀具分别放置,严禁将刀具不加任何包装就放在一起。
4、注意刃口的保护;千万不要碰到或者掉地上。
5、刀具使用时,如果有螺丝防卡剂的话,一定要添加,这样可以防止螺丝卡死。
二、刀具的日常维护1、减少人手上的汗液与刀柄接触,尽量不徒手抓取刀具,徒手抓取刀具后及时涂抹防锈油。
刀具 调研 报告

刀具调研报告
《刀具调研报告》
调研目的:本次调研旨在了解目前市面上刀具的种类、品质和价格,为消费者购买刀具提供参考。
调研方法:采用问卷调查和实地走访的方式进行调研,共涉及10家刀具品牌的产品。
调研结果:
1. 刀具种类
根据调研结果,市面上的刀具种类繁多,包括厨房刀具、户外刀具、办公刀具等。
其中,厨房刀具的种类最为丰富,包括菜刀、水果刀、砍骨刀等。
而户外刀具则包括多功能刀、瑞士军刀等。
2. 品质评比
在调研中,我们对比了不同品牌的刀具品质,包括材质、刀刃锋利度、手柄舒适度等。
结果显示,一些知名品牌的刀具在品质上有一定的优势,而一些小众品牌的刀具在价格较低的情况下也具有一定的性能。
3. 价格比较
在调研中,我们发现刀具的价格差异较大,有些品牌的刀具价格昂贵,而一些小众品牌则价格较为亲民。
不同种类的刀具价格也有所区别,如厨房刀具的价格相对较高,而办公刀具的价
格相对较低。
调研总结:
通过本次调研,我们了解到刀具种类繁多,品质和价格差异较大。
消费者在购买刀具时,应根据自己的需求和预算进行选择。
同时,对于刀具品质也应有一定的认知,避免盲目追求价格低廉而忽视品质。
希望本次调研结果对消费者购买刀具时能有所帮助。
复杂刀具实习报告

一、实习背景随着工业技术的不断进步,刀具在制造业中的应用越来越广泛。
复杂刀具作为一种高精度、高效率的切削工具,在加工各种复杂零件时发挥着至关重要的作用。
为了深入了解复杂刀具的制造工艺和使用方法,提高自己的专业技能,我于2023年在XX刀具制造有限公司进行了为期一个月的实习。
二、实习目的1. 了解复杂刀具的种类、特点和应用领域;2. 掌握复杂刀具的制造工艺和加工方法;3. 学习复杂刀具的维护保养知识;4. 提高自己的实际操作能力和解决问题的能力。
三、实习内容1. 复杂刀具的种类及特点实习期间,我了解了复杂刀具的种类,如端铣刀、面铣刀、球头铣刀等。
这些刀具具有高精度、高效率、高寿命等特点,适用于加工各种复杂零件。
2. 复杂刀具的制造工艺在实习过程中,我学习了复杂刀具的制造工艺,包括刀具材料的选择、刀具形状的设计、刀具热处理、刀具研磨等环节。
其中,刀具材料的选择对刀具的性能有很大影响,常用的刀具材料有高速钢、硬质合金等。
3. 复杂刀具的加工方法复杂刀具的加工方法主要包括车削、铣削、磨削等。
实习期间,我亲自动手操作车床、铣床和磨床,掌握了刀具的加工方法。
4. 复杂刀具的维护保养为了延长刀具的使用寿命,我学习了复杂刀具的维护保养知识。
主要包括:刀具的清洗、润滑、储存等方面。
四、实习体会1. 实践是检验真理的唯一标准。
通过实习,我深刻体会到理论知识与实际操作相结合的重要性。
2. 复杂刀具的制造工艺要求严格,每一个环节都关系到刀具的性能。
因此,在实习过程中,我严谨对待每一个环节,力求做到最好。
3. 实习过程中,我学会了与同事沟通、协作,共同完成工作任务。
这使我认识到团队精神的重要性。
4. 通过实习,我对复杂刀具有了更深入的了解,为今后从事相关工作打下了坚实的基础。
五、实习总结本次实习使我受益匪浅,不仅掌握了复杂刀具的制造工艺、加工方法和维护保养知识,还提高了自己的实际操作能力和解决问题的能力。
在今后的学习和工作中,我将继续努力,为我国制造业的发展贡献自己的力量。
刀具调研报告
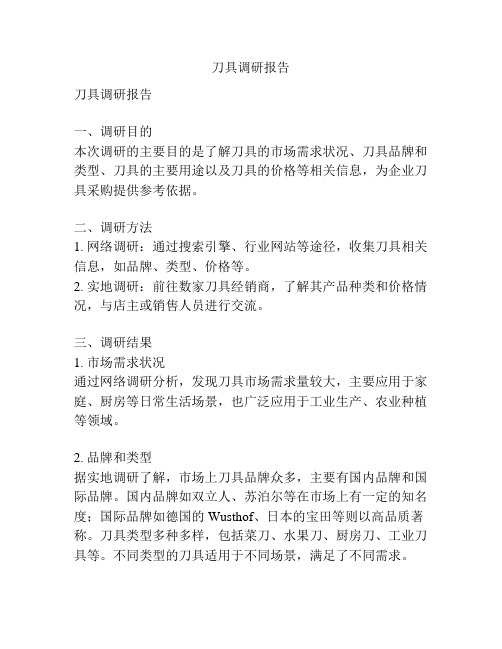
刀具调研报告刀具调研报告一、调研目的本次调研的主要目的是了解刀具的市场需求状况、刀具品牌和类型、刀具的主要用途以及刀具的价格等相关信息,为企业刀具采购提供参考依据。
二、调研方法1. 网络调研:通过搜索引擎、行业网站等途径,收集刀具相关信息,如品牌、类型、价格等。
2. 实地调研:前往数家刀具经销商,了解其产品种类和价格情况,与店主或销售人员进行交流。
三、调研结果1. 市场需求状况通过网络调研分析,发现刀具市场需求量较大,主要应用于家庭、厨房等日常生活场景,也广泛应用于工业生产、农业种植等领域。
2. 品牌和类型据实地调研了解,市场上刀具品牌众多,主要有国内品牌和国际品牌。
国内品牌如双立人、苏泊尔等在市场上有一定的知名度;国际品牌如德国的Wusthof、日本的宝田等则以高品质著称。
刀具类型多种多样,包括菜刀、水果刀、厨房刀、工业刀具等。
不同类型的刀具适用于不同场景,满足了不同需求。
3. 刀具用途刀具用途广泛,主要应用于以下几个领域:(1) 家庭使用:包括切割食材、烹饪等。
(2) 工业生产:用于金属加工、木工等。
(3) 农业种植:用于修剪植物、农作物收割等。
4. 刀具价格经过调研发现,刀具的价格因品牌、材料、型号等不同而有较大差异。
一般来说,国际品牌的刀具价格较高,而国内品牌的刀具价格相对较低。
不同工艺、材料和尺寸的刀具也会影响其价格水平。
四、调研结论根据对市场需求、品牌和类型、用途以及价格的调研,我们可以得出以下结论:1. 刀具市场需求量大,应用领域广泛,从家庭到工业都有不同程度的需求。
2. 市场上存在众多刀具品牌和类型,消费者可以根据自己的需求选择合适的刀具。
3. 刀具的价格因品牌、材料和型号不同而有较大差异,消费者可以根据自身经济条件和需求选择适合的产品。
五、建议针对以上调研结果,我们给出以下建议:1. 企业应根据市场需求不断研发新型刀具产品,满足消费者的不同需求。
2. 企业应选择合适的刀具品牌供应商,确保刀具的品质稳定可靠。
数控铣工课题实习报告
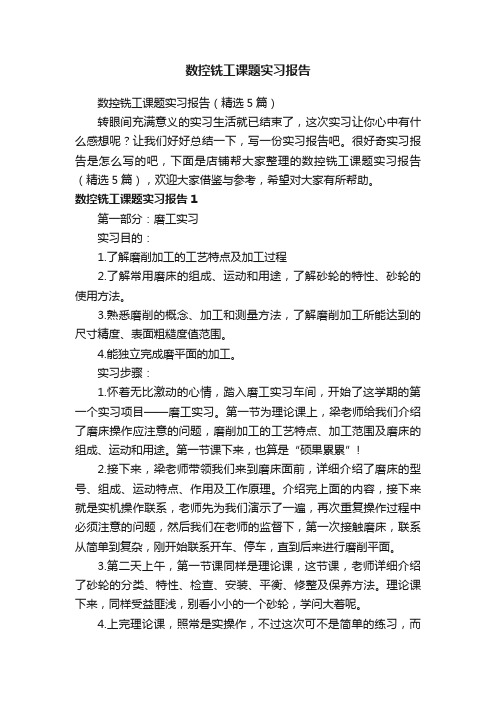
数控铣工课题实习报告数控铣工课题实习报告(精选5篇)转眼间充满意义的实习生活就已结束了,这次实习让你心中有什么感想呢?让我们好好总结一下,写一份实习报告吧。
很好奇实习报告是怎么写的吧,下面是店铺帮大家整理的数控铣工课题实习报告(精选5篇),欢迎大家借鉴与参考,希望对大家有所帮助。
数控铣工课题实习报告1第一部分:磨工实习实习目的:1.了解磨削加工的工艺特点及加工过程2.了解常用磨床的组成、运动和用途,了解砂轮的特性、砂轮的使用方法。
3.熟悉磨削的概念、加工和测量方法,了解磨削加工所能达到的尺寸精度、表面粗糙度值范围。
4.能独立完成磨平面的加工。
实习步骤:1.怀着无比激动的心情,踏入磨工实习车间,开始了这学期的第一个实习项目——磨工实习。
第一节为理论课上,梁老师给我们介绍了磨床操作应注意的问题,磨削加工的工艺特点、加工范围及磨床的组成、运动和用途。
第一节课下来,也算是“硕果累累”!2.接下来,梁老师带领我们来到磨床面前,详细介绍了磨床的型号、组成、运动特点、作用及工作原理。
介绍完上面的内容,接下来就是实机操作联系,老师先为我们演示了一遍,再次重复操作过程中必须注意的问题,然后我们在老师的监督下,第一次接触磨床,联系从简单到复杂,刚开始联系开车、停车,直到后来进行磨削平面。
3.第二天上午,第一节课同样是理论课,这节课,老师详细介绍了砂轮的分类、特性、检查、安装、平衡、修整及保养方法。
理论课下来,同样受益匪浅,别看小小的一个砂轮,学问大着呢。
4.上完理论课,照常是实操作,不过这次可不是简单的练习,而是一次“小测试”,老师为我们规定了加工后达到的尺寸精度、表面粗糙度值。
5.在磨工实习最后的时间里,我们实习小组在老师的指导下,已实现了实习目的,但我们还要进行一次测试,以检验每个同学所达到的程度……随着测试结束,磨工实习也拉下帷幕……实习总结:1.两天的实习下来,使我对整个磨削加工有了深刻的了解,也达到了预期目的。
铣刀技术实训报告

一、实训目的本次铣刀技术实训旨在使学生了解铣刀的基本结构、种类、用途及加工原理,掌握铣刀的选用、安装、调整和使用方法,提高学生对铣刀操作技能的熟练程度,为今后从事机械加工工作打下坚实基础。
二、实训内容1. 铣刀的基本结构及种类铣刀是铣削加工中常用的刀具,主要由刀体、刀齿和刀柄三部分组成。
刀体是铣刀的主体,用于支撑刀齿;刀齿是铣刀的切削部分,用于完成切削任务;刀柄是铣刀与机床的连接部分,用于传递切削力和扭矩。
根据铣刀的用途和结构,可分为以下几种类型:(1)圆柱铣刀:用于加工平面、台阶、键槽等。
(2)端铣刀:用于加工端面、台阶、键槽等。
(3)角度铣刀:用于加工斜面、斜槽等。
(4)立铣刀:用于加工立式工件上的平面、台阶、键槽等。
(5)球头铣刀:用于加工球形表面、球面孔等。
2. 铣刀的选用、安装、调整和使用方法(1)铣刀选用根据加工工件的材料、形状、尺寸和加工要求,选择合适的铣刀类型、规格和精度等级。
(2)铣刀安装将铣刀插入机床主轴,并调整铣刀的位置,使其与工件加工表面保持一定的距离。
(3)铣刀调整调整铣刀的切削角度、切削深度和切削速度,以确保加工质量和效率。
(4)铣刀使用启动机床,使铣刀与工件接触,开始切削。
在切削过程中,注意观察铣刀的切削状态,及时调整切削参数,以保证加工质量。
三、实训过程1. 铣刀的基本结构及种类认识通过观察实物和查阅资料,了解铣刀的基本结构、种类、用途及加工原理。
2. 铣刀的选用、安装、调整和使用方法实践(1)选用合适的铣刀:根据加工工件的材料、形状、尺寸和加工要求,选择合适的铣刀类型、规格和精度等级。
(2)安装铣刀:将铣刀插入机床主轴,并调整铣刀的位置,使其与工件加工表面保持一定的距离。
(3)调整铣刀:调整铣刀的切削角度、切削深度和切削速度,以确保加工质量和效率。
(4)铣刀使用:启动机床,使铣刀与工件接触,开始切削。
在切削过程中,注意观察铣刀的切削状态,及时调整切削参数,以保证加工质量。
- 1、下载文档前请自行甄别文档内容的完整性,平台不提供额外的编辑、内容补充、找答案等附加服务。
- 2、"仅部分预览"的文档,不可在线预览部分如存在完整性等问题,可反馈申请退款(可完整预览的文档不适用该条件!)。
- 3、如文档侵犯您的权益,请联系客服反馈,我们会尽快为您处理(人工客服工作时间:9:00-18:30)。
关于P20模具钢的球头铣刀刀轴方向的调查报告摘要:加工诱导残余应力的产生机理是一个复杂的非线性和热力耦合问题。
在加工过程中,切削力和切削温度必须同时考虑。
本文则讨论了刀轴方向和每齿进给的切削速度对切削力、切削温度和残余应力的影响,同时并分析了进给方向倾斜角度对应下的有效切削速度。
切削力可以通过铣削实验获得,而切削温度则是通过有限元法获得。
此外,文章中还讨论了有效切削速度对切削力、切削温度和残余应力的影响及它们之间的关系。
为了更好地让读者理解铣削过程,本文则同时采用了实验和数值方法。
实验数据分析后便得出几个结论。
在进给方向的倾斜角影响有效切削速度,进而将影响切削力、切削温度和残余应力。
为了降低切削力,进给方向倾斜角优先选择是5°至30°。
工件温度的总体趋势呈现抛物线形状,而切屑的温度随进给方向倾斜角的增大而增大。
进给方向残余应力几乎随着每齿进速增加而增加,但放置整个进给速度的范围来看,这并不明显。
为了在工件表面产生残余压应力,倾斜角则优先选择在5°至15°。
关键词:P20模具钢球头铣刀刀轴方向1.引言P20模具钢由于经过适当热处理而获得的良好抗磨损和腐蚀性能则被广泛用于生产注塑模具。
此外,复杂曲面被普遍应用到现代产品设计,这促使了多轴加工的大量使用。
因此,P20模具钢的多轴加工值得特别关注,而且球头立铣刀普遍被应用在模具制造业中。
总体而言,加工后的表面质量(表面粗糙度、加工硬化和残余应力)始终是一个重要的研究领域,因为它对模具寿命和使用性能有显著的影响。
许多有关面粗糙度的研究已经发表。
加工后随之产生的物理因素包括加工硬化和残余应力,而残余应力在决定工件疲劳寿命、耐腐蚀性和尺寸稳定方面有重要作用,故其是评价加工后表面完整性的重要指标之一。
金属切削过程伴随高应变速率和高温耦合问题,并将产生极大应变,同时会产生切削力和切削热,这通常导致非均匀的塑性变形,最终残余应力会诱导产生。
不同进给率和倾斜角对应的残余应力受许多因素的影响,这涉及几何学、运动学和机械学。
产生机理非常复杂。
切削条件在使用不同的进给方向倾斜角度条件下是不同的,这包括刀具和工件之间的接触区域、参与切削切削刃的切削速度、挤压和摩擦环境和传热条件。
最近,有关残余应力的研究取得了重大进展。
威斯纳计算了AISI304正交加工后热影响下的残余应力并讨论了切削速度和切削深度对加工诱导残余应力的影响。
雅克布斯等研究了工件内多个点的位置、轴向切削深度和进给速率对加工诱导残余应力的影响。
有限元法是一种模拟加工过程的有效解决方案;纳斯尔等通过对不锈钢AISI316正交切削的分析,研究了工件材料的影响特性—热导率和软化指数对加工诱导残余应力的影响,并同舒尔茨等研究了刃口半径对残余应力的影响;前者通过对伴随连续切屑形成的奥氏体不锈钢AISI 316L正交干切削,提出了一种基于ABAXQUS/EXPLICIT模拟的有限元模型,而后通过使用ABAQUS/STANDARD,研究了有关标准45号钢残余应力的影响。
赛特和邓主要研究了刀具—切屑交界面摩擦系数和刀具前角对残余应力的影响并详细阐述了正交切削有限元模拟的设定。
黛米等出于考虑工件和球头铣刀之间的位置对残余应力的影响,通过在五轴数控加工机床钛合金用Ti-6AL-4V的球头铣刀铣削加工,研究了能够影响切削速度的工件倾角对残余应力的影响,但该研究是通过指定工件的几何位置而不是改变刀轴方向来实现刀具和工件的相对位置。
苏用了包括许多现存机械加工模型的分析方法,通过螺旋立铣刀铣削和硬车削,建立了有关正交切削残余应力的模型。
从上面的描述来看,有关球头铣刀刀轴方向和残余应力之间关系的研究甚少。
本文旨在研究进给方向刀具倾角并每齿进给量对切削力、切削温度和加工诱导表面残余应力的影响。
研究通过实验和数值方法,分析测定了切削速度、切削力和切削温度,并阐述了切削速度,切削力和切削温度对铣削过程中残余应力的影响。
模具钢通常用于生产复杂曲面的产品,在该材料的多轴加工过程中,倾角是一个重要的因素。
因此,本研究显示了它的重要性和价值。
2.实验和仿真的详细说明2.1. 实验设定该实验使用了机床DMU60P hi-dyn DECKEL MAHO。
工件材料是P20模具钢。
104×75mm工件的顶面被分成30个区域。
实验中使用的双齿刀具是碳化涂层硬质合金立铣刀。
加工坐标系、切削方向和刀具如图1所示。
在坐标系中,z轴与垂直加工表面的方向一致,x轴与垂直刀具进给的方向一致,y轴与进给方向一致。
实验加工过程使用如图2所示。
Kistler 9257 b测力计和电荷放大器用于测量切削力。
Xstress3000用于测量残余应力,X3000应力分析仪由两个对称的探测器组成,用来记录来自两个相反方向的衍射独立信号,每个探测器使用互的方法设置峰值并能保证较高的测量精度。
表1展示了球头立铣刀每齿进给量和倾角的结合条件。
切削深度和行距都是0.5mm。
主轴转速n= 10,000转/分钟,每齿进给量fz 范围是从0.1至0.3mm/z和球头立铣刀倾斜角范围是从0到45。
在进给方向的倾斜角方定义为刀具轴线与垂直于切削速度的平面间的夹度;当倾斜角度为正时,切削条件是逆铣。
该实验采用顺铣加工。
2.2. 有限元模型的设定有限元方法是预测切削过程的一种有效的方法。
因为切削温度的测定是困难的,本文采用了有限元方法是为了获得切削温度的变化规律,这是模拟的首要目的。
工件是固定的,并且刀具移动方式是平移和旋转。
工件与刀具的初始温度为20°。
在仿真过程中,与环境的热交换和热磁通被忽略。
工件材料是P20模具钢,表2给出了材料的化学组成元素。
工件的导热性和比热容都被定义为温度的函数。
工件材料的热发射率值恒定设置为等0.7。
图3则是工件的几何形状设定,以便模拟实际切削过程。
椭圆范围里,曲线和零件边界线围成的部分是切削区域。
Generalized—Johnson–Cook模型用于描述切削过程中的塑形变形。
表达式确定如下。
其中,为工件材料流动应力,是等效塑性应变,是等效塑性应变率,是参考塑性应变。
A、B、C、D、E、M和n是5个材料参数,在使用材料的默认设置常数库时,它们被视为定常量,具体值如表3所示,这与文献【20】中的研究近似一致。
T是当前的温度,Tmelt 是工件材料的熔化温度,并且Troom是室温,在室温下材料常数是确定的。
在上述方程中,Troom 、Tmelt和Tb应是绝对温度。
表4中列出来P20模具钢的物理性能,包括密度,硬度和热性能。
方程2中以公式定义的克罗夫特 - 莱瑟姆标准定理是用来描述仿真过程中切屑的形成。
其中,εf是有效应变,σ1为屈服应力,而D是材料常数。
当最大拉伸住应力沿着塑形应变路径的积分值为D时,工件将产生切屑碎片。
刀具和工件被划为一个个四面体单元的网格。
图4展示了网格划分和工件的边界条件,并且坐标系的设定和图1相同。
网格重新化分技术和局部细化技术适于在工件的网格划分。
工件中所有单元的数量是30000,并且在细化区域网格密度是其外部区域的10000倍。
建模时,球头立铣刀是刚性的,其几何结构如图5所示。
网格的总数为15000;细化区域网格密度是其外部区域的10000倍。
刀轴的投影如图2所示,并且刀轴投影和工件弧形中心线之间的距离设置为0.5,这是为了确保进给间距为0.5mm。
球头立铣刀的最低点与图3所描述的切平面相切,这可以使切削深度为0.5mm。
所有的设置都是为了确保仿真环境与实际切削情况一致。
同时,仿真过程考虑了球头铣刀头热传导条件。
刀具材料的热导率,热容量和发射率被近似设置为常数。
刀具的运动如图6所示,它是由沿进给方向的平移和围绕刀轴的旋转组成,并且其设置与铣削试验中的切削参数一致。
进给速度对应于每齿进给,齿数和主轴转速,它是由下式确定,其中z是齿的数目。
3.有效切削速度的分析由于复杂的几何形状特征,不同球头铣刀切削的刃将参与切割。
在每齿进给相同的情况下,切削刃上切削点的速度因进给方向倾斜角度的不同而不同。
因此,在特殊切削条件下,用来评估实际切削速度意义的有效切削速度是不同的。
进一步的分析如下。
图7演示了计算切削刃各点切削速度的原理。
二维图片可以代替三维的情况。
弧AB、BC和CD是球头立铣刀切削刃在平面中的投影。
以L1为刀具轴线(β=0°),刀尖点是B,切削刃的投影是AD,分布在刀轴两边对称的两条线是AB和BD。
当L 2是刀具轴线(β是正值)时,刀尖的点是C,切削刃的投影仍是AD,分布在刀轴两边对称的两条线是AC和CD。
是切削深度。
切削过程中,在刀尖横截面AD下面的刀刃可能会图7中,aP切到工件。
当虚拟刀齿(signal tooth)在工件中切削时,与未加工表现接触的切削刃通过B点(刀尖和加工表面的切点),并且实际切削刃则被包括在了截面AD以下刀尖和以进给方向为法线(normal)的面之间的区域,在图8中其是A 区域。
图8展示了实际平面及在进给方向上倾斜的球头立铣刀的投影。
当刀轴是图7所示的L1或L2时,球面各点的切削速度用3和4公式计算。
A E是从A点到L2的垂直距离,DF是从D点到L2的垂直距离,ap为切削深度,当β= 0°和R是球头立铣刀的半径时,其等于切削的轴向深度的。
由于切削刃每个点中切削速度不同,有效速度是用来估算单个齿切进切出过程中的速度。
计算详情如下。
图9展示了有效切削速度的计算原理。
AE和BF都垂直于刀轴。
β是进给方向上的倾斜角度,κ是OA和刀轴的夹角,P是弧AB上一点,是切削刃上的一个投影点。
γ是过点P刀具中心O和刀轴之间的夹角。
4.实验和仿真的结果分析4.1.有效切削速度计算结果的详细阐述图10则显示了有效切削速度随进给方向倾角变化的规律。
条形的高度代表了有效切削速度;折线则是用来连接(the practical attachment)有效切削速度的数据点。
随着β的增加,有效切削速度则表现增加的倾向。
因为倾角不同,则参与切削的切削刃的单元不同,有效切削刃的切削半径不同,两个刃之间的有效切削速度不同。
从第三部分的分析可以看出,切削单元上的切削点(each point in the cutting edge element)的切削速度随倾角的增加而变大。
故有效切削速度随倾斜角度的增大而增大。
因此,切削温度、切削力和加工引起的残余应力将受到影响。
4.2.切削力的分析切削力是至关重要的动态物理加工因素。
在每个方向上的最大切削力图11.这三个阶多项式拟合用为了更好地描述切削力的变动用在进料方向的倾斜角度,并所述方法还采用了绘制切割的变化曲线温度和残余应力在下面的文本。
F Z = 0.3 mm / z并且随进给方向倾斜角度的增加有小的变化,Fxmax大约是200 N,而当β= 15°首先下降,然后随进给方向倾斜角度的增加时,Fymax和F z max呈现最小值。