HESD6003-99汽车内饰材料的易燃性测试方法
汽车内饰件燃烧标准 韩国-概述说明以及解释

汽车内饰件燃烧标准韩国-概述说明以及解释1.引言1.1 概述汽车内饰件燃烧标准是指在汽车制造和使用过程中,对车内使用的各种材料和装饰件在燃烧过程中所释放的有害物质进行规范和限制的标准。
这些标准旨在保证汽车内部的安全性和可靠性,以减少因装饰材料燃烧引发的火灾和有毒气体对乘车人员的伤害。
随着汽车产业的快速发展和消费者对汽车安全性和环保性的关注度提高,韩国作为汽车生产大国,也对汽车内饰件燃烧标准进行了制定和实施。
这一举措旨在提高韩国汽车的安全性和可靠性,保证乘车人员的出行安全。
韩国汽车内饰件燃烧标准的制定和实施不仅需要依靠相关法律法规的支持,还需要各相关产业的共同努力和配合。
从设计、生产到销售和使用的各个环节,都需要对汽车内饰件的材料和装饰进行严格的燃烧测试和评估,确保其符合韩国的燃烧标准。
虽然韩国已经建立了一套完善的汽车内饰件燃烧标准体系,但仍然存在一些问题和挑战。
例如,标准的制定和实施过程中可能存在的法规缺失或不完善,以及监督和检测手段的不足。
因此,还需要不断改进和完善相关的法律法规,加强对韩国汽车内饰件燃烧标准的监管和检测,以确保标准的贯彻执行和有效实施。
总之,韩国汽车内饰件燃烧标准的制定和实施是为了保障汽车内部安全和乘车人员的健康,提高韩国汽车产业的竞争力。
韩国应该在继续完善标准体系的同时,加强对标准的监管和检测,进一步提升汽车内饰件的燃烧安全性,为消费者提供更加安全和可靠的汽车产品。
1.2 文章结构文章结构部分的内容可以包括以下内容:文章结构部分旨在介绍本文的整体框架和各个章节的主要内容。
它有助于读者对文章的整体构思有一个清晰的了解,并能有针对性地查找感兴趣的部分。
本文分为引言、正文和结论三个主要部分。
在引言部分,我们会概述本文的主题和背景,引起读者的兴趣。
随后,我们会介绍文章的结构框架,包括各个章节的主题和内容,并说明各个章节的关系。
最后,我们会解释本文的目的,即我们撰写此文的动机和预期达到的效果。
车用内饰材料的燃烧安全性能检测_董激文

( 2) 内饰材料的氧指数 OI≥22% 。对于不同 材料的试验方法应按以下执行: ①针对纺织品及塑 料、橡胶类涂附织物,试验方法按 GB / T 5454 《纺 织品 燃烧性能试验 氧指数法》的规定执行。②其 他塑料材料,试验方法按 GB / T 2406. 2 《塑料燃烧 性能试验方法 氧指数法》的规定执行。
— 43 —
标准
产业用纺织品
总第 273 期
表 1 常见的几种标准和法规
序号 国别 标准代号
标准名称
备注
1 中国 GB 8410—2006[1] 汽车内饰材料的 汽车强制性标准
燃烧特性
2 中国 GB 24407—2012[2] 专用校车安全技 校车强制性标准
术条件
3 中国 TB/T 3237—2010[3] 动车组用内装材 铁道行业标准
造防火通用规范 火标准
13 欧盟 EN 45545-2:2004[13] 轨道车辆材料和元 欧盟轨道车辆防
件防火性能要求 火标准
2. 1 GB 8410—2006 《汽 车 内 饰 材 料 的 燃 烧 特 性》测试
GB 8410—2006 《汽 车 内 饰 材 料 的 燃 烧 特 性》[1]是我国汽车内饰件的强制性标准,适用于所 有汽车内饰材料。此标准非等效采用美国联邦机 动车辆安全标准 FMVSS 571. 302[5]。此标准使用 至今,已经得到汽车业的广泛认可,众多的国产汽 车品牌均采用此标准来测试内饰材料的燃烧性能, 其水平燃烧测试已经成为国内汽车内饰件供销双 方必检的项目。另外,此标准在 2003 年正式成为 我国第一批 3C 产品认证的指定检测项目。 2. 1. 1 测试原理
汽车内饰材料燃烧试验仪技术规格书

汽车车内饰材料燃烧试验仪
基本简介:
1、汽车内饰材料燃烧试验主要是根据国标 GB8410-2006 及美标 FMVSS 571.302 等标准规定的 模拟燃烧性能安全试验项目。
2、汽车内饰材料燃烧试验是采用规定尺寸的本生灯和特定燃气源 (液化石油气或煤气),按 一定的火焰高度和一定的施焰角度对水平状态的汽车内饰材料施焰若干时间,以试品点燃、持续时间和燃烧长度等来评定其可燃性及着火危险性。
3、汽车内饰材料燃烧试验仪主要针对汽车内饰材料的可燃性进行定性评定。
适用于各种类型的汽车内饰材料生产厂家及其材料部件的研究、生产和质检部门,也适用于绝缘材料、工 程塑料或其它固体可燃材料行业。
技术参数:
1、 燃烧器:Φ9.5mm ± 0.3mm 长约 100mm 本生灯一个
2、 试验倾角:本生灯 90°垂直对着水平放置的样品燃烧
3、 火焰高度:20mm ± 2mm 到 100mm±2mm 可调(一般调为 38mm)
4、 施焰时间:0-999.9s±0.1s 可调(一般选择为 15s)
5、 燃烧气体:液化石油气或煤气
6、 温度范围:0~200℃ (显示测试状态下工作室内部温度)
7、 试验过程:试验程序手动控制
8、 参照标准:GB8410-2006,FMVSS 571.302
9、 工作室体积:385mm 宽×204mm 深×360mm 高(约 0.03m3)
10、设备外尺寸:550mm 宽×210mm 深×550mm 高。
探究汽车内饰材料阻燃试验标准及问题建议

探究汽车内饰材料阻燃试验标准及问题建议作者:侯晓佳张月来源:《西部论丛》2018年第10期摘要:本文主要根据国家标准对汽车内饰材料的阻燃试验标准进行了一定的分析,并结合实际试验中存在的问题进行了探讨,提出了几点建议。
检测单位应该在汽车内饰材料的阻燃试验中能够尽早完善存在的问题,提高汽车内饰材料的阻燃性能以及安全性能。
关键词:汽车内饰材料阻燃试验问题建议随着社会的不断发展,人们的物质生活水平逐渐提高,汽车作为主要的交通工具被广泛的应用于人们的日常出行之中,随着汽车使用数量的不断增加,由此所导致的安全事故也在逐年上涨。
在汽车的使用过程中,极易引起火灾而给人们的人身及财产安全带来极大的损害,在发生火灾以后,由于汽车内饰材料的阻燃性能较差,导致火势迅速蔓延,因此,为了更好的降低汽车火灾所带来的危害,必须要完善汽车的内饰材料的阻燃性能。
1.汽车内饰材料的种类在汽车中,包括多种内饰材料,例如汽车坐垫、安全带、装饰性衬板、仪表盘、遮阳板、杂物箱等多种汽车驾驶室内的有机材料,同时还包括减少车辆碰撞时产生的冲击力的缓冲装置等多种单一及复合材料。
根据汽车内饰材料的原料进行分类可以将其分为塑料泡沫类、纤维类以及橡胶类。
泡沫塑料类则主要包括汽车的门板、顶棚等多种内部零件;纤维类则包括汽车驾驶室内的座椅面料、地毯、气囊等纺织品;橡胶类材料主要是汽车轮胎以及内部装饰物的涂层等。
2.汽车内饰材料阻燃试验标准分析众所周知,当发生火灾之后,对人体起到致命性伤害的往往并不是在燃烧过程中产生的热辐射,主要是由于人们吸收过多燃烧过程中产生的浓烟以及烟气的毒气,从而导致机体受到严重的损伤。
在大量的研究调查中发现,真正在火灾中死亡的人员中基本有70%以上的死者都是由于吸入过多的烟尘及毒气昏迷致死的。
在国家相关标准中将内饰材料分为单一材料以及层积复合材料。
根据燃烧速度的不同可以将燃烧试验的指标分为五个到等级。
通过在某检测机构的近四年来的燃烧试验数据进行分析,首先针对不同材料进行完善的分类:单一材料主要包括棉毡、人造革、PVC、尼龙、橡胶、PU、TPE、等材质,在这些材质之中,PU的燃烧速度最快,其他材质的燃烧速度则都在A-0级别之中。
汽车内饰材料的燃烧特性标准规定测试方法

汽车内饰材料的燃烧特性标准规定测试方法青岛众邦仪器有限公司技术部1、将预处理过的汽车内饰材料试样取出,把表面起毛或簇绒的试样平放在平整的台面上,用长度至少为110mm,每25mm内有7~8个光滑圆齿的金属梳在起毛表面上延绒毛相反方向梳两次。
2、在燃气灯的空气进口关闭状态下点燃燃气灯,将火焰按火焰高度标志板调整,使火焰高度为38mm。
在开始第一次实验前,火焰应在此状态下至少稳定地燃烧1min,然后熄灭。
3、将试样暴露面朝下装入试样支架。
安装试样使其两边和一端被U形支架夹住,自由端与U 形支架开口对齐。
当试样宽度不足,U形支架不能夹住试样,或试样自由端柔软和易弯曲会造成不稳定燃烧时,才将试样放在耐热金属线的试样支架上进行燃烧试验。
4、将试样支架推进燃烧箱,试样放在燃烧箱中央,置于水平位置。
在燃气灯空气进口关闭状态下点燃燃气灯,并使火焰高度为38mm,使试样自由端处于火焰中引燃15s,然后熄掉火焰(关闭燃气灯阀门)。
5、火焰从试样自由端起向前燃烧,在传播火焰根部通过第一标线的瞬间开始计时。
注意观察燃烧较快一面的火焰传播情况,计时以火焰传播较快的一面为准。
6、当火焰达到第二标线或者第二标线之前熄灭,则测量从第一标线起到火焰熄灭时的燃烧距离。
燃烧距离是指试样表面或内部已经烧损部分的长度。
7、如果试样的非暴露面经过切割,则应以暴露面的火焰传播速度为准进行计时。
8、燃烧速度的要求不适用于切割试样所形成的表面。
9、如果从计时开始,试样长时间缓慢燃烧,则可以在试验计时20min时中止试验,并记录燃烧时间及燃烧距离。
10、当进行一系列试验或重复试验时,下一次试验前燃烧箱内和试样支架最高温度不应超过30℃。
汽车内饰燃烧试验仪的使用方法及注意事项

汽车内饰燃烧试验仪的使用方法及注意事项汽车内饰燃烧试验仪是一种重要的测试设备,用于评估汽车内饰材料的燃烧性能和安全性。
它能够模拟真实的火灾场景,检测材料在火焰作用下的燃烧特性和烟雾生成情况。
下面将介绍试验仪的使用方法和注意事项,以帮助用户正确操作设备并确保实验的准确性和安全性。
一、设备准备:1、安装环境:选择安装试验仪的环境时,应确保通风良好、无易燃物,并保持适宜的温度和湿度。
2、电源连接:将试验仪连接到稳定可靠的电源,并确保电源电压符合设备要求。
3、校准和检查:在使用之前,应对设备进行校准和检查,确保各项参数和传感器的准确性和正常工作。
二、操作步骤:1、样品准备:根据实验要求,准备好待测试的汽车内饰材料样品,并根据标准规定的尺寸和形状进行切割和准备。
2、样品安装:将样品固定在试验台上,并确保样品的安装位置正确。
注意避免样品之间的干扰和接触。
3、参数设定:根据实验要求和相关标准,设置试验仪的参数,包括点火源的位置、火焰大小和试验时间等。
确保设备在合适的条件下进行试验。
4、操作开始:确认设备的各项设置正确后,启动试验仪,开始试验。
在试验过程中,应密切关注样品的燃烧情况和烟雾生成情况。
5、数据记录:记录试验过程中的关键数据,如燃烧时间、燃烧速率和烟雾密度等。
确保数据的准确性和完整性。
6、结果分析:根据试验结果,评估样品的燃烧性能和烟雾生成情况,并与相关标准进行对比和分析。
三、注意事项:1、安全操作:在使用汽车内饰燃烧试验仪时,应遵循安全操作规程,佩戴个人防护装备,并确保实验室具备相应的安全设施和应急措施。
2、设备维护:定期清洁设备的外部和内部部件,保持设备的干净整洁。
同时,定期对设备进行维护和校准,确保设备的正常运行和准确性。
3、样品选择:选择合适的样品进行试验,确保样品的代表性和一致性。
同时,注意样品的尺寸和形状符合标准要求。
4、参数设置:根据实验要求和标准规定,正确设置试验仪的参数,确保试验的可重复性和准确性。
汽车内饰材料阻燃试验标准探究及问题建议
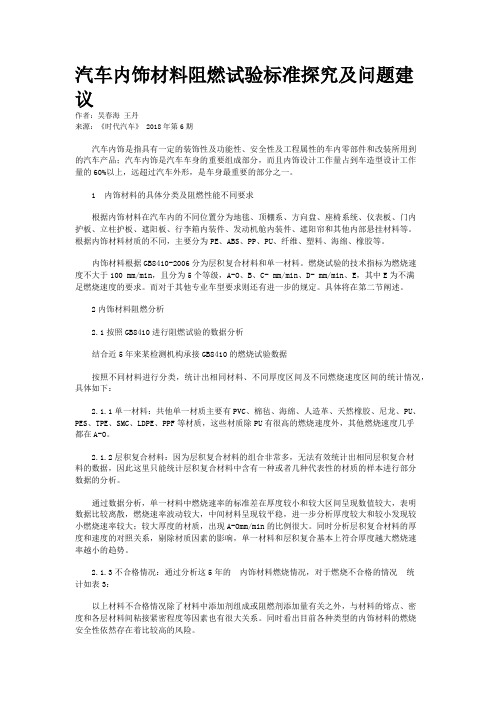
汽车内饰材料阻燃试验标准探究及问题建议作者:吴春海王丹来源:《时代汽车》 2018年第6期汽车内饰是指具有一定的装饰性及功能性、安全性及工程属性的车内零部件和改装所用到的汽车产品;汽车内饰是汽车车身的重要组成部分,而且内饰设计工作量占到车造型设计工作量的60%以上,远超过汽车外形,是车身最重要的部分之一。
1 内饰材料的具体分类及阻燃性能不同要求根据内饰材料在汽车内的不同位置分为地毯、顶棚系、方向盘、座椅系统、仪表板、门内护板、立柱护板、遮阳板、行李箱内装件、发动机舱内装件、遮阳帘和其他内部悬挂材料等。
根据内饰材料材质的不同,主要分为PE、ABS、PP、PU、纤维、塑料、海绵、橡胶等。
内饰材料根据GB8410-2006分为层积复合材料和单一材料。
燃烧试验的技术指标为燃烧速度不大于100 mm/min,且分为5个等级,A-O、B、C- mm/min、D- mm/min、E,其中E为不满足燃烧速度的要求。
而对于其他专业车型要求则还有进一步的规定。
具体将在第二节阐述。
2内饰材料阻燃分析2.1按照GB8410进行阻燃试验的数据分析结合近5年来某检测机构承接GB8410的燃烧试验数据按照不同材料进行分类,统计出相同材料、不同厚度区间及不同燃烧速度区间的统计情况,具体如下:2.1.1单一材料:共他单一材质主要有PVC、棉毡、海绵、人造革、天然橡胶、尼龙、PU、PES、TPE、SMC、LDPE、PPF等材质,这些材质除PU有很高的燃烧速度外,其他燃烧速度几乎都在A-O。
2.1.2层积复合材料:因为层积复合材料的组合非常多,无法有效统计出相同层积复合材料的数据,因此这里只能统计层积复合材料中含有一种或者几种代表性的材质的样本进行部分数据的分析。
通过数据分析,单一材料中燃烧速率的标准差在厚度较小和较大区间呈现数值较大,表明数据比较离散,燃烧速率波动较大,中间材料呈现较平稳,进一步分析厚度较大和较小发现较小燃烧速率较大;较大厚度的材质,出现A-Omm/min的比例很大。
汽车内饰材料及其阻燃测试标准概况
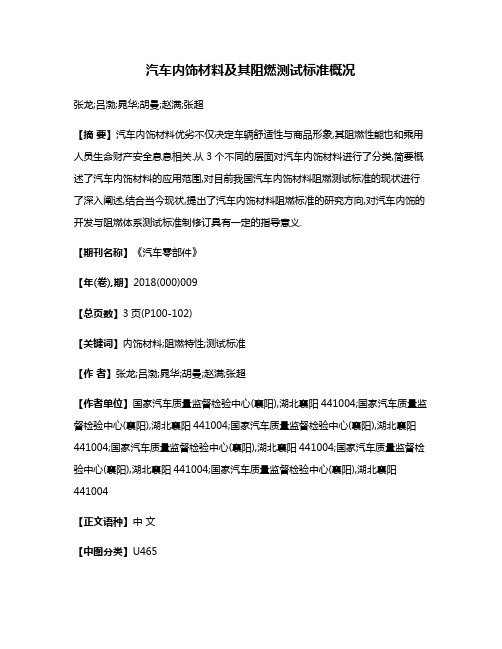
汽车内饰材料及其阻燃测试标准概况张龙;吕渤;晁华;胡曼;赵满;张超【摘要】汽车内饰材料优劣不仅决定车辆舒适性与商品形象,其阻燃性能也和乘用人员生命财产安全息息相关.从3个不同的层面对汽车内饰材料进行了分类,简要概述了汽车内饰材料的应用范围,对目前我国汽车内饰材料阻燃测试标准的现状进行了深入阐述,结合当今现状,提出了汽车内饰材料阻燃标准的研究方向,对汽车内饰的开发与阻燃体系测试标准制修订具有一定的指导意义.【期刊名称】《汽车零部件》【年(卷),期】2018(000)009【总页数】3页(P100-102)【关键词】内饰材料;阻燃特性;测试标准【作者】张龙;吕渤;晁华;胡曼;赵满;张超【作者单位】国家汽车质量监督检验中心(襄阳),湖北襄阳441004;国家汽车质量监督检验中心(襄阳),湖北襄阳441004;国家汽车质量监督检验中心(襄阳),湖北襄阳441004;国家汽车质量监督检验中心(襄阳),湖北襄阳441004;国家汽车质量监督检验中心(襄阳),湖北襄阳441004;国家汽车质量监督检验中心(襄阳),湖北襄阳441004【正文语种】中文【中图分类】U4650 引言随着我国交通技术的高效持续发展与进步,以及人们对车辆的需求和依赖日益加剧,促使我国成为世界上最大的汽车产销国。
为了争得相对应的这一巨大的汽车经济市场,众多整车及配套供应厂商如雨后春笋般涌现,导致汽车领域竞争加剧。
汽车内饰材料在汽车生产成本中占据很大一部分,各厂商为了提高竞争力大多采用压缩成本的低价策略抢占市场,使汽车内饰材料良莠不齐。
而内饰材料的优劣会直接影响到车辆的舒适性及驾乘人员的安全性,研发出既能提升汽车档次增加汽车舒适性,又能确保安全的内饰材料,是汽车开发工程师极力解决的问题。
1 汽车内饰材料的分类汽车内饰材料种类繁多,按原料材质可分为纤维、塑料泡沫、天然橡胶及合成橡胶三大类[1]。
汽车内饰中常用的纤维有棉纤维、羊毛、涤纶、芳纶、PBO、PPS、碳纤维、玻璃纤维等诸多新型纤维,大多应用于地毯、气囊、座椅面料、窗帘、遮阳帘、表面覆盖及装饰位置;塑料因具有密度小、尺寸稳定性好、触感好、耐化学性且易成型等良好的综合性能使其在汽车内饰材料中占比较大,常见的塑料类材料有PP、PVC、PET、ABS、PE、PU、PPO及其他改性塑料,常应用于门内护板、汽车立柱、仪表板、遮阳板等位置;橡胶材料如SBR、EPM、EPDM、TPO等,多应用于密封条,仪表板、地板覆盖物以及织物涂层。
车用内饰材料燃烧安全性能检测研究周倩倩

车用内饰材料燃烧安全性能检测研究周倩倩发布时间:2023-06-03T01:38:17.162Z 来源:《中国科技人才》2023年6期作者:周倩倩[导读] 随着汽车行业的稳健发展,汽车内饰材料受到关注,内饰材料的燃烧性与汽车行驶的安全性息息相关,需要提高重视程度。
车用内饰材料涉及内容众多,主要包括车里的座椅,地毯,吸音棉等,这些材料的燃烧安全性检测均属于纺织品类的检测范畴。
为提升车用内饰材料的安全性能,本文将介绍常规的安全性能测试标准,在此基础上对内饰材料燃烧安全性提出新的要求,以便为车用内饰材料安全性增强提供有益的参考。
迅控检测技术(上海)有限公司 201306摘要:随着汽车行业的稳健发展,汽车内饰材料受到关注,内饰材料的燃烧性与汽车行驶的安全性息息相关,需要提高重视程度。
车用内饰材料涉及内容众多,主要包括车里的座椅,地毯,吸音棉等,这些材料的燃烧安全性检测均属于纺织品类的检测范畴。
为提升车用内饰材料的安全性能,本文将介绍常规的安全性能测试标准,在此基础上对内饰材料燃烧安全性提出新的要求,以便为车用内饰材料安全性增强提供有益的参考。
关键词:安全性能;车用内饰材料;燃烧;性能检测引言:汽车内饰材料对安全性的要求较高,主要是汽车内部材料,特指层积复合材料或者单一性材料,如座垫、座椅靠背以及发动机罩覆盖物等。
此外,还将包括撞车时缓冲装置等材料。
随着社会的进步,车用内饰材料标准越来越严格,内饰件质量的好坏会直接影响车辆的安全性和舒适性,为了满足行业需求,形成了统一的内饰件考核体系,内饰材料燃烧安全性是内饰件考核的重点内容。
1车用内饰材料的质量要求现阶段,车用内饰材料不断发展,质量要求越来越高,主要体现在以下方面:(1)内饰材料常规性能。
结合现实经验可知,内饰材料的常规属性涉及内容多,其中主要囊括原材料成分、物理化学性能等,除此之外,还需考虑老化性能等问题,确保车用内饰材料的应用品质。
(2)内饰材料有害物释放需在正常的标准范围内,如气味、甲醛等气体需得到合理的控制,保障车内环境的同时,提高行车的舒适体验度。
[精品文档]C206汽车内饰材料的可燃性
![[精品文档]C206汽车内饰材料的可燃性](https://img.taocdn.com/s3/m/89681e5132687e21af45b307e87101f69e31fb6f.png)
HES公司总部枥木市研发中心HES1、范围本标准旨在对汽车内隔板所采用的、法律规范有特殊可燃性要求的非金属材料(以下简称“汽车内饰材料”)的可燃性进行说明。
备注:本标准的制订符合日本国第302号FMVSS法规第150号法令与第98号海湾国家标准。
部件典型范例见附件参考表1清单。
2、可燃性汽车内饰材料在进行第3条规定的燃烧试验时,应满足下列要求:2.1 汽车内饰材料应具备以下特征:1)阻燃性2)自熄性,或3)燃烧速度不超过表1中不同发货目的地的规定值,火焰不得蔓延至材料表面。
表1注释(*1):海湾国家指伊朗、伊拉克、沙特阿拉伯、阿拉伯联合酋长国、阿曼、卡塔尔、巴林岛与科威特。
2.2 燃烧应在不超过规定的燃烧速度的条件下达到饱和点,或在336小时材料性能退化时间范围内呈下降趋势。
3、燃烧试验汽车内饰材料的燃烧试验应符合HES D 6003的规定。
4、检验汽车内饰材料在开始进行燃烧试验后,应满足相关可燃性要求。
但是,大批量生产时进行燃烧试验通常比较困难,因此,供应商在向购买商提交燃烧试验数据、并得到购买商审批同意后,可采用下列检查方法。
4.1 若有数据表明材料的燃烧速度下降或燃烧速度无变化,在以后的材料检验过程中应省去材料性能退化处理过程,只要求进行相应的调整处理。
备注:一般说来,材料性能退化会降低氯乙烯、皮革与塑料材料的燃烧速度,并提高发泡材料与织物等的燃烧速度。
4.2 若有数据表明在材料性能退化处理后,燃烧速度上升、然后达到饱和点,则在以后的材料检验过程中应省去材料性能退化处理过程,只要求进行相应的调整处理。
调整处理所用的参考值为规定的燃烧速度减去因材料性能退化导致的燃烧速度增加值。
备注:在计算阻燃材料或自熄灭材料的燃烧速度的增加值时,燃烧速度应设定为零。
4.3 若有数据表明材料性能退化处理导致燃烧速度的逐渐上升,材料性能退化处理时间应延长至336个小时(两周)。
根据燃烧速度是否达到饱和的情况,采取下列步骤:4.3 .1 若有数据表明燃烧速度在336小时的处理时间内达到饱和,后续的材料检验工作应只包括调整处理,而材料性能退化处理则通过采用参考值省略(参考值等于规定值减去材料性能退化导致的燃烧速度的增加值)。
车用内饰纺织材料阻燃性能检测及标准概述

纤·标准论坛Fiber · Standard Forum1 引言随着经济的迅速腾飞,我国已成为世界上的汽车生产与消费大国。
伴随着汽车带来的各种便利,频发的交通事故如火灾等对车内乘员的生命、财产安全威胁同样不容忽视[1]。
汽车内饰用纺织材料是一类包含有汽车内饰零件所用的单一材料或层积复合材料,包括坐垫、座椅套、安全带、头枕、窗帘等,与乘员关系最为密切。
因而为了避免或延缓燃烧的扩展,使乘员能够有一定时间安全地离开发生火灾的车辆,对车用内饰纺织材料阻燃性能的检测评价变得十分重要,这也使得越来越多的国家及地区重视和关注内饰材料的阻燃检测。
因此,本文尝试对我国目前存在的汽车内饰阻燃检测标准进行归纳总结,以期提供一个车用内饰纺织材料阻燃检测标准的综述。
首先介绍了我国现存的相关阻燃检测标准,接着对车用内饰材料的燃烧特性检测进行了分析与比较,具体讨论了氧指数、水平/垂直燃烧、熔融性能等七大阻燃常用指标。
2 汽车内饰材料的阻燃特性测试标准汽车内饰材料应具有良好的阻燃性能,以保证一旦汽车着火后乘客有足够时间离开。
本节将先对我国目前的汽车内饰阻燃检测标准进行总结。
(1)强制国家标准。
2019年10月,强制性国家标准GB 38262—2019《客车内饰材料的燃烧特性》发布,并于2020年7月1日正式实施。
该标准适用于M2、M3类客车内饰材料燃烧特性的评定,同时规定了对客车内饰材料的取样要求、燃烧特性、氧指数、烟密度、烟毒性等试验。
比如,水平燃烧应按GB 8410规定进行试验,而垂直燃烧按GB/T 32086规定试验。
氧指数则按材料种类不同分为3种:纺织、橡胶和塑料应分别按GB/T 5454、GB/T 10707与GB/ T 2406.2—2009进行试验;烟密度按GB/T 8627试验;燃烧性能等级按GB 8624—2012评定等。
除了对纺织材料进行细致规定外,还规定了不同种类内饰材料的燃烧特性,比如对纺织材料和座椅用皮革材料,要求水平燃烧等级不低于B 级,垂直燃速≤100mm/min,烟密度等级≤75%;对弹性软垫材料,则要求水平燃烧等级为A-0mm/min等。
特定种类汽车内饰材料垂直燃烧特性技术

特定种类汽车内饰材料垂直燃烧特性技术1 范围本标准规定了特定种类汽车内饰材料垂直燃烧特性的技术要求和试验方法。
本标准适用于运载超过22名乘客的M3类汽车内饰用窗帘、遮阳帘和/或其它内部悬挂材料,不适用于有站立乘客的城市客车。
2 术语和定义下列术语和定义适用于本文件。
2.1燃烧速度 burning rate燃烧距离与所用时间的比值,单位为毫米每分钟(mm/min)。
2.2内饰材料interior material窗帘、遮阳帘和/或其它内部悬挂材料。
3 技术要求垂直燃烧速度应不大于100 mm/min。
4 试验方法4.1 原理将试样垂直固定到矩形框架上,在燃烧箱中用规定火焰引燃试样,测定试样燃烧距离和所用时间。
4.2 试验装置及器具4.2.1 试样固定架试样固定架应是一个矩形框架,结构如图1所示。
框架高560 mm,由两根间距为150 mm的平行杆连接组成,杆上有固定试样的固定针。
固定针直径应不大于2 mm,长度至少27 mm。
将试样固定架安装在通风橱内相应支架上,保证固定架在试验期间始终处于垂直状态。
为将试样固定在固定针上,并离框架有一段距离,需在固定针附近安装直径为2 mm,高度至少为20 mm的定位柱。
4.2.2 压板使用U形压板保证试样在试样固定架上的垂直平整性。
U形压板应平整且具有刚性,用适当材料制成、尺寸相当于试样固定架尺寸,厚度为1.0 mm±0.1 mm。
在压板的左右两侧钻出直径大约为4 mm的12个圆孔,圆孔位置应保证其圆心间距等于试样固定架上固定针之间的距离(见图1)。
4.2.3 燃气灯燃气灯提供试验火源,其描述和结构需遵照附录A的规定。
4.2.4 燃气燃气灯使用的燃气为工业用丙烷气体、丁烷气体或液化石油气。
4.2.5 标记线白色丝光棉线,线密度最大为50 tex。
单位为毫米1——第三标记线;2——第二标记线;3——第一标记线;4——固定针;5——定位柱;6——试样;7——压板;8——燃气灯。
汽车内饰材料燃烧试验装置的工作条件及指标介绍

汽车内饰材料燃烧试验装置的工作条件及指标介绍汽车内饰材料燃烧试验装置是用来评估汽车内饰材料在火灾情况下的燃烧性能的设备。
该设备的工作条件和指标具有重要的意义,对保障汽车内饰材料的安全性能起到了关键作用。
下面详细介绍汽车内饰材料燃烧试验装置的工作条件以及指标。
1.工作条件:(1)温度条件:汽车内饰材料燃烧试验装置的工作温度应符合相应的标准要求。
一般情况下,试验装置的工作温度应介于20℃到80℃之间,以模拟真实的环境温度。
(2)气氛条件:燃烧试验通常在固定的氧气浓度下进行,以确定材料的燃烧性能。
一般情况下,空气中的氧气浓度约为21%,燃烧试验装置应确保氧气的浓度在此范围内。
(3)湿度条件:汽车内饰材料在潮湿环境下的燃烧性能也是需要考虑的。
湿度条件可以通过控制试验装置内部的湿度来实现。
一般情况下,湿度应保持在30%到70%之间。
(4)试验装置结构条件:燃烧试验装置应具备合适的结构,以满足试验需求和标准要求。
试验装置通常由试样支架、燃烧室、热释放检测仪器等组成,确保试验的精确性和可靠性。
2.指标要求:(1)燃烧性能评价指标:汽车内饰材料燃烧试验装置的主要指标之一是燃烧性能评价指标。
常见的燃烧性能评价指标有燃烧速率、火焰传播速度、烟雾密度等。
这些指标可以通过试验装置中的相应传感器进行测量和分析。
(2)热释放速率指标:热释放速率指标能够反映材料燃烧时释放出的热量,从而评估材料的火灾危险性。
热释放速率指标一般以功率耗散单位面积(kW/m²)来表示。
(3)有毒气体生成指标:有毒气体生成是火灾过程中的一个重要指标,它与人员疏散和逃生的安全性密切相关。
有毒气体生成指标一般以气体浓度或流速来表示,如CO(一氧化碳)、CO₂(二氧化碳)等。
(4)烟雾密度指标:烟雾是火灾中最常见的危险因素之一,能够阻碍人员疏散和逃生,同时降低视线和呼吸空气质量。
烟雾密度指标一般以光传输百分比来表示,如光传输百分比50%(TSP50)。
2017 - 汽车内饰材料阻燃性能
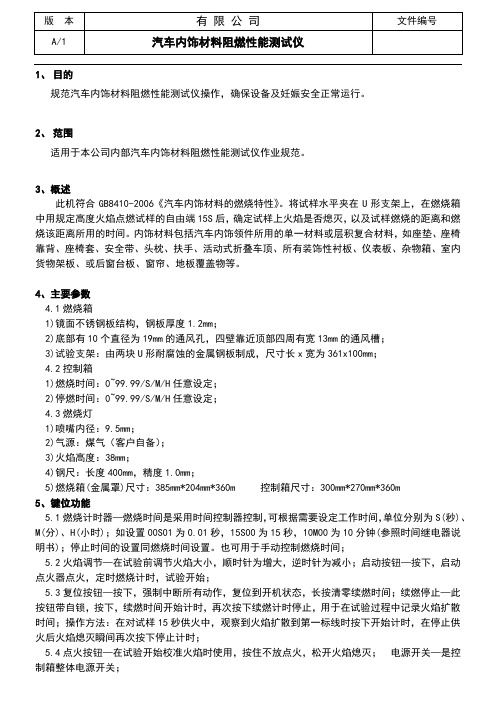
1、目的规范汽车内饰材料阻燃性能测试仪操作,确保设备及妊娠安全正常运行。
2、范围适用于本公司内部汽车内饰材料阻燃性能测试仪作业规范。
3、概述此机符合GB8410-2006《汽车内饰材料的燃烧特性》。
将试样水平夹在U形支架上,在燃烧箱中用规定高度火焰点燃试样的自由端15S后,确定试样上火焰是否熄灭,以及试样燃烧的距离和燃烧该距离所用的时间。
内饰材料包括汽车内饰领件所用的单一材料或层积复合材料,如座垫、座椅靠背、座椅套、安全带、头枕、扶手、活动式折叠车顶、所有装饰性衬板、仪表板、杂物箱、室内货物架板、或后窗台板、窗帘、地板覆盖物等。
4、主要参数4.1燃烧箱1)镜面不锈钢板结构,钢板厚度1.2mm;2)底部有10个直径为19mm的通风孔,四壁靠近顶部四周有宽13mm的通风槽;3)试验支架:由两块U形耐腐蚀的金属钢板制成,尺寸长x宽为361x100mm;4.2控制箱1)燃烧时间:0~99.99/S/M/H任意设定;2)停燃时间:0~99.99/S/M/H任意设定;4.3燃烧灯1)喷嘴内径:9.5mm;2)气源:煤气(客户自备);3)火焰高度:38mm;4)钢尺:长度400mm,精度1.0mm;5)燃烧箱(金属罩)尺寸:385mm*204mm*360m 控制箱尺寸:300mm*270mm*360m5、键位功能5.1燃烧计时器—燃烧时间是采用时间控制器控制,可根据需要设定工作时间,单位分别为S(秒)、M(分)、H(小时);如设置00S01为0.01秒,15S00为15秒,10M00为10分钟(参照时间继电器说明书);停止时间的设置同燃烧时间设置。
也可用于手动控制燃烧时间;5.2火焰调节—在试验前调节火焰大小,顺时针为增大,逆时针为减小;启动按钮—按下,启动点火器点火,定时燃烧计时,试验开始;5.3复位按钮—按下,强制中断所有动作,复位到开机状态,长按清零续燃时间;续燃停止—此按钮带自锁,按下,续燃时间开始计时,再次按下续燃计时停止,用于在试验过程中记录火焰扩散时间;操作方法:在对试样15秒供火中,观察到火焰扩散到第一标线时按下开始计时,在停止供火后火焰熄灭瞬间再次按下停止计时;5.4点火按钮—在试验开始校准火焰时使用,按住不放点火,松开火焰熄灭;电源开关—是控制箱整体电源开关;6、试验方法与要求6.1试样选择:试样的厚度为零件厚度,但不超过12mm。
车用内饰材料的燃烧安全性能检测

车用内饰材料的燃烧安全性能检测董激文;陈蕾;季晓丹【期刊名称】《产业用纺织品》【年(卷),期】2013(31)6【摘要】Nowadays, more and more attention is paid to the burning behaviour of automotive interior materials in the world.Several general burning test methods of the automotive interior materials were introduced and the testing method, testing requirement and jugement were analyzed in detail .Meanwhile, the burning standards of the railway train intherior materials and elements were briefly introduced .% 汽车内饰材料的燃烧性能越来越受到人们的重视。
介绍汽车内饰材料燃烧性能的几个常规测试标准,从测试方法到评价要求一一进行解析;同时,对轨道交通燃烧标准也做了简单介绍。
【总页数】7页(P43-49)【作者】董激文;陈蕾;季晓丹【作者单位】江苏省出入境检验检疫局纺织工业产品检测中心,国家产业用纺织品检测重点实验室,无锡,214101;江苏省出入境检验检疫局纺织工业产品检测中心,国家产业用纺织品检测重点实验室,无锡,214101;江苏省出入境检验检疫局纺织工业产品检测中心,国家产业用纺织品检测重点实验室,无锡,214101【正文语种】中文【中图分类】TS07【相关文献】1.车用内饰材料燃烧安全性能检测 [J], 董激文;陈蕾;季晓丹2.浅谈汽车内饰材料的分类及燃烧特性检测 [J], 陈鲁铁3.浅谈汽车内饰材料的分类及燃烧特性检测 [J], 陈鲁铁;4.汽车用内饰材料物性改善研究 [J], 匡建武;冯李明;丁磊5.电动汽车用锂离子电池安全性能检测浅析 [J], 何岩;高敬迟;张菡;姜克平;王敏因版权原因,仅展示原文概要,查看原文内容请购买。
- 1、下载文档前请自行甄别文档内容的完整性,平台不提供额外的编辑、内容补充、找答案等附加服务。
- 2、"仅部分预览"的文档,不可在线预览部分如存在完整性等问题,可反馈申请退款(可完整预览的文档不适用该条件!)。
- 3、如文档侵犯您的权益,请联系客服反馈,我们会尽快为您处理(人工客服工作时间:9:00-18:30)。
Table 1
Div.
Application
Deterioration(*1)
C onditioning
Application
Treatment
Examples
1 M aterials
Hold in a 100
Hold in a 21
Instrument
exposed to high
constant
2 M aterials other
Hold in a 80
Seat covering,
than 1
constant
Roof lining,
temperature bath
Door lining,
for 0(*2), 50, and
Seat foaming,
100 hours.
Sun visor,
Side lining,
Floor insulator
etc.
3 M aterials
Hold in a 50 x
where
95% RH thermo-
flammability is
hygrostat for 0(*2),
required
50, and 100 hours.
Notes: (*1) If the burning rate continues to increase after 100 hours of deterioration treatment, the treatment time shall be extended until it is confirmed that the burning rate has reached saturation or shows a decrease within 336 hours. The times of plottings within the extension period shall be set so that the plots clearly show the burning trend. (*2) Deterioration treatment for 0 hours means conditioning only. 2.4 Number of Test Pieces The number of test pieces shall be ten for each test, as a rule.
Passenger-com partm ent space
1 2 .7
A Bonded B Test m aterial: A +B
A Bonded
B
1 2 .7
ANon-bonded B Bonded
1 2 .7
Test m aterial: A +B
C
Cut
Test m aterial: A & B +C
2. TESTING CONDITIONS 2.1 Standard Condition of Testing Laboratory The standard condition of a testing laboratory shall, as a rule, be 21oC (70o F) and 50% relative humidity. However, if it is difficult to maintain the testing laboratory in standard condition, the temperature may be 20 + 2oC and a relative humidity, 55 5%. In this case, the test temperature and the relative humidity shall be recorded on the test results sheet. Remarks: A test may be done in other condition of temperature and relative humidity than the specified one, if it is confirmed that the test results are correlated with those in the specified condition, and if HONDA's approval is obtained. 2.2 Preparation of Test Piece 2.2.1 If the thickness of non-metallic automobile interior materials does not exceed 12.7 mm, the thinnest part of the material shall be cut as a test piece. If the material thickness exceeds 12.7 mm, cut the material so that the thickness is not more than 12.7 mm and so that the surface facing the passengercompartment space side is included.
2.2.4 If the width and the length of a test piece available from the product are less than those specified in 2.2.2, the test piece shall be of the largest possible width and/or length. If the width or length is not sufficient for preparing a satisfactory test piece, a piece of the same material and thickness as the product cut to 100 mm x 356 mm may be used as a test piece. 2.2.5 For materials having direction of their properties, cut a test piece in the direction that will provide the most adverse test results. 2.2.6 For seat belts and tubes, cut to 356 mm long to make a test piece. 2.2.7 For products having two or more colors, select the color which is most adverse for testing.
P assenger-com partm ent space
A
A
A N on-bonded
1 2 .7
1 2 .7
B Test m aterial: A
Test m aterial: A Cut
Test m aterial: A and B
2.2.1.2 A composite non-metallic material (non-metallic material which is bonded to other material(s) at all points of contact) shall be prepared as a composite non-metallic material. Remarks: A material fused to other material(s) at every contact point is regarded as bonded material even if adhesives are not used, and sampled as a composite non-metallic material.
2.3 Deterioration Treatment and Conditioning of Test Pieces
Before testing, each test piece shall be subject to the deterioration treatment and conditioning as specified in Table 1. Perform tests immediately after conditioning of the test pieces.
2.2.1.1 A single non-metallic material (non-metallic material which is not bonded to any other material at any point of contact) shall be prepared by itself.
(70 F) x 50% panel
temperature in
temperature bath RH condition at
covering,
compartment
for 0(*2), 50, and least for 24
Defroster
100 .
hours.
garnish, etc.
Remarks: "A + B" and "B + C" are composite non-metallic materials. 2.2.2 Test pieces of 100 mm (4 inches) wide and 356 mm (14 inches) long, as a rule, shall be cut from a product. 2.2.3 When it is not possible to obtain a flat test piece from a product because of surface curvature, the test piece shall be cut from the part with the least curvature. Thickness shall not be more than 12.7 mm at any point of the test piece. If the curvature is too large to provide a satisfac-tory test piece, the test may be done using the test pieces of 100 mm x 356 mm which are the same material and the same thickness as the product.