碱性蚀刻液中铜回收与废液、铜氨废水的循环使用
线路板蚀刻液循环回收系统

线路板蚀刻液循环回收系统一、概述IT产业的印制线路板(PCB)行业是一个对环境污染性较大的行业,他在蚀刻生产工艺过程中会产生大量的失效蚀刻废液,该废液中富含铜(135~165g/L)、氨及氯化铵。
传统处理方法是把失效蚀刻液给回收公司生产硫酸铜,其中大量含铵液体得不到有效利用,造成资源浪费,特别对线路板厂没有一点效益。
为此我司引进国外先进技术及采用专业物料,针对"蚀刻生产工序"专门设计制造本"系统"。
本"系统"采用先进的溶剂萃取电解技术,对废液进行PH值、络合剂及蚀刻液添加剂的浓度进行调整,使其重新恢复蚀刻功能。
对蚀刻工序产出的液体废物(废蚀刻液、一级洗涤水、二级洗涤水)进行有效处理并回收回用,帮助企业达到清洁生产之要求。
本"系统"与蚀刻机连接后自动循环工作,使蚀刻工序成为既达到清洁生产的要求又大大降低成本并获得巨大的经济效益和环保效益,可为企业实现,降耗、环保、获益的可持续发展的目标。
碱性[蚀刻液回收再生系统]设备采用"萃取分离-电沉积铜"工艺。
"萃取分离"是将废蚀刻液中的铜离子分离出来,使废蚀刻液获得再生,再生蚀刻液经调整参数后,返回蚀刻机循环使用。
"电沉积铜"是将萃取分离出来的铜离子电沉积成高纯度电解铜。
碱性[蚀刻液回收再生系统]设备是一套高新环保型、全封闭式系统,无废水、废气及废物排放。
该系统与蚀刻机相互连接后,自动循环运作,进行蚀刻液和氨洗水的回收及再生工作,蚀刻效果稳定;它的性能优越,使用寿命长,能为贵公司创造丰厚的经济效益。
其主要功能和特点表现如下:(1)、将废蚀刻液进行再生,经再生后的蚀刻液可以循环使用;(2)、将废蚀刻液和氨洗水中的铜离子进行回收,还原成高纯度(含铜量99.95%)以上的电解铜,铜回收率100%;(3)、该设备操作维护简单,在安装调试过程中不影响生产,安装调试完毕即可投入使用。
印制板蚀刻废液循环利用及铜回收新技术及设备

《印制板含铜废液再生及铜回收成套设备技术规范》编制说明(征求意见稿)编制单位:深圳市拓鑫环保设备有限公司中国环保机械行业协会2010年7月1 前言印制板含铜废液再生及铜回收成套设备技术规范是工业和信息化部2009年第二批工业行业标准制修订计划中批准制定的行业标准,标准号为2009-2863T-JB。
2009年12月15日工业和信息化部正式下达印制板含铜废液再生及铜回收成套设备技术规范标准,主要起划单位在2010年初开始了印制板含铜废液再生及铜回收技术、工艺路线的调查工作。
在选取了有特点的行业企业后,对含铜废液再生及铜回收成套设备的运行进行了系统的监测;并对污染物治理技术进行了详细的调研。
在这些实验工作与调研的基础上,结合国内、外相关技术要求,开展了本标准的制订工作。
2 制订本标准的必要性到2007年中国大陆从事PCB生产的企业已超过3500家,PCB年产值达到1162.73亿元,增长16%,产量近1.5亿平方米,占世界比例近30%,已成为世界第一大PCB生产国。
但是,PCB生产过程中会附产出多种废物,其中最难处理和处置的是铜蚀刻废液。
其特点一是污染指数极高,属危害品(Hazard);二是产出量大,每平方米PCB需耗蚀刻液2~2.5升,我国PCB业的铜蚀刻废液年产约45-60万立方米;三是内含铜、氨等多种宝贵资源,废液含铜可高达120—190g/L,预计我国PCB行业中以各种形式蚀刻下来的铜在2010年将达到约18万吨,这约是中国铜年产量的20%和世界铜年产量的1%。
对于这样一种既是危害品又是综合资源的废物,若有高效的处理技术则可变废为宝,促进PCB行业的健康成长,处理不当则可能造成严重污染,随着PCB行业增长其排放物已经在“长三角”和“珠三角”地区造成了许多环境污染问题。
甚至影响当地的社会、经济发展。
我国PCB产业规模巨大并仍在快速增长,产生大量铜蚀刻废液,造成铜和其它化学原料的严重浪费和的环境污染。
碱性蚀刻液循环再生技术2013215

碱性蚀刻液循环再生系统建议计划书2013年2月15日一、项目背景近20年来,中国的PCB行业一直保持10-00%的年增长速度,目前有多种规模的PCB企业3500多家,月产量达到1.2亿平方米。
蚀刻是PCB生产中耗药水量较大的工序,也是产生废液和废水最大的工序,一般而言,每生产一平方米正常厚度(18μm)的双面板消耗蚀刻液约为2~3升,并产出废蚀刻液2~3升。
我国PCB行业每月消耗精铜6万吨/月以上,产出的铜蚀刻废液中总铜量在5万吨/月以上,对社会尤其是PCB厂周边地区的水资源和土壤造成了严重污染。
铜是一种存在于土壤及人畜体内的重金属元素,土壤中含量一般在0.2ppm左右,过量的铜会与人畜体内的酶发生沉淀/络合反应,发生酶中毒而丧失生理功能。
自然界中的铜通过水体、植物等转移至人畜体内,使人畜体内的微量元素平衡遭到破坏,导致重金属在体内的不正常积累,产生致病变性、致癌性等结果。
探索铜蚀刻过程的清洁生产技术,使铜蚀刻废液消除在生产过程中,实现在线循环再生,以彻底杜绝污染源及其污染扩散,实现真正意义上的源头治理,既是环境保护部门强制执法的第一选择,也是PCB行业降低生产成本,走可持续发展之路的必然选择。
二、项目运作模式2.1系统设备的提供1)我公司免费提供一成套碱性蚀刻液循环再生设备,废液处理能力100吨/月,设备造价200万元/套。
2)贵公司负责免费提供设备安装运作所需要的场地和相关水电接入到循环再生设备生产车间等条件。
2.2系统设备运作1)设备运作由我公司派专人和工程师24小时配合贵公司运作管理;2)设备运作费用由我公司自行负责;3)再生子液的化学药剂等费用由我公司负责;4)贵公司负责设备和我公司现场工作人员的基本安全,为我公司驻厂工作人员提供食宿。
2.3系统设备维护1)设备维护由我公司负责;2)设备维护费用由我公司自行负责;3)设备日常管理记录由我公司负责。
2.4收益共享分配1)设备运作所产生的效益实现共享原则;2)回收铜贵公司享有按合同的分配比例分配;3)回收铜由我公司回收、处理,每次回收将邀请贵公司人员到场记账互签;4)铜销售价格以当期上海金属交易所价格为准,每次提取铜后我公司7天内将贵公司所得汇入贵公司账户;三、设备工艺原理碱性蚀刻液在线循环技术采用溶剂萃取膜处理—电解还原法,从失效蚀铜液中分离回收铜,同时通过补加药剂,使失效蚀铜液得到有效回收并循环使用,废液回收率利用率100%,铜回收率100%。
碱性蚀刻废液再生新方法研
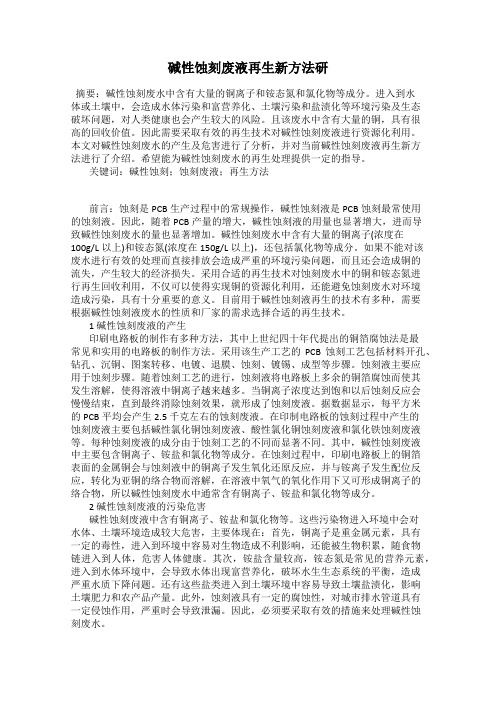
碱性蚀刻废液再生新方法研摘要:碱性蚀刻废水中含有大量的铜离子和铵态氮和氯化物等成分。
进入到水体或土壤中,会造成水体污染和富营养化、土壤污染和盐渍化等环境污染及生态破坏问题,对人类健康也会产生较大的风险。
且该废水中含有大量的铜,具有很高的回收价值。
因此需要采取有效的再生技术对碱性蚀刻废液进行资源化利用。
本文对碱性蚀刻废水的产生及危害进行了分析,并对当前碱性蚀刻废液再生新方法进行了介绍。
希望能为碱性蚀刻废水的再生处理提供一定的指导。
关键词:碱性蚀刻;蚀刻废液;再生方法前言:蚀刻是PCB生产过程中的常规操作,碱性蚀刻液是PCB蚀刻最常使用的蚀刻液。
因此,随着PCB产量的增大,碱性蚀刻液的用量也显著增大,进而导致碱性蚀刻废水的量也显著增加。
碱性蚀刻废水中含有大量的铜离子(浓度在100g/L以上)和铵态氮(浓度在150g/L以上),还包括氯化物等成分。
如果不能对该废水进行有效的处理而直接排放会造成严重的环境污染问题,而且还会造成铜的流失,产生较大的经济损失。
采用合适的再生技术对蚀刻废水中的铜和铵态氮进行再生回收利用,不仅可以使得实现铜的资源化利用,还能避免蚀刻废水对环境造成污染,具有十分重要的意义。
目前用于碱性蚀刻液再生的技术有多种,需要根据碱性蚀刻液废水的性质和厂家的需求选择合适的再生技术。
1 碱性蚀刻废液的产生印刷电路板的制作有多种方法,其中上世纪四十年代提出的铜箔腐蚀法是最常见和实用的电路板的制作方法。
采用该生产工艺的PCB蚀刻工艺包括材料开孔、钻孔、沉铜、图案转移、电镀、退膜、蚀刻、镀锡、成型等步骤。
蚀刻液主要应用于蚀刻步骤。
随着蚀刻工艺的进行,蚀刻液将电路板上多余的铜箔腐蚀而使其发生溶解,使得溶液中铜离子越来越多。
当铜离子浓度达到饱和以后蚀刻反应会慢慢结束,直到最终消除蚀刻效果,就形成了蚀刻废液。
据数据显示,每平方米的PCB平均会产生2.5 千克左右的蚀刻废液。
在印制电路板的蚀刻过程中产生的蚀刻废液主要包括碱性氯化铜蚀刻废液、酸性氯化铜蚀刻废液和氯化铁蚀刻废液等。
碱性蚀刻液循环再生系统

碱性蚀刻液循环再生系统
一、技术简介
碱性蚀刻液循环再生系统是专门针对PCB印制线路板厂生产中产生的碱性蚀刻废液而设计的,采用先进的封闭式自体循环和平行式无损分离技术(CSC-PLS)进行金属铜的分离和蚀刻液的回用,经严格有效的工艺过程,实现了溶液的长期循环再生和100%铜回收率的目标,同时将生产运行成本控制到最低。
该系统与蚀刻机在线闭环连接,自动循环运作。
二、设备说明
1、工艺流程
蚀刻机中溢流出的碱性蚀刻废液进入母液罐,再用泵送入电解槽。
调整主机内铜离子浓度、氯离子浓度和碱度至规定标准,然后通电电解。
取出产品电解铜,将溶液泵至再生子液罐,并检测溶液各离子浓度、pH值,根据检测结果调整各成分含量,调整完毕再次检测,合格后泵入子液罐中待PCB厂家使用。
三、环保指标
◆该系统采用封闭式自体循环和无损分离技术(CSC-PLS)实现了废液的100%回用
◆在整个过程中无固体废弃物、废液、废气产生
◆完全符合国家清洁生产、节能减排的环保要求
四、特点及优势
◆本系统采用PLS平行式无损分离技术,整个过程无需使用任何萃取剂、添加剂,真正实现了对废蚀刻液的无损分离,保证了蚀刻液回用的质量。
◆本系统采用CSC封闭式自体循环技术对废蚀刻液进行循环再生,整个过程既不带入其他外来物质,也没有产生有害物质,更不会破坏溶液成分,再生蚀刻液性能可以与新购子液相媲美,特别适用于高精度PCB 板制作。
◆该系统稳定性强,设备操作简便,便于维护。
采用一站式闭环控制系统,使设备运行更加可靠,运行成本为同行业最低。
印制板蚀刻废液循环利用及铜回收新技术及设备
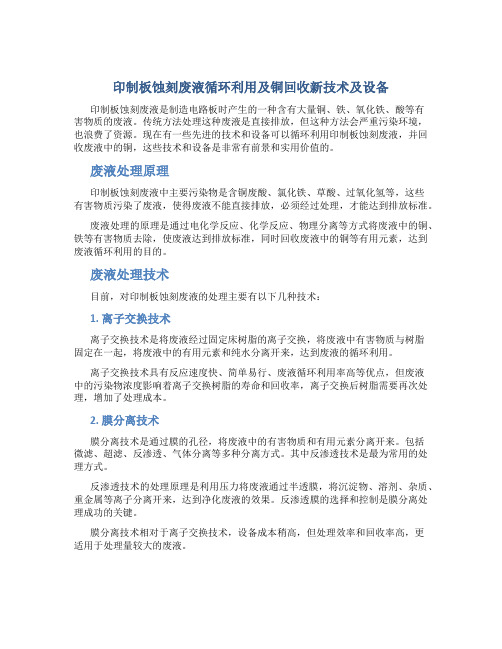
印制板蚀刻废液循环利用及铜回收新技术及设备印制板蚀刻废液是制造电路板时产生的一种含有大量铜、铁、氧化铁、酸等有害物质的废液。
传统方法处理这种废液是直接排放,但这种方法会严重污染环境,也浪费了资源。
现在有一些先进的技术和设备可以循环利用印制板蚀刻废液,并回收废液中的铜,这些技术和设备是非常有前景和实用价值的。
废液处理原理印制板蚀刻废液中主要污染物是含铜废酸、氯化铁、草酸、过氧化氢等,这些有害物质污染了废液,使得废液不能直接排放,必须经过处理,才能达到排放标准。
废液处理的原理是通过电化学反应、化学反应、物理分离等方式将废液中的铜、铁等有害物质去除,使废液达到排放标准,同时回收废液中的铜等有用元素,达到废液循环利用的目的。
废液处理技术目前,对印制板蚀刻废液的处理主要有以下几种技术:1. 离子交换技术离子交换技术是将废液经过固定床树脂的离子交换,将废液中有害物质与树脂固定在一起,将废液中的有用元素和纯水分离开来,达到废液的循环利用。
离子交换技术具有反应速度快、简单易行、废液循环利用率高等优点,但废液中的污染物浓度影响着离子交换树脂的寿命和回收率,离子交换后树脂需要再次处理,增加了处理成本。
2. 膜分离技术膜分离技术是通过膜的孔径,将废液中的有害物质和有用元素分离开来。
包括微滤、超滤、反渗透、气体分离等多种分离方式。
其中反渗透技术是最为常用的处理方式。
反渗透技术的处理原理是利用压力将废液通过半透膜,将沉淀物、溶剂、杂质、重金属等离子分离开来,达到净化废液的效果。
反渗透膜的选择和控制是膜分离处理成功的关键。
膜分离技术相对于离子交换技术,设备成本稍高,但处理效率和回收率高,更适用于处理量较大的废液。
3. 微生物处理技术微生物处理技术是利用微生物的去除能力,将有害物质降解为无害物质,是一种较为有潜力的处理技术。
这种技术存在工艺简单、处理成本低等优点。
目前,微生物处理技术主要包括好氧微生物法、厌氧微生物法和真菌生物法等,其中好氧微生物法的效果较好。
碱性蚀刻液再生循环处理系统介绍
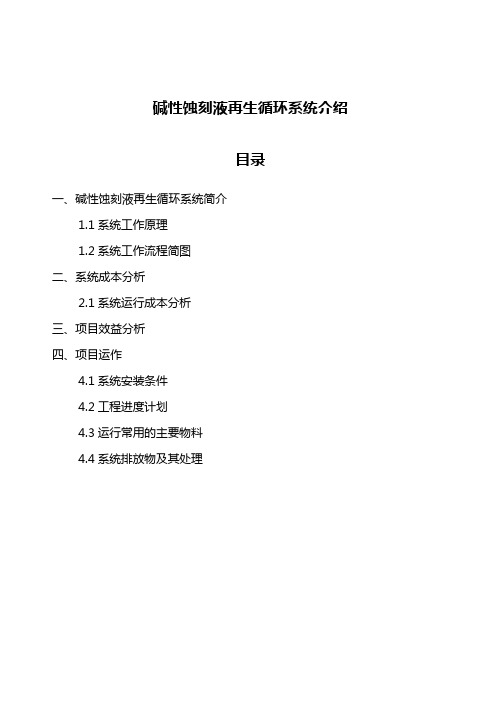
碱性蚀刻液再生循环系统介绍目录一、碱性蚀刻液再生循环系统简介1.1系统工作原理1.2系统工作流程简图二、系统成本分析2.1系统运行成本分析三、项目效益分析四、项目运作4.1系统安装条件4.2工程进度计划4.3运行常用的主要物料4.4系统排放物及其处理一、碱性蚀刻液再生循环系统简介1.1系统工作原理本系统采用多级萃取-反萃及电解再生工艺组合,可实现碱性蚀刻液完全回用零排放,是将碱性蚀刻废液提铜处理和再生利用进行组合的系统设备,可根据需要调整再生液的品质,完全确保PCB企业蚀刻工序产品质量的稳定。
该系统主要由以下部分组成:铜分离系统、铜提取系统、存储及调配系统。
1)铜分离系统:是将废蚀刻液中的铜离子通过铜吸附剂从废液中无损分离吸取铜离子,并将铜离子转移到铜提取系统,释放铜离子后的吸铜剂再回到此系统循环工作。
2)铜提取系统:吸铜剂中的铜离子释放到此系统中,通过电解提取高纯度产品铜。
3)存储及调配系统:系统将已降低铜含量的蚀刻液通过组份调节,使Cu2+、Cl-、PH 值及相关工艺元素达至生产所需要求,待生产所用。
整个系统工作时无排放封闭式循环运行。
系统工作时,只需在碱性蚀刻设备的溢流排出口接一管道,直接将废液引入再生循环设备中,经过系统处理后,再通过自动添加系统循环回到蚀刻工序,整个系统无排放封闭式循环运行,系统设备与生产线对接时,产线不需停机。
1.2系统工作流程简图碱性蚀刻液在线循环技术工艺原理图本项目所用的碱性蚀刻液再生循环系统,已通过市场实际使用认可,可实现PCB碱性蚀刻废液零排放,达到清洁生产的要求:1)碱性蚀刻废液全部转变为循环再生使用的蚀刻新液及金属铜板。
2)由于实现碱性蚀刻废液的零排放,大量原有处理工艺浪费的化工原料被全部循环再生使用,综合处理成本更低,效益大幅提升,更利于污染物总体排放量的控制。
二、系统成本分析2.1系统运行成本分析(废液处理量100吨/月)生产物料成本明细表(元/吨铜)项目名称吨铜耗量价格运营支出/吨铜1 萃取剂16L 220元/L 3520元2 硫酸(98%)100kg 1.6元/ kg 160元3 电费3500度0.7元/度2450元4 水10m35元/ m350元5 液氨0.2吨5500元/吨1100元6 蚀刻盐0.2吨2000元/吨400元7 添加剂20L 15元/L 300元8 阳极片0.33片6000元/片1980元9 阴极片(铜片)5片100元/片(抵后)500元9 设备维护100元10 人工工资3人4500元/人1350元吨铜总成本11910元/吨三、项目效益分析铜价假设为45000元/吨计算(实际价格参照当期上海有色金属交易网报价),以每月100吨废液(含铜10%质量比)为例,对系统作经济效益分析:1)月产铜量:100吨×10%=10吨。
PCB碱性蚀刻液的资源回收及高氨氮废水的处理、应用
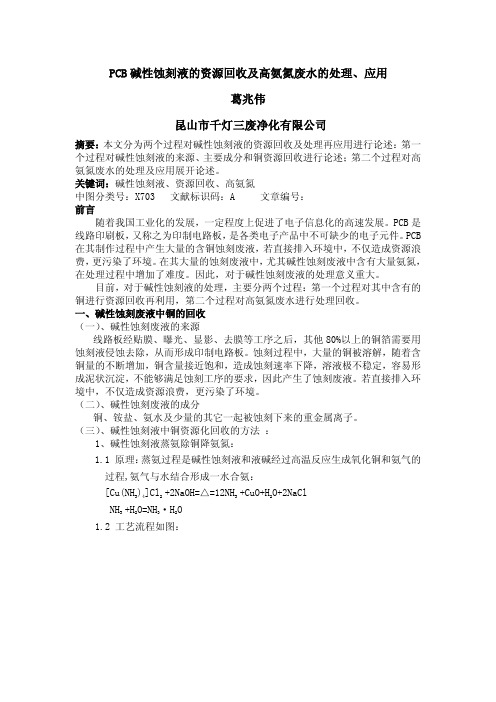
液销往PCB线路板厂,重新回到蚀刻生产线。 4、碱性蚀刻液再生的意义: 综上,本文提出的碱性蚀刻液再生的方法,不仅把碱性蚀刻废液中含有的铜
进行了资源回收,而且能够使全部废液再生,整个过程无废水排放;再生过程中 只需添加氨水和碳酸氢铵的添加剂来补充期间消耗的铵根,生产的碱性蚀刻液又 回归PCB线路板厂,达到了资源回收以及循环经济。 三、结论
综上所述,通过碱性蚀刻液蒸氨或酸碱中和生产铜产品,得到氧化铜、硫 酸铜或碱式氯化铜等产品,进行铜产品的资源回收。而分离铜后的高氨氮废水, 通过三效蒸发浓缩,得到氯化铵产品进行销售,馏出水通过RO膜后生产去离子水, 回用于生产,一方面减少了废水的排放,另一方面节约了水资源。
1.蒸发浓缩: 1.1 碱性蚀刻液通过一系列物理、化学反应后,得到高氨氮废水。 1.2 蒸发浓缩原理: 1.2.1 蒸发器降膜结构: 采用降膜结构蒸发器流程如下,溶液进入蒸发器顶部的进料室,靠分布器将 溶液平均分配到各传热管,并在管内壁形成连续向下流动的液膜。溶液受热蒸发, 蒸发出来的二次蒸汽沿管子中心与管壁液膜同方向向下流动,随后流入蒸发器下 部的分离室,蒸汽与物料在此分离。物料进入泵吸入口,蒸汽进入分离器进一步 除去挟带的液滴。第一效经过分离后的蒸汽作为第二效的加热蒸汽使用,第二效 经过分离后的蒸汽作为第三效的加热蒸汽使用,第三效的二次蒸汽去冷凝器。因 为二次蒸汽得到充分利用,故三效蒸发器的耗汽量为单效的三分之一。溶液流向 与蒸汽相反,首先进入第三效,顺次进入第二效,第一效,浓缩液从第一效排出。 1.2.2 蒸发器升膜结构: 采用升膜结构蒸发器流程如下,高氨氮溶液通过板式换热器时被馏出水进行 预热后进入一效蒸发器,进入一效蒸发器的加热蒸汽加热由提升泵从板换预热器 抽到一效蒸发器的物料,加热蒸汽冷凝成冷凝水进入冷凝水罐,物料经过加热产 生二次蒸汽,二次蒸汽将物料带到第一效分离器,经过分离器分离成热物料和二
碱性蚀刻液铜回收工艺

碱性蚀刻液铜回收工艺
简介:
碱性蚀刻液是用蚀刻线路板铜的药液,主要成分:氨水+氯化铵+添加剂。
一般生产车间排出的废液含铜量为110~130g/l。
此废液回收价值高,收回方法,其一:萃取电解法。
此法利用萃取剂萃取出铜离子之后,用硫酸铜溶液做电解液进行电解。
其优点在于电解出来的铜纯度高,一般电解出来的铜都可以达到三个九以上。
以下
是萃取电解的工艺流程
注明:
1.萃取槽,萃取剂和原液混合萃取,然后分相,上层为含铜萃液,下层为萃余液。
2.水洗槽1主要是水洗含铜萃液中的氨根离子,称洗氨。
3.反萃槽,是用硫酸溶液将含铜萃液中的铜洗出来,形成硫酸铜溶液即电解液。
4.水洗槽2,主要是用水洗掉萃取液中残留的硫酸根。
称洗硫。
5.隔油缸,油其实是指残留的萃取剂。
6.本工艺,蚀刻液循环,萃取剂循环,电解液循环。
洗水排出处理。
酸碱性蚀刻液再生及铜回收系统
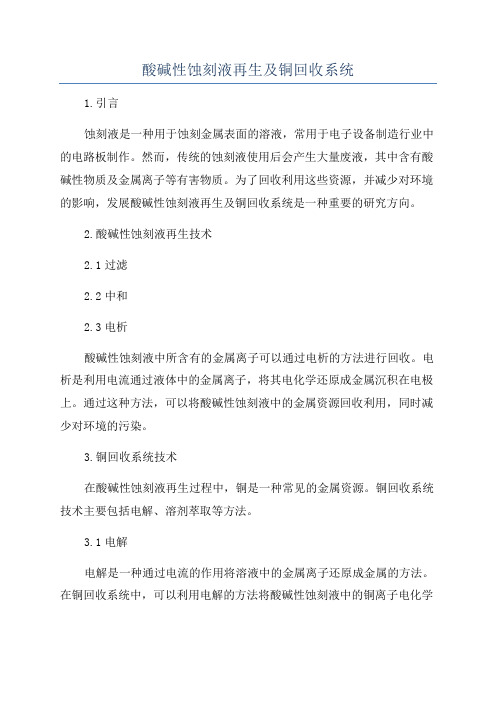
酸碱性蚀刻液再生及铜回收系统1.引言蚀刻液是一种用于蚀刻金属表面的溶液,常用于电子设备制造行业中的电路板制作。
然而,传统的蚀刻液使用后会产生大量废液,其中含有酸碱性物质及金属离子等有害物质。
为了回收利用这些资源,并减少对环境的影响,发展酸碱性蚀刻液再生及铜回收系统是一种重要的研究方向。
2.酸碱性蚀刻液再生技术2.1过滤2.2中和2.3电析酸碱性蚀刻液中所含有的金属离子可以通过电析的方法进行回收。
电析是利用电流通过液体中的金属离子,将其电化学还原成金属沉积在电极上。
通过这种方法,可以将酸碱性蚀刻液中的金属资源回收利用,同时减少对环境的污染。
3.铜回收系统技术在酸碱性蚀刻液再生过程中,铜是一种常见的金属资源。
铜回收系统技术主要包括电解、溶剂萃取等方法。
3.1电解电解是一种通过电流的作用将溶液中的金属离子还原成金属的方法。
在铜回收系统中,可以利用电解的方法将酸碱性蚀刻液中的铜离子电化学还原成铜金属。
这种方法具有高效、环保的特点,能够有效地回收利用酸碱性蚀刻液中的铜资源。
3.2溶剂萃取溶剂萃取是通过溶剂选择性地吸附和分离溶液中的特定成分的方法。
适当选择合适的溶剂,可以实现对酸碱性蚀刻液中的铜离子的吸附和回收。
这种方法具有操作简单、回收率高的特点,是一种常用的铜回收系统技术。
4.酸碱性蚀刻液再生及铜回收系统的优势4.1资源回收利用通过再生技术可以将酸碱性蚀刻液中的酸碱物质和金属离子回收利用,减少对自然资源的消耗。
4.2环境友好再生系统能够有效地处理和减少酸碱性蚀刻液中的废液,减少对环境的污染。
4.3经济效益通过再生和回收技术,可以降低酸碱性蚀刻液的成本,提高资源利用效率,从而带来经济效益。
5.结论酸碱性蚀刻液再生及铜回收系统是一种重要的研究方向,通过过滤、中和和电析等方法可以实现酸碱性蚀刻液的再生和回收利用。
通过电解和溶剂萃取等方法可以实现酸碱性蚀刻液中的铜离子的回收。
这些技术具有资源回收利用、环境友好和经济效益等优势,对于推动电子设备制造行业的可持续发展具有重要意义。
碱性蚀刻液循环再生系统

套
项
36
钛板组件
1050×660mm
组
37
阴极片组件
1065×714mm
组
3
40
抽风管道工程 废气处理塔组件
项 2440×1380×1200 组
41
电气及管道工程
项
42
电控组件
1200×800×400 组
43
电控系统
配电组件
800×600×400
组
44
50
储存设备
电气工程 大型存储系统
项
PT-10000L
套
51
中型存储系统
PT-6000L
套
1 1
1
1
32000
1
1
1
1
28000
1
1
1
1
1
31000
1
1
1
1
5
115
5
5 102000
4
10 4 1 5 1 1
60
300000
55
11000
1
1 12000
1
1 1
1
23000
1
4
57000
2
以客为尊、实现9双913赢!
五、设备清单、造价(100 吨/月废液处理规模)
序号 成品名称
1
2
铜
3
分
解
4
系
统
5
6
7
半成品名称
规格
单位 单套数量 金额
废液中转缸组件
1490×600×650 组
1
3500
再生中转缸组件
1810×1105×650 组
碱性蚀刻液中铜回收与废液铜氨废水的循环使用

碱性蚀刻液中铜回收与废液铜氨废水的循环使用碱性蚀刻液是一种用于蚀刻金属的溶液,其中包含有机酸、无机碱和助剂等成分。
在电子工业和光学工业中,铜是一种常见的材料,因此碱性蚀刻液中铜的回收和废液、铜氨废水的循环使用对于节约资源和保护环境具有重要意义。
铜的回收主要通过两个步骤完成:溶解铜和沉淀回收。
在碱性蚀刻液中,铜往往以离子的形式存在,因此可以通过加入还原剂将铜离子还原为金属铜。
还原剂常用的有二氧化硫、亚硫酸氢钠等。
还原反应可以用如下方程式表示:Cu2++2e-->Cu还原反应后,金属铜会从溶液中沉淀下来。
回收的金属铜可以用于再生和再利用。
在回收铜的过程中,也会产生一定量的废液和铜氨废水。
这些废液和铜氨废水富含有机酸、无机碱以及其他含有金属离子的溶质。
为了循环利用这些废液和铜氨废水,可以采用以下步骤:1.废液的中和:废液中的有机酸和无机碱可以互相中和,生成一定量的水和盐。
中和反应需要适当的酸碱指示剂来监测中和的程度,以确保中和反应完全。
2.沉淀回收:通过加入适当的还原剂,将溶液中的金属离子还原为金属沉淀,再通过过滤或离心等方法将沉淀分离出来。
沉淀可以通过烘干和熔融等方法得到金属的纯度较高的形态。
3.废液的再处理:在回收过程中生成的中和盐可以进一步处理,以从中提取有价值的化学物质或进行其他处理方式。
例如,可以通过晶体生长技术,将盐析出为晶体,再进行相应的晶体提纯工艺。
4.循环水系统:对于铜氨废水,可以采用循环水系统来回收和再利用。
该系统包括废水处理装置和循环水泵等设备,通过处理废水中的氨、铜离子和其他污染物,将废水进行处理后,再循环使用于蚀刻工艺中。
通过铜的回收和废液、铜氨废水的循环使用,可以减少资源的消耗和废液的排放,实现对环境的保护和可持续发展的要求。
同时,回收金属铜也可以带来经济效益,提高蚀刻液的利用率和生产效率。
因此,在碱性蚀刻液中铜回收和废液、铜氨废水的循环使用方面的研究和应用有着广阔的发展前景。
- 1、下载文档前请自行甄别文档内容的完整性,平台不提供额外的编辑、内容补充、找答案等附加服务。
- 2、"仅部分预览"的文档,不可在线预览部分如存在完整性等问题,可反馈申请退款(可完整预览的文档不适用该条件!)。
- 3、如文档侵犯您的权益,请联系客服反馈,我们会尽快为您处理(人工客服工作时间:9:00-18:30)。
碱性蚀刻液中铜回收与废液、铜氨废水的循环使用目前碱性蚀刻液由危险废物回收商进行资源化回收铜,生产硫酸铜产品,没有对氨进行回收和处理,也不能回收失效的蚀刻液和铜氨废水的循环使用,对环境有一定的影响,且导致运输过程的能源消耗和成本增加。
为响应国家“清洁生产、变废为宝、发展循环经济、创建节约型社会”的号召,计划安装“在线含铜废蚀刻液的资源化回收”成套设备。
2009年1~7月份含铜废蚀刻液产生量为:月份Jan-09Feb-09Mar-09Apr-09May-09Jun-09350504656543503566蚀刻废液量(T)碱性蚀刻废液和后面的水洗产生的铜氨废水为本公司主要NH3-N的排放源。
二、减少末端处理前的污染因子—NH3-N1、氨氮对环境的影响氮素物质对水体环境和人类都具有很大的危害,主要表现在以下几个方面:氨氮会消耗水体中的溶解氧;氨氮会与氯反应生成氯胺或氮气,增加氯的用量;含氮化合物对人和其它生物有毒害作用:①氨氮对鱼类有毒害作用;②NO3-和NO2-可被转化为亚硝胺——一种“三致”物质;③水中NO3-高,可导致婴儿患变性血色蛋白症——“Bluebaby”;加速水体的“富营养化”过程;所谓“富营养化”就是指水中的藻类大量繁殖而引起水质恶化,其主要因子是N和P(尤其是P);解决的办法主要就是要严格控制污染源,降低排入水环境的废水中的N、P含量。
2、线路板废水中的氨氮来源目前碱性蚀刻缸1) Cu2+: 125~145~165g/L 2) Clˉ: 4.0~4.8~5.3N3) PH值: 8.0~8.4~8.8(PH计读数) 4)比重: 1.165~1.190~1.215)温度: 47~53℃6)缸体积1025L7)补充液配制:Clˉ4.0~5.3N ; OHˉ3.4~3.9N单耗:(1) 蚀板盐:60Kg/ K Sq.Ft(2) 蚀板液210LT/ K Sq.Ft。
实际补充蚀刻子液2.5~3吨/天。
氨水洗缸1) NH3.H2O: 20% , 30~45~60g/L2)缸体积95L单耗:氨水95LT/ K Sq.Ft碱性蚀刻生产线的月产量:由此可见:按照理论计算,月产30万平方英尺的蚀刻线排放浓的蚀刻废液大约:300,000*210/1000 =63,000L=63m3=63*1.19=75吨,大约含铜=75*145=10807Kg=10.8吨/月=129.6吨/年。
按照2008年实际消耗的蚀刻量,推算月产30万平方英尺的蚀刻线的实际量为840吨蚀刻液/年,大约可产生97吨电解铜/年,小于标准单耗,说明生产控制良好。
消耗的氨水量大约为:950*30*12=342000Kg=342吨三、废液回收利用的工艺选择1、回收技术现状及发展方向铜回收中化学法常见在危险品回收公司使用,电解法常见在线路板公司自行回收。
特点如下:2、常规的工艺特点针对一条碱性时刻拉(300K SqFt)资源化回收的设计。
在实际应用中主要在反萃取后有机相中夹滞了大量的硫酸根(SO2-2),影响萃取效果以及再生的蚀刻液的质量,严重时甚至影响萃取工艺控制操作,被迫停产,清理萃取槽,并使残液也不能再生回用。
同时,还存在反萃液中夹滞大量氯化物进入电解槽,造成电耗高,腐蚀电极,并产生氯气,影响环境。
比较好的工艺。
如:蚀刻液一萃取一电积(ET-SX-EW)再生闭路循环工艺,从根本上解决了原有工艺中存在硫酸根(SO42-)和氯离子(CI-)夹带问题,克服了原工艺存在的缺陷。
使用本工艺处理失效蚀刻液时,可随意调节,在被萃取液中能萃取一定量的铜或全部萃取铜,萃取出来的铜,可以用电解法生产紫铜板或用生产硫酸铜。
萃取后的残液中铵(NH4CI、(NH4)2HCO3其本无损失,可再生后返回蚀刻系统循环使用。
采用国内外先进的萃取剂和萃取设备,即可减少夹带有机相造成萃取剂损失的问题,保持萃取剂消耗少的水平,又保证有机相与水相的稳定比例状态。
因此使用本工艺可减少投资,保持操作稳定运行,并可为企业取得较大的经济利益。
失效蚀刻液经过滤除什物后,直接进入萃取系统用萃取剂提铜,分离后的萃取液经反萃处理后,提取反萃取液中的铜(反萃取液送到电解槽中用连续电解沉积工艺生产紫铜板)。
也可通过结晶生产硫酸铜晶体。
萃取后的残液(蚀刻液)经调整PH及添加少量速蚀添加剂再生成新的蚀刻溶液,返回蚀刻槽中循环使用。
萃取剂在萃取系统中也可循环使用。
1、目前一些公司使用回收系统存在如下问题:1)萃取剂有萃氨反应。
因此积累后产生沉淀。
氨进入电沉积槽。
2)无洗氯离子洗涤槽,而是用漂洗水再萃取。
因此夹滞氯化氨进入反萃取槽造成电解槽中氯离子积累。
影响钛阳极及阴极铜质量。
3)萃取剂水洗分层不理想;慢及水有不清现象。
4)反萃取后夹滞有硫酸根(SO4-2)未进行再生洗涤的有机相,因此硫酸根会进入再生蚀刻液中中,积累较多后沉淀。
2、拟用新工艺及新萃取剂,采用全萃取铜工艺,配制新的蚀刻液不含铜,百分百回收。
1)采用洗氯离子及洗硫酸根离子新的工艺。
2)采用永久阳极(钛涂铱)及永久纯钛阴板。
纯钛板阴极比不锈钢容易剥落,不上镀,阴极铜取出槽后,水冲洗冷却即分离,反复使用20年以上,因此不须外购始极铜片。
3)采用新萃取剂,最大优点:耐水洗,及耐高酸反萃,水洗分层快清晰。
价格是MX-80或NC-300.60%。
缺点是萃取容量较低。
4)新萃取剂无萃取氨反应。
因此氨不进入电解槽。
(1) 萃取后电解法回收铜的设备(包括萃取设备+中间槽、电解槽、电极、控制器、泵、连接管道、地面处理、通风等);估计为60~70g/L的铜含量(因为氨水洗进入其中),实际废蚀刻液量:5吨/天左右。
或分离氨水洗,平均125~165g/L的铜含量,实际废蚀刻液:2.5~3吨/天左右。
(2) 100%蚀刻液(2.5~3吨/天)回生产线(包括氨水洗),要求中间槽容积满足连续生产。
3、本回收系统的特点循环蚀刻液再生系统,乃专门为电子线路板的碱性蚀刻工序而设,当此系统与碱性蚀板机连接后,便能有如下表现:◆将已蚀板的碱性蚀刻液还原再生,经再生后的碱性蚀刻液可以循环再用;◆将已蚀板的碱性蚀刻液内的铜离子进行回收,铜离子将会还原成为有价值的金属铜;◆将蚀刻后段水洗的水进行回收,经回收后的水亦可循环再用。
A.采用本系统后的蚀刻工序:◆把在本系统已准备的碱性蚀刻液注入蚀刻生产线;◆在蚀刻生产过程中,蚀刻液中的含铜量不断增加;◆把在蚀刻完成后的高含铜量的蚀刻液及一级水洗所排放的清洗水输入本系统;◆本系统将高含铜量的蚀刻液及清洗水循环再生,并从中萃取铜;◆把再生的碱性蚀刻液及清洗水注入蚀刻生产线。
B.采用本系统后及未采用本系统的比较:•低投资额 -只须投入较低投资,便能实时使用此系统;•实时回报 -由系统启动开始,公司便实时节省购买蚀刻液的费用;•保护环境 -蚀刻液及清洗水循环再用,非常环保。
6、设备与安装规格四、综合利用技术的环保性1、可实现减少90%的蚀刻液排放;2、节约资源-蚀刻子液达到70%;3、可实现减少70~90%的铜氨废水液排放。
五、经济效益设备投资83万元,基建及外围管道投资35万元,项目投资总额为118万元。
一、经济效益——我国每年可有47亿元的铜被回收1.铜回收经济指数月生产线路板2万平方米的PCB生产企业,日排出废含铜蚀刻液2500升,含铜量为140g/L,日回收350kg金属铜。
350kg×300(天)/年=105吨/年电解铜,电解铜市价为35000元/吨,每年可节约367.5万元。
每吨铜回收成本为0.47万元,则每年105吨可节约50万元(0.47万元/吨铜,包括药水、水电、人工、铜片等)2.蚀刻子液再生经济指数按日排出废蚀刻液2500升,日购蚀刻子液2500升×(每升市价为1.6元)日消耗子液的费用4000元。
现经该设备的再生蚀刻液,只需添加少量氨水、氯化铵及添加剂,蚀刻子液合计消耗原料1250元/日。
每年可节约费用为:4000元/日-1250元/日=2750元×300天/年=82.5万元/年3.经济总指数年铜产值367.5万元-生产成本50万元=317.5万元。
蚀刻液节约成本82.5万元/年317.5万元+82.5万元=年创纯利润400万元。
4.设备投资成本整套设备的价格为170万元,回收周期为7个月~8个月。
5.设备的占地面积占地面积(包括化验室)总共约为150平方米左右。
二、环保和社会效益据中国印制电路行业协会的统计调查,我国的PCB企业有1000多家,平均日产生含铜废蚀刻液2500立方米-3000立方米,按每立方140kg-150kg的铜含量计算,每日就能从废液中回收金属铜450吨,一年能回收铜13.5万吨,相当于10多个年产万吨铜厂的年生产量。
按上海铜交所的铜价3.5万元/吨,仅此一项每年就有47亿元的铜再生产值,能为国家增加税收近8亿元。
从环保方面分析,众所周知矿山冶金是污染大户,如果从矿山中得到10万吨金属铜,开采中产生的污染有:TMT、粉尘及水土流失;选矿时的污染有:重金属污泥;冶炼时产生的大气污染有:SO2、CO2及粉尘,不仅如此,而且还破坏生态平衡。
但是该回收铜设备不产生新的污染源,铜回收率可达到99.5%,是理想的清洁生产生产设备,在设备的销售过程中也能为国家创造税收近3.5亿元。
三、采用萃取技术实现双赢PCB行业是金属资源消耗形的行业,被视为重金属污染严重的行业,但也是应用金属资源最多的行业,也就是说,重金属污染的合理回收、再生就等同于开发了资源,是财富。
PCB生产过程中所应用的贵金属有:金、银、钯、铑,*金属有:铜、镍、锡等,其中铜蚀刻废液在PCB行业中用量最大,很有回收价值,是金属资源十分丰富的废液。
那么如何选择好合适的先进工艺进行铜回收及废液再生,成为业内迫切需要解决的课题。
采用传统工艺有污染,选用进口设备非常贵,所以经过反复筛选决定,采用萃取技术分离废液中的铜离子,使铜得到回收,废液得到再生。
该工艺的最大优点是:萃取铜后不会破坏废液中萃余液成分,对蚀刻废液的再生回用奠定了基础,降铜后的废蚀刻液只需加入少许的蚀刻盐及氨水,调整各技术参数后就可在生产线循环使用,不会浪费降铜后的废蚀刻液,节约了生产成本,提高了企业的市场竞争力。
而萃取溶液的循环再生和制备硫酸铜溶液同时完成,再电解硫酸铜溶液就能得到阴极电解铜。
这种方法减轻了环保污水处理厂的负担,取得了环保效益和经济效益的双赢,发展前景非常乐观,且做到了清洁生产,确保《清洁生产法》的落实。
1.引进外国的重金属废液态离子吸附剂,能有效分离废液中的重金属离子并转化成无任何污染的金属铜(废水中的重金属含量低于0.5ppm/L以下),此项工艺技术是目前世界上最先进的,从国外采购原料,在国内配制。