parker伺服电机型号手册
派克机电产品纵览说明书

■ᅠ高技术应用的控制器■ᅠ基于工业以太网的运动控制系统■ᅠ集成多轴运动控制器■ᅠ智能伺服驱动器■ᅠ工业以太网多轴伺服驱动器■ᅠ通用伺服驱动器■ᅠ智能直流调速器■ᅠ通用直流调速器派克机电产品纵览运动控制驱动技术直流调速器■ᅠ智能交流变频器■ᅠ通用交流变频器交流变频器2■ᅠ滚珠丝杠驱动工作台■ᅠ直线电机驱动工作台■ᅠ高精度微型工作台■ᅠ经济型■ᅠ高精度高精度执行器与工作台行星齿轮减速机■ᅠ伺服电机■ᅠ防爆伺服电机■ᅠ高速大功率伺服电机■ᅠ高性能车载电机■ᅠ直线电机组件■ᅠ直驱电机■ᅠ高性能伺服电机■ᅠ电动缸■ᅠ线性执行器电机执行器3ACR 系列是派克主要的独立封装的运动控制器,能够实现多达八轴的运动控制。
简单易用的项目开发组件,使应用系统构建及维护快速,高效。
ACR74C/78C 是4轴/8轴运动控制器;ACR74T 是集成4轴步进电机驱动器的驱控一体机;ACR74V/78V 是集成4轴/8轴低压伺服驱动器的驱控一体机。
强大、集成化和为机械市场设计的派克自动化运动控制器(PAC)为OEM 提供了基于标准的自动化解决方案,能够满足严苛的应用要求。
PAC 将先进逻辑、多轴运动、信号处理和网络发布的可视化整合到一个以性能为导向的解决方案中,进而消除不必要的硬件和通信链接,并提高开发者的效率。
PAC网络架构派克自动化运动控制器 - PACACR 控制器系列•ᅠ K eywords: PAC CPU 运算能力更强•ᅠP AC: EtherCAT, 多轴插补•ᅠA CR:模拟量模式,简单易用ACR7C/7V ACR7000PAC3404智能伺服驱动器 - Compax3Compax3是派克汉尼汾不同国家和地区推出的伺服驱动器产品。
驱动器系列包括单轴,多轴驱动器,还有液压控制器。
这一系列驱动的功率从1到110kVA。
这一伺服驱动器的整个研发及制造过程全部在德国完成。
另外的生产基地也在美国建成。
作为一款销往不同国家和地区的伺服驱动控制器,Compax3在世界各地都有销售。
PARKER伺服电机SMN选型手册

High-Torque Design, Compact PackageParker’s SMN series of rotary servo motors combines a high-performance segmented stator design with competitive pricing for today’s demanding servo applications. The modern eight-pole segmented stator architecture produces extremely high torque values for a given motor volume. The SMN motor family is offered in frame sizes ranging from 60 mm to 142 mm and is available with resolver, quadrature encoder or high-resolution SinCos feedback devices.SMN Motor Features• High performance per dollar• High torque density package• 1.4 – 14.5 N-m continuous torque range• Brushless construction• Resolver, encoder or SinCos (absolute) feedback • Five frame sizes from 60 mm to 142 mm• IP64 standard• IP65 optionMotor Part Numbering SystemSeriesSMN -SMN FamilyFrame060 - 60mm082 - 82mm100 - 100mm115 - 115mm142 - 142mmStack2WindingPQSTVZFeedbackTypeFeedbackResolution41 - Resolver, single speed2F - Quadrature encoder,2048 line5D - SinCos w/ Hiperface™absolute encoder (Stegmann)ShaftK - KeywayConnectorP - PS styleOptionsN - NoneB - HoldingbrakeV - IP65 (shaftseal)10002000300040005000600070001000200030004000500060007000102030405010002000300040005000600070001.132.263.394.525.6501.132.263.394.525.65010020030040050010020030040050011.322.633.945.256.5011.322.633.945.256.5SMN0602TSpeed (RPM)T o r q u e (i n -l b )Torque (Nm)0501001502002503005.6511.317.022.628.333.9SMN1152TT o r q u e (i n -l b )Torque (Nm)SMN1422SSpeed (RPM)T o r q u e (i n -l b )Torque (Nm)SMN1422PT o r q u e (i n -l b )Torque (Nm)10203040501000200030004000500060007000SMN0602ZSpeed (RPM)T o r q u e (i n -l b )Torque (Nm)204060801001202.264.526.789.0411.313.7SMN0822SSpeed (RPM)T o r q u e (i n -l b )Torque (Nm)0501001502002503003505.6511.317.022.628.333.939.650100150200501001502005.6511.317.022.65.6511.317.022.6SMN1152QSpeed (RPM)Speed (RPM)Speed (RPM)T o r q u e (i n -l b )Torque (Nm)20406080100010002000300040005000600070000100020003000400050006000700010002000300040005000600070001000200030004000500060007000100020003000400050006000700010002000300040005000600070002.264.526.781.0411.3SMN0822VSpeed (RPM)T o r q u e (i n -l b )Torque (Nm)SMN1002SSpeed (RPM)T o r q u e (i n -l b )Torque (Nm)SMN1002PSpeed (RPM)T o r q u e (i n -l b )Torque (Nm)Peak (120V)Peak (240V)Peak (460V)ContinuousMotor Speed-Torque Performance Curves1 @ 25˚ C ambient motor connected to a 10”x10”x1/4” aluminum mounting plate; @ 40˚ C ambient, derate phase currents and torques by 7%.2 For higher-speed operation, please call the factory.3 Measured line to line, +/- 10%.4 Value is measured peak of sine wave.5 +/- 30%, line to line, inductance bridge measurement @ 1Khz.6 Initial winding temperature mut be 60˚ C or less before peak7 Direct current through a pair of motor phases of a trapezoidally (six state) commutated motor.8 Peak of sinusoidal current in any phase for a sinusoidallycommutated motor.9 Total motor torque per peak of the sinusoidal amps measured in any phase, +/- 10%.10 Maximum time duration with 2 times (or 3 times) rated current applied with initial winding temperature at 60˚ C.Dimensional SMN Motors SMNxxSMN0602 with Sin/Cos Encoder Option - 5D。
浦克尔(Parker)电机驱动系列FL20系列产品说明说明书
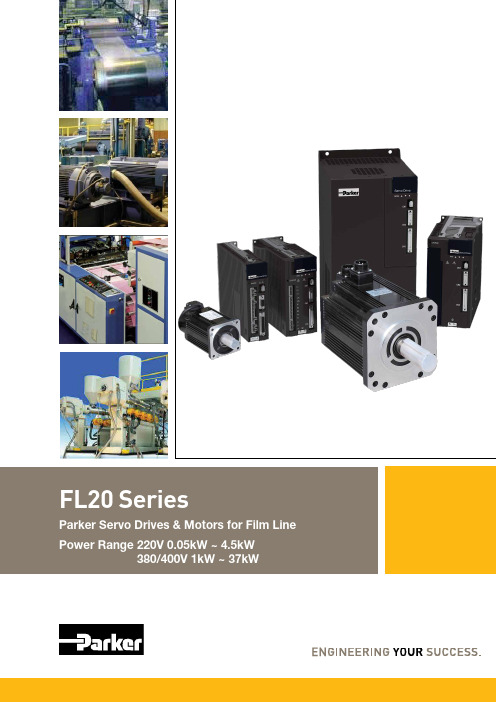
Power Range 2Parker FL20 SeriesServo drive · motorWARNING — USER RESPONSIBILITYFAILURE OR IMPROPER SELECTION OR IMPROPER USE OF THE PRODUCTS DESCRIBED HEREIN OR RELATED ITEMS CAN CAUSE DEATH, PERSONAL INJURY AND PROPERTY DAMAGE.• This document and other information from Parker-Hannifi n Corporation, its subsidiaries and authorized distributors provide product or system options for further investigation by users having technical expertise.• The user, through its own analysis and testing, is solely responsible for making the fi nal selection of the system and components and assuring that all performance, endurance, maintenance, safety and warning requirements of the application are met. The user must analyze all aspects of the application, follow applicable industry standards, and follow the information concerning the product in the current product catalog and in any other materials provided from Parker or its subsidiaries or authorized distributors.• To the extent that Parker or its subsidiaries or authorized distributors provide component or system options based upon data or specifi cations provided by the user, the user is responsible for determining that suchdata and specifi cations are suitable and suffi cient for all applications and reasonably foreseeable uses of the components or systems.Parker FL20 SeriesServo drive · motorFL20 Servo DriveDrive overview (5)Technical characteristics (6)Drive component (8)Terminal details (10)Wiring diagram (13)Connection to Peripheral Devices (14)Typical main circuit wiring (15)Ordering code - Drive (16)Drive dimensions (18)Servo MotorServo motor overview (22)Ordering code - Motor (23)Technical characteristics (24)Motor dimensions (27)Accessories (32)Parker FL20 Series Servo drive · motorGlobal Product DesignParker Hannifin has more than 40 years experience in the design and manufacturing of drives, controls, motors and mechanical products. With dedicated global productdevelopment teams, Parker draws on industry-leading technological leadership and experience from engineering teams in Europe, North America and Asia.Local Application Expertise Parker has local engineering resources committed to adapting and applying our current products and technologies to best fit our customers’ needs.Manufacturing to Meet Our Customers’ NeedsParker is committed to meeting the increasing service demands that our customers require to succeed in the global industrial market. Parker’s manufacturing teams seek continuous improvement through the implementation of lean manufacturing methods throughout the process. We measure ourselves on meeting our customers’ expectations of quality and delivery, not just our own. In order to meet these expectations, Parker operates and continues to invest in ourmanufacturing facilities in Europe, North America and Asia.Parker HannifinThe global leader in motion and control technologiesWuxi, China Littlehampton, UK Charlotte NC, USA Chennai, IndiaJangan, KoreaParker provides sales assistance and local technical support through a network of dedicated sales teams and authorized technical distributors.For contact information, please refer to the Sales Offices on the back cover of this document or visit Electromechanical Worldwide Manufacturing Locations EuropeLittlehampton, United Kingdom Dijon, FranceOffenburg, Germany Filderstadt, Germany Milan, Italy AsiaWuxi, China Jangan, Korea Chennai, IndiaNorth AmericaRohnert Park, California Irwin, PennsylvaniaCharlotte, NorthCarolina NewUlm, MinnesotaParker FL20 SeriesServo drive · motorOverviewDescriptionFL20-S Series Servo Drives is a high performance drive particularly suitable for Film Line and similarapplications. It has a 1.2kHz frequency response with a full closed loop functionality. The feedback options are incremental encoder, absolute encoder and resolver.The FL20-S has in-built RS485/232 port for PC monitoring. It also has CANopen and EtherCATcommunication as options. The Parker PAC controller with its EtherCAT communication can be used as a complete solution for applications that need a controller as well as servo drives and motors.FL20C is the in built EtherCAT version of the FL20S. The I/Os are optimized as most of the commands would be through the EtherCAT communication.Features• Flexibility• Full closed loop control or multi-position control or interrupted position control • Gantry synchronization • Gain switchingFaster• Frequency response 1.2kHz • Dual-core processors • 23-bit absolute encoderPowerful• Built-in PLC Function• Pulse command Frequency up to 4Mhz • RS485/232, CANopen, EtherCAT• RS485/232 interface connected to PC SoftwareFL20 series Servo Drives for Film Line ApplicationsTechnical CharacteristicsParker FL20 SeriesServo drive · motorTechnical CharacteristicsFL20-S Servo Drive SpecificationsParker FL20 SeriesServo drive · motor Technical CharacteristicsFL20-C Servo Drive SpecificationsParker FL20 Series Servo drive · motorDrive ComponentInput Signal for FL20-S DrivesCharging IndicatorThe LED will light up when incoming poweris given. The DC Link capacitors will retain charge for some time even if power is turnedoff. Do not attempt to touch the power terminals as long as this LED is ‘ON”.Main Power InputOperator PanelSerial Communication Port (CN1)PC, PLC, CNC and other host controllerEncoder Interface (CN2)Connected with the servo motorInput and output signal (CN3)Command input, the monitor signal output terminal.Ground Connection.Must connect to ground at all times to avoid electric shock.Control Power InputBraking resistor connectionDC Reactor ConnectionServo Motor Connection1) 2connected power supply.2) 3forbidden to connect.1 phase 220V .Parker FL20 Series Servo drive · motorDrive ComponentInput Signal for FL20-C DrivesThe LED will light up when incoming poweris given. The DC Link capacitors will retain charge for some time even if power is turnedoff. Do not attempt to touch the power terminals as long as this LED is ‘ON”.Main Power InputOperator PanelSerial Communication Port (CN1)PC, PLC, CNC and other host controllerEncoder Interface (CN2)Connected with the servo motorInput and output signal (CN3)Command input, the monitor signal output terminal.Ground Connection.Must connect to ground at all times to avoid electric shock.Control Power InputBraking resistor connectionDC Reactor ConnectionServo Motor Connection1) 2connected power supply.2) 3forbidden to connect.1 phase 220V .Parker FL20 Series Servo drive · motorCN2 Terminal DefinitionFigure: From the wire side to drive side lookFigure: From the wire side to drive side lookTerminal DetailsCN1 Terminal DefinitionFigure: CN1 terminal definition (from the wire side to drive side view)Parker FL20 Series Servo drive · motorTerminal DetailsCN3 Terminal Definition for FL20-S Drives12Parker FL20 Series Servo drive · motorOther SignalCommunication PortTerminal DetailsCN3 Terminal Definition for FL20-C DrivesParker FL20 SeriesServo drive · motor Wiring diagramConnected to the shell1314Parker FL20 Series Servo drive · motor伺服电机PC ,PLC ORcommunication Servo motorConnection to Peripheral Devices(1 phase 220V, only L1 and L3 should be connected.)15Parker FL20 Series Servo drive · motorTypical main circuit wiringFor 220V servo driveFor 380V servo driveNote)For 220V input servo drive, L1C and L2C should be connected to power supply.For 220V single phase connect to L1 and L3.For 380V input servo drive, L1C and L2C are forbidden to connectPanel16Parker FL20 Series Servo drive · motorOrdering CodeFL20-S Series DriveNote)-EtherCAT, CANopen communication cards1.0kW, M2 Frame 152 T3 M2 1.5kW, M2 Frame 202 T3 M32kW, M3 Frame 302 T3 M33kW, M3 Frame 452 T3 M3 4.5kW, M3 Frame 552 T3 M3 5.5kW, M3 Frame 752 T3 MM47.5kW, MM4 Frame 113 T3 MM411kW, MM4 Frame 153 T3 M415kW, M4 Frame 183 T3 M518kW, M5 Frame 223 T3 M522kW, M5 Frame 303 T3 M630kW, M6 Frame 373 T3 M637kW, M6 FrameB3Built in Brake Unit + Dynamic Brake Note) - F or build in and external resistors details please 48 x 175 x 195B3(no braking resister)M275 x 175 x 195B1, B3M3100 x 203 x 218B1, B3M3(5.5kW)100 x 203 x 218B1MM4150 x 336 x 203B1(no braking resister)M4185 x 380 x 215B1(no braking resister)M5210 x 420 x 215B1(no braking resister)M6268.4 x 498 x 234B1(no braking resister)Note)- Specification subject to change without notice.Optional Communication CardParker FL20 SeriesServo drive · motor Ordering CodeFL20-C Series Drive202 T3 M32kW, M3 Frame 302 T3 M33kW, M3 Frame 452 T3 M3 4.5kW, M3 Frame 552 T3 M3 5.5kW, M3 Frame 752 T3 MM47.5kW, MM4 Frame 113 T3 MM411kW, MM4 Frame 153 T3 M415kW, M4 Frame 183 T3 M518kW, M5 Frame 223 T3 M522kW, M5 Frame 303 T3 M630kW, M6 Frame 373 T3 M637kW, M6 Frame B3Built-in Brake Unit + Dynamic Brake Note)- F or build in and external resistors details pleaseM148 x 175 x 195resistor)M275 x 175 x 195B1, B3M3100 x 203 x 218B1, B3M3(5.5kW)100 x 203 x 218B1MM4150 x 336 x 203B1(No built-in brakingresistor)M4185 x 380 x 215B1(No built-in brakingresistor)M5210 x 420 x 215B1(No built-in brakingresistor)M6268.4 x 498 x 234B1(No built-in brakingresistor)Note)- Specification subject to change without notice.17Parker FL20 SeriesServo drive · motorDrive Dimensions M1 Frame dimensionsM2 Frame dimensions18Parker FL20 SeriesServo drive · motor M3 Frame dimensionsMM4 Frame dimensions1920Parker FL20 Series Servo drive · motorDrive DimensionsM5 Frame dimensionsParker FL20 SeriesServo drive · motorM6 Frame dimensions2122Parker FL20 Series Servo drive · motorServo motorOverviewDescriptionServo motor is the latest development of a high-performance motor to meet the customer‘s requirement and the needs of actual market; supports wiring flexible, cost-effective standard AC servo position system.Servo motor nameplateMotor Current Rated Grade GradeRated Installation Product No.MA102F67EDM74211009038TYPE : FMMA-102F67ED FM17 - 0110R6EEDFLTH. CI .F IP54 No. :Rated Power : 11 kW Magnetic Field Angle :Production Date :AC permanent magnetic synchronous servo motorRated voltage : 380 V Rated Current : 23 A Speed : 1700 r/min Fan Voltage: 220 VRated Torque : 64 N·M M = 5 Nm23Parker FL20 Series Servo drive · motorOrdering CodeServo Motor (for 180 Flange and less)Servo Motor (for 180 and 250 spigot motor)R Resolver F 14-core 2500 ppr Incremental encoder G 8-core 2500 ppr Incremental encoder H 4-core 23-bit Incremental encoder S 4-core 17-bit Absolute encoder T4-core 23-bit Absolute encoderResolver F 14-core 2500 ppr Incremental encoder G 8-core 2500 ppr Incremental encoder H 4-core 23-bit Incremental encoder S 4-core 17-bit Absolute encoder T4-core 23-bit Absolute encoderSmooth shaft with C hole DKeyway shaft with C holeNote)The servo motors are used for both 220V and 380V .Parker FL20 SeriesServo drive · motorTechnical CharacteristicsServo Motor Specifications (220V – Incremental, Absolute Encoder and Resolver)Note)• These part numbers are based on Incremental Encoder Type.• Three-phase AC servo motor type permanent magnet synchronous motor, natural cooling, protection class IP65.• The matched servo drive and motor can work with the most situation. But for some special situation, please contact to Parker sales team.24Parker FL20 SeriesServo drive · motor Servo Motor Specifications (380V – Incremental, Absolute Encoder and Resolver)Note)• These part numbers are based on Incremental Encoder Type.• Three-phase AC servo motor type permanent magnet synchronous motor, natural cooling, protection class IP65.• The matched servo drive and motor can work with the most situation. But for some special situation, please contact to Parker sales team.2526Parker FL20 Series Servo drive · motorServo Motor Specifications (380V – Incremental, Absolute Encoder and Resolver)Note)• These part numbers are based on Incremental Encoder Type.• On behalf of the motor shaft extension brake category, please refer to [naming rules servo motor] in this manual.• The matched servo drive and motor can work with the most situation. But for some special situation, please contact to Parker sales team.27Parker FL20 Series Servo drive · motorMotor DimensionsServo motor60 Flange80 FlangeTolerance grade not noted refer to GB/T 1804-2000-Mencoder plugencoder plug28Parker FL20 Series Servo drive · motorMotor DimensionsServo motor110 FlangeTolerance grade not noted refer to GB/T 1804-2000-MWaterproof rubber cover of aviation plug29Parker FL20 SeriesServo drive · motor130 FlangeWaterproof rubber cover of aviation plugTolerance grade not noted refer to GB/T 1804-2000-M30Parker FL20 Series Servo drive · motorMotor DimensionsServo motor180 Flange MotorWaterproof rubber cover ofaviation plugTolerance grade not noted refer to GB/T 1804-2000-M31Parker FL20 SeriesServo drive · motorFM15, FM17, FM20 series, Air-coolingNote)• 1-phase 220V power supply of 50 /60 Hz is usable for servomotor fan. • Green terminal definition: K-220VAC, L-220VAC, M-PE.Parker FL20 SeriesServo drive · motorAccessoriesFeedback Cable• Absolute Encoder Cable (Maximun length : 30m)2) Encoder cable with L aviation plug((applicable for 110, 130 and 180 flange servo motor)1) Encoder cable with DB plug((applicable for 80 flange and below 80 flange servo motor)32Parker FL20 SeriesServo drive · motor • Resolver Feedback Cable (Maximun length : 30m)2) Feedback cable with I aviation plug (applicable for servo motor with base No. E, F)Control Cable• Control cable (Maximum length : 30m)Note)33• ZL4-4PO-XXX is single strand cable, grounding cable is yellow-green cable of 2.5 mm2.Parker FL20 SeriesServo drive · motorAccessoriesCommunication Cable• EtherCAT cable (Maximum length : 30m)Power Cable(Servo motor power line form L- Plug power line (for 800W of Servo motors), Maximum length : 30m)[ 220V Servo Motor Power cable ]Note)• HK4A cable is suitable for flange below 180 with aviation plug.• HK4B is suitable for 180 flange with aviation plug.• The unit of length is m.34Parker FL20 SeriesServo drive · motor[ 380V Servo Motor Power cable ]Note)• HK4A cable is suitable for flange below 180 with aviation plug.• HK4B is suitable for 180 flange with aviation plug.• The unit of length is m.35Parker FL20 SeriesServo drive · motorAccessoriesPower Cable(Servo motor power line form L- Plug power line (for 800W of Servo motors), Maximum length : 30m)[ 380V Servo Motor Power cable for >180Frame ]36MemoMemoAerospaceKey MarketsAftermarket services Commercial transports EnginesGeneral & business aviation Helicopters Launch vehicles Military aircraft MissilesPower generation Regional transportsUnmanned aerial vehiclesKey ProductsControl systems & actuation products Engine systems & componentsFluid conveyance systems & componentsFluid metering, delivery & atomization devicesFuel systems & components Fuel tank inerting systems Hydraulic systems & componentsThermal management Wheels & brakesElectromechanicalKey MarketsAerospaceFactory automation Life science & medical Machine toolsPackaging machinery Paper machineryPlastics machinery & converting Primary metalsSemiconductor & electronics TextileWire & cableKey ProductsAC/DC drives & systemsElectric actuators, gantry robots & slidesElectrohydrostatic actuation systems Electromechanical actuation systems Human machine interface Linear motorsStepper motors, servo motors, drives & controls Structural extrusionsPneumaticsKey MarketsAerospaceConveyor & material handling Factory automation Life science & medical Machine toolsPackaging machineryTransportation & automotiveKey ProductsAir preparationBrass fittings & valves ManifoldsPneumatic accessoriesPneumatic actuators & grippers Pneumatic valves & controls Quick disconnects Rotary actuatorsRubber & thermoplastic hose & couplingsStructural extrusionsThermoplastic tubing & fittings Vacuum generators, cups & sensorsFluid & Gas HandlingKey MarketsAerial lift AgricultureBulk chemical handling Construction machinery Food & beverage Fuel & gas delivery Industrial machinery Life sciences Marine Mining Mobile Oil & gasRenewable energy TransportationKey ProductsCheck valvesConnectors for low pressure fluid conveyance Deep sea umbilicals Diagnostic equipment Hose couplings Industrial hose Mooring systems & power cablesPTFE hose & tubing Quick couplingsRubber & thermoplastic hose Tube fittings & adapters Tubing & plastic fittingsHydraulicsKey MarketsAerial lift AgricultureAlternative energy Construction machinery ForestryIndustrial machinery Machine tools MarineMaterial handling Mining Oil & gasPower generation Refuse vehicles Renewable energy Truck hydraulics Turf equipmentKey ProductsAccumulators Cartridge valvesElectrohydraulic actuators Human machine interfaces Hybrid drivesHydraulic cylindersHydraulic motors & pumps Hydraulic systemsHydraulic valves & controls Hydrostatic steeringIntegrated hydraulic circuits Power take-offs Power units Rotary actuators SensorsProcess ControlKey MarketsAlternative fuels Biopharmaceuticals Chemical & refining Food & beverage Marine & shipbuilding Medical & dental Microelectronics Nuclear PowerOffshore oil exploration Oil & gasPharmaceuticals Power generation Pulp & paper SteelWater/wastewaterKey ProductsAnalytical InstrumentsAnalytical sample conditioning products & systems Chemical injection fittings & valvesFluoropolymer chemical delivery fittings, valves & pumpsHigh purity gas delivery fittings, valves, regulators & digital flow controllers Industrial mass flow meters/controllersPermanent no-weld tube fittings Precision industrial regulators & flow controllersProcess control double block & bleedsProcess control fittings, valves, regulators & manifold valvesSealing & ShieldingKey MarketsAerospaceChemical processing Consumer Fluid power General industrial Information technology Life sciences Microelectronics Military Oil & gasPower generation Renewable energy Telecommunications TransportationKey ProductsDynamic seals Elastomeric o-ringsElectro-medical instrument design & assembly EMI shieldingExtruded & precision-cut,fabricated elastomeric seals High temperature metal seals Homogeneous & inserted elastomeric shapesMedical device fabrication & assemblyMetal & plastic retained composite sealsShielded optical windows Silicone tubing & extrusions Thermal managementVibration dampeningParker’s Motion & Control TechnologiesAt Parker, we’re guided by a relentless drive to help our customers become more productive and achieve higher levels of profitabil-ity by engineering the best systems for their require-ments. It means looking at customer applications from many angles to find new ways to create value. What-ever the motion and control technology need, Parker has the experience, breadth of product and global reach to consistently deliver. No company knows more about motion and control technol-ogy than Parker. For further info call 00800 27 27 5374Climate ControlKey MarketsAgriculture Air conditioningConstruction Machinery Food & beverage Industrial machinery Life sciences Oil & gasPrecision cooling Process Refrigeration TransportationKey ProductsAccumulatorsAdvanced actuators CO 2 controlsElectronic controllers Filter driersHand shut-off valves Heat exchangers Hose & fittingsPressure regulating valves Refrigerant distributors Safety relief valves Smart pumps Solenoid valvesThermostatic expansion valvesFiltrationKey MarketsAerospaceFood & beverageIndustrial plant & equipment Life sciences MarineMobile equipment Oil & gasPower generation & renewable energy ProcessTransportation Water PurificationKey ProductsAnalytical gas generatorsCompressed air filters & dryersEngine air, coolant, fuel & oil filtration systems Fluid condition monitoring systems Hydraulic & lubrication filters Hydrogen, nitrogen & zero air generatorsInstrumentation filters Membrane & fiber filters Microfiltration Sterile air filtrationWater desalination & purification filters & systemsDec. 2017© 2017 Parker Hannifin Corporation Parker Hannifin Corporation Automation Group AP This catalogue is offered to you by;Parker Asia PacificChinaSales OfficeShanghai office: 86 21 2899 5000Parker Hannifin Motion&Control Co. Ltd.280 Yunqiao Road, Jin Qiao Export Processing Zone, Shanghai 201206, ChinaSales OfficeGuangzhou Office: 86 20 3212 1688 Parker Hannifin Motion&Control Co. Ltd.Room 202, Building F , Guangdong Soft Science Park, No 11, Caipin Road, Guangzhou Science City, Luo Gang District, Guangzhou 510663, ChinaSales OfficeBeijing office: 86 10 6561 0520Parker Hannifin Motion&Control Co. Ltd.Suite 8B01, 8th Floor, Hanwei Plaza,7 Guanghua Road, Chaoyang District, Beijing 100004, P .R.ChinaAutomation DivisionWUXI plant: 86 510 8116 7000Parker Hannifin Motion and Control (Wuxi) Company Ltd.No.200, Furong Zhong Si Lu, Xishan Economic Development Zone, Wuxi 214101, Jiangsu, ChinaJapanSales OfficeAsahi Plant: 81 479 64 2282********************Kuroda Pneumatics Ltd.10243 Kamakazu, Asahi-shi, Chiba 289-2505 Japan Automation DivisionAsahi Plant: 81 479 64 2282Kuroda Pneumatics Ltd.10243 Kamakazu, Asahi-shi, Chiba 289-2505 JapanKoreaSales OfficeSeoul Office: 82 2 559 040011F , U-Space1 B, 660, Daewangpangyo-ro, Bundang-gu, Seongnam-si, Gyeonggi-do, 13494, Korea Automation DivisionJang An Plant: 82 31 359 0700Parker Korea Ltd.23, Jangangongdan 1-gil, Jangan-myeon, Hwaseong-si, Gyeonggi-do, 18579, KoreaIndiaSales OfficePHI Chennai Sales office: 91 44 4391 0799Parker Hannifin India Private. Limited,Plot no. P41/2, Eight Avenue, Domestic Tariff Area,Mahindra world city, Chengalpattu, Kanchipuram District, Pin : 603002, Tamil Nadu, IndiaAutomation DivisionPHI Chennai MWC Plant: 91 44 4391 0703 Parker Hannifin India Private. Limited,Plot no. P41/2, Eight Avenue, Domestic Tariff Area,Mahindra world city, Chengalpattu, Kanchipuram District, Pin : 603002, Tamil Nadu, IndiaTaiwanSales OfficeTaipei Office: 88 6 2 2298 8987Parker Hannifin Taiwan Co., Ltd.8F ., No.22 Wuquan 7th Road., Wugu Dist., New Taipei City, 248, Taiwan (R.O.C)ThailandSales OfficeBangkok Office: 66 2 186 7000Parker Hannifin (Thailand) Co., Ltd.1265 Rama 9 Road, Suanluang Bangkok 10250 ThailandSingaporeSales OfficeOffice: 65 6887 6300Parker Hannifin Singapore Pte Ltd.11th Fourth Chin Bee Road Singapore 619702MalaysiaSales OfficeSelangor Office: 60 3 7849 0800Parker Hannifin Industrial (M) Sdn Bhd No.11 Persiaran Pasak BumiSeksyen U8, Bukit Jelutong Industrial Park 40150 Shah Alam, Selangor, MalaysiaIndonesiaSales OfficeOffice: 62 21 7588 1906PT. Parker Hannifin IndonesiaWisma Contromatic, Jalan Kapten SoebijantoDjodjohadikusumo, Kav. Sunburst Block CBD II No.15 BSD (Bumi Serpong Damai), Tangerang 15311, IndonesiaVietnamSales OfficeOffice: 84 8 3999 1600Parker Hannifin Vietnam Co., Ltd.4th Floor, VRG office building, 177 Hai Ba Trung, Ward 6, District 3, Ho Chi Minh City, VietnamAustraliaSales OfficeOffice: 61 2 9634 7777Parker Hannifin (Australia) Automation Department 9 Carrington Rd Castle Hill, NSW, 2154 AustraliaNew ZealandSales OfficeOffice: 64 9 574 1744Parker Hannifin (NZ) Ltd.5 Bowden Road, Mt Wellington 1060, Auckland, New Zealand。
Parker IM20系列电液伺服系统说明书

前言感谢您选用Parker伺服控制系统!同时,您将享受到我们为您提供的全面、真诚的服务。
IM20系列伺服驱动器容量范围广,能够完美地实现伺服油泵控制,是目前市场上性价比较高的中大功率伺服驱动器。
本手册将为您提供安装调试、操作使用、故障诊断及日常维护的有关注意事项,在安装、使用前请仔细阅读。
本手册随驱动器一起提供,请妥善保管,以备以后查阅和维护使用。
当您在使用中发现任何问题,而本手册无法为您提供解答时,请与本公司联系咨询。
我们的专业技术服务人员将竭诚为您服务,并希望您能继续选用我们的产品,敬请提出宝贵的意见和建议!本公司致力于产品的不断改善和功能升级,手册提供资料如有变更,恕不一一通知。
最新及详细版使用手册会在公司网站()上进行公布。
■安全标识本产品的安全运行取决于正确的安装和操作以及运输与保养维护,请务必遵守本手册中使用的如下安全标识:错误的操作将引发危险情况,导致人身伤亡。
错误的操作将引发危险情况,导致轻度或中度人身伤害,损坏设备。
另外,该标识中所述事项有时也可能造成严重的后果。
驱动器及电机上标识符的意义如下:电压高,有电击危险。
表面热,禁止触摸。
目录前言 (1)1使用须知 (6)1.1 产品确认事项 (6)1.2 伺服驱动器的铭牌 (6)1.3 伺服电机的铭牌 (6)1.4 驱动器命名规则 (7)1.5 伺服电机命名规则 (8)1.6 产品外观 (10)1.7 安全须知 (10)1.7.1 安装、布线注意事项 (10)1.7.2 运行、维护注意事项 (11)1.7.3 废弃注意事项 (11)2 伺服系统技术规范及选型 (12)2.1 伺服驱动器技术规范和参数 (12)2.1.1伺服驱动器技术规范 (12)2.1.3伺服驱动器外围配线、磁珠使用指导 (14)2.2 伺服电机技术规范和参数 (15)2.2.1 伺服电机技术条件 (15)2.2.2 伺服电机主要参数 (15)2.3 伺服系统油泵选型计算 (17)2.3.1伺服驱动器、电机、油泵的选型计算方法 (17)2.3.2伺服、电机、油泵的组合配置 (18)3 产品安装 (21)3.1 驱动器安装 (21)3.1.1 驱动器结构尺寸 (21)3.1.2 驱动器安装 (22)3.2 伺服电机安装 (22)3.3 制动单元及制动电阻 (23)4 电气连接 (25)4.1 电液系统构成 (25)4.2 电气连接 (26)4.2.1 主电路接线示意 (27)4.2.2 控制端子功能简介和接线示意图 (27)4.2.3 拨码开关介绍 (29)5 操作面板和功能参数 (30)5.1 面板显示说明 (30)5.2 面板操作 (31)5.3 参数设置 (31)5.4 功能码区内和区间的切换 (31)5.5 面板显示内容 (33)5.6参数设定 (34)5.6.1 基本参数 (34)5.6.2运行控制 (34)5.6.3 多功能输入输出 (36)5.6.4 模拟量检测和输入输出 (38)5.6.5 能耗制动和保护控制 (39)5.6.6 电机控制参数 (40)5.6.7 压力控制参数 (42)5.6.8 多泵合流控制 (45)5.6.8.1多泵合流控制参数 (45)5.6.8.2多泵合流控制示意图 (48)6 注塑机整机调试步骤 (49)7 故障分析处理 (51)8 日常检查和保养 (57)8.1定期检查 (57)8.2易损件更换 (57)8.3存储 (57)附录一功能码速查表 (58)附录二注塑机卡说明 (72)附录三伺服电机结构尺寸示意图 (73)9敬告用户 (81)1使用须知1.1 产品确认事项产品到货之后,请对如下项目进行检查并确认。
PARKER派克MPE系列伺服电动机技术手册

options and reduced complexity.
70.8
Continuous Peak
8
• Eight models covering three
frame sizes of 40, 60 and 80 mm
62.0
• 1.4 to 31.3 in-lbs continuous
MPE080
phone: 800.358.9068 / 707.584.7558 fax: 707.584.8015 email: emn_support@
0 0
1000
2000
3000
4000
0 5000
Speed RPM
MPE Common Specifications
1.2
0.26 2.3
Rated Shaft Output Power 1, 2, 3, 4 Current at Rated Speed 1, 2, 3, 4 Voltage Constant 4. 7 Torque Constant 4, 7 Resistance 4, 9
Pout Ir Ke
Tr
in-lb
6.0
10.6
Rated Shaft Output Power 1, 2, 3, 4 Current at Rated Speed 1, 2, 3, 4 Voltage Constant 4. 7 Torque Constant 4, 7 Resistance 4, 9
Pout Ir Ke
Arms Vrms/krpm Nm/Arms
ohm
Rated Shaft Output Power 1, 2, 3, 4 Current at Rated Speed 1, 2, 3, 4 Voltage Constant 4. 7 Torque Constant 4, 7 Resistance 4, 9
Parker XLM系列线性电动机位置器说明书
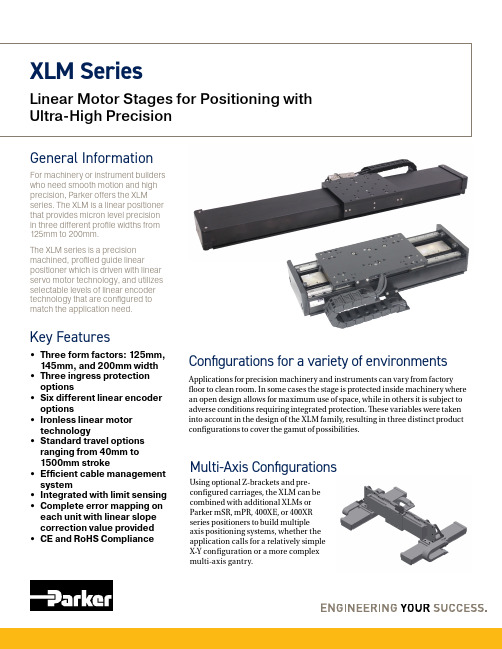
XLM SeriesLinear Motor Stages for Positioning withUltra-High PrecisionGeneral InformationFor machinery or instrument builderswho need smooth motion and highprecision, Parker offers the XLMseries. The XLM is a linear positionerthat provides micron level precisionin three different profile widths from125mm to 200mm.The XLM series is a precisionmachined, profiled guide linearpositioner which is driven with linearservo motor technology, and utilizesselectable levels of linear encodertechnology that are configured tomatch the application need.Configurations for a variety of environmentsApplications for precision machinery and instruments can vary from factoryfloor to clean room. In some cases the stage is protected inside machinery wherean open design allows for maximum use of space, while in others it is subject toadverse conditions requiring integrated protection. These variables were takeninto account in the design of the XLM family, resulting in three distinct productconfigurations to cover the gamut of possibilities.Key Features• Three form factors: 125mm,145mm, and 200mm width• Three ingress protectionoptions• Six different linear encoderoptions• Ironless linear motortechnology• Standard travel optionsranging from 40mm to1500mm stroke• Efficient cable managementsystem• Integrated with limit sensing• Complete error mapping oneach unit with linear slopecorrection value provided• CE and RoHS ComplianceMulti-Axis ConfigurationsUsing optional Z-brackets and pre-configured carriages, the XLM can becombined with additional XLMs orParker mSR, mPR, 400XE, or 400XRseries positioners to build multipleaxis positioning systems, whether theapplication calls for a relatively simpleX-Y configuration or a more complexmulti-axis gantry.XLM Series Linear Motor StagesOpen Design "U"Type UA/UB• Lower profile • Narrower width•Less operating friction• Solid top cover• Protection against falling materials• No increase in frictionCovered Design "C"Type CA, CB, CC• IP30 environmental protection• Protection against objects >2.5mmSealed Design "S"Type SA, SB, SCIngress Protection OptionsBasic Specifications1 Stage mounted to granite surface, 0.01 micron optical encoder2Measurements taken at 35 mm above the center of the carriage, with linear slope correction.3Please refer to XLM catalog for more details.These accessory assemblies are used tomechanically couple multiple XLM unitsand allow for flexibility in the geometryof the system. The “R” module allowsfor rotation between axes, while the“RT” incorporates both rotation andtranslation.RTR ModulesMultiple styles of Z-Brackets are available for additional flexibility ofcarriage configuration or building multi-axis systems. The brackets canmount at 3, 6, 9, and 12 o’clock positions, and can mount directly toXLM125 and XLM145 open, closed, and sealed versions. Z-Bracketscan accept Parker 401XE, 402XE, 403XE, 404XE, and 404XR stages.See full catalog for compatibility.XLM Series - Options and Accessories -Carriage OptionsA number of carriage choices are available for each XLM size. Carriages are available with standard “X” patternholes to accomodate XML Z-brackets, toe clamps, or RT/R adapters, with base holes for additional XLMs in amulti-axis configuration, and with hole patterns for other Parker positioners.A range of Toe Clamps can be used to connect multipleXLM units together to create a multi-axis system. Theyare also recommended for covered and sealed versionsto eliminate the need to open the unit for mounting. Allhardware is included with Toe Clamps.Toe ClampsZ-BracketsPROPRIETARY INFORMATIONPARKER HANNIFIN CORP.METRIC UNITSSTANDARD TOLERANCES,UNLESS OTHERWISE SPECIFIEDALL THREADS TO BEI.S.O. 4g6g OR 4H6H(COARSE PITCH)SCM5 Base Mtg HolesMounts XLM125 Toe ClampsMounts XLM125/145 Z-BracketsOptional Carriage Adaper Plate- 102-9018-01This plate mounts to Standard Carriage 102-9Mounts 402XE Center Mtg. HolesMounts 403XE Center Mtg. HolesMounts 404XR Toe ClampsMounts mSR100 Base Mtg. HolesMounts mPR100 (shifted 9.5mm up)XLM125 CarriagesOMMMMMM XLMPROPRIETPARKERMETRIC UNITSALL DIMENSIONS ARE IN MILLIMETERS(UNLESS OTHERWISE SPECIFIED)STANDARD TOLERANCES,UNLESS OTHERWISE SPECIFIEDALL THREADS TO BEI.S.O. 4g6g OR 4H6H(COARSE PITCH)DECIMALS.X5 Base MMounts XLM125 Toe ClaMounts XLM125/145 Z-BOptional Carriage AdaperThis plate mounts to StanMounts 402XE Center MtgMounts 403XE Center MtgMounts 404XR Toe ClampMounts mSR100 Base MtMounts mPR100 (shiftedXLM125 Carria X Pattern XE/XR Pattern mSR/mPR PatternXLM Series Linear Motor Stages4BRO-XLM 3-2023© 2023 Parker Hannifin CorporationParker Hannifin CorporationElectronic Motion and Controls Div.1140 Sandy Hill Road Irwin, PA 15642phone 800 358 9070fax 724 861 /emcXLM Ordering InformationFill in an order code from each of the numbered fields to create a complete part numberOrder Example:q Series XLMSerieswBase Size (width in mm)125125 mm wide profile 145145 mm wide profile 200200 mm wide profileeWinding & Pole Length P2Parallel, 2 pole length P3Parallel, 3 pole length P4Parallel, 4 pole lengthrSealing and Carriage Type UA Uncovered with Carriage A MountUB Uncovered with Carriage B MountCA Covered with Carriage A MountCB Covered with Carriage B MountCC Covered with Carriage C MountSA Sealed with Carriage A MountSB Sealed with Carriage B MountSCSealed with Carriage C Mountt Travel (mm) - See XLM catalog for available travel lengths by base size and features.yEncoder E11µ optical incremental E20.1µ optical incremental E30.01µ optical incremental SC Sine/Cosine 1V p-pR1Absolute BiSS-C 50 nm, 32 Bit, value increases right to leftR2Absolute BiSS-C 5 nm, 32 Bit, value increases right to leftR3Absolute BiSS-C 50 nm, 32 Bit, value increases left to rightR4Absolute BiSS-C 5 nm, 32 Bit, value increases left to rightuScale SSteeliCable Type C1 3 meter cable direct from carriage, no connectors C25 meter cable direct from carriage, no connectors, Sine/Cosine and Absolute ONLY (SC, R1, R2, R3, & R4)C3Carriage-mounted connectors with 3muniversal extension cables C4Carriage-mounted connectors with 5muniversal extension cables C5Carriage-mounted connectors with 3mP-Drive extension cables (Not available with SC, R1, R2, R3, and R4 configurations)C6Carriage-mounted connectors with 5mP-Drive extension cables (Not available with SC, R1, R2, R3, and R4 configurations)oCable Carrier K0NoneK1Side carrier, narrow, cable exit to rightK2Side carrier, medium, cable exit to rightK3Side carrier, wide, cable exit to rightK4Side carrier, narrow, cable exit to leftK5Side carrier, medium, cable exit to leftK6Side carrier, wide, cableexit to leftRight sideLeft sideCable exit。
Parker Hannifin MPP MPJ系列无刷 servo 电机产品介绍说明书

J Series Servo Motors Brushless servo motors featuring high performance,The MPP (MaxPlusPlus) Series is the industry’s highest performing servo motor. Utilizing eight-pole segmented lamination technology, the MPP produces more torque in a shorter package. Use MPP motors for higher torque applications, customization options, or when high performance is required. The MPJ (MaxPlus-J) Series of rotary servo motors fromParker features the same design characteristics as the MPP , but with 3 - 8 times the inertia of the standard MPP . This is a perfect solution for your applications requiring a high inertia servo motor.Common Customized Options:• Shafts (longer, shorter, diameter change, hollow shafts)• Front flange (bolt circle, pilot, NEMA dimensions)• Motors coatings (white, PTFE, steel-it grey)• Non-standard feedback devices• Special connectors •Special stator windingsThe MPP Series features a new design that offers lower inertia and higher power, all in a smaller motor package. These brushless servo motors are designed for the demanding applications found in today’s high-performance servo systems.The MPP motors feature segmented core technology, which can yield up to 40%higher torque per unit size than conventionally wound servo motors. “Potted” stators improve heat transfer for better thermal efficiency, resulting in increased torque at the motor shaft. High-energy neodymium magnets are employed for higher rates of acceleration.The MPP/MPJ family of brushless servo motors redefines performance, flexibility, and reliability.MPP/MP J SeriesLow & High lnertia Rotary Servo MotorsParker will customize any MPP/MPJ motor to meet your specific system requirements. Parker does customs like no one else. We are specialists at customs, offering unrivaled custom motor solutions and support.Low & High lnertia Rotary Servo MotorsMPP/MPJ Motor Features• Segmented core technology – very high torque-to-inertia ratio – 40% higher torque • Potted stator design for improved thermal efficiency • MPP available in 92, 100, 115, 142, 190 and 270 frame sizes• MPJ available in 92,100, 115 and 142 frame sizes• Continuous stall torque: 1.5 Nm (14 lb-in) to 157 Nm(1396 lb-in)• Peak torque: 5 Nm (44 lb-in) to 513 Nm (4540 lb-in)• Brushless construction• H igh-performanceneodymium magnetsMPP/MP J Series Servo Motors• Thermistor protection • Resolver, incrementalencoder, or single- or multi-turn absolute encoders • 24 volt failsafe brake (optional) • Right-angle rotatable PS-style connectors• IP64 standard, IP65 optional shaft seal• Best-in-class lead-time, two year warranty •CE and UL7 The winding temperature at the motor rated speed may be lower than the winding maximum due to feedback or amplifier limitations.8Refer to the product part number configurator for the IP rating character. All servo motors with a “V” designator in the part number for the shaft seal option are rated IP65. All other motors are rated for IP64, provided the feedback device is encased in an aluminum housing. Motors that have exposed feedback devices are rated at IP40.MPP/MP J Size 92 Specifications1 Assumes motor is mounted to an aluminum plate with dimensions of 12” x 12” x 1/2” for 92 mm motor frames.2 Maximum winding temperature is 155°C. Thermal protection device threshold may be at a lower temperature.3 These ratings are valid for Parker drives. Other drives may not achieve the same ratings.4 ±10%5 ±30% @ 1kHz6 Reference onlyNote: These specifications are based on theoretical motor performance and are not specific to any amplifier.MPP/MPJ Size 92 Speed-Torque PerformanceMPP/MP J Size 100 Specifications1 Assumes motor is mounted to an aluminum plate with dimensions of 12” x 12” x 1/2” for 100 mm motor frames.2 Maximum winding temperature is 155°C. Thermal protection device threshold may be at a lower temperature.3 These ratings are valid for Parker drives. Other drives may not achieve the same ratings.4 ±10%5 ±30% @ 1kHz6 Reference onlyNote: These specifications are based on theoretical motor performance and are not specific to any amplifier.MPP/MPJ Size 100 Speed-Torque PerformanceMPP/MP J Size 115 Specifications1 Assumes motor is mounted to an aluminum plate with dimensions of 12” x 12” x 1/2” for 115 mm motor frames.2 Maximum winding temperature is 155°C. Thermal protection device threshold may be at a lower temperature.3 These ratings are valid for Parker drives. Other drives may not achieve the same ratings.4 ±10%5 ±30% @ 1kHz6 Reference onlyNote: These specifications are based on theoretical motor performance and are not specific to any amplifier.MPP/MPJ Size 115 Speed-Torque PerformanceMPP/MP J Size 142 Specifications1 Assumes motor is mounted to an aluminum plate with dimensions of 12” x 12” x 1” for 142 mm motor frames.2 Maximum winding temperature is 155°C. Thermal protection device threshold may be at a lower temperature.3 These ratings are valid for Parker drives. Other drives may not achieve the same ratings.4 ±10%5 ±30% @ 1kHz6 Reference onlyNote: These specifications are based on theoretical motor performance and are not specific to any amplifier.MPP/MPJ Size 142 Speed-Torque PerformanceMPP Size 190 Specifications 230 VAC Models1 Assumes motor is mounted to an aluminum plate with dimensions of 12” x 12” x 1” for 190 mm motor frames.2 Maximum winding temperature is 155°C. Thermal protection device threshold may be at a lower temperature.3 These ratings are valid for Parker drives. Other drives may not achieve the same ratings.4 ±10%5 ±30% @ 1kHz6 Reference onlyNote: These specifications are based on theoretical motor performance and are not specific to any amplifier.MPP Size 190 Speed-Torque PerformanceMPP Size 270 Specifications1 Assumes motor is mounted to an aluminum plate with dimensions of 21” x 21” x 1” for 270 mm motor frames.2 Maximum winding temperature is 155°C. Thermal protection device threshold may be at a lower temperature.3 These ratings are valid for Parker drives. Other drives may not achieve the same ratings.4 ±10%5 ±30% @ 1kHz6 Reference onlyNote: These specifications are based on theoretical motor performance and are not specific to any amplifier.MPP Size 270 Speed-Torque PerformanceFrame Sizes 92 – 142MPP/MP J DimensionsDimensions – mm (in)MPP/MPJ115x 48.5 (1.91”); MPP/MPJ142x 51.6 (2.03”)Dimensions – mm (in)Frame Sizes 190 – 270MPP/MP J Optionsavailable in standard lengths of 10, 25, 50 feet. Other lengths available. -yy denotes cable length in feet. Cables available in standard lengths of10, 15, 30 feet.Power CablesIf selecting BiSS-C/P-series encoder with P-series drive, use power cable with -yy suffix2Compax3 with firmware version R092-42, hardware version CPT17 or newer.3If this encoder is used with P-Series drive, choose power cable with -yy suffix.1 Motor sizes 92 – 142 use size 1.0 PS Connector; sizes 190 – 270 use size 1.5 PS Connector2-xx denotes cable length in feet. Motor power and feedback cables available in standard lengths of 10, 25, 50 feet.-yy denotes cable length in feet. Available in standard lengths of 10, 15, and 30 feet. Other lengths are available. Drive current values are default values. When running Drive PWM frequency at values other than default, current output values will change. Please consult drive manual for current values, and select motor power cable accordingly. Use “-yy” cables for P-Series encoder with P-series drive.cables available in standard lengths of 3, 10, 20 meters.The PS connector option for MPP/MPJ motors feature high-quality Hypertac - Interconnectron circular connectors mounted to the motor body. These connectors are a right-angle mount and can be fully rotated. This allows for greater cable routing options. Mating cables are specified and ordered separately. The PS option joins the motor phase wires and brake leads into a one connector. The second connector has motor feedback signals, Hall effect signals, and thermistor signals.MPP/MP J OptionsResolver Feedback(Order Code 41)Absolute EncodersIncremental Encoder/Hall(order code 3E)“PS” and “PF”Connectors (all motor sizes)Phase B-APhase A-CClockwise rotation as viewed from front shaft.Phase C-BHall #1Hall #2Hall #3Commutation ChartYELLOW/WHITER2R1RED/WHITEBLACKS3S1REDSTATOR SECONDARY Phasing Equation:For CW rotation of rotor E S1-S3 = KE R1-R2E S2-S4 = KE R1-R2 SINÿResolver Schematic DiagramIncremental Encoder SpecificationsHall Effect SpecificationsSICK Hiperface Absolute Encoder SpecificationsResolver SpecificationsHeidenhain Absolute Encoder SpecificationsBiSS-C Encoder Specifications(Order Code 4B)MPP/MP J Options* Consult factory for exact weights and inertia for specific motor.**Verify current capability of amplifier’s brake circuitry.MPP/MP J Ordering Information Fill in an order code from each of the numbered fields to create a complete model order code.Order Example:MPJ 092 2 C 1E – N PS BIssue Date Jan2021© 2021 Parker Hannifin CorporationParker Hannifin CorporationElectromechanical & Drives Division 1140 Sandy Hill Road Irwin, PA 15642 USA Tel: (724) 861-8200 800-245-6903Fax: (724) 861-3330Email:**********************EM&D Sales OfficesAustraliaParker Hannifin (Australia) Pty Ltd.9 Carrington Road Castle Hill NSW 2154AustraliaTel: +61 (0) 2 9634-7777 Fax: +61 (0) 2 9634 3749BrazilParker Hannifin Ind. Com Ltda.Av. Lucas Nogueira Garcez 2181Esperança12325-900 Jacareí, SP Tel: 12 3954 5100Fax: 12 3954 5262Email: a ***************************CanadaParker Hannifin (Canada) Inc.160 Chisholm DrMilton, Ontario L9T 3G9 Tel: 905-693-3000 Fax: 905-876-1958Email:****************************ChinaParker Hannifin Motion & Control (Shanghai) Co., Ltd280 Yunqiao Rd. Jin Qiao Export Processing ZoneShanghai 201206, China Tel: (86-21) 50312525Fax: (86-21) 64459717FranceParker SSD Parvex 8 avenue du Lac B.P . 249F-21007 Dijon CedexTel: +33 (0) 3 80 42 41 40Fax: +33 (0) 3 80 42 41 23GermanyElectromechanical EuropeParker Hannifin GmbH & Co KG Robert-Bosch-Strasse 22 D-77656 Offenburg GermanyTel: +49 (0) 781 509 0Fax: +49 (0) 781 509 98176Email:********************IndiaParker Hannifin India Pvt. LtdAutomation Group-SSD Drives Div.133 & 151 Developed Plots Estate Perungudi, Chennai 600 096Tel: 044-4391-0799Fax: 044-4391-0700ItalyParker Hannifin SpA Via Gounod 120092 Cinsello Balsamo Milano, ItalyTel: +39 02 361081Fax: +39 02 36108400Email: ********************KoreaParker Hannifin Korea9th Floor KAMCO Yangjae Tower 949-3 Dogok 1-dong Gangnam-gu Seoul 135-860, Korea Tel: 82-2-559-0454Fax: 82-2-556-8187MexicoParker Hannifin de Mexico Eje uno Norte No.100Parque Industrial Toluca 2000 Toluca, CP 50100 México Tel: 52-722-275-4200Fax: 52-722-279-0316SingaporeParker Hannifin Singapore Pte Ltd 11, Fourth Chin Bee Road Singapore 619702Tel: (65) 6887 6300Fax: (65) 6265 5125/6261 4929TaiwanParker Hannifin Taiwan Co., Ltd No. 40, Wuchiuan 3rd Road Wuku Industrial ParkTaipei County, Taiwan 248ROCTel: 886 2 2298 8987Fax: 886 2 2298 8982ThailandParker Hannifin (Thailand) Co., Ltd.1265 Rama 9 RoadSuanluang, Bangkok 10250 ThailandTel: (66) 2 186 7000Fax: (66) 2 374 1645UKParker Hannifin Ltd.Tachbrook Park Drive Tachbrook Park Warwick CV34 6TUTel: +44 (0) 1926 317970Fax: +44 (0) 1926 317980USAParker Hannifin Electromechanical & Drives Division/Compumotor/CTC 5500 Business Park DriveRohnert Park, CA 94928 USA Tel: 704-588-3246 800-358-9070Fax: 707-584-8015Email:**********************Parker Hannifin Electromechanical & Drives Division/Daedal 1140 Sandy Hill Road Irwin, PA 15642Tel: 704-588-3246 800-358-9070Fax: 724-861-3330Email:**********************Parker Hannifin Electromechanical & Drives Division 2101 N. Broadway New Ulm, MN 56073Tel: 704-588-3246 800-358-9070Email:**********************。
Parker产品操作手册说明书

Operating ManualThank you for your choice of Parker product. Please read this operating manual carefully and use the product correctly. Keep this operating manual in case questions arise about this product in the future. If this operating manual becomes unreadable or lost, consult our distributors or Parker sales offices.For Safety UseThe following safety precautions are provided to prevent damage and injury to personnel and to provide instructions on the correct usage of this product. These precautions are classified into 3 categories: “CAUTION”, ”WARNING”, and “DANGER” according to the severity of possible injury or damage and the likelihood of such injury or damage. Be sure to comply with all precautions. Also comply with safety regulations such as JIS B 8370(*1), Industrial Safety and Health Law, and High Pressure Gas Safety Law, and ISO 4414(*2).Danger:Indicates an impeding hazardous situation whichmay arise due to improper handling or operationand could result in serious personal injury or death.Warning:Indicates a potentially hazardous situation which may arise due to improper handling or operationand could result in serious personal injury or death.Caution:Indicates a potentially hazardous situation which may arise due to improper handling or operationand could result in personal injury or property-damage-only accidents.*1 JIS B8370 : General Rules for Pneumatic Systems*2 ISO 4414: Pneumatic fluid power recommendations for the application of equipment totransmission control system.● This product is designed for air blowgun.Do not use it for other purposes.● Use compressed air from an air compressor.Do not use air from a high pressure tank or any other gas.● Do not blow air from air blowgun towards personnel or animals.Direct air blow or substance blown by air blow can potentially cause injury for humans or animals.● Wear safety glasses and ear plugs.Regardless of the use of this product, wear safety glasses and earplugs when operating an air blowgun. Without proper protection, injury to eyes due to blown dust or noise induced deafness would be potentially caused.● Do not disassemble or modify this product.Disassembling or modification may causes safety accidents in addition to operation failure.● Attach a pipe fitting or joint properly.If a pipe fitting or joint are attached improperly, it may cause danger such as hose whip due to unplugged piping. Confirm the connection of hose, tube or coupler joint is tight as well as the connection to this product prior to use.● Do not use for medical equipment or cooking equipmentThis product contains a small amount of lubricant. If there is concern for contamination due to lubricant, do not use.SpecificationsFluid Compressed air Pressure Range 0.35 to 0.8MPaMaximum Flow *1 1300L/min (@0.5MPa) Ambient Temperature*210 to 50℃ Pulse Adjustment Range5 to 15HzPort SizeIN Rc1/4OUTR1/4Weight155g*1 “Maximum Flow” in this case is the flow capacity of this product,and actual flow consumption is depending on the attached air blowgun.*2 If the temperature is under the specified temperature, pulse blowmay be unstable. In this case, please use it as continuous blow temporally for a while to reach specified temperature. This product works correctly within the specified ambient temperature.Connection≪取付例≫1. Before Piping, thoroughly flush the inside of each pipe toremove chips, machining oil, and dust etc. If sealing tape is used for the thread, leave 1.5 to 2 thread turns unwrapped. Do not use liquid sealant. It has possibility to contaminate the product and may cause malfunction.Push-in fitting or joint such as coupler(Sold Separately) Air Saver Unit for Air Blowgun“Air Saver Module” HASV08R9IM-E009-aIssued :Jan.14.2016Air blowgun“Air Saver Module”HASV08R Reference blowgun:Parker LegrisPart Number: 0659 00 13(Sold Separately)WarningCaution<Example of attachment>2.When installing piping or a joint, prevent contamination of chips or sealing agent. Also tightening torque should be within the range indicated below.Port Size Tightening Torque (N ・m)R ・Rc1/412 to 143.An air filter (Nominal filtration rating of 5 micron or smaller) must be placed upstream of piping. There is no need for additional lubrication.4. Attach the piping towards the direction of air flow described on the body. If it is opposite direction, this product does not work.5.This product must be attached directly to an air blow gun. If connected with any part such as coupler, it has the possibility to decrease the capability due to pressure loss.6.This product is not water & drip proof. Do not install this product in a place with direct water contact (rain, etc). Also install this product in a place without dew condensation or direct sunlight.Product Function[Pulse Adjustment Screw]This is a throttle valve for pulse ON time adjustment (Approx.5 to 15 Hz). When tightening this screw clockwise with flat-bladedscrewdriver, the air ON time will be longer. When loosening the screw counter clockwise, the air ON time will be shorter. The air OFF time is fixed for approx. 30ms. Adjust the air ON time in accordance with using air blowgun or object. Control angle is approx. single rotation of the screw. When tightening at the end of clockwise, it will stop air output, however it is not malfunction.[Pulse/ Continuous Switching Button]Press this button when requiring continuous blow. When pushing this button, air blows continuously. To keep continuous blow, press this button and turn the button 90 degrees. To release from this mode, press this button and turn counter clockwise for pulse blow mode.DimensionsNotes for Usage● Discharge drain from upstream air filter periodically. If periodic drain discharge is difficult, Parker recommends setting up an air filter with automatic drain.● Maintenance compressor periodically. If sludge, which isproduced in compressor oil, enters pneumatic equipment, it will cause operation failure of pneumatic equipment. Coalescing filter removes oil and sludge which cannot be removed by air filter. Parker recommends setting up a coalescing filter.Effect of Pulse BlowIn many factories, air blow accounts for more than 50% of total compressed air consumption. Pulse blow can be a measure forsaving energy by reducing the consumption of compressed air while maintaining the same capability of air blow operation.・Hole machining, tap, chip removing of complex shape work ・Removing stuck dust or viscous liquid ・Blowing at narrow space・Reducing load of compressor ・Energy saving activityPulse blow is especially effective for works listed above, however it is not for all applications. There is a possibility to reduce the removal effectiveness depending on the air blowgun. Parker recommends attaching to an air blowgun that has nozzle diameter bigger than I.D.2mm and low pressure loss.Also, for the case of using reduced pressure for air supply, installing this product without regulator enables a low energy loss circuit, which provides improved blow effectiveness compared to the current circuit.Kuroda Pneumatics Ltd(Parker Hannifin Automation Division Japan)10243 Kamakazu, Asahi city, Chiba 289-2505, JapanE-mail:********************10HzWhen screwing, seal tape may enters the product and cause malfunction.Leave space of 1.5 -2 turnsUse half width seal tape. It may reduce cost as well. Cut with knife.(Not good)(Good) Air Blow Gun Connecting Port (R1/4)Pulse Control Trimmer[Note] ● Please contact our distributors or Parker for after-sales service. ● Please keep this operating manual.15HzPressure Supply Port (Rc1/4)Vent HolePulse/ContinuousSwitching ButtonFlow Flow Current Circuit Pulse Blow A i r C o n s u m p t i o n L /m i nA i r C o n s u m p t i o n L /m i nTime (sec)Time (sec) Pulse Adjustment Screw (ON Time Control)Pulse/ Continuous Switching button Time Time。
派克伺服电机M系列使用手册
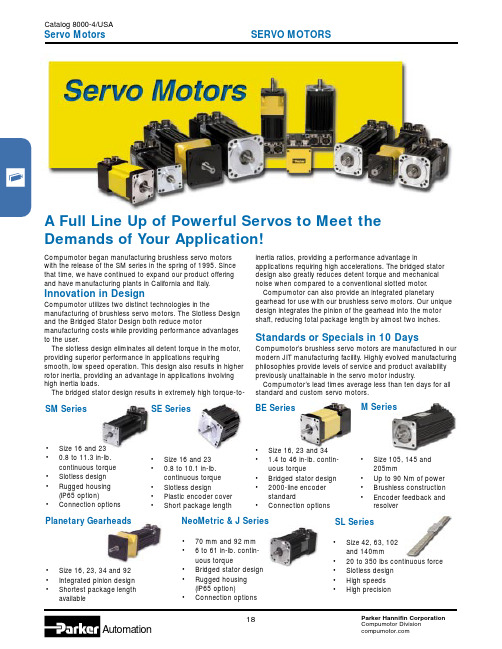
•Size 16 and 23•0.8 to 11.3 in-lb.continuous torque •Slotless design •Rugged housing (IP65 option)•Connection optionsSM Series SE Series•Size 16 and 23•0.8 to 10.1 in-lb.continuous torque •Slotless design•Plastic encoder cover •Short package lengthBE Series•Size 16, 23 and 34• 1.4 to 46 in-lb. contin-uous torque•Bridged stator design •2000-line encoder standard•Connection optionsNeoMetric & J Series•70 mm and 92 mm •6 to 61 in-lb. contin-uous torque•Bridged stator design •Rugged housing (IP65 option)•Connection options•Size 16, 23, 34 and 92•Integrated pinion design •Shortest package length availablePlanetary Gearheads SL SeriesM SeriesA Full Line Up of Powerful Servos to Meet the Demands of Your Application!Compumotor began manufacturing brushless servo motors with the release of the SM series in the spring of 1995. Since that time, we have continued to expand our product offering and have manufacturing plants in California and Italy.Innovation in DesignCompumotor utilizes two distinct technologies in themanufacturing of brushless servo motors. The Slotless Design and the Bridged Stator Design both reduce motormanufacturing costs while providing performance advantages to the user.The slotless design eliminates all detent torque in the motor,providing superior performance in applications requiringsmooth, low speed operation. This design also results in higher rotor inertia, providing an advantage in applications involving high inertia loads.The bridged stator design results in extremely high torque-to-inertia ratios, providing a performance advantage inapplications requiring high accelerations. The bridged stator design also greatly reduces detent torque and mechanical noise when compared to a conventional slotted pumotor can also provide an integrated planetarygearhead for use with our brushless servo motors. Our unique design integrates the pinion of the gearhead into the motor shaft, reducing total package length by almost two inches.Standards or Specials in 10 DaysCompumotor’s brushless servo motors are manufactured in our modern JIT manufacturing facility. Highly evolved manufacturing philosophies provide levels of service and product availability previously unattainable in the servo motor industry.Compumotor’s lead times average less than ten days for all standard and custom servo motors.•Size 105, 145 and 205mm•Up to 90 Nm of power •Brushless construction •Encoder feedback and resolver•Size 42, 63, 102and 140mm•20 to 350 lbs continuous force •Slotless design •High speeds •High precisionFeedback•Higher resolutionencoders•Higher temperatureencodersCommon Special RequestsConnectorization•Right angle connector housing•MS connectors on back cover•Special cable lengths•Hi-flex cables•Customer specified cablesand connectors•Cable exiting throughback coverFlanges•Tapped mounting holes•Customer specified flanges•Face mountBrakes•Internal or externalShafts•Special lengths•Special flats•Special keyways•Special shaft diameters•Metric shaft diameters•Hollow shafts•Rear Shaft Extension•Double flats•Shaft pinning•Pressed on gears•Center tapped•Special shaft materialsGearheads•Non-standard ratios•Customer specifiedflanges•Customer specifiedoutput shaft Compumotor offers a broad range of standard options with allof our brushless servo motor families. Our numerous shaft,feedback and connection options will fulfill the needs of most ofour customers. However, we realize that from time to time theneed arises to have a custom motor designed specially for yourapplication.Whether you need custom connectors, mounting, or acustom winding, Compumotor can build a motor designed toyour exact specifications. Compumotor provides these specialdesigns for our customers with:•Minimal impact on product lead time•Modest impact on pricing•No minimum quantitiesCompumotor’s modern manufacturing system allows us tooffer custom motor solutions without sacrificing product qualityand availability. All of our custom motors are built in ourstandard servo motor work cell, and our computerized customproduct tracking system allows us to provide consistent, high-quality custom products. And, because custom motormanufacturing is integrated into our standard manufacturingprocess, we can often build and ship custom designed motorsand cables in the same time frame as standard products.Compumotor provides this service for one simple reason: tomake it easier for you, our customer, to integrate a Compumo-tor servo motor into your application. We provide more thanjust a component, we provide a custom designed servo motorsolution.Custom Designed Servo Motors for YourSpecific Application!Windings:•Specific bus voltageFeatures•Size 105, 145 and 205mm diameters •53 to 115 lb-in continuous torque •Brushless construction •Thermal protection •IP65 option•Resolver and encoder feedback options •Two-year warranty•CAD (.dxf) drawings available •CE compliant•Electrically released brakes availableLow Cost,High PerformanceThe M Series is Compumotor’s newest series of motors.Completing Compumotor’s line of servos, the M Series moves innovative design into larger-frame motors, yet they remain affordably priced. An eight-pole design allows for highlydynamic motion while minimizing power loss within the motor itself.Part Numbering System1Standard resolver not compatible w/ APEX drives. Please contact Compumotor’s Custom Servo Motor group for motors compatible with the APEX series of drives 2Pipe thread only available in M2053 and M2054 resolver motors 3StandardM SeriesFrame,Magnet Length1053 1453 14551054 1454 20522053 2054WindingJ, K, L, M, N,P , R, SFeedbackJ - 2000 ppr encoderR - Resolver 1ShaftN - Normal K - Keyway 3ConnectionMS - Military style PT - Pipe thread 2OptionsN - None V - IP65B - Brake1 @ 40˚ C ambient, derate phase currents and torques by 7%.2 For higher-speed operation, please call the factory.3 Measured line to line, +/- 10%.4 Value is measured peak of sine wave.5 +/- 30%, line to line, inductance bridge measurement @ 1Khz.6 Initial winding temperature mut be 60˚ C or less before peak current is applied.7 Direct current through a pair of motor phases of a trapezoidally (six state) commutated motor.8 Peak of sinusoidal current in any phase for a sinusoidallycommutated motor.9 Total motor torque per peak of the sinusoidal amps measured in any phase, +/- 10%.10 Maximum time duration with 2 times (or 3 times) rated current applied with initial winding temperature at 60˚ C.M Series Performance Curves10002000300040005000600005010015020025005.6011.216.822.428.010002000300040005000600005010015020025030005.6011.216.822.428.033.650010001500200025003000350040004500100200300400500600700800011.222.433.644.856.067.279.489.6050010001500200025003000350040004500020040060080010001200500100015002000250030000400800120016002000044.889.6134.179.224.M1053KSpeed (RPM)T o r q u e (L b -i n )T orque (Nm)M1054KSpeed (RPM)T o r q u e (L b -i n )T orque (Nm)M1453LSpeed (RPM)T o r q u e (L b -i n )T orque (Nm)M1455PSpeed (RPM)T o r q u e (L b -i n )T orque (Nm)M2052PSpeed (RPM)T o r q u e (L b -i n )T orque (Nm)50010001500200025003000050010001500200025003000056.0112.168.224.280.336.M2054SSpeed (RPM)T o r q u e (L b -i n )T orque (Nm)M2053R Speed (RPM)T o r q u e (L b -i n )T orque (Nm)5001000150020002500300035004000450002004006008001000120022.444.867.289.6112.134.022.444.867.289.6112.134.M1454NSpeed (RPM)T o r q u e (L b -i n )T orque (Nm)CONTINUOUS PEAK(560VDC)I cs (sine) = 109.4 amps, I pk (sine) = 328.2 amps I cs (sine) = 85.0 amps, I pk (sine) = 255.0 amps I cs (sine) = 55.7 amps, I pk (sine) = 167.1 ampsI cs (sine) = 63.6 amps, I pk (sine) = 190.8 ampsI cs (sine) = 60.9 amps, I pk (sine) = 182.7 ampsI cs (sine) = 40.7 amps, I pk (sine) = 122.1 ampsI cs (sine) = 23.7 amps, I pk (sine) = 71.1 amps I cs (sine) = 20.3 amps, I pk (sine) = 60.9 amps05001000150020002500300005001000150020002500300035004000056.0112.168.224.280.336.395.448.M Series Dimensional Drawings Dimensions in inches (mm)105 mm Dimensional Drawing145 mm Dimensional DrawingWiring and Cable Specifications“MS” Connection OptionsThe M Series Motors are available standard with “MS”connectors. These bayonet-style connectors provide quick-disconnect. Mating cables are specified and ordered separately. With the “MS” connection option, the motor phase and brake wires are in one connector, and the hall,encoder, and temperature switch wires are in the other connector. This option works well when using an amplifier with a built-in controller, or when all cables enter into acabinet or enclosure and then are wired into a terminal strip .“PT” Connection OptionsThe M2053 and M2054 motors with resolver feedback are available with the PT connector option due to the high current requirements of these motors. A terminal block is available inside the motor housing to make the required connections.M Series, Feedback SpecificationsCommutation ChartPhase B-A Phase A-CClockwise rotation as viewed from front shaft.PhaseC-BHall #1Hall #2Hall #3。
派克伺服电机NK型号手册

Electromechanical Worldwide Manufacturing Locations
Europe Littlehampton, United Kingdom Dijon, France Offenburg, Germany Filderstadt, Germany Milan, Italy Asia Wuxi, China Chennai, India North America Rohnert Park, California Irwin, Pennsylvania Charlotte, North Carolina New Ulm, Minnesota
Local Manufacturing and Support in Europe Parker provides sales assistance and local technical support through a network of dedicated sales teams and authorized technical distributors throughout Europe. For contact information, please refer to the Sales Offices on the back cover of this document or visit
2
1
Frameless Servo Motor - NK Series Overview���������������������������������������������������������������������������� 5 Technical Data������������������������������������������������������������������� 6 Associated Drives�������������������������������������������������������������� 7 Dimensions������������������������������������������������������������������������ 8 Order Code������������������������������������������������������������������������� 9
Parker LCB系列线性电机说明书

L C B S e r i e sContentsOverview....................................................................................................70Specifications............................................................................................73T echnical.Data .LCB040.Loading/Wear........................................................................74.LCB060.Loading/Wear........................................................................76.Drive.Torque.Requirements................................................................78.Deflection............................................................................................79Dimensions................................................................................................80Options......................................................................................................82Accessories .Sliding.Blocks......................................................................................83.External.Bumpers...............................................................................83.Electrical.Limit.Switches.....................................................................84.Clamping.Profiles................................................................................85.T rmation .Basic.Unit............................................................................................87.Intermediate.Drive.Shaft.....................................................................88Application.Fax.Form (89)LCB Compact Linear ActuatorParker.Hannifin.CorporationActuator.DivisionWadsworth,A Phone:.1-866-P ARK-ACTemail:*************************website:/actuatorL C B S e r i e s70Actuator Division1-866-PARK-ACTThe LCB SeriesLCB Markets and ApplicationsThe.LCB.series.rodless.actuator.has.proven.to.be.a.robust.and.reliable.solution.for.numerous.motion.control.appli-cations.across.many.markets.and.industries...Listed.below.are.some.examples.of.where.and.how.the.LCB.series.rodless.actuator.has.been.successfully.applied..............The.LCB.series.of.linear.actuators.incorporates.a.low.friction,.dry.running.sliding.bearing.carriage.that.provides.long.and.reliable.travel.life.even.at.100%.duty.cycle...The.low.mass.of.the.carriage.and.steel.reinforced.timing.belt.design.allows.for.very.high.acceleration.and.velocity...With.accelerations.exceeding.2G’s.and.speeds.up.to.8.m/s,parable.throughput.to.linear.motors.at.a.fraction.of.the.cost..The.simple,bined.with.Parker.motors.and.controls,.the.LCB.offers.a.fully.programmable,.high.performance.solution.at.a.great.value.......The LCB design means . . . .•.Increased.throughput.–.100%.Duty.Cycle.Operation•.High.acceleration.(20.m/s 2).and.velocity.(8.m/s)•.T wo.profile.sizes.(LCB040.&.LCB060).•.Dry.running,.low.friction.bearings.provide.long,.reliable.life•pared.to.other.bearing.type•.High.static.load.capacity.-.Well.suited.to.withstand.pressing..forces.at.standstill.......•.Short,.medium,.and.long.carriages.available.to.optimize..moment.load.capacity.L C B S e r i e s71Actuator Division1-866-PARK-ACT1 Guide The.external.sliding.guide.is.incorpo-rated.as.part.of.the.aluminum.profile..It.is.unnecessary.to.adjust.two.separate.guiding.rails..The.guide.is.maintenance.free.with.integrated.dry-film.lubricant.2 Sliding CarriageThe.sliding.carriage.is.available.in.three.lengths..With.a.longer.sliding.carriage,.there.is.greater.distance.between.the.sliding.blocks..This.improves.the.load.capacity.with.respect.to.yaw.and.pitch.moments.3 Sliding BlocksLow.friction.sliding.blocks.provide.smooth.motion.throughout.travel..Sliding.blocks.can.be.easily.changed.within.2.minutes.without.detensioning.the.timing.belt.4 Spacer PlatesThe.timing.belt.of.the.LCB040.is.ten-sioned.directly.at.the.sliding.carriage.by.means.of.spacer.plates.5 Tensioning StationOn.the.LCB060,.the.timing.belt.is.tensioned.via.tensioning.screws.at.the.tensioning.station.6 ProfileThe.profile.is.available.in.two.sizes.and.resistant.to.flexing..The.closed.profile.provides.high.torsional.stiffness..Profiles.are.dirt.tolerant,pact.design.means.minimum.installation.space.is.required.Construction7 Timing Belt DriveHigh.stiffness.and.accuracy.are.provided.by.the.generously-dimensioned.timing.belt.8 Drive Options•..Linear.actuator.with.free.shaft.end.•..Coupling.(9).&.gearbox.•..Coupling,.gearbox.&.motor.•..Coupling.&.direct.drive.motor.(10).LCB040LCB06072Actuator Division1-866-PARK-ACTDual Axis ActuatorsFor.a.dual-axis.actuator.with.the.driveon.the.right.side,.you.need.two.LCB.basic.units:.1).the.right.unit.with.drive.option.RDN.and.2).the.left.unit.with.drive.option.RSN.For.a.dual-axis.actuator,.two.LCB.basic.units.and.a.shaft.corresponding.to.the.desired.center-distance.are.required..Parker.will.deliver.the.two.basic.units.(with.mounted.couplings.–.if.this.was.ordered).and.a.separate.shaft.kit..See.page.88.for.shaft.kit.ordering.Center Distance(from.center.line.to.center.line)For.a.dual-axis.actuator.with.the.drive.on.the.left.side,.you.need.two.LCB.basic.units:.1).the.left.unit.with.drive.option.LDN.and.2).the.right.unit.with.drive.option.LSN.L C B S e r i e s73Actuator Division1-866-PARK-ACT1...Repeatability.is.unidirectional,.achieved.under.ideal.conditions.and.slow.speeds....Actual.repeatability.may.vary.with.the.application..Operating Temperature Range0°.to.60°C.(32°.to.140°F).Available Stroke LengthsLCB Specifications74Actuator Division1-866-PARK-ACTLCB040 Life vs. LoadThe.diagrams.are.valid.solely.for.guidance.and.under.ideal.operating.conditions..The.diagrams.are.based.on.a.trapezoidal.motion.sequence.with.3.identically.long.sections.for.acceleration,.constant.travel.and.deceleration.The.diagrams.are.based.on.defined.payloads.of.1.kg..Shown.are.the.respective.mass.centroids.with.their.typical.load.arms.Actuator LifeNaturally,.the.sliding.guiding.has.already.a.slight.play.under.new.condition,.so.that.the.guiding.does.not.jam.and.the.slid-ing.carriage.moves.smoothly..The.play.is.measured.as.a.gap.for.each.slide.and.is.approx..0.1.to.0.2mm.in.normal.direction.and.at.the.sides.During.the.operation,.the.play.increases.according.to.the.loads.shown.in.the.diagrams.If.a.certain.state.of.wear.is.reached.(the.wear.limit..is.0.5mm.for.the.LCB040),.the.slides.can.be.exchanged.easily.within.a.few.minutes..After.the.exchange,ing the DiagramsLife.is.shown.for.each.length.of.carriage:.short.(S),.medium.(M).and.long.(L)..The.diagrams.can.be.interpolated.with.respect.to.lifetime.and.extrapolated.with.respect.to.load..(for.example:.halved.operational.performance.results.in.halved.wear,eage.in.km).T r a v e l (1000k m )Acceleration,m/s 2T r a v e l (1000k m )Acceleration (m/s 2)T r a v e l (1000k m )Acceleration (m/s 2)T r a v e l (1000k m )Acceleration (m/s 2)L C B S e r i e s75Actuator Division1-866-PARK-ACTT r a v e l (1000k m )Acceleration (m/s 2)T r a v e l (1000k m )Acceleration (m/s 2)T r a v e l (1000k m )Acceleration (m/s 2)T r a v e l (1000k m )Acceleration (m/s2)T r a v e l (1000k m )Acceleration (m/s 2)24681012141618T r a v e l (1000k m )Acceleration (m/s 2)76Actuator Division1-866-PARK-ACTLCB060 Life vs. LoadThe.diagrams.are.valid.solely.for.guidance.and.under.ideal.operating.conditions..The.diagrams.are.based.on.a.trapezoidal.motion.sequence.with.3.identically.long.sections.for.acceleration,.constant.travel.and.deceleration.The.diagrams.are.based.on.defined.payloads.of.5.kgs.Shown.are.the.respective.mass.centroids.with.their.typical.load.arms.Actuator LifeNaturally,.the.sliding.guiding.has.already.a.slight.play.under.new.condition,.so.that.the.guiding.does.not.jam.and.the.slid-ing.carriage.moves.smoothly..The.play.is.measured.as.a.gap.for.each.slide.and.is.approx..0.1.to.0.2mm.in.normal.direction.and.at.the.sides.During.the.operation,.the.play.increases.according.to.the.loads.shown.in.the.diagrams.If.a.certain.state.of.wear.is.reached,stest.however.at.the.wear.limit.(1.0mm.for.the.LCB060),.the.slides.can.be.exchanged.easily.within.a.few.minutes..After.the.exchange,ing the DiagramsLife.is.shown.for.each.length.of.carriage:.short.(S),.medium.(M).and.long.(L)..The.diagrams.can.be.interpolated.with.respect.to.lifetime.and.extrapolated.with.respect.to.load..(for.example:.halved.operational.performance.results.in.halved.wear,eage.in.km).T r a v e l (1000k m )Acceleration (m/s 2)T r a v e l (1000k m )Acceleration (m/s 2)T r a v e l (1000k m )Acceleration (m/s 2)T r a v e l (1000k m )Acceleration (m/s 2)78Actuator Division1-866-PARK-ACTLCB Drive Torque RequirementsThe.graphs.include.both.acceleration.and.friction.forces.(2.2)(4.4)(6.6)(8.8)(11.0)(13.2)Payload,kg (lb)D r i v i n g T o r q u e ,N m (l b -i n)(2.2)(4.4)(6.6)(8.8)(11.0)(13.2)Payload,kg (lb)3.2(28.4)2.8(24.8)2.4(21.3)2.0(17.8)1.6(14.2)1.2(10.6)0.8(7.1)0.4(3.5)0.0D r i v i n g T o r q u e ,N m (l b -i n)14(124)12(10710(89)6(53)4(36)2(18)0.0D r i v i n g T o r q u e ,N m (l b -i n )8(71)(11)(22)(33)(44)(55)(66)Payload,kg (lb)(11)(22)(33)(44)(55)(66)Payload,kg (lb)14(124)12(10710(89)6(53)4(36)2(18)0.0D r i v i n g T o r q u e ,N m (l b -i n )8(71)LCB040 – Horizontal Mounting PositionLCB040 – Vertical Mounting PositionLCB060 – Horizontal Mounting PositionLCB060 – Vertical Mounting PositionLocation of Mass Barycenter or Point of Force Application2:1.RuleDrawing.shows.example.of.the.pitch.moment..Also.valid.for.roll.and.yaw.moments.respectively.I L .=.Load.lever I T .=.Support.LeverL C B S e r i e sDeflectionGraphs.show.deflection.vs..distance.between.mountings.and.load.1.0(0.225)10.0(2.25)100.0(22.5)1000.0(225)10000.02250Distance between Mountings (SA),mmF o r c e F n ,N (l b )0.1(0.0225)Distance between Mountings (SA),mm1.0(0.225)10.0(2.25)100.0(22.5)1000.0(225)10000.02250F o r c e F n ,N (l b )0.1(0.0225)LCB040LCB060LCB040 Basic DimensionsShortcarriageSMediumcarriageMSectionA-ADetailY(enlarged)x deDetailX(enlarged)NecessforchatheplasDrivestationLSDrivestationRSDrivestationLD/RDL C B S e r i e sLCB060 Basic DimensionsD r i v e s t a t i o n L SD r i v e s t a t i o n R SD r i v e s t a t i o n L D /R DDrive Orientation (R, L)Right/left.indication.looking.from.load.attachment.plate.to.drive.module.Drive Shaft (S, D)Double.shaft.(D).models.have.an.additional.shaft.on.the.op-ed.to.attach.the.shaft.for.dual-axis.actuators.With Free Drive ShaftThe.threads.to.attach.the.coupling.are.on.the.side.defined.under."Drive.Orientation". With Attached Coupling KitThe.coupling.kit.is.always.mounted.in.the.factory..Carriage Length (S, M, L)All.sliding.carriages.have.4.sliding.blocks..On.a.longer. sliding.carriage,.the.load.bearing.capacity.for.yaw.and.pitch.moments.(My.and.Mz).is.greater.L C B S e r i e sSliding BlocksThe.sliding.block.is.a.wearing.part..Four.(4).pieces.are.required.per.linear.actuator.External BumpersA-AElectrical Limit Switches1.PNP.normally.closed.contact2.Load3.LoadLCB040LCB060L C B S e r i e sClamping Profilesed.in.conjunction.with.the.standard.load.attachment.plate.to.rapidly.install.and.attach.various.conbinations.of.linear.actuators..T ed.in.the.range.of.the.drive.or.of.the.clamping.station.LCB040LCB060T-Nuts and Boltsponents. to.the.T-slots.of.the.profile.T-NutsT-Slot Bolts and NutsDIN.562DIN.934DIN.787L C B S e r i e s1.Not.all.motor/binations..bined.with.Gearbox.Option.“0”.(no.gearbox),.this.option.is.direct.mount.with.no.flange.included.patibility.and.coding.4.Stroke.is.measured.bumper.to.bumper.Maximum Standard Stroke LengthConnecting ShaftDual-Axis Actuator DimensionsLCB040LCB060L C B S e r i e s89Actuator Division1-866-PARK-ACTFaxcompletedformto(330)*****************************************Contact Information:Name.______________________________________.Phone.__________________________Company.___________________________________.email.___________________________City,.State,.Zip._________________________________________________________________Application SketchNOTES:Please.include.the.critical.dimensions.in.your.sketch.In.order.to.achieve.the.best.solution,.it.is.important.that.you.provide.as.much.in-formation.as.possible.Motion ProfileMoves Distance (Stroke)Time Thrust or Load DwellFirst.Motion Second.Motion Third.Motion Fourth.MotionMoment LoadingX.distance._______Y.distance._______Z.distance._______Environmental Requirements1. Operating Temperature .Max._______.....Min._______2. Comtanimation .(check.one)..Particle.....Liquid.Type:._______________________3. Special Considerations .________________.._____________________________________.._____________________________________Application Requirements:1. Overall Stroke .(add.25mm.per.end.minimum).____________2. Cylinder Orientation .(check.one)...Horizontal............Inverted.......Side.Mount....Vertical...Angle:..Degree._________3. Load/Tooling Weight __________________________4. Repeatability Requirements .____________________...Unidirectional.......Bidirectional5. Is the load externally guided?.(check.one)...Y es.......No.If.yes,.how?._________________________________6. Is the actuator body supported?.(check.one)..Y es.......No.If.yes,.how?._________________________________7. Life Requirements .(cycles,.distance.or.years).Hours.per.day._________....Days.per.year._________8. Special Considerations .______________________________..___________________________________________________..___________________________________________________..___________________________________________________Please attach another sheet if more room is needed.90Actuator Division1-866-PARK-ACTMotor, Drive and Control Options:1. Motor Options .(check.all.that.apply)...Stepper.............Servo...Parker.Supplied.........Customer.Supplied.(provide.print).2. Other Options .(check.one)...Drive............Drive/Controller.......Controller3. Available Line Voltage .____________4. Switches/Sensors .(quantity).End.of.Travel._______..........Home._________5. Brake Option .(check.one)...Motor........6. Special Options ._______________________________________.____________________________________________________.____________________________________________________.____________________________________________________.____________________________________________________Actuator Type and Mounting1. Drive Orientation .(check.one)..2. Drive Shaft .(check.one)...Double.Shaft3. Carriage Style (check one): See ....Medium.Carriage.....Long.Carriage..。
Parker Hannifin 电机控制器技术手册说明书
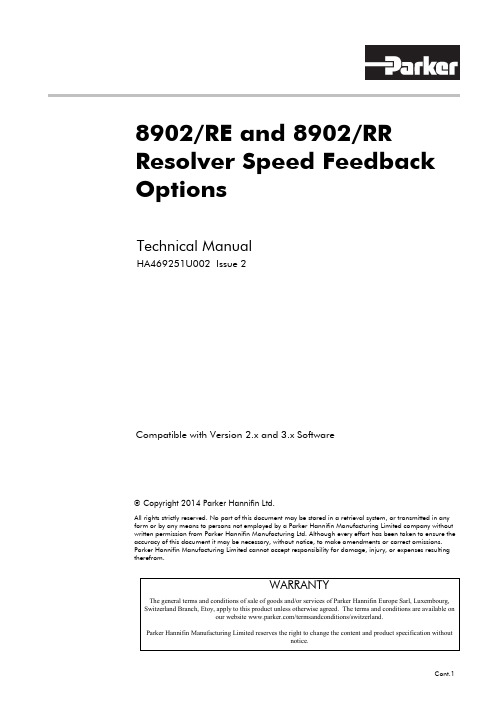
8902/RE and 8902/RR Resolver Speed Feedback OptionsTechnical ManualHA469251U002 Issue 2Compatible with Version 2.x and 3.x SoftwareCopyright 2014 Parker Hannifin Ltd.All rights strictly reserved. No part of this document may be stored in a retrieval system, or transmitted in any form or by any means to persons not employed by a Parker Hannifin Manufacturing Limited company without written permission from Parker Hannifin Manufacturing Ltd. Although every effort has been taken to ensure the accuracy of this document it may be necessary, without notice, to make amendments or correct omissions. Parker Hannifin Manufacturing Limited cannot accept responsibility for damage, injury, or expenses resulting therefrom.WARRANTYThe general terms and conditions of sale of goods and/or services of Parker Hannifin Europe Sarl, Luxembourg, Switzerland Branch, Etoy, apply to this product unless otherwise agreed. The terms and conditions are available onour website /termsandconditions/switzerland.Parker Hannifin Manufacturing Limited reserves the right to change the content and product specification withoutnotice.Cont.1WARNING!During commissioning, remove the fuses (or trip the circuit breaker) on your 3-phase supply.Make sure the power is OFF, and that it cannot be switched on accidentally whilst youare working.REFER TO YOUR MAIN PRODUCT MANUAL FOR SPECIFIC SAFETYINFORMATION ABOUT THE DEVICE YOU ARE CONTROLLING IMPORTANT:Please read this information BEFORE installing the equipment.Intended UsersThis manual is to be made available to all persons who are required to install, configure orservice equipment described herein, or any other associated operation.The information given is intended to highlight safety issues, EMC considerations, and to enablethe user to obtain maximum benefit from the equipment.Application AreaThe equipment described is intended for industrial motor speed control utilising AC induction orAC synchronous machines.PersonnelInstallation, operation and maintenance of the equipment should be carried out by qualifiedpersonnel. A qualified person is someone who is technically competent and familiar with allsafety information and established safety practices; with the installation process, operation andmaintenance of this equipment; and with all the hazards involved.SafetyAll control and signal terminals are SELV, i.e. protected by double insulation.EMCIn a domestic environment this product may cause radio interference in which case the user maybe required to take adequate counter-measures.This equipment contains electrostatic discharge (ESD) sensitive parts. Observe static controlprecautions when handling, installing and servicing this product.Cont.2Cont.3CAUTION!At any time, there may be a loss of motor control and separate/independent application measures should be taken to ensure that such loss of motor control cannot present a safety hazard.RISK ASSESSMENTUnder fault conditions, power loss or unintended operating conditions, the drive may not operate as intended. In particular:• Stored energy might not discharge to safe levels as quickly as suggested, and can still be present even though the drive appears to be switched off• The motor's direction of rotation might not be controlled• The motor speed might not be controlled • The motor might be energisedA drive is a component within a drive system that may influence its operation or effects under a fault condition. Consideration must be given to: • Stored energy• Supply disconnects• Sequencing logic• Unintended operationContentsContents PageCont.41 Description (1)•Features (1)•Part Number (1)•Used On (1)•Specifications – Resolver Interface (8902/RE and 8902/RR) (2)•Specifications – Resolver Interface (8902/RE and 8902/RR) (2)•Specifications – Emulated Encoder (8902/RR only) (2)Recommended Spare Parts (2)Installation (3)Fitting the Option (3)Wiring the System (4)•D-Type Connections (4)Approved Resolvers (6)Encoder Emulation (7)Initial Set-up (8)Configuring the 890 Drive (8)•RESOLVER Function Block (8)Motor Phasing (10)18902/RE Resolver Speed Feedback OptionDescriptionThe 8902/RE and 8902/RR Resolver Speed Feedback Options allow resolvers to be connected directly to the motor controller to provide highly accurate speed feedback measurement. In addition, the 8902/RR provides an emulated pulse encoder output.FeaturesThe Option has the following features:• Contains two differential inputs on channels Sin and Cos • Contains a carrier output signal to power the Resolver • 8902/RR contains three differential outputs, emulating a pulse encoder.Part NumberThe part number for the Resolver Speed Feedback Option is :8902/RE/00/008902/RE/00/FF (indicates a factory-fitted Option)8902/RR/00/008902/RR/00/FF (indicates a factory-fitted Option)Used OnThis Option can be used on 890 drives with the following Product Codes:890SD/.. 890SD Standalone Drive 890CD/.. 890CD Common Bus Drive890P…..Refer to the 890 Engineering Reference Manual, Appendix E for Product Code details.Note: 8902/RE may be supplied as Style1 orStyle 2 (refer Figure 1 and 2).Figure 1 - Style 1: 8902/RE Resolver SpeedFeedback OptionFigure 2 –Style 2: 8902/RR Resolver Speed Feedback Option28902/RE Resolver Speed Feedback OptionSpecifications – Resolver Interface (8902/RE and 8902/RR)Maximum Speed8902/RE:Up to 50,000RPM (with 2 pole resolver ) 8902/RR:Up to 30,000RPM (with 2 pole resolver )Carrier Output Signal 7Vrms, 8kHz Maximum Carrier Supply 70mA rms Maximum Input Voltage ±12V peak Accuracy < 5 minutesResolution Equivalent to 16 bits per electrical revolution of resolverInputsDifferential inputs, Zin ~2 k Ω Maximum input voltage : 12VpeakIsolationNoneSpecifications – Emulated Encoder (8902/RR only)Signal amplitude Compatible with RS422 and RS485 Outputs3 Differential pairs Signal nomenclatureA andB quadrature Z index pulse Number of lines per revolution 1024Isolation Outputs are isolated from drive electronicsRecommended Spare PartsWe recommend that you keep one Option as a spare to reduce down-time.38902/RE Resolver Speed Feedback OptionFigure 3 Rear ofControl Board ABBAInstallationFitting the OptionIf the Option is not factory-fitted, follow the proceduregiven below.WARNING!Disconnect all sources of power beforeattempting installation.CautionThis Option contains ESD (Electrostatic Discharge)sensitive parts. Observe static control precautions whenhandling, installing and servicing this Option.1.Undo the two screws securing Option A and Option Bto the front of the drive. If Options are not fitted,completely remove the blank covers for the Option Aand Option B slots.2.Undo the screws (A) located in the top and bottomhandles of the control board. Gently pull on the handlesto withdraw the board from the drive, supporting anyattached option boards. Note that the boards are slidingin top and bottom slots.3.Remove any other Options that are fitted to the controlboard.4.Offer up the Resolver Option through the "OPTION F"cut-out as shown opposite.5.Fit the two locating pegs of the large connector on therear edge of the option board into the locating holes onthe control board, as shown below.6.Fit the two screws and crinkle washers (C) at the rear edge of the Option.DO NOT OVERTIGHTEN.Tightening torque : 0.2Nm (28 oz-in).7.Secure with the two screws (B) to the front of the controlboard.The front panel screws (B) are self-tapping and can bequite hard to turn. This turning torque must not betransferred through the option board to the control boardconnector. To avoid this hold the option board with onehand, while tightening the front panel screws with theother. DO NOT hold the control board while tighteningthese screws.8.Refit any other Options that were removed from the controlboard.9.Replace the control board (with attached Options) into thedrive.10.Tighten the Option A and Option B screws; or importantly,fit the blank covers and secure with the screws.48902/RE Resolver Speed Feedback OptionWiring the SystemWARNING!Disconnect all sources of power before attempting installation.CautionThis Option contains ESD (Electrostatic Discharge) sensitive parts. Observe static controlprecautions when handling, installing and servicing this Option.D-Type ConnectionsNote: For correct operation, carrier, sine and cosine must be connected as specified. Poorperformance/motor behaviour may occur if these signals are left unconnected or are connected incorrectly.Take special care wiring the resolvers to the Option due to the low level of the signals. Ideally use twisted-pair, screened cable with an overall screen and a screen over each individual pair. It may be possible to use a cable with just a screen over each individual pair. The signal pairs should have characteristic impedance of 120Ω. To ensure compliance with the EMC Directive the overall cable screen should be connected to the connector body and to the cable clamp. Connect overall screen and individual screens together, on each side of the cable. Use the resolver manufacturer's recommended cable.1234567891011121314151 Sin+ input23 Cos+ input4 not connected5 not connected6 not connected78 + carrier input, reference voltage9 Sin- input10 11 Cos- input 12 not connected 13 not connected 14 not connected15 - carrier input, reference voltagenot connected not connectednot connected OPTION BOARD+ -+ -SinCos +-+-RESOLVERSin Cos +-+-Power+-BracketX30X30 Terminal:Carrier Input+-Figure 4 Wiring Diagram 8902/RE58902/RE Resolver Speed Feedback Option134567891011121314151 Sin+ input23 Cos+ input4 Index Z+ output5 Quadrature A+ output6 Quadrature B+ output78 + carrier input, reference voltage9 Sin- input 10 11 Cos- input12 Index Z- output13 Quadrature A- output 14 Quadrature B- output15 - carrier input, reference voltagenot connected not connectednot connected OPTION BOARD+ -+ -Sin Cos +-+-RESOLVERSin Cos +-+-Power+-BracketX36X36 T erminal:Carrier Input+-2+-+-+-Q u a d r a t u r e AQ u a d r a t u r e B I n d e x ZT o encoder inputFigure 5 Wiring Diagram 8902/RR68902/RE Resolver Speed Feedback Option Resolver DiagramCOSINE input : Vcos = V(S1-S3) = V(R1-R2) x TR x cosθSINE input : Vsin = V(S2-S4) = V(R1-R2) x TR x sinθWith : Vin = V(R1-R2) : carrier signal ( reference voltage )TR = transformation ratioϕ = positionApproved ResolversParker SSD Drives approve the following Resolvers for use with the 8902/RE Speed FeedbackOption.Tamagawa TS2610N71E64Tamagawa TS2620N701E11Tamagawa TS2620N861E11Tamagawa TS2640N821E64Encoder EmulationEncoder emulation creates three differential pairs, A, B and Z. These emulate a 1024 lineencoder rotating at the same speed and direction as the resolver. Clockwise rotation of theencoder shaft normally causes channel A to lead channel B, but this could reverse depending onthe resolver wiring.Initial Set-upConfiguring the 890 DriveNote:The DSE 890 Configuration Tool is Parker SSD Drives’ Windows-based blockprogramming software and is supplied with each drive.Use the DSE 890 Configuration Tool to configure the RESOLVER function block, as detailedbelow.You will require a PMAC (Permanent Magnet AC) Configuration when using DSE 890: create a"New Configuration" in DSE 890 and select "890 Permanent Magnet AC" in the dialog box.Double-click on the MOTOR CONTROL function block in the new configuration to display theRESOLVER function block.DSE 890 offers a "Motor Wizard" to quickly enter parameter information into the RESOLVERfunction block: from the menu at the top of the screen select Edit → Motor Wizard. In the pop-up dialog box you can now select the motor and resolver from the drop-down lists.Alternatively, you can enter parameter information directly into the RESOLVER function block.The parameters are described below.RESOLVER Function BlockSETUP::MOTOR CONTROL::RESOLVERThis block allows Speed Feedback to be measured using a resolver.Note:Only parameters relevant to the Resolver are described below.Parameter DescriptionsNAME Range:Resolver name/designationPOLES Range: 2 to 20Number of resolver poles. In case of multi-pair poles resolver, the resolution of the resolveroption is multiplied by the number of pair poles.RATIO Range: 0.2 to 1.0Transformation ratio of the resolverSPEED MAX Range: 0 to 231 (user units)Mechanical maximum speed supported by the resolver.ACCURACY Range: 0 to 60.0 minutesThis parameter represents the nominal accuracy of the resolver. (This information is onlyinformative and could be left unspecified).CARRIER VOLTAGE Range: 5.0 to 10.0 VrmsThis parameter represents the nominal carrier voltage for the resolver. (This information isonly informative and could be left unspecified).CURRENT Range: 0.0 to 70mA rmsThis information represents the nominal current needed to run the resolver. (This informationis only informative and could be left unspecified).INERTIA Range: 10.0 to 100000 Kgcm²This information represents the resolver rotor inertia. (This information is only informativeand could be left unspecified).Parameter DescriptionsTRIP Range: FALSE-TRUEThis information gives the resolver processing state :-TRUE : the drive has tripped. Verify the connection of the resolver.-FALSE : the system is able to run. The position and speed information are available. POSITION SET UP Range : - 180° to 180° Relative position between the position 0 degree from the resolver and the Parvexconvention for the motor phasing.Refer to "Motor Phasing" below.INIT DONE Range: FALSE-TRUEThis information gives the resolver processing init state :-TRUE : the resolver processing is running, the init state is completed and the speed and position information are normally available-FALSE : the initialisation phase is on-going. Position and speed information are not available.The initialisation phase could be viewed :-at power on,-after a trip and reset action.REVERSE CNT DIR Range: FALSE-TRUE This input allows you to reverse the counting direction of the resolver feedback.FALSE : counting direction is positive when the motor spins in a clockwise direction, looking to the front shaft of the motorTRUE : counting direction is negative when the motor spins in a clockwise direction, looking to the front shaft of the motorSPEED FILTER Range : 10.0 to 1000.0 Hz This input allows you to select the cutting frequency of the first order low pass filter applied to the resolver speed output.Motor PhasingThe control of PMAC brushless motors is allowed if the relative position between the stator andthe rotor is well known. The resolver must be set up to define the relative position between theresolver and the 3 motor phases. For the 890 drive, the convention is as follows :♦when the motor runs in a clockwise direction, looking to the front shaft of the motor, the 3successive phases are M1, M2 and M3 as shown below.♦The resolver must be adjusted in a way to give a position of 0 degrees when the M1 motorphase crosses the 0 Volt line in a rising variation. For example, a 6 pole motor associatedwith a 2 pole resolver will give the following curves:。
派克Parker伺服电机SMHSMB选型手册
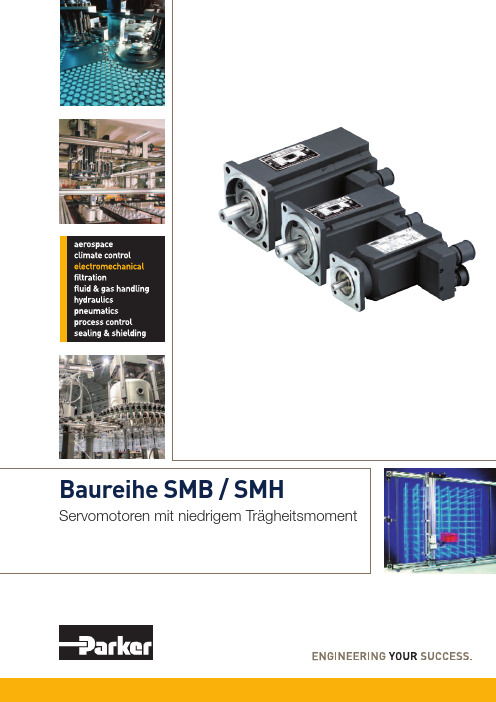
Lokale Fertigung und Support in Europa Ein Netzwerk engagierter Verkaufsteams und autorisierter Fachhändler bietet Beratung und garantiert lokalen technischen Support. Die Kontaktdaten der Verkaufsbüros finden Sie auf der Rückseite dieses Dokuments oder Sie besuchen unsere Website:
2
1
பைடு நூலகம்
Servomotoren mit niedrigem Trägheitsmoment - SMB / SMH Übersicht��������������������������������������������������������������������������� 5 Technische Daten��������������������������������������������������������������� 6
Technische Daten��������������������������������������������������������������������������������������������� 6 Geschwindigkeits-/Momentendiagramme������������������������������������������������������ 8 Abmessungen von Standardmotoren mit Resolver Feedback���������������������� 11
Parker Servo Motors选择指南说明书

Servo MotorsRotary Motor Selection GuideThis document provides a quick selection guide for Parker Servo Motors. To select the correct motor using the table below, use the columns in order going from left to right (starting with voltage). General motor descriptions are provided on page 2 of this document to assist in selecting the correct motor family. Additional information on each of the motors can be found on the product web pages. (See links in comments below)IP20 - Not protected from liquids or dust.IP40 - Not protected from liquids.IP54 - Protected from limited dust, water spray from any direction. IP65 - Dust-tight, high pressure water jets. IP69K - Dust-tight, high pressure & temp wash down.Parker Hannifin CorporationElectromechanical and Drives Division 9225 Forsyth Park Dr.Charlotte, NC 28273Tel: (704) 587- 3246Fax: (704) /emn© 2017 Parker HannifinSpecifications are subject to changeParker offers a wide variety of motors to meet the needs of many applications. Motortechnologies that provide high power density, or better inertia matching. Motors that provide rapid acceleration or zero cogging. And still others offer the most competitive solution for high volume OEM opportunities. All are high performance brushless servo motors offering a wide range of power starting at 50 watts and going all the way up to 22 KW. Feedback options such as incremental and absolute encoders, resolvers and fail safe brakes areoffered across the product lines.BRO-SM-0217Parker’s ability to offer specialized motors is unmatched. Many of our standard motors can be customized to meet specific needs. Examples include unique windings to optimize power management, high speed motors up to 30,000 rpm, and special environments such as high/low temperature, clean room, or vacuum and mechanical modifications such as modified shafts or special connectors - even special coatings such as mil-spec paint or nickel plate. For the right opportunity, Parker will even design a motor from scratch such as one that pow -ered an electric motorcycle for the commercial market. With a full team of design engineers under the roof of about 100,000 sq-ft manufacturing facility, Parker has the core competency to put the most demanding applications into motion.Parker provides a variety of motors to meet unique application requirements. Motors that are designed to be explosion proof or are to be used in harsh washdown environments (IP69k) found in the food and beverage industry. Motors that can be directly coupled to what they are driving with a very high degree of positional accuracy as well as others that can be directly built into equipment to save space and to improve performance. All are high performance brushless servo motors with options such as incremental and absolute encoders, resolvers, and failsafe brakes.New Ulm, MN - Motor and Gearhead Business UnitFor 25 years, our New Ulm location has delivered high quality rotary servo motors, gearheads, and gearmotors. Standard products and core expertise support customer application development through the custom engineered solutions process. With a focus on providing a superior customer experience, the business unit has grown in industries such as automotive, aerospace, semiconductor, packaging, robotics, and more recently vehicle electrification. The New Ulm location has a strong foundation and is ISO 9001:2008 certified and AS 9001/TS16949 compliant.Industrial MotorsStandardized to Fit Your Environment Needs“Tailor-made” Motor Solutions。
ParkerEMD无刷伺服电机HJ系列型号手册

Order code motors ..................................................................................29 Order code cables ...................................................................................30
Automation
3
Parker Hannifin GmbH EMD HAUSER
192-060011 N5
Servo motors
Synchronous servo motors manufactured by Parker Hannifin, Elektromechanik Europa
Todays' levels of electrical drive technology mean that different specific synchronous servo motors are required depending on the application in question.
Automation
Synchronous Servo Motors
Catalogue: 192-060011 N5 / UK Version 5 / December 2000
192-060011 N5
Servo motors
Automation
2
Parker Hannifin GmbH EMD HAUSER
Options ......................................................................................................15 Motor overview of HDY – motors ............................................................16 Dimensional drawings..............................................................................17
ssd派克RX系列直流伺服电机手册
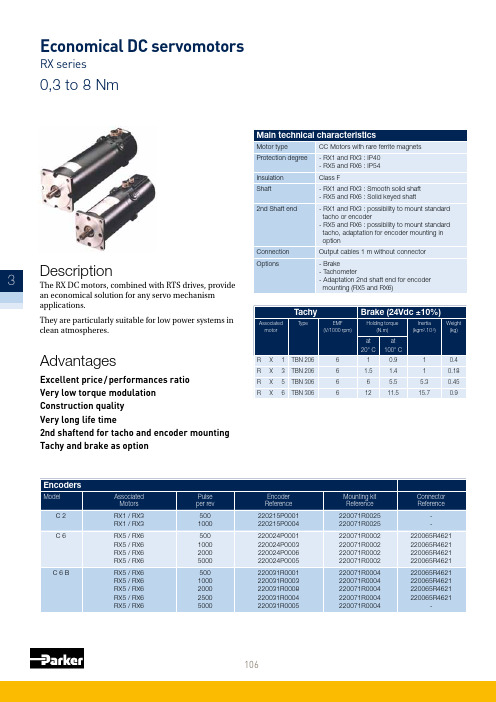
Typical combination
RTS 3/10-40 M RTS 10/20-60 * RTS 10/20-60 * RTS 10/20-60 * RTS 12/24-130 T RTS 12/24-130 T RTS 12/24-130 T RTS 20/40-130 T
3
107
Economical DC servomotors
4
Motor + Tacho + Encoder adaptation (size 5 and 6 only)
5
Motor + Brake + Encoder adaptation (size 5 and 6 only)
6
Motor + Tacho + Brake + Encoder adaptation (size 5 and 6 only)
Insulation
Class F
Shaft
- RX1 and RX3 : Smooth solid shaft - RX5 and RX6 : Solid keyed shaft
2nd Shaft end
- RX1 and RX3 : possibility to mount standard tacho or encoder
Inertia (kgm2.10-5)
Weight (kg)
Advantages
Excellent price / performances ratio
at
at
20° C 100° C
R X 1 TBN 206
6
1
0.9
1
0.4
R X 3 TBN 206
派克汉尼汾FL20系列伺服驱动器和电机说明书
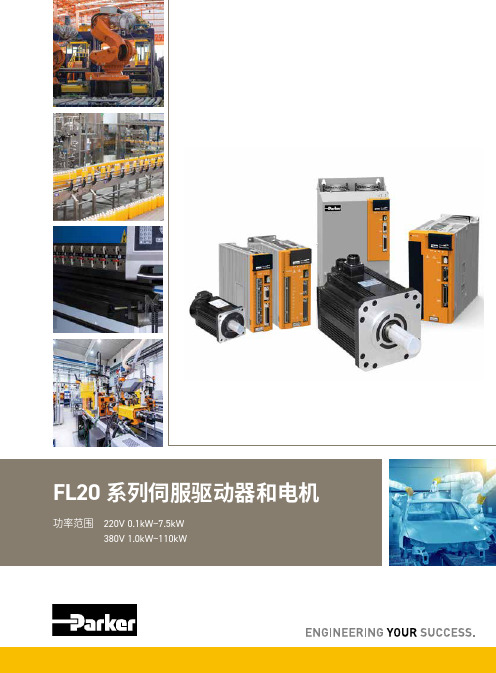
警告 - 用户责任错误以及不恰当的选择者使用本文档所描述的产品及其相关部件,能够导致死亡、人身伤害及财产损失。
� 来自派克汉尼汾公司产品以及其它的相关信息,它附属的机构或者授权的经销商在技术上具有专业知识并为长远投资的客户提供 产品或系统选件。
� 用户通过自己的分析和测试,单独并负责地做出最后的系统和组件的选型,并确认符合性能、耐用性、维修、安全设置以及应用 方面的警告要求。
用户必须认真进行在应用、遵循合适的工业标准以及遵循产品目录或其它由派克、其附属机构、经销商提供的 材料中所涉及的信息等所有方面的分析。
� 派克、其附属机构或者经销商基于数据或规格提供组件或系统选件给客户,客户负责任的决定这些数据和规格是合适的并且符合 所需的应用,并合理地使用这些组件或系统。
FL20 伺服驱动器FM 系列伺服电机概览...........................................................................................5订货号.......................................................................................6技术参数...................................................................................7驱动器接口..............................................................................10端子信息.................................................................................12输入输出信号配线..................................................................16连接到外围设备......................................................................17典型主电路配线......................................................................18伺服驱动器尺寸......................................................................20概览.........................................................................................24订货号.....................................................................................25产品一览表 (26)技术参数.................................................................................29电机TN曲线图.........................................................................32电机尺寸.................................................................................36配件.........................................................................................41优选驱动器和电机匹配表. (44)派克汉尼汾运动与控制领域的先行者前沿的产品设计在伺服、控制、 电机和机械产品的设计和制造方面,派克拥有超过40 年的经验。
Parker Hannifin BE Series Servo Motors说明书

Contact Information:Parker Hannifin CorporationElectromechanical & Drives Division 9225 Forsyth Park Dr.Charlotte, NC 28273phone: 800.358.9068 / 704.588.3246fax: 707.584.8029email:**********************/emdusaThe BE Series is designed specifically as a very cost-effective alternative to comparably sized servos. The BE Series also provides exceptional torque with the design’s increased number of magnetic poles. Comparably sized servos have four magnetic poles on the rotor, while BE Series motors have eight.Parker’s BE Series brushless servo motors produce high continuous stall torque in a cost-saving and performance-enhancing package.Unlike traditional servo motors, the BE Series does not have a separate metal housing. Instead, the motorstator laminations are not only used for performance, but provide both structural integrity and the motor shape. This design reduces both material costs and the time required to assemble the motor.In addition to the manufacturingadvantages, the exposed laminations reduce thermal resistance. This allows the heat generated by the motor to escape to the ambient surroundings more efficiently, thus improving time in the peak region and duty cycle.Parker’s wide range of Bayside ® planetary gearheads are perfectly matched to the BE Series motor. Easy selection can be made using Parker’s MotionSizer.Features• NEMA 16, 23, and 34 sizes• From 1.4 to 46.8 in-lb (5.24 Nm) continuous torque• Brushless construction• Eight-pole open-laminationdesign provides increased torque and lower cost• High torque density packaging • Bridged stator design – quiet operation• High performance neodymium magnets• Thermoswitch protection on NEMA 23 and 34 sizes• 2000 line encoder standard (8000 ppr post-quad)• Resolver feedback option• Several connector design choices • Holding brake option available on size 34, custom order on size 23• Custom modifications available • Industry-leading 10-day delivery • Two year warranty• STP solid models and CAD (dxf) drawings available (free download at )BE Series Servo Motors NEMA Size 16 Performance (Data at 120 VAC)Note: These specifications are based on theoretical motor performance and are not specific to any amplifier.1 @ 25°C ambient, 125°C winding temperature, motor connected to a 10” x 10” x 1/4” aluminum mounting plate; @ 40°C ambient derate phase currents and torques by 6%.2 Maximum winding temperature is 155 °C. Thermal protection device threshold may be at a lower temperature.3 These ratings are valid for Parker drives. Other drives may not achieve the same ratings.4 Maximum speed is 5000 rpm.5 Measured line-to-line, ±10%. ±30%, line-to-line inductance bridge measurement @1Khz.6 Reference only.7 Total motor torque per peak of the sinusoidal amps measured in any phase, ±10%.8 Initial winding temperature must be 60°C or less before peak current is applied.9 No thermal switch within BE16. Use servo drive thermal model for overtemp protection or lower peak current.NEMA Size 16 Speed-T orque PerformanceBE Series Servo Motors NEMA Size 23 Performance (Data at 240 VAC)1 @ 25°C ambient, 125°C winding temperature, motor connected to a 10” x 10” x 1/4” aluminum mounting plate;@ 40°C ambient derate phase currents and torques by 6%.2 Maximum winding temperature is 155 °C. Thermal protection device threshold may be at a lower temperature.3 These ratings are valid for Parker drives. Other drives may not achieve the same ratings.4 Maximum speed is 5000 RPM.5 Measured line-to-line, ±10%. ±30%, line-to-line inductance bridge measurement @1Khz.6 Reference only.7 Total motor torque per peak of the sinusoidal amps measured in any phase, ±10%.8 Initial winding temperature must be 60°C or less before peak current is applied.9 Use servo drive thermal model for overtemp protection or lower peak current.NEMA Size 23 Speed-T orque PerformanceBE Series Servo Motors NEMA Size 34 Performance (Data at 240 VAC)1 @ 25°C ambient, 125°C winding temperature, motor connected to a 10” x 10” x 1/4” aluminum mounting plate;@ 40°C ambient derate phase currents and torques by 6%.2 Maximum winding temperature is 155 °C. Thermal protection device threshold may be at a lower temperature.3 These ratings are valid for Parker drives. Other drives may not achieve the same ratings.4 Maximum speed is 5000 RPM, except BE344 which is limited to 3000 RPM max speed.5 Measured line-to-line, ±10%. ±30%, line-to-line inductance bridge measurement @1Khz.6 Reference only.7 Total motor torque per peak of the sinusoidal amps measured in any phase, ±10%.8 Initial winding temperature must be 60°C or less before peak current is applied.9 Use servo drive thermal model for overtemp protection or lower peak current.NEMA Size 34 Speed-T orque PerformanceBE Series Servo MotorsDimensions — NEMA Size 16Inches (mm)FL ConnectionFO Connection(-xFOx)Dimensions — NEMA Size 23Inches (mm)FO Connection(-xFOx)BE Series Servo Motors1.49MS Connection(-xMSx)FO Connection(-xFOx)Dimensions — NEMA Size 34Inches (mm)Recommended Parker Drives for BE Series MotorBE Series Servo MotorsCable OptionsInclude length to complete power cable part number:XX = Cable Length (ft)For example, 05 = 5 ftStock Lengths: 10, 25, 50 feetNon-Stock Lengths: 5, 15, 20, 30, 35, 40 and 45 feetPower Cables** All power cables have flying lead ends. All PS connector type power cables include brake leads, whether or not the motor has a brake. Feedback Cables (with Parker drive-compatible terminations)*Include brake leads, whether or not the motor has a brake.Feedback OptionsResolver Specifications* @ 90°CEncoder SpecificationsR2R1S3S1S1-S3 R1-R2E S2-S4 = KE R1-R2 SINØPhase B-APhase A-CClockwise rotation as viewed from front shaft.Phase C-BHall #1Hall #2Hall #3Resolver SchematicCommutation ChartElectrically-Released Brake OptionPS Option – Parker Standard (-xPSx) Pin ConnectionsBE Series Servo MotorsPS Incremental Encoder/Hall (J, L and Q) PinPowerThe PS connector option for the BE motors features high-quality Hypertac - Interconnectron circular connectors mounted to the motor body.Mating cables are specified and ordered separately. The PS option joins the motor phase wires and brake leadsIP65.NOTE: For customers preferring to build their own mating cables, a PS connector kit (Part #: PS-CONN-KIT), is available. The kit contains a mating PS power connector, PS feedback connector and connector pins, allowing customers to build cables to their own specification. Special tools are not included in the kit.MS Option – Military Style (-xMSx) Pin ConnectionsMS Incremental Encoder/Hall and Brake (J andPowerFeedbackThe “MS” connection option for the BE Series motors provides quickdisconnect, bayonet style connectors attached to the motor body. Mating cables are specified and ordered separately.With the “MS” connection option, the motor phase wires are in one connector, and the hall, encoder, temperature switch, and brake wires are in the other connector. This option works well when using an amplifier with a built-in controller, or when all cables enter into a cabinet or enclosure and then are wired into a terminal strip.When specifying the “R” (resolver) feedback option, the motor phase wires reside in one connector, the resolver signal, temperature switch, and brake wires in the other.Wiring Connections for:FL Option – Flying Leads with Enclosed Feedback (-xFLx) FO Option – Flying Leads with Exposed Feedback (-xFOx) 10 Option – 10’ Cable (-x10x)BE Series Servo MotorsMotor Power LeadsFO/FL Flying LeadsThe FO/FL cable option for the BE motors features 18” flying leads for both feedback and power connections. The only variable is whether or not the feedback device is fully enclosed (FL) or fully exposed (FO).These options are for OEM customers that wish to reduce cost as much as possible and fully integrate their own cable solutions.10 - 10’ hard wired cableThe 10’ cable option for the BE motors uses the standard Parker cable hard wired into the rear of the motor. The cables have full strain relief and completely enclosed feedback. While custom lengths are available, it is not recommended to exceed 10 feet between motor and drive.34NEMA Size 34 framee Stack Configuration01/2 stack magnet (NEMA 23 only)1 1 stack magnet2 2 stack magnet3 3 stack magnet4 4 stack magnet (NEMA 16 and 34 only)r Winding*C NEMA 16 onlyZ NEMA 16 onlyD NEMA 16 and 23 onlyF AllG NEMA 23 and 34 onlyH NEMA 34 onlyJ NEMA 34 onlyK NEMA 34 onlyL NEMA 34 only* Select based on appropriate performance characteristics, see pages 2-7)y Shaft OptionsN Round shaftF FlatK Keyway (not available on NEMA 16)u Connector OptionsPS Parker standard connectors, all feedbackoptions1010 ft. cableFL Flying leads, 18” (housed feedback)FO Flying leads, 18” (exposed feedback)MS Military stylei OptionsN NoneB Brake (NEMA 23 and 34 only)Need more torque? Use a Parker gearhead!Gearhead Advantages• Multiply torque allowing smaller motors (and drives) to be used,saving $$• Reduce the reflected inertial load to the motor, making it easier totune and increase stiffness and stability• Have high sideload capacity• Increase low speed smoothness• Shorten inline length with right-angle gearheadsParker Gen II Stealth® gearheads are designed with helical planetary gears that provide low backlash, high-stiffness, high torque and long life. Stealth gearheads are ideal for high performance applications. Parker PV series gearheads are standard-grade gearheads with high sideload capacity and the power of a planetary gearhead in a cost-effective solution.Issue Date 5/17/2019© 2019 Parker Hannifin Corporation BRO-BE-0519Parker Hannifin CorporationElectromechanical & Drives Division 9225 Forsyth Park Dr.Charlotte, NC 28273 USA /emdusaTel: 800-358-9070 / 704-588-3246 Fax: 707-584-8015BE Series: Made in the USAEM&D Sales OfficesAustraliaParker Hannifin (Australia) Pty Ltd.9 Carrington Road Castle Hill NSW 2154AustraliaTel: +61 (0) 2 9842 5150 Fax: +61 (0) 2 9842 5111BrazilParker Hannifin Ind. Com Ltda.Estrada Municipal Joel de Paula, 900São José dos Campos São Paulo Brazil 12247-015Tel: *****************************CanadaParker Canada Div.160 Chisholm DrMilton, Ontario L9T 3G9 Tel: 905-693-3000 Fax: 905-876-1958 ******************ChinaParker Hannifin Motion & Control (Shanghai) Co., Ltd280 Yunqiao Rd. Jin Qiao Export Processing ZoneShanghai 201206, China Tel: +86-21-28995000Fax: +86-21-2158348975***************************FranceParker Hannifin France SAS 142, rue de la Forêt74130 Contamine-sur-Arve Tel +33 (0)4 50 25 80 25Fax +33 (0)4 50 25 24 25************************GermanyElectromechanical EuropeParker Hannifin GmbH & Co KG Robert-Bosch-Strasse 22 D-77656 Offenburg GermanyTel: +49 (0) 781 509 0Fax: +49 (0) 781 509 98176********************IndiaParker Hannifin India Pvt. LtdAutomation Group-SSD Drives Div.133 & 151 Developed Plots Estate Perungudi, Chennai 600 096Tel: 044-4391-0799Fax: 044-4391-0700ItalyParker Hannifin SpA Via Gounod 120092 Cinsello Balsamo Milano, ItalyTel: +39 02 361081Fax: +39 02 36108400********************KoreaParker Hannifin Korea9th Floor KAMCO Yangjae Tower 949-3 Dogok 1-dong Gangnam-gu Seoul 135-860, Korea Tel: 82-2-559-0454Fax: 82-2-556-8187*******************MexicoParker Hannifin de Mexico Eje uno Norte No.100Parque Industrial Toluca 2000 Toluca, CP 50100 México Tel: 52-722-275-4200Fax: 52-722-279-0316*******************SingaporeParker Hannifin Singapore Pte Ltd 11, Fourth Chin Bee Road Singapore 619702Tel: (65) 6887 6300Fax: (65) 6265 5125TaiwanParker Hannifin Taiwan Co., Ltd 8F No 22 Wuquan 7th Road Wuku DistrictNew Taipei City 24890 Taiwan Tel: 886 2 2298 8987Fax: 886 2 2298 8982*************************ThailandParker Hannifin (Thailand) Co., Ltd.1265 Rama 9 RoadSuanluang, Bangkok 10250 ThailandTel: (66) 2 186 7000Fax: (66) 2 374 1645*********************UKParker Sales Co. UK Tachbrook Park Drive Tachbrook Park Warwick CV34 6TUTel: +44 (0)1926 317 878********************USAParker Hannifin EM&D (Main Office and Drives Business Unit)9225 Forsyth Park Drive Charlotte NC 28273 USA Tel: (704) 588-3246 800-358-9070Fax: (704) 588-3249**********************Parker Hannifin EM&D (Intelligent Motion Business Unit)1140 Sandy Hill Road Irwin, PA 15642 USA Tel: (724) 861-8200 800-245-6903Fax: (724) 861-3330Parker Hannifin EM&D (Gearhead & Motor Business Unit)2101 North BroadwayNew Ulm, Minnesota 56073 USA Tel: (507) 354-1616 800-358-9070Fax: (507) 233-2390Parker Hannifin EM&D (Intelligent Motion Business Unit)5500 Business Park Drive Rohnert Park, CA 94928 USA Tel: (707) 584-7558 800-358-9070Fax: (707) 584-8015Parker Hannifin EM&D (IPS)135 Quadral DriveWadsworth, OH 44281 USA Tel: (330) 334-3335 800-358-9070Fax: (330) 334-2350。
Parker 产品说明书
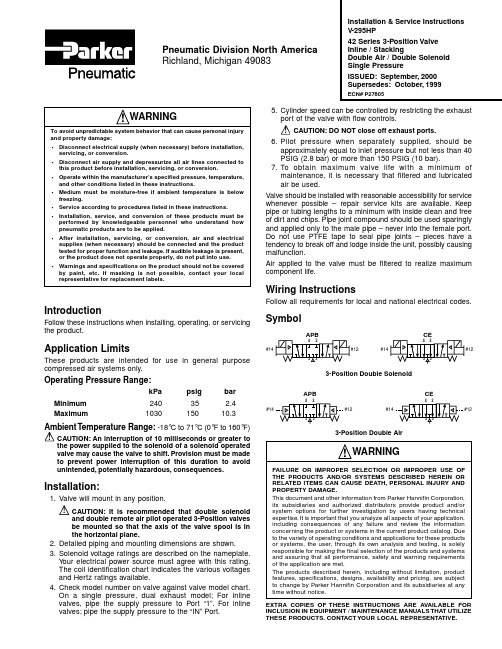
IntroductionFollow these instructions when installing, operating, or servicing the product.Application LimitsThese products are intended for use in general purpose compressed air systems only.Operating Pressure Range:kPapsig bar Minimum 24035 2.4Maximum103015010.3Ambient Temperature Range: -18°C to 71°C (0°F to 160°F)!CAUTION: An interruption of 10 milliseconds or greater tothe power supplied to the solenoid of a solenoid operated valve may cause the valve to shift. Provision must be made to prevent power interruption of this duration to avoid unintended, potentially hazardous, consequences.Installation:1.Valve will mount in any position.!CAUTION: It is recommended that double solenoidand double remote air pilot operated 3-Position valves be mounted so that the axis of the valve spool is in the horizontal plane.2.Detailed piping and mounting dimensions are shown.3.Solenoid voltage ratings are described on the nameplate.Y our electrical power source must agree with this rating.The coil identification chart indicates the various voltages and Hertz ratings available.4.Check model number on valve against valve model chart.On a single pressure, dual exhaust model; For inline valves, pipe the supply pressure to Port “1”. For inline valves; pipe the supply pressure to the “IN ” Port.5.Cylinder speed can be controlled by restricting the exhaust port of the valve with flow controls.!CAUTION: DO NOT close off exhaust ports.6.Pilot pressure when separately supplied, should be approximately equal to inlet pressure but not less than 40PSIG (2.8 bar) or more than 150 PSIG (10 bar).7.To obtain maximum valve life with a minimum of maintenance, it is necessary that filtered and lubricated air be used.Valve should be installed with reasonable accessibility for service whenever possible – repair service kits are available. Keep pipe or tubing lengths to a minimum with inside clean and free of dirt and chips. Pipe joint compound should be used sparingly and applied only to the male pipe – never into the female port.Do not use PTFE tape to seal pipe joints – pieces have a tendency to break off and lodge inside the unit, possibly causing malfunction.Air applied to the valve must be filtered to realize maximum component life.Wiring InstructionsFollow all requirements for local and national electrical codes.SymbolAPBCE#143-Position Double SolenoidCE#14APB3-Position Double AirInstallation & Service Instructions V -295HP42 Series 3-Position Valve Inline / StackingDouble Air / Double Solenoid Single PressureISSUED: September, 2000Supersedes: October, 1999ECN# P27805Pneumatic Division North America Richland, Michigan 49083!!WARNINGTo avoid unpredictable system behavior that can cause personal injury and property damage:•Disconnect electrical supply (when necessary) before installation,servicing, or conversion.•Disconnect air supply and depressurize all air lines connected to this product before installation, servicing, or conversion.•Operate within the manufacturer’s specified pressure, temperature,and other conditions listed in these instructions.•Medium must be moisture-free if ambient temperature is below freezing.•Service according to procedures listed in these instructions.•Installation, service, and conversion of these products must be performed by knowledgeable personnel who understand how pneumatic products are to be applied.•After installation, servicing, or conversion, air and electrical supplies (when necessary) should be connected and the product tested for proper function and leakage. If audible leakage is present,or the product does not operate properly, do not put into use.•Warnings and specifications on the product should not be covered by paint, etc. If masking is not possible, contact your local representative for replacement labels.WARNINGFAILURE OR IMPROPER SELECTION OR IMPROPER USE OF THE PRODUCTS AND/OR SYSTEMS DESCRIBED HEREIN OR RELATED ITEMS CAN CAUSE DEATH, PERSONAL INJURY AND PROPERTY DAMAGE.This document and other information from Parker Hannifin Corporation,its subsidiaries and authorized distributors provide product and/or system options for further investigation by users having technical expertise. It is important that you analyze all aspects of your application,including consequences of any failure and review the information concerning the product or systems in the current product catalog. Due to the variety of operating conditions and applications for these products or systems, the user, through its own analysis and testing, is solely responsible for making the final selection of the products and systems and assuring that all performance, safety and warning requirements of the application are met.The products described herein, including without limitation, product features, specifications, designs, availability and pricing, are subject to change by Parker Hannifin Corporation and its subsidiaries at any time without notice.EXTRA COPIES OF THESE INSTRUCTIONS ARE AVAILABLE FOR INCLUSION IN EQUIPMENT / MAINTENANCE MANUALS THA T UTILIZE THESE PRODUCTS. CONTACT YOUR LOCAL REPRESENTATIVE.42 Series 3-Position Valve V-295HPMaintenance Hints & TroubleshootingValve Not Shifting Completely:1.Be sure supply pressure is 40 PSIG or greater at the valveduring the shift.2.Check for possible restrictions in air supply, such as sharpbends and undersize hose fittings.3.Check for possible pilot exhaust restriction.4.Check spool for smooth movement.5.Check seals and gaskets for improper installation, dirt anddamage.Slow Air Leakage Though Exhaust Ports:1.Check for internal leakage in the cylinder being operatedby the valve.2.Check condition of seals on spool and the valve body bore.3.Check condition of seal on poppet assembly and their matingsurfaces in the pilot body.4.Check for missing, damaged or incorrectly assembled sealsand O-rings.Noisy Solenoid:1.Check voltage and frequency.2.Inspect fixed pole assembly for nicked and damaged matingsurfaces and dirt. Replace parts, if damaged.3.Check override access area for excessive dirt.Valve Service Procedures:!CAUTION: Always shut off air supply and bleed off trapped pressure in the valve. For solenoid operated valves, turn off electrical power source.PREP ARATION: Lightly lubricate all rubber soft goods (o-rings, gaskets, and spool seals) found in the service kits. Use non-detergent hydrocarbon base oil, or grease (preferably grease). This lubrication will help retain seals and gaskets in position for easier reassembly.!CAUTION: DO NOT use synthetic oils such as esters or fire retardant type compressor oils.Servicing Valve BodyT o Disassemble:1.For “Stacking” solenoid operated valves: Follow steps 1and 2 under servicing solenoid section and pilot body.2.For “Inline” solenoid operated valves: Follow step 2 underservicing solenoid section and pilot body.3.Air pilot valve: Remove both air pilot operators (Item 19)from valve body by loosening the two end mounting screws (Item 21).4.Remove the piston (Item 28) from each end of valve bodybore.5.T o disassemble the main valve, loosen the two spool screws,and remove all internal parts.!CAUTION: Slowly loosen the two spool screws to avoida rapid release of the spool screw, shoulder sleeve,and spring retainer, due to the compression ofcentering springs.6.The spring retainer and shoulder sleeve at the oppositeend of the spools must also be removed.7.Thoroughly clean the valve interior and inspect for nicks,voids, pits, and deep scratches.T o Reassemble:1.Place shoulder sleeve (Item 25) inside spring retainer(Item 26). Insert spool screw (Item 24) and attach to the spool (Item 23) with engagement of two (2) full threads. 2.Slide one (1) centering spring (Item 27) over the spool andinstall into the valve body bore.3.On the opposite end of the valve, install the remainingcentering spring, shoulder sleeve, spring retainer and spool screw.NOTE: Tighten spool screws to 5.1 to 6.8 Nm (45 to 60 in. lbs.).4.Replace piston O-rings (Item 29) and install into each endof valve body bore with the flat surface outward.5.Solenoid operated valve: Insert mounting screws (Item 7A)into pilot body. This will assist you in positioning the pilot body to adaptor body gasket (Item 16), the adaptor plate (Item 17), to body gasket (Item 18) for easier mounting to the valve body. (For stacking valves, thread the solenoid lead wires through the spacer and into the junction box) NOTE:All four (4) parts must have correct alignment in relationship with the pilot hole in valve body.6.Attach the pilot body and solenoid assembly to valve bodyand tighten mounting screws from 3.4 to 4.5 Nm (30 to 40 in. lbs.). (For stacking valves, reconnect solenoid coil lead wires, attach junction box top plate assembly (Item 36) and tighten the mounting screws 3.4 to 4.5 Nm (30 to 40 in.lbs.).7.Air pilot valve: Attach air pilot operators (Item 19) to thevalve body with mounting screws (Item 21) and tighten 3.4 to 4.5 Nm (30 to 40 in. lbs.).8.T urn on air supply (for solenoid valves; turn on electricalpower source) check valve for proper function and for internal and external air leakage.Servicing Solenoid Section:1.For stacking valves: Remove junction box top plate assembly(Item 36) by loosening the two mounting screws, and disconnect the lead wires in the junction box.NOTE: DO NOT disconnect lead wires by cutting.2.Remove pilot body and solenoid as an assembly byloosening the two end mounting screws (Item 7A).3.Remove solenoid coil by loosening the two top mountingscrews (Item 7) and lifting solenoid from pilot body. Remove guide sleeve (Item 2), plunger assembly (Item 3), override seal (Item 4), solenoid coil to pilot body seal (Item 6), and mounting screws (Item 7A).4.Remove fixed pole assembly (Item 15), by turning counter-clockwise until threads are fully disengaged, and plunger pin (Item 14).5.Replace plunger pin (Item 14), and reassemble fixed poleassembly (Item 15) to pilot body by turning clockwise and tighten 3.4 to 4.5 Nm (30 to 40 in. lbs.).!CAUTION: DO NOT exceed torque specifications. This could cause severe damage to the pilot body poppetseating ledge, and result in valve malfunction.6.Replace solenoid to pilot body seal (Item 6), guide sleeve(Item 2) by resting on fixed pole assembly, and plunger assembly (Item 3) by setting inside guide sleeve.7.Mount solenoid coil over guide sleeve. Replace overrideseal (Item 4), attach solenoid top plate (Item 5) with the top mounting screws (Item 7) and tighten to 3.4 to 4.5 Nm (30 to 40 in. lbs.).8.Insert end mounting screws (Item 7A) into pilot body. Positionpilot body to adaptor gasket (Item 16), the adaptor plate (Item 17), to valve body gasket (Item 18). For stacking valves, thread the solenoid coil lead wires through the sleeve and into the junction box.NOTE:All four (4) parts must have correct alignment in relationship with the pilot hole in valve body9.Attach the pilot body and solenoid assembly to the valvebody and tighten the end mounting screws to 3.4 to 4.5 Nm (30 to 40 in. lbs.). For stacking valves, reconnect solenoid coil lead wires, attach junction box top plate assembly (Item 36), and tighten the mounting screws to3.4 to4.5 Nm (30 to 40 in. lbs.).Servicing Pilot Body1.For stacking valves: Follow steps 1, 2 and 3 under servicing solenoid section.2.For inline valves follow steps 2 and 3 under servicing solenoid section.3.Remove fixed pole assembly (Item 15) by turning counter-clockwise until threads are fully disengaged. Remove plunger pin (Item 14), bore insert (Item 12), poppet assembly (Item 11), and poppet return spring (Item 10).4.Thoroughly clean the pilot body interior and inspect for nicks, voids, pits, and deep scratches.5.Install poppet return spring (Item 10). Assemble bore insert seals (Item 13) to bore insert (Item 12). Assemble poppet assembly (Item 15) into bore insert. Position poppet assembly with seal at top as shown below. Failure to do so can cause plunger to be propelled from unit when air is applied. Install with poppet assembly, seating against the poppet return spring.6.Install plunger pin (Item 14) and reassemble fixed pole assembly (Item 15) to pilot body by turning clockwise and tighten 3.4 to 4.5 Nm (30 to 40 in. lbs.).!CAUTION: DO NOT exceed torque specifications. Thiscould cause severe damage to the pilot body poppet seating ledge, and result in valve malfunction.7.Before attaching solenoid coil, suggest inspecting the guide sleeve (Item 2) for excessive wear, and the plunger assembly (Item 3) for battered and flared metal conditions.If items appear in this described condition, they should be replaced.42 Series 3-Position ValveV-29HP8.If conditions are not noted, place guide sleeve over fixed pole assembly, and plunger assembly inside guide sleeve. Mount solenoid coil over guide sleeve and tighten to pilot body tightening screws 3.4 to 4.5 Nm (30to 40 in. lbs.).9.Insert end mounting screws (Item 7A) into pilot body.Position pilot body to adaptor plate gasket (Item 16), the adaptor plate (Item 17), to body gasket (Item 18) for easier mounting to valve body . For stacking valves, thread the solenoid coil lead wires through the spacer (Item 38) and into the junction box.NOTE:All four (4) parts must have correct alignment inrelationship with the pilot hole in valve body.10.Attach pilot body and solenoid assembly to valve bodyand tighten the end mounting screws 3.4 to 4.5 Nm (30 to 40 in. lbs.). For stacking valves, reconnect solenoid coil lead wires and attach junction box top plate assembly (Item 36). Tighten the mounting screws 3.4 to 4.5 Nm (30to 40 in. lbs.).3-Position Stacking 3-Position InlineValve Body Service Kits,Consisting of Items -PS2009P7A, 16, 18, 21, 23, 24, 27, 29Solenoid Service Kit(Two Kits Required For Double Solenoid),Consisting of Items -PS2013BP2, 3, 4, 6, 7, 14, 15Pilot Body Service Kit(Two Kits Required For Double Solenoid),Consisting of Items -PS2015BP7A, 10, 11, 11A, 12, 13, 16, 18Service Kits:Voltage/Frequency Standard Lead Wire Type -Standard Lead Wire Type -* ISO 4400 3-Pin Connector60Hz. AC 50Hz. AC DC InlineStackingType24V22VL0051442CP L0071812CP L0058172CP 12V L0051445CP L0071815CP L0058175CP 24VL0051449CP L0071819CP L0058179CP 120V 110V L0051453CP L0071823CP L0058183CP 240V220VL0051457CP L0071827CP L0058187CP 120VL0051460CPL0071830CPL0058190CP* NOTE:Female connector, gasket and M3 mounting screw for ISO 4400 3-Pin Connector T ype Solenoid must be orderedseparately (PS2028BP). For Indicator Light order POO74023.Coil Selection:42 Series 3-Position Valve V-295HP。