触摸屏工艺流程介绍
触摸屏工艺流程范文
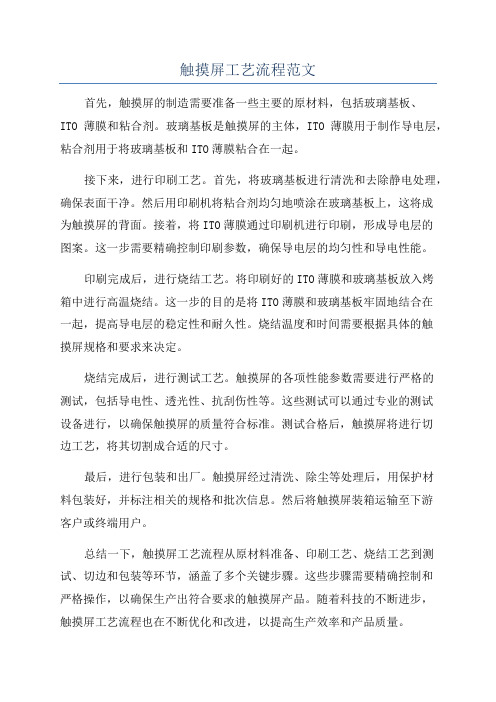
触摸屏工艺流程范文首先,触摸屏的制造需要准备一些主要的原材料,包括玻璃基板、ITO薄膜和粘合剂。
玻璃基板是触摸屏的主体,ITO薄膜用于制作导电层,粘合剂用于将玻璃基板和ITO薄膜粘合在一起。
接下来,进行印刷工艺。
首先,将玻璃基板进行清洗和去除静电处理,确保表面干净。
然后用印刷机将粘合剂均匀地喷涂在玻璃基板上,这将成为触摸屏的背面。
接着,将ITO薄膜通过印刷机进行印刷,形成导电层的图案。
这一步需要精确控制印刷参数,确保导电层的均匀性和导电性能。
印刷完成后,进行烧结工艺。
将印刷好的ITO薄膜和玻璃基板放入烤箱中进行高温烧结。
这一步的目的是将ITO薄膜和玻璃基板牢固地结合在一起,提高导电层的稳定性和耐久性。
烧结温度和时间需要根据具体的触摸屏规格和要求来决定。
烧结完成后,进行测试工艺。
触摸屏的各项性能参数需要进行严格的测试,包括导电性、透光性、抗刮伤性等。
这些测试可以通过专业的测试设备进行,以确保触摸屏的质量符合标准。
测试合格后,触摸屏将进行切边工艺,将其切割成合适的尺寸。
最后,进行包装和出厂。
触摸屏经过清洗、除尘等处理后,用保护材料包装好,并标注相关的规格和批次信息。
然后将触摸屏装箱运输至下游客户或终端用户。
总结一下,触摸屏工艺流程从原材料准备、印刷工艺、烧结工艺到测试、切边和包装等环节,涵盖了多个关键步骤。
这些步骤需要精确控制和严格操作,以确保生产出符合要求的触摸屏产品。
随着科技的不断进步,触摸屏工艺流程也在不断优化和改进,以提高生产效率和产品质量。
触摸屏 工艺流程
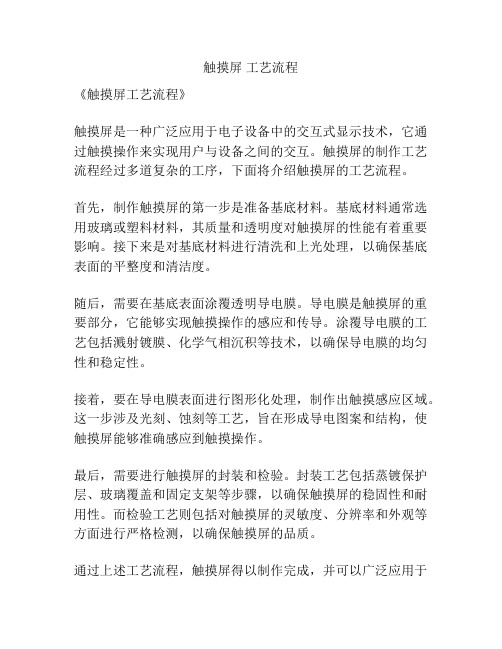
触摸屏工艺流程
《触摸屏工艺流程》
触摸屏是一种广泛应用于电子设备中的交互式显示技术,它通过触摸操作来实现用户与设备之间的交互。
触摸屏的制作工艺流程经过多道复杂的工序,下面将介绍触摸屏的工艺流程。
首先,制作触摸屏的第一步是准备基底材料。
基底材料通常选用玻璃或塑料材料,其质量和透明度对触摸屏的性能有着重要影响。
接下来是对基底材料进行清洗和上光处理,以确保基底表面的平整度和清洁度。
随后,需要在基底表面涂覆透明导电膜。
导电膜是触摸屏的重要部分,它能够实现触摸操作的感应和传导。
涂覆导电膜的工艺包括溅射镀膜、化学气相沉积等技术,以确保导电膜的均匀性和稳定性。
接着,要在导电膜表面进行图形化处理,制作出触摸感应区域。
这一步涉及光刻、蚀刻等工艺,旨在形成导电图案和结构,使触摸屏能够准确感应到触摸操作。
最后,需要进行触摸屏的封装和检验。
封装工艺包括蒸镀保护层、玻璃覆盖和固定支架等步骤,以确保触摸屏的稳固性和耐用性。
而检验工艺则包括对触摸屏的灵敏度、分辨率和外观等方面进行严格检测,以确保触摸屏的品质。
通过上述工艺流程,触摸屏得以制作完成,并可以广泛应用于
智能手机、平板电脑、电视等各种电子设备中。
触摸屏工艺的不断发展和创新,也将为电子设备的交互体验带来更多可能性和便利性。
触摸屏工艺流程介绍

IC本压 外观检查
目的: 用自动设备把粘贴好的IC进行在次加压紧固,使IC不能有脱落的现象 目的: 用肉眼检查产品外型是否按标准制造(不允许有规格规定外的不良发生)
显微镜检查
目的: ACF导电粒子的确认,是否在规格数量内,(在确认A/M是否在基准内)
FOG ACF 粘贴
目的: 用固定的ACF粘贴机把ACF粘在PANEL PAD部规定的部位(COG导电球5EA以上,
目标达成
11/42
FPC 压贴
ATT 检查 外观 检查 M/T 检查
SI (硅胶)涂布
U/V 硬化 外观 检查
输出
目的: FPC 输出端子同PANEL PAD部的输出端子进行相对端子重合紧密连在一起 目的: 对前工程压贴后的部位进行品质确认,是否有无异常发生(主要是ACF导电球是否正常) 目的: 用肉眼检查产品外型是否按标准制造(不允许有规格规定外的不良发生) 目的: 对FPC压贴后的LCD进行画质有无异常检查 目的: 把硅胶(液体状态)涂布在IC四周的表面 (保护IC受到外部撞、压及受潮)
目的: 为下一工程做生产准备,准备好原材料等待生产 目的: 对PANEL 的 PAD部位进行异物及杂质彻底清扫
目标达成
10/42
COG ACF压贴
IC粘贴/假压 IC 本压
显微镜检查
目的: 用自动设备把ACF自动粘贴在PANEL PAD部规定部位相紧密结合
目的: 用自动加压设备把IC粘贴在所规定的部位,然后在轻轻的压一下 (使其不能有掉落现象) 目的: 用自动设备把粘贴好的IC进行在次加压紧固,使IC不能有脱落的现象
上POL’附贴
目的: 本工程是按规格把偏光片(POL’)附贴在 PANEL CF玻璃表面上
触摸屏tp的工艺流程

触摸屏tp的工艺流程
触摸屏(Touch Panel,简称TP)的制造工艺流程通常包括以下步骤:基板准备:选择基板材料,如玻璃、塑料等,进行切割、打磨和清洗,确保表面平整干净。
ITO膜涂布:在基板表面涂覆一层导电性的氧化铟锡(ITO)薄膜,用于实现触摸操作的导电功能。
光刻:通过光刻技术,将ITO膜上的电极图案进行曝光、显影,形成电极线路。
蒸发金属:在ITO膜上蒸发一层金属薄膜,用于提高导电性能和耐磨性。
局部蚀刻:利用化学蚀刻技术,去除金属薄膜的多余部分,保留需要的电极图案。
绝缘层涂覆:在导电层上涂覆一层绝缘材料,用于隔离导电线路,防止短路。
ITO感应层涂布:在绝缘层上再次涂覆一层ITO薄膜,形成触摸面板的感应层。
光刻感应区域:通过光刻技术,将ITO感应层上的感应图案进行曝光、显影,形成触摸区域。
装配:将触摸面板与显示屏或其他设备组合装配,确保连接和固定。
测试:对组装好的触摸屏进行功能测试,包括触摸灵敏度、准确性等性能测试。
包装:对测试合格的触摸屏进行包装,包括防静电包装、外包装等,最终出厂销售。
这些步骤构成了触摸屏制造的主要工艺流程,每个步骤都需要精密的设备和技术来确保产品质量。
不同类型的触摸屏可能会有一些额外的工艺步骤或特殊处理,但总体流程大致如上所述。
触摸屏工艺流程
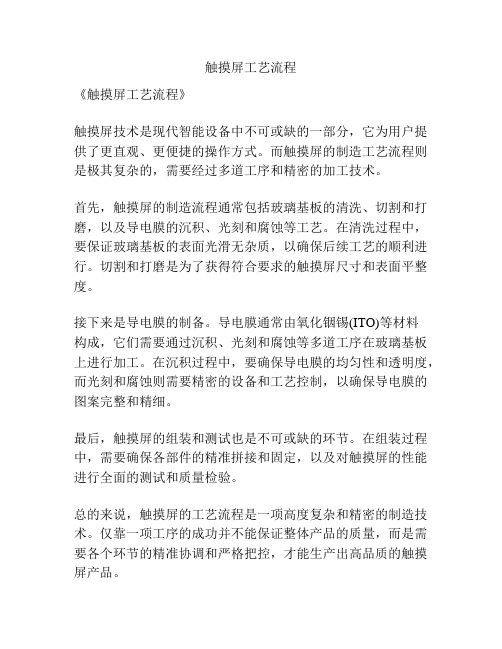
触摸屏工艺流程
《触摸屏工艺流程》
触摸屏技术是现代智能设备中不可或缺的一部分,它为用户提供了更直观、更便捷的操作方式。
而触摸屏的制造工艺流程则是极其复杂的,需要经过多道工序和精密的加工技术。
首先,触摸屏的制造流程通常包括玻璃基板的清洗、切割和打磨,以及导电膜的沉积、光刻和腐蚀等工艺。
在清洗过程中,要保证玻璃基板的表面光滑无杂质,以确保后续工艺的顺利进行。
切割和打磨是为了获得符合要求的触摸屏尺寸和表面平整度。
接下来是导电膜的制备。
导电膜通常由氧化铟锡(ITO)等材料
构成,它们需要通过沉积、光刻和腐蚀等多道工序在玻璃基板上进行加工。
在沉积过程中,要确保导电膜的均匀性和透明度,而光刻和腐蚀则需要精密的设备和工艺控制,以确保导电膜的图案完整和精细。
最后,触摸屏的组装和测试也是不可或缺的环节。
在组装过程中,需要确保各部件的精准拼接和固定,以及对触摸屏的性能进行全面的测试和质量检验。
总的来说,触摸屏的工艺流程是一项高度复杂和精密的制造技术。
仅靠一项工序的成功并不能保证整体产品的质量,而是需要各个环节的精准协调和严格把控,才能生产出高品质的触摸屏产品。
触摸屏生产工艺

触摸屏生产工艺
触摸屏生产工艺是指生产触摸屏的整个工艺流程,包括材料准备、工艺加工、装配和测试等环节。
首先,触摸屏的生产过程从材料准备开始。
主要材料有ITO
薄膜、玻璃基板、导电胶、导电纤维等。
材料准备需要精确计算每个材料的尺寸和数量,并进行齐全的采购。
接着,进行工艺加工。
首先是ITO薄膜的制备,通过光刻、
附着、曝光、蚀刻等步骤,将ITO薄膜制作成预定形状和大小。
然后是玻璃基板的处理,包括清洗、切割和抛光等步骤,以确保基板的质量和平整度。
接下来是导电胶和导电纤维的加工,通过喷涂或印刷等方式,将导电胶和导电纤维均匀地涂布在ITO薄膜上。
然后,进行装配工艺。
将ITO薄膜贴附在玻璃基板上,形成
触摸屏的结构。
这一步需要精确控制温度和压力,以确保ITO 薄膜和玻璃基板的结合度。
同时,还需要进行高精度的定位和对齐,以确保触摸屏的灵敏度和精确度。
最后,进行测试工艺。
对已装配的触摸屏进行功能、性能和质量的测试,确保产品符合相关标准和要求。
测试主要包括电气特性测试、触摸精度和触摸感应测试等。
只有通过严格的测试,才能保证产品的品质和稳定性。
总的来说,触摸屏生产工艺包括材料准备、工艺加工、装配和测试等环节。
每个环节都需要精确的操作和严格的控制,以确
保产品的质量和性能。
随着科技的不断发展,触摸屏的生产工艺也在不断创新和改进,以满足不断增长的市场需求。
生产手机触摸屏的工作流程

生产手机触摸屏的工作流程第一步,原材料准备生产手机触摸屏的第一步是原材料的准备。
触摸屏的主要材料是玻璃和导电膜,玻璃通常是用特制的玻璃原料,经过特殊的处理,使其具有一定的硬度和透明度,而导电膜则是一层薄膜,具有导电性能。
这些原材料都需要经过严格的筛选和检测,确保其质量符合生产要求。
第二步,玻璃加工在玻璃加工环节,首先是将玻璃原料进行切割和打磨,将原材料切割成手机触摸屏的大小,并进行表面的抛光处理,以保证触摸屏的平整度和透明度。
接下来是对玻璃进行化学处理,使其具有一定的硬度和抗刮性能。
这一步是非常关键的,因为触摸屏的硬度和抗刮性能直接关系到手机的使用寿命和外观。
第三步,导电膜涂覆导电膜是触摸屏的重要组成部分,它可以使触摸屏实现电容触控功能。
在导电膜涂覆环节,首先需要将导电膜涂覆在玻璃表面上,然后进行干燥和固化处理,使导电膜与玻璃表面紧密结合,并具有良好的导电性能。
导电膜的涂覆和固化工艺是非常复杂的,需要严格控制涂料的涂布厚度和固化时间,以确保触摸屏的灵敏度和稳定性。
第四步,图案印刷在图案印刷环节,需要将触摸屏上的图案和标识印刷在玻璃表面上,通常采用丝网印刷或喷墨印刷技术。
印刷的图案和标识需要具有一定的耐磨性和耐腐蚀性,以保证触摸屏的外观和使用寿命。
第五步,热压处理在热压处理环节,需要将导电膜和玻璃进行热压处理,使其形成一体化的结构。
热压处理可以提高导电膜与玻璃的结合强度,并保证触摸屏的稳定性和耐久性。
同时,热压处理也可以消除导电膜和玻璃之间的气泡,使触摸屏的表面更加平整和透明。
第六步,检验和包装在检验环节,需要对生产好的触摸屏进行严格的检查和测试,包括外观检查、功能测试和耐久性测试等。
只有经过严格的检验合格后,触摸屏才能进入包装环节。
在包装环节,需要将触摸屏进行包装,并贴上防静电标识,以确保其在运输和使用过程中不受静电影响。
以上就是生产手机触摸屏的主要工作流程,整个生产过程需要经过多道工序和严格的检验,以确保触摸屏的质量和稳定性。
触摸屏生产工艺流程

触摸屏生产工艺流程触摸屏是目前电子产品中最常见的输入设备之一,它广泛应用于智能手机、平板电脑、笔记本电脑和其他电子设备上。
触摸屏的生产工艺流程包括以下几个主要步骤。
首先,触摸屏的生产需要准备基板。
通常使用玻璃或透明塑料作为基板材料。
基板必须通过机械或化学方式进行打磨和清洗,以确保表面的平整度和清洁度。
接下来,需要创建导电层。
导电层是触摸屏的核心部分,它可以感应到用户的触摸动作。
常用的导电层材料有导电银胶或导电膜。
导电层可以通过丝网印刷技术或蒸发沉积技术在基板上进行涂覆和制备。
然后,在导电层上需要制作透明导电电极。
透明导电电极通常使用氧化铟锡(ITO)材料,该材料具有良好的光透过性和导电性能。
透明导电电极可以通过蒸发沉积或丝网印刷技术制备。
接着,需要进行检测和修复。
在导电层和透明导电电极制备完成后,需要对其进行光学和电学性能测试,以确保其质量和性能符合要求。
如果发现问题,需要进行修复或更换。
下一步,是制作触摸层。
触摸层的作用是感应用户的触摸动作并将其转化为电信号。
常见的触摸层材料有电容式触摸屏和电阻式触摸屏。
电容式触摸屏使用一层或多层导电膜来感应触摸,而电阻式触摸屏则使用两层导电玻璃之间的电阻感应触摸。
最后,进行组装和封装。
在触摸屏的生产中,需要将各个层次的材料按照设计要求进行组装,并使用粘合剂或胶水对其进行固定。
随后,触摸屏还需要进行表面处理,如抛光和涂层,以提高触摸屏的耐磨性和防刮性。
综上所述,触摸屏的生产工艺包括基板准备、导电层制备、透明导电电极制作、检测和修复、触摸层制作和组装封装等主要步骤。
每个步骤都是相互关联的,需要精确的操作和控制,才能生产出高质量的触摸屏产品。
不断改进触摸屏生产工艺,提高生产效率和降低成本,对于满足不断增长的市场需求至关重要。
触摸屏工艺流程图

触摸屏工艺流程图触摸屏工艺流程图是指在制造触摸屏产品时所需要的一系列工艺流程。
触摸屏是一种通过触摸屏幕表面与用户的触摸来实现与设备的交互的技术。
触摸屏工艺流程图描述了从材料准备到成品测试的全部流程。
本文将简单介绍触摸屏工艺流程图的主要环节。
第一步:材料准备触摸屏工艺流程的第一步是准备所需材料。
主要包括ITO玻璃、ITO膜、导电胶、保护膜等。
这些材料是制造触摸屏不可缺少的基础材料。
第二步:ITO膜镀膜在这一步骤中,将ITO膜通过物理镀膜或化学溶胶-凝胶法涂覆在ITO玻璃上。
ITO膜是触摸屏不可或缺的一部分,具有导电功能,可以实现与用户的触摸交互。
第三步:切割和打孔在这一步骤中,通过切割和打孔将镀覆有ITO膜的ITO玻璃切割和打孔成为所需的触摸屏形状和规格。
打孔是为了提供触摸屏的按键功能,使用户能够通过触摸屏进行操作。
第四步:导电胶注胶在这一步中,将导电胶注入到切割和打孔后的ITO玻璃上,以实现电导功能。
导电胶是触摸屏内部的重要组成部分,它通过导电将用户触摸的信号传送给设备。
第五步:层叠结构在这一步中,将ITO玻璃与其他层叠材料进行组合并粘合在一起,形成触摸屏的层叠结构。
层叠结构的设计是为了实现触摸屏的灵敏度和稳定性。
第六步:贴膜在这一步中,将保护膜贴在层叠结构的表面,以保护触摸屏表面免受划伤和污染。
保护膜还可以提高触摸屏的外观和耐用性。
第七步:热压在这一步骤中,对触摸屏进行热压,以确保层叠结构的各层材料紧密粘合,形成坚固的触摸屏结构。
第八步:测试在这一步中,对制成的触摸屏产品进行各种测试,以确保其功能正常并达到设计要求。
主要的测试项目包括触摸灵敏度、精度、耐用性等。
第九步:完成在经过测试合格后,触摸屏产品将进行包装,准备出厂。
然后可以被应用于各种电子设备,如智能手机、平板电脑等。
以上是触摸屏工艺流程图的主要环节。
在实际制造中,还会有更多的细节和工艺步骤,以满足不同产品的需求和要求。
触摸屏工艺流程图对于指导制造过程和确保产品质量至关重要,它是触摸屏行业的重要组成部分。
触摸屏生产工艺流程

触摸屏生产工艺流程
《触摸屏生产工艺流程》
触摸屏是现代电子设备中不可或缺的一部分,其生产工艺流程经过多道工序,需要精密的设备和技术。
下面是触摸屏生产工艺流程的简要介绍:
1.基板加工:首先,选择适当的基板材料,如玻璃、塑料等,然后进行切割、打磨、清洗等工序,使其得到符合要求的形状和平整度。
2.导电膜涂布:在基板上涂布导电膜,通常使用的是导电性能优异的氧化铟锡膜(ITO膜),该膜能够在表面形成均匀的导电层。
3.光刻:通过光刻技术,在导电膜上形成图案,以便以后制作电路和导线。
4.蒸镀:使用真空蒸镀技术,在基板上蒸镀一层金属膜,以提高导电膜的电导率和耐腐蚀性。
5.玻璃粘合:将制作好的导电膜基板与玻璃基板进行粘合,通常使用光敏胶或者UV固化胶进行粘合。
6.成型和热压:将粘合好的基板进行成型和热压,使其结构更加牢固和平整。
7.测试与调试:对制作好的触摸屏进行测试和调试,以确保其
质量和性能符合要求。
8.包装:最后,对通过测试的触摸屏进行包装,以便运输和销售。
触摸屏生产工艺流程中需要运用到许多先进的技术和设备,如光刻机、蒸镀机、热压机等,同时还需要高精度的工艺控制和质量检测手段,才能保证生产出高质量的触摸屏产品。
在未来,随着技术的不断进步,触摸屏生产工艺流程也将不断完善和提升,以满足越来越多的应用需求。
触摸屏生产工艺流程

触摸屏生产工艺流程触摸屏生产工艺流程是指通过一系列工艺操作,将原材料转化为成品触摸屏的过程。
下面是一个大致的触摸屏生产工艺流程:1. 材料准备:首先准备好触摸屏制作所需的原材料,主要包括ITO玻璃基板、ITO膜材料、导电胶等。
2. 玻璃基板清洗:将ITO玻璃基板进行清洗处理,以去除表面污垢和杂质,保证基板的质量。
3. ITO膜涂布:将透明的导电膜材料涂布在玻璃基板上,形成导电层。
此步骤需要通过特殊的涂布机和涂布工艺来实现。
4. UV固化:经过ITO膜涂布的玻璃基板进行UV固化处理,使导电膜材料充分固化,提高导电性能。
5. 制作电极:使用光刻工艺和腐蚀等方法,在ITO膜层上形成导电电极的图案。
6. 安装IC芯片:将触摸屏所需的芯片组装到基板上,这些芯片将负责接收和处理触摸操作的信号。
7. 封装:进行触摸屏的封装,将触控芯片等元器件固定在基板上,并采取相应措施保护其免受外部环境的影响。
8. 电路连接:将基板上的触控芯片与其他电子元器件连接起来,完成电路的连通。
9. 按键测试:对触摸屏进行按键测试,确保触摸功能正常。
10. 清洁处理:对触摸屏进行清洁处理,去除表面的尘埃和污渍。
11. 组装:将触摸屏和其他部件组装在一起,形成最终的触摸屏产品。
12. 过检测试:对成品触摸屏进行全面的过检测试,确保产品的质量和可靠性。
13. 包装:将通过测试的触摸屏进行包装,以保护产品的完整性,并方便运输和销售。
14. 成品入库:将包装好的触摸屏成品入库,以备发货或销售。
触摸屏生产工艺需要经过多个环节的操作,每个环节都需要严格控制和管理,以保证触摸屏产品的质量和性能。
在实际生产中,通常会借助自动化设备和机器人技术,提高生产效率和产品一致性。
同时,还需要进行质量检测和监控,确保每一道工序都符合要求,从而保证最终生产出来的产品质量可靠。
电容触摸屏工艺流程

电容触摸屏工艺流程
一、电容触摸屏制造流程
1、衬底处理:衬底清洗→衬底干燥→衬底打磨→衬底洗涤。
2、开孔工艺:衬底对位→孔洞定位→孔洞切割→孔洞清洗。
3、ITO膜处理:ITO膜去除保护膜→ITO膜洗涤→ITO膜温热固化
→ITO膜清洗→ITO膜柔性熔接→ITO膜干燥。
4、衬底金手指处理:金手指铺展→金手指加热固化→金手指干燥→金手指定位→金手指回流焊接。
5、衬底元件封装:元件定位→元件焊接→元件焊锡→元件焊接→元件清洗。
6、衬底电容片处理:电容片定位→电容片焊接→电容片清洗→电容片焊接→电容片柔性熔接→电容片热压定型→电容片清洗→电容片抛光。
7、衬底电容片测试:电容片计算→电容片电路测试→电容片图像测试→电容片性能测试。
8、衬底成品检测:衬底外观检测→衬底触摸测试→衬底静电测试→衬底电容测试。
二、生产缺陷预防
1、避免衬底起皱:衬底在高温热处理时容易产生起皱,因此应采取积极措施,在适当位置使用合适的能量密度,对衬底进行多道温热处理来确保衬底的规则性,确保衬底成品的质量。
2、避免衬底斑点:衬底在安装过程中容易产生斑点,应采取一定的措施来避免这种情况的出现。
触摸屏 工艺流程

触摸屏工艺流程触摸屏是一种通过人体电容输入设备的平面式装置,广泛应用于智能手机、平板电脑、游戏机、汽车导航等电子产品中。
触摸屏的制造需要经历一系列的工艺流程。
首先,制造触摸屏的第一步是制备透明导电膜。
透明导电膜通常采用氧化铟锡(ITO)材料,通过化学气相沉积或物理汽相沉积的方法制备。
这一步骤非常重要,因为导电膜的质量直接影响触摸屏的灵敏度和可靠性。
接下来,将制备好的透明导电膜放置在玻璃基板上,通过蒸发或溅射等技术手段将膜层固定在基板上。
这个过程需要高精度的设备和控制,以确保导电膜均匀且具有良好的附着力。
随后,需要对导电膜进行光刻处理。
光刻是一种利用光敏感胶层制作微细图案的技术,通过照射光源并使用掩模遮光,在导电膜上形成触摸点或导线等结构。
光刻过程需要多次曝光、显影和蚀刻等步骤,以形成所需的图案。
完成光刻之后,需要进行触摸屏的装配。
在装配过程中,首先将制作好的触摸屏玻璃与液晶显示屏背板进行粘合,形成完整的触摸显示结构。
随后,通过紧固螺丝、焊接线路等方式,将触摸屏与其他电子部件进行连接,组成完整的触摸屏模组。
最后,还需要对触摸屏进行测试和调试。
通过专业的测试设备,对触摸屏的触摸灵敏度、多点触控能力、面板平整度等进行全面检测,确保产品质量符合标准。
此外,还要对触摸屏模组进行调试,确保触摸信号的稳定和准确。
以上就是触摸屏的工艺流程。
通过精细的制造工艺和严格的质量控制,触摸屏能够提供用户友好的触摸体验,成为现代电子产品中不可或缺的组成部分。
随着科技的发展和创新,触摸屏的工艺流程也在不断演进,以适应市场的需求和技术的进步。
触摸屏生产工艺及其流程
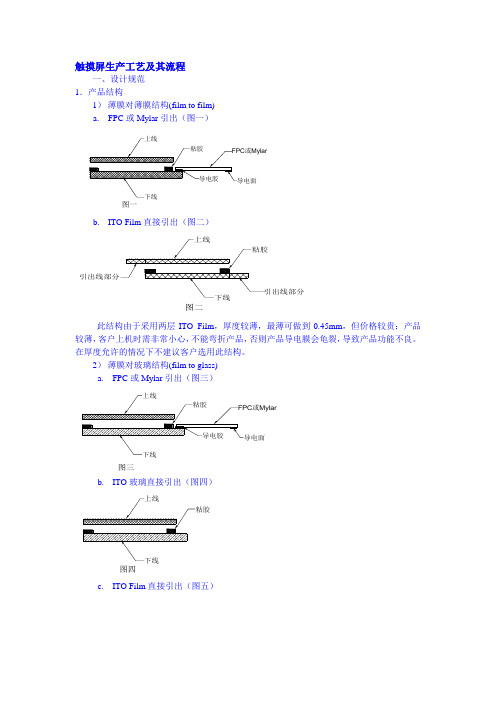
触摸屏生产工艺及其流程一、设计规范1.产品结构1)薄膜对薄膜结构(film to film)a.FPC或Mylar引出(图一)或Mylar图一b.ITO Film直接引出(图二)图二此结构由于采用两层ITO Film,厚度较薄,最薄可做到0.45mm,但价格较贵;产品较薄,客户上机时需非常小心,不能弯折产品,否则产品导电膜会龟裂,导致产品功能不良。
在厚度允许的情况下不建议客户选用此结构。
2)薄膜对玻璃结构(film to glass)a.FPC或Mylar引出(图三)或Mylar图三b.ITO玻璃直接引出(图四)c.ITO Film直接引出(图五)图五此结构成本低,工艺成熟,透明度高,引出线可随意选择,厚度可调整。
b、c两类型采用点胶形式比压合形式好,因上线材料较厚,采用压合时效果不太好;而压头大小也要合适,如果比实际压合面积大会压坏材料。
3)薄膜对薄膜含承托板结构(film to film+PC or glass )或Mylar此结构成本高,结构多,透明度低,OCA与Film贴合时良率低,此结构不建议客户使用。
引出线可采用Mylar或FPC。
或Mylar图七线路部分设计原则1)常用术语a. 外形尺寸(Out dimension):产品的外形面积b. 可视区(View dimension):透明区,装机后可看到的区域。
此区域不能出现不透明的走线及键片等c. 驱动面积(Active dimension):实际可操作的区域。
………………驱动面积比可视面积小………………d. 键片(Spacer):用于粘合上、下线路的双面胶。
e. 承托板:粘于下线背面,起支撑产品的作用。
由于材料增多,产品透明度有所降低f. 敏感区:驱动面积与键片内框的距离。
由于存在键片高度落差,当使用不当,很容易在此区域造成ITO膜断裂导致产品功能不良。
在产品设计上必须考虑周详。
此区域虽小,但不容忽视。
g. 蚀刻:把多余的ITO用酸腐蚀掉。
触摸屏的工艺流程
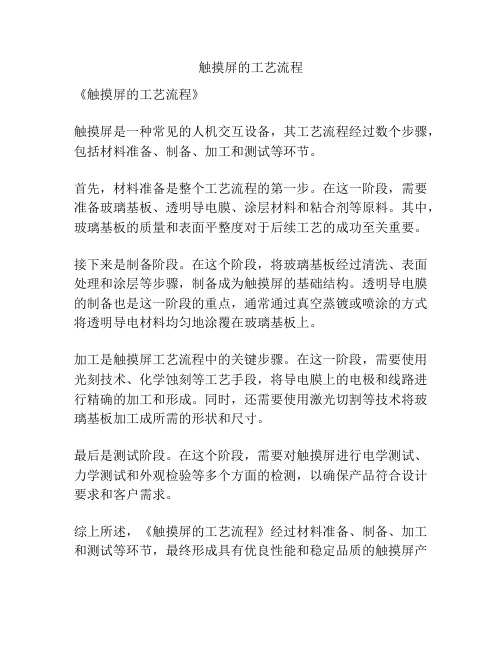
触摸屏的工艺流程
《触摸屏的工艺流程》
触摸屏是一种常见的人机交互设备,其工艺流程经过数个步骤,包括材料准备、制备、加工和测试等环节。
首先,材料准备是整个工艺流程的第一步。
在这一阶段,需要准备玻璃基板、透明导电膜、涂层材料和粘合剂等原料。
其中,玻璃基板的质量和表面平整度对于后续工艺的成功至关重要。
接下来是制备阶段。
在这个阶段,将玻璃基板经过清洗、表面处理和涂层等步骤,制备成为触摸屏的基础结构。
透明导电膜的制备也是这一阶段的重点,通常通过真空蒸镀或喷涂的方式将透明导电材料均匀地涂覆在玻璃基板上。
加工是触摸屏工艺流程中的关键步骤。
在这一阶段,需要使用光刻技术、化学蚀刻等工艺手段,将导电膜上的电极和线路进行精确的加工和形成。
同时,还需要使用激光切割等技术将玻璃基板加工成所需的形状和尺寸。
最后是测试阶段。
在这个阶段,需要对触摸屏进行电学测试、力学测试和外观检验等多个方面的检测,以确保产品符合设计要求和客户需求。
综上所述,《触摸屏的工艺流程》经过材料准备、制备、加工和测试等环节,最终形成具有优良性能和稳定品质的触摸屏产
品。
随着技术的不断进步和创新,触摸屏的工艺流程也在不断优化和改进,为用户提供更好的使用体验。
触摸屏贴合工艺流程资料

贴合工艺流程一.工艺流程:(一).OCA贴合流程(二)OCR贴合流程二.主要设备及作业方式:(一).切割、裂片:主要工艺过程:1. 将大块sensor 玻璃切割成小 panel 的制程 ,有镭射切割和刀轮切割两种方式,目前一般采用刀轮切割即可。
2. 有厂家研制出在大片上贴小保护膜的设备,可防止切割过程中产生的碎屑污染sensor 表面。
有厂家直接切割,然后将小片sensor 进行清洗。
3. 裂片有设备裂片和人工裂片两种方式,一般7inch 以下大部分厂家采用人工裂片方式,切割时在大片玻璃下垫一张纸,切割完成后,将纸抽出,到旁边的作业台上进行人工裂片。
裂片时先横向裂成条,在逐条裂成片。
(二).研磨清洗:1. 将裂成的小片周边进行研磨,现小尺寸一般厂家都不做研磨。
2. 清洗:采用纯水超声波清洗后烘干。
3.外观检查、贴保护膜清洗后的小片,进行全数外观检查,有无擦划伤、裂痕、污染等,良品贴保护膜。
3. ACF 贴附:大板小片5.FPC 压合(bonding )目的:让 touch sensor 与 IC 驱动功能连接。
註注: FPCa : 加上一个 “a ” 代表已焊上 IC , R & C 等component , “a ”为 為assembly 的意思.为加强FPC 强度及防止水汽渗入,有工艺在FPC bonding 后在FPC 周围涂布少量的UV 胶,经紫外灯照射后固化。
现在一般厂家已不再采用此工艺。
连接系统板 端的金手指FPCa bonding padI电容FPCaUV带状输送机FPC seal将UV Resin 涂布于FPC 周围及Glass edge UV cure固化涂布于FPC 及Glass edge 处的胶處6.贴合:将FPC bonding 后的Sensor 与cover glass 贴合在一起,依据所用胶材的不同,目前有两种贴合方式,一种是OCA 贴合,一种是OCR 贴合。
触摸屏贴合工艺流程
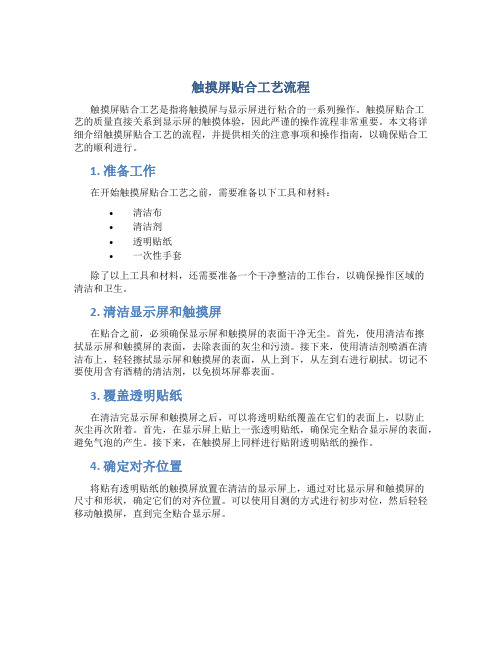
触摸屏贴合工艺流程触摸屏贴合工艺是指将触摸屏与显示屏进行粘合的一系列操作。
触摸屏贴合工艺的质量直接关系到显示屏的触摸体验,因此严谨的操作流程非常重要。
本文将详细介绍触摸屏贴合工艺的流程,并提供相关的注意事项和操作指南,以确保贴合工艺的顺利进行。
1. 准备工作在开始触摸屏贴合工艺之前,需要准备以下工具和材料:•清洁布•清洁剂•透明贴纸•一次性手套除了以上工具和材料,还需要准备一个干净整洁的工作台,以确保操作区域的清洁和卫生。
2. 清洁显示屏和触摸屏在贴合之前,必须确保显示屏和触摸屏的表面干净无尘。
首先,使用清洁布擦拭显示屏和触摸屏的表面,去除表面的灰尘和污渍。
接下来,使用清洁剂喷洒在清洁布上,轻轻擦拭显示屏和触摸屏的表面,从上到下,从左到右进行刷拭。
切记不要使用含有酒精的清洁剂,以免损坏屏幕表面。
3. 覆盖透明贴纸在清洁完显示屏和触摸屏之后,可以将透明贴纸覆盖在它们的表面上,以防止灰尘再次附着。
首先,在显示屏上贴上一张透明贴纸,确保完全贴合显示屏的表面,避免气泡的产生。
接下来,在触摸屏上同样进行贴附透明贴纸的操作。
4. 确定对齐位置将贴有透明贴纸的触摸屏放置在清洁的显示屏上,通过对比显示屏和触摸屏的尺寸和形状,确定它们的对齐位置。
可以使用目测的方式进行初步对位,然后轻轻移动触摸屏,直到完全贴合显示屏。
5. 粘合操作在确定好对位位置后,可以开始进行粘合操作。
首先,将触摸屏从显示屏上取下,并将触摸屏的背面涂抹上适量的透明胶水。
然后,将触摸屏小心地放置在显示屏上,并轻轻按压,使其与显示屏充分贴合。
6. 底部固定为了加强贴合效果,并确保触摸屏的稳定性,可以使用底部固定的方式进行固定。
一般情况下,贴合的显示屏和触摸屏边缘会有一定的空隙,可使用透明胶水或专用胶带进行固定。
将透明胶水或固定带涂抹在显示屏和触摸屏边缘的空隙处,并轻轻按压,使其紧密固定。
7. 压力处理在完成底部固定操作后,需要施加一定的压力,以促进触摸屏和显示屏的贴合效果。
触摸屏工艺流程
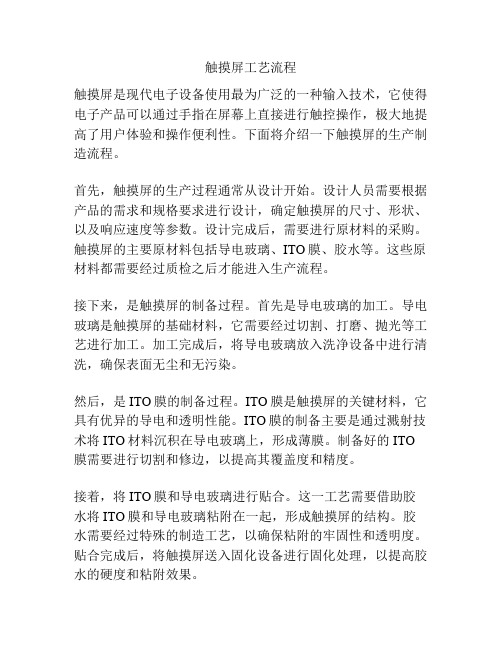
触摸屏工艺流程触摸屏是现代电子设备使用最为广泛的一种输入技术,它使得电子产品可以通过手指在屏幕上直接进行触控操作,极大地提高了用户体验和操作便利性。
下面将介绍一下触摸屏的生产制造流程。
首先,触摸屏的生产过程通常从设计开始。
设计人员需要根据产品的需求和规格要求进行设计,确定触摸屏的尺寸、形状、以及响应速度等参数。
设计完成后,需要进行原材料的采购。
触摸屏的主要原材料包括导电玻璃、ITO膜、胶水等。
这些原材料都需要经过质检之后才能进入生产流程。
接下来,是触摸屏的制备过程。
首先是导电玻璃的加工。
导电玻璃是触摸屏的基础材料,它需要经过切割、打磨、抛光等工艺进行加工。
加工完成后,将导电玻璃放入洗净设备中进行清洗,确保表面无尘和无污染。
然后,是ITO膜的制备过程。
ITO膜是触摸屏的关键材料,它具有优异的导电和透明性能。
ITO膜的制备主要是通过溅射技术将ITO材料沉积在导电玻璃上,形成薄膜。
制备好的ITO 膜需要进行切割和修边,以提高其覆盖度和精度。
接着,将ITO膜和导电玻璃进行贴合。
这一工艺需要借助胶水将ITO膜和导电玻璃粘附在一起,形成触摸屏的结构。
胶水需要经过特殊的制造工艺,以确保粘附的牢固性和透明度。
贴合完成后,将触摸屏送入固化设备进行固化处理,以提高胶水的硬度和粘附效果。
最后,是触摸屏的后处理工艺。
后处理主要包括表面处理和检测。
表面处理是将触摸屏的表面进行抛光和涂层处理,以提高表面的光滑度和耐磨性。
检测主要是通过特定的仪器和设备对触摸屏的电性能、光学性能、以及机械性能等进行检测和测量,确保触摸屏的质量符合要求。
以上就是触摸屏的制造工艺流程。
触摸屏的生产制造需要严格控制每个环节的质量,以确保触摸屏能够稳定可靠地工作。
随着技术的不断发展,触摸屏的制造工艺也在不断改进和创新,以适应不同产品的需求和市场的变化。
触摸屏贴合工艺流程资料
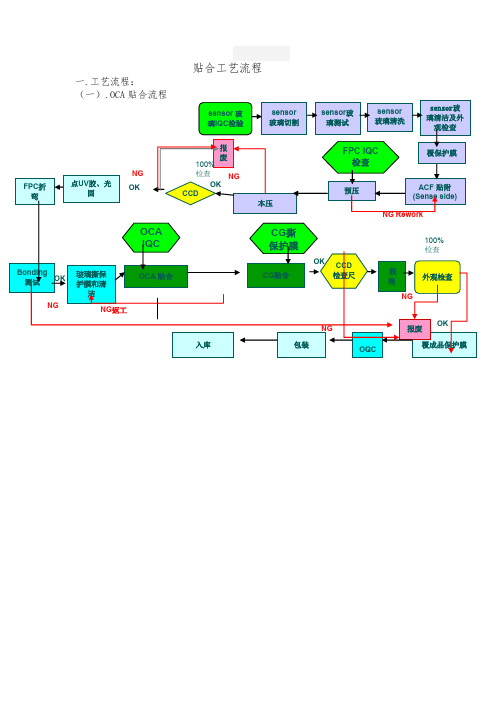
贴合工艺流程一.工艺流程:(二)OCR贴合流程二.主要设备及作业方式:(一).切割、裂片:主要工艺过程:1.将大块sensor玻璃切割成小panel 的制程 ,有镭射切割和刀轮切割两种方式,目前一般采用刀轮切割即可。
2.有厂家研制出在大片上贴小保护膜的设备,可防止切割过程中产生的碎屑污染sensor表面。
有厂家直接切割,然后将小片sensor进行清洗。
3.裂片有设备裂片和人工裂片两种方式,一般7inch以下大部分厂家采用人工裂片方式,切割时在大片玻璃下垫一张纸,切割完成后,将纸抽出,到旁边的作业台上进行人工裂片。
裂片时先横向裂成条,在逐条裂成片。
(二).研磨清洗:1.将裂成的小片周边进行研磨,现小尺寸一般厂家都不做研磨。
2.清洗:采用纯水超声波清洗后烘干。
3.外观检查、贴保护膜清洗后的小片,进行全数外观检查,有无擦划伤、裂痕、污染等,良品贴保护膜。
3.ACF贴附:小片FPC bonding pad5.FPC 压合(bonding )目的:让 touch sensor 与 IC 驱动功能连接。
註注: FPCa : 加上一个 “a ” 代表已焊上 IC , R & C 等component , “a ”为 為assembly 的意思.为加强FPC 强度及防止水汽渗入,有工艺在FPC bonding 后在FPC 周围涂布少量的UV 胶,经紫外灯照射后固化。
现在一般厂家已不再采用此工艺。
6.贴合:将FPC bonding 后的Sensor 与cover glass 贴合在一起,依据所用胶材的不同,目前有两种贴合方式,一种是OCA 贴合,一种是OCR 贴合。
OCA 贴合分两步,第一步将OCA 膜贴在sensor 上,俗称软贴硬,第二部将贴过OCA 膜的sensor 与盖板玻璃贴合在一起,俗称硬贴硬。
第一步:软贴硬连接系统板端的金手指FPCa bonding pad I 电容 FPCa UVFPC seal 将UV Resin 涂布于FPC 周围及Glass edge 处,加强FPC 强度及防止水汽渗入 UV cure固化涂布于FPC 及Glass edge 处的胶處所采用的设备一般为半自动OCA 贴附机,人工放置sensor 到设备台面上,人工撕除OCA 上层的隔离纸(可用一小段胶带粘下来,较方便),设备自动对位后完成贴附。
- 1、下载文档前请自行甄别文档内容的完整性,平台不提供额外的编辑、内容补充、找答案等附加服务。
- 2、"仅部分预览"的文档,不可在线预览部分如存在完整性等问题,可反馈申请退款(可完整预览的文档不适用该条件!)。
- 3、如文档侵犯您的权益,请联系客服反馈,我们会尽快为您处理(人工客服工作时间:9:00-18:30)。
•
团结奋斗
目标达成
5/42
学习内容
一、制造TEAM总工艺流程
资材入库
POL’附贴
COG压贴
组 装
出库
二、POL’附贴、COG压贴工艺流程
1. 半自动工程 1-1) POL’附贴(偏光片) 资材准备
目的: 根据P/O申请入库当天生产所需要的资材(注意确认当日的生产型号及数量)
下POL’附贴
目的: 本工程是按规格把偏光片(POL’)附贴在 PANEL TFT玻璃表面上
品質定義﹕就是以最經濟的方法﹐提顧客滿意的產品與服務
团结奋斗 目标达成
2/42
向員工宣導---品質三不 & 物品三定觀念
• • • • • • • 1. 不制造不良品 2. 不接受不良品 3. 不送出不良品 1. 定 品 2. 定 位 3. 定 量
团结奋斗
目标达成
3/42
管理意識
• 品質---是制造出來的
FPC 压贴
目的: FPC 输出端子同PANEL PAD部的输出端子进行相对端子重合紧密连在一起
团结奋斗
目标达成
8/42
显微镜检查
目的: ACF导电粒子的确认,是否在规格数量内
M/T 检查
目的: 对FPC压贴后的LCD进行画质有无异常检查
外观 输出
目的:用肉眼检查产品外型是否按标准制造(不允许有规格规定外的不良发生),
够成LOT 填好传票流入下一工程
2. 自动(AUTO)工程 2-1) AUTO POL’
PANEL 洗净
目的: 在粘POL’之前,用专用工具把LCD表面进行异物及杂质的清理
PANEL 投入
目的: 为下一工程做生产准备,准备好原材料等待生产
POL’ 粘贴
目的: 本工程是按规格把偏光片(POL’)附贴在 PANEL玻璃表面上
输出
目的: 把产品按LOT别进行收集,收集时要注意外观的确认
热处理
(auto clave)
目的: 在真空状态下,用一定的时间同压力,加强PANEL与POL’的密贴性设备
外观检查
目的: 用肉眼检查产品外型是否按标准制造(不允许有规格规定外的不良发生)
B M S
PANEL投入
目的: 为下一工程做生产准备,准备好原材料等待生产 目的: 对PANEL 的 PAD部位进行异物及杂质彻底清扫
3. 从前往后
团结奋斗
目标达成
15/42
五.设备日常维护
一、设备维护 目的 1. 在于实现生产设备运营的效率最大化。 2. 减少由于故障引起的停产损失; 3. 减少修理费用; 4. 减少制品不良; 5. 提高设备的启动率; 6. 以适当的SPARE减少再库品; 7. 以设备的有效运营来减少制造成本; 8. 以设备的安全运营来减少突然性事故的发生;
CNT 检查
目的: 确认CNT部位是否有不良缺陷
外观 检查
目的: 用肉眼检查产品外型是否按标准制造(不允许有规格规定外的不良发生)
电 算
目的: 把良品产品进行收集够成LOT,进行电算移交下一工程(注意产品混入)
团结奋斗
目标达成
14/42
四、清扫顺序及方法
1. 清扫周期
1. 上班时各工位 5分钟进行设备及桌面完全清扫 2. 个别工程按照工作别清扫周期进行清扫
团结奋斗
目标达成
9/42
V/I 检查 A V T 检 查 外观检查 L/T 切线
目的: 粘上POL’后的PANEL对LCD的画质是否有异常进行检查的工序 目的: 用肉眼检查产品外型是否按标准制造(不允许有规格规定外的不良发生) 目的: 用激光(LASER)剪断 LCD TFT规定的回路组成的细微金属排线
团结奋斗
目标达成
11/42
FPC 压贴
目的: FPC 输出端子同PANEL PAD部的输出端子进行相对端子重合紧密连在一起
ATT 检查
目的: 对前工程压贴后的部位进行品质确认,是否有无异常发生(主要是ACF导电球是否正常) 目的: 用肉眼检查产品外型是否按标准制造(不允许有规格规定外的不良发生) 目的: 对FPC压贴后的LCD进行画质有无异常检查
IC本压
目的: 用自动设备把粘贴好的IC进行在次加压紧固,使IC不能有脱落的现象
外观检查
目的: 用肉眼检查产品外型是否按标准制造(不允许有规格规定外的不良发生)
显微镜检查
目的: ACF导电粒子的确认,是否在规格数量内,(在确认A/M是否在基准内)
FOG ACF 粘贴
目的: 用固定的ACF粘贴机把ACF粘在PANEL PAD部规定的部位(COG导电球5EA以上,
目
1 2
3 4 5
录
品质意识教育 品质意识教育
教育流程 教育流程
作业方法及注意事项
维护设备目的 清扫顺序及方法
维护设备目的
团结奋斗
目标达成
1/42
管理理念
品質觀念—高標準,精緻化,零缺陷;
優秀的產品是優秀的人做出來的. • • • • • • • • 质量管理理念: A. 质量是制造出来的,不是检查员检查出来的 B. 第一次就把事情做好 C. 管生产的人就要管质量 员工在现场生产过程中要做到:“三確認” “确认上道工序零部件的加工质量” “确认本工序加工的技术、工艺要求和加工质量” “确认交付到下道工序的完成品质量
在此: 请接受我诚挚的谢意,我非常感谢大家对我的帮助与支持!!
团结奋斗
目标达成
17/42
外观 检查
目的: 用肉眼检查产品外型是否按标准制造(不允许有规格规定外的不良发生)
L/T(切线)
目的: 用激光(LASER)剪断 LCD TFT规定的回路组成的细微金属排线
L/T出货检查
(OG)
目的: 确认通过L/T工程的产品是否有异常现象的发生;够成LOT填好传票流入下一工程
1-2) COG 压贴 PANEL洗净
自动洗净
团结奋斗
目标达成
10/42
COG ACF压贴
目的: 用自动设备把ACF自动粘贴在PANEL PAD部规定部位相紧密结合
IC粘贴/假压
目的: 用自动加压设备把IC粘贴在所规定的部位,然后在轻轻的压一下 (使其不能有掉落现象) 目的: 用自动设备把粘贴好的IC进行在次加压紧固,使IC不能有脱落的现象
9. 延长设备的使用寿命
团结奋斗
目标达成
16/42
感想与不足
1、感 想 通过本次学习,让我从中学到了很多知识,给我带来了非常大的收获,也让我领会到了自身的不足;
从不知道到了解,从陌生到熟悉!并且做到了与人有效的沟通,在以后的工作中,我将把我学到的知识运 用到工作中,让我同我们的同事们一起合作;不管是工作还是生活,都需要人与人之间的相互帮助,默契
配合,相互学习、信任、利用团队的凝聚力,大家同心协力来解决我们生活与工作中所遇到的问题,将
优点进行全力分享,将缺点全力分析并进行有效的改善,让自己成为员工与公司上层领导的有效桥梁, 达到到我们预定的各项指标,相信我们将会做得更好! 2、不足 在学习过程中,还有很多不知道的地方,不良的具体区分及辨认,发生原因的分析等…….! 希望在 以后工作中多多积累经验,同时更希望得到各位领导及同事的大力帮助与支持!
M/K 打印
目的: 用喷墨激光打印机按顾客的要求事项 打印在固定位置上
M/TP
目的: 性能检查(对产品所需的性能进行输入)
团结奋斗
目标达成
13/42
F/T
目的: 最终画质检查(对画质有无异常及确认在肉眼状态下看不见的缺陷)
TAPE粘贴
目的: 按顾客的要求把TAPE贴在上POL’的固定位置
目的: 对PANEL 的 PAD部位进行异物及杂质彻底洗浄
COG ACF压贴
目的: 用自动设备把ACF自动粘贴在PANEL PAD部规定部位相紧密结合
团结奋斗
目标达成
7/42
COG ACF检查
目的: 用电脑自动程序对上工程附贴好的ACF进行品质确认(异常时自动报警)
IC粘贴/假压
目的: 用自动加压设备把IC粘贴在所规定的部位,然后在轻轻的压一下(使其不能有掉落现象)
2. 清扫工具
1. 无尘布 2. 酒精(I.P.A) 3. 棉棒 4. 吸尘器(小型) 5. 牙刷
3. 注意事项
1. 清扫时设备一定要确认是否在手动状态(一定在手动状态下清扫设备,避免压伤\夹伤) 2.清扫传送时,要确认是否处于关闭状态 3. 酒精不能过量
4. 清扫顺序
1. 从高往下进行清扫 2. 从内往外
IC 本压
显微镜检查
目的: ACF导电粒子的确认,是否在规格数量内
FOG ACF 粘贴
目的: 用固定的ACF粘贴机把ACF粘在PANEL PAD部规定的部位
自动检查ACF
目的: 设备自动对ACF 粘贴后的品质进行确认,有无异常发生
FPC 假压
目的: 用自动加压设备把FPC粘贴在所规定的部位,然后在轻轻的压一下 (使其不能有掉现象)
外观 检查
M/T 检查
SI (硅胶)涂布
目的: 把硅胶(液体状态)涂布在IC四周的表面 (保护IC受到外部撞、压及受潮)
U/V 硬化
目的: 用紫外线在一定的温度下,把液态状的硅胶变成固体 目的: 用肉眼检查产品外型是否按标准制造(不允许有规格规定外的不良发生) 目的: 把产品按LOT别进行收集,收集时要注意外观的确认
外观 检查
输出
团结奋斗
目标达成
12/42
三、组装 工艺流程(LMS198GF02)
B/L 组装
目的: 把B/L组装在Panel的下POL,结合在一起。