热轧薄规格带钢塔形产生原因及控制措施
热轧质量缺陷及产生原因
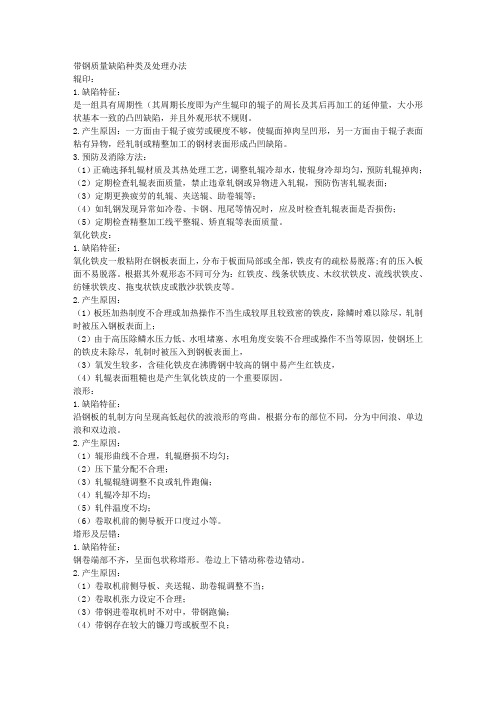
带钢质量缺陷种类及处理办法辊印:1.缺陷特征:是一组具有周期性(其周期长度即为产生辊印的辊子的周长及其后再加工的延伸量,大小形状基本一致的凸凹缺陷,并且外观形状不规则。
2.产生原因:一方面由于辊子疲劳或硬度不够,使辊面掉肉呈凹形,另一方面由于辊子表面粘有异物,经轧制或精整加工的钢材表面形成凸凹缺陷。
3.预防及消除方法:(1)正确选择轧辊材质及其热处理工艺,调整轧辊冷却水,使辊身冷却均匀,预防轧辊掉肉;(2)定期检查轧辊表面质量,禁止违章轧钢或异物进入轧辊,预防伤害轧辊表面;(3)定期更换疲劳的轧辊、夹送辊、助卷辊等;(4)如轧钢发现异常如冷卷、卡钢、甩尾等情况时,应及时检查轧辊表面是否损伤;(5)定期检查精整加工线平整辊、矫直辊等表面质量。
氧化铁皮:1.缺陷特征:氧化铁皮一般粘附在钢板表面上,分布于板面局部或全部,铁皮有的疏松易脱落;有的压入板面不易脱落。
根据其外观形态不同可分为:红铁皮、线条状铁皮、木纹状铁皮、流线状铁皮、纺锤状铁皮、拖曳状铁皮或散沙状铁皮等。
2.产生原因:(1)板坯加热制度不合理或加热操作不当生成较厚且较致密的铁皮,除鳞时难以除尽,轧制时被压入钢板表面上;(2)由于高压除鳞水压力低、水咀堵塞、水咀角度安装不合理或操作不当等原因,使钢坯上的铁皮未除尽,轧制时被压入到钢板表面上,(3)氧发生较多,含硅化铁皮在沸腾钢中较高的钢中易产生红铁皮,(4)轧辊表面粗糙也是产生氧化铁皮的一个重要原因。
浪形:1.缺陷特征:沿钢板的轧制方向呈现高低起伏的波浪形的弯曲。
根据分布的部位不同,分为中间浪、单边浪和双边浪。
2.产生原因:(1)辊形曲线不合理,轧辊磨损不均匀;(2)压下量分配不合理;(3)轧辊辊缝调整不良或轧件跑偏;(4)轧辊冷却不均;(5)轧件温度不均;(6)卷取机前的侧导板开口度过小等。
塔形及层错:1.缺陷特征:钢卷端部不齐,呈面包状称塔形。
卷边上下错动称卷边错动。
2.产生原因:(1)卷取机前侧导板、夹送辊、助卷辊调整不当;(2)卷取机张力设定不合理;(3)带钢进卷取机时不对中,带钢跑偏;(4)带钢存在较大的镰刀弯或板型不良;(5)卷取机卸卷时将钢卷头部拽出。
热轧带钢卷取塔形问题分析及控制措施

热轧带钢卷取塔形问题分析及控制措施王克柱【摘要】Based on analysis of production process, the telescoping problem resulted in inner telescoping generated by uneven force of the strip head and outside telescoping caused by tail tension reduction. The side guide ruler parallelism of the coiler and short stroke control sequence were transformed, resolving the inner telescoping. The upper pinch roll crown was 0.75 mm, lower pinch roll crown was 1.5 mm and then the roller type was rationally allocated. At the same time, the pinch roller pressure correction function was developed and the coiler tension setting was optimized. After optimization and improvement, the defective products due to telescoping were reduced by 60%and the comprehensive qualified rate was increased.% 通过对生产过程的分析,卷取塔形主要由带钢头部不均匀受力产生的内塔形及尾部张力减少产生的外塔形导致。
改造卷取机侧导尺平行度及短行程控制时序,解决了内塔形的问题;上夹送辊凸度为0.75 mm,下夹送辊凸度为1.5 mm,合理配置辊型;同时开发了夹送辊压力修正功能并优化卷取机张力设定。
热轧带钢板形的常见影响因素与措施
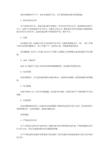
热轧带钢板形生产中,容易出现板形不良,其主要的影响因素及控制措施:1、板坯加热及冷却由于加热时间不足,或是轧制过程中除磷水、冷却水的不均匀分布,造成钢坯的表面与中心、边部与中部的温度分布不均匀,在板坯长度方向,断面宽向及厚向的温差直接影响轧制力和内应力的分布,造成轧制过程中带钢延伸不均,板形不良。
2、轧辊1)轧辊热凸度。
轧辊沿长度方向加热和冷却不均,轧辊的热膨胀也不一样,一般工作辊中部比边部的热膨胀大,使工作辊产生一定的热凸度,直接影响最终板形。
2)轧辊磨损。
轧件与工作辊之间以及工作辊与支撑辊之间的摩擦会造成轧辊的不均匀磨损。
3、AGC大幅动作AGC过大幅度下压或上抬容易加剧带钢跑偏程度,造成板形的剧烈变化。
4、轧机间隙轧机间隙增大,会引起轧辊的横向及轴向窜动,会影响设备精度,最终影响板形控制精度。
5、轧件跑偏如果开始咬入时,轧件存在跑偏量,如未能及时消除,轧制后便会产生整体板形不良的现象。
6、轧机刚度轧机两侧刚度的差异,造成轧机实际弹跳值与模型设定值存在较大差异,在轧钢过程中带钢两侧存在一定厚度偏差,影响轧制稳定性。
改进措施:1、严格加热及冷却生产中要保证坯料在炉加热时间,根据轧制节奏合理控制各段炉温,严格控制板坯水印在15℃以内,保证各温度监测点的实测温度准确。
生产中要定期对轧辊冷却系统进行检查维护,保证轧辊冷却系统沿辊身长度方向冷却的均匀性。
2、轧辊及时更换轧辊是避免轧辊过度磨损,改善带钢板形的有效手段,同时,应合理选择轧辊材质,减少轧辊表面磨损,尽可能减少有害变形区的不利影响。
3、AGC在保证成品厚度满足要求前提下适当降低AGC调整限幅。
4、减小轧机间隙定期检查牌坊滑板、轴承座衬板、轧辊挡板、支承辊垫板等的磨损情况,对磨损严重的及时进行修补更换,并保证轧辊装配到位,使轧制过程中轧辊不出现横向、轴向窜动。
5、轧件对中对于轧件跑偏问题,通过提高加热炉出钢精度,更换磨损严重的辊道,减小轧件初始跑偏量,同时根据现场来料跑偏情况配合动态调整粗轧机前立辊中心线,提高轧件对中程度,避免跑偏造成的板形较大变化。
热轧带钢生产中的板形控制(2篇)

热轧带钢生产中的板形控制在带钢生产中,只有保证其良好的板形,才能确保生产顺利进行,才能使产品产量、质量不断提高。
当带钢内部残余应力足够大时,会使带钢翘曲,表现为侧弯、边浪、小边浪、小中浪。
在带钢钢种确定的情况下,产生翘曲与带钢的宽度、厚度有关。
带材越薄、越宽,生产中越易翘曲。
而目前市场对带材的需求是既宽且薄,因此,良好的板形控制非常重要。
一、生产中出现板形问题的主要原因1.带钢的不均匀受热或冷却带钢加热或冷却不均时会在内部产生应力,当其值超过极限就会出现板形问题。
在宽度方向上出现应力不均时会产生边浪或小边浪。
2.坯料尺寸不合如果坯料尺寸不合规格,断面厚薄不均,则会造成带材宽度方向延伸不均。
3.辊缝设置不合理如果辊缝设置不均匀,单边差较大,则会导致带材延伸不一致。
4.轧辊问题(1)在轧制过程中,轧辊因受较大轧制力、热凸度、磨损等影响,会出现一段有害变形区。
(2)由于轧辊材质或铸造问题,使用中会出现较大磨损;意外事故也会导致轧辊端部剥落,使带材受力严重不均,出现侧弯。
(3)轧辊导卫固定不牢,轧辊轴承座和机架窗口间隙大,也会引起轧辊横向窜动。
二、预防措施1.严格执行加热制度,保证加热质量生产中必须严格执行加热制度、停轧降温制度。
要根据轧制节奏需要,合理控制各段炉温,保证开轧温度,并使坯料加热均匀。
2.保证坯料表面质量和尺寸精度装炉前要对坯料进行表面检查,及时清除表面缺陷,并保证尺寸精度。
3.合理设置辊缝根据轧制规程合理调整各道次压下量,轧制速度必须与压下量相适应。
轧制过程中精轧机组保持小套量微张力轧制,精、粗轧机组之间保持无张力微堆轧制。
粗轧单边差不大于05mm,精轧单边差不大于003mm。
4.正确选择轧辊材质,合理设计轧辊辊型根据轧制过程中出现的轧辊有害变形区大小,计算支撑辊的弯曲挠度,合理设计辊型。
在支撑辊两端改为阶梯形过度。
另外,应合理选择轧辊材质,减少轧辊表面磨损,并尽可能减少有害变形区。
热轧时,轧辊表面既承受高温又承受水的激冷,因而产生的工作应力、热应力和疲劳应力可导致辊面产生裂纹。
热轧带钢生产中的板形控制范文
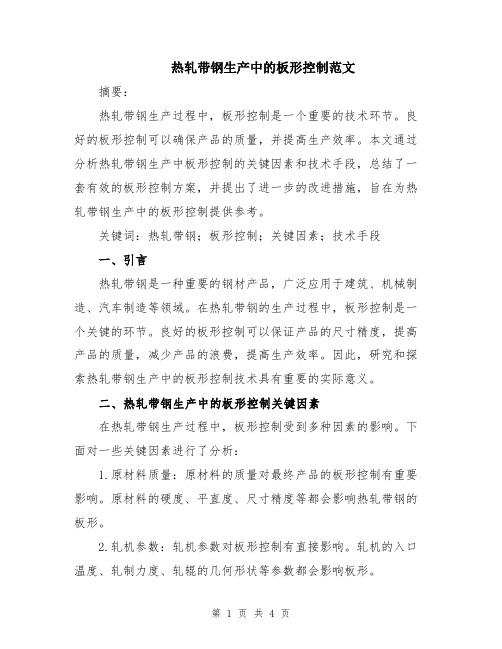
热轧带钢生产中的板形控制范文摘要:热轧带钢生产过程中,板形控制是一个重要的技术环节。
良好的板形控制可以确保产品的质量,并提高生产效率。
本文通过分析热轧带钢生产中板形控制的关键因素和技术手段,总结了一套有效的板形控制方案,并提出了进一步的改进措施,旨在为热轧带钢生产中的板形控制提供参考。
关键词:热轧带钢;板形控制;关键因素;技术手段一、引言热轧带钢是一种重要的钢材产品,广泛应用于建筑、机械制造、汽车制造等领域。
在热轧带钢的生产过程中,板形控制是一个关键的环节。
良好的板形控制可以保证产品的尺寸精度,提高产品的质量,减少产品的浪费,提高生产效率。
因此,研究和探索热轧带钢生产中的板形控制技术具有重要的实际意义。
二、热轧带钢生产中的板形控制关键因素在热轧带钢生产过程中,板形控制受到多种因素的影响。
下面对一些关键因素进行了分析:1.原材料质量:原材料的质量对最终产品的板形控制有重要影响。
原材料的硬度、平直度、尺寸精度等都会影响热轧带钢的板形。
2.轧机参数:轧机参数对板形控制有直接影响。
轧机的入口温度、轧制力度、轧辊的几何形状等参数都会影响板形。
3.辊道调整:辊道的调整能够直接改变板形。
通过调整辊道的水平度、垂直度、辊冠等参数,可以获得理想的板形。
4.冷却措施:冷却措施可以改变钢材的温度分布,进而影响板形。
冷却方式、冷却速度等参数都会对板形产生影响。
以上因素只是热轧带钢生产中的一部分,还有许多其他因素也会对板形控制产生影响。
了解这些关键因素,并采取相应的措施进行控制,是有效控制板形的基础。
三、热轧带钢生产中的板形控制技术手段在热轧带钢生产中,有多种技术手段可用于板形控制。
下面介绍几种常用的技术手段:1.辊道调整:通过调整辊道的水平度、垂直度、辊冠等参数,可以改变钢材的板形。
辊道调整是热轧带钢生产中最常用的板形控制手段之一。
2.冷却措施:通过改变冷却方式、冷却速度等参数,可以改变热轧带钢的板形。
冷却措施是一个非常有效的板形控制手段。
热轧带钢卷取塔形形成原因及改善分析措施

热轧带钢卷取塔形形成原因及改善分析措施作者:魏明贺来源:《科学与财富》2014年第13期摘要:针对热轧钢卷塔形缺陷,从生产工艺和过程控制方面对其生产的机理进行了分析,并结合现场生产情况提出了改善措施,减少塔形的产生,提高产品卷形质量和经济效益。
关键词:带钢;塔形;改善措施1 概述通钢热连轧机生产线主体设备主要有两座辊道式加热炉、两架粗轧机、五架精轧机架和两台地下卷取机,该生产线以PC交叉、工作辊窜辊、自动宽度控制和自动厚度控制等一系列先进的技术手段为特征,产品质量高,市场竞争力强。
生产主要品种为1.6~12.7mm厚,900~1530mm宽的碳素结构钢、低合金钢、汽车大梁钢、管线钢等。
年产量300万吨。
带钢的卷取是热轧的最后一道关键工序,卷取机是热轧线上必不可少的极为重要的设备。
钢卷塔形是最常见的卷取缺陷,占产品次品总量的30%左右,带来的诸多危险如下:(1)钢卷塔形严重影响产品外观形象,造成经济损失;(2)钢卷塔形易造成带钢边部折边和破裂、降低成才率;(3)钢卷塔形影响产品标号和运输。
针对钢卷塔形的成因进行分析,同时提出改善措施,以提高钢卷卷形质量。
2 塔形形成原因2.1 原料板坯的影响原料板坯存在楔形,易造成钢卷塔形。
板坯楔形不仅包括通常所说的几何楔形,而且还包括温度楔形。
板坯几何楔形是指板坯沿宽度方向上厚度从一侧到另外一侧逐渐增大或减少。
原料板坯存在几何楔形,在轧制过程中轧件将逐渐偏离轧制中心,轧后出现镰刀弯,导致卷取后出现塔形。
板坯温度楔形是指板坯沿宽度方向上温度逐渐增高或降低。
由于板坯温度不均,使得轧件变形抗力不一致,轧制力P发布不均。
根据如下弹跳方程(公式1)可知,轧制力分布不均引起轧件厚度h不均,造成轧制过程不稳定,易出现塔形。
h=S3+■ (公式1)2.2 轧制过程稳定性的影响带坯进入精轧机组时,特别是F1轧机,带坯对中状态将直接决定着轧制过程的稳定性。
为了使带坯能够顺利穿带,必须提高轧机入口侧导板对中精度和设定合理的间隙余量,保证带坯进入轧机时的对中性。
热轧薄材板凸度控制

热轧薄材板凸度控制随着现代工业的发展,热轧薄材板在工业生产中扮演着重要的角色。
热轧薄材板广泛应用于汽车制造、船舶建造、压力容器、航空航天等领域。
在生产过程中,热轧薄材板的凸度控制问题一直是制造商面临的难题。
凸度不仅影响了产品的质量,还会给生产带来额外的成本和麻烦。
研究和控制热轧薄材板凸度,对提高产品质量和生产效率具有非常重要的意义。
一、热轧薄材板凸度的形成原因热轧薄材板的凸度是指板材在加热、轧制和冷却过程中产生的一种弯曲形变。
其形成主要有以下几个原因:1.材料特性:热轧薄材板在轧制过程中,会受到温度和应力的影响,导致板材内部结构发生变化,从而产生弯曲形变。
2.轧机操作:轧机的工作状态和轧辊调整不当,会导致板材受到不均匀的挤压,从而形成凸度。
3.冷却过程:板材在冷却过程中,由于温度变化不均匀,会导致板材内部产生不同程度的收缩,进而产生凸度。
热轧薄材板的凸度一旦超出允许范围,就会对产品的质量造成严重影响。
凸度过大会导致板材塑性变形不均匀,严重影响板材的表面质量和力学性能,从而降低产品的使用价值。
如果凸度严重,还会增加生产成本,影响生产效率,降低企业的竞争力。
控制热轧薄材板凸度是非常重要的。
1.材料选择:选择合适的原材料是控制热轧薄材板凸度的第一步。
优质的原材料具有较好的塑性和韧性,能够在轧制过程中减小内部应力,并且易于形变,从而降低凸度的产生。
2.轧机调整:合理的轧机调整是控制热轧薄材板凸度的关键。
轧机的工作状态和轧辊的调整对板材形变有着直接的影响。
操作人员需要熟练掌握轧机的操作技巧,根据板材的材料和规格,合理调整轧机的工作参数,以减小凸度的产生。
3.冷却控制:冷却过程对热轧薄材板凸度也有着重要的影响。
要合理控制板材的冷却速度和温度分布,避免板材内部产生不均匀的收缩,减小凸度的产生。
通过以上几个方面的控制,可以有效减小热轧薄材板的凸度,提高产品的质量和生产效率。
具体的操作和控制还需要根据不同的板材材料和规格来进行调整,生产厂家可以根据实际情况进行合理的控制。
热轧带钢塔形产生原因及预防
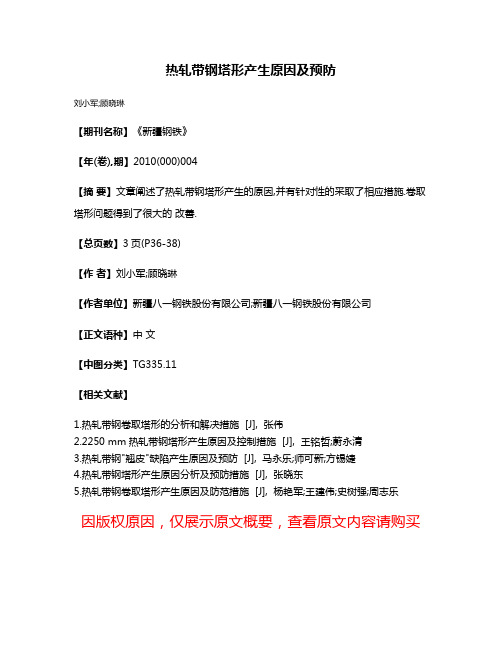
热轧带钢塔形产生原因及预防
刘小军;顾晓琳
【期刊名称】《新疆钢铁》
【年(卷),期】2010(000)004
【摘要】文章阐述了热轧带钢塔形产生的原因,并有针对性的采取了相应措施.卷取塔形问题得到了很大的改善.
【总页数】3页(P36-38)
【作者】刘小军;顾晓琳
【作者单位】新疆八一钢铁股份有限公司;新疆八一钢铁股份有限公司
【正文语种】中文
【中图分类】TG335.11
【相关文献】
1.热轧带钢卷取塔形的分析和解决措施 [J], 张伟
2.2250 mm热轧带钢塔形产生原因及控制措施 [J], 王铭哲;蔚永清
3.热轧带钢"翘皮"缺陷产生原因及预防 [J], 马永乐;师可新;方锡婕
4.热轧带钢塔形产生原因分析及预防措施 [J], 张晓东
5.热轧带钢卷取塔形产生原因及防范措施 [J], 杨艳军;王建伟;史树强;周志乐
因版权原因,仅展示原文概要,查看原文内容请购买。
热轧带钢生产中的板形控制
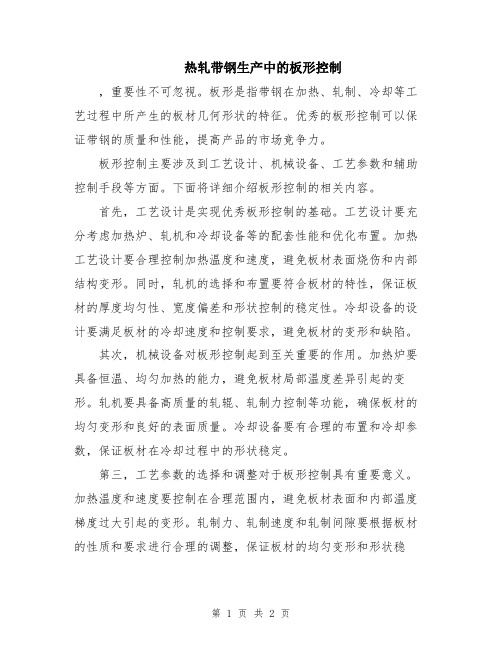
热轧带钢生产中的板形控制,重要性不可忽视。
板形是指带钢在加热、轧制、冷却等工艺过程中所产生的板材几何形状的特征。
优秀的板形控制可以保证带钢的质量和性能,提高产品的市场竞争力。
板形控制主要涉及到工艺设计、机械设备、工艺参数和辅助控制手段等方面。
下面将详细介绍板形控制的相关内容。
首先,工艺设计是实现优秀板形控制的基础。
工艺设计要充分考虑加热炉、轧机和冷却设备等的配套性能和优化布置。
加热工艺设计要合理控制加热温度和速度,避免板材表面烧伤和内部结构变形。
同时,轧机的选择和布置要符合板材的特性,保证板材的厚度均匀性、宽度偏差和形状控制的稳定性。
冷却设备的设计要满足板材的冷却速度和控制要求,避免板材的变形和缺陷。
其次,机械设备对板形控制起到至关重要的作用。
加热炉要具备恒温、均匀加热的能力,避免板材局部温度差异引起的变形。
轧机要具备高质量的轧辊、轧制力控制等功能,确保板材的均匀变形和良好的表面质量。
冷却设备要有合理的布置和冷却参数,保证板材在冷却过程中的形状稳定。
第三,工艺参数的选择和调整对于板形控制具有重要意义。
加热温度和速度要控制在合理范围内,避免板材表面和内部温度梯度过大引起的变形。
轧制力、轧制速度和轧制间隙要根据板材的性质和要求进行合理的调整,保证板材的均匀变形和形状稳定。
冷却温度和速度等参数要控制在合理的范围内,避免板材在冷却过程中的变形和缺陷。
最后,辅助控制手段的应用可以提高板形控制的精度和稳定性。
例如,引入轧制力控制系统、辊形调整系统和垫板调整系统等,可以实时监测和调整轧机的工作状态,及时纠正板材的偏差和变形。
同时,利用数字化技术和智能控制系统,对板形控制进行实时监测和数据分析,提高板形控制的效果和精度。
总之,热轧带钢生产中的板形控制是一项复杂而关键的工作。
通过合理的工艺设计、优质的机械设备、合理的工艺参数和先进的辅助控制手段的应用,可以实现优秀的板形控制,提高带钢产品的质量和竞争力。
热轧带钢常见质量缺陷及其控制措施分析

热轧带钢常见质量缺陷及其控制措施分析作者:弓习峰来源:《中国科技博览》2017年第33期[摘要]对于企业而言,板材的轧制板材质量对其的经济效益有着直接的影响,更是体现了轧钢的水平现状,本文针对热轧带钢常见质量缺陷及其控制措施进行了论述,希望有一定的参考价值。
[关键词]热轧带钢;质量缺陷;控制措施中图分类号:TG335.11 文献标识码:A 文章编号:1009-914X(2017)33-0135-01前言社会的发展,促进了行业的进步和发展,也使得生产市场竞争越来越激烈,怎么对生产用原料的生产成本进行降低,让原料引起的质量问题的发生率减少,提升带钢质量,避免出现带钢镰刀弯,这是目前非常重要的研究课题。
通过对热轧带钢在生产的过程中出现的的质量问题的原因进行深入的分析和探究,运用有效的措施对这些问题进行合理的解决,这对提高热轧带钢产品质量有着十分重要的意义。
一、概述通常情况下,热轧带钢的具体质量要求包括:成品规格、凸度等方面允许的偏差,其中,卷形缺陷指标具体有塔型、镰刀弯等方面的偏差值,带钢表面和内部缺陷的要求具体有表面洁净度、折叠、气泡、铁皮压入、气泡、折叠等,其中还包括带头带尾精度指标、几何尺寸要求。
但是,在实际的生产当中,成品质量依然和理想标准不相符。
这就要求我们对常见的热轧带钢质量缺陷采取有效的控制措施,采用分类分析的方法,制定出系统的控制方案。
文中结合热轧生产线的设备特性及生产工艺流程,重点分析和阐述了带钢氧化铁皮压入及带钢镰刀弯两种质量缺陷成因及控制改进实践方案。
二、邯钢2250热轧生产线的设备特性及生产工艺流程邯钢2250热轧的粗轧机组是双四辊可逆式粗轧机组布置,可以在R1和R2两架粗轧机上实现3+3、3+5或0+7道次的可逆轧制,把板坯轧制成35 mm-60 mm厚的目标中间坯。
双四辊可逆式粗轧机组的优越性在于能够实现大压下量轧制,充分释放粗轧机R1的能力。
粗轧高温大压下的工艺设置可以有效破碎铸坯树枝状晶,从而改善组织的均匀性;四辊轧机比二辊轧机轧制更稳定,对板坯的轧制控制精度更高,更利于生产出高精度的中间坯[1]。
热轧带钢卷取塔形与层错缺陷的分析和改善

热轧带钢卷取塔形与层错缺陷的分析和改善赵永达1 王猛1 李建国2 周景鑫1(1.河北钢铁股份有限公司承德分公司提钒钢轧二厂;2.河北钢铁股份有限公司承德分公司钒钛工程技术研究中心,河北承德,067102)【摘要】在实际生产中针对出现的塔形卷与层错卷,分析产生原因并制定合理的改善措施,减少不合格卷产生,提高了成材率和产品形象。
【关键词】卷取塔形层错改善1.前言提高钢卷卷形一直是热连轧企业的一个难题,特别是轧制薄规格板带及厚规格的高强度钢。
面对激烈的市场竞争和客户越来越高的要求,卷形已经成为生产过程中的质量指标。
卷形的好坏不但影响着运输及吊运,而且还影响着下道工序的加工和使用。
更重要的是卷形还代表着一个企业的形象,良好的卷形会为企业争取更大的效益。
承钢提钒钢轧二厂1780mm热轧卷取机设备是由一重制造,SIMENS提供电气控制,采用两台地下三辊式卷取机,由8组热输出辊道,1组机上辊道,侧导板,夹送辊,芯轴,助卷辊,和卸卷小车构成,并在卷取机出口设置打包机构。
先期的调试为以后的顺行提供了保障,但随着轧制品种和规格的增加,出现了一些新的问题。
下面针对1780mm热轧卷取存在的一些问题进行分析,并制定措施。
2.生产过程中出现的塔形卷分析塔形卷形式主要是头部塔形与钢卷整体称面包状。
头部塔形超出60mm及被降级,但在实际生产当中,对于轧制h≤3mm的带钢,带钢头部出精轧机架不易控制,致使头部进入侧导板之时有明显跑偏现象,所以必然头部几圈出现塔形,这种塔形在钢卷下线时经过夹钳吊运会减轻或消除。
此情况改善控制主要在侧导板处,现侧导板控制动作时序如下:图1 卷取前导板控制图带钢到达机前HMD时进行短行程动作,进入夹送辊后关闭余量进而进行压力动态控制,所以,在安全范围内减少短行程与余量的值,能够改善薄带钢头部塔形状况。
经验值短行程单侧值可取得安全范围值为30mm~40mm,余量取10mm~15mm。
另外一种现象是面包卷,对于此现象轧制h≤3mm易出现。
浅析热轧带钢表面质量控制

浅析热轧带钢表面质量控制作者:薛彦珍来源:《科学导报·学术》2020年第36期摘;;要:现代化建设当中,钢铁行业的竞争压力日渐加大,如何减少钢铁生产过程中的成本投入与质量问题开始成为行业关注的热点。
本文将主要讨论热轧带钢表面常见的质量问题与控制措施,仅供参考。
关键词:热轧带钢;质量控制;措施1.热轧带钢表面常见质量缺陷与发生原因(1)麻面麻面是指带钢热轧过程中表面形成较多无规则凹坑现象,原因主要以下三点:其一,氧化铁皮压入。
轧件表面覆盖的氧化铁皮未去除干净,经过轧制后被压入其中。
其二,轧辊的轧制量过大造成辊面老,轧制量过多是造成热轧带钢麻面的重要原因。
其三,轧辊的冷却方法不正确或冷却能力不够,导致轧辊表面严重磨损。
(2)裂纹热轧带钢表面也容易出现裂纹,原因有:连铸坯浇筑过程未有效把握浇筑过程中的速度,影响钢凝固与冷却导致钢表面出现气孔、接痕等。
轧制时应力过于集中造成表面裂纹,比如划痕、划伤等。
钢中含有游离态氮元素,加速裂纹的拓展,甚至可能引起钢材断裂。
(3)压痕压痕是热轧带钢一常见质量问题。
一方面轧辊或者夹送辊的冷却不良造成表面明显凸起,机组运行时产品表面就会出现规律性压痕。
另一方面成品或前面道次轧辊表面掉块也会造成产品不同程度规律性压痕。
(4)划痕就划痕而言,其可能是接触了尖锐的棱角,钢带表面产生了一条或者多条划痕,具体原因有:轧线沉头螺丝冒出、过渡板或间隙处有废钢片残留、活套辊/自由辊转动不灵活或活套角度过大、三角区滚动体或卷取输送辊堵转等。
在卧式卷取系统中,输送轨道未正常运转,使得轧件堆叠等也会造成表面划伤,影响热轧带钢表面质量。
(5)氧化铁皮压入氧化铁皮可以被划分为一次氧化与二次氧化铁皮,其中一次氧化铁皮不规则分布于带钢之上,在炉内就已形成,一次氧化铁皮主要由四氧化三铁构成,该种物质为暗红色固体,被轧入钢材中很难彻底清除,导致钢带呈现翘皮等表面缺陷。
二次氧化铁皮发生于初次除鳞后,氧化铁皮的厚度与氧化时间和反应温度相关。
热轧板形的优化与控制

Ke y W o r d s: h o t c o nt i nu ou s r ol l i n g;pr o il f e s ha pe;op t i mi z a t i o n;c o nt r ol
Abs t r a c t :I t i s a na l y z e d t he p r o il f e s h a p e p r ob l em i n s t r i p s t e e l p r o du c t i o n i n 2# 1 4 5 0 ho t c o n t i nu o us r o l l i n g mi l l s e t ,t h e ma i n a f f e c t i ng f a c t or s f o un d ou t ,i mpr o vi n g m ea s u r e s p r op os e d.W i t h c o nt i n u o us op t i mi z a t i o n,
t h e a d j u s t i n g p r e c i s i o n o f mi l l i s g u a r a n t e e d , t h e r o l l i n g s t a b i l i z a t i o n i mp r o v e d , w a s t e p r o d u c t s c a u s e d b y a b —
1
引 言
形产 生影 响 。
2 . 1 生 产 中 出现 板 形 问题 的 主 要 原 因
2 . 1 . 1 板 形 调 整
热轧带钢塔形产生原因及预防

热轧带钢塔形产生原因及预防刘小军;顾晓琳【摘要】文章阐述了热轧带钢塔形产生的原因,并有针对性的采取了相应措施.卷取塔形问题得到了很大的改善.【期刊名称】《新疆钢铁》【年(卷),期】2010(000)004【总页数】3页(P36-38)【关键词】热轧带钢;塔形;侧导板【作者】刘小军;顾晓琳【作者单位】新疆八一钢铁股份有限公司;新疆八一钢铁股份有限公司【正文语种】中文【中图分类】TG335.11八钢公司1750mm热轧年设计能力300万t,2006年7月投产。
在生产过程中钢卷时有塔形现象发生,严重影响了带钢的质量和成材率,并且对钢卷打捆、步进梁运输以及装车也有很大影响。
为此,针对热轧带钢塔形问题进行分析,探索解决的措施。
八钢1750mm热轧生产线上有2台三助卷辊全液压地下卷取机,带钢头部接近卷取机时,通过卷取机前的液压侧导板完成对带钢头部的引导和对中,保证带钢沿着轧制中心线的位置进入夹送辊,然后在上下导板的引导下进入设定的助卷辊与卷筒形成的辊缝中完成带钢的卷取。
卷取过程中出现的塔形主要有头部塔形、尾部塔形和层间塔形3类。
(1)夹送辊下辊不水平。
安装初期测试下辊水平度满足要求(±0.2mm/全长),但是随着轧制时间的延长,磨损量的不均,可能造成下辊水平度发生变化,因而在卷取过程中极易形成塔形。
图1为下夹送辊水平度的测量示意图。
当轧制薄规格时,轧烂的尾部会对夹送辊辊面造成损伤;卷取堆钢处理冷态钢时,也会对夹送辊辊面造成损伤。
当辊面损伤时,为了不影响带钢的表面质量,操作人员会手动打磨,这样会加重夹送辊的磨损和不水平的程度。
减少尾部轧烂和制定合理的处理卷取堆钢的措施是保证下夹送辊水平度的有效方法。
(2)卷筒与助卷辊之间的轴线不平行,带钢在通过之间的辊缝时,除了承受压在带钢上的径向力之外,还存在切向力,在切向力作用下带钢发生横向移动进而形成塔形[1]。
为了减少由于卷筒与助卷辊之间的轴线不平行而产生塔形的几率,每次更换玩卷筒或助卷辊都要测量其平行度,将其稳定在允许的误差范围内(±0.3mm)。
热轧带钢生产中的板形控制范本(2篇)

热轧带钢生产中的板形控制范本热轧带钢的生产中,板形控制是一个非常重要的环节,它直接影响到带钢的质量和使用性能。
为了达到良好的板形控制效果,需要在整个热轧生产过程中采取一系列的措施。
以下是一些常见的板形控制范本,供参考。
1. 选择合适的轧辊形状和尺寸轧辊是热轧带钢生产过程中最重要的工具,轧辊的形状和尺寸对板形控制有很大的影响。
在选择轧辊时,需要考虑带钢的规格、材质和工艺要求等因素,选择合适的轧辊形状和尺寸,以确保板形控制的有效性。
2. 控制轧辊的径向力和侧向力轧辊的径向力和侧向力是影响板形的重要因素。
过大的径向力和侧向力会导致带钢的板形不均匀,甚至产生波浪形板形。
在轧制过程中,要控制好轧辊的径向力和侧向力,使其保持在合适的范围内,以获得良好的板形效果。
3. 控制轧制温度和冷却方式轧制温度和冷却方式对板形控制有很大的影响。
合理的轧制温度可以减少板形变形的趋势,而适当的冷却方式可以帮助稳定板形。
在生产过程中,要控制好轧制温度和冷却方式,以达到最佳的板形控制效果。
4. 使用适当的辊系排列方式辊系排列方式指的是轧机中辊系的布置方式。
不同的辊系排列方式会对板形控制产生不同的影响。
在选择辊系排列方式时,要考虑带钢的规格和工艺要求,选择合适的排列方式,以保证板形控制的效果。
5. 控制轧制压力和过程参数轧制压力和过程参数是影响板形的重要因素。
较大的轧制压力和不合适的过程参数会导致板形的不稳定性和变形。
在热轧带钢生产过程中,要控制好轧制压力和过程参数,使其处于合适的范围内,以获得良好的板形控制效果。
综上所述,热轧带钢生产中的板形控制是一个复杂的过程,需要在整个生产过程中采取一系列的措施。
通过选择合适的轧辊形状和尺寸、控制轧辊的径向力和侧向力、控制轧制温度和冷却方式、使用适当的辊系排列方式以及控制轧制压力和过程参数等手段,可以有效地控制板形,提高热轧带钢的质量和使用性能。
热轧带钢生产中的板形控制范本(二)一、引言热轧带钢作为重要的金属材料之一,在工业生产中具有广泛的应用。
热轧钢带卷取塔形控制方法的研究
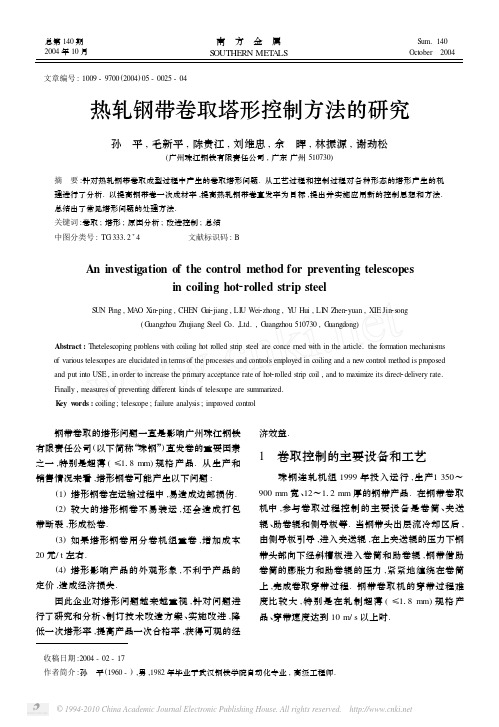
图 2. 这时夹送辊的控制由位置控制转换为压力控
制. 两边均衡的压力控制能有效的防止钢带凸度引
起的带头跑偏.
© 1994-2010 China Academic Journal Electronic Publishing House. All rights reserved.
卷取带载过程控制不好有两种可能性 :超前或 滞后.
(1) 带载超前 :钢带未进入卷筒 ,提前膨胀 ,会 造成带头无法夹紧 ,内圈松动 ,侧导板动作太早会引 起穿带失败事故.
(2) 带载滞后 ,钢带已进入卷筒 ,膨胀不及时 , 带头没有形成有效的压力 ,带头移动引起滑动头塔 形 ,侧导板工作太晚产生较大的塔形. 31114 侧导板纠偏控制功能的优化
图 3 侧导板控制特性优化
(1) 侧导板的控制特性优化. Y 轴的 X = 0 点 就是卷取带载信号 ,调整特性曲线后见图 3 ,可提前 的时间是 t1. 但不能过大 ,过大就可能引起位置超 调 ,超调对卷取有一定的影响 ,是引起卷取堆钢的因 素之一.
(2) 侧导板纠偏提前. 将侧导板的纠偏提前到 钢带进入夹送辊后就进行控制 ,这就对侧导板的控 制提出了要求. 在改变工作特性曲线的基础上 ,相 当于移动了特性曲线可提前的时间 t2 ,见图 4. 这个 时间是速度的比例函数 ,保证对不同厚度的钢带都 有效.
总第 140 期 2004 年 10 月
南 方 金 属 SOUTHERN METALS
Sum.
October
140 2004
文章编号 : 1009 - 9700 (2004) 05 - 0025 - 04
热轧钢带卷取塔形控制方法的研究
这种塔形多半是松卷引起的 , 可参照文献[1] . 另一类是由于侧导板的压力不够 ,卷取的张力超过 了侧导板的压力 ,控制由位置控制变成了压力控制 , 通过调整侧导板的 RFG值 ,两侧导板形成差开 RFG
带钢外观质量缺陷

带钢外观质量缺陷及预防措施一、热轧板材外观质量的主要问题根据热轧板带材的发展形势,板带的外观“美”已成为市场竞争的重要指标。
然而由于钢铁产品生产的特殊性,钢铁企业板带产品的外观质量问题比较普遍,主要包括:卷形不良、氧化铁皮卷、结疤、折边、辊印、划伤、边裂、浪形、规格偏差、其他等。
1、卷形不良(1)塔形卷塔形卷是一种带钢边部卷绕不平齐,一处或多处呈螺旋状出边的不良卷形。
主要分为头塔和尾塔两种。
头塔是由于带钢头部偏离轧制中心线或2—3圈后从轧制中心线偏离导致的。
尾塔是由于带钢尾部偏离轧制中心线或2—3圈后从轧制中心线偏离导致的。
(2)塔形卷形成原因①带钢自身原因来料镰刀弯、楔形、异常凸度以及波浪、气泡、头部温度低,材质硬度大等都容易产生头部塔形。
对策是要求精轧调整压下水平,卷取操作方面应尽早打开助卷辊。
②操作上的原因导板夹力过大,带钢弓起,运行不平稳,以及带钢中心偏离导板中心进入卷取机。
对策是采用适当的夹紧力、夹紧方法,以及适当的导板开口度。
③设备上的原因侧导板的部分松动以及动作不一致,夹紧力不足、侧导板偏心、下夹送辊不水平、夹送辊左右辊缝不平衡。
由于带钢尾部从精轧抛出时,带钢张力比正常状态低,因此,平时因为高张力而未能表现出来的使带钢横向移动的力就变得明显,使带钢横向移动后卷取,有时可以通过改变减速点来达到控制尾部张力。
(3)松卷松卷是指钢卷没有卷紧,处于松散状况的缺陷卷。
对策是根据带钢的厚度、宽度、材质、卷取温度、卷取速度设定合适的张力。
2、氧化铁皮卷(麻点、粘结、黑线)氧化铁皮是影响热轧带钢表面质量的重要因素之一,氧化铁皮压入的板材酸洗后,会严重影响后道工序冷轧板的表面质量,造成产品质量下降。
(1)一次氧化铁皮钢坯表面与高温炉气生成的氧化铁皮称为一次氧化铁皮,一次氧化铁皮压入缺陷呈小斑点、大块斑痕和带状条纹形式不规则地分布在带钢上,常伴有粗糙的麻点状表面。
一次氧化铁皮压入产生的原因有以下几个方面:①加热方面的原因:加热温度高,加热时间长;炉内气氛不好,供入风量过大;炉内形成负压,吸入冷风;炉内加热温度低于规程规定的最低温度过多。
- 1、下载文档前请自行甄别文档内容的完整性,平台不提供额外的编辑、内容补充、找答案等附加服务。
- 2、"仅部分预览"的文档,不可在线预览部分如存在完整性等问题,可反馈申请退款(可完整预览的文档不适用该条件!)。
- 3、如文档侵犯您的权益,请联系客服反馈,我们会尽快为您处理(人工客服工作时间:9:00-18:30)。
热轧薄规格带钢塔形产生原因及控制措施
摘要:针对唐钢热轧薄规格带钢卷取过程中易产生塔形的问题,从卷取区域设备和工艺控制对各种塔形形成原因进行分析,采取相应控制措施,减少带钢塔形,改善钢卷外观质量。
关键词:热轧带钢卷取机塔形侧导板
0 前言
唐钢1810线为薄板坯连铸连轧生产线,最初整条生产线设计能力为年产300万吨,于2004年7月份投产,其生产线工艺布置图见图1。
随着设备日益磨损和薄规格带钢所占比例不断增加,生产出来的钢卷塔形现象越来越严重,特别是厚度规格≤2.0mm带钢塔形问题更为突出,不仅影响板卷实物质量和成材率,而且严重影响公司利益和形象。
1、钢卷塔形形成的原因
影响钢卷塔形形成的直接因素和间接因素很多,主要包括设备原因和工艺控制原因两个方面。
1.1塔形缺陷的种类
塔形主要有头部塔形、层间塔形和尾部塔形几大类,同时也有部分是混合塔形。
1.1.1头部塔形
头部塔形主要是由于带钢进入卷取机时头部已经偏离中心线,经过卷取侧导板强制性纠偏后,带钢重新回到轧制中心线,形成头部塔形。
1.1.2层间塔形
层间塔形主要是由于末架精轧机与卷取之间建立的张力不稳定,造成带钢在辊道上左右摆动。
1.1.3尾部塔形
尾部塔形主要是由于在轧制过程中钢带跑偏严重,侧导板强制纠偏,形成弧形路径,在轧制过程中钢带未回到中心线上,末架精轧机抛钢张力消失后,带钢在辊道上左右摆动。
1.2设备原因
1.2.1夹送辊上下辊之间不水平
夹送辊上下辊之间不水平分为两种情况。
第一,安装新夹送辊时,由于上下辊之间轴线不平行,造成在卷钢过程中容易形成塔形。
第二,使用一段时间后,沿辊身长度方向磨损不均匀,造成上下辊面不水平,在卷钢过程中极易形成塔形。
1.2.2芯轴与助卷辊之间不水平
当带钢头部进入卷取机时,头部几圈在助卷辊压力下紧紧缠绕在芯轴上,如果助卷辊与芯轴之间不水平,带钢受到助卷辊压力不一致,造成带钢头部发生横向移动形成塔形[1]。
1.2.3侧导板控制异常
侧导板运行速度过快或者运行速度过慢,均会导致带钢对中难以控制,容易出现塔形。
在轧制薄规格带钢时,由于穿带速度快,头部塔形较为严重。
1.2.4助卷辊压力异常
助卷辊实际压力是由助卷臂液压缸活塞两侧的压力传感器测量的。
当压力传感器反映迟钝或者位置传感器误差大时,助卷辊压力异常,在卸卷外抽时头部松卷产生塔形。
1.2.5热金属探测器检测不准确
当带钢头部经过hmd时,系统向侧导板发出动作指令。
如果hmd
信号检测不准确,系统发出的指令相对滞后,现场侧导板实际动作也相对滞后。
这对于高速穿带薄规格带钢来说,头部一段距离侧导板没有起到纠偏作用,容易出现头部塔形[2]。
1.2.6芯轴涨缩精度不准确
由于芯轴参与带钢全程卷取磨损重而且更换周期长,造成芯轴设备精度要求不能得到保证,在卸卷外抽时头部松卷产生塔形[3]。
1.3工艺控制原因
1.3.1板坯存在楔形、镰刀弯和头尾形状不好
由于板坯来料本身原因,在轧制过程中控制较困难,容易形成塔形。
1.3.2带钢偏离轧制中心线
末架精轧机两侧轧制力不平衡,压下量不相同带钢厚度也不相同,造成跑偏严重,侧导板强制纠偏后带钢不能完全回到中心线,形成塔形。
1.3.3张力波动影响
末架精轧机抛钢之前,主要由芯轴与末架精轧机之间建立张力。
而末架精轧机抛钢之后,芯轴与末架精轧机之间张力消失,芯轴与
夹送辊之间建立起新的张力,如果张力波动大,带钢在辊道上左右摆动,尾部出现塔形。
1.3.4夹送辊压力影响
夹送辊压力值有一个压力基准值由系统自动控制,当带钢头部经过夹送辊时,在特定的时间内夹送辊压力值未能达到设定压力值,造成夹送辊不能很好地控制带钢头部,形成头部塔形;当夹送辊控制方式由位置控制转为压力控制时,如果夹送辊两侧压力偏差超出允许范围,带钢会向一侧跑偏,造成尾部几圈形成塔形。
2、控制塔形措施
2.1减少板坯镰刀弯、控制板坯头尾形状
对结晶器下口进行精确测量、精确定位,加强对扇型段的维护,保证设备处于良好运行状态,从而保证了板坯的平直度。
调整摆剪间隙对控制板坯头尾形状也起到一定作用。
2.2卷取区域设备定期维护
加强卷取侧导板、卷取夹送辊、卷取机内部各个零件设备定期点检、测量、维护。
例如,发现卷取侧导板磨损严重时及时进行补焊或者更换;卷取夹送辊和助卷辊制定合理的更换周期;其它设备零件进行定期润滑;更换新夹送辊和助卷辊后进行精度调节;建立卷取区域全部设备精度数据档案,发现问题及时解决。
2.3侧导板动作时序优化
侧导板主要起到对中和导向作用,要求其具备一定夹紧力、稳定性和快速性。
如果侧导板开闭速度过快,带钢边部很容易被夹住,
生产稳定性不能得到保证;如果侧导板开闭速度过慢,带钢头部没有被及时夹紧,头部容易出现塔形。
针对以上情况,可以通过修改侧导板短行程行时间来控制头部塔形。
侧导板短行程时序为sg前hmd on+延时,控制器根据机架速度和距离(l1、l2)计算出短行程开始时间,见图2。
2.4带钢头部跟踪信号进行优化
建立带钢头部位置与轧机速度之间的函数。
当检测到带钢头部时,系统开始计算位于夹送辊前的带钢头部位置值,向侧导板发出动作指令。
由于轧机速度受制于很多因素影响,带钢头部位置计算会存在误差,因此需要对参数进行不断修改、摸索,使带钢头部跟踪信号检测准确。
2.5夹送辊压力控制优化
根据不同厚度带钢,通过对比实际监控压力值与设定压力值,将夹送辊设定压力值进行修改,使转换准时、正确,有效地控制头部塔形;由于系统不能控制两侧压力,可通过调整夹送辊水平来消除两侧压力偏差,有效地控制尾部塔形。
3、结束语
在结合生产实际的基础上,通过分析带钢塔形产生原因,采取相应控制措施,较好地解决了薄规格带卷塔形缺陷,卷形质量得到明显改善。
参考文献:
[1]侯俊山.钢板卷取机钢卷塔形的原因分析及其对策[j].山西机
械,2000,(12):56-57.
[2]于千.热轧带钢卷取塔形产生原因及防范措施[j].轧钢,2007,(3):59-60.
[3]胡平.攀钢1450mm热轧板塔形的控制[j].新疆钢铁,2003,(2):33-35.
[4]林良怀,谢劲松.减少轧制薄规格的钢卷塔形改善热轧板卷外观[j].冶金丛刊,2004,(6):21-22.
作者简介:董跃星(1984-),男,助理工程师,2007年毕业于黑龙江工程学院金属材料专业,现在河北钢铁股份有限公司唐山分公司第一钢轧厂从事轧钢技术工作。