成型零件尺寸计算及型腔壁厚计算
第6章 注塑模具结构及设计(4)-成型零件设计

一、分型面的形式
二、分型面的选择 选择分型面的原则是: 1、分型面应选择在塑件外形最大轮廓处 当初步确定塑件的分型方向后,分型面应选在塑件外形最大 轮廓处,即通过该方向上塑件的截面积最大,否则塑件无法从 型腔中脱出。 2、应尽量减少塑件(型腔)在分型面上的投影面积 注塑机都规定其相应模具所允许的最大成型面积以及额定锁 模力,注射成型过程中,当塑件(包括浇注系统)在分型面上 的投影面积超过允许的最大成型面积时,将会出现涨模溢料现 象,这时注射成型所需的合模力也会超过额定锁模力。因此, 选择分型面时,应考虑对成型面积的影响。(教材P67图4-34)
6、3、2 结构设计 成型零件主要包括型腔、型芯、镶拼件、各种成型杆与成 型环。
塑件生产对成型零件的要求: 足够的强度、刚度、硬度(HRC30以上)、耐磨性; 足够的精度和适当的表面粗糙度(一般Ra<0.4μm);
一定的耐热疲劳性和耐腐蚀性,生产腐蚀性塑料还要特 别防护(选耐蚀材料或电镀硬铬)。
7、无损塑件外观 图示塑件,底部带有环形支撑面,若分型面 按图(a)中方案设计,会在环形支撑面处留下毛 边痕迹。如果改为图(b)中方案、毛边产生在塑 件端面,去除后对塑件外观无损。
8、对侧向抽芯的影响 一般注塑模的侧向抽芯,都是借助模具打开时的开模运 动。通过模具的抽芯机构进行抽芯,在有限的开模行程内, 完成的抽芯距离有限制。因此,对于带有互相垂直的两个 方向都有孔或凹槽的塑件,应避免长距离抽芯。
2、镶拼型芯结构 为便于加工,形状复杂的型芯可采用镶拼组合式结构, 如图所示。
采用组合式行行行可大大改善加工和热处理的工艺性。 但设计和制造这类型芯时,必须注意结构的合理性,应 保证型芯和小型芯镶块的强度、防止热处理变形,应避 免尖角与薄壁。
塑料成型成型零件尺寸的计算
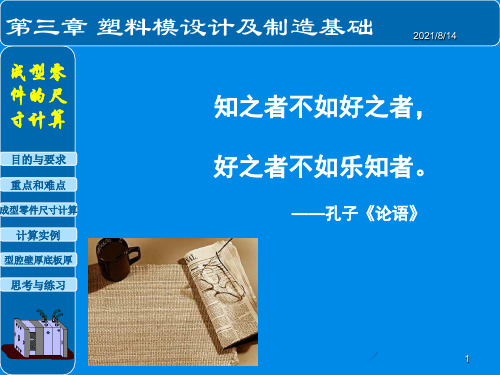
5
第三章 塑料模设计及制造基础 2021/8/14
成型零 件的尺 寸计算
目的与要求 重点和难点
成型零件尺寸计算
计算实例
型腔壁厚底板厚
思考与练习
磨损量的取值原则:
磨损量的大小取决于塑料品种、模具材料及热处理。
小批量生产时,c取小值,甚至可以不考虑。 玻璃纤维等增强塑料对成形零件磨损大,c应取大值。 模具材料耐磨,表面强化好,c应取小值。 垂直于脱模方向的模具表面不考虑磨损。 平行于脱模方向的模具表面要考虑磨损。 小型塑件的模具磨损对塑件影响较大。
目的与要求 重点和难点
成型零件尺寸计算
计算实例
型腔壁厚底板厚
思考与练习
hM 2 z(hs 2)(hs 2)S cp
整理得: hM(hshsScp3 2)0 -z
标注制造公差后得:
h0
M z
(hshs Scp
2 3)-0z
17
第三章 塑料模设计及制造基础 2021/8/14
成型零 件的尺 寸计算
目的与要求 重点和难点
d2M=[3.5+3.5×0.008+0.75×0.16]-0.053 =3.65-0.053 ⑶ 扩孔直径:d3=6.5+0.2 计算得z=0.067
d3M=[6.5+6.5×0.008+0.75×0.20]-0.067 =6.7-0.067 ⑷ 内孔深度:h1=19+0.28 计算得z=0.093
标注公差后得:lM-0z (lslsScp 3 4)-0z 13
第三章 塑料模设计及制造基础 2021/8/14
成型零 件的尺 寸计算
※式中Δ前的系数x可取在1/2~3/4之间; ※有脱模斜度时型芯径向尺寸确定
757 塑料套筒注射模设计
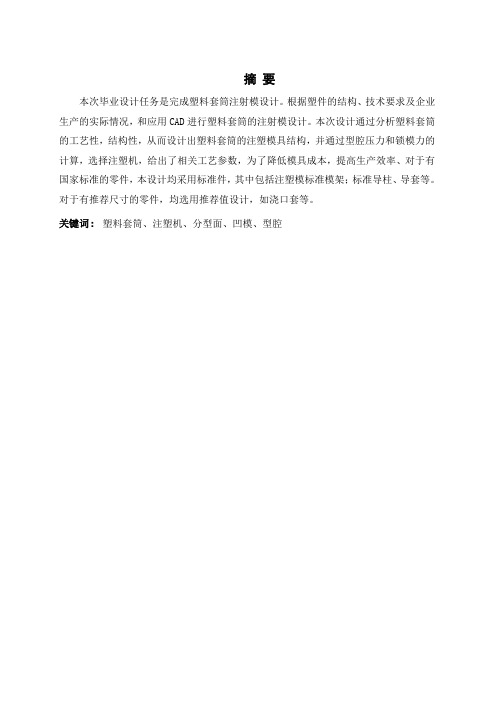
2
4.1 型腔布置 ............................................................. 14 4.2 成型零件的结构确定 ................................................... 15 4.2.1 凹模设计 ........................................................... 15 4.2.2 凸模设计 ........................................................... 15 4.3 导向定位机构的设计 ................................................... 15 4.4 推出机构设计 ......................................................... 15 5 主要零部件的设计计算 ................................................... 16 5.1 成型零件尺寸计算 ..................................................... 16 5.1.1 型腔计算 ........................................................... 16 5.1.2 型芯计算 ........................................................... 16 5.1.2 型芯计算 ........................................................... 18 5.2 模具型腔壁厚的确定 ................................................... 18 6 标准模架的选择......................................................... 18 6.1 模板的周界尺寸的确定 ................................................. 18 6.2 A 板厚度的确定 ....................................................... 19 6.3 B 板厚度的确定 ....................................................... 19 6.4 C 板厚度的确定 ....................................................... 19 6.5 标准模架的选择....................................................... 19 7 导柱和导套的加工....................................................... 19 7.1 导柱的加工 ........................................................... 19 7.1.1 用两顶尖孔定位装夹 ................................................. 20 7.1.2 用外圆柱表面定位装夹 ............................................... 20 7.1.3 外圆与顶尖相结合的定位装夹 ......................................... 20 7.1.4 影响导柱车削加工质量的因素 ......................................... 20 7.2 导套的加工 ........................................................... 21 8 模具总装图 ............................................................. 21 8.1 模具总装图........................................................ 21 8.2 模具的安装试模....................................................... 23 结束语 ................................................................... 25
经验尺寸和公式总汇
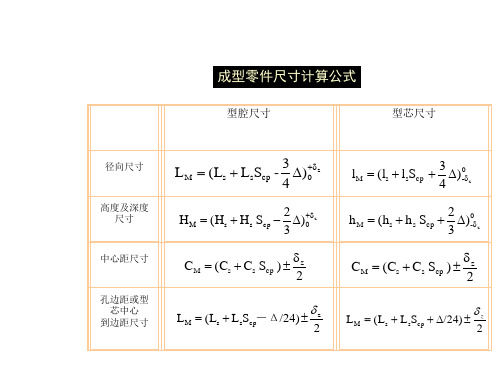
矩形凹模内 侧短边长
b
整体凹模
镶拼式凹模
壁厚 S
凹模壁厚 模套壁厚
S1
S2
~40
25
9
22
>40 ~ 50 25 ~ 30 9 ~ 10 22 ~ 25
>50 ~ 60 30 ~ 35 10 ~ 11 25 ~ 28
>60 ~ 70 35 ~ 42 11 ~ 12 28 ~ 35
五、分流道设计与制造
3.分流道的尺寸设计
流道的直径过大:不仅浪费材料, 而且冷却时间增长, 成 型周期也随之增长, 造成成本上的浪费。
流道的直径过小:材料的流动阻力大, 易造成充填不足, 或者必须增加射出压力才能充填。
因此流道直径应适合产品的重量或投影面积。
流道直径(mm) 4 6 8 10 12
产品重量(g) 95 375
375以上 大型
流道直径(mm) 4 6 8 10 12
投影面积(cm2) 10以下 200 500 1200 大型
§4.3普通浇注系统的设计
五、分流道设计与制造
2.分流道的尺寸设计
流道长度宜短, 因为长的流道不但会造成压力损失,不利 于生产性,同時也浪费材料;但过短, 产品的残余应力增大, 并且容易产生毛边。
流道长度可以按如下经验公式计算:
D=
D——分流道直徑mm W——产品质量g L——流道長度mm
支承板厚度 H
15 15 ~ 20 20 ~ 25 25 ~ 30 30 ~ 40
>40
※当塑件的投影面积较大时,支承板会很厚,为减小厚度可加支柱。 加一个支柱:H′=H/2.7 加两个支柱:H″=H/4.3
※板厚值也可参考表3-22
成型零部件尺寸及力学计算
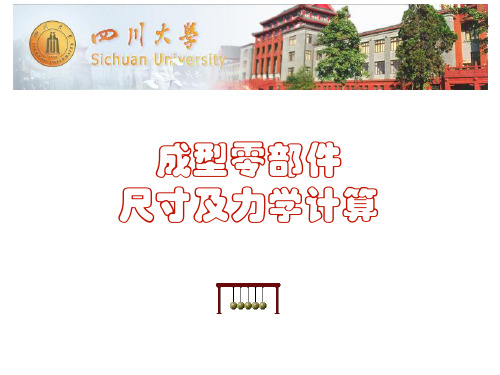
塑料成型模具成型零部件尺寸及力学计算塑料成型模具重点、难点•重点:•收缩的定义和重要性•计算型腔尺寸的方法•理解按极限尺寸计算和按平均收缩率计算的差别•模具常用的修模方法•难点:•按极限尺寸计算型腔尺寸的方法塑料成型模具塑料制品精度塑料原料收缩δS估算收缩率不准确δSS 模具零件制造误差δm 模具零件磨损δw 配合与安装误差δq影响因素制品公差Δ≥δS +δSS +δm +δw +δq因此,塑料制品的精度往往较低,应尽量选用低精度。
否则制品精度的提高会使模具的制造费用成指数幂增加。
制品公差标准GB/T14486-1993塑料成型模具成型零件制造误差在0~500mm 内。
、、、、,、IT 、IT 、IT 、IT IT a i m m D 。
D D a i a m m 160100644025 12111098,:: ,::)001.045.0(3其值分别对应常用精度系数公差单位型腔零件尺寸型腔零件制造公差δδ+=⋅=组合式型腔的制造公差要用尺寸链来决定制造误差约与成正比。
当制品尺寸较小时,型腔零件的制造误差约占制品公差的三分之一。
3D塑料成型模具塑料原料收缩理论收缩指的是在高温高压下注射入模腔中的塑料所成型出来的制品比模腔尺寸要小的现象。
常以mm/mm 或%来表示每种塑料的收缩或膨胀或压缩率可能不同原则1:塑料的压力、体积和温度之间有一种联系。
影响压力、温度和时间的因素都将影响收缩。
原则2:塑料受热时会膨胀,当冷却到原来的温度时又会收缩到原来的体积。
原则3:塑料受压时其体积会缩小,当压力恢复时又会膨胀到原来的体积。
塑料成型模具塑料制品收缩过程刚开始注塑时,压力小,但与模腔壁接触的塑料凝固后马上收缩模腔充满后,压力升高,塑料被压缩,但可补料以补偿收缩保持压力直到浇口冻结和阀式浇口关闭,补料停止继续收缩,压力持续下降,直至顶出,收缩还将继续重要因素:注射压力和浇口封闭时间塑料成型模具塑料原料收缩率影响收缩率的因素有:从理论上计算收缩率是不大可能的左边大部分是模具设计者或制造者控制不了的导致收缩率的波动•材料规格•加入回收塑料•加入填充剂•顶出时制品的温度•注射压力及保压压力•制品壁厚和流动阻力•制品形状•模具设计多数塑料在顶出后几小时会达到总收缩量的90%,其余的10%在10天内完成,少数塑料要几个月时间在高于室温下退火,可加速松驰,终止收缩,但吸湿塑料还会有尺寸变化m mL m m L 。
注射模具成型零件的设计.pptx
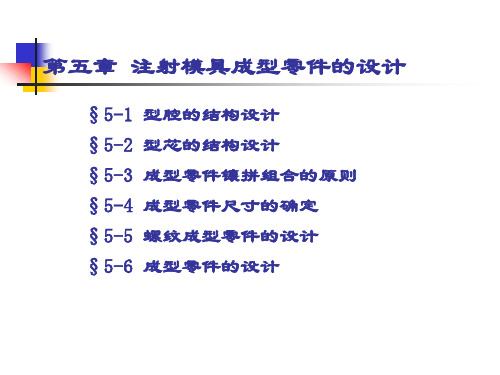
第四节 成型零件尺寸的确定
一、影响塑件尺寸的因素 成型收缩率的选择和成型收缩的波动引起的尺寸误差 成型零件的制造误差、组装误差及相对移动引起的误差; 成型零件脱模斜度引起的误差 成型零件磨损及化学腐蚀引起的误差 二、确定成型零件尺寸的原则
1.综合考虑以下因素,确定合适的塑料收缩率 塑件壁厚、形状及嵌件:壁厚较大、形状较复杂或有时嵌件取偏小值 熔料流向:与进料方向平行的尺寸取偏小值 浇口截面积:浇口截面积小的比大的收缩率大,应取偏大值 与浇口的距离:近的部位比远的部位收缩率小,应选较小值 型腔尺寸取小于平均收缩率的值,型芯尺寸取大于平均收缩率的值 2.据成型零件的性质决定各部分成型尺寸:图5-17 3.脱模斜度的取向:型腔尺寸以大端为准,脱模斜度向缩小方向取得;型
第二节 型芯的结构设计
型芯又叫凸模,是构成塑件内部几何形状的零件。包括主体型芯、小型芯、侧 抽芯和成型杆及螺纹型芯等
一、型芯的结构形式 完全整体式图5-11 主体型芯与动模板做成一体。结构简单,强度、刚度较
好;费工费材,不易修复和更换,只用于形状简单的单型腔或强度、刚度要 求很高的注射模 整体嵌入式图5-12 将主体型芯镶嵌在模板上并固定 局部组合式图5-13、图5-14 塑件局部有不同形状的孔或沟槽不易加工时, 在主体型芯上局部镶嵌与之对应的形状,以简化加工工艺,便于制造和维修 完全组合式图5-15由多块分解的小型芯镶拼组合而成,用于形状规则又难于 整体加工的塑件 二、小型芯的固定形式 图5-16
Δ
2.型芯尺寸
d——型芯径向最大基本寸 d0—塑件径向最小基本尺寸
h —— 型芯高度最大尺寸 h0—塑件内形深度最小尺寸
3.中心距尺寸
保证同心度和尺寸精度,且便于热处理 局部组合式图5-3 型腔由整块材料制成,局部镶有成型嵌件。用于型腔较深、
注射模具成型零件的设计

第四节 成型零件尺寸的确定
一、影响塑件尺寸的因素 成型收缩率的选择和成型收缩的波动引起的尺寸误差 成型零件的制造误差、组装误差及相对移动引起的误差; 成型零件脱模斜度引起的误差 成型零件磨损及化学腐蚀引起的误差 二、确定成型零件尺寸的原则
1.综合考虑以下因素,确定合适的塑料收缩率 塑件壁厚、形状及嵌件:壁厚较大、形状较复杂或有时嵌件取偏小值 熔料流向:与进料方向平行的尺寸取偏小值 浇口截面积:浇口截面积小的比大的收缩率大,应取偏大值 与浇口的距离:近的部位比远的部位收缩率小,应选较小值 型腔尺寸取小于平均收缩率的值,型芯尺寸取大于平均收缩率的值 2.据成型零件的性质决定各部分成型尺寸:图5-17 3.脱模斜度的取向:型腔尺寸以大端为准,脱模斜度向缩小方向取得;型
二、型腔壁厚和底板厚度的计算
1.注射过程中型腔所受的力
合模时的压应力;注射压力;保压压力;开模时的拉应力
2. 型腔壁厚和底板厚度计算的必要性:图5-7.8.9.10
型腔刚度不足时会产生弹性变形,型腔向外膨胀,影响塑件质量和尺寸 精度,并产生溢料、飞边
型腔强度不足时会产生塑型变形,可引起型腔永久变形甚至破裂
S刚
22.8 57 98.7 131 145 195 249
S强
35 71 106 131 141 177 212
结论
当圆形型腔内半径r=86mm和矩形型腔的长边L1=370mm时,按刚度和 强度分别算得的侧壁厚度相等。故取r=86mm和L1=370mm为临界值, 当小于该值时按强度计算,大于该值时按刚度计算
塑件螺纹为M20x2-6H/5g,6g,塑料收缩率为0.6%,计算螺纹型环和型芯的各部
分尺寸。
五、小直径螺纹型芯安装形式图5-24
孔边距计算
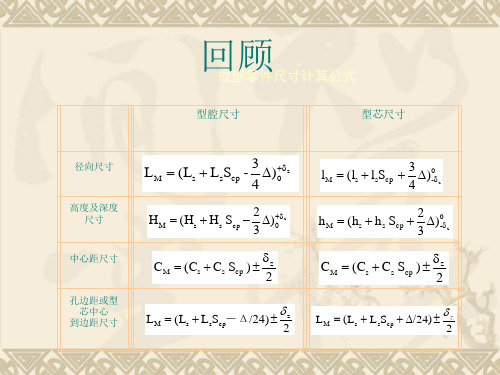
当塑件的投影面积较大时,支承板会很 厚,为减小厚度可加支柱。 加一个支:H′=H/2.7 加两个支柱:H″=H/4.3
项目训练
根据壳体塑件的尺寸和型腔布置方案完 成下列设计计算 1、确定凹模镶件尺寸和模套的壁厚 确定支承板的厚度 2、确定支承板的厚度 确定壳体塑件模具的标准模架 3、确定壳体塑件模具的标准模架
高度及深度 尺寸
中心距尺寸
C M = (Cs + Cs Scp ) ±
δz 2
δz
2
C M = (Cs + Cs Scp ) ±
δz 2
δz
2
孔边距或型 芯中心 到边距尺寸
L M = (Ls + L sScp-Δ/24) ±
L M = (L s + L sScp + ∆/24) ±
主要内容
一、凹模上的孔边距计算 二、型芯上的孔边距计算 三、型腔壁厚与底板厚度的确定
表中壁厚是边长比L/b=1.8时的参考尺寸,当L/b>1.8时壁厚应适当增大。
3.支承板厚度的计算
塑件在分型面上的投影面积 A(cm A(cm2) 支承板厚度 H
~5 >5 ~ 10 >10 ~ 50 >50 ~ 100 >100 ~ 200 >200
15 15 ~ 20 20 ~ 25 25 ~ 30 30 ~ 40 >40
1).模塑过程中模具承受的力 ) 设备施加的锁模力 熔融塑料作用于型腔内壁的压 力 2).型腔受内压力作用发生膨 2) . 胀变形 影响塑件的尺寸精度 配合面处产生溢料飞边 小型腔的许用变形量小,压力 作用会导致其破坏
大型腔以刚度为主计算, 大型腔以刚度为主计算,小型腔以强度为主计算 圆形凹模直径: ﹤ ~ 圆形凹模直径:D﹤67~86mm时以强度计算为主 时以强度计算为主 矩形凹模长边: ﹤ 矩形凹模长边:L﹤108~136mm时以强度计算为主 ~ 时以强度计算为主
《塑料注塑模结构设计》7成型零部件设计7
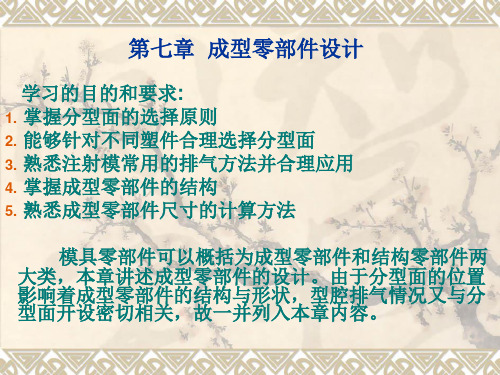
5 瓣合式凹模(镶拼式凹模) 镶拼式凹模)
组成凹模的每一个镶块都是活动的, 组成凹模的每一个镶块都是活动的,它们被模套或其他锁合装置 箍合在一起 适用: 适用:有侧凹或侧孔的制品 当瓣合模块数量等于2时 可将他们组成的凹模成为哈夫凹模。 当瓣合模块数量等于 时,可将他们组成的凹模成为哈夫凹模。
瓣合式凹模结构示意图
二 设计要点
排气槽(或孔 位置和大小的选定 主要依靠经验, 排气槽 或孔)位置和大小的选定,主要依靠经验,经过试模 或孔 位置和大小的选定, 后再修改或增加。 后再修改或增加。 基本的设计要点可归纳如下: 基本的设计要点可归纳如下: 1.排气要保证迅速、完全,排气速度要与充模速度相适应; .排气要保证迅速、完全,排气速度要与充模速度相适应; 2.排气槽(孔)尽量设在塑件较厚的成型部位 2.排气槽(孔)尽量设在塑件较厚的成型部位; 尽量设在塑件较厚的成型部位; 3.排气槽应尽量设在分型面上,但排气槽溢料产生的毛边应不 .排气槽应尽量设在分型面上, 妨碍塑件脱模; 妨碍塑件脱模; 4.排气槽应尽量设在料流的终点,如流道、冷料井的尽端; .排气槽应尽量设在料流的终点,如流道、冷料井的尽端; 5.为了模具制造和清模的方便,排气槽应尽量设在凹模的一面; .为了模具制造和清模的方便,排气槽应尽量设在凹模的一面; 6.排气槽排气方向不应朝向操作面,防止注射时漏料烫伤人; .排气槽排气方向不应朝向操作面,防止注射时漏料烫伤人; 7.排气槽 孔)不应有死角,防止积存冷料; 不应有死角, .排气槽(孔 不应有死角 防止积存冷料;
一 凹模结构设计
凹模是成型塑件外表面的成型零件。 凹模是成型塑件外表面的成型零件。 凹模的基本结构:整体式、整体嵌入式和组合式、镶拼式。 凹模的基本结构:整体式、整体嵌入式和组合式、镶拼式。
成型零件工作的尺寸计算实例

铝合金铸件铸造技术
B、深度尺寸有50,4,5±0.2,25±0.5等,计算结果如下:
50, 4, 5±0.2, 25±0.5
HM=49.87+0.1550 HM=3.81+0.0750 HM=4.95+0.10 HM=25+0.250
3)型芯尺寸计算 A、型芯径向尺寸有φ40+0.340, φ32+0.170, φ7等 B、型芯高度尺寸有10,37。
铝合金铸件铸造技术
根据:DM=(D+DK-0.7 △)+δ0得 对φ48 0-0.17尺寸,DM =(48+48×0.6%-0.7×0.17)0.17/50
= 48.17+0.0340(mm) 同理: φ85尺寸的DM =84.9 +0.2180(mm) 从模具结构图可以看出,该尺寸受滑块分型面的影响,故应 灾计算的基础上减少0.05mm,并适当提高模具的制造精度 DM=84.85+0.160(mm)。
材料:YL102 未注公差IT14,未注铸造圆角R2
支座压铸件成形零件尺寸计算图
铝合金铸件铸造技术
成形零件尺寸计算步骤: 1)确定压铸件的收缩率K
查表可以得到该压铸件的收缩条件为混合收缩,收缩率为 0.5%~0.7% ,取平均值K=0.6% 。 2)型腔尺寸计算 A、径向尺寸有φ85,
型腔壁厚和底版厚度

注射模具成型零部件设计
§2.3 成型零部件工作尺寸计算
二.壁厚旳受力分析 1.模塑过程中模具承受旳力 设备(注塑机)施加旳锁模力; 熔融塑料作用于型腔内壁旳压力。
2.型腔受内压力作用发生膨胀变形 影响塑件旳尺寸精度; 配合面处产生溢料飞边; 小型腔旳许用变形量小,压力作用会造 成其破坏。
当分界值不明确时按两种措施计算型腔壁厚值,取其大者。
注射模具成型零部件设计
§2.3 成型零部件工作尺寸计算
二.壁厚旳受力分析
(2) 刚度计算条件因为模具旳特殊性,应从下列三个方面来考虑:(型腔侧 壁旳最大允许变形量δ)
从中小型塑件旳尺寸精度考虑:δ≤Δ/5
部分尺寸要求较高旳精度,要求模具型腔应具有很好旳刚性,以确保塑料熔体 注入型腔时不产生过大旳弹性变形。此时,型腔旳充许变形量[] 由塑件尺寸和公 差值来拟定。
圆形凹模直径:D﹤67~86mm时以强度计算为主
矩形凹模长边:L﹤108~136mm时以强度计算为主.
当分界值不明确时按两种措施计算型腔壁厚值,取其大者。
注射模具成型零部件设计
§2.3 成型零部件工作尺寸计算 一、计算法
1.矩形侧壁和底板厚度旳计算法:圆形凹模壁厚
注射模具成型零部件设计
§2.3 成型零部件工作尺寸计算 一、计算法
§2.3 成型零部件工作尺寸计算 二、经验法
1.矩形凹模壁厚
矩形凹模 内侧短边长
b
整体凹模壁 厚 S
镶拼式凹模
凹模壁厚 模套壁厚
S1
S2
~40
25
9
22
>40 ~ 50 25 ~ 30 9 ~ 10 22 ~ 25
塑料模成型零部件强度和刚度是计算

第三节成型零部件的设计成型零部件的强度与刚度的计算一、模具强度及刚度概念从工程力学的角度上讲:构件刚度—是指构件抵抗变形的能力构件强度—是指某种材料抵抗破坏的能力,即材料破坏时所需要的应力。
模塑成型过程中,型腔受到塑料熔体的压力会产生一定的内应力及变形。
若型腔或底板壁厚不够,当内应力超过材料的许用应力时,型腔会因强度不够而破裂。
若型腔刚度不足也会发生过大的弹性变形,因此导致溢料、影响塑件尺寸和精度、脱模困难。
型腔刚度计算的依据可归纳为以下几个方面:(1)防止溢料(2)保证塑件精度(3)有利于脱模二、壁厚的受力分析1.模塑过程中模具承受的力设备施加的锁模力注射过程中塑料流动的注射压力浇口封闭前一瞬间的保压压力开模时的拉应力2.型腔受内压力作用发生膨胀变形影响塑件的尺寸精度配合面处产生溢料飞边小型腔的许用变形量小,压力作用会导致其破坏3.型腔壁厚的最大允许变形量δ从中小型塑件的尺寸精度考虑:δ≤Δ/5从不产生溢料飞边考虑:δ﹤塑料的溢料值(表5-3)保证塑件的顺利脱模:δ≤S·t(收缩量腔力学计算的特征和性质:大型腔以刚度为主计算,小型腔以强度为主计算圆形凹模直径:D﹤67~86mm时以强度计算为主矩形凹模长边:L﹤108~136mm时以强度计算为主4.型腔壁厚和底板壁厚的校核型腔要承受塑料融体的高压作用若壁厚不够可表现为:刚度不够——产生过大的弹性变形。
强度不够——型腔发生塑性变形、破裂型腔壁厚计算以最大压力为准大型模具以刚度计算为主小型模具以强度计算为主刚度与强度的校核目的保证强度和刚度(1).刚度——防止过大弹性变形⑴从保证塑件精度要求方面出发:要求弹性变形δ<1/5Δ弹性变形量[δ]由塑件的尺寸公差值决定⑵从保证模具型腔不发生溢料方面出发:由塑料粘度特性决定弹性变形值应小于制件收缩值型腔尺寸+弹性变形=制件尺寸+热膨胀(收缩)值当变形大于热收缩值时,冷却减压后,型腔弹性恢复,塑件收缩导致制件尺寸大于型腔尺寸以致难以脱模2.强度——防止型腔变形、破裂刚度和强度校核,其选择以一分解值为标准影响因素:(1) 型腔形状(2) 模具材料的许用应力(3) 型腔的允许变形量(4) 塑料融体压力单型腔侧壁厚度tc的经验计算公式为:tc=0.20t+17(型腔压力PM<49MPa)。
成型零件尺寸计算
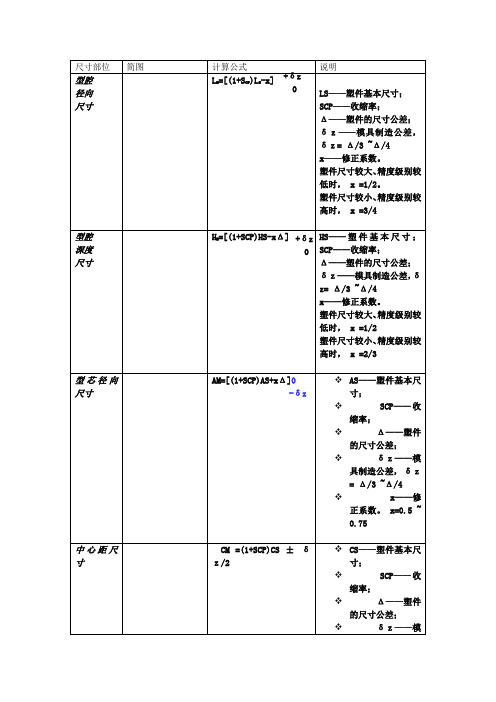
简图
计算公式 LM=[(1+SCP)LS-x]
型腔 径向 尺寸
+δ z 0
说明 LS——塑件基本尺寸; SCP——收缩率; Δ ——塑件的尺寸公差; δ z——模具制造公差, δ z= Δ /3 ~Δ /4 x——修正系数。 塑件尺寸较大、 精度级别较 低时, x =1/2。 塑件尺寸较小、 精度级别较 高时, x =3/4
型腔 深度 尺寸
HM=[(1+SCP)HS-xΔ ] +δ z HS—— 塑 件 基 本 尺 寸 ; 0 SCP——收缩率; Δ ——塑件的尺寸公差; δ z——模具制造公差, δ z= Δ /3 ~Δ /4 x——修正系数。 塑件尺寸较大、 精度级别较 低时, x =1/2 塑件尺寸较小、 精度级别较 高时, x =2/3 AM=[(1+SCP)AS+xΔ ]0 -δ z AS——塑件基本尺 寸; SCP—— 收 缩率; Δ ——塑件 的尺寸公差; δ z——模 具制造公差, δ z = Δ /3 ~Δ /4 x——修 正系数。 x=0.5 ~ 0.75 CS——塑件基本尺 寸; SCP—— 收 缩率; Δ ——塑件 的尺寸公差; δ z——模
型芯径向 尺寸
中心距尺 寸
CM =(1+SCP)CS ± δ z/2
具制造公差, δ z = Δ /3 ~ Δ /4
型芯高度 尺寸
BM=[(1+SCP)BS+xΔ ] 0 -δ z
BS——塑件基本尺 寸; SCP—— 收 缩率; Δ ——塑件 的尺寸公差; δ z——模 具制造公差, δ z = Δ /3 ~Δ /4 x—— 修正系数。 x=1/2 ~ 2/3 塑 件尺寸较大、精度 级别较低时, x =1/2
侧抽芯注射模具设计与制造

1、建立塑件三维模型 分析塑件图,完成三维建模 方法: 1)拉伸,倒圆角 2)抽壳 3)侧面打孔 4)创建加强筋
2、进入注塑模向导 1)项目名称:取个人姓名拼音 2)坐标系:Z轴指向定模 3)收缩率:2% 4)毛坯大小默认
3、布局 1)一模两件矩形平衡式布局 2)测量两型腔的实际间距 3)修改毛坯尺寸,保证型腔间距为:28 4)型腔布局的编辑
插入部件视图 在装配图的右上角插入塑件视图
制作标题栏、明细表及技术要求
装配图
单元三 卡盒2注塑模具制造 1、型腔板加工工艺规程
(1)铣(刨) 铣(刨)四周及两平面,厚度留余量0.4~0.6mm (2)平磨 磨两端面及相邻两侧面,对角尺。表面粗糙度为Ra0.8µm。 (3)划线 钳工划型孔形状及螺孔等位置线。 (4)铣 按图样要求铣出型腔,单边留余量0.3~0.5mm。 (5)钳 钳工钻螺孔、攻螺纹等。 (6)热处理 热处理 (7)电加工 采用电极精加工型腔。 (8)钳 钳工休整抛光。 (9)表面处理 按图样要求镀铬等。 (10)钳 钳工修整检验
型腔数量的确定及型的排列 该塑件采用一模一件成型,型腔布置在模具的中间,这样有利于浇注系统的排列和模具的平衡。
”
浇注系统的设计 主流道设计 根据手册差得XS-ZY-125型注射机喷嘴的有关尺寸: 喷嘴球头半径R0=12 喷嘴孔直径d0=Φ4 根据模具主流道与喷嘴的关系: R= R0+(1~2)=14 d= d0+(0.5~1)=5
模具温度℃
50~80
注射压力MPa
60~100
填写成型工艺规程卡
单元二:纸杯托注射模具设计 注射模结构设计 分型面的选择 根据分型面的选择原则,分型面应选择在塑件截面最大处,尽量取在料流末端,利于排气,保证塑件表面质量,考虑不影响塑件的外观质量以及成型后能顺利取出塑件,且应尽能将侧抽芯机构留在动模一侧,选取如下图所示截面为分型面。
塑料成型工艺及摸具设计,王群,叶久新(第2版)第四章03
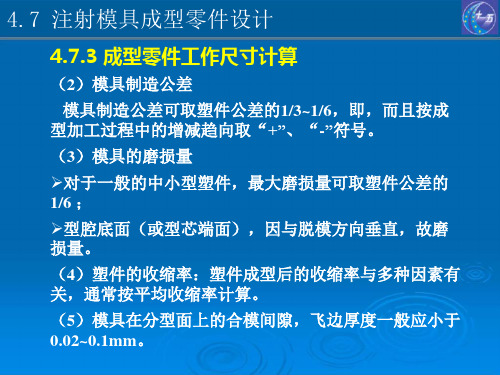
H
0.54
L
(
F脱
BE
)
1 3
4.9 脱模机构设计
4 .推块脱模
4.9 脱模机构设计
4 .推块脱模
4.9 脱模机构设计
4 .推块脱模
4.9 脱模机构设计
5.利用成型零件的脱模机构
4.9 脱模机构设计
5.利用成型零件的脱模机构
4.9 脱模机构设计
5.利用成型零件的脱模机构
4.9 脱模机构设计
4.9 脱模机构设计
1)推杆的固定形式
4.9 脱模机构设计
2)圆形横截面推杆的配合形式
4.9 脱模机构设计
(5)推出机构的导向
4.9 脱模机构设计
(5)推出机构的导向
4.9 脱模机构设计
(5)推出机构的导向
4.9 脱模机构设计
(5)推出机构的导向
4.9 脱模机构设计
(5)推出机构的导向
设计时应考虑采用便于机械加工及钳修加工的结构
4.7 注射模具成型零件设计
对于无需精密配合的部位可设计空刀槽,以节约加工工时
4.7 注射模具成型零件设计
对于不配合的过孔尽量作得大一些
4.7 注射模具成型零件设计
对于不影响成型的拐角部位进行倒角或倒圆,以便装配
4.7 注射模具成型零件设计
采用非圆形推杆时应考虑加工工艺性
4.9 脱模机构设计
3 脱模板脱模机构 (1)脱模板的结构形式
4.9 脱模机构设计
3 脱模板脱模机构 (1)脱模板的结构形式
4.9 脱模机构设计
3 脱模板脱模机构 (1)脱模板的结构形式
4.9 脱模机构设计
脱模板与型芯的配合形式
4.9 脱模机构设计
型腔数目的确定及排布

第三部分型腔数目的确定及排布一:型腔数目的确定及排布已知的体积V塑或质量W塑,又因为此产品属大批量生产的中型塑件,综合考虑生产率和生产成本等各种因素,以及注射机的型号选择,初步确定采用一模一腔排布的模具形式。
由塑件的外形尺寸和机械加工的因素,根据所用材料SPVC材质硬度不高,材料弹性模量比较小可采用强制脱模方式。
塑件用顶料杆顶出的强制脱模方法。
排布图如下图示:第四部分模具结构形式的确定上面分析可知本模具采用一模一腔,顶料杆顶出,又因为采用单腔模具,所以浇注系统较简单,只有进料口,既直浇口。
综合上几步的分析,因此基本上可确定模具形式为P5 型。
它由两块模板组成,用于直浇口,简单整体型腔的注射模。
注释:直浇口;又称主流道型浇口,在单型腔模中,塑料熔体直接流入型腔,因而压力损失小,进料速度快,成型比较容易;另外它传递压力好,保压补缩作用强,模具结构简单,紧凑,制造方便,但去除浇口困难。
应用范围:适合各种塑料成型,尤其加工热敏性及高黏度材料成型高质量的大型或深腔壳体。
第五部分注射机的型号和规格一、注射量的计算通过对塑体的质量与体积估算过程得出估算值,塑体质量m1为154g,体积为114cm3。
流道凝料的质量m2还是个未知数,可按塑件质量的0.6倍来计算。
从上述分析确定为一模一腔,所以注射量为M=1.6n×m1=1.6×1×154=246.2(g)二、塑件和流道凝料在分型面上的投影面积及所需锁模力的计算。
1、流道凝料包括交口在分型面上的投影面积A2,在模具设计前是个未知值,根据多型腔的统计分析,A2是每个塑件在分型面上的投影面积A1的0.2~0.5倍,因此可用0.35n A1来进行估算,所以A= n A1+ A2= n A1+0.35n A1=1.35×1×12265.625=16558.5938mm2式中A1=п×d2/4=0.78×125×125=12265.625 mm22、锁模力的计算F n=A ×p型=16558.6×25=413965N=413.965KN式中型腔平均压力为25MPa。
- 1、下载文档前请自行甄别文档内容的完整性,平台不提供额外的编辑、内容补充、找答案等附加服务。
- 2、"仅部分预览"的文档,不可在线预览部分如存在完整性等问题,可反馈申请退款(可完整预览的文档不适用该条件!)。
- 3、如文档侵犯您的权益,请联系客服反馈,我们会尽快为您处理(人工客服工作时间:9:00-18:30)。
❖ 目的与要求
▪ 1.掌握成型零件尺寸的计算方法 ▪ 2.会分析型腔壁厚和底板厚度受力情况,会运用公式
和查表选择数据确定型腔壁厚和底板厚度;
❖ 重点和难点
▪ 重点:成型零件尺寸的计算方法;公式的运用和选择 表中的数据确定型腔壁厚和底板厚度
▪ 难点:各个公式的运用和选择表中的数据
成型零件尺寸计算
❖3.3.3 成型零件的尺寸计算
一、成型零件的工作尺寸 ▪ 成型零件工作尺寸包括:
• 型芯和型腔的径向尺寸 • 型芯和型腔的深度尺寸 • 中心距尺寸