沙钢冷轧设备单体试运转方案(硅钢连退机组)
冷轧工程-连退、热镀锌报告(正式)

1、前言受新余钢铁有限责任公司工程管理处委托,按中冶南方工程技术有限公司提出的“新余钢厂三期技改冷轧工程连退、热镀锌施工图设计阶段工程地质勘察任务书”和“地质勘探位置图”的要求,我院于2008年8月至9月期间对冷轧工程连退、热镀锌车间拟建场地进行了施工图设计阶段岩土工程详细勘察工作。
拟建的冷轧工程-连退、热镀锌场地位于新钢公司三期技改厂区三号地块内,天工大道东侧,三体技改主体区热轧生产线北侧。
本次勘察拟建建(构)筑物具体情况如下表1:表1本次勘察技术要求及要求提交勘察资料内容详见:“施工图设计阶段工程地质勘察任务书”及“地质勘探位置图”(附件1、2)。
根据勘察技术要求本次勘察严格执行下列规范:《岩土工程勘察规范》(GB50021-2001);《建筑地基基础设计规范》(GB50007-2002);《建筑抗震设计规范》(GB50011-2001);《建筑桩基技术规范》(JGJ94-94);《建筑地基处理技术规范》(JGJ79-2002);《建筑基坑支护技术规范》(JGJ120-99);《土工试验方法标准》(GB/T50123-1999);《工程岩体试验方法标准》(GB/T50266-1999);《水质分析规程》(YS5226-94);《标准贯入试验规程》(YS5213-2000);《圆锥动力触探试验规程》(YS5219-2000)等相关规范规程。
本工程的工程重要性等级为二级,场地复杂等级为二级(中等复杂场地),地基复杂程度为二级,本次岩土工程勘察等级为乙级。
本次勘察采用钻探并辅以适当的原位测试与室内试验相结合的勘察方法,第四系地层采用冲击钻进,岩层中采用回转钻进。
勘探点沿建(构)筑物外轮廓线建(构)筑物角点及主要设备基础位置按中等复杂地基布置,为满足勘察技术及有关规范要求,本次勘察完成的工作内容和工作量如下表2:表 2尚需说明(1)本次勘察勘探点的数量及位置由委托单位确定,共布置勘探孔179个,编号为1~179号。
硅钢连续退火操作
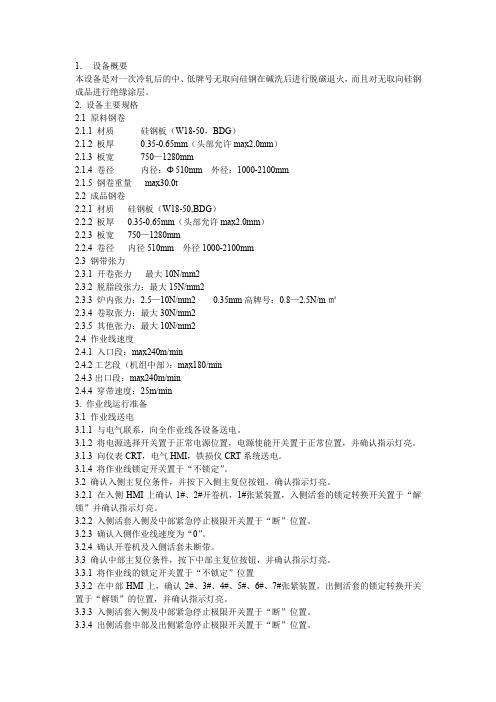
1.设备概要本设备是对一次冷轧后的中、低牌号无取向硅钢在碱洗后进行脱碳退火,而且对无取向硅钢成品进行绝缘涂层。
2. 设备主要规格2.1 原料钢卷2.1.1 材质硅钢板(W18-50,BDG)2.1.2 板厚0.35-0.65mm(头部允许max2.0mm)2.1.3 板宽750—1280mm2.1.4 卷径内径:Φ510mm 外径:1000-2100mm2.1.5 钢卷重量max30.0t2.2 成品钢卷2.2.1 材质硅钢板(W18-50,BDG)2.2.2 板厚0.35-0.65mm(头部允许max2.0mm)2.2.3 板宽750—1280mm2.2.4 卷径内径510mm 外径1000-2100mm2.3 钢带张力2.3.1 开卷张力最大10N/mm22.3.2 脱脂段张力:最大15N/mm22.3.3 炉内张力:2.5—10N/mm2 0.35mm高牌号:0.8—2.5N/m㎡2.3.4 卷取张力:最大30N/mm22.3.5 其他张力:最大10N/mm22.4 作业线速度2.4.1 入口段:max240m/min2.4.2工艺段(机组中部):max180/min2.4.3出口段:max240m/min2.4.4 穿带速度:25m/min3. 作业线运行准备3.1 作业线送电3.1.1 与电气联系,向全作业线各设备送电。
3.1.2 将电源选择开关置于正常电源位置,电源使能开关置于正常位置,并确认指示灯亮。
3.1.3 向仪表CRT,电气HMI,铁损仪CRT系统送电。
3.1.4 将作业线锁定开关置于“不锁定”。
3.2 确认入侧主复位条件,并按下入侧主复位按钮,确认指示灯亮。
3.2.1 在入侧HMI上确认1#、2#开卷机,1#张紧装置,入侧活套的锁定转换开关置于“解锁”并确认指示灯亮。
3.2.2 入侧活套入侧及中部紧急停止极限开关置于“断”位置。
3.2.3 确认入侧作业线速度为“0”。
3.2.4 确认开卷机及入侧活套未断带。
硅钢工艺及设备

硅钢连续退火生产工艺及装备2.8.3硅钢连续退火机组2.8.3.1设备选型电工钢连续退火及涂层机组用于生产高质量的中、低牌号无取向电工钢,以满足市场上日益增长的小型电机、微型电机、密闭电机、间歇电机、整流器用电工钢的需求。
退火机组是硅钢生产的重要工序。
2.8.3.3主要设备组成及技术性能1.00入口段设备1.01入口步进梁数量:1套位置:位于轧后库与机组入口之间,与机组中心线平行。
功能:将钢卷从轧后库运输到机组入口1#过渡鞍座上。
结构:步进梁主要由动梁、轨道、鞍座、拉杆和拖链等组成。
步进梁动梁由液压缸驱动横移和升降。
步进梁动梁、鞍座均为焊接钢结构型式。
主要技术参数:—卷重:max.25t—卷位:6个—输送重量:max.6×25=150t—卷位间距:3000mm—升降行程:约230mm—横移液压缸:Φ140/Φ100×3000mm×1—升降液压缸:Φ250/Φ160×845mm×2—润滑:干油润滑1.02入口过渡车数量:1套位置:位于1#、2#入口过渡鞍座之间,运行方向平行于机组中心线。
功能:将钢卷从1#过渡鞍座运输到2#过渡鞍座上。
结构:往返小车主要由车体、传动系统、轨道和拖链组成。
车体由液压缸、剪刀型活动支撑和行走轮组成。
齿轮电机驱动车体沿轨道移行,液压缸驱动车体升降。
升降液压缸由2个Φ160/Φ110液压缸组成。
传动系统由两台齿轮电机组成。
主要技术参数:卷重:max.25t升降液压缸:Φ160/Φ110×300mm×2移行距离:~6500mm齿轮电机:3kw,2台/套传动速度:max.15m/min润滑:干油润滑 1.031#、2#入口钢卷鞍座数量:2套(1卷/套)位置:分别位于1#、2#开卷机中心线操作侧延长线基础上。
功能:1#过渡鞍座用于从步进梁接受钢卷,并用1#钢卷小车向1#开卷机运输或用入口往返小车向2#过渡鞍座运输;2#过渡鞍座用于从入口往返小车接受钢卷并存放,或再向2#开卷机运输。
硅钢连续退火线卷取机带尾定位控制的应用_欧阳帆

Dl 2
(4.7)
图4.1 带尾定位长度示意图
-209-
》 》
(4.3)
学术交流
激活交换点定位时,立即发出自动减速信号。 4.3 带尾定位长度的计算 在实际生产中,按照工艺的要求带钢在卷 取机上卷取结束后,带尾必须停留在卷取机一 个相对固定的位置上(本方案设计为5点钟方 向),为下一个生产工序打下良好的基础,如 出口小车卸卷自动、打捆机包扎捆带等,这样 既可以节约人工劳动量,又有效提高了生产效 率。鉴于此,控制系统需提供带尾自动定位的 功能[2]。 在带尾定位控制过程中,最重要的就是带 尾定位长度的计算[3]。提高定位精度的最有效 手段,就是研究出带尾定位长度的控制算法。 当飞剪分卷完成后,即触发启动TDC系统的带 卷定位功能模块。卷取机将以爬行速度(30m/ min)运转,本机组中,出口5#转向加送辊或 6#转向夹送辊前的光电开关作为带尾检测器。 在卷取机卷取运行时,光电开关始终处于遮光 状态。当带尾到达5#转向加送辊或6#转向夹送 辊前的光电开关时,光电开关处于通光状态, 同时向TDC系统发送带尾到达信号。此时TDC系 统开始计算卷取卷筒卷取带卷的长度,然后将 其与系统计算的定位长度进行比较判断,并发 出停车指令。带尾定位长度的组成示意图如图 4.1所示。
那么带尾定位长度L就可以计算出来了: (4.8) L=L1+L2+L3+L4 通过此功能块接受POSITI功能块的定位逻 辑,完成相应的定位的实际行程的计算和剩余 距离计算。定位1-定位11属于速度线1;定位 12-定位21属于速度线2;定位22-定位32属于 速度线3。当定位启动时,通过一个脉冲进入 定位程序,读取定位控制字,定位末速度,定 位距离。通过获取定位控制字的定位高电平来 进行定位剩余距离计算。当定位结束时,通过 又一个脉冲和定位控制字的定位低电平退出定 位程序。当启动一个定位后,定位进入执行状 态,如果此时再一次启动这个定位,则此定位 继续在原定位的基础上继续执行,前面(原定 位)取消。 5.结论 文章以中冶新材冷轧硅钢连续退火机组 的出口自动减速系统的实现思想为主体,进行 了细致的研究,重点讨论了带卷剩余长度的控 制算法;同时对带尾自动定位系统进行剖析, 推导出有效的定位长度计算公式,大大减少了 TDC系统的运行负荷,提高了控制精度,充分 发挥了作业机组的生产效率。经过反复实践论 证,带尾定位控制十分精确,从投产未出现故 障。此方法同样可以其他同行业连续生产线中 使用。
连退机组工艺及设备简介

连退机组工艺及设备简介(总19页)本页仅作为文档封面,使用时可以删除This document is for reference only-rar21year.March连退机组工艺及设备简介一、连退机组工艺简介连退机组是新钢冷轧带钢厂的一条主要生产机组。
年产量为700000t/a,规格范围:厚度:~2.00mm;宽度700~1430mm。
总体上连退机组分为三部分,入口段、炉子段、出口段。
主要工序包括清洗、退火、平整、表面检查及精整各主要工序。
1、清洗:用碱喷淋清洗、电解清洗和机械刷洗、漂洗的方法去除带钢表面残留的轧制油及各种表面污迹。
2、退火:将因冷轧而产生加工硬化的带钢进行再结晶退火,改善微观组织,获得所需要的强度、塑性及冲压成形性。
3、平整:A.改善材料机械性能,扩大材料塑性变形范围;B.消除材料屈服平台,防止冲压不均匀变形;C.改善板形,获得良好带钢平直度;D.改善带钢表面结构,获得合适的表面粗糙度。
4、检查和精整:A.将带钢剪成合适的成品宽度;B.对带钢检查表面状态进行检查并记录;C.在带钢卷取至规定重量时进行分卷,切除焊缝、头尾超差部分及有缺陷部分,并切取试样;D.按照要求对带钢表面均匀涂敷防锈油;E.对带钢进行打捆、称重、粘贴标签。
1、产品品种范围CQ, DQ, DDQ, EDDQ, SEDDQ,HSS2、产品规格范围(设计大纲)- 带钢厚度:-2.0mm (厚度偏差±10%)- 带钢宽度:700-1430mm- 最大横截面积:×1430mm2(2860mm2)3+/- 10 mm4、卷重入口: max出口: max5、机组速度入口段:1) 60-650 mpm ,Max650mpm,2)入口侧的加/减速:0.50m/s2,3)穿带速度(带头/带尾):60 mpm;工艺段:1)Max420mpm, 2)炉段正常的加/减速 : +/- 0.1 m/s²,3) 穿带速度 : 30 m/min max,4)最小的操作速度 : 40 m/min,5) 最大加速度 : + 0.1 m/s²,6)工艺段正常停机减速度- 0.15 m/s²,7) 快停速度 : - 0.33 m/s²8) 断带时事故减速 : - 0.33 m/s²,9)事故停机:大约在内工艺段由全速至完全停机。
轧钢试车方案

连轧试车方案一、试车组织机构组长:副组长:机械组:润滑组:电器组:二、试车前对现场及设备的要求说明:(1)参加设备运转的人员,要熟悉设备说明书、相关的技术文件,了解设备的构造和性能,掌握设备的操作规程,操作方法和安全操作规程。
(2)试运转所需要的工具、材料、防护用品准备齐全,各种能源介质确保供应。
(3)危险部位和易燃部位设置好安全防护和灭火装置。
(4)设备及周围环境清理干净,并要装备必要的照明和通讯设备。
1.电器方面1.1直流电机接线正确、紧固,绝缘良好1.2直流电机内部清洁,无杂物,碳刷与整流子接触良好,碳刷无损坏,刷架紧固良好1.3直流电机空水冷却器风机转向正确,水系统供水正常,空水冷却器及供水管道无泄露1.4脉冲编码器连接牢固,同心度良好1.5传动柜主回路、控制回路接线正确牢固,电压、电流用万用表检测正常1.6传动柜参数设置正确,检测保护装置良好2.机械方面2.1减速机地脚螺栓牢固,各部件齐全完整2.2油泵启动后,对所有减速机及1#、2#飞剪手动盘车3-5圈,减速机无杂音、死点,无别劲、卡劲现象2.3对直流电机手动盘车3-5圈,电机转动灵活,无别劲、卡劲现象2.4直流电机地脚螺栓牢固2.5所有干油润滑点(轧辊、飞剪、减速机接手等),润滑脂充足、到位3.润滑系统3.1润滑管路畅通,所有控制阀门开关正确,各润滑点共油良好,油流指示器完好,视窗处油流清晰,无泄漏3.2稀油站油位正常,安全阀设置合理,油泵启动后,油压、油温、流量应符合设计和设备技术文件的规定三、试车前各小组人员齐全,检查无误后并经小组组长确认,请示试车组组长试车,由试车组长组织试车,通知所有试车人员后,下达命令。
四、运转步骤试运转按安装后的调试、单体试运转、无负荷联动运转三个步骤。
1.安装后的调试:每台设备安装完毕,首先进行调试,以检验设备安装的正确性,在确认安装符合设备技术文件规定后,再进行单体试运转。
2.单体试运转步骤为:先手动后电动,先点动后连续,先低速后中速、高速。
沙钢冷轧设备单体试运转实施专业技术方案(硅钢连退机组)

A2施工组织设计(方案)报审表施工组织设计(方案)审批表(A)ZD·03·05·J01—2011(A)江苏沙钢集团扬子江冷轧板有限公司沙钢1420冷轧硅钢连续退火机组机械设备安装工程单体设备试运转调试方案中冶天工上海十三冶建设有限公司沙钢扬子江冷轧板工程工程经理部2012年11月目录1、方案编制依据 ------------------------——----012、工程简况及生产工艺流程 ---------------——---013、调试前的准备工作 ----------------------—--044、入口段、出口段设备试运转调试-----------———--055、清洗段设备试运转调试-------------------126、活套设备试运转调试-------———--—--197、风机试运转调试------——---------------208、工机具及材料表-------------------------------299、单体设备试运转安全技术措施-------------------3510、附表:1、调试人员管理体系2、试运转记录样表3、单体试车安全确认书1、方案编制依据1420冷轧硅钢连续退火机组各系统施工图《轧机机械设备工程安装验收规范》GB50386-2006《机械设备安装工程施工及验收通用规范》GBJ231-98《冶金机械液压、润滑和气动设备工程安装验收规范》GB50387-2006 《工业金属管道工程施工及验收规范》GB50235-97《现场设备、工业管道焊接工程施工及验收规范》GB50236-98《压缩机、风机、泵安装工程施工及验收规范》GB50275-982、工程简况及生产工艺流程1420冷轧硅钢连续退火机组由1#、2#硅钢连续退火机组组成,在入口段,钢卷吊放在固定鞍座上,经过测量宽度、对中、旋转等操作后由运卷小车运输到开卷机卷筒上。
轧机试车方案

轧线工艺设备及辅助系统无负荷单体试车方案编制单位:施工单位:编制人:审批人:二零零八年四月二十六日目录1 试车组织2 总则3 液压系统的调试4 气动系统的调试5 稀油润滑系统的调试6 干油润滑系统的调试7 高压除鳞水系统调试8 主轧区设备调试9 冷床区设备调试10 精整区设备调试11 安全措施1 试车组织成立试车指挥组,由指挥组统一组织、指挥。
试车指挥组下设个区域试车小组。
指挥组由下列人员组成。
1.1 试车指挥组1.2 区域试车小组1.2.1 轧机区试车小组组长:组员:1.2.2 减定径机区试车小组组长:组员:1.2.3 钢坯修磨区试车小组组长:组员:1.2.4 冷床、精整区试车小组组长:组员:2 总则2.1 通用规定2.1.1 设备无负荷试车分无负荷单体、无负荷联动试车。
本方案仅负责无负荷单体试车部分,无负荷联动试车方案由中冶赛迪三电小组另行编制。
2.1.2 无负荷单体试车由安装单位负责组织,以安装单位为主,设计、设备供货商配合。
无负荷联动试车由中冶赛迪负责组织,以三电调试小组为主,安装单位、设备供货商配合。
2.1.3 无负荷联动试车合格后总承包单位、施工单位、监理单位、建设单位(用户)在试车合格证上签字,并办理实物移交。
设备移交用户保管,并作负荷试车准备。
对试车中暴露出的问题以及需改进完善的部分做好书面记录,在收尾过程中处理,不影响实物移交。
2.1.4 试车前由中冶成工棒材项目部总工程师(或相当于总工程师)作试车交底。
参加试车工作的全体人员要认真学习此试车方案。
2.1.5 试车由现场指挥一人发令(其他任何人有意见向指挥讲,无权对操作者发指令),指令应清晰、简洁(避免口齿不清),操作者只能听指挥的指令,操作人员不得自行开机、停机;如遇设备突然冒烟、异常声响、剧烈振动等重大特殊情况岗位人员有权立即停车。
2.1.6 试车时各部位都要安排专人在岗监护,试车未结束不得擅自离岗。
2.1.7 对设备运行期间如发现设备运转有问题及时报告指挥,由指挥决定是否停机检查。
浅谈沙钢1420mm冷轧普通连退机组前期电气施工技术管理

集和整 理施工过程 资料 ,特别是对 于建筑 电气工 程施 工的 隐蔽 工程验收资料 ,对于未经监 理等相关人员在 隐蔽验收
记 录表 上签字 的工序 交接单 ,电气 施工技术人 员不得 让作 业人员进行下道工序 的施工 ,防止技术监督流于形 式。 1 . 4 技术协调 建筑 工程的施工是 复杂的 ,它包 括土建 、给排水 、通
沙钢 1 4 2 0 mm 冷轧普通连退机组 主要 由中冶南方工程技
术有 限公司负责设计 ,普通连 退机组主要分 为人 口段 、炉 子段 、出 口段 和入 口电气室 、出 口电气 室等区域 ,在前 期
施工 过程 中的配 管和接地 ,电气施工技 术人员应及 时配 合 土建 专业施工进度 ,对常见 的质量 问题通 过相应 的技术 管 理严格控制 ,确保施工质量 。
时也 要 根 据 施 工 现 场 实 际 情 况 调 整 施 工 计 划 ,通 过 技 术 监
1 前期主要技术管理要点
对建 筑电气工程 开展技术 管理 ,既是建 筑 电气工程 施 工质 量 的保 证 ,也 是保 证建 筑 电气 工程 的顺 利 施工 的 前 提 ,以下为笔者对沙钢 1 4 2 0 mm 冷轧普通连退机组前期 电气 施工过程 中总结 的一些技术管理要点 ,具体 内容如下 :
料和设备 的可用性 ,此外电气施工 技术人员要做 好材料 和 设 备说 明书 、合格证 、质 保书 的核 实工作 ,对建 筑电气工 程施 工所采用 的材料和设备严 把检测关 和使用关 ,对 于没 有产 品检验合 格证和不符 合设 计要求 的材料和设备不 允进
场使用 ,对符合 进场条件 的材 料和设备要及 时填写 《 材料
沙钢转底机械试车方案

沙钢固废综合处理、资源循环利用项目转底炉工程--转底机械试车方案编制人:侯平审核:吴高奇北京神雾热能技术有限公司一、试车内容沙钢转底炉工程转底机械设备一套,其主要部件包括:支撑辊装置、定心装置、上下框架、传动装置、水封装置及刮渣装置。
辅助设备:液压系统、干油润滑系统。
二、试车目的转底机械的试车分冷态空负荷单机试车和热负荷联动试车。
空负荷单机试车主要为了检查转底机械运行时,机械运转的平稳性及转底的跑偏;运行时各部件接触情况(具体检查内情:支撑辊与下框架轨道面接触间隙、定心装置与定心导板接触情况、传动装置与销齿咬合情况、水封槽与刮渣板之间间隙)是否满足设计要求,检查转底机械运行时转底机械与炉体结构、耐材、管道、其它设备相关位置关系,以保证转底机械在各运行中不刮蹭、碰撞,各转动部件转动灵活。
三、试车的组织机构转底机械的试车由北京神雾公司组织,业主、监理、江苏院负责各相关单位的协调,江都冶金工程公司、南京中山炉负责对试车过程中发现的施工问题进行处理;神雾公司对电气、仪系统负责,设备制造厂家指导试车并对试车过程中因设备自身原因造成的问题进行处理。
试车组织机构人员名单:试车小组组长:(宏昌钢板项目部负责人)试车小组副组长:试车小组成员:宏昌钢板:北京神雾:江都冶金工程公司:南京中山炉:设备制造厂家:扬州江冶机电设备有限公司:液压设备现场调试人员安全巡查:各专业配合调试人员:钳工:4人电工;4人仪表工:2人电气焊工:3人管工:2人四、试车条件:●试车前已编制完试车方案,应经相关单位部门批准;●试车前,各专业相关调试人员已接受技术交底,熟悉所试设备的构造、性能、设备技术文件,掌握本专业操作规程以及试车过程中对所试设备故障原因的判断和处理方法等试运转操作;●设备底座二次灌浆施工完毕,强度达到要求;●机械设备必须安装完毕,所有的紧固螺栓都已紧固,试车前需一一检查;●电气设备必须安装完毕,达到全部受电条件,操作箱、操作台具备手动启动、停止功能;●液压、润滑、气动、水冷管道安装完毕,管道冲洗、吹扫、试压完毕,并能正常投入使用,随时满足机械动作要求;●机械设备上的所有干油润滑点都应加上足额的符合图纸要求的润滑介质;●设备的机前控制定位系统,行程开关、接近开关、压力开关、液位开关等现场仪表装配完毕,满足设备动作的行程动作要求;●机械设备表面已清扫干净;●各专业试车过程中调试(检测)和事故处理所需工具、材料和检测仪表已准备并符合试车要求;●试车时应具备必要的照明和通风设备;●试车前的安全措施、所需器材、人员落实到位;试车时,业主方、监理方、总包方、施工方、设备生产厂家、必须同时在场,经过上述几方确认后方可进行试车。
冷轧连续退火炉工艺工作总结

目录摘要 (2)一、引言............................................................................................................................................................ 3二、主体............................................................................................................................................................ 3(一)、安全.............................................................................................................................................. 31、安全教育培训.............................................................................................................................. 32、机械点检安全规程...................................................................................................................... 43、岗位安全生产职责...................................................................................................................... 5(二)连退机组工艺................................................................................................................................ 51、连退机组的主要任务及原理 ...................................................................................................... 81.1连退机组主要任务.............................................................................................................. 81.2、机组工艺原理................................................................................................................... 82、连续退火工艺及设备.............................................................................................................. 102.1 入口密封室..................................................................................................................... 112.2 预热/无氧化加热炉...................................................................................................... 122.3 1#炉喉........................................................................................................................... 122.4 辐射管加热段................................................................................................................. 132.5 均热段............................................................................................................................. 142.6 2#炉喉.............................................................................................................................. 152.7 管冷段........................................................................................................................... 152.8 膨胀节........................................................................................................................... 162.9 保护气体循环喷射冷却器 ............................................................................................. 172.9 出口密封室..................................................................................................................... 182.10 最终气体喷射冷却....................................................................................................... 19三、总结........................................................................................................................................................ 20(一)、收获与总结.............................................................................................................................. 20(二)、对学校开设课程的建议.......................................................................................................... 21致谢:............................................................................................................................................................ 21摘要:硅钢被誉为钢铁行业的“工艺品”,广泛的应用于各种电机和变压器的中心部件,其制造工艺复杂,装备总类多,设备自动化程度较高,生产过程困难,对各项指标的要求较高。
连退机组生产冷轧硅钢表面氧化控制研究

2 1 0 2年 第 1期
’
ANGANG T ECH NOL OGY
总 第 3 3期 7
’~
- -
磊
。… … -_●●
●
- - -
连 退 机组 生产 冷 轧硅 钢 表 面 氧化控 制研 究
马 云龙
( 鞍钢 股份 有 限公 司冷轧硅 钢厂 , 宁 鞍 山 1 4 2 ) 辽 1 0 1 摘 要 :通过 热 力学和 动 力学原 理 分析 了现行 工 况 下连退机 组 冷却段 生产硅 钢 时钢板 发 生
重影 响 了硅 钢产 品 的质量 和 产能 ,对 连退 线 的生 进 行无 机 物涂层 ,从而 得 到铁 损 、磁 感等 性 能合
产节 奏 和作 业率 都 产生 了一 定影 响 。事 故原 因基 格 、 实效 满 足要 求 、 面绝 缘 度合 适 的冷 轧硅 钢 磁 表 本 上 都 是 因 为 冷 却 段 的 氧 气超 标 或 水 分 超 标 所 产 品 。
3 氧 化 反 应 的 热力 学 分 析
31 标 准压 力 下的 热力 学分 析 . 列 于表 1中。
表 1 各 物质 中 的标 准 焓和 标 准 熵
可见 , 含 量 已经 低 到工 业 生产 无 法控 制 的 程度 。 氧 也 就 是说 , 氧化 反应必 然 发生 。因此 在工 业生 产 此
n a i i e i nay e a e n p i cp e fb t he mo y a c nd d n mi s el ng ln s a l z d b s d o rn i l s o o h t r d n mi s a y a c .Ex e i n a p rme t l su e r t d e t e a d t h e t dis a e su i d wih r g r o t e tmpe aur ft o ln e to ,c n e to x g n a d t e r t e o he c o i g s ci n o tn fo y e n h
硅钢连退机组急停系统测试及改造-精选文档

硅钢连退机组急停系统测试及改造中冶南方(新余)冷轧新材料技术XX公司是一家以生产中低牌号硅钢为产品的公司。
该公司所拥有的连续退火线使用了一套由西门子S7-315F 为平台设计的独立急停系统。
通过急停系统与主控TDC系统的通讯协调来保证连退机组在事故时能快速停车。
但在实际生产应用中,当主控TDC系统出现故障时,因控制失效易造成堆带、断带事故。
本次改造对系统进行了有针对性的功能的测试及改造。
1.连退线的自控与急停系统的构成及原理1.1连退线机组自动化设备分布连退线机组分为入口段、入口活套、清洗段、退火炉段、干燥段、出口活套和出口段几部分。
通过开卷机、卷取机、入出口活套主卷扬、1 -7#张力辊维持生产线的运行和张力稳定。
具体分布如图1 所示。
1.2连退线控制系统组成连退线自控系统由四部分组成:主令控制系统,顺序控制系统,传动控制系统,急停控制系统,HMI人机画面系统。
主令控制系统是由西门子TDC控制器构成,负责全线的速度、张力、物料跟踪等功能。
顺控系统由西门子S7-400系列PLC构成,负责全线公辅设备以及顺序控制。
传动系统由西门子最新的SinamicsS120系列传动系统组成。
急停系统由西门子专门用于安全急停系统的S7-315F系列PLC组成。
HMI人机界面是由两台工程计算机搭载WINCC平台组成的冗余服务器,连接现场4台客户机完成人机互动。
1.3急停动作流程当急停动作被触发时。
首先由急停系统获取触发信号,经处理通过Profibus-DP网路将其传给主令控制系统TDC由TDC分配各段动作任务下发至S7-400 顺控系统,同时将停车速度斜坡发给传动系统。
传动接收到速度后执行停车动作,当停车完成后返回完成信号给主令。
主令系统接收到完成信号后转给急停系统,急停系统接收到完成信号,或者延时时间到后切断现场站输出信号供电。
ET2.使用中存在的问题在正常生产中急停系统能够稳定正常的工作。
但由于TDC系统的不稳定,时常产生死机故障的情况。
冷轧硅钢连续退火机组卷取张力控制系统设计与实现—欧阳帆

UDC
密级
学 位 论 文
冷轧硅钢连续退火机组卷取张力控制系统设计 与实现
作 者 姓 名 : 欧阳帆 指 导 教 师 : 何大阔 教授 东北大学信息科学与工程学院
王 洪 教授级工程师 新余钢铁集团公司 申请学位级别: 硕士 学科专业名称: 控制工程 论文提交日期: 2013 年 7 月 学位授予日期: 评 阅 人 : 论文答辩日期: 答辩委员会主席: 2013 年 8 月 学 科 类 别 : 专业学位
Keywords:Constant tension control;Coiler;TDC; Coil diameter calculation; Moment compensations;
-III-
东北大学硕士学位论文
目录
目录
独创性声明 ................................................................................................... I 摘 要 .......................................................................................................... II ABSTRACT ............................................................................................... III 第1章 绪论 .............................................................................................. 1
硅钢连退机组自动化控制系统

硅钢连退机组自动化控制系统朱保汉(中冶南方工程技术有限公司原武汉钢铁设计研究总院武汉)摘要:本文主要介绍了鞍钢冷轧硅钢处理线的自动控制系统,并对控制系统功能进行了描述。
关键字:SCAL;自动化;PLC; HMI;工业以太网;WinCC;STEP 7Abastract:The paper introduce the automatic control system of Angang cold roll Silicon process line . Describing Control system function. Keywords:SCAL;Automation;PLC; HMI; Industrial Ethernet; WinCC ;STEP70.前言为满足国内市场对冷轧硅钢的需求,鞍钢决定新建一冷轧硅钢厂,年产80万t中低牌号无取向硅钢,其中包括1条酸洗连轧机组(PL-TCM)、4条硅钢连续退火及涂层机组(SACL)、2条重卷机组和2条包装机组。
其中NO.1电工钢(硅钢)连续退火涂层机组(NO.1 SACL)是其中第一条电工钢连续退火涂层机组,该机组是国内第一条全部由国内设计、制造及软件编程调试的SACL机组。
鞍钢SACL机组是由武汉院总承包,进行工艺设计、非标设备设计和自动化系统设计及软件编程调试,该处理线采用了先进的自动化控制系统。
1.设备描述SACL机组的工艺组成为:入口段(包括焊机)、入口活套、碱洗段(包括碱液混合系统、碱液喷洗系统、碱液刷洗系统、高压水喷洗系统、水刷洗系统、热水喷洗系统)、退火炉段(包括PH炉、NOF炉、RTF炉、SF炉、RJC炉)、涂层段、干燥段(DF-DS/BS炉、AJC炉)、出口活套、出口段。
SACL机组的工艺概貌如下:机组主要技术参数如下:生产品种:中、低牌号无取向电工钢生产能力: 22.8万 t/a产品:冷轧硅钢带卷原料钢卷外径: max.:2000mmmin.:800mm钢卷内径: 610mm钢卷重量: max.:25000kg带钢宽度: max.:1250mmmin.:750mm带钢厚度: max.:0.65mmmin.:0.35mm机组速度入口段:线速度 max.:240m/min加速度 ~20m/sec2正常启/停~40m/sec2快停穿带速度 25m/min工艺段:线速度 max.:180m/min加速度 ~10m/sec2正常启/停~20m/sec2快停出口段:线速度 max.:240m/min加速度 ~20m/sec2正常启/停~40m/sec2快停穿带速度 25m/min紧急停车时间:由最高速度到停止时间 ~6s2.电气传动和控制系统电气传动和控制系统是工厂自动化综合控制系统的一部份,由可编程控制器(PLC)和全数字式调节系统所构成,它根据过程计算机(L2)的控制指令及设定参数来完成自动化控制功能。
硅钢连退机组带钢起筋原因与控制对策研究

【 关键词】 硅钢 连续退火 起 筋 控制
r
CAUS ES AND CoNTRo L S TRATEGY FoR RI DGE BUCKLE oF
0
S I LI CoN S TE EL I N CoNTI NUoUS ANNEAL I NG LI NE
s i l i c o n s t e e l ,t h e ma i n f a c t o r s w e r e a n a l y z e d a n d c o r r e s p o n d i n g s o l u t i o n wa s p r o p o s e d i n e a c h c o l d
L u Yu l o n g Che n Ga ng Z h u Zh i y o n g Z ha n g Xi u c h e n g
( J i a n g s u S h a g a n g G r o u p , Z h a n g j i a g a n g J i a n g s u 2 1 5 6 2 5, C h i n a )
r o l l i n g p r o c e s s ,wh i c h wa s p r o v e d t o b e e f f e c t i v e .
【 K e y Wo r d s 】 S i l i c o n S t e e l , C o n t i n u o u s A n n e a l i n g , R i d g e B u c k l e , C o n t r o l
5 0 W4 7 0~5 O Wl 3 0 0、 6 5 W8 0 0~6 5 W1 6 0 0等 , 厚 度
规格 为 0 . 3 5~0 . 6 5 m m、 宽度规格为 7 5 0~1 3 0 0 m m。产 品主要 应 用 在 小 型 电机 、 微型电机 、 密 闭
硅钢连续退火线试车方案

目录一、编制依据及说明 (1)二、工程特点 (1)三、单体试车组织结构 (2)四、试车前的准备; (2)五、单机调试的一般程序 (3)5.1机组设备单体试运转规程 (3)六、具体单体无负荷试车 (9)6.1碱液循环系统(泵)设备试车 (9)6.2工艺段设备单体无负荷试车 (10)6.3清洗段单体无负荷试车 (27)6.4炉子段单体无负荷试车 (32)七、安全保证措施 (32)三硅钢CA5/CA6退火机组单体无负荷试车方案一、编制依据及说明1.1 中冶南方工程技术有限公司提供的设计安装图纸;1.2《冶金机械设备安装施工验收规范》;1.3《机械设备安装工程施工及验收规范》;二、工程特点2.1说明:本方案适用于武钢三硅钢CA5/CA6机组工程设备的调试;2.1.1工程概况、工程特点武钢三硅钢CA5/CA6机组工程是武钢三硅钢主要配套项目之一,位于已建成的武钢三硅钢厂房内,与武钢二硅钢相邻。
设备基础结构总长度340米,分布在轴线106—134之间。
宽度在轴线G—H之间40米范围内。
机组设备基础结构总长度345米,总宽41.5米。
由无氧化炉,RTF炉,SF炉,DS,BS炉开卷,卷取,出入口活套, 1#-10纠偏辊, 1#--7#张力辊, 1#--4#张力计辊, 1#-5#转向辊,1#,2#热风干燥器,气刀, 涂层机, 焊机, 挤干辊,1#-7#转向夹送辊, 出口剪,双层剪, 测厚仪, 碱涮洗槽, 热水涮洗槽, 水涮洗槽, 高压水涮洗槽, 电解清洗槽, 碱喷淋装置, 加湿装置等组成;本次调试内容有:通风系统设备;清洗系统设备;工艺段设备和炉设备,(具体调试设备清单及其检查记录附后)。
三、单体试车组织结构四、试车前的准备;1、主厂房内侧瓦等已安装完毕;2、各设备电机、接线交线已完毕。
并已确认通电。
3、各种极限、光电开关已安装完毕,并已通电;4、设备二次灌浆已完成;5、电机冷却水管已配置完毕并验收合格;且已充满水;6、冷却风机已安装验收合格并通电;7、各能源介质管道已配置完毕并验收合格;且已充满介质;8、各设备的减速机稀油润滑系统已调试完毕,且稀油正常循环(流量、流速等达到设计要求);9、干油系统已验收合格,可以向各个润滑点供润滑油。
- 1、下载文档前请自行甄别文档内容的完整性,平台不提供额外的编辑、内容补充、找答案等附加服务。
- 2、"仅部分预览"的文档,不可在线预览部分如存在完整性等问题,可反馈申请退款(可完整预览的文档不适用该条件!)。
- 3、如文档侵犯您的权益,请联系客服反馈,我们会尽快为您处理(人工客服工作时间:9:00-18:30)。
A2施工组织设计(方案)报审表施工组织设计(方案)审批表(A)江苏沙钢集团扬子江冷轧板有限公司沙钢1420冷轧硅钢连续退火机组机械设备安装工程单体设备试运转调试方案中冶天工上海十三冶建设有限公司沙钢扬子江冷轧板工程项目经理部2012年11月目录1、方案编制依据 ------------------------——----012、工程概况及生产工艺流程 ---------------——---013、调试前的准备工作 ----------------------—--044、入口段、出口段设备试运转调试-----------———--055、清洗段设备试运转调试-------------------126、活套设备试运转调试-------———--—--197、风机试运转调试------——---------------208、工机具及材料表-------------------------------299、单体设备试运转安全技术措施-------------------3510、附表:1、调试人员管理体系2、试运转记录样表3、单体试车安全确认书1、方案编制依据1420冷轧硅钢连续退火机组各系统施工图《轧机机械设备工程安装验收规范》GB50386-2006 《机械设备安装工程施工及验收通用规范》GBJ231-98 《冶金机械液压、润滑和气动设备工程安装验收规范》GB50387-2006《工业金属管道工程施工及验收规范》GB50235-97《现场设备、工业管道焊接工程施工及验收规范》GB50236-98《压缩机、风机、泵安装工程施工及验收规范》GB50275-982、工程概况及生产工艺流程1420冷轧硅钢连续退火机组由1#、2#硅钢连续退火机组组成,在入口段,钢卷吊放在固定鞍座上,经过测量宽度、对中、旋转等操作后由运卷小车运输到开卷机卷筒上。
钢卷带头由在开卷器引导下送至双层剪进行切头,废料送到废料运输机上送入废料斗,钢带进入焊机进行焊接,焊机焊接完成后钢带进入入口活套,再进入清洗段进行碱洗、冲洗、烘干后,进入连续退火炉、涂层机、干燥段进入出口活套,经分切、重卷后形成成品。
3、调试前的准备工作根据甲方提供的图纸及工程施工规范的要求,试车设备已安装完毕,并且通过甲方和监理验收。
符合《机械设备安装工程施工及验收通用规范》,《轧机设备工程安装验收规范》,《现场设备、工业管道焊接工程施工及验收规范》的有关要求。
试车设备电源已安装,现场打点接线完成,液压系统、稀油润滑系统安装完毕并循环油冲洗合格,油气管路安装完毕并试压吹扫合格,冷却水管已安装并冲洗合格,压缩空气管道安装完毕并试压吹扫合格、干油润滑管道已安装,管道已冲洗试压。
试车设备生产厂技术人员,甲方人员、设计人员、监理及相关部门负责人应到调试现场参与、指导调试工作,确认试车结果,及时处理试车当中设备出现的问题。
设备的各个转动部位和减速机的润滑油、润滑脂均按要求添加完。
设备周围杂物清理干净,并设置好必要的照明和安全围栏。
试运转中所需的各种工具、材料和通讯设施已准备齐全。
现场调试时,必须有足够的照明条件。
成立试运转领导小组,每个单体设备试车时设专人统一指挥,调试前办理各专业调试确认单,试运转的操作应由熟练的操作人员执行,并进行技术交底。
试运转区域设置安全栏杆,悬挂好安全标志,并设专人看护,非试运转人员严禁入内,消防器材到位。
试运转结束后,应及时将试车参数的记录填写好。
试车小组组织相关试车人员对机械设备安装进行复查确认,电气模拟操作各极限位置,各种保护开关应灵敏可靠。
现场对地脚螺栓、联接螺栓必须紧固、无松动现象,对传动辊、减输机、电机手动盘车应无卡阻现象。
各台设备注入指定牌号的油品到规定油位,检查管路及接头处无泄漏现象;检查各润滑点有润滑油。
气动制动器打开时两侧间隙一致,闸轮、闸皮上不得有油污。
液压润滑管路冲洗合格,并经过压力测试,蓄能器按规定压力充填氮气。
检查检速机、电机、各传动部件档块均焊接牢固,鼓形联轴器外齿圈是否固定牢固,轨道、旋转部件清理无杂物。
4、入口段、出口段设备试运转调试入口段、出口段调试主要设备调试项目及程序4.1、入口、出口钢卷上料运输系统●单体试车项目:A钢卷小车升降/前后运动B托辊站托辊旋转C钢卷称重标定、钢卷宽度/外径测量摆臂上下摆动●准备工作:A现场检查液压缸接头无渗漏,步进梁轨道无杂物后B轴承座加注润滑脂C将钢卷小车齿轮马达制动器脱开,人工推动小车来回移动自如●主要步骤:A启动电机带动小车移动,确认小车运行平稳、托链运行无卡滞,启动小车升降液压缸,升降往复运动B启动托辊旋转马达检查旋转方向、检查旋转平滑速度稳定●检查项目:A检查液压缸动作平滑速度稳定。
B检查限位开关位置准确C 检查钢卷小车移动行程5600mm,升降行程1193±2mm4.2、开卷机、卷取机●单体试车项目:A卷筒涨径/缩径B开卷机电机及减速机旋转C开卷机前移/后退、外支撑摆上/摆下、开卷器上升/下降D抱闸气动盘式制动器打开/关闭●准备工作:A检查鼓形联轴器外齿圈已完全脱开,并固定好,人工盘动减速机、辊体运转自如B检查电机、减速机轴承座进行甘油加注C检查减速机内齿轮油是否已加注到位D减速机气动抱闸先调试正常E调整检测元件位置●主要步骤:A卷取机先进行卷筒电机单试,开卷机变频电机单试先起动电机风扇,再点动电机确认正反转,启动电动机连续运行1小时,B电机调试正常后恢复电机与减速机联轴器,点动电机带减速机运转5-10次,联轴器内填充满润滑脂,齿轮箱自带稀油润滑站,单试前稀油站先行起动调试正常。
点动调试正常后连续运行1小时,运行过程中检测轴承座温度,观查箱体有无燥音、震动。
D减速机气动缸抱闸调试程序:确认压缩空气已送至电控单向阀前,按压电控单向阀体手动控制按钮,接通气缸压缩空气观查抱闸动作,调整抱闸拉杆,通过手动确认完后再进行现场操作箱的电控操作。
E再进行平移液压缸运动、涨缩液压缸、外支撑、开卷器运动。
在开卷机水平滑轨上涂抹润滑油,起动移动液压缸调整限位开关。
卷筒涨缩液压缸调试先起动涨缩液压缸,使涨缩缸打开/缩回。
起动外支撑液压缸顶紧卷筒端头●检查项目:A在运转过程中利用测温仪检查轴承座温度(滚动轴承温升小于40℃,最高温度小于80℃),电机、减速机、卷取机本体在运行过程中无卡阻颤动、平稳灵活B检查涨缩缸设定压力10MPa,检查卷取机横移行程±150mmC检查外支撑支撑臂伸缩动作2~3次,动作无卡阻与卷筒端头接触紧密无间隙D开卷器压辊摆动动作2~3次,动作无卡阻,压下压力调定7MPa E调整检测元件位置4.3、转向夹送辊●单体试车项目:A上辊升降气缸动作B夹送辊传动●准备工作:A 用手盘动辊子正反转动自如 B 轴承是否加足干油●主要步骤:A启动上辊升降气缸,点动3-5次运转平稳无卡滞B启动夹送辊电机点动确认方向,连续运转1小时●检查项目:A检查升降气缸行程160mmB电机运转正常,减速箱无噪音4.4、入口双层分切剪、废料收集装置●单体试车项目:A上、下通道翻板试验B上、下通道剪前夹送辊升降试验C上、下通道剪前夹送辊传动试验D.上、下通道剪刃侧隙确认E上、下通道剪切动作试验F剪刃架锁紧液压缸动作试验●准备工作:A轴承及衬板是加足干油,滑轨内涂抹润滑油,检查机架内无杂物,剪刃部位无杂物●主要步骤:A启动上、下通道翻板气缸,往复运动3~5次、无卡阻动作自如B启动上、下通道剪前夹送辊升降气缸, 往复运动3~5次、升降动作自如,无卡阻C启动上、下通道剪前夹送辊电机,点动3-5次,再连续运转1小时D启动上、下通道剪刃动作液压缸,点动3-5次,无卡阻动作自如E启动剪刃架锁紧液压缸点动3-5次,运行平稳F启动废料皮带驱动电机电动确认方向,连续运转●检查项目:A检查翻板气缸行程120mmB 剪前夹送辊上辊压上后,确认气缸行程270mmC确认剪刃升降行程240mmD确认剪刃升降行程30mmF调整检测元件位置4.5、张力辊●单体试车项目:A压辊压下/抬起、压辊传动电机运转B张力辊电机/减速机运转、减速机气动盘式制动器打开/关闭、●准备工作:A检查鼓形联轴器外齿圈已完全脱开,并固定好,B检查电机、减速机轴承座进行甘油加注C检查减速机内齿轮油是否已加注到位D减速机气动抱闸先调试正常E手动盘车确保电机、减速机均能盘动●主要步骤:A电机单试先起动电机风扇,再点动电机确认正反转,启动电动机连续运行1小时,B电机调试正常后恢复电机与减速机联轴器,点动电机带减速机运转5-10次,联轴器内填充满润滑脂,点动调试正常后连续运行1小时,运行过程中检测轴承座温度,观查箱体有无燥音、震动。
C恢复电机、减速机联轴器接手进行减速机调试D启动压辊液压缸,上下往复运动●检查项目:A检查压辊液压缸行程220mmB调整压辊控制检测元件位置4.6、纠偏辊●单体试车项目:纠偏液压缸伸缩,带动纠偏辊摆动●准备工作:在纠偏辊摆动滑道上涂抹甘油●主要步骤:启动液压缸来回往复运动3-5次运动平稳,无卡阻5、清洗段设备试运转调试碱洗段工艺段主要设备调试项目及程序5.1、挤干辊●单体试车项目:挤干辊气缸上升/下降●准备工作:检查现场气管接头无漏气现象●主要步骤:挤干辊驱动气缸先进行手动调试,接近开关位置调试好后,转由现场操作箱控制调试启动上辊升降气缸点动运行3-5次。
●检查项目:检查上辊升降气缸行程60mm 检查调整检测元件位置5.2、碱液循环系统、漂洗水循环系统、碱雾循环系统●单体试车项目:碱泵试运转、碱雾风机试运转●准备工作:对碱泵、风机进行手动盘车●主要步骤:逐个启动碱泵、风机点动运转3-5次●检查项目:水泵及风机运转平稳,无异响5.3、热风干燥器●单体试车项目:风机运转●准备工作:A检查机体内部无杂物,风机轴承座加注甘油润滑脂,手动盘动风机确认风机叶轮无摩擦,主轴无卡阻。
B确认压缩空气是否送到位C确认蒸气是否送到位D确认冷凝水排水管通畅●主要步骤:A启动风机电机点动2-3次,连续运转1小时B电机带风机运转点动3-5次,连续运转1小时C起动风机,开启蒸气阀门观查风温达到110℃●检查项目:A检查压力表、温度显示B风机轴承温度(滚动轴承温升小于40℃,最高温度小于80℃)6. 活套设备试运转调试●单体试车项目:A活套车前进/后退BD绳轮电机/减速机运转、减速机气动盘式制动器打开/关闭、●准备工作:A清理轨道杂物,人工推动活套车检查活套车与平台无干涉B 检查绳轮驱动电机、减速机、钢丝绳盘之间鼓形联轴器外齿圈已完全脱开,并固定好,C对电机、减速机轴承座进行甘油加注,检查减速机内齿轮油是否已加注到位D减速机气动抱闸先调试正常E手动盘车确保电机、减速机、均能盘动F手动盘动钢丝绳驱动盘确认无卡阻后穿小车驱动钢丝绳●主要步骤:A手动推动活套小车往复推动3次,检查有无干涉B脱开联轴器进行张力辊电机单试电动电机2-3次,连续运转1小时C恢复电机、减速机联轴器接手进行减速机调试先点动2-3次,连续运转1小时D电机驱动减速机带动活套小车在轨道来回往复运动3-5次。