涡流检测通用工艺规程(修订)
NBT47013涡流检测通用工艺规程

目录1主题内容和适用范围 (2)2依据标准 (2)3人员要求 (2)4检测设备和器材 (3)4.1检测仪器和检测线圈及辅助装置 (3)4.2涡流检测系统的组合性能 (3)4.3对比试样 (4)4.4备检工件 (4)4.5检测环境 (5)5安全要求 (5)5.1防止电流短路引起的电击造成人体伤害。
(5)5.2防止检测现场温度、湿度、有害环境造成人体伤害。
(5)6检测施工流程 (5)6.1检测施工流程图 (5)6.2实施检测过程说明 (6)7工艺文件及附属文件要求 (7)7.1工艺规程 (7)7.2操作指导书 (8)8铁磁性管材涡流检测 (10)8.1适用范围 (10)8.2对比试样 (10)8.3检测程序 (11)9非铁磁性管材涡流检测 (11)9.1适用范围 (11)9.2对比试样 (11)9.3检测设备 (13)9.4检测程序 (13)涡流检测工艺规程1主题内容和适用范围1.1本规程规定了涡流检测人员资格、仪器、探头、对比试样、检测范围、检测方法和质量分级等。
1.2本规程依据NB/T47013.6的要求编写,采用EEC35++型涡流检测仪器,满足引用标准中相关标准、规范的要求。
适用于在制和在用承压设备用导电金属材料管材、零部件、焊接接头表面及近表面缺陷的涡流测量方法,适用于金属基体表面覆盖层厚度的磁性法和涡流法检测。
1.3本规程与工程所要求执行的有关标准、规范、施工技术文件有抵触时,应以有关标准、规范、施工技术文件为准。
2依据标准2.1 TSG Z8001 特种设备无损检测人员考核规则2.2 GB/T5126 铝及铝合金冷拉薄壁管材涡流探伤方法2.3 GB/T5248 铜及铜合金无缝管涡流探伤方法2.4 GB/T7735 钢管涡流探伤检验方法2.5 GB/T12406.6 无损检测术语涡流检测2.6 GB/T12969.2 钛及钛合金管材涡流探伤方法2.7 NB/T47013.1 承压设备无损检测第1部分:通用部分2.8 NB/T47013.6 承压设备无损检测第6部分:涡流检测以上文件以其当前有效版本为准,其最新版本也适用于本工艺规程。
放置式线圈零部件涡流检测工艺规程

1 适用范围本规程适用于釆用放置式线圈检测由导电性材料制成的规则或不规则零部件的涡流检测方法。
2 规范性引用文件NB/T 47013.6-2015 承压设备无损检测第6部分:涡流检测。
3检测人员3.1 从事承压设备的非铁磁性性管涡流检测的人员,应按照《特种设备无损检测人员考核与监督管理规则》的要求取得涡流检测资格。
3.2 涡流检测人员资格级别分为III(高)级、II(中)级、I(初)级。
取得不同资格级别的人员,只能从事与该资格级别相应的涡流检测工作,并负相应的技术责任。
3.3 从事涡流检测的人员应具备一定的电磁方面的专业知识。
4 检测要求4.1 被检测区域应无润滑脂、油、锈或其他妨碍检测的物质;非磁性被检件表面不应有磁性粉末。
如不满足上述要求,应进行清除,清除时不应损伤被检零件的表面。
4. 2 检测表面应光滑,表面粗糙度不大于6.3μm,在对比试样人工缺陷上获得的信号与被检表面得到的噪声信号之比应不小于3:1。
4.3 被检部位的非导电覆盖层厚度一般不超过150μm,否则应釆用相近厚度非导电膜片覆盖在对比试样人工缺陷上进行检测灵敏度的补偿调整。
5 涡流检测系统涡流检测系统至少由涡流仪、探头和对比试样组成。
涡流检测系统可以是自动、半自动或手动检测系统。
5.1 涡流仪5.1.1 涡流仪应具有阻抗平面显示和时基显示方式。
5.1.2 应能够通过检测频率、晌应信号相位和增益的调节良好地对连续性感应产生的涡流相应变化。
5.2 探头5.2.1 涡流检测过程中应根据检测对象和检测要求,选择大小、形状和频率合适的涡流探头。
5.2.2 涡流检测可以采用屏蔽或非屏蔽的差动或绝对式涡流探头。
5.2.3 涡流探头不应对施加的压力变化产生干扰信号。
标题放置式线圈零部件涡流检测工艺规程5.2.4 探头标识应至少包括系列号、频率等信息。
5.2.5 为了防止探头的磨损,检测时可在探头顶部贴上耐磨的保护层。
5.2.6 检测过程中应随时检查探头的磨损情况,一旦发现磨损影响检测时,应停止使用。
涡流检测

涡流检测1 总则1.1 适用范围本通用工艺规定了承压设备涡流检测方法及质量分级要求,适用于承压设备用导电性金属材料和焊接接头表面及近表面缺陷检测。
1.2 引用标准、规程、法规GB/T 5126 铝及铝合金冷拉薄壁管材涡流探伤方法GB/T 5248 铜及铜合金无缝管涡流探伤方法GB/T 7735 钢管涡流探伤检验方法GB/T 12604.6 无损检测术语涡流检测GB/T 14480 涡流探伤系统性能测试方法JB/T4730.1 承压设备无损检测第1部分:通用要求2 一般要求2.1 检测系统2.1.1 涡流检测系统一般包括涡流检测仪、检测线圈及辅助装置(如磁饱和装置、机械传动装置、记录装置、退磁装置等)。
2.1.2 涡流检测系统应能以适当频率的交变信号激励检测线圈,并能够感应和处理检测线圈对被检测对象电磁特性变化所产生的响应。
2.1.3 涡流检测系统性能应满足本部分及相关标准要求,有关仪器性能的测试项目与测试方法参照GB/T 14480等的有关要求进行。
2.1.3.1 检测能力应满足产品验收标准或技术合同确定的要求。
2.1.3.2 对管材相同尺寸人工缺陷响应的周向灵敏度差应不大于3dB。
2.1.3.3 端部检测盲区应满足产品验收标准或技术合同的有关要求。
2.1.3.4 检测系统的缺陷分辨力一般应优于30mm,如果产品验收标准或技术合同另有明确要求,按产品验收标准或技术合同规定执行。
2.1.3.5 检测仪器应具有可显示检测信号幅度和相位的功能,仪器的激励频率调节和增益范围应满足检测要求。
2.1.4 检测线圈的形式和有关参数应与所使用的检测仪器、检测对象和检测要求相适应。
2.1.5 磁化装置应能连续对检测线圈通过的被检件或其局部进行饱和磁化处理。
若被检件不允许存在剩磁,磁化装置还应配备退磁装置,该装置应能有效去除被检件的剩磁。
2.1.6 机械传动装置应能保证被检件与检测线圈之间以规定的方式平稳地作相对运动,且不应造成被检件表面损伤,不应有影响检验信号的振动。
涡流测厚仪操作规程

涡流测厚仪操作规程第一章总则第一条为了保证涡流测厚仪的正常使用, 确保测厚结果的准确性和可靠性, 根据国家标准和相关要求制定本操作规程。
第二条涡流测厚仪用于测量金属或非金属表面的厚度, 适用于工业领域各个行业。
第三条涡流测厚仪的使用人员必须经过专业培训, 且取得相关证书, 方可独立操作。
第四条涡流测厚仪必须按照规定的操作规程进行使用, 不得擅自更改或改动。
第五条涡流测厚仪的操作人员必须严格按照操作规程进行操作, 确保实施安全。
第二章设备设施及其检查第六条涡流测厚仪应保持干燥、清洁、无尘、无水滴等环境。
第七条涡流测厚仪的电源应稳定、可靠, 电源线应完好, 无断裂、破损现象。
第八条涡流测厚仪应进行定期维护和校准, 确保设备工作正常。
第九条在使用前, 应对涡流测厚仪进行详细的检查, 确保各项指标符合要求。
第十条使用前还应对涡流测厚仪的测量头进行检查, 无磨损、破损、腐蚀等现象。
第三章操作流程第十一条涡流测厚仪的操作人员应仔细阅读操作说明书, 了解涡流测厚仪的使用方法和注意事项。
第十二条涡流测厚仪的操作人员应戴好防护手套、工作服和安全鞋, 确保人身安全。
第十三条涡流测厚仪的操作人员应将被测物体放置在水平的台面上, 避免测量误差。
第十四条打开涡流测厚仪的电源开关, 等待仪表启动, 确保仪表工作正常。
第十五条使用涡流测厚仪前, 应选用合适的测量探头, 并将其固定在测量头上。
第十六条将涡流测厚仪的测量头贴近被测物体的表面, 确保与表面紧密接触。
第十七条按下涡流测厚仪上的测量按钮, 开始进行厚度测量。
第十八条在测量过程中, 持续、平稳地移动涡流测厚仪的测量头, 以便全面测量。
第十九条在测量结束后, 按下涡流测厚仪上的停止按钮, 停止测量。
第四章注意事项第二十条涡流测厚仪的操作人员应注意仪器的防护, 避免碰撞、挤压, 保护仪器的完好。
第二十一条涡流测厚仪的使用人员应防止测量头的磨损和腐蚀, 严禁用硬物敲击测量头。
涡流检测通用工艺规程
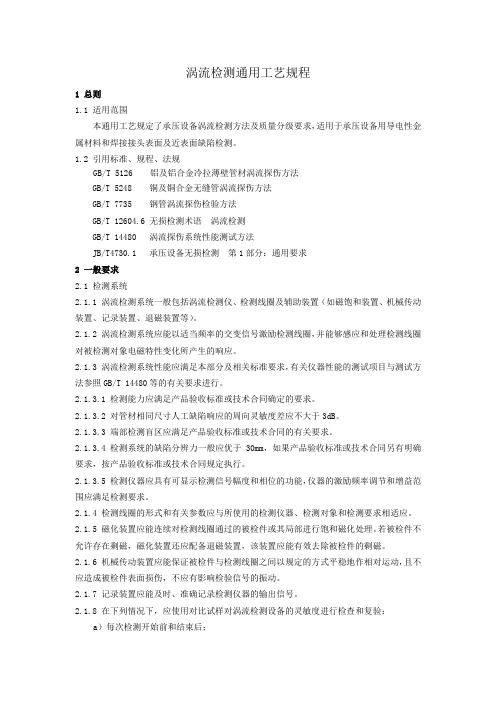
涡流检测通用工艺规程1 总则1.1 适用范围本通用工艺规定了承压设备涡流检测方法及质量分级要求,适用于承压设备用导电性金属材料和焊接接头表面及近表面缺陷检测。
1.2 引用标准、规程、法规GB/T 5126 铝及铝合金冷拉薄壁管材涡流探伤方法GB/T 5248 铜及铜合金无缝管涡流探伤方法GB/T 7735 钢管涡流探伤检验方法GB/T 12604.6 无损检测术语涡流检测GB/T 14480 涡流探伤系统性能测试方法JB/T4730.1 承压设备无损检测第1部分:通用要求2 一般要求2.1 检测系统2.1.1 涡流检测系统一般包括涡流检测仪、检测线圈及辅助装置(如磁饱和装置、机械传动装置、记录装置、退磁装置等)。
2.1.2 涡流检测系统应能以适当频率的交变信号激励检测线圈,并能够感应和处理检测线圈对被检测对象电磁特性变化所产生的响应。
2.1.3 涡流检测系统性能应满足本部分及相关标准要求,有关仪器性能的测试项目与测试方法参照GB/T 14480等的有关要求进行。
2.1.3.1 检测能力应满足产品验收标准或技术合同确定的要求。
2.1.3.2 对管材相同尺寸人工缺陷响应的周向灵敏度差应不大于3dB。
2.1.3.3 端部检测盲区应满足产品验收标准或技术合同的有关要求。
2.1.3.4 检测系统的缺陷分辨力一般应优于30mm,如果产品验收标准或技术合同另有明确要求,按产品验收标准或技术合同规定执行。
2.1.3.5 检测仪器应具有可显示检测信号幅度和相位的功能,仪器的激励频率调节和增益范围应满足检测要求。
2.1.4 检测线圈的形式和有关参数应与所使用的检测仪器、检测对象和检测要求相适应。
2.1.5 磁化装置应能连续对检测线圈通过的被检件或其局部进行饱和磁化处理。
若被检件不允许存在剩磁,磁化装置还应配备退磁装置,该装置应能有效去除被检件的剩磁。
2.1.6 机械传动装置应能保证被检件与检测线圈之间以规定的方式平稳地作相对运动,且不应造成被检件表面损伤,不应有影响检验信号的振动。
精密型涡流机操作规程(3篇)
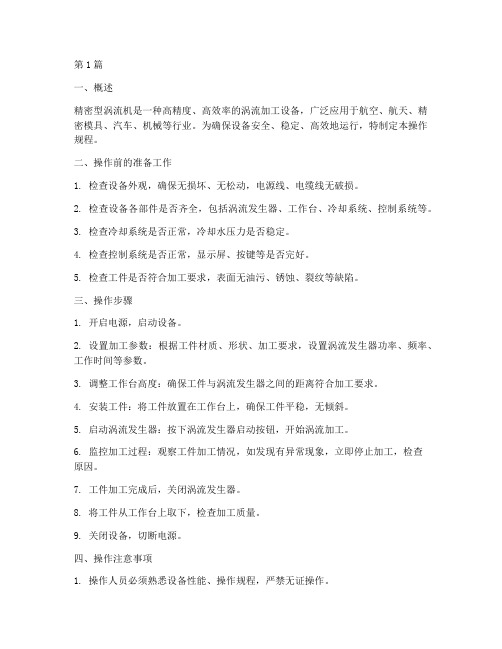
第1篇一、概述精密型涡流机是一种高精度、高效率的涡流加工设备,广泛应用于航空、航天、精密模具、汽车、机械等行业。
为确保设备安全、稳定、高效地运行,特制定本操作规程。
二、操作前的准备工作1. 检查设备外观,确保无损坏、无松动,电源线、电缆线无破损。
2. 检查设备各部件是否齐全,包括涡流发生器、工作台、冷却系统、控制系统等。
3. 检查冷却系统是否正常,冷却水压力是否稳定。
4. 检查控制系统是否正常,显示屏、按键等是否完好。
5. 检查工件是否符合加工要求,表面无油污、锈蚀、裂纹等缺陷。
三、操作步骤1. 开启电源,启动设备。
2. 设置加工参数:根据工件材质、形状、加工要求,设置涡流发生器功率、频率、工作时间等参数。
3. 调整工作台高度:确保工件与涡流发生器之间的距离符合加工要求。
4. 安装工件:将工件放置在工作台上,确保工件平稳,无倾斜。
5. 启动涡流发生器:按下涡流发生器启动按钮,开始涡流加工。
6. 监控加工过程:观察工件加工情况,如发现有异常现象,立即停止加工,检查原因。
7. 工件加工完成后,关闭涡流发生器。
8. 将工件从工作台上取下,检查加工质量。
9. 关闭设备,切断电源。
四、操作注意事项1. 操作人员必须熟悉设备性能、操作规程,严禁无证操作。
2. 操作过程中,严禁触摸涡流发生器、工作台等高温部件。
3. 设备运行时,严禁将手或物品伸入涡流发生器、工作台等区域。
4. 操作过程中,如发现设备异常,应立即停止操作,切断电源,检查原因。
5. 严禁在设备运行过程中调整加工参数。
6. 操作完毕后,清理设备,确保设备清洁、无油污。
五、维护保养1. 定期检查设备各部件,发现损坏、松动等现象,及时更换或紧固。
2. 定期检查冷却系统,确保冷却水压力稳定,冷却效果良好。
3. 定期检查控制系统,确保显示屏、按键等部件完好。
4. 定期检查涡流发生器,确保功率、频率等参数符合要求。
5. 定期检查工件夹具,确保夹具无损坏、无松动。
涡流测厚仪操作规程范本

涡流测厚仪操作规程范本一、概述涡流测厚仪是一种非接触式测厚仪器,主要用于测量金属材料的厚度,广泛应用于航空、航天、船舶、化工等行业。
为了确保涡流测厚仪的正常使用和保护仪器的安全性,制定了本操作规程。
二、仪器说明1. 仪器名称:涡流测厚仪2. 仪器型号、编号:[填写具体型号和编号]3. 仪器结构及工作原理:[填写仪器的结构和工作原理]4. 仪器技术指标:[填写仪器的技术指标]三、安全注意事项1. 使用前需对仪器进行安全检查,确保仪器正常工作。
2. 操作人员必须穿戴好防护装备,包括手套、眼镜等。
3. 使用涡流测厚仪时,应确保测量环境干燥、清洁,并远离易燃、易爆物品。
4. 禁止无证人员擅自使用仪器,以免造成人员伤害和财产损失。
四、操作步骤1. 准备工作(1)核对涡流测厚仪型号、编号是否正确。
(2)检查仪器的外观是否损坏,必要时进行维修或更换。
(3)检查仪器的电源是否正常工作。
(4)检查涡流测厚仪探头是否完好,需要更换时及时更换。
(5)确认测量环境干燥、清洁。
2. 开机与校准(1)接通仪器电源,等待仪器自检完成。
(2)根据涡流测厚仪说明书,进行仪器的校准。
确保仪器测量结果的准确性。
3. 测量操作(1)将仪器的探头贴紧待测物体表面。
(2)按下测量按钮,仪器开始测量。
(3)观察仪器显示屏上的测量结果,记录下测量值。
(4)将探头从待测物体上移开,继续对其他位置进行测量。
(5)测量结束后,按下停止按钮,关闭仪器。
4. 数据处理与记录(1)将测量得到的数据记录在指定的记录表格中。
(2)对于重要的测量数据,可以进行二次确认,以确保测量结果的准确性。
(3)将记录表格保存,并按照规定的程序进行归档。
五、仪器保养1. 每次使用后,应将仪器进行清洁,特别是探头部分。
2. 定期对涡流测厚仪进行校准,以确保测量结果的准确性。
3. 仪器长时间不使用时,应将仪器存放在干燥、通风的地方,避免灰尘或湿气进入仪器。
4. 定期对仪器进行维护保养,如更换电池、清洁电路板等。
涡流检测通用工艺规程(修订)
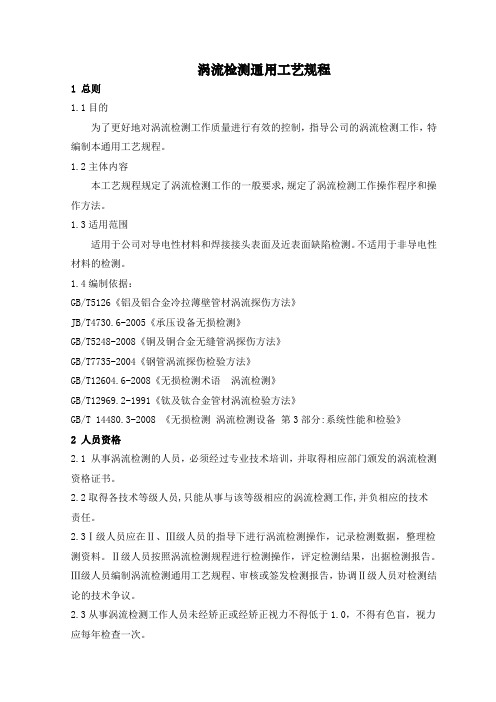
涡流检测通用工艺规程1 总则1.1目的为了更好地对涡流检测工作质量进行有效的控制,指导公司的涡流检测工作,特编制本通用工艺规程。
1.2主体内容本工艺规程规定了涡流检测工作的一般要求,规定了涡流检测工作操作程序和操作方法。
1.3适用范围适用于公司对导电性材料和焊接接头表面及近表面缺陷检测。
不适用于非导电性材料的检测。
1.4编制依据:GB/T5126《铝及铝合金冷拉薄壁管材涡流探伤方法》JB/T4730.6-2005《承压设备无损检测》GB/T5248-2008《铜及铜合金无缝管涡探伤方法》GB/T7735-2004《钢管涡流探伤检验方法》GB/T12604.6-2008《无损检测术语涡流检测》GB/T12969.2-1991《钛及钛合金管材涡流检验方法》GB/T 14480.3-2008 《无损检测涡流检测设备第3部分:系统性能和检验》2 人员资格2.1 从事涡流检测的人员,必须经过专业技术培训,并取得相应部门颁发的涡流检测资格证书。
2.2取得各技术等级人员,只能从事与该等级相应的涡流检测工作,并负相应的技术责任。
2.3Ⅰ级人员应在Ⅱ、Ⅲ级人员的指导下进行涡流检测操作,记录检测数据,整理检测资料。
Ⅱ级人员按照涡流检测规程进行检测操作,评定检测结果,出据检测报告。
Ⅲ级人员编制涡流检测通用工艺规程、审核或签发检测报告,协调Ⅱ级人员对检测结论的技术争议。
2.3从事涡流检测工作人员未经矫正或经矫正视力不得低于1.0,不得有色盲,视力应每年检查一次。
3 作业前的准备及应具备的条件:3.1检测前,应对被检工件的形状、尺寸、位置等有足够的了解,以便于合理选择检测系统及方法。
3.2检测作业场所附近不应有影响仪器设备正常工作的磁场、震动、腐蚀性气体及其他干扰。
3.3检测作业场所附近不得有火源、易燃、易爆品等。
3.4实施检测的场地温度和相对湿度应控制在仪器设备和被检件允许的范围内。
4 设备、工具和材料:4.1涡流检测系统及要求4.1.1涡流检测系统一般包括涡流检测仪(表1)、检测线圈及辅助装置(如记录装置等)。
涡流测厚仪操作规程模版

涡流测厚仪操作规程模版一、目的和适用范围本操作规程适用于涡流测厚仪的使用和操作。
涡流测厚仪是一种用于测量金属或合金材料薄壁厚度的装置,可以广泛应用于工业生产和质量监测中。
本规程旨在规范涡流测厚仪的使用和操作,确保测量结果的准确性和可靠性。
二、定义和缩写1. 涡流测厚仪:一种利用涡流原理测量金属或合金材料薄壁厚度的装置。
2. 送检件:待测量的金属或合金材料薄壁件。
3. 测厚仪:涡流测厚仪。
4. 壁厚:指金属或合金材料薄壁的厚度。
三、操作流程1. 准备工作(1)确认送检件的材料和尺寸,并与实际测量要求进行对比。
(2)检查涡流测厚仪的电源是否正常,仪器是否完好,各个部位是否松动或堵塞。
(3)根据实际测量要求选择合适的涡流探头,并安装在测厚仪上。
2. 开机和校准(1)接通涡流测厚仪的电源,并按照操作说明进行开机。
(2)选择校准功能并按照操作说明进行校准。
(3)校准完毕后,进行零点校准,确保测量结果的准确性。
3. 测量操作(1)将送检件放置在水平台上,并用夹具夹住。
(2)将涡流探头贴近送检件的表面,并使探头与检测区域垂直。
(3)按下测量按钮开始测量,待测量结果稳定后,记录测量值。
(4)根据需要,可进行多次测量并记录平均值。
4. 出口结果(1)测量结果可以通过涡流测厚仪的显示屏进行直接读数。
(2)也可以通过打印机或数据接口将测量结果导出。
5. 关机和维护(1)测量完毕后,先关闭涡流测厚仪的测量功能,再断开电源。
(2)对仪器进行清洁和维护,确保仪器的正常使用和寿命。
四、操作注意事项1. 涡流测厚仪的使用和操作必须由经过培训并具有相关资质的人员进行。
2. 在操作涡流测厚仪之前,必须对送检件进行外观检查和准备工作,确保送检件的表面干净、平整且无损伤。
3. 使用涡流测厚仪时,必须选择合适的探头,探头与检测区域的接触要紧密,避免探头移动或摆动。
4. 测量过程中,要保持送检件和探头的稳定,防止出现震动、摇晃或变形等情况。
小径管涡流检测专用工艺
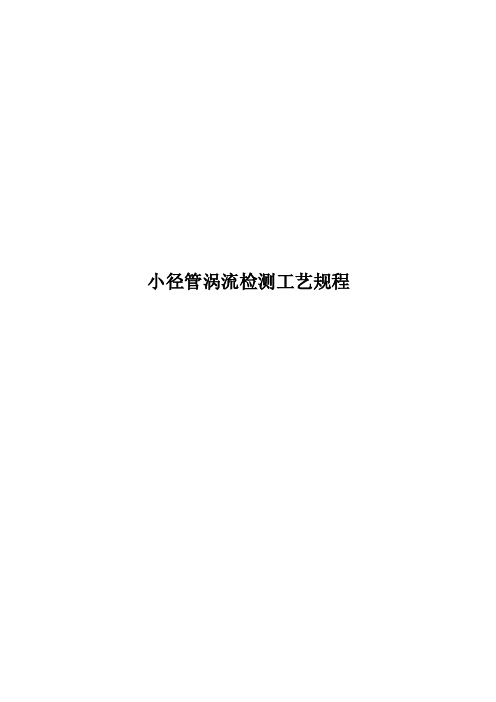
小径管涡流检测工艺规程小径管涡流检测工艺规程1 检测原理涡流探伤是以电磁感应原理为基础的。
当管件经过交流电的线圈时,管件的不连续(如缺陷等)将使涡流场发生变化,而以靠近表层和近表层影响最大,导致线圈阻抗或感应电压产生变化,检测这一变化就可得到有关管件缺陷或不连续性的信息。
2 适用范围:一般是用于管径4~100mm的表面和近表面缺陷的探伤。
3 检验方法:涡流探伤一般分为穿过式线圈探伤和放置式(点式)线圈探伤两种方法。
3.1 穿过式线圈探伤:注:图示是一种多线圈方案的简图,多线圈可以是分列式或初级线圈、双差动线圈等图1 穿过式线圈涡流检测示意图a.根据被检件规格选择适当规格尺寸线圈,采用被检件与检测线圈作相对匀速直线运动的方式进行检验。
b.为了抑制铁磁性材料磁性不均匀对检验结果的影响,检验时须采用磁饱和技术,检验后应进行有效的退磁。
3.2放置式(点式)线圈探伤:a. 根据检件规格选择适当尺寸的旋转头或探头支架,采用圆钢与线圈作相对匀速旋转运动或匀速直线运动的方式进行检验。
b. 检验时保证良好的同心度,注意克服提离效应的影响,保证正常检验时缺陷信幅度波动不大于2dB。
3.3 检验结果评定采用自然缺陷信与人工缺陷信当量比较法。
4 仪器设备:涡流检验用仪器设备一般包括探伤仪、检测线圈、机械传动装置、记录装置和磁化装置。
探伤仪: 涡流探伤仪分为便携式和非便携式的单频、双频或多频涡流探伤仪、探伤仪主要由激励单元、信号处理单元和显示单元组成:a. 激励单元应能产生足够幅值和适当频率的交变电流b. 通过调节信号处理单元,应能明显区分试祥上的人工缺陷信号和嗓声信号c. 显示单元应能监视检验结果,显示缺陷信号的幅值或幅值与相位。
当缺陷信号等于或大于验收水平时,需有声音和(或)灯光报警指示。
5 探头: 涡流检验探头一般分为外穿探头、内穿探头、远扬探头、点式探头以及焊缝专用探头。
在绝对模式、1KHz~1MHz频率下工作,在被检工件或校准试块上提离时应能在仪器上产生满屏提离信号。
2023年涡流测厚仪操作规程

2023年涡流测厚仪操作规程涡流测厚仪操作规程第一章总则第一条为了规范和保证涡流测厚仪的安全使用,确保测量结果准确可靠,特制定本操作规程。
第二条本操作规程适用于2023年使用的涡流测厚仪操作。
第三条涡流测厚仪操作人员必须接受相关培训,具备相应的实际操作经验,方可进行操作。
第四条涡流测厚仪应定期进行校验检测,确保其测量准确度符合要求。
第五条涡流测厚仪在使用前必须进行外观检查,确认其完好无损。
第六条涡流测厚仪在使用过程中应严格按照操作规程进行操作,不得随意更改参数或使用错误操作方法。
第七条涡流测厚仪操作过程中发现问题应及时报修,不得使用故障设备。
第八条涡流测厚仪应放置在干燥、通风良好的场所,远离高温、潮湿等有害环境。
第九条涡流测厚仪的使用单位应建立相应的档案记录,包括设备购置、校验、维护保养等情况。
第十条涡流测厚仪应经常进行维护保养,确保设备长期稳定可靠的工作。
第二章操作要求第十一条涡流测厚仪操作人员必须清楚了解涡流测厚仪的测量原理和工作原理。
第十二条在进行测量前,涡流测厚仪的传感器必须经过预热,保证传感器的稳定性。
第十三条确保被测对象的工作温度必须在涡流测厚仪的工作温度范围内,避免温度变化对测量结果的影响。
第十四条涡流测厚仪的工作电源必须稳定,否则会影响测量的准确度。
第十五条在进行实际测量前,首先应选择适当的探头,并进行充分测试,确保探头的工作状态正常。
第十六条涡流测厚仪的测量位置应选取平整、光滑的表面,避免边角等位置对测量结果的影响。
第十七条涡流测厚仪应与被测对象保持良好的接触,确保传感器与被测表面完全贴合。
第十八条涡流测厚仪的测量速度应适中,不得过快或过慢,以避免测量结果的不准确。
第十九条在测量过程中应注意测量结果的稳定性,避免外部因素对测量的影响。
第二十条涡流测厚仪测量结束后,应及时关闭设备,避免长时间空转浪费能源。
第三章安全措施第二十一条操作人员必须佩戴个人防护装备,确保自身安全。
第二十二条涡流测厚仪操作过程中,禁止使用金属制品作为敲击物,以免损坏传感器。
涡流检测(indoc整理)

常规涡流检测使用的频率较高(几百到几兆赫兹),渗透深度通常
较浅,因此常规涡流检测是一种表面或近表面的无损检测方法。
第五章 涡流检测 (Eddy Current Tes.)
内 容
5.1涡流检测的基本原理 5.2 涡流检测的阻抗分析法 5.3 涡流检测的应用
前 言
利用电磁感应原理,通过检测被检工件内感生涡流的变
化来无损地评定导电材料及其工件的某些性能,或发现缺陷
的无损检测方法称为涡流检测。 涡流检测是控制各种金属材料及少数非金属导电材料 (如石墨)及其产品品质的主要手段之一。与其他无损检测 方法相比,涡流检测更容易实现检测自动化,特别是对管材、
Z :阻抗,单位为欧姆 R :电阻,单位为欧姆 X :电抗,单位为欧姆 j 是虚数单位
Z R jX
电感L
线圈在磁通发生变化时能产生电动势e,
线圈匝数
d d e N dt dt N Li
电感
磁链
磁通
N L i i
互感M
当线圈1中的电流变化时所激发的变化磁场,会在它相邻的 另一线圈2中产生感应电动势;同样,线圈2中上的电流变化时, 也会在线圈1中产生感应电动势。这种现象称为互感现象,以互 感系数M表示,简称互感。所产生的感应电动势称为互感电动势。
Z0 R1 jX1 R1 jL1
空载阻抗
电阻
电抗
初级线圈
次级线圈
线圈耦合互感电路
当初级线圈与次级线圈(被检对象)相互耦合时,由于互感的 作用,闭合的次级线圈中会产生感应电流,而这个电流反过来又 会影响初级线圈中的电压和电流。这种影响可以用次级线圈电路 阻抗通过互感M反映到初级线圈电路的等效阻抗Ze来体现。Z0与 Ze之和Z称为初级线圈的视在阻抗。
涡流机操作规程(3篇)
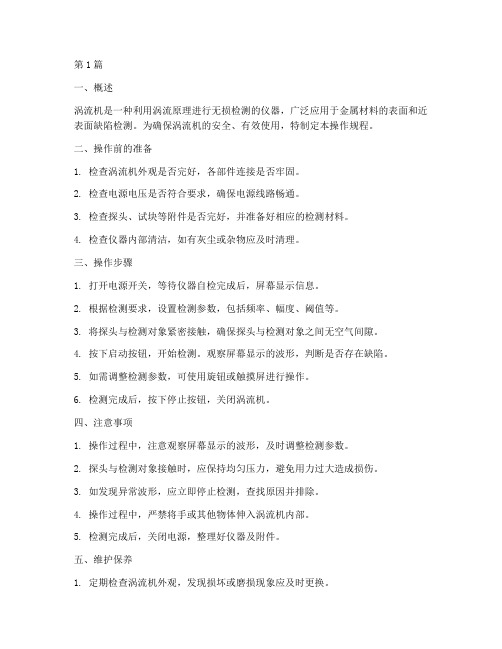
第1篇一、概述涡流机是一种利用涡流原理进行无损检测的仪器,广泛应用于金属材料的表面和近表面缺陷检测。
为确保涡流机的安全、有效使用,特制定本操作规程。
二、操作前的准备1. 检查涡流机外观是否完好,各部件连接是否牢固。
2. 检查电源电压是否符合要求,确保电源线路畅通。
3. 检查探头、试块等附件是否完好,并准备好相应的检测材料。
4. 检查仪器内部清洁,如有灰尘或杂物应及时清理。
三、操作步骤1. 打开电源开关,等待仪器自检完成后,屏幕显示信息。
2. 根据检测要求,设置检测参数,包括频率、幅度、阈值等。
3. 将探头与检测对象紧密接触,确保探头与检测对象之间无空气间隙。
4. 按下启动按钮,开始检测。
观察屏幕显示的波形,判断是否存在缺陷。
5. 如需调整检测参数,可使用旋钮或触摸屏进行操作。
6. 检测完成后,按下停止按钮,关闭涡流机。
四、注意事项1. 操作过程中,注意观察屏幕显示的波形,及时调整检测参数。
2. 探头与检测对象接触时,应保持均匀压力,避免用力过大造成损伤。
3. 如发现异常波形,应立即停止检测,查找原因并排除。
4. 操作过程中,严禁将手或其他物体伸入涡流机内部。
5. 检测完成后,关闭电源,整理好仪器及附件。
五、维护保养1. 定期检查涡流机外观,发现损坏或磨损现象应及时更换。
2. 定期清理仪器内部灰尘,保持仪器清洁。
3. 定期检查电源线路,确保线路畅通。
4. 如长时间不使用,应将仪器存放在干燥、通风的环境中。
5. 定期对涡流机进行校准,确保检测精度。
六、安全注意事项1. 操作过程中,注意观察涡流机运行状态,发现异常情况立即停止操作。
2. 操作人员应熟悉涡流机操作规程,确保安全操作。
3. 操作人员应佩戴防护眼镜,避免检测过程中眼睛受到伤害。
4. 仪器运输、搬运过程中,注意轻拿轻放,防止碰撞。
5. 操作人员应了解涡流机相关安全知识,提高安全意识。
本规程适用于涡流机的操作、维护保养及安全注意事项,操作人员应严格遵守。
涡流检测
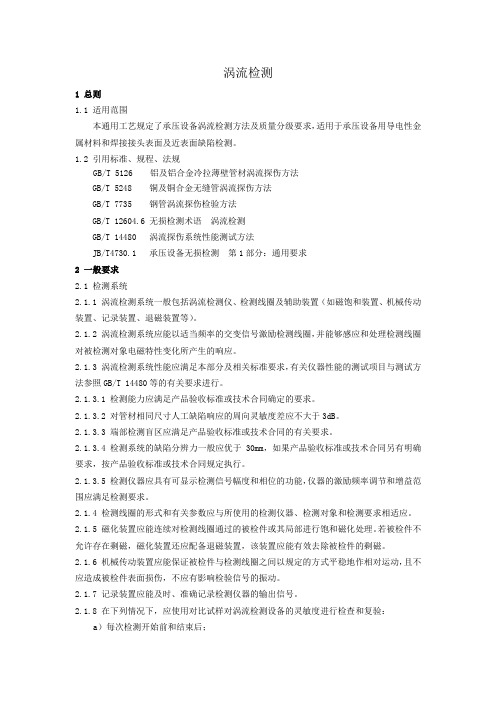
涡流检测1 总则1.1 适用范围本通用工艺规定了承压设备涡流检测方法及质量分级要求,适用于承压设备用导电性金属材料和焊接接头表面及近表面缺陷检测。
1.2 引用标准、规程、法规GB/T 5126 铝及铝合金冷拉薄壁管材涡流探伤方法GB/T 5248 铜及铜合金无缝管涡流探伤方法GB/T 7735 钢管涡流探伤检验方法GB/T 12604.6 无损检测术语涡流检测GB/T 14480 涡流探伤系统性能测试方法JB/T4730.1 承压设备无损检测第1部分:通用要求2 一般要求2.1 检测系统2.1.1 涡流检测系统一般包括涡流检测仪、检测线圈及辅助装置(如磁饱和装置、机械传动装置、记录装置、退磁装置等)。
2.1.2 涡流检测系统应能以适当频率的交变信号激励检测线圈,并能够感应和处理检测线圈对被检测对象电磁特性变化所产生的响应。
2.1.3 涡流检测系统性能应满足本部分及相关标准要求,有关仪器性能的测试项目与测试方法参照GB/T 14480等的有关要求进行。
2.1.3.1 检测能力应满足产品验收标准或技术合同确定的要求。
2.1.3.2 对管材相同尺寸人工缺陷响应的周向灵敏度差应不大于3dB。
2.1.3.3 端部检测盲区应满足产品验收标准或技术合同的有关要求。
2.1.3.4 检测系统的缺陷分辨力一般应优于30mm,如果产品验收标准或技术合同另有明确要求,按产品验收标准或技术合同规定执行。
2.1.3.5 检测仪器应具有可显示检测信号幅度和相位的功能,仪器的激励频率调节和增益范围应满足检测要求。
2.1.4 检测线圈的形式和有关参数应与所使用的检测仪器、检测对象和检测要求相适应。
2.1.5 磁化装置应能连续对检测线圈通过的被检件或其局部进行饱和磁化处理。
若被检件不允许存在剩磁,磁化装置还应配备退磁装置,该装置应能有效去除被检件的剩磁。
2.1.6 机械传动装置应能保证被检件与检测线圈之间以规定的方式平稳地作相对运动,且不应造成被检件表面损伤,不应有影响检验信号的振动。
涡流测厚仪操作规程通用版

操作规程编号:YTO-FS-PD406涡流测厚仪操作规程通用版In Order T o Standardize The Management Of Daily Behavior, The Activities And T asks Are Controlled By The Determined Terms, So As T o Achieve The Effect Of Safe Production And Reduce Hidden Dangers.标准/ 权威/ 规范/ 实用Authoritative And Practical Standards涡流测厚仪操作规程通用版使用提示:本操作规程文件可用于工作中为规范日常行为与作业运行过程的管理,通过对确定的条款对活动和任务实施控制,使活动和任务在受控状态,从而达到安全生产和减少隐患的效果。
文件下载后可定制修改,请根据实际需要进行调整和使用。
1 清除净被测物件上的污物、尘土和水。
将仪器的探头擦拭干净。
2 按下开关键,仪器自检完毕发出一鸣音,显示”0 0”便可以进行测量操作。
3 将探头平稳、垂直地放落在被测件上,待仪器鸣叫一声,显示器上便显示出涂层的厚度值。
然后再抬头高探头,重新落下,进行下一次测量这样反复5—10次,就可以完成一个测量序列。
4 在测试过程中,如因探头放置不平稳,或探头太脏等原因,显示出明显的错误值,此时应按下清除键,将错误值删除。
否则将影响整体测试结果的准确性。
5 按统计键5次,可顺次显示出以下统计数:MEAN—平均值;MAX—最大值;MIN—最小值;S—标准偏差;N—测量次数。
6 统计程序完成后,可接着进行下一次测量序列。
若需要获得更多的连续统计数据,只要按两次上调键时,接着再进行测量,则测量出的数据和以前的数据是连续累加的。
7 在测量过程中,若误按校准键时,可再连续按2次该键以便消除校正状态。
若误按校后又进行了测量,可先用清除键将前次的数字删去(按一次清除键则删除前一个数字,连按二次则将前面的全部误测数8 在测试过程中,如果出现负数值,要用清除键将其删去。
涡流测厚仪操作规程范文

涡流测厚仪操作规程范文一、目的和范围本操作规程是为了规范涡流测厚仪的操作流程,确保仪器的正确使用和测量结果的准确性。
适用于涡流测厚仪的日常操作和维护。
二、设备及材料1. 涡流测厚仪:包括主机、传感器等组成。
2. 参考块:标定用的金属块,用于校准仪器。
三、操作程序1. 准备工作(1)检查涡流测厚仪的配件是否完整,主机和传感器是否工作正常。
(2)确认待测物表面光洁,无腐蚀、氧化层等影响测量的情况。
(3)校准涡流测厚仪:a. 将涡流测厚仪主机与参考块相连。
b. 打开涡流测厚仪主机电源,按照说明书进行校准操作。
c. 调节涡流测厚仪主机的增益,使得显示屏上的读数与参考块上的标定值尽量接近或相等。
d. 校准完成后,关闭涡流测厚仪主机电源。
2. 测量操作(1)将传感器与涡流测厚仪主机连接好,并确保连接牢固。
(2)打开涡流测厚仪主机电源。
(3)将传感器贴近待测物的表面,并使其垂直于表面放置。
(4)观察涡流测厚仪主机的显示屏,并记录读数。
(5)测量完成后,关闭涡流测厚仪主机电源。
3. 结果处理(1)将测量得到的读数与参考块上的标定值进行比对,如果误差较大,则需要重新校准或检查仪器是否故障。
(2)记录测量结果,包括待测物的位置、测量时间、测厚值等信息。
(3)根据测量结果判断待测物的厚度是否符合要求,如不符合,需要采取相应的措施。
四、操作注意事项1. 操作前应充分了解涡流测厚仪的使用方法和注意事项。
2. 注意保持测量环境的干净和安静,以避免干扰测量结果。
3. 涡流测厚仪的传感器不能与待测物表面产生间隙,否则会影响测量结果的准确性。
4. 涡流测厚仪的传感器不可碰撞、摔落或受到其他机械损伤。
5. 测量时需按照操作规程进行,不得随意更改参数或操作流程。
6. 测量结果需经过验证和比对,确保准确性和可靠性。
五、维护保养1. 涡流测厚仪主机和传感器应定期进行检查和维护,发现问题及时修复或更换。
2. 在不使用涡流测厚仪时,应将主机电源关闭,并妥善存放,避免受潮、受热、受灰尘等。
涡流测厚仪操作规程

涡流测厚仪操作规程第一章总则第一条为了规范涡流测厚仪的使用,确保测量的准确性和安全性,特制定本操作规程。
第二条本规程适用于所有使用涡流测厚仪进行厚度测量工作的人员。
第二章涡流测厚仪的构成与工作原理第三条涡流测厚仪由主机、传感器和计算机组成。
第四条涡流测厚仪的工作原理是利用涡流感应现象,通过电磁感应原理测量导电材料的厚度。
第三章涡流测厚仪的检查与准备第五条使用涡流测厚仪前,应检查仪器是否完好,传感器是否正常工作。
第六条涡流测厚仪的电源应接入稳定的电源,防止因电压不稳造成测量误差。
第七条检查涡流测厚仪的传感器是否与测量材料接触良好,杜绝杂质的干扰。
第四章涡流测厚仪的操作流程第八条打开涡流测厚仪电源,并按照仪器说明书进行启动操作。
第九条选择合适的传感器,并将其与测量材料接触。
第十条选取正确的工作模式和测量范围。
第十一条调节仪器的增益和滤波器,确保信号清晰可靠。
第十二条按下开始测量按钮,记录测量数值。
第十三条测量完成后,关闭涡流测厚仪电源,并进行相关数据处理和存储。
第五章涡流测厚仪的注意事项第十四条在使用过程中,应严格按照仪器操作规程进行操作,避免误操作造成仪器损坏。
第十五条使用涡流测厚仪时,应保持测量环境的稳定,避免外界干扰对测量结果造成影响。
第十六条测量前应确保测量材料及测量部位清洁,避免杂质对测量结果的干扰。
第十七条使用涡流测厚仪时,应注意安全,避免触电和其他安全事故的发生。
第十八条定期对涡流测厚仪进行维护和检修,保证仪器的正常工作。
第六章涡流测厚仪的维护与保养第十九条涡流测厚仪应定期进行校准,确保测量精确度。
第二十条保持涡流测厚仪的清洁,防止灰尘和污垢的积累。
第二十一条定期检查传感器的接触情况和状态,确保正常工作。
第二十二条使用完毕后,及时将涡流测厚仪存放到安全、干燥的地方。
第七章处理涡流测厚仪故障第二十三条如果涡流测厚仪出现故障,应立即停止使用,并由专业人员进行维修。
第二十四条在维修期间,应注意保护涡流测厚仪,避免进一步损坏。
NBT47013涡流检测通用工艺规程

目录1主题内容和适用范围 (2)2依据标准 (2)3人员要求 (2)4检测设备和器材 (3)4.1检测仪器和检测线圈及辅助装置 (3)4.2涡流检测系统的组合性能 (3)4.3对比试样 (4)4.4备检工件 (4)4.5检测环境 (5)5安全要求 (5)5.1防止电流短路引起的电击造成人体伤害。
(5)5.2防止检测现场温度、湿度、有害环境造成人体伤害。
(5)6检测施工流程 (5)6.1检测施工流程图 (5)6.2实施检测过程说明 (6)7工艺文件及附属文件要求 (7)7.1工艺规程 (7)7.2操作指导书 (8)8铁磁性管材涡流检测 (10)8.1适用范围 (10)8.2对比试样 (10)8.3检测程序 (11)9非铁磁性管材涡流检测 (11)9.1适用范围 (11)9.2对比试样 (11)9.3检测设备 (13)9.4检测程序 (13)涡流检测工艺规程1主题内容和适用范围1.1本规程规定了涡流检测人员资格、仪器、探头、对比试样、检测范围、检测方法和质量分级等。
1.2本规程依据NB/T47013.6的要求编写,采用EEC35++型涡流检测仪器,满足引用标准中相关标准、规范的要求。
适用于在制和在用承压设备用导电金属材料管材、零部件、焊接接头表面及近表面缺陷的涡流测量方法,适用于金属基体表面覆盖层厚度的磁性法和涡流法检测。
1.3本规程与工程所要求执行的有关标准、规范、施工技术文件有抵触时,应以有关标准、规范、施工技术文件为准。
2依据标准2.1 TSG Z8001 特种设备无损检测人员考核规则2.2 GB/T5126 铝及铝合金冷拉薄壁管材涡流探伤方法2.3 GB/T5248 铜及铜合金无缝管涡流探伤方法2.4 GB/T7735 钢管涡流探伤检验方法2.5 GB/T12406.6 无损检测术语涡流检测2.6 GB/T12969.2 钛及钛合金管材涡流探伤方法2.7 NB/T47013.1 承压设备无损检测第1部分:通用部分2.8 NB/T47013.6 承压设备无损检测第6部分:涡流检测以上文件以其当前有效版本为准,其最新版本也适用于本工艺规程。
- 1、下载文档前请自行甄别文档内容的完整性,平台不提供额外的编辑、内容补充、找答案等附加服务。
- 2、"仅部分预览"的文档,不可在线预览部分如存在完整性等问题,可反馈申请退款(可完整预览的文档不适用该条件!)。
- 3、如文档侵犯您的权益,请联系客服反馈,我们会尽快为您处理(人工客服工作时间:9:00-18:30)。
涡流检测通用工艺规程1 总则1.1目的为了更好地对涡流检测工作质量进行有效的控制,指导公司的涡流检测工作,特编制本通用工艺规程。
1.2主体内容本工艺规程规定了涡流检测工作的一般要求,规定了涡流检测工作操作程序和操作方法。
1.3适用范围适用于公司对导电性材料和焊接接头表面及近表面缺陷检测。
不适用于非导电性材料的检测。
1.4编制依据:GB/T5126《铝及铝合金冷拉薄壁管材涡流探伤方法》JB/T4730.6-2005《承压设备无损检测》GB/T5248-2008《铜及铜合金无缝管涡探伤方法》GB/T7735-2004《钢管涡流探伤检验方法》GB/T12604.6-2008《无损检测术语涡流检测》GB/T12969.2-1991《钛及钛合金管材涡流检验方法》GB/T 14480.3-2008 《无损检测涡流检测设备第3部分:系统性能和检验》2 人员资格2.1 从事涡流检测的人员,必须经过专业技术培训,并取得相应部门颁发的涡流检测资格证书。
2.2取得各技术等级人员,只能从事与该等级相应的涡流检测工作,并负相应的技术责任。
2.3Ⅰ级人员应在Ⅱ、Ⅲ级人员的指导下进行涡流检测操作,记录检测数据,整理检测资料。
Ⅱ级人员按照涡流检测规程进行检测操作,评定检测结果,出据检测报告。
Ⅲ级人员编制涡流检测通用工艺规程、审核或签发检测报告,协调Ⅱ级人员对检测结论的技术争议。
2.3从事涡流检测工作人员未经矫正或经矫正视力不得低于1.0,不得有色盲,视力应每年检查一次。
3 作业前的准备及应具备的条件:3.1检测前,应对被检工件的形状、尺寸、位置等有足够的了解,以便于合理选择检测系统及方法。
3.2检测作业场所附近不应有影响仪器设备正常工作的磁场、震动、腐蚀性气体及其他干扰。
3.3检测作业场所附近不得有火源、易燃、易爆品等。
3.4实施检测的场地温度和相对湿度应控制在仪器设备和被检件允许的范围内。
4 设备、工具和材料:4.1涡流检测系统及要求4.1.1涡流检测系统一般包括涡流检测仪(表1)、检测线圈及辅助装置(如记录装置等)。
表1 涡流检测仪一览表4.1.2 涡流检测系统应能以适当频率的交变信号激励检测线圈,并能够感应和处理检测线圈对被检测对象磁特性变化所产生的影响。
4.1.3涡流检测系统性能应满足相关标准要求,有关仪器性能的测试项目与测试方法参照GB/T14480的有关要求进行。
(1)检测能力应满足产品验收标准或技术合同确定的要求。
(2)对管材相同尺寸人工缺陷响应的周向灵敏度差应不大于3dB。
(3)端部检测盲区应满足产品验收标准或技术合同的相关要求。
(4)检测系统的缺陷分辨力一般应优于30mm,如果产品验收标准或技术合同另有明确要求,按产品验收标准或技术合同规定执行。
(5)检测仪器应具有可显示检测信号幅度和相位的功能,仪器的激励频率调节和增益范围应满足检测要求。
4.1.4检测线圈的形式和有关参数应与所使用的检测仪器、检测对象和检测要求相适应。
4.1.5记录装置应能及时、准确记录检测仪器的输出信号。
4.2对比式样4.2.1对比试样主要用于调节涡流检测仪检测灵敏度、确定验收水平和保证检测结果准确性。
4.2.2 对比试样应与被检对象具有相同或相近规格、牌号、热处理状态、表面状态和电磁性能。
4.2.3 对比试样上加工的人工缺陷应采用适当的方法进行测定,并满足相关标准或技术条件的要求。
4.2.4 对比试样上人工缺陷的尺寸不应解释为检测设备可以探测到的缺陷的最小尺寸。
4.3辅助材料4.3.1检测所用的辅助材料见表2。
表2 辅助材料4.4安全器具4.4.1安全器具见表3。
表3 安全器具4.5被检工件4.5.1被检工件表面应清洁、无毛刺,不应有影响实施涡流检测的粉尘及其他污物,特别是铁磁性粉屑;如不满足要求,应加以清除,清除时不应损坏被检件表面。
4.5.2 被检工件表面粗糙度、尺寸公差、弯曲度等参数应满足相关产品技术条件要求。
5 作业程序、方法和内容5.1铁磁性钢管的涡流检测5.1.1本条规定了承压设备用铁磁性无缝钢管、焊接钢管(埋弧焊钢管除外)等管材产品的涡流检测方法。
适用于外径不小于4mm 钢管的涡流检测。
验收等级分为A 级和B 级,见表4。
表4 对比试样通孔直径 mm5.1.2对比试样上人工缺陷的形状为通孔或槽。
5.1.2.1通孔是在在对比试样钢管中部加工3个通孔,对于焊接钢管至少应有1个孔在焊缝上,沿圆周方向相隔120°±5°对称分布,轴向间距不小于200mm 。
此外,在对比试样钢管端部小于等于200mm 处,加工2个相同尺寸的通孔,以检查端部效应,见图1。
图1 对比试样上通孔位置注:钻孔时应保持钻头稳定,防止局部过热和表面产生毛刺。
当钻头直径小于1.10mm 时,其钻孔直径不得比规定值大0.10mm 。
当钻头直径不小于1.10mm 时,其钻孔直径不得比规定值大0.20mm 。
5.1.2.2槽是在管子上加工形状为纵向矩形槽,平行于钢管的主轴线。
槽的宽度不大于1.5mm ,长度为25mm ,其深度为管子公称壁厚的5%,最小深度为0.3mm ,最大深度为1.3mm 。
深度允许偏差为槽深的±15%,或者是±0.05mm ,取其大者。
5.1.3根据被检产品、作业条件、可户要求等选择检测方法(如内穿过式、外穿过式、放置式等)。
5.1.4铁磁性钢管涡流检测的频率在1-500kHz范围内选择。
5.1.5检测线圈的内径或外径与被检管材的内外径相匹配,其填充系数大于或等于0.6。
5.1.5检测设备通电后,应进行不低于10min的系统预运转。
5.1.6在于检验条件相同的条件下,调节检验设备,使对比试样通过探头时,仪器显示出清晰可辨的人工标准缺陷信号。
5.1.7按规定的验收水平调整灵敏度时,信噪比应不小于6dB。
作为产品验收或质量等级评定的人工缺陷响应信号的幅度应在仪器荧光屏满刻度的30%~50%。
对比试样和检测线圈之间的相对移动速度应与被检钢管与检测线圈之间的实际相对移动速度相同。
5.1.8对比试样中间3个对称通孔的显示幅度应基本一致,选取最低幅度作为检测设备的触发报警电平。
5.1.9采用记录报警时,三个人工标准缺陷的显示幅度应基本一致,相差不大于平均幅度的±10%。
三个人工标准缺陷信号应调到记录满幅度的50%-70%之间的某一幅度,其差别应不大于平均记录幅度的±10%,选取其中最低的幅度为记录标准报警幅度。
此时信号应处于仪器记录仪组合的线性区内。
5.2非铁磁性金属管材涡流检测5.2 1本条适用于非铁磁性金属管材产品的涡流检测方法。
对于铜及铜合金无缝管,可检测管材的壁厚小于等于3mm,外径小于等于50mm;对于铝及铝合金管,可检测管材的壁厚小于等于2mm,外径小于等于38mm;对于钛及钛合金管,可检测管材的壁厚小于等于4.5mm,外径小于等于30mm。
其他规格的管材制品可参照此条执行。
5.2.2对比试样5.2.1.1铜及铜合金的对比试样人工缺陷为垂直于管壁的通孔。
沿轴向加工5个相同孔径的通孔,其中,2个通孔分别距离管端小于等于100mm,中间3个通孔之间的间距为500mm±10mm,并沿圆周方向相隔120°±5°分布,见图2。
图2 对比试样上通孔位置5.2.1.2人工缺陷的孔径尺寸与被检管材外径的对应关系应符合表5的规定。
孔径偏差不大于±0.05mm 。
表5 无缝铜及铜合金对比试样管人工缺陷的孔径尺寸(mm )5.2.1.3铝及铝合金对比试样上人工缺陷为垂直于管壁的通孔,沿轴向加工5个相同孔径的通孔,其中,2个通孔分别距离管端100mm ±5mm ,中间3个通孔之间的间距为150mm ±10mm 并周向相隔120°±5°分布,见图6。
图3 对比试样管规格及相应通孔位置5.2.1.4人工缺陷的孔径尺寸与被检管材外径的对应关系应符合表6的规定,孔径偏差±0.05mm 。
表6 铝及铝合金对比试样管人工缺陷的孔径尺寸5.2.1.5钛及钛合金对比试样上人工缺陷为垂直于管壁的通孔。
沿轴向加工5个相同孔径的通孔,其中,2个通孔分别距离管端100mm±5mm,中间3个通孔之间的间距为300mm~500mm,并沿圆周方向相隔120°±5°分布,参见图1。
对比试样上通孔直径为0.8 mm±0.05mm。
5.2.2根据被检产品、作业条件、可户要求等选择检测方法(如内穿过式、外穿过式、放置式等)。
5.2.3非铁磁性金属管材涡流检测的频率在1-125kHz范围内选择。
5.2.4检测线圈的内径或外径与被检管材的内外径相匹配,其填充系数大于或等于0.6。
5.2.5检测设备通电后,应进行不低于10min的系统预运转。
5.2.6在于检验条件相同的条件下,调节检验设备,使对比试样通过探头时,仪器显示出清晰可辨的人工标准缺陷信号。
5.1.7按规定的验收水平调整灵敏度时,铜及铜合金信噪比应不小于10dB,铝及铝合金钛及钛合金信噪比应不小于6dB,。
作为产品验收或质量等级评定的人工缺陷响应信号的幅度应在仪器荧光屏满刻度的30%~50%。
对比试样和检测线圈之间的相对移动速度应与被检钢管与检测线圈之间的实际相对移动速度相同且应满足仪器允许的检测速度上。
5.2.8对比试样中间3个对称通孔的显示幅度应基本一致,选取最低幅度作为检测设备的触发报警电平。
5.2.9采用记录报警时,三个人工标准缺陷的显示幅度应基本一致,相差不大于平均幅度的±10%。
三个人工标准缺陷信号应调到记录满幅度的50%-70%之间的某一幅度,其差别应不大于平均记录幅度的±10%,选取其中最低的幅度为记录标准报警幅度。
此时信号应处于仪器记录仪组合的线性区内。
6 检测结果的评定与处理6.1检验结果可根据缺陷响应信号的幅值和相位进行综合评定。
缺陷深度应依据缺陷响应信号的相位角进行评定。
6.2制造管材的评定与处理6.2.1 质量验收等级的规定应按供需双方合同,或按有关产品标准要求。
6.2.2 经检验未发现尺寸(包括深度)超过验收标准缺陷的管材为涡流检测合格品。
6.2.3经检验发现有尺寸(包括深度)超过验收标准缺陷的管材,可复探或应用其他检测方法加以验证。
若仍发现有超过验收标准的缺陷,则该管材为涡流检测不合格品。
6.2.4 不合格的管材经设计部门或委托检验方同意,可在缺陷部位进行清除或修补后重新进行检测。
如满足6.2.2要求可作为检测合格品,否则为检测不合格品。
6.3在用设备的合格等级应与业主协商,按有关规程确定。
7 记录、报告和资料存档7.1缺陷的记录:所有相关缺陷的显示可以将其图片保存与电脑,以便与分析。