制程管理计划1
制程管理(1)

第一章何谓制程(过程)Process一、所谓作业中之制程(过程),即是泛指制造、工程、工作、业务、服务之所有过程。
二、所有过程的质量要做好,即是要做好制品质量、工程质量工作质量、业务质量及服务质量。
第二章制程(过程)管制的概念一、掌握影响质量的有关因素,于工作进行的过程中,对这些因素加以管制,使结果亦能在管制状态谓之。
二、管制≠检查,质量是于制造过程中形成的,若制程能力不足,则不良率高,检查费用也高,但又无法做好质量保证。
三、制程管制不能只管制结果,而对工作的过程亦须加以管制,亦即要结果好,过程一定要先做好,如图所示。
四、构成制程的有关因素是动态的,会随着时间经过而产生变动,制程要管制的是异常原因的变动。
(有关因素如5M)第三章制程变动的因素及管制状态一、制程变动的原因制程必定会有变动,无法做出完全同样的产品,其变动的原因可分为两类;一为偶然原因,另一为异常原因。
二、制程的状态又可分为两种1.制程在管制状态所谓制程在管制状态,即指作业过程中,引起变动的原因多属偶然原因,很少有异常原因发生。
所有作业皆按一定标准及规定进行,很少发生异常现象,这种制程就是在管制状态的制程,能够保持稳定的结果,会在一定能预测的范围、一定状况下产生变动。
2.制程非管制状态作业过程中,经常发生的异常原因的变动,作业无一定的标准、规定,全由担常者随着自己的意思进行作业;或者是虽然有标准、规定,但未按规定作业、未依作业标准进行等,这种制程出现的结果是不稳定的状态,无法预测的变动随时在发生。
第四章制程管制之基本观念及前提一、制程管制应先确立的基本观念1.制程要在管制状态,才有办法进行管制─即过程有关因素须在正常的、安定的状况下2.在管制状态下,不一定代表做好质量保证─管制点的设定是否周密?是否与顾客要求的质量有关连?─制程能力是否足够?二、制程被管制之基本前提1.制程进入管制状态(并不代表没有不良发生)2.进行制程能力研究,如图示No3.制程能力值(Cp)足够,能满足质量标准,使用管制图才有意义。
1BRC管理程序 分供方管理
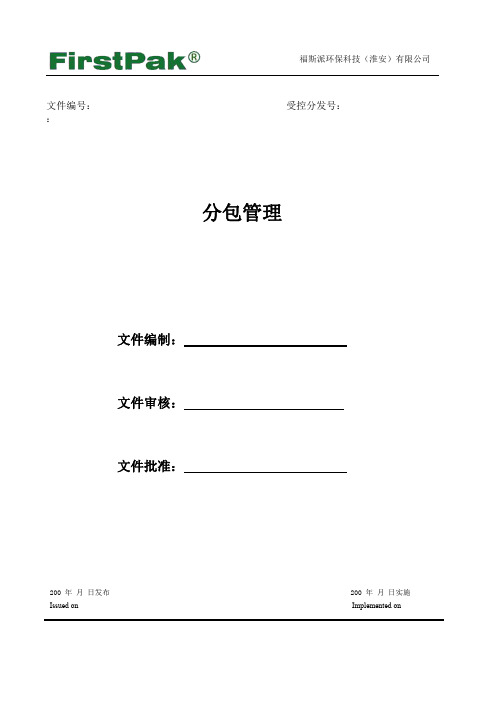
文件编号:受控分发号::分包管理文件编制:文件审核:文件批准:福斯派环保科技(淮安)有限公司200年月日发布200年月日实施Issued on Implementedon审核:分包管理批准:1.目的Purpose:确保产品外协加工过程有效控制,保证外协产品质量,满足生产需要,达到生产高效、合理控制成本之目的。
2.适用范围Scope:2.1用于本公司人员、设备不足,生产能力负荷已达饱和时。
2.2协作厂商有专门性的技术,利用外协品质较佳且价格较廉。
3.职责Responsibility:3.1采购部外检组负责主导外协厂商的选择、监管、单价跟进、外协工作协调和管理(交期、返工与理赔等);采购部负责人负责《外协加工合同》的签署,建立合格《外协厂商名录》及《外协厂商管理台帐》;3.2生产部负责外协加工产品之申报,产品外协生产过程控制管理,重大事项进行决策和向总经理汇报。
3.3生技部负责提供外协加工产品的工艺技术标准与注重点给品质部,并解答各种技术问题。
3.4生产部跟单员负责确定外协加工计划,准备外协产品所需材料,外协资料的分发、更改和回收,跟催产品进度和交期,确保外协产品按时按质按量返回;重大事项向生产经理汇报。
3.5质量部负责外协产品质量的监督、控制、验收及质量事故的处理,协助协作工厂改善质量、提高交货能力。
负责将产品之品质标准、工艺要求、生产注重点等相关要求,形成文件资料交采购部外检组与生产部跟单员。
3.6外协工厂的考核评鉴须由质量部、生产部、采购部会同前往评定。
评定内容包括掌握外协工厂的经营状况,确保其供应的产品质量符合本公司的需要;了解协作工厂的能力与潜力,提供外协单位选择的依据。
评定标准为1.质量45%,2.供应能力(交货期)20%,3.价格15%,4.管理及其它20%(注:外协厂商的选择、评定与考核的具体细则参照供应商评审管理有关制度,由采购部负责人建立《外协厂商名录》及《外协厂商管理台帐》;选择合格外协厂商之后,还必须经过试用、及考核达标后,才能正式成为本公司的协作厂商。
SOP-QM-028 生产制程异常处理办法(1)

发行部门:一、目的对生产制程中出现的异常,进行有效地处理和控制,确保生产单位可以达成客户的交期。
二、适用范围本公司生产制程中已存在及潜在的问题点三、定义:缺料异常:产线按照生产计划进行生产,所需物料没有到位,造成产线停线无法生产。
部品异常:生产线所需部品出现不良缺陷,致使产品无法组立。
设备异常:可能是事故前兆,尚未造成损失,原因未明,致使设备无法正常运转。
品质异常:在制造过程中出现了品质问题而导致的异常。
四、权责:异常原因的分析、调查:责任单位。
措施的提出:责任单位措施的审核:责任单位主管措施效果的确认:品管。
《不合格品处理单》,归档:品管五、流程详述5.1异常提出.相应规定发出不合格品处理单的情况下按本流程执行。
5.1.1生产部在制程中发现缺料异常,生产线长立即反馈上级主管,并联络业务担当,担当确认物料不能及时到产线时,产线将记录停线时间及停线所产生的费用。
5.1.2生产部在制程中发现单部品来料异常,应填写《不合格品处理单》经上级主管确认,并提交品管部担当,负责分析原因及改善对策。
5.1.3生产部在制程中使用的设备或治具出现异常,应在设备管理卡或治具送修申请单上注明异常内容,由工程部担当进行维修处理。
5.1.4生产部在制程中成品出现品质异常,生产线长及时反馈上级主管,经确认是由部品来料不良造成,因此造成产线工时的浪费要记录,如需必要产品全检要填写《全检报告书》。
PQC定期检查发现品质不良,及时向上级主管汇报,并记录在《制程巡回检查表》上,发现严重致命缺陷时,不良品要隔离放置,由品管部、工程部分析原因及改善对策。
5.2 原因分析接到《不合格品处理单》后,接受人必须及时分析异常产生的原因。
分析的结果须填写于相应的表单中。
一般地,原因分析必须针对异常的根本原因,以确保后续动作的有效性。
对预防措施,责任单位须尽可能分析出可能的原因,以确保后续动作的有效性。
5.3 评价防止需求进行原因分析后,责任部门要从此异常的严重程度、造成的品质和环境影响程序、发生机率等方面,评估采取纠正措施和预防措施是否必要,若不必要须将原因和结论记录于不合格品处理单上。
NDC1-09~95 HSF过程管理计划(QC工程图)

检验指导书
——
目测
手动操作
自检
巡检
巡检记录
班长
品管
31
入库
托盘
叉车
实物对账
分类放置
入库产品实物与生产计划入库数量核对一致,库房按产品型号\规格\物料标识分类Байду номын сангаас置
LXW17.502—02《仓库管理制度》
——
目测
自检
稽查
入库单
ERP电子账目
入库员
库管员
品管
△:品质抽检工序*:首检工序☆:关键工序。
LX/WI6.401-08《ROHS与非ROHS物料区分管理办法》
巡检记录
库管员
班长
品管
现场巡检指品管员对工序巡回检查,每次抽检4-6个产品,频次2h/次。
绕线
*
☆
2
线圈绕制
先锋自动绕线机
外观
线圈匝数线圈阻值
线圈尺寸
排线均匀,无胀包
工艺卡片
检验指导书
游标卡尺
电阻、匝数测试仪
目测
自检
首检
巡检
首检记录
巡检记录
LX/WI6.401-04《执行ROHS指令产品现场制程、成品控制方法》
LX/WI6.401-08《ROHS与非ROHS物料区分管理办法》
巡检记录
班长
品管
21
壳体移印
移印机
外观
尺寸
内容
牢固性
内容正确,规格与计划工单一致,尺寸符合图纸及检验要求,印字清晰,端正,牢固
图纸
工艺卡片
检验指导书
游标卡尺
3M胶带
目测
自检
首检
巡检
制程能力分析与对策1
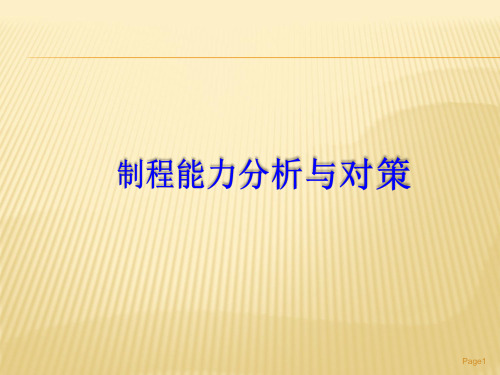
SCENE
没有“自然而然 理所当然 没有 自然而然”,“理所当然 。无处不 自然而然 理所当然”。 在的管理成就我们习以为常的社会生活面 貌。
Page2
SCEE
"管理 和"发明 管理"和 发明 发明" 管理 一样源自人类"解决 一样源自人类 解决 问题避免再发生问题 "的必要和 改善现状 的必要和"改善现状 的必要和 改善现状, 追求更方便更舒适生 的欲望。 活"的欲望。 的欲望
狭义的制程能力为衡量制程产品一致性和符合规 格的能力,由准确能力(Ca)与精密能力 格的能力, 准确能力 与精密能力(Cp)合成作综 合成作综 合判断。 合判断。
变异,即使在相同的制造条 任何制造过程都存在有变异 任何制造过程都存在有变异 即使在相同的制造条 件下生产,批与批间仍存在变异,也就是 一致性 一致性”程度 件下生产 批与批间仍存在变异,也就是“一致性 程度 批与批间仍存在变异 的不同。 的不同。
n Σ Xi 平均值: 平均值:X= i=1 n
n
標准差σ= Σ(X – X )2/n 標准差
i=1
平均值 “ = AVERAGE ( 标准差 “ = STDEV ( :
:
)”
)”
Page17
EXCEL表上填入规格中心值及上 表上填入规格中心值及上 下限, 下限,如果只有单边规格那就只填入上 限或下限。 限或下限。
Page13
Ca: Capability of Accuracy 准确度; Cp: Capability of 准确度; Precision 精密度,Cpk 综合制程能力。 精密度, 综合制程能力。
双边规格
Ca Ca = 平均值 – 规格中心 规格范围 / 2
[制程检验作业] 流程控制卡(一)
![[制程检验作业] 流程控制卡(一)](https://img.taocdn.com/s3/m/52634e4633687e21af45a92b.png)
3、生产组长或稽核中心稽核发现未按规定进行首件检验时,处罚责任制程品管员20元/次。
[制程检验作业]流程控制卡(四)
项目
失控点
失控后果描述
控制点设计精要
4
未建立品质异常处理机制
1.异常得不到及时的处理,造成不必要的 Nhomakorabea时,材料损失;
2、制程品管组长查核制程品管员巡检过程及记录;
3、生产组长监督制程品管员的巡检项目及频率;
4、生产组长、成品品管员监督制程检验漏失情况;
5、将“制程巡检、互检”列入稽核中心《品管部稽核清单》,每周抽查稽核。
责任:
1、对未按要求操作的员工进行纠正,巡检中发现重复错误操作问题,处罚操作工10元/次,如造成经济损失时,按照《赔偿管理制度》进行赔偿;
3、制程品管员将抽样内容记在《制程检验报告》中。
制约:
1、制程品管组长审核《制程产品检验记录》,确认实际抽样数是否符合《抽样计划》要求;
2、将制程抽样数“列入稽核中心《品管部稽核清单》,每周抽查稽核。
责任:
1、制程品管组长审核《制程产品检验记录》或稽核中心稽核发现未按《抽样计划》进行抽样时,处罚责任制程品管员10元/次;
[制程检验作业]流程控制卡(二)
项目
失控点
失控后果描述
控制点设计精要
2
制程产品抽样随意
检验员抽样随意性大,没有依据产品批量、品质重要生进行合理的抽样,容易出现检验漏失,造成品质事故及损失。
标准:
1、制订《抽样计划》,要求制程品管员在产品检验时依《抽样计划》进行抽样;
2、根据各工序工艺验证度及实际品质状况,对相关工序重点控制;
5W2H法[1]汇总
![5W2H法[1]汇总](https://img.taocdn.com/s3/m/361827cc76eeaeaad0f33000.png)
例:
4
③谁 (who) ? 例: 谁来办是方便? 谁会生产? 谁可以做? 谁是顾客? 谁被忽略了? 谁是决策人? 谁会受益?
5
④ 何时 (when) ? 例: 何时要完成? 何时安装? 何时销售? 何时是最佳营业时间? 何时工作人员容易疲劳? 何时产量最高? 何时完成最为适宜? 需要几天才算合理?
22
其中,零件加工和装配的每一道次都需建 立标准作业程序,并以书面方式明确显示, 要求操作人员务心遵守,如此才能达成产 品品质的稳定性。 拟订制程计划时,同时要考虑制程的合理 化,机械化和自动化的应用。
8
多少 (how much) ? 功能指标达到多少? 销售了多少? 成本多少? 输出功率多少? 效率多高? 尺寸多少? 重量多少?
9
【找出主要优缺点】 如果现行的做法或产品经过7个问题的审 核已无懈可击,便可认为这一做法或产品 可取。如果7个问题中有一个答复不能令人 满意,则表示这方面还有改进的余地,如 果哪方面的答复有独创的优点,则可以扩 大产品这方面的效用。
提出疑问对于发现问题的解决方法是 极其重要的,创造力高的人,都具有善于 提问的能力,众所周知,提出一个好的问 题,就意味着问题解决了的一半,提出问 题的技巧高,可以发挥人的想象力。采用 5W2H的方法提出问题,可以一个方面一个 方面去分析问题,这样,不仅有利于较系 统和周密地想问题,使思维更带条理性, 也有利于较深入地发掘问题和有针对性地 提出更从的可行设想。 13
生产规则
生产规则是指产品在实际进行生产前需要做 的准备工作,是介于设计与加工之间的阶段, 亦即将生产预测的结果转换成一个如何达成 的完整生产活动,且大都是由生产组织中的 决策单位所负责,生产规则的内容包括:
经营计划工作计划7篇
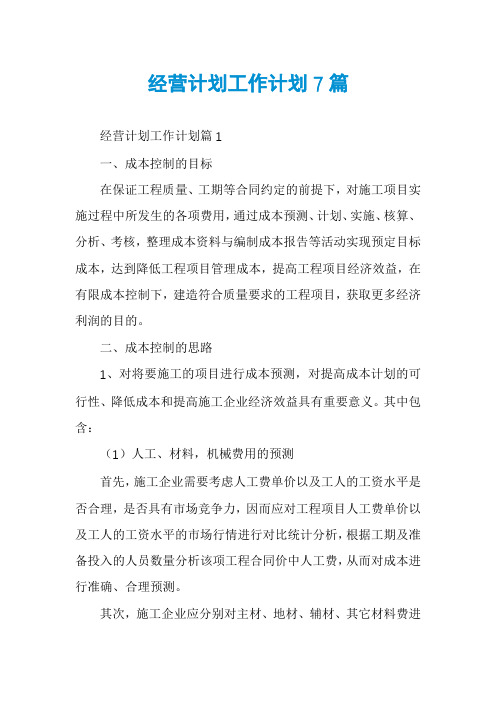
经营计划工作计划7篇经营计划工作计划篇1一、成本控制的目标在保证工程质量、工期等合同约定的前提下,对施工项目实施过程中所发生的各项费用,通过成本预测、计划、实施、核算、分析、考核,整理成本资料与编制成本报告等活动实现预定目标成本,达到降低工程项目管理成本,提高工程项目经济效益,在有限成本控制下,建造符合质量要求的工程项目,获取更多经济利润的目的。
二、成本控制的思路1、对将要施工的项目进行成本预测,对提高成本计划的可行性、降低成本和提高施工企业经济效益具有重要意义。
其中包含:(1)人工、材料,机械费用的预测首先,施工企业需要考虑人工费单价以及工人的工资水平是否合理,是否具有市场竞争力,因而应对工程项目人工费单价以及工人的工资水平的市场行情进行对比统计分析,根据工期及准备投入的人员数量分析该项工程合同价中人工费,从而对成本进行准确、合理预测。
其次,施工企业应分别对主材、地材、辅材、其它材料费进行逐项分析,且重新核定材料的供应时间、地点、购买价、运输方式及装卸费,分析合同定额中规定的材料规格与实际购买材料规格的差异,其主要原因在于材料费占建安费的比重极大,只有控制了此项费用,工程项目成本才可以得以控制。
再次,由于投标施组中的机械设备的型号、数量一般是采用定额中的施工方法套算出来的,与工程项目实际施工一般存在差异,施工效率也有差异,因此,在机械使用费中要详细测算实际将要发生的机械使用费,考虑其差异性可能带来的成本增加。
(2)施工方案变更引起费用变化的预测另外,还应当关注成本失控的风险预测。
成本失控的风险预测,是施工企业对在工程项目中实施可能影响项目工程目标实现的所有可能性因素进行事前分析与预测,并提前做好应对措施。
施工企业通常应该事前分析的事项包括:对工程项目技术特征的认识,如结构特征,地质特征等;对业主单位有关情况的分析,包括业主单位的信用、资金充足情况、既往业绩等;对项目组织系统内部的分析,包括组织设计、资源配备、人力资源制度等以及对项目所在地的交通、能源、电力、气候的分析。
工艺质量控制计划 (1)

1.0 目的:2.0 适用范围:3.0 生产质量管控计划:使用设备(工具)名称设备(工具)要求设备记录表单工具频率数量参照文件标准记录表单报告处 原材料尺寸规格(长,宽,材料厚度)卷尺,千分尺,《进料检验和试验管理规定》《进料检验和试验报告单》IQC IQC组长 粗糙度检验(针对特别要求材料)粗糙度测试仪《纠正和预防措施控制规定》《材质证明书》SQE 板材镀锌层检测膜厚计《ROHS 环保证明》 外观要求, 平整度塞尺,钢直尺 材质确认,供应商测试报告 盐雾测试盐雾测试机 铆钉` 螺母` 垫片的材质及规格要求(是否符合ROHS 的相关要求,有相关证明和报告)卡尺,牙规 包材的质量要求(是否符合ROHS 的相关要求,有相关证明和报告)擦纹机工作气压=5kg/cm2,砂袋摆幅=6--10mm 《设备保养记录表》擦纹纹路方向比对样板 产品图纸,《工序检验作业指导书》《制程检验记录表》作业员当班制造班长砂袋对应型号表面要求目视《制程检验和试验管理规定》IPQC 剪口组长覆膜机工作电压=220V,粘性强度测试,测试 产品图纸,《制程检验和试验管理规定》作业员QE 覆膜粘性强度,材质不可有任何破损,必须贴平不可有皱纹目视《工序检验作业指导书》IPQC 工作气压=5kg/cm2,《设备保养记录表》材质及厚度卡尺,材质报告《剪口作业指导书》《制程检验记录表》作业员确认各刀站,模具正确且固定不松动尺寸要求卡尺《工序检验作业指导书》《不良品物料停用单》IPQC 外观要求GB-2828-87标准:S-1《制程检验和试验管理规定》检查电,气,水,是否畅通毛刺的整修状况目视,手感对应的产品工程图纸安全注意事项产品摆放按加工要求钻床工作电压=220V,《设备保养记录表》沉空位置,数量比对样品1次/0.5H ≥1PCS 《工序检验作业指导书》《制程检验记录表》作业员当班制造班长钻头根据产品加工要求选择《模具管理台帐》沉孔标准三次元测试《制程检验和试验管理规定》《不良品物料停用单》IPQC 外围组长传统冲床传统冲床吨位≤25T波形位置,数量比对图纸对应的产品工程图纸QE 字印模具要有明确产品的定位装置冲波的规格标准卡尺传统冲床传统冲床吨位≤25T冲桥的位置,数量比对图纸冲桥模具要有明确产品的定位装置冲桥的尺寸控制卡尺传统冲床传统冲床吨位≤25T字印位置,内容,大小标准卡尺冲波模具按产品编号对应的模具编号字印方向目视传统冲床吨位≤25T 抽芽在产品上的位置,大小规格卡尺《工序检验作业指导书》《制程检验记录表》有安全防工伤控制系统抽芽方向目视比对图纸《制程检验和试验管理规定》抽芽模具按产品编号对应的模具编号丝攻机有安全防工伤控制系统攻牙位置,数量,方向目视比对图纸《工序检验作业指导书》《制程检验记录表》第一页,共异 宝馨科技各生产加工部门和品检部门。
来料、制程、出货品质控制方案

来料品质控制方案1、目的:为了有效的控制物料,以满足产品的品质要求,确保所有用于本公司生产的物料都在品质控制状态下,防止因不合格物料所导致的各种不良和不合格品的误用、混用。
2、定义:1、IQC:来料品质控制;2、合格:满足规定的要求,包括图纸、检验卡片上所规定的尺寸要求和各项性能指标;3、不合格:未满足规定要求,对产品的品质产生影响的指标达不到相应的要求;4、特采:来料经IQC检查判定为不合格时,由于生产计划等原因而对此批来料做特别采用要求;5、加工/挑选:来料经IQC检查,判定为不合格,单考虑到生产及出货计划以及不合格的项目严重程度而做出的最终决定。
三、职责:1、IQC:a、来料检查(仓库提供<<来料通知单>>工程部提供规格书);b、检查报废物料,对仓库或工厂提出要报废的物料作出判定;c、出仓重检,即对保存周期超过一段时间的物料重检以确定是否失效;d、检查回仓物料,即贵工厂使用的余料进行检查,以确定是入库,还是退供应商或报废;e、评估新的供应商,对新引进之供应商由采购主导,协同工程对其进行评估,以确定是否为合格供应商;f、辅导供应商改善(需采购、工程配合工作);g、对怀疑不良的物料进行有效的实验、分析;h、对其检验应有相应的记录、标识,并将检查结果通知相关部门,以便于判定、追溯。
2、品质主管:负责不合格的判定、处理。
4、作业流程:1、IQC在接到货仓来料通知后,应在第一时间内对该批物料按照《检验文件》总显影的检验卡片所规定的内容进行检查;2、检查时必须严格按《检验文件》作业,对有出入的数据必须组装成品和半成品进行效果鉴定;3、检查完毕,将检查结果及相关数据记录在《IQC检验报告》上交品质主管审核;4、检验合格,对该检验批做好标识,于该批检验物料上贴"IQC PASSED"标签,并将检验副本交各相关部门,正本由品质部保存;5、如检验不合格,IQC需将不良样品和检验报告交品质主管判定,品质主管评估该缺陷是否对产品的最终品质有影响,根据相应的不良的严重项目的严重程度做出最终判定,分别为:特采、加工/挑选、退货,宁签署处理意见;6、IQC根据品质主管的最终处理意见对相应的检验批做好相应标识,退供应商用“IQC REJECTED”标签,判定为特采的用IQC特采标签,判定为选用的用IQC选用标签;7、对判定为选用的,IQC需在IQC选用标签上注明需选用的不良点,以便在生产是做针对性的选别,IPQC也需要对有问题的项目重点跟进;8、经判定为退货、特采、加工/挑选的,由品质主管填写品质异常联络单,并签署处理意见后交公司采购、PMC,再由采购传真至供应商,并联络供应商改善,品质异常联络单正本由品质部存档,以便对后续来料进行跟踪确认。
生产物料损耗管理方法(1)
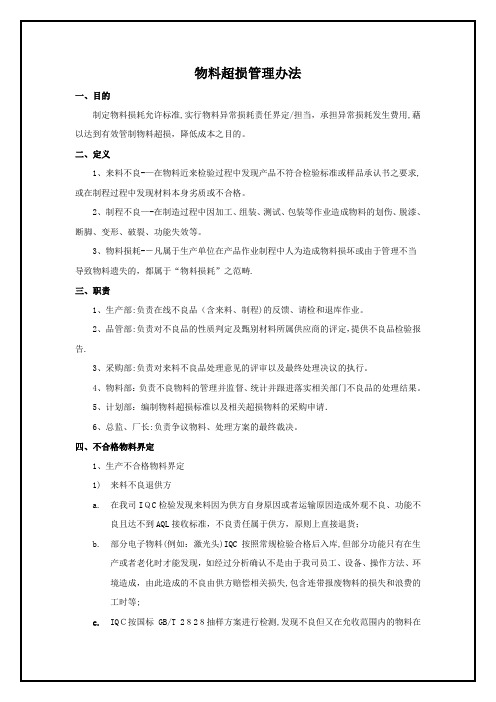
物料超损管理办法一、目的制定物料损耗允许标准,实行物料异常损耗责任界定/担当,承担异常损耗发生费用,藉以达到有效管制物料超损,降低成本之目的。
二、定义1、来料不良-—在物料近来检验过程中发现产品不符合检验标准或样品承认书之要求,或在制程过程中发现材料本身劣质或不合格。
2、制程不良—-在制造过程中因加工、组装、测试、包装等作业造成物料的划伤、脱漆、断脚、变形、破裂、功能失效等。
3、物料损耗--凡属于生产单位在产品作业制程中人为造成物料损坏或由于管理不当导致物料遗失的,都属于“物料损耗”之范畴.三、职责1、生产部:负责在线不良品(含来料、制程)的反馈、请检和退库作业。
2、品管部:负责对不良品的性质判定及甄别材料所属供应商的评定,提供不良品检验报告.3、采购部:负责对来料不良品处理意见的评审以及最终处理决议的执行。
4、物料部:负责不良物料的管理并监督、统计并跟进落实相关部门不良品的处理结果。
5、计划部:编制物料超损标准以及相关超损物料的采购申请.6、总监、厂长:负责争议物料、处理方案的最终裁决。
四、不合格物料界定1、生产不合格物料界定1)来料不良退供方a.在我司IQC检验发现来料因为供方自身原因或者运输原因造成外观不良、功能不良且达不到AQL接收标准,不良责任属于供方,原则上直接退货;b.部分电子物料(例如:激光头)IQC按照常规检验合格后入库,但部分功能只有在生产或者老化时才能发现,如经过分析确认不是由于我司员工、设备、操作方法、环境造成,由此造成的不良由供方赔偿相关损失,包含连带报废物料的损失和浪费的工时等;c.IQC按国标GB/T 2828抽样方案进行检测,发现不良但又在允收范围内的物料在使用过程中出现的不良不在“物料损耗”之定义内.d.已被IQC判定为不合格但由于生产急需而作特别采用(MRB)处理的物料,在制程过程中出现的不良不在“物料损耗”之定义内。
2)制程不良a.对于机壳、面板、导光柱、按键、包装盒、说明书、合格证等物料的外观在生产部第一个投入这些物料的工序确认出来的不良归属于来料不良,对于在后面工序发现的不良归属于生产制程不良;b.对于LED灯不亮、蜂鸣器无声音、PCBA上缺件等不良在观澜PCBA检验工序确认出来的物料不良归属于来料不良,对于在后面工序发现的不良归属于生产制程不良;3)其它对于在制程中发现的物料不良能确认是供方造成的,其处理方案依次为采购与供方沟通换货。
LOT管理程序(1)
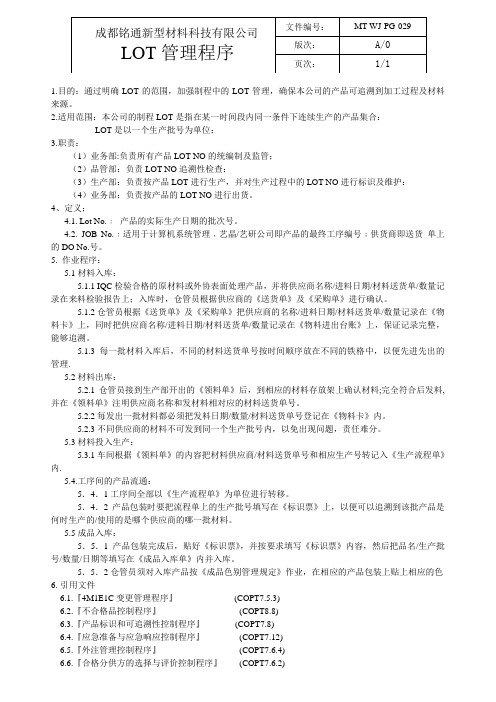
1.目的:通过明确LOT的范围,加强制程中的LOT管理,确保本公司的产品可追溯到加工过程及材料来源。
2.适用范围:本公司的制程LOT是指在某一时间段内同一条件下连续生产的产品集合:LOT是以一个生产批号为单位:3.职责:(1)业务部:负责所有产品LOT NO的统编制及监管;(2)品管部:负责LOT NO追溯性检查:(3)生产部:负责按产品LOT进行生产,并对生产过程中的LOT NO进行标识及维护:(4)业务部:负责按产品的LOT NO进行出货。
4、定义;4.1. Lot No.﹕产品的实际生产日期的批次号。
4.2. JOB No.﹕适用于计算机系统管理﹐艺晶/艺研公司即产品的最终工序编号﹔供货商即送货单上的DO No.号。
5. 作业程序:5.1材料入库:5.1.1 IQC检验合格的原材料或外协表面处理产品,并将供应商名称/进料日期/材料送货单/数量记录在来料检验报告上;入库时,仓管员根据供应商的《送货单》及《采购单》进行确认。
5.1.2仓管员根据《送货单》及《采购单》把供应商的名称/进料日期/材料送货单/数量记录在《物料卡》上,同时把供应商名称/进料日期/材料送货单/数量记录在《物料进出台账》上,保证记录完整,能够追溯。
5.1.3 每一批材料入库后,不同的材料送货单号按时间顺序放在不同的铁格中,以便先进先出的管理.5.2材料出库:5.2.1仓管员接到生产部开出的《领料单》后,到相应的材料存放架上确认材料;完全符合后发料,并在《领料单》注明供应商名称和发材料相对应的材料送货单号。
5.2.2每发出一批材料都必须把发料日期/数量/材料送货单号登记在《物料卡》内。
5.2.3不同供应商的材料不可发到同一个生产批号内,以免出现问题,责任难分。
5.3材料投入生产:5.3.1车间根据《领料单》的内容把材料供应商/材料送货单号和相应生产号转记入《生产流程单》内.5.4.工序间的产品流通:5.4.1工序间全部以《生产流程单》为单位进行转移。
IPQC制程巡检管理办法-1

1. 目的: 规范 IPQC 制程品质控制重点及作业方法,使产品在生产过程中得到有效控制。 2. 适用范围: 适用于本公司内的 IPQC 检验工作。 3. 定义: 3.1 IPQC:即生产过程品质控制(In process Quality Control),是指领料生 产以后,到成品加工完成时的品质管理活动; 3.2 RoHS: Restriction of the Use of Certain Hazardous Substances in Electrical and Electronic Equipment(电子电气设备中限制使用某些有 害物质指令); 3.3 SOP: Standard Operation Process 的简称,即标准作业指导书。 3.4 BOM:物料清单; 3.5 ECN:工程变更通知单; 3.6 首件:生产过程每批量,经自检合格的第一件成品或材料变更﹑工艺变更后自检合格。 的第一件成品,必要时数量可为 2—3PCS。 4.职责: 4.1 品保部 IPQC 依据本文件规定对生产过程品质进行检查控制。 4.2 IPQC 首件确认,对异常进行确认: 4.2.1 若异常现象 IPQC 能够立即判定原因,并且能够解决,则与生产拉长一起制定纠正措 施并执行,IPQC 对纠正措施进行跟踪验证,验证数量不少于 100PCS 无问题方可正常 生产。 4.2.2 若 IPQC 不能立即判定原因,则立即通知品质工程师或品质主管。 4.2.3 品质工程师或品质主管根据不良现象立即通知相关人员,工程与生产等部门相关工 程师在接到通知后,十分钟内必须到达现场,组成异常处理小组对不良问题进行 分析。 4.2.3.1 找出真正的不良原因之后,相关的责任单位应在四工作时之内给出纠正措施,八个 小时时内给出预防措施;IPQC 跟进改善措施实行后的 200 台机(若批量小于 200PCS 则需跟踪同型号下一批次的生产),以确定改善措施是否有效,如果措施有效,对 此不良问题结案,必要时将措施纳入相关作业文件;如果改善措施无效,责任单 位重新制定改善措施;直到经跟踪验证有效为止。 4.2.3.2 若半小时内不能分析出异常原因,则 IPQC 立即要求生产停止,对已生产的 产品进行标识并隔离,按 4.4 进行处理。 4.3 品质异常停线的处理。 4.3.1 生产线停线的时机(不合格比率以 500pcs 为基数) A、当制程异常的不良率达到或超过《制程品质管制目标值》中停线目标值时; B、当品质异常超出品质管制报警界限,而相关部门在半小时内无法改善时; C、出现其它重大品质事故,可以影响到产品特性功能的重大不良; 4.3.2 IPQC 按要求在《环境/品质异常处理报告》上面注明停线,经品保部课长/协理确 认后, 通知生产停止, 同时通知各相关部门工程师、 主管及主管生产的副总,按 4.3.3 执行。 4 3.2.1 当找出真正的不良原因之后,各部门协商给出临时有效的改善措施 4.3.2.2 品保部跟进措施实行后的 50PCS 板。如果改善措施有效则复线;如果改善
制程作业流程及方法培训-IPQC培训1

变更事项、IPQC项目审核
记录保存
IPQICP检QC验检、I验P处Q、理C技检流能验程、、处处理理流流程程
朗驰欣创
首件异常处理
首件 异常
如生产单位对 IPQC判定有争 议请QE或品质 主管确认,依 QE确认为准
产品品质异常处理
出现有差异的 需复测一次
异常提出
核对样品及资料
将首件资料 及样品退回
朗驰欣创
IPQC 培训资料 品质部 houyuhui
IPQC检验、技能、处理流程
朗驰欣创
IPQC-制程品质检验
• I ---------- Inspect(检查、检验) • P --------- Process(过程、步骤) • Q --------- Quality(品质、质量) • C --------- Control(控制、管控)
IPQICP检QC验检、I验P处Q、理C技检流能验程、、处处理理流流程程
朗驰欣创
制程控制,是指产品从物料投入生产到产品最终包装 过程的品质控制。
• 2)巡回检验 巡回检验就是检验工人按一定的时间间隔和路线,依次到工作地或生产 现场,用抽查的形式,检查刚加工出来的产品是否符合图纸、工艺或检 验指导书中所规定的要求。在大批大量生产时,巡回检验一般与使用工 序控制图相结合,是对生产过程发生异常状态实行报警,防止成批出现 废品的重要措施。当巡回检验发现工序有问题时,应进行两项工作: 一、是寻找工序不正常的原因,并采取有效的纠正措施,以恢复其正常 状态; 二、是对上次巡检后到本次巡检前所生产的产品,全部进行重检和筛选 ,以防不合格品流入下道工序(或用户) 。 巡回检验是按生产过程的时间顺序进行的,因此有利于判断工序生产状 态随时间过程而发生的变化,这对保证整批加工产品的质量是极为有利 的。为此,工序加工出来的产品应按加工的时间顺序存放,这一点很重 要,但常被忽视 。
2024年个人能力提升计划范文(七篇)

2024年个人能力提升计划范文一、秉持公正,树立榜样,并高效完成领导临时交予的各项任务。
二、针对个人在财务管理方面的见解与措施,提出以下要求:务必实现财务治理的科学化,核算的规范化,费用控制的全面合理化,同时加强监督力度,细化工作流程,切实发挥财务管理的核心作用。
此举旨在推动财务运作向更合理、更健康的方向发展,确保与公司整体发展步调相一致。
展望未来,我将紧抓改革契机,继续强化现金管理,提升个人业务能力,充分展现财务的职能价值,全力以赴完成年度工作计划,以最大化地服务于公司,为公司稳健发展贡献更大力量。
三、关于个人能力提升计划(教师篇):教师,作为文化传承的使者与新一代的培养者,在当今社会激烈的竞争中,面临着更高的职业要求。
作为青年教师,为更好地适应新时代教育改革,丰富专业知识,提升素养,胜任教育教学工作,特制定以下个人提升计划:(一)自我剖析优点:性格随和,待人宽容,工作认真负责,积极参与,能够一丝不苟地完成各项任务。
不足:由于经验有限,科研投入不足,自我感觉专业功底尚浅。
虽经课程改革洗礼,教育观念有所转变,但仍需不断学习,尤其是业务知识与理论,以及个人基本功的强化与提升。
(二)提升计划1. 理论学习:深入学习新课程理念,掌握所教学科的专业特点,勤于思考,养成多思多写的习惯,力求教学最优化,逐步形成独特的教学风格。
2. 教学常规:严格执行学校日常教学规范,注重教学质量,持续培养学生良好习惯。
3. 自我反思:勤于总结教学经验,在反思中不断完善自我。
4. 基本功训练:坚持练习书法、简笔画等基本功,不断提升个人技能水平。
5. 信息技术应用:积极掌握现代信息技术,利用网络资源辅助教学,提升教学效果。
(三)具体措施1. 专业提升:通过阅读教育专著、期刊杂志等,丰富文化素养,了解最新教育动态与理念;在老教师指导下,通过听课、交流等方式,提升专业素养与教学能力。
2. 教学常规:精心备课,细心批改作业,注重教学质量与细节;特别关注后进生,采用有效策略促进其全面发展。
- 1、下载文档前请自行甄别文档内容的完整性,平台不提供额外的编辑、内容补充、找答案等附加服务。
- 2、"仅部分预览"的文档,不可在线预览部分如存在完整性等问题,可反馈申请退款(可完整预览的文档不适用该条件!)。
- 3、如文档侵犯您的权益,请联系客服反馈,我们会尽快为您处理(人工客服工作时间:9:00-18:30)。
正常檢驗單次 1.目視 入庫驗收報 品保 抽樣法 MIL- 2.分厘卡 開單記錄表 STD-105E 3.投影機 NL-041A版 FQC檢驗日報 一覽表 NP028A版 全數 目視 LOT管理 NL-071A版 入庫驗收單 NL-022A4版 沖壓課
依端子零件檢驗規范
依端子包裝作業規范
14
入庫
數量
目視
沖壓課
條件對照表 CY-200006415A版 操作手冊 CY-9906062A2 版 保養辦法 CY-9906058A2版
9
初件檢驗
1.外觀 2.尺寸
1.壓傷跳屑毛邊扇形 2.依據端子零件檢驗 規范
1.每日初件 2.每批初件 3.更換材料 4.模具修改 1次/2H
1.分厘卡 沖壓初件制 品管課 2.投影機 程檢驗記錄 3.目視 表 NL-021A1 版 1.目視 2.投影機 3.分厘卡 RD-051A2版 沖壓生產自 主檢驗表 沖壓課
1.材料更換
目視
工作指示單 NC-011A3版
沖壓課
7
原料安裝
料架 送料機
動作確認
沖壓課
組合狀態
依據工作指示單
1.材料更換
目視
工作指示單 NC-011A3版
沖壓課
操作與保養辦法 CY-9906059A1版
8
沖壓試作
沖壓機
動作確認
沖壓課
沖壓條件對 噸位以上 照 沖床行程模具高度床台規格沖壓速度節距-
1.每日初件 2.每批初件 3.更換材料 4.模具修改
依據工作指示單 發料單
每批工令
3
生產排配
沖床
沖壓機器操作手 冊
沖壓機台生產 每批工令 排配表
沖壓課
機台調度
依據生產排程
次/月
目視
沖壓課
4
模具確認
模具
模具編號
依據工作指 示單架模前 確認
沖壓課
沖壓條件對 噸位以上 照 沖床行程模具高度床台規格沖壓速度節距依工作指示單
1.每日初件 2.每批初件 3.模具修改
目視
沖壓課
條件對照表
5
模具安裝
模具 沖床
動作確認
依沖壓模具維 架模前確認 修與保養辦法
沖壓課
組合狀態
1.更換材料 2.模具修改
目視
沖壓課
沖(塑)模具維修提報 單 NL-023A3版
6
原料確認
素材規格 厚*寬 料架(送料機) 1. 1次/日 操作與保養辦 2. 1次/周 法 3. 1次/月 依照沖壓機器 1. 1次/日 操作手冊/沖 2. 1次/周 壓機保養辦法 3. 1次/月
依端子零件檢驗規范
10
沖壓生產
沖壓機
動作確認
依照沖壓機器 1. 1次/日 操作手冊/沖壓 2. 1次/周 機保養辦法 3. 1次/月
沖壓課
1.外觀 2.尺寸
1.壓傷跳屑毛邊扇形 2.依端子自主檢驗表
依 表
端子自主檢驗
11
製程抽檢
1.外觀 2.尺寸
1.壓傷跳屑毛邊扇形 2小時/次 2.依端子零件檢驗規范
制程管理計劃(PMP) (沖壓)
料號: 步 流程圖 驟 1 2 品名: 製程名稱 設備名稱 進料銅材 檢驗 生產準備 沖床 沖壓機器操作手 冊 工作指示單 每批工令 沖壓課 設 管理項目 備 管 管理基準 管 理 頻 度 理 責任單位 管制項目 銅材:厚度* 寬度 數量 版本: 方 品 管制基準 制訂日期: 法 質 頻 度 每批 管 理 檢驗量具 記錄方式 責任單位 卡尺 進貨驗收單 品保 分厘卡 NC-025 A4版 目視 工作指示單 NC-011A4版 發料單 NL-013A3版 生產排配 表 NL-001A版 工作指示單 NC-011A3版 產企部 頁次 備 註
1.卡尺 IPQC巡回檢 2.投影機 驗記錄表 3.目視 NP-073A4版
品管課
依端子零件檢驗規范
12
包裝
收料機
動作確認
收料機操作手 1次/日 冊與保養辦法
沖壓課
數量
一盤 一箱
全數
目視
沖壓生產日 報表 NL-070A版
沖壓課
依端子包裝作業規范
13
檢驗
1.外觀 2.尺寸 3.包裝
1.壓傷.跳屑.毛邊 2.間隙: 卡伸點: 凸點: 3.依包裝作業規范 一盤 一箱
核定: 會簽單位: □組裝一部: □組裝二部: □零件制造部:
審核: □開發工程部:
制表: □品保部: