钢结构的裂纹成因及防范措施 改
钢结构产生裂缝的原因分析及解决措施

钢结构产生裂缝的原因分析及解决措施前言钢结构是一种常用的建筑结构形式,具有高强度、耐久性和稳定性等优点。
然而,有时钢结构会出现裂缝问题,给结构的安全性和稳定性带来威胁。
本文将分析钢结构产生裂缝的原因,并提出解决措施以防止或修复这些裂缝。
裂缝的原因分析1. 载荷超载:如果钢结构超过了其承载能力,会导致裂缝的产生。
这可能是由于设计错误、运输或安装失误等问题所引起。
因此,在设计和施工过程中,应确保载荷不超过钢结构的承载能力。
2. 施工质量问题:不良的施工质量也是导致钢结构裂缝的原因之一。
例如,焊接质量不合格、连接件失稳或材料缺陷等都可能导致裂缝的产生。
因此,在施工过程中,应严格遵守相关的施工标准和质量控制要求。
3. 环境因素:环境因素如温度变化、湿度和风力等也可能引起钢结构裂缝。
例如,温度变化引起的热胀冷缩效应可能导致结构的变形和应力集中,最终导致裂缝的产生。
因此,在设计和使用钢结构时,应考虑环境因素对结构的影响,并采取相应的措施进行管理和保护。
解决措施1. 加强设计和施工质量管理:在钢结构的设计和施工过程中,应加强质量管理,确保设计规范和施工标准得到严格遵守。
同时,对焊接、连接等关键工艺进行监控和检测,确保施工质量符合要求。
2. 载荷控制和监测:确保钢结构的载荷不超过其承载能力,合理进行结构设计和分析,以防止载荷超载。
此外,对钢结构进行定期监测,及时发现载荷异常,做出及时调整和维护。
3. 应对环境因素:针对环境因素的影响,采取相应的措施进行管理和保护。
例如,在高温季节,可以采取隔热措施,减少结构受热膨胀的影响;在潮湿环境下,采取防锈措施,防止钢结构受潮和腐蚀。
结论钢结构裂缝的产生与多种因素相关,包括载荷超载、施工质量问题和环境因素等。
通过加强设计和施工质量管理,控制和监测载荷,以及应对环境因素,可以有效预防和解决钢结构裂缝问题,提升结构的安全性和稳定性。
建筑钢结构焊接裂纹的产生机理及防止措施
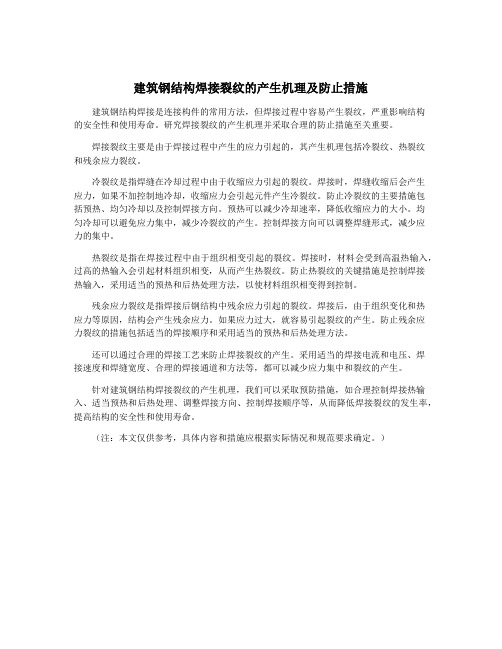
建筑钢结构焊接裂纹的产生机理及防止措施建筑钢结构焊接是连接构件的常用方法,但焊接过程中容易产生裂纹,严重影响结构的安全性和使用寿命。
研究焊接裂纹的产生机理并采取合理的防止措施至关重要。
焊接裂纹主要是由于焊接过程中产生的应力引起的,其产生机理包括冷裂纹、热裂纹和残余应力裂纹。
冷裂纹是指焊缝在冷却过程中由于收缩应力引起的裂纹。
焊接时,焊缝收缩后会产生应力,如果不加控制地冷却,收缩应力会引起元件产生冷裂纹。
防止冷裂纹的主要措施包括预热、均匀冷却以及控制焊接方向。
预热可以减少冷却速率,降低收缩应力的大小。
均匀冷却可以避免应力集中,减少冷裂纹的产生。
控制焊接方向可以调整焊缝形式,减少应力的集中。
热裂纹是指在焊接过程中由于组织相变引起的裂纹。
焊接时,材料会受到高温热输入,过高的热输入会引起材料组织相变,从而产生热裂纹。
防止热裂纹的关键措施是控制焊接热输入,采用适当的预热和后热处理方法,以使材料组织相变得到控制。
残余应力裂纹是指焊接后钢结构中残余应力引起的裂纹。
焊接后,由于组织变化和热应力等原因,结构会产生残余应力。
如果应力过大,就容易引起裂纹的产生。
防止残余应力裂纹的措施包括适当的焊接顺序和采用适当的预热和后热处理方法。
还可以通过合理的焊接工艺来防止焊接裂纹的产生。
采用适当的焊接电流和电压、焊接速度和焊缝宽度、合理的焊接通道和方法等,都可以减少应力集中和裂纹的产生。
针对建筑钢结构焊接裂纹的产生机理,我们可以采取预防措施,如合理控制焊接热输入、适当预热和后热处理、调整焊接方向、控制焊接顺序等,从而降低焊接裂纹的发生率,提高结构的安全性和使用寿命。
(注:本文仅供参考,具体内容和措施应根据实际情况和规范要求确定。
)。
建筑钢结构焊接裂纹的产生机理及防治措施

建筑钢结构焊接裂纹的产生机理及防治措施标签:焊接裂纹;建筑;防治现阶段,随着市场经济的不断发展,建筑行业市场的竞争压力逐渐增加,这对部分建筑企业来说是一个很大的挑战。
为在激烈的竞争当中得以生存,工程质量情况逐渐得到越来越多建筑企业的重视,工程质量的提升不仅可以实现企业价值的最大化,还能在一定程度上把握对成本的管控。
因此,本文以建筑钢结构为基础,对焊接中裂纹的产生机理和防治进行研究。
一、裂纹的产生机理及特征建筑钢在焊接的过程中很容易产生裂纹,主要分为三种形式:热裂纹、冷裂纹、层状撕裂。
(一)热裂纹热裂纹是复杂钢结构中较容易出现的一种裂纹形式,其产生的主要原因是在焊接后结晶的过程中受到高温。
热裂纹通常会出现在焊接缝当中,并在缝隙当中呈现纵向分布,是焊接过程中经常出现的一种裂纹。
根据所受温度的不同,热裂纹呈现的形式也有所差异,主要分为三种:凝固裂纹。
这种裂纹又称结晶裂纹,主要在焊接快结束前脆性温度间的焊缝金属凝固所形成。
焊缝金属结晶的过程中,由于液层之间存在韧性较低的杂质,金属在冷却不均的情况下拉伸超过临界值,即导致热裂缝的出现。
液化裂缝。
这种热裂缝的产生是由于一些低熔点的金属或金属化合物在焊接中产生的热量引起晶界焊接热,从而影响液化而产生的裂纹。
塑料裂纹。
又被称为多层焊接,其产生原因主要是受焊接热循环的影响,导致金属材料塑性降低,受到拉应力在晶界进行二次结晶而形成的裂纹。
(二)冷裂纹冷裂纹通常在焊接结束后冷却的过程中出现,有的是直接出现,也有一部分是在经过一段时间后出现,这种产生后不会立即出现而是随着时间的推移慢慢显露出来的裂纹,被称为延迟裂纹。
冷裂纹大多为延迟裂纹,通常产生在低、中合金钢焊接的热影响区域,很少部分在焊接缝上,裂纹横纵不一,由于大部分冷裂纹都不是直接出现,因此具有一定的隐蔽性。
经相关统计显示,冷裂纹产生的主要原因分为以下几种:钢的淬硬趋势焊接头氢含量焊接头拘束度。
(三)层状撕裂层状撕裂在钢结构焊接的过程中主要分为两种,一种裂点出现在焊缝的根部附近,由根部向四周蔓延,另一种是出现在含热区,主要是焊接过程中在收缩应力具有很强拉伸性的情况下,由一些非金属的杂质扩散而成。
钢结构焊接裂纹的种类及对策

钢结构焊接裂纹的种类及对策根据裂纹发生的时间大致可以将裂纹分成高温裂纹和低温裂纹两大类。
1、低温裂纹根据裂纹是低温裂纹常见的一种形态,其产生原因如下:(1)主要是由于焊接金属含氢量较高所致氢的来源有多种途径,如焊条中的有机物,结晶水,焊接坡口和它的附近粘有水份、油污及来自空气中的水份等。
(2)焊接拉头的约束力较大,例如厚板焊接时接头固定不牢、焊接顺序不当等均有可能产生较大的约束应力而导致裂纹的发生。
(3)当母材碳当量较高,冷却速度较快,热影响区的硬化从而导致裂纹的发生。
对于根部裂纹的防止措施:(1)选用低氢或超低氢焊条或其他焊接材料。
(2)对焊条或焊剂等进行必要的烘焙,使用时注意保管。
(3)焊前,应将焊接坡口及其附近的水份、油污、铁锈等杂质清理干净。
(4)选择正确的焊接顺序和焊接方向,一般长构件焊接时最好采用由中间向两端对称施焊的方法。
(5)进行焊前预热及后热控制冷却速度,以防止热影响区硬化。
2、高温裂纹焊道下梨状裂纹是常见的高温裂纹的一种,主要发生在埋弧焊或二氧化碳气体保护焊中,手工电弧焊则很少发生。
焊道下梨状裂纹的产生原因主要是焊接条件不当,如电压过低、电流过高,在焊缝冷却收缩时使焊道的断面形状呈现梨形。
防止措施:选择适当的焊接电压、焊接电流;焊道的成形一般控制在宽度与高度之比为1:1.4较适宜。
弧坑裂纹也是高温裂纹的一种,其产生原因主要是弧坑处的冷却速度过快,弧坑处的凹形未充分填满所致。
防止措施是安装必要的引弧板和引出板,在焊接因故中断或在焊缝终端应注意填满弧坑。
焊接裂纹的修补措施如下:(1)通过超声波或磁粉探险伤检查出裂纹的部位和界限。
(2)沿焊接裂纹界限各向焊缝两端延长50mm,将焊缝金属或部分母材用碳弧气刨等刨去。
(3)选择正确的焊接规范,焊接材料,以及采取预热、控制层间温度和后热等工艺措施进行补焊。
建筑钢结构焊接裂纹的产生机理及防止措施

建筑钢结构焊接裂纹的产生机理及防止措施钢结构作为建筑工程中重要的材料之一,广泛应用于不同类型的建筑物中。
然而,在钢结构的生产和施工过程中,焊接裂纹是一个常见的问题,会导致结构的强度和稳定性受到影响,甚至可能引发严重的事故。
因此,了解钢结构焊接裂纹的产生机理,采取防止措施,对于保障钢结构的安全性和可靠性具有重要意义。
钢结构焊接裂纹的产生机理主要有以下几个方面:
1. 材料缺陷:焊接过程中,如果钢材本身就存在缺陷,比如孔洞、气孔、裂纹等,容易在焊接过程中扩大,形成焊接裂纹。
2. 焊接过程中的热应力:钢材在焊接过程中会受到热应力的影响,会产生变形和应力集中的问题。
如果应力集中过于严重,就会导致焊接裂纹的产生。
3. 焊接参数不当:焊接参数的选择不当,比如电流、电压、焊接速度等不合理,容易导致焊接温度不均匀,从而引发焊接裂纹。
为了防止钢结构焊接裂纹的产生,可以采取以下措施:
1. 选择质量好的材料:在选材的过程中,应选择质量好的钢材,尽可能避免存在缺陷的材料被用于焊接。
2. 确定合理的焊接参数:在焊接过程中,应根据钢材的材质和焊接方式确定合理的焊接参数,保证焊接温度均匀,减少应力集中的问题。
3. 采用预热和后热处理技术:在焊接前进行预热,可以减少焊接过程中的热应力,从而避免焊接裂纹的产生。
在焊接后进行后热处
理,可以降低残余应力,进一步保证结构的稳定性和安全性。
总之,了解钢结构焊接裂纹的产生机理,采取有效的防止措施,对于确保建筑物整体的安全性和可靠性具有重要意义。
建筑钢结构焊接裂纹的产生机理及防治措施
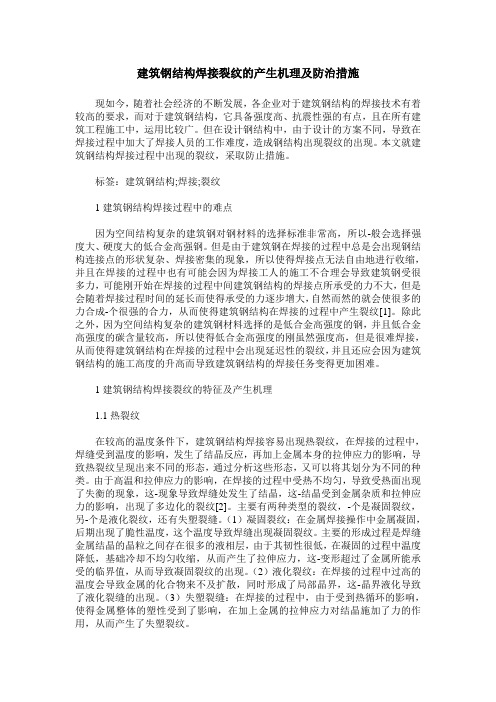
建筑钢结构焊接裂纹的产生机理及防治措施现如今,随着社会经济的不断发展,各企业对于建筑钢结构的焊接技术有着较高的要求,而对于建筑钢结构,它具备强度高、抗震性强的有点,且在所有建筑工程施工中,运用比较广。
但在设计钢结构中,由于设计的方案不同,导致在焊接过程中加大了焊接人员的工作难度,造成钢结构出现裂纹的出现。
本文就建筑钢结构焊接过程中出现的裂纹,采取防止措施。
标签:建筑钢结构;焊接;裂纹1建筑钢结构焊接过程中的难点因为空间结构复杂的建筑钢对钢材料的选择标准非常高,所以-般会选择强度大、硬度大的低合金高强钢。
但是由于建筑钢在焊接的过程中总是会出现钢结构连接点的形状复杂、焊接密集的现象,所以使得焊接点无法自由地进行收缩,并且在焊接的过程中也有可能会因为焊接工人的施工不合理会导致建筑钢受很多力,可能刚开始在焊接的过程中间建筑钢结构的焊接点所承受的力不大,但是会随着焊接过程时间的延长而使得承受的力逐步增大,自然而然的就会使很多的力合成-个很强的合力,从而使得建筑钢结构在焊接的过程中产生裂纹[1]。
除此之外,因为空间结构复杂的建筑钢材料选择的是低合金高强度的钢,并且低合金高强度的碳含量较高,所以使得低合金高强度的刚虽然强度高,但是很难焊接,从而使得建筑钢结构在焊接的过程中会出现延迟性的裂纹,并且还应会因为建筑钢结构的施工高度的升高而导致建筑钢结构的焊接任务变得更加困难。
1建筑钢结构焊接裂纹的特征及产生机理1.1热裂纹在较高的温度条件下,建筑钢结构焊接容易出现热裂纹,在焊接的过程中,焊缝受到温度的影响,发生了结晶反应,再加上金属本身的拉伸应力的影响,导致热裂纹呈现出来不同的形态,通过分析这些形态,又可以将其划分为不同的种类。
由于高温和拉伸应力的影响,在焊接的过程中受热不均匀,导致受热面出现了失衡的现象,这-现象导致焊缝处发生了结晶,这-结晶受到金属杂质和拉伸应力的影响,出现了多边化的裂纹[2]。
主要有两种类型的裂纹,-个是凝固裂纹,另-个是液化裂纹,还有失塑裂缝。
钢结构裂纹成因分析及防范措施_0
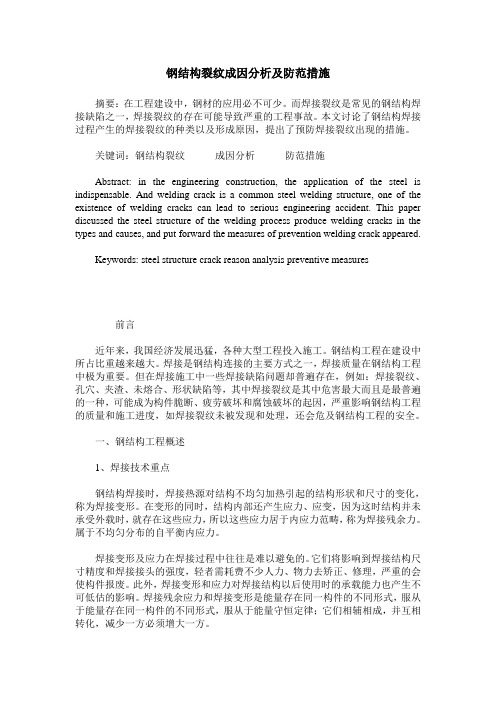
钢结构裂纹成因分析及防范措施摘要:在工程建设中,钢材的应用必不可少。
而焊接裂纹是常见的钢结构焊接缺陷之一,焊接裂纹的存在可能导致严重的工程事故。
本文讨论了钢结构焊接过程产生的焊接裂纹的种类以及形成原因,提出了预防焊接裂纹出现的措施。
关键词:钢结构裂纹成因分析防范措施Abstract: in the engineering construction, the application of the steel is indispensable. And welding crack is a common steel welding structure, one of the existence of welding cracks can lead to serious engineering accident. This paper discussed the steel structure of the welding process produce welding cracks in the types and causes, and put forward the measures of prevention welding crack appeared.Keywords: steel structure crack reason analysis preventive measures前言近年来,我国经济发展迅猛,各种大型工程投入施工。
钢结构工程在建设中所占比重越来越大。
焊接是钢结构连接的主要方式之一,焊接质量在钢结构工程中极为重要。
但在焊接施工中一些焊接缺陷问题却普遍存在,例如:焊接裂纹、孔穴、夹渣、未熔合、形状缺陷等,其中焊接裂纹是其中危害最大而且是最普遍的一种,可能成为构件脆断、疲劳破坏和腐蚀破坏的起因,严重影响钢结构工程的质量和施工进度,如焊接裂纹未被发现和处理,还会危及钢结构工程的安全。
建筑钢结构焊接裂纹的产生机理及防止措施

建筑钢结构焊接裂纹的产生机理及防止措施建筑钢结构是目前常见的建筑结构之一,它具有高强、轻量、简洁美观等优点。
然而,在实际使用中,钢结构存在一些问题,其中之一就是焊接裂纹的产生。
本文将探讨建筑钢结构焊接裂纹的产生机理及防止措施。
一、焊接裂纹的产生机理焊接裂纹主要可分为热裂纹、冷裂纹、应力裂纹。
1.热裂纹焊接时,由于局部加热,使钢材产生热变形。
当其塑性变低且残余应力积累时,钢材易于出现裂纹。
热裂纹主要是由于热应力造成的。
2.冷裂纹一般在焊后自然冷却时出现,这种裂纹的发生对于焊接工艺、材料和钢结构的使用情况等很敏感。
冷裂纹主要是由于低温下的脆性造成的。
3.应力裂纹应力裂纹主要是由于因材料、尺寸和结构等造成永久性变形产生的应力,使焊缝发生断裂。
这种裂纹的主要表现是在进行负载、温度等变化时,在原有断口处产生裂纹。
二、焊接裂纹的防止措施1.材料选择焊接材料的选择并不是随便选用,应根据实际情况选择专业的材料并在正确的离子层选择。
2.焊接工艺合理的焊接工艺非常重要。
在焊接的过程中,应该注意控制焊接的速度和节奏,以避免局部高温、局部残余应力的发生。
此外,焊接的工艺应掌握得当,包括电极的选择、焊接电流、焊接时间、频率等,以确保焊接缝有足够的强度。
3.质量控制如果缺乏质量控制,很容易忽略焊接过程中的每个细节,如使用的电极、焊接速度和温度控制等,这将极大地影响焊接接头的质量。
因此,应及时检查焊缝的质量,减少焊接裂纹等质量问题的发生。
4.故障修复当发现要素问题后,应及时进行修复。
例如,当发现焊接过程中电极受到污染时,应停止焊接并更换电极。
当发现焊接过程中有缺陷时,应及时纠正,以确保焊接的质量。
5.不断改进工艺不断改进工艺也是防止焊接裂纹的重要措施。
随着科技的不断进步,随着工艺的提高,新的焊接方法和材料的出现,改进工艺是防止焊接裂纹的重要手段。
总之,建筑钢结构焊接裂纹对建筑钢结构的使用具有一定的影响,为防止焊接裂纹的发生,应注意材料的选择、焊接工艺的合理性、质量控制等多个方面,并不断改进工艺。
钢结构的裂缝控制与维修
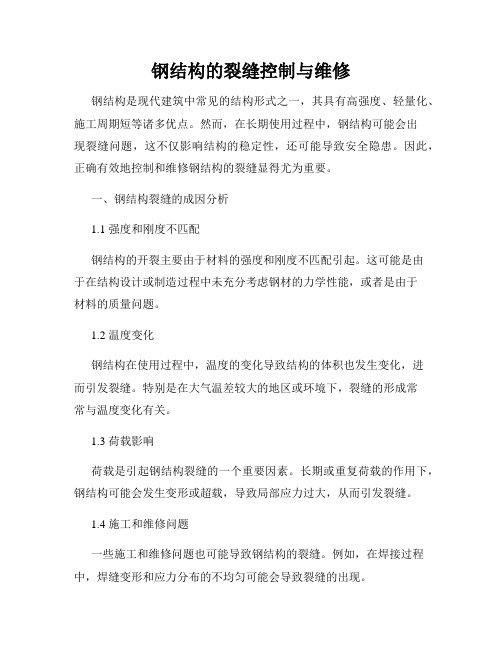
钢结构的裂缝控制与维修钢结构是现代建筑中常见的结构形式之一,其具有高强度、轻量化、施工周期短等诸多优点。
然而,在长期使用过程中,钢结构可能会出现裂缝问题,这不仅影响结构的稳定性,还可能导致安全隐患。
因此,正确有效地控制和维修钢结构的裂缝显得尤为重要。
一、钢结构裂缝的成因分析1.1 强度和刚度不匹配钢结构的开裂主要由于材料的强度和刚度不匹配引起。
这可能是由于在结构设计或制造过程中未充分考虑钢材的力学性能,或者是由于材料的质量问题。
1.2 温度变化钢结构在使用过程中,温度的变化导致结构的体积也发生变化,进而引发裂缝。
特别是在大气温差较大的地区或环境下,裂缝的形成常常与温度变化有关。
1.3 荷载影响荷载是引起钢结构裂缝的一个重要因素。
长期或重复荷载的作用下,钢结构可能会发生变形或超载,导致局部应力过大,从而引发裂缝。
1.4 施工和维修问题一些施工和维修问题也可能导致钢结构的裂缝。
例如,在焊接过程中,焊缝变形和应力分布的不均匀可能会导致裂缝的出现。
二、钢结构裂缝的控制措施2.1 结构设计阶段控制在结构设计阶段,应充分考虑钢结构的力学性能,合理选取材料,并采取合适的结构形式和连接方式,以减小应力集中和变形,从而控制裂缝的产生。
此外,还应根据实际情况考虑桥墩、梁体等部位的钢筋配筋,以提高结构的抗裂性能。
2.2 建筑施工过程控制在钢结构的建筑施工过程中,应严格按照相关规范和施工工艺要求进行操作,避免过度冲击、过度变形等问题的发生。
此外,对于焊接接头,应进行合理的预热、焊接顺序和冷却措施,以避免焊接引起的裂缝。
2.3 检测与监控通过定期的结构检测与监控,可以及早发现钢结构裂缝的迹象,并采取相应的控制措施。
常用的监测方法包括:测挠、应变、温度、振动等,这些数据的采集可以通过传感器进行实时监测和记录。
三、钢结构裂缝的维修方法3.1 补强加固对于出现裂缝的钢结构,在进行维修时,可以采用补强加固的方法。
首先需要通过有效的补强材料对结构进行加固,以提高结构的抗裂能力。
浅析钢结构焊接裂纹的产生原因及防止措施
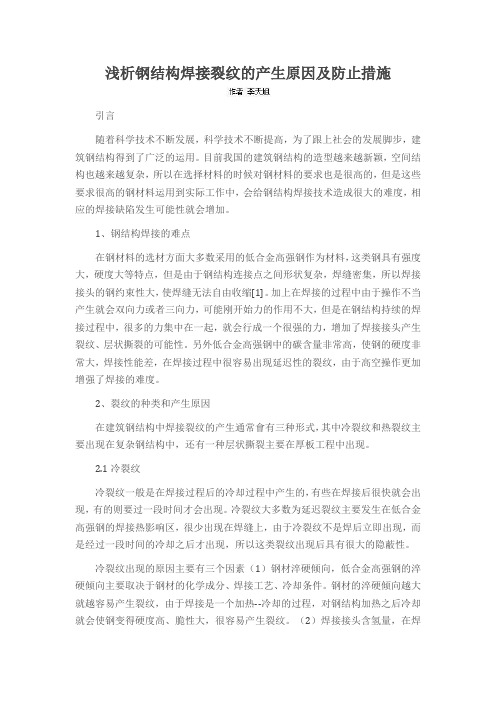
浅析钢结构焊接裂纹的产生原因及防止措施引言随着科学技术不断发展,科学技术不断提高,为了跟上社会的发展脚步,建筑钢结构得到了广泛的运用。
目前我国的建筑钢结构的造型越来越新颖,空间结构也越来越复杂,所以在选择材料的时候对钢材料的要求也是很高的,但是这些要求很高的钢材料运用到实际工作中,会给钢结构焊接技术造成很大的难度,相应的焊接缺陷发生可能性就会增加。
1、钢结构焊接的难点在钢材料的选材方面大多数采用的低合金高强钢作为材料,这类钢具有强度大,硬度大等特点,但是由于钢结构连接点之间形状复杂,焊缝密集,所以焊接接头的钢约束性大,使焊缝无法自由收缩[1]。
加上在焊接的过程中由于操作不当产生就会双向力或者三向力,可能刚开始力的作用不大,但是在钢结构持续的焊接过程中,很多的力集中在一起,就会行成一个很强的力,增加了焊接接头产生裂纹、层状撕裂的可能性。
另外低合金高强钢中的碳含量非常高,使钢的硬度非常大,焊接性能差,在焊接过程中很容易出现延迟性的裂纹,由于高空操作更加增强了焊接的难度。
2、裂纹的种类和产生原因在建筑钢结构中焊接裂纹的产生通常會有三种形式,其中冷裂纹和热裂纹主要出现在复杂钢结构中,还有一种层状撕裂主要在厚板工程中出现。
2.1冷裂纹冷裂纹一般是在焊接过程后的冷却过程中产生的,有些在焊接后很快就会出现,有的则要过一段时间才会出现。
冷裂纹大多数为延迟裂纹主要发生在低合金高强钢的焊接热影响区,很少出现在焊缝上,由于冷裂纹不是焊后立即出现,而是经过一段时间的冷却之后才出现,所以这类裂纹出现后具有很大的隐蔽性。
冷裂纹出现的原因主要有三个因素(1)钢材淬硬倾向,低合金高强钢的淬硬倾向主要取决于钢材的化学成分、焊接工艺、冷却条件。
钢材的淬硬倾向越大就越容易产生裂纹,由于焊接是一个加热--冷却的过程,对钢结构加热之后冷却就会使钢变得硬度高、脆性大,很容易产生裂纹。
(2)焊接接头含氢量,在焊接的过程中大量的溶解于熔池中,焊接结束之后进入冷却的环节,氢就会极力的逸出,但是由于冷却速度较快有些氢不能很快的逸出而保留在金属中,是钢内部出现中空的现象,也会导致钢结构脆性很大。
建筑钢结构焊接裂纹的产生机理及防止措施

建筑钢结构焊接裂纹的产生机理及防止措施建筑钢结构是现代建筑中广泛采用的结构形式,而钢结构的连接方式主要依赖于焊接。
然而,焊接过程中很容易出现裂纹,严重影响建筑物的使用寿命和安全性。
本文将介绍建筑钢结构焊接裂纹的产生机理及防止措施。
一、焊接裂纹的产生机理1. 焊接应力引起的裂纹焊接时会产生热应力和冷却应力,这些应力超过钢材的强度极限,容易导致裂纹产生。
此类裂纹往往在焊接后立即就能够显现出来。
2. 焊接结构变形引起的裂纹焊接后,结构体内部产生热变形和形变应力,如果没有经过充分的处理,就会在应力集中处出现裂纹。
这种裂纹通常会在一段时间后才能被发现。
3. 焊接材料过硬引起的裂纹焊接中使用的材料必须具备良好的可焊性。
如果使用的材料过硬,容易导致焊接裂纹的产生。
这种裂纹通常出现在较脆的区域,例如焊缝位置处。
二、防止焊接裂纹的措施1. 确保焊接材料的质量选择合适的焊接材料,确保其具备良好的可焊性和强度。
同时,在焊接过程中,严格控制焊接材料的质量,减少材料中的夹杂物和气孔,降低焊接裂纹的风险。
2. 控制焊接应力在焊接过程中,尽量避免产生过多的热应力和冷却应力。
可以采用多次短时间的焊接,使其产生的应力得到缓解。
此外,在焊接后对焊接结构进行热处理,也可以有效控制应力。
3. 提高焊接工艺水平提高焊接工艺水平,使焊接质量得到保障。
例如,合理选择焊接电流和电压、控制焊接速度、正确选择焊接角度等。
同时,要严格按照焊接规范执行焊接工艺,确保焊接质量。
总之,建筑钢结构焊接裂纹的产生具有一定的规律性和可预见性。
只要采取合适的防止措施,就能够有效地控制焊接裂纹的产生,提高建筑物的使用寿命和安全性。
钢结构裂纹成因分析及防范措施
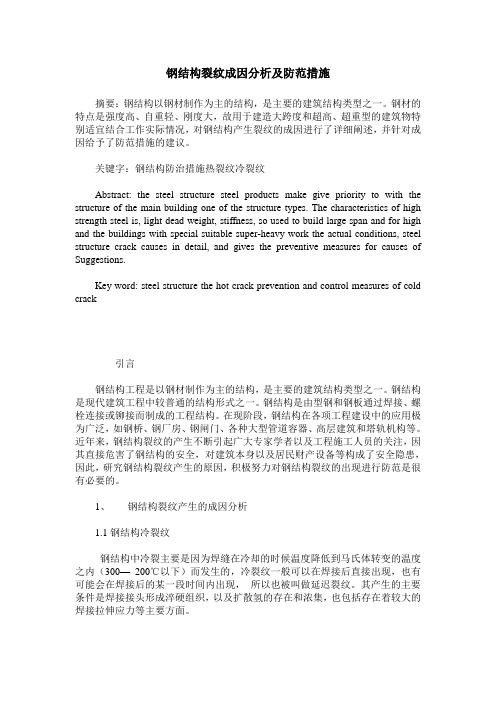
钢结构裂纹成因分析及防范措施摘要:钢结构以钢材制作为主的结构,是主要的建筑结构类型之一。
钢材的特点是强度高、自重轻、刚度大,故用于建造大跨度和超高、超重型的建筑物特别适宜结合工作实际情况,对钢结构产生裂纹的成因进行了详细阐述,并针对成因给予了防范措施的建议。
关键字:钢结构防治措施热裂纹冷裂纹Abstract: the steel structure steel products make give priority to with the structure of the main building one of the structure types. The characteristics of high strength steel is, light dead weight, stiffness, so used to build large span and for high and the buildings with special suitable super-heavy work the actual conditions, steel structure crack causes in detail, and gives the preventive measures for causes of Suggestions.Key word: steel structure the hot crack prevention and control measures of cold crack引言钢结构工程是以钢材制作为主的结构,是主要的建筑结构类型之一。
钢结构是现代建筑工程中较普通的结构形式之一。
钢结构是由型钢和钢板通过焊接、螺栓连接或铆接而制成的工程结构。
在现阶段,钢结构在各项工程建设中的应用极为广泛,如钢桥、钢厂房、钢闸门、各种大型管道容器、高层建筑和塔轨机构等。
近年来,钢结构裂纹的产生不断引起广大专家学者以及工程施工人员的关注,因其直接危害了钢结构的安全,对建筑本身以及居民财产设备等构成了安全隐患,因此,研究钢结构裂纹产生的原因,积极努力对钢结构裂纹的出现进行防范是很有必要的。
建筑钢结构焊接裂纹产生原因及防治措施探究

建筑钢结构焊接裂纹产生原因及防治措施探究摘要:作为当前建筑施工的重要形态,钢筋结构的应用不仅能保证工程建设的稳定性和耐久性,更能实现其生产成本的控制和经济效益收获。
然而工程建设中,钢筋结构的质量提升受到其焊接裂纹的直接影响。
本文阐述建筑钢结构焊接裂纹的主要形态,并对热裂纹、冷裂纹、及层状撕裂的产生原因进行分析;然后针对性的提出防治措施。
以期有利于建筑钢结构焊接质量的提升,进而推动建筑工程的进一步发展。
关键词:建筑工程;焊接裂纹;原因;对策随着建筑施工技术的不断成熟,建筑结构的应用形态发生了重大改变。
当前环境下,钢筋结构是建筑工程的重要应用形式,与传统结构形式相比,钢筋结构材料不仅具有较好的刚度和强度优势,而且在抗震性能和经济效益方面效果突出;其充分满足了人们对建筑稳定性和耐久性的质量要求。
然而在实践过程中,钢筋结构建筑对于焊接的质量控制较为严格,一旦施工过程不准确,就容易导致焊接裂纹的产生;基于此,进行建筑钢结构焊接裂纹的防治已成为现代建筑工程人员研究的重要内容,本文就此展开分析。
一、建筑钢结构焊接裂纹的主要形态焊接裂纹是建筑钢结构的主要病害之一,其对于建筑工程的发展具有深刻影响:一方面,其制约了钢筋结构工程应用性能的发挥,在影响工程质量的同时,对建设单位经济效益和社会效益的实现造成较大阻碍。
另一方面,其影响业主的应用安全,对于人们生活质量提升影响重大。
实践过程中,建筑钢结构的焊接裂纹主要包含了以下类型:其一,焊接热裂纹。
这种裂纹在较高的温度下产生,并且包含了结晶裂纹和液化裂纹两种形态[1]。
其中,前者形成于焊接熔池初次结晶过程中,而后者的产生是受到了重铸收缩礼的影响。
其二,焊接冷裂纹。
与其它裂纹相比,冷裂纹主要产生于低、中合金钢焊接区域,并且具有延迟性与潜在性的特征,安全隐患较大。
需要注意的是,冷裂纹一般在300~200℃以下产生。
其三,层状撕裂纹。
层状撕裂纹主要出现在钢结构焊缝根部、边缘脚趾处以及焊接热影响区;其是影响钢筋结构质量提升的重要原因(如图1)。
钢结构裂纹成因分析及防范措施

钢结构裂纹成因分析及防范措施摘要:根据工程实践经验,对钢结构裂纹产生的内在原因和外在原因进行了分析,提出了有针对性的解决措施,取得了较好的效果。
关键词:钢结构;裂纹;安装;防治措施Abstract: according to the practical engineering experience, the steel structure crack the internal cause and external causes are analyzed, and the corresponding solutions, and good results have been achieved.Keywords: steel structure; Crack; Installation; Prevention and control measures 引言:焊接裂纹是钢结构制作过程中经常发生且危害较大的质量通病。
近儿年来,安钢集团1 2 0 T转炉及1 5 0 T转炉一1 7 8 0 mm 热连轧主厂房均为钢结构,厂房柱子为焊接H型钢,公辅外网管道为卷焊管,总制作量多达一万多吨,在初期制作过程中,不时发现焊接裂纹,如某分公司管道制作过程中出现纵向裂纹,降低焊接接头的承载能力,最终导致焊接结构的破坏,缩短结构寿命,间接延误工程工期,增加工程施工成本。
焊接裂纹是钢结构制作过程中危害最大的缺陷,一旦发现必须进行返修焊接。
下面结合工程实践,对钢结构制作过程中裂纹产生的原因及防治措施进行简要分析。
1、裂纹产生某工程钢结构加工任务由我司承制,工地由某地施工单位安装,2012 年1月18日,施工人员在安装现场巡检中,发现工程23m标高处外取热器下支座梁与框架梁连接节点腹板处出现裂纹,接报后,承制与安装双方进行了现场调查,平台钢结构主次梁焊接接头部位存在裂纹缺陷,拿出补修方案并100%探伤,并委托专业单位对裂纹梁主材进行硬度检测和现场取样分析。
钢结构焊接裂纹的原因及预防措施

感谢您的观看
THANKS
焊接速度过快或过 慢,使得焊缝未能 充分熔合,容易产 生裂纹。
结构设计问题
结构设计不合理,如焊缝位置不当、焊缝数量过多等,导致焊缝受力不均,容易 产生裂纹。
构件制作过程中预留的应力没有得到有效释放,焊接过程中容易引起应力集中, 导致裂纹产生。
施工环境影响
施工环境温度过低,使得钢材 变脆,容易产生裂纹。
优化结构设计
在满足使用要求的前提下,尽量减少应力 集中部位的设计。
05
结论与展望
结论
焊接裂纹是钢结构中常见的缺陷之一,可能导致结构承载能力下降、安全性能降 低甚至发生事故。
分析了钢结构焊接裂纹的成因,主要包括材料、设计、施工和使用环境等因素。
针对不同的裂纹类型和成因,提出了相应的预防和补救措施,包括选用合适的材 料、优化结构设计、提高施工质量和加强定期检查等方面。
预热处理
在焊接前对钢材进行预热处理,降低因温差导致 的应力,减少裂纹产生的可能性。
后热处理
在焊接完成后进行后热处理,进一步消除焊接应 力,防止裂纹的产生。
04
案例分析
工程概况
项目名称
某大桥钢结构桥梁
工程背景
该大桥为城市主干道的重要组成部分,钢结构桥梁采用高强度钢 材焊接而成。
工程特点
钢结构构件多,焊接工作量大,对焊接质量要求高。
钢结构焊接裂纹的原因及预 防措施
2023-11-06
目 录
• 概述 • 钢结构焊接裂纹的原因 • 预防钢结构焊接裂纹的措施 • 案例分析 • 结论与展望
01
概述
钢结构焊接裂纹的定义
• 钢结构焊接裂纹是指在焊接过程中,由于受到材料、设计、 对钢结构的强度和稳定性产生严重影响。
浅谈钢结构的裂缝成因及控制方法
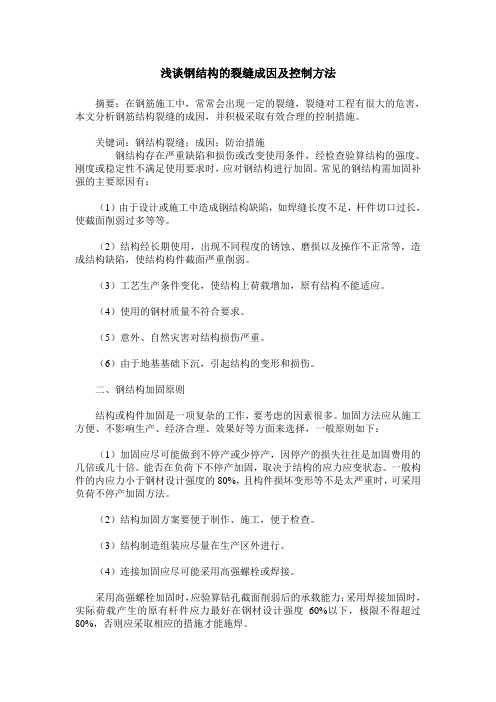
浅谈钢结构的裂缝成因及控制方法摘要:在钢筋施工中,常常会出现一定的裂缝,裂缝对工程有很大的危害,本文分析钢筋结构裂缝的成因,并积极采取有效合理的控制措施。
关键词:钢结构裂缝;成因;防治措施钢结构存在严重缺陷和损伤或改变使用条件,经检查验算结构的强度、刚度或稳定性不满足使用要求时,应对钢结构进行加固。
常见的钢结构需加固补强的主要原因有:(1)由于设计或施工中造成钢结构缺陷,如焊缝长度不足,杆件切口过长,使截面削弱过多等等。
(2)结构经长期使用,出现不同程度的锈蚀、磨损以及操作不正常等,造成结构缺陷,使结构构件截面严重削弱。
(3)工艺生产条件变化,使结构上荷载增加,原有结构不能适应。
(4)使用的钢材质量不符合要求。
(5)意外、自然灾害对结构损伤严重。
(6)由于地基基础下沉,引起结构的变形和损伤。
二、钢结构加固原则结构或构件加固是一项复杂的工作,要考虑的因素很多。
加固方法应从施工方便、不影响生产、经济合理、效果好等方面来选择,一般原则如下:(1)加固应尽可能做到不停产或少停产,因停产的损失往往是加固费用的几倍或几十倍。
能否在负荷下不停产加固,取决于结构的应力应变状态。
一般构件的内应力小于钢材设计强度的80%,且构件损坏变形等不是太严重时,可采用负荷不停产加固方法。
(2)结构加固方案要便于制作、施工,便于检查。
(3)结构制造组装应尽量在生产区外进行。
(4)连接加固应尽可能采用高强螺栓或焊接。
采用高强螺栓加固时,应验算钻孔截面削弱后的承载能力;采用焊接加固时,实际荷载产生的原有杆件应力最好在钢材设计强度60%以下,极限不得超过80%,否则应采取相应的措施才能施焊。
三、钢结构加固方法(一)、加固方法概述钢结构加固的主要方法有:减轻荷载、改变计算图形、加大原结构构件截面和连接强度、阻止裂纹扩展等。
当有成熟经验时,也可采用其他的加固方法。
经鉴定需要加固的钢结构,根据损害范围一般分为局部加固和全面加固。
增加原有构件截面的加固方法是最费料最费工的方法(但往往是可行的方法);改变计算简图的方法最有效且多种多样,其费用也大大下降。
钢结构焊接裂纹的原因及防治措施

钢结构焊接裂纹的原因及防治措施钢结构是现代建筑中常见的结构形式之一,它具有重量轻、强度高、施工速度快等优点,因此被广泛应用于各类建筑工程中。
然而,在钢结构的制造和施工过程中,焊接裂纹往往成为一个常见的质量问题。
本文将探讨钢结构焊接裂纹的形成原因,并提出相应的防治措施。
一、焊接裂纹的形成原因1.1 材料问题钢材的组织结构和化学成分不合理是导致焊接裂纹的主要原因之一。
当钢材中含有含碳、硫、磷等含量超过规定标准的元素时,焊接时易产生高硬度和脆性物质,从而引发裂纹的形成。
1.2 焊接参数不当焊接过程中,焊接电流、焊接速度、焊接温度等焊接参数的选择不当,都可能导致焊接裂纹的生成。
例如,焊接电流过大会导致材料过热,从而在焊接接头中产生裂纹。
1.3 体积收缩差异钢材在焊接过程中会受到热量的影响而发生热胀冷缩,而焊接接头中的同时发生焊接金属的热收缩和焊接基体的冷缩,而两者之间的体积收缩差异可能引起焊接裂纹的形成。
1.4 焊接应力焊接过程中,焊接热量引入工件,产生应力集中,而大的应力集中可能导致焊接裂纹的生成。
特别是当焊接接头应力集中点的应力超过材料的承载极限时,裂纹便会发生。
二、焊接裂纹的防治措施2.1 材料严格控制在钢结构的制造和施工过程中,应严格控制材料的质量。
选用质量合格、符合要求的钢材,特别是控制其中的碳含量、硫含量、磷含量等关键成分的含量。
2.2 合理选择焊接参数在焊接过程中,应根据具体的钢材和焊接需求,合理选择焊接参数。
通过调整焊接电流、焊接速度、焊接温度等参数,确保焊接接头的均匀加热,避免产生过度应力。
2.3 预热和后续热处理对于较大尺寸、厚度较大的焊接接头,应进行预热处理。
通过预热可以减少焊接接头的冷缩和应力积聚,从而减少焊接裂纹的产生。
同时,在焊接完成后,可采取适当的后续热处理,通过热处理来消除残余应力。
2.4 控制焊接应力在焊接过程中,应合理控制焊接应力。
可以通过选用合适的焊接顺序、采用适当的焊接顺序交替焊接等方法,来减少焊接接头中的应力集中,降低焊接裂纹的风险。
钢结构焊接工艺常见质量通病及控制措施

钢结构焊接工艺常见质量通病及控制措施在钢结构的制作过程中,焊接是其中一个关键的工艺。
尽管焊接是一个普遍采用的工艺,但仍然存在许多质量通病,例如裂纹、气孔、结构变形等。
在一个钢结构项目中,如果焊接制造不合格,这将会导致安全问题以及质量问题。
因此,钢结构焊接必须保证质量。
本文将讨论钢结构焊接工艺中的常见质量通病及控制措施。
裂纹裂纹是钢结构焊接的一个常见质量通病。
裂纹的主要原因是其焊接热影响区(HAZ)处的钢材变形和塑性变形,这会导致 HA Z出现冷裂纹和热裂纹。
这些裂纹不仅会导致制造不合格,还会降低钢结构的强度和稳定性。
针对裂纹的控制措施如下:•采用低氢电极,以降低氢的含量;•加强热控制,特别是对于材料的前热和焊接后的加热和冷却过程;•合理的焊接顺序和技术参数,避免过度的热影响区;•采用预加热的方法。
气孔气孔是钢结构焊接的另一个常见质量通病。
气孔的主要原因是焊接时的不良金属熔融和氧化还原反应。
这些小气泡将会形成焊接孔,而且加强了通孔的形成。
正确的焊接控制和维护,可以有效地控制气孔的生成:•采用良好的流体力学和电极加料控制;•避免油脂、腐蚀物和表面水分的污染;•加强预热、后热和热处理;•采用自动化焊接方法,以降低人为因素对气孔的影响。
结构变形钢结构焊接时,由于热的影响,容易导致结构变形。
在钢结构焊接制造过程中,因为需要保证钢材的尺寸精度和方向性,因此要控制结构变形。
以下是针对钢结构焊接时结构变形的控制措施:•提供适当的支撑设备,保证焊接质量;•聚焦于焊接顺序和技术参数;•采用较低的焊接电流和速度,进行轮廓加热;•加强热处理。
焊接脆化焊接脆化是钢结构焊接的一个常见质量通病。
焊接脆化的主要原因是钢材的化学成分和焊接的工艺参数不稳定。
这种焊接脆化是不允许存在的,因为它在使用中会逐渐变得更脆弱而最终断裂。
所以,针对焊接脆化的控制措施如下:•采用标准的焊接工艺,以保证焊接质量;•自动焊接方法;•选择具有补偿效应的材料,以提高焊接质量;•注意加工和设备维护,防止钢材的表面氧化。
- 1、下载文档前请自行甄别文档内容的完整性,平台不提供额外的编辑、内容补充、找答案等附加服务。
- 2、"仅部分预览"的文档,不可在线预览部分如存在完整性等问题,可反馈申请退款(可完整预览的文档不适用该条件!)。
- 3、如文档侵犯您的权益,请联系客服反馈,我们会尽快为您处理(人工客服工作时间:9:00-18:30)。
钢结构的裂纹成因及防范措施
钱汉忠
南通新华钢结构工程有限公司
摘要:宿迁恒力国际大酒店工程采用劲性钢结构与钢筋混凝土组成的混合结构。
因此,在钢构件的制作和安装过程中,对钢构件的质量控制显得尤为重要。
尤其是对钢构件焊接过程中的裂纹控制。
本文分析了本工程制作和安装过程中钢结构裂纹产生的原因,提出了有针对性的解决措施,取得了较好的结果。
关键词:钢结构;安装;裂纹;解决措施;
1、裂纹产生
施工人员在安装现场质量检查中,发现工程12.6m标高处支座梁与框架梁连接节点腹板处出现裂纹,接报后,承制与安装双方进行了现场调查,平台钢结构主次梁梁焊接接头部位存在裂纹缺陷,拿出补修方案并100%探伤,并委托专业单位对裂纹梁主材进行硬度检测和现场取样分析。
此次复检共检查类同梁12根,发现裂纹仅此1条,裂纹产生的位置在主腹板与次梁腹板连接焊缝位置。
焊接接头部位存在的裂纹为个别现象,裂纹在接头的热影响区围绕接头呈半弧形。
裂裂纹形态见图1梁立面截面图。
图1梁立面截面图
2、裂纹产生的原因分析
蒸馏平台钢结构所用钢材为Q345B低合金钢,进厂原材料经过严格的各项复
检,化学成分和力学性能均满足GB/T15911994《低合金高强度结构钢》的要求。
经现场硬度检测和现场取样分析,化学成分和力学性能均符合国标要求,见表1和表2。
表1 C
Mn Si P S V Nb Ti 0.18 1.33 0.5 0.035
0.03 0.05 0.04 0.01
表2 Mpa s /δ
Mpa b /δ %/s δ J C A kv /)20(︒+ 360 530
23 38
在正常情况下该钢种可焊性良好,不易产生焊接裂纹。
安装现场发现的裂纹分布于焊接接头的热影响区,具有延迟性,由此可以断定此种裂纹为焊接冷裂纹中的延迟裂纹。
裂纹产生的主要原因分析如下。
2.1施工人员自作主张,在插入接头位增加焊接补强板
在梁结构设计过程中设计并没有增加筋板和补强板,施工人员在安装前擅自在腹板侧增加一块补强板,工序上先进行了补强焊接,然后将次梁插入,随后安装梁,将梁腹板紧贴补强在主梁腹板处进行二次焊接, 造成局部区域焊缝密度过大,使得焊接时这些部位的拘束应力过大,而拘束应力大是产生冷裂纹的重要原因之一,这就大大增加了裂纹产生的可能性。
如图2所示。
图2 擅自增加的补强板
2.2 焊接施工现场条件较差,工艺制定和执行不良,特别是焊前预热和焊后缓冷不到位
焊接工艺技术防止缺陷产生的措施主要有:焊前预热、焊后缓冷;选用合适焊条和工艺参数,使用前在保温箱内按规定的温度、时间加热保温,使用时放置在保温桶内取用等。
该处主材腹板分别16mm、20mm厚,翼板分别25mm、32mm厚,无拘束度常温下该结构腹板间角焊道不需进行预热和焊后缓冷。
《铁路钢桥制造规范》(TB10212)17.2.6、17.4.4规定:焊接环境温度,低合金高强度结构钢不应低于5℃。
该工程冬季裂纹发生时日当地气象部门气温数据温度为(-7~-19℃),焊接过程中遭遇严寒的影响而未采取有效的防护措施(焊补强板侧时未预热),也无焊后良好保温消除应力热处理措施,焊缝金属冷却速度很快,对焊缝周围产生张力,同时焊缝中也容易出现淬硬的马氏体组织。
对于Q345来说低碳合金元素含量比低碳钢多,材料淬硬倾向和出现裂纹的倾向大。
当残余应力达到材料的屈服极限时,焊缝金属产生塑性变形,当变形量超过材料的极限时产生裂纹,这是裂纹产生的主因。
2.3 构造刚性约束大,施工时,荷载分布不尽合理
该结构次梁安装中端部已受刚性约束,在梁焊接时梁上的钢构件已经安装,构件的荷载通过临时支撑被传递到平台梁上,临时支撑位置不合理,以构件中心为重心,重心向1轴侧只有一个支撑立于该次梁上,此次梁承受相对较大荷载,而此荷载又全部通过次梁的焊接接头传到框架梁腹板上,增加了腹板处的内应力,直接导致焊缝区残余应力增大。
原则上在有荷载情况下应该卸载后施焊,施工没有充分重视焊接时荷载的因素,造成主梁腹板焊缝区拘束应力过大,这也增加了裂纹产生的可能性。
通过以上分析可以看出,由于各种措施不得当,使得焊缝中形成淬硬组织;同时封闭的刚性约束加上焊接时荷载较大,造成焊接接头部位很大的拘束应力,在这些因素的共同作用下,产生了焊接冷裂纹。
3、防范与改善措施
接工艺支持要求后,针对裂纹返修制定如下返修工艺方案:
3.1 先卸除荷载缺陷处荷载,尽量增加焊缝收缩的自由度。
3.2 选经验丰富的有资质证焊工和气刨施工补修人员。
3.3 选低氢型焊条材料:E5015或E5016φ3.2mm(350℃烘焙1h)。
ER50-6气体保护焊丝,规格:φ1.2mm,使用富氩混合气或含水符合GB50205要求的纯CO 。
严格烘干和保温措施。
3.4 采用PT/超声波探伤对缺陷定位,焊缝缺陷可见范围两端各+50mm。
焊缝缺陷的剔除用碳弧气刨加砂轮打磨干净渗碳层。
补修焊工参与缺陷的剔除工作,确保剔除部位正确,严禁在返修区域或母材上造成新的缺陷;
3.5 焊接前,对焊缝两侧75~100mm宽周围区域用氧-乙炔火焰加热到120℃(考虑T型接头实际热传导情况和环境温度低于0℃),用温度器在距焊缝100mm处测量,为防止大风带来的不利影响应搭设临时防风棚。
3.6 焊道周围20mm范围内的锈、水、油污等杂质的清理要彻底,在次梁侧用8mm 碳棒刨轻刨并打磨干净渗碳层,深度控制8mm左右,用手工电弧焊施焊,也可用气体保护焊。
为防止裂缝出现在敏感的第一道焊缝和焊根,适当加大电流,减慢焊速。
焊完一遍后,彻底清理焊道。
尽量采用多层多道焊或分段间隔焊跳焊以减少焊接残余应力的产生,一面完成后,在腹板另一侧清根彻底后补焊,要求连续施工,中途停工需在施工前检查焊道质量并重新预热,焊缝不得有弧坑、夹渣、裂纹、咬边以防止形成应力集中。
3.7焊后热处理,防止焊接区域迅速冷却而产生裂纹,在焊缝两侧100mm宽,后热至200℃,消氢和消除应力1h,后用石棉等保温缓冷。
3.8若存在经设计、业主方确认的加劲补强板方案,参考以上预热后热方案执行。
4、结束语
采取以上针对性措施后,经过对现场返修焊道100%超声检验和100%目视检查,未发现焊缝表面裂纹缺陷。
经过数天后的再次复检,也未发现延迟裂纹出现。
因此,可以确定上述对裂纹产生的原因分析准确,所采取的防范和返修工艺措施效果良好。
在本工程应用的现场安装方面的经验,可以对今后复杂结构和环境条件的安装起到积极的借鉴作用。
参考文献
[1]钢结构设计手册(第三版). 北京: 中国建筑工业出版社.。