鼓形齿的成形磨削方法及其分析
成型磨齿裂纹产生原因分析及工艺优化措施
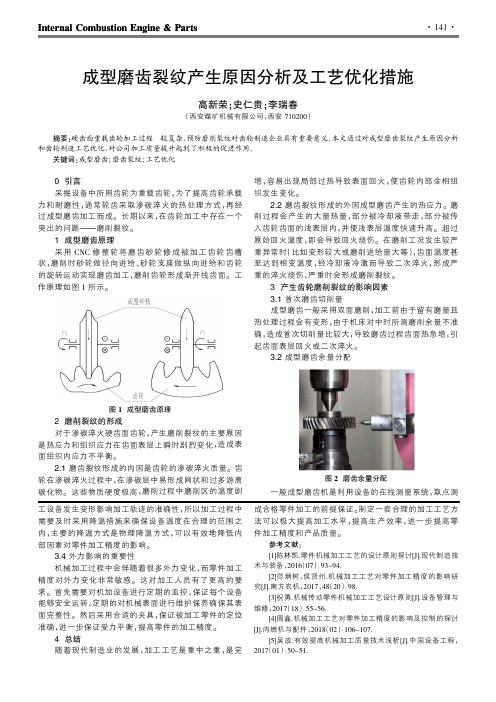
图1成型磨齿原理2磨削裂纹的形成对于渗碳淬火硬齿面齿轮,产生磨削裂纹的主要原因是热应力和组织应力在齿面表层上瞬时剧烈变化,造成表面组织内应力不平衡。
2.1磨齿裂纹形成的内因是齿轮的渗碳淬火质量。
齿轮在渗碳淬火过程中,在渗碳层中易形成网状和过多游离碳化物。
这些物质硬度极高,磨削过程中磨削区的温度剧图2磨齿余量分配一般成型磨齿机是利用设备的在线测量系统,工设备发生变形影响加工轨迹的准确性,所以加工过程中需要及时采用降温措施来确保设备温度在合理的范围之主要的降温方式是物理降温方式,可以有效地降低内部因素对零件加工精度的影响。
3.4外力影响的重要性机械加工过程中会伴随着很多外力变化,而零件加工精度对外力变化非常敏感。
这对加工人员有了更高的要成合格零件加工的前提保证。
制定一套合理的加工工艺方法可以极大提高加工水平,提高生产效率,进一步提高零件加工精度和产品质量。
参考文献:陈林凯.零件机械加工工艺的设计原则探讨[J].2016(07):93-94.范炳树,侯贤州.机械加工工艺对零件加工精度的影响研南方农机,2017,48(20):98.机械传动零件机械加工工艺设计原则[J].18):55-56.机械加工工艺对零件加工精度的影响及控制的探讨图3齿槽对中位置磨齿对中后,为防止首次切削量过大,须扩大公法线加即给必要的安全距离,安全距离一般保证此时需考虑加工齿轮结构形状及变形后的最大磨削余量与最小磨削余量。
从磨削条件优化正确选择砂轮并优化修整参数采用成型磨齿,磨削齿面渗碳淬火硬度的齿轮,使用适合渗碳淬火硬齿面齿轮磨削的G19VSP-PSX砂轮。
在保证齿面光洁度情况下,粗磨用粒度小的,精磨用粒度大的。
采用金刚石修整轮并优化修整参数,使砂轮达到最佳修磨效果。
调整冷却位置,以达到最佳冷却效果在磨削前,检查油嘴位置、冷却液压力、过滤系统是否图4冷却管位置通过对成型磨齿裂纹形成原因分析和齿轮冷热加工大大降低了齿轮磨削裂纹概率,提高了齿轮加为企业创造了良好的经济效益。
鼓形齿——精选推荐

我个人觉得应该没有那么核心,当然多数人会这么认为,基于以下几点理由:1)修形其实说白了很简单,因为齿轮再复杂只有两个方向(齿形(或称齿高)、齿向(或称齿长)),理解了这一点问题就简单了;2)修形量一般来自于经验,即使你的数据告诉别人也只能作为参考,因为应用领域不同、精度不同、制造工艺不同,而且经验数据,稍微有点差别不会影响结果;3)齿轮传动是两个以上齿轮配合,单个齿轮修形再好也无用,关键是一对齿轮综合考虑,调试很重要,如果一个齿轮不修形,用另一个修形去与之配合,这样问题会更简单,因为变量少了;4)大家的方法不同,比如齿顶修缘,有用直线的、有用圆弧的、有用抛物线的、有用二次样条曲线的,同样的量,修形的结果可能会不同;制造工艺也不同,有机加工的(滚、插、剃),有CAD造型后数控铣的、有用模具锻造的,结果也会不同;关键还是一对齿轮的配合质量,同样可以只修一个;《转》有意识地微量修整齿轮的齿面,使其偏离理论齿面的工艺措施。
按修形部位的不同,轮齿修形可分为齿廓修形和齿向修形。
齿廓修形微量修整齿廓,使其偏离理论齿廓。
齿廓修形包括修缘、修根和挖根等.修缘是对齿顶附近的齿廓修形。
通过修缘可以减轻轮齿的冲击振动和噪声,减小动载荷,改善齿面的润滑状态,减缓或防止胶合破坏。
修根是对齿根附近的齿廓修形。
修根的作用与修缘基本相同,但修根使齿根弯曲强度削弱。
采用磨削工艺修形时,为提高工效有时以小齿轮修根代替配对大齿轮修缘。
挖根是对轮齿的齿根过渡曲面进行修整。
经淬火和渗碳的硬齿面齿轮,在热处理后需要磨齿,为避免齿根部磨削烧伤和保持残余压应力的有利作用,齿根部不应磨削,为此在切制时可进行挖根。
此外,通过挖根可增大齿根过渡曲线的曲率半径,以减小齿根圆角处的应力集中。
齿向修形沿齿线方向微量修整齿面,使其偏离理论齿面。
通过齿向修形可以改善载荷沿轮齿接触线的不均匀分布,提高齿轮承载能力。
齿向修形的方法主要有齿端修薄、螺旋角修整、鼓形修整和曲面修整等.齿端修薄是对轮齿的一端或两端在一小段齿宽上将齿厚向端部逐渐削薄它是最简单的修形方法,但修整效果较差。
鼓形齿加工方法研究
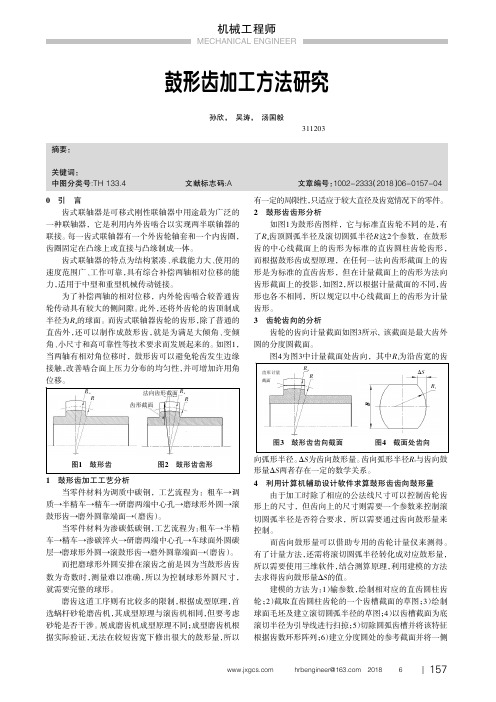
鼓形齿加工方法研究孙欣,吴涛,汤国毅(杭州前进齿轮箱集团股份有限公司,杭州311203)摘要:鼓形齿连接轴是齿式联轴器的重要组成部件。
介绍了此类零件加工的原理、鼓形量测算方法、计量及调试方法等。
结合计算机辅助设计方法建立模型,来测算出零件所需调试量,精确有效地加工出此类零件。
关键词:鼓形齿;加工方法;计算机辅助建模;测算;编程;滚齿中图分类号:TH 133.4文献标志码:A文章编号:员园园圆原圆猿猿猿(圆园员8)0远原园157原园40引言齿式联轴器是可移式刚性联轴器中用途最为广泛的一种联轴器,它是利用内外齿啮合以实现两半联轴器的联接。
每一齿式联轴器有一个外齿轮轴套和一个内齿圈,齿圈固定在凸缘上或直接与凸缘制成一体。
齿式联轴器的特点为结构紧凑、承载能力大、使用的速度范围广、工作可靠,具有综合补偿两轴相对位移的能力,适用于中型和重型机械传动链接。
为了补偿两轴的相对位移,内外轮齿啮合较普通齿轮传动具有较大的侧间隙。
此外,还将外齿轮的齿顶制成半径为R a 的球面。
而齿式联轴器齿轮的齿形,除了普通的直齿外,还可以制作成鼓形齿,就是为满足大倾角、变倾角、小尺寸和高可靠性等技术要求而发展起来的。
如图1,当两轴有相对角位移时,鼓形齿可以避免轮齿发生边缘接触,改善啮合面上压力分布的均匀性,并可增加许用角1鼓形齿加工工艺分析当零件材料为调质中碳钢,工艺流程为:粗车寅调质寅半精车寅精车寅研磨两端中心孔寅磨球形外圆寅滚鼓形齿寅磨外圆靠端面寅(磨齿)。
当零件材料为渗碳低碳钢,工艺流程为:粗车寅半精车寅精车寅渗碳淬火寅研磨两端中心孔寅车球面外圆碳层寅磨球形外圆寅滚鼓形齿寅磨外圆靠端面寅(磨齿)。
而把磨球形外圆安排在滚齿之前是因为当鼓形齿齿数为奇数时,测量难以准确,所以为控制球形外圆尺寸,就需要完整的球形。
磨齿这道工序则有比较多的限制,根据成型原理,首选蜗杆砂轮磨齿机,其成型原理与滚齿机相同,但要考虑砂轮是否干涉。
展成磨齿机成型原理不同;成型磨齿机根据实际验证,无法在较短齿宽下修出很大的鼓形量,所以有一定的局限性,只适应于较大直径及齿宽情况下的零件。
齿轮磨削工艺技术
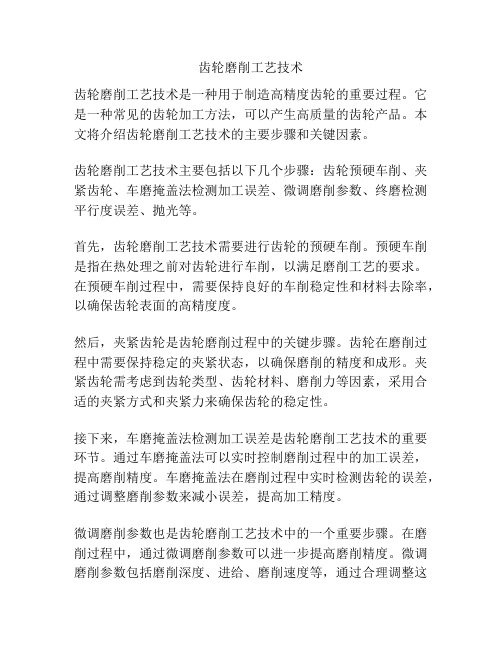
齿轮磨削工艺技术齿轮磨削工艺技术是一种用于制造高精度齿轮的重要过程。
它是一种常见的齿轮加工方法,可以产生高质量的齿轮产品。
本文将介绍齿轮磨削工艺技术的主要步骤和关键因素。
齿轮磨削工艺技术主要包括以下几个步骤:齿轮预硬车削、夹紧齿轮、车磨掩盖法检测加工误差、微调磨削参数、终磨检测平行度误差、抛光等。
首先,齿轮磨削工艺技术需要进行齿轮的预硬车削。
预硬车削是指在热处理之前对齿轮进行车削,以满足磨削工艺的要求。
在预硬车削过程中,需要保持良好的车削稳定性和材料去除率,以确保齿轮表面的高精度度。
然后,夹紧齿轮是齿轮磨削过程中的关键步骤。
齿轮在磨削过程中需要保持稳定的夹紧状态,以确保磨削的精度和成形。
夹紧齿轮需考虑到齿轮类型、齿轮材料、磨削力等因素,采用合适的夹紧方式和夹紧力来确保齿轮的稳定性。
接下来,车磨掩盖法检测加工误差是齿轮磨削工艺技术的重要环节。
通过车磨掩盖法可以实时控制磨削过程中的加工误差,提高磨削精度。
车磨掩盖法在磨削过程中实时检测齿轮的误差,通过调整磨削参数来减小误差,提高加工精度。
微调磨削参数也是齿轮磨削工艺技术中的一个重要步骤。
在磨削过程中,通过微调磨削参数可以进一步提高磨削精度。
微调磨削参数包括磨削深度、进给、磨削速度等,通过合理调整这些参数可以减小磨削误差,提高加工精度。
终磨检测平行度误差也是齿轮磨削工艺技术中的一个关键环节。
通过终磨检测可以准确测量齿轮的平行度误差,进一步改善加工精度。
终磨检测平行度误差需要使用高精度的测量仪器和设备,以确保测量结果的准确性。
最后,齿轮磨削工艺技术还需要进行抛光等后续处理。
抛光可以进一步提高精度和光洁度,使得齿轮的表面更加光滑和平整。
总的来说,齿轮磨削工艺技术是一种制造高精度齿轮的重要方法。
通过预硬车削、夹紧齿轮、车磨掩盖法检测加工误差、微调磨削参数、终磨检测平行度误差和抛光等步骤,可以获得高质量的齿轮产品。
这些步骤中的关键因素包括材料选用、磨削参数调整、夹紧方式等,需要进行合理的选择和调整,以实现高精度度的齿轮磨削。
航空高精度鼓形齿轮加工及齿面修形方法研究

航空高精度鼓形齿轮加工及齿面修形方法研究作者:王长清来源:《科技创新与应用》2016年第35期摘要:在航空领域使用的鼓形齿轮,具有尺寸精度高、结构复杂且集成化程度高的特点,导致该类零件的加工格外困难。
文章主要介绍了基于多用途、高精度新型数控磨齿机和不可修整CBN砂轮加工鼓形齿轮的方法,研究加工过程中的齿形齿向误差分析和修正方法,填补了公司在加工小模数鼓形齿方面的技术空白。
关键词:鼓形齿;多轴数控磨削;鼓形量分布1 概述鼓形齿轮与直齿轮相比,以其承载能力强、角位移补偿量大、齿面啮合良好、噪声小等优点,在联轴器等民用产品广泛使用。
航空用鼓形齿轮,一般用于具有弹性要求的轴类齿轮传扭结构件上,属于关键零部件。
见图1,由于航空用鼓形齿轮的齿形轮廓特殊和尺寸精度要求高,只能用高精度数控磨齿机进行加工。
2 齿轮加工参数设定所使用的数控磨齿机具备四轴联动功能,具备多位置主轴和多种自动找正功能,配置西门子SINUMERIK 840D系统,具备良好的人及交互界面和强大的模拟功能。
(1)基本参数设定。
输入齿数、法向模数、法向压力角、跨棒距尺寸、量棒直径、跨齿数、齿形点频率等参数。
(2)确定渐进磨削方式。
为了避免在砂轮过于锋利等原因而导致的过切现象出现,数控系统设置了特殊的渐进磨齿方式。
15个齿磨削完成后,再重新把初始3个留有余量的齿进行最终尺寸的磨削,保证磨削精度。
3 齿形磨削及调整在工件第一个齿槽试磨完成后,必须在齿轮测量机上对齿形进行检测,依据检测结果对机床进行调整,对于CBN磨轮来说,齿形上的余量是否均匀、余量过多或过少不是“齿形调整”的主要内容。
4 齿向磨削及调整齿向磨削主要是齿面的鼓形量分布及调整,也是该零件加工的关键。
鼓形分布的调整是鼓形调整的依据,首先需要必须确保检验状态与标准的一致性。
如图2所示,在齿向的(零件轴线方向)鼓形曲线上测量所取的曲线段不同,测量结果也将不同。
若测量中取了左侧鼓形线中的A1-A2-A3线段,右侧鼓形线中的B1-B2-B3线段,测量结果就会显示鼓形有角度误差,上端齿形小,下端齿形大。
鼓形齿加工工艺

鼓形齿加工工艺
鼓形齿加工工艺是一种常见的齿轮制造方法,也是一种重要的齿轮加工工艺之一。
该工艺采用切削方法来加工齿轮,通过将齿轮的齿形和轮廓与齿轮机床上的刀具相匹配,从而实现齿轮的高效加工。
鼓形齿加工工艺的主要特点是:一是加工精度高,能够生产高精度、高强度的齿轮。
二是工艺稳定,可靠性高,生产效率高。
三是适用范围广,能够加工各种不同类型的齿轮,如直齿轮、斜齿轮、螺旋齿轮等。
鼓形齿加工工艺的主要步骤包括:齿轮加工前的准备工作,如测量、选择刀具等;齿轮加工前的预处理,如清洗、去油等;齿轮加工的主要过程,包括切削、调整刀具和齿轮的精度等;齿轮加工完成后的后处理,如清洗、检验等。
鼓形齿加工工艺的发展始于19世纪末期,目前已经成为了齿轮加工领域中的重要工艺之一。
随着科技的不断进步,鼓形齿加工工艺的加工精度和工艺稳定性也将得到进一步提高,其在工业生产中的应用也将越来越广泛。
- 1 -。
鼓形齿加工工艺

鼓形齿加工工艺
鼓形齿加工是一种常见的齿轮加工方式,其工艺流程包括齿形设计、加工准备、车削加工和磨削加工等步骤。
首先,鼓形齿的齿形设计需要考虑传动比、齿面的强度和平稳性等因素,同时根据齿轮的材质和精度要求进行合理的齿形设计。
对于加工准备,需要根据齿轮的尺寸和形状确定加工工艺路线和加工工具的选择,包括车削刀具、磨削砂轮等。
在车削加工过程中,需要注意切削速度、进给量和切削深度等参数的控制,以及刀具的润滑和冷却等问题,避免产生过多的热量和表面质量不佳的情况。
在磨削加工过程中,需要选择合适的砂轮和砂轮的结构形式,控制磨削参数和加工技巧,以获得较高的加工精度和表面质量。
总的来说,鼓形齿加工需要进行全面的工艺设计和加工参数的优化,以满足齿轮的精度和强度要求。
- 1 -。
齿部特殊修形磨齿加工研究

齿部特殊修形磨齿加工研究【摘要】通过研究成型磨齿齿形成型原理,精确控制齿形,实现快速调整。
通过研究砂轮修整原理掌握齿顶修缘磨齿加工,合理选择修形方式。
通过研究砂轮磨削成型及修整原理形成齿形齿向鼓形中心调整策略。
【关键词】成型法磨齿、齿轮精度、分段修形、齿顶修缘、鼓形中心1、齿部精度的对比分析目前重型汽车变速箱齿轮齿形要求齿形整体为一段圆弧,使用圆弧修形即可实现齿形的加工。
乘用车新能源变速箱齿轮齿形要求齿顶增加了修缘fko。
齿形分为主齿形和齿顶修缘,为了啮合的平稳性,对齿形鼓形中心要求严格,不能采取常规的修形方式进行加工,需寻求其它加工方式。
传统重型汽车变速器齿轮对于齿向仅要求齿向fhβ平均值,乘用车新能源变速器齿轮为了保证产品的噪音满足要求,对于齿向增加了Vβf及变动量的要求。
基于上述分析,乘用车新能源变速器齿轮相较于重卡变速器齿轮,加工难度大。
对于小批量产品采用蜗杆磨齿加工前期需投入金刚滚轮及砂轮,成本较高。
未固化产品齿形存在后期更改图纸的可能性,会导致金刚滚轮报废。
故本次加工采用成型磨齿加工。
2、修形方式产品图纸要求齿形分段评定,分为主齿形和齿顶修缘,且需要精准控制齿形压力角、鼓形大小和鼓形高点位置,为保证加工精度,首先要选取合适的齿形修形方式。
2.1、齿顶直线倒角修形齿顶直线倒角修行将整段齿形分为两段,两段结合处无光滑过渡,选择选取前提条件如下:①齿顶倒角修缘量,它是单边齿厚的减少量,产品图要求0.2mm②过渡圆角半径R,过渡圆角半径必须大于所选金刚石修整轮半径0.05mm以上,产品图要求R2。
③齿顶倒角起始圆直径,即渐开线终止圆直径。
YK7340A成型磨齿机自带金刚滚轮R1.5不满足上述条件,故未选择上述修行方式。
2.2、标准修行目前可供选择的方式还有标准修形,通过对修形各起点和终点的位置进行精确控制达到精确调整齿形压力角、鼓形量、鼓形值。
对照产品图纸齿形要求可以看出主齿形段的直线段比例尽可能小,可以保证主齿形圆滑。
航空高精度鼓形齿轮加工及齿面修形方法研究
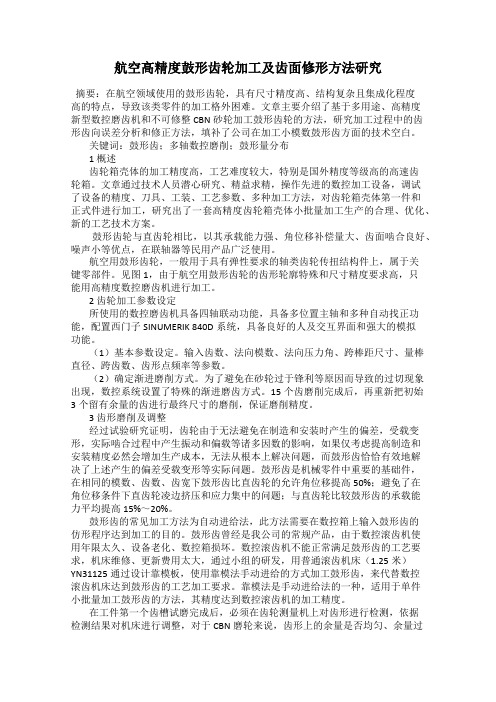
航空高精度鼓形齿轮加工及齿面修形方法研究摘要:在航空领域使用的鼓形齿轮,具有尺寸精度高、结构复杂且集成化程度高的特点,导致该类零件的加工格外困难。
文章主要介绍了基于多用途、高精度新型数控磨齿机和不可修整CBN砂轮加工鼓形齿轮的方法,研究加工过程中的齿形齿向误差分析和修正方法,填补了公司在加工小模数鼓形齿方面的技术空白。
关键词:鼓形齿;多轴数控磨削;鼓形量分布1 概述齿轮箱壳体的加工精度高,工艺难度较大,特别是国外精度等级高的高速齿轮箱。
文章通过技术人员潜心研究、精益求精,操作先进的数控加工设备,调试了设备的精度、刀具、工装、工艺参数、多种加工方法,对齿轮箱壳体第一件和正式件进行加工,研究出了一套高精度齿轮箱壳体小批量加工生产的合理、优化、新的工艺技术方案。
鼓形齿轮与直齿轮相比,以其承载能力强、角位移补偿量大、齿面啮合良好、噪声小等优点,在联轴器等民用产品广泛使用。
航空用鼓形齿轮,一般用于具有弹性要求的轴类齿轮传扭结构件上,属于关键零部件。
见图1,由于航空用鼓形齿轮的齿形轮廓特殊和尺寸精度要求高,只能用高精度数控磨齿机进行加工。
2 齿轮加工参数设定所使用的数控磨齿机具备四轴联动功能,具备多位置主轴和多种自动找正功能,配置西门子SINUMERIK 840D系统,具备良好的人及交互界面和强大的模拟功能。
(1)基本参数设定。
输入齿数、法向模数、法向压力角、跨棒距尺寸、量棒直径、跨齿数、齿形点频率等参数。
(2)确定渐进磨削方式。
为了避免在砂轮过于锋利等原因而导致的过切现象出现,数控系统设置了特殊的渐进磨齿方式。
15个齿磨削完成后,再重新把初始3个留有余量的齿进行最终尺寸的磨削,保证磨削精度。
3 齿形磨削及调整经过试验研究证明,齿轮由于无法避免在制造和安装时产生的偏差,受载变形,实际啮合过程中产生振动和偏载等诸多因数的影响,如果仅考虑提高制造和安装精度必然会增加生产成本,无法从根本上解决问题,而鼓形齿恰恰有效地解决了上述产生的偏差受载变形等实际问题。
鼓型齿式联轴器加工工艺
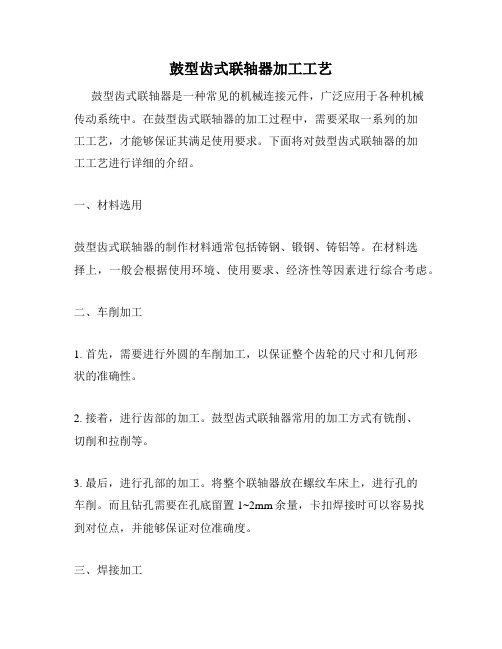
鼓型齿式联轴器加工工艺鼓型齿式联轴器是一种常见的机械连接元件,广泛应用于各种机械传动系统中。
在鼓型齿式联轴器的加工过程中,需要采取一系列的加工工艺,才能够保证其满足使用要求。
下面将对鼓型齿式联轴器的加工工艺进行详细的介绍。
一、材料选用鼓型齿式联轴器的制作材料通常包括铸钢、锻钢、铸铝等。
在材料选择上,一般会根据使用环境、使用要求、经济性等因素进行综合考虑。
二、车削加工1. 首先,需要进行外圆的车削加工,以保证整个齿轮的尺寸和几何形状的准确性。
2. 接着,进行齿部的加工。
鼓型齿式联轴器常用的加工方式有铣削、切削和拉削等。
3. 最后,进行孔部的加工。
将整个联轴器放在螺纹车床上,进行孔的车削。
而且钻孔需要在孔底留置1~2mm余量,卡扣焊接时可以容易找到对位点,并能够保证对位准确度。
三、焊接加工1. 接下来,是鼓型齿式联轴器的焊接加工。
焊接采用CO2 气体保护焊、埋弧焊、手工电弧焊等方式。
2. 在焊接前需要先预热处理。
具体的预热温度和保温时间取决于材质和尺寸等因素。
3. 焊接完毕后,需要进行清理焊渣和打磨等加工工序,以保障齿轮的质量。
四、热处理工艺1. 冷却后,进行淬火处理,以提高齿轮的硬度和耐磨性。
2. 淬火结束后还需进行回火处理,以消除内部应力和提高齿轮的塑性。
五、质量检测在加工完成之后,还需要进行质量检测以保证其满足使用要求。
主要检测内容包括尺寸精度、力学性能、表面质量等。
以上就是鼓型齿式联轴器加工工艺的详细介绍。
在加工过程中需要严格按照加工工艺要求进行操作,才能够保证齿轮的质量和稳定性。
成形法加工齿形的方法

成形法加工齿形的方法
成形法加工齿形的方法包括铣齿、成形磨齿、滚齿和插齿等。
其中,铣齿属于成形法加工,是用盘形模数铣刀或指状铣刀铣齿,刀具的齿廓与齿轮齿面的形状相适应。
该方法加工效率和加工精度均较低,仅适用于单件小批生产。
成形磨齿则是采用与被切齿轮齿槽形状相符的成形砂轮磨削齿轮齿面,主要用于淬硬的圆柱齿轮。
滚齿和插齿属于展成法加工,是通过刀具与工件按一定运动关系作相对运动,形成展成运动,由展成运动来切削齿形。
其中,滚齿是用齿轮滚刀在卧式滚齿机上加工齿轮,是一种常用的齿轮加工方法,适用于大量生产圆柱齿轮和蜗轮等。
插齿是用插齿刀在插齿机上加工齿轮,生产效率比滚齿低,但适用于加工内齿轮和多联齿轮。
一种精准滚鼓形齿加工对刀方法
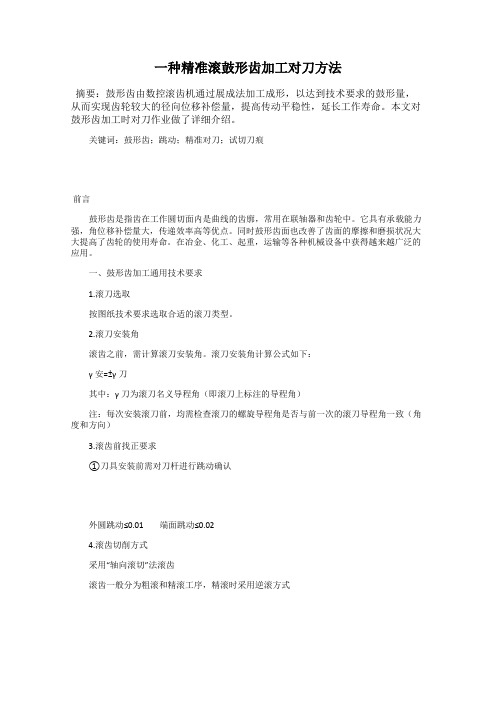
一种精准滚鼓形齿加工对刀方法摘要:鼓形齿由数控滚齿机通过展成法加工成形,以达到技术要求的鼓形量,从而实现齿轮较大的径向位移补偿量,提高传动平稳性,延长工作寿命。
本文对鼓形齿加工时对刀作业做了详细介绍。
关键词:鼓形齿;跳动;精准对刀;试切刀痕前言鼓形齿是指齿在工作圆切面内是曲线的齿廓,常用在联轴器和齿轮中。
它具有承载能力强,角位移补偿量大,传递效率高等优点。
同时鼓形齿面也改善了齿面的摩擦和磨损状况大大提高了齿轮的使用寿命。
在冶金、化工、起重,运输等各种机械设备中获得越来越广泛的应用。
一、鼓形齿加工通用技术要求1.滚刀选取按图纸技术要求选取合适的滚刀类型。
2.滚刀安装角滚齿之前,需计算滚刀安装角。
滚刀安装角计算公式如下:γ安=±γ刀其中:γ刀为滚刀名义导程角(即滚刀上标注的导程角)注:每次安装滚刀前,均需检查滚刀的螺旋导程角是否与前一次的滚刀导程角一致(角度和方向)3.滚齿前找正要求①刀具安装前需对刀杆进行跳动确认外圆跳动≤0.01端面跳动≤0.024.滚齿切削方式采用“轴向滚切”法滚齿滚齿一般分为粗滚和精滚工序,精滚时采用逆滚方式试加工刀痕示意图4.为保证产品质量要求,产品在滚齿加工时要求进行首件检验加工5.加工结束后,检查轮齿两端齿顶厚度,确认是否有变化,若有变化需调整机床6.公法线需100%检测,轮齿两端齿顶厚度需100%外观检查判断,也可通过齿轮测量仪进行检测评定。
齿轮测量仪检测报告:结论:鼓形齿轮齿形的加工是鼓形齿的关键工序,而鼓形齿精确的对刀操作又是该工序中的重要项点,对刀中心能有效保证齿轮鼓形量中心处于齿宽中线,齿顶两端的减薄量均匀对称,从而保证鼓形齿啮合时的接触精度,提高传递扭矩的平稳性和可靠性,便于安装和拆卸,充分发挥鼓形齿的效能。
参考文献:[1]易传云、肖来元鼓形齿联轴器[M].武汉.华中理工大学出版社.1999[2]王青云,阮启刚.鼓形齿齿轮的数控加工[J].黄石高等专科学校学报,2003,19(2):1-2.[3]谢红,周国平,杨君伟,等.数控化改造 Y3180H 滚齿机加工鼓形齿齿轮[J].制造技术与机床,2005(2):41-42.[4]张海涛.350km/h 高速动车组用鼓形齿联轴器的研究与开发[D].成都:西南交通大学,2007:1-2.。
鼓筒轴的蓖齿磨削技术

鼓筒轴的蓖齿磨削技术
陆湘秀
【期刊名称】《航空工艺技术》
【年(卷),期】1996(0)3
【摘要】概述了鼓筒轴的主要作用、特点;重点论述了蓖齿成型工艺,如工艺参数的选择、砂轮滚刀、砂轮滚刀心轴、磨工心棒结构设计;并简单地介绍了蓖齿的测量。
【总页数】2页(P35-36)
【关键词】篦齿;磨削;工艺;航空发动机
【作者】陆湘秀
【作者单位】南方动力机械公司
【正文语种】中文
【中图分类】V232.2;V261.25
【相关文献】
1.鼓型齿接轴内循环润滑技术优化 [J], 高伟
2.鼓筒轴篦齿的磨削技术 [J], 陆湘秀
3.鼓筒轴的篦齿磨削技术 [J], 陆湘秀
4.摆线齿轮的鼓形齿磨削 [J], 张建军;梁锡昌
5.摆线马达鼓形齿传动轴共轭齿面及其近似加工方法 [J], 陈忠强
因版权原因,仅展示原文概要,查看原文内容请购买。